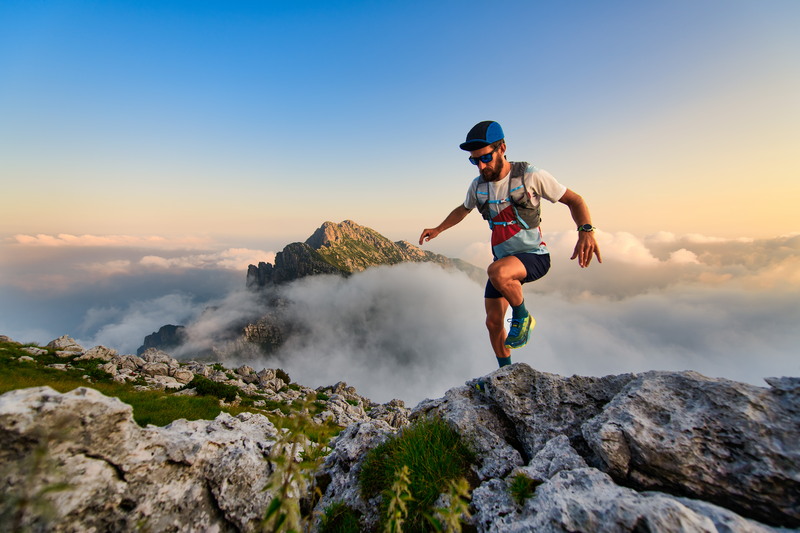
94% of researchers rate our articles as excellent or good
Learn more about the work of our research integrity team to safeguard the quality of each article we publish.
Find out more
REVIEW article
Front. Sustain. , 20 May 2022
Sec. Waste Management
Volume 3 - 2022 | https://doi.org/10.3389/frsus.2022.901885
This article is part of the Research Topic Integrated Resource Network Optimization for Sustainable Development View all 7 articles
As a result of public pressure and government legislation to reduce plastic waste there has been a sharp rise in the manufacture and use of alternatives to conventional plastics including compostable and biodegradable plastics. If these plastics are not collected separately, they can contaminate plastic recycling, organic waste streams, and the environment. To deal with this contamination requires effective identification and sorting of these different polymer types to ensure they are separated and composted at end of life. This review provides the comprehensive overview of the identification and sorting technologies that can be applied to sort compostable and biodegradable plastics including gravity-based sorting, flotation sorting, triboelectrostatic sorting, image-based sorting, spectral based sorting, hyperspectral imaging and tracer-based sorting. The advantages and limitations of each sorting approach are discussed within a circular economy framework.
Plastic waste is a major environmental global concern. Most plastic packaging in current use are conventional plastics derived from a petrochemical refining and manufacturing processes. These plastics are important to modern society but if they pollute the environment they persist for decades harming wildlife and ecosystems. One of the strategies to address this problem has been the development of compostable plastics which are designed to biodegrade at their end of life in controlled conditions, e.g., industrial composting. Compostable plastics are not intended, nor are they capable of, biodegrading reliably in uncontrolled conditions, e.g., open countryside, or in water.
The global compostable plastic market was valued at $991.2 million in 2019 and is expected to reach $3,102.6 million by 2027 (Research, 2022). There is potential for compostable plastics to have positive impact on environments such as the reduction in pollution, reduction in greenhouse gas emission, and in the use of renewable carbon sources (Song et al., 2009). However, many of these potential advantages will only be realized if these compostable plastics do not enter the environment, do not pollute other waste streams and are collected separately for organic waste processing. A key enabling technology to achieve this aim, and thus achieve the potential of compostable plastics to minimize pollution, is the successful sorting and separation of these plastics in the home and at waste processing plants. Reviewing the technologies for achieving this task is the focus of this paper.
Plastic is referred to as conventional or bioplastic depending on its carbon source, either fossil-based or bio-based, respectively. Conventional plastics are durable polymers such as polyethylene (PE), polypropylene (PP) or polyethylene terephthalate (PET) derived from fossil fuels. These polymers can also be made from bio-derived sources, these are referred to as bioplastics, see Figure 1. The term bioplastics also encompasses a variety of bio-based polymers such as polylactic acid (PLA), polyhydroxyalkanoates (PHA) or starch blends derived from plant sources such as starch, cellulose or lignin.
Figure 1. Identification of bioplastics (Pathak et al., 2014).
All plastics regardless of whether they are bio-based or fossil-based behave differently at their end of life. They can either be designed to be durable and persist in the environment or to be biodegradable over a period of time defined by the environment (Kjeldsen et al., 2019). Biodegradable plastic is a source of carbon and energy for naturally occurring microorganisms, mainly bacteria and fungi, and broken down and transformed into new cell biomass and, ultimately, simple molecules such as carbon dioxide (CO2) and water over a period of time (Vert et al., 2012). The rate of biodegradation of a plastic polymer largely depends on its physical and chemical properties and composition, as well as the environmental conditions to which it is exposed (Siracusa et al., 2008). Thus, there is no guarantee they will biodegrade since they may not experience the right environmental conditions. Composting is a process where these environmental conditions are controlled, and a subset of biodegradable plastics are designed to be undergo biological degradation in a compost site in a fixed period of time, leaving no visibly distinguishable or toxic residues (Vert et al., 2012).
Two industrial processes are typically used to process biodegradable and compostable plastics: industrial composting (IC) and anaerobic digestion (AD). IC facilities are designed to undertake aerobic composting of organic matter (food and garden waste) to produce compost. Compostable plastics must be complaint with EN 13432 which is designed to be compatible with industrial composting systems. AD facilities are designed to undertake anaerobic composting of organic matter to produce biogas (CO2 and methane) and digestate (Song et al., 2009; European Bioplastics, 2019). They are generally not suitable for compostable plastics but some biodegradable plastics are biodigestable in these systems. Home composting is an informal method of composting that takes place in a domestic setting where temperatures and levels of humidity are generally lower and less controlled than industrial settings (European Bioplastics, 2015). Some plastics are marketed and certified as “home compostable”, but these are a small subset of the biodegradable plastics sold onto the market such as tea bags and food caddy liners (Lesswaste, 2022).
There are many types of aerobic industrial composting systems, the most representative at full scale level are In Vessel Composting (IVC) and Open Air Windrow Composting Process (OAW). In aerobic conditions microorganisms consume oxygen while breaking down organic waste to produce CO2, water, compost, and heat, in two distinct phases; active composting and curing. In the active composting phase microorganisms actively break down the organic waste using it as a source of nutrients, thereby generating heat while during the curing phase the microbial activity slows down, temperatures drop, and the compost matures. The compost produced is sold to farmers and other agricultural businesses as a fertilizer and soil improver.
IVC is appropriate to treat food waste, garden waste and compostable plastics. These organic wastes which come from local authority waste collection as well as commercial sources are delivered to enclosed reception area. Compostable plastics and conventional plastics in the form of packaging and food caddy liners are often mixed into the food and garden waste. Some IC plants remove all of this material, regardless of its composition, since they cannot reliably sort and separate the compostable plastics. In such screening processes the large pieces of contamination are pulled out when it first arrives in the reception area. After that the food waste is depackaged and shredded to a uniform size and loaded into a tunnel. The composting process is started by naturally occurring micro-organisms already in the waste. The materials are broken down, releasing the nutrients. During this step, the temperature goes up to 60–70°C. The composting process continues between 1 and 3 weeks until all parts of composting mass reaches the required temperature. The moisture, oxygen level and temperature are carefully monitored to ensure that the materials are sanitized. Once the sanitization process is complete, the compost is left to mature in an open windrow or an enclosed area for ~10–14 weeks to ensure stabilization. The last stage is screening to eliminate contamination using a large automated trommel to sieve out bits of plastic and produce a suitable grade of compost (Zero Waste Scotland, 2021).
Open Windrow composting is a simpler less controlled process that IVC which is used to process crop residues and garden waste and other. The feedstock is shredded, mixed and placed into windrow along a non-permeable surface. The windrows are turned on a regular basis to improve oxygen content, distribute heat to regulate temperature. The composting process which typically takes 16 weeks, depending on maturity requirement and local climate. The last stage is screening to eliminate contaminant and grade the finished products (WRAP, 2016b).
In an anaerobic digestor, bacteria degrade the organic waste in the absence of oxygen, producing biogas (methane and CO2) and digestate (Bátori et al., 2018). Different technologies exist that largely depend on the type of the feedstock and are distinguished by temperature, moisture content, the regime of digesters and the separation of the metabolic stages. The performance and results of anaerobic digestion depend on conditions such as the pH, feedstock composition, and other characteristics such as well as the microbial strains used as the inoculum (Pagliano et al., 2017). Generally, the produced digestate is then aerobically composted to reduce the residual microbial activity and obtain complete maturity of the compost (WRAP, 2016a; EPA, 2021).
AD technologies can be classified as wet AD or dry AD. The main distinction between these systems is total solids (TS) used in digestion process. Wet AD systems are designed to process biodegradable feedstock into a digestate slurry with typically <15% total solids while the solid matter concentration in dry AD system is from 20 to 40%. Wet AD systems are more appropriate to treat low solid feedstock such as food waste as well as producing higher biogas in shorter period of time (QUBE, 2018). Wet AD plants have improved energy balance and economic performance compared to dry AD plants (Mata-Alvarez et al., 2000; Angelonidi and Smith, 2015). They are generally equipped with screening systems to remove packaging before it enters the digestor (Angelonidi and Smith, 2015).
Biodegradable plastics and conventional plastics in the form of packaging and food caddy liners often accompany food waste when they are collected. Most AD plants depackage this material, regardless of its composition, since it can clog the system. Although some biodegradable plastics are digestable by AD plants, reliably sorting and separating them from conventional plastics material is problematic.
Biodegradation testing standards (ISO and ASTM) have been designed to determine the biodegradability of plastics in soil, compost, landfill, marine, or other aquatic environments (Funabashi et al., 2009; Siracusa, 2019). The EU standard for compostable and biodegradable packaging EN 13432:2000 defines the criteria that must be met for a material to be suitable for commercial industrial composting and anaerobic digestion (European Bioplastics, 2016): test material (packaging and organic waste) has to show disintegration and loss of visibility in the final compost; after 3 months, no more than 10% of the initial weight of the test material should be retained after sieving it through 2 mm mesh size. Within a maximum of 6 months, 90% of the carbon in the test material must be converted to CO2, having the same rate of biodegradation as natural materials. The test material must have no negative effects on the composting process and no adverse effect on the quality of the compost produced, including the heavy metals content. Additionally, EN 13432 states that anaerobic biodegradation and disintegration can be verified as an option. The degree of biodegradation (biogas production) has to be at least 50% after 2 months, as aerobic composting follows anaerobic fermentation, during which time biodegradation can continue. The standard requires that after 5 weeks of combined anaerobic and aerobic treatment, at most 10% of the original sample of compostable plastic may remain after sieving through 2 mm mesh size. For non-packaging plastics, a different EU standard exists: EN 14995:2006; however, the same requirements apply (European Bioplastics, 2016). The standards specify requirements for the identification and labeling of commercially compostable plastics (European Bioplastics, 2016). Manufacturers of compostable plastics can obtain certification from a number of certification bodies. The certification gives visibility to compostable plastics and helps customers identify them.
In Europe, the most important certification schemes that comply with EN 13432 are DIN-CERTCO (Germany), TÜV AUSTRIA (formerly Vinçotte), OK Compost label (Belgium), and COMPOSTABILE—CIC (Italy) (Association for Organics Recycling, 2011). In the UK, the Association for Organics Recycling operates a certification scheme in partnership with Germany's DIN-CERTCO scheme that aligns with the requirements of EN 13432 (BPF, 2019). Although there is currently no international or European standard for home composting, the following national regulations, standards, and certifications exist: UNI 11183 (Italy), AS 5810 (Australia), NTT51-800 (France), and OK Compost (Belgium) (Association for Organics Recycling, 2011). In the UK, the Publicly Available Specifications PAS100 and PAS110 provide a baseline quality specification for compost and digestate, respectively (BSI, 2018).
When there is no separate collection for compostable or biodegradable plastics citizens often place these packaging materials in the recycling collection bin. Once in the recycling waste stream these plastics are hard to distinguish from recyclable plastics such as PET, PP and PE resulting in contamination of the recyclate of these polymers and a reduction in their physical properties and value (Song et al., 2009; Stokes, 2017; Jackson, 2018). As the proportion of compostable plastics increases there is a need for automatic sorting systems to reduce this type of contamination and to divert it to an industrial composting waste stream.
In this Introduction we have summarized the main uses, compositions, waste processing methods and standards that apply to biodegradable and compostable plastics. The aim of this paper is to provide a comprehensive overview of the state of the art in the field of identification and sorting technologies that have potential to automatically sort compostable and biodegradable plastics for the purpose of increasing the rate of composting of compostable plastics and reducing the cross-contamination of conventional plastic recycling. Since compostable plastics are introduced into markets to reduce the environmental impact of packaging, for each sorting technology we also comment on the environmental impacts of the technologies themselves, such as use of energy use, water use and chemical processes.
The manual sorting method is the identification and classification of plastics using their unique characteristics such as color, shape, labeling and appearance (Saiter et al., 2011). As with all materials this technique is labor intensive and subject to human error (Wienaah, 2007). Research shows machine sorting accuracy is 30% higher than manual sorting Eikeseth (2013). Many compostable plastics are certified and carry a label such as the DIN-CERTCO label. However, manufacturers of products often produce their own labels which are not certified and state “100% biodegradable” or “100% compostable”. Such labels lead to confusion and lead to errors in manual sorting (Greenpeace, 2020; WRAP, 2020). Without clear labels it is very difficult to identify a plastic as biodegradable or compostable due to the similarity in color, shape and appearance to conventional plastics.
Plastics can be sorted according to their density differences. The pre-processes for gravity-based sorting involve shredding into small flakes (10–20 mm), cleaning and sieving (Maisel et al., 2020). This is followed by either a process involving centrifugal (hydrocyclones), sink-float in water, and air gravity sorting (Lupo et al., 2016). The method is widely used for plastic separation because it is easily automated, flexible, comparatively simple and is suitable for high-capacity processes. It is relatively slow and not applicable to sorting all plastics since it relies on density differences (Gent et al., 2009a; Hu et al., 2013).
The densities of biodegradable polymers and conventional polymers differ from each other as shown in Table 1. Gravity-based sorting has been used to sort biodegradable plastics such as PLA from polyolefins (HDPE, LDPE and PP) (Vilaplana and Karlsson, 2008). To be successful the intermediate density of the process medium must be between the sorted plastic materials. For instance, plain water (density 1 g/cm3) is appropriate medium to separate HDPE (which floats) from PLA (which sinks). However, the efficiency of the system reduces when sorting plastics with similar densities. For instance, the efficiency level of separating PLA from HDPE is lower than separating Polycaprolactone (PCL) from HDPE because the density of PCL is closer to that of HDPE (Lahtela and Kärki, 2018). Separating PET from PLA using this approach is complicated and requires multiple steps (Park et al., 2008). Various recycling processes start by sink-float sorting, with heavier plastics sorted by other methods (Serranti et al., 2015; Wang et al., 2015).
Table 1. Density of plastics materials (Niaounakis, 2015).
Centrifugal sorting, also known as a hydrocyclone sorting (Lahtela and Kärki, 2018), is a method that uses centrifugal forces to separate mixtures of plastic with different densities and thicknesses. The centrifuge sorting system consists of two main parts which are a conical and linked cylindrical body in which there is a tangential entrance for the feeding suspension, see Figure 2. Plastics are passed through shredder and granulator to reduce the size to 10–20 mm (ANDRITZ, 2021). The flakes then enter the cyclone where the low density materials move upward to the overflow whereas the denser particles move downward (Schwerzler, 2005). There are two types of hydrocyclones, these are conocylindrical cyclones and cylindrical cyclones. The concepts of two methods are similar but the operating angle is different. The operating angle of conocylindral cyclones is about 30 degrees from the horizontal axis while cylindrical cyclones are operated vertically (Gent et al., 2009b). The plastics sort by density based on their hygroscopic properties. The accuracy is reduced by the tendency of flakes to stick together under certain parameters such as aspect ratio and particle size. Other parameters that have an influence on efficiency of this sorting system are pressure drop, shearing effect and aspect ratio (Gent et al., 2009b; Yuan et al., 2015). Hydroclones are an effective tool for sorting finely ground plastic material. The downside of this method are the multiple steps of the sorting process. It is also inefficient to sort plastics with similar densities such as PBST (1.35 g/cm3) and PET (1.35–1.40 g/cm3) (Michigan, 2021). Although biodegradable plastics are often food contaminated this is not a barrier for use since the sorting technique begins with washing which removes contamination (ANDRITZ, 2020).
Figure 2. Schematics of sorting mechanisms: (A) hydrocyclone; (B) sink—float and flotation mechanism; (C) air gravity sorting (Vaško, 2015).
Flotation sorting concept utilizes hydrophobic properties and surface tension to separate types of plastic (Shent et al., 1999; Gundupalli et al., 2017). The gaseous bubbles come into contact with the hydrophobic particles and then they are carried on the top of flotation apparatus, see Figure 2.
The difference in wettability of the polymers, bubble attachment, solvent quality, size of flake and reaction time are important factors that affect efficiency. In some cases, the surface modification such as flame treatment, wet oxidation and boiling treatment is necessary when the wettability properties are not dissimilar enough (Saisinchai, 2014; Wang et al., 2015). The method results in high sorting efficiency (more than 90%) and a low operational costs (Guo et al., 2016). However, this comes at an environmental cost due to use of chemicals in multiple steps and the production of waste. For example, the chemical reagents such as tannic acid, calcium lignosulfonate are used to promote the selective wettability of its components (Pita and Castilho, 2017).
Floating sorting is used as a technique to sort plastics of similar densities. However, modifying the chemical structure is used to increase efficiency. For instance, Pongstabodee et al. (2008) have shown that calcium chloride can be used to increase wettability of plastics because of the calcium ions act as a bridge between wetting and plastic surface (Pongstabodee et al., 2008). Mallampati et al. (2016) have used this technique to sort PVC from other plastics (Mallampati et al., 2016).
From Table 1, the densities of most biodegradable plastics are above 1 g/cm3 which is similar to PVC, PET and PC making gravity approaches unsuccessful in separating these types of plastics from biodegradable plastics. Flotation sorting techniques are more applicable in these cases (Wang et al., 2015).
Air Tabling is a method that creates less waste than the wet gravity methods avoiding the chemical pretreatment of plastics for surface modification and treatment of water from the process for discharge and dewatering used in Floatation Methods (Dodbiba et al., 2005).
Air Table is a dry gravity sorting machine which consists of a porous desk powered by an eccentric drive to impart the longitudinal vibration. An electric fan which is located below the porous deck generates the upward airflow as shown in Figure 2. The moving bed of mixed plastic flakes is fluidized by upward airflow being blown through a porous deck, which together with the longitudinal vibration causes high-density flakes to settle on the deck and contact its surface, while low-density flakes float on top of the bed. Then, the high-density particles are vibrated uphill along the end slope toward the higher side. At the end of each forward stroke of vibration, the motion of the porous deck is sharply reversed, but the high-density particles continue to move forward during most of the backward stroke due to their momentum. The vibration proceeds until they overflow from the discharge end of the deck at its higher end before entering into the collecting bin. The low-density particles, which remain fluidized, drift downhill in the direction of the deck inclination due to gravitational pull and flow into the collecting bin. The difference in density between the plastics correlates with sorting efficiency with 450 kg/m3 being the minimum difference required (Dodbiba et al., 2003). For instance PVC flakes can be sorted from PP with efficiencies 93.7% for PVC and 92.5% for PP being achieved (Dodbiba et al., 2005). Although theoretically applicable to biodegradable plastics there are no reports or published experimental results (Carvalho et al., 2007).
Triboelectric sorting is also known as contact electrification or frictional electrification. The principle of this method is based on charging mechanisms that originate from the difference of surface properties between two materials which create an electric charge between them when in contact called tribocharging phenomenon (Wu et al., 2013). The sorted plastics move toward negative or positive electrode depending on their charges.
In this sorting technique, optimum charge density and selective charging of materials are important factors to achieve high accuracy level of separation (Park et al., 2008; Wu et al., 2013). This sorting technique is appropriate for both conventional (i.e., PVC, PET, and ABS) and biodegradable plastics (i.e., PLA, PCL, and PHBV). The maximum purity of polymeric fractions obtained during the electrostatic separation process is often more than 80% (Zenkiewicz et al., 2015).
Tribocharging of plastics only happens on the surface to a depth of 30 nm (Lee, 1994; Watson and Yu, 1997). This means that size plays a vital role in sorting efficiency because the electrostatic force scales inversely with size. Reducing the size of the material below a certain limit also has negative effects such as high cost in pretreatment steps and increased collision between same the type of plastic reducing the sorting efficiency (Wu et al., 2013). Thus, pretreatment of materials is needed before sorting, in practice the plastics are flaked into optimum size (1–13 mm).
Charging is performed and accumulated through repeated rubbing (Taylor and Secker, 1994). Various devices have been developed for plastic particle charging in triboelectrostatic sorting. These devices can be divided into two mechanisms namely solid single-phase and gas solid two phase. The solid single-phase mechanism is a type of charger with rotary blades, rotating tube and vibrating devices. The gas charger is two-phase mechanism involving propeller-type chargers, a cyclone, and a fluidized bed.
Solid single-phase turbocharging involves a rotating tube into which plastic flakes are fed into (Inculet et al., 1994). The cylindrical tube rotates along an axis that is inclined slightly to the horizontal. Thus, the plastic flakes travel though the tube due to gravity. The magnitude of charge accumulated on each flake depends on length of tube and inclined angle. The rotating tube may have ribs in order to increase degree of mixing. The advantages of this mechanism are mechanical simplicity and the low power requirement. The downsides of the rotating tube are low collision frequency leading to low charging efficiency.
A common type of gas tribocharger is a fluidized bed. Air turbulence is generated in chamber and then the plastic flakes are conveyed upward with a gas flow and are impeded by air resistance, gravity forces and air dynamic pressure. The plastic flakes make contact with the wall and each other. The main concept of the fluidized bed is simply that the plastic particles rub against each other and get enough charge to be separated using an electric field. A small inter-electrode distance and high voltage applied are important factors to improve the separation results (Younes et al., 2015).
Park et al. (2008) developed a two-stage system to separate three types of shredded plastics including PVC, PET, and ABS. The plastics are shredded and electrically neutralized. Subsequently, they are passed through cyclone charger with flowing air. PVC negatively charged flakes are removed at the first stage. In the second stage, the remaining PET and ABS flake materials are neutralized and enter the cyclone charger with flowing air. The ABS positively charged flakes moved to the negative electrode while PET negatively charged flakes moved to positive electrode. In this process all three plastics can be separated from each other (Park et al., 2008). Bendimerad et al. (2009) also developed the system for PVC and PE waste separation using triboelectrostatic sorting (Bendimerad et al., 2009). In 2015, triboelectric sorting was applied to separate biodegradable plastics including PLA, PCL and Poly(3-hydroxybutyrate-co-3-hydroxyvalerate) (PHBV). The result showed that the purity of PLA and PCL obtained was 99.3 and 98.7%, respectively. However, the purity of PHBV was around 80% (Zenkiewicz et al., 2015).
The advantages of triboelectrostatic sorting are the low cost, high efficiency and low environmental impact (Cui and Forssberg, 2003).
Image based identification is an approach for analyzing images of an object by detecting their texture and shape, extracting important features and drawing conclusions. It can be performed at different accuracy degrees, depending on concept required and information type. Image recognition consists of four different tasks including image recognition, tagging, detection and segmentation (Deepomatic, 2020).
In the plastic waste management industry, image recognition is becoming a popular technology to identify types of plastic packaging. There are variety algorithms applied to classify plastic types such as Support Vector Machine (SVM) and Convolutional Neural networks (CNN) (Saha, 2018).
To create the neural network, multiple datasets of plastic waste images are required. After data preparation, the huge numbers of features are extracted from the images and transformed into thousands of features. They are then labeled and assigned the category. The images in their extracted forms enter into a filter for training the network. The output of the model is a label that match the image with its features coming from the input. Once the model is trained, it can be used to predict the new images (Google Developers, 2021).
Yang and Thung (2016) used the support vector machine (SVM), with scale-invariant feature transform (SIFT) features, and a convolutional neural network (CNN) method to classify images of a single objects in a waste stream and classify them into six different categories: metal, paper, glass, plastic, trash, and cardboard by associating their characteristic product shapes with the material. In this way they achieved a 63% classification accuracy for the trained SVM and 22% classification accuracy for the CNN (Yang and Thung, 2016). Sakr et al. (2016) obtained results showing that SVMs achieved a high classification accuracy of 94.8% while CNNs only achieved 83% (Sakr et al., 2016).
Awe et al. (2017) applied a CNN model to classify waste into three categories which are landfill, recycling and paper. The mean average precision of this method was 68% (Awe et al., 2017). Google's eNet-based vision was used to classify urban waste by Rad et al. (2017). The accuracy of this system is between 63 and 77% for classifying waste types including plastic bottle, metal can, cigarettes, paper, and vegetable (Rad et al., 2017).
This image recognition system can work with high-speed conveyor belt and has been successfully applied at a large scale. Many recycling companies combine visible image data with live image processing and analysis using AI deep learning techniques to recognize and sort different types of plastic (Greyparrot, 2021; Hayes, 2021). The drawback of this approach is that while the method can classify bottles, coffee pods, and tubs but it is unable to identify chemical structure of plastics. Hence, it cannot unambiguously distinguish between biodegradable and conventional plastics in the same product format.
Another type of image detection technology is based on a digital watermark (invisible barcode/QR code). This is a visual symbol added directly to a label, usually in a repeatedly tiled manner (Holygrail, 2017). When plastic packaging with digital watermarks enters a waste sorting facility it can be detected and decoded by high solution camera on the high-speed sorting line. The line then sorts the plastic packaging into streams according to its attributes (Southey, 2020). Even if the plastics are damaged or crushed and contaminated with food waste, because of the tiled nature of the watermark some fraction of it is often still visible and there is evidence that the sorting machine camera/processor can still see and analyze this information (Sykes, 2018).
Digital watermarks can also be detected by barcode scanners and smartphones to help citizens manually sort waste at home. The number of available codes is virtually unlimited and can provide a wide range of attributes such as type of plastics used, biodegradable vs. conventional plastics, food vs. non-food usage, etc. (Holygrail, 2017). The drawback of this technology is that it requires a high degree of standardization and agreement across global industries, and access to active databases that match the digital watermark to the information about the product and material.
Near Infrared spectroscopy (NIR) is one of the most effective techniques for automated sorting of biodegradable plastics without any surface pre-treatment. The NIR wavelength range is 700–2,500 nm (Masoumi et al., 2012). In this region, the absorbance and reflectance of light in NIR spectral range is due to overtone or combination vibrations of the C-H, O-H, N-H, and C-O bonds in polymers. The observed NIR spectra can be characteristically attributed to specific plastic resins, thus enabling identification of specific polymer types.
To identify the type of plastic, visible light is directed onto a plastic product typically traveling on a conveyor belt underneath a NIR camera. The NIR reflectance is captured and the peaks in the spectrum are identified and pattern matched to a database of NIR spectra of known plastics. This enables automatic identification. The advantages of this technique are reliable and rapid identification with a low environmental impact (Cui and Forssberg, 2003). It is widely used industrially to identify conventional and biodegradable plastic products which are then mechanical sorting using a variety of approached including jets of air, see Figure 3.
Figure 3. NIR spectra of plastics and schematic of NIR plastic sorting unit (Mattley, 2020).
NIR sorting systems can deal simultaneously with multiple polymer types. A “two filter” system for classifying 5 types of resin: PVC, PET, HDPE, PP, and PS was proposed by Masoumi et al. in 2012 (Masoumi et al., 2012). This system is called the “Two-Filter” approach since two optical filters are used to separate two specific wavelengths of spectrum. The sorting system consists of 3 main units which are the identification unit, the control unit and the throwing unit. When the plastics pass through optical sensors, they are determined by the identification unit and control unit. The target polymers are ejected from the plastic stream by ejection nozzles in the throwing unit. Parameters such the presence of labels, caps, thickness and surface contamination and color have been shown to affect the sorting efficiency of the system.
In 2013, Gertman applied NIR sorting technique to separate PLA from mixed plastics stream. The study illustrated that PLA cups, bottles and clamshells can be recovered 99.6% from other mixed containers.
The other application of NIR sorting technology is to detect microplastic (2–4 mm). Infrared radiation interacts with the microplastic particle, creating characteristic IR absorption pattern. This data is fed to a machine learning algorithm to then identify microplastic particles (Bruker, 2021).
The classification of black plastics is the main limitation of NIR technology. To overcome this limitation, spectroscopy in the mid infrared spectral region (MIR) offers a possibility to identify black plastics. In the MIR spectral region from 2.5 to about 16 μm wavelength, which corresponds a wavenumber range from 4,000 to about 600 cm−1, the different kinds of plastic material show additional vibrational modes like deformation, rocking, and twisting modes due to their molecular structure. Besides the C–H bond, other bonds like O–H, N–H and O–C also contribute with their fundamental vibrations to the spectral features. The various molecular groups with their different vibrational modes generate a unique spectrum of each polymer in the spectral range between 2,500 and 600 cm−1, which allow a definite identification of black plastics (Rani et al., 2019).
The other limitations of NIR sorting techniques are that they are an indirect method that requires the development of a multivariate calibration model against a suitable reference method. This limits the accuracy of the NIR analytical method to that of the reference method. In addition, the development of accurate multivariate calibration models is time consuming, requiring the availability of a large number of samples to cover all possible sources of variability in the spectra (Menezes et al., 2009).
Hyperspectral imaging (HSI) is a technique that combines the properties of digital imaging with spectroscopy (Geladi et al., 2007; Kamruzzaman and Sun, 2016). Using this approach, it is possible to detect the spectral signature of each pixel of the acquired image in different wavelength regions (visible, near infrared, short-wave infrared, etc.) according to the characteristics of the selected sensing device. A hyperspectral image can thus be considered as a three-dimensional dataset with two spatial dimensions and one spectral dimension, the so-called “hypercube” (Serranti et al., 2011). HSI can be considered one of the best and most powerful non-destructive technologies for accurate and detailed information extraction from the acquired images, with a high level of flexibility. The large amount of spectral information collected by HSI from the sample surfaces must be processed in order to extract the information of interest. As with NIR, a preliminary step in any inspection or quality control logic development, is the development libraries of reference spectra, to be utilized for unknown sample recognition. Since this is a relatively new technique for sorting plastics, such libraries are in the early stages.
The main advantage of this sorting technique is that since the entire signature spectrum is acquired at each pixel of materials, multi-material plastic products with varying thickness can be readily identified. Thus, all plastic types including conventional plastics and biodegradable plastics can be identified regardless of material size and thickness. The downsides are costs, and real-time computing complexity. The hypercube is very large therefore significant data storage is necessary.
Different pre-processing algorithms are applied to hyperspectral data to reduce the effect of possible external sources of variability. Principal Component Analysis (PCA) is used to provide an overview of the complex multivariate data. PCA decomposes spectral data into several principal components (PCs), linear combinations of the original data, embedding the spectral variations of each collected spectral data set (Wold et al., 1987). The first few PCs, resulting from PCA, are used to analyse the common features among samples: samples characterized by similar spectral signatures tend to aggregate in the score plot as a cluster (Xu and Gowen, 2020). Finally, the recognition of different products and/or materials is obtained utilizing classification methods, such as Partial Least-Squares Discriminant Analysis (PLS-DA). PLS-DA is a supervised classification technique requiring prior knowledge of the data and allowing the classification of samples into predefined groups. To classify samples a discriminant function is built from a reference sample set and then applied to an unknown set.
Another powerful classification method for multi-material plastics is hierarchical modeling. Adopting this kind of classification logic, objects are divided into subsets and then they are split again into further subsets, until each of them contains only a single object. During each step, sample objects with known composition are selected, isolated and compared through successive PLS-DA classification models.
Many researchers have used short wave infrared (SWIR) hyperspectral imaging for detecting and identifying macro and microplastics (Mehrubeoglu et al., 2020). For the macro level, Balsi et al. (2018) use SWIR spectral imaging in the range 900–1,700 nm for spectral characterization of polymers including PS, PVC, PLA, PET, PC, and three types of PE (LDPE, HDPE, and LLDPE). The absorption peaks of different types of plastic are identified by continuum removal method (Balsi et al., 2018). Hibbitts et al. (2019) applied this technique to separate plastic objects such as PS, PP, PE and fiberglass by using the first harmonic of the vibration of carbon-hydrogen (C-H) from 1,650–1,750 nm. They investigated that the most effective ratio to detect and identify different plastic types is 1,540–1,710 nm. Serranti et al. (2019) also used the combination of chemometrics and SWIR hyperspectral imaging in the range between 1,000 and 2,500 nm to identify the polymer particles such as PE, PP and PS (size <5 mm) from marine environment. Bonifazi et al. (2013) have applied hyperspectral imaging to enhance the efficiency of polyolefin recycling system while Moroni et al. (2015) used hyperspectral imaging to separate PET and PVC. The selected wavelength range in this experiment is visible (400–1,000 nm) and SWIR (900–1,700 nm). They concluded that SWIR is more effective to differentiate PET and PVC and the most effective absorption ratio to identify PET and PVC is the value at 1,656 and 1,712 nm. Recently Moroni and Mei (2020) used hyperspectral imaging to separate PS, PET and PLA samples at their different stages of life cycle (virgin to plastic waste). In order to separate three types of plastics, the correlation matrix and distinctive absorption bands as spectral indices were applied. The first spectral index of 1,170–1,650 nm was used to separate PET from PS and PLA. Subsequently, the second spectral index of 1,160–1,140 nm was applied to separate PLA from PS. Caballero et al. (2019) describe the use of hyperspectral imaging to separate polymers with flame retardants to allow grouping of plastics with the same polymer type and additive content necessary for recycling. The decision tree that included a partial least square and hierarchical models was used to identify the types of plastic. The accuracy was higher than 90% in all cases.
For the micro level, hyperspectral imaging was used to detect microplastic which is contamination in seawater. The performance of this technology can detect microplastic with the size down to 300 μm (Karlsson et al., 2016). Zhang et al. (2019) also used hyperspectral imaging to detect microplastic polymer flakes including PC, PET, PP, PS and PE with sizes between 0.1 and 1 mm. A support vector machine classification algorithm (SVM) was applied to analyse hyperspectral images in order to classify the different types of polymers. Chaczko et al. (2019) also applied the combination of deep learning method to analyse hyperspectral images for microplastic detection. Around 1,000 samples were used for model training and the model was tested by 100 samples. The results showed that the classification accuracy of the model in controlled environment was ~95%.
Tracer based sorting (TBS) technology makes it possible to identify a material thanks to the signature of a tracer and not its intrinsic properties (Maris et al., 2012). It addresses the identification problem associated with dark colored polymers by using additives (often fluorescent markers) that can be easily identified (Brunner et al., 2015). TBS is a capable technology of sorting biodegradable plastics. This sorting technique can increase sorting purity, regardless of how badly the biodegradable plastics are deformed or contaminated. Thus, many companies in Europe have implemented this sorting technology to improve the recycling/composting quality of plastic packaging (Sykes, 2018).
Fluorescent markers are inorganic and organic substances that exhibit unique fluorescent characteristic in visible wavelength when excited by ultraviolet light (Ahmad, 2000). As shown in Figure 4 the small amounts of fluorophores are incorporated into polymers during resin manufacturing phase. The concentration of marker needs to be as low as possible [part per million (ppm) or sub part per million] (Brunner et al., 2015; Arenas-Vivo et al., 2017) for two main reasons. The high concentration of fluorophores can have impact on mechanical properties and visual appearance. Moreover, the cost of products is increased when adding additional fluorescent markers (Kosior et al., 2015). The lowest marker concentration is essentially defined by the ability of the measurement system to acquire fluorescence emission spectra with a signal-to-noise ratio (SNR) large enough to reliably perform the classification task. In case of black plastics which absorbs large part of the fluorescent light from the markers, a marker concentration (up to ~100 ppm) is needed (Brunner et al., 2015).
Figure 4. The basic concept of plastic identification and sorting based upon the automated sorting of plastic waste labeled by fluorescent tracers (Brunner et al., 2015).
During the life phase, plastic labeled with fluorescent marker must resist environmental influences such as UV radiation or high temperature (Ahmad, 2004; Maris et al., 2012; Brunner et al., 2015). After this phase, plastics with fluorescent markers are collected and shredded into pieces. They are then separated from other types of waste such as metals and form a stream of mixed plastic flakes. In the identification/classification stage, the polymers are irradiated by excitation light, and their optical signatures collected. When a type of marker is identified, the sorting unit is then activated and an air nozzle blows the polymer flake into an appropriate bin (Ahmad, 2004; Brunner et al., 2015).
In 2015, the tracer-based sorting was applied to macro sorting of polypropylene. The conclusion of this study was the marker concentration down to 3,000 ppm could reliably detected under commercially sorting conditions of 3 m/s and 1.9 tons per hour. Packaging with fluorophore were positively sorted from mixed PP with a yield of 74% and a purity of 93% in single pass and 99.5% in double pass. The label shape area and shape also had impact on the efficiency of the system. The additional cost of packaging material was ~0.4–15% of the USD 0.01 price of an applied label (Kosior et al., 2015). Magnetic tracers have also been tested to sort plastic waste. The advantage of this technology is that it is insensitive to other additives and colorants in incorporated in plastic resins. The limitation is that more than one magnetic marker cannot be applied (Mankosa and Luttrell, 2005) so limiting the number of polymers that can be uniquely sorted.
We have shown in this review that there are several technologies capable of sorting and separating biodegradable and compostable plastics. However, they do not work isolation. To be effective they need to be part of, and fit into, the existing waste management system. In the UK there are various systems used to process household and commercial waste. Organic waste is processed by Industrial Composting (In Vessel Composting and Open Windrow) or Anaerobic Digestion. While mixed recycling is usually transported to material recovery facilities (MRFs) where materials are separated and sorted for processing and recycling. At present biodegradable and compostable are not automatically detected and are treated as contamination. In this section, we highlight five scenarios where effective sorting technologies for compostable plastic are needed to help improve the recycling and composting rates and reduce contamination, these are summarized in Figure 5.
Figure 5. Different scenarios of compostable plastic identification and sorting as part of a circular economy.
There is little evidence that home composting is a sustainable way to manage compostable and biodegradable plastics. This is because the conditions in a home compost need to be managed very carefully to successfully compost such plastics. The European Committee for Standardization (CEN) has prepared a standard on home composting indicating that only small items such as tea bags are considered as compatible with home composting under well managed conditions (European Bioplastics, 2015, 2018). There are also a variety of national standards for home compostable plastics such as TÜV AUSTRIA BELGIUM certification, DIN CERTCO certification. However, that citizens find the label confusing, and often mistake plastics labeled as “biodegradable” and “industrially compostable” as suitable for home composting. This leads to incomplete biodegradation, the production of microplastics and contamination of compost. Digital watermarking is a technology that might help citizens determine which plastics are suitable for home composting. The digital label could be read by a smartphone and provide abundant information including the correct disposal method. Citizens would also require access to technology (phone) and software for detection. This might be an economic barrier.
Compostable plastics often contaminate the recycling of conventional plastics such as HDPE and PET reducing their value. Due to low proportion of compostable plastics in the market, recyclers have not yet invested in equipment to sort and separate compostable plastics (Hopewell et al., 2009). However, if the trend of compostable products continues to increase the automatic separation collection and sorting of compostable plastics may be required.
There are many established sorting technologies which are appropriate for compostable plastics such as centrifugal sorting, sink float sorting, flotation, triboelectric sorting. They are reliable for bulk sorting or separating compostable parts of product once flaked. The installation and operation of these process all have environmental impacts. Sink-float separation techniques use both significant power and water resources, see Table 2, at significant environmental cost. A life cycle assessment would need to be carried out to assess the overall impact of installing these systems.
The modern methods of digital watermarking and tracer based sorting are more suited to sorting individual compostable products from a mixed waste stream. The factors determining their implementation depending on the relative purity of the waste stream, environmental cost, and system adoption of the standards for tracer or digital watermarking (Holygrail, 2017). The study shows that applying tracer-based sorting technology is more environmentally friendly than conventional recycling due to higher recycling rate. It can save up to 1,227 kg CO2 eq/Mg (Kusch et al., 2021).
In the absence of tracer standards or digital watermarking many recyclers have use optical sorting system (NIR based sensor) to sort compostable plastics and improve sorting purity (Gertman, 2013). Hyperspectral imaging combined with AI promises to be even more effective since it combines between spatial and spectral information which can enhance the efficiency for multi-material products.
These compostable plastic sorting technologies are able to enhance sorting purity from mixed recycling collections. However, the operation costs of automatic sorting of compostable plastics sorting from mixed waste streams is high and can only be justified by higher market revenues achieved because of higher purity level of sorting (EEA, 2020).
Separate food waste collections are an important component of sustainability plans for developed economies since they divert organic waste from landfill where it creates greenhouse warming gases. If organic waste is delivered to AD it is used to create biogas. In IVC facilities organic waste is turned into compost which is used as a soil fertilizer. AD facilities are not designed to process compostable plastics and all plastics including compostable and biodegradable plastics are removed in the pre-screening process. IVC facilities are able to accept compostable plastics however they do not have automatic sorting and separating technology to distinguish between compostable and non-compostable packaging, so these facilities suffer from contamination problems. In the United Kingdom, it is voluntary for AD and IVC plants to meet compost quality specifications including minimum standards of plastic contamination [The British Standards Institution's Specification (BSI PAS 110) for AD and (BSI PAS 100) for IVC]. However, it is incentivised through use of recognized certification schemes and commercial demand (Organic-Recycling, 2018). It is a legal requirement for EU that compost and digestate being produced must meet certain standard covering the production process and product quality (ECN, 2022).
The site vetting procedure of plastic in the food waste is thus very important. Ideally, when the food waste is delivered to the AD sites, any compostable plastics should be automatically sorted and fed into IVC facilities. However, currently such automatic sorting systems are not implemented and so all plastics (compostable and biodegradable plastics included) are treated as contaminants and sent to landfill or incineration (REA, 2021).
Advanced sorting technologies including spectral based sorting, digital watermarking and tracer-based sorting are able to offer a good solution to this problem. After food waste is delivered and depackaged at AD facilities, compostable plastics could be separated and sent to IVC facilities for composting. Likewise at IVC facilities automatic sorting could allow the operators to separate out the non-compostable plastics and so reduce their contamination. One uncertainly is which of these techniques is best when plastics are contaminated with food waste (Serranti et al., 2015; Holygrail, 2017; Kusch et al., 2021). Other potential issues might be commercial viability of introducing a two stages process because of the limitations on space for two stages process, and the additional costs of transporting sorted compostable plastics to an IVC site. Table 2 summarizes shows that only a few sorting systems are applicable in this scenario.
Open air windrow (OAW) process is usually used to compost garden waste (WRAP, 2016). In the current system when garden waste is delivered to composting facilities. They are visually inspected to remove plastic contaminants, shredded and shaped into a windrow on a non-permeable surface to produce compost. Loads of garden waste arriving with high level of contaminants (plastic bags) are typically rejected and send to landfill or incineration. This is financially and environmentally less optimal for the operator and yet is required to minimize plastic contamination. Ideally an automatic sorting system could be used to reduce the number of rejected loads by detecting compostable plastics and sending them to IVC facilities for composting. This would need to be done before shredding and the task of successfully separating plastic bags that are embedded in branches and attached by thorns is a non-trivial task. Currently no techniques are available to reliably carry out this type of automatic sorting. Table 2 illustrates that there are very few options for Scenario 4.
When composting various types of organic residues, the finished product always contains a certain amount of contamination such as flakes of plastic film (Edo et al., 2022; REA, 2021). These contaminants need to be reduced in order to improve compost quality. Currently, trommel and density sorting are applied to screen the compost and reduce contamination. However, the levels of contaminants from the current screening process is unacceptably high (SEPA, 2019).
To improve the accuracy of the current system advanced sorting technologies could be used. The spectral based sorting technology (FTIR-ATR and hyperspectral imaging technology) has been confirmed as useful screening tool for identifying type of plastic recovered from the digestates that pass the 2 mm sieve (Kristina Borg Olesen, 2018; Serranti et al., 2019; REA, 2021). Currently, the FTIR spectral imaging has been applied to determine microplastic content but it only detects conventional plastics and has not yet been optimized to detect biodegradable or compostable microplastics. NIR and HIS combined with machine learning algorithm is a potentially more accurate and effective technology (Li et al., 2021). Further work needs to be done to improve automatic identification of biodegradable and compostable microplastics.
NT, DP, and MM wrote the paper and analyzed the different scenarios. All authors contributed to the article and approved the submitted version.
This work was carried out at the UCL Plastic Waste Innovation Hub and was funded by a Thai Government PhD scholarship, and a NERC grant NE/V010735/1.
The authors declare that the research was conducted in the absence of any commercial or financial relationships that could be construed as a potential conflict of interest.
All claims expressed in this article are solely those of the authors and do not necessarily represent those of their affiliated organizations, or those of the publisher, the editors and the reviewers. Any product that may be evaluated in this article, or claim that may be made by its manufacturer, is not guaranteed or endorsed by the publisher.
Ahmad, S. (2004). A new technology for automatic identification and sorting of plastics for recycling. Environ. Technol. 25, 1143–1149. doi: 10.1080/09593332508618380
Ahmad, S. R. (2000). Marking of products with fluorescent tracers in binary combinations for automatic identification and sorting. Assembly Automat. 20, 58–65. doi: 10.1108/01445150010311617
AIM (2021). Pioneering Digital Watermarks for Smart Packaging Recycling in the EU. Available online at: https://www.aim.be/wp-content/themes/aim/pdfs/Digital%20Watermarks%20Initiative%20HolyGrail%202.0%20-%20general%20presentation%20for%20PDF.pdf (accessed December 1, 2021).
ANDRITZ (2020). Setting Standards in Plastics Recycling. Available online at: https://www.andritz.com/resource/blob/13438/297b6952b75c42dd26e8b11e27b4c15b/se-censor-centrifuge-en-data.pdf (accessed June 29, 2021).
ANDRITZ (2021). Separation Setting Standards in Plastics Recycling. Available online at:https://www.andritz.com/resource/blob/13438/297b6952b75c42dd26e8b11e27b4c15b/se-censor-centrifuge-en-data.pdf (accessed December 1, 2021).
Angelonidi, E., and Smith, S. R. (2015). A comparison of wet and dry anaerobic digestion processes for the treatment of municipal solid waste and food waste. Water Environ. J. 29, 549–557 doi: 10.1111/wej.12130
Arenas-Vivo, A., Beltran, F., Alcazar, V., De La Orden, M., and Urreaga, J. M. (2017). Fluorescence labeling of high density polyethylene for identification and separation of selected containers in plastics waste streams. Comparison of thermal and photochemical stability of different fluorescent tracers. Mater. Today Commun. 12, 125–132. doi: 10.1016/j.mtcomm.2017.07.008
ASG (2020). Sink Float Seperation Tank. Available online at: https://www.plasticrecyclingmachine.net/sink-float-separation-tank/ (accessed December 1, 2021).
Association for Organics Recycling (2011). Concise guide to Compostable Products and Packaging UK Local Authority Guidance. Available online at: http://www.organics-recycling.org.uk/uploads/article1983/EN%2013432%20Compostable%20Products%20and%20Packaging.pdf (accessed December 1, 2020).
Awe, O., Mengistu, R., and Sreedhar, V. (2017). Smart trash net: Waste localization and classification. p. 1–6. Available online at: http://cs229.stanford.edu/proj2017/finalreports/5226723.pdf
Balsi, M., Esposito, S., and Moroni, M. (2018). “Hyperspectral characterization of marine plastic litters,” in 2018 IEEE international workshop on metrology for the sea; learning to measure sea health parameters (MetroSea). IEEE, 28–32.
Bátori, V., Åkesson, D., Zamani, A., Taherzadeh, M. J., and Horváth, I. S. (2018). Anaerobic degradation of bioplastics: a review. Waste Manage. 80, 406–413. doi: 10.1016/j.wasman.2018.09.040
Bendimerad, S., Tilmatine, A., Ziane, M., and Dascalescu, L. (2009). Plastic wastes recovery using free-fall triboelectric separator. Int. J. Environ. Stud. 66, 529–538. doi: 10.1080/00207230902722838
Bianna Recycling (2022). Trommels. Available online at: https://biannarecycling.com/en/trommel/ (accessed December 1, 2021).
Bobulski, J., and Kubanek, M. (2019). “Waste classification system using image processing and convolutional neural networks,” in International Work-Conference on Artificial Neural Networks, eds I. Rojas, G. Joya, and A. Catla (Gran Canaria: Springer), 350–361.
Bonifazi, G., Capobianco, G., Palmieri, R., and Serranti, S. (2019). Hyperspectral imaging applied to the waste recycling sector. Spectrosc. Eur. 31, 8–11. doi: 10.1117/12.2014909
Bonifazi, G., D'agostini, M., Dall'ava, A., Serranti, S., and Turioni, F. (2013). A new hyperspectral imaging based device for quality control in plastic recycling. Optical Sensors 2013. International Society for Optics and Photonics, 87741M.
BPF (2019). Packaging Waste Directive & Compostable Packaging. Available online at: https://www.bpf.co.uk/topics/standards_for_compostability.aspx (accessed December 1, 2021).
Bruker (2021). Microplastic Analysis. Available online at: https://www.bruker.com/en/applications/detection-and-environmental/environmental/Microplastics-Analysis.html (accessed Oct 4, 2021).
Brunner, S., Fomin, P., and Kargel, C. (2015). Automated sorting of polymer flakes: Fluorescence labeling and development of a measurement system prototype. Waste Manage. 38, 49–60. doi: 10.1016/j.wasman.2014.12.006
BSI (2018). Specification for Composted Materials. Available online at: http://www.organics-recycling.org.uk/uploads/article3362/PAS%20100.pdf (accessed December 1, 2020).
Caballero, D., Bevilacqua, M., and Amigo, J. M. (2019). Application of hyperspectral imaging and chemometrics for classifying plastics with brominated flame retardants. J. Spectral Imaging 8, 1–16. doi: 10.1255/jsi.2019.a1
Carvalho, M., Agante, E., and Durão, F. (2007). Recovery of PET from packaging plastics mixtures by wet shaking table. Waste Manage. 27, 1747–1754. doi: 10.1016/j.wasman.2006.08.015
CCBA (2021). Waste Recycling Conveyor. Available online at: https://www.conveyor-belt-spares.co.uk/waste-recycling-conveyor.asp (accessed December 1, 2021).
Chaczko, Z., Wajs-Chaczko, P., Tien, D., and Haidar, Y. (2019). “Detection of microplastics using machine learning,” in 2019 International Conference on Machine Learning and Cybernetics (ICMLC). IEEE, 1–8.
Coveya (2021). Specialist Conveyors for Recycling & Waste Management. Available online at: https://www.coveya.co.uk/content/uploads/2020/10/Coveya-Recycling-Waste-Management-Brochure-Spreads.pdf (accessed December 1, 2021).
Cui, J., and Forssberg, E. (2003). Mechanical recycling of waste electric and electronic equipment: a review. J. Hazard. Mater. 99, 243–263. doi: 10.1016/S0304-3894(03)00061-X
Deepomatic (2020). What Is Image Recognition? Available online at: https://deepomatic.com/en/what-is-image-recognition (accessed March 13, 2021).
Dodbiba, G., Sadaki, J., Okaya, K., Shibayama, A., and Fujita, T. (2005). The use of air tabling and triboelectric separation for separating a mixture of three plastics. Miner. Eng. 18, 1350–1360. doi: 10.1016/j.mineng.2005.02.015
Dodbiba, G., Shibayama, A., Sadaki, J., and Fujita, T. (2003). Combination of triboelectrostatic separation and air tabling for sorting plastics from a multi-component plastic mixture. Mater. Trans. 44, 2427–2435. doi: 10.2320/matertrans.44.2427
ECN (2022). Fertilising Product Regulation. Available https://www.compostnetwork.info/policy/from-waste/product-regulation/#require (accessed April 12, 2022).
Edo, C., Fernández-Piñas, F., and Rosal, R. (2022). Microplastics identification and quantification in the composted organic fraction of municipal solid waste. Sci. Total Environ. 813, 151902. doi: 10.1016/j.scitotenv.2021.151902
EEA (2020). Bio-Waste in Europe — Turning Challenges Into Opportunities. Available online at: https://www.eea.europa.eu/publications/bio-waste-in-europe/download (accessed June 10, 2021).
Eikeseth, U. (2013). Machines Are Better Than People at Sorting Household Trash. Available online at: https://sciencenorway.no/environmental-technology-forskningno-government/machines-are-better-than-people-at-sorting-household-trash/1384332 (accessed June 12, 2021).
Eisenreich, N., Kull, H., and Thinnes, E. (1992). “Waste management of energetic materials and polymers,” in 23rd Ann. Conference of the Inst. Chem. Tech Karlsruhe (Germany), 1–59.
EPA (2021). How Does Anaerobic Digestion Work? Available online at: https://www.epa.gov/agstar/how-does-anaerobic-digestion-work (accessed December 1, 2021).
European Bioplastics (2015). Home Composting. Available online at: https://docs.european-bioplastics.org/publications/bp/EUBP_BP_Home_composting.pdf (accessed April 11, 2022).
European Bioplastics (2016). What Are the Required Circumstances for a Compostable Product to Compost? Available online at: https://www.european-bioplastics.org/faq-items/what-are-the-required-circumstances-for-a-compostable-product-to-compost/ (accessed December 1, 2020).
European Bioplastics (2018). Home Composting of Compostable Bioplastics. Available online at: https://docs.european-bioplastics.org/publications/pp/EUBP_PP_Home_composting.pdf (accessed December 1, 2021).
European Bioplastics (2019). Market Drivers And Development. Available online at: https://www.european-bioplastics.org/market/market-drivers/ (accessed October 15, 2020).
Funabashi, M., Ninomiya, F., and Kunioka, M. (2009). Biodegradability evaluation of polymers by ISO 14855-2. Int. J. Mol. Sci. 10, 3635–3654. doi: 10.3390/ijms10083635
Geladi, P., Grahn, H., and Burger, J. (2007). “Multivariate images, hyperspectral imaging: background and equipment,” in Techniques and Applications of Hyperspectral Image Analysis, eds H. F. Grahn and P.Geladi (Hoboken, NJ: John Wiley and Sons), 1–15.
Gent, M. R., Menendez, M., Toraño, J., and Diego, I. (2009a). Recycling of plastic waste by density separation: prospects for optimization. Waste Manage. Res. 27, 175–187. doi: 10.1177/0734242X08096950
Gent, M. R., Menendez, M., Toraño, J., Isidro, D., and Torno, S. (2009b). Cylinder cyclone (LARCODEMS) density media separation of plastic wastes. Waste Manage. 29, 1819–1827. doi: 10.1016/j.wasman.2008.12.026
Gertman, R. (2013). Sorting Out Bioplastics. Available online at: https://resource-recycling.com/images/Gertman0713rr.pdf (accessed June 11, 2021).
Google Developers (2021). Image Classification. Available online at: https://developers.google.com/machine-learning/practica/image-classification/convolutional-neural-networks (accessed March 13, 2021).
Greenpeace (2020). Biodegradable Plastics: Breaking Down the Facts. Available online at: https://www.greenpeace.org/static/planet4-eastasia-stateless/84075f56-biodegradable-plastics-report.pdf (accessed February 28, 2022).
Greyparrot (2021). AI-Driven Waste Recognition System. Available online at: https://www.greyparrot.ai/waste-composition-analysis-software (accessed October 1, 2021).
Gundupalli, S. P., Hait, S., and Thakur, A. (2017). A review on automated sorting of source-separated municipal solid waste for recycling. Waste Manage. 60, 56–74. doi: 10.1016/j.wasman.2016.09.015
Guo, J., Li, X., Guo, Y., Ruan, J., Qiao, Q., Zhang, J., et al. (2016). Research on flotation technique of separating PET from plastic packaging wastes. Proc. Environ. Sci. 31, 178–184. doi: 10.1016/j.proenv.2016.02.024
Hayes, J. (2021). AI-Driven Robotics Key to Recycling's Challenges. Available online at: https://eandt.theiet.org/content/articles/2021/09/ai-driven-robotics-key-to-recycling-s-challenges/ (accessed October 1, 2021).
Hibbitts, C. A., Bekker, D., Hanson, T., Knuth, A., Goldberg, A., Ryan, K., et al. (2019). “Dual-band discrimination and imaging of plastic objects,” in Detection and Sensing of Mines, Explosive Objects, and Obscured Targets XXIV. International Society for Optics and Photonics, 1101211.
Holygrail (2017). HolyGrail: Tagging Packaging for Accurate Sorting and High-Quality Recycling. Available online at: https://www.newplasticseconomy.org/assets/doc/Holy-Grail.pdf (accessed June 10, 2021).
Hopewell, J., Dvorak, R., and Kosior, E. (2009). Plastics recycling: challenges and opportunities. Philos. Trans. R. Soc. B Biol. Sci. 364, 2115–2126. doi: 10.1098/rstb.2008.0311
Hu, B., Fraunholz, N., and Rem, P. (2010). Wetting technologies for high-accuracy sink-float separations in water-based media. Open Waste Manage. J. 3, 71–80. doi: 10.2174/1876400201003010071
Hu, B., Serranti, S., Fraunholcz, N., Di Maio, F., and Bonifazi, G. (2013). Recycling-oriented characterization of polyolefin packaging waste. Waste Manage. 33, 574–584. doi: 10.1016/j.wasman.2012.11.018
Inculet, I., Castle, G., and Brown, J. (1994). “Tribo-electrification system for electrostatic separation of plastics,” in Proceedings of 1994 IEEE Industry Applications Society Annual Meeting. IEEE, 1397–1399.
Jackson, P. (2018). What's the Problem With Plant-Based Packaging? Available online at: https://www.recyclingwasteworld.co.uk/in-depth-article/whats-the-problem-with-plant-based-packaging/178541/ (accessed April 11, 2022).
Kamruzzaman, M., and Sun, D.-W. (2016). “Introduction to hyperspectral imaging technology,” Computer Vision Technology for Food Quality Evaluation, ed D.-W. Sun (Amsterdam: Elsevier).
Karlsson, T. M., Grahn, H., Van Bavel, B., and Geladi, P. (2016). Hyperspectral imaging and data analysis for detecting and determining plastic contamination in seawater filtrates. J. Near Infrared Spectrosc. 24, 141–149. doi: 10.1255/jnirs.1212
Kjeldsen, A., Price, M., Lilley, C., and Guzniczak, E. (2019). A Review of Standards for Biodegradable Plastics. Available online at: www.assets.publishing.service.gov.uk/government/uploads/system/uploads/attachment_data/file/817684/review-standards-for-biodegradable-plastics-IBioIC.pdf (accessed October 10, 2019).
Kosior, E., Mitchell, J., Davies, K., Kay, M., Ahmad, R., Billiet, E., et al. (2015). “Intelligent labels as a basis For auto-sorting Of plastic packaging,” in 73rd Annual Technical Conference. Orlando, USA: IEEE. 2118–2112.
Kristina Borg Olesen, N. (2018). Analysis of Microplastics using FTIR Imaging. Available online at: https://www.agilent.com/cs/library/applications/5991-8271EN_microplastics_ftir_application.pdf (accessed April 4, 2022).
Kusch, A., Gasde, J., Deregowski, C., Woidasky, J., Lang-Koetz, C., and Viere, T. (2021). Sorting and recycling of lightweight packaging in Germany—climate impacts and options for increasing circularity using tracer-based-sorting. Mater. Circular Econ. 3, 1–15. doi: 10.1007/s42824-021-00022-6
Lahtela, V., and Kärki, T. (2018). Mechanical sorting processing of waste material before composite manufacturing-a review. J. Eng. Sci. Technol. Rev. 11, 20–25. doi: 10.25103/jestr.116.06
Lee, L.-H. (1994). Dual mechanism for metal-polymer contact electrification. J. Electrostat. 32, 1–29. doi: 10.1016/0304-3886(94)90026-4
Lesswaste (2022). Compostable, Degradable, Biodegradable and Oxodegradable Plastics. Available online at: https://www.lesswaste.org.uk/recycle/compostable-degradable-biodegradable-and-oxodegradable-plastics/ (accessed Feb 28, 2022).
Li, Y., Yao, J., Nie, P., Feng, X., and Liu, J. (2021). An effective method for the rapid detection of microplastics in soil. Chemosphere 276, 128696. doi: 10.1016/j.chemosphere.2020.128696
Lupo, E., Moroni, M., La Marca, F., Fulco, S., and Pinzi, V. (2016). Investigation on an innovative technology for wet separation of plastic wastes. Waste Manage. 51, 3–12. doi: 10.1016/j.wasman.2016.02.030
Maisel, F., Chancerel, P., Dimitrova, G., Emmerich, J., Nissen, N. F., and Schneider-Ramelow, M. (2020). Preparing WEEE plastics for recycling–How optimal particle sizes in pre-processing can improve the separation efficiency of high quality plastics. Resources Conserv. Recycling 154, 104619. doi: 10.1016/j.resconrec.2019.104619
Mallampati, S. R., Heo, J. H., and Park, M. H. (2016). Hybrid selective surface hydrophilization and froth flotation separation of hazardous chlorinated plastics from E-waste with novel nanoscale metallic calcium composite. J. Hazard. Mater. 306, 13–23. doi: 10.1016/j.jhazmat.2015.11.054
Mankosa, M. J., and Luttrell, G. H. (2005). Plastic Material Having Enhanced Magnetic Susceptibility, Method of Making and Method of Separating. Available online at: https://patents.google.com/patent/US6920982 (accessed April 14, 2021).
Maris, E., Aoussat, A., Naffrechoux, E., and Froelich, D. (2012). Polymer tracer detection systems with UV fluorescence spectrometry to improve product recyclability. Miner. Eng. 29, 77–88. doi: 10.1016/j.mineng.2011.09.016
Masoumi, H., Safavi, S. M., and Khani, Z. (2012). Identification and classification of plastic resins using near infrared reflectance. Int. J. Mech. Indus. Eng. 6, 213–220. doi: 10.5281/zenodo.1076916
Mata-Alvarez, J., Macé, S., and Llabres, P. (2000). Anaerobic digestion of organic solid wastes International Journal of Mechanical and Industrial Engineering, 6, 213-20. An overview of research achievements and perspectives. Bioresour. Technol. 74, 3–16 doi: 10.1016/S0960-8524(00)00023-7
Mattley, Y. (2020). Spectroscopy for Plastics Recycling. Available online at: https://www.monospektra.com/spectroscopy-for-plastics-recycling/ (accessed June 10, 2021).
Mehrubeoglu, M., Van Sickle, A., and Turner, J. (2020). “Detection and identification of plastics using SWIR hyperspectral imaging,” in Imaging Spectrometry XXIV: Applications, Sensors, and Processing. International Society for Optics and Photonics, 115040G.
Menezes, J. C., Ferreira, A., Rodrigues, L., Brás, L., and Alves, T. (2009). Chemometrics Role Within the PAT Context: Examples From Primary Pharmaceutical Manufacturing. Amsterdam: Elseiver.
Michigan, U. O. (2021). Cyclones/Hydrocyclones. Available online at: https://encyclopedia.che.engin.umich.edu/Pages/TransportStorage/CyclonesHydroCyclones/CyclonesHydroCyclones.html (accessed April 29, 2021).
Moroni, M., and Mei, A. (2020). Characterization and separation of traditional and bio-plastics by hyperspectral devices. Appl. Sci. 10, 2800. doi: 10.3390/app10082800
Moroni, M., Mei, A., Leonardi, A., Lupo, E., and Marca, F. L. (2015). PET and PVC separation with hyperspectral imagery. Sensors 15, 2205–2227. doi: 10.3390/s150102205
Organic-Recycling (2018). PAS 100 and Compost Quality Specifications. Available online at: http://www.organics-recycling.org.uk/page.php?article=1800 (accessed December 4, 2021).
Packaging Europe (2021). NEXTLOOPP Unveils Results of Tracer-Based Sorting Trials. Available online at: https://packagingeurope.com/nextloopp-unveils-results-of-tracer-based-sorting-trials/ (accessed December 1, 2021).
Pagliano, G., Ventorino, V., Panico, A., and Pepe, O. (2017). Integrated systems for biopolymers and bioenergy production from organic waste and by-products: a review of microbial processes. Biotechnol. Biofuels 10, 1–24. doi: 10.1186/s13068-017-0802-4
Park, C.-H., Jeon, H.-S., Yu, H.-S., Han, O.-H., and Park, J.-K. (2008). Application of electrostatic separation to the recycling of plastic wastes: separation of PVC, PET, and ABS. Environ. Sci. Technol. 42, 249–255. doi: 10.1021/es070698h
Pathak, S., Sneha, C., and Mathew, B. B. (2014). Bioplastics: its timeline based scenario & challenges. J. Polymer Biopolymer Phys. Chem. 2, 84–90. doi: 10.12691/jpbpc-2-4-5
Pita, F., and Castilho, A. (2017). Separation of plastics by froth flotation. The role of size, shape and density of the particles. Waste Manage. 60, 91–99. doi: 10.1016/j.wasman.2016.07.041
Pongstabodee, S., Kunachitpimol, N., and Damronglerd, S. (2008). Combination of three-stage sink–float method and selective flotation technique for separation of mixed post-consumer plastic waste. Waste Manage. 28, 475–483. doi: 10.1016/j.wasman.2007.03.005
ProdecologiaUA. (2017). Separation on Triboelectric Separator of Mix of Plastics PP+PE. Available online at: https://www.youtube.com/watch?v=lMvhiVpMNM8 (accessed December 1, 2021).
QUBE (2018). What Is Wet Anaerobic Digestion? Available online at: https://www.quberenewables.co.uk/new-blog/what-is-wet-anaerobic-digestion (accessed December 1, 2021).
Rad, M. S., Von Kaenel, A., Droux, A., Tieche, F., Ouerhani, N., Ekenel, H. K., et al. (2017). “A computer vision system to localize and classify wastes on the streets,” in International Conference on Computer Vision Systems, eds M. Liu, H. Chen, and M. Vincze (Shezhen: Springer), 195–204.
Rani, M., Marchesi, C., Federici, S., Rovelli, G., Alessandri, I., Vassalini, I., et al. (2019). Miniaturized near-infrared (MicroNIR) spectrometer in plastic waste sorting. Materials 12, 2740. doi: 10.3390/ma12172740
REA (2021). Policy on Liners and Re-purposed Bags Suitable for Separate Collection of Targeted Food Waste Streams From Households, Businesses and Non-domestic Premises in Eng. Available online at: https://www.r-e-a.net/wp-content/uploads/2021/08/REA_policy_on_liners_and_re-purposed_bags_for_collecting_targeted_food_waste_streams_FINAL_v1-1_18082021.pdf (accessed December 1, 2021).
Research, A. M. (2022). Compostable Plastic Market. Available online at: https://www.alliedmarketresearch.com/compostable-plastic-market-A06578 (accessed Feb 28, 2022).
RS (2021). Neublade Airstrip. Available online at: https://docs.rs-online.com/7051/0900766b80b5824c.pdf (accessed December 1, 2021).
Saha, S. (2018). A Comprehensive Guide to Convolutional Neural Networks — the ELI5 Way. Available online at: https://towardsdatascience.com/a-comprehensive-guide-to-convolutional-neural-networks-the-eli5-way-3bd2b1164a53 (accessed March 12, 2021).
Saisinchai, S. (2014). Separation of PVC from PET/PVC mixtures using flotation by calcium lignosulfonate depressant. Eng. J. 18, 45–54. doi: 10.4186/ej.2014.18.1.45
Saiter, J., Sreekumar, P., and Youssef, B. (2011). “Different ways for re-using polymer based wastes,” in The Examples of Works Done in European Countries, eds A. Fainleib and O. Grigoryeva (Transworld Research Network Publishing), 261–291.
Sakr, G. E., Mokbel, M., Darwich, A., Khneisser, M. N., and Hadi, A. (2016). “Comparing deep learning and support vector machines for autonomous waste sorting,” in 2016 IEEE International Multidisciplinary Conference on Engineering Technology (IMCET). IEEE, 207–212.
Schwerzler, G. I. (2005). Recycling of glaze waste through hydrocyclone separation. Powder technology 160, 135–140. doi: 10.1016/j.powtec.2005.08.032
SEPA (2019). Plastic in Food Waste at Compost Sites. Available online at: https://www.sepa.org.uk/media/536296/191125-final-compost-input-quality-report-v6.pdf (accessed December 1, 2021).
Serranti, S., Fiore, L., Bonifazi, G., Takeshima, A., Takeuchi, H., and Kashiwada, S. (2019). “Microplastics characterization by hyperspectral imaging in the SWIR range,” in SPIE Future Sensing Technologies. International Society for Optics and Photonics, 1119710.
Serranti, S., Gargiulo, A., and Bonifazi, G. (2011). Characterization of post-consumer polyolefin wastes by hyperspectral imaging for quality control in recycling processes. Waste Manage. 31, 2217–2227. doi: 10.1016/j.wasman.2011.06.007
Serranti, S., Luciani, V., Bonifazi, G., Hu, B., and Rem, P. C. (2015). An innovative recycling process to obtain pure polyethylene and polypropylene from household waste. Waste Management 35, 12–20. doi: 10.1016/j.wasman.2014.10.017
Shent, H., Pugh, R., and Forssberg, E. (1999). A review of plastics waste recycling and the flotation of plastics. Resources Conserv. Recycling 25, 85–109. doi: 10.1016/S0921-3449(98)00017-2
Shuguang (2020). Automatic Electrostatic Separation Mixed Plastic Physical Sorting Machine. Available online at: https://www.alibaba.com/product-detail/Automatic-electrostatic-separation-mixed-plastic-physical_1600269979725.html?spm=a2700.galleryofferlist.normal_offer.d_title.121e5954JmTPwi&s=p (accessed December 1, 2021).
Sionine (2021). Mineral Froth Flotation Machine (flotation cell) for All Kinds of Ores as Flotation Separator. Available online at: https://sinonine.en.made-in-china.com/product/moEQKgRxqdAj/China-Mineral-Froth-Flotation-Machine-flotation-cell-for-All-Kinds-of-Ores-as-Flotation-Separator-.html (accessed December 1, 2021).
Siracusa, V. (2019). Microbial degradation of synthetic biopolymers waste. Polymers 11, 1066. doi: 10.3390/polym11061066
Siracusa, V., Rocculi, P., Romani, S., and Dalla Rosa, M. (2008). Biodegradable polymers for food packaging: a review. Trends Food Sci. Technol. 19, 634–643. doi: 10.1016/j.tifs.2008.07.003
Song, J., Murphy, R., Narayan, R., and Davies, G. (2009). Biodegradable and compostable alternatives to conventional plastics. Philos. Trans. R. Soc. B Biol. Sci. 364, 2127–2139. doi: 10.1098/rstb.2008.0289
Southey, F. (2020). Digital Watermarks : Pepsico, Nestle and Unilever Back Sorting Tech Packaging Recycling (accessed October 1, 2021).
Stokes, G. (2017). The Myth of Plant Based Food Packaging - PLA Plastic From Corn and It's Darker Side (accessed April 11, 2022).
Sykes, T. (2018). Sorting the Plastic Recycling Problem. Available online at: https://packagingeurope.com/sorting-plastic-recycling-tracers-digital-watermarks-tomra-procter-gamble/ (accessed June 11, 2021).
Taylor, D. M., and Secker, P. E. (1994). Industrial Electrostatics: Fundamentals and Measurements. Taunton: Research Studies Press.
Vaško, T. (2015). Methods of waste separation in the process of recycling. Tehnički glasnik 9, 345–351. Available online at: https://hrcak.srce.hr/clanak/220448
Vert, M., Doi, Y., Hellwich, K.-H., Hess, M., Hodge, P., Kubisa, P., et al. (2012). Terminology for biorelated polymers and applications (IUPAC Recommendations 2012). Pure Appl. Chem. 84, 377–410. doi: 10.1351/PAC-REC-10-12-04
Vilaplana, F., and Karlsson, S. (2008). Quality concepts for the improved use of recycled polymeric materials: a review. Macromol. Mater. Eng. 293, 274–297. doi: 10.1002/mame.200700393
Wang, C.-Q., Wang, H., Fu, J.-G., and Liu, Y.-N. (2015). Flotation separation of waste plastics for recycling—A review. Waste Manage. 41, 28–38. doi: 10.1016/j.wasman.2015.03.027
Watson, P. K., and Yu, Z.-Z. (1997). The contact electrification of polymers and the depth of charge penetration. J. Electrostat. 40, 67–72. doi: 10.1016/S0304-3886(97)00016-8
Wienaah, M. M. (2007). Sustainable Plastic Waste Management: A Case of Accra, Ghana. Arkitektur och samhällsbyggnad, Kungliga Tekniska högskolan.
Wold, S., Esbensen, K., and Geladi, P. (1987). Principal component analysis. Chemometr. Intelligent Lab. Syst. 2, 37–52. doi: 10.1016/0169-7439(87)80084-9
WRAP (2016a). Anaerobic Digestion: The Process. Available online at: Https://wrap.org.uk/resources/guide/anaerobic-digestion-process (accessed December 1, 2020).
WRAP (2016b). Open Windrow Composting. Available online at: https://wrap.org.uk/resources/guide/open-windrow-composting (accessed December 1, 2021).
WRAP (2020). On-Pack Labelling and Citizen Recycling Behaviour. Available online at: https://wrap.org.uk/sites/default/files/2021-09/WRAP-On-pack-labelling-and-recycling-behaviour_0.pdf (accessed February 18, 2022).
Wu, G., Li, J., and Xu, Z. (2013). Triboelectrostatic separation for granular plastic waste recycling: a review. Waste Manage. 33, 585–597. doi: 10.1016/j.wasman.2012.10.014
Xu, J. L., and Gowen, A. A. (2020). Spatial-spectral analysis method using texture features combined with PCA for information extraction in hyperspectral images. J. Chemom. 34, e3132. doi: 10.1002/cem.3132
Yang, M., and Thung, G. (2016). “Classification of trash for recyclability status,” in CS229 Project Report 2016.
Younes, A., Younes, M., Sayah, H., Samuila, A., and Dascalescu, L. (2015). Experimental and numerical modeling of a new tribo-electrostatic separation process for granular plastics mixtures. Particulate Sci. Technol. 33, 189–196. doi: 10.1080/02726351.2014.948976
Yuan, H., Fu, S., Tan, W., He, J., and Wu, K. (2015). Study on the hydrocyclonic separation of waste plastics with different density. Waste Manage. 45, 108–111. doi: 10.1016/j.wasman.2015.01.037
Zenkiewicz, M., Zuk, T., and Markiewicz, E. (2015). Triboelectric series and electrostatic separation of some biopolymers. Polym. Test. 42, 192–198. doi: 10.1016/j.polymertesting.2015.01.009
Zero Waste Scotland (2021). What Is In-Vessel Composting? Available online at: https://www.zerowastescotland.org.uk/content/what-vessel-composting (accessed December 1, 2021).
Zhang, Y., Wang, X., Shan, J., Zhao, J., Zhang, W., Liu, L., et al. (2019). Hyperspectral imaging based method for rapid detection of microplastics in the intestinal tracts of fish. Environ. Sci. Technol. 53, 5151–5158. doi: 10.1021/acs.est.8b07321
Keywords: identification technologies, sorting technologies, compostable plastics, biodegradable plastics, plastic waste management
Citation: Taneepanichskul N, Purkiss D and Miodownik M (2022) A Review of Sorting and Separating Technologies Suitable for Compostable and Biodegradable Plastic Packaging. Front. Sustain. 3:901885. doi: 10.3389/frsus.2022.901885
Received: 22 March 2022; Accepted: 22 April 2022;
Published: 20 May 2022.
Edited by:
Atiq Zaman, Curtin University, AustraliaReviewed by:
Francesco Degli-Innocenti, Novamont S.p.A. - Chimica Vivente per la Qualità della Vita, ItalyCopyright © 2022 Taneepanichskul, Purkiss and Miodownik. This is an open-access article distributed under the terms of the Creative Commons Attribution License (CC BY). The use, distribution or reproduction in other forums is permitted, provided the original author(s) and the copyright owner(s) are credited and that the original publication in this journal is cited, in accordance with accepted academic practice. No use, distribution or reproduction is permitted which does not comply with these terms.
*Correspondence: Danielle Purkiss, ZGFuaWVsbGUucHVya2lzc0B1Y2wuYWMudWs=; Mark Miodownik, bS5taW9kb3duaWtAdWNsLmFjLnVr
Disclaimer: All claims expressed in this article are solely those of the authors and do not necessarily represent those of their affiliated organizations, or those of the publisher, the editors and the reviewers. Any product that may be evaluated in this article or claim that may be made by its manufacturer is not guaranteed or endorsed by the publisher.
Research integrity at Frontiers
Learn more about the work of our research integrity team to safeguard the quality of each article we publish.