- School of Engineering, Indian Institute of Technology Mandi, Mandi, India
Methane is a popular alternative fuel for internal combustion engines due to its availability in many forms such as methane hydrates, natural gas, biogas, compressed natural gas, liquid natural gas, synthetic natural gas, and pipe natural gas. Methane can be effectively used in existing diesel engines in dual-fuel mode with few modifications. Dual-fuel technology helps bridge existing conventional fuel and alternative gaseous fuel-powered conventional engines. The properties of methane, including its higher calorific value, abundant diffusion, and wider flammability limit make it a suitable fuel for improving the performance of compression ignition engine in dual-fuel mode. Methane-diesel dual-fuel engines are an effective technology for reducing vehicle pollution and partially replacing conventional fuels for transport applications. Therefore, a comprehensive review is needed to document the various pathways for the utilization of methane in dual-fuel engines. This study critically compared the combustion, noise, performance, and emission characteristics of various methane-fueled engines to identify the current challenges and future perspectives for the synergistic use of methane to reduce emissions from internal combustion engines.
Introduction
The consumption rates of petroleum products are increasing daily as the number of end-users is increasing. However, petroleum sources are limited (tepco, 2009) and are expected to be completely depleted in the next few decades. In 2018, the Organization of Petroleum Exporting Countries (OPEC) reported 1497.98 billion barrels of crude oil reserves worldwide (Organization of the Petroleum Exporting Countries, 2020). Recent studies have revealed that the global oil demand will rise to 5.7 million barrels per day between 2019 and 2025 (opec, 2020; IEA, 2020). However, the limited oil reserves can meet this increasing demand for only 53 years (csmonitor, 2014). Additionally, the increasing prices of petroleum products and importing oil adversely affect the gross domestic product (GDP) of net petroleum-importing countries (Quartz, 2014). The 2019 British Petroleum Report showed that India imported 227.5 million tons of crude oil in 2018 (Goss, 1982), at a cost of approximately 125 billion dollars (Abdi, 2018). Additionally, pollutant emissions from the growing transport sector threaten human life. Post-treatment devices and fuel injection equipment have been applied for the efficient solution of emission problems in the last half-decade (Tripathi et al., 2017a; Tripathi et al., 2017b; Nag et al., 2017; Tripathi and Dhar, 2017). These devices and equipment are efficient but increase the number of mechanical components in vehicles, in addition to causing space challenges and increased prices. Therefore, recent research in the transport sector has also attempted to find clean and efficient alternate fuels for conventional internal combustion engines (Mao et al., 2020; Stančin et al., 2020). Blending and dual-fuel mode options bridge diesel fuel and alternative gaseous fuels. Alternative transport fuels are fuels other than gasoline and diesel. In recent decades, researchers have explored alternative fuels such as hydrogen, methane, biodiesel, and alcohols (Shukla et al., 2017; Sharma and Dhar, 2018a; Tripathi et al., 2020a). India can be a major producer of methane-based fuels if large-scale gas hydrate processing and biogas purification is efficiently implemented (Demirbas, 2010). With 87–96% methane and a fraction of ethane, propane, iso-butane, and butane, India produced 9858.471 million metric standard cubic meters of natural gas in 2016–2017 (State-wise Gross, 2014).
The use of gaseous fuels in vehicles is an efficient method for reducing harmful pollutants (Sharma and Dhar, 2018b; Nag et al., 2019a; Tripathi et al., 2019). Among various available gaseous fuels, methane and hydrogen have emerged as preferred choices for engine application. Compared to hydrogen, methane is a highly attractive option as 1) it requires less space for on-board storage and fewer leakage problems due to its comparatively higher density, 2) it is less hazardous and required less safety equipment owing to its higher ignition energy compared to that of hydrogen, and 3) it is easily and abundantly available in nature compared to hydrogen. The large-scale use of methane or natural gas in existing internal combustion engine fleets provides in many pollution mitigation advantages. In most of the world, diesel is expected to continue as a major transport fuel at least for two decades. The reduction of city pollution is an urgent requirement in most urban habitats worldwide. In the context of assessing the role of gaseous fuels as a bridge and developing a synergistic strategy to make existing IC engines cleaner, along with other developments in engine technology, this study focused on methane-diesel dual-fuel combustion engines.
Methane availability
Methane can be produced for engine utilization from both non-renewable and renewable energy sources. Methane as natural gas is abundantly available in nature in the form of fossil fuels. Thus, methane is a highly attractive choice for fueling future internal combustion engines. The main sources of methane availability are discussed in the following subsections.
Non-renewable sources of methane: Natural gas
Methane is a primary component of natural gas (Table 1). Natural gas is formed by the decomposition of animal matter and plants under high pressure by anaerobic bacteria.
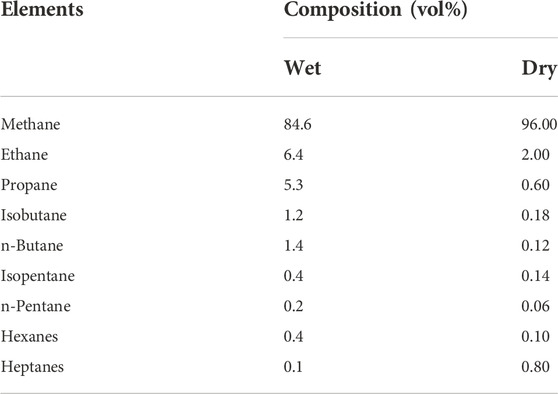
Table 1. Natural gas composition (Faramawy et al., 2016).
There are three types of natural gas: 1) biogenic, 2) primary thermogenic, and 3) secondary thermogenic. Biogenic natural gas is formed at low temperatures from organic matter. It is dry and contains mainly methane as the primary component. Primary thermogenic natural gas is produced from the thermal cracking of organic matter into hydrocarbon, liquids, and gases. Secondary thermogenic natural gas is produced from the thermal cracking of oil into gases and pyrobitumen. Thermogenic natural gas is formed at a higher temperature and depth. It contains methane as well as ethane, butane, propane-like wet gas components, and condensate hydrocarbon (pow-methane). Recent studies show that natural gas is a predominate alternative fuel among available choices and shows promise as a fuel owing to its 1) easy availability, 2) comparatively lower cost, 3) higher calorific value, 4) lower hazard compared to hydrogen, 5) lower production of NOx and soot emission by diesel engines in dual-fuel mode, and 6) existing infrastructure for purification, transportation, and refilling in many countries (Semin and Bakar, 2008; Shah et al., 2011; Alcheikhhamdon and Hoorfar, 2016; Faramawy et al., 2016; Wei and Geng, 2016; You et al., 2020). Natural gas is currently widely used in various forms such as CNG, bio-CNG, LNG, PNG, and SNG. Compressed natural gas (CNG) is natural gas stored at 20–25 mega Pascal pressure in cylindrical or spherical vessels. The use of CNG in the transport sector reduces the problem of pollutants but increases fuel storage and distribution costs. The number of CNG vehicles is increasing by 30% per year (energy, 2016). Bio-CNG is a step ahead among CNG applications in diesel engines as it supplies methane from renewable sources (Channappagoudra et al., 2020). Liquid natural gas (LNG) is natural gas that is cooled to −162°C and 25 kilo Pascal pressure to condense it into liquid form that is stored in vessels for transportation. LNG results in a higher reduction in volume compared to CNG. LNG has a 1.4–2.4-fold higher energy density compared to CNG (Comparison, 1992). LNG provides a solution for large-scale methane supply in urban areas (Hribar et al., 2019). Piped natural gas (PNG) is natural gas supplied through a pipe. Compared to LPG (liquid petroleum gas), PNG is economical and safe as it is piped at 21 millibars (200-fold lower than LPG) (Gujarat, 2019). Synthetic natural gas (SNG) is the natural gas produced from coal, biogas, wood, or other organic matter and mainly contains methane as its primary component (Kopyscinski et al., 2010).
Renewable sources of methane: Biogas
Biogas is produced from the decomposition of food, human, and animal wastes in an oxygen-free environment (Bedoić et al., 2020). Methane is the main component of biogas (Table 2).
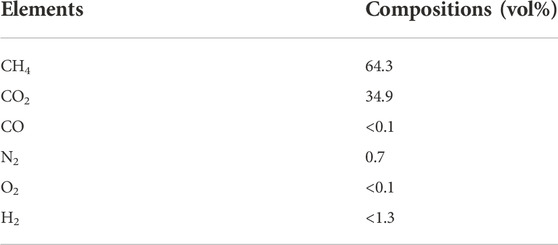
Table 2. Biogas composition (Kuo and Dow, 2017).
Biogas is produced in four stages. In the first stage, organic polymers are broken down. In the second stage, organic acid, NH3, H2, and CO2 are formed by acidogenic bacteria. In the third stage, H2, NH3, CO2, and CH3COOH are formed through organic acids. In the fourth stage, CH4 and CO2 are formed. India and China have been focusing on biogas production since 1960. India mainly utilizes floating drum digesters, while China mainly utilizes fixed dome digesters for biogas production. Mittal et al. reported that India produced 2.07 billion m3/year of biogas in 2018. India has 5 million family biogas plants, 400 biogas off-grid plants, and 56 operational biogas plants (Mittal et al., 2018). Since 2006, biogas has emerged as the predominant vehicle fuel in terms of market demand in Sweden, compared to natural gas (Hameedi, 2018). Recent studies have revealed that biogas is preferred for dual-fuel engines over single-fuel engines (Deheri et al., 2020; Khayum et al., 2020). The methane content in biogas can be increased by 1) increasing the volatile solid ratio in manure, 2) the addition of organic and inorganic chemicals in the slurry, 3) the pretreatment of manure, 4) the proper selection of temperature ranges for mesophilic and thermophilic digestion, and 5) enhancing the mixing process to increase the contact between the substrate and the bacteria population, 6) creating artificial conditions in which bacteria can grow (Goswami, 2004). Biogas is upgraded into bio-CNG through various techniques, including 1) physical and chemical absorption, 2) pressure swing adsorption, 3) membrane separation, 4) cryogenic separation, and 5) water scrubbing (Singhal et al., 2017). Gielen et al. predicted that 63% of the total global energy supply will be achieved through renewable energy by 2050. More than 30% of renewable energy will be achieved through biomass; the remaining renewable energy will be provided through wind, solar, hydro, geothermal, and other sources (Gielen et al., 2019).
Hydrates: A promising rich source of methane
Other than natural gas and biogas, methane hydrate is also an abundant source of methane. Methane hydrate has an ice-like crystalline solid in which a methane molecule is trapped among H2O molecules. The melting of this ice releases CH4 (King). Methane hydrate is the highest methane density source (1 m3 of melted methane hydrate releases approximately 160 m3 of CH4 gas). Some estimates report the presence of 1011 billion m3 of methane in the form of methane hydrate beneath the oceans and permafrost (eniscuola). According to the U.S. Geological Survey, the North Slope of Alaska contains gas hydrate reserves of around 25.2–157.8 trillion cubic feet, with mean values of around 85 trillion cubic feet (hydrate, 2008). Methane hydrate (CH46H2O) is formed at low temperatures (-15°C) and high pressure (20 bar) in the bulk presence of CH4 and H2O molecules (eniscuola).
Methane as an alternative fuel for IC engines
The predicted high demand for methane has motivated researchers to upgrade the features of methane from those of NG and develop more CNG/PNG/L/NG industries with safe and economical distribution networks (Purwanto et al., 2016). Methane has no carbon-carbon bonds and the lowest carbon-to-hydrogen ratio among abundantly available hydrocarbons. These chemical properties make methane a clean and promising fuel for internal combustion engines. Methane-enriched fuel-powered vehicles have lower life cycles of greenhouse gas emissions compared to those of traditional diesel fuels (Ou et al., 2012). The ringing intensity, which is the main cause of noise, has been reduced with natural gas supplementation in diesel engines to reduce the peak pressure during combustion (Kirsten et al., 2016). The knocking tendency has been reduced with natural gas supplementation in diesel engines to reduce the chances of abnormal combustion by premixing natural gas with air (Kirsten et al., 2016). The adiabatic flame temperature that is directly related to the number of carbon atoms is lower for natural gas compared to diesel fuel, which results in lower NOx emissions (Glaude et al., 2010). Karim suggested that the high compression ratios in diesel engines support methane supplementation (Karim, 2003a). Karagoz et al. reported that the optimum natural gas supplementation in diesel engines resulted in lower emissions of smoke, soot, and NOx compared to pure diesel operation (Karagöz et al., 2016). Most of the newly discovered alternative fuels have challenges in ensuring large-scale supply due to limited production; in contrast, methane does not have these challenges as it has large reserves in nature in the form of natural gas (Eren and Polat, 2020). Moreover, methane can be produced in large quantities from biogas, which is an efficient technique for the management of household and animal wastes (Tabatabaei et al., 2020a; Tabatabaei et al., 2020b; Guilera et al., 2020; Qyyum et al., 2020). Methane can also be utilized in existing engines without much modification (Tripathi et al., 2020a; Tripathi et al., 2020b; Tripathi et al., 2020c). The essential features of methane are described in Table 3 (Di Iorio et al., 2016a; Di Iorio et al., 2016b).
Methane has poor combustion properties, including a high specific heat capacity, slow burning rate, less reactivity, low energy storage density compared to liquid fuels, high compression ratio requirement for auto-ignition, and high auto-ignition temperature compared to diesel fuel (Di Iorio et al., 2017). These poor combustion properties may be encountered when considering methane as a fuel for compression ignition engines. Methane can be injected in both spark and compression ignition engines. However, the injection of methane in spark ignition engines is limited because of the 1) low volumetric efficiency of methane compared to gasoline fuel, 2) knock tendency of methane due to its high octane number, 3) high compression ratio of methane (Song et al., 2017). There are no such limitations in compression ignition engines. Direct injection and port fuel injection are popular techniques for methane injection in compression ignition engines. The direct injection of methane is challenging due to the complexity of operation and durability of injectors. The port fuel injection of methane is an easy process in which an existing compression diesel ignition engines is slightly modified to a dual-fuel compression ignition engine. In port fuel injection, methane is naturally aspirated with air through the intake manifold based on the energy share replacement of diesel fuel through the volume displacement of air (Tripathi et al., 2020a; Tripathi et al., 2020b; Tripathi et al., 2020c). In this technique, the injection control of methane and diesel is independent. In the absence of methane, the vehicle can operate on pure diesel. This feature encourages large-scale implementation with minimal modification to existing engines and motivates researchers to further explore methane dual-fuel engines as a bridge between conventional diesel-powered vehicles and future methane-powered vehicles. In the transportation sector, natural gas-fueled vehicles predominate because 1) natural gas does not require refining: normal processing is sufficient for its direct use as a fuel in engines; 2) natural gas can be supplied through pipe networks; thus, there are no challenges related to storage, road traffic, and other interruptions in the supply system; 3) natural gas does not experience evaporation loss, contrary to most liquid fuels, 4) methane is the cheapest fuel among diesel, petrol, and LPG; moreover, the use of methane is economical, at 45% relative to diesel, 65% relative to petrol, and 30% relative to LPG; 6) CO2 emission is reduced by 25% compared to petrol-powered vehicles; 7) methane does not emit large-sized particulate matter, benzene, and aromatic hydrocarbon; 8) the emissions of CO, NOx, and SO2 are reduced compared to those of traditional fuel (Grigg, 2011). Methane is a highly promising upcoming fuel. Therefore, many cities are installing pipelines for methane delivery with minimum losses and leakage (Ahmadian Behrooz, 2016). The subsequent sections of this paper review the various methods of methane utilization in compression ignition engines, with particular emphasis on dual-fuel methane engines.
Life cycle assessment of methane-fueled engines
The life cycle assessment (LCA) technique is helpful in determining the environmental aspects associated with each stage of the life cycle of any product or service (US EPA, 2006). The stages of the life cycle are the extraction of raw material, production, use, and disposal of any product or service. This section discusses the LCA of methane-fueled vehicles. In their LCA, Zhiyi and Xunmin (2019) reported that LNG and CNG-powered heavy-duty trucks showed 11.17 and 5.18% lower life cycle greenhouse gas emissions compared to those in diesel-powered trucks. They also concluded that the production and supply of natural gas cause up to 86.7% of the total life cycle methane emissions. Bengtsson et al. performed a comparative LCA of LNG and heavy fuel oil (Bengtsson et al., 2011), reporting that the use of LNG reduced NOx emissions by up to 90% and global warming by up to 20% compared to heavy fuel oil. Yuan et al. reported that passenger cars and trucks fueled with either CNG or LNG resulted in maximums of 17 and 15% reductions in life cycle greenhouse gas emissions compared to traditional fossil fuels (Yuan et al., 2019). Methane leakage was 2% for the entire life cycle of greenhouse gases. Domestic natural gas supply chains comprise 67% of total methane leakage and its transportation contributes 42–86% of methane leakage. Moreover, in the assessment of life cycle costs per vehicle, the replacement of diesel with CNG in light-duty trucks resulted in a life cycle greenhouse gas emission of 34% and a savings of 30,000 dollars (Shahraeeni et al., 2015). Papong et al. divided the life cycle of bio-CNG into six steps (Papong et al., 2014): 1) digestion, 2) cleaning and upgrading, 3) compression, 4) transportation, 5) refueling gas stations, and 6) combustion or use in internal combustion engines. Among these steps, the upgrading step was the main energy consumption step, which consumes 42–48% of the total energy consumption. The life cycle analysis of greenhouse gases showed that methane leakage was the main cause of greenhouse gas emissions. This condition also occurs during the upgrading and digestion steps (Papong et al., 2014). Natural gas showed the lowest life cycle for GHG emission compared to conventional diesel and petrol fuel (Biernat et al., 2021) (Figure 1).
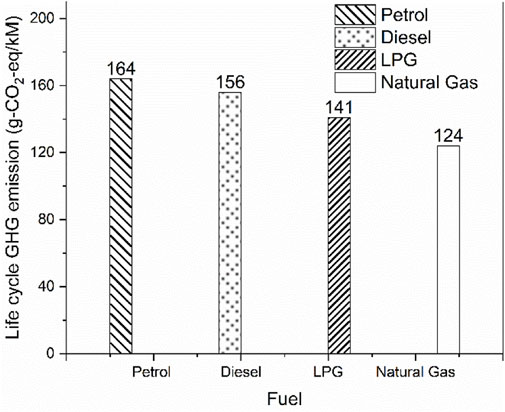
Figure 1. Life cycle assessment of GHG emissions for different fuels (Biernat et al., 2021).
Methane-fueled engines
Methane has generally been used in spark ignition engines in single-fuel mode because of its higher auto-ignition temperature. Spark ignition engines have limited compression ratios, which also limits engine efficiency. Once produced, the spark is not sufficient to burn all methane since methane has a lower flame speed (Gambino et al., 1991). Although twin spark plugs may help solve this problem, diesel dual-fuel mode has efficiently solved this problem by providing several ignition sources. These multiple ignition sources provide different diesel-air packets inside the combustion chamber. Methane spark ignition engines have problems with combustion stability and power generation, which may be effectively reduced with the exhaust gas recirculation technique; however, this reduces the engine efficiency (Blarigan et al., 2012). Methane spark ignition engines have 10% less power and 3% less thermal efficiency compared to those in gasoline engines (Gonca et al., 2018). Methane spark ignition engines also have problems with pumping losses and poor part-load efficiency (Königsson, 2014). Methane single-fueled compression ignition engines have not gained acceptance for the following reasons: 1) the higher compression ratio; 2) the need for significant modifications to the ignition system and cylinder designs; 3) the higher auto-ignition temperature and the lower reactivity of methane 4) the higher specific heat capacity; and 5) the slower burning rate. Methane dual-fuel engines have the potential to solve these problems by supplementing methane with other fuels that can compensate for the poor combustion properties of methane.
Methane-diesel dual-fuel engines
A comparison of methane dual-fuel compression and spark ignition engines showed higher efficiency and lower emissions in methane dual-fuel compression ignition engines (Karim, 1982). Methane is inducted into compression ignition engines by direct or port fuel injection methods. Methane direct injection with diesel fuel in compression ignition engines requires a special injector to handle both methane and diesel fuel injection. Brown et al. reported that a pilot quantity of diesel is injected to increase the in-cylinder temperature and that the main diesel fuel injection is performed later for the ignition of methane for more efficient combustion in M-DDF engines (Brown et al., 2011). Methane direct injection with diesel fuel in compression ignition engines is not preferred because of 1) a lack of fuel flexibility, which prevents engines from running in single-fuel mode if diesel is not available, which is not a problem in port-fuel mode in DDF engines, as it is possible to run the engine in single diesel fuel mode, 2) un-throttled operation that corresponds to improper mixing as directly injected methane in the engine cylinder does not get adequate time for mixing and instead participates in diffusion flame combustion, 3) complicated and costly processing, and 4) high emission levels of CH4, NOx, and particulate matter (Königsson, 2014). In port fuel-injected M-DDF engines, methane is naturally aspirated with air through the intake manifold (Figure 2). The quantity of supplied methane depends on the energy share of methane and diesel fuel, which is achieved by the displacement of air volume intake. The injection controls of methane and diesel are independent. In the absence of methane, the vehicle can run on diesel fuel alone, which makes it suitable for large-scale commercial adaptation with minimum modification of the existing fuel supply and engine infrastructure for diesel engines. The following section provides a detailed analysis of port fuel-injected M-DDF engine combustion, performance, and emissions.
M-DDF engine characteristics
Comparisons of methane injection strategies
Figure 1 illustrates the different arrangements for methane injection into engine cylinders. In methane single-fuel spark ignition engines, a homogeneous mixture of methane and air is sucked into the engine cylinder and combustion is initiated with a spark plug. The same process occurs in gasoline spark ignition engines with methane supplementation. However, the supplementation of methane in diesel engines cannot replace diesel completely due to the higher auto-ignition temperature of methane. Table 4shows the comparisons of natural gas combustion during different engine cycles. Although natural gas supplementation in the stoichiometric Otto cycle has lower efficiency, it has the benefit that a three-way catalytic converter (a non-selective catalytic reduction device) can be effectively used to reduce both NOx and CO emissions. Natural gas combustion in lean burn Otto cycle engines is generally initiated by a spark plug but micro pilot diesel fuel. Glow plugs are also an option. Natural gas supplementation in dual-fuel premixed cycles requires a minimum of 15% pilot diesel fuel supplementation to start the ignition of injected methane (Jääskeläinen, 2019). The direct injection of natural gas requires high pressure, which is why these engines also known as high-pressure direct injection (HPDI) gas-diesel engines. Among these options, port fuel-injected natural gas-diesel dual-fuel engines are preferred as they require fewer modifications for the conversion of existing diesel engines into dual-fuel engines (Jääskeläinen, 2019).
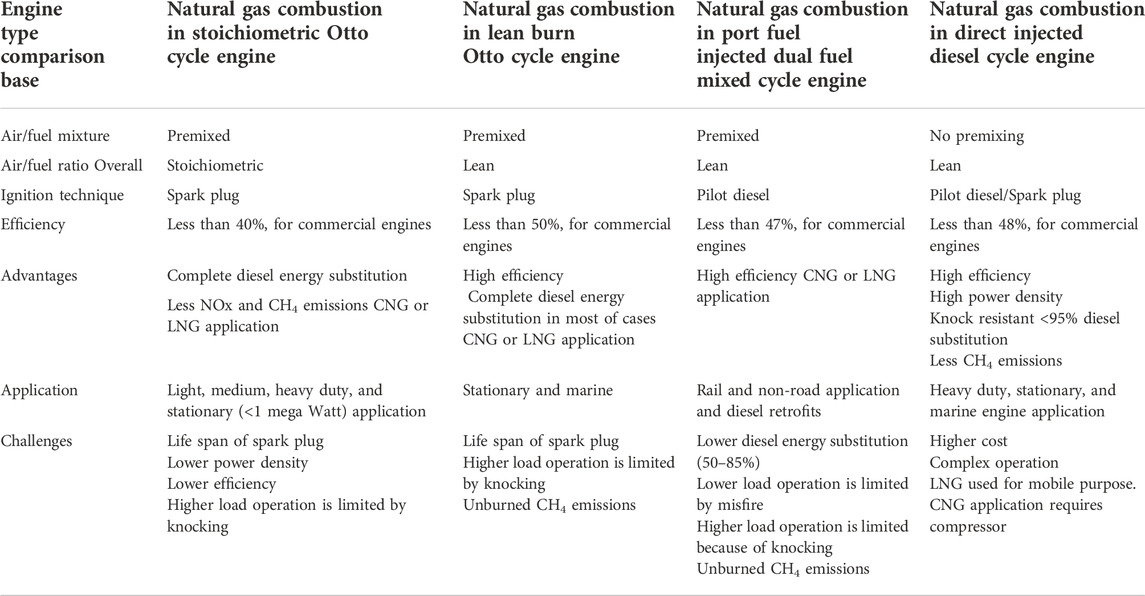
Table 4. Methane injection strategies (Jääskeläinen, 2019).
Song et al. analyzed methane direct-injection spark ignition engines, reporting that injection timing variation had a larger effect on the torque and volumetric efficiency compared to injection pressure (Song et al., 2016). Ahmad et al. described three important parameters on which dual-fuel operation is mainly dependent; namely, pilot diesel quantity, methane equivalence ratio, and initial charge temperature (Ahmad et al., 2019). Higher methane supplementation in methane direct-injection diesel engines resulted in an increased ignition delay period and hydrocarbon emissions and decreased heat release rate, NOx, and smoke emissions (Zhang et al., 2006). In this type of engine, the higher hydrocarbon emissions can be effectively solved with the variation of diesel injection timing (Liu et al., 2019). The problem of higher hydrocarbon and CO emissions in port fuel-injected natural gas-diesel dual-fuel engines can be effectively reduced with a reduced injection of pilot diesel fuel and a delayed start of the energizing timing for diesel fuel (Park et al., 2019). As discussed earlier, port fuel injection of methane in diesel engines is the easiest way to achieve methane supplementation in diesel engines with small engine modifications and higher efficiency. Thus, methane port fuel-injected diesel engines have been further analyzed to provide insight into their characteristics to inform the redesign to increase the efficiency and effectiveness of M-DDF engines in commercial and operational contexts.
Combustion, noise, and vibration characteristics
Diesel single-fuel combustion is characterized as non-premixed combustion as only air is available for the compression and only a small part of the fuel is premixed during ignition delay. Tripathi et al. described that in port fuel-injected M-DDF engines, after the compression of air and methane, the temperature of the mixture does not reach the auto-ignition temperature of diesel and increases the ignition delay period (Tripathi et al., 2020c). Increased methane levels in diesel engines increase the combustion noise level (pressure rise rate) (Selim, 2001; Nielsen et al., 1987) due to the extended ignition delay period to accumulate a large charge that burns suddenly and increases the pressure rise rate. Engine load is an important parameter that affects the combustion noise, as combustion noise increases proportionally with engine load. The increase in the number of automobiles on the road not only created harmful emissions but also produced high levels of noise pollution. Nag et al. studied the noise, vibration, and combustion characteristics of gaseous fuel-supplemented diesel engines (Nag et al., 2019b). They reported decreased noise and vibration levels compared to those in pure diesel engines. Methane and diesel are two different fuels with different reactivity and physical state when burned in the same combustion cycle. Thus, it is of research interest to analyze this combustion. Vibration, noise, or oscillation occur in natural gas-diesel dual-fuel engines due to the sudden rapid burning of a large quantity of charge, similar to knocking or ringing. Ringing is defined as the occurrence of a pressure wave during dual-fuel combustion (Kirsten et al., 2016). These pressure waves may persist until the end of combustion. Ringing combustion has 5–10-fold higher pressure oscillations than those of knocking combustion and causes higher noise (Eng et al., 2002). The dual-fuel technique helps resolve ringing combustion as it has negative effects on pressure oscillations (Kirsten et al., 2016). As the diesel quantity is reduced, the ringing combustion in the premixed zone is reduced. In common rail engines at low pressure, there is poor mixing but smoother combustion, which results in less ringing. At higher pressures, mixing improves; when combustion happens suddenly, ringing becomes a problem. As natural gas is injected into the diesel engines, knocking and lower power density are challenges faced by Otto engines due to the limitation of the compression ratio. In the Otto cycle, the end charge absorbs the heat, pressure, and temperatures and produces an opposite flame front that causes knocking (Eng et al., 2002). Similar events happen in natural gas-diesel dual-fuel engines (Kirsten et al., 2016). Thus, low parameters are highly dependent on cycle-to-cycle variations of the properties of the in-cylinder charge.
Effects of load
At low load or temperature conditions, methane combustion is delayed because 1) at lower temperatures, it is difficult to break C-H bonds, as this reaction requires high energy (40 kJ), 2) slower attack by oxygen atoms, 3) the reactivity of methane decreases with temperature, and 4) the availability of free radicals is reduced at lower temperatures (Glassman et al., 2014). Gunea et al. (1998) suggested that the performance of M-DDF engines can be increased at lower load conditions by 1) using pilot fuel with a higher cetane number, 2) lowering the nozzle opening, 3) reducing the air intake by bypassing the excess air to provide a richer fuel-air mixture (Karim, 2003b), 4) skipping firing in multi-cylinder engines, 5) increasing the intake air temperature by preheating or by increasing the water jacket temperature, and 5) adding some other fuel during light load conditions (Khalil and Karim, 2002). At part load, only a fraction of the methane participates in combustion; the remaining methane either impinges into the cylinder wall or piston head or moves out with exhaust gases. Papagiannakis et al. reported that higher engine loads resulted in higher combustion pressure and heat release rate in M-DDF engines (Papagiannakis and Hountalas, 2003). In dual-fuel mode, the pressure and heat release rate increase with increasing load. These effects occur due to 1) an increased combustion temperature and 2) an increased mass flow rate of charge. The same trends in pressure, heat release rate, and noise (rate of pressure rise) with changes in the load in CNG-methane dual-fuel engines were reported by Abdelaal and Hegab (2012). Figure 3 shows that as engine load increases in methane-diesel dual-fuel engines, the rate of heat release increases dramatically (Tripathi et al., 2020a). This occurs due to the 1) more active participation of methane in combustion at higher loads, 2) increased oxidation rate and more rapid chemical reactions at higher loads, 3) enhanced combustion as the air-fuel ratio approaches a stoichiometric level at higher loads, and 4) increased numbers of free radicals at higher loads.
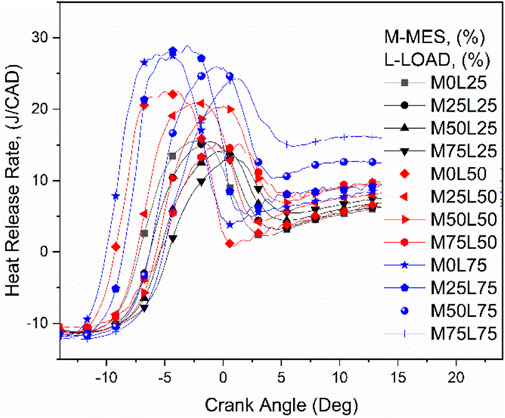
Figure 3. Effects of methane energy share (MES) on heat release rates for different engine loads (Tripathi et al., 2020a).
Effects of EGR
The supplementation of methane fuel in diesel engines increases the cycle-to-cycle variation in measured combustion characteristics. This problem can be easily solved using the exhaust gas recirculation technique. In this technique, some part of the exhaust gas is re-circulated with the intake air, which reduces the specific heat capacity of the intake mixture and results in a lower combustion pressure, heat release rate, and NOx emissions. Abdelaal and Hegab reported reduced combustion pressure, heat release rate, and noise level (pressure rise rate) and an increased ignition delay period with increasing EGR (Figure 4) (Abdelaal and Hegab, 2012). These effects occurred because of 1) the replacement of oxygen with EGR gases (carbon dioxide and water) in the combustion chamber, which adversely affected the combustion process, 2) increased ignition delay by EGR gases (Karim et al., 1989), 3) a decreased charge temperature due to the mixing of air with EGR gases, 4) a reduction of the partial pressure of oxygen by EGR gases, 5) an increase in the specific heat capacity of the cylinder charges by EGR. Since EGR reduces the combustion pressure, the rate of pressure rise also decreases with increased EGR levels. Thus, combustion noise, which is highly dependent on the rate of pressure rise with respect to the crank angle, is also reduced. Higher EGR levels cause unstable combustion in natural gas-diesel dual-fuel engines (Chen et al., 2020). Tomita et al. focused on moderate utilization of EGR levels for effective combustion (Tomita et al., 2002).
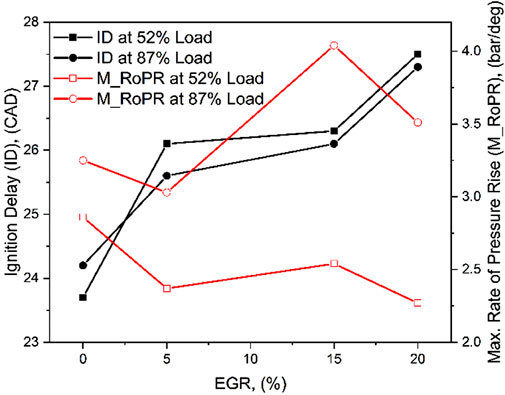
Figure 4. Effects of EGR on ignition delay and maximum rate of pressure rise in CNG-diesel dual-fuel engines (Abdelaal and Hegab, 2012).
Effects of methane fuel replacement shares
Papagiannakis and Hountalas (2003) investigate the effects of varying natural gas ratios on combustion pressure, heat release rate, and ignition delay in natural gas-diesel dual-fuel engines. They reported an increased natural gas supplementation ratio decreased the peak pressure and heat release rate. An increase in natural gas ratio from 0 to 85% resulted in reductions in the peak pressure of 10 and 17.93% at loads of 40 and 80%, respectively. Natural gas burns slowly and most of its fraction remains unburned during the early part of combustion, resulting in reduced combustion pressure and heat release rate. The ignition delay period and combustion duration also increase with increased natural gas share. Figure 3 demonstrated the reduced rate of heat released with increasing methane energy share in diesel engines (Tripathi et al., 2020a). This occurs due to the replacement of oxygen with methane, which causes the incomplete combustion of alkanes. As the methane share increases, the combustion pressure of methane-diesel dual-fuel engines decreases (Figure 5) (Tripathi et al., 2020a). With increased methane share, more oxygen content is replaced in the intake manifold, resulting in the incomplete oxidation of methane and other hydrocarbons in the engine cylinders. As the methane content increases in the engine cylinders, a lower temperature is achieved after the compression stroke due to the higher specific heat capacity of methane, which makes it difficult for methane to achieve high auto-ignition temperatures compared to those in diesel fuel, which negatively affects combustion. Higher methane content in the engine cylinders quenches the flame during combustion as methane has a lower flame propagating speed, which results in incomplete combustion. Higher methane energy shares reduce the energy share of diesel, which acts as multiple ignition sources for methane in the engine cylinders. The difficulty in the ignition of methane reduces the combustion pressure and heat release rate. At higher loads, the MDDF engine characteristics are more sensitive to changes in methane energy share as methane rapidly participates in combustion at higher temperatures. Hence, at higher loads, methane supplementation results in higher combustion pressures and heat release rates compared to those at lower loads.
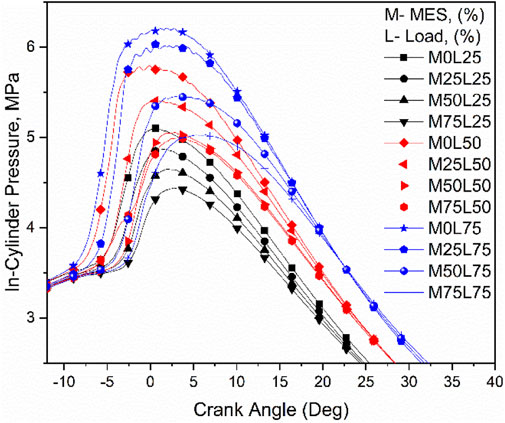
Figure 5. Effect of methane energy share (MES) on in-cylinder pressure of methane-diesel dual fuel-engines at different loads (Tripathi et al., 2020a).
Effects of diesel injection strategies
Diesel injection plays a crucial role in the combustion of diesel fuel. Yousefi et al. investigated the effects of diesel injection strategies in NG-DDF engines (Yousefi et al., 2019). They reported that advancing the diesel injection timing increased the maximum combustion pressure. Advanced diesel injection timing enhances the premixing process, resulting in an earlier start of combustion and a reduced ignition delay period. The earlier combustion start increases the combustion pressure and heat release rate for MDDF combustion. Figure 6 shows the effects of diesel injection strategies on the combustion characteristics in natural gas-diesel dual-fuel engines (Yousefi et al., 2018). As the first start of injection timing (SOI1) is advanced from 28° BTDC, the initial start of combustion (SOC) is also advanced. The SOC is advanced due to the enhanced premixing of natural gas and air. Further increases in SOI1 timing retarded the SOC due to the lower temperature inside the engine cylinder. The variation in maximum pressure rise rate (MPRR) showed a trend like that for the SOC variation curve.
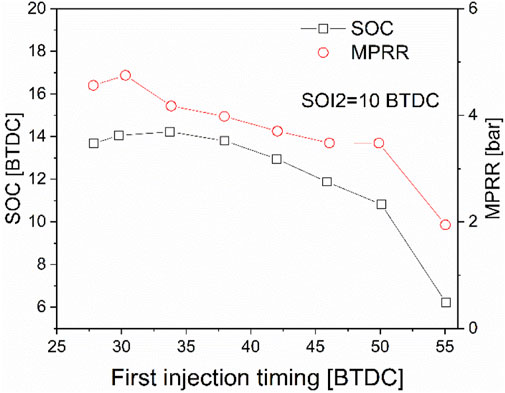
Figure 6. Effects of SOI1 timing on the SOC and MPRR of methane-diesel dual-fuel engines (Yousefi et al., 2018).
In M-DDF engines, methane is sucked and compressed with air. The temperature achieved at the end of the compression of air-methane mixtures is less than that achieved after the compression of pure air. This is because of the high specific heat capacity of methane compared to that of air. Thus, methane enrichment in diesel engines results in slower combustion and lower in-cylinder pressure and HRR compared to those for pure diesel operation. Generally, HRR vs. the crank angle curve of diesel fuel shows four combustion phases; namely, the ignition delay period followed by the premix combustion and then controlled combustion periods, and finally the combustion phase. In the case of diesel fuel, the mixing-controlled combustion phase has a long combustion duration, during which diesel fuel is mainly burned. In the case of dual-fuel combustion, methane enrichment increases the premixed fuel mixture, which burns suddenly and fully or partially skips the mixing-controlled combustion phase depending on the enrichment (Wei and Geng, 2016). The peak of the HRR curve of MDDF engines was lower than that for pure diesel operation, as methane burns and releases heat slowly. Some studies have also reported the opposite trend for pressure and HRR with methane enrichment, as discussed earlier. These studies reported that methane enrichment in diesel fuel resulted in higher heat release rates due to increased OH radical formation, as well as in increased ignition delay period (Zang et al., 2016; Wei et al., 2018). In the case of dual-fuel combustion, combustion mainly occurred in the post-combustion phase, which explained the higher exhaust temperature. MDDF engines have an extended ignition delay period as methane supplementation alters the amount of free radicals and the mixing process, which increases the physical delay and suppresses the auto-ignition temperature of diesel (Karim et al., 1989). Methane supplementation in diesel engines has the start of combustion and extended the ignition delay, which shifted combustion overall towards the expansion stroke that resulted in reduced brake power output. Magno et al. (2015) reported that cases with combustion and ignition delay are mainly controlled by diesel injection strategies and are independent of the injected amounts of methane. Combustion noise [pressure rise rate] increases with load due to the increase in ignition delay, which accumulates more fuel that burns suddenly and increases pressure for increased rates as well. Lower engine speed results in lower cylinder pressures and HRR due to lower in-cylinder temperature and more time for the combustion process. Table 5 summarizes combustion characteristics, as well as the results of the comparisons between the combustion characteristics of diesel engines and the methane-diesel dual-fuel engine. The results studies regarding the addition of methane in diesel engines are controversial. While most studies reported decreased peak pressure and HRR with methane addition, while a few studies reported the opposite. However, there is no disagreement in the literature regarding the increase in ignition delay with methane supplementation. Table 5 describes the effects of the variation of parameters on the combustion characteristics of MDDF engines. Most studies showed that an increased load results in increased peak pressure, HRR, CD, and combustion noise. In contrast, increased speed, EGR level, and methane energy share decrease the peak pressure, HRR, CD, and noise.
Performance characteristics
Performance characteristics are important indicators for the utilization of fuel for power output. This section discusses various performance parameters such as brake thermal efficiency, brake-specific fuel consumption, brake power, volumetric efficiency, etc. in methane-diesel dual-fuel engines. The effects of load, EGR, methane energy share, and injection strategies on performance characteristics are also discussed.
Effects of load
Abdelaal and Hegab investigated the effects of load on the performance of CNG-diesel dual-fuel engine. They reported an increase in engine load due to the BTE of CNG-diesel dual-fuel engines (Abdelaal and Hegab, 2012). The increase in load results in a higher combustion temperature, which stimulates methane to more actively participate in combustion and contribute to brake power, causing higher BTE at higher loads. Methane requires a higher compression ratio for auto-ignition (29:1) compared to that of diesel (15:1). Thus, it can be more highly compressed without ignition, resulting in increased thermal efficiency (Fraser et al., 1991). Papagiannakis et al. experimentally assessed the effect of load on BSFC at 40, 60, and 80% of the engine load for natural gas-diesel dual-fuel engines. They reported that at part load, the utilization of gaseous fuel was poor due to a lower combustion temperature, which also contributed to a lower brake power (BP) and higher BSFC (Papagiannakis and Hountalas, 2003). For MDDF engines, as engine load increases, the BTE is increased for each level of methane supplementation (Figure 7). At higher loads, combustion temperatures increased, which helped methane to achieve its high auto-ignition temperature. High combustion temperatures at higher loads also help in the oxidation of methane and other hydrocarbons (Tripathi et al., 2020b).
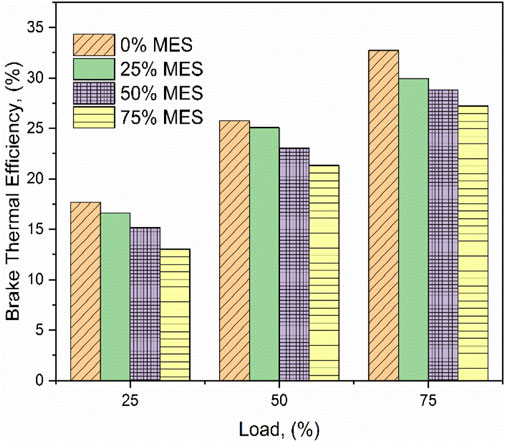
Figure 7. Effect of load on the brake thermal efficiency of methane-diesel dual-fuel engines (Tripathi et al., 2020b).
Effects of EGR
It is important to study the effect of EGR on the performance characteristics of M-DDF engines as it directly affects engine BTE. Abdelaal and Hegab examined the effect of EGR on BTE and the equivalence ratio of methane-diesel dual-fuel engines (Figure 8) (Abdelaal and Hegab, 2012). They reported an increase in EGR level up to 20% increased the BTE and reduced the equivalence ratio at loads <70%. In contrast, increased EGR levels up to 20% decreased the BTE and increased the equivalence ratio at loads >80%. At lower loads, the BTE increased with increased EGR due to the re-combustion of EGR gases, which contribute to higher power output and increased BTE. These partially hot EGR gases act as a preheater for intake air that enhances the BTE. The number of active radicals increased in the combustion chamber due to increased EGR level, which enhanced the BTE at lower and medium loads. At higher loads, BTE decreased with increased EGR due to the expansion of EGR gases at high temperatures, which replaced the oxygen content and reduced the volumetric efficiency, resulting in a reduced BTE. At higher loads, more carbon dioxide was present in the combustion chamber, which increased the specific heat capacity for intake charge to suppress combustion and reduce the BTE. At lower loads, increased EGR level reduced fuel consumption due to the presence of highly active hydrocarbons and radicals, which decreased the equivalence ratio. EGR replaced a significant amount of air at higher loads, resulting in a higher equivalence ratio.
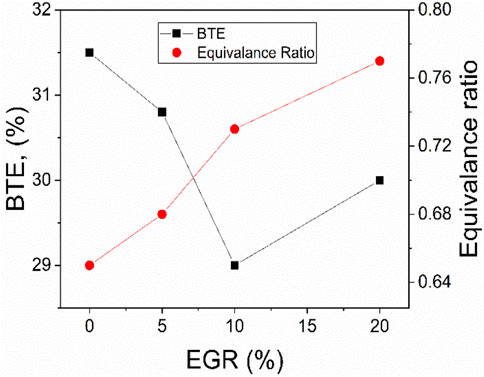
Figure 8. Effect of EGR on the performance characteristics of CNG-diesel dual-fuel engines at 90% load (Abdelaal and Hegab, 2012).
Effects of methane fuel replacement
Belgiorno et al. (2018) examined the effect of different methane energy shares on the thermal efficiency of MDDF engines at different pilot fuel quantities. They reported that increased methane injection resulted in increased and decreased thermal efficiency at higher and lower loads, respectively. due to the more active participation of methane combustion at higher load conditions. Tripathi et al. studied the effect of methane energy share on heat balance sheets in MDDF engines (Tripathi et al., 2020b), reporting reduced energy equivalent to brake power output, heat absorbed by exhaust gases, and heat absorbed by cooling water with increases in MES from 0 to 75%. These findings occurred due to the incomplete combustion of methane, which does not contribute to BP and the heat absorbed by exhaust gas and cooling water. In contrast, the unaccounted heat loss increased at different engine loads with increased methane energy share. The unaccounted loss increased because most of the methane burns after the combustion stage due to extended SOC timing, prolonged ignition delay, and slow burning speed of methane. Moreover, increased methane energy share resulted in increased heat removed by the exhaust gases. As the methane gas supplementation ratio increased in diesel engines, the brake-specific energy consumption (BSEC) increased for each load condition (Figure 9) (Tripathi et al., 2020b). The BSEC is reciprocal of the BTE. As the BTE decreases with methane energy share (Figure 7), the BSEC increased with MES.
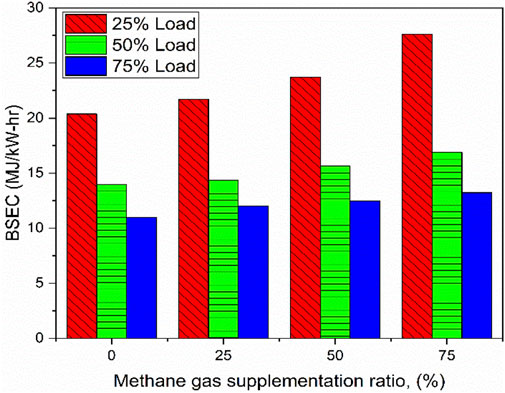
Figure 9. Effect of methane gas supplementation on the brake-specific energy consumption (BSEC) in methane-diesel dual-fuel engines (Tripathi et al., 2020b).
Effects of diesel injection strategies
Yousefi et al. (2019) investigated the effects of diesel injection strategies on the performance characteristics of NG-DDF engines, reporting that advancing the diesel injection timing enhanced the premixing of air-NG, which increased the thermal efficiency. Cameretti et al. explored the effect of diesel injection timing on the global efficiency of a natural gas-diesel dual-fuel engine (Cameretti et al., 2016). They observed that the global efficiency first increased and then decreased as the diesel injection timing was advanced. The global efficiency of natural gas-diesel engines peaked at around 35.5% at the start of the pilot timing, corresponding to 32.5° before the top dead center. Furthermore, advancing the injection timing decreased the global efficiency of natural gas-diesel dual-fuel engines.
The addition of methane in diesel engines through the air intake port replaces the oxygen content that reduces the volumetric efficiency and power output. Diesel injection techniques are effective in enhancing engine performance. The BTE of MDDF engines is reduced in part-load conditions. The BTE decreases because the lean mixture of methane-air at low loads prevents the diesel fuel from combusting; thus, a major portion of fuel remains unburned and is emitted as exhaust. In contrast, at higher engine loads, the BTE of MDDF engines was enhanced. At higher loads, the flame becomes more stable due to higher combustion and boundary temperatures that result in increased brake power output and brake thermal efficiency. In the case of methane-enriched diesel combustion, the coefficient of variance (COV) for the indicated mean effective pressure (IMEP) increases. Since existing CI engines were manufactured for single-fuel rather than dual-fuel combustion, MDDF engines have higher COV values for maximum pressure and indicated mean effective pressures. In the case of natural aspiration, the methane induction is not the same in each cycle because different atmospheric and operating conditions and resistance offered by frictional pathways and valve hindrance lead to higher COV values for IMEP. EGR helps address cycle-to-cycle variations in MDDF engines. The COV for IMEP is higher at part-load conditions compared to those at higher loads. At higher loads, higher combustion temperature and higher intake of premixed charge result in a compact combustion duration that reduces the COV for IMEP. The BSFC is reduced at higher loads due to better fuel utilization at high temperatures. Table 6 describes the effects of methane addition on the performance characteristics of methane-diesel dual-fuel engines. This table also shows the results of the comparisons of performance characteristics between diesel and MDDF engines, demonstrating the disagreement in the literature regarding the effect of methane addition in diesel engines on engine BTE and BSFC. Most of the literature suggests that methane addition in diesel engines results in reduced BTE and increased BSFC. However, some studies reported the opposite trends. Methane supplementation reduces volumetric efficiency. Increased loads result in increased BTE and reduced BSFC, while increased engine speed and MES result in increased BSFC.
Regulated emissions
Gaseous emissions
The addition of methane to diesel fuel in dual-fuel mode reduces the in-cylinder temperature (Hountalas and Papagiannakis, 2000), which directly reduces NOx formation (Mustafi and Raine, 2008). Methane has slow flame development and flame propagation speed, which result in higher HC and CO emissions (Mustafi and Raine, 2008). The addition of methane at different loads and speeds also differently affects engine emissions (Iorio et al., 2017). Cozzolini et al. (2013) analyzed the emissions from M-DDF engines at different speeds and loads in European stationary cycle (ESC) modes. They observed that at low speed and load (torque), the M-DDF engine showed lower NOx emissions and particulate matter concentrations and higher CO and non-methane HC emissions compared to those of conventional diesel fuel operation. In contrast, at high speed and load, the comparative emission trends reverted. Moreover, the CO2 emission was lower in the methane-diesel dual-fuel engine in ESC modes, which will help reduce global warming. The unburned methane from diesel-methane dual-fuel engines was higher at low load and speed conditions compared to those at higher load and speed conditions.
Effects of load
Abdelaal and Hegab investigated the effect of load on M-DDF engine emission characteristics. They reported that with increased load, NO formation increased by the thermal route, as it mainly depended on combustion temperature (Abdelaal and Hegab, 2012). The HC and CO emissions decreased with increased engine load due to enhanced oxidation and complete combustion of HC and CO species. Varying the load showed the same trends in NOx, HC, and CO emissions for natural gas-diesel dual-fuel engines (Papagiannakis and Hountalas, 2003). At higher loads, the NOx and soot emissions increased whereas HC and CO emissions decreased in NG-DDF engines. This is due to 1) the increased burning rate of gaseous fuel at higher temperatures caused by a higher load 2) the enhanced oxidation of hydrocarbon species, and 3) the reduced amount of unburned fuel.
Effects of EGR
Higher EGR levels decrease NOx emissions and only marginally affect HC emissions (Figure 10) (Abdelaal and Hegab, 2012). NOx emissions decrease with EGR level due to the decreased combustion temperature. EGR recirculates unburned hydrocarbons and carbon monoxide, which increases the chance that they will burn completely at part load, and reduces HC emissions. This phenomenon intensifies at higher EGR levels. At higher loads, HC and CO emissions also increased EGR levels. This effect occurs due to the unavailability of oxygen as EGR gases expand more at higher loads and replace more oxygen in the engine cylinders. The EGR technique recirculates HC and CO gases and completely burns them into CO2 and H2O emissions. This explains the increased CO2 emissions with increasing EGR levels. In contrast, the EGR technique reduces CO2 emissions at higher load conditions as it creates an oxygen deficiency.
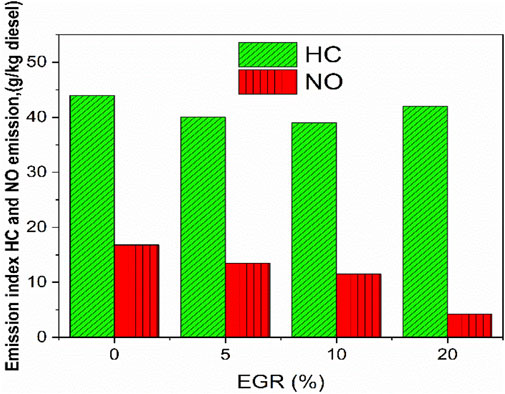
Figure 10. Effect of EGR on the emission characteristics of CNG-diesel dual-fuel engines at 90% engine load (Abdelaal and Hegab, 2012).
Effects of diesel injection strategies
The varying diesel injection strategies may solve the problems of higher HC and CO emissions from M-DDF engines. The earlier injection of diesel fuel allows more time for premixing and ignition (Nwafor, 2000). Diesel/pilot fuel split injection techniques can effectively enhance combustion and thermal efficiency with reduced emissions. In the split injection technique, a fraction of diesel fuel is injected and burned earlier to increase the temperature of the methane-air mixture needed for main combustion (Yousefi et al., 2019).
Effects of methane fuel replacement
Hernandez et al. experimented with M-DDF engines for varying MES levels (0-40%). They found that NOx and PM emissions were effectively reduced and HC and CO emissions were increased compared to those in conventional diesel engines (Hernández et al., 2016). Ghazal et al. assessed the effects of varying MES levels (0–90%) in M-DDF turbocharged engines, reporting that HC and CO emissions first increased and then decreased with maximum reduction (35%) in NOx emission at an MES level of 50% MES (Ghazal, 2018). Figure 11 shows the effect of methane fuel replacement on different engine emissions in M-DDF engines (Tripathi et al., 2020c). These findings demonstrate the trade-off between NOx and hydrocarbon emissions and between CO and CO2 emissions. As methane energy share increased from 0 to 75%, the NOx emission decreased while that of hydrocarbon (HC) emissions increased. Most of the methane remained unburned and was emitted as HC emissions. The incomplete combustion corresponds to lower combustion pressure and temperature NOx emission. However, as the methane supplementation ratio increased from 0 to 50%, the CO emissions decreased while the CO2 emissions increased. This occurred due to the presence of highly active O and OH radicals in higher quantities with methane supplementation which affects the chemical reaction and increases the oxidation of CO into CO2. With further increases in methane energy share (75% methane energy share), CO emissions dramatically increase, while CO2 emissions decrease. At 75% MES, a large portion of the oxygen is replaced by methane in the intake manifold, which adversely affects CO oxidation and increases CO emission. At 75% MES, the diesel quantity is very low to ensure the complete combustion of methane, as methane cannot ignite by itself due to its higher auto-ignition temperature. Incomplete combustion results in higher CO emissions.
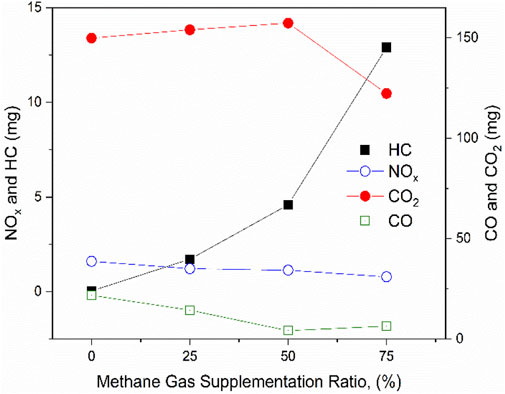
Figure 11. Effect of the methane gas supplementation ratio on different gaseous emissions from methane diesel dual-fuel engines (Tripathi et al., 2020c).
NOx emissions decrease significantly with methane enrichment in diesel engines at lower loads. Since most NOx is formed through the thermal route and mainly depends on combustion temperature, methane supplementation reduces the combustion temperature due to its higher specific heat capacity. Due to this reduction in temperature, NOx emissions are reduced with increasing methane energy share, especially at lower loads. THC emissions increase with methane enrichment in diesel engines. Methane has a lower flame propagation speed and remains unburned at the end of combustion, thus directly contributing to THC emission. During the valve overlap timing, some methane is emitted through the exhaust manifold without participating in combustion due to its gaseous nature as THC emission. Some fraction of methane impinges on the cylinder boundary wall and piston head and does not participate in combustion. This methane is released during the expansion stroke and contributes to THC emissions. CO emission is also increased with methane supplementation in diesel engines. Methane supplementation causes lower oxygen content and combustion temperatures, both of which adversely affect CO into CO2 oxidation and increase CO emissions. Haung et al. studied methane-diesel dual-combustion, reporting that CO emission first decreased with the advancement of the first diesel injection timing due to higher OH and O radical concentrations. Further advances in first diesel injection timing increased CO emissions due to the inhibition of CO to CO2 oxidation (Huang et al., 2019). CO2 emission is reduced with the addition of methane to diesel engines because of the incomplete oxidation of CO and reduced numbers of C and H atoms in methane fuel compared to conventional diesel fuel. Table 7 describes the effects of methane supplementation on emission and the characteristics of methane-diesel dual-fuel engines. The addition of methane to diesel engines reduces NOx emissions and increases THC, CO, and CH4 emissions. Table 7 also describes the effects of variation of different engine operating parameters on emission characteristics in MDDF engines. Most studies reported that increased load in MDDF engines results in increased NOx and reduced THC and CO emissions. Increased speed results in reduced NOx and increased THC and CO emissions.
Particulate matter emissions
The main problem of compression ignition engines is particulate matter emission. Higher particulate formation occurs due to high carbon-to-hydrogen ratios in conventional CI engine fuels and fuel-rich packet formation inside the engine combustion chamber. The addition of methane to CI engines reduces the PM emission as it has lower amounts of carbon and hydrogen atoms compared to those in conventional fuel. PM emission is also reduced with methane supplementation owning to the physical state of gaseous methane fuel, as it improves the in-cylinder fuel-air mixing compared to conventional liquid diesel fuel. Methane expands widely in the engine cylinders. This enhances the mixing and reduces the chances of rich fuel packet formation, as well as reducing PM emissions. Boretti (2019) reported that quick vaporization of CNG resulted in drastic PM emissions. Lounici et al. (2014b) investigated biogas-diesel dual-fuel engines, reporting decreased PM emission compared to pure diesel operation. The authors suggested that the lower combustion efficiency and gaseous nature of methane gas were the main causes of the reduced particulate emission from biogas-DDF engines. As the methane supplementation ratio increases in diesel engines, the particulate concentration decreases (Figure 12) (Tripathi et al., 2020b). PM emission is reduced with methane energy supplementation due to reduced carbon-to-carbon and carbon-to-hydrogen bonds. Moreover, increased engine load increases particulate matter emission (Tripathi et al., 2020b). PM formation is reduced at increased loads as higher temperatures oxidize more hydrocarbon species and reduce PM emissions.
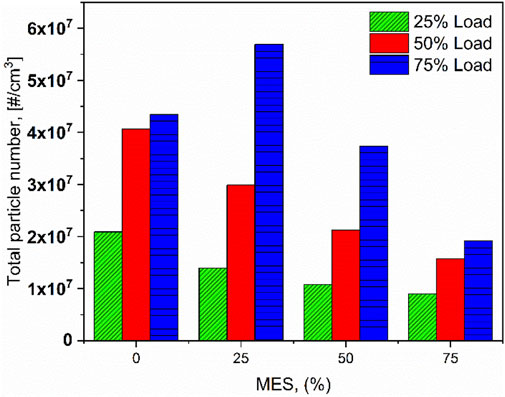
Figure 12. Particulate matter concentrations from methane-DDF engines (Tripathi et al., 2020b).
Table 8 summarizes the particulate matter emissions of methane diesel dual-fuel engines and the comparisons of particulate matter emissions between diesel and MDDF engines. The effects of methane supplementation on the PM emissions from the engines remain controversial. While most studies reported reduced PM emissions in MDDF engines compared to diesel engines (Gunea et al., 1998; Liu et al., 2003a; Wannatong et al., 2007; Zang et al., 2016), several studies reported increased PM emissions from MDDF engines compared to those in diesel engines (Belgiorno et al., 2018). Generally, the addition of fuel-borne catalysts to CI engines is the preferred choice for reducing PM emission; however, early injection in methane-diesel engines is also an effective technique for reducing PM emissions (Shukla et al., 2021; Tripathi et al., 2022). This technique is shown in Table 8, which also describes the effect of parameter variation on PM emission in MDDF engines. Increased load or speed in MDDF engines results in increased PM emissions, while increased MES reduces PM emissions.
Unregulated emissions
Unregulated emissions are emissions whose limits are not fixed by government emission legislation. Unregulated emissions on prolonged exposure may cause serious environmental damage and health problems (Agarwal et al., 2016). The study of unregulated emissions from vehicles becomes important when we consider the large-scale implementation of any alternative fuel (Agarwal et al., 2018). Sharma et al. studied the unregulated emissions in gaseous fuel-supplemented DDF engines, reporting that gaseous fuel helps reduce unregulated emissions from dual-fuel engines (Sharma and Dhar, 2019). Although unregulated emissions are smaller in quantity, they may play a significant role in human health risk and particulate matter formation. Guo et al. studied the unregulated emissions from CNG-DDF engines, reporting that increased unregulated emissions of methane, ethane, ethylene, acetylene, propylene, and formaldehyde and acetaldehyde increased and decreased benzaldehyde emission compared to conventional diesel fuel operation (Guo et al., 2018). The field of unregulated emissions from methane diesel dual-fuel engines has not been extensively explored and limited studies are available. More analysis of the future prospects and the effective design of after-treatment devices is needed. Tripathi et al. reported that methane addition to diesel fuel reduces the unregulated emission for each engine load condition (Figure 13) (Tripathi et al., 2020a). Methane supplementation reduced the available oxygen content in the engine cylinders as well as the combustion temperature, which restricted some chemical reaction routes and resulted in a reduced formation of unregulated species. The detailed mechanisms by which these pollutants are formed, as well as their kinetics and dependencies on methane, require further investigation.
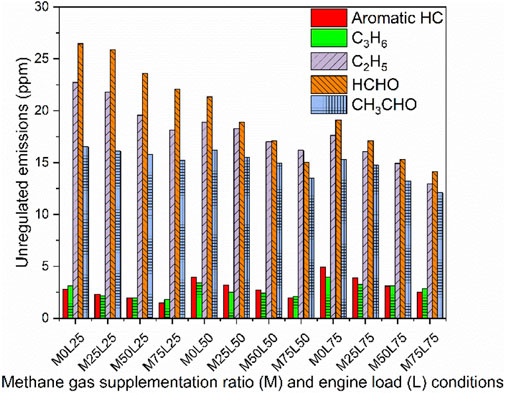
Figure 13. Effects of methane gas supplementation ratio and engine load on unregulated emissions from methane-diesel dual-fuel engines (Tripathi et al., 2020a).
Summary and future prospects
Compared to other alternative fuels, the promising features of methane make it a suitable alternative fuel for engines. Methane has renewable energy sources (biogas) as well as a vast supply from non-renewable energy sources such as natural gas. It also has huge availability as methane hydrate for future use. Another benefit is that it can be utilized in engines in various forms such as natural gas, biogas, CNG, SNG, LNG, etc. The life cycle analysis of methane-diesel dual-fuel engines showed a reduction in life cycle greenhouse gas emission and cost. Methane can operate in single-fuel mode in SI engines; however, pumping loss results in poor efficiency at partial load. Methane can also operate in single-fuel mode in CI engines; however, this ability has not been extensively explored as it requires the redesign of existing engines to accommodate high compression ratio conditions. Methane can be used in SI engines in dual-fuel mode as methane-petrol dual-fuel engines but has the limitation of lean burn operation. Methane can be utilized in CI engines in dual-fuel mode in two ways: through direct injection or port fuel injection. Port-injected methane CI engines are the preferred choice among the available options due to the requirement for small modifications to the main engine system. The comparison of the combustion characteristics of methane-diesel dual-fuel engines to conventional diesel fuel engines showed the adverse effects of methane supplementation in most studies due to the higher specific heat capacity and slower burning rate of methane. Most studies reported that M-DDF engines have lower combustion pressure, combustion noise, and heat release rate with a prolonged ignition delay period compared to those in pure diesel operation. The comparison of performance between M-DDF and diesel engines demonstrated the degraded performance of M-DDF engines with methane share owing to the lower combustion temperature, as most of the methane remains unburned or burned after the combustion stage. The brake thermal efficiency and brake power along with volumetric efficiency are also reduced with methane supplementation. The comparison of regulated emissions between MDDF and diesel engines showed reduced NOx and particulate matter emissions and increased CH4, THC, and CO2 emissions with methane supplementation. The NOx emission is decreased as the combustion temperature is reduced with methane share, while soot emission is reduced due to reduced C-C and C-H bonds with methane share. The THC and CH4 emissions increased because unburned methane is emitted as THC and CH4 emissions. CO emission is increased with methane supplementation as the amount of oxygen for CO oxidation is reduced. The comparison of unregulated emissions between methane-diesel dual-fuel and diesel engines showed reduced unregulated emissions with methane supplementation in diesel fuel. Methane supplementation reduced the C-C and C-H bonds that inhibited the formation of complex chemical species, which resulted in reduced unregulated emissions. The engine noise and vibration levels were reduced with methane supplementation due to reduced pressure rise and heat release rates with methane supplementation in methane diesel dual-fuel engines.
Overall, methane is an attractive choice for filling the increasing gap between future energy demand and supply. Methane supplementation in dual-fuel mode of CI engines has not been comprehensively explored; however, the available literature has suggested its advantage in terms of reduced PM and NOx emissions, noise, and vibrations with minimal modifications to existing CI designs. The challenges for methane-diesel dual-fuel engines include knocking at higher loads, misfires at lower loads, higher greenhouse emissions in as CH4 exhaust emissions, space constraints, leakage problems, etc. To ensure the large-scale deployment of methane-diesel dual-fuel engines, challenges such as increased CO and HC emissions and small reductions in engine performance with respect to baseline diesel-fueled CI engines must be resolved by optimizing diesel injection strategies, mapping methane supplementation levels to engine loads, adjusting EGR levels based on the methane supplementation level, etc. This detailed review of methane use in dual-fuel mode provides a basis for bridging diesel dual-fuel engines and the large-scale utilization of gas or other new alternate fuels in CI engines.
Author contributions
GT: primary draft writing; AD: primary draft writing, study conception, editing.
Acknowledgments
The authors received research funding from DST-SERB, provided by the government of India (Project No. ECR/2015/000135, “Study of Synergistic Use of Hydrogen and other Alternative Fuels in a Dual Fuel Engine for Emissions Reduction”).
Conflict of interest
The authors declare that the research was conducted in the absence of any commercial or financial relationships that could be construed as a potential conflict of interest.
Publisher’s note
All claims expressed in this article are solely those of the authors and do not necessarily represent those of their affiliated organizations, or those of the publisher, the editors, and the reviewers. Any product that may be evaluated in this article, or claim that may be made by its manufacturer, is not guaranteed or endorsed by the publisher.
Abbreviations
BSEC, brake-specific energy consumption; BSFC, brake-specific fuel consumption; CAD, crank angle degree; CI, compression ignition; CNG, compressed natural gas; Deg, degree; HRR, heat release rate, J/CAD; ID, ignition delay; M-DDF, methane-diesel dual-fuel; NG, natural gas; LNG, liquid natural gas; PNG, piped natural gas; SNG, synthetic natural gas.
References
Abdelaal, M. M., and Hegab, A. H. (2012). Combustion and emission characteristics of a natural gas-fueled diesel engine with EGR. Energy Convers. Manag. 64, 301–312. doi:10.1016/j.enconman.2012.05.021
Abdi, B. (2018). India’s crude oil import bill to peak at record $125 bn in current fiscal: Oil ministry. Econ Times Energy World. Available at: https://energy.economictimes.indiatimes.com/news/oil-and-gas/indias-crude-oil-import-bill-to-peak-at-record-125-billion-in-current-fiscal-oil-ministry/66319124.
Agarwal, A., and Assanis, D. N. (1998). Multi-dimensional modeling of natural gas ignition under compression ignition conditions using detailed chemistry. SAE Tech. Pap. 980136, 16. doi:10.4271/980136
Agarwal, A. K., Ateeq, B., Gupta, T., Singh, A. P., Pandey, S. K., Sharma, N., et al. (2018). Toxicity and mutagenicity of exhaust from compressed natural gas: Could this be a clean solution for megacities with mixed-traffic conditions? Environ. Pollut. 239, 499–511. doi:10.1016/j.envpol.2018.04.028
Agarwal, A. K., Chandra Shukla, P., Patel, C., Gupta, J. G., Sharma, N., Prasad, R. K., et al. (2016). Unregulated emissions and health risk potential from biodiesel (KB5, KB20) and methanol blend (M5) fuelled transportation diesel engines. Renew. Energy 98, 283–291. doi:10.1016/j.renene.2016.03.058
Ahmad, Z., Kaario, O., Qiang, C., Vuorinen, V., and Larmi, M. (2019). A parametric investigation of diesel/methane dual-fuel combustion progression/stages in a heavy-duty optical engine. Appl. Energy 251, 113191. doi:10.1016/j.apenergy.2019.04.187
Ahmadian Behrooz, H. (2016). Managing demand uncertainty in natural gas transmission networks. J. Nat. Gas. Sci. Eng. 34, 100–111. doi:10.1016/j.jngse.2016.06.051
Alcheikhhamdon, Y., and Hoorfar, M. (2016). Natural gas quality enhancement: A review of the conventional treatment processes, and the industrial challenges facing emerging technologies. J. Nat. Gas. Sci. Eng. 34, 689–701. doi:10.1016/j.jngse.2016.07.034
Bedoić, R., Špehar, A., Puljko, J., Čuček, L., Ćosić, B., Pukšec, T., et al. (2020). Opportunities and challenges: Experimental and kinetic analysis of anaerobic co-digestion of food waste and rendering industry streams for biogas production. Renew. Sustain. Energy Rev. 130, 109951. doi:10.1016/j.rser.2020.109951
Belgiorno, G., Di Blasio, G., and Beatrice, C. (2018). Parametric study and optimization of the main engine calibration parameters and compression ratio of a methane-diesel dual fuel engine. Fuel 222, 821–840. doi:10.1016/j.fuel.2018.02.038
Bengtsson, S., Andersson, K., and Fridell, E. (2011). A comparative life cycle assessment of marine fuels: Liquefied natural gas and three other fossil fuels. Proc. Institution Mech. Eng. Part M J. Eng. Marit. Environ. 225, 97–110. doi:10.1177/1475090211402136
Biernat, K., Samson-Bręk, I., Chłopek, Z., Owczuk, M., and Matuszewska, A. (2021). Assessment of the environmental impact of using methane fuels to supply internal combustion engines. Energies 14 (11), 3356. doi:10.3390/en14113356
Blarigan, A. V., Kozarac, D., Seiser, R., Cattolica, R., Chen, J-Y., and Dibble, R. Experimental study of methane fuel oxycombustion in an SI engine. Proc. ASME 2012 Intern. Combust. Engine Div. Fall Tech. Conf. ICEF2012 23, 2012, 2012. doi:10.1115/ICEF2012-92109
Boretti, A. (2019). Advantages and disadvantages of diesel single and dual-fuel engines. Front. Mech. Eng. 5, 1–15. doi:10.3389/fmech.2019.00064
Brown, B. S., Laforet, C. A., Rogak, S. N., and Munsh, S. R. (2011). Comparison of injectors for compression ignition of natural gas with entrained diesel. Int. J. Engine Res. 12, 109–122. doi:10.1243/14680874JER590
Cameretti, M. C., Tuccillo, R., SimioDe, L., Iannaccone, S., and Ciaravola, U. (2016). A numerical and experimental study of dual fuel diesel engine for different injection timings. Appl. Therm. Eng. 101, 630–638. doi:10.1016/j.applthermaleng.2015.12.071
Channappagoudra, M., Ramesh, K., and Manavendra, G. (2020). Effect of injection timing on modified direct injection diesel engine performance operated with dairy scum biodiesel and Bio-CNG. Renew. Energy 147, 1019–1032. doi:10.1016/j.renene.2019.09.070
Cheenkachorn, K., Poompipatpong, C., and Ho, C. G. (2013). Performance and emissions of a heavy-duty diesel engine fuelled with diesel and LNG (liquid natural gas). Energy 53, 52–57. doi:10.1016/j.energy.2013.02.027
Chen, Y., Zhu, Z., Chen, Y., Huang, H., Zhu, Z., Lv, D., et al. (2020). Study of injection pressure couple with EGR on combustion performance and emissions of natural gas-diesel dual-fuel engine. Fuel 261, 116409. doi:10.1016/j.fuel.2019.116409
Chen, Z., Zhang, F., Xu, B., Zhang, Q., and Liu, J. (2017). Influence of methane content on a LNG heavy-duty engine with high compression ratio. Energy 128, 329–336. doi:10.1016/j.energy.2017.04.039
Cozzolini, A., Littera, D., Ryskamp, R., Smallwood, J., Besch, M., Velardi, M., et al. (2013). Characteristics of exhaust emissions from a heavy-duty diesel engine retrofitted to operate in methane/diesel dual-fuel mode. SAE Tech. Pap. 6. doi:10.4271/2013-24-0181
csmonitor (2014). How long will world’s oil reserves last. Christ Sci. Monit. Available at: https://www.csmonitor.com/Environment/Energy-Voices/2014/0714/How-long-will-world-s-oil-reserves-last-53-years-says-BP.
Deheri, C., Acharya, S. K., Thatoi, D. N., and Mohanty, A. P. (2020). A review on performance of biogas and hydrogen on diesel engine in dual fuel mode. Fuel 260, 116337. doi:10.1016/j.fuel.2019.116337
Demirbas, A. (2010). Methane gas hydrate: As a natural gas source. Green Energy Technol. 34, 113–160. doi:10.1007/978-1-84882-872-8_4
Di Iorio, S., Magno, A., Mancaruso, E., and Vaglieco, B. M. (2017). Analysis of the effects of diesel/methane dual fuel combustion on nitrogen oxides and particle formation through optical investigation in a real engine. Fuel Process. Technol. 159, 200–210. doi:10.1016/j.fuproc.2017.01.009
Di Iorio, S., Magno, A., Mancaruso, E., and Vaglieco, B. M. (2016). Characterization of particle number and mass size distributions from a small compression ignition engine operating in diesel/methane dual fuel mode. Fuel 180, 613–623. doi:10.1016/j.fuel.2016.04.108
Di Iorio, S., Magno, A., Mancaruso, E., and Vaglieco, B. M. (2016). Performance, gaseous and particle emissions of a small compression ignition engine operating in diesel/methane dual fuel mode. SAE Tech. Pap. 2016, 2688. doi:10.4271/2016-01-0771
energy (2016). Compressed natural gas fueling stations. Available at: https://afdc.energy.gov/fuels/natural_gas_cng_stations.html.
energy Petroleum – oil and natural gas. Available at: https://energy4me.org/.
Eng, J., Technical, S. a. E., and Series, P. (2002). Characterization of pressure waves in HCCI combustion reprinted from : Homogeneous charge compression ignition engines. Sae 2002, 01–2859. doi:10.4271/2002-01-2859
eniscuola Methane hydrates. Energy Environ Eni Sch n. Available at: http://www.eniscuola.net/en/argomento/natural-gas1/methane-hydrates/special-ice/.
Eren, T., and Polat, C. (2020). Natural gas underground storage and oil recovery with horizontal wells. J. Pet. Sci. Eng. 187, 106753. doi:10.1016/j.petrol.2019.106753
Faramawy, S., Zaki, T., and Sakr, A. A. E. (2016). Natural gas origin, composition, and processing: A review. J. Nat. Gas. Sci. Eng. 34, 34–54. doi:10.1016/j.jngse.2016.06.030
Fraser, R. A., Siebers, D. L., and Edwards, C. F. (1991). Autoignition of methane and natural gas in a simulated diesel environment. SAE Tech. Pap., 910227. doi:10.4271/910227
Gambino, M., Iannaccone, S., and Unich, A. (1991). Heavy-duty spark ignition engines fueled with methane. J. Eng. Gas. Turbine. Power 113, 359–364. doi:10.1115/1.2906238
Ghazal, O. H. (2018). Air pollution reduction and environment protection using methane fuel for turbocharged CI engines. J. Ecol. Eng. 19, 52–58. doi:10.12911/22998993/91276
Gielen, D., Boshell, F., Saygin, D., Bazilian, M. D., Wagner, N., and Gorini, R. (2019). The role of renewable energy in the global energy transformation. Energy Strategy Rev. 24, 38–50. doi:10.1016/j.esr.2019.01.006
Glaude, P. A., Fournet, R., Bounaceur, R., and Molière, M. (2010). Adiabatic flame temperature from biofuels and fossil fuels and derived effect on NOx emissions. Fuel Process. Technol. 91, 229–235. doi:10.1016/j.fuproc.2009.10.002
Gonca, G., Cakir, M., and Sahin, B. (2018). Performance characteristics and emission formations of a spark ignition (SI) engine fueled with different gaseous fuels. Arab. J. Sci. Eng. 43, 4487–4499. doi:10.1007/s13369-017-2906-3
Goswami, S. (2004). Optimization of methane production from solid organic waste shyam goswami abstract key words. Available at: http://home.eng.iastate.edu/∼tge/ce421-521/ShyamGoswami.pdf.
Grigg, N. S. (2011). Transportation sector. Infrastruct. Financ., 65–96. doi:10.1002/9781118266182.ch4
Guilera, J., Andreu, T., Basset, N., Boeltken, T., Timm, F., Mallol, I., et al. (2020). Synthetic natural gas production from biogas in a waste water treatment plant. Renew. Energy 146, 1301–1308. doi:10.1016/j.renene.2019.07.044
Gujarat, P. N. G. (2019). Gas ltd India’s larg CGD Co. Available at: https://www.gujaratgas.com/knowledge-center/faqs/png/.
Gunea, C., Razavi, M. R. M., and Karim, G. A. (1998). The effects of pilot fuel quality on dual fuel engine ignition delay. SAE Tech. Pap., 982453. doi:10.4271/982453
Guo, H., Liko, B., Luque, L., and Littlejohns, J. (2018). Combustion performance and unburned hydrocarbon emissions of a natural gas-diesel dual fuel engine at a low load condition. J. Eng. Gas. Turbine. Power 140, 1–9. doi:10.1115/1.4039758
Hameedi, A. (2018). Project ge biomass how Russian waste can help Finland to reduce its reliance on nuclear power biogas : A sustainable fuel to power vehicles in Sweden. Available at: https://projectge.org/biomass/.
Hernández, J. J., Lapuerta, M., and Barba, J. (2016). Separate effect of H2, CH4 and CO on diesel engine performance and emissions under partial diesel fuel replacement. Fuel 165, 173–184. doi:10.1016/j.fuel.2015.10.054
Hountalas, D. T., and Papagiannakis, R. G. (2000). Development of a simulation model for direct injection dual fuel diesel-natural gas engines. SAE Tech. Pap. doi:10.4271/2000-01-0286
Hribar, R., Potočnik, P., Šilc, J., and Papa, G. (2019). A comparison of models for forecasting the residential natural gas demand of an urban area. Energy 167, 511–522. doi:10.1016/j.energy.2018.10.175
Huang, H., Zhu, Z., Chen, Y., Chen, Y., Lv, D., Zhu, J., et al. (2019). Experimental and numerical study of multiple injection effects on combustion and emission characteristics of natural gas–diesel dual-fuel engine. Energy Convers. Manag. 183, 84–96. doi:10.1016/j.enconman.2018.12.110
IEA Oil 2020 – march. 2020. Available at: https://www.iea.org/reports/oil-2020.
Imran, S., Emberson, D. R., Ihracska, B., Wen, D. S., Crookes, R. J., and Korakianitis, T. (2014). Effect of pilot fuel quantity and type on performance and emissions of natural gas and hydrogen based combustion in a compression ignition engine. Int. J. Hydrogen Energy 39, 5163–5175. doi:10.1016/j.ijhydene.2013.12.108
Iorio, S., Magno, A., Mancaruso, E., and Vaglieco, B. (2017). Diesel/methane dual fuel strategy to improve environmental performance of energy power systems. Int. J. Heat. Technol. 34, S581–S588. doi:10.18280/ijht.34sp0254
Jääskeläinen, H. (2019). Natural gas engines. DieselNet. Available at: https://dieselnet.com/tech/engine_natural-gas.php.
Karagöz, Y., Sandalci, T., Koylu, U. O., Dalkiliç, A. S., and Wongwises, S. (2016). Effect of the use of natural gas-diesel fuel mixture on performance, emissions, and combustion characteristics of a compression ignition engine. Adv. Mech. Eng. 8, 168781401664322–13. doi:10.1177/1687814016643228
Karim, G. A. (1980). A review of combustion processes in the dual fuel engine-The gas diesel engine. Prog. Energy Combust. Sci. 6, 277–85. doi:10.1016/0360-1285(80)90019-2
Karim, G. A. (2003). Combustion in gas fueled compression ignition engines of the dual fuel type. J. Eng. Gas. Turbine. Power 125, 827–36. doi:10.1115/1.1581894
Karim, G. A. (2003). Combustion in gas fueled compression: Ignition engines of the dual fuel type. J. Eng. Gas. Turbine. Power 125, 827–36. doi:10.1115/1.1581894
Karim, G. A., Jones, W., and Raine, R. R. (1989). An examination of the ignition delay period in dual fuel engines. SAE Tech. Pap. 120, 892140–31. doi:10.4271/892140
Karim, G. A., and Khan, M. O. (1968). Examination of effective rates of combustion heat release in a dual-fuel engine. J. Mech. Eng. Sci. 10, 13–23. doi:10.1243/jmes_jour_1968_010_004_02
Khalil, E. B., and Karim, G. A. (2002). A kinetic investigation of the role of changes in the composition of natural gas in engine applications. J. Eng. Gas. Turbine. Power 124, 404–11. doi:10.1115/1.1445438
Khayum, N., Anbarasu, S., and Murugan, S. (2020). Combined effect of fuel injecting timing and nozzle opening pressure of a biogas-biodiesel fuelled diesel engine. Fuel 262, 116505. doi:10.1016/j.fuel.2019.116505
King, H. M. Methane hydrate. Geosci News Inf n. Available at: https://geology.com/articles/methane-hydrates/.
Kirsten, M., Pirker, G., Redtenbacher, C., Wimmer, A., and Chmela, F. (2016). Advanced knock detection for diesel/natural gas engine operation. SAE Int. J. Engines 9–1583. doi:10.4271/2016-01-0785
Königsson, F. (2014). On combustion in the CNG - diesel dual fuel engine. Stockholm: KTH Royal Institute of Technology.
Kopyscinski, J., Schildhauer, T. J., and Biollaz, S. M. A. (2010). Production of synthetic natural gas ( SNG ) from coal and dry biomass – a technology review from 1950 to 2009. Fuel 89, 1763–83. doi:10.1016/j.fuel.2010.01.027
Kuo, J., and Dow, J. (2017). Biogas production from anaerobic digestion of food waste and relevant air quality implications. J. Air Waste Manag. Assoc. 67, 1000–11. doi:10.1080/10962247.2017.1316326
Li, Y., Li, H., Guo, H., Li, Y., and Yao, M. (2017). A numerical investigation on methane combustion and emissions from a natural gas-diesel dual fuel engine using CFD model. Appl. Energy 205, 153–62. doi:10.1016/j.apenergy.2017.07.071
Liu, H., Li, J., Wang, J., Wu, C., Liu, B., Dong, J., et al. (2019). Effects of injection strategies on low-speed marine engines using the dual fuel of high-pressure direct-injection natural gas and diesel. Energy Sci. Eng. 7, 1994–2010. doi:10.1002/ese3.406
Liu, S., Wang, Z., and Ren, J. (2003). Development of compressed natural gas/diesel dual-fuel turbocharged compression ignition engine. Proc. Institution Mech. Eng. Part D J. Automob. Eng. 217, 839–45. doi:10.1177/095440700321700910
Liu, S., Wang, Z., and Ren, J. (2003). Development of compressed natural gas/diesel dual-fuel turbocharged compression ignition engine. Proc. Institution Mech. Eng. Part D J. Automob. Eng. 217, 839–45. doi:10.1177/095440700321700910
Liu, Z., and Karim, G. A. (1997). Simulation of combustion processes in gas-fuelled diesel engines. Proc. Institution Mech. Eng. Part A J. Power Energy 211, 159–69. doi:10.1243/0957650971537079
Lounici, M. S., Loubar, K., Tarabet, L., Balistrou, M., Niculescu, D. C., and Tazerout, M. (2014). Towards improvement of natural gas-diesel dual fuel mode: An experimental investigation on performance and exhaust emissions. Energy 64, 200–11. doi:10.1016/j.energy.2013.10.091
Lounici, M. S., Loubar, K., Tazerout, M., Balistrou, M., and Tarabet, L. (2014). Experimental investigation on the performance and exhaust emission of biogas-diesel dual-fuel combustion in a CI engine. SAE Tech. Pap. 2014, 992. doi:10.4271/2014-01-2689
Magno, A., Mancaruso, E., and Vaglieco, B. M. Combustion analysis of dual fuel operation in single cylinder research engine fuelled with methane and diesel. SAE Tech. Pap. 2015;24, 2015–24. doi:10.4271/2015-24-2461
Mansour, C., Bounif, A., Aris, A., and Gaillard, F. (2001). Gas-Diesel (dual-fuel) modeling in diesel engine environment. Int. J. Therm. Sci. 40, 409–24. doi:10.1016/S1290-0729(01)01223-6
Mao, D., Ghadikolaei, M. A., Cheung, C. S., Shen, Z., Cui, W., and Wong, P. K. (2020). Influence of alternative fuels on the particulate matter micro and nano-structures, volatility and oxidation reactivity in a compression ignition engine. Renew. Sustain. Energy Rev. 132, 110108. doi:10.1016/j.rser.2020.110108
Mittal, S., Ahlgren, E. O., and Shukla, P. R. (2018). Barriers to biogas dissemination in India: A review. Energy Policy 112, 361–70. doi:10.1016/j.enpol.2017.10.027
Mustafi, N. N., and Raine, R. R. (2008). A study of the emissions of a dual fuel engine operating with alternative gaseous fuels. SAE Tech. Pap. 2008, 12. doi:10.4271/2008-01-1394
Nag, S., Sharma, P., Gupta, A., and Dhar, A. (2019). Combustion, vibration and noise analysis of hydrogen-diesel dual fuelled engine. Fuel 241, 488–94. doi:10.1016/j.fuel.2018.12.055
Nag, S., Sharma, P., Gupta, A., and Dhar, A. (2019). Experimental study of engine performance and emissions for hydrogen diesel dual fuel engine with exhaust gas recirculation. Int. J. Hydrogen Energy 44, 12163–75. doi:10.1016/j.ijhydene.2019.03.120
Nag, S., Thangavelu, S. B., Tripathi, G., Dhar, A., and Gupta, A. (2017). Studies on temperature variation in automotive exhaust thermoelectric generator with exhaust pipe length. J. Energy Environ. Sustain 3, 82–6. doi:10.47469/JEES.2017.v03.100037
Nielsen, O. B., Ovale, B., and Sorenson, S. Ignition delay in the dual fuel engine. SAE Tech. Pap. Ser. 870589, 1987. 96. doi:10.4271/870589
Nwafor, O. M. I. (2000). Effect of advanced injection timing on the performance of natural gas in diesel engines. Sadhana 25, 11–20. doi:10.1007/BF02703803
opec OPEC monthly oil market report - april 2020. Available at: www.opec.org.
Organization of the Petroleum Exporting Countries (2020). Opec. Available at: https://www.opec.org/opec_web/en/data_graphs/330.htm.
Ou, X., Yan, X., Zhang, X., and Liu, Z. (2012). Life-cycle analysis on energy consumption and GHG emission intensities of alternative vehicle fuels in China. Appl. Energy 90, 218–24. doi:10.1016/j.apenergy.2011.03.032
Papagiannakis, R. G., and Hountalas, D. T. (2004). Combustion and exhaust emission characteristics of a dual fuel compression ignition engine operated with pilot diesel fuel and natural gas. Energy Convers. Manag. 45, 2971–87. doi:10.1016/j.enconman.2004.01.013
Papagiannakis, R. G., and Hountalas, D. T. (2003). Experimental investigation concerning the effect of natural gas percentage on performance and emissions of a DI dual fuel diesel engine. Appl. Therm. Eng. 23, 353–65. doi:10.1016/s1359-4311(02)00187-4
Papong, S., Rotwiroon, P., Chatchupong, T., and Malakul, P. (2014). Life cycle energy and environmental assessment of bio-CNG utilization from cassava starch wastewater treatment plants in Thailand. Renew. Energy 65, 64–9. doi:10.1016/j.renene.2013.07.012
Park, H., Shim, E., and Bae, C. (2019). Injection strategy in natural gas–diesel dual-fuel premixed charge compression ignition combustion under low load conditions. Engineering 5, 548–57. doi:10.1016/j.eng.2019.03.005
pow-methane Methane - fuels for the future. Available at: http://pow-methane.weebly.com/suitability--availability.html.
Purwanto, W. W., Muharam, Y., Pratama, Y. W., Hartono, D., Soedirman, H., and Anindhito, R. (2016). Status and outlook of natural gas industry development in Indonesia. J. Nat. Gas. Sci. Eng. 29, 55–65. doi:10.1016/j.jngse.2015.12.053
Quartz (2014). Why India is spending $330 million a day on imported oil and gas—Quartz. Available at: https://qz.com/247213/why-india-is-spending-330-million-a-day-on-imported-oil-and-gas/.
Qyyum, M. A., Haider, J., Qadeer, K., Valentina, V., Khan, A., Yasin, M., et al. (2020). Biogas to liquefied biomethane: Assessment of 3P’s–Production, processing, and prospects. Renew. Sustain. Energy Rev. 119, 109561. doi:10.1016/j.rser.2019.109561
Ryu, K. Effects of pilot injection timing on the combustion and emissions characteristics in a diesel engine using biodiesel–CNG dual fuel. Appl. Energy 2013;111:721–30. doi:10.1016/j.apenergy.2013.05.046
Selim, M. Y. E. (2001). Pressure-time characteristics in diesel engine fueled with natural gas. Renew. Energy 22, 473–89. doi:10.1016/S0960-1481(00)00115-4
Selim, M. Y. E. (2004). Sensitivity of dual fuel engine combustion and knocking limits to gaseous fuel composition. Energy Convers. Manag. 45, 411–25. doi:10.1016/S0196-8904(03)00150-X
Semin, Bakar R. A., and Bakar, R. A. (2008). A technical review of compressed natural gas as an alternative fuel for internal combustion engines. Am. J. Eng. Appl. Sci. 1, 302–11. doi:10.3844/ajeassp.2008.302.311
Shah, A., Thipse, S. S., Tyagi, A., Rairikar, S. D., Kavthekar, K. P., Marathe, N. V., et al. (2011). Literature review and simulation of dual fuel diesel-CNG engines. SAE Tech. Pap. doi:10.4271/2011-26-0001
Shahraeeni, M., Ahmed, S., Malek, K., Van Drimmelen, B., and Kjeang, E. (2015). Life cycle emissions and cost of transportation systems: Case study on diesel and natural gas for light duty trucks in municipal fleet operations. J. Nat. Gas. Sci. Eng. 24, 26–34. doi:10.1016/j.jngse.2015.03.009
Sharma, P., and Dhar, A. (2018). Compression ratio influence on combustion and emissions characteristic of hydrogen diesel dual fuel CI engine: Numerical Study. Fuel 222, 852–8. doi:10.1016/j.fuel.2018.02.108
Sharma, P., and Dhar, A. (2019). Effect of hydrogen fumigation on combustion stability and unregulated emissions in a diesel fuelled compression ignition engine. Appl. Energy 253, 113620. doi:10.1016/j.apenergy.2019.113620
Sharma, P., and Dhar, A. (2018). Effect of hydrogen supplementation on engine performance and emissions. Int. J. Hydrogen Energy 43, 7570–80. doi:10.1016/j.ijhydene.2018.02.181
Shoemaker, N. T., Srinivasan, K. K., Krishnan, S. R., Gibson, C. M., and Polk, A. C. (2011). Comparison of propane and methane performance and emissions in a turbocharged direct injection dual fuel engine. J. Eng. Gas. Turbine. Power 133, 092806. doi:10.1115/1.4002895
Shukla, M., Singh, K., Tripathi, G., Dhar, A., and Sharma, O. P. (2017). Investigation of performance and emissions of 10 % n-butanol/diesel blend in an IDICI engine. J. Energy Environ. Sustain 3, 77–81. doi:10.47469/JEES.2017.v03.100036
Shukla, M. K., Tripathi, G., Farooqui, S. A., Sinha, A. K., and Dhar, A. (2021). Effect of Au/CeO2 as fuel borne catalysts on performance, combustion and emissions characteristics of CI engine. Clean. Eng. Technol. 5, 100335. doi:10.1016/j.clet.2021.100335
Singhal, S., Agarwal, S., Arora, S., Sharma, P., and Singhal, N. (2017). Upgrading techniques for transformation of biogas to bio-CNG: A review. Int. J. Energy Res. 41, 1657–69. doi:10.1002/er.3719
Song, J., Choi, M., Kim, D., and Park, S. (2016). Combustion characteristics of methane direct injection engine under various injection timings and injection pressures. Proc. ASME 2017, ICEF2016–9. 1–10. doi:10.1115/icef2016-9437
Song, J., Choi, M., Kim, D., and Park, S. (2017). Combustion characteristics of methane direct injection engine under various injection timings and injection pressures. J. Eng. Gas. Turbine. Power 139. doi:10.1115/1.4035817
Stančin, H., Mikulčić, H., Wang, X., and Duić, N. (2020). A review on alternative fuels in future energy system. Renew. Sustain. Energy Rev. 128, 109927. doi:10.1016/j.rser.2020.109927
State-wise Gross Production of natural gas in India during 2014-15 to 2016-17 | open government data platform India blog 2019:2018–9. Available at: https://community.data.gov.in/state-wise-gross-production-of-natural-gas-in-india-during-2014-15-to-2016-17/.
Tabatabaei, M., Aghbashlo, M., Valijanian, E., Kazemi Shariat Panahi, H., Nizami, A. S., Ghanavati, H., et al. (2020). A comprehensive review on recent biological innovations to improve biogas production, Part 1: Upstream strategies. Renew. Energy 146, 1204–20. doi:10.1016/j.renene.2019.07.037
Tabatabaei, M., Aghbashlo, M., Valijanian, E., Kazemi Shariat Panahi, H., Nizami, A. S., Ghanavati, H., et al. (2020). A comprehensive review on recent biological innovations to improve biogas production, Part 2: Mainstream and downstream strategies. Renew. Energy 146, 1392–407. doi:10.1016/j.renene.2019.07.047
Tarabet, L., Loubar, K., Lounici, M. S., Khiari, K., Belmrabet, T., and Tazerout, M. (2014). Experimental investigation of di diesel engine operating with eucalyptus biodiesel/natural gas under dual fuel mode. Fuel 133, 129–38. doi:10.1016/j.fuel.2014.05.008
tepco Fukushima daiichi our business investor relations about TEPCO reaching for sustainability 2009:2009–11. Available at: http://www.tepco.co.jp/en/challenge/csr/sustainability/index-e.html.
Tomita, E., Kawahara, N., Piao, Z., and Yamaguchi, R. (2002). Effects of EGR and early injection of diesel fuel on combustion characteristics and exhaust emissions in a methane dual fuel engine. SAE Trans., 1377–1386. doi:10.4271/2002-01-2723
Tripathi, G., and Dhar, A. (2017). Exhaust heat recovery options for diesel locomotives. Locomot. Rail road transp. Singapore: Springer, 27–40.
Tripathi, G., Dhar, A., and Sadiki, A. (2017). Adv. Intern. Combust. Engine res. New York: Springer, 159–79. Recent Advancements in After-Treatment Technology for Internal Combustion Engines—An Overview.
Tripathi, G., Nag, S., Dhar, A., and Patil, D. V. (2017). Fuel injection equipment (FIE) design for the new-generation alternative fuel-powered diesel engines gaurav. Prospect. Altern. Transp. Fuels, 387–405. Singapore: Springer. doi:10.1007/978-981-10-7518-6_16
Tripathi, G., Sharma, P., and Dhar, A. (2020). Computational study of diesel dual fuel characteristics for varying methane energy shares. Ijaert 11, 311–20. Available at: http://www.iaeme.com/MasterAdmin/Journal_uploads/IJARET/VOLUME_11_ISSUE_3/IJARET_11_03_027.pdf.
Tripathi, G., Sharma, P., and Dhar, A. (2022). Computational study of diesel injection strategies for methane-diesel dual fuel engine. Clean. Eng. Technol. 6, 100393. doi:10.1016/j.clet.2021.100393
Tripathi, G., Sharma, P., and Dhar, A. (2020). Effect of methane augmentation on combustion stability and unregulated emissions in compression ignition engine. Fuel 263, 116672. doi:10.1016/j.fuel.2019.116672
Tripathi, G., Sharma, P., and Dhar, A. (2020). Effect of methane augmentations on engine performance and emissions. Alexandria Eng. J. 59, 429–39. doi:10.1016/j.aej.2020.01.012
Tripathi, G., Sharma, P., Dhar, A., and Sadiki, A. (2019). Computational investigation of diesel injection strategies in hydrogen-diesel dual fuel engine. Sustain. Energy Technol. Assessments 36, 100543. doi:10.1016/j.seta.2019.100543
US EPA (2006). US EPA life cycle assessment: Principles and practice. Scientific applications international corporation.
Wannatong, K., Akarapanyavit, N., Siengsanorh, S., and Chanchaona, S. (2007). Combustion and knock characteristics of natural gas diesel dual fuel engine. SAE Tech. Pap. 9, 1894. doi:10.4271/2007-01-2047
Wei, H., Qi, J., Zhou, L., Zhao, W., and Shu, G. (2018). Ignition characteristics of methane/n -heptane fuel blends under engine-like conditions. Energy fuels. 32, 6264–77. doi:10.1021/acs.energyfuels.7b04128
Wei, L., and Geng, P. (2016). A review on natural gas/diesel dual fuel combustion, emissions and performance. Fuel Process. Technol. 142, 264–78. doi:10.1016/j.fuproc.2015.09.018
Xiao, F., Sohrabi, A., and Karim, G. A. (2007). Reducing the environmental impact of fugitive gas emissions through combustion in diesel engines. SAE Tech. Pap. 6, 1900. doi:10.4271/2007-01-2048
You, J., Liu, Z., Wang, Z., Wang, D., and Xu, Y. (2020). Impact of natural gas injection strategies on combustion and emissions of a dual fuel natural gas engine ignited with diesel at low loads. Fuel 260, 116414. doi:10.1016/j.fuel.2019.116414
Yousefi, A., Guo, H., and Birouk, M. (2018). An experimental and numerical study on diesel injection split of a natural gas/diesel dual-fuel engine at a low engine load. Fuel 212, 332–46. doi:10.1016/j.fuel.2017.10.053
Yousefi, A., Guo, H., and Birouk, M. (2019). Effect of diesel injection timing on the combustion of natural gas/diesel dual-fuel engine at low-high load and low-high speed conditions. Fuel 235, 838–46. doi:10.1016/j.fuel.2018.08.064
Yuan, Z., Ou, X., Peng, T., and Yan, X. (2019). Life cycle greenhouse gas emissions of multi-pathways natural gas vehicles in China considering methane leakage. Appl. Energy 253, 113472. doi:10.1016/j.apenergy.2019.113472
Zang, R., Yao, C., Yin, Z., Geng, P., Hu, J., and Wu, T. (2016). Mechanistic study of ignition characteristics of diesel/methanol and diesel/methane dual fuel engine. Energy fuels. 30, 8630–7. doi:10.1021/acs.energyfuels.6b00716
Zhang, J., Jiang, D., Huang, Z., Wang, X., and Wei, Q. (2006). Performance and emissions of direct injection diesel engine fueled with diesel fuel containing dissolved methane. Energy fuels. 20, 504–11. doi:10.1021/ef0502094
Keywords: methane, dual fuel, compression ignition, engine performance, particulate emissions, combustion characteristics, unregulated emissions
Citation: Tripathi G and Dhar A (2022) Performance, emissions, and combustion characteristics of methane-diesel dual-fuel engines: A review. Front. Therm. Eng. 2:870077. doi: 10.3389/fther.2022.870077
Received: 05 February 2022; Accepted: 29 June 2022;
Published: 12 September 2022.
Edited by:
Zhiguo Qu, Xi’an Jiaotong University, ChinaReviewed by:
Alagumalai Avinash, GMR Institute of Technology, IndiaChen Liang, National New Energy Vehicle Development and Research Center, China
Huan Xi, Xi’an Jiaotong University, China
Copyright © 2022 Tripathi and Dhar. This is an open-access article distributed under the terms of the Creative Commons Attribution License (CC BY). The use, distribution or reproduction in other forums is permitted, provided the original author(s) and the copyright owner(s) are credited and that the original publication in this journal is cited, in accordance with accepted academic practice. No use, distribution or reproduction is permitted which does not comply with these terms.
*Correspondence: Atul Dhar, YWRkQGlpdG1hbmRpLmFjLmlu