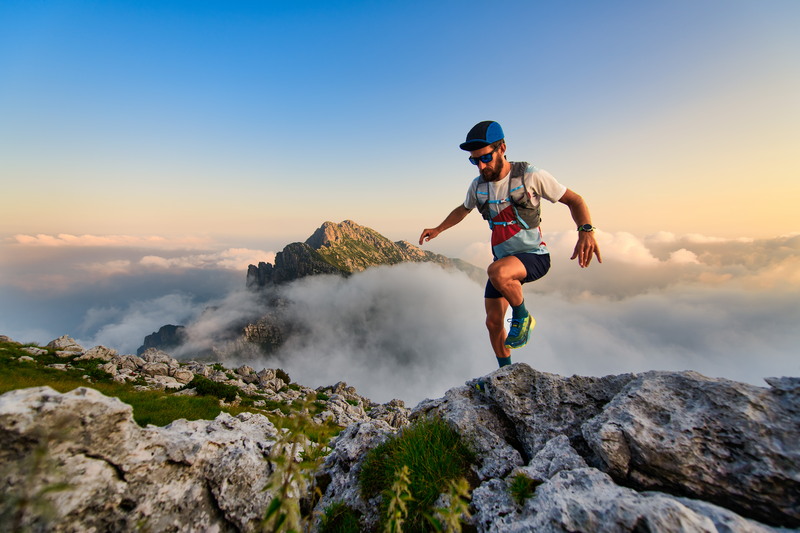
94% of researchers rate our articles as excellent or good
Learn more about the work of our research integrity team to safeguard the quality of each article we publish.
Find out more
FIELD GRAND CHALLENGE article
Front. Batter. Electrochem. , 25 November 2022
Volume 1 - 2022 | https://doi.org/10.3389/fbael.2022.1066276
Batteries are ubiquitous in our society and, as such, are used largely everywhere in our daily lives. The battery, literally an amazing concoction of chemicals brought together to convert chemical energy to electrical energy via electrochemical reactions, are truly exceptional in their functionality and actually operate in a symbiotic fashion. The battery, sometimes called a cell (an individual battery) generally consists of two electrodes with different potentials (i.e., cell voltage), a separator, and an electrolyte. The electrodes, the anode and cathode, are the primary parts and consist of a variety of materials with different functionalities. These mainly affect the specific capacity and cell voltage. The cathode stores a lithium source, while the anode acts as its host. The electrolyte transfers charge-carrying ions from the cathode to the anode and back again. The separator maintains a certain distance between the two electrodes, providing a barrier to short circuiting. Beyond these eye-catching functional features, the designers of the cell also consider energy density, lifetime, and safety.
Since its first invention in 1859, the rechargeable battery has been technically developed from lead-acid to lithium-ion batteries. Interestingly, groundbreaking developments existed during the era of lithium-ion batteries in the 1970s–1980s. In the late 1970s, Dr. M. Stanley Whittingham at Exxon Mobil explored the idea of a rechargeable battery. The electrodes consisted of titanium disulfide and lithium metal, however, they led to many safety concerns. In the 1980s, Professor John B. Goodenough designed a lithium cobalt oxide (LiCoO2) cathode, and Professor Rachid Yazami proved that graphite anode could electrochemically intercalate lithium. Building on these discoveries, Professor Akira Yoshino of Asahi Chemical built the first prototype of a lithium-ion battery in 1985. In early 1990, Sony and Asahi Kasei made tremendous progress toward a commercial-level lithium-ion battery, and, in 1991 released and sold the first true commercialized Li-ion battery, that consisted of a coke anode coupled with a layered LiCoO2 cathode. Since then, major international companies in Japan, Korea, and China have focused on continuously improving the technologies to deliver next-generation batteries. In 2019, three scientists, M. Stanley Whittingham, John B. Goodenough, and Akira Yoshino were awarded the Nobel Prize in Chemistry in recognition of their contributions.
Various types of batteries have been widely applied in devices ranging from portable information technology (IT) devices to electric vehicles (EVs) and grid storage based batteries. Actually, the field moves so fast that it is hard to keep up with the technological advances. In particular, strategic technologies are moving forward quickly towards less-flammable, fast-charging, high-energy-density batteries, and full-scale modules. The batteries used in EVs are classified into three types: soft pouch-, hard cylindrical-, and prismatic-cells. Regardless of their shapes, the functionalities are identical. With the prospect of a complete ban on internal combustion engine vehicles in the next 2 decades, current battery technologies are still insufficient for satisfying the global green economy. A future EV should feature at least 500 km (∼300 miles) of driving range, have a fast-charging capability, and structurally meet non-flammable requirements. It should not be sensitive to environmental temperature fluctuations. In particular, the risks of an organic liquid electrolyte are being gradually exposed and questioned due to increasing car accidents with fire or explosion and situations where extreme outside temperatures can jeopardize safety margins.
From the viewpoint of materials, the utilization of solid electrolytes and lithium metal is highly desirable for next-generation batteries. In the late 1980s, Moli Energy, a Canadian company, was the first to commercialize a lithium-metal rechargeable battery with a molybdenum disulfide cathode and became a main player in the battery market race. In particular, the 2.2 V Molicel is Moli’s flagship battery, earmarked for NTT mobile in Japan. In terms of the battery technology, however, there was a major safety hazard in their batteries. Eventually, dendritic lithium growth and significant volume change became uncontrollable during short-term charge and long-term discharge, leading to internal short-circuits, explosions, and catching fire. The use of lithium metal faded out in the industry until another groundbreaking technology was achieved. To commercialize these lithium-metal batteries, inevitable growth of lithium dendrite should be suppressed. The essential key approaches are to increase ionic conductivity in solid electrolyte interphase layer and mechanical stability through electrolyte additive, separator design, and interlayer coating.
In a conventional battery, graphite or graphite-silicon composite is used as the anode, and lithium layered or spinel metal oxides or lithium metal phosphates are selectively used in terms of cost, performance, and safety. The anode still faces limitations or challenges, however, in meeting the need for high-energy density because of the low theoretical capacity of graphite (372 mAh g-1). Silicon (4,200 mAh g−1) is one of the more promising anodes, but it has unavoidable volume expansion and poor thermal stability. Both silicon suboxide (SiOx, 0 < x < 2) and silicon composites have also been tried, but with marginal success. To solve the underlying technical issue, bare lithium metal has recently been revived as an ideal electrode due to its high theoretical capacity (3,860 mAh g−1), low redox potential (- 3.04 V vs standard hydrogen electrode), and low density (0.534 g cm−3). Lithium metal is essential for the solid-state battery. The use of solid electrolyte is a primary technique to overcome safety issues. This configuration minimizes any side reactions and eliminates the explosion risk derived from the organic electrolyte. To reach the commercial-level, sulfide-based argyrodite-type electrolyte with the chemical formula Li6PS5X (X = Cl, Br, I) needs further enhancement of its operational stability against moisture to suppress hydrogen sulfide evolution. The ionic conductivity of argyrodite-type solid-electrolyte was estimated to be around 10–3 S cm−1. Such a value is comparable to that of the typical organic carbonate-based liquid electrolytes.
Also, cost-effective batteries, i.e., non-lithium batteries, are alternatively based on technologies beyond lithium-ion, such as sodium-ion, zinc-ion, and potassium-ion batteries. This is because insufficient natural resources and soaring prices for Li-ion batteries would accelerate research to find a new cell chemistry. Just recently, the lithium-ion battery market has rapidly increased, so lithium has reached a high price. More environmentally friendly storage systems are also needed to meet our requirements. Consumption of lithium resources is proportional to market requirements. Lithium extraction has a negative side, however, on the way to our battery future. Mining directly leads to soil degradation and water shortages, and destroys the local ecosystem. This would rapidly increase global warming, especially in South Africa and Chile. In the case of the cobalt used in the cathode, extraction from mining alone cannot meet future consumption demands. Recycling technology to deal with the battery materials and studies on batteries made from abundant materials should be considered. In 1997, Professor Goodenough invented lithium iron phosphate (LiFePO4) batteries. The energy density of lithium nickel manganese cobalt oxide (LiNiMnCoO2, NMC) as cathode is much higher than that of lithium iron phosphate by a factor of 50%. This material is well commercialized, but the aim of an abundant, non-toxic, and environmentally friendly cathode still remains elusive in layered transition metal oxide cathodes. From raw materials costs, both iron and phosphorus are much cheaper than other elements, leading to cost reduction of the entire battery systems. New types of designs are underway to overcome the drawbacks of low energy-density.
For portable IT devices and EVs, fast-charging capability has become an important factor for widespread adoption. Without a new electrode design, the performance of most batteries fades out due to unexpected degradation of the two electrodes, particularly when stored at high states-of-charge, exposed to elevated temperatures, and/or experience exceedingly fast high-speed charging processes. Sluggish interfacial kinetics is the main reason for a slow charging time. When a battery is quickly charged, lithium ions tend to be locally plated on the graphite surface, leading to blockage of lithium intercalation. By stabilizing the interfacial reaction between the graphite and the organic electrolyte, particularly against metal plating, the migration of lithium-ions can be further improved. A solid electrolyte interphase which is passivating against further electrolyte decomposition is present, as found by Professor Emanuel Peled. Because the electrolyte is thermodynamically unstable with respect to the low voltage of the graphite (or lithiated graphite) anode, this SEI unavoidably exists during cell operation, and must be maintained for long-term cycling. The electrodes will react with an organic electrolyte to form the heterogeneous phases in a thin layer, leading to the consumption of the organic electrolyte used in the cell. Even if such a layer has ionic conductivity, it shows almost no electronically conductive properties. We need to understand these complex reactions, while moving forward with solid-state electrolytes.
A market research company projects that the global battery industry will grow at a compound annual growth of more than 10% up to 2027. If the nation’s battery industry wishes to capture a sizeable share of this valuable market, it must have access to novel research on battery materials. We have no doubt that rechargeable batteries can obviously solve the energy crisis and environmental concerns. Beyond current battery technologies, crucial features of and challenges for batteries and their electrochemistry still remain as follows: (i) high-energy density, (ii) solid-state electrolyte, (iii) cost-conscious, (iv) fast-charging, and (iv) cycle and calendar lifetime. All these features strongly depend on the design and chemistry of electrode materials. Our continuous efforts should pave the way to solve all limitations of current battery technologies in the near future. I would like to invite all of you to participate in Frontiers in Batteries and Electrochemistry, aimed at all aspects of battery materials, as well as modelling, electrochemistry, integration of systems, and supercapacitors, to contribute to future energy research and to a society devoid of fossil fuels and ultimately stemming our ensuing climate crisis.
The author confirms that he is the sole author of this work and has approved it for publication.
The author declares that the research was conducted in the absence of any commercial or financial relationship that could be construed as a potential conflict of interest.
All claims expressed in this article are solely those of the authors and do not necessarily represent those of their affiliated organizations, or those of the publisher, the editors and the reviewers. Any product that may be evaluated in this article, or claim that may be made by its manufacturer, is not guaranteed or endorsed by the publisher.
Keywords: batteries, electrochemistry, fast-charging, high-energy density, solid electrolyte
Citation: Kim JH (2022) Grand challenges and opportunities in batteries and electrochemistry. Front. Batteries Electrochem. 1:1066276. doi: 10.3389/fbael.2022.1066276
Received: 10 October 2022; Accepted: 16 November 2022;
Published: 25 November 2022.
Edited by:
Christopher Johnson, Argonne National Laboratory (DOE), United StatesCopyright © 2022 Kim. This is an open-access article distributed under the terms of the Creative Commons Attribution License (CC BY). The use, distribution or reproduction in other forums is permitted, provided the original author(s) and the copyright owner(s) are credited and that the original publication in this journal is cited, in accordance with accepted academic practice. No use, distribution or reproduction is permitted which does not comply with these terms.
*Correspondence: Jung Ho Kim, amhrQHVvdy5lZHUuYXU=
Disclaimer: All claims expressed in this article are solely those of the authors and do not necessarily represent those of their affiliated organizations, or those of the publisher, the editors and the reviewers. Any product that may be evaluated in this article or claim that may be made by its manufacturer is not guaranteed or endorsed by the publisher.
Research integrity at Frontiers
Learn more about the work of our research integrity team to safeguard the quality of each article we publish.