- 1Department of Chemical and Materials Engineering, University of Kentucky, Lexington, KY, United States
- 2The Institute of Energy: Sustainability, Environment, and Equity, Stony Brook University, Stony Brook, NY, United States
- 3Sandia National Laboratories, Albuquerque, NM, United States
The need for clean, renewable energy has driven the expansion of renewable energy generators, such as wind and solar. However, to achieve a robust and responsive electrical grid based on such inherently intermittent renewable energy sources, grid-scale energy storage is essential. The unmet need for this critical component has motivated extensive grid-scale battery research, especially exploring chemistries “beyond Li-ion”. Among others, molten sodium (Na) batteries, which date back to the 1960s with Na-S, have seen a strong revival, owing mostly to raw material abundance and the excellent electrochemical properties of Na metal. Recently, many groups have demonstrated important advances in battery chemistries, electrolytes, and interfaces to lower material and operating costs, enhance cyclability, and understand key mechanisms that drive failure in molten Na batteries. For widespread implementation of molten Na batteries, though, further optimization, cost reduction, and mechanistic insight is necessary. In this light, this work provides a brief history of mature molten Na technologies, a comprehensive review of recent progress, and explores possibilities for future advancements.
1 Introduction
Energy use is a foundational aspect of human society. However, the continued use of non-renewable fossil fuels, such as oil, coal, and natural gas, is unsustainable (Burnham and Braun, 1990; Cross and Phillips, 1990; Perera, 2017; Kreps, 2020; Arnold and Osborne, 2023). Furthermore, their combustion releases carbon dioxide gas that accumulates in the atmosphere and leads to global warming (Archer et al., 2009; Andres et al., 2012; Ediger, 2019). The harmful effects of fossil fuels have led to the development of new, renewable methods to generate electricity. Namely, wind and solar energy have emerged as promising options to address the global energy crisis (Ackermann and Söder, 2000; Mekhilef et al., 2011). Wind turbines are spun solely with the power of wind, eliminating the need for steam turbines that rely on fossil fuels (Balat, 2009). Photovoltaic panels are composed of semiconducting materials that absorb energetic photons from the Sun and excite electrons that can then flow and generate electricity (El Chaar et al., 2011). Neither of these methods require fossil fuels to harness energy and their expansion significantly reduces the carbon footprint left by electricity generation (Bhandari et al., 2020; Lu et al., 2023). Importantly, these clean energy sources not only serve to replace fossil fuels for electricity generation, but they offer routes to satisfy growing demands for vehicle and industrial electrification (Yuan et al., 2021). These transformative new demands for clean, around-the-clock electricity stand to strain the existing grid infrastructure.
Additionally, both wind and solar suffer from intermittent and variable electricity generation (Anvari et al., 2016). Although the total energy harvested by wind and solar would be sufficient to support many critical industry sectors, significant amounts of energy may be wasted due to fluctuating, mismatched supply and demand, or limitations on the ability to transmit and distribute the energy when and where it is needed (Islam et al., 2014). Fossil fuels are then still necessary to supply an agile and reliable energy supply during times of peak demand or unplanned outages (Jebaselvi and Paramasivam, 2013; Calero et al., 2022). To combat fluctuating supply and demand and to relieve transmission congestion issues, many renewable generators utilize energy storage to reclaim energy that would be lost during periods of peak production, and to maintain a stable, responsive energy supply during periods of peak demand (Anvari et al., 2016; Kosowatz, 2018; Moran et al., 2018; Denholm et al., 2020; Rahman et al., 2020; Calero et al., 2022). In addition to short-term energy management (2–4 h), there is hope that long-duration energy storage (LDES) (>10–12 h) can strengthen the electrical grid during extended generation outages to further reduce reliance on fossil fuels (Albertus et al., 2020; Guerra, 2021; International Energy Agency, 2022; Long Duration Energy Storage Council, 2022; Denholm et al., 2023). Moreover, electrification of the transportation and industrial manufacturing sectors, which add significant load to the electrical grid, will absolutely require large-scale, extended-duration storage to meet energy demands (Pereirinha et al., 2018; Wei et al., 2019).
Rechargeable batteries are a promising energy storage solution. (Zhu et al., 2022a). Since the commercialization of the lithium-ion battery in the 1990s, battery-powered devices have become an integral part of society (Nagaura, 1990). However, lithium-ion batteries can encounter issues with materials supply chains, safety, and most importantly, cost (Helbig et al., 2018a; Helbig et al., 2018b; Wentker et al., 2019a; Wentker et al., 2019b; Karabelli et al., 2020; Chen et al., 2021; Kebede et al., 2021). This has led to exploration of many “beyond Li-ion” battery chemistries, which rely on cheaper, more sustainable materials. Molten sodium (Na) batteries, which were first introduced with the Na-sulfur (S) battery in the 1960s, are promising for grid-scale energy storage due to the widespread abundance of Na resources and the desirable electrochemical properties of Na metal (1,166 mA h g-1, -2.71 V vs. SHE) (Kummer and Weber, 1968; Coetzer, 1986; Karabelli et al., 2020). Their potential for effective grid-scale storage has led to the recent revitalization of molten Na battery research, with many groups tackling issues related to cost, lifetime, and energy/power density. This research progress has ignited commercialization efforts for various molten Na chemistries, by companies such as Enlighten Innovations, Inlyte Energy, Solstice, and Adena Power. This review aims to highlight recent progress and important remaining challenges in the field of molten Na batteries. Some important research and commercialization efforts are highlighted in Figure 1. Clear from this figure is the fact that although molten Na batteries have been in development for decades, the increased focus on these technologies in the last 10 years reveals a revitalization of this promising, Na-based set of technologies.
2 Early molten Na batteries
2.1 Na-S batteries
Na-S batteries were first developed in the 1960s by the Ford Motor Company (Kummer and Weber, 1968). Na-S cells couple an elemental S positive electrode with the Na negative electrode. The S electrode may be composited with carbon or absorbed in a carbon sponge to improve electronic conduction within the electrode. Traditionally, these cells were operated in excess of 300 °C, where the S electrode is also molten (Kummer and Weber, 1968; Weiner, 1977; Sudworth and Tilley, 1986). The two molten electrodes mandate a solid electrolyte to provide electrode containment, ion conduction, and electron blockage (Yung-Fang Yu and Kummer, 1967; Whittingham and Huggins, 1971a; Whittingham and Huggins, 1971b). Traditionally,
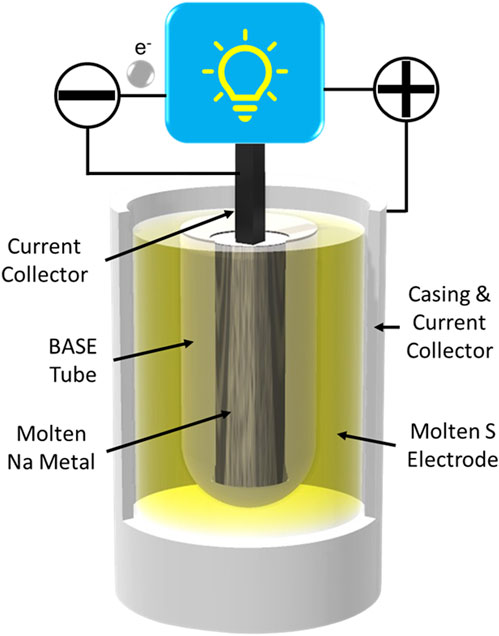
FIGURE 2. Illustration of a tubular molten Na-S battery configuration using a
During discharge of Na-S batteries, Na metal at the negative electrode is oxidized to Na+ ions. These ions pass through the BASE and react with the sulfur electrode to form a series of sodium polysulfides, ranging from Na2S8 to Na2S2. However, Na2S2 solidifies and cannot be reverted to elemental sulfur upon charging, so discharge should be ceased before any Na2S2 is formed. The negative and positive half-cell reactions and overall cell reaction are listed in Eqs 1–3.
Since these reactions occur in sequential stages, the potential at each composition slightly changes. An average voltage of ∼2.0 V is produced from these reactions (Kummer and Weber, 1968; Weiner, 1977; Sudworth and Tilley, 1986).
Na-S batteries have been successfully commercialized for grid-scale storage by NGK Insulators, LTD, and they have deployed 720 MW/4.9 GWh of storage around the world in more than 200 cities (Spoerke et al., 2030). NGK provides batteries that possess energy and power densities of 367 Wh L−1 and 36 W kg−1, respectively, and can achieve cycle lives of ∼4,500 cycles (NGL-Insulator, 2023). However, their high temperature operation (above 300°C) and engineering measures to address the hazardous reactivity of sodium and sulfur led to elevated operating costs and historically limited their application (Ohi, 1992; National Research Council, 2012; NGL-Insulator, 2023). Through a recent partnership between NGK and chemical manufacturer BASF, these batteries have been further optimized to improve lifetimes (7,300 projected cycles) and reduce costs (NAS Batteries, 2023).
2.2 ZEBRA batteries
In the 1980s, the first Na metal halide (NaMH) batteries were developed under the Zero-Emission Battery Research Activities (ZEBRA) project (Coetzer, 1986). This chemistry sought to improve upon the Na-S battery. ZEBRA batteries also use molten sodium metal negative electrodes and BASE as the solid electrolyte. However, the positive electrode of a ZEBRA battery consists of a molten sodium tetrachloroaluminate (NaAlCl4) salt mixed with NiCl2 (and, sometimes, FeCl2) particles. The NaAlCl4, which is often referred to as a secondary electrolyte or catholyte, melts near 154 °C and helps to alleviate the issue of ionic conductivity of Na+ in the positive electrode (Coetzer, 1986; Bones et al., 1989; Sudworth, 2001). The early ZEBRA battery configuration is similar to a Na-S cell, with the S electrode (e.g., as shown in Figure 2) replaced by the halide salt/catholyte mixture. The half-cell reactions for the positive electrode are listed in Eqs 4, 5. Note that the negative half-cell reaction is the same as the Na-S chemistry (Eq. 1).
The primary NiCl2 reaction leads to a voltage plateau near 2.58 V, while the FeCl2 (if included) reaction occurs at a plateau near 2.35 V (Coetzer, 1986; Bones et al., 1989; Sudworth, 2001). These typically occur sequentially, with the NiCl2 discharging first, followed by the FeCl2 discharge. These two separate plateaus can be useful for gauging the SOC of the battery. FeCl2 addition can also serve to reduce the internal resistance of the cell, increasing the power (high current) capability of ZEBRA batteries. At high current, the polarization within ZEBRA batteries may be high enough that the voltage plateau is below 2.35 V and both reactions occur simultaneously (Dustmann, 2004; Sakaebe et al., 2014).
Besides the higher voltage, ZEBRA batteries are believed to be inherently safer than Na-S, requiring fewer engineering controls to address the hazardous reactivity of high temperature molten Na and S. If the ceramic electrolyte in a ZEBRA battery were to fail (a phenomenon that will be discussed in detail later) the reaction between Na metal and NaAlCl4 (Eq. 6):
produces only benign salt and Al metal, and is far less violent than the reaction between Na and S (Trickett, 1998; Dustmann, 2004; Sakaebe et al., 2014) Moreover, the high Na+ conductivity afforded by the NaAlCl4 catholyte allows for a slight reduction in temperature, with ZEBRA batteries capable of operating near 250°C. NaAlCl4 also prevents chlorine gas formation if the battery is overcharged through a secondary reaction (Eq. 7) with Ni metal:
Finally, ZEBRA batteries can be assembled in the discharged state, where it is not necessary to handle air and moisture-sensitive Na metal.
Traditional ZEBRA batteries have been successfully commercialized by FZSoNick and have found a niche in grid-scale as well as select mobile storage applications, totaling 500 MWh of total storage (Fzsonick, 2023a; Spoerke et al., 2030). These batteries provide an energy density of ∼90 Wh L−1, attain cycle lives up to 4,500 cycles at 80% depth of discharge (DOD), and display total energy efficiencies near 90% (accounting for the energy needed to maintain their operating temperature) (Fzsonick, 2023b). One common concern with ZEBRA batteries is the inclusion of Ni metal, which has a relatively high “supply risk” (SR - a score from 0 to 100 that quantifies a material’s susceptibility to supply concerns). This is mainly attributed to its high and increasing demand, which is partially fueled by its extensive use in Li-ion batteries (Helbig et al., 2018a; Wentker et al., 2019a). As with Na-S, it is desirable to lower costs by reducing the operating temperature of ZEBRA batteries, but this is limited by two factors. Firstly, the catholyte becomes viscous at lower temperatures and solidifies below 154°C, eliminating the high Na+ conductivity in the positive electrolyte and compromising the ability to cycle reliably (Bones et al., 1989). Secondly, the conductivity of the BASE exponentially decreases with decreasing temperature (Kummer, 1972; Dustmann, 2004). Potential remedies to these issues for ZEBRA batteries and their descendants are addressed in the following sections. Table 1 compares commercial Na-S and ZEBRA battery systems to other current energy storage technologies (as described by the World Energy Council) (Gardner et al., 2016).
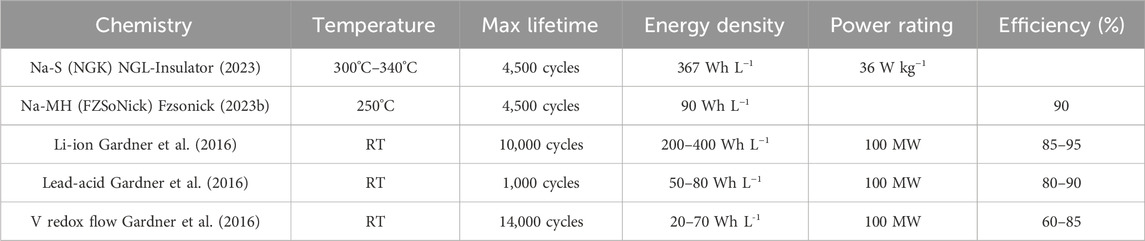
TABLE 1. Comparison of commercialized molten Na energy technologies with other chemistries. Information for other chemistries sourced from the World Energy Council.
3 Next-generation molten sodium batteries
Significant research has recently been conducted to improve molten Na batteries, particularly for grid-scale energy storage. Figure 3 illustrates recently reported gravimetric and volumetric energy densities of various chemistries as a function of temperature (numeric values for these points are included in Table 2) (Parthasarathy et al., 2007; Lu et al., 2013a; Lu et al., 2013b; Li et al., 2013; Lu et al., 2014; Kim et al., 2015a; Li et al., 2015a; Shamie et al., 2015; Spatocco et al., 2015; Li et al., 2016a; Liu et al., 2016; Xu et al., 2016; Ao et al., 2017a; Chang et al., 2017; Holzapfel et al., 2017; Small et al., 2017; Xue et al., 2017; Chang et al., 2018a; Chang et al., 2018b; Jung et al., 2018; Lu et al., 2018; Yang et al., 2018; Ahn et al., 2019; Jin et al., 2019a; Nikiforidis et al., 2019; Niu et al., 2019; Ding et al., 2020a; Gross et al., 2020a; Li et al., 2020a; Zhan et al., 2020a; Ding et al., 2020b; Zhan et al., 2020b; Gao et al., 2020; Gross et al., 2021; Niu et al., 2021; Wang et al., 2021; Flynn et al., 2022; Zhou et al., 2022; Heinz et al., 2023; Lan et al., 2023; Weller et al., 2023) To reduce operating and material costs, lower temperature molten Na batteries are the most desirable. As such, ZEBRA-style batteries have garnered more recent attention than their Na-S counterparts, due to the higher melting points of sodium/sulfur compounds, as well as the safer inherent reactivity of the ZEBRA molten salts. However, Figure 3 shows that Na-S type batteries, and various other chemistries, are also promising for next-generation molten Na batteries. Newer chemistries, such as a higher voltage Na-I battery, liquid metal batteries (LMBs), and Na flow batteries (NFBs) have been developed and promise to lower costs while maintaining the necessary energy densities for grid-scale storage. In these next-generation batteries, particular interest has been paid to improving positive electrode performance and developing effective solid electrolytes (and often, coatings) to regulate the sodium|electrolyte interface. This section will highlight recent works dedicated to developing these next-generation molten Na batteries. Generalized schematics of the battery technologies covered in this section are shown in Figure 4.
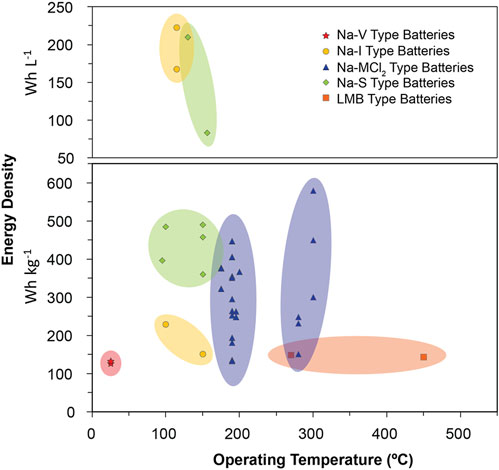
FIGURE 3. Gravimetric and volumetric energy densities of recent molten Na battery reports. Numeric values for points in the figure are included in Table 2.
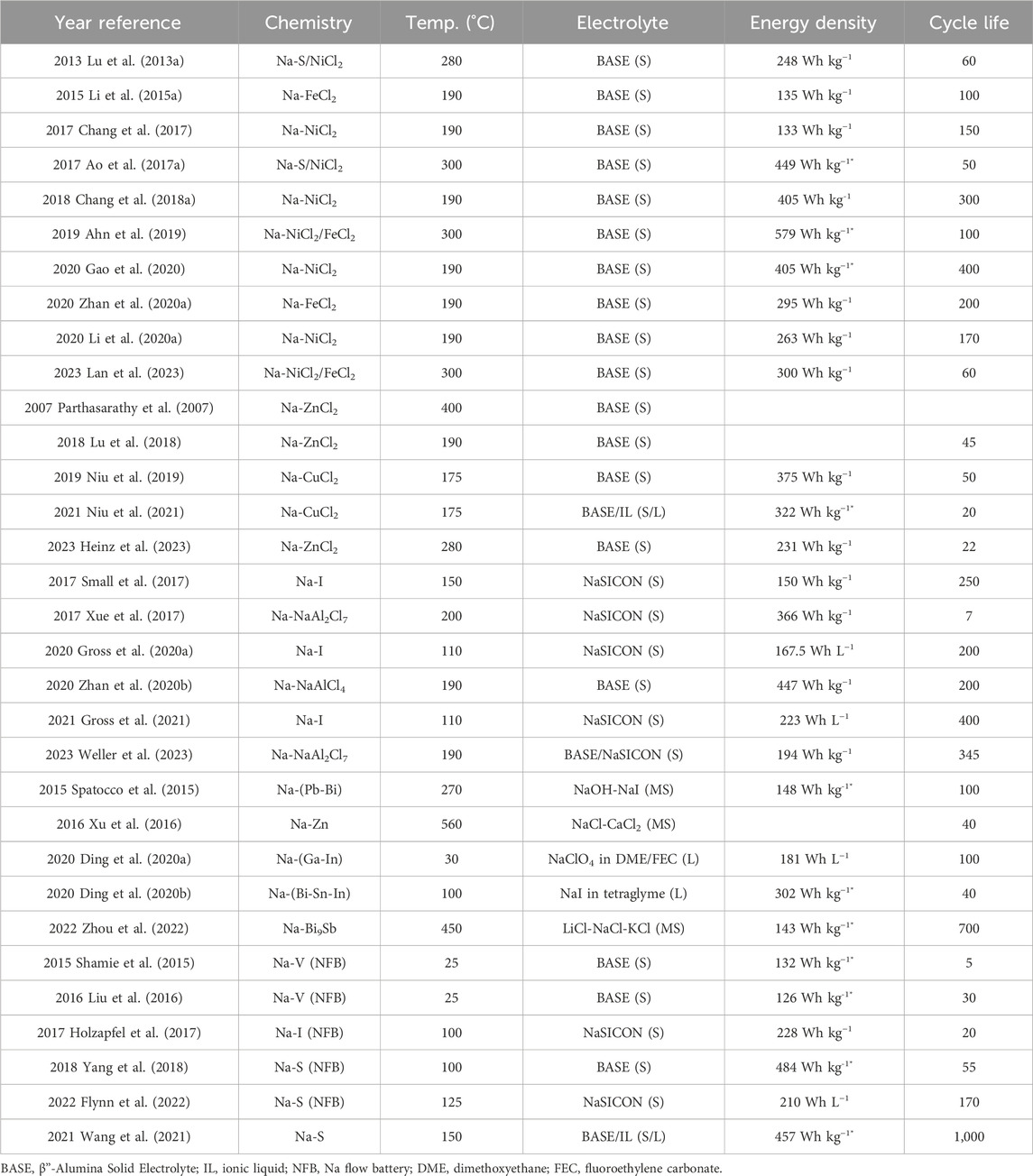
TABLE 2. Summary of performance metrics in recent molten Na battery publications. Energy densities marked with * were estimated based on information available in the publications. In Electrolyte column, S, L, and MS indicates solid, liquid, or molten salt, respectively. For any blank entries, information was not provided or able to be calculated.

FIGURE 4. Schematics of (A) ZEBRA-style molten sodium batteries (AM = active material), (B) fully molten metal halide batteries, (C) liquid metal batteries (LMB), and (D) sodium flow batteries (NFB).
3.1 Lower-temperature molten sodium batteries
3.1.1 ZEBRA-style batteries
As stated previously, the NaAlCl4 catholyte in ZEBRA batteries liquefies near 154°C. Na metal is molten at temperatures above 98°C. This means that, theoretically, ZEBRA batteries could be operated at temperatures as low as 154°C and still maintain the benefits of a liquid catholyte and negative electrode. Namely, these benefits are higher conductivity of active Na+ ions and improved contact at the catholyte|electrolyte interface (a liquid|solid interface as opposed to a solid|solid interface) (Gerovasili et al., 2014; Lu et al., 2014; Li et al., 2016a). However, in practice, it is difficult to decrease the temperature to 154°C. The difficulties can be attributed to the increased catholyte viscosity and decreased Na+ conductivity in both the catholyte and solid electrolyte. In the classical tubular configuration, temperatures down to 240°C have been studied by Gerovasili et al. (2014) Interestingly, at these reduced temperatures, the solid salt particles (NiCl2 and particularly NaCl) maintain a smaller average particle size compared to operation at higher temperatures. This is beneficial as the smaller particles provide more active surface area for the electrochemical reactions to proceed, leading to less polarization. These findings would point to lower temperatures as preferable for ZEBRA battery operation, but they are limited to ∼240°C in the tubular configuration due to the reduced catholyte conductivity at that temperature (Gerovasili et al., 2014).
To take advantage of the benefits at temperatures below 240°C, planar configurations of the ZEBRA battery have been proposed (Lu et al., 2012; Li et al., 2014; Lu et al., 2017). A planar ZEBRA-style battery configuration is illustrated in Figure 4A. The thinner electrodes used in planar designs shorten diffusion pathways and increase active surface area to lessen the effect of lower conductivity in the positive electrode. A planar design also allows for the use of thinner electrolytes (which can improve energy and power density) and facilitates easier cell packing and thermal regulation. In 2016, Li et al. demonstrated a planar Na-NiCl2 battery that operated as low as 190°C with an energy density of 350 Wh kg−1 and a lifetime of over 1,000 cycles (Li et al., 2016a). The improved energy density was attributed to the planar design and the lower temperature slowed particle growth, leading to a long cycle life. Further, reducing excess Ni content in the positive electrode can boost energy density, both reducing cost and enhancing performance (Li et al., 2013; Li et al., 2016a; Chang et al., 2018a). Planar ZEBRA-style cells have also been operated near 300°C to reduce electrolyte resistance and enable high current densities up to 80 mA cm−2. (Lan et al., 2023).
To further enhance the performance of Na-NiCl2 cells, various cathode architectures have been proposed. Positive electrodes composed of carbon fibers with dispersed Ni particles can maintain a conductive network and constrain particle growth during cycling (Li et al., 2020a; Gao et al., 2020). Li et al. showed that NiCl2/graphene aerogel positive electrodes with high electronic conductivity exhibited low polarization and allowed for the reduction of excess Ni (Li et al., 2021a). Ni-coated graphite particles introduced by Chang et al. provided robust conductive pathways in the electrode, whilst also eliminating a portion of electrochemically inactive Ni (Chang et al., 2017). Encapsulating Ni particles within a Ni3S2 shell was shown to mitigate particle growth and enhance cycle life of Na-NiCl2 cells (Ao et al., 2017a; Ao et al., 2017b). These studies generally suggest that architectures capable of limiting Ni particle growth can effectively improve the performance of Na-NiCl2 cells (Kim et al., 2017; Ahn et al., 2019).
Additional reports have shown that costs can be reduced by partially or completely eliminating Ni from the positive electrode. Lu et al. showed that a combination Na-S/NiCl2 battery could operate with capacity contribution from both active materials (Lu et al., 2013a). FeCl2 is a common additive to NiCl2 positive electrodes in ZEBRA cells, but positive electrodes using purely FeCl2 have also been reported and completely eliminate the supply risk of Ni (Li et al., 2015a; Zhan et al., 2020a; Frusteri et al., 2022). These lower-cost batteries may sacrifice some energy density (295 Wh kg−1) to reduce positive electrode material costs by ∼94% (1.95 $ kWh−1 for FeCl2 vs. 31.78 $ kWh for NiCl2) (Li et al., 2015a; Zhan et al., 2020a).
3.1.2 Metal chlorides beyond NiCl2 and FeCl2
Other metal chlorides can be substituted for NiCl2 and FeCl2 in molten sodium batteries. Parthasarathy et al. (2007) proposed a high-temperature (400°C) Na-ZnCl2 that used a ZnCl2/NaCl catholyte and benefited from lower-cost and non-corrosive ZnCl2. The cell relied on the overall reaction (Eq. 8):
and provided a discharge voltage of ∼2.0 V. Researchers have since tried to lower the operating temperature of Na-ZnCl2 cells to further reduce costs. Lu et al. used the traditional NaAlCl4 catholyte to reduce the temperature to 280 °C. Zn and NaCl particle growth was limited at this temperature which helped maintain cell reversibility (Lu et al., 2013c) The same group eventually lowered the temperature even further to 190°C and proposed the following two-step reaction mechanism (Eqs 9, 10):
that provided discharge voltages of 1.94 and 2.13 V, respectively (Lu et al., 2018) Similar to NiCl2/FeCl2 batteries, electrode architectures and different NaCl/ZnCl2 ratios have been studied to understand the influence of particle growth on battery performance (Kim et al., 2015b; Lee et al., 2019) This extensive effort has led to the recent demonstration of high capacity (38 Ah) tubular Na-ZnCl2 cells by Heinz et al. (from the Solstice project) which benefited from an improved understanding of the AlCl3-NaCl-ZnCl2 secondary electrolyte and precursor morphology (Heinz et al., 2023; Kumar et al., 2023; Solstice, 2023; Sieuw et al., 2024).
In addition to ZnCl2, CuCl2 has been explored as a potential positive electrode material. Niu et al. reported a Na-CuCl2 battery that operated at 175°C and relied on a 1-ethyl-3-methylimidazolium bis(trifluoromethylsulfonyl)imide ([EMIM][TFSI]) ionic liquid catholyte. The group also reported similar issues related to particle growth and aggregation during cycling (Niu et al., 2019; Niu et al., 2021).
3.1.3 Fully molten metal halide batteries
The absolute minimum temperature of classical ZEBRA batteries (which use NiCl2 and FeCl2) is the melting point of the NaAlCl4 catholyte, 154°C. However, since Na is molten as low as 98°C, new positive electrode materials have the potential to further reduce temperature while maintaining the benefits of liquid electrodes. In 2017, Small et al. introduced a new molten NaMH battery chemistry that could be operated down to 120°C that relied on the electrochemical couple of Na and iodide (Small et al., 2017). This lower temperature was enabled by using a NaI-AlCl3 positive electrode. A 50:50 (atomic %) mixture of these salts has a melting point near 95°C, even lower than that of Na metal, unlocking a new temperature regime for molten Na batteries. This fully molten design is illustrated in Figure 4B. The elements in these electrodes are abundant (Al is the second most abundant element in the Earth’s crust) and, along with the temperature decrease, provide the opportunity for significant cost reduction for grid-scale storage (Small et al., 2017). As opposed to many of the metal-chloride batteries that used BASE, the NaI batteries used the Na Super Ionic CONductor (NaSICON) as the solid electrolyte, with the formula Na1+xZr2SixP3-xO12 (with 0 ≤ x ≤ 3) (Goodenough et al., 1976). NaSICON was selected for this chemistry due to improved conductivity at moderate temperatures, allowing higher current densities to be passed through the batteries below 150°C (Small et al., 2017). NaSICON will be discussed in more detail in a following section.
The ideal positive half-cell and overall reactions are listed in Eqs 11, 12. Note that this chemistry still employs a molten Na negative electrode with the same half-cell reaction as shown in Eq. 1.
This reaction would provide a theoretical voltage of 3.24 V, higher than Na-S or the previous metal chloride batteries. In practice, the reported batteries showed voltages just below 3 V due to various polarization sources. The elevated voltage and high concentration of redox-active I− in the molten salt allow for an energy density of 150 Wh kg−1, slightly higher than the traditional ZEBRA chemistry. These batteries were capable of cycling under various conditions for >3,000 h, with the added benefit that the electrode materials could be cooled, solidified, and reheated to their liquid state without adverse affecting performance. The ability to reversibly freeze and melt the active materials means that these batteries could survive harsh conditions even if their thermal regulation failed, which is extremely important for resilient storage. Further, this new chemistry was shown to be extremely safe, with negligible gas formation and only benign products (e.g., Al, NaI and NaCl) formed upon mixture of the positive and negative active materials (Small et al., 2017).
The Na-I batteries could be optimized to reduce the temperature even further. Gross et al. reported that if NaI-AlBr3 was used as the positive electrode instead of NaI-AlCl3, the batteries could be operated down to 110°C (Gross et al., 2020a). However, the new positive electrode suffered from significantly slower redox kinetics that limited high-current applications. Reaction kinetics could be improved by using a NaI-GaCl3 positive electrode that was found to operate similarly to AlCl3 and even elevated the nominal cell voltage to an impressive 3.65 V (Lee et al., 2021; Percival et al., 2021). The increased voltage was attributed to the complexation environment of I− and
Fully molten Na-Al batteries can also be fabricated using purely molten sodium chloroaluminate as the catholyte (the same catholyte from ZEBRA batteries without any NiCl2 or FeCl2 particles). The trivalent aluminum should provide excellent energy density according to Eq. 13:
which has a theoretical potential of 1.8 V. Xue et al. used NaAl2Cl7 as a catholyte and achieved 366 Wh kg−1 with limited cyclability. (Xue et al., 2017) Other groups opted for the basic NaAlCl4 catholyte, which could benefit from a simpler one-step conversion reaction and less corrosivity than the acidic NaAl2Cl7, and showed an extremely high energy density of 447 Wh kg−1 over 200 cycles (Zhan et al., 2020b) The acidic NaAl2Cl7 melt continues to be of particular interest, though, due to its higher theoretical energy density (∼493 Wh kg−1) (Weller et al., 2023) Fully molten NaMH batteries mitigate the concerns of particle ripening and disconnection that plague their ZEBRA counterparts and are an intriguing option for long-life, high-current molten Na batteries.
3.1.4 Molten sodium batteries beyond metal halide
The potential of molten Na batteries for grid-scale storage has motivated the development of many chemistries beyond metal halides. Liquid metal batteries (LMBs) are one example of these molten Na chemistries. These batteries contain two fully molten metallic electrodes and a molten salt electrolyte. The three molten layers naturally separate due to density differences to avoid short-circuiting as shown in Figure 4C; (Kim et al., 2013). Though the first LMBs can be traced back to 1960, the chemistry has regained attention for grid storage recently (Bernard, 1960; Crouthamel and Recht, 1967; Kim et al., 2013; Li et al., 2016b). Bi, Pb, Sn, Sb, Ga, In, Zn, and various other metals have been considered potential positive electrodes. (Kim et al., 2013). In 2016, Xu et al. reported a Na-Zn LMB that operated at 560 °C and combined molten Na and Zn electrodes with a NaCl-CaCl2 molten salt electrolyte (Xu et al., 2016). Spatocco et al. demonstrated that lower-temperature (270°C) Na-LMBs were possible when they reported a Na-(Pb-Bi) battery with a NaOH-NaI molten salt electrolyte (Spatocco et al., 2015). One prominent issue with Na-based LMBs has been the solubility of Na in the molten salt electrolytes, leading to relatively high self-discharge rates. In 2022, Zhou et al. reported a multi-cationic electrolyte of LiCl-NaCl-KCl that had limited Na solubility leading to smaller rates of self-discharge and stability over 700 cycles (Zhou et al., 2022). More details regarding molten salt electrolytes will be discussed in a subsequent section.
Anoterh strategy to improve Na-LMBs is to lower the temperature even further in order to use more traditional organic electrolytes. This has been demonstrated by Ding et al. in a Na-(Ga-In) battery operated at 30°C that used a NaClO4 in dimethoxyethane/fluoroethylene carbonate electrolyte. A Na-K alloy was used as the negative electrode to maintain all-molten electrodes at this low temperature (Ding et al., 2020a). The same group also reported a Na-(Bi-Sn-In) LMB at 100°C with a NaI in tetraglyme electrolyte that eliminated the use of costly Ga and In (Ding et al., 2020b). The low operating voltage (<2 V) of LMBs may somewhat limit their applicability, but their low cost, high capacity, and high reversibility are promising for grid-scale storage.
Metal-air batteries have potential as high energy density storage systems, due to the compact and lightweight carbon cathodes that mediate oxygen electrochemistry. While research has been limited, molten Na-air batteries were first explored by Peled et al., who used carbon- and cobalt oxide-based positive electrodes coupled with a polyethylene oxide (PEO) + NaTf electrolyte at 105°C (Peled et al., 2013). The electrolyte showed a wide voltage window, and the batteries exhibited good cyclability, but sluggish oxygen electrochemistry resulted in low current densities. Recently, Zhu et al. demonstrated a molten Na-air battery that used Ni powder mixed with a NaNO3 + KNO3 + CsNO3 eutectic molten salt as the positive electrode (Zhu et al., 2022b). The group showed that the nitrate anions in the molten salt mediated an overall 2e−/O2 reaction that formed Na2O2 as the final discharge product. Full cells could be cycled 400 times with a capacity of 0.5 mA h cm−2 at 5 mA cm−2. Further improvement and understanding of oxygen electrochemistry will be vital to further advancing molten Na-air batteries.
Another emerging chemistry is that of molten Na flow batteries (NFBs). The concept of NFBs was proposed by Shamie et al. using a Na-V redox couple as an example and is illustrated in Figure 4D. The batteries would be operated in the same fashion as conventional flow batteries, with a liquid catholyte and molten sodium as the anolyte being pumped from a large reservoir into an electrochemical cell. They suggested that a traditional vanadium redox-flow catholyte could be cycled between V3+ and V5+ to attain a high theoretical specific energy of ∼355 Wh kg−1 (Shamie et al., 2015). The group later demonstrated this concept using a Na-Cs alloy (molten at RT) coupled with a BASE separator and V-based aqueous catholyte, and the cell retained >99% of its original capacity over 30 cycles (Liu et al., 2016). However, the cost limitations of V-based NFBs has motivated research into other redox couples. NFBs using aqueous bromine and iodine catholytes have been reported by Holzapfel et al. and were able to achieve energy densities near 200 Wh kg−1 (Holzapfel et al., 2017; Gerbig et al., 2023). While room-temperature molten alloys (Na-K and Na-Cs) are intriguing materials for molten Na batteries, they react aggressively with air and moisture (even more so than pure Na metal) and significant engineering controls will be necessary to successfully implement them in LMBs, especially if they are paired with an aqueous catholyte.
The original Na-S chemistry has also been adapted to a NFB by various groups. The Na-S NFBs still use molten Na negative electrodes and a solid electrolyte of BASE or NaSICON but utilize S sources that can be converted to flow-type batteries. Yang et al. used a suspension of S and C particles in a 1 M NaI tetraglyme solution as a catholyte to achieve a Na-S NFB that maintained a capacity of 484 mA h g−1 after 55 cycles. Flynn et al. instead used sodium polysulfide (Na2Sx) dissolved in an organic solvent to fabricate an NFB capable of 170 cycles with a specific energy of 210 Wh/L at ∼120°C (Flynn et al., 2022). The technology described by Flynn et al is being further developed by Enlighten Innovations and is in the advanced stages of precommercial development (Enlighten, 2023). The ability to decouple energy and power in NFBs could prove vital to addressing the diverse demands of grid-scale energy storage. Finally, though details are outside the scope of this review, it is worthwhile to mention that room temperature Na-S batteries have been explored but are yet to be commercialized, as they are often plagued by the electrochemical irreversibility of solid polysulfide compounds or soluble polysulfide shuttling in aqueous electrolytes (Kim et al., 2016; Wei et al., 2016; Gross and Manthiram, 2019; Wang et al., 2020a; Wang et al., 2020b). A summary of various molten Na-based battery research reports is provided in Table 2. The authors believe it important to emphasize that these research reports do not represent the commercial performance of molten Na batteries, which have much longer cycle lives (1,000 s of cycles).
3.2 Electrolytes for molten sodium batteries
3.2.1 ”-alumina solid electrolyte (BASE)
BASE was initially thought to be a polymorph of Al2O3, but, in the early 1900s, Pauling showed that the structure contained sodium (Pauling, 1927). In 1967, Yao and Kummer of the Ford Motor Company first reported fast ion conduction in BASE, which was instrumental in the development of the first Na-S battery in the late 1960s. Since then, BASE has been used widely in both Na-S and ZEBRA batteries and has even found use in several all-solid-state battery (ASSB) technologies (Wenzel et al., 2016; Bay et al., 2020; Fertig et al., 2022; Fertig et al., 2023).
Beta aluminum oxides are comprised of alternating closely-packed layers and loosely-packed layers. The closely-packed layers serve as structural layers that consist of four layers of oxygen ions that contain aluminum (Al) ions in tetrahedral and octahedral interstitial sites. The loosely-packed layers contain mobile Na ions that can be driven under the influence of an electric field. The mobile Na provides the conductivity necessary to make useful solid electrolytes. There are two crystal structures of beta alumina oxides–
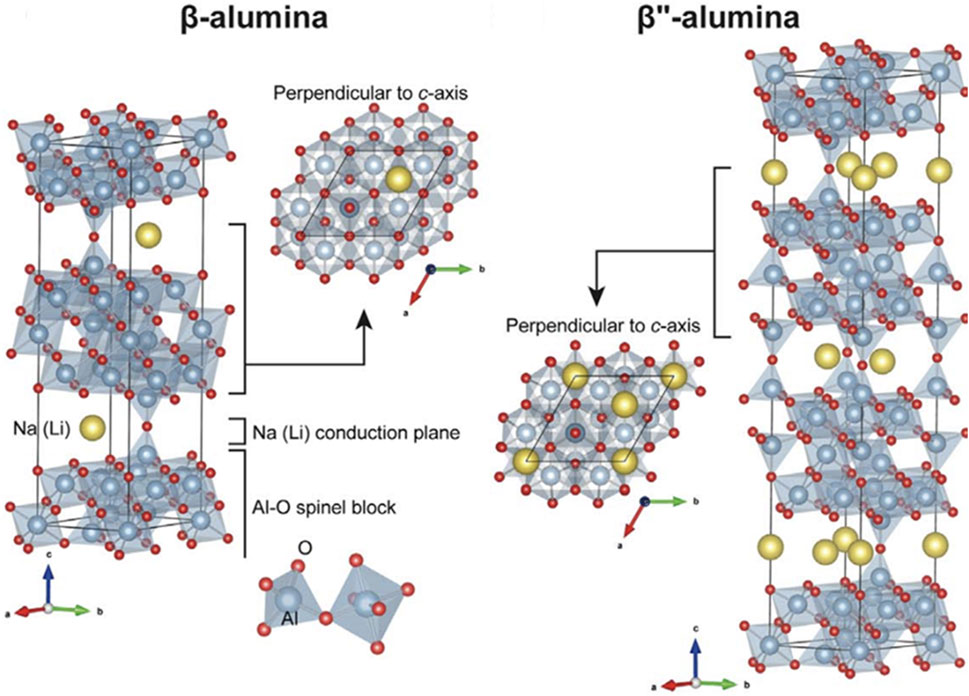
FIGURE 5. Structures of Na
The properties of BASE can be manipulated through careful control of its composition and processing parameters. Several authors have shown that aliovalent doping of the Al3+ sites in the structural layers with magnesium (Mg2+) or lithium (Li+) leads to excess negative charge that can be balanced by additional mobile Na+ ions (Bates et al., 1981; Lee et al., 2017; Dirksen et al., 2021). BASE is fabricated through solid-state reaction, sol-gel processes, or co-precipitation (Ray and Subbarao, 1975; Choy et al., 1993; van Zyl et al., 1993; Certo et al., 1998; Park et al., 2005; Mali and Petric, 2012; Barison et al., 2015). These methods all rely on first synthesizing BASE in its powder form and then sintering to attain the final desired shape. The sintering process can impact many characteristics of BASE such as phase purity and microstructure. The low-conductivity
Multiple advanced techniques are being explored to further improve the manufacturing and microstructure of BASE. Spark plasma sintering (SPS) is a promising processing technique that uses pulsed AC or DC current to rapidly heat a compressed powder and can lower sintering times from many hours to mere minutes. Koganei et al. showed that 98% dense BASE could be obtained using SPS by heating under compression to 1,400°C (100°C min−1), holding for 15 min, and allowing the pellets to cool naturally. The quick temperature ramp and short hold time can significantly reduce the cost of heating to such high temperatures and also minimize the volatilization of sodium, leading to lower cost, enhanced compositional control, and, critically, an extremely high room-temperature conductivity of 19 mS cm−1 (Koganei et al., 2014). Li et al. used lower-temperature (1,300°C) SPS to obtain >96% dense BASE with a conductivity of 183 mS cm−1 at 350°C (Li et al., 2020b). Freeze drying before SPS and high-temperature sintering after SPS have also been shown to produce mechanically strong, highly conductive (239 mS cm−1 at 350°C), but the high-temperature step negates some of the benefits of pure SPS processing (Li et al., 2021b). All groups attributed the high (and anisotropic) conductivities to highly c-axis oriented BASE. Similarly, microwave-assisted sintering has been preliminarily investigated and produced 86% dense BASE by applying 2,450 MHz microwaves during a 40 min hold at 1,300°C. (Mortalò et al., 2020).
Cold sintering also has the potential to lower the cost of fabricating BASE. Cold sintering uses a transient secondary phase to assist in obtaining the desired phase. Briefly, the electrolyte powder is mixed in an aqueous solution or with a (relatively) low melting point material (such as NaOH) and heated. At elevated temperatures, the transient liquid phase can promote densification at lower temperatures before evaporating or extruding from the die. For example, Grady et al. showed that >92% dense BASE could be obtained at 375 °C using a transient fused NaOH solvent. The BASE pellets exhibited a conductivity of 10 mS cm−1 at 300°C, which could be improved by heating the pellets to 1,000°C (Grady et al., 2021). Optimizing sintering parameters, particularly by minimizing time and/or temperature, remains as the most practical pathway for reducing BASE (and thereby molten Na battery) costs and efforts in this field should be prioritized.
3.2.2 Na Super Ionic CONductor (NaSICON)
NaSICON is an oxide ceramic with the formula Na1+xZr2SixP3-xO12, 0 ≤ x ≤ 3, that was reported by Hong and Goodenough in 1976 (Goodenough et al., 1976). NaSICON is a solid solution of NaZr2P3O12 and Na4Zr2Si3O12 and has a rhombohedral structure (R
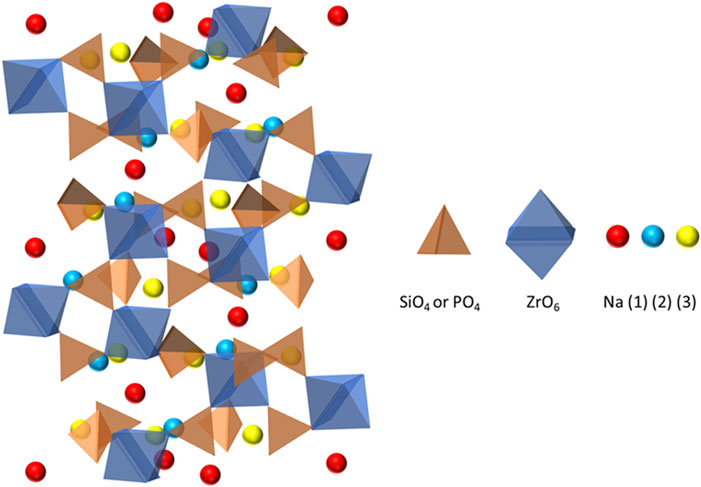
FIGURE 6. Structure of NaSICON showing interconnected silicate/phosphate tetrahedra and zirconia octahedra.
Since its discovery, NaSICON has been proposed as a replacement for BASE due to its excellent Na+ conductivity, particularly at lower temperature, as well as its environmental insensitivity, and its ease of machineability. The conductivity at lower temperatures makes it a particularly useful electrolyte as molten Na batteries push towards operating temperatures below 200 °C. Using the nominal NaSICON composition, Na3Zr2Si2PO4, Small et al. reported a NaSICON conductivity of 140 mS cm−1 at 200°C, slightly higher than BASE at the same temperature. NaSICON’s excellent low-temperature conductivity became more evident at room temperature, where its conductivity (>1 mS cm-1) was quite higher than BASE (Small et al., 2017). The improved conductivity at lower temperatures is thought to be, at least partially, a result of the three-dimensional NaSICON framework, as opposed to relying on two-dimensional conduction planes in BASE (Goodenough et al., 1976; Kohler et al., 1983; Kohler and Schulz, 1985; Boilot et al., 1988; Guin and Tietz, 2015; Small et al., 2017). Furthermore, aliovalent doping of the Zr site in NaSICON can raise the room-temperature conductivity even higher to above 2 mS cm−1. (Jolley et al., 2015a). Like BASE, doping the Zr4+ site with lower valent cations, such as Al, Y, Fe, Co., Ni, or Zn, results in an increased concentration of Na+ ions to achieve charge neutrality (Jolley et al., 2015b; Samiee et al., 2017). Grain size and presence of grain boundaries also influence the ionic conductivity, with larger grains typically leading to higher total conductivities (Fuentes et al., 2001; Nieto-Muñoz et al., 2020).
Many similar manufacturing techniques used for BASE have been successfully applied to NaSICON. However, NaSICON has one critical processing advantage compared to BASE. NaSICON can traditionally be sintered at much lower temperatures (∼1,100°C–1,200°C) with mostly complete conversion to the desired phase and high density (Goodenough et al., 1976; Gross et al., 2020b). This is much lower than the 1,450°C typically necessary for BASE and can significantly lower production costs (Ray and Subbarao, 1975; Liu et al., 2020). This is vitally important as the solid electrolyte is often viewed as one of the costlier components in molten Na batteries, often due to their high sintering temperatures (Lu et al., 2010b; Lu et al., 2013c). Liquid phase sintering using additives such as Bi2O3, Na2SiO3, or Na3BO3 enables sintering temperatures as low as 900°C and can reduce densification times due to enhanced liquid-state diffusion (Noi et al., 2018; Suzuki et al., 2018; Oh et al., 2019; Miao et al., 2021). Sol gel-processing, which dates back to the 1980s, can bring processing temperatures to ∼700°C. (Shimizu et al., 1997; Zhang et al., 2004; Bell et al., 2014). Fused hydroxide cold sintering at 375°C by Grady et al. achieved 93% dense NaSICON with a room-temperature conductivity of 0.2 mS cm−1. (Grady et al., 2020). A recent patent using the fused hydroxide cold sintering method reported 89% densification of NaSICON at just 150°C, but this lower density resulted in a conductivity of 1.13 x 10−5 mS cm−1 at 35°C. (Bock et al., 2023). Aqueous transient phases can push the cold sintering temperature even lower, as demonstrated by Leng et al., who showed that 83% dense Mg-doped NaSICON could be obtained by cold sintering at 140°C. However, a second annealing step at 1,100°C was necessary to achieve a room-temperature conductivity of 1.36 mS cm−1. (Leng et al., 2018). This method was further explored by combining cold sintering with liquid phase sintering using a Bi2O3 additive that melted near 820°C and helped increase the final conductivity >1.5 mS cm−1 (Leng et al., 2019). Room temperature fabrication of thin NaSICON films (3.5–10
One concern with the use of NaSICON for Na batteries is the chemical compatibility with Na metal. Early studies presented theoretical and experimental evidence that NaSICON was unstable in the presence of Na metal (Schmid et al., 1982; Tsai and Hong, 1983). These were mainly focused on using NaSICON as an electrolyte for Na-S batteries, and experimental studies were accordingly carried out near 300°C. Discoloration, lattice parameter changes, and fracturing were observed after immersing NaSICON in molten Na metal for extended periods of time. These changes indicated reaction with Na, which would have increased the Na content of NaSICON and subsequently caused stresses in the electrolytes, leading to fracture (Kreuer and Warhus, 1986). Further studies suggested that these degradation pathways were kinetically dominated, meaning that stable performance at lower temperatures could be possible (Warhus et al., 1988; Zhang et al., 2020a). Accordingly, Zhou et al., from the Goodenough group, showed that NaSICON was chemically stable in the presence of Na metal up to at least 175°C. As predicted, at temperatures above 300°C, NaSICON could be partially reduced and amorphized upon reaction with Na, but this actually improved molten Na wetting (Zhou et al., 2017). The low-temperature stability and non-catastrophic pathways at elevated temperatures imply that NaSICON can be used without significant risk of chemical decomposition in long-lifetime molten Na batteries.
3.2.3 Glass and glass-ceramic conductors
While BASE and NaSICON have traditionally been the primary electrolyte options for molten Na batteries, other Na+-conducting materials have been proposed as potential electrolytes. Borate, aluminosilicate, and NaSICON-glass (NASIGLAS) electrolytes were explored in early Na-S cells, but BASE was ultimately favored for its higher conductivity and corrosion resistance (Susman et al., 1983; Herczog, 1985; Bloom et al., 1986; Sudworth and Tilley, 1986). The low-cost materials and processing (typically at lower temperatures) has helped retain interest in glass electrolytes. Braga et al. prepared amorphous A2.99M0.005OCl1-z(OH)x (A = Li or Na, M = Ba or Ca) electrolytes at just 230°C–250°C with room-temperature conductivities >10 mS cm−1. (Braga et al., 2016). Reports of sulfide (Na3BS3, Na2S-GeS2, Na2S-P2S5, Na2S-GeS2-P2S5), oxide (Na2.8Ca0.1Al2Ga0.5P2.7O12, Na2O-Al2O3-P2O5-Nb2O5, Na3Al1.8Si1.65P1.8O12 and Na3Al2P3O12), and oxysulfide (Na3PS4-xOx and Na4P2S7-6xO4.62xN0.92x) glasses have also shown room-temperature conductivities >0.1 mS cm−1, and their conductivities often depend strongly on dopant concentrations (Nose et al., 2015; Allu et al., 2018; Keshri et al., 2020; Lazar et al., 2020; Keshri et al., 2021; Tsuji et al., 2021; Chi et al., 2022; Keshri et al., 2022; Nasu et al., 2022; Olson et al., 2023). The elimination of grain boundaries in glass electrolytes is thought of as a distinct advantage over traditional ceramics, as grain boundaries often have reduced conductivity or may act as failure pathways for dendrites.
In addition to the pure glassy electrolytes, glass-ceramic composite electrolytes have recently garnered interest, due to the typically higher conductivity of the ceramic phase. Glass-ceramic composites are often synthesized by fully or partially crystallizing the glassy phase at elevated temperatures. One early example from Hayashi et al. is that of Na3PS4, where the glassy phase was crystallized to cubic Na3PS4 by heating to above 270°C and the resulting electrolyte had a room temperature conductivity of 0.2 mS cm−1 (Hayashi et al., 2012; Hayashi et al., 2014; Tatsumisago and Hayashi, 2014). Since then, many glass-ceramic electrolytes have been proposed using the crystallization technique. These also fall into the categories of sulfides (such as Na3PS4-Na4SiS4, Na2.9375PS3.9375Cl0.0625, Na3PS4-Na4GeS4, Na3PS4-NaI, Na10GeP2S12, and Na3SixSb1-xS4-yBry) and oxides (such as Na1+x[SnxGe2−x(PO4)3], Na3+x[ZrxSc2-x(PO4)3], Na1+yTi2SiyP3-yO12, (Na2O + NaF)–TiO2–B2O3–P2O5–ZrF4, Na3Zr2Si2PO12-NaF, Na1+xYyGax−yGe2−x(PO4)3, and Na2O-Y2O3-SiO2) and may exhibit room-temperature conductivities as high as 2.26 mS cm−1 (Na3SixSb1-xS4-yBry), but are typically reported to be near 0.1 mS cm−1 (Tanibata et al., 2014; Li et al., 2015b; Hibi et al., 2015; Ni et al., 2015; Chu et al., 2016; Gandi et al., 2018; Manchgesang et al., 2018; Tanibata et al., 2018; Tsuji et al., 2018; Nieto-Muñoz et al., 2019; Shao et al., 2019; Sundar et al., 2019; Gong et al., 2023). Sintered, crystalline thiophosphates with tungsten dopants (Na3-xSb1-xWxS4, and Na3-xP1-xWxS4) can attain even higher room-temperature conductivities, reaching as high as 41 mS cm−1 (Hayashi et al., 2019; Fuchs et al., 2020). While these electrolytes show promising Na+ conductivities, they have not been demonstrated in molten Na batteries. Instead, the studies often showcase their performance in solid-state Na batteries or symmetric cells. The stability of the electrolytes at elevated temperatures and compatibility with molten Na will be important considerations if they are to be applied in molten Na batteries.
3.2.4 Molten salt electrolytes
LMBs were discussed previously and use molten salt electrolytes to separate two molten metallic electrode layers based on density. An 80:20 NaOH-NaI eutectic mixture was shown to have a low melting point of 220 °C, a conductivity of ∼500 mS cm−1 at 250°C, and was demonstrated for 112 cycles in a Na|NaI-NaOH|Pb-Bi cell. (Spatocco et al., 2015). A 50:50 NaCl-CaCl2 electrolyte with a melting point near 500°C enabled a Na-Zn metal battery to operate stably for 40 cycles. (Xu et al., 2016). In addition to these binary systems, multi-cationic systems have also been explored, often with the goal of reducing the solubility of Na in the electrolyte. A LiCl-NaCl-KCl molten salt electrolyte from Zhou et al. exhibited a melting point of ∼400 °C and a Na+ conductivity of 65 mS cm−1 at 450°C, and was used as the electrolyte in a Na|LiCl-NaCl-KCl|BixSb cell cycled 700 times (Zhou et al., 2022). Phase diagrams and exchange reaction equilibria constants for the ternary system were also modeled by the same group (Ding et al., 2023). Another ternary system using iodide salts, LiI-NaI-KI, with a melting point of ∼290 °C was demonstrated by Gong et al. and estimated to have a Na+ conductivity of 28 mS cm−1 above 350°C (Gong et al., 2020). A low melting point (154°C) nitrate-based ternary molten salt, NaNO3-KNO3-CsNO3, coupled with a BASE membrane enabled a molten Na-O2 cell to operate at just 170°C for 400 cycles with no capacity fade (Zhu et al., 2022b). A similar triflate-based multi-cationic molten salt electrolyte has been demonstrated for high-temperature lithium batteries, and likely could find applications in molten Na batteries (Tu et al., 2010). Versatile molten salt chemistries using multiple components are a promising avenue for developing moderate-temperature electrolytes with tunable physical and electrochemical properties.
3.2.5 Alternative sodium ion conductors
In addition to the previous classes of electrolytes, a few emerging electrolytes could show promise for molten Na batteries. Na+-conducting polymer electrolytes using Na salts in a polymer scaffold, such as polyethylene oxide (PEO), have been widely studied, but PEO often melts below 100°C and is susceptible to attack by molten Na. As such, polymer electrolytes have not yet been studied in molten Na batteries. As lower-temperature Na alloys are employed or advanced polymers are synthesized, there may be an opportunity for low-cost, mechanically tough, and easily processable electrolytes (Boschin and Johansson, 2015; Zhang et al., 2020b; Nimah et al., 2015; Koduru et al., 2016; Qiao et al., 2020). Polyborate salts emerged as a potential solid electrolyte when the high conductivity (100 mS cm−1 at 256°C) of Na2B12H12 was reported by Udovic et al. in 2014. (Udovic et al., 2014). Since then, further studies of polyborates utilizing various anions (such as NaCB9H10, NaCB11H12, and NaB11H14 Na(HCB11H5X6) (X = Br or Cl), Na3B24H23) have shed light on the high-temperature order-disorder transition and “paddle-wheel” conduction mechanism in these salts (Tang et al., 2016; Kweon et al., 2017; Tang et al., 2017; Jørgensen et al., 2020; Jin et al., 2023). These and other highly-conductive salts may prove extremely valuable for molten Na batteries, particularly if their conductive phases can be stabilized at intermediate temperatures. Schematics and structures of these various sodium ion conductors are shown in Figure 7. A summary of electrolyte compositions, synthesis conditions, and resultant conductivities is provided in Table 3.
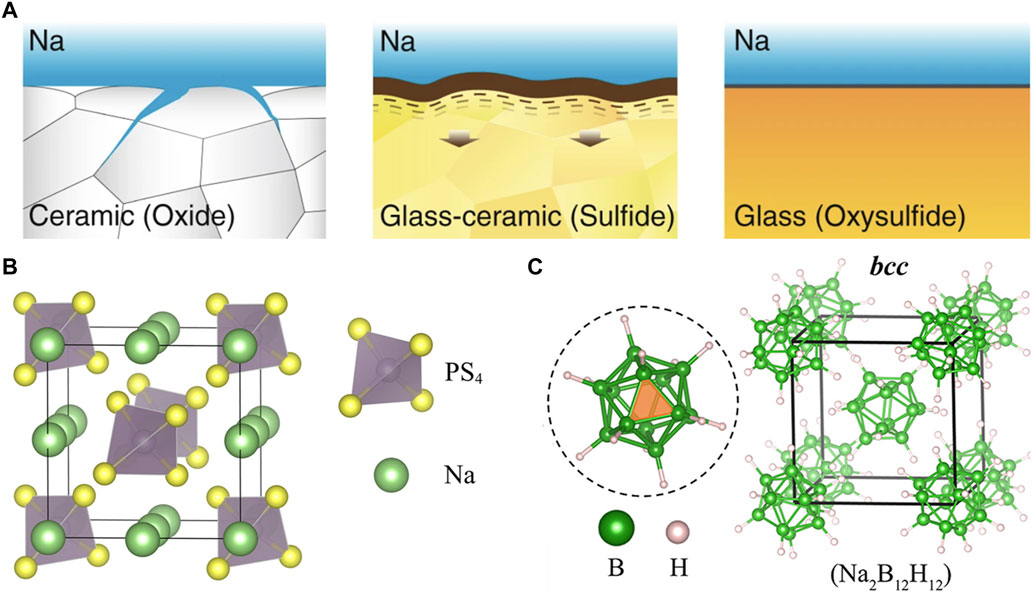
FIGURE 7. (A) Illustrations of ceramic, glass-ceramic, and glass microstructures and sodium interface behavior. Reprinted with permission from Ref. 201. (B) Structure of Na3PS4 electrolyte. Reprinted with permission from Ref. 225. (C) Structure of Na2B12H12 electrolyte. Reprinted with permission from Ref. 238. Copyright 2017, American Chemical Society.
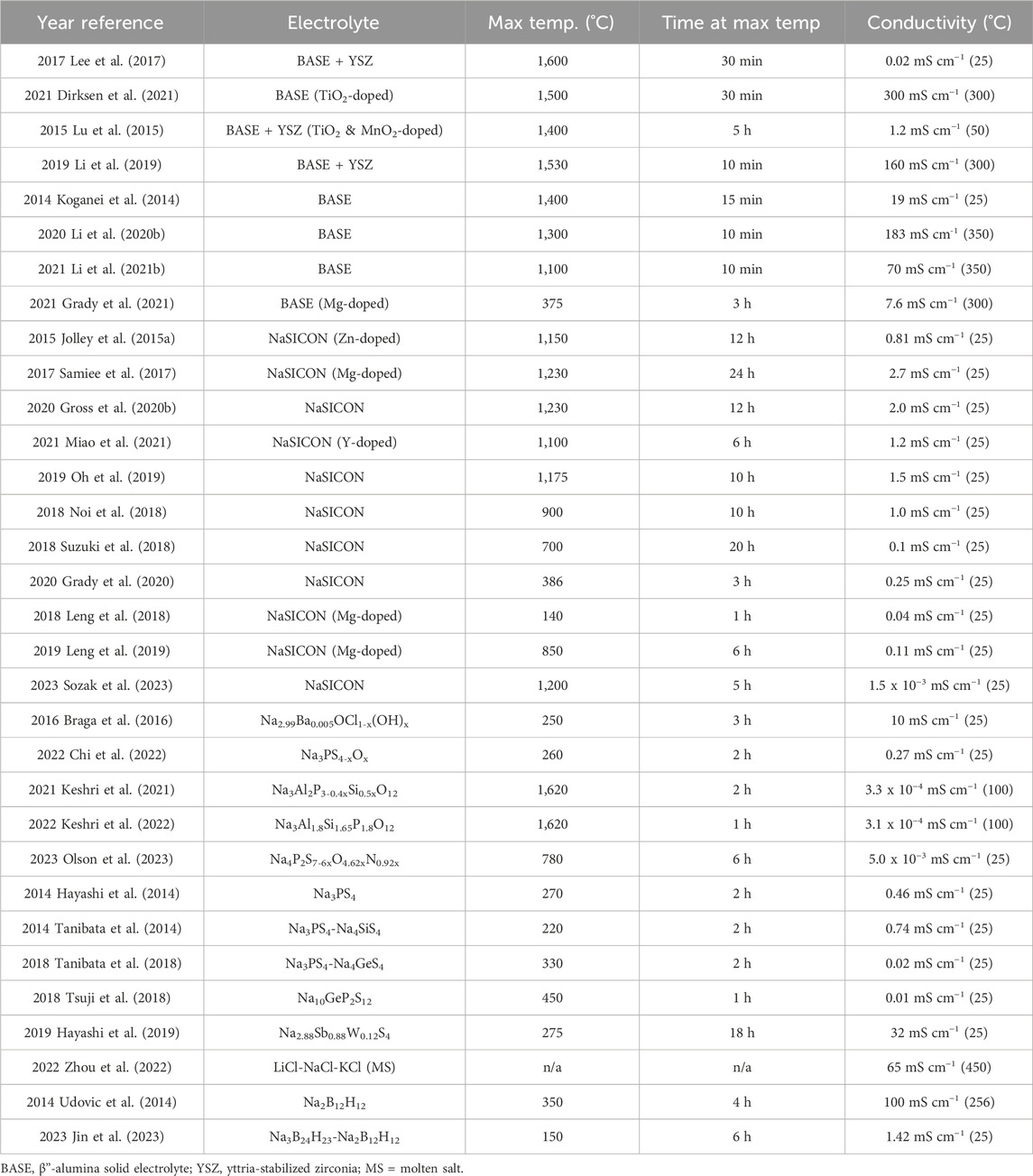
TABLE 3. Summary of electrolyte compositions, synthesis conditions, and resultant conductivities. For the “Max Temp.” columns, the maximum temperature during synthesis and the hold time necessary are listed. For conductivity, the lowest temperature that was reported in the original publication is listed here.
3.3 Na|Electrolyte interfaces
3.3.1 Mode I and II failure in solid electrolytes
In addition to the chemical reduction or amorphization that may occur in sodium solid electrolytes, applying potential and passing current may introduce further failure mechanisms in solid electrolytes. Electrochemical breakdown of BASE was first reported by Armstrong et al., who observed sodium penetration (i.e., dendrites) through BASE in Na|BASE|Na symmetric cells above 100 mA cm−2 (Armstrong et al., 1974). The time to failure depended on both the current density (higher current → faster breakdown) and surface preparation (rougher surface → faster breakdown). The dependence on surface preparation suggested that surface flaws influenced dendrite formation. It was hypothesized that molten Na metal would preferentially wet and fill some surface pores and microcracks, depending on local geometry and surface chemistry. The features with good wetting (contact angle,
where ΔP is the Poiseuille pressure from the “flow” of metal (due to Na plating), η is the viscosity of molten Na metal, i is the applied current density, Vm is the molar volume of sodium, a is the crack length, n is the number of electrons in the reaction (1 for reduction of Na+), F is the Faraday constant, and b is the crack tip radius (Armstrong et al., 1974) If this pressure reached a critical value, related to the fracture stress of electrolyte. This pressure-driven mechanism was termed Mode I failure (Figures 8A–C). Various authors have reported improvements to Eq. 14 to describe crack shapes more accurately and have extended its use to estimate the “critical” current density, at which Mode I failure will occur (Richman and Tennenhouse, 1975; Brennan, 1980; De Jonghe et al., 1981; Feldman and De Jonghe, 1982; Viswanathan and Virkar, 1982; Virkar and Viswanathan, 1983) In addition to the early reports of sharp cracks from surface imperfections, Mode I failure has also been observed as Na-filled cracks that are influenced by grain boundaries (Figure 8B) as well as large, diffusive fronts that extend from the stripping interface (Figure 8C).
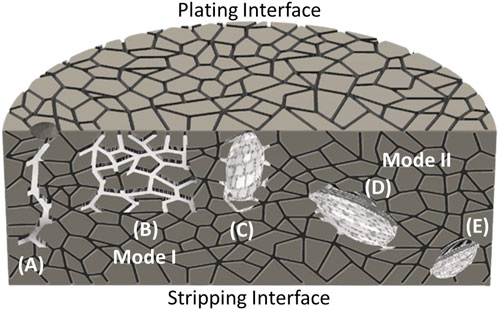
FIGURE 8. Illustration of Mode I and Mode II failure modes in solid electrolyte. Mode I has been observed as (A) large cracks stemming from surface imperfections, (B) grain boundaries filled with sodium, or (C) large, diffusive fronts that extend from the plating interface. Mode II has typically been observed as metal inclusions that stem from (D) the middle of the electrolyte interior or even (E) near the stripping interface.
Failure of Na solid electrolytes has also been observed at current densities considerably lower than those calculated to cause fracturing based on Eq. 14. De Jonghe et al. reported darkening in BASE used in Na-S cells during long duration testing (Jonghe et al., 1981). Reduction by Na metal increased BASE’s electronic conductivity and allowed electrons to recombine with mobile Na+ ions to form Na metal penetration during cycling. This electronic conductivity-driven failure has been termed Mode II failure (De Jonghe et al., 1981). In contrast to Mode I, Mode II failure points can occur near the plating interface (may be difficult to distinguish from Mode I), the stripping interface (Figure 8E), or anywhere within the interior of the electrolyte (Figure 8D). While Mode I was typically viewed as the predominant failure mechanism in molten Na cells, particularly at high current densities, recent works have emphasized the importance of Mode II. Hill et al. used unidirectional current tests to show that Mode I and Mode II sodium penetration occurred significantly in NaSICON electrolytes at 100 mA cm−2(110°C) (Hill et al., 2023). Subsequent ex-situ cross-sectional SEM imaging by the same group showed that Mode I could be mitigated at 500 mA cm−2 by using an interfacial coating, but Mode II was more difficult to suppress due to inherent electronic conductivity and microstructural features in NaSICON. The importance of Mode II has also been emphasized in electrolyte studies for solid-state batteries and its influence in molten Na batteries should be further explored (Han et al., 2019; Gorai et al., 2021; Wang et al., 2022; Shao et al., 2023). Detailed electrolyte studies utilizing unidirectional testing, conductivity vs. temperature series, and operando imaging would be beneficial to further understanding these important failure mechanisms (Fuchs et al., 2023; Counihan et al., 2024).
3.3.2 Interfacial coatings for solid electrolytes
One popular and effective strategy to mitigate solid electrolyte failure has been introducing interfacial coatings to facilitate uniform charge transfer between electrode and electrolyte. Better charge transfer could be due to enhanced wetting of liquid electrodes, improved interfacial contact for solid electrodes, or preventing the formation of less-conductive surface species at electrode-electrolyte interfaces (such as calcium-based impurities from BASE) (Lu et al., 2010b; Cheng et al., 2019; Cui et al., 2022; Gao et al., 2022). Particularly, a coating for the electrolyte|negative electrode (alkali metal) interface has been prioritized as it has been identified as the most susceptible to failure. Various authors have proposed coatings that typically relied on a porous carbon layer, a thin metal layer, or a combination of both (Hu et al., 2012; Ahlbrecht et al., 2017; Jin et al., 2019a; Gross et al., 2020b; Landmann et al., 2020). Generally, these coatings provide better wetting (smaller contact angle,
Carbon-based coatings have been shown to significantly improve the performance of Na solid electrolytes and are commonly used in traditional ZEBRA batteries (Sudworth, 2001). Porous carbon can improve the contact angle between Na metal and the electrolyte and serve as a reservoir of Na metal during high-current operation. Hu et al. fabricated a porous carbon coating of ∼6.6
Metal and metal oxide coatings are another potentially effective approach to improving solid electrolyte performance. Recent reports from Hu et al. highlighted Ni nanowires (2013) and iron oxide (2014) as excellent coatings, enabling current densities up to 1.5 and 3.9 A cm−2, respectively. The group proposed that the high current densities resulted from higher surface energy metals providing better inherent wetting and more surface area for wetting (Hu et al., 2013; Hu et al., 2014). However, this review was not able to identify any further works utilizing Ni- or Fe-based coatings for molten Na batteries. The lack of further Ni- and Fe-based coating reports seems to be, at least partially, due to the recognition of chemical reactivity as an influential factor in coating performance. Metals that are known to react with Na, such as Pb, Sn, Bi, and In, have been identified as potential interfacial coatings. In 2013, Reed et al. showed that sputtered Sn coatings enabled complete molten Na wetting (
Based on the success of carbon and metal-based coatings, it is logical that a composite carbon-metal coating could provide better overall performance based on benefits from each of the components. Composite coatings of Pb or Sn nanoparticles in a porous carbon black matrix were fabricated by Li et al. and both coatings showed fast sodium wetting and wicking at 120°C. The enhanced wetting at lower temperatures was attributed to the higher surface area contributed by the carbon black along with the alloying behavior of the Pb or Sn particles. (Li et al., 2022). Weller et al. later applied the same coating to BASE and NaSICON for use in Na-Al batteries. (Weller et al., 2023). Further studies into molten sodium behavior with composite carbon-metal coatings were not found in this review, but another three-dimensional cross-linking carbon fiber decorated with Sn nanoparticles has been used to improve current density in RT
The general coating approaches applied by researchers are illustrated in Figure 9. A summary of coated electrolyte systems and the maximum current density reported with them is also provided in Table 4. It is important to note that many of these studies did not explicitly search for a maximum current density and the coatings in these studies provide other potential benefits, such as improved wettability and cycle life, as discussed in the text.
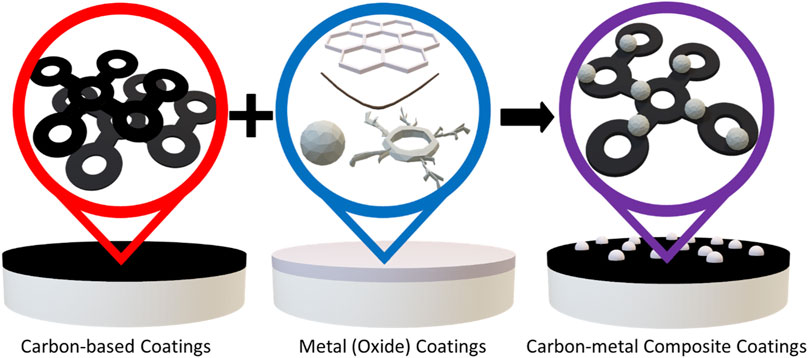
FIGURE 9. Illustration of general coating approaches used for molten Na|solid electrolyte interfaces. Various studies have reported using carbon-based coatings, metal (oxide) coatings, and composite carbon-metal coatings.
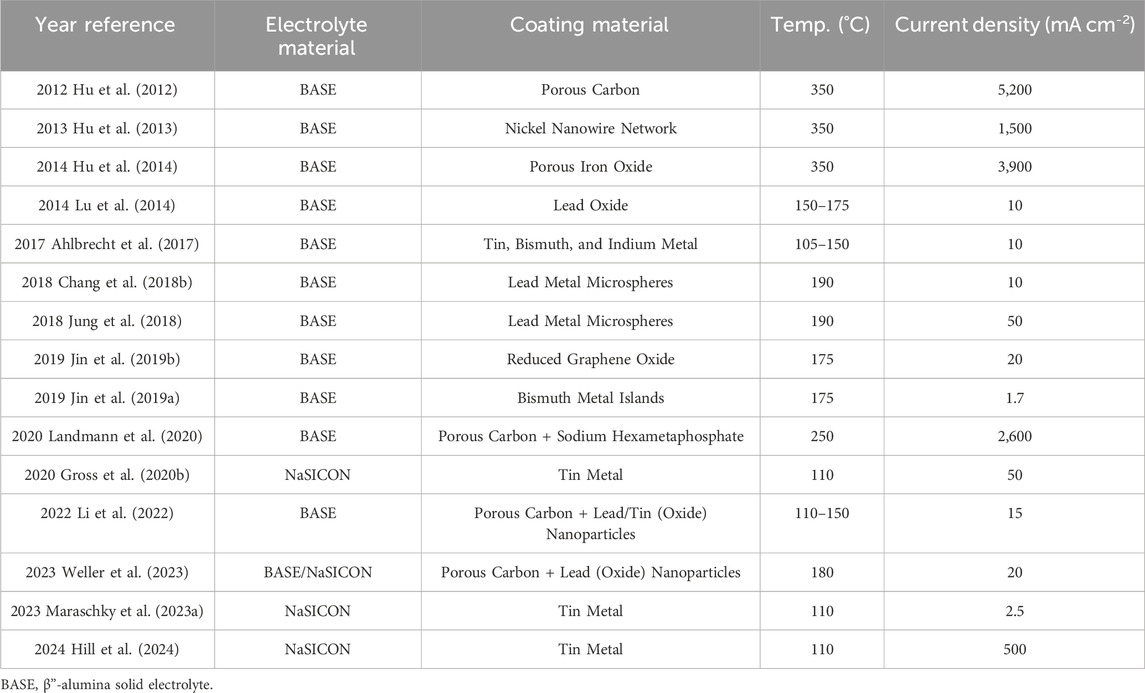
TABLE 4. Summary of interfacial coatings and their maximum current density at the given temperature in recent molten Na battery reports.
4 Summary and outlook
Molten Na batteries are promising stationary and grid-scale energy storage technologies with a long history of development and a recent acceleration of renewed innovation. The natural abundance of many of the elements used in molten Na batteries make them particularly attractive for grid-scale, long-duration energy storage and will help to realize a clean, reliable, and resilient electrical grid. Various technologies, including Na-S and ZEBRA-style batteries, are already contributing to stationary storage solutions and many more technologies are on the horizon. Lower temperature chemistries have the potential to operate below 120°C and further reduce costs for grid-scale storage. Na-alloy negative electrodes could push operating temperatures even closer to room temperature. Emerging molten Na flow batteries can design unique cell stacks that decouple energy and power density to meet the diverse demands of the electrical grid. To enable these new batteries, many advancements have been made in solid electrolyte chemistries, manufacturing, and interface regulation. Lower-temperature sintering and thin electrolyte fabrication l ower costs, while aliovalent doping and interfacial coatings create high-conductivity, dendrite-resistant electrolytes. As researchers continue to make breakthroughs in electrodes, electrolytes, and, critically, the interfaces between them, molten Na batteries will become a staple of the electrical grid of the future.
Author contributions
RH: Visualization, Writing–original draft, Writing–review and editing. MG: Visualization, Writing–review and editing. SP: Writing–review and editing. AP: Writing–review and editing. LS: Writing–review and editing. ES: Writing–review and editing. Y-TC: Writing–review and editing.
Funding
The author(s) declare that no financial support was received for the research, authorship, and/or publication of this article.
Acknowledgments
The authors would like to acknowledge the support of the Energy Storage Program, managed by Der. Imre Gyuk, in the U.S. Department of Energy’s Office of Electricity. Sandia National Laboratories is a multi-mission laboratory managed and operated by National Technology & Engineering Solutions of Sandia, LLC (NTESS), a wholly owned subsidiary of Honeywell International Inc., for the U.S. Department of Energy’s National Nuclear Security Administration (DOE/NNSA) under contract DE-NA0003525. This written work is authored by an employee of NTESS. The employee, not NTESS, owns the right, title and interest in and to the written work and is responsible for its contents. The publisher acknowledges that the U.S. Government retains a non-exclusive, paid-up, irrevocable, world-wide license to publish or reproduce the published form of this written work or allow others to do so, for U.S. Government purposes. The DOE will provide public access to results of federally sponsored research in accordance with the DOE Public Access Plan.
Conflict of interest
The authors declare that the research was conducted in the absence of any commercial or financial relationships that could be construed as a potential conflict of interest.
The author(s) declared that they were an editorial board member of Frontiers, at the time of submission. This had no impact on the peer review process and the final decision.
Publisher’s note
All claims expressed in this article are solely those of the authors and do not necessarily represent those of their affiliated organizations, or those of the publisher, the editors and the reviewers. Any product that may be evaluated in this article, or claim that may be made by its manufacturer, is not guaranteed or endorsed by the publisher.
Author disclaimer
Any subjective views or opinions that might be expressed in the written work do not necessarily represent the views of the U.S. Government.
References
Ackermann, T., and Söder, L. (2000). Wind energy technology and current status: a review. Renew. Sustain. Energy Rev. 4 (4), 315–374. doi:10.1016/S1364-0321(00)00004-6
Ahlbrecht, K., Bucharsky, C., Holzapfel, M., Tübke, J., and Hoffmann, M. J. (2017). Investigation of the wetting behavior of Na and Na alloys on uncoated and coated Na-β-alumina at temperatures below 150 °C. Ionics 23 (5), 1319–1327. doi:10.1007/s11581-017-2017-x
Ahn, B.-M., Ahn, C.-W., Hahn, B.-D., Choi, J.-J., Kim, Y.-D., Lim, S.-K., et al. (2019). Easy approach to realize low cost and high cell capacity in sodium nickel-iron chloride battery. Compos. Part B Eng. 168, 442–447. doi:10.1016/j.compositesb.2019.03.064
Albertus, P., Manser, J. S., and Litzelman, S. (2020). Long-duration electricity storage applications, economics, and technologies. Joule 4 (1), 21–32. doi:10.1016/j.joule.2019.11.009
Allu, A. R., Balaji, S., and Annapurna, K. (2018). Electrical and mechanical properties of Na2.8Ca0.1Al2Ga0.5P2.7O12 glass based electrolyte materials: influence of Ag+ ion-exchange. J. Non-Crystalline Solids 498, 323–330. doi:10.1016/j.jnoncrysol.2018.03.043
Almond, D. P., West, A. R., and Grant, R. J. (1982). Temperature dependence of the a.c. conductivity of Naβ-alumina. Solid State Commun. 44, 1277–1280. doi:10.1016/0038-1098(82)91103-6
Andres, R. J., Boden, T. A., Bréon, F. M., Ciais, P., Davis, S., Erickson, D., et al. (2012). A synthesis of carbon dioxide emissions from fossil-fuel combustion. Biogeosciences 9 (5), 1845–1871. doi:10.5194/bg-9-1845-2012
Anvari, M., Lohmann, G., Wächter, M., Milan, P., Lorenz, E., Heinemann, D., et al. (2016). Short term fluctuations of wind and solar power systems. New J. Phys. 18 (6), 063027. doi:10.1088/1367-2630/18/6/063027
Ao, X., Wen, Z., Hu, Y., Wu, T., Wu, X., and He, Q. (2017a). Enhanced cycle performance of a Na/NiCl2 battery based on Ni particles encapsulated with Ni3S2 layer. J. Power Sources 340, 411–418. doi:10.1016/j.jpowsour.2016.11.091
Ao, X., Wen, Z., Wu, X., Wu, T., and Wu, M. (2017b). Self-repairing function of Ni3S2 layer on Ni particles in the Na/NiCl2 cells with the addition of sulfur in the catholyte. ACS Appl. Mat. Interfaces 9 (25), 21234–21242. doi:10.1021/acsami.7b03873
Archer, D., Eby, M., Brovkin, V., Ridgwell, A., Cao, L., Mikolajewicz, U., et al. (2009). Atmospheric lifetime of fossil fuel carbon dioxide. Annu. Rev. Earth Planet. Sci. 37 (1), 117–134. doi:10.1146/annurev.earth.031208.100206
Armstrong, R. D., Dickinson, T., and Turner, J. (1974). The breakdown of β-alumina ceramic electrolyte. Electrochimica Acta 19 (5), 187–192. doi:10.1016/0013-4686(74)85065-6
Arnold, B. J. (2023). “1 - coal formation,” in The coal handbook Editor D Osborne. Second Edition (Sawston, United Kingdom: Woodhead Publishing), 3–21.
Balat, M. A. (2009). A review of modern wind turbine technology. Energy Sources, Part A Recovery, Util. Environ. Eff. 31 (17), 1561–1572. doi:10.1080/15567030802094045
Barison, S., Fasolin, S., Mortalò, C., Boldrini, S., and Fabrizio, M. (2015). Effect of precursors on β-alumina electrolyte preparation. J. Eur. Ceram. Soc. 35 (7), 2099–2107. doi:10.1016/j.jeurceramsoc.2015.01.006
Bates, J. B., Engstrom, H., Wang, J. C., Larson, B. C., Dudney, N. J., and Brundage, W. E. (1981). Composition, ion-ion correlations and conductivity of beta″-alumina. Solid State Ionics 5, 159–162. doi:10.1016/0167-2738(81)90217-4
Bay, M.-C., Wang, M., Grissa, R., Heinz, M. V. F., Sakamoto, J., and Battaglia, C. (2020). Sodium plating from Na-β″-Alumina ceramics at room temperature, paving the way for fast-charging all-solid-state batteries. Adv. Energy Mater. 10 (3), 1902899. doi:10.1002/aenm.201902899
Beevers, C., and Ross, Μ. A. S. (1937). The crystal structure of “beta alumina” Na2O·11Al2O3. Z. für Kristallogr. Mater. 97 (1-6), 59–66. doi:10.1524/zkri.1937.97.1.59
Bell, N. S., Edney, C., Wheeler, J. S., Ingersoll, D., and Spoerke, E. D. (2014). The influences of excess sodium on low-temperature NaSICON synthesis. J. Am. Ceram. Soc. 97 (12), 3744–3748. doi:10.1111/jace.13167
Bhandari, R., Kumar, B., and Mayer, F. (2020). Life cycle greenhouse gas emission from wind farms in reference to turbine sizes and capacity factors. J. Clean. Prod. 277, 123385. doi:10.1016/j.jclepro.2020.123385
Bloom, I., Kucera, G., Bradley, J., Nelson, P., and Roche, M. (1986). Low-resistivity glass electrolytes for sodium-sulfur cells. USA: Argonne National Lab., IL.
Bock, J. A., Spoerke, E. D., Brown-Shaklee, H. J., and Small, L. J. (2023). Solution-assisted densification of NaSICON ceramics. U. S. U.S. Pat. no. 11/600 856.
Boilot, J. P., Collin, G., and Colomban, P. (1987). Crystal structure of the true nasicon: Na3Zr2Si2PO12. Mater. Res. Bull. 22 (5), 669–676. doi:10.1016/0025-5408(87)90116-4
Boilot, J. P., Collin, G., and Colomban, P. (1988). Relation structure-fast ion conduction in the NASICON solid solution. J. Solid State Chem. 73 (1), 160–171. doi:10.1016/0022-4596(88)90065-5
Bones, R. J., Teagle, D. A., Brooker, S. D., and Cullen, F. L. (1989). Development of a Ni, NiCl2 positive electrode for a liquid sodium (ZEBRA) battery cell. J. Electrochem. Soc. 136 (5), 1274–1277. doi:10.1149/1.2096905
Boschin, A., and Johansson, P. (2015). Characterization of NaX (X: TFSI, FSI)–PEO based solid polymer electrolytes for sodium batteries. Electrochimica Acta 175, 124–133. doi:10.1016/j.electacta.2015.03.228
Braga, M. H., Murchison, A. J., Ferreira, J. A., Singh, P., and Goodenough, J. B. (2016). Glass-amorphous alkali-ion solid electrolytes and their performance in symmetrical cells. Energy & Environ. Sci. 9 (3), 948–954. doi:10.1039/c5ee02924d
Brennan, M. P. J. (1980). The failure of beta-alumina electrolyte by a dendritic penetration mechanism. Electrochimica Acta 25, 621–627. doi:10.1016/0013-4686(80)87067-8
Burnham, A. K., and Braun, R. L. (1990). Development of a detailed model of petroleum formation, destruction, and expulsion from lacustrine and marine source rocks. Org. Geochem. 16 (1), 27–39. doi:10.1016/0146-6380(90)90023-S
Calero, I., Cañizares, C. A., Bhattacharya, K., and Baldick, R. (2022). Duck-curve mitigation in power grids with high penetration of PV generation. IEEE Trans. Smart Grid 13 (1), 314–329. doi:10.1109/TSG.2021.3122398
Certo, J., Furtado, C. S., Ferreira, A. J., and Perdigão, J. M. (1998). Na-β Alumina powder processing by a Na2CO3 precipitation method. Ionics 4 (1-2), 124–128. doi:10.1007/bf02375790
Chang, H.-J., Canfield, N. L., Jung, K., Sprenkle, V. L., and Li, G. (2017). Advanced Na-NiCl2 battery using nickel-coated graphite with core–shell microarchitecture. ACS Appl. Mat. Interfaces 9 (13), 11609–11614. doi:10.1021/acsami.7b00271
Chang, H. J., Lu, X., Bonnett, J. F., Canfield, N. L., Han, K., Engelhard, M. H., et al. (2018b). Decorating β′′-alumina solid-state electrolytes with micron Pb spherical particles for improving Na wettability at lower temperatures. J. Mat. Chem. A 6, 19703–19711. doi:10.1039/C8TA06745G
Chang, H. J., Lu, X., Bonnett, J. F., Canfield, N. L., Son, S., Park, Y. C., et al. (2018a). Ni-less cathodes for high energy density, intermediate temperature Na–NiCl2 batteries. Adv. Mater. Interfaces 5 (10), 1701592. doi:10.1002/admi.201701592
Chen, Y., Kang, Y., Zhao, Y., Wang, L., Liu, J., Li, Y., et al. (2021). A review of lithium-ion battery safety concerns: the issues, strategies, and testing standards. J. Energy Chem. 59, 83–99. doi:10.1016/j.jechem.2020.10.017
Cheng, Q., Li, A., Li, N., Li, S., Zangiabadi, A., Li, T. D., et al. (2019). Stabilizing solid electrolyte-anode interface in Li-metal batteries by boron nitride-based nanocomposite coating. Joule 3 (6), 1510–1522. doi:10.1016/j.joule.2019.03.022
Chi, C., Katsui, H., and Goto, T. (2017). Effect of Li addition on the formation of Na-β/βʹʹ-alumina film by laser chemical vapor deposition. Ceram. Int. 43 (1), 1278–1283. Part B). doi:10.1016/j.ceramint.2016.10.077
Chi, X., Zhang, Y., Hao, F., Kmiec, S., Dong, H., Xu, R., et al. (2022). An electrochemically stable homogeneous glassy electrolyte formed at room temperature for all-solid-state sodium batteries. Nat. Commun. 13 (1), 2854. doi:10.1038/s41467-022-30517-y
Choy, J.-H., Yoo, J.-S., Han, Y.-S., and Kim, Y.-H. (1993). Citrate sol-gel method for the preparation of β/β′'-alumina. Mater. Lett. 16 (4), 226–230. doi:10.1016/0167-577X(93)90169-X
Chu, I.-H., Kompella, C. S., Nguyen, H., Zhu, Z., Hy, S., Deng, Z., et al. (2016). Room-temperature all-solid-state rechargeable sodium-ion batteries with a Cl-doped Na3PS4 superionic conductor. Sci. Rep. 6 (1), 33733. doi:10.1038/srep33733
Coetzer, J. (1986). A new high energy density battery system. J. Power Sources 18 (4), 377–380. doi:10.1016/0378-7753(86)80093-3
Counihan, M. J., Chavan, K. S., Barai, P., Powers, D. J., Zhang, Y., Srinivasan, V., et al. (2024). The phantom menace of dynamic soft-shorts in solid-state battery research. Joule 8, 64–90. doi:10.1016/j.joule.2023.11.007
Cross, A. T., and Phillips, T. L. (1990). Coal-forming through time in north America. Int. J. Coal Geol. 16 (1), 1–46. doi:10.1016/0166-5162(90)90012-N
Crouthamel, C. E., and Recht, H. L. (1967). Regenerative EMF cells. Washington, D.C.: ACS Publications.
Cui, C., Zeng, C., Huang, G., Feng, X., Zhang, Y., Zhai, T., et al. (2022). In situ visualizing the interfacial failure mechanism and modification promotion of LAGP solid electrolyte toward Li metal anode. Adv. Energy Mater. 12 (41), 2202250. doi:10.1002/aenm.202202250
De Jonghe, L. C., Feldman, L., and Buechele, A. (1981). Failure modes of Na-beta alumina. Solid State Ionics 5, 267–269. doi:10.1016/0167-2738(81)90244-7
Dell, R., and Moseley, P. (1981). Beta-alumina electrolyte for use in sodium/sulphur batteries: Part I. Fundamental properties. J. Power Sources 6 (2), 143–160. doi:10.1016/0378-7753(81)80020-1
Denholm, P., Cole, W., and Blair, N. (2023). Moving beyond 4-hour Li-ion batteries: challenges and opportunities for long (er)-Duration energy storage. United States: NREL is a national laboratory of the U.S. Department of Energy.
Denholm, P., Nunemaker, J., Gagnon, P., and Cole, W. (2020). The potential for battery energy storage to provide peaking capacity in the United States. Renew. Energy 151, 1269–1277. doi:10.1016/j.renene.2019.11.117
Ding, W., Gong, Q., Liang, S., Hoffmann, R., Zhou, H., Li, H., et al. (2023). Multi-cationic molten salt electrolyte of high-performance sodium liquid metal battery for grid storage. J. Power Sources 553, 232254. doi:10.1016/j.jpowsour.2022.232254
Ding, Y., Guo, X., Qian, Y., Xue, L., Dolocan, A., and Yu, G. (2020a). Room-temperature all-liquid-metal batteries based on fusible alloys with regulated interfacial chemistry and wetting. Adv. Mater. 32 (30), 2002577. doi:10.1002/adma.202002577
Ding, Y., Guo, X., Qian, Y., and Yu, G. (2020b). Low-temperature multielement fusible alloy-based molten sodium batteries for grid-scale energy storage. ACS Cent. Sci. 6 (12), 2287–2293. doi:10.1021/acscentsci.0c01035
Dirksen, C. L., Skadell, K., Schulz, M., Fertig, M. P., and Stelter, M. (2021). Influence of 3d transition metal doping on lithium stabilized Na-β″-Alumina solid electrolytes. Materials 14 (18), 5389. doi:10.3390/ma14185389
Dustmann, C.-H. (2004). Advances in ZEBRA batteries. J. Power Sources 127 (1), 85–92. doi:10.1016/j.jpowsour.2003.09.039
Ediger, V. Ş. (2019). An integrated review and analysis of multi-energy transition from fossil fuels to renewables. Energy Procedia 156, 2–6. doi:10.1016/j.egypro.2018.11.073
El Chaar, L., lamont, L. A., and El Zein, N. (2011). Review of photovoltaic technologies. Renew. Sustain. Energy Rev. 15 (5), 2165–2175. doi:10.1016/j.rser.2011.01.004
Engstrom, H., Bates, J., Brundage, W., and Wang, J. (1981). Ionic conductivity of sodium beta ″-alumina. Solid State Ionics 2 (4), 265–276. doi:10.1016/0167-2738(81)90027-8
Enlighten (2023). Enlighten. https://enlighteninc.com/ (Accessed December 30, 2023).
Feldman, L. A., and De Jonghe, L. C. (1982). Initiation of mode I degradation in sodium-beta alumina electrolytes. J. Mat. Sci. 17, 517–524. doi:10.1007/BF00591486
Fertig, M. P., Skadell, K., Schulz, M., Dirksen, C., Adelhelm, P., and Stelter, M. (2022). From high-to low-temperature: the revival of sodium-beta alumina for sodium solid-state batteries. Batter. Supercaps 5, e202100131. doi:10.1002/BATT.202100131
Fertig, M. P., Skadell, K., Wegner, K., Schulz, M., and Stelter, M. (2023). A medium-temperature all-solid-state sodium battery utilizing sodium-beta alumina and a polymeric composite positive electrode. J. Electrochem. Soc. 170 (5), 050501. doi:10.1149/1945-7111/accf39
Flynn, A., Taggert, D., Johnston, J., Christensen, M., Makowski, M., Moss, R., et al. (2022). “Novel sodium – polysulfide flow battery grid-scale energy storage technology,” in 2022 IEEE Electrical Energy Storage Application and Technologies Conference, Austin, Texas, USA, 8-9 Nov. 2022, 1–3. doi:10.1109/EESAT55007.2022.9998026
Frusteri, L., Leonardi, S. G., Samperi, M., Antonucci, V., and D'Urso, C. (2022). Characterization and testing of cathode materials for high temperature sodium nickel-iron chloride battery. J. Energy Storage 55, 105503. doi:10.1016/j.est.2022.105503
Fuchs, T., Culver, S. P., Till, P., and Zeier, W. G. (2020). Defect-mediated conductivity enhancements in Na3–xPn1–xWxS4 (pn = P, Sb) using aliovalent substitutions. ACS Energy Lett. 5 (1), 146–151. doi:10.1021/acsenergylett.9b02537
Fuchs, T., Haslam, C. G., Richter, F. H., Sakamoto, J., and Janek, J. (2023). Evaluating the use of critical current density tests of symmetric lithium transference cells with solid electrolytes. Adv. Energy Mater. 13 (45), 2302383. doi:10.1002/aenm.202302383
Fuentes, R. O., Figueiredo, F. M., Marques, F. M. B., and Franco, J. I. (2001). Influence of microstructure on the electrical properties of NASICON materials. Solid State Ionics 140 (1), 173–179. doi:10.1016/S0167-2738(01)00701-9
Fzsonick (2023a). Green & safe salt battery. https://www.fzsonick.com/home (Accessed December 30, 2023).
Fzsonick (2023b). Industrial energy storage. https://www.fzsonick.com/applications/industrial-energy-storage (Accessed December 30, 2023).
Gandi, S., Chinta, S. R., Ojha, P. K., Surendra Babu, M. S., and Ravuri, B. R. (2018). High Na-ion conducting Na1+ x[SnxGe2− x(PO4)3] glass-ceramic electrolytes: structural and electrochemical impedance studies. J. Am. Ceram. Soc. 101 (1), 167–177. doi:10.1111/jace.15103
Gao, L., Chen, J., Chen, Q., and Kong, X. (2022). The chemical evolution of solid electrolyte interface in sodium metal batteries. Sci. Adv. 8 (6), eabm4606. doi:10.1126/sciadv.abm4606
Gao, X., Hu, Y., Li, Y., Wang, J., Wu, X., Yang, J., et al. (2020). High-rate and long-life intermediate-temperature Na–NiCl2 battery with dual-functional Ni–carbon composite nanofiber network. ACS Appl. Mat. Interfaces 12 (22), 24767–24776. doi:10.1021/acsami.0c04470
Gardner, P., Jones, F., Rowe, M., Nouri, A., and van de Vegte, H. (2016). E-storage: shifting from cost to value Wind and solar applications. London, United Kingdom: World Energy Council.
Gerbig, F., Holzapfel, M., and Nirschl, H. (2023). Simulating the impact of glassy carbon foam electrodes on the performance of sodium iodine batteries. J. Electrochem. Soc. 170 (4), 040517. doi:10.1149/1945-7111/accab7
Gerovasili, E., May, J. F., and Sauer, D. U. (2014). Experimental evaluation of the performance of the sodium metal chloride battery below usual operating temperatures. J. Power Sources 251, 137–144. doi:10.1016/j.jpowsour.2013.11.046
Gong, Q., Ding, W., Bonk, A., Li, H., Wang, K., Jianu, A., et al. (2020). Molten iodide salt electrolyte for low-temperature low-cost sodium-based liquid metal battery. J. Power Sources 475, 228674. doi:10.1016/j.jpowsour.2020.228674
Gong, Z., Shu, L., Yin, J., Gao, C., Liu, Y., Zhou, X., et al. (2023). Double-substituted Na3SbS4 Glass–Ceramic electrolyte with excellent performance for sodium-ion batteries. Ceram. Int. 49 (23), 37445–37453. doi:10.1016/j.ceramint.2023.09.070
Goodenough, J. B., Hong, H. Y. P., and Kafalas, J. A. (1976). Fast Na+-ion transport in skeleton structures. Mater. Res. Bull. 11, 203–220. doi:10.1016/0025-5408(76)90077-5
Gorai, P., Famprikis, T., Singh, B., Stevanović, V., and Canepa, P. (2021). Devil is in the defects: electronic conductivity in solid electrolytes. Chem. Mat. 33 (18), 7484–7498. doi:10.1021/acs.chemmater.1c02345
Grady, Z., Ndayishimiye, A., and Randall, C. (2021). A dramatic reduction in the sintering temperature of the refractory sodium β′′-alumina solid electrolyte via cold sintering. J. Mat. Chem. A 9 (38), 22002–22014. doi:10.1039/d1ta05933e
Grady, Z. M., Tsuji, K., Ndayishimiye, A., Hwan-Seo, J., and Randall, C. A. (2020). Densification of a solid-state NASICON sodium-ion electrolyte below 400 °C by cold sintering with a fused hydroxide solvent. ACS Appl. Energy Mater. 3 (5), 4356–4366. doi:10.1021/acsaem.0c00047
Gross, M. M., and Manthiram, A. (2019). Development of low-cost sodium-aqueous polysulfide hybrid batteries. Energy Storage Mater. 19, 346–351. doi:10.1016/j.ensm.2019.03.026
Gross, M. M., Percival, S. J., Lee, R. Y., Peretti, A. S., Spoerke, E. D., and Small, L. J. (2021). A high-voltage, low-temperature molten sodium battery enabled by metal halide catholyte chemistry. Cell Rep. Phys. Sci. 2 (7), 100489. ARTN 100489. doi:10.1016/j.xcrp.2021.100489
Gross, M. M., Percival, S. J., Small, L. J., Lamb, J., Peretti, A. S., and Spoerke, E. D. (2020a). Low-temperature molten sodium batteries. ACS Appl. Energy Mater. 3 (11), 11456–11462. doi:10.1021/acsaem.0c02385
Gross, M. M., Small, L. J., Peretti, A. S., Percival, S. J., Rodriguez, M. A., and Spoerke, E. D. (2020b). Tin-based ionic chaperone phases to improve low temperature molten sodium-NaSICON interfaces. J. Mat. Chem. A 8, 17012–17018. doi:10.1039/d0ta03571h
Guerra, O. J. (2021). Beyond short-duration energy storage. Nat. Energy 6 (5), 460–461. doi:10.1038/s41560-021-00837-2
Guin, M., and Tietz, F. (2015). Survey of the transport properties of sodium superionic conductor materials for use in sodium batteries. J. Power Sources 273, 1056–1064. doi:10.1016/j.jpowsour.2014.09.137
Han, F., Westover, A. S., Yue, J., Fan, X., Wang, F., Chi, M., et al. (2019). High electronic conductivity as the origin of lithium dendrite formation within solid electrolytes. Nat. Energy 4, 187–196. doi:10.1038/s41560-018-0312-z
Hayashi, A., Masuzawa, N., Yubuchi, S., Tsuji, F., Hotehama, C., Sakuda, A., et al. (2019). A sodium-ion sulfide solid electrolyte with unprecedented conductivity at room temperature. Nat. Commun. 10 (1), 5266. doi:10.1038/s41467-019-13178-2
Hayashi, A., Noi, K., Sakuda, A., and Tatsumisago, M. (2012). Superionic glass-ceramic electrolytes for room-temperature rechargeable sodium batteries. Nat. Commun. 3 (1), 856. doi:10.1038/ncomms1843
Hayashi, A., Noi, K., Tanibata, N., Nagao, M., and Tatsumisago, M. (2014). High sodium ion conductivity of glass–ceramic electrolytes with cubic Na3PS4. J. Power Sources 258, 420–423. doi:10.1016/j.jpowsour.2014.02.054
Heinz, M. V. F., Sieuw, L., Lan, T., Turconi, A., Basso, D., Vagliani, F., et al. (2023). Cell design strategies for sodium-zinc chloride (Na-ZnCl2) batteries, and first demonstration of tubular cells with 38 Ah capacity. Electrochimica Acta 464, 142881. doi:10.1016/j.electacta.2023.142881
Helbig, C., Bradshaw, A. M., Wietschel, L., Thorenz, A., and Tuma, A. (2018a). Supply risks associated with lithium-ion battery materials. J. Clean. Prod. 172, 274–286. doi:10.1016/j.jclepro.2017.10.122
Helbig, C., Bradshaw, A. M., Wietschel, L., Thorenz, A., and Tuma, A. (2018b). Supply risks associated with lithium-ion battery materials. J. Clean. Prod. 172, 274–286. doi:10.1016/j.jclepro.2017.10.122
Herczog, A. (1985). Sodium ion conducting glasses for the sodium-sulfur battery. J. Electrochem. Soc. 132 (7), 1539–1545. doi:10.1149/1.2114161
Hibi, Y., Tanibata, N., Hayashi, A., and Tatsumisago, M. (2015). Preparation of sodium ion conducting Na3PS4-NaI glasses by a mechanochemical technique. Solid State Ionics 270, 6–9. Article. doi:10.1016/j.ssi.2014.11.024
Hill, R., Peretti, A., Small, L. J., Spoerke, E. D., and Cheng, Y.-T. (2023). Molten sodium penetration in NaSICON electrolytes at 0.1 A cm–2. ACS Appl. Energy Mater. 6 (4), 2515–2523. doi:10.1021/acsaem.2c03944
Hill, R. C., Peretti, A. S., Maraschky, A. M., Small, L. J., Spoerke, E. D., and Cheng, Y.-T. (2024). Can a coating mitigate molten Na dendrite growth in NaSICON under high current density? ACS Appl. Energy Mater. 7, 810–819. doi:10.1021/acsaem.3c02994
Holzapfel, M., Wilde, D., Hupbauer, C., Ahlbrecht, K., and Berger, T. (2017). Medium-temperature molten sodium batteries with aqueous bromine and iodine cathodes. Electrochimica Acta 237, 12–21. doi:10.1016/j.electacta.2017.03.152
Hu, Y., Wen, Z., and Wu, X. (2014). Porous iron oxide coating on β″-alumina ceramics for Na-based batteries. Solid State Ionics 262, 133–137. doi:10.1016/j.ssi.2013.08.033
Hu, Y., Wen, Z., Wu, X., and Jin, J. (2012). Low-cost shape-control synthesis of porous carbon film on β″-alumina ceramics for Na-based battery application. J. Power Sources 219, 1–8. doi:10.1016/j.jpowsour.2012.07.025
Hu, Y., Wen, Z., Wu, X., and Lu, Y. (2013). Nickel nanowire network coating to alleviate interfacial polarization for Na-beta battery applications. J. Power Sources 240, 786–795. doi:10.1016/j.jpowsour.2013.04.056
Islam, M. A., Hasanuzzaman, M., Rahim, N. A., Nahar, A., and Hosenuzzaman, M. (2014). Global renewable energy-based electricity generation and smart grid system for energy security. Sci. World J. 2014, 1–13. doi:10.1155/2014/197136
Jebaselvi, G. A., and Paramasivam, S. (2013). Analysis on renewable energy systems. Renew. Sustain. Energy Rev. 28, 625–634. doi:10.1016/j.rser.2013.07.033
Jin, D., Choi, S., Jang, W., Soon, A., Kim, J., Moon, H., et al. (2019a). Bismuth islands for low-temperature sodium-beta alumina batteries. ACS Appl. Mat. Interfaces 11 (3), 2917–2924. doi:10.1021/acsami.8b13954
Jin, D., Lee, H. G., Choi, S., Kim, S., Lee, Y., Son, S., et al. (2019b). Sparked reduced graphene oxide for low-temperature sodium-beta alumina batteries. Nano Lett. 19 (12), 8811–8820. doi:10.1021/acs.nanolett.9b03646
Jin, M., Cheng, S., Yang, Z., Luo, Y., and Guo, Y. (2023). A novel high-voltage solid electrolyte of Na3B24H23 for 4 V all-solid-state sodium battery. Chem. Eng. J. 455, 140904. doi:10.1016/j.cej.2022.140904
Jolley, A. G., Cohn, G., Hitz, G. T., and Wachsman, E. D. (2015a). Improving the ionic conductivity of NASICON through aliovalent cation substitution of Na3Zr2Si2PO12. Ionics 21 (11), 3031–3038. doi:10.1007/s11581-015-1498-8
Jolley, A. G., Taylor, D. D., Schreiber, N. J., and Wachsman, E. D. (2015b). Structural investigation of monoclinic-rhombohedral phase transition in Na3Zr2Si2PO12 and doped NaSICON. J. Am. Ceram. Soc. 98 (9), 2902–2907. doi:10.1111/jace.13692
Jonghe, L. C., Feldman, L., and Beuchele, A. (1981). Slow degradation and electron conduction in sodium/beta-aluminas. J. Mat. Sci. 16, 780–786. doi:10.1007/BF00552217
Jørgensen, M., Shea, P. T., Tomich, A. W., Varley, J. B., Bercx, M., Lovera, S., et al. (2020). Understanding superionic conductivity in lithium and sodium salts of weakly coordinating closo-hexahalocarbaborate anions. Chem. Mat. 32 (4), 1475–1487. doi:10.1021/acs.chemmater.9b04383
Jung, K., Chang, H.-J., Bonnett, J. F., Canfield, N. L., Sprenkle, V. L., and Li, G. (2018). An advanced Na-NiCl2 battery using bi-layer (dense/micro-porous) β″-alumina solid-state electrolytes. J. Power Sources 396, 297–303. doi:10.1016/j.jpowsour.2018.06.039
Karabelli, D., Singh, S., Kiemel, S., Koller, J., Konarov, A., Stubhan, F., et al. (2020). Sodium-based batteries: in search of the best compromise between sustainability and maximization of electric performance. Front. Energy Res. 8. Review. doi:10.3389/fenrg.2020.605129
Kebede, A. A., Coosemans, T., Messagie, M., Jemal, T., Behabtu, H. A., Van Mierlo, J., et al. (2021). Techno-economic analysis of lithium-ion and lead-acid batteries in stationary energy storage application. J. Energy Storage 40, 102748. doi:10.1016/j.est.2021.102748
Keshri, S. R., Bodewad, V. V., Jagtap, A. A., Nasani, N., Balaji, S., Annapurna, K., et al. (2020). Influence of NaF on the ionic conductivity of sodium aluminophosphate glass electrolytes. Mater. Lett. 271, 127763. doi:10.1016/j.matlet.2020.127763
Keshri, S. R., Ganisetti, S., Kumar, R., Gaddam, A., Illath, K., Ajithkumar, T. G., et al. (2021). Ionic conductivity of Na3Al2P3O12 glass electrolytes—role of charge compensators. Inorg. Chem. 60 (17), 12893–12905. doi:10.1021/acs.inorgchem.1c01280
Keshri, S. R., Mandal, I., Ganisetti, S., Kasimuthumaniyan, S., Kumar, R., Gaddam, A., et al. (2022). Elucidating the influence of structure and Ag+-Na+ ion-exchange on crack-resistance and ionic conductivity of Na3Al1.8Si1.65P1.8O12 glass electrolyte. Acta Mater. 227, 117745. doi:10.1016/j.actamat.2022.117745
Kim, H., Boysen, D. A., Newhouse, J. M., Spatocco, B. L., Chung, B., Burke, P. J., et al. (2013). Liquid metal batteries: past, present, and future. Chem. Rev. 113 (3), 2075–2099. doi:10.1021/cr300205k
Kim, H.-T., Kim, S.-I., Choi, H.-L., Park, W.-I., and Kim, C.-s. (2015b). Effect of Zn/NaCl ratios on the charge/discharge performance in Na-ZnCl2 battery. J. Korean Cryst. Growth Cryst. Technol. 25 (2), 74–79. doi:10.6111/jkcgct.2015.25.2.074
Kim, I., Park, J.-Y., Kim, C. H., Park, J.-W., Ahn, J.-P., Ahn, J.-H., et al. (2016). A room temperature Na/S battery using a β″ alumina solid electrolyte separator, tetraethylene glycol dimethyl ether electrolyte, and a S/C composite cathode. J. Power Sources 301, 332–337. doi:10.1016/j.jpowsour.2015.09.120
Kim, J., Jo, S. H., Bhavaraju, S., Eccleston, A., and Kang, S. O. (2015a). Low temperature performance of sodium–nickel chloride batteries with NaSICON solid electrolyte. J. Electroanal. Chem. 759, 201–206. doi:10.1016/j.jelechem.2015.11.022
Kim, K., Mundy, J., and Chen, W. (1979). Diffusion and ionic conductivity in sodium beta alumina. J. Phys. Chem. Solids 40 (10), 743–755. doi:10.1016/0022-3697(79)90157-4
Kim, M., Ahn, C.-W., Hahn, B.-D., Jung, K., Park, Y.-C., Cho, N.-u., et al. (2017). Effects of Ni particle morphology on cell performance of Na/NiCl2 battery. Metals Mater. Int. 23 (6), 1234–1240. doi:10.1007/s12540-017-7062-5
Kim, S. M., Lee, S. M., Jung, K., Park, Y. C., Cho, N. u., Choi, J. H., et al. (2015c). Influence of carbon coating on beta-alumina membrane for sodium–nickel chloride battery. Bull. Korean Chem. Soc. 36 (12), 2869–2874. doi:10.1002/bkcs.10584
Koduru, H. K., Iliev, M., Kondamareddy, K., Karashanova, D., Vlakhov, T., Zhao, X.-Z., et al. (2016). Investigations on Poly (ethylene oxide)(PEO)-blend based solid polymer electrolytes for sodium ion batteries. J. Phys. Conf. Ser. 764, 012006. doi:10.1088/1742-6596/764/1/012006
Koganei, K., Oyama, T., Inada, M., Enomoto, N., and Hayashi, K. (2014). C-axis oriented β ″-alumina ceramics with anisotropic ionic conductivity prepared by spark plasma sintering. Solid State Ionics 267, 22–26. doi:10.1016/j.ssi.2014.09.003
Kohler, H., and Schulz, H. (1985). NASICON solid electrolytes part I: the Na+-diffusion path and its relation to the structure. Mater. Res. Bull. 20 (12), 1461–1471. doi:10.1016/0025-5408(85)90164-3
Kohler, H., Schulz, H., and Melnikov, O. (1983). Composition and conduction mechanism of the NASICON structure X-ray diffraction study on two crystals at different temperatures. Mater. Res. Bull. 18 (9), 1143–1152. doi:10.1016/0025-5408(83)90158-7
Kosowatz, J. (2018). Energy storage smooths the duck curve. Mech. Eng. 140 (06), 30–35. doi:10.1115/1.2018-JUN-1
Kreps, B. H. (2020). The rising costs of fossil-fuel extraction: an energy crisis that will not go away. Am. J. Econ. Sociol. 79 (3), 695–717. doi:10.1111/ajes.12336
Kreuer, K. D., and Warhus, U. (1986). NASICON solid electrolytes: Part IV Chemical durability. Mater. Res. Bull. 21 (3), 357–363. doi:10.1016/0025-5408(86)90193-5
Kumar, S., Ding, W., Hoffmann, R., Sieuw, L., Heinz, M. V., Weber, N., et al. (2023). AlCl3-NaCl-ZnCl2 secondary electrolyte in next-generation ZEBRA (Na-ZnCl2) battery. Batteries 9 (8), 401. doi:10.3390/batteries9080401
Kummer, J. T. (1972). β-Alumina electrolytes. Prog. Solid State Chem. 7, 141–175. doi:10.1016/0079-6786(72)90007-6
Kummer, J. T., and Weber, N. (1968). A sodium-sulfur secondary battery. Sae Trans., 1003–1028. doi:10.4271/670179
Kweon, K. E., Varley, J. B., Shea, P., Adelstein, N., Mehta, P., Heo, T. W., et al. (2017). Structural, chemical, and dynamical frustration: origins of superionic conductivity in closo-borate solid electrolytes. Chem. Mat. 29 (21), 9142–9153. doi:10.1021/acs.chemmater.7b02902
Lai, H., Wang, J., Cai, M., Song, Z., Gao, X., Wu, X., et al. (2022). Double-functional 3D cross-linking carbon fiber with Sn particle coating layer for improving interfacial performance of Na-β ″-Al2O3 batteries. Chem. Eng. J. 433, 133545. doi:10.1016/j.cej.2021.133545
Lan, T., Graeber, G., Sieuw, L., Svaluto-Ferro, E., Vagliani, F., Basso, D., et al. (2023). Planar sodium-nickel chloride batteries with high areal capacity for sustainable energy storage. Adv. Funct. Mater. 33 (33), 2302040. doi:10.1002/adfm.202302040
Landmann, D., Graeber, G., Heinz, M. V. F., Haussener, S., and Battaglia, C. (2020). Sodium plating and stripping from Na-β"-alumina ceramics beyond 1000 mA/cm2. Mater. Today Energy 18, 100515. doi:10.1016/J.MTENER.2020.100515
Lazar, M., Kmiec, S., Joyce, A., and Martin, S. W. (2020). Investigations into reactions between sodium metal and Na3PS4–xOx solid-state electrolytes: enhanced stability of the Na3PS3O solid-state electrolyte. ACS Appl. energy Mater. 3, 11559–11569. doi:10.1021/acsaem.0c00914
Lee, D.-H., Lee, S.-T., Kim, J.-S., and Lim, S.-K. (2017). Analysis of properties of partially stabilized zirconia-doped Na+-beta-alumina prepared by calcining-cum-sintering process. Mater. Res. Bull. 96, 143–148. doi:10.1016/j.materresbull.2017.05.003
Lee, R. Y., Percival, S. J., and Small, L. J. (2021). Electrochemical modeling of iodide oxidation in metal-halide molten salts. J. Electrochem. Soc. 168 (12), 126511. doi:10.1149/1945-7111/ac3e7a
Lee, Y., Kim, H.-J., Byun, D.-J., Cho, K.-K., Ahn, J.-H., and Kim, C.-S. (2019). Electrochemically activated Na–ZnCl2 battery using a carbon matrix in the cathode compartment. J. Power Sources 440, 227110. doi:10.1016/j.jpowsour.2019.227110
Leng, H., Huang, J., Nie, J., and Luo, J. (2018). Cold sintering and ionic conductivities of Na3.256Mg0.128Zr1.872Si2PO12 solid electrolytes. J. Power Sources 391, 170–179. doi:10.1016/j.jpowsour.2018.04.067
Leng, H. Y., Nie, J. Y., and Luo, J. (2019). Combining cold sintering and Bi2O3-Activated liquid-phase sintering to fabricate high-conductivity Mg-doped NASICON at reduced temperatures. J. Materiomics 5 (2), 237–246. Article. doi:10.1016/j.jmat.2019.02.005
Li, C., Jiang, S., Lv, J.-w., and Zheng, T. (2015b). Ionic conductivities of Na–Ge–P glass ceramics as solid electrolyte. J. Alloys Compd. 633, 246–249. doi:10.1016/j.jallcom.2014.12.183
Li, G., Lu, X., Kim, J. Y., Lemmon, J. P., and Sprenkle, V. L. (2013). Cell degradation of a Na–NiCl2 (ZEBRA) battery. J. Mat. Chem. A 1 (47), 14935. doi:10.1039/c3ta13644b
Li, G., Lu, X., Kim, J. Y., Lemmon, J. P., and Sprenkle, V. L. (2014). Improved cycling behavior of ZEBRA battery operated at intermediate temperature of 175 °C. J. Power Sources 249, 414–417. doi:10.1016/j.jpowsour.2013.10.110
Li, G., Lu, X., Kim, J. Y., Meinhardt, K. D., Chang, H. J., Canfield, N. L., et al. (2016a). Advanced intermediate temperature sodium–nickel chloride batteries with ultra-high energy density. Nat. Commun. 7 (1), 10683. doi:10.1038/ncomms10683
Li, G., Lu, X., Kim, J. Y., Viswanathan, V. V., Meinhardt, K. D., Engelhard, M. H., et al. (2015a). An advanced Na–FeCl2 ZEBRA battery for stationary energy storage application. Adv. Energy Mater. 5 (12), 1500357. doi:10.1002/aenm.201500357
Li, H., Fan, H., Zhang, J., Wen, Y., Chen, G., Zhu, Y., et al. (2019). Sintering behavior and properties of lithium stabilized sodium β'' - alumina ceramics with YSZ addition. Ceram. Int. 45 (6), 6744–6752. doi:10.1016/j.ceramint.2018.12.165
Li, H., Yin, H., Wang, K., Cheng, S., Jiang, K., and Sadoway, D. R. (2016b). Liquid metal electrodes for energy storage batteries. Adv. Energy Mater. 6 (14), 1600483. doi:10.1002/aenm.201600483
Li, K., Ma, M., Yang, Y., Liang, S., and Zhang, X. (2021b). Preparation of β"-Al2O3 electrolytes by freeze-drying and SPS. Ceram. Int. 47 (11), 15017–15022. doi:10.1016/j.ceramint.2021.02.057
Li, K., Yang, Y., Zhang, X., and Liang, S. (2020b). Highly oriented β ″-alumina ceramics with excellent ionic conductivity and mechanical performance obtained by spark plasma sintering technique. J. Mat. Sci. 55, 8435–8443. doi:10.1007/s10853-020-04423-x
Li, M. M., Tripathi, S., Polikarpov, E., Canfield, N. L., Han, K. S., Weller, J. M., et al. (2022). Interfacial engineering with a nanoparticle-decorated porous carbon structure on β″-alumina solid-state electrolytes for molten sodium batteries. ACS Appl. Mat. Interfaces 14 (22), 25534–25544. doi:10.1021/acsami.2c05245
Li, Y., Shi, L., Gao, X., Wang, J., Hu, Y., Wu, X., et al. (2021a). Constructing a charged-state Na-NiCl2 battery with NiCl2/graphene aerogel composite as cathode. Chem. Eng. J. 421, 127853. doi:10.1016/j.cej.2020.127853
Li, Y., Wu, X., Wang, J., Gao, X., Hu, Y., and Wen, Z. (2020a). Ni-less cathode with 3D free-standing conductive network for planar Na-NiCl2 batteries. Chem. Eng. J. 387, 124059. doi:10.1016/j.cej.2020.124059
Liu, C., Shamie, J. S., Shaw, L. L., and Sprenkle, V. L. (2016). An ambient temperature molten sodium–vanadium battery with aqueous flowing catholyte. ACS Appl. Mat. Interfaces 8 (2), 1545–1552. doi:10.1021/acsami.5b11503
Liu, Z., Chen, J., Wang, X., Wang, Y., Wang, D., and Mao, Z. (2020). Synthesis and characterization of high ionic-conductive sodium beta-alumina solid electrolyte derived from boehmite. J. Mat. Sci. Mat. Electron. 31 (20), 17670–17678. doi:10.1007/s10854-020-04321-7
Long Duration Energy Storage Council (2022). The journey to net-zero: an action plan to unlock a secure, net-zero power system. Long Duration Energy Storage Council.
Lu, J., Tang, J., Shan, R., Li, G., Rao, P., and Zhang, N. (2023). Spatiotemporal analysis of the future carbon footprint of solar electricity in the United States by a dynamic life cycle assessment. iScience 26 (3), 106188. doi:10.1016/j.isci.2023.106188
Lu, X., Chang, H. J., Bonnett, J. F., Canfield, N. L., Jung, K., Sprenkle, V. L., et al. (2017). Effect of cathode thickness on the performance of planar Na-NiCl2 battery. J. Power Sources 365, 456–462. doi:10.1016/j.jpowsour.2017.07.029
Lu, X., Chang, H. J., Bonnett, J. F., Canfield, N. L., Jung, K., Sprenkle, V. L., et al. (2018). An intermediate-temperature high-performance Na–ZnCl2 battery. ACS Omega 3 (11), 15702–15708. doi:10.1021/acsomega.8b02112
Lu, X., Kirby, B. W., Xu, W., Li, G., Kim, J. Y., Lemmon, J. P., et al. (2013b). Advanced intermediate-temperature Na–S battery. Energy Environ. Sci. 6 (1), 299–306. doi:10.1039/C2EE23606K
Lu, X., Lemmon, J. P., Sprenkle, V., and Yang, Z. (2010a). Sodium-beta alumina batteries: status and challenges. JOM 62 (9), 31–36. doi:10.1007/s11837-010-0132-5
Lu, X., Li, G., Kim, J. Y., Lemmon, J. P., Sprenkle, V. L., and Yang, Z. (2012). The effects of temperature on the electrochemical performance of sodium–nickel chloride batteries. J. Power Sources 215, 288–295. doi:10.1016/j.jpowsour.2012.05.020
Lu, X., Li, G., Kim, J. Y., Lemmon, J. P., Sprenkle, V. L., and Yang, Z. (2013c). A novel low-cost sodium–zinc chloride battery. Energy & Environ. Sci. 6 (6), 1837. doi:10.1039/c3ee24244g
Lu, X., Li, G., Kim, J. Y., Mei, D., Lemmon, J. P., Sprenkle, V. L., et al. (2014). Liquid-metal electrode to enable ultra-low temperature sodium–beta alumina batteries for renewable energy storage. Nat. Commun. 5 (1), 4578. doi:10.1038/ncomms5578
Lu, X., Li, G., Kim, J. Y., Meinhardt, K. D., and Sprenkle, V. L. (2015). Enhanced sintering of β″-Al2O3/YSZ with the sintering aids of TiO2 and MnO2. J. Power Sources 295, 167–174. doi:10.1016/j.jpowsour.2015.06.147
Lu, X., Xia, G., Lemmon, J. P., and Yang, Z. (2010b). Advanced materials for sodium-beta alumina batteries: status, challenges and perspectives. J. Power Sources 195 (9), 2431–2442. doi:10.1016/j.jpowsour.2009.11.120
Lu, X. C., Lemmon, J. P., Kim, J. Y., Sprenkle, V. L., and Yang, Z. G. (2013a). High energy density Na-S/NiCl2 hybrid battery. J. Power Sources 224, 312–316. doi:10.1016/j.jpowsour.2012.09.108
Mali, A., and Petric, A. (2012). Synthesis of sodium β″-alumina powder by sol–gel combustion. J. Eur. Ceram. Soc. 32 (6), 1229–1234. doi:10.1016/j.jeurceramsoc.2011.11.004
Manchgesang, W., Wagner, D., Motylenko, M., Schilm, J., Rafaja, D., and Meyer, D. C. (2018). Influence of the glass-ceramic synthesis route on the ionicconductivity of the sodium solid electrolyte Na2O-Y2O3-SiO2 (NYS). Acta Crystallogr. Sect. A 74, E286. Meeting Abstract. doi:10.1107/s2053273318090861
Maraschky, A. M., Meyerson, M. L., Percival, S. J., Lowry, D. R., Meserole, S., Williard, J. N., et al. (2023a). Impact of catholyte lewis acidity at the molten salt–NaSICON interface in low-temperature molten sodium batteries. J. Phys. Chem. C 127 (3), 1293–1302. doi:10.1021/acs.jpcc.2c06240
Maraschky, A. M., Percival, S. J., Lee, R. Y., Meyerson, M. L., Peretti, A. S., Spoerke, E. D., et al. (2023b). Electrode blocking due to redox reactions in aluminum chloride-sodium iodide molten salts. J. Electrochem. Soc. 170 (6), 066504. doi:10.1149/1945-7111/acd874
Mekhilef, S., Saidur, R., and Safari, A. (2011). A review on solar energy use in industries. Renew. Sustain. Energy Rev. 15 (4), 1777–1790. doi:10.1016/j.rser.2010.12.018
Miao, R. J., Cao, X. G., Wang, W. G., and Zhang, H. Y. (2021). Influence of Bi2O3 additive on the electrochemical performance of Na3.1 Y0.1Zr1.9Si2PO12 inorganic solid electrolyte. Ceram. Int. 47 (12), 17455–17462. Article. doi:10.1016/j.ceramint.2021.03.062
Moran, E. F., Lopez, M. C., Moore, N., Müller, N., and Hyndman, D. W. (2018). Sustainable hydropower in the 21st century. Proc. Natl. Acad. Sci. 115 (47), 11891–11898. doi:10.1073/pnas.1809426115
Mortalò, C., Rosa, R., Veronesi, P., Fasolin, S., Zin, V., Deambrosis, S. M., et al. (2020). Microwave assisted sintering of Na-β’’-Al2O3 in single mode cavities: insights in the use of 2450 MHz frequency and preliminary experiments at 5800 MHz. Ceram. Int. 46 (18), 28767–28777. Part A). doi:10.1016/j.ceramint.2020.08.039
NAS Batteries (2023). Designed for stationary energy storage. Available at: https://www.basf.com/global/en/who-we-are/organization/group-companies/BASF-Stationary-Energy-Storage-GmbH/designed-for-stationary-energy-storage.html (Accessed December 30, 2023).
Nasu, A., Inaoka, T., Tsuji, F., Motohashi, K., Sakuda, A., Tatsumisago, M., et al. (2022). Formation of passivate interphases by Na3BS3-glass solid electrolytes in all-solid-state sodium-metal batteries. ACS Appl. Mat. Interfaces 14 (21), 24480–24485. doi:10.1021/acsami.2c05090
National Research Council (2012). The role of the chemical sciences in finding alternatives to critical resources: a workshop summary. Washington (DC): National Academies Press.
NGL-Insulator (2023). About NAS batteries. https://www.ngk-insulators.com/en/product/nas-about.html (Accessed December 30, 2023).
Ni, Y., Zheng, R., Tan, X., Yue, W., Lv, P., Yang, J., et al. (2015). A fluorophosphate glass–ceramic electrolyte with superior ionic conductivity and stability for Na-ion batteries. J. Mat. Chem. A 3 (34), 17558–17562. doi:10.1039/c5ta03030g
Nieto-Muñoz, A. M., Ortiz-Mosquera, J. F., and Rodrigues, A. C. M. (2019). Novel sodium superionic conductor of the Na1+yTi2SiyP3-yO12 series for application as solid electrolyte. Electrochimica Acta 319, 922–932. doi:10.1016/j.electacta.2019.07.032
Nieto-Muñoz, A. M., Ortiz-Mosquera, J. F., and Rodrigues, A. C. M. (2020). The impact of heat-treatment protocol on the grain size and ionic conductivity of NASICON glass-ceramics. J. Eur. Ceram. Soc. 40 (15), 5634–5645. doi:10.1016/j.jeurceramsoc.2020.05.026
Nikiforidis, G., Jongerden, G. J., Jongerden, E. F., Van De Sanden, M. C. M., and Tsampas, M. N. (2019). An electrochemical study on the cathode of the intermediate temperature tubular sodium-sulfur (NaS) battery. J. Electrochem. Soc. 166 (2), A135–A142. doi:10.1149/2.0491902jes
Nimah, Y. L., Cheng, M.-Y., Cheng, J. H., Rick, J., and Hwang, B.-J. (2015). Solid-state polymer nanocomposite electrolyte of TiO2/PEO/NaClO4 for sodium ion batteries. J. Power Sources 278, 375–381. doi:10.1016/j.jpowsour.2014.11.047
Niu, C., Ji, L., Chen, Y., Ma, S., Zhang, Y., Liu, X., et al. (2021). Low-melting-point ionic liquid electrolyte for an intermediate-temperature sodium–copper chloride battery. Energy & Fuels 35 (15), 12538–12545. doi:10.1021/acs.energyfuels.1c00833
Niu, C., Zhang, Y., Ma, S., Wan, Y., Yang, H., and Liu, X. (2019). An intermediate temperature sodium copper chloride battery using ionic liquid electrolyte and its degradation mechanism. Ionics 25, 4189–4196. doi:10.1007/s11581-019-03003-7
Noi, K., Suzuki, K., Tanibata, N., Hayashi, A., and Tatsumisago, M. (2018). Liquid-phase sintering of highly Na+ ion conducting Na3Zr2Si2PO12 ceramics using Na3BO3 additive. J. Am. Ceram. Soc. 101 (3), 1255–1265. Article. doi:10.1111/jace.15288
Nose, M., Kato, A., Sakuda, A., Hayashi, A., and Tatsumisago, M. (2015). Evaluation of mechanical properties of Na2S–P2S5 sulfide glass electrolytes. J. Mat. Chem. A 3 (44), 22061–22065. doi:10.1039/C5TA05590C
Oh, J. A. S., He, L. C., Plewa, A., Morita, M., Zhao, Y., Sakamoto, T., et al. (2019). Composite NASICON (Na3Zr2Si2PO12) solid-state electrolyte with enhanced Na+ ionic conductivity: effect of liquid phase sintering. ACS Appl. Mat. Interfaces 11 (43), 40125–40133. Article. doi:10.1021/acsami.9b14986
Ohi, J. M. (1992). Environmental, health, and safety issues of sodium-sulfur batteries for electric and hybrid vehicles. Golden, CO (United States): National Renewable Energy Lab.
Olson, M., Wheaton, J., Okkema, M., Oldham, N., and Martin, S. W. (2023). Optimized thin film processing of sodium mixed oxy-sulfide-nitride glassy solid electrolytes for all-solid-state batteries. ACS Appl. energy Mater. 6 (11), 5842–5855. doi:10.1021/acsaem.3c00294
Park, H. C., Lee, Y. B., Lee, S. G., Lee, C. H., Kim, J. K., Hong, S. S., et al. (2005). Synthesis of beta-alumina powders by microwave heating from solution-derived precipitates. Ceram. Int. 31 (2), 293–296. doi:10.1016/j.ceramint.2004.05.019
Parthasarathy, P., Weber, N., and Virkar, A. V. (2007). High temperature sodium-zinc chloride batteries with sodium beta-alumina solid electrolyte. ECS Trans. 6 (14), 67–76. doi:10.1149/1.2811944
Pauling, L. (1927). The sizes of ions and the structure of ionic crystals. J. Am. Chem. Soc. 49 (3), 765–790. doi:10.1021/ja01402a019
Peled, E., Golodnitsky, D., Hadar, R., Mazor, H., Goor, M., and Burstein, L. (2013). Challenges and obstacles in the development of sodium–air batteries. J. Power Sources 244, 771–776. doi:10.1016/j.jpowsour.2013.01.177
Percival, S. J., Lee, R. Y., Gross, M. M., Peretti, A. S., Small, L. J., and Spoerke, E. D. (2021). Electrochemistry of the NaI-AlBr3 molten salt system: a redox-active, low-temperature molten salt electrolyte. J. Electrochem. Soc. 168 (3), 036510. doi:10.1149/1945-7111/abebae
Percival, S. J., Small, L. J., and Spoerke, E. D. (2018). Electrochemistry of the NaI-AlCl3 molten salt system for use as catholyte in sodium metal batteries. J. Electrochem. Soc. 165 (14), A3531–A3536. doi:10.1149/2.1191814jes
Pereirinha, P. G., González, M., Carrilero, I., Anseán, D., Alonso, J., and Viera, J. C. (2018). Main trends and challenges in road transportation electrification. Transp. Res. Procedia 33, 235–242. doi:10.1016/j.trpro.2018.10.096
Perera, F. P. (2017). Multiple threats to child health from fossil fuel combustion: impacts of air pollution and climate change. Environ. Health Perspect. 125 (2), 141–148. doi:10.1289/ehp299
Qiao, L., Judez, X., Rojo, T., Armand, M., and Zhang, H. (2020). Review—polymer electrolytes for sodium batteries. J. Electrochem. Soc. 167 (7), 070534. doi:10.1149/1945-7111/ab7aa0
Rahman, M. M., Oni, A. O., Gemechu, E., and Kumar, A. (2020). Assessment of energy storage technologies: a review. Energy Convers. Manag. 223, 113295. doi:10.1016/j.enconman.2020.113295
Rajagopalan, R., Zhang, Z., Tang, Y., Jia, C., Ji, X., and Wang, H. (2021). Understanding crystal structures, ion diffusion mechanisms and sodium storage behaviors of NASICON materials. Energy Storage Mater. 34, 171–193. doi:10.1016/j.ensm.2020.09.007
Ray, A. K., and Subbarao, E. C. (1975). Synthesis of sodium β and β″ alumina. Mater. Res. Bull. 10 (6), 583–590. doi:10.1016/0025-5408(75)90186-5
Reed, D., Coffey, G., Mast, E., Canfield, N., Mansurov, J., Lu, X., et al. (2013). Wetting of sodium on β ″-Al2O3/YSZ composites for low temperature planar sodium-metal halide batteries. J. Power Sources 227, 94–100. doi:10.1016/j.jpowsour.2012.11.034
Richman, R. H., and Tennenhouse, G. J. (1975). A model for degradation of ceramic electrolytes in Na-S batteries. J. Am. Ceram. Soc. 58, 63–67. doi:10.1111/J.1151-2916.1975.TB18986.X
Sakaebe, H. (2014). “ZEBRA batteries,” in Encyclopedia of applied electrochemistry. Editors G Kreysa, K Ota, and R F Savinell (New York: Springer), 2165–2169.
Samiee, M., Radhakrishnan, B., Rice, Z., Deng, Z., Meng, Y. S., Ong, S. P., et al. (2017). Divalent-doped Na3Zr2Si2PO12 natrium superionic conductor: improving the ionic conductivity via simultaneously optimizing the phase and chemistry of the primary and secondary phases. J. Power Sources 347, 229–237. doi:10.1016/j.jpowsour.2017.02.042
Schmid, H., De Jonghe, L. C., and Cameron, C. (1982). Chemical stability of nasicon. Solid State Ionics 6, 57–63. doi:10.1016/0167-2738(82)90096-0
Shamie, J. S., Liu, C., Shaw, L. L., and Sprenkle, V. L. (2015). Room temperature, hybrid sodium-based flow batteries with multi-electron transfer redox reactions. Sci. Rep. 5 (1), 11215. doi:10.1038/srep11215
Shao, B., Huang, Y., and Han, F. (2023). Electronic conductivity of lithium solid electrolytes. Adv. Energy Mater. 13 (16), 2204098. doi:10.1002/aenm.202204098
Shao, Y., Zhong, G., Lu, Y., Liu, L., Zhao, C., Zhang, Q., et al. (2019). A novel NASICON-based glass-ceramic composite electrolyte with enhanced Na-ion conductivity. Energy Storage Mater. 23, 514–521. doi:10.1016/j.ensm.2019.04.009
Shimizu, Y., Azuma, Y., and Michishita, S. (1997). Sol–gel synthesis of NASICON discs from aqueous solution. J. Mat. Chem. 7 (8), 1457–1460. doi:10.1039/a608364a
Sieuw, L., Lan, T., Svaluto-Ferro, E., Vagliani, F., Kumar, S., Ding, W., et al. (2024). Influence of precursor morphology and cathode processing on performance and cycle life of sodium-zinc chloride (Na-ZnCl2) battery cells. Energy Storage Mater. 64, 103077. doi:10.1016/j.ensm.2023.103077
Small, L. J., Eccleston, A., Lamb, J., Read, A. C., Robins, M., Meaders, T., et al. (2017). Next generation molten NaI batteries for grid scale energy storage. J. Power Sources 360, 569–574. doi:10.1016/j.jpowsour.2017.06.038
Solstice (2023). Solstice Available at: https://www.solstice-battery.eu/about/ (Accessed December-30-2023).
Sozak, M., Nazarenus, T., Exner, J., Kita, J., and Moos, R. (2023). Room temperature manufacture of dense NaSICON solid electrolyte films for all-solid-state-sodium batteries. J. Mat. Sci. 58 (24), 10108–10119. doi:10.1007/s10853-023-08642-w
Spatocco, B. L., Ouchi, T., Lambotte, G., Burke, P. J., and Sadoway, D. R. (2015). Low-temperature molten salt electrolytes for membrane-free sodium metal batteries. J. Electrochem. Soc. 162 (14), A2729–A2736. doi:10.1149/2.0441514jes
Spoerke, E. D., Durvasulu, V., and Balliet, H. (2030). Sodium batteries technology strategy assesssment. Storage Innov., 2023.
Stevens, R., and Binner, J. G. P. (1984). Structure, properties and production of β-alumina. J. Mat. Sci. 19 (3), 695–715. doi:10.1007/bf00540440
Sudworth, J. L. (2001). The sodium/nickel chloride (ZEBRA) battery. J. Power Sources 100, 149–163. doi:10.1016/S0378-7753(01)00891-6
Sundar, G., Suman, G., Kumar, K., Dutta, D., and Rao, R. (2019). Investigation on the applicability of high Na-ion conducting Na3+ x[ZrxSc2-x(PO4)3] glass-ceramic electrolyte for use in safer Na-ion batteries. J. Phys. Chem. Solids 126, 209–218. doi:10.1016/j.jpcs.2018.11.016
Susman, S., Delbecq, C. J., McMillan, J. A., and Roche, M. F. (1983). NASIGLAS: a new vitreous electrolyte. Solid State Ionics 9-10, 667–673. doi:10.1016/0167-2738(83)90312-0
Suzuki, K., Noi, K., Hayashi, A., and Tatsumisago, M. (2018). Low temperature sintering of Na1+xZr2SixP3-xO12 by the addition of Na3BO3. Scr. Mater. 145, 67–70. Article. doi:10.1016/j.scriptamat.2017.10.010
Tang, W. S., Dimitrievska, M., Stavila, V., Zhou, W., Wu, H., Talin, A. A., et al. (2017). Order–disorder transitions and superionic conductivity in the sodium nido-undeca (carba) borates. Chem. Mat. 29 (24), 10496–10509. doi:10.1021/acs.chemmater.7b04332
Tang, W. S., Yoshida, K., Soloninin, A. V., Skoryunov, R. V., Babanova, O. A., Skripov, A. V., et al. (2016). Stabilizing superionic-conducting structures via mixed-anion solid solutions of monocarba-closo-borate salts. ACS Energy Lett. 1 (4), 659–664. doi:10.1021/acsenergylett.6b00310
Tanibata, N., Noi, K., Hayashi, A., Kitamura, N., Idemoto, Y., and Tatsumisago, M. (2014). X-ray crystal structure analysis of sodium-ion conductivity in 94Na3PS4⋅6Na4SiS4 glass-ceramic electrolytes. ChemElectroChem 1 (7), 1130–1132. doi:10.1002/celc.201402016
Tanibata, N., Noi, K., Hayashi, A., and Tatsumisago, M. (2018). Preparation and characterization of Na3PS4–Na4GeS4 glass and glass-ceramic electrolytes. Solid State Ionics 320, 193–198. doi:10.1016/j.ssi.2018.02.042
Tatsumisago, M., and Hayashi, A. (2014). Sulfide glass-ceramic electrolytes for all-solid-state lithium and sodium batteries. Int. J. Appl. Glass Sci. 5 (3), 226–235. doi:10.1111/ijag.12084
Trickett, D. (1998). Current status of health and safety issues of sodium/metal chloride (ZEBRA) batteries. Golden, CO (United States): National Renewable Energy Lab.
Tsai, C. L., and Hong, H. Y. P. (1983). Investigation of phases and stability of solid electrolytes in the NASICON system. Mater. Res. Bull. 18 (11), 1399–1407. doi:10.1016/0025-5408(83)90048-X
Tsuji, F., Nasu, A., Hotehama, C., Sakuda, A., Tatsumisago, M., and Hayashi, A. (2021). Preparation and characterization of sodium-ion conductive Na3BS3 glass and glass–ceramic electrolytes. Mat. Adv. 2 (5), 1676–1682. doi:10.1039/d0ma00777c
Tsuji, F., Tanibata, N., Sakuda, A., Hayashi, A., and Tatsumisago, M. (2018). Preparation of sodium ion conductive Na10GeP2S12 glass-ceramic electrolytes. Chem. Lett. 47 (1), 13–15. Article. doi:10.1246/cl.170836
Tu, X., Chu, Y., and Ma, C. (2010). New ternary molten salt electrolyte based on alkali metal triflates. Ionics 16 (1), 81–84. doi:10.1007/s11581-009-0390-9
Udovic, T. J., Matsuo, M., Unemoto, A., Verdal, N., Stavila, V., Skripov, A. V., et al. (2014). Sodium superionic conduction in Na2B12H12. Chem. Commun. 50 (28), 3750–3752. doi:10.1039/C3CC49805K
van Zyl, A., Thackeray, M. M., Duncan, G. K., Kingon, A. I., and Heckroodt, R. O. (1993). The synthesis of beta alumina from aluminium hydroxide and oxyhydroxide precursors. Mater. Res. Bull. 28 (2), 145–157. doi:10.1016/0025-5408(93)90083-P
Virkar, A. (2008). A high temperature electrochemical energy storage system based on sodium beta-alumina solid electrolyte (Base). Salt Lake City, UT (United States): Univ. of Utah.
Virkar, A. V., and Viswanathan, L. (1983). A three-dimensional approach to the electrolytic degradation of solid electrolytes. J. Mat. Sci. 18 (4), 1202–1212. doi:10.1007/bf00551990
Viswanathan, L., and Virkar, A. V. (1982). Wetting characteristics of sodium on β″-alumina and on nasicon. J. Mat. Sci. 17, 753–759. doi:10.1007/BF00540372
Wang, D., Hwang, J., Chen, C. Y., Kubota, K., Matsumoto, K., and Hagiwara, R. (2021). A β-alumina/inorganic ionic liquid dual electrolyte for intermediate-temperature sodium–sulfur batteries. Adv. Funct. Mater. 31 (48), 9. doi:10.1002/adfm.202105524
Wang, N., Wang, Y., Bai, Z., Fang, Z., Zhang, X., Xu, Z., et al. (2020b). High-performance room-temperature sodium–sulfur battery enabled by electrocatalytic sodium polysulfides full conversion. Energy & Environ. Sci. 13 (2), 562–570. doi:10.1039/c9ee03251g
Wang, X., Chen, J., Mao, Z., and Wang, D. (2022). Effective resistance to dendrite growth of NASICON solid electrolyte with lower electronic conductivity. Chem. Eng. J. 427, 130899. doi:10.1016/j.cej.2021.130899
Wang, Y., Zhou, D., Palomares, V., Shanmukaraj, D., Sun, B., Tang, X., et al. (2020a). Revitalising sodium–sulfur batteries for non-high-temperature operation: a crucial review. Energy & Environ. Sci. 13 (11), 3848–3879. doi:10.1039/d0ee02203a
Warhus, U., Maier, J., and Rabenau, A. (1988). Thermodynamics of NASICON (Na1+xZr2SixP3−xO12). J. Solid State Chem. 72 (1), 113–125. doi:10.1016/0022-4596(88)90014-X
Wei, M., McMillan, C. A., and de la Rue du Can, S. (2019). Electrification of industry: potential, challenges and outlook. Curr. Sustainable/Renewable Energy Rep. 6 (4), 140–148. doi:10.1007/s40518-019-00136-1
Wei, S., Xu, S., Agrawral, A., Choudhury, S., Lu, Y., Tu, Z., et al. (2016). A stable room-temperature sodium–sulfur battery. Nat. Commun. 7 (1), 11722. doi:10.1038/ncomms11722
Weiner, S. A. (1977). “The sodium-sulfur battery: problems and promises,” in Solid state chemistry of energy conversion and storage (Washington, D.C: American Chemical Society), 205–224.
Weller, J. M., Li, M. M., Polikarpov, E., Han, K. S., Kidner, N., Patel, A., et al. (2023). Unlocking the NaCl-AlCl3 phase diagram for low-cost, long-duration Na-Al batteries. Energy Storage Mater. 56, 108–120. doi:10.1016/j.ensm.2023.01.009
Wentker, M., Greenwood, M., Asaba, M. C., and Leker, J. (2019a). A raw material criticality and environmental impact assessment of state-of-the-art and post-lithium-ion cathode technologies. J. Energy Storage 26, 101022. doi:10.1016/j.est.2019.101022
Wentker, M., Greenwood, M., Asaba, M. C., and Leker, J. (2019b). A raw material criticality and environmental impact assessment of state-of-the-art and post-lithium-ion cathode technologies. J. Energy Storage 26, 101022. doi:10.1016/j.est.2019.101022
Wenzel, S., Leichtweiss, T., Weber, D. A., Sann, J., Zeier, W. G., and Janek, J. (2016). Interfacial reactivity benchmarking of the sodium ion conductors Na3PS4 and sodium β-alumina for protected sodium metal anodes and sodium all-solid-state batteries. ACS Appl. Mat. Interfaces 8 (41), 28216–28224. doi:10.1021/acsami.6b10119
Whittingham, M. S., and Huggins, R. A. (1971a). Measurement of sodium ion transport in beta alumina using reversible solid electrodes. J. Chem. Phys. 54 (1), 414–416. doi:10.1063/1.1674623
Whittingham, M. S., and Huggins, R. A. (1971b). Transport properties of silver beta alumina. J. Electrochem. Soc. 118 (1), 1. doi:10.1149/1.2407944
Xu, J., Kjos, O. S., Osen, K. S., Martinez, A. M., Kongstein, O. E., and Haarberg, G. M. (2016). Na-Zn liquid metal battery. J. Power Sources 332, 274–280. doi:10.1016/j.jpowsour.2016.09.125
Xue, L., Xin, S., Goodenough, J. B., and Angell, C. A. (2017). An inverse aluminum battery: putting the aluminum as the cathode. ACS Energy Lett. 2 (7), 1534–1538. doi:10.1021/acsenergylett.7b00234
Yang, F., Mousavie, S. M. A., Oh, T. K., Yang, T., Lu, Y., Farley, C., et al. (2018). Sodium–sulfur flow battery for low-cost electrical storage. Adv. Energy Mater. 8 (11), 1701991. doi:10.1002/aenm.201701991
Youngblood, G. E., Miller, G. R., and Gordon, R. S. (1978). Relative effects of phase conversion and grain size on sodium ion conduction in polycrystalline, lithia-stabilized β-alumina. J. Am. Ceram. Soc. 61 (1-2), 86–87. doi:10.1111/j.1151-2916.1978.tb09238.x
Yuan, M., Thellufsen, J. Z., Lund, H., and Liang, Y. (2021). The electrification of transportation in energy transition. Energy 236, 121564. doi:10.1016/j.energy.2021.121564
Yung-Fang Yu, Y., and Kummer, J. T. (1967). Ion exchange properties of and rates of ionic diffusion in beta-alumina. J. Inorg. Nucl. Chem. 29 (9), 2453–2475. doi:10.1016/0022-1902(67)80301-4
Zhan, X., Bonnett, J. F., Engelhard, M. H., Reed, D. M., Sprenkle, V. L., and Li, G. (2020b). A high-performance Na–Al battery based on reversible NaAlCl4 catholyte. Adv. Energy Mater. 10 (40), 2001378. doi:10.1002/aenm.202001378
Zhan, X., Bowden, M. E., Lu, X., Bonnett, J. F., Lemmon, T., Reed, D. M., et al. (2020a). A low-cost durable Na-FeCl2 battery with ultrahigh rate capability. Adv. Energy Mater. 10 (10), 1903472. doi:10.1002/aenm.201903472
Zhang, Q., Lu, Y., Guo, W., Shao, Y., Liu, L., Lu, J., et al. (2021). Hunting sodium dendrites in NASICON-based solid-state electrolytes. Energy Mat. Adv. 2021, 1–10. doi:10.34133/2021/9870879
Zhang, Q., Lu, Y., Yu, H., Yang, G., Liu, Q., Wang, Z., et al. (2020b). PEO-NaPF6 blended polymer electrolyte for solid state sodium battery. J. Electrochem. Soc. 167 (7), 070523. doi:10.1149/1945-7111/ab741b
Zhang, S., Quan, B., Zhao, Z., Zhao, B., He, Y., and Chen, W. (2004). Preparation and characterization of NASICON with a new sol–gel process. Mater. Lett. 58 (1), 226–229. doi:10.1016/S0167-577X(03)00450-6
Zhang, Z., Wenzel, S., Zhu, Y., Sann, J., Shen, L., Yang, J., et al. (2020a). Na3Zr2Si2PO12: a stable Na+-ion solid electrolyte for solid-state batteries. ACS Appl. Energy Mater. 3 (8), 7427–7437. doi:10.1021/acsaem.0c00820
Zhou, H., Li, H., Gong, Q., Yan, S., Zhou, X., Liang, S., et al. (2022). A sodium liquid metal battery based on the multi-cationic electrolyte for grid energy storage. Energy Storage Mater. 50, 572–579. doi:10.1016/j.ensm.2022.05.032
Zhou, W., Li, Y., Xin, S., and Goodenough, J. B. (2017). Rechargeable sodium all-solid-state battery. ACS Cent. Sci. 3, 52–57. doi:10.1021/acscentsci.6b00321
Zhu, Y. G., Leverick, G., Accogli, A., Gordiz, K., Zhang, Y., and Shao-Horn, Y. (2022b). A high-rate and high-efficiency molten-salt sodium–oxygen battery. Energy & Environ. Sci. 15 (11), 4636–4646. doi:10.1039/D2EE01774A
Keywords: sodium batteries, grid storage, solid electrolytes, interfaces, ZEBRA, Na-S
Citation: Hill RC, Gross MS, Percival SJ, Peretti AS, Small LJ, Spoerke ED and Cheng Y-T (2024) Molten sodium batteries: advances in chemistries, electrolytes, and interfaces. Front. Batteries Electrochem. 3:1369305. doi: 10.3389/fbael.2024.1369305
Received: 12 January 2024; Accepted: 29 February 2024;
Published: 08 March 2024.
Edited by:
Xingcheng Xiao, General Motors, United StatesReviewed by:
Yifan Zhao, General Motors, United StatesJohn Vaughey, Argonne National Laboratory (DOE), United States
Copyright © 2024 Hill, Gross, Percival, Peretti, Small, Spoerke and Cheng. This is an open-access article distributed under the terms of the Creative Commons Attribution License (CC BY). The use, distribution or reproduction in other forums is permitted, provided the original author(s) and the copyright owner(s) are credited and that the original publication in this journal is cited, in accordance with accepted academic practice. No use, distribution or reproduction is permitted which does not comply with these terms.
*Correspondence: Ryan C. Hill, cnlhbi5jLmhpbGxAc3Rvbnlicm9vay5lZHU=