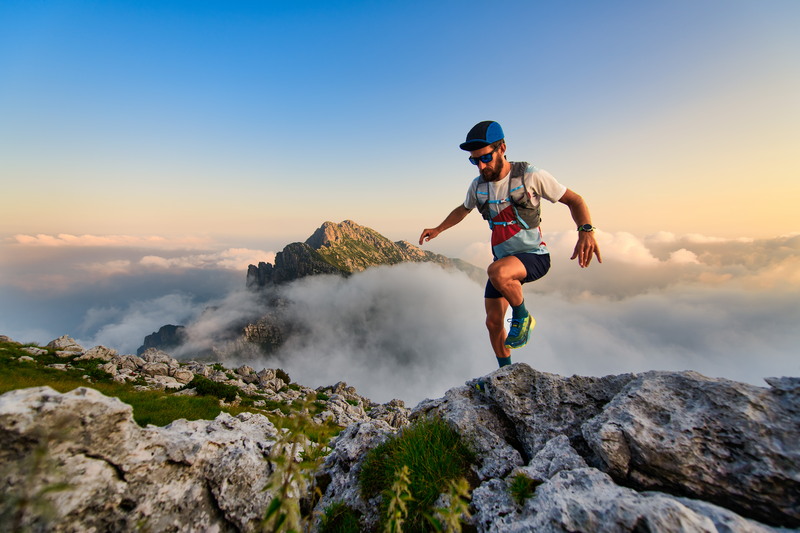
95% of researchers rate our articles as excellent or good
Learn more about the work of our research integrity team to safeguard the quality of each article we publish.
Find out more
REVIEW article
Front. Batter. Electrochem. , 29 September 2023
Sec. Next Generation Batteries and Technologies
Volume 2 - 2023 | https://doi.org/10.3389/fbael.2023.1272439
This article is part of the Research Topic Frontiers in Batteries and Electrochemistry: Review Collection View all 4 articles
To achieve a high energy density for Li-ion batteries (LIBs) in a limited space, thick electrodes play an important role by minimizing passive component at the unit cell level and allowing higher active material loading within the same volume. Currently, the capacity of active materials is close to the theoretical capacity; therefore, thick electrodes provide the clearest solution for the development of high-energy-density batteries. However, further research is needed to resolve the electrochemical and mechanical instabilities inside the electrode owing to its increased thickness. This review summarizes the various methods and recent research aimed at fabricating electrodes with low-torsion and uniform pore structure for fast ion transport, based on an in-depth consideration of the challenges encountered in thick electrodes. In addition, future developments and research directions necessary to apply these methods to the industry are presented. This review will be a valuable milestone for manufacturing robust thick electrodes with high performance and for realizing ultrahigh-capacity/density batteries in the future.
Li-ion batteries (LIBs) are manufactured in a wide range of sizes for different uses. Smaller batteries are used for small accessories, such as portable electronic devices and larger one’s for electric vehicles (EVs) and Energy Storage Systems (ESSs) that are employed in residential and industrial applications (Park et al., 2021a; Kim, 2022). To ensure stable and efficient utilization of battery cells, it is common to use a module that combines several cells and further bundle these modules into a pack. A cell that serves as the smallest functional unit of a battery must possess high capacity per unit volume to deliver superior performance within the limited space constraints of EVs (Väyrynen and Salminen, 2012; Astaneh et al., 2022).
With the increasing utilization of medium- and large-sized batteries, extensive research is being conducted to enhance their capacity, energy density, and stability. High energy densities can be achieved through two approaches. The first involves the development of novel battery materials with high specific capacities (Tarascon and Armand, 2001; Scrosati et al., 2011; Blomgren, 2016; Myung et al., 2016; Winter et al., 2018; Zubi et al., 2018; Zhao et al., 2022). This is done by examining existing studies on next-generation battery materials. To date, substantial progress has been made in improving the energy density of Li-ion batteries, reaching a value of 300 W h kg-1 for short durations. This was accomplished by adopting high Ni cathode materials (Ni content of ≥80%), Si-based anodes, and high-voltage electrolytes to achieve high energy densities ≥350 W h kg-1 but maxing at 500 W h kg-1. Currently, research is focused on the development of new paradigm batteries with new systems and advanced materials, including Li-S, Li-O2, Li-CO2 (Rosenman et al., 2015; Kwak et al., 2020; Yu and Manthiram, 2020; Dang et al., 2022).
The second approach focuses on increasing the quantity of active materials within the battery electrodes (Sun et al., 2017; Liu et al., 2018; Shen et al., 2018; Kuang et al., 2019; Shi et al., 2019). Conventional LIBs used in EVs and ESSs are challenged with reduction of capacity per unit volume because of the increased utilization of non-energy storage components and number of modules and packs. Therefore, a key factor in enhancing battery performance is to reduce the presence of components unrelated to energy storage, such as current collectors and separators. As shown in Figure 1, when five batteries using cathodes and anodes with a thickness of 25 μm are stacked, the electrode component accounts for 56% of the total volume. However, in the case of a battery with the same volume, but using a 200 μm thick electrode, the electrode component occupies 88% of the total volume. This demonstrates that batteries with high-load thick electrodes can generate more energy within the same volume as conventional batteries (Kuang et al., 2019). Although active research has been conducted on Li metals and all-solid-state batteries (ASSBs), the removal of current collectors and separators, which play vital roles in batteries, remains challenging. Therefore, the capacity per unit volume can be increased without modifying the entire battery or increasing the number of non-energy storage components by adopting a thick electrode design to increase the amount of active material (Sun et al., 2017; Liu et al., 2018; Shen et al., 2018; Park et al., 2022).
FIGURE 1. Schematic diagram and component’s ratio graph of conventional battery and thick electrode based battery Reproduced with permission from Wiley (Kuang et al., 2019).
Various methods have been explored, such as reducing the use of binders and conductive materials in conventional electrode manufacturing, and creating thick electrodes through stacking. However, there are physical limitations in stacking an electrode slurry beyond a certain thickness using existing electrode manufacturing techniques. The ratio of active materials, binders, and conductive materials used in electrode manufacturing, the amount of solvent and electrolyte, viscosity, and pressure inside the cell must be considered during cell operation (Singh et al., 2015; Kumberg et al., 2019; Hou et al., 2020; Reynolds et al., 2021). However, if the binders are reduced and the ratio of active materials is increased, the bonding force between the materials in the electrode may decrease, resulting in collapse of the electrode structure (Chen et al., 2013). Therefore, increasing the thickness while maintaining the ratio of electrode materials is an effective way to increase the number of active materials. In addition, research on the production of dry-thick electrodes using binders such as polytetrafluoroethylene is in progress (Li et al., 2022a; Ryu et al., 2023; Wang et al., 2023). However, the dry manufacturing process for electrode fabrication does not involve the use of solvents, which can result in a lack of uniform distribution of electrode materials; further optimization and development are still required for commercialization. Even if the electrode is manufactured considering the above experimental variables, ion and electron conduction are the dominant variables in the battery operation. In conventional electrodes, the rate-determining step (RDS) is governed primarily by electron movement (Jow et al., 2018; Hu et al., 2020). However, as the thickness increases, insufficient Li-ion transport owing to inferior electrolyte penetration becomes dominant in determining the RDS. Consequently, it is crucial to design an electrode structure that facilitates the vigorous movement of Li-ions within thick electrodes.
Recent research on LIB electrodes has focused on suppressing electrode degradation during cycling and improving electronic and ionic conductivity. To achieve this, various approaches such as coating, doping, and optimizing the interaction with binders have been employed to mitigate structural damage. Studies have also been conducted on the use of 1–3D conductive materials to enhance electronic conductivity by forming conductive pathways between the electrode materials (Ban et al., 2011; Shah et al., 2014; Kim et al., 2017; Gao et al., 2018; Wei et al., 2018; Kim et al., 2019a; Peng et al., 2022). Although considerable progress has been made in improving electrode performance, it is crucial that the ionic conductivity is enhanced. This can be achieved by designing electrode structures that allow for uniform Li-ion diffusion by reducing the tortuosity.
Therefore, this study focuses on providing a brief review on the structural design of thick electrodes to enhance Li-ion mobility. A deep and comprehensive understanding of the electrochemistry occurring in thick electrodes is essential for determining critical factors for its design and the logic behind it. Hence, this study also provides an overview of the electrochemical reaction imbalance resulting from the reduced Li-ion mobility in thick electrodes and a perspective to address this issue before introducing related research. Each strategy was designed to facilitate Li-ion movement and induce uniform electrochemical reactions by controlling the porosity, tortuosity, electroconductivity, and other factors. In each section, the feasibility with respect to the processability and influence on electrode stability, as well as the merits and demerits of each technique was investigated. Consequently, the disadvantages and advantages of thick electrodes based on the aforementioned contents were emphasized. Additionally, valuable insights into future research directions in which thick electrodes and manufacturing methods should be developed were also provided.
Electrodes, make up one of the four major components of a battery and are a source of energy. Much research has been conducted on this component to determine the theoretical capacity of the active materials among the electrode materials (Thackeray et al., 2007; Kraytsberg and Ein-eli, 2012; Andre et al., 2015; Kim et al., 2019b; Li et al., 2020; Wang et al., 2020; Aryal et al., 2021; Fang et al., 2021; Kaneda et al., 2021; Tsai et al., 2021; Lv et al., 2022). Current collectors and separators are also major components, however, they can be classified as passive components from an energy storage perspective because they do not contain any lithium source that contributes to the battery’s capacity. Thick electrodes provide high energy expressions and economic benefits by reducing the use of passive components and increasing the ratio of active materials.
However, as the mass loading of the active materials increased, the electrode thickness increased. During the drying process, as the temperature increases the light conductive materials and binders rise to the top of the electrode, which results in the delamination of the current collector and low adhesion between the electrode materials, resulting in microcracks (Zhang et al., 2021; Klemens et al., 2022). This makes the distribution of the electrode materials sporadic as the electrode thickness increases, which limits the laminated thickness. In addition, increasing the thickness degrades the Li-ion and electron mobilities. The electrolyte that delivers Li-ions does not impregnate the entire electrode evenly as the thickness increases and causes a local reaction to accelerate the deterioration of the electrode (Xu et al., 2019; Kang et al., 2022b; Cronau et al., 2022; Kang et al., 2023). This has been confirmed by several studies that support the necessity of designing an electrode structure for Li-ion transport.
Kang et al. analyzed the degradation behavior of a high-loading NCM622 cathode during cycling (Park et al., 2020). As the cycles progressed, the accumulated ion diffusion limitations and exposure to excessive effective current led to surface degradation of the active materials, resulting in an uneven electrochemical reaction within the thick electrodes as shown in Figures 2A, B. This indicates that in thick electrodes, Li-ion diffusion dominates electronic conduction and acts as an RDS. Additionally, Lee et al. introduced high-loading multi-stacked electrodes to investigate the degradation behavior along the thickness direction during cycling (Figure 2C) (Kim et al., 2021). A thicker solid-electrolyte interphase (SEI) is formed in regions closer to the electrolyte, leading to pore clogging. As a result, the ion resistance increased at the electrode surface, and degradation was accelerated owing to the ongoing reactions. These considerations with increasing mass loading of the electrode highlighted the importance of vigorous Li-ion transport in thick electrodes.
FIGURE 2. Characteristics of thick electrodes and possible drawbacks. (A) Schematic diagram of electrode degradation in thick electrodes. (B) SEM images of top and bottom layer in thick electrodes after cycling. (A,B) Reproduced with permission from Elsevier (Park et al., 2020). (C) Schematic diagram of the deterioration of Li-ion mobility through the electrolyte after cycling. Reproduced with permission from Elsevier (Kim et al., 2021). (D) Schematic diagram of the ion transfer pathway in three kinds of electrodes.
Based on previous studies, during cycling in thick electrodes, it was confirmed that a gradient of Li-ion movement occurred. The reaction mainly occurred on the electrode surface, and the reaction in the bulk area decreased as the depth increased. The electrolyte surface reaction increased stress to the electrode active material and collapsed it, subsequently forming a non-uniform SEI, that reduces the electrochemical performance of the battery. Therefore, there is a need to induce a uniform electrochemical reaction, regardless of the depth of the electrode, by forming a path that allows the movement of the electrolyte inside the thick electrodes, as shown in Figure 2D. This implies that the electrode structure should be designed to reduce the tortuosity of the electrode and as a result, numerous studies on thick electrodes have been conducted for this purpose.
To induce a uniform electrochemical reaction throughout thick electrodes, a structural design for electrolyte penetration is required. The template architecture clearly shows a vertically aligned pore structure and provides a solution to easily manufacture electrodes with low tortuosity. In this section, we briefly review previous approaches for the pore structure design of thick electrodes using different templating methods.
Ice-templating utilizes the growth of ice crystals by freezing water (<0°C) to form ice columns, thereby forming the internal architecture of the electrodes. Water, unlike other substances, expands when it changes from a liquid to a solid state and this is because of the peculiarity of its crystal structure. Water molecules that reach the freezing point exhibit reduced molecular motion and form hexagonal ring-shaped crystal structures with empty spaces inside when hydrogen bonds are formed, resulting in an increase in volume. The ice crystals are then removed by drying, forming a porous structure within the electrode. These pores facilitate the movement of electrolytes and enhances Li-ion conductivity within the electrode. The ice-templating is utilized in the electrode architecture and has a considerable impact on electrolyte penetration and Li-ion diffusion. This method is primarily used for active materials that use deionized water as the solvent, such as LiMn2O4 or LiFePO4 (LFP) (Huang and Grant, 2018; Jung et al., 2018; Huang et al., 2019; Li et al., 2022a; He et al., 2022).
In a study conducted by Li et al. ice-templating was applied to NCM712, and an improved performance was observed compared with the conventional electrode. To utilize the ice-templating, an electrode using a water-soluble binder, carboxymethyl cellulose sodium (CMC-Na), was fabricated, instead of the commonly used PVdF binder. The tortuosity of the prepared electrode was 1.7, which was 1.5 lower than that of the conventional electrode (Li et al., 2022b). Therefore, to use the ice-templating, it is necessary to switch to a water-soluble binder. Research is also underway to utilize water-soluble binders such as carboxymethyl cellulose/styrene-butadiene rubber, polyacrylic acid (PAA), xanthan gum (XG), konjac gum (KG), and locust bean gum (Yang et al., 2021; Yang et al., 2022). There are examples of the application of ice-templating to NCM811, that utilizes a high-Ni cathode material. Yang et al. synthesized the binder by combining XG and KG. This binder exhibited an improved viscosity through the double helical structure of XG and cross-linking with KG, and it also offered advantages in enhancing electronic conductivity through its interaction with the conductive additive carbon nanotubes (Figure 3A) (Yang et al., 2021).
FIGURE 3. Thick electrode pore structure design by different templating methods. (A) The fabrication diagram and SEM images of thick electrodes via ice-templating. Reproduced with permission from Wiley (Yang et al., 2021). (B) Schematic diagram of the preparation process of thick electrodes via magnetic templating. Reproduced with permission from Wiley (Li et al., 2018). (C) Schematic diagram and SEM images of the 3D electrodes that derived from wood. Reproduced with permission from Wiley (Chen et al., 2017).
The prepared electrodes underwent structural formation by removing the ice through the ice-templating process after freezing in liquid nitrogen. The electrodes manufactured through ice-templating showed a porosity retention of approximately 90% or more, regardless of the depth; however, the stacked electrodes showed a decrease in porosity retention as the depth increased. Additionally, it is possible to set different porosities for the upper and lower parts of the electrode depending on the crystal growth direction. When the region with the lower porosity is positioned towards the separator, it results in a superior capacity (Huang et al., 2019). However, the ice template method may present potential performance limitations of the cathode, especially when used as active materials in ternary compounds containing Ni, Co, and Mn. The method inevitably uses water as the solvent of slurry, causing Li and transition metal dissolution and HF formation (Zhan et al., 2018; Li, 2020; Lee et al., 2022). Furthermore, the formation of residual Li byproducts and the resulting increase in the slurry pH due to water can induce corrosion of the entire cell, necessitating the introduction of additives and additional processes.
Magnetic templating is a method for forming the internal architecture of an electrode. This is done by incorporating a magnetic material that can form an aligned structure in magnetic fields as an additive during the electrode slurry manufacturing process and applying a magnetic field during the casting or drying process. Representative magnetic materials include Fe2O3, Fe3O4, Co3O4, and Co, which can exist in a solvent as an emulsion or coated onto electrodes as active materials (Billaud et al., 2016; Sander et al., 2016; Li et al., 2018; Ma et al., 2021; Ju et al., 2022; Yang et al., 2023).
Sander et al. utilized magnetized nylon and magnetic fluid to create pore structures through the application of magnetic fields and the subsequent removal of magnetic materials, resulting in a porosity of 39% (Sander et al., 2016). The LiCoO2 (LCO) electrode produced using this method exhibited an improved performance at high C-rates compared with an electrode with 40% porosity. This highlights the importance of providing clear pathways for Li-ion transport in high-load electrodes. When emulsion-based magnetic materials are used, the degree of arrangement may vary depending on slurry viscosity. Li et al. analyzed the arrangement of magnetic materials in various binders applicable to LCO cathodes. They mentioned the need to find suitable binder materials for magnetic templating because the uniform arrangement of magnetic particles becomes challenging when the slurry viscosity increases owing to the binder characteristics (Figure 3B) (Li et al., 2018). Billaud et al. performed magnetic templating by adsorbing superparamagnetic Fe3O4 nanoparticles onto graphite flakes. After the application of the magnetic field, the graphite flakes were aligned vertically within the electrode, resulting in a four-fold reduction in tortuosity. This led to an increased Li-ion transport pathway, resulting in a 1.6 to 3 times faster charging rate in the high-loading electrodes (Billaud et al., 2016). The approach of adsorbing magnetic materials onto electrode materials can be applied not only to graphite flakes but also to other materials, thereby expanding the scope of magnetic templating.
Magnetic templating offers various applications depending on the type and application method of the magnetized materials. This allows for the formation of an effective Li-ion transport pathway through the application of a magnetic field without the issues associated with water-based methods, such as phase inversion or ice-templating. However, there is a potential for negative effects on the electrode owing to the need for high-temperature treatments and the use of removers such as kerosene to remove the additives employed in the process. Therefore, it is important to consider magnetized materials that are unreactive or that can provide positive effects within the operating range of the battery.
Biomass templating was inspired by the vertical movement of water and nutrients in the wood vessels of tree stems. Naturally structured wood provides not only low tortuosity but also high mechanical strength, abundant functional groups, and the potential for enhanced electronic conductivity through calcination. Therefore, research on wood-based thick electrodes with improved ion and electron mobilities is ongoing.
Chen et al. fabricated a LFP cathode with a thickness of 800 μm and a mass loading of 60 mg cm-2 using a wood-inspired carbon framework as shown in Figure 3C (Chen et al., 2017). The electrode with embedded LFP nanoparticles exhibited enhanced properties compared to the carbon framework, including an improved surface morphology compared to conventionally cast electrodes with a similar thickness. Moreover, electrochemical evaluations demonstrated improved rate capability and an extended life cycle of over 100 cycles, even at high C rates. Cui et al. also utilized a biomass template to fabricate a thick LCO cathode through a sol-gel process and calcination (Lu et al., 2018). By repeating the process and adjusting the amount of active materials, they achieved a high areal capacity and demonstrated superior rate capability and ion conductivity compared with conventional LCO cathodes.
Biomass templating offers the advantage of providing pre-existing ion pathways for electrode fabrication. However, this raises concerns regarding environmental degradation owing to the use of naturally occurring wood. To address this issue, research should focus on developing carbon frameworks with similar structures, which would require optimization of industrial processes and mass production.
To summarize, the use of templates allows for detailed control over the shape, size, and orientation of the pore microstructure. The ice-templating method enables the formation of pore structures in electrodes that use water as a solvent, simply by varying the temperature conditions, and allows for the control of pore gradients based on the direction of the water crystal growth. Magnetic and biomass templating can be used to adjust the shape and size of pore architectures by selecting magnetized materials and templates. The template method can dramatically improve the Li-ion mobility of thick electrodes; however, it entails additional costs and cathode damage issues owing to changes in the existing process and post-processing of the template.
The template method yields a clear pore structure; however, the amount of active material is reduced by the proportion occupied by the template. To solve this problem, a method of utilizing the electrode manufacturing process through the introduction of additives without using a template or forming a pore architecture through post-treatment of the manufactured electrode was studied.
The bubble formation method utilizes thermal decomposition of a foaming agent to induce bubble formation during electrode drying. Unlike previously described methods, the bubble formation method can generate pores during the drying process without the need for additional procedures. The viscosity of the slurry and the decomposition temperature are the main parameters that influence pore formation through bubble generation. Additionally, size control of the foaming agent offers the advantage of adjusting the channel diameter. Xiong et al. utilized NH4HCO3 as a foaming agent to induce bubble formation at 60 °C through the following reaction (Xiong et al., 2021).
The formed bubbles were subsequently removed during the drying process, revealing cone-shaped pores, which were maintained even after the calendaring process with roll press equipment. Using this method, a thick NCM cathode with a mass loading of 30 mg cm-2 demonstrated a 7-fold increase in capacity compared to that of a conventional electrode (5.0 C). This indicated that the channels formed by the bubbles effectively served as electrolyte pathways (Figure 4A). Although few studies have reported the bubble formation method, it is possible to form pores under the temperature conditions of the drying process without considerable changes to the existing process. Notably, additional effects could be obtained depending on the type of foaming agent used.
FIGURE 4. Thick electrode pore structure design by non-templating methods. (A) The fabrication diagram and SEM images of thick electrodes using the bubble formation. Reproduced with permission from Wiley (Xiong et al., 2021). (B) Schematic diagram and SEM images of thick electrodes via laser patterning. Reproduced with permission from Elsevier (Park et al., 2021b). (C) Schematic diagram and SEM images of thick electrodes via phase inversion. Reproduced with permission from Wiley (Resing et al., 2023). (D) Schematic diagram of preparation process of thick electrodes using patterned blade casting. Reproduced with permission from Wiley (Plateau et al., 2022).
Laser patterning is a method of forming vertical pore architecture in a manufactured electrode by direct etching using a laser. Unlike the methods mentioned earlier, which require the introduction of solvents, additives, or templates, laser patterning can be performed on manufactured electrodes without the need for process changes. This enabled the formation of pores with consistent spacing and thickness (Zhu et al., 2019; Chen et al., 2020; Park et al., 2021b; Song et al., 2021).
Kim et al. utilized a laser-patterning method to fabricate thick LCO cathodes with uniform micropores (thickness of 700 μm) and graphite anodes (thickness of 650 μm) (Park et al., 2021b). The manufactured electrodes exhibited no chemical reactions, thermal damage, or structural damage caused by the laser irradiation. At 0.1 C, the laser-patterned cells exhibited a five-fold increase in areal discharge capacity compared to conventional electrodes. This improvement can be attributed to the increased porosity and reduced tortuosity of both the anode and cathode, resulting in enhanced ion conductivity (Figure 4B). Dasgupta et al. employed layer patterning to manufacture graphite anodes for fast charging (Chen et al., 2020). Using this method, they achieved the formation of vertical pore channels, resulting in capacity retentions of over 97% and 93% after 100 cycles at high C-rates of 4.0 and 6.0 C, respectively. Even after 600 cycles under the same conditions, capacity retentions of 91% and 86% were observed, respectively, indicating that the pores formed through laser patterning served as diffusion pathways for rapid ion transport.
Laser patterning offers the advantage of creating uniform pores in the fabricated electrodes. However, this may lead to material damage during the laser patterning process, potentially accelerating degradation. In addition, the cost implications of implementing this method in manufacturing processes should be considered.
Phase inversion is a method used to form the internal architectures of electrodes by substituting a solvent with a non-solvent. This method is primarily used to form porous structures in separators, and current research is underway to apply it to the formation of internal architectures in electrodes (Huang, 2012; Wang et al., 2021; Huang et al., 2022). The formation of structures via phase inversion can be explained by the ternary phase equilibrium of the polymer/solvent/non-solvent system. When moving inside the binodal curve in the ternary phase equilibrium diagram, a phase separation occurs, leading to the formation of an internal architecture. This pathway is determined by the ratio of the rate at which the solvent is extracted from the interior of the electrode to the rate at which the non-solvent penetrates the electrode. When the electrode slurry is cast and immersed in a non-solvent, only the solvent evaporates from the surface. As soon as the slurry was placed in the non-solvent, the solvent was extracted from the electrode surface (Figure 4C) (Resing et al., 2023). During this process, the slurry ratio increases at the top of the electrode, resulting in the formation of a relatively dense skin layer. Therefore, this skin layer must be removed, which can be achieved by introducing a stainless-steel mesh beneath it or by use of sandpaper to remove it.
Phase inversion research is actively progressing and is not limited to the simple formation of the internal structure of the electrode. Studies are being conducted on methods to further maximize the Li-ion mobility. One approach involves the removal of the skin layer using a stainless-steel mesh to adjust the pore sizes of the upper and lower parts of the electrode and form an asymmetric architecture. For example, small pores formed between the upper part of the stainless-steel mesh and the electrode surface, whereas large pores formed beneath it (Wu et al., 2021a). Zhang et al. confirmed the sizes of the small and large pores within the asymmetric electrode structure by determining the size of the small pores (20–40 μm) and large pores (60–120 μm) (Zhang et al., 2022). Based on this, they compared two cases, where 1) small and 2) large pores were positioned closer to the separator, respectively. The results showed that when the large pores were positioned closer to the separator, they facilitated the effective infiltration of the electrolyte, leading to efficient Li-ion movement. In another study, Wu et al. used a polyacrylonitrile (PAN) polymer with swelling properties in water as a binder in the phase inversion process (Wu et al., 2021b). They encapsulated LFP cathode active materials with PAN, and as the phase inversion progressed, water was absorbed, leading to the formation of gaps through the hydrophobic carbon nanofibers via capillary forces. These gaps act as pores after drying, facilitating electrolyte penetration, and serving as ion transportation pathways. However, phase inversion method is expected that using non-solvents with low levels of Li-ions and transition metal precipitation instead of water would serve as a key approach for designing the internal architecture of the post-coating electrode. The use of non-aqueous solvents in electrode manufacturing for LIBs remains an area that requires further research (Hussain et al., 2023). The exploration of alternative solvents beyond water represents an undiscovered area, and there is a need for additional studies in this area.
Patterned blade casting is a method of forming a micropore structure during the casting process by modifying the blade used in the conventional slurry casting method. This is noteworthy because it allows the formation of pore structures without the need for additional additives or process modifications. Park et al. used a patterned blade to fabricate a high-loading electrode with a 3D pore structure (Plateau et al., 2022). The electrode with the 3D pore structure, which was manufactured with a mass that was 5–6 times higher than that of the conventional electrode, exhibited a 32.5% increase in areal capacity. Compared to the conventional electrode, the microcast electrode demonstrated greater efficiency, improved Li-ion mobility, and potential for manufacturing high-energy-density electrodes (Figure 4D).
Patterned blade casting offers the advantage of easy formation of a pore architecture without considerably changing the process, and efficient Li-ion penetration can be achieved by simply modifying the blade shape. This indicates the possibility of large-scale production of high-loading electrodes with pore structures on a scaled-up pilot scale without major changes in the process. However, because the pore architecture is formed during the slurry casting process, it is necessary to consider variables such as the slurry viscosity, drying temperature, and time to maintain the structure.
The use of NaCl as an additive exploited its solubility in water. In this concept, NaCl is added to the electrode slurry during the electrode manufacturing process and then washed with water after electrode fabrication to create a porous structure at the locations where NaCl is positioned.
Deng et al. investigated the effects of NaCl washing on the porous structure and performance of Li4Ti5O12 (LTO) anodes (Deng et al., 2020). They constructed three electrode layers with different NaCl concentrations, representing 0, 50, and 100% of the total electrode weight, to enhance the electrolyte penetration. Specifically, they formed a gradient of internal pore concentrations within the electrode, starting from the top, at different NaCl ratios. The resulting pore concentration gradient facilitated smooth electrolyte penetration through the lower part of the electrode, leading to an improved electrochemical performance (Figure 5A). Seznec et al. fabricated high loading LFP and LTO electrodes using micro-NaCl prepared through the spark plasma sintering technique (Figure 5B) (Elango et al., 2018). The fabricated electrodes with a thickness of 100 μm exhibited uniform pores and a four-fold increase in areal capacity compared with electrodes produced using conventional methods. This result supports the potential of pore architecture formation to enable the operation of high-loading electrodes and the development of electrodes with high energy densities.
FIGURE 5. (A) Schematic diagram of the preparation process in thick electrodes via leaching of salt. (B) Scheme showing the three steps of fabrication of thick electrodes using NaCl salt as the templating agent. Reproduced with permission from Wiley (Elango et al., 2018).
This approach involves incorporating a water-based process for NaCl removal, which introduces a limitation owing to the potential capacity reduction of specific electrode active materials such as NCM caused using water. If an additive that dissolves in a solvent other than water is used, the side reactions caused by water can be solved. In addition, if the additive is dissolved by the electrolyte in the cell unit, a pore architecture can be formed in situ without any additional processes. However, it is necessary to select additives that do not dissolve in the solvent used in the slurry preparation step and that do not cause side reactions in the battery operating range.
In summary, the non-templating method offers many advantages. Technologies such as laser patterning and patterned blade casting do not require additional processes to remove additives or templates, and it is possible to form detailed pore architectures through laser and blade control. Bubble formation, phase inversion, and salt leaching methods can remove the foaming agent, salt, and non-solvent used in the phase inversion process through conventional drying processes. Therefore, non-templating methods can be considered as the most viable approach for industrialization and mass production. However, it is necessary to carefully consider the physical damage, cost, and energy of the electrode that may occur during pore structure formation.
Previous studies on the formation of the internal structure of electrodes have explored various methods, such as ice-templating, phase inversion, and magnet templating, to achieve vertically aligned structures. Recent research demonstrated a combination of magnet templating and phase inversion methods, leveraging the characteristics and advantages of each method. Notably, Wu et al. conducted a study where they coated the magnetic material, Fe3O4, onto the LFP cathode active material and this was used as the main ingredient for the electrode slurry (Wu et al., 2022). During casting of the aluminum current collector onto the slurry, a magnetic field was applied using neodymium magnets to induce a concentration gradient of the active materials within the electrode. The concentration gradient formed through magnetic templating facilitated penetration of the electrolyte, particularly in the upper region of the electrode, where it was relatively easier for the electrolyte to infiltrate (Figures 6A, B). This addresses the primary issue of the unreacted active materials in the lower region of the cathode. Additionally, the phase inversion method was employed to create internal voids within the electrode, further enhancing electrolyte infiltration and resolving the problem of limited Li-ion movement that occurs in conventional cathodes.
FIGURE 6. (A) Schematic diagram of the LFP gradient in the pore structure of designed thick electrodes. (B) Surface and cross-sectional SEM images of the thick electrodes via magnetic templating and phase inversion. (A,B) Reproduced with permission from American Chemical Society (Wu et al., 2022).
The use of these two methods to form the pore architectures in this study is noteworthy. To reduce the non-reactive regions in the electrode due to Li-ion degradation, a magnetized material coating was applied to induce an increased gradient of the active material distribution in the electrolyte interface direction. Subsequently, a porous structure was formed through phase inversion to address the main issue of ion transport limitations in the electrode. Electrodes fabricated using these two methods provide value by offering a fundamental solution for reducing the tortuosity and additional benefits for the effective utilization of active materials. However, it is necessary to consider the limitations of applying these methods to high-Ni cathodes because of the aqueous processes mentioned in each method section as well as the potential side reactions within the battery operating range when using magnetized materials.
In addition to sluggish Li-ion mobility, thick electrodes have several limitations, such as electronic conductivity, thickness in the wet process, and dispersion of the electrode slurry (Tao et al., 2011; De guzman et al., 2013; Boyce et al., 2021). Although these are currently not major issues, there is a possibility that they will become bottlenecks in the future; therefore, these issues also need improvement. Accordingly, studies are being conducted to overcome the limitations of the slurry casting method based on the viscosity of thick electrodes and to increase the mass loading of active materials using materials that simultaneously act as binders and conductive materials. This section introduces a strategy to improve the thickness of electrodes in addition to the mainstream methods of fabricating electrodes with low tortuosity by forming a pore structure.
Existing wet electrode manufacturing methods suffer from uneven electrode fabrication, where relatively lighter conductive and binder materials tend to migrate towards the top of the electrode by capillary force during the solvent drying processes. This problem is caused by the low adhesion force between the materials and current collector, leading to delamination. Additionally, the cohesive force between the electrode materials is reduced, resulting in the formation of microcracks within the electrode. This becomes more critical for thick electrodes, where the detrimental effects are amplified (Zhang et al., 2021).
To address these issues, research is being conducted to develop thick electrodes using a continuous casting method called multi-layer casting, which involves stacking electrode layers. This method introduces advantages in terms of electron conductivity and ion transport by incorporating differences in the ratio and particle size of the active materials among the electrode layers (Wood et al., 2021; Kang et al., 2022a; Wang et al., 2022). Wang et al. developed a 103.5 μm thick LFP cathode using the multi-layer casting method, with different conductive material contents for the bottom (10, 18 wt%) and the top layer (10, 2 wt%) (Wang et al., 2022). A single-layer LFP cathode with a mass loading of 7.1 mg cm-2 exhibited a capacity of 80 mA h g-1 at 340 mA g-1, while the multi-layer electrode with a top layer conductive material content of 2 wt% and a mass loading of 11.4 mg cm-2 showed a capacity of 130 mA h g-1 (Figures 7A, B). Lee et al. used an Al mesh as a current collector to fabricate multi-stacked NCM622 cathodes (Kim et al., 2021). During the charge-discharge process, the electrochemical reactions at the top of the thick electrodes are dominant because of the gradient of Li-ion diffusion with thickness. To alleviate pore clogging caused by the formation of a SEI from the electrolyte and reactions, active materials with different particle sizes were employed in the top, middle, and bottom regions. The large particles at the top formed wider pores through particle-to-particle contact, enhancing the penetration of Li-ions into the lower region of the electrode. The particle-size gradient electrode exhibited improved cycle performance owing to reduced degradation compared to the uniform-size electrode.
FIGURE 7. (A) Schematic diagram of preparation process in multi-layered designed thick electrodes. (B) Cross-sectional SEM images of single and multi-layer thick electrodes. (A,B) Reproduced with permission from Elsevier (Wang et al., 2022).
The multilayer casting method offers the advantage of manufacturing electrodes without considerable changes to the existing process and can alleviate material inhomogeneity during the drying process by increasing the electrode thickness. The use of a pilot-scale slot-die coater in industries demonstrates its potential for the rapid optimization of multilayer electrodes in an industrial setting. However, there are also shortcomings associated with the multilayer casting method. Firstly, the binder of the bottom layer may be dissolved in the solvent of the top layer slurry during top layer casting, which may reduce the stability of the electrode structure. Drying and calendaring processes are added as the casting process repeats, which can cause an increase in process costs. In addition, compared to the aforementioned methods, the multilayer casting method is difficult to achieve significant changes in tortuosity and porosity. Therefore, To improve this problem, there is a need for additional research to adjust the porosity, tortuosity, and characteristics of the electrode materials in each layer.
In electrodes, the Li-ion mobility decreases with increasing electrode thickness. While Li-ion mobility is the rate-determining step, electronic conductivity is also an important factor, especially at high C rates. Therefore, various research efforts are underway to enhance electronic conductivity, with carbon nanotubes (CNTs) being a representative material (Kiebeke and Gruner, 2007; Landi et al., 2009; De las casas and Li, 2012). The traditional carbon black used in electrodes forms a conductive network known as a zero-dimensional (0D) conductive material. However, 0D conductive materials lack sufficient interactive forces for effective contact with other substances, necessitating the use of additional binders. These binders can act as electrical insulators and hinder electronic movement. The carbon nanotubes with a high length-to-diameter ratio in a one-dimensional form exhibit excellent electrical and mechanical properties. One notable aspect is that the strong interaction between the CNTs enables the formation of a robust infiltration network, allowing the production of electrodes without the need for binders, which contribute to resistance. By eliminating the use of binders, the weight ratio of active materials or conductive additives can be increased, leading to higher areal capacities and improved electronic conductivities. Research utilizing CNTs is ongoing, focusing on the development of thick electrodes utilizing the properties of single- (SWCNTs) and multi-walled carbon nanotubes (MWCNTs) (Luo et al., 2012; Toprakci et al., 2012).
Park et al. used SWCNTs as binders and conductive additives to fabricate Si-based anodes with high areal capacities. When a certain amount of SWCNTs is used, a 2D quasi-continuous CNT network is formed between the Si particles. This network not only localizes the Si particles, but also creates 10 nm-sized pores, enabling electrolyte movement (Figures 8A, B) (Park et al., 2019). Additionally, it addresses the issue of volume expansion. Kim et al. formed a 3D CNT network by utilizing the properties of both SWCNTs and MWCNTs. By mixing 9 wt% MWCNTs and 0.2 wt% SWCNTs, the electronic conductivity improved, and the adhesion between the NCM particles increased without the use of binders.
FIGURE 8. (A) Schematic diagram and cross-sectional SEM images of Si/CNT segregated network composite anodes with mass fraction. (B) Cross-sectional SEM images of Si/CNT network, Si/CNT and NMC/CNT thick electrodes. (A,B) Reproduced with permission from Nature (Park et al., 2019).
This method of employing CNTs offers the advantages of increasing the weight ratio of active materials, enhancing the energy density without the need for binders, and improving electronic conductivity. However, achieving a proper dispersion when using CNTs remains challenging. Agglomeration can occur within an electrode, leading to increased resistance. To address this issue, the utilization of interfacial agents or other methods to enhance CNTs dispersibility is possible, but further research on improving dispersibility is required for commercialization.
In this review, the recent progress in the necessity, problems, and solutions of thick electrodes with an in-depth analysis to gain insight into electrode deterioration and high-energy-density batteries are presented (Figure 9). Thick electrodes reduce the use of dead-volume materials and increase the proportion of active materials, thereby providing high-energy expression and economic benefits. Therefore, the development of thick electrodes is a realistic and reasonable approach to improve the energy densities of batteries without the development of innovative electrode materials. However, the challenges associated with the increase in thickness owing to the increase in the mass loading of active materials must be addressed for the continuous advancement of thick electrodes. During the wet process, the rise of low-mass electrode materials caused by capillary force during the drying process impairs the properties of the electrode, leading to delamination and microcracks. Moreover, the decrease in Li-ion transport throughout the entire electrode, owing to the increase in thickness, accelerates the electrode degradation caused by low ionic conductivity. Among these, sluggish Li-ion transport is well known to be the most dominant factor in the degradation of batteries with thick electrodes; therefore, careful attention is needed.
FIGURE 9. Overview of key factors and various pore structure design methods to improve performance in thick electrodes.
To address these issues, several studies have been conducted to manufacture electrodes with improved properties and ionic conductivities. These approaches can be divided into three main categories: 1) pore structure design with a templating method for enhancing Li-ion transport; 2) pore structure design with a non-templating method for enhancing Li-ion transport; and 3) other methods, including multi-layer electrode design for a robust electrode and electroconductive pathway design with carbon nanotubes.
The fundamental direction of most studies on enhancing electrode performance has been to create pathways within the electrode that allow for easy Li-ion movement. The pore structures formed through the introduction of templates, additives, and processes facilitate smooth Li-ion transport within the electrode during continuous charge/discharge cycles and induce uniform electrochemical reactions. However, certain processes, such as biomass and magnetic templating, may require post-treatment of the templates and additives used for pore structure formation, leading to additional costs and energy consumption. Additionally, for processes such as ice-templating and phase inversion, the limitations related to the use of high-Ni active materials due to water usage should be considered. Furthermore, the excessive loss of electrode materials during the path formation process for enhancing ion conductivity could diminish the purpose of the electrode for high loading and high energy density.
Therefore, in the formation of pore structures, both tortuosity and porosity must be considered important factors. In addition to research on electrode structure formation, studies on fundamental aspects such as material transport behavior and degradation mechanisms within the electrode must be considered. Additional research on improving the adhesion between electrode materials and current collectors, as well as the enhancement of material dispersion during the electrode manufacturing process, should also be continued from a future-oriented perspective. Currently, research on dry electrodes using binder fibrillation without the use of solvents is actively underway, considering the environmental aspects. Although not covered in this review, they are expected to play a substantial role in the future development of high-energy-density electrodes. Finally, there is a need for active communication among lab-scale, pilot-scale, and industrial applications until mass production becomes feasible. The development of precise and mass-production-friendly equipment such as slot-die coaters, 3D printers, and laser ablation devices will provide considerable advantages for enhancing electrode performance. The ongoing interest in electrodes is believed to serve as a link between solutions for next-generation batteries, such as Li metal, ASSBs, Si anodes, and the previous generation of batteries.
KK: Supervision, Writing–original draft, Writing–review and editing. YS: Writing–original draft. BP: Writing–original draft, Writing–review and editing.
The author(s) declare that no financial support was received for the research, authorship, and of this article.
YS, and BP contributed equally to this work. The authors acknowledge the support by the Technology Innovation Program (20017477) funded by the Ministry of Trade, Industry, and Energy (MOTIE, Korea).
The authors declare that the research was conducted in the absence of any commercial or financial relationships that could be construed as a potential conflict of interest.
All claims expressed in this article are solely those of the authors and do not necessarily represent those of their affiliated organizations, or those of the publisher, the editors and the reviewers. Any product that may be evaluated in this article, or claim that may be made by its manufacturer, is not guaranteed or endorsed by the publisher.
Andre, D., Kim, S.-J., Lamp, P., Lux, S. F., Maglia, F., Paschos, O., et al. (2015). Future generations of cathode materials: aan automotive industry perspective. J. Mater. Chem. A 3, 6709–6732. doi:10.1039/c5ta00361j
Aryal, S., Durham, J. L., Lipson, A. L., Pupek, K. Z., and Kahvecioglu, O. (2021). Roles of Mn and Co in Ni-rich layered oxide cathodes synthesized utilizing a Taylor Vortex Reactor. Electrochimica Acta 391, 138929. doi:10.1016/j.electacta.2021.138929
Astaneh, M., Andric, J., Løfdahl, L., and Stopp, P. (2022). Multiphysics simulation optimization framework for lithium-ion battery pack design for electric vehicle applications. Energy 239, 122092. doi:10.1016/j.energy.2021.122092
Ban, C., Li, Z., Wu, Z., Kirkham, M. J., Chen, L., Jung, Y. S., et al. (2011). Extremely durable high-rate capability of a LiNi0.4Mn0.4Co0.2O2 cathode enabled with single-walled carbon nanotubes. Adv. Energy Mater. 1, 58–62. doi:10.1002/aenm.201000001
Billaud, J., Bouville, F., Magrini, T., Villevieille, C., and Studart, A. R. (2016). Magnetically aligned graphite electrodes for high-rate performance Li-ion batteries. Nat. Energy 1, 16097. doi:10.1038/nenergy.2016.97
Blomgren, G. E. (2016). The development and future of lithium ion batteries. J. Electrochem. Soc. 164, A5019–A5025. doi:10.1149/2.0251701jes
Boyce, A. M., Cumming, D. J., Huang, C., Zankowski, S. P., Grant, P. S., Brett, D. J. L., et al. (2021). Design of scalable, next-generation thick electrodes: opportunities and challenges. ACS Nano 15, 18624–18632. doi:10.1021/acsnano.1c09687
Chen, C., Zhang, Y., Li, Y., Kuang, Y., Song, J., Luo, W., et al. (2017). Highly conductive, lightweight, low-tortuosity carbon frameworks as ultrathick 3D current collectors. Adv. Energy Mater. 7, 1700595. doi:10.1002/aenm.201700595
Chen, J., Liu, J., Qi, Y., Sun, T., and Li, X. (2013). Unveiling the roles of binder in the mechanical integrity of electrodes for lithium-ion batteries. J. Electrochem. Soc. 160, A1502–A1509. doi:10.1149/2.088309jes
Chen, K.-H., Namkoong, M. J., Goel, V., Yang, C., Kazemiabnavi, S., Mortuza, S. M., et al. (2020). Efficient fast-charging of lithium-ion batteries enabled by laser-patterned three-dimensional graphite anode architectures. J. Power Sources 471, 228475. doi:10.1016/j.jpowsour.2020.228475
Cronau, M., Paulus, A., Pescara, L. P., Kroll, M., Renz, D., Mekontso, J. A., et al. (2022). What limits the rate capability of ultrathick composite electrodes in lithium-ion batteries? A case study on the thickness-dependent impedance of LiCoO2 cathodes. Batter. Supercaps 5, e202200194. doi:10.1002/batt.202200194
Dang, C., Mu, Q., Xie, X., Sun, X., Yang, X., Zhang, Y., et al. (2022). Recent progress in cathode catalyst for nonaqueous lithium oxygen batteries: a review. Adv. Compos. Hybrid Mater. 5, 606–626. doi:10.1007/s42114-022-00500-8
De guzman, R. C., Yang, J., Cheng, M. M.-C., Salley, S. O., and Simon ng, K. Y. (2013). A silicon nanoparticle/reduced graphene oxide composite anode with excellent nanoparticle dispersion to improve lithium ion battery performance. J. Mater. Sci. 48, 4823–4833. doi:10.1007/s10853-012-7094-7
De las casas, C., and Li, W. (2012). A review of application of carbon nanotubes for lithium ion battery anode material. J. Power Sources 208, 74–85. doi:10.1016/j.jpowsour.2012.02.013
Deng, W., Shi, W., Liu, Q., Jiang, J., Li, X., and Feng, X. (2020). Constructing gradient porous structure in thick Li4Ti5O12 electrode for high-energy and stable lithium-ion batteries. ACS Sustain. Chem. Eng. 8, 17062–17068. doi:10.1021/acssuschemeng.0c04716
Elango, R., Demortiêre, A., Andrade, V., Morcrette, M., and Seznec, V. (2018). Thick binder-free electrodes for Li–ion battery fabricated using templating approach and spark plasma sintering reveals high areal capacity. Adv. Energy Mater. 8, 1703031.
Fang, K., Xie, Q., Wang, C., Qiu, X., Wang, Y., Yang, W., et al. (2021). Understanding the feasibility of manganese substitution for cobalt in the synthesis of nickel-rich and cobalt-free cathode materials. ACS Appl. Energy Mater. 4, 7190–7200. doi:10.1021/acsaem.1c01292
Gao, L., Jin, Y., Liu, X., Xu, M., Lai, X., and Shui, J. (2018). A rationally assembled graphene nanoribbon/graphene framework for high volumetric energy and power density Li-ion batteries. Nanoscale 10, 7676–7684. doi:10.1039/c8nr00692j
He, R., Lei, S., Liu, M., Qin, M., Zhong, W., Cheng, S., et al. (2022). Enhanced dynamic phase stability and suppressed Mn dissolution in low-tortuosity spinel LMO electrode. Energy Mater. Adv. 2022, 34133. doi:10.34133/energymatadv.0004
Hou, S., Gao, T., Li, X., and Wang, C. (2020). Operando probing ion and electron transport in porous electrodes. Nano Energy 67, 104254. doi:10.1016/j.nanoen.2019.104254
Hu, J., Wu, B., Cao, X., Bi, Y., Chae, S., Niu, C., et al. (2020). Evolution of the rate-limiting step: from thin film to thick Ni-rich cathodes. J. Power Sources 454, 227966. doi:10.1016/j.jpowsour.2020.227966
Huang, C., Dontigny, M., Zaghib, K., and Grant, P. S. (2019). Low-tortuosity and graded lithium ion battery cathodes by ice templating. J. Mater. Chem. A 7, 21421–21431. doi:10.1039/c9ta07269a
Huang, C., and Grant, P. S. (2018). Coral-like directional porosity lithium ion battery cathodes by ice templating. J. Mater. Chem. A 6, 14689–14699. doi:10.1039/c8ta05049j
Huang, X. (2012). A lithium-ion battery separator prepared using a phase inversion process. J. Power Sources 216, 216–221. doi:10.1016/j.jpowsour.2012.05.019
Huang, Z., Chen, Y., Han, Q., Su, M., Liu, Y., Wang, S., et al. (2022). Vapor-induced phase inversion of poly (m-phenylene isophthalamide) modified polyethylene separator for high-performance lithium-ion batteries. Chem. Eng. J. 429, 132429. doi:10.1016/j.cej.2021.132429
Hussain, A., Mehmood, A., Saleem, A., Majeed, M. K., Raza, W., Iqbal, R., et al. (2023). Polyetherimide membrane with tunable porous morphology for safe lithium metal-based batteries. Chem. Eng. J. 453, 139804. doi:10.1016/j.cej.2022.139804
Jow, T. R., Delp, S. A., Allen, J. L., Jones, J.-P., and Smart, M. C. (2018). Factors limiting Li+ charge transfer kinetics in Li-ion batteries. J. Electrochem. Soc. 165, A361–A367. doi:10.1149/2.1221802jes
Ju, Z., Zhang, X., Wu, J., King, S. T., Chang, C. C., Yan, S., et al. (2022). Tortuosity engineering for improved charge storage kinetics in high-areal-capacity battery electrodes. Nano Lett. 22, 6700–6708. doi:10.1021/acs.nanolett.2c02100
Jung, W. K., Baek, C., Kim, J.-H., Moon, S., Kim, D. S., Jung, Y. H., et al. (2018). A highly-aligned lamellar structure of ice-templated LiFePO4 cathode for enhanced rate capability. Mater. Des. 139, 89–95. doi:10.1016/j.matdes.2017.11.003
Kaneda, H., Furuichi, Y., Ikezawa, A., and Arai, H. (2021). Effects of aluminum substitution in nickel-rich layered LiNixAl1−xO2 (x = 0.92, 0.95) positive electrode materials for Li-ion batteries on high-rate cycle performance. J. Mater. Chem. A 9, 21981–21994. doi:10.1039/d1ta04312a
Kang, H., Kim, Y. M., Park, B. K., Yang, J. H., Jeong, S., Kim, K. J., et al. (2022b). Effective dual-layer fabrication solution for the lateral axial failure of the electrode in lithium-ion batteries. Int. J. Energy Res. 46, 23973–23983. doi:10.1002/er.8694
Kang, J., Atwair, M., Nam, I., and Lee, C.-J. (2023). Experimental and numerical investigation on effects of thickness of NCM622 cathode in Li-ion batteries for high energy and power density. Energy 263, 125801. doi:10.1016/j.energy.2022.125801
Kang, H., Jia, Y., Zhu, G., Wang, J. V., Huang, B., and Fan, Y. (2022a). How electrode thicknesses influence performance of cylindrical lithium-ion batteries. J. Energy Storage 46, 103827. doi:10.1016/j.est.2021.103827
Kiebeke, A., and Gruner, G. (2007). Carbon nanotube based battery architecture. Appiled Phys. Lett. 91, 144104.
Kim, D.-W., Zettsu, N., and Teshima, K. (2017). Three-dimensional electric micro-grid networks for high-energy-density lithium-ion battery cathodes. J. Mater. Chem. A 5, 22797–22804. doi:10.1039/c7ta05042a
Kim, D.-W., Zettsu, N., and Teshima, K. (2019a). Three-dimensional SWCNT and MWCNT hybrid networks for extremely high-loading and high rate cathode materials. J. Mater. Chem. A 7, 17412–17419. doi:10.1039/c9ta03870a
Kim, D.-W., Kuo, L.-Y., Kaghazchi, P., Yoon, C. S., and Sun, Y.-K. (2019b). Quaternary layered Ni-rich NCMA cathode for lithium-ion batteries. ACS Energy Lett. 4, 576–582. doi:10.1021/acsenergylett.8b02499
Kim, H., Oh, S. K., Lee, J., Doo, S. W., Kim, Y., and Lee, K. T. (2021). Failure mode of thick cathodes for Li-ion batteries: variation of state-of-charge along the electrode thickness direction. Electrochimica Acta 370, 137743. doi:10.1016/j.electacta.2021.137743
Kim, J. H. (2022). Grand challenges and opportunities in batteries and electrochemistry. Front. Batter. Electrochem. 1, 1066276. doi:10.3389/fbael.2022.1066276
Klemens, J., Schneider, L., Herbst, E. C., Bohn, N., Müller, M., Bauer, W., et al. (2022). Drying of NCM cathode electrodes with porous, nanostructured particles versus compact solid particles: comparative study of binder migration as a function of drying conditions. Energy Technol. 10, 2100985. doi:10.1002/ente.202100985
Kraytsberg, A., and Ein-eli, Y. (2012). Higher, stronger, better A review of 5 volt cathode materials for advanced lithium-ion batteries. Adv. Energy Mater. 2, 922–939. doi:10.1002/aenm.201200068
Kuang, Y., Chen, C., Kirsch, D., and Hu, L. (2019). Thick electrode batteries: principles, opportunities, and challenges. Adv. Energy Mater. 9, 1901457. doi:10.1002/aenm.201901457
Kumberg, J., Mþller, M., Diehm, R., Spiegel, S., Wachsmann, C., Bauer, W., et al. (2019). Drying of lithium-ion battery anodes for use in high-energy cells: influence of electrode thickness on drying time, adhesion, and crack formation. Energy Technol. 7, 1900722.
Kwak, W. J., RosySharon, D., Sharon, D., Xia, C., Kim, H., Johnson, L. R., et al. (2020). Lithium-Oxygen batteries and related systems: potential, status, and future. Chem. Rev. 120, 6626–6683. doi:10.1021/acs.chemrev.9b00609
Landi, B. J., Ganter, M. J., Cress, C. D., Dileo, R. A., and Raffaelle, R. P. (2009). Carbon nanotubes for lithium ion batteries. Energy and Environ. Sci. 2, 638–654. doi:10.1039/b904116h
Lee, W., Lee, S., Lee, E., Choi, M., Thangavel, R., Lee, Y., et al. (2022). Destabilization of the surface structure of Ni-rich layered materials by water-washing process. Energy Storage Mater. 44, 441–451. doi:10.1016/j.ensm.2021.11.006
Li, L., Erb, R. M., Wang, J., Wang, J., and Chiang, Y. M. (2018). Fabrication of low-tortuosity ultrahigh-area-capacity battery electrodes through magnetic alignment of emulsion-based slurries. Adv. Energy Mater. 9, 1802472. doi:10.1002/aenm.201802472
Li, S., Tian, G., Xiong, R., He, R., Chen, S., Zhou, H., et al. (2022b). Enhanced homogeneity of electrochemical reaction via low tortuosity enabling high-voltage nickel-rich layered oxide thick-electrode. Energy Storage Mater. 46, 443–451. doi:10.1016/j.ensm.2022.01.035
Li, W., Lee, S., and Manthiram, A. (2020). High-Nickel NMA: A cobalt-free alternative to NMC and NCA cathodes for lithium-ion batteries. Adv. Mater. 32, e2002718. doi:10.1002/adma.202002718
Li, W. (2020). Review—an unpredictable hazard in lithium-ion batteries from transition metal ions: dissolution from cathodes, deposition on anodes and elimination strategies. J. Electrochem. Soc. 167, 090514. doi:10.1149/1945-7111/ab847f
Li, S., Wu, Y., Wang, Z., Xu, J., Ma, T., Chen, L., et al. (2022a). Progress in solvent-free dry-film technology for batteries and supercapacitors. Mater. Today 55, 92–109. doi:10.1016/j.mattod.2022.04.008
Liu, B., Zhang, J.-G., and Xu, W. (2018). Advancing lithium metal batteries. Joule 2, 833–845. doi:10.1016/j.joule.2018.03.008
Lu, L. L., Lu, Y. Y., Xiao, Z. J., Zhang, T. W., Zhou, F., Ma, T., et al. (2018). Wood-inspired high-performance ultrathick bulk battery electrodes. Adv. Mater. 30, e1706745. doi:10.1002/adma.201706745
Luo, S., Wang, K., Wang, J., Jiang, K., Li, Q., and Fan, S. (2012). Binder-free LiCoO2/carbon nanotube cathodes for high-performance lithium ion batteries. Adv. Mater 24, 2294–2298. doi:10.1002/adma.201104720
Lv, Y., Huang, S., Zhao, Y., Roy, S., Lu, X., Hou, Y., et al. (2022). A review of nickel-rich layered oxide cathodes: synthetic strategies, structural characteristics, failure mechanism, improvement approaches and prospects. Appl. Energy 305, 117849. doi:10.1016/j.apenergy.2021.117849
Ma, J., Qiao, Y., Huang, M., Shang, H., Zhou, H., Li, T., et al. (2021). Low tortuosity thick cathode design in high loading lithium sulfur batteries enabled by magnetic hollow carbon fibers. Appl. Surf. Sci. 542, 148664. doi:10.1016/j.apsusc.2020.148664
Myung, S.-T., Maglia, F., Park, K.-J., Yoon, C. S., Lamp, P., Kim, S.-J., et al. (2016). Nickel-Rich layered cathode materials for automotive lithium-ion batteries: achievements and perspectives. ACS Energy Lett. 2, 196–223. doi:10.1021/acsenergylett.6b00594
Park, B. K., Jeong, Y. K., Yang, S. Y., Kwon, S., Yang, J. H., Kim, Y. M., et al. (2021a). Deterioration behavior of aluminum pouch film used as packaging materials for pouch-type lithium-ion batteries. J. Power Sources 506, 230222. doi:10.1016/j.jpowsour.2021.230222
Park, B. K., Jeon, C., Kim, W., Bong, S.-J., Jeong, S., and Kim, H.-J. (2021b). Challenges, laser processing and electrochemical characteristics on application of ultra-thick electrode for high-energy lithium-ion battery. J. Power Sources 482, 228948. doi:10.1016/j.jpowsour.2020.228948
Park, B. K., Kim, H., Kim, K. S., Kim, H.-S., Han, S. H., Yu, J.-S., et al. (2022). Interface design considering intrinsic properties of dielectric materials to minimize space-charge layer effect between oxide cathode and sulfide solid electrolyte in all-solid-state batteries. Adv. Energy Mater. 12, 2201208. doi:10.1002/aenm.202201208
Park, K.-Y., Park, J.-W., Seong, W. M., Yoon, K., Hwang, T.-H., Ko, K.-H., et al. (2020). Understanding capacity fading mechanism of thick electrodes for lithium-ion rechargeable batteries. J. Power Sources 468, 228369. doi:10.1016/j.jpowsour.2020.228369
Park, S.-H., King, P. J., Tian, R., Boland, C. S., Coelho, J., Zhang, C., et al. (2019). High areal capacity battery electrodes enabled by segregated nanotube networks. Nat. Energy 4, 560–567. doi:10.1038/s41560-019-0398-y
Peng, J., Li, W., Wu, Z., Li, H., Zeng, P., Chen, G., et al. (2022). Si/C composite embedded nano-Si in 3D porous carbon matrix and enwound by conductive CNTs as anode of lithium-ion batteries. Sustain. Mater. Technol. 32, e00410. doi:10.1016/j.susmat.2022.e00410
Plateau, T. P., Pham, H., Zhu, Y., Leu, M., and Park, J. (2022). Enabling ultrathick electrodes via a microcasting process for high energy and power density lithium-ion batteries. Adv. Energy Mater. 12, 2201353. doi:10.1002/aenm.202201353
Resing, A. B., Fukuda, C., and Werner, J. G. (2023). Architected low-tortuosity electrodes with tunable porosity from nonequilibrium soft-matter processing. Adv. Mater. 35, e2209694. doi:10.1002/adma.202209694
Reynolds, C. D., Slater, P. R., Hare, S. D., Simmons, M. J. H., and Kendrick, E. (2021). A review of metrology in lithium-ion electrode coating processes. Mater. Des. 209, 109971. doi:10.1016/j.matdes.2021.109971
Rosenman, A., Markevich, E., Salitra, G., Aurbach, D., Garsuch, A., and Chesneau, F. F. (2015). Review on Li-sulfur battery systems: an integral perspective. Adv. Energy Mater. 5, 1500212. doi:10.1002/aenm.201500212
Ryu, M., Hong, Y. K., Lee, S. Y., and Park, J. H. (2023). Ultrahigh loading dry-process for solvent-free lithium-ion battery electrode fabrication. Nat. Commun. 14, 1316. doi:10.1038/s41467-023-37009-7
Sander, J. S., Erb, R. M., Li, L., Gurijala, A., and Chiang, Y. M. (2016). High-performance battery electrodes via magnetic templating. Nat. Energy 1, 16099. doi:10.1038/nenergy.2016.99
Scrosati, B., Hassoun, J., and Sun, Y.-K. (2011). Lithium-ion batteries. A look into the future. Energy and Environ. Sci. 4, 3287–3295. doi:10.1039/c1ee01388b
Shah, A., Ates, M. N., Kotz, S., Seo, J., Abraham, K. M., Somu, S., et al. (2014). A layered carbon nanotube architecture for high power lithium ion batteries. J. Electrochem. Soc. 161, A989–A995. doi:10.1149/2.052406jes
Shen, X., Liu, H., Cheng, X.-B., Yan, C., and Huang, J.-Q. (2018). Beyond lithium ion batteries: higher energy density battery systems based on lithium metal anodes. Energy Storage Mater. 12, 161–175. doi:10.1016/j.ensm.2017.12.002
Shi, P., Zhang, X. Q., Shen, X., Zhang, R., Liu, H., and Zhang, Q. (2019). A review of composite lithium metal anode for practical applications. Adv. Mater. Technol. 5, 1900806. doi:10.1002/admt.201900806
Singh, M., Kaiser, J., and Hahn, H. (2015). Thick electrodes for high energy lithium ion batteries. J. Electrochem. Soc. 162, A1196–A1201. doi:10.1149/2.0401507jes
Song, Z., Zhu, P., Pfleging, W., and Sun, J. (2021). Electrochemical performance of thick-film Li(Ni(0.6)Mn(0.2)Co(0.2))O(2) cathode with hierarchic structures and laser ablation. Nanomater. (Basel) 11, 2962. doi:10.3390/nano11112962
Sun, C., Liu, J., Gong, Y., Wilkinson, D. P., and Zhang, J. (2017). Recent advances in all-solid-state rechargeable lithium batteries. Nano Energy 33, 363–386. doi:10.1016/j.nanoen.2017.01.028
Tao, T., Glushenkov, A. M., Zhang, C., Zhang, H., Zhou, D., Guo, Z., et al. (2011). MoO3 nanoparticles dispersed uniformly in carbon matrix: a high capacity composite anode for Li-ion batteries. J. Mater. Chem. 21, 9350–9355. doi:10.1039/c1jm10220f
Tarascon, J.-M., and Armand, M. (2001). Issues and challenges facing rechargeable lithium batteries. Nature 414, 359–367. doi:10.1038/35104644
Thackeray, M. M., Kang, S.-H., Johnson, C. S., Vaughey, J. T., Benedek, R., and Hackney, S. A. (2007). Li2MnO3-stabilized LiMO2 (M = Mn, Ni, Co) electrodes for lithium-ion batteries. J. Mater. Chem. 17, 3112–3125. doi:10.1039/b702425h
Toprakci, O., Toprakci, H. A., Ji, L., Xu, G., Lin, Z., and Zhang, X. (2012). Carbon nanotube-loaded electrospun LiFePO4/carbon composite nanofibers as stable and binder-free cathodes for rechargeable lithium-ion batteries. ACS Appl. Mater Interfaces 4, 1273–1280. doi:10.1021/am201527r
Tsai, Y.-T., Wu, C.-Y., and Duh, J.-G. (2021). Synthesis of Ni-rich NMC cathode material by redox-assisted deposition method for lithium ion batteries. Electrochimica Acta 381, 138244. doi:10.1016/j.electacta.2021.138244
Väyrynen, A., and Salminen, J. (2012). Lithium ion battery production. J. Chem. Thermodyn. 46, 80–85. doi:10.1016/j.jct.2011.09.005
Wang, H., Li, J., Miao, Z., Huang, K., Liao, Y., Xu, X., et al. (2023). Hierarchical electrode architecture enabling ultrahigh-capacity LiFePO4 cathodes with low tortuosity. ACS Appl. Mater Interfaces 15, 26824–26833. doi:10.1021/acsami.3c04072
Wang, J., Wang, M., Ren, N., Dong, J., Li, Y., and Chen, C. (2021). High-areal-capacity thick cathode with vertically-aligned micro-channels for advanced lithium ion batteries. Energy Storage Mater. 39, 287–293. doi:10.1016/j.ensm.2021.04.030
Wang, Q., Chen, Z., Zhang, X., Lin, C., Feng, Y., and Zhang, Y. (2022). Structural engineering for double-layer high-load LiFePO4 electrode with vertical imparity distribution of conductive additives. J. Power Sources 527, 231106. doi:10.1016/j.jpowsour.2022.231106
Wang, X., Ding, Y. L., Deng, Y. P., and Chen, Z. (2020). Ni-Rich/Co-Poor layered cathode for automotive Li-ion batteries: promises and challenges. Adv. Energy Mater. 10, 1903864. doi:10.1002/aenm.201903864
Wei, X., Guan, Y., Zheng, X., Zhu, Q., Shen, J., Qiao, N., et al. (2018). Improvement on high rate performance of LiFePO4 cathodes using graphene as a conductive agent. Appl. Surf. Sci. 440, 748–754. doi:10.1016/j.apsusc.2018.01.201
Winter, M., Barnett, B., and Xu, K. (2018). Before Li ion batteries. Chem. Rev. 118, 11433–11456. doi:10.1021/acs.chemrev.8b00422
Wood, M., Li, J., Du, Z., Daniel, C., Dunlop, A. R., Polzin, B. J., et al. (2021). Impact of secondary particle size and two-layer architectures on the high-rate performance of thick electrodes in lithium-ion battery pouch cells. J. Power Sources 515, 230429. doi:10.1016/j.jpowsour.2021.230429
Wu, J., Ju, Z., Zhang, X., Quilty, C., Takeuchi, K. J., Bock, D. C., et al. (2021a). Ultrahigh-capacity and scalable architected battery electrodes via tortuosity modulation. ACS Nano 15, 19109–19118. doi:10.1021/acsnano.1c06491
Wu, J., Ju, Z., Zhang, X., Takeuchi, K. J., Marschilok, A. C., Takeuchi, E. S., et al. (2021b). Building efficient ion pathway in highly densified thick electrodes with high gravimetric and volumetric energy densities. Nano Lett. 21, 9339–9346. doi:10.1021/acs.nanolett.1c03724
Wu, J., Ju, Z., Zhang, X., Xu, X., Takeuchi, K. J., Marschilok, A. C., et al. (2022). Low-tortuosity thick electrodes with active materials gradient design for enhanced energy storage. ACS Nano16, 4805–4812. doi:10.1021/acsnano.2c00129
Xiong, R., Zhang, Y., Wang, Y., Song, L., Li, M., Yang, H., et al. (2021). Scalable manufacture of high-performance battery electrodes enabled by a template-free method. Small Methods 5, e2100280. doi:10.1002/smtd.202100280
Xu, M., Reichman, B., and Wang, X. (2019). Modeling the effect of electrode thickness on the performance of lithium-ion batteries with experimental validation. Energy 186, 115864. doi:10.1016/j.energy.2019.115864
Yang, K., Jiang, Y., and Huang, C. (2023). Magnetically aligned NMC811 electrodes for enhancing electrochemical characterization. Electrochem. Commun. 149, 107471. doi:10.1016/j.elecom.2023.107471
Yang, K., Yang, L., Wang, Z., Guo, B., Song, Z., Fu, Y., et al. (2021). Constructing a highly efficient aligned conductive network to facilitate depolarized high-areal-capacity electrodes in Li-ion batteries. Adv. Energy Mater. 11, 2100601. doi:10.1002/aenm.202100601
Yang, S., Zhou, C., Wang, Q., Chen, B., Zhao, Y., Guo, B., et al. (2022). Highly aligned ultra-thick gel-based cathodes unlocking ultra-high energy density batteries. Energy and Environ. Mater. 5, 1332–1339. doi:10.1002/eem2.12252
Yu, X., and Manthiram, A. (2020). Recent advances in lithium–carbon dioxide batteries. Small Struct. 1, 2000027. doi:10.1002/sstr.202000027
Zhan, C., Wu, T., Lu, J., and Amine, K. (2018). Dissolution, migration, and deposition of transition metal ions in Li-ion batteries exemplified by Mn-based cathodes – A critical review. Energy and Environ. Sci. 11, 243–257. doi:10.1039/c7ee03122j
Zhang, X., Hui, Z., King, S. T., Wu, J., Ju, Z., Takeuchi, K. J., et al. (2022). Gradient architecture design in scalable porous battery electrodes. Nano Lett. 22, 2521–2528. doi:10.1021/acs.nanolett.2c00385
Zhang, Y. S., Courtier, N. E., Zhang, Z., Liu, K., Bailey, J. J., Boyce, A. M., et al. (2021). A review of lithium-ion battery electrode drying: mechanisms and metrology. Adv. Energy Mater. 12, 2102233. doi:10.1002/aenm.202102233
Zhao, G., Wang, X., and Negnevitsky, M. (2022). Connecting battery technologies for electric vehicles from battery materials to management. iScience 25, 103744. doi:10.1016/j.isci.2022.103744
Zhu, P., Seifert, H. J., and Pfleging, W. (2019). The ultrafast laser ablation of Li(Ni0.6Mn0.2Co0.2)O2 electrodes with high mass loading. Appl. Sci. 9, 4067. doi:10.3390/app9194067
Keywords: thick electrodes, ion pathway, li-ion battery, electrode design, lithium-ion transport
Citation: Sim YB, Park BK and Kim KJ (2023) Reasonable design of thick electrodes in lithium-ion batteries. Front. Batteries Electrochem. 2:1272439. doi: 10.3389/fbael.2023.1272439
Received: 04 August 2023; Accepted: 21 September 2023;
Published: 29 September 2023.
Edited by:
Min-Sik Park, Kyung Hee University, Republic of KoreaReviewed by:
Janghyuk Moon, Chung-Ang University, Republic of KoreaCopyright © 2023 Sim, Park and Kim. This is an open-access article distributed under the terms of the Creative Commons Attribution License (CC BY). The use, distribution or reproduction in other forums is permitted, provided the original author(s) and the copyright owner(s) are credited and that the original publication in this journal is cited, in accordance with accepted academic practice. No use, distribution or reproduction is permitted which does not comply with these terms.
*Correspondence: Ki Jae Kim, a2lqYWVraW1Ac2trdS5lZHU=
†These authors have contributed equally to this work
Disclaimer: All claims expressed in this article are solely those of the authors and do not necessarily represent those of their affiliated organizations, or those of the publisher, the editors and the reviewers. Any product that may be evaluated in this article or claim that may be made by its manufacturer is not guaranteed or endorsed by the publisher.
Research integrity at Frontiers
Learn more about the work of our research integrity team to safeguard the quality of each article we publish.