- 1Centro de Investigaciones en Óptica A. C., León, Mexico
- 2Facultad de Ciencias Físico Matemáticas, Universidad Autónoma de Coahuila, Unidad Camporredondo, Saltillo, Mexico
The dynamic range of optical fiber refractive index sensors is mainly determined by the refractive index (RI) of the sensor surface in contact with the sample under test. In case of the refractive index sensor based on the hybrid fiber Fabry–Perot interferometer (HFFPI), the largest measurable refractive index value is equal to that of the fiber core. In this work, we demonstrate that it is possible to extend the refractive index dynamic range of a HFFPI by simply adjusting the optical path length (OPL) of the air and solid cavity to be equal or differ by just a small amount. Two isometric versions of the HFFPI (i-HFFPI) with a total length of 100 and 172 μm, where the OPL of the air and solid cavity are very similar, were fabricated and tested. The interferometers were immersed in different samples with a refractive index ranging from 1.000 to 1.733. The response of the interferometers was analyzed in the Fourier domain, and it was possible to establish a one-to-one relationship between the refractive index of the liquid sample and the amplitude of one of the peaks in the Fourier spectra. The amplitude of this peak experienced a linear increment when the RI of the surrounding medium was increased. Tracking the amplitude changes of a Fourier spectrum peak is straightforward which simplifies the online monitoring of the sensor. These features make this compact refractive index fiber sensor very appealing for biosensing applications.
Introduction
Fresnel reflection-based optical fiber refractive index sensors (FR-OFRIS) have proliferated in recent years since their structure is very simple, but also because the sensor interrogation is through monitoring the change in the intensity of the light reflected at the fiber tip end-face (Ran et al., 2008; Gong et al., 2010a; Gong et al., 2010b; Choi et al., 2010; Wang and Wang, 2012; Jiang et al., 2013b; Jáuregui-Vázquez et al., 2013; Chen et al., 2017; Zhu and Huang, 2021). The first and yet simplest approach was reported in 1987, and it basically consisted of a single-mode fiber tip, a laser, a beam splitter, and photodetectors (Meyer and Eesley, 1987). Since then, an important number of fiber-optic sensors to detect physical, chemical, or biological magnitudes using FR-OFRIS have been proposed. Because of their unique features, it is expected that these devices could evolve and, eventually, replace the current refractive index monitoring techniques used in clinical diagnosis (Li, 2020), in petrochemical industries (Joel and Okoro, 2019), or in food and beverage production (Aronne and Malara, 2019), since it is well known that these devices take advantages of the inherent characteristics of optical fiber technology. In some cases, optical fiber sensors are the most suitable or even the unique technological solution, for example, when the amount of the sample or the access to the sample location is a concern. In order to fulfill the demanding requirements of some applications, three important issues, regarding the performance of the FR-OFRIS, must be addressed: first, the relatively poor resolution of these devices compared with that displayed by the evanescent wave-based optical fiber sensors; second, it is well known that the FR-OFRIS response is basically dependent on the changes of the intensity reflected by the fiber tip end-face, and then the accuracy and repeatability of these devices are determined by the optical source stability; and finally, these devices exhibit refractive index ambiguity, that is, two samples with a different refractive index could produce the same intensity response. Ambiguity has a negative impact since it limits the refractive index measurement dynamic range of the FR-OFRIS. Different strategies have been followed to enhance the sensitivity and resolution or increase the dynamic range of these fiber refractometers, but the most successful one involved the exploitation of the optical interference phenomenon. Interesting FR-OFRIS based on multimode interference (MI) (Brientin et al., 2021), strong coupled multicore fiber interferometers (SCMCFI) (Flores-Bravo et al., 2021), Michelson interferometers (MiI) (Meng et al., 2011), or hybrid fiber Fabry–Perot interferometers (HFFPI) (Wang and Wang, 2012; Jiang et al., 2013a; Jiang et al., 2013b; Liu et al., 2017; Rodríguez-Quiroz et al., 2019; Zhang et al., 2021) have been demonstrated. Although the different versions of the interferometric FR-OFRIS proposed so far have contributed to improving the sensitivity and resolution, only the HFFPI version of the FR-OFRIS demonstrated that it is possible to avoid the refractive index ambiguity (Dominguez-Flores et al., 2020a; Rodríguez-Quiroz et al., 2020). To avoid the refractive index ambiguity, it was necessary to deposit a high refractive index thin film in the end-face of the fiber tip (Jiang et al., 2013a; Dominguez-Flores et al., 2020b), to make a post-processing analysis of the reflectance (Dominguez-Flores et al., 2020a), or to photo-imprint an optical fiber Bragg grating in series with the HFFPI (Rodríguez-Quiroz et al., 2020).
In this work, we demonstrate that it is possible to increase the dynamic range of a refractive index-based HFFPI sensor by adjusting the OPL of the air and solid cavity. Typically, the largest refractive index value that can be measured with a HFFPI is smaller than that of the effective RI of the fundamental mode of the SMF core. Two isometric HFFPI (i-HFFPI), with a total physical length of 100 and 172 μm, were fabricated and tested to demonstrate that it is possible to measure the refractive index of the fiber surrounding the medium in a range from 1.000 to 1.733, without ambiguity. This is the first time, to our knowledge, that such ultra-long refractive index dynamic is measured directly from the reflectance of the HFFPI that consists of a capillary fiber (CF) in series with a segment of the single-mode fiber (SMF). The response of the interferometers was analyzed in the Fourier domain; the reflectance exhibited a series of peaks whose amplitude was modulated by the refractive index of the external medium. It was possible to establish a one-to-one relationship between the amplitude of one of the peaks of the Fourier spectrum and the refractive index of the surrounding media. To our knowledge, the largest refractive index dynamic range was measured without ambiguity using fiber-optic sensors (Zhou et al., 2011; Lu et al., 2012; Jáuregui-Vázquez et al., 2013; Liu et al., 2013; Li et al., 2014; Urrutia et al., 2019).
Principle of Operation of the Sensor and Fabrication Process
Analysis of the Characteristic Reflectance of the i-HFFPI
The process to fabricate the HFFPIs analyzed in this work can be described as follows: first, a CF was spliced to a SMF, and then the CF was cleaved to leave a section of length
where
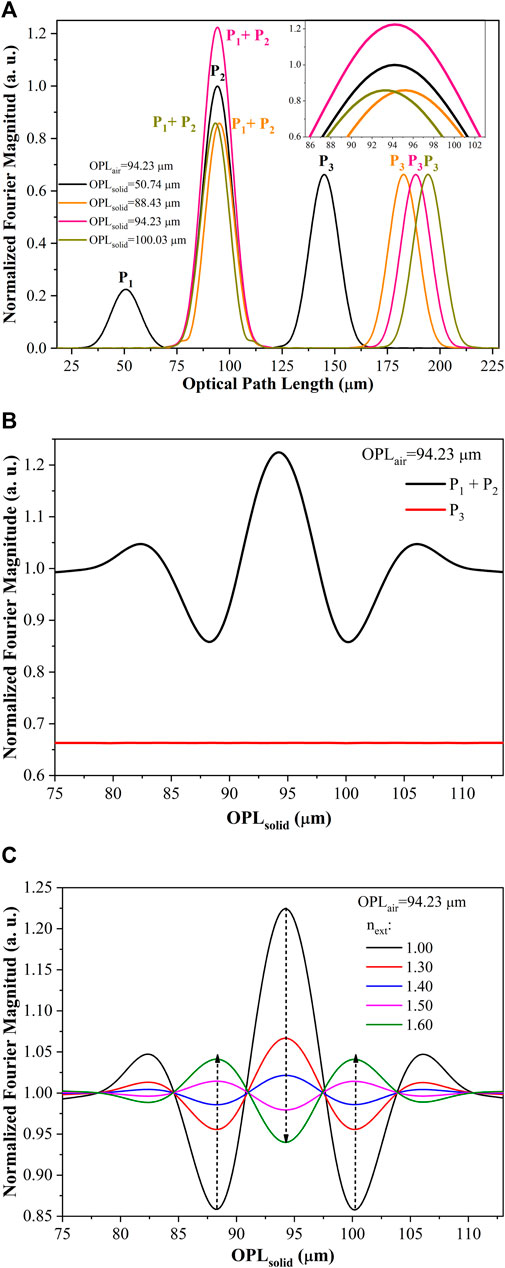
FIGURE 2. (A) Reflectance of the HFFPI in the Fourier domain and (B) maximum amplitude of the overlapped (black line) and
In order to elucidate the behavior of the amplitude of the resulting peak
The effect of the RI of the external medium in the amplitude of the peak
Experimental Refractometric Response of i-HFFPI
From the aforementioned discussion, several i-HFFPI
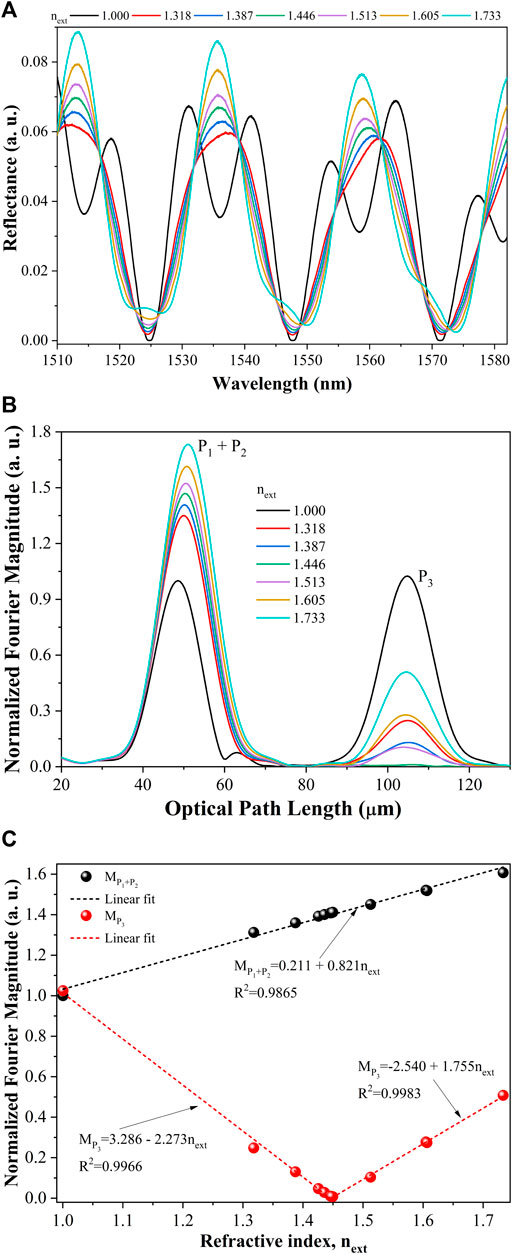
FIGURE 3. (A) Experimental spectra of the optical reflectance and (B) the corresponding Fourier transform. (C) Changes in the magnitude of the Fourier spectra peak when the i-HFFPI was immersed in different Cargille oils.
One important aspect of the response of these devices is the analysis of the stability in time and the analysis of the repeatability. The i-HFFPI with cavity lengths of
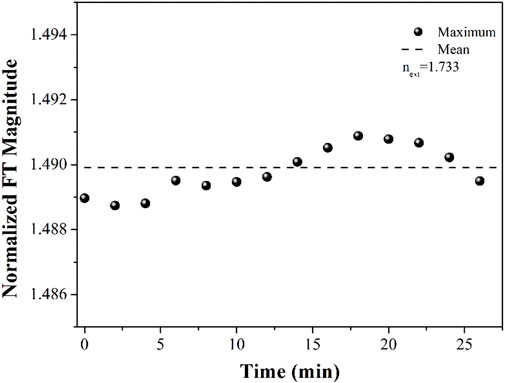
FIGURE 4. Variation of the maximum peak amplitude in time when the fiber tip was immersed in a liquid sample with a refractive index value of 1.733.
The response of the other i-HFFPI was fabricated, this one with
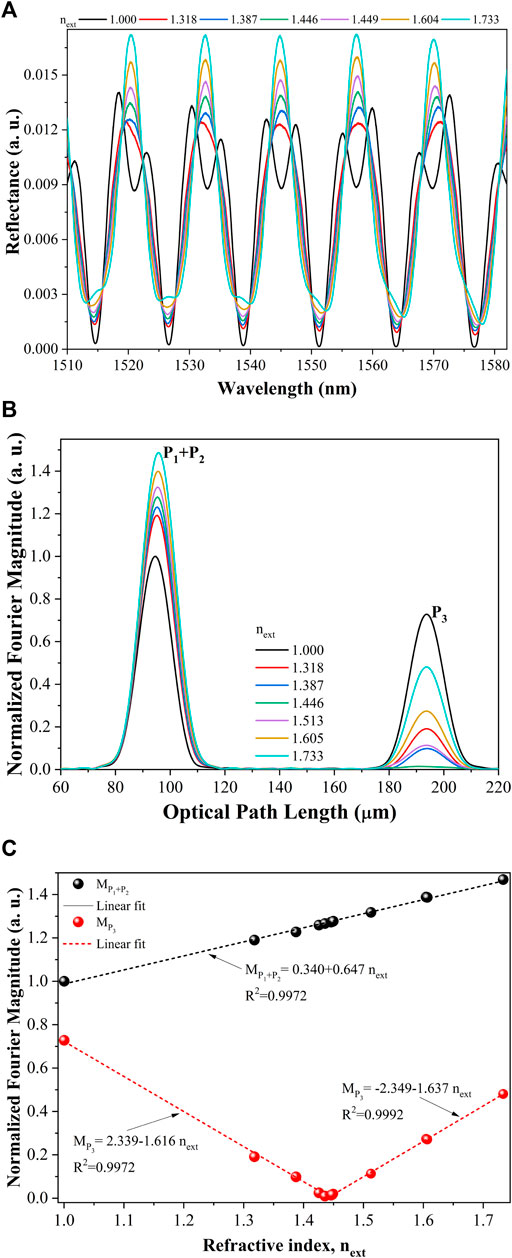
FIGURE 5. (A) Experimental spectra of the optical reflectance and (B) the corresponding Fourier transform. (C) Changes in the magnitude of the Fourier spectra peak when the i-HFFPI was immersed in different Cargille oils.
Conclusion
In summary, an optical fiber refractive index sensor with an ultra-long dynamic range [1, 1.733] was proposed and demonstrated. This sensor is based on the changes of the intensity reflected by the end-face of an isometric hybrid fiber Fabry–Perot interferometer (i-HFFPI) caused by the changes of the refractive index of the fiber tip surrounding the medium. The particular structure of the interferometer, where the optical path length of the air and solid cavities are very similar, allows correlating the refractive index of the surrounding media with the amplitude of one of the peaks of the interferometer spectra in the Fourier domain. In this i-HFFPI, it was possible to avoid the characteristic ambiguity of the FR-OFRIS without the need to coat the fiber tip end-face with a high refractive index thin film. The sensibility of the sensor can be improved by reducing the length of the two cavities of the interferometer. The interrogation technique of this FR-OFRIS is based on tracking the amplitude of one of the peaks of the Fourier spectra, which is simple to be accomplished and easy to be performed online for real-time measurement applications. The structure and fabrication process of the i-HFFPI is also simple.
Data Availability Statement
The original contributions presented in the study are included in the article/Supplementary Material, further inquiries can be directed to the corresponding author.
Author Contributions
CD-F: methodology, formal analysis, investigation, writing—original draft, visualization, and software. DM-H: conceptualization, methodology, formal analysis, writing—original draft, validation, visualization, and software. AV-H: methodology and data analysis. AR: analysis of results, review, and editing. OR-Q: visualization and software. RO-V: conceptualization, writing—review and editing, and resources. All authors contributed to manuscript revision, and read and approved the submitted version.
Funding
This study was funded by Consejo Nacional de Ciencia y Tecnología (México).
Conflict of Interest
The authors declare that the research was conducted in the absence of any commercial or financial relationships that could be construed as a potential conflict of interest.
Publisher’s Note
All claims expressed in this article are solely those of the authors and do not necessarily represent those of their affiliated organizations, or those of the publisher, the editors, and the reviewers. Any product that may be evaluated in this article, or claim that may be made by its manufacturer, is not guaranteed or endorsed by the publisher.
Acknowledgments
The authors want to acknowledge the Consejo Nacional de Ciencia y Tecnología (Mexico) CONACYT for financial support through the Ph. D. scholarship of C. E. Domínguez-Flores and K. Reyes, and postdoctoral scholarship of O. Rodríguez Quiroz.
References
Aronne, G., and Malara, P. (2019). Fiber‐optic Refractometer for In Vivo Sugar Concentration Measurements of Low‐nectar‐producing Flowers. New Phytol. 224, 987–993. doi:10.1111/nph.16084
Brientin, A., Leduc, D., Gaillard, V., Girard, M., and Lupi, C. (2021). Numerical and Experimental Study of a Multimode Optical Fiber Sensor Based on Fresnel Reflection at the Fiber Tip for Refractive index Measurement. Opt. Laser Techn. 143, 107315. doi:10.1016/j.optlastec.2021.107315
Chen, P., Shu, X., Cao, H., and Sugden, K. (2017). High-sensitivity and Large-Dynamic-Range Refractive index Sensors Employing Weak Composite Fabry-Perot Cavities. Opt. Lett. 42, 3145–3148. doi:10.1364/OL.42.003145
Choi, H. Y., Mudhana, G., Park, K. S., Paek, U.-C., and Lee, B. H. (2010). Cross-talk Free and Ultra-compact Fiber Optic Sensor for Simultaneous Measurement of Temperature and Refractive index. Opt. Express 18, 141. doi:10.1364/OE.18.000141
Dominguez-Flores, C. E., Rodriguez-Quiroz, O., Monzon-Hernandez, D., Ascorbe, J., Corres, J. M., and Arregui, F. J. (2020b). Dual-Cavity Fiber Fabry-Perot Interferometer Coated with SnO2 for Relative Humidity and Temperature Sensing. IEEE Sensors J. 20, 14195–14201. doi:10.1109/JSEN.2020.3008167
Dominguez-Flores, C. E., Rodriguez-Quiroz, O., and Monzon-Hernandez, D. (2021a). Simple Signal Processing Method to Enlarge the Dynamic Range of the Fresnel Reflection-Based Fiber Fabry-Perot Refractive index Sensors. J. Lightwave Technol. 39, 1497–1503. doi:10.1109/JLT.2020.3039419
Flores-Bravo, J. A., Fernandez, R., Antonio Lopez, E., Zubia, J., Schulzgen, A., Amezcua Correa, R., et al. (2021). Simultaneous Sensing of Refractive Index and Temperature with Supermode Interference. J. Lightwave Technol. 39, 7351–7357. doi:10.1109/JLT.2021.3113863
Gong, Y., Yu Guo, Y., Yun-Jiang Rao, Y. J., Tian Zhao, T., and Yu Wu, Y. (2010a). Fiber-Optic Fabry-Pérot Sensor Based on Periodic Focusing Effect of Graded-Index Multimode Fibers. IEEE Photon. Technol. Lett. 22, 1708–1710. doi:10.1109/LPT.2010.2082518
Gong, Y., Zhao, T., Rao, Y.-J., Wu, Y., and Guo, Y. (2010b). A ray-transfer-matrix Model for Hybrid Fiber Fabry-Perot Sensor Based on Graded-index Multimode Fiber. Opt. Express 18, 15844. doi:10.1364/oe.18.015844
Jáuregui-Vázquez, D., Estudillo-Ayala, J., Rojas-Laguna, R., Vargas-Rodríguez, E., Sierra-Hernández, J., Hernández-García, J., et al. (2013). An All Fiber Intrinsic Fabry-Perot Interferometer Based on an Air-Microcavity. Sensors 13, 6355–6364. doi:10.3390/s130506355
Jiang, M., Li, Q.-S., Wang, J.-N., Jin, Z., Sui, Q., Ma, Y., et al. (2013a). TiO_2 Nanoparticle Thin Film-Coated Optical Fiber Fabry-Perot Sensor. Opt. Express 21, 3083. doi:10.1364/oe.21.003083
Jiang, M., Qiu-Shun Li, Q. S., Jun-Nan Wang, J. N., Wei-Guo Yao, W. G., Zhongwei Jin, Z., Qingmei Sui, Q., et al. (2013b). Optical Response of Fiber-Optic Fabry-Perot Refractive-index Tip Sensor Coated with Polyelectrolyte Multilayer Ultra-thin Films. J. Lightwave Technol. 31, 2321–2326. doi:10.1109/JLT.2013.2262022
Joel, G., and Okoro, L. N. (2019). Recent Advances in the Use of Sensors and Markers for Fuel Adulteration Detection : A Review. Int. J. Res. Sci. Innov. VI, 82–89. doi:10.51244/IJRSI
Li, J. (2020). A Review: Development of Novel Fiber-Optic Platforms for Bulk and Surface Refractive index Sensing Applications. Sensors Actuators Rep. 2, 100018. doi:10.1016/j.snr.2020.100018
Li, Z., Liao, C., Wang, Y., Dong, X., Liu, S., Yang, K., et al. (2014). Ultrasensitive Refractive index Sensor Based on a Mach-Zehnder Interferometer Created in Twin-Core Fiber. Opt. Lett. 39, 4982. doi:10.1364/ol.39.004982
Liu, B.-H., Jiang, Y.-X., Zhu, X.-S., Tang, X.-L., and Shi, Y.-W. (2013). Hollow Fiber Surface Plasmon Resonance Sensor for the Detection of Liquid with High Refractive index. Opt. Express 21, 32349. doi:10.1364/oe.21.032349
Liu, X., Jiang, M., Sui, Q., Geng, X., and Song, F. (2017). HCPCF-based In-Line Fiber Fabry-Perot Refractometer and High Sensitivity Signal Processing Method. Photonic Sens 7, 336–344. doi:10.1007/s13320-017-0392-6
Lu, P., Harris, J., Wang, X., Lin, G., Chen, L., and Bao, X. (2012). Tapered-fiber-based Refractive index Sensor at an Air/solution Interface. Appl. Opt. 51, 7368. doi:10.1364/ao.51.007368
Meng, H., Shen, W., Zhang, G., Wu, X., Wang, W., Tan, C., et al. (2011). Michelson Interferometer-Based Fiber-Optic Sensing of Liquid Refractive index. Sensors Actuators B: Chem. 160, 720–723. doi:10.1016/j.snb.2011.08.054
Meyer, M. S., and Eesley, G. L. (1987). Optical Fiber Refractometer. Rev. Scientific Instr. 58, 2047–2048. doi:10.1063/1.1139513
Ran, Z. L., Rao, Y. J., Liu, W. J., Liao, X., and Chiang, K. S. (2008). Laser-micromachined Fabry-Perot Optical Fiber Tip Sensor for High-Resolution Temperature-independent Measurement of Refractive index. Opt. Express 16, 2252. doi:10.1364/oe.16.002252
Rodríguez-Quiroz, O., Domínguez-Flores, C. E., Monzón-Hernández, D., Morales-Narváez, E., Minkovich, V. P., and López-Cortés, D. (2020). Unambiguous Refractive-index Measurement in a Wide Dynamic-Range Using a Hybrid Fiber Fabry-Perot Interferometer Assisted by a Fiber Bragg Grating. Opt. Laser Techn. 128, 106236. doi:10.1016/j.optlastec.2020.106236
Rodriguez-Quiroz, O., Dominguez-Flores, C. E., Monzon-Hernandez, D., and Moreno-Hernandez, C. (2019). Hybrid Fiber Fabry-Perot Interferometer with Improved Refractometric Response. J. Lightwave Technol. 37, 4268–4274. doi:10.1109/JLT.2019.2922836
Urrutia, A., Del Villar, I., Zubiate, P., and Zamarreño, C. R. (2019). A Comprehensive Review of Optical Fiber Refractometers: Toward a Standard Comparative Criterion. Laser Photon. Rev. 13, 1900094. doi:10.1002/lpor.201900094
Wang, T., and Wang, M. (2012). Fabry-Pérot Fiber Sensor for Simultaneous Measurement of Refractive Index and Temperature Based on an In-Fiber Ellipsoidal Cavity. IEEE Photon. Technol. Lett. 24, 1733–1736. doi:10.1109/LPT.2012.2212184
Zhang, W., Li, H., Zhu, L., Dong, M., and Meng, F. (2021). Dual-Parameter Optical Fiber Probe Based on a Three-Beam Fabry-Perot Interferometer. IEEE Sensors J. 21, 4635–4643. doi:10.1109/JSEN.2020.3034915
Zhang, Z., He, J., Du, B., Zhang, F., Guo, K., and Wang, Y. (2018). Measurement of High Pressure and High Temperature Using a Dual-Cavity Fabry-Perot Interferometer Created in cascade Hollow-Core Fibers. Opt. Lett. 43, 6009–6012. doi:10.1364/OL.43.006009
Zhou, K., Yan, Z., Zhang, L., and Bennion, I. (2011). Refractometer Based on Fiber Bragg Grating Fabry-Pérot Cavity Embedded with a Narrow Microchannel. Opt. Express 19, 11769–11779. doi:10.1364/oe.19.011769
Keywords: refractometer, optical sensor, fiber optics, Fabry–Perot interferometer, Fourier analysis
Citation: Domínguez-Flores CE, Valdés-Hernández AI, Reyes AK, Monzón-Hernández D, Rodríguez-Quiroz O and Ochoa-Valiente R (2022) Ultra-Long Range Refractive Index Fiber Sensor. Front. Sens. 3:855251. doi: 10.3389/fsens.2022.855251
Received: 14 January 2022; Accepted: 03 March 2022;
Published: 05 April 2022.
Edited by:
Bing Sun, Nanjing University of Posts and Telecommunications, ChinaReviewed by:
Jin Li, Northeastern University, ChinaXinghu Fu, Yanshan University, China
Xizhen Xu, Shenzhen University, China
Copyright © 2022 Domínguez-Flores, Valdés-Hernández, Reyes, Monzón-Hernández, Rodríguez-Quiroz and Ochoa-Valiente. This is an open-access article distributed under the terms of the Creative Commons Attribution License (CC BY). The use, distribution or reproduction in other forums is permitted, provided the original author(s) and the copyright owner(s) are credited and that the original publication in this journal is cited, in accordance with accepted academic practice. No use, distribution or reproduction is permitted which does not comply with these terms.
*Correspondence: David Monzón-Hernández, ZG1vbnpvbkBjaW8ubXg=