- 1Department of Microbiology, Faculty of Science, Chulalongkorn University, Bangkok, Thailand
- 2Department of Chemical Engineering, Chungbuk National University, Cheongju, Chungbuk, Republic of Korea
- 3International Center for Biotechnology, Osaka University, Osaka, Japan
Cassava pulp is one of the most abundant agricultural residues that can cause serious disposal problems. This study aimed to apply a biorefinery approach by examining the feasibility of microwave-assisted cassava pulp hydrolysis to attain sustainable management and efficient use of natural resources. Four factors, namely, the liquid-to-solid ratio (20 mL/g, 10 mL/g, 7.5 mL/g, and 5 mL/g), types of acids (H2SO4 and H3PO4), watt power (600 W, 700 W, and 800 W) and time (3, 5 and 8 min), were carefully investigated. The highest fermentable sugar content of 88.1 g/L ± 0.7 g/L (0.88 g fermentable sugars/g dry cassava pulp) was achieved when 20 mL/g cassava pulp was hydrolyzed with 2.5% (v/v) H2SO4 under microwave irradiation at 800 W for 8 min. Glucose was a major product (82.0 g/L ± 5.2 g/L). The inhibitor concentration was 5.17 g/L ± 0.01 g/L, and the levulinic acid concentration was 5.15 g/L ± 0.01 g/L. The results indicated that the liquid-to-solid ratio, diluted acid concentration, irradiation watt power and time were important factors in producing fermentable sugars from acid hydrolysis under microwave irradiation. The crude hydrolysate was used for PHB production by Cupriavidus necator strain A-04. The hydrolysate to nutrients ratio of 30:70 (v/v) yielded a cell dry weight of 7.5 g/L ± 0.1 g/L containing PHB content of 66.8% ± 0.3% (w/w), resulting in a yield
1 Introduction
Recently, biorefinery has been adopted as a bottom line technology in biotechnological processes because it integrates white and green biotechnology by converting lignocellulosic wastes into high-value-added products to attain sustainability (Barcelos et al., 2018; Areepak et al., 2022). Approximately 181.5 billion tons per year of lignocellulosic wastes have been significantly generated, whereas only 8.2 billion tons per year are used to produce value-added food and non-food bioproducts; however, 1.2 billion tons from agriculture residues are still leftover (Ubando et al., 2020; Areepak et al., 2022). According to the report of the Food and Agriculture Organization (FAO) in 2019, approximately 14 per cent of the global food, which is worth $400 billion annually, was lost after it was harvested before arriving at the stores (FAO, 2019). Meanwhile, the United Nations Environment Program (UNEP)’s Food Waste Index Report reveals that an additional 17 per cent of food is wasted in retail and by consumers, particularly in households (United Nations Environment Programme, 2021). Theoretically, individuals who are a part of the food supply chain are responsible for making their own decisions so that they will maximize their own profits or consumers’ benefits. For example, a food processor might experience some physical food loss that could be reduced by investing in better operational management or more advanced equipment; however, the cost of doing so would be greater than the potential value of the food that could be recovered, so the food processor decides not to proceed that tasks (Food and Agriculture Organization, 2019). Therefore, agricultural food waste evaluation is crucial from both an environmental and financial standpoint. The impact of agricultural food waste has a detrimental influence on food security and nutrition and notably contributes to greenhouse gas (GHG) emissions, serious environmental issues, natural ecosystem degradation, and biodiversity loss. There is an urgent need to significantly boost the usage of agricultural food wastes, which are renewable resources. Predominant examples of renewable resources include crop wastes and leftovers produced during crop production and food processing. These factors motivate scientists to devise strategies for turning agricultural and industrial food wastes into useful value-added products. One of the examples of agricultural food wastes is casava pulp derived from cassava industries. The negative impact of cassava wastes on the environment and health has been one of the challenges. In this regard, the organic wastes from cassava-based industries have enormous potential to generate diverse higher-value products by adopting a biorefinery concept (Pandey et al., 2000; Zhang et al., 2016). For instance, casava pulp can be used as the primary substrates for microorganisms to produce valuable products such as enzymes, antibiotics, polysaccharides, antioxidants, organic acids, biofuels, biogas, biosurfactant, biopolymers and other beneficial biochemical products (Zhang et al., 2016). It has a considerable potential for bioconversion into value-added products via biorefinery due to its complex biochemical compositions containing high organic content, which enables the cassava industries to be both economically and environmentally sustainable.
Cassava (Manihot esculenta), widely recognized as manioc, yucca, and tapioca plant, is the third largest food carbohydrate source cultivated in tropical and subtropical regions (Tur and Bibiloni, 2016). It has been widely used in i) human food, ii) animal feed, iii) biofuel, and iv) biotechnological factories (Sowcharoensuk, 2021). Approximately 302 million tons of cassava were produced worldwide in 2021/22. The biggest cassava starch producer is Nigeria (21.6%). Thailand has been ranked as the second largest cassava starch producer (10.7%) and exporter with a production capacity of 35.1 million tons (Office of Agricultural Economics, 2021). Consequently, cassava pulp is also generated in a large amount, approximately 10% of raw material, and contains 40%–60% of residual starch trapped in residual fibers (Sudha et al., 2015). Cassava pulp is easily available, inexpensive, plentiful, and renewable agriculture residues (Sriroth et al., 2000). Additionally, the utilization of cassava pulp is considered as the second-generation biorefineries since it is biomass waste and non-edible crops as feedstock (Mathioudakis et al., 2017). Despite the fact that a lot of cassava pulp is generated, the issue persists since the process is unmanaged and the cassava waste is typically kept in an open location. Accordingly, it immediately spoils and emits an unpleasant and strong scent. Moreover, the use of cassava pulp has been proposed in various applications, such as animal feeds (Diarra and Devi, 2015; Dagaew et al., 2022; Pongsub et al., 2022), bioethanol (Rattanachomsri et al., 2009; Siriwong et al., 2019), succinic acid (Sawisit et al., 2015), lactic acid (Thongchul et al., 2010; Gali et al., 2021), fertilizer (Phun-iam et al., 2018; Hasanudin et al., 2019), biogas (Lerdlattaporn et al., 2021), biodegradable polymer (Hierro-Iglesias et al., 2022) and biocomposites (Nguyen et al., 2020; Nithikarnjanatharn and Samsalee, 2022). Clearly, high value-added products can be created from leftover cassava wastes generated by the cassava industry. In addition to the direct use of cassava pulp, our focus was on the preparation of fermentable sugars for the microbial cultivation to produce value-added products because of its rich organic nature and low ash content owing to a great opportunity to utilize it in various biorefinery platforms (Pandey et al., 2000; Zhang et al., 2016).
This study focuses on development of fast and simple method for conversion of cassava pulp to fermentable sugars with low inhibitor concentrations. The hydrolysis of cassava pulp has been extensively studied through alkaline pretreatment of lignin (Kanchanasuta et al., 2020), acid hydrolysis (Binder and Raines, 2010), enzyme hydrolysis (Rattanachomsri et al., 2009; Bunterngsook et al., 2017) and a combination of the above methods (Thongchul et al., 2010). The significant time and energy consumption of the aforementioned technologies are their shortcomings. This generally happens when optimizing different material properties by adjusting existing strategies. More recently, some scientists have reported microwave-assisted hydrolysis based on a microwave synthesis reactor that offers temperature control, time and radiation watt input. Microwave-assisted hydrolysis has been of interest because it is a quick and simple method for converting biomass into useful products (Tsubaki et al., 2008; Yoshida et al., 2010; Zhang and Zhao, 2010; Sweygers et al., 2018; Shangdiar et al., 2022). These reports have inspired us to use household microwaves to assist diluted acid hydrolysis using cassava pulp for biodegradable polyhydroxybutyrate (PHB) production. The objective of this study was to develop direct hydrolysis and saccharification processes based on the synergistic action of diluted acid and microwaves for cassava pulp without a pregelatinization step. Crude hydrolysate without inhibitor removal obtained from optimized conditions was applied in PHB production using the levolinic acid-tolerant, glucose- and fructose-utilizing bacterium Cupriavidus necator strain A-04 (Sukruansuwan and Napathorn, 2018). This study proposes a non-pretreatment and non-hyperthermal saccharification process as an alternative method for bioconversion of cassava pulp to PHB and other value-added products.
2 Article types
Original Research Articles in a Research Topic Title: “The Value of Microbial Bioreactors to Meet Challenges in The Circular Bioeconomy".
Topic Editor(s): Wan Abd Al Qadr Imad Wan Mohtar, Neil J Rowan, Zul Ilham.
3 Materials and methods
3.1 PHB-producing strains
Cupriavidus necator strain A-04, which was previously reported to tolerate inhibitors in pineapple waste hydrolysate and to convert fermentable sugars without detoxification to PHB, was used in this study (Chanprateep and Kulpreecha, 2006; Chanprateep et al., 2008; Sukruansuwan and Napathorn, 2018; Wongmoon and Napathorn, 2022). The bacterial strain was cultured on a nutrient agar slant at 4°C. Stock cultures were maintained at −80°C in a 15% (v/v) glycerol solution.
3.2 Carbon sources
Fresh casava pulp was obtained from Thai Wah Public Company Limited (Thailand). It was dried in a hot-air oven (UN55, Memmert GmbH + Co. KG, Schwabach, Germany) setting the temperature at 65°C overnight and milled using a high-speed blender with maximum speed at 45,000 rpm (1,800-W, Healthy mix GP 3.5, Taiwan). Next, they were sieved with 20 mesh to obtain particle sizes less than 0.841 mm (−20 mesh). The moisture content was determined according to AOAC Official Method 934.06 (AOA, 1999). The chemical compositions of casava pulp were determined according to the Technical Association of Pulp and Paper Industry (TAPPI) standard methods parameters (TAPPI T 204 cm-07, TAPPI T203 om-09, TAPPI T9 m-54, TAPPI T222 om-15, TAPPI T-211). The remaining cassava starch was extracted from cassava pulp (Ahtong and Charoenkongthum, 2002).
3.3 Microwave irradiation
Microwave irradiation was conducted using a household microwave oven (max output; 800 W, ME711K model, Samsung Electronics Co., Ltd., Malaysia). The position of the hot spot inside the microwave chamber was identified using copying paper. The amount of dried and sieved cassava pulp was varied from 5, 10, 15 and 20 (w/v) and dissolved in 100 mL of 0.25% (v/v) H2SO4 or H3PO4 and microwaved in a closed system in a 500 mL Duran® round bottle with a high-temperature red polybutylene terephthalate (PBT) screw cap with a polytetrafluoroethylene (PTFE) silicone cap liner. The types of acid, concentrations, watts power and irradiation time were investigated as one factor at a time. The concentrations of H2SO4 and H3PO4 were varied individually from 0%, 0.25%, 0.5%, 1%, and 2% (w/v) using a microwave with 800 W for 8 min by placing an Erlenmeyer flask on the identified hotspot. Then, the watt output was varied from 600 W, 700 W, and 800 W, and the heating time was varied from 3, 5 and 8 min. Water was used as a control experiment under identical conditions. The temperature of the resulting samples was measured. The supernatant was filtered through Whatman filter paper (No. 1, pore size of 11 μm, Sigma‒Aldrich Corp., St. Louis, MO, United States). The filtrate was neutralized using 2 M NaOH to obtain neutralized hydrolysate.
3.4 Culture conditions for PHB production from hydrolysate
Firstly, seed culture was prepared in 500-mL Erlenmeyer flasks containing 100 mL of preculture medium. The seed culture medium formula was 2 g/L yeast extract, 10 g/L polypeptone and 1 g/L MgSO4∙7H2O (Yabueng and Napathorn, 2018). The seed culture was grown on a rotary incubator shaker (Innova 4,300, New Brunswick Scientific Co., Inc., Edison, NJ, United States) at 30°C and 200 rpm for 24 h. The bacterial cells were separated from seed culture medium by centrifugation and washed to remove residual medium with 0.85% sodium chloride solution and resuspended in 100 mL 0.85% sodium chloride solution. Next, to promote the synthesis of PHB, the cells suspension were transferred into a production medium which was the same as previously described (Sukruansuwan and Napathorn, 2018) with modifications to favor cell growth and PHB production. The ratio of hydrolysate to production medium was varied from 100:0%, 90:10%, 80:20%, 70:30%, 60:40%, and 50:50% (v/v). The cultivation was performed in a shaken flask cultivation at 30°C and incubated on rotary shaker with shaking speed at 200 rpm for 96 h. Culture samples were harvested at 12-h intervals.
3.5 Analytical methods
Bacterial cell growth was monitored as cell dry mass, CDM, which was performed by cell filtration. Briefly, cellulose nitrate membrane with pore size of 0.22 μm (Sartorius, Goettingen, Germany) was weighted beforehand. Then, 5 mL of the culture broth was filtrated and dried at 80°C overnight and kept in desiccators until a constant weight was obtained. The residual cell mass, RCM, was calculated by subtracting the amount of PHB from CDM. The whole-cell methyl esterification was performed with additional modifications from Bruanegg et al. (1978) to quantify PHB in dried cells by gas chromatography (Model CP3800, Varian Inc., Walnut Creek, CA, United States) using a Carbowax-PEG capillary column (0.25-μm df, 0.25-mm ID, 60-m length, Varian Inc.) (Braunegg et al., 1978; Chanprateep et al., 2001). The benzoic acid was used as internal standard. The commercialized natural origin PHB was used as external standard (Sigma‒Aldrich Corp.). The concentration of monosaccharide (xylose, glucose, fructose, galactose and arabinose) and disaccharide (sucrose and cellobiose) in hydrolysate were analyzed by a high-performance liquid chromatograph (Model 626, Alltech Inc., Nicholasville, KY, United States) as described previously (Sukruansuwan and Napathorn, 2018). The eluent solution was water at a flow rate of 0.6 mL/min. The operating temperature was set at 60°C. The concentration of inhibitors (levulinic acid, 5-hydroxymethyl furfural (5-HMF) and furfural) in hydrolysate were analyzed using HPLC equipped with an ultraviolet (UV) detector setting a wavelength of 285 nm (Prostar 335, Varian Inc., Walnut Creek, CA, United States) and a ChromSpher C18 column (4.6-mm ID × 250-mm length, Varian Inc., Walnut Creek, CA, United States). The mixed solution of methanol:acetic acid:water (12:1:88, v/v) was used as the eluent solution at a flow rate of 1.0 mL/min at the operating temperature of 25°C. The concentration of
3.6 Data analysis
The data shown in this study were obtained from at least three independent experiments and expressed as the mean values ± standard deviations (SDs). Analysis of variance by t-test or one-way ANOVA was conducted using SPSS version 22 (IBM Corp., Armonk, NY, United States). Differences were considered significant at p < 0.05.
4 Results
4.1 Lignocellulosic compositions of casava pulp
The chemical composition of cassava pulp used in this study was analyzed, and the major components were 49.0% ± 0.2% (w/w) starch, 25.4% ± 0.2% (w/w) cellulose, 6.1% ± 0.01% (w/w) hemicellulose, 5.8% ± 0.01% (w/w) lignin and 11.0% ± 0.03% (w/w) others (such as protein, fat, ash) with a moisture content of 78.7% ± 0.5% (w/w), as shown in Table 1. Therefore, starch and lignocellulosic fibrous material remaining in cassava pulp are abundant tropical agro-industrial biowaste that can be revalorized to valuable and green products through integrative biorefineries. In this study, the lignocellulosic compositions of cassava pulp may be different from those reported previously depending on the starch milling process, plant variety, growth conditions, soil conditions, and other environmental factors, such as pH, temperature, fertilizer, watering and climate (Sriroth et al., 2000; Rattanachomsri et al., 2009; Virunanon et al., 2013; Sudha et al., 2015).
4.2 Optimal conditions for microwave-assisted cassava hydrolysis
Factors influencing dilute acid hydrolysis, including reactant concentration, liquid-to-solid ratio, watt power and irradiation time, were carefully investigated in this study. The −20 mesh particle size was applied for cassava pulp hydrolysis according to a previous report (Sukruansuwan and Napathorn, 2018).
4.2.1 Effects of dry casava pulp content on the hydrolysis reaction
It has been reported the sugar yield from lignocellulosic materials increased as the liquid-to-solid ratio increased. Nevertheless, the overall cost of hydrolysis increases resulting in an increase in the cost of the subsequent fermentation and downstream processes (Chen, 2015). Generally, a liquid-to-solid ratio of 5 mL/g–20 mL/g was suggested for the acid hydrolysis reaction. In this study, the liquid-to-solid ratio was varied from 20 mL/g, 10 mL/g, 7.5 mL/g, and 5 mL/g (equal to the amount of dry casava pulp 5%, 10%, 15%, and 20% (w/v) in the 100 mL hydrolysis reaction). First, microwave irradiation was performed using 2.5% (v/v) H2SO4 at 800 W for 8 min. It was found that a liquid-to-solid ratio less than 20 mL/g was not suitable for the hydrolysis reaction, as starch granules absorbed all acid solution and became glutinous solution. Then, after microwave irradiation, the heat energy resulted in burnt and brown gelatinization (Supplementary Figure S1). The hydrolysate solution could not be separated from starch gelatinization. In addition, as shown in Figure 1, the liquid-to-solid ratio of 20 mL/g hydrolyzed with 2.5% (v/v) H2SO4, 800 W for 8 min gave the highest concentration of fermentable sugars and inhibitors. Notably, glucose (82.0 g/L ± 5.3 g/L) was a major component, followed by xylose (30.7 g/L ± 3.7 g/L), galactose (4.7 g/L ± 0.9 g/L) and arabinose (1.4 g/L ± 0.2 g/L). Fructose was not detected under this condition. The major inhibitor composition was levulinic acid (5.2 g/L ± 0.1 g/L), followed by 5-HMF (0.02 g/L ± 0.0 g/L) and furfural (0.005 g/L ± 0.0 g/L). The total concentration of fermentable sugar was 88.1 g/L ± 0.6 g/L, resulting in a yield coefficient of g-fermentable sugars from g-cassava pulp (
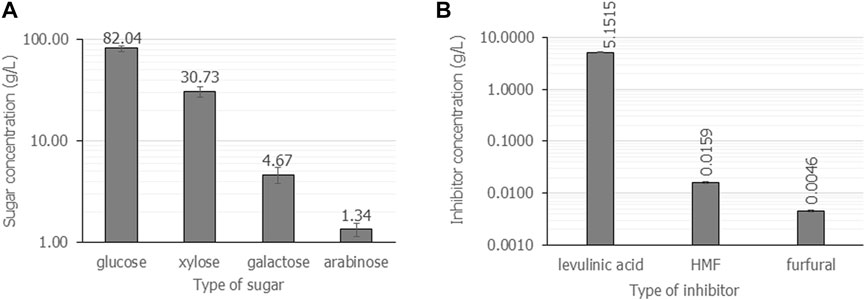
FIGURE 1. The composition of fermentable sugars (A) and inhibitors (B) when cassava pulp was hydrolyzed with liquid-to-solid ratios of 20 mL/g using 2.5% (v/v) H2SO4 under microwave irradiation at 800 W for 8 min. All the data are representative of the results of three independent experiments and are expressed as the mean values ± standard deviations (SD).
4.2.2 Effect of acid types and concentrations from casava pulp hydrolysis under microwave irradiation on the yield of sugars and inhibitors
Next, cassava pulp was hydrolyzed with three different solutions: H3PO4, H2SO4 and water. The concentration of acids was varied from 1%, 1.5%, 2%, 2.5%, and 3% (v/v) at different hydrolysis times for 1, 3, 6 and 8 min with an irradiation power of 800 W. The result shows that, as a control experiment, water hydrolysis of cassava pulp with a liquid-to-solid ratio of 20 mL/g at 800 W for 8 min gave 1.3 g/L ± 0.01 g/L, 1.9 g/L ± 0.01 g/L, 2.27 g/L ± 0.01 g/L, and 2.93 g/L ± 0.01 g/L of total fermentable sugars, respectively. The irradiation time had a positive effect on increasing fermentable sugar concentrations, which may be attributed to increasing the reactant temperature.
Consequently, the hydrolysis of casava pulp using a liquid-to-solid ratio of 20 mL/g by 1%, 1.5%, 2%, 2.5%, and 3.0% (v/v) H3PO4 at different irradiation times of 1, 3, 6 and 8 min was investigated. The irradiation power was set at 800 W. Unfortunately, H3PO4 gave a glutinous solution, and it was impossible to obtain filtrated hydrolysate, as shown in Supplementary Figure S2. Hence, the use of H3PO4 for acid hydrolysis was omitted in this study, as cassava pulp hydrolysis requires higher concentrations and stronger acids than H3PO4. The resulting fermentable sugars and inhibitors obtained from 3% H3PO4 at 800 W for 8 min are presented in Table 3.
In parallel, H2SO4 was tested under the same range of acid concentrations. Figure 2 shows the composition of fermentable sugars and inhibitors obtained from cassava pulp the hydrolysis with 1%, 1.5%, 2%, 2.5%, and 3% (v/v) H2SO4 under microwave irradiation at 800 W for 8 min. The results summarized in Figures 2A revealed that cassava pulp hydrolysis under microwave irradiation using 2.5% (v/v) H2SO4 gave the highest glucose concentration and total fermentable sugars. Notably, glucose was a major component in all experiments. Notwithstanding, at 3.0% (v/v) H2SO4, xylose was the major component (63.60 g/L ± 2.4 g/L), but total fermentable sugars decreased from 88.1 g/L ± 0.6 g/L to 80.8 g/L ± 0.7 g/L (Figure 2B). Xylose was not produced with H2SO4 concentrations lower than 2.0% (v/v) (Figure 2A). Additionally, the highest 5.6 g/L ± 0.69 g/L inhibitors were obtained with 2.0% (v/v) H2SO4 (Figure 2B), and levulinic acid was the major component. Overall, the concentration of 1.5% (v/v) (v/v) H2SO4 was the optimal acid concentration for cassava pulp hydrolysis under microwave irradiation based on unpresented xylose.
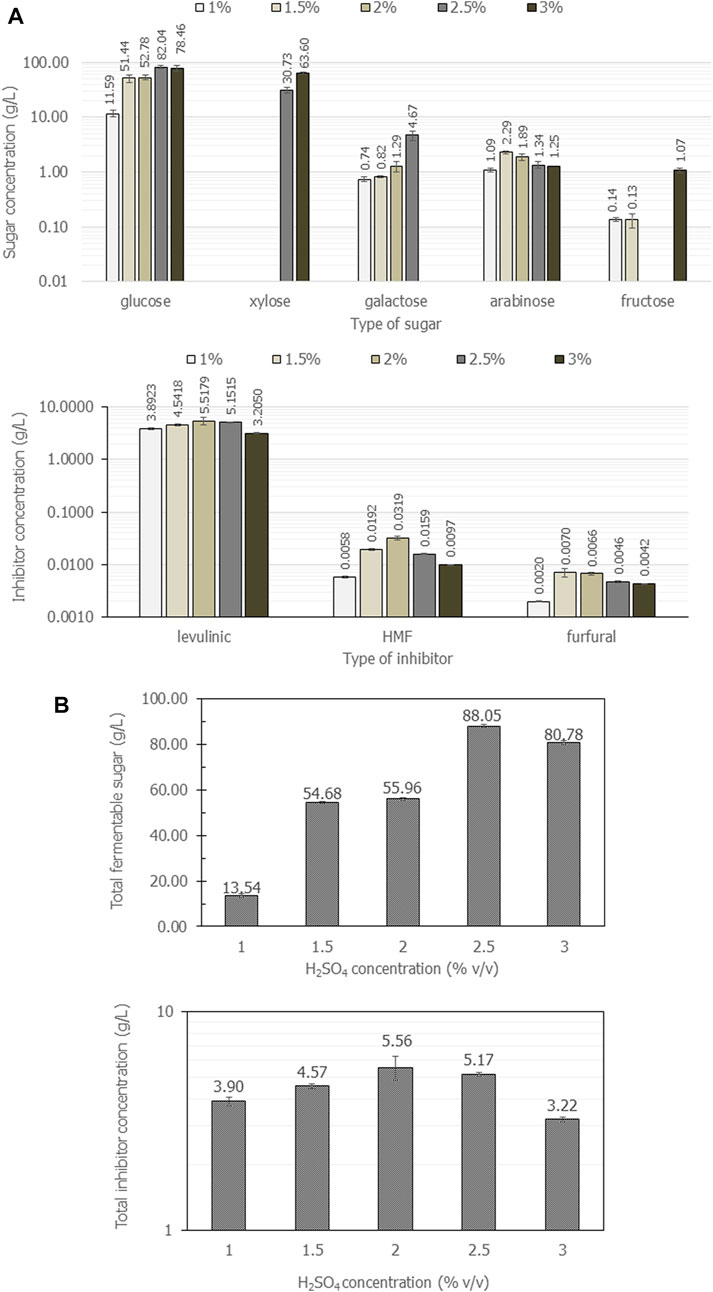
FIGURE 2. The composition of fermentable sugars and inhibitors (A) and total amount of fermentable sugars and inhibitors (B) when cassava pulp was hydrolyzed with liquid-to-solid ratios of 20 mL/g using 1%, 1.5%, 2%, 2.5%, and 4% (v/v) H2SO4 under microwave irradiation at 800 W for different times for 3, 5 and 8 min. All the data are representative of the results of three independent experiments and are expressed as the mean values ± standard deviations (SD).
4.2.3 Effect of microwave irradiation power and time on total fermentable sugars
The wattage power and time were carefully investigated in detail for cassava pulp hydrolysis using H2SO4. The summarized results are demonstrated in Figure 3; Table 2. In Figure 3, the cassava pulp hydrolysis condition was 2.5% (v/v) H2SO4, and the irradiation power was varied at 600 W (Figure 3A), 700 W (Figure 3B) and 800 W (Figure 3C) for 3, 5 and 8 min, respectively. The total fermentable sugars increased from 39.0 g/L ± 0.6 g/L (
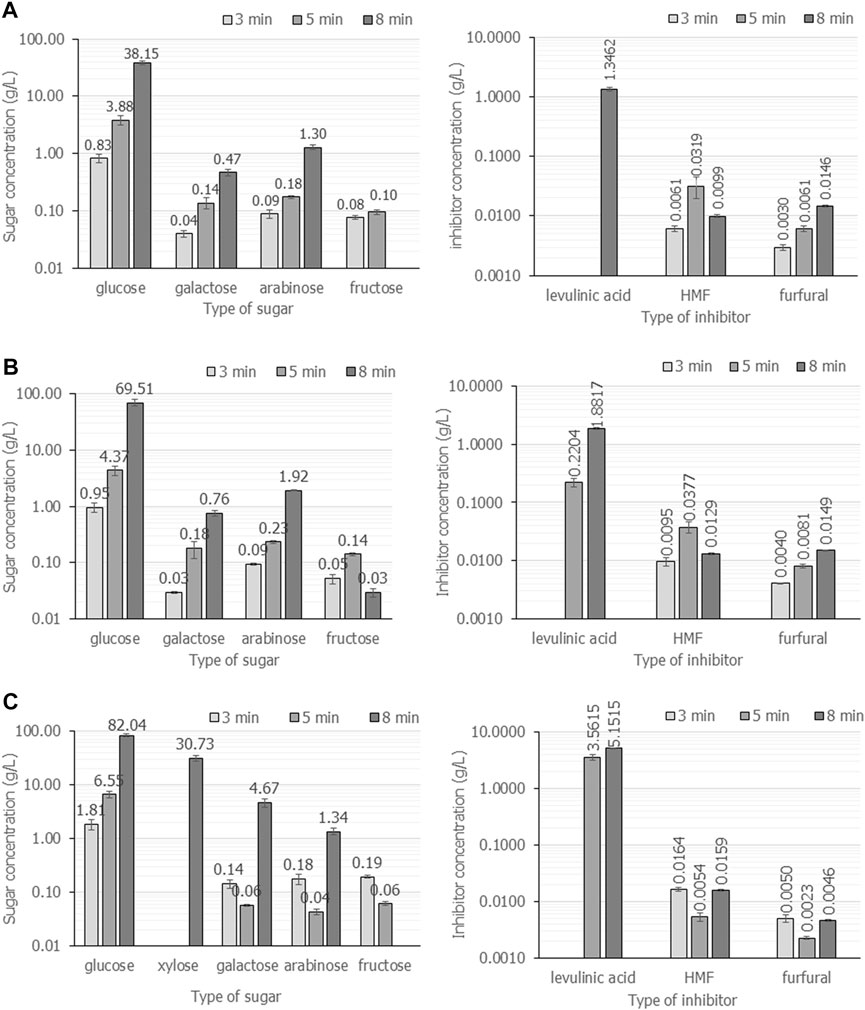
FIGURE 3. The composition of fermentable sugars and inhibitors when cassava pulp was hydrolyzed with liquid-to-solid ratios of 20 mL/g using 2.5% (v/v) H2SO4 under microwave irradiation at 600 W (A), 700 W (B) and 800 W (C) for 3, 5 and 8 min, respectively. All the data are representative of the results of three independent experiments and are expressed as the mean values ± standard deviations (SD).
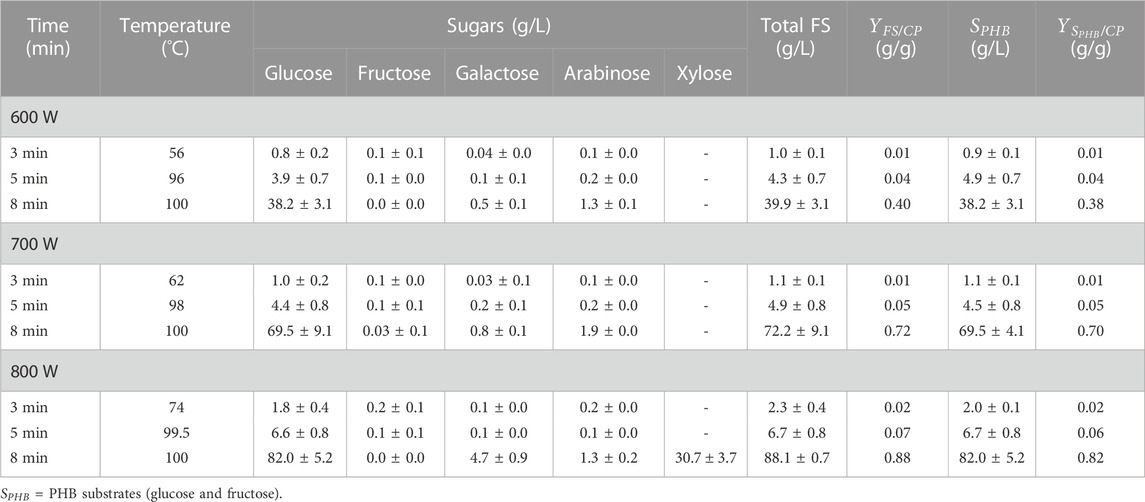
TABLE 2. Effect of wattage power and time on sugar yield and reactant temperature. Five grams of samples were hydrolyzed with 2.5% (v/v) H2SO4 and wattage power was varied at 600 W, 700 W, and 800 W for 3, 5 and 8 min.
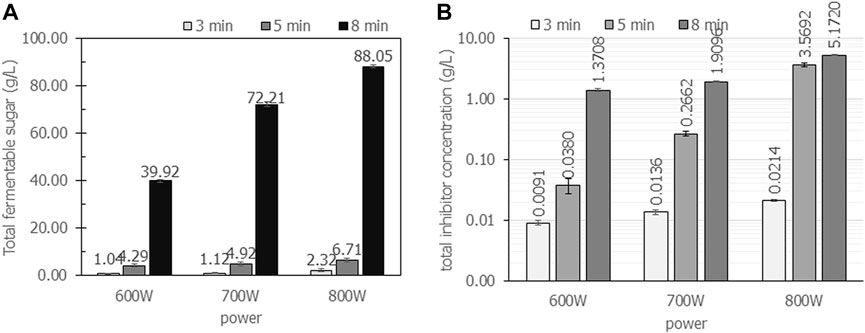
FIGURE 4. The total concentration of fermentable sugars and inhibitors when cassava pulp was hydrolyzed with liquid-to-solid ratios of 20 mL/g using 2.5% (v/v) H2SO4 under microwave irradiation at 600 W, 700 W and 800 W for 3, 5 and 8 min, respectively. All the data are representative of the results of three independent experiments and are expressed as the mean values ± standard deviations (SD).
The effect of irradiation power and time on the total concentration of sugars and inhibitors is clearly observed. The maximum power of the household microwave is 800 W. An irradiation time above 8 min results in boiling of the acid solution that causes volatile acids and is harmful to the operator. The effect of irradiation power and time on reactant temperature is depicted in Table 2. Increasing irradiation time resulted in increasing reaction temperature. For an irradiation time of 8 min, the reaction temperature reached 100°C in all experiments. In addition, the sugar concentration of 88.1 g/L ± 0.7 g/L containing glucose concentration of 82.0 g/L ± 5.2 g/L would be enough for further microbial conversion to value-added products, i.e., polyhydroxybutyrate production.
Finally, the effects of H2SO4 concentration, irradiation power and irradiation time on total fermentable sugars and inhibitors are summarized in Table 3. The fermentable sugars increased as the H2SO4 concentration, irradiation power and time increased. The hydrolysate obtained from 2.0% (v/v) or 1.5% (v/v) H2SO4 with an irradiation power of 800 W for 8 min was suitable for microorganisms sensitive to xylose.
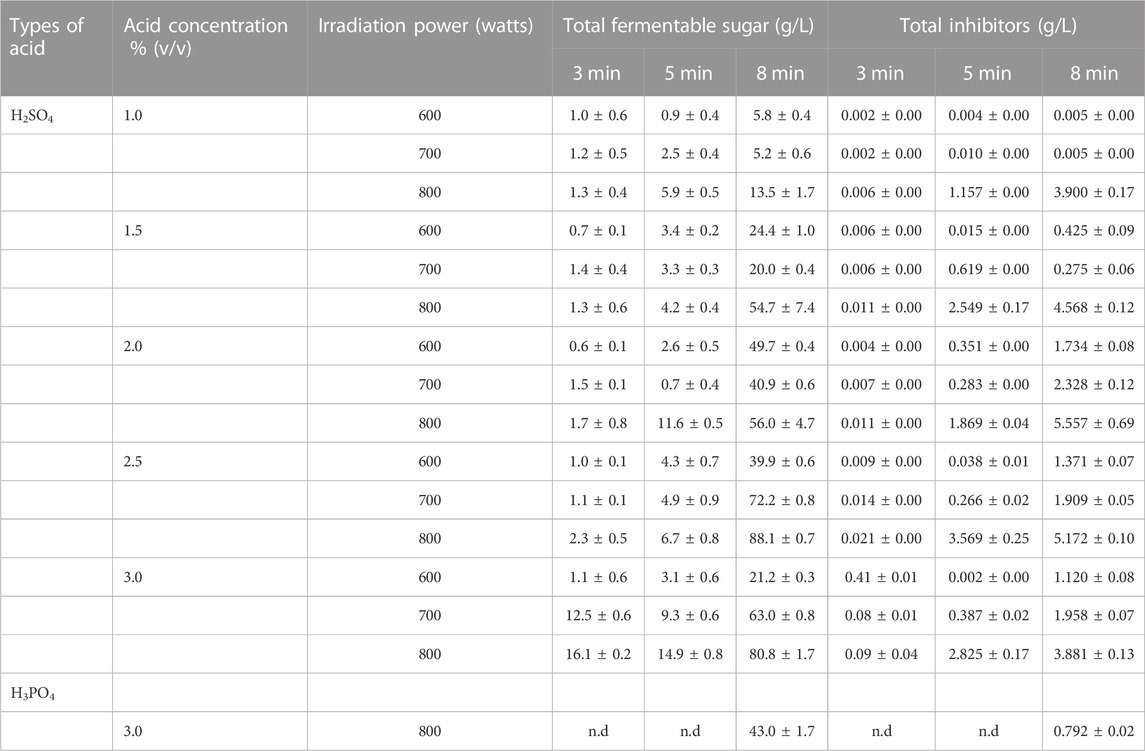
TABLE 3. Effect of H2SO4 concentration, irradiation power and time on total fermentable sugar. Five grams of samples were hydrolyzed with 1, 1.5, 2, 2.5, 3% (v/v) H2SO4 and 3% (v/v) H3PO4 and wattage power was varied at 600 W, 700 W, and 800 W for 3, 5 and 8 min.
Overall, as shown in Table 2, the irradiation power and time play the most important role in the internal thermal effect which is generated by the direct interaction between the heated material and electromagnetic field in microwave heating, and consequently producing rapid and volumetric heating (Özbek et al., 2021). In addition to the thermal effects of microwave, the non-thermal effects also provide a physical explosion effect within the microfibers, which speed up the breakdown of the resistant lignocellulosic structure. These abovementioned factors may cause a shorter time in the cassava pulp conversion to sugars by the application of microwave with dilute acid catalyst.
4.3 PHB production by Cupriavidus necator strain A04 using cassava pulp hydrolysate without removal of inhibitors
The high concentration of fermentable sugars obtained from microwave-assisted acid cassava pulp hydrolysis can be considered a food waste biorefinery framework. Glucose was the major component containing low concentrations of inhibitors. Therefore, the hydrolysates can be applied in various aspects for microbial products without the need for alkaline pretreatment and inhibitor removal steps. In this study, a case study was tested for biodegradable polyhydroxybutyrate (PHB) production. In a previous study, Cupriavidus neactor strain A-04 was reported to tolerate inhibitors present in the hydrolysate prepared from pineapple core and pineapple peel and produced PHB without removal of inhibitors (Sukruansuwan and Napathorn, 2018). Thus, C. necator strain A-04 was chosen as a model for converting hydrolysate prepared from cassava pulp to PHB. The
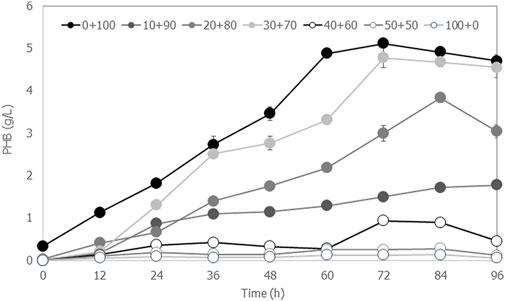
FIGURE 5. Time courses of PHB production by Cupriavidus necator strain A-04 when the hydrolysate was mixed with mineral salt medium at ratios of 0:100, 10:90, 20:80, 30:70, 40:60, 50:50 and 100:0 (v/v), where the C/N ratio was set at 200. All the data are representative of the results of three independent experiments and are expressed as the mean values ± standard deviations (SD).
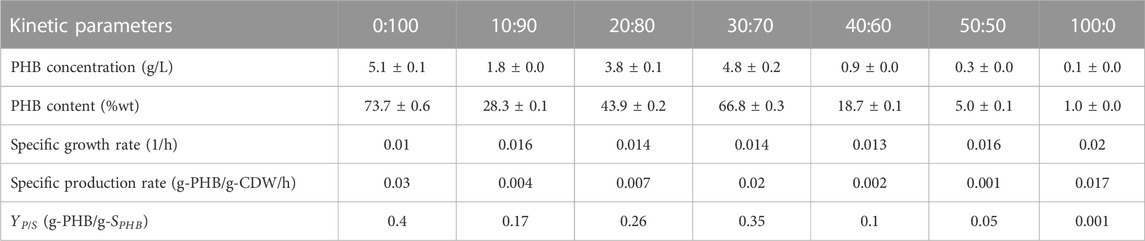
TABLE 4. Kinetics of cell growth, sugar consumption and PHB production by Cupriavidus necator strain A-04 using hydrolysate mixed with mineral salts medium 0:100, 10:90, 20:80, 30:70, 40:60, 50:50 and 100:0 (v/v) where C/N ratio was set at 200 in all experiments.
5 Discussion
To comply with a circular bioeconomy, the conversion of lignocellulosic agricultural and forestry wastes to biofuels, chemicals and biopolymers using clean and green processes has been considered a second-generation biorefinery. As demonstrated in Table 1, cassava pulp is a rich starch waste containing 40%–80% starch and 20%–40% fibers depending on the starch milling technology, plant variety and other environmental factors (Zhang et al., 2016; Bunterngsook et al., 2017). The milling process can be operated either manually or mechanically. For instance, the effect of starch milling machines on cooked cassava flour quality has been studied using the milling commenced with mortar mill, attrition, hammer, and the pin mills (Adesina and Bolaji, 2013). The composition of cassava pulp varied due to the difference in starch extraction efficiency which contributes to starch content remaining in fibers. The cassava pulp used in this study was obtained using the wet milling process with a saw-tooth rasper (Sriroth et al., 2000; Tran et al., 2015). In this study, the cassava pulp consisted of 40.6% ± 0.2% starch, 40.4% ± 0.2% cellulose and 6.1% ± 1.0% hemicellulose. Due to the effectiveness of the milling process utilized by the starch producing company, the starch concentration trapped in cassava pulp was one of the lowest in Thailand (see Table 1). The lignin content was only 2.0% ± 0.1%, so alkaline pretreatment to remove lignin was not necessary.
Lignocellulosic biomass typically has a lignin that is the most recalcitrant component and consists of three major components: cellulose, hemicellulose and lignin (Chuetor et al., 2021). Among the most abundant lignocellulosic biomass for biorefineries, cassava pulp has been one of the most studied crop wastes after rice and corn in various utilization options. The hydrolysis of cassava pulp has been reported based on various approaches, such as acid hydrolysis (Phowan and Danvirutai, 2014; Kurdi and Hansawasdi, 2015), enzymatic hydrolysis (Bunterngsook et al., 2017; Siriwong et al., 2019), and a combination of acid and enzymatic hydrolysis (Thongchul et al., 2010; Wattanagonniyom et al., 2017; Efeovbokhan et al., 2019; Areepak et al., 2022). Recently, microwave-assisted hydrolysis has gained some interest as it is an express and simple method for adopting biorefineries (Tsubaki et al., 2008; Hermiati et al., 2012; Klangpetch et al., 2022). In this study, household microwaves were chosen and tested for their potential use in microwave-assisted hydrolysis strategies due to their price and easy operation.
The highest fermentable sugar concentration of 88.05 g/L ± 7.65 g/L was obtained with 2.5% (v/v) H2SO4, whereas 3%, 2%, 1.5%, and 1% (v/v) H2SO4 resulted in fermentable sugar concentrations of 80.78 g/L ± 10.72 g/L, 55.96 g/L ± 4.66 g/L, 54.68 g/L ± 7.41 g/L, and 13.54 g/L ± 1.67 g/L, respectively. The effect of acid concentration in this study was similar to previous reports that used microwave-assisted pretreatment of sweet sorghum bagasse and the obtained hydrolysate was used for bioethanol production. The concentration of H2SO4 was varied from 1%, 3%, 5%, and 7% (v/v) under microwave irradiation at 300 W for 10 min. The total sugar concentration increased when the acid concentration increased (Ndaba, 2013). It has been reported that acid hydrolysis techniques was classified to two types based on acid concentration: concentrated acid hydrolysis at a low temperature or diluted acid hydrolysis at a high temperature (Chen, 2015; Saadon et al., 2022). Concentrated acid hydrolysis, 72% H2SO4, 42% HCl or 83% H3PO4 phosphoric acid, can completely solubilize crystalline cellulose at low temperatures of approximately 25°C–70°C, resulting in the homogeneous hydrolysis of cellulose. Diluted acid hydrolysis is normally operated with concentrations of 0.3%–2.5% at high temperatures of approximately 120°C–210°C (Rashid et al., 2021). In comparison, concentrated acid hydrolysis facilitate effective lignocellulosic hydrolysis better than dilute acid hydrolysis because two steps hydrolysis were simultaneously occurred: a decrystallization step that the crystal structure of lignin and fiber were swollen and digested by more than 60% (v/v) H2SO4 and a hydrolysis step with 20%–30% (v/v) H2SO4 to deliver sugars from the decrystallized fiber (Zhang and Bao, 2020). For instance, mixed wood chips hydrolysis using concentrated acid yielded 72%–82% glucose (Iranmahboob et al., 2002). The inhibitors as byproducts of microwave-assisted cassava pulp hydrolysis were very low due to the use of diluted acid in a short heating time. In addition, this method does not require an alkaline pretreatment as well as inhibitor removal steps. The overall cost can be reduced from the reduction of waste treatment costs and the water used for washing and neutralizing (Cheng et al., 2010; Sukruansuwan and Napathorn, 2018).
The advantage of using acid hydrolysis is concurrent lignin extraction with simultaneous saccharification. In this study, with the employment of microwave irradiation-assisted acid hydrolysis, lignin was not degraded to microbial inhibitors due to diluted acid concentration and a short heating time, but the condition was favorable for converting hemicellulose, which is more susceptible to acid hydrolysis, into soluble sugars and oligomers (Samuel et al., 2010), and then cellulose and lignin because they possess the highest level of resist to acids hydrolysis. Generally, diluted acid hydrolysis is performed at a concentration of 10%. With the use of the microwave synthesis reactor, the operating temperature occurred in acid hydrolysis reaction can be modulated between 100°C and 240°C. The pressure can be raised up to more than 1 MPa, which is higher than the saturated vapor pressure of the liquid. The advantages of dilute acid hydrolysis include the use of low acid concentration that offers low impact on the environment and simple waste management, and low material costs. Nevertheless, the progress of the dilute acid hydrolysis development was very slow. The key issue is that the temperature is an important factor influencing the rate of hydrolysis. On one hand, the hydrolysis rate will increase by 1 time as the temperature rises by 10°C. On the other hand, high temperature will stimulate the rate of monosaccharide decomposition. In this regard, as acid hydrolysis under high temperature is applied, the reaction time should be shortened. The increases in acid concentration, therefore, led to the increase of overall processing costs. Additionally, the equipment also needs to be the corrosion-resistance materials, resulting in the increase of equipment costs, which hampers industrial production opportunity. Normally, the concentration of dilute acid should not more than 10%. The temperature of the reactant after microwave-assisted dilute acid hydrolysis is summarized in Table 2.
Prior literature on acid hydrolysis mostly emphasized inorganic acids, including HCl and H2SO4. The main reason is that acid hydrolysis with HCl is superior to that with H2SO4; however, waste treatment with HCl is more difficult than with H2SO4. Additionally, the process using HCl is more expensive than that using H2SO4 because it requires equipment that has the higher level of corrosion resistance. Sugars present in the hydrolysates (sucrose, glucose, fructose, galactose, arabinose, xylose) were considered fermentable sugars (sucrose, glucose, fructose, galactose, arabinose) and PHB substrates (glucose and fructose) (Chanprateep et al., 2008; Sukruansuwan and Napathorn, 2018). The organic compounds that were considered microbial growth inhibitors [levulinic acid (LA), 5-(hydroxymethyl)furfural (5-HMF) and furfural (FAL)] in the hydrolysate samples were also analyzed. Under this condition, the obtained total fermentable sugars were 88.1 g/L ± 0.7 g/L (82.0 g/L ± 5.2 g/L glucose, 4.7 g/L ± 0.9 g/L galactose and 1.3 g/L ± 0.3 g/L arabinose) and 30.7 g/L ± 3.7 g/L xylose. In addition, microbial growth inhibitors in the microwave-assisted acid hydrolysis were 5.15 g/L ± 0.13 g/L levulinic acid (LA), 0.01 ± 0.01 5-(hydroxymethyl) furfural (5-HMF) and 0.004 g/L ± 0.01 g/L furfural (FAL), respectively. Fermentable sugars yielded from g-dry pulp was 0.88 g/g-dry cassava pulp, which was similar to the previous report using acid hydrolysis with HCl under steam conditions at 121°C and 15 psi for up to 2 h (Thongchul et al., 2010). Based on the above results, microwave-assisted cassava pulp hydrolysis showed high potential for the preparation of low-cost fermentable sugars suitable for microbial conversion. There have been some reports on similar research rationals using microwave-assisted hydrothermal conditions. However, the microwave used in these studies was different from this study. Hermiati et al. (2012) applied a microwave reactor instrument with variable and controlled frequencies of microwave energy so that it could offer temperature control in the temperature range of 180°C–240°C. The hydrolysis was performed without the use of acids but with the combination of adding activated carbon to remove inhibitors during microwave-assisted hydrolysis. Their study demonstrated that the presence of 1.0 g/g activated carbon in microwave-assisted hydrolysis resulted in the highest yield of glucose from cassava pulp (52.27%) when the temperature was set at 210°C for 15 min. Nevertheless, the method and conditions proposed in this study offer a shorter time, lower temperature and easier procedure than those in this report.
The application of crude hydrolysate was demonstrated by culturing Cupriavidus nector strain A-04 for biodegradable PHB production. The PHB content was 66.8% ± 0.3% with 4.8 g/L ± 0.2 g/L PHB and 7.5 g/L ± 0.1 g/L CDM. The coefficient yield
6 Conclusion
This study demonstrated the factors affecting fermentable sugar and inhibitor concentrations generated by microwave-assisted hydrolysis of cassava pulp as a food waste biorefinery for PHB production. The results are summarized in Table 3. According to this study, the optimal liquid-to-solid ratio was 20 mL/g. Hydrolysis using H3PO4 was not possible for microwave-assisted cassava pulp hydrolysis, which could require higher acid concentrations that will increase the overall cost. The conditions proposed in this study offer a short irradiation time of 8 min with 800 W for all concentrations of H2SO4. At 2.5% (v/v) H2SO4 with an irradiation power of 800 W for 8 min, a nearly 82% yield of glucose and 88% yield of fermentable sugars were obtained from untreated cassava pulp. However, xylose was also generated under this intense condition, where a concentration of H2SO4 lower than 2.5% (v/v) did not generate xylose. Because levulenic acid is generated by acid-catalyzed dehydration of glucose, therefore, under 3.0% (v/v) H2SO4 with an irradiation power of 800 W for 8 min, the glucose concentration was lower than that obtained from 2.5% (v/v) H2SO4. Additionally, inhibitor concentrations were higher than those obtained from acid concentrations below 2.5% (v/v). This study suggested that diluted acid concentrations were more effective than concentrated acid concentrations. This simple chemical process, which requires neither food/feed-based alternatives nor cellulase enzymes, could enable crude fermentable sugars to be the renewable carbon source of microorganisms for a scalable biorefinery. C. nector strain A-04 could utilize fermentable sugars from crude hydrolysate. A 66.8% ± 0.3% PHB content with 4.8 g/L ± 0.2 g/L PHB and 7.5 g/L ± 0.1 g/L CDM was obtained with a coefficient yield
Data availability statement
The raw data supporting the conclusion of this article will be made available by the authors, without undue reservation.
Author contributions
PP performed the experiments and discussed the results. KP provided guidance and suggestions for the experimental design of microwave assisted hydrolysis. BK provided guidance and suggestions for the experimental design. SN provided conceptualization, supervision, validation, writing original draft and review and editing manuscript. All authors read and approved the final version of the manuscript.
Funding
This research was supported in part by the 90th Anniversary of Chulalongkorn University (Ratchadapiseksomphot) Endowment Fund.
Conflict of interest
The authors declare that the research was conducted in the absence of any commercial or financial relationships that could be construed as a potential conflict of interest.
Publisher’s note
All claims expressed in this article are solely those of the authors and do not necessarily represent those of their affiliated organizations, or those of the publisher, the editors and the reviewers. Any product that may be evaluated in this article, or claim that may be made by its manufacturer, is not guaranteed or endorsed by the publisher.
Supplementary material
The Supplementary Material for this article can be found online at: https://www.frontiersin.org/articles/10.3389/fbioe.2023.1131053/full#supplementary-material
References
Adesina, B., and Bolaji, O. (2013). Effect of milling machines and sieve sizes on cooked cassava flour quality. Niger. Food J. 31, 115–119. doi:10.1016/s0189-7241(15)30065-5
Ahtong, D., and Charoenkongthum, K. (2002). Thermal properties and moisture absorption of LDPE/banana starch biocomposite films. J. Metals, Mater. Minerals 12 (1), 1–10. Retrieved from https://www.jmmm.material.chula.ac.th/index.php/jmmm/article/view/1272
Akaracharanya, A., Kesornsit, J., Leepipatpiboon, N., Srinorakutara, T., Kitpreechavanich, V., and Tolieng, V. (2011). Evaluation of the waste from cassava starch production as a substrate for ethanol fermentation by Saccharomyces cerevisiae. Ann. Microbiol. 61, 431–436. doi:10.1007/s13213-010-0155-8
Aoa, C. (1999). Official method of analysis of AOAC international. Oxford: Oxford University Press. Method 934.06. Moisture in dried fruits.
Areepak, C., Jiradechakorn, T., Chuetor, S., Phalakornkule, C., Sriariyanun, M., Raita, M., et al. (2022). Improvement of lignocellulosic pretreatment efficiency by combined chemo-Mechanical pretreatment for energy consumption reduction and biofuel production. Renew. Energy 182, 1094–1102. doi:10.1016/j.renene.2021.11.002
Barcelos, M. C., Lupki, F. B., Campolina, G. A., Nelson, D. L., and Molina, G. (2018). The colors of biotechnology: General overview and developments of white, green and blue areas. FEMS Microbiol. Lett. 1, 365. doi:10.1093/femsle/fny239
Binder, J. B., and Raines, R. T. (2010). Fermentable sugars by chemical hydrolysis of biomass. Proc. Natl. Acad. Sci. 107, 4516–4521. doi:10.1073/pnas.0912073107
Braunegg, G., Sonnleitner, B., and Lafferty, R. (1978). A rapid gas chromatographic method for the determination of poly-β-hydroxybutyric acid in microbial biomass. Appl. Microbiol. Biotechnol. 6, 29–37. doi:10.1007/bf00500854
Bunterngsook, B., Laothanachareon, T., Natrchalayuth, S., Lertphanich, S., Fujii, T., Inoue, H., et al. (2017). Optimization of a minimal synergistic enzyme system for hydrolysis of raw cassava pulp. RSC Adv. 7, 48444–48453. doi:10.1039/c7ra08472b
Carvalho, W., Batista, M. A., Canilha, L., Santos, J. C., Converti, A., and Silva, S. S. (2004). Sugarcane bagasse hydrolysis with phosphoric and sulfuric acids and hydrolysate detoxification for xylitol production. J. Chem. Technol. Biotechnol. Int. Res. Process, Environ. Clean Technol. 79, 1308–1312. doi:10.1002/jctb.1131
Chanprateep, S., Abe, N., Shimizu, H., Yamane, T., and Shioya, S. (2001). Multivariable control of alcohol concentrations in the production of polyhydroxyalkanoates (PHAs) by Paracoccus denitrificans. Biotechnol. Bioeng. 74, 116–124. doi:10.1002/bit.1101
Chanprateep, S., Katakura, Y., Visetkoop, S., Shimizu, H., Kulpreecha, S., and Shioya, S. (2008). Characterization of new isolated Ralstonia eutropha strain A-04 and kinetic study of biodegradable copolyester poly(3-hydroxybutyrate-co-4-hydroxybutyrate) production. J. Industrial Microbiol. Biotechnol. 35, 1205–1215. doi:10.1007/s10295-008-0427-5
Chanprateep, S., and Kulpreecha, S. (2006). Production and characterization of biodegradable terpolymer poly (3-hydroxybutyrate-co-3-hydroxyvalerate-co-4-hydroxybutyrate) by Alcaligenes sp. A-04. J. Biosci. Bioeng. 101, 51–56. doi:10.1263/jbb.101.51
Chen, H. (2015). Lignocellulose biorefinery engineering: Principles and applications. United Kingdom: Woodhead Publishing.
Cheng, Y. S., Zheng, Y., Yu, C. W., Dooley, T. M., Jenkins, B. M., and Vandergheynst, J. S. (2010). Evaluation of high solids alkaline pretreatment of rice straw. Appl. Biochem. Biotechnol. 162, 1768–1784. doi:10.1007/s12010-010-8958-4
Chuetor, S., Ruiz, T., Barakat, A., Laosiripojana, N., Champreda, V., and Sriariyanun, M. (2021). Evaluation of rice straw biopowder from alkaline-mechanical pretreatment by hydro-textural approach. Bioresour. Technol. 323, 124619. doi:10.1016/j.biortech.2020.124619
Dagaew, G., Wongtangtintharn, S., Suntara, C., Prachumchai, R., Wanapat, M., and Cherdthong, A. (2022). Feed utilization efficiency and ruminal metabolites in beef cattle fed with cassava pulp fermented yeast waste replacement soybean meal. Sci. Rep. 12, 16090. doi:10.1038/s41598-022-20471-6
De Souza, L., Manasa, Y., and Shivakumar, S. (2020). Bioconversion of lignocellulosic substrates for the production of polyhydroxyalkanoates. Biocatal. Agric. Biotechnol. 28, 101754. doi:10.1016/j.bcab.2020.101754
Diarra, S. S., and Devi, A. (2015). Feeding value of some cassava by-products meal for poultry: A review. Pak. J. Nutr. 14, 735–741. doi:10.3923/pjn.2015.735.741
Efeovbokhan, V. E., Egwari, L., Alagbe, E. E., Adeyemi, J. T., and Taiwo, O. S. (2019). Production of bioethanol from hybrid cassava pulp and peel using microbial and acid hydrolysis. BioResources 14, 2596–2609. https://jtatm.textiles.ncsu.edu/index.php/BioRes/article/view/BioRes_14_2_2596_Efeovbokhan_Bioethanol_Hybrid_Cassava_Pulp
Fao (2019). The State of Food and Agriculture 2019. Moving forward on food loss and waste reduction. Rome: Fao Publishing.
Gali, K. K., Tadi, S. R. R., Arun, E., Mohan, N., Swaminathan, N., Katiyar, V., et al. (2021). Cost-effective valorization of cassava fibrous waste into enantiomerically pure D-lactic acid: Process engineering and kinetic modelling approach. Environ. Technol. Innovation 22, 101519. doi:10.1016/j.eti.2021.101519
Hasanudin, U., Kustyawati, M. E., Iryani, D. A., Haryanto, A., and Triyono, S. (2019). Estimation of energy and organic fertilizer generation from small scale tapioca industrial waste. IOP Conf. Ser. Earth Environ. Sci. IOP Publ. 230, 012084. doi:10.1088/1755-1315/230/1/012084
Hermiati, E., Azuma, J.-I., Tsubaki, S., Mangunwidjaja, D., Sunarti, T. C., Suparno, O., et al. (2012). Improvement of microwave-assisted hydrolysis of cassava pulp and tapioca flour by addition of activated carbon. Carbohydr. Polym. 87, 939–942. doi:10.1016/j.carbpol.2011.08.033
Hierro-Iglesias, C., Chimphango, A., Thornley, P., and Fernández-Castané, A. (2022). Opportunities for the development of cassava waste biorefineries for the production of polyhydroxyalkanoates in Sub-Saharan Africa. Biomass Bioenergy 166, 106600. doi:10.1016/j.biombioe.2022.106600
Iranmahboob, J., Nadim, F., and Monemi, S. (2002). Optimizing acid-hydrolysis: A critical step for production of ethanol from mixed wood chips. Biomass bioenergy 22, 401–404. doi:10.1016/s0961-9534(02)00016-8
Jiang, S., Daly, H., Xiang, H., Yan, Y., Zhang, H., Hardacre, C., et al. (2019). Microwave-assisted catalyst-free hydrolysis of fibrous cellulose for deriving sugars and biochemicals. Front. Chem. Sci. Eng. 13, 718–726. doi:10.1007/s11705-019-1804-5
Kanchanasuta, S., Sillaparassamee, O., Champreda, V., Singhakant, C., and Pisutpaisal, N. (2020). Optimization of pretreatment process of cassava rhizome for bio-succinic fermentation by Actinobacillus succinogenes. Biomass Convers. Biorefinery 12, 4917–4924. doi:10.1007/s13399-020-00954-0
Kemper, A. (1974). Determination of sub-microquantities of ammonium and nitrates in soils with phenol, sodiumnitroprusside and hypochlorite. Geoderma 12, 201–206. doi:10.1016/0016-7061(74)90068-8
Khanpanuek, S., Lunprom, S., Reungsang, A., and Salakkam, A. (2022). Repeated-batch simultaneous saccharification and fermentation of cassava pulp for ethanol production using amylases and Saccharomyces cerevisiae immobilized on bacterial cellulose. Biochem. Eng. J. 177, 108258. doi:10.1016/j.bej.2021.108258
Klangpetch, W., Pattarapisitporn, A., Phongthai, S., Utama-Ang, N., Laokuldilok, T., Tangjaidee, P., et al. (2022). Microwave-assisted enzymatic hydrolysis to produce xylooligosaccharides from rice husk alkali-soluble arabinoxylan. Sci. Rep. 12, 11–12. doi:10.1038/s41598-021-03360-2
Kurdi, P., and Hansawasdi, C. (2015). Assessment of the prebiotic potential of oligosaccharide mixtures from rice bran and cassava pulp. LWT-Food Sci. Technol. 63, 1288–1293. doi:10.1016/j.lwt.2015.04.031
Lerdlattaporn, R., Phalakornkule, C., Trakulvichean, S., and Songkasiri, W. (2021). Implementing circular economy concept by converting cassava pulp and wastewater to biogas for sustainable production in starch industry. Sustain. Environ. Res. 31, 20. doi:10.1186/s42834-021-00093-9
Ma, H., Liu, W.-W., Chen, X., Wu, Y.-J., and Yu, Z.-L. (2009). Enhanced enzymatic saccharification of rice straw by microwave pretreatment. Bioresour. Technol. 100, 1279–1284. doi:10.1016/j.biortech.2008.08.045
Mathioudakis, V., Gerbens-Leenes, P., Van Der Meer, T. H., and Hoekstra, A. Y. (2017). The water footprint of second-generation bioenergy: A comparison of biomass feedstocks and conversion techniques. J. Clean. Prod. 148, 571–582. doi:10.1016/j.jclepro.2017.02.032
Ndaba, B. (2013). Microwave assisted pretreatment of sweet sorghum bagasse for bioethanol production. South Africa: North-West University.
Nguyen, T. C., Ruksakulpiwat, C., and Ruksakulpiwat, Y. (2020). Effect of cellulose nanofibers from cassava pulp on physical properties of poly (lactic acid) biocomposites. J. Thermoplast. Compos. Mater. 33, 1094–1108. doi:10.1177/0892705718820395
Nithikarnjanatharn, J., and Samsalee, N. (2022). Effect of cassava pulp on Physical, Mechanical, and biodegradable properties of Poly (Butylene-Succinate)-Based biocomposites. Alexandria Eng. J. 61, 10171–10181. doi:10.1016/j.aej.2022.03.052
Office of Agricultural Economics (2021). Cassava factories: Plantation area, harvested area, total yield and yield per Rai in Thailand in 2021. Available https://www.oae.go.th/assets/portals/1/files/%E0%B8%A1%E0%B8%B1%E0%B8%99%E0%B8%AA%E0%B8%B3%E0%B8%9B%E0%B8%B0%E0%B8%AB%E0%B8%A5%E0%B8%B1%E0%B8%87%E0%B8%9B%E0%B8%B5%2064.pdf (Accessed November 7, 2022).
Özbek, H. N., Koçak Yanık, D., Fadıloğlu, S., and Göğüş, F. (2021). Effect of microwave-assisted alkali pre-treatment on fractionation of pistachio shell and enzymatic hydrolysis of cellulose-rich residues. J. Chem. Technol. Biotechnol. 96 (2), 521–531. doi:10.1002/jctb.6569
Pandey, A., Soccol, C. R., Nigam, P., and Soccol, V. T. (2000). Biotechnological potential of agro-industrial residues. I: Sugarcane bagasse. Bioresour. Technol. 74, 69–80. doi:10.1016/s0960-8524(99)00142-x
Pandey, A., Soccol, C. R., Nigam, P., Soccol, V. T., Vandenberghe, L. P., and Mohan, R. (2000). Biotechnological potential of agro-industrial residues. II: Cassava bagasse. Bioresour. Technol. 74, 81–87. doi:10.1016/s0960-8524(99)00143-1
Phowan, P., and Danvirutai, P. (2014). Hydrogen production from cassava pulp hydrolysate by mixed seed cultures: Effects of initial pH, substrate and biomass concentrations. Biomass Bioenergy 64, 1–10. doi:10.1016/j.biombioe.2014.03.057
Phun-Iam, M., Anusontpornperm, S., Thanachit, S., and Kheoruenromne, I. (2018). Yield response of cassava Huay Bong 80 variety grown in an Oxyaquic Paleustult to cassava starch waste and nitrogen fertilizer. Agric. Nat. Resour. 52, 573–580. doi:10.1016/j.anres.2018.11.026
Pongsub, S., Suntara, C., Khota, W., Boontiam, W., and Cherdthong, A. (2022). The chemical composition, fermentation end-product of silage, and aerobic stability of cassava pulp fermented with lactobacillus casei TH14 and additives. Veterinary Sci. 9, 617. doi:10.3390/vetsci9110617
Poomipuk, N., Reungsang, A., and Plangklang, P. (2014). Poly-β-hydroxyalkanoates production from cassava starch hydrolysate by Cupriavidus sp. KKU38. Int. J. Biol. Macromol. 65, 51–64. doi:10.1016/j.ijbiomac.2014.01.002
Rashid, T., Sher, F., Rasheed, T., Zafar, F., Zhang, S., and Murugesan, T. (2021). Evaluation of current and future solvents for selective lignin dissolution–A review. J. Mol. Liq. 321, 114577. doi:10.1016/j.molliq.2020.114577
Rattanachomsri, U., Tanapongpipat, S., Eurwilaichitr, L., and Champreda, V. (2009). Simultaneous non-thermal saccharification of cassava pulp by multi-enzyme activity and ethanol fermentation by Candida tropicalis. J. Biosci. Bioeng. 107, 488–493. doi:10.1016/j.jbiosc.2008.12.024
Saadon, S. Z. a. H., Osman, N. B., and Yusup, S. (2022). in Value-chain of biofuels (Netherlands: Elsevier).Pretreatment of fiber-based biomass material for lignin extraction
Samuel, R., Pu, Y., Foston, M., and Ragauskas, A. J. (2010). Solid-state NMR characterization of switchgrass cellulose after dilute acid pretreatment. Biofuels 1, 85–90. doi:10.4155/bfs.09.17
Sasaki, C., Sumitomo, Y., Odashima, K., Asada, C., and Nakamura, Y. (2021). Microwave-assisted hydrolysis of cellulose in towel and wheat straw using freeze-thawing with NaOH. Waste Biomass Valorization 12, 3331–3339. doi:10.1007/s12649-020-01219-7
Sawisit, A., Jantama, S. S., Kanchanatawee, S., and Jantama, K. (2015). Efficient utilization of cassava pulp for succinate production by metabolically engineered Escherichia coli KJ122. Bioprocess Biosyst. Eng. 38, 175–187. doi:10.1007/s00449-014-1257-7
Shangdiar, S., Lin, Y.-C., Ponnusamy, V. K., and Wu, T.-Y. (2022). Pretreatment of lignocellulosic biomass from sugar bagasse under microwave assisted dilute acid hydrolysis for biobutanol production. Bioresour. Technol. 361, 127724. doi:10.1016/j.biortech.2022.127724
Sinsukudomchai, P., Duangdao Honda, K., and Napathorn, S. C. (2023). “Green composites made of polyhydroxybutyrate and long-chain fatty acid esterified microcrystalline cellulose from pineapple leaf,”. PLOS ONE.
Siriwong, T., Laimeheriwa, B., Aini, U. N., Cahyanto, M. N., Reungsang, A., and Salakkam, A. (2019). Cold hydrolysis of cassava pulp and its use in simultaneous saccharification and fermentation (SSF) process for ethanol fermentation. J. Biotechnol. 292, 57–63. doi:10.1016/j.jbiotec.2019.01.003
Sriroth, K., Chollakup, R., Chotineeranat, S., Piyachomkwan, K., and Oates, C. G. (2000). Processing of cassava waste for improved biomass utilization. Bioresour. Technol. 71, 63–69. doi:10.1016/s0960-8524(99)00051-6
Sriroth, K., Piyachomkwan, K., Wanlapatit, S., and Oates, C. G. (2000). Cassava starch technology: The Thai experience. Starch-Stärke 52 (12), 439–449. doi:10.1002/1521-379x(200012)52:12<439::aid-star439>3.0.co;2-e
Sudha, A., Sivakumar, V., Sangeetha, V., and Devi, K. (2015). Enhancing fermentable sugar yield from cassava pulp for bioethanol production: Microwave-coupled enzymatic hydrolysis approach. Bioprocess Biosyst. Eng. 38, 1509–1515. doi:10.1007/s00449-015-1393-8
Sukruansuwan, V., and Napathorn, S. C. (2018). Use of agro-industrial residue from the canned pineapple industry for polyhydroxybutyrate production by Cupriavidus necator strain A-04. Biotechnol. biofuels 11, 202–215. doi:10.1186/s13068-018-1207-8
Sweygers, N., Dewil, R., and Appels, L. (2018). Production of levulinic acid and furfural by microwave-assisted hydrolysis from model compounds: Effect of temperature, acid concentration and reaction time. Waste biomass valorization 9, 343–355. doi:10.1007/s12649-016-9797-5
Thongchul, N., Navankasattusas, S., and Yang, S.-T. (2010). Production of lactic acid and ethanol by Rhizopus oryzae integrated with cassava pulp hydrolysis. Bioprocess Biosyst. Eng. 33, 407–416. doi:10.1007/s00449-009-0341-x
Tran, T., Da, G., Moreno-Santander, M. A., Vélez-Hernández, G. A., Giraldo-Toro, A., Piyachomkwan, K., et al. (2015). A comparison of energy use, water use and carbon footprint of cassava starch production in Thailand, Vietnam and Colombia. Resour. Conservation Recycl. 100, 31–40. doi:10.1016/j.resconrec.2015.04.007
Tsubaki, S., Iida, H., Sakamoto, M., and Azuma, J.-I. (2008). Microwave heating of tea residue yields polysaccharides, polyphenols, and plant biopolyester. J. Agric. food Chem. 56, 11293–11299. doi:10.1021/jf802253s
Ubando, A. T., Felix, C. B., and Chen, W.-H. (2020). Biorefineries in circular bioeconomy: A comprehensive review. Bioresour. Technol. 299, 122585. doi:10.1016/j.biortech.2019.122585
United Nations Environment Program (2021). UNEP food waste Index report. London: United Nations Environment Program.
Virunanon, C., Ouephanit, C., Burapatana, V., and Chulalaksananukul, W. (2013). Cassava pulp enzymatic hydrolysis process as a preliminary step in bio-alcohols production from waste starchy resources. J. Clean. Prod. 39, 273–279. doi:10.1016/j.jclepro.2012.07.055
Wattanagonniyom, T., Lee, W.-C., Tolieng, V., Tanasupawat, S., and Akaracharanya, A. (2017). Co-fermentation of cassava waste pulp hydrolysate with molasses to ethanol for economic optimization. Ann. Microbiol. 67, 157–163. doi:10.1007/s13213-016-1245-z
Wongmoon, C., and Napathorn, S. C. (2022). Front Bioeng Biotechnol 10, 1086636. doi:10.3389/fbioe.2022.1086636
Yabueng, N., and Napathorn, S. C. (2018). Toward non-toxic and simple recovery process of poly (3-hydroxybutyrate) using the green solvent 1, 3-dioxolane. Process Biochem. 69, 197–207. doi:10.1016/j.procbio.2018.02.025
Yoshida, T., Tsubaki, S., Teramoto, Y., and Azuma, J.-I. (2010). Optimization of microwave-assisted extraction of carbohydrates from industrial waste of corn starch production using response surface methodology. Bioresour. Technol. 101, 7820–7826. doi:10.1016/j.biortech.2010.05.011
Zhang, J., and Bao, J. (2020). Editor V. Bisaria. (Netherlands: Springer), 1–14.Lignocellulose pretreatment using acid as catalyst," in Handbook of biorefinery Research and technology
Zhang, M., Xie, L., Yin, Z., Khanal, S. K., and Zhou, Q. (2016). Biorefinery approach for cassava-based industrial wastes: Current status and opportunities. Bioresour. Technol. 215, 50–62. doi:10.1016/j.biortech.2016.04.026
Zhang, Z., and Zhao, Z. K. (2010). Microwave-assisted conversion of lignocellulosic biomass into furans in ionic liquid. Bioresour. Technol. 101, 1111–1114. doi:10.1016/j.biortech.2009.09.010
Keywords: polyhydroxybutyrate, biorefinery, cassava starch industry, microwave, low-cost PHB production, valorization of agri-food wastes
Citation: Prasertsilp P, Pattaragulwanit K, Kim BS and Napathorn SC (2023) Microwave-assisted cassava pulp hydrolysis as food waste biorefinery for biodegradable polyhydroxybutyrate production. Front. Bioeng. Biotechnol. 11:1131053. doi: 10.3389/fbioe.2023.1131053
Received: 24 December 2022; Accepted: 22 February 2023;
Published: 06 March 2023.
Edited by:
Wan Abd Al Qadr Imad Wan-Mohtar, University of Malaya, MalaysiaReviewed by:
Kit Wayne Chew, Nanyang Technological University, SingaporeSuan Shi, China Agricultural University, China
Copyright © 2023 Prasertsilp, Pattaragulwanit, Kim and Napathorn. This is an open-access article distributed under the terms of the Creative Commons Attribution License (CC BY). The use, distribution or reproduction in other forums is permitted, provided the original author(s) and the copyright owner(s) are credited and that the original publication in this journal is cited, in accordance with accepted academic practice. No use, distribution or reproduction is permitted which does not comply with these terms.
*Correspondence: Suchada Chanprateep Napathorn, c3VjaGFkYS5jaGFAY2h1bGEuYWMudGg=