- 1Department of Sustainable Development, Environmental Science and Engineering (SEED), KTH Royal Institute of Technology, Stockholm, Sweden
- 2Sustainability Office, KTH Royal Institute of Technology, Stockholm, Sweden
- 3Division of Sustainable and Construction, Mälardalens University, Västerås, Sweden
Circular public procurement (CPP) is one way to increase sustainability and circularity in public spending. As previous research focuses primarily on procurement, more insight is needed on the latter stages CPP. Real-life examples of CPP implementation are also required to promote the concept to practitioners, improve governance, and add depth to the literature. This study, therefore, provides in-depth knowledge of CPP implementation and management by analyzing a case of circular furniture flows and its implications for the procuring organization. The focus on furniture is motivated by the large volumes sent to landfills every year despite its remanufacturing potential, as well as the large environmental impact for production, a potentially long lifetime, and an often-high purchasing price. The results show that strategic decisions to prioritize sustainability are necessary when resource efficiency and cost reductions do not align in a short-term perspective. A more centralized governance structure facilitates decisions on reuse, remanufacturing and disposal in an organization, e.g., coordination of products for remanufacturing, pooling products for reuse, and standardization of design choices. Follow-up and inventory systems are crucial tools for integrating previously installed products with CPP, keeping track of circular flows, and providing feedback to improve subsequent procurements. Crucial elements in the follow-up include adaptation to circularity in the economy system and accounting for the prolonged life and reuse of furniture. The study's results emphasize how an organization's prerequisites play an essential part in the implementation of CPP and that contextual solutions are needed for circular challenges. The study contributes to the fields of policy implementation, CPP, and the use of circular business models in a public context, as well as to the less explored field of procurement in a circular economy context. Suggestions for future research include studies on product categories with other environmental impact profiles, and on waste management regulations that can make or break circular systems.
1. Introduction
Public procurement, i.e., the process by which public authorities purchase goods and services, can be used as a tool for promoting more socially and ecologically sound production and consumption (UNEP, 2014; European Commission, 2015; Alhola et al., 2019). Considering the large volume of goods and services procured each year—in the EU, this accounts for almost 15% of GDP (European Commission, 2015)—public procurement can make a difference to sustainable development if done in the right way (Milios, 2017; Sönnichsen and Clement, 2019). Furthermore, public authorities are essential to implementing the circular economy and achieving national sustainability goals, and thus can lead this transition process (European Commission, 2017b; Alhola et al., 2019; Ntsondé and Aggeri, 2021; Government Offices of Sweden, 2022).
It has previously been stated that the circular economy concept has mostly been driven by practitioners and policy makers (Korhonen et al., 2018). Other studies suggest that research has focused on concepts and less on real-world applications and processes (Leipold et al., 2023). Thus, there is a need to combine empirical implementation studies with concepts. This is supported by Koop et al. (2021) stating that the practical feasibility, both in technical and organizational operations, for business models need to be further examined to achieve a circular economy. Additionally, organizational culture, business strategy and management models have inherent barriers to adopt new ways of working, making these areas important to explore further for the circular economy implementation (Korhonen et al., 2018). In terms of focus areas, the procurement process has not been a main topic in the circular economy field (Eisenreich et al., 2022), even though procurement is stated to be strategically important for circular solutions (Alhola et al., 2019; Farooque et al., 2019). However, in recent years, circular public procurement (CPP) has gained more attention. It can be defined as a purchasing process that aims to “contribute to closed energy and material loops within supply chains, whilst minimizing, and in the best case avoiding, negative environmental impacts and waste creation across their whole life-cycle” (European Commission, 2017b). In the EU's Circular Economy Action Plan (European Commission, 2015), public procurement is identified as one of the best ways to increase sustainability and circularity, and furniture is one of the prioritized product groups. The importance of applying the Eco Design Directive European Commission (2009) to more products is highlighted in the plan, and keywords such as durability, reusability, reparability, remanufacturing and incentivizing products-as-a-service are emphasized for achieving more circularity and sustainability. Although plans and narratives are holistic, the EU's policy focus does not reflect this, and emphasizes ‘end-of-pipe' solutions (Calisto Friant et al., 2021). There is a need for more empirical studies of successful and unsuccessful CPP implementation, as well as product-specific studies to help governments and practitioners keep up with best practices (Qazi and Appolloni, 2022).
Approximately 85% of municipal furniture waste in the EU is sent to landfill or incinerated (EESC, 2022). Although incineration for heat is better from a waste hierarchy standpoint, both landfill and incineration are less advantageous choices from a circular economy perspective than e.g., reuse and remanufacture. These 10 million tons of waste are mainly due to a lack of spare parts and consumer information, as well as poor product quality and design (European Environmental Bureau, 2017). The main environmental impact of furniture stems from production and material supply, while maintenance and cleaning in the use phase are negligible (Cordella and Hidalgo, 2016). Remanufacturing, i.e., refurbishing and upgrading where the value of the product is maintained (Beamon, 1999), is thus an interesting prospect for furniture since it has the potential for a long life and is expensive to replace (Öhgren et al., 2019). However, the fast-changing design preferences for furniture have more in common with fast-moving consumer goods (Pieroni et al., 2021). Thus, design choices to improve remanufacturing possibilities are vital (Sundin et al., 2009). Services to renovate, refurbish, take-back and disassemble are offered by some companies in the furniture sector, but most of the potential has not yet been realized (Pieroni et al., 2021). The reuse of furniture is common but only on a local scale, and this does not fulfill larger environmental and economic goals (European Environmental Bureau, 2017).
This type of circular business model, known as product-service systems (PSS), mainly used in the private sector, is also a way for public procurement to be more resource efficient and decrease consumption (Milios, 2017). While the PSS business models provide drivers and barriers in a private setting such as a need of a changed customer mindset, new payment models and remanufacturing infrastructure, the pubic context provides additional aspects. Studies of CPP often focus on the drivers of, and barriers to, the implementation of this policy tool (Alhola et al., 2019; Kristensen et al., 2021; Lingegård et al., 2021a). Common barriers include a lack of knowledge and resources, a lack of commitment from top management, unfavorable mindset and a lack of product in the market, while drivers include change agents within the organization and clear policy and incentives (Testa et al., 2012; Grandia et al., 2015; Sönnichsen and Clement, 2019; Qazi and Appolloni, 2022). Thus, the barriers span from organizational factors within the procuring organization to the factors including the supply chain in terms of product characteristics.
There are a few studies on the potential of CPP for furniture (Alhola et al., 2019; Öhgren et al., 2019; Kristensen et al., 2021), but studies on implemented CPP for furniture are scarce (Ntsondé and Aggeri, 2021) and more in-depth knowledge is needed. The potential for tension between new and conventional furniture procurement approaches needs to be further analyzed (Ntsondé and Aggeri, 2021), as well as the potential of alternative business models for furniture procurement, including services such as PSS (Besch, 2005; Öhgren et al., 2019). Previous research calls for in-depth studies on procurement practices using observations and interviews to better understand procuring organizations' readiness for CPP (Kristensen et al., 2021).
Unsurprisingly, CPP studies generally focus on the procurement phase, but implementation, management and follow-up are equally important for CPP to achieve true circularity, improve contracts, and connect to the sustainability management of procuring organizations. This implementation of policy at all levels of organizations is essential for successful CPP. Therefore, this study aims to provide in-depth knowledge about the implementation and management of CPP by analyzing an implemented case of circular furniture flows and its implications and challenges for procuring organizations. This is done by specifically focusing on the implementation of the contract and thus providing knowledge on the contextual solutions and the organizational adaptations needed for the circular solutions by building upon previous knowledge in the PSS field. In this way, this study contribute to the implementation of circular solutions in the public sector by combining the fields of policy implementation, organizational change and business models, thus exemplifying the cross-sectional characteristics and the multiple competences needed to promote and implement advances for circular economy in public procurement. Furthermore, the study contributes to the less explored field of procurement in a circular economy context. This article starts with a literature review providing context, a point of reference and foundation for the discussion and thus contribution of the study. Section 3 describes the methodological choices made for this case study, followed by Section 4 where the results of the data collection is presented following the steps of the procurement implementation process. In Section 5 includes the discussion based on the identified themes for implementation challenges and drivers. Finally, the conclusion, limitations and future research suggestions are all in Section 6.
2. Literature review
The existing literature on sustainable public procurement (SPP) and CPP focuses mainly on the procurement stage of the process. It is, therefore, necessary to include other bodies of literature to fully analyze the data on the implementation of CPP in organizations following the procurement stage and contract signing. PSS is a complementary field of literature that offers the perspective of circular business models and is a way to implement circularity through CPP (see, e.g., Bocken et al., 2016; Milios, 2018).
2.1. Product-service systems for furniture
New business models are one way to contribute to the systemic change needed for a circular economy transition (Bocken et al., 2016; Witjes and Lozano, 2016). Product-service systems (PSS) are business models that aim to provide incentives for more intensive product use, reuse of parts, decoupling value from the delivered physical product (see, e.g., Tukker, 2015; Kjaer et al., 2016), and prolonging product life (Bocken et al., 2016). This can be realized by adding additional services to a product, sharing and leasing, and by providing a function, e.g., a result with no predetermined product such as a pay-per-service unit or a function (see Tukker, 2004).
As most of the environmental impact of furniture can be attributed to its production and material supply (Cordella and Hidalgo, 2016), taking steps to prolong its life makes sense. There are a few examples of viable PSS business models for furniture, including services such as refurbishing, relocating and recycling (Copani and Behnam, 2020), maintenance and repair (Inagaki et al., 2022), and remanufacturing (Krystofik et al., 2018). These are all PSS examples based on product offerings with additional services. For any industry to transition into a circular economy, end-of-life processes such as remanufacturing and reuse are important. Reuse is defined as reselling used products or materials without additional processing, while remanufacturing is replacing or refurbishing worn or broken parts and maintaining the original functionality of products (Beamon, 1999). Remanufacturing prolongs product life and decreases the need for material, meeting customer needs by preserving the original value and improving resource efficiency (Pigosso et al., 2010). Barriers to remanufacturing include a lack of standardization for operations, materials and assembly steps, and incomplete information (Kurilova-Palisaitiene et al., 2018). These types of standard or checklist assure best performance and should be developed by the employees directly involved in the process (Kurilova-Palisaitiene et al., 2018). Furthermore, inventory is also key to remanufacturing. The need for access to products for remanufacturing can result in a large inventory occupying space to compensate for fluctuation in the inflow of products (Kurilova-Palisaitiene et al., 2018). Thus, inventory capacity and cost are vital parts of a business model, including remanufacturing (Tolio et al., 2017).
To improve the possibility for remanufacturing, proactive choices must be taken in the design phase (see, e.g., Sundin et al., 2009). Standardized parts in modules can facilitate both servicing and remanufacturing (Lindkvist and Sundin, 2016), and by carefully selecting materials and increasing the use of the furniture, its environmental impact can be reduced (Cordella and Hidalgo, 2016). Design choices made for new furniture need to consider the furniture's lifetime, maximize recycling and remanufacturing options, and consider the materials to be used (Bumgardner and Nicholls, 2020), i.e., minimizing the number of materials and components, making them easy to identity and separate, and increasing the use of recyclable and reusable materials (Cordella and Hidalgo, 2016).
Research generally holds that office furniture is not suitable for a contract where the provider keeps ownership of the furniture, such as leasing or providing a function for the furniture (Besch, 2005; Krystofik et al., 2018; Öhgren et al., 2019). The most common reason for this is that ever-changing design preferences reduce possibilities for reuse (Besch, 2005; Krystofik et al., 2018; Öhgren et al., 2019; Pieroni et al., 2021). Furthermore, the increased complexity of contracts and efforts to change management routines are often too bothersome for procuring organizations (Öhgren et al., 2019).
2.2. Public procurement implementation
Public procurement is a policy tool for promoting more socially and ecologically sound production and consumption (Commission of the European Communities, 2008; UNEP, 2014; Alhola et al., 2019), and CPP has in recent years gained more attention. European Commission (2017a) defines CPP as “a purchasing process that aims to contribute to closed energy and material loops within supply chains, whilst minimizing, and in the best case avoiding, negative environmental impacts and waste creation across their whole life-cycle.”
The use of PSS in CPP has started to gain momentum in various sectors such as food systems (Molin et al., 2021), infrastructure (Lingegård et al., 2021a) and IT products (Crafoord et al., 2018). Previous CPP studies on furniture include conceptual studies of CPP's potential (Öhgren et al., 2019), analyses of the tendering process (Ntsondé and Aggeri, 2021), and overviews of CPP implemented on a smaller scale (Alhola et al., 2019; Kristensen et al., 2021). Thus, there is a clear need to dig deeper into CPP for furniture and include phases other than tendering.
However, CPP requires more than procurement using green criteria (GPP) and sustainable criteria (SPP). Kristensen et al. (2021) identify three other requirements: (1) Earlier market engagement and other technical specifications and criteria, (2) Increased collaboration internally and externally due to life cycle perspective, (3) A shift toward producing more services through PSS, which requires collaboration with new stakeholders and a change in normal practices. Grandia and Voncken (2019) confirm this need for change, saying that public procurers cannot assume they will work in the same way with CPP as with other types of procurement, and that adaption will likely be needed. Furthermore, there are many solutions to the challenges of CPP implementation, but these are also dependent on contextual conditions such as jurisdiction (Qazi and Appolloni, 2022). This also applies to SPP, where factors influencing implementation need to be contextualized to avoid increased bureaucracy and transaction costs (see, e.g., Lingegård et al., 2021b). These are great challenges, considering the tendency of the public sector to rely on existing products instead of promoting innovation (Uyarra and Flanagan, 2010). While government regulation is the main driver of sustainable procurement, frontrunner suppliers and client requirements are right behind (Ruparathna and Hewage, 2015), which shows the importance of a properly functioning procuring organization and market. The lack of knowledge and experience of CPP in the public sector is the main barrier to implementation (Uyarra et al., 2014; Trindade et al., 2017; Vejaratnam et al., 2020).
Furthermore, increased collaboration is vital (Kristensen et al., 2021) and strategies for effectively engaging with suppliers are becoming more important, moving away from compliance-related approaches (Meehan and Bryde, 2011). However, a lack of interaction between procurer and supplier remains the main barrier to the implementation of innovative solutions though public procurement (Uyarra et al., 2014).
The literature points to other vital factors for implementing CPP, such as the commitment to change, understanding the long-term benefits of change, and knowing the organizational strategy and goals at all levels (Sönnichsen and Clement, 2019). To achieve this, individual learning and training, workshops, and dissemination of best practices are crucial (Testa et al., 2016; Sönnichsen and Clement, 2019). In this way, the development of knowledge and organizational capacity is not hindered by potential silo structures (Björklund and Gustafsson, 2015). The reluctance to reuse and regenerate materials due to uncertain quality must also end, since it hinders circularity at all levels of implementation (Qazi and Appolloni, 2022). Public organizations need to consider employees' cautious perceptions of the increased cost of remanufacturing, which are often due to a lack of life cycle cost approaches (Polonsky et al., 2022), w accentuated by additional time and energy spent on finding green alternatives (Rane and Thakker, 2020). There is no typicalal user mindset for circular offerings; instead, it's based on how they perceive the challenges associated with their engagement and behavior related to the offering (Gomes et al., 2022). If not managed, the shift in mindset needed can cause a major barrier to circular offerings (Sundin et al., 2009).
Sustainability policy and guidelines form at different levels (internationally, nationally, and locally) and contribute to a complexity that can cause confusion at the operational level and, therefore, inertia in procurement decision-making (Meehan and Bryde, 2011). This complexity is also due to internal actors with different objectives for, e.g., the procurement criteria used. This becomes more evident in a decentralized organization and can lead to internal conflicts (Polonsky et al., 2022). Organizational changes at every level—including responsibilities, roles, and functions—are thus necessary when implementing policy by public procurement (Testa et al., 2012). To effectively contribute to sustainability, new procedures need to be integrated into organizational strategies, which then create cultural, managerial and operational change (Trindade et al., 2017). Furthermore, top management needs to be committed to sustainability (Brammer and Walker, 2011; Vejaratnam et al., 2020), and bringing it into the procurement process redefines the options and adds a dimension other than price, quality and time (Meehan and Bryde, 2011). This requires new competence as well as new organizational and operational links between different functions in the organization, such as procurement and sustainability (Testa et al., 2016).
Overly specific tenders and a lack of competence and risk management in procuring organizations are other barriers mentioned in the literature (Uyarra et al., 2014). For instance, procurers need to be open to including reused products, in this case, furniture (Öhgren et al., 2019). Specific individuals in organizations are often identified as “change agents” who drive sustainability innovation in procurement, and it is important for top management of public organizations to support such individuals (Eikelboom et al., 2018). Strong leadership and managerial commitment are therefore key determinants of CPP implementation (see, e.g., Brammer and Walker, 2011; Vejaratnam et al., 2020).
3. Method
This study is based on a case study of a public organization (KTH Royal Institute of Technology), where CPP of furniture was implemented. The focus of the case study—conducted between spring 2021 and summer 2022—is the challenges experienced after the contract signing, that is, when implementing the circular furniture flows in the operational activities.
KTH is the largest technical university in Sweden, with 13,524 full-time students and 5,197 employees. It therefore requires a large volume of furniture for its many activities. This was one of the first contract implementations of circular furniture flows for a public organization in Sweden, and this case study provides valuable in-depth insight into it. According to Eisenhardt (1989), case studies can be used to accomplish many different aims, and this study explores the implementation of CPP in a public organization and illustrates the complexity and adaption needed to achieve it. For such an in-depth investigation of complex issues with many variables, a case study methodology is suitable (Merriam, 1998; Yin, 2014). Being a single case study, analytical generalization, where the investigator generalizes a set of results to some broader setting (Yin, 2014), is suitable. In this study, this broader setting includes policy implementation, PSS, organizational change, and circular public procurement processes. These areas were all included in the literature review which focused on providing background, a point of reference and a foundation for the discussion and, thus contribution of the study. This framework consisting of concepts and theories provided the lens though which the phenomena is studied, (see, e.g., Merriam and Tisdell, 2016). In conducting the literature review, keywords from these areas were used with or without the combining with “furniture” or “office furniture” to not only provide a theoretical framework but also state-of-the-art for business models for furniture and thus build on this knowledge.
3.1. Data collection
The qualitative data for this study were collected from documents, by participating in workshops, and by conducting interviews. By using several sources of information, triangulation was made possible (see, e.g., Eisenhardt, 1989). A semi-structured interview guide was used to capture the perspectives of different stakeholders in relation to the circular furniture flows. The main topics and questions about the circular contract were defined, while leaving room for follow-up questions, if needed. Project documentation was used to both complement and confirm the information from the interviews. The documents reviewed included a sustainability plan for the procuring organization, tender documents, documents explaining the schools' furniture purchasing process before the new contract, and the pre-study done by KTH before the procurement process. Additionally, data on the procurement and use of furniture in the organization prior to the CPP contract were collected using a questionnaire. The information was provided by the schools' infrastructure managers, janitors, architects from the real estate department, and the central administration (CA) for waste. Complete data for each school were received.
The primary data were collected from workshops and interviews. Several workshops took place when KTH started implementing the contract. The authors participated in these workshops as observers and facilitators but did not engage in the discussions to avoid influencing the respondents. The notes taken during each workshop were compared with each other and with the data from the interviews, which established the data's reliability and validity (see, e.g., Merriam, 1998). The participating staff came from the central administration and the schools, representing several key roles in the furniture flows (see Table 1). Each workshop had around 20 participants. The initial workshop was held in 2021, but since the administrative routines for the contract took some time to settle, the following workshops were not held until 2022. The workshops provided data regarding the challenges identified, the changes needed, and any other general comments on the contract.
The interviews aimed to gain more in-depth knowledge (see, e.g., Kvale, 1997) about the challenges identified and actions needed regarding the implementation of the project and new contract. The selection of the ten respondents, see Table 2, emphasizes the representation of different governance levels as well as key functions in the implementation of the contract, such as responsible for waste management, budget, or inventory. The selection was made both from data collection in terms of workshop material and also in regards to important functions and key stages from the literature (e.g., previously identified barriers or key functions) guiding the decision. The interviews were conducted and recorded at the end of June 2022 and each interview lasted between 40 and 60 min. The respondents were chosen from the CA and the schools, so the results are applicable to the whole organization. A semi-structured interview guide (see Appendix 1) was used with defined key topics and questions about furniture flows and CPP implementation, but it still allowed for follow-up questions, if needed. The same interview guide was used for all the respondents but the focus of their answers depended on their role in the organization and the implementation of the contract. Finally, the interviews were summarized and sent to the respondents to verify and validate the data (see Patton, 2002).
3.2. Data analysis
The documents and data from each school provided background information on the procurement process and the criteria for CPP, while the workshop data shed light on the complex and intertwined changes needed for the implementation to work. The interviews provided more depth on these changes, as well as the perspective of each key actor.
Illustrating the circular furniture flows, Figure 1 was created based on documents and workshop data. It was essential to pin down the key stages and flows needed in the organization for the flows to function. In this way, a common picture could be used during the interviews to further analyze the flows and the challenges that arose.
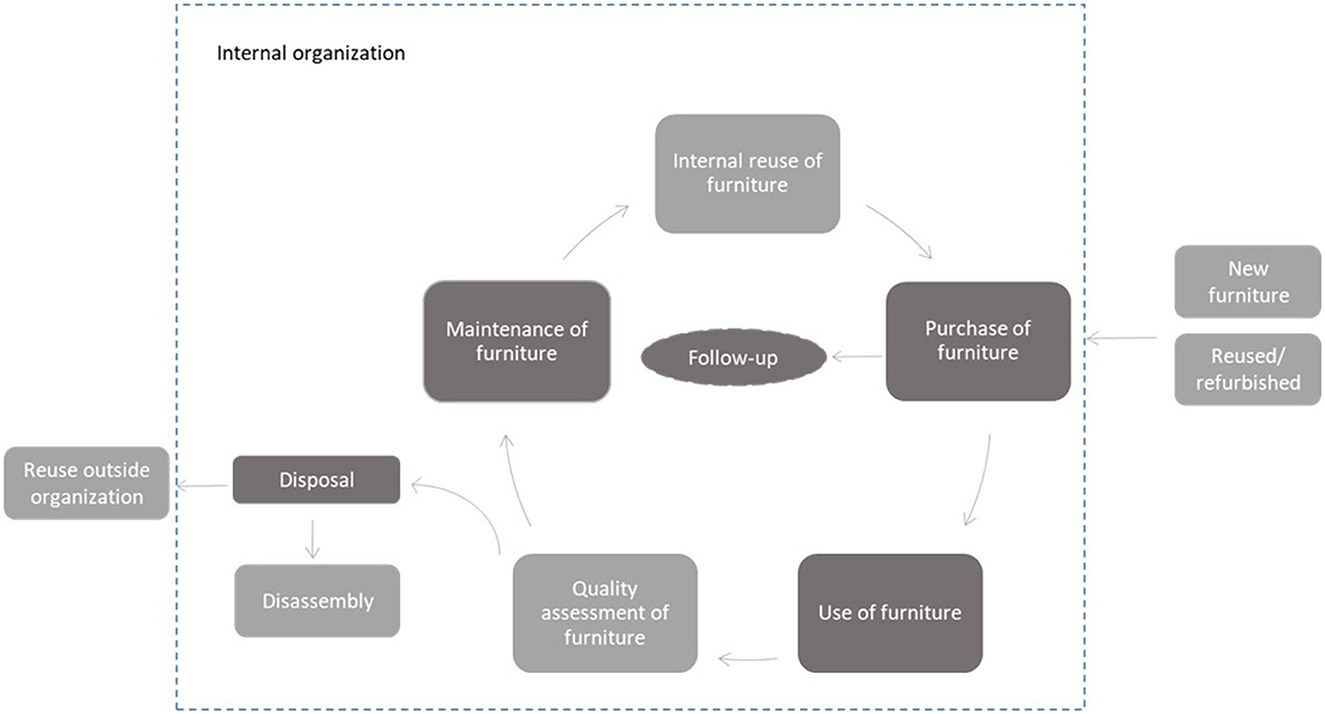
Figure 1. Illustration of the circular furniture flows, where darker boxes indicate the main stages. Purchase of furniture: (1) internal reuse, (2) external reuse, and (3) external new. Use of furniture: products in use. Quality assessment of furniture: (1) maintenance of furniture, and (2) disposal. Disposal of furniture: (1) disposal and disassembly in fractions for recycling or landfill, and (2) external reuse and potential later recycling. Maintenance of furniture: (1) no action, (2) reconditioning, (3) renovation, and (4) re-design, e.g., repainting. Internal reuse: (1) intermediate storage, and (2) direct reuse. Follow-up: performed yearly for purchases.
The data from the interviews were categorized according to the key stages derived from Figure 1 (purchase, use, maintenance, disposal, and follow-up). This categorizing of data was performed for each respondent. Brief summaries and keywords were used to condense the respondents' answers for each stage. This provided an overview of the interview data, hence themes including the major challenges and drivers for the implementation of the CPP contract in the organization could be identified. These three overarching themes, identified in the different stages of the furniture flows, focused on organizational governance, product design and business models and knowledge and information in regard to users and process owners. The discussion is structured following these three themes: (1) Governance, support and follow-up, (2) Ownership and standardization, and (3) Knowledge, information and attitudes. The identified themes and key aspects were compared to the literature in a pattern-matching approach (see, e.g., Yin, 2014). These themes were then discussed using the PSS literature to complement the policy implementation literature, thus providing an in-depth discussion of the implications of the implementation of the CPP contract.
4. Results
In this section, KTH's furniture procurement process prior to CPP is presented, as well as the strategy that led to CPP and the key aspects of the CPP tender. The implementation of the circular furniture flows in the organizational processes is then presented based on the interviews and workshops.
4.1. Sustainability management and goals
Internal policy documents and the interview with the head of the real estate group provided the contextual background on why KTH decided to engage in CPP for furniture. As a part of its environmental management system, KTH had an overall sustainability goal (2021–2025) and climate goals for 2045 to manage its resources in line with sustainable development. From a procurement perspective, the goal was to include a life cycle perspective and sustainability criteria for all purchases (KTH, 2022)—for furniture, this meant increasing the lifetime and reduce the waste. The real estate group and sustainability office at KTH started the project “Circular furniture flows” in 2021. At the time, neither framework agreements for the public sector nor any circular criteria were available from the National Agency for Public Procurement.
4.2. Contract criteria and scope
The key aspects of the CPP for furniture were reviewed in the tender documents and other internal documentation on the contract. The contract was procured in 2021 and the supplier was asked to provide quality products from a circular and sustainability perspective, including services to prolong the lifetime of the products. The services and circular criteria used included:
• Product-related services such as wallpapering and repair of furniture.
• Repossession of discarded furniture. Loan/rental of furniture in agreed time periods.
• Assembly, inventory, delivery control, unpacking and removal of packaging.
• Services such as reconditioning, renovation and re-design, e.g., repainting/resizing.
• Renovation of existing furniture with at least a 1-year guarantee.
• At least 10% of the products can be re-used and at least 20% can be renovated/recycled, such as removable textiles or simple disassembly.
• Option for barcode marking of furniture.
• Sale of furniture at market value on the supplier's website.
• Removal of furniture for disposal.
Additionally, all products had to comply with Swedish standards (Möbelfakta) regarding ergonomics, safety and durability for furnishings in public environments. The 4-year framework agreement was estimated to be worth 8 m euros, including new purchases and remanufacturing services. Two tenders were received from two suppliers. Eighteen months into the CPP contract, remanufacturing accounted for 13% of all purchases. The contract provided an option for the disposal of furniture, though KTH had a separate contract for waste management on the campus.
4.3. The supplier perspective
The supplier had 10 years of experience with its business model, including reuse and remanufacturing. In the interview, the supplier explained that these concepts were increasingly sought after by buyers, and that sustainability had become a vital part of its brand. Generally, the supplier acted as a middleman, providing new furniture from manufacturers. The supplied furniture conformed to environmental standards and was slightly more expensive than other options. The main purpose of the contract for the procuring organization was to reduce new purchases, and the supplier also provided remanufacturing services. The supplier stated that customers generally viewed remanufacturing as a bit expensive, but also that it was necessary to increase adoption to generate an economy of scale in order to lower prices.
4.4. Main stages in the circular furniture flows
The implementation of the circular furniture flows is illustrated in Figure 1, which was created using documentation from the tender and the contract, as well as additional information from the workshops. The key stages of the flows (purchase, use, maintenance and disposal, and follow-up) are indicated with a darker color. The important work processes (acting as the glue between the main stages) are illustrated with lighter boxes.
4.5. Purchase of furniture
4.5.1. Prior to the CPP contract
Every school and the CA purchased furniture for offices and lab environments using their annual budget. In four out of the five schools, the institutions owned the furniture, while in the fifth school, the furniture was owned by the school. The real estate group, which was centrally responsible for KTH's properties, owned all the furniture for the teaching and study spaces. The purchasing function differed between schools, and each school had appointed their own personnel to purchase furniture for the institutions. Some schools had service centers that purchased furniture after input from a customer (teachers and researchers) at the institutional level. In others, furniture was purchased by an appointed person (e.g., the head of the school or department). Either way, the purchases needed approval from someone in the Department. One of the schools had decided on a standard design for office furniture available for every employee, and all purchases were centrally managed by the school. The purchase of non-standard furniture had to be approved by the financial manager.
4.5.2. Implementing the CPP contract
The supplier emphasized remanufacturing services as an important part of its business model, and said that the requirements for reuse services and sustainability in the tender had been clear from the beginning. The supplier also said the main challenge was the next step, which was implementing the contract in the whole organization, as this would require users to be trained on the reuse services, understand the circular flows, and why it was important to work with reuse and sustainability. This view was shared by the resondents that emphasized the need for the contract to be continuously promoted in the organization. The infrastructure officer and the architect from the real estate group suggested having a centralized organization for sharing information and following up on the contract and the furniture flows, stating that “we should be one KTH.”
None of the respondents had any direct criticism of the contract. In the procurement stage, the relevant sustainability requirements were set, but the respondents said the requirements were mostly suggested by the real estate group. As described by one contract officer, the real estate group had “the right skills and a strong drive to work with circular furniture flows and contribute to the university sustainability goals.” Still, most respondents pointed out that the responsible and knowledgeable people in the schools were not involved early on in the procurement process. One procurement officer from a school pointed out that this could harm the implementation since the services procured may not correspond to the real needs of the schools. The head of the real estate group said that, for future circular procurements, the schools needed to be involved at an early stage in order to communicate their needs.
KTH has tried to have design concepts for each building, and the architect at the real estate group stated it was important not to move furniture between buildings. This was discussed in a workshop as a potential barrier to the reuse of furniture and problematic in terms of the need to have separate storage rooms for each building. The real estate manager suggested having centralized ownership of furniture to minimize the purchase of cheap furniture or furniture outside the standard. She also called for stricter governance on what types of furniture were included. However, one of the janitors said increased standardization might provoke some users who were used to making their own design decisions.
4.6. Use, maintenance and reuse of furniture
4.6.1. Prior to the CPP contract
There was no complete inventory or inspection of all furniture at KTH, including both furniture in use or in storage, although the real estate group carried out an annual inventory in educational environments and CA offices. Inventory and inspection of furniture were usually carried out in connection with renovation or construction of buildings. There was an annual monitoring of the cost of furniture purchased each year, but not the volume purchased. Similarly, the volume of reused and discarded furniture was unknown. As far as the renovation of furniture was concerned, some maintenance took place and parts of furniture (e.g., spare tops and underframes of chairs) were kept in storage. Additionally, some furniture was given to the recycling center for disassembly. It was common to discard old used furniture and purchase new items during renovation, relocation, or staff changes, and this was sometimes cheaper than refurbishing. Schools tried to refurbish and have storage rooms for used furniture. Janitors in some schools communicated with each other about used furniture that could be used as an alternative to new purchases. However, if no one wanted the furniture, it was discarded.
4.6.2. Implementing the CPP contract
The respondents all agreed that there was no formal procedure for the CA and the schools concerning the reuse of furniture, and they all had different procedures for renovating furniture. The head of the department at one school pointed to the need for school-level information on how to use the services in the contract. Most of the respondents were uncertain whether furniture could be given to staff and students and how to circulate it internally among the schools and the CA. The purchasing officer at one school said: “It is important to have good procedures to make it easy to do the right thing. Otherwise, the resistance will build.”
Both central and school-level respondents pointed to the challenges of decentralized organization, where each school was responsible for the management of its furniture. The need for training and common procedures was highlighted by the controller at the economic department. One janitor described the difficulty of finding information on other schools' furniture in storage that could be reused at his school and be a cheaper alternative to purchasing new. The head of the real estate group pointed to the need for communicating procedures to the responsible people at the school-level. Procedures should include how to reuse furniture and how to apply and monitor the contract during the contract period. The central contract officer thought it important to communicate to all persons involved that they had a responsibility to adapt to circular furniture flows. As an infrastructure officer at one of the schools pointed out: “We need to have a common forum for discussing the reuse of furniture at KTH.”
Most of the respondents were also missing financial incentives to reuse furniture. One barrier identified by janitors and purchasing officers was the cost of refurbishing: “It is more expensive to refurbish than to buy new furniture,” a janitor stated. One architect stated that larger batches of similar furniture sent for remanufacturing lowered the cost per item, and that this was an approach used by the CA. However, a janitor stated that this also created challenges for smaller projects and everyday changes of furniture: “We will not have large batches unless we store the used furniture, which will be expensive for the school considering the rent for a storage facility.” The head of the real estate group explained that cost could not be the main incentive for sustainability, since it was easier and cheaper to buy new than to reuse and renovate. The driver had to be sustainability itself, even though economic incentives generally steered decisions according to the head of the group. She also added that the geopolitical changes in the world were affecting delivery times of new products, and were creating bigger incentives to take care of current stock.
The economy controller and contract officer at the CA's economic department reflected on the weaknesses in the planning of furniture purchases, which made it easier to buy new instead of refurbishing. The weakness was the short lead time between the decisions and when the furniture was needed, which left no time to renovate, find used furniture from other schools, or buy reused furniture from the supplier. The CA's janitor pointed out the need for clearer mandates and responsible managers to prioritize reuse over new purchases. The economy controller expressed a similar view that KTH needed to prioritize the sustainability goals and be aware that this initially could cost more. All the respondents agreed it was important to change from linear to circular furniture flows to achieve the sustainability goals. The interviewed janitor at the school and the CA for waste both emphasized that it was important to reuse furniture and avoid wear and tear. The head of the real estate group added: ”In order for this to be sustainable in the long term, the whole society needs to switch to circular flows.“
4.7. Disposal of furniture
4.7.1. Prior to the CPP contract
There was no centralized management for the sale and disposal of furniture, with each school and the CA being responsible for their own furniture. The CA for waste had responsibility for the contract with the supplier of disposal services. The schools used this supplier to handle their furniture disposal. Furniture could be disposed of due to ergonomic aspects, e.g., when changing to adjustable tables for all employees. If there were tabletops in good condition, the challenge was to find working underframes, for instance. Furniture that was deemed unsuitable but was still functional was sometimes given to, or traded with, other schools. However, the respondents were uncertain whether a public organization was allowed to give away furniture in this way. In one of the workshops, an economy controller explained that giving furniture to internal and other public organizations was permissible.
In general, the disposal of furniture and how this was done depended on the individual employee and their networks. However, if the furniture was broken, the schools usually engaged the organization's craftsmen to dispose of it. In the case of large volumes, the schools would bring in containers and collect furniture for disposal. A similar process was used by the CA.
4.7.2. Implementing the CPP contract
The CA for waste and the janitors agreed it was easy to get the waste supplier to pick up furniture for disposal, and they worked together to take care of it. Although there were no formal procedures in place for the CA and schools to sort furniture for disposal, everyone had similar informal practices as the same supplier was procured for all disposal services. There was no forum for janitors and the CA for waste to share information and follow up on waste management. A more efficient process, working with the supplier to follow up the flows internally was suggested. They all agreed it was important to develop these procedures so that circular flows could be implemented to meet legal requirements for waste. Furthermore, the CA for waste stated that, in the following year, additional legal requirements for textiles would be introduced in waste management. These included the disassembly of furniture into fractions which was not always done at the time. Additionally, they highlighted the need for a common warehouse at the university for storing furniture instead of the 39 rooms currently in use for waste management. The head of the real estate group explained the need for a properly staffed recycling station on-site: “Not every person at KTH can stand with a screwdriver and work with furniture disassembly.” Giving janitors and other school staff the responsibility to physically move furniture for reuse or for disposal, was proposed during the workshops, but the CA for waste thought this would reduce the possibility of disposing of the furniture immediately. Instead, suggestions for an additional external supplier to collect, sort, and disassemble furniture were offered.
For larger projects, it was easier to make decisions from a waste management perspective in line with the CPP contract, while, in everyday work, decisions were made at short notice. During the workshops, this difference was highlighted as a challenge for the full implementation of the CPP contract. The need for the operational part of the organization to adapt and create lead times in the process was seen as an important step going forward. The head of department at one of the schools said there was a strong willingness within the organization to work with circular furniture flows, so the necessary changes needed to implement them were manageable.
4.8. Follow up on the furniture flow
4.8.1. Prior to the contract
No one has the complete picture of all the furniture in use and in storage at KTH. This weakness is partly due to inefficient procedures at the economy department, which needs a better way to support the manual inventory done by the CA and the schools every year. Furthermore, purchased furniture was registered but, most of the time, not specified; as one janitor explained: “The specifications stated interior decoration for House X−2 million SEK. It is impossible to derive the details.” Also, once its economic lifetime had elapsed, the furniture was not visible in any system. Incentives for central storage of furniture did not exist and each department stored its own. The head of department at one of the schools explained the result of this: “Many cubic meters of old furniture from previous inventory rounds are stored in the attic and forgotten.”
4.8.2. Implementation of the CPP contract
The respondents from the CA and the schools all agreed that the monitoring of furniture needed to be improved in the organization—both centrally at the CA level and within schools. The head of the real estate group said they had statistics from the supplier regarding what was purchased and the quantities, but that this was not communicated and analyzed for understanding the furniture flows. As the CA for waste pointed out: “The university needs to have an internal inventory and monitoring system to follow the flow of furniture within the university”—that included the furniture in use and in stock. However, during a workshop, the CA for waste and the janitors deemed this difficult due to the lack of current inventory, which made it impossible to gain an overview of the furniture in use prior to the contract. During the workshops a digital solution was proposed for inventory, but it could not be supplier-specific since KTH needed to own its own inventory even when a new supplier was awarded a contract. The janitors argued for a tool, such as an app, that could easily be used for inventory. This initiated a discussion on using labels on furniture, but this was seen as an expensive solution. As a next step, a meeting was suggested with the procurement department to discuss how to procure a digital inventory tool.
The identified challenge of managing the reuse of furniture, and the amortization of the value of the furniture between departments in the economy system, prompted the CA's economy controller to call a joint meeting after the second workshop. The head of procurement, the inventory controller, the project leader, and the head of sustainability all participated in this meeting and the agenda was, as the economy controller put it, “to focus on how to solve these issues and not whether it is possible to solve them.” After the meeting, the economy controller emphasized the importance of “starting discussions outside their organizational silos.” Ultimately, the meeting created more questions than answers, but it was seen as a step in the right direction. It was decided that new furniture would be introduced into the economy system first, and then the furniture in use would be included with the help of the future inventory tool. However, issues such as how long furniture would be allowed to stay in storage before sale or disposal, how to account for sales between schools, and what resources to use for this additional workload, remained to be solved.
Besides an inventory of the furniture in use and in storage, the waste indicator was another major measure highlighted during the workshops. The infrastructure officer and the purchasing officer at one of the schools considered this important to improve the contract and the work on reuse, despite the barriers. The architect at the real estate group argued that, “we also have a responsibility to follow up against the university's sustainability goals and the indicators that exist to ensure that the amount of furniture that becomes waste is reduced.” The Architect added that the responsible people also needed information showing whether their work had been successful in increasing the reuse of furniture.
5. Discussion
This discussion is structured into the three overarching themes identified in the different stages of the furniture flows: (1) Governance, support and follow-up, (2) Ownership and standardization, and (3) Knowledge, information and attitudes. These themes highlight the major challenges for the implementation of the CPP contract in the organization.
In this case, the CPP contract included both reuse and remanufacturing of furniture. When compared to Figure 1's options available for maintenance, option 1 (no action) corresponds to reuse, while options, 2 (reconditioning), 3 (renovation), and 4 (re-design) are all types of upgrade and are thus remanufacturing as defined by Beamon (1999). If compared to the PSS types, this CPP contract corresponds to a product-related PSS where the product is the main part and different types of services are added (see Tukker, 2004). However, it became evident from the analysis that this contract was not complete in terms of the services needed to support the circular flows. For instance, additional moving, transport and disassembly services were needed to reduce workload for existing staff and facilitate implementation. CPP is a learning process for every procuring organization, and this was the first attempt at KTH. The knowledge and experience gained from this CPP process can improve future procurements by overcoming the knowledge barrier that is a major obstacle for CPP implementation (Testa et al., 2016; Sönnichsen and Clement, 2019).
5.1. Governance, support and follow-up
The organization had sustainability goals for public procurement, and even though circularity was not mentioned specifically, life cycle perspective, resource efficiency and sustainability criteria were emphasized (KTH, 2022). The incentive for KTH to adopt remanufacturing, therefore, was its ambition to reach its sustainability goals for reduction of waste and improved resource efficiency through public procurement. For this reason, the top management made strategic decisions that were important for policy implementation though CPP (Testa et al., 2012; Vejaratnam et al., 2020). However, when resource efficiency and cost reductions did not align, the staff requested mandates and incentives for sustainability. The procuring organization was large and had both the resources and knowledge to perform a CPP process. However, the same aspects that facilitated the procurement process hindered the implementation of the circular flows in the organization. Due to its large size, the organization consisted of five different schools and several departments within each school, which created a decentralized governance structure. Decentralization is known to add to the complexity of procurement processes (Polonsky et al., 2022) in organizations where confusion exists due to the mix of policy and guidelines at different levels (Meehan and Bryde, 2011). In this case, the furniture was procured, used, maintained and disposed of as deemed practical for each school, resulting in a diverse stock of furniture in use and in storage. The CA, which was in charge of furniture for educational spaces, also had a parallel process for handling furniture that made it more complicated.
Generally, a significant risk for remanufacturing companies is the fluctuant inflow of used products (Kurilova-Palisaitiene et al., 2018), while in this case the main risks were more or less put on the procuring organization. For instance, the cost and capacity for furniture inventory, identified as a vital part of remanufacturing businesses (Tolio et al., 2017), all fell on the procuring organization, as did the huge challenge of keeping track of furniture inventory. The lack of overall inventory was a fundamental problem for KTH that seemed very difficult to solve. In fact, the staff thought it impossible to identify all the furniture already in use and they therefore wanted to focus only on new furniture. Thus, uncertainty over the installed base of furniture created a challenge when the new circular flow of furniture was to be implemented. This type of information is essential for circular flows to work, and Kurilova-Palisaitiene et al. (2018) emphasize the importance of complete information regarding products in remanufacturing processes.
Thus, a functional, accessible and up-to-date inventory system was needed. The organization needed to decide whether to include all the existing furniture or just a selection since this was a task the janitors deemed insurmountable. This system needed to be compatible with the economy system to avoid unnecessary transaction costs and hindering follow-up of the flows. KTH also needed to decide how and to what supplier the system would be delivered, since ownership of the inventory was needed by KTH even if the supplier changed. This potential lock-in effect, where suppliers own vital information, can create information asymmetry. Ownership of its own statistics is crucial for any organization keen on following up on cost and sustainability goals, as well as tracking continuous improvement, e.g., ISO 14001 (ISO, 2015). In this case, these statistics needed to include inventory, such as the type of furniture and cost, as well as the volume of disposed furniture, since the organization had a goal to reduce waste. Thus, monitoring needed to happen both from the CA and at the school-level in order to complete the flows. Information was also needed about the volume and condition of the furniture. To ensure the best performance, all this information had to be structured in a standardized way that was adapted to the remanufacturing process (see, e.g., Kurilova-Palisaitiene et al., 2018).
This inventory system also needed to be compatible with the organization's economic system. However, KTH's economy system was based on a linear flow of products and thus struggled to adapt to a circular approach. Several challenges were identified in relation to the furniture flows, e.g., the lack of inventory for the installed base of furniture, and the fact that furniture was no longer visible in the system once its economic lifetime had expired. Additionally, the management of reuse between departments and schools created issues with the amortization of the economic value. All this pointed to an economic governance in need of change in order for the circular furniture flows to be fully implemented.
5.2. Ownership and standardization
The diversity of furniture types and design choices within the procuring organization caused problems when implementing the circular flows. The different schools and buildings had different design concepts, which, over time, were compromised when ad hoc furniture purchases were made. The organization thus struggled to maintain a uniformity of furniture in use and keep a coherent design with the contrasting new and old furniture. This lack of uniformity can hinder the remanufacturing process, where standardization both in terms of products and procedures is beneficial (Kurilova-Palisaitiene et al., 2018). Implementing a standard assortment of furniture and transferring the ownership of furniture to the CA would create better prerequisites for coordinating the purchase and maintenance of the furniture. In this way, the maintenance cost per item would decrease if larger batches were used, facilitated by a common storage station, and the reuse of furniture would be facilitated by having similar furniture everywhere. The common storage station would also solve the high cost of storing furniture at the school-level, as pointed out by a janitor. This is important, as inventory cost and capacity are essential parts of any remanufacturing business model (Tolio et al., 2017). Thus, it is crucial to understand that a high level of furniture storage is undesirable, except to coordinate larger batches for remanufacturing or reuse, while minimizing intermediate storage.
However, contrary to most examples in the literature, these aspects and the risk of fluctuations in the inflow of products were on the procuring organization, not the supplier. This would not have been the case if the business model had been more geared toward proving a result (see Tukker, 2004), since the supplier would then have been responsible for the flow. From the supplier perspective, the business models had been developed to meet the increased market demand for circularity and remanufacturing. However, a significant part of the contract was still new furniture purchases, thus remanufacturing services could be seen as more of an add-on than the core of the contract. The procuring organization intended to keep buying new furniture, using environmental criteria, and limiting the choices to a few models and designs. This would benefit future remanufacturing, since the critical design phase sets the possibilities for remanufacturing and disassembly (Sundin et al., 2009; Cordella and Hidalgo, 2016; Öhgren et al., 2019; Bumgardner and Nicholls, 2020). Future procurements could also include more result-based PSS (see Tukker, 2004) if there is a more homogenous base of furniture and if the procurer has sufficient knowledge to handle the additional complexity this might entail.
For larger projects, larger batches of furniture are easier to create, but everyday changes of furniture will likely create coordination issues and maintenance costs that might be hard for a department or school to bear. Larger renovation projects will eventually become part of management and everyday life. To secure an inflow of furniture for remanufacturing and reuse in the storage station, the organization must create guidelines on which options to choose after the use stage. E.g., factors supporting the decision on when furniture should be given away or sold internally. Other options are to disassemble and reuse parts, or exit the internal loop and sell through the supplier. KTH's routines and guidelines at the time of the interviews were adapted to a linear flow with a start and an end, and the new routines need to support the circular flows. According to Kurilova-Palisaitiene et al. (2018), routines and guidelines are best formulated by the employees directly involved in the process, so janitors and employees with budget responsibility are key actors here, since only they know what support they need in these stages.
Also, it became evident from the barriers to sending furniture for maintenance or using refurbished furniture, that the challenges in the organization extended far beyond the lack of guidelines. Additional services were needed to collect, disassemble and transport furniture within the organization, so the contract needed the assistance of third-party services to function. In this way, the additional workload on the employees was reduced, which was important since the perceived time and effort spent to make the environmentally sound decisions could have been acting as an inhibiter for implementation (see Rane and Thakker, 2020). One could argue that these third-party services should have been included in the contract in the first place, although the organization had a contractor for all waste management activities, which could have been a more efficient option. Either way, this was a first attempt at this type of contract and the organization will continue to learn as it goes.
For maintenance, coordination from common procedures and guidelines is vital as the batches of furniture sent to, e.g., refurbishing, need to reach a critical size to reduce remanufacturing cost per item, and this critical size remained to be decided by KTH. If it turns out to cost more to renovate than to purchase new furniture, the heads of the schools will need to have mandates to make the decision to renovate, if indeed the organization prioritizes sustainability over cost. In fact, the perception of increased cost of remanufacturing is often due to a lack of life cycle cost perspective (Polonsky et al., 2022). Public organizations are thought to lead sustainability and circularity by example (Commission of the European Communities, 2008; Alhola et al., 2019), so, if this is true, top management needs to adopt a long-term perspective and see beyond the traditional focus on initial cost. The determining factors to support choices between reuse, remanufacturing and new purchases also remained to be decided by KTH, which points to increased internal collaboration due to the life cycle perspective on the CPP (see, e.g., Kristensen et al., 2021).
5.3. Knowledge, information and attitudes
In the literature, a lack of resources and knowledge is identified as the main barrier to the implementation of CPP (see, e.g., Testa et al., 2016). In the case study, the supplier stated that its main concern was for KTH to implement the new contract throughout the whole organization. In the interviews, the respondents provided different perspectives on the implementation but also different knowledge levels on circular flows in general. The head of the real estate group and the architects were more knowledgeable and were first to push the process of CPP. They can be identified as change agents—a wellknown concept in the literature describing individuals striving for change (Eikelboom et al., 2018). However, it became clear, due to, e.g., the need for common routines and guidelines, that this small group of people was not enough and that implementation was needed at all levels of the organization. Furthermore, perhaps the strong ambition to drive the CPP project resulted in shortcuts that became visible after the procurement stage. Mostly, this was reflected in the exclusion of the users and the schools from the procurement process, where the scope and aim of the process were first set. In a decentralized organization, different actors have diverse perspectives and use diverse criteria, which can cause internal conflicts in a procurement setting (Polonsky et al., 2022). Several respondents in this study raised concerns about this exclusion, stating it could negatively affect the implementation if the users felt detached from the process, and that it could also increase the barriers identified earlier, such as not bothering to send a chair for maintenance instead of disposal. These barriers associated with the users' mindset require a new mindset, i.e., a shift from the ‘wear and tear' approach to a focus on prolonged lifetime for products. Previous studies show that this mindset change is difficult to achieve (Sundin et al., 2009; Gomes et al., 2022).
It is not only the content of the CPP and changes in disposal routines that require a change of mindset. While standardization could create better opportunities for remanufacturing, it could also cause a backlash in the organization, provoking some users who are used to making their own design decisions. Furthermore, the architects must reassess their design choices and consider used furniture in storage and how it can be refurbished to work, perhaps resulting in fewer new purchases. Yet again, coordination for this is vital, but perhaps less difficult for larger projects where project planning is started early (as discussed in Section 5.1). Additionally, a move to consolidate KTH's furniture storage into a common storage room may limit individual departments' and schools' possibility to control their own furniture flows. To avoid this, users need to trust the processes and procedures developed for the furniture flows to work. Again, this points to the importance of creating processes and procedures to facilitate new work processes and to disseminate information, which could be a daunting task considering the diverse set of stakeholders.
6. Conclusions and contributions
The study contributes to the less explored field of procurement in a circular economy context by providing an in-depth case study showing how the prerequisites of the organization play an important part in the implementation of CPP and that contextual solutions are needed for circular challenges. As such, the study adds to previous research on how CPP requires adaption from previous linear approaches by providing in-depth analysis on the organizational adaptations needed in terms of processes and governance. The era of CPP is still in its early stages and public procurers have a learning process in front of them, and for this feedback from implemented contract is crucial. However, even though the public context provides additional complexity (such as when CPP is not complete in terms of the services needed), the possibility of renegotiations is limited due to the Act of Public Procurement. After the procurement stage, the implementation of CPP can benefit immensely from previous work within the PSS field. Whereas, the bulk of PSS literature focuses on private industry, this study contributes rare empirical findings on the implementation of PSS and remanufacturing in a public procurement setting. This study further contributes to the fields of policy implementation and CPP by focusing on the implementation of a CPP contract in the public sector after the procurement phase, which is a focus rarely discussed in previous studies. While the criteria for the tender and the services included in it are important, none of these matters if the CPP contract is not fully implemented in the procuring organization. In the case study, many issues remain to be solved after the procurement phase, so to improve circular solutions in future, it is important to take these next phases into account prior to the procurement ph.
This study also contributes with managerial implications that are important to take into account when implementing and managing CPP contracts in an organization.
• The scope of the CPP contract is crucial and the procuring organization needs to consider what is optimal both for the CPP contract and the organization. Additional services may be needed to reduce organizational resistance. These services, in combination with established routines and guidelines, are the glue that holds the main stages of the circular flow together.
• Strategic decisions to prioritize sustainability are needed when resource efficiency and cost reductions do not align in a short-term perspective. This could be the case whenever the cost of remanufacturing exceeds the cost of purchasing new products.
• A more centralized governance structure facilitates decisions on reuse, remanufacturing and disposal in the organization, e.g., the standardization of design choices, the coordination of products for remanufacturing, and the pooling of products for reuse.
• Follow-up and inventory systems are crucial for integrating previously installed products with CPP, keeping track of circular flows, and providing feedback to improve subsequent procurements.
• Adaptation to circularity and accounting for prolonged life and reuse of furniture are normally not possible in an economy system based on linear flows.
This study is based on a single case study, so additional empirical studies would assist in confirming and complementing these findings. Although the results focus mostly on organizational changes when implementing circular flows for furniture, the results are also applicable to other product types. However, for products with a significant environmental impact during, for example, the use phase, it is important to consider whether that will imply changes in the governance of the use phase. Thus, more studies focusing on different products, and how to implement circular flows for them in a public setting, would strengthen the literature for policy implementation of CPP and PSS.
This study has underlined the importance of a functional follow-up routine for improving subsequent procurements. Therefore, future research should focus on how to establish this feedback loop and how to reap the benefits from it, both in terms of procurement and environmental management. Also relevant is the regulation of waste management, which can make or break a circular system, and thus needs continuous research.
Data availability statement
The raw data supporting the conclusions of this article will be made available by the authors, without undue reservation.
Author contributions
All authors listed have made a substantial, direct, and intellectual contribution to the work and approved it for publication.
Funding
This research was funded by the Swedish Research Council Formas 2017-00263.
Acknowledgments
The authors would like to express their gratitude to the respondents in this study for their participation in the data collection process.
Conflict of interest
The authors declare that the research was conducted in the absence of any commercial or financial relationships that could be construed as a potential conflict of interest.
Publisher's note
All claims expressed in this article are solely those of the authors and do not necessarily represent those of their affiliated organizations, or those of the publisher, the editors and the reviewers. Any product that may be evaluated in this article, or claim that may be made by its manufacturer, is not guaranteed or endorsed by the publisher.
References
Alhola, K., Ryding, S. O., Salmenpera, H., and Busch, N. J. (2019). Exploiting the potential of public procurement: opportunities for circular economy. J. Ind. Ecol. 23, 96–109. doi: 10.1111/jiec.12770
Besch, K. (2005). Product-service systems for office furniture: barriers and opportunities on the European market. J. Clean. Product. 13, 1083–1094. doi: 10.1016/j.jclepro.2004.12.003
Björklund, M., and Gustafsson, S. (2015). Toward sustainability with the coordinated freight distribution of municipal goods. J. Clean. Product. 98, 194–204. doi: 10.1016/j.jclepro.2014.10.043
Bocken, N. M. P., de Pauw, I., Bakker, C., and van der Grinten, B. (2016). Product design and business model strategies for a circular economy. J. Ind. Product. Eng. 33, 308–320. doi: 10.1080/21681015.2016.1172124
Brammer, S., and Walker, H. (2011). Sustainable procurement in the public sector: an international comparative study. Int. J. Oper. Product. Manag. 31, 452–476. doi: 10.1108/01443571111119551
Bumgardner, M. S., and Nicholls, D. L. (2020). Sustainable practices in furniture design: a literature study on customization, biomimicry, competitiveness, and product communication. Forests 11, 1277. doi: 10.3390/f11121277
Calisto Friant, M., Vermeulen, W. J. V., and Salomone, R. (2021). Analysing European Union circular economy policies: words vs. actions. Sustain. Product. Consumpt. 27, 337–353. doi: 10.1016/j.spc.2020.11.001
Commission of the European Communities (2008). Public Procurement for a Better Environment. Brussels: Commission of the European communities. Available online at: https://eur-lex.europa.eu/legal-content/EN/TXT/PDF/?uri=CELEX:52008DC0400andfrom=EN (accessed May 12, 2019).
Copani, G., and Behnam, S. (2020). Remanufacturing with upgrade PSS for new sustainable business models. CIRP J. Manuf. Sci. Technol. 29, 245–256. doi: 10.1016/j.cirpj.2018.10.005
Cordella, M., and Hidalgo, C. (2016). Analysis of key environmental areas in the design and labelling of furniture products: application of a screening approach based on a literature review of LCA studies. Sustain. Product. Consumpt. 8, 64–77. doi: 10.1016/j.spc.2016.07.002
Crafoord, K., Dalhammar, C., and Milios, L. (2018). The use of public procurement to incentivize longer lifetime and remanufacturing of computers. Proced. CIRP 73, 137–141. doi: 10.1016/j.procir.2018.03.316
European Commission (2009). ”Eco design directive,“ in: European Commission Document 32009L0125. Brussels: European Commission. Available online at: https://eur-lex.europa.eu/legal-content/EN/TXT/?uri=CELEX:32009L0125 (accessed September 27, 2022).
EES (2022). The European Furniture Industry: Its Recovery Towards an Innovative, Green and Circular Economy. Brussels: European Economic and Social Committee. Available online at: https://www.eesc.europa.eu/en/our-work/opinions-information-reports/opinions/european-furniture-industry-its-recovery-towards-innovative-green-and-circular-economy (accessed September 6, 2022).
Eikelboom, M. E., Gelderman, C., and Semeijn, J. (2018). Sustainable innovation in public procurement: the decisive role of the individual. J. Public Procure. 18, 190–201. doi: 10.1108/JOPP-09-2018-012
Eisenhardt, K. M. (1989). Building theories from case study research. Acad. Manag. Rev. 14, 532–550.
Eisenreich, A., Füller, J., Stuchtey, M., and Gimenez-Jimenez, D. (2022). Toward a circular value chain: impact of the circular economy on a company's value chain processes. J. Clean. Product. 378, 134375. doi: 10.1016/j.jclepro.2022.134375
European Commission (2015). Closing the Loop: An EU Action Plan for the Circular Economy. Brussels: European Commission.
European Commission (2017a). Public Procurement for a Circular Economy. Brussels: European Commission. Available online at: https://ec.europa.eu/environment/gpp/pdf/Public_procurement_circular_economy_brochure.pdf (accessed June 26, 2021).
European Commission (2017b). Strategic Public Procurement: Brochure. Brussels: European Commission. Available online at: http://ec.europa.eu/DocsRoom/documents/25984 (accessed January 25, 2019).
European Environmental Bureau (2017). Circular Economy Opportunities in the Furniture Sector. Brussels: European Environmental Bureau. Available online at: https://eeb.org/library/circular-economy-opportunities-in-the-furniture-sector/ (accessed September 5, 2022).
Farooque, M., Zhang, A., Thürer, M., Qu, T., and Huisingh, D. (2019). Circular supply chain management: a definition and structured literature review. J. Clean. Product. 228, 882–900. doi: 10.1016/j.jclepro.2019.04.303
Gomes, G. M., Moreira, N., and Ometto, A. R. (2022). Role of consumer mindsets, behaviour, and influencing factors in circular consumption systems: a systematic review. Sustain. Product. Consumpt. 32, 1–14. doi: 10.1016/j.spc.2022.04.005
Government Offices of Sweden (2022). Ökat Fokus På Cirkulär Och Fossilfri Upphandling. New York, NY: Press Release.
Grandia, J., Steijn, B., and Kuipers, B. (2015). It is not easy being green: increasing sustainable public procurement behaviour. Innovation 28, 243–260. doi: 10.1080/13511610.2015.1024639
Grandia, J., and Voncken, D. (2019). Sustainable public procurement: the impact of ability, motivation, and opportunity on the implementation of different types of sustainable public procurement. Sustainability 11, 5215. doi: 10.3390/su11195215
Inagaki, Y., Mitake, Y., Tsuji, S., Alfarisi, S., Wang, H., and Shimomura, Y. (2022). Extracting the relationship between product-service system features and their implementation barriers based on a literature review. Proced. CIRP 109, 197–202. doi: 10.1016/j.procir.2022.05.236
ISO (2015). ISO 14001:2015, Environmental Management Systems: Requirements with Guidance for Use. Belgium: ISO CEN.
Kjaer, L. L., Pagoropoulos, A., Schmidt, J. H., and McAloone, T. C. (2016), Challenges when evaluating Product/Service-Systems through Life Cycle Assessment. J. Clean. Prod. 120, 95–104.
Koop, C., Grosse Erdmann, J., Koller, J., and Döpper, F. (2021). Circular business models for remanufacturing in the electric bicycle industry. Front. Sustain. 2, 785036. doi: 10.3389/frsus.2021.785036
Korhonen, J., Honkasalo, A., and Seppälä, J. (2018). Circular economy: the concept and its limitations. Ecol. Econ. 143, 37–46. doi: 10.1016/j.ecolecon.2017.06.041
Kristensen, H. S., Mosgaard, M. A., and Remmen, A. (2021). Circular public procurement practices in Danish municipalities. J. Clean. Product. 281, 124962. doi: 10.1016/j.jclepro.2020.124962
Krystofik, M., Luccitti, A., Parnell, K., and Thurston, M. (2018). Adaptive remanufacturing for multiple lifecycles: a case study in office furniture. Resour. Conserv. Recycl. 135, 14–23. doi: 10.1016/j.resconrec.2017.07.028
KTH Royal Institute of Technology.. (2022). Policy for Sustainable Development for KTH. Available online at: https://www.kth.se/en/om/miljo-hallbar-utveckling/policy-for-hallbar-utveckling-for-kth-1.553616 (accessed September 27, 2022).
Kurilova-Palisaitiene, J., Sundin, E., and Poksinska, B. (2018). Remanufacturing challenges and possible lean improvements. J. Clean. Product. 172, 3225–3236. doi: 10.1016/j.jclepro.2017.11.023
Leipold, S., Petit-Boix, A., Luo, A., Helander, H., Simoens, M., Ashton, W. S., et al. (2023). Lessons, narratives, and research directions for a sustainable circular economy. J. Ind. Ecol. 27, 6–18. doi: 10.1111/jiec.13346
Lindkvist, L., and Sundin, E. (2016). The role of product-service systems regarding information feedback transfer in the product life-cycle including remanufacturing. Proced. CIRP 47, 311–316. doi: 10.1016/j.procir.2016.03.088
Lingegård, S., Havenvid, M. I., and Eriksson, P. E. (2021a). Circular public procurement through integrated contracts in the infrastructure sector. Sustainability 13, 11983. doi: 10.3390/su132111983
Lingegård, S., Olsson, J. A., Kadefors, A., and Uppenberg, S. (2021b). Sustainable public procurement in large infrastructure projects—policy implementation for carbon emission reductions. Sustainability 13, 11182. doi: 10.3390/su132011182
Meehan, J., and Bryde, D. (2011). Sustainable procurement practice. Bus. Strat. Environ. 20, 94–106. doi: 10.1002/bse.678
Merriam, S. B. (1998). Qualitative Research and Case Study Applications in Education. San Francisco: Jossey-Bass.
Merriam, S. B., and Tisdell, E. J. (2016). Qualitative Research a Guide to Design and Implementation, 4th edn. San Fransisco: Jossey-Bass.
Milios, L. (2017). Advancing to a circular economy: three essential ingredients for a comprehensive policy mix. Sustain. Sci. 14, 1–18.
Milios, L. (2018). Advancing to a circular economy: three essential ingredients for a comprehensive policy mix. Sustain. Sci. 13, 861–878. doi: 10.1007/s11625-017-0502-9
Molin, E., Martin, M., and Björklund, A. (2021). Addressing Sustainability within public procurement of food: a systematic literature review. Sustainability 13, 13395. doi: 10.3390/su132313395
Ntsondé, J., and Aggeri, F. (2021). Stimulating innovation and creating new markets: the potential of circular public procurement. J. Clean. Product. 308, 127303. doi: 10.1016/j.jclepro.2021.127303
Öhgren, M., Milios, L., Dalhammar, C., and Lindahl, M. (2019). Public procurement of reconditioned furniture and the potential transition to product service systems solutions. Proced. CIRP 83, 151–156. doi: 10.1016/j.procir.2019.02.134
Patton, Q. (2002). Qualitative Reserach and Evaluation Methods, 3rd edn. Thousand Oaks: Sage Publications.
Pieroni, M. P. P., McAloone, T. C., and Pigosso, D. C. A. (2021). Circular economy business model innovation: sectorial patterns within manufacturing companies. J. Clean. Product. 286, 124921. doi: 10.1016/j.jclepro.2020.124921
Pigosso, D. C. A., Zanette, E. T., Filho, A. G., Ometto, A. R., and Rozenfeld, H. (2010). Ecodesign methods focused on remanufacturing. J. Clean. Product. 18, 21–31. doi: 10.1016/j.jclepro.2009.09.005
Polonsky, M. J., Wijayasundara, M., Noel, W., and Vocino, A. (2022). Identifying the drivers and barriers of the public sector procurement of products with recycled material or recovered content: a systematic review and research propositions. J. Clean. Product. 358, 131780. doi: 10.1016/j.jclepro.2022.131780
Qazi, A. A., and Appolloni, A. (2022). A systematic review on barriers and enablers toward circular procurement management. Sustain. Product. Consumpt. 33, 343–359. doi: 10.1016/j.spc.2022.07.013
Rane, S. B., and Thakker, S. V. (2020). Green procurement process model based on blockchain–IoT integrated architecture for a sustainable business. Manag. Environ. Qual. Int. J. 31, 741–763. doi: 10.1108/MEQ-06-2019-0136
Ruparathna, R., and Hewage, K. (2015). Sustainable procurement in the Canadian construction industry: current practices, drivers and opportunities. J. Clean. Product. 109, 305–314. doi: 10.1016/j.jclepro.2015.07.007
Sönnichsen, S. D., and Clement, J. (2019). Review of green and sustainable public procurement: towards circular public procurement. J. Clean. Product. 14, 118901. doi: 10.1016/j.jclepro.2019.118901
Sundin, E., Lindahl, M., and Ijomah, W. (2009). Product design for product/service systems. J. Manuf. Technol. Manag. 20, 723–753. doi: 10.1108/17410380910961073
Testa, F., Annunziata, E., Iraldo, F., and Frey, M. (2016). Drawbacks and opportunities of green public procurement: an effective tool for sustainable production. J. Clean. Product. 112, 1893–1900. doi: 10.1016/j.jclepro.2014.09.092
Testa, F., Iraldo, F., Frey, M., and Daddi, T. (2012). What factors influence the uptake of GPP (green public procurement) practices? New evidence from an Italian survey. Ecol. Econ. 82, 88–96. doi: 10.1016/j.ecolecon.2012.07.011
Tolio, T., Bernard, A., Colledani, M., Kara, S., Seliger, G., Duflou, J., et al. (2017). Design, management and control of demanufacturing and remanufacturing systems. CIRP Ann. 66, 585–609. doi: 10.1016/j.cirp.2017.05.001
Trindade, P. C., Antunes, P., and Partidário, P. (2017). SPP toolbox: supporting sustainable public procurement in the context of socio-technical transitions. Sustainability 10, 11347. doi: 10.3390/su10010067
Tukker, A. (2004). Eight types of product–service system: eight ways to sustainability? Experiences from SusProNet. Bus. Strat. Environ. 13, 246–260. doi: 10.1002/bse.414
Tukker, A. (2015). Product services for a resource-efficient and circular economy: a review. J. Clean. Product. 97, 76–91. doi: 10.1016/j.jclepro.2013.11.049
UNEP (2014). Buying for a Better World: A Guide on Sustainable Procurement for the UN System. Paris: UNEP. Available online at: https://www.ungm.org/Areas/Public/Downloads/BFABW_Final_web.pdf (accessed May 12, 2019).
Uyarra, E., Edler, J., Garcia-Estevez, J., Georghiou, L., and Yeow, J. (2014). Barriers to innovation through public procurement: a supplier perspective. Technovation 34, 631–645. doi: 10.1016/j.technovation.2014.04.003
Uyarra, E., and Flanagan, K. (2010). Understanding the innovation impacts of public procurement. Eur. Plan. Stud. 18, 123–143. doi: 10.1080/09654310903343567
Vejaratnam, N., Mohamad, Z. F., and Chenayah, S. (2020). A systematic review of barriers impeding the implementation of government green procurement. J. Public Procur. 20, 451–471. doi: 10.1108/JOPP-02-2020-0013
Witjes, S., and Lozano, R. (2016). Towards a more circular economy: proposing a framework linking sustainable public procurement and sustainable business models. Resour. Conserv. Recycl. 112, 37–44. doi: 10.1016/j.resconrec.2016.04.015
Yin, R. K. (2014). Case study research. Design and methods, 5th edn. New York, NY: SAGE Publications.
Appendix A
1. Interview guide
The interview guide followed the key stages in the circular furniture flow process.
Procurement
• What barriers do you identify for the circular furniture flows at this stage?
• What drivers do you identify for the circular furniture flows at this stage?
• Which are the key functions for the circular furniture flows at this stage?
• What type of information is needed for the circular furniture flows and when is this information needed?
Use and maintenance
• What barriers do you identify for the circular furniture flows at this stage?
• What drivers do you identify for the circular furniture flows at this stage?
• Which are the key functions for the circular furniture flows at this stage?
• What type of information is needed for the circular furniture flows and when is this information needed?
Disposal
• What barriers do you identify for the circular furniture flows at this stage?
• What drivers do you identify for the circular furniture flows at this stage?
• Which are the key functions for the circular furniture flows at this stage?
• What type of information is needed for the circular furniture flows and when is this information needed?
Follow-up/improvement
• What barriers do you identify for the circular furniture flows at this stage?
• What drivers do you identify for the circular furniture flows at this stage?
• Which are the key functions for the circular furniture flows at this stage?
• What type of information is needed for the circular furniture flows and when is this information needed?
Keywords: circular economy (CE), furniture, product-service systems (PSS), public procurement, remanufacturing, organizational change
Citation: Lingegård S and von Oelreich K (2023) Implementation and management of a circular public procurement contract for furniture. Front. Sustain. 4:1136725. doi: 10.3389/frsus.2023.1136725
Received: 03 January 2023; Accepted: 13 March 2023;
Published: 30 March 2023.
Edited by:
Idiano D'Adamo, Sapienza University of Rome, ItalyReviewed by:
Giacomo Di Foggia, University of Milano-Bicocca, ItalySimon Peter Nadeem, University of Derby, United Kingdom
Copyright © 2023 Lingegård and von Oelreich. This is an open-access article distributed under the terms of the Creative Commons Attribution License (CC BY). The use, distribution or reproduction in other forums is permitted, provided the original author(s) and the copyright owner(s) are credited and that the original publication in this journal is cited, in accordance with accepted academic practice. No use, distribution or reproduction is permitted which does not comply with these terms.
*Correspondence: Sofia Lingegård, c29maWEubGluZ2VnYXJkQGFiZS5rdGguc2U=