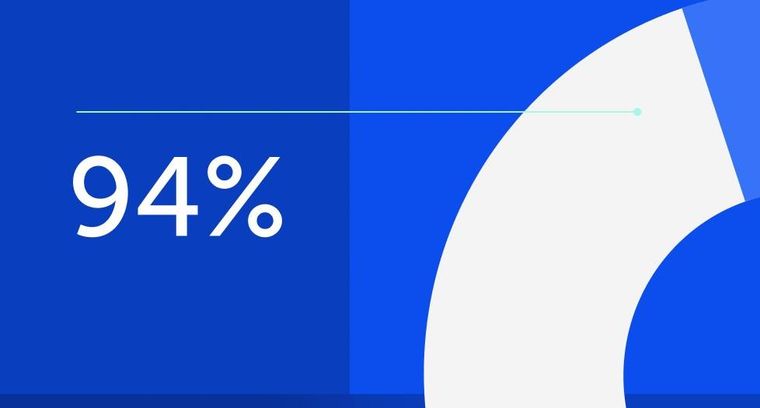
94% of researchers rate our articles as excellent or good
Learn more about the work of our research integrity team to safeguard the quality of each article we publish.
Find out more
ORIGINAL RESEARCH article
Front. Bioeng. Biotechnol., 16 December 2022
Sec. Bioprocess Engineering
Volume 10 - 2022 | https://doi.org/10.3389/fbioe.2022.1082341
This article is part of the Research TopicGenetic Engineering, Pretreatment, Thermochemical, and Biochemconversion for Lignocellulose ValorizationView all 11 articles
Lignin, an abundant aromatic biopolymer, has the potential to produce various biofuels and chemicals through biorefinery activities and is expected to benefit the future circular economy. Microwave-assisted efficient degradation of lignin in methanol/formic acid over Ru/C catalyst cooperated with metal chloride was investigated, concerning the effect of type and dosage of metal chloride, dosage of Ru/C, reaction temperature, and reaction time on depolymerized product yield and distribution. Results showed that 91.1 wt% yield of bio-oil including 13.4 wt% monomers was obtained under the optimum condition. Yields of guaiacol-type compounds and 2,3-dihydrobenzofuran were promoted in the presence of ZnCl2. Formic acid played two roles: (1) acid-catalyzed cleavage of linkages; (2) acted as an in situ hydrogen donor for hydrodeoxygenation in the presence of Ru/C. A possible mechanism for lignin degradation was proposed. This work will provide a beneficial approach for efficient depolymerization of lignin and controllable product distribution.
The global population growth and the development of industrialization lead to a rising demand for fuels and chemicals, resulting in many societal problems, such as energy security and environmental concerns (Sun et al., 2018; Wang et al., 2019; Jing et al., 2020; Ma et al., 2021). Developing renewable and environment-friendly energy has become an essential measure for many countries to promote energy transformation. Lignin, which constitutes up to 40% of the energy content of most terrestrial plants, shows great potential to produce liquid fuel or petroleum-based aromatic chemicals owing to its aromatic building blocks (Regalbuto, 2009; Barta et al., 2010; Cao et al., 2019; Ekielski and Mishra, 2020; Tang et al., 2022; Zhou et al., 2022).
Despite various challenges associated with lignin valorization, several strategies have emerged that could deliver value-added products, such as biological (Chong et al., 2018) and chemical process (Li et al., 2015). In particular, a wide range of thermochemical approaches for converting lignin into aromatic-rich bio-oil, including pyrolysis (Shao et al., 2017; Cao et al., 2021), acid/base catalytic hydrolysis (Deuss et al., 2015; Hernández-Ramos et al., 2020), oxidation (Lancefield et al., 2015; Sun et al., 2020) and reductive depolymerization (Liu et al., 2019), have been extensively investigated. Bio-oil is a higher energy content transportable liquid for subsequent production of biofuels and aromatic chemicals. Previous researches have indicated that solvents and catalysts have significant effects on lignin depolymerization. Various solvents (such as water, alcohol, formic acid, etc.) were investigated during the lignin valorization process. Shu et al. (2016b) investigated the influence of solvent on lignin depolymerization, and concluded that supercritical methanol showed the bested depolymerization performance. Hidajat et al. (2018) used formic acid as hydrogen source to produce oxygen-free aromatics, achieving high-calorific-value oil (> 40 MJ kg−1) with a high content of oxygen-free aromatics (6.8 wt%). Various kinds of catalysts, including homogeneous and heterogeneous catalysts, have been extensively tested (Wang et al., 2019). Kristianto et al. (2017) reported the depolymerization of concentrated acid hydrolysis lignin using a Ru/C catalyst in ethanol/formic acid media, achieving a high bio-oil yield of ∼70 wt% and a high heating value of 32.7 MJ kg−1. Luo et al. (2020) used boric acid as a novel homogeneous catalyst coupled with Ru/C to overcome the product separation problem and perform the hydrodeoxygenation (HDO) of phenolic compounds and raw lignin oil. The content of hydrocarbons increases from 7.9% to 93.1% at 260°C. Most of these thermochemical approaches required relatively harsh reaction conditions (high reaction temperature and/or high pressure). Therefore, it is urgent to explore mild reaction conditions and technologies for converting lignin into high-value liquid fuel and/or aromatic chemicals.
Recently, in comparison with those conventional heating processes, microwave-assisted depolymerization of lignin has attracted increasing attention on account of its advantages of fast heating rate and high heating efficiency (Liu et al., 2017; Zhou et al., 2019; Cederholm et al., 2020). Microwave heating occurs via dipole rotation and ionic conduction. Therefore, polar solvents which have high microwave absorption abilities are adopted as additional microwave receptors. Moreover, the addition of molecular hydrogen will increase the cost and risk of the process (Jiang et al., 2019). Consequently, the use of polar hydrogen-donating reagents (methanol, ethanol, formic acid, et al.) would be potentially safer and more cost-effective (Zhou et al., 2018). Toledano et al. investigated the influence of various hydrogen-donating solvents on lignin depolymerization under microwave conditions, finding that formic acid showed the best performance (Toledano et al., 2013). Apart from solvents, catalysts also played an essential role in the microwave-assisted depolymerization of lignin. Noble metal-based catalysts (such as Pd, Pt, and Ru, etc.) were proved to be effective for lignin depolymerization (Zhang et al., 2019; Wang et al., 2021). Previous studies indicated that the combination of the noble metal with acid catalyst had better performances for lignin depolymerization (Klein et al., 2016; Bjelić et al., 2020; Jiang et al., 2021). Shu et al. investigated the catalytic performances of various metal chlorides cooperated with Pd/C for lignin depolymerization and observed that the highest yield (28.5 wt%) of phenolic monomers was obtained with CrCl3 under harsh conditions (4 MPa H2, 260°C, 5 h) (Shu et al., 2015).
In our previous work, microwave-assisted degradation of alkaline lignin in methanol/formic acid (FA) media was investigated, and 72.0 wt% yield of bio-oil including 6.7 wt% monomers was achieved at 160°C and a FA-to-lignin mass ratio of 4 after a reaction time of 30 min (Shao et al., 2018). Herein, highly efficient depolymerization of lignin in methanol/formic acid over Ru/C catalyst cooperated with metal chlorides assisted by microwave heating is reported. The effects of catalyst, reaction temperature, and reaction time on the product yield and distribution are studied in detail. The possible mechanism of lignin depolymerization is proposed.
The alkaline lignin was provided by Shandong Longlive Bio-Technology Co., Ltd., China, a by-product of xylooligosaccharides production from corn cob. The lignin was composed of 90.81% Klason lignin, 3.61% acid-soluble lignin, 0.63% sugars, 2.16% ash, and 2.79% others (Shao et al., 2018). 5 wt% Ru/C, formic acid (FA, 99%), ethyl acetate (HPLC grade, 99.9%), and acetophenone (standard for GC, 99.5%) were provided by Aladdin® company. Methanol (99.5%), ethyl acetate (99.5%), and tetrahydrofuran (THF, 99.0%) were analytical grade and provided by Beijing Chemical Works. AlCl3, CrCl3, LiCl, NaCl, FeCl3, FeCl2, MgCl2, ZnCl2, KCl, and Zn(OAC)2 were also analytical grade and purchased from Macklin® company. All reagents were used as received.
Microwave-assisted depolymerization of lignin was carried out in microwave digestion instrument (MDS-6G, Sineo Microwave Technology Co., Ltd., China). Methanol and formic acid (FA) were chosen as solvent and hydrogen donor during the depolymerization process. Ru/C and metal chloride were used as catalysts. For a typical experiment, 1 g lignin, 1 mmol metal chloride, 0.2 g 5 wt% Ru/C, 20 ml methanol, and 4 g formic acid (FA) were added into the digestion tank. The reaction was conducted at 400 W under settled reaction temperature (140, 160, and 180°C) and reaction time (15, 30, and 45 min). After the reaction, the mixture was cooled down to ambient temperature.
The products separation was as follows. The reaction mixture was first filtered, and the filter cake was washed three times with methanol. The solid fraction 1 (including catalyst and residue) was obtained. The filtrate was collected and subjected to rotary evaporation, followed by adding ethyl acetate. The resulting mixture was filtered again. The solid fraction 2 was obtained. The filtrate was rotary evaporated, achieving the bio-oil. The solid fractions were washed with THF and filtered, achieving the residue and catalyst. The yields of bio-oil, aromatic monomers, and residue were calculated according to the following equations:
Where WAM, WBO, WR, and WL depict the weight of aromatic monomer, bio-oil, residue, and starting lignin, respectively.
Qualitative and quantitative analysis of aromatic monomers in bio-oil were carried out by SHIMADZU GC–MS-QP 2010 SE and SHIMADZU GC-2010 Plus with a FID detector equipped with HP-5 capillary columns (30 m × 0.25 mm × 0.25 μm), respectively. The oven temperature was programmed from 50°C to 300°C with a 10°C /min heating rate. The injector was kept at 250°C with a split ratio of 20, using helium as carrier gas. Acetophenone was used as the internal standard.
Various products can be obtained after lignin depolymerization. Table 1 shows the effect of different metal chloride on bio-oil, aromatic monomer, and residue yields. The specific aromatic monomer distribution and yield are shown in Supplementary Table S1. Generally, the distribution of depolymerized lignin products was complex. According to the specific functional groups, products were classified into four categories: 2,3-dihydrobenzofuran (DHBF), phenol-type compounds (H), guaiacol-type compounds (G), and syringol-type compounds (S). It should be noted that no chloride-contained compounds were detected in products, indicating that dissolved chloride did not react with the lignin.
As shown in Table 1, the bio-oil yield increased slightly after adding Ru/C catalyst, but the promotion effect on the aromatic monomer yield was not significant. The yield of bio-oil increased or decreased when metal chloride was added. It is generally known that Cl is a high electronegativity element, and Cl−1 was widely used in biomass dissolution and conversion as an excellent nucleophilic regent (Long et al., 2011; Shu et al., 2015). C-O bond in cellulose was easier to be broken in most cellulose conversion reactions using chloride ionic liquids as solvent (Swatloski et al., 2002). Lignin contained a large number of ether bonds, especially the β-O-4′ bonds. Therefore, it is considered that Cl−1 in metal chloride can work in lignin depolymerization. Data in Table 1 showed that ZnCl2, CrCl3, and FeCl3 significantly promoted lignin depolymerization. The common feature was the higher valence of metal cation. The result showed that metal cations also affected lignin depolymerization, which may be related to the Lewis acid strength of metal cation. It has been reported that metal cations can produce more acid centers (Miessler et al., 2013), promoting lignin depolymerization. One more interesting phenomenon, metal cations of AlCl3 and MgCl2 also had high valence, but the bio-oil yield was lower than that of other high-valent metal cations. This might be caused by hydrated metal chloride used in the experiment, such as AlCl3•6H2O and MgCl2•6H2O. Water present in the reagents might affect lignin depolymerization, which was also confirmed by the high residue yield.
Yields of bio-oil and aromatic monomers were the highest in the presence of ZnCl2. The result differed from Shu et al. (2018)’s research, who believed that CrCl3 provided a better catalytic effect. The higher valence of Cr3+ in CrCl3 could produce more acidic centers, which promoted lignin depolymerization. Cr3+ was first conjunct with O and benzene ring of lignin molecule to form a stable complex. Synchronously, Cl− with high electronegativity was connected to lignin molecule, resulting in the breakage of C-O bonds (Tang et al., 2021). Furthermore, hydrogenolysis was promoted by capturing hydrogen under the polarization effect of Cl− and the synergic effect of Pd/C (Parsell et al., 2013). The product distribution was significantly different by comparing the aromatic monomers generated from ZnCl2 and CrCl3 synergistic Ru/C catalytic depolymerization of lignin. For example, when ZnCl2 was used, the yield of 4-ethylphenol (H2, 0.89 wt%) was the highest among the H-type compounds, without the generation of p-coumaric acid (H4). When CrCl3 was used, it showed the opposite result that the yield of H4 (1.55 wt%) was the highest among the H-type compounds without H2. The result indicated that the catalytic mechanism of ZnCl2 and CrCl3 was different. Compared with other metal chloride, using ZnCl2 could facilitate the formation of H4 and increase the yield of G-type compounds. Besides, the highest yield (5.58 wt%) of 2,3-dihydrobenzofuran (DHBF) was obtained. Significant decreases of bio-oil and total aromatic monomers were exhibited when ZnCl2 was replaced by Zn(OAc)2. Meanwhile, a dramatic change of product distribution occurred, especially the S-type compounds. It indicated that the synergic effect between Zn2+ and Cl− was contributed to improve the yields of bio-oil and aromatic monomer. Data showed that lignin could be efficiently depolymerized under the catalyst of ZnCl2 cooperated with Ru/C.
The effect of ZnCl2 dosage on lignin depolymerization was investigated. As shown in Table 2, the category and yield of S-type compounds decreased with the increase of ZnCl2 dosage. Only S3 was produced when the dosage of ZnCl2 was 1 and 2 mmol. As the dosage of ZnCl2 was further increased to 3 mmol, no S-type compounds were produced. In view of the lower yield of S-type compounds in depolymerized products, yields of bio-oil, total monomers, DHBF, H-type, and G-type compounds were mainly discussed as follows.
As shown in Figure 1, the yield of bio-oil increased with increasing ZnCl2 dosage. And the highest bio-oil yield of 93.4 wt% was obtained when 3 mmol ZnCl2 was used. The yield of total monomers rose from 5.38 wt% to 13.4 wt% with increasing ZnCl2 dosage from 0 to 2 mmol. However, as ZnCl2 dosage was further increased to 3 mmol, yield of total monomers decreased to 11.6 wt%. This phenomenon suggested that lignin depolymerization was favored at high ZnCl2 dosage; meanwhile, repolymerization of monomers to form oligomers was also promoted. Among the monomers, DHBF was abundantly produced; the yield first increased to 5.6 wt% and then decreased to 2.03 wt% as a function of ZnCl2 dosage. The yield of H-type compounds increased as the amount of ZnCl2 increased, and the highest yield (5.63 wt%) was obtained when 3 mmol ZnCl2 was used. It should be noted that H2 was produced only in the presence of ZnCl2, and phenol was produced only when the ZnCl2 dosage was more than 2 mmol. The yields of H2 and phenol were proportional to ZnCl2 dosage. This phenomenon indicated that increasing the dosage of ZnCl2 was conductive to the formation of H1 and H2. The highest yield (1.91 wt%) of p-coumaric acid appeared when the ZnCl2 dosage was 0.5 mmol. Further increasing ZnCl2 dosage, no p-coumaric acid was detected in products. This indicated that high ZnCl2 dosage inhibited the production of p-coumaric acid. For G-type compounds, the yield first increased to 6.4 wt% and then decreased to 3.92 wt% as a function of ZnCl2 dosage. The decrease in the yield of G-type compounds was mainly caused by a decline of G3, G4, G5, and G6. The yields of G1 and G2 showed similar variation tendency with H1 and H2, respectively, when increasing ZnCl2 dosage. The result indicated great significance for controlling the selectivity of depolymerized products by varying ZnCl2 dosage.
FIGURE 1. Effect of ZnCl2 dosage on the yield of depolymerized products. Condition: 1 g lignin, 0.2 g 5 wt% Ru/C, 20 ml methanol, 4 g formic acid, 160°C, 30 min.
The effect of Ru/C dosage had also been carefully examined. Table 3 shows the distribution of aromatic monomers. When the amount of ZnCl2 was 2 mmol, there were basically no S-type phenolic compounds in the products regardless of the amount of Ru/C. As can be seen from Figure 2, the yield of bio-oil increased after adding Ru/C catalyst. The highest bio-oil yield (91.1 wt%) and total aromatic monomer yield (13.4 wt%) were obtained when 0.2 g Ru/C was used. Further adding Ru/C dosage would decrease the yields of bio-oil and total aromatic monomer. According to Figure 2, the amount of Ru/C had little effect on the yield of DHBF, but mainly affected the yield of H-type and G-type compounds. The yield of H-type compound was proportional to the amount of Ru/C, and the main products were H1 and H2. For G-type compounds, the highest yield (6.4 wt%) was obtained when 0.2 g Ru/C was used. The yield of G1 increased after the addition of Ru/C, but the amount of Ru/C had little effect on the yield, basically keeping at 0.9 wt%. The increase of Ru/C dosage was beneficial to the production of G2, but decreased the yield of G4. According to Table 4, when the amount of Ru/C increased, the yield of the products containing carbonyl group or double bonds in the side chain showed a decreasing trend. In contrast, the yield of products without unsaturated bonds in the side chain tended to increase. The result demonstrated that Ru/C facilitated hydrodeoxygenation in the side chain of benzene ring (Chen et al., 2015). The reason was that formic acid, as an in situ hydrogen source, could generate active hydrogen species using Ru/C catalyst under solvothermal conditions (Kristianto et al., 2017), which could facilitate hydrodeoxygenation. The role of formic acid was different from our previous study (Shao et al., 2018), in which formic acid acted through acid-catalyzed cleavage of linkages in lignin. In the presence of Ru/C, formic acid played two roles: (1) acid-catalyzed cleavage of linkages; (2) acted as an in situ hydrogen donor.
FIGURE 2. Effect of Ru/C dosage on the yield of depolymerized products Condition: 1 g lignin, 2 mmol ZnCl2, 20 ml methanol, 4 g formic acid, 160°C, 30 min.
The effect of reaction temperature on lignin depolymerization was investigated (Figure 3). It could be found that lignin depolymerization was highly dependent on temperature. Yields of bio-oil and total aromatic monomers were sharply increased with the elevation of reaction temperature. Remarkably, a noticeable rise was exhibited in the temperature range of 140–160°C. Wherein, yield of bio-oil increased from 77.6 wt% to 91.1 wt%, and yield of total aromatic monomers increased from 8.22 wt% to 13.4 wt%. This indicated that a higher reaction temperature seemed to have a positive influence on lignin depolymerization. However, further increasing the temperature to 180°C, yields of bio-oil and total aromatic monomers decreased to 83.9 wt% and 8.69 wt%, where repolymerization of monomers and oligomers was considered to be responsible for this (Long et al., 2014). As can be seen in Table 4, no other S-type phenolic compounds were produced except for S3 at 160°C. The yield of DHBF first increased to 2.48 wt% and then decreased to 1.45 wt% as a function of temperature. It should be noted that yield of H-type phenolic compounds increased with the elevated reaction temperature, and the highest yield (4.97 wt%) appeared at 180°C. The yield of total G-type phenolic compounds showed a similar tendency with that of bio-oil and total aromatic monomers when reaction temperature rose. One more interesting phenomenon, G4 could be detected only reaction temperature was 160°C. Product distribution showed excessive high temperature promoted the production of H-type compounds, but inhibited G-type compounds, aggravating the repolymerization (Lin et al., 2015). An appropriate temperature is adopted to optimize the yield of product.
FIGURE 3. Effect of reaction temperature on the yield of depolymerized products Condition: 1 g lignin, 2 mmol ZnCl2, 0.2 g 5 wt% Ru/C, 20 ml methanol, 4 g formic acid, 30 min.
Figure 4 shows the effect of reaction time on lignin depolymerization, and product distribution is shown in Table 5. As reaction time increased from 15 min to 30 min, bio-oil yield increased from 75.3 wt% to 91.1 wt%, and the total aromatic monomers yield reached 13.4 wt%. Further prolonging the reaction time to 45 min, significant decrease occurred in bio-oil and total aromatic monomers yield, which were 81.8 wt% and 10.6 wt% respectively. Data in Table 5 showed that there were fewer kinds of aromatic monomers when reaction time was 15 min. DHBF and H-type compounds were the major products, which yields were 2.28 wt% and 3.87 wt% respectively. These indicated that short reaction time led to insufficient bond rupture. For G-type compounds, the total yield first increased and then decreased as reaction time increased from 15 min to 45 min. It should be noted that yields of G1 and G2 had been rising with the increase of time. However, other G-type compounds appeared in the products only when the reaction time reached 30 min, which decreased in the case of prolonging the reaction time. These results illustrated that appropriate reaction time was favorable for lignin depolymerization. Short reaction time would make the reaction incomplete. Repolymerization of lignin-derived intermediates was promoted at long reaction time (Miller et al., 2002; Toledano et al., 2014; Shu et al., 2016a). Therefore, it is necessary to determine the ideal reaction time for the efficient depolymerization of lignin.
FIGURE 4. Effect of reaction time on the yield of depolymerized products Condition: 1 g lignin, 2 mmol ZnCl2, 0.2 g 5 wt% Ru/C, 20 ml methanol, 4 g formic acid, 160°C.
According to the 2D HSQC NMR spectrum of lignin reported in our previous research (Shao et al., 2018), a large number of β-O-4′ and phenylcoumarin structure existed in the lignin structure (Supplementary Figures S1, S2). During lignin depolymerization, the cleavage of C-O and C-C bonds was realized, producing the aromatic monomers and oligomers. DHBF was mainly produced through breaking Cα-Car bond of phenylcoumaran structure. The possible mechanism of DHBF formation was proposed (Figure 5). It should be noted that the fracture of Cα-Car bond and ring-opening of phenylfuran ring could not carried out simultaneously according to density functional theory. The result demonstrated yield of lignin-derived bio-oil and aromatic monomers, especially the alkyl phenol and alkyl guaiacol, was effectively improved in the presence of Ru/C and ZnCl2. The possible mechanism of lignin depolymerization under the synergetic catalysis of Ru/C and ZnCl2 was proposed (Figure 6). A stable complex of Zn2+ coordinated to the oxygen atoms in lignin molecule was formed (Klein et al., 2016; Wang et al., 2016). Synchronously, the high electronegativity Cl− was attached to the lignin molecule, selectively weakening the C-O bonds. Afterwards, the cleavage of C-O bonds (including β-O-4 and -OCH3 bonds) and C-C bonds occurred under the synergic of Ru/C and the polarization effect of Cl− (Parsell et al., 2013). Finally, various phenols containing alkyl substituents were obtained through a series of typical reactions, such as hydrogenation, dehydration, hydrolysis. Thus, the product distribution can be efficiently controlled by adjusting the type and content of catalyst, reaction temperature, and reaction time.
Alkali lignin could be efficiently depolymerized by the synergetic catalysis of Ru/C and ZnCl2 under microwave heating. 91.1 wt% yield of bio-oil including 13.4 wt% monomers was obtained under the optimum condition (FA-to-lignin mass ratio of 4, Ru/C dosage of 0.2 g, ZnCl2 dosage of 2 mmol, 160°C, and 30 min). Formic acid played two roles: (1) acid-catalyzed cleavage of linkages; (2) acted as in situ hydrogen donor for hydrodeoxygenation in the presence of Ru/C. This research provided a valuable reference to degrade lignin efficiently and adjust the product distribution under microwave heating.
The original contributions presented in the study are included in the article/Supplementary Material; further inquiries can be directed to the corresponding authors.
LS: conceptualization, methodology, formal analysis, investigation, writing—original draft preparation, writing—review and editing, funding acquisition. CW: methodology, writing—review and editing, funding acquisition. YL: formal analysis, writing—review and editing, funding acquisition. MW: methodology, validation, data curation. LW: investigation, software, data curation. FX: conceptualization, writing—review and editing, project administration.
This research was funded by the National Natural Science Foundation of China (Grant No. 32171718, 32001275), Shandong Provincial Natural Science Foundation (Grant No. ZR2019BC074), the Foundation of Qilu University of Technology (Shandong Academy of Science) (Grant No. 2022JBZ01-05).
Authors LS and LW were employed by the company of Shandong Chenming Paper Holdings Co., Ltd.
The remaining authors declare that the research was conducted in the absence of any commercial or financial relationships that could be construed as a potential conflict of interest.
All claims expressed in this article are solely those of the authors and do not necessarily represent those of their affiliated organizations, or those of the publisher, the editors and the reviewers. Any product that may be evaluated in this article, or claim that may be made by its manufacturer, is not guaranteed or endorsed by the publisher.
The Supplementary Material for this article can be found online at: https://www.frontiersin.org/articles/10.3389/fbioe.2022.1082341/full#supplementary-material
Barta, K., Matson, T. D., Fettig, M. L., Scott, S. L., Iretskii, A. V., and Ford, P. C. (2010). Catalytic disassembly of an organosolv lignin via hydrogen transfer from supercritical methanol. Green Chem. 12 (9), 1640–1647. doi:10.1039/C0GC00181C
Bjelić, A., Likozar, B., and Grilc, M. (2020). Scaling of lignin monomer hydrogenation, hydrodeoxygenation and hydrocracking reaction micro-kinetics over solid metal/acid catalysts to aromatic oligomers. Chem. Eng. J. 399, 125712. doi:10.1016/j.cej.2020.125712
Cao, X., Shao, L., Huang, W., Wang, C., Mao, J., Xu, F., et al. (2021). Thermal degradation of lignins fractionated by gradient acid precipitation. J. Anal. Appl. Pyrolysis 157, 105200. doi:10.1016/j.jaap.2021.105200
Cao, Y., Chen, S. S., Zhang, S., Ok, Y. S., Matsagar, B. M., Wu, K. C. W., et al. (2019). Advances in lignin valorization towards bio-based chemicals and fuels: Lignin biorefinery. Bioresour. Technol. 291, 121878. doi:10.1016/j.biortech.2019.121878
Cederholm, L., Xu, Y., Tagami, A., Sevastyanova, O., Odelius, K., and Hakkarainen, M. (2020). Microwave processing of lignin in green solvents: A high-yield process to narrow-dispersity oligomers. Ind. Crops Prod. 145, 112152. doi:10.1016/j.indcrop.2020.112152
Chen, M. Y., Huang, Y. B., Pang, H., Liu, X. X., and Fu, Y. (2015). Hydrodeoxygenation of lignin-derived phenols into alkanes over carbon nanotube supported Ru catalysts in biphasic systems. Green Chem. 17 (3), 1710–1717. doi:10.1039/C4GC01992J
Chong, G., Huang, X., Di, J., Xu, D., He, Y., Pei, Y., et al. (2018). Biodegradation of alkali lignin by a newly isolated Rhodococcus pyridinivorans CCZU-B16. Bioprocess Biosyst. Eng. 41 (4), 501–510. doi:10.1007/s00449-017-1884-x
Deuss, P. J., Scott, M., Tran, F., Westwood, N. J., de Vries, J. G., and Barta, K. (2015). Aromatic monomers by in situ conversion of reactive intermediates in the acid-catalyzed depolymerization of lignin. J. Am. Chem. Soc. 137 (23), 7456–7467. doi:10.1021/jacs.5b03693
Ekielski, A., and Mishra, P. K. (2020). Lignin for bioeconomy: The present and future role of technical lignin. Int. J. Mol. Sci. 22 (1), 63. doi:10.3390/ijms22010063
Hernández-Ramos, F., Fernández-Rodríguez, J., Alriols, M. G., Labidi, J., and Erdocia, X. (2020). Study of a renewable capping agent addition in lignin base catalyzed depolymerization process. Fuel 280, 118524. doi:10.1016/j.fuel.2020.118524
Hidajat, M. J., Riaz, A., and Kim, J. (2018). A two-step approach for producing oxygen-free aromatics from lignin using formic acid as a hydrogen source. Chem. Eng. J. 348, 799–810. doi:10.1016/j.cej.2018.05.036
Jiang, L., Guo, H., Li, C., Zhou, P., and Zhang, Z. (2019). Selective cleavage of lignin and lignin model compounds without external hydrogen, catalyzed by heterogeneous nickel catalysts. Chem. Sci. 10 (16), 4458–4468. doi:10.1039/C9SC00691E
Jiang, W., Cao, J. P., Xie, J. X., Zhao, L., Zhang, C., Zhao, X. Y., et al. (2021). Catalytic hydrodeoxygenation of lignin and its model compounds to hydrocarbon fuels over a metal/acid Ru/HZSM-5 catalyst. Energy fuels. 35, 19543–19552. doi:10.1021/acs.energyfuels.1c03169
Jing, Y., Dong, L., Guo, Y., Liu, X., and Wang, Y. (2020). Chemicals from lignin: A review of catalytic conversion involving hydrogen. ChemSusChem 13 (17), 4181–4198. doi:10.1002/cssc.201903174
Klein, I., Marcum, C., Kenttämaa, H., and Abu-Omar, M. M. (2016). Mechanistic investigation of the Zn/Pd/C catalyzed cleavage and hydrodeoxygenation of lignin. Green Chem. 18 (8), 2399–2405. doi:10.1039/C5GC01325A
Kristianto, I., Limarta, S. O., Lee, H., Ha, J. M., Suh, D. J., and Jae, J. (2017). Effective depolymerization of concentrated acid hydrolysis lignin using a carbon-supported ruthenium catalyst in ethanol/formic acid media. Bioresour. Technol. 234, 424–431. doi:10.1016/j.biortech.2017.03.070
Lancefield, C. S., Ojo, O. S., Tran, F., and Westwood, N. J. (2015). Isolation of functionalized phenolic monomers through selective oxidation and C-O bond cleavage of the β-O-4 linkages in lignin. Angew. Chem. 127 (1), 260–264. doi:10.1002/ange.201409408
Li, C., Zhao, X., Wang, A., Huber, G. W., and Zhang, T. (2015). Catalytic transformation of lignin for the production of chemicals and fuels. Chem. Rev. 115 (21), 11559–11624. doi:10.1021/acs.chemrev.5b00155
Lin, Y. C., Li, C. L., Wan, H. P., Lee, H. T., and Liu, C. F. (2015). Catalytic Hydrodeoxygenation of guaiacol on Rh-based and sulfided CoMo and NiMo catalysts. Energy fuels. 25 (3), 890–896. doi:10.1021/ef101521z
Liu, Q., Li, P., Liu, N., and Shen, D. (2017). Lignin depolymerization to aromatic monomers and oligomers in isopropanol assisted by microwave heating. Polym. Degrad. Stab. 135, 54–60. doi:10.1016/j.polymdegradstab.2016.11.016
Liu, X., Li, H., Xiao, L. P., Sun, R. C., and Song, G. (2019). Chemodivergent hydrogenolysis of eucalyptus lignin with Ni@ZIF-8 catalyst. Green Chem. 21 (6), 1498–1504. doi:10.1039/C8GC03511C
Long, J., Guo, B., Li, X., Jiang, Y., Wang, F., Tsang, S. C., et al. (2011). One step catalytic conversion of cellulose to sustainable chemicals utilizing cooperative ionic liquid pairs. Green Chem. 13 (9), 2334. doi:10.1039/c1gc15597k
Long, J., Qi, Z., Wang, T., Zhang, X., Ying, X., and Ma, L. (2014). An efficient and economical process for lignin depolymerization in biomass-derived solvent tetrahydrofuran. Bioresour. Technol. 154 (1), 10–17. doi:10.1016/j.biortech.2013.12.020
Luo, B., Li, R., Shu, R., Wang, C., Zhang, J., and Chen, Y. (2020). Boric acid as a novel homogeneous catalyst coupled with Ru/C for hydrodeoxygenation of phenolic compounds and raw lignin oil. Ind. Eng. Chem. Res. 59 (39), 17192–17199. doi:10.1021/acs.iecr.0c00888
Ma, C., Kim, T. H., Liu, K., Ma, M. G., Choi, S. E., and Si, C. (2021). Multifunctional lignin-based composite materials for emerging applications. Front. Bioeng. Biotechnol. 9, 708976. doi:10.3389/fbioe.2021.708976
Miessler, G., Fischer, P., and Tarr, D. (2013). Inorganic chemistry: Pearson new international edition. London: Pearson Higher Education.
Miller, J. E., Evans, L., Mudd, J. E., and Brown, K. A. (2002). Batch microreactor studies of lignin depolymerization by bases. 2. aqueous solvents. Office Sci. Tech. Inf. Tech. Rep. 30 (2), 61–78. doi:10.2172/800964
Parsell, T., Owen, B., Klein, I., Jarrell, T., Marcum, C., Haupert, L., et al. (2013). Cleavage and hydrodeoxygenation (HDO) of C-O bonds relevant to lignin conversion using Pd/Zn synergistic catalysis. Chem. Sci. 4 (2), 806–813. doi:10.1039/C2SC21657D
Regalbuto, J. R. (2009). Cellulosic biofuels-got gasoline? Science 325 (5942), 822–824. doi:10.1126/science.1174581
Shao, L., Zhang, Q., You, T., Zhang, X., and Xu, F. (2018). Microwave-assisted efficient depolymerization of alkaline lignin in methanol/formic acid media. Bioresour. Technol. 264, 238–243. doi:10.1016/j.biortech.2018.05.083
Shao, L., Zhang, X., Chen, F., and Xu, F. (2017). Fast pyrolysis of Kraft lignins fractionated by ultrafiltration. J. Anal. Appl. Pyrolysis 128, 27–34. doi:10.1016/j.jaap.2017.11.003
Shu, R., Long, J., Xu, Y., Ma, L., Zhang, Q., Wang, T., et al. (2016a). Investigation on the structural effect of lignin during the hydrogenolysis process. Bioresour. Technol. 200, 14–22. doi:10.1016/j.biortech.2015.09.112
Shu, R., Long, J., Yuan, Z., Zhang, Q., Wang, T., Wang, C., et al. (2015). Efficient and product-controlled depolymerization of lignin oriented by metal chloride cooperated with Pd/C. Bioresour. Technol. 179, 84–90. doi:10.1016/j.biortech.2014.12.021
Shu, R., Xu, Y., Ma, L., Zhang, Q., Wang, C., and Chen, Y. (2018). Controllable production of guaiacols and phenols from lignin depolymerization using Pd/C catalyst cooperated with metal chloride. Chem. Eng. J. 338, 457–464. doi:10.1016/j.cej.2018.01.002
Shu, R., Zhang, Q., Ma, L., Xu, Y., Chen, P., Wang, C., et al. (2016b). Insight into the solvent, temperature and time effects on the hydrogenolysis of hydrolyzed lignin. Bioresour. Technol. 221, 568–575. doi:10.1016/j.biortech.2016.09.043
Sun, C., Zheng, L., Xu, W., Dushkin, A. V., and Su, W. (2020). Mechanochemical cleavage of lignin models and lignin via oxidation and a subsequent base-catalyzed strategy. Green Chem. 22 (11), 3489–3494. doi:10.1039/D0GC00372G
Sun, Z., Fridrich, B., De Santi, A., Elangovan, S., and Barta, K. (2018). Bright side of lignin depolymerization: toward new platform chemicals. Chem. Rev. 118 (2), 614–678. doi:10.1021/acs.chemrev.7b00588
Swatloski, R. P., Spear, S. K., Holbrey, J. D., and Rogers, R. D. (2002). Dissolution of cellose with ionic liquids. J. Am. Chem. Soc. 124 (18), 4974–4975. doi:10.1021/ja025790m
Tang, W., Huang, C., Ling, Z., Lai, C., and Yong, Q. (2022). Insight into the mechanism of humic acid’s dissolution capacity for lignin in the biomass substrates. ACS Sustain. Chem. Eng. 10, 14648–14657. doi:10.1021/acssuschemeng.2c05471
Tang, W., Wu, X., Huang, C., Ling, Z., Lai, C., and Yong, Q. (2021). Revealing the influence of metallic chlorides pretreatment on chemical structures of lignin and enzymatic hydrolysis of waste wheat straw. Bioresour. Technol. 342, 125983. doi:10.1016/j.biortech.2021.125983
Toledano, A., Serrano, L., and Labidi, J. (2014). Improving base catalyzed lignin depolymerization by avoiding lignin repolymerization. Fuel 116, 617–624. doi:10.1016/j.fuel.2013.08.071
Toledano, A., Serrano, L., Labidi, J., Pineda, A., Balu, A. M., and Luque, R. (2013). Heterogeneously catalysed mild hydrogenolytic depolymerisation of lignin under microwave irradiation with hydrogen-donating solvents. Chemcatchem 5 (4), 977–985. doi:10.1002/cctc.201200616
Wang, H., Pu, Y., Ragauskas, A., and Yang, B. (2019). From lignin to valuable products–strategies, challenges, and prospects. Bioresour. Technol. 271, 449–461. doi:10.1016/j.biortech.2018.09.072
Wang, H., Zhang, L., Deng, T., Hao, R., Hou, X., Cort, J. R., et al. (2016). ZnCl2 induced catalytic conversion of softwood lignin to aromatics and hydrocarbons. Green Chem. 18 (9), 2802–2810. doi:10.1039/C5GC02967H
Wang, S., Zhang, K., Li, H., Xiao, L. P., and Song, G. (2021). Selective hydrogenolysis of catechyl lignin into propenylcatechol over an atomically dispersed ruthenium catalyst. Nat. Commun. 12 (1), 416–419. doi:10.1038/s41467-020-20684-1
Zhang, K., Li, H., Xiao, L. P., Wang, B., Sun, R. C., and Song, G. (2019). Sequential utilization of bamboo biomass through reductive catalytic fractionation of lignin. Bioresour. Technol. 285, 121335. doi:10.1016/j.biortech.2019.121335
Zhou, M., Sharma, B. K., Li, J., Zhao, J., Xu, J., and Jiang, J. (2019). Catalytic valorization of lignin to liquid fuels over solid acid catalyst assisted by microwave heating. Fuel 239, 239–244. doi:10.1016/j.fuel.2018.10.144
Zhou, M., Sharma, B. K., Liu, P., Xia, H., Xu, J., and Jiang, J. (2018). Microwave assisted depolymerization of alkaline lignin over hydrotalcite-based CuNiAl mixed oxides. ACS Sustain. Chem. Eng. 6 (9), 11519–11528. doi:10.1021/acssuschemeng.8b01697
Keywords: lignin, microwave, degradation, synergetic catalysis, controllable product distribution
Citation: Shao L, Wang C, Liu Y, Wang M, Wang L and Xu F (2022) Efficient depolymerization of lignin through microwave-assisted Ru/C catalyst cooperated with metal chloride in methanol/formic acid media. Front. Bioeng. Biotechnol. 10:1082341. doi: 10.3389/fbioe.2022.1082341
Received: 09 November 2022; Accepted: 05 December 2022;
Published: 16 December 2022.
Edited by:
Jiaxing Xu, Huaiyin Normal University, ChinaReviewed by:
Xiaojun Shen, Dalian Institute of Chemical Physics (CAS), ChinaCopyright © 2022 Shao, Wang, Liu, Wang, Wang and Xu. This is an open-access article distributed under the terms of the Creative Commons Attribution License (CC BY). The use, distribution or reproduction in other forums is permitted, provided the original author(s) and the copyright owner(s) are credited and that the original publication in this journal is cited, in accordance with accepted academic practice. No use, distribution or reproduction is permitted which does not comply with these terms.
*Correspondence: Chao Wang, Y2hhb3dhbmdAcWx1LmVkdS5jbg==; Yu Liu, bGVvbGl1eXVAMTYzLmNvbQ==; Feng Xu, eGZ4MzE1QGJqZnUuZWR1LmNu
Disclaimer: All claims expressed in this article are solely those of the authors and do not necessarily represent those of their affiliated organizations, or those of the publisher, the editors and the reviewers. Any product that may be evaluated in this article or claim that may be made by its manufacturer is not guaranteed or endorsed by the publisher.
Research integrity at Frontiers
Learn more about the work of our research integrity team to safeguard the quality of each article we publish.