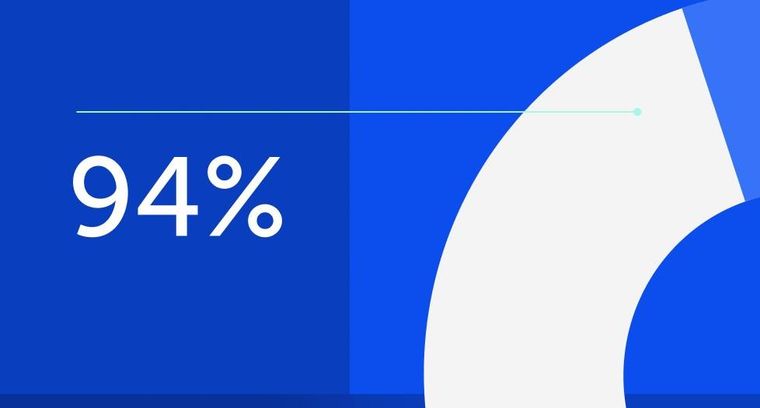
94% of researchers rate our articles as excellent or good
Learn more about the work of our research integrity team to safeguard the quality of each article we publish.
Find out more
ORIGINAL RESEARCH article
Front. Sustain., 29 November 2022
Sec. Sustainable Chemical Process Design
Volume 3 - 2022 | https://doi.org/10.3389/frsus.2022.1057190
This article is part of the Research TopicCurrent and Emerging Trends in CO2 Utilization Towards the Global Challenge of SustainabilityView all 5 articles
Dimethyl ether (DME) could have a promising future as a sustainable diesel fuel replacement as it requires only relatively minor engine modifications. It can be produced from renewable H2 and captured CO2 using Power-to-X technologies. To gain support through the EU Renewable Energy Directive, the production and use of CO2-derived DME as a fuel needs to produce emission savings of at least 70% over the petrodiesel alternative. This study assesses the carbon footprint of producing DME via the sorption-enhanced DME synthesis (SEDMES) process and using it as a transport fuel, compared to producing and using fossil-based petrodiesel. The cradle-to-grave (well-to-wheel) carbon footprint of using DME as a transport fuel is found to be 77% lower than for petrodiesel, if offshore wind power is used for H2 synthesis and DME production. If renewable energy is also used for CO2 capture and waste heat is used for the DME production and purification steps, the DME carbon footprint has the potential to be over 90% lower than that of the fossil-fuel comparator.
Dimethyl ether (DME) can be either blended with diesel fuel or used as a diesel fuel replacement with only minor modifications to the injection system plus installation of a pressure tank, similar to that used for liquid petroleum gas (LPG) to store the DME in liquid form (Park and Lee, 2013). When combusted as a transport fuel, air pollution is reduced compared to conventional petrodiesel, with reductions in NOx and SOx as well as particulates (Semelsberger et al., 2006). What makes DME especially interesting is that it can be produced from captured CO2 using Power-to-X technologies, making it a renewable liquid or gaseous transport fuel of non-biological origin (here abbreviated to RFNBO) according to the EU Renewable Energy Directive (RED II). Such fuels are characterized by their embodied energy being derived from renewable energy, usually electricity, hence their alternative name of e-fuels. Considering the difficulty experienced in electrifying heavy goods vehicles, DME could have a promising future as a sustainable diesel fuel replacement. However, for this to happen, the production of CO2-derived DME and its subsequent use as a fuel would need to result in carbon emissions over 70% lower than the petrodiesel alternative.
RED II does not provide support for renewable fuels directly, but Article 25 directs Member States to set an obligation upon transport fuel suppliers to ensure that by 2030 at least 14% of the final energy consumed by the transport sector arises from renewable energy (European Parliament, 2018). In July 2021 the Commission published a proposal to revise the transport fuels target to comprise a 13% reduction in the greenhouse gas intensity by 2030 (equivalent to an energy-based target of 28%) along with a new target of 2.6% for RFNBOs (European Commission, 2021). The demand for such fuels from fuel suppliers who need to fulfill the obligation is expected to increase the value of such fuels considerably. RFNBOs include hydrogen generated through the electrolysis of water using renewable electricity if the resulting H2 is used directly in a vehicle powered by a H2 fuel cell. Other RFNBOs can be produced by reacting the resulting H2 with captured CO2 to produce alcohols, ethers, or hydrocarbon fuels. Article 25(2) of RED II explains that if the use of RFNBOs can be shown to achieve greenhouse gas (GHG) emission savings of at least 70%, then they will be eligible to be supplied by fuel suppliers to meet their RED II obligation.
This study compares the carbon footprint arising from the production and use of DME as a diesel road- fuel replacement with the carbon footprint from the production and use of petrodiesel. The DME production process evaluated is the sorption-enhanced DME synthesis (SEDMES) process being developed as part of the EU Interreg 2 Seas Electrons to high value Chemical products (E2C) project. In this project, a demonstration facility (TRL 5 moving to 6) is being built which is capable of reacting renewable H2 with captured CO2 to generate DME directly using SEDMES (Boon et al., 2019; Van Kampen et al., 2019, 2020, 2021). SEDMES increases the conversion efficiency of CO2 to DME over other production processes (Hansen et al., 1995; Müller and Hübsch, 2020; Khadzhiev et al., 2017; Sheldon, 2017), by the in-situ removal of the H2O formed by the use of selective absorbents. However, the carbon footprint of the process has not been determined—until now.
A techno-economic assessment of the SEDMES process developed as part of the E2C project has already been published (Skorikova et al., 2020), as has a financial assessment of another CO2-derived DME process (Michailos et al., 2019). Environmental lifecycle assessments (LCAs) of CO2-derived DME are very limited in number (Matzen and Demirel, 2016; Bongartz et al., 2018; Parvez et al., 2018; Tomatis et al., 2019) and many of those have focused upon forms of Bio-DME such as that derived from the gasification of biomass to produce syngas (Parvez et al., 2018; Tomatis et al., 2019). The carbon footprint assessment conducted in this study uses the modeling used for the techno-economic assessment, which is provided in detail elsewhere (Skorikova et al., 2020). This study is the first time that the carbon footprint of DME produced using SEDMES has been evaluated, and also the first time that the carbon footprint of the production and use of Power-to-X derived DME as an e-fuel, has been evaluated against policy requirements.
Resource availability: Inventory data are provided in the Supplementary material.
Dimethyl ether can be produced from CO2 and H2 in a two-step process where methanol is produced in the first step, before being dehydrated to produce DME. A single-step process is also possible, but can result in low DME yields due to the accumulation of water. This can beproduced during three distinct steps: during the methanol synthesis reaction, during the reverse water gas-shift reaction and during the methanol dehydration reactions. Water produced in this way leads to an equilibrium within the reactor (De Falco et al., 2016). Sorption-enhanced reactions offer the effective removal of this water using a selective sorbent, which shifts the reaction equilibrium to the product.
The Power-to-X DME production process being assessed has already been modeled and described in Skorikova et al. (2020), where further details are available. Briefly, captured CO2 is supplied at 30 bar to the SEDMES reactor, together with H2 produced by a 40 MW PEM electrolyser.
PEM electrolysis was selected as the source of the H2 as it is expected that PEM will soon become the preferred choice over the currently industrially used alkaline electrolyzers. The electricity input for the PEM electrolyzer is assumed to be 40 MW. Saturated hydrogen comes out of the electrolyzer at 80° C and 30 bara containing 1.5 wt% of water. It is cooled to 28.2°C in order to reduce the water level to nearly 0 wt%. The operating pressure of the SEDMES unit is determined by the electrolyzer so that the H2 does not need to be additionally pressurized, which contributes to the savings on a compressor installation and operation.
CO2 is supplied to the SEDMES reactor at 30 bara, where it is mixed with the H2 in stoichiometric ratio and preheated to the SEDMES operating temperature The SEDMES process consists of three packed-bed reactor tubes which are cycled to allow blowdown/purging/repressurisation stages to enable continuous production. DME synthesis happens on the sorbent/catalyst bed at 275°C which requires preheating. However, DME formation is an exothermic process, so the reactor tubes are packed within a shell supplied with a cooling media. This approach allows smart heat integration within the process which heavily reduces its carbon intensity.
Finally, DME purification is conducted as part of downstream processing (DSP). The SEDMES product is initially cooled and sent to a flash drum to separate the non-condensables such as unconverted H2 and the CO by-product. Depending on the temperature in the separator, some fractions of CO2 and DME may be removed as gas fractions. The column is operated at the pressure of the SEDMES product stream (29 bara), so a compact compressor is needed to recycle the non-condensables back to the SEDMES reactor. Next, a first distillation column is used for the separation of CO2 and DME—the most energy-intensive process due to similar characteristics of these compounds. Removed CO2 with a small fraction of DME is compressed and recycled back to the SEDMES reactor to eliminate losses of the feed or the product. Finally, DME is separated from methanol and water in a second distillation column until the desired purity is achieved. It is then cooled and stored in a tank ready for transportation.
This study has the goal to assess the carbon footprint of producing DME via the SEDMES process and using it as a transport fuel, compared to producing and using petrodiesel. The aim is to assess whether the SEDMES technology can reduce the carbon footprint of production and use of a transport fuel compared to the equivalent footprint for petrodiesel by at least 70% as specified by RED II. As DME has a lower energy density than diesel fuel, the footprint is to be compared per MJ of each fuel. The plant modeled is based on one of the two pilot demonstration plants under construction as part of the E2C project. The considered capacity is 23,400 tons DME/year, corresponding to that modeled in the business case analysis (Skorikova et al., 2020). The geographical scope of the analysis is the Interreg 2 Seas region adjacent to the Channel and the southern sector of the North Sea—simplified here to UK, France, Belgium and the Netherlands.
The carbon footprint was calculated using SimaPro 9 with Ecoinvent version 3.6 and using the IPCC 2013 GWP 100a method for measuring climate change impact. To enable the impact of the source of the CO2 utilized to be properly assessed, system expansion and substitution techniques were used when the CO2 came from an industrial source. The system boundary is presented in Figure 1, showing the inclusion of CO2 source, but not including the O2 by-product of electrolysis and pollutants released during DME usage as a transport fuel, other than CO2. As subsequently described, the specific details of the CO2 capture have not been modeled, but the CO2 footprint of the capture as obtained from published literature is included instead.
Figure 1. The study system boundary (represented by the dotted line) when using system expansion to determine the carbon footprint of the Power-to-X DME process when using CO2 captured from a bioethanol plant.
An attributional approach, to quantify the environmental impacts that can be attributed to DME, as well as the contributions of individual processes, was used. To divide the environmental impact of processes that produced more than one output (i.e., multifunctional processes), mass allocation was used throughout the study. Oxygen produced by the electrolyser was assumed to be vented to air rather than being compressed and sold as a product.
Ecoinvent's allocation at the point of substitution (APOS) inventory data were used to model the background processes. In this system model, burdens are attributed proportionally to the processes. To test the influence of such system model in the results, all calculations were also performed with the alternative cut-off system model provided by Ecoinvent, in which primary production of materials is allocated only to the primary user of a material. Results obtained by both system models differed only by a small fraction (e.g., <0.2% when GB electricity was used), therefore the choice of the system model does not significantly influence LCA results.
A study conducted by Oak Ridge National Laboratory and Volvo North America (Szybist et al., 2014) concluded that, in spite of the different energy densities, a heavy-duty truck engine running on DME produces a similar level of efficiency as a truck engine running on conventional diesel fuel. As a consequence, the functional unit used to compare the carbon footprint of DME with that of petrodiesel is 1 MJ fuel. The reference flow, i.e., the basis on which all mass flows within the system boundaries are calculated, is 1 kg DME produced. Lifecycle inventory data is provided in Supplementary material.
The carbon footprint of DME and petrodiesel during combustion differs per MJ, therefore any assessment comparing the two fuels needs to include an assessment of the footprint of the two fuels during use rather than just during production. This approach matches the requirements of RED II, which states that the use of RFNBOs must achieve the specified 70% reduction in GHG emissions. Therefore, the assessment followed a cradle-to-grave (or well-to-wheel) approach.
Annex V of RED II provides guidance on calculating the greenhouse gas impacts of biofuels, but at the time of writing, rules for RFNBOs have not yet been published. Biofuels are required to be compared to a fossil fuel comparator with a footprint of 94 g CO2eq/MJ (European Parliament, 2018), so this study assumes that RFNBOs will be compared to the same comparator. A 70% reduction compared to 94 g CO2eq/MJ implies that the cradle-to-grave emissions of any new RFNBOs need to be lower than 28 g CO2eq/MJ to gain support through RED II.
The Power-to-X DME production process can be divided into four processes: CO2 capture, H2 production by PEM electrolysis, DME production by SEDMES, and DME purification as part of DSP. Inventory data is provided in Supplementary material.
Feedstock CO2 required: The Lower Heating Value of DME is 28.9 MJ/kg and according to the reaction stoichiometry, the SEDMES process converts 1.911 kg CO2 into 1 kg DME, therefore 66.1 g CO2 is required per MJ DME. In practice, however, the carbon-efficiency of a single-pass is only around 80%. Much of the CO2 which does not form DME is converted to carbon monoxide (CO), while around 1% remains as unreacted CO2 and a fraction of the input carbon leaves the reaction vessel as methanol. As both the CO and the unreacted CO2 is recycled back into the reactor, only the carbon lost as methanol needs to be replaced, leading to a small increase in the feedstock CO2 required to 67 g CO2/MJ DME.
Carbon footprint determination: As a cradle-to-grave footprint is required, the footprint of capturing the required CO2 is needed. Carbon capture does not form part of the E2C project, which is focused upon the actual DME production. As a consequence, the project has not performed modeling of different CO2 capture technology that could be used in this analysis. To avoid modeling CO2 capture technologies which has already been done elsewhere, published data was utilized.
The carbon footprint of feedstock CO2 captured from a variety of different sources has been published by Müller et al. (2020). As expected, it was found that CO2 captured from a concentrated source (such as flue gas from a bioethanol plant) has a lower footprint than CO2 captured from a dilute source such as the atmosphere. In their modeling, they described a conventional corn bioethanol plant which emits 960 g CO2 per kg ethanol produced. This plant would therefore produce 70 g of ethanol while producing the 67 g of CO2 required as feedstock to produce 1 MJ DME. This forms the functional unit when system expansion is used. The overall carbon footprint of the CO2 captured from the above bioethanol plant (i.e., the CO2 captured plus that emitted as a result of the capture process) was reported to be −940 g CO2 per kg CO2 captured.
When CO2 was captured from the atmosphere using direct air capture (DAC) technology, the reported footprint was −590 g CO2 per kg CO2 captured (Müller et al., 2020). That modeling assumed that both technologies used electricity from an average of the EU-28 grids and that heat was supplied from natural gas (assuming an EU-28 mix from the GaBi database). The carbon intensity of the electricity used to obtain these footprints was high at 477 g CO2eq/kWh.
The above authors also modeled the footprint of carbon capture in a low-carbon future when the electricity was from renewable sources and synthetic methane was substituted for natural gas. In that scenario, the footprint of CO2 capture from a bioethanol plant was reported to be −990 g CO2 per kg CO2 captured and that from DAC was −980 g CO2 per kg CO2 captured.
A model PEM electrolyser was created within SimaPro based upon a fuel cell included in Ecoinvent. This was modified by replacing tetrafluoroethylene as the separator with a Nafion proton exchange membrane and adding an aqueous sulphuric acid solution (assuming 15 %wt. for the anode and 20 %wt. for the cathode (Sun and Hsiau, 2019). Copper and titanium were added to the model due to their respective use as current collectors and bipolar plates in the PEM (Bareiß et al., 2019). The PEM unit was assumed to have a lifetime of 15 years.
The oxygen produced during electrolysis was assumed to be vented to air rather than being captured, compressed and sold as a product. Depending upon the allocation scenario chosen, it is possible that a reduction in the overall H2 production footprint could be achieved by determination of the avoided footprint of O2 produced by conventional means, but this would be offset by the additional energy required to compress the O2 prior to sale.
The SEDMES reactor and the downstream processing unit had been modeled as part of the E2C business case analysis (Skorikova et al., 2020). That modeling was utilized so that the carbon footprint and the techno- economic analyses make the same assumptions in terms of technology, scale and utility use.
The infrastructure of the SEDMES unit was modeled in SimaPro based upon a methanol plant. The footprint of the Cu/ZnO/Al2O3 catalyst was calculated assuming a 67%, 29% and 5% mass composition ratio respectively. The copper material was assumed to be of a purity equivalent to a copper cathode to account for the footprint of the added processing required. Zinc oxide and aluminum oxide were selected from the global market. Water released from the process unit is represented as softened water in the technosphere as it is the water with the lowest amount of processing available in Ecoinvent.
The SEDMES reaction is not 100% efficient and some unreacted H2 and CO2 plus reaction products CO and methanol are removed from the SEDMES reaction vessel at the end of the reaction cycle and enter the DSP unit. As well as purifying the DME produced, the DSP unit therefore also involves recycling the gaseous H2, CO2 and CO back to the reaction vessel and collecting the methanol produced. Due to the sorption-enhanced process, H2O in the output stream is low at only around 0.03%, so in terms of the LCA this is allocated to wastewater.
Hydrogen production has a significant carbon footprint, so recycling the unreacted H2 results in this action delivering a negative footprint since it means that we can avoid the production of that quantity of H2. On the other hand, capturing CO2 results in the capture process having a negative carbon footprint if the CO2 captured is included. This means that the act of recycling unreacted CO2 results in a positive footprint as less carbon negative CO2 is now required. To avoid such complications in the footprint of the DSP unit, the recycled H2 was subtracted from the PEM process and recycled CO2 was subtracted from the CO2 capture unit.
Between 1–2% of the carbon supplied by the CO2 leaves the reaction vessel in the form of methanol (Liuzzi et al., 2020), and when performing an LCA a decision needs to be made how this should be handled. It could be treated as a waste or as a co-product along with DME. It was considered more likely that in a commercial environment it would be treated as a co-product and sold onto the chemicals market, rather than disposed of as a waste. In this case it generates a small negative footprint (−0.5 g CO2eq/MJ DME) due to the avoidance of fossil-derived methanol. The next section shows that this negative footprint is only a minor component of the overall DME footprint so it is felt it does not significantly distort the data in an unrealistic way.
The carbon footprint of each of the four processes making up the overall DME production process was determined assuming the use of six different sources of electricity available in Ecoinvent: the national grids of France, Belgium, UK and Netherlands, plus offshore wind and solar PV. However, Ecoinvent (versions 3.6 and 3.7) uses electricity data from 2014 for the four national markets. The actual carbon intensity of electricity supplied today is well below the 2014 level due to increasing use of renewables. The carbon intensity used by Ecoinvent for the national electricity supplies compared to data provided by the European Environment Agency (2020) is presented in the Supplementary material.
By plotting the carbon intensity of the electricity used against the carbon footprint of DME production (i.e., the sum of the PEM, SEDMES and DSP processes) the graph presented in Figure 2 was created.
Figure 2. Plot of the carbon footprint of DME production against the modeled carbon intensity of the six different sources of electricity used (assuming the carbon intensity of the four countries as provided by the European Environment Agency, 2020).
The footprint of CO2 capture was not included because these six electricity sources were not used in modeling that footprint (the capture footprint was taken from the literature as previously described).
By creating individual plots similar to that presented in Figure 2 for the PEM electrolysis, SEDMES and DSP processes, the carbon footprint of each process was determined assuming 2019 electricity carbon intensity data rather than the 2014 data used by Ecoinvent. The data supplied by Ecoinvent for offshore wind and solar PV were used unchanged.
The footprint of each of the four processes are reviewed in turn and are summarized in Table 1. The source of the electricity, heat and CO2 used has a significant effect upon the footprint of the PEM, SEDMES and DSP steps. To allow analysis of the relative contributions of these processes, it is assumed that heat is provided by steam from the chemicals industry (Ecoinvent assumes around 104 g CO2eq/MJ heat) and the CO2 used is captured from a bioethanol plant. Electricity from the British (GB) grid is used to compare to electricity derived from offshore wind, as it has a carbon intensity toward the center of the range between The Netherlands and France.
The footprint of capturing CO2 from a bioethanol plant was reported to be −940 g CO2 per kg CO2 when EU average grid electricity was used. Capturing the 67 g CO2 required to produce each MJ of DME therefore results in an overall capture footprint of −63 g CO2eq/MJ DME. Alternatively, the −940 g CO2 per kg CO2 figure indicates that capturing each kg of CO2 results in the emission of 60 g CO2 by the capture process itself. When scaled to the 67 g CO2 required as feedstock per MJ DME production, 4 g of additional CO2 will be emitted.
Using renewable energy for both the electricity and heat required in the capture process reportedly reduces the footprint to −990 g CO2 per kg CO2, meaning that the footprint would be −66.3 g CO2/MJ DME or 0.67 g of CO2 is emitted to capture the CO2 required to produce each MJ DME.
The footprint of capturing CO2 using DAC with EU average grid electricity was reported to be −590 g CO2 per kg CO2 captured, so the footprint of the CO2 required to produce each MJ of DME is −39.5 g CO2eq/MJ DME. The alternative view is that capturing each kg of CO2 results in the emission of 410 g CO2 by the capture process. When scaled to the 67 g CO2 required as feedstock per MJ DME production, approximately 27.5 g of additional CO2 is emitted.
Using renewable energy reportedly reduced the DAC footprint to −980 g CO2 per kg CO2, meaning that the footprint when using DAC is almost identical to the footprint when using concentrated CO2 from a bioethanol plant (i.e., approximately −65.7 g CO2/MJ DME). Alternatively, 1.34 g CO2 is emitted by the act of capturing the CO2 required to produce each MJ of DME.
Construction of the electrolyser stack was found to have a significant carbon footprint, amounting to over 83 tons CO2eq, largely due to components such as platinum, titanium, the Nafion membrane and the electricity required in its construction (44% was due to the platinum). However, when this construction footprint is distributed across the total quantity of DME produced over the modeled 15 year working life of the electrolyser, it actually comprises <1% of the overall PEM footprint when the footprint of the electrolyser usage is included. This is consistent with the findings of Bareiß et al. (2019), who also reported that the construction of the stack contributed <1% of the footprint of a PEM electrolyser over its lifetime. In our model, the electricity required to run the electrolyser accounted for over 99% of the carbon footprint of this process step, even when electricity with a low- carbon intensity was used. When GB grid electricity is used, the combined PEM footprint amounts to 110 g CO2eq/MJ DME, when offshore wind power is used the PEM footprint is 7.6 g CO2eq/MJ DME.
The construction component of the footprint used for the SEDMES reactor, and the downstream processing (DSP) unit was based upon the Ecoinvent construction footprint of a methanol plant. It identified that steel contributed 57%, followed by diesel and electricity used in the construction process which together contributed a further 23%. Zinc, copper and nickel came next in terms of percentage contribution, followed by concrete. In order to allocate the construction footprint between the two process units, the footprint of the methanol plant construction was split equally between the SEDMES unit construction and the DSP unit construction. This approach was considered to be acceptable because the combined plant construction footprint, as with the electrolyser, is a small proportion of the overall SEDMES and DSP footprint once it has been divided over the modeled 20-year lifetime of the plant. The combined SEDMES and DSP construction footprint was 0.2 g CO2eq/MJ DME.
To ensure that the construction footprint of the SEDMES unit was as close to reality as possible, the footprint of the zeolite and catalysts specific to the SEDMES process were included within the calculation of the overall SEDMES footprint. When heat is supplied by steam from the chemicals industry, it contributes approximately 97% of the SEDMES carbon footprint. The bulk of the remaining 3% is contributed by the zeolite support and the copper component of the catalyst.
The overall footprint of the SEDMES process is 6.8 g CO2eq/MJ DME irrespective of the electricity source, meaning that construction of the reactor plus the catalysts and support contributed approximately 4% to the overall SEDMES footprint.
The main task of the DSP unit is the purification of the DME by distillation. The requirement for heat and electricity forms a large proportion of this carbon footprint. The overall footprint of the DSP process was determined to be 5.4 g CO2eq/MJ DME if GB electricity was used, or 3.7 if offshore wind power was utilized. The construction of the DSP unit only contributed between 1.9 and 2.7% of the overall DSP footprint.
The positive carbon footprints of the individual DME production processes described above when using GB grid electricity or offshore power (and heat from steam from the chemicals industry) are summarized in Table 1. It is immediately apparent that the PEM electrolyser contributes 90% of the positive production footprint when GB grid electricity is used and this is almost exclusively due to electricity use. The carbon intensity of the electricity used is therefore of paramount importance.
Before determining the overall footprint of the process, a sensitivity analysis is conducted to determine how sensitive the system is to changing the source of the three main inputs: electricity, heat and CO2. This is combined with a contribution analysis which enables the assessment of which process contributes most to the overall carbon footprint.
The carbon footprint of DME production is highly sensitive to the carbon intensity of the electricity used, with a doubling of the electricity carbon intensity causing the footprint to almost double. The relationship between electricity source and the relative contributions made to the overall production footprint by the PEM electrolysis, SEDMES and the DSP process steps is revealed in Figure 3A.
Figure 3. (A) The carbon footprint of the DME production depending upon the electricity source: offshore wind, solar photovoltaics and French, Belgian, British and Dutch grid electricity (the four nations considered represent those within the 2 Seas region as defined by Interreg). The relative contributions of the PEM electrolysis, SEDMES and DSP processes are shown. The footprint of CO2 capture from a bioethanol plant is provided purely for context as described in the text. (B) The relative contribution toward the DME production footprint of PEM electrolysis, SEDMES and DSP when electricity is derived from an offshore wind farm compared to the Dutch electrical grid. (C) Relative contribution toward the DME production footprint of the PEM electrolysis, SEDMES and DSP processes when the source of the heat is changed from steam produced within the chemicals industry (Steam), to natural gas to waste heat from municipal waste incineration (MWI). (D) The DME footprint, including the negative CO2 capture footprint, when the production steps (PEM, SEDMES and DSP) are powered using different electricity sources: offshore wind, solar PV, and the four national electricity grids. The three bars each represent a different CO2 capture option: DAC powered by European grid-average electricity; bioethanol plant flue-gas capture powered by European grid-average electricity; either DAC or bioethanol plant capture powered using renewable electricity and heat (a single bar is shown as they are almost identical when renewable power and heat are used).
The scenarios presented all use heat supplied as steam from the chemicals industry. The negative footprint of the CO2 capture step is presented in this figure simply to provide context and an idea of the scale of the negative capture footprint compared to the positive footprints generated by the PEM, SEDMES and DSP processes. Literature-derived values for the footprint of CO2 captured from a bioethanol plant assuming average EU-27 grid mix electricity (−63.0 g CO2eq/MJ DME) when national electricity was used for DME production and renewable electricity (−66.3 g CO2eq/MJ DME) when electricity from wind or solar was used for DME production.
More detail on the relative contributions of the PEM, SEDMES and DSP processes to the positive DME production footprint is provided in Figure 3B. Two contrasting scenarios are presented, with electricity being supplied by low carbon intensity offshore wind and the high carbon intensity Dutch grid.
The source of the heat used in the SEDMES and DSP processes has a significant impact upon the carbon footprint of those processes. Ecoinvent assumes steam from the chemicals industry has a carbon footprint per MJ of 103.5, heat from natural gas 74.2 and waste heat from municipal waste incineration (MWI) 8.75 g CO2eq/MJ. Figure 3C shows the relative contribution of the PEM, SEDMES and DSP steps to the carbon footprint of DME production for the three different heat sources, when used in conjunction with electricity from offshore wind and CO2 captured from a bioethanol plant.
Figure 3C reveals that the combined production carbon footprint is halved by switching the heat source from steam generated within the chemicals industry to waste heat from MWI. As the heat source is changed to one with a lower carbon intensity, the carbon footprint of the SEDMES and DSP steps reduce from 58% of the overall footprint to just over 9%, reflecting the high heat requirement of these processes.
It was previously explained that the footprint of the CO2 capture process depends upon both the concentration of CO2 in the source and the electricity used. According to the capture footprints described in Müller et al. (2020) which are used in this work, the footprint of CO2 captured from an industrial source such as a bioethanol plant (where the CO2 in the flue gas is already very concentrated) is around 59% lower than when captured from the air (where the CO2 is dilute) using DAC technology. However, when the electricity and heat used for capture are renewable, then the difference in footprint between the two capture technologies reduces to around 1% as shown by the data in Table 1.
When the negative CO2 capture footprint is included in the production footprint calculation, the overall DME footprint is as presented in Figure 3D. The figure uses the same data as is presented in Figure 3C with six different electricity sources, all using the same heat source for consistency (steam from chemicals industry). Three CO2 capture options are compared: DAC powered by European grid average electricity, flue-gas captured from a bioethanol plant using the same electricity, and CO2 captured using either technology but powered by renewable electricity and heat (as the footprint of CO2 capture from DAC is almost identical to that from a concentrated source if renewable electricity and heat are used).
So far, we have determined the DME production footprint (i.e., cradle-to-gate), but in order to see whether this process meets the requirements of RED II we need to look at the production of the feedstock CO2 and the use of DME as a transport fuel—i.e., a cradle-to-grave assessment. In order to do this, system expansion is used to include the footprint of the bioethanol plant to source CO2. However, this makes a multi-product system with the footprint relating to both the ethanol as well as the DME. To enable us to focus solely upon the DME footprint we use substitution to remove the ethanol from the system. The conceptual process used is presented in Figure 4.
Figure 4. Carbon-flow in the conventional system compared to the Power-to-X system using offshore wind power and heat derived from steam from the chemicals industry. Substitution is used to subtract the emissions from the bioethanol plant, leaving just the emissions from DME production and use.
The expanded system including the bioethanol plant is multi-functional as it produces both ethanol and DME. The functional unit therefore has two components, 1 MJ DME and 70 g ethanol. The calculation used assumes complete combustion of DME which would produce 66 g CO2eq/MJ DME and that the carbon footprint of fuel distribution will be the same for both systems.
By subtracting the conventional bioethanol plant from the Power-to-X system we remove bioethanol from the functional unit and the emissions arising from the bioethanol plant from the system emissions. This leaves just the emissions arising from the DME fuel production and combustion. Using system expansion and substitution gives a well-to-wheel (or cradle-to-grave) carbon footprint for producing DME via the SEDMES process and using it as a transport fuel of 21 g CO2eq/MJ DME. When compared to the fossil fuel figure of 94 g CO2eq/MJ fuel as provided as comparator by the RED II, a reduction of 77% is achieved.
If the feedstock CO2 is obtained from DAC rather than from an industrial flue-gas, the system is not multi-functional because there are no co-products such as ethanol being produced. Consequently, when using DAC, although we still need to include the footprint of capturing the feedstock CO2, we do not need to perform the substitution step. Figure 5 provides a carbon-flow diagram.
Figure 5. Carbon-flow when DAC is used to supply the CO2 required. The figures assume that DAC uses electricity with an EU grid average carbon intensity (Müller et al., 2020).
Using system expansion with substitution when CO2 is captured from a bioethanol plant as described, the well-to-wheel (WTW) footprint of the modeled DME plant is presented in Table 2 when using various scenarios for electricity, heat and CO2 source. Two sets of results are obtained, using either EU-average grid electricity or renewables for CO2 capture.
Table 2. The Power-to-X DME well-to-wheel or cradle-to-grave carbon footprints when DME is produced using different sources of electricity, heat and CO2.
The carbon intensity of the electricity used from the six different sources modeled was plotted against the WTW carbon footprint of DME to produce the graph presented in Figure 6. For consistency, it was assumed that the required heat was derived from steam arising from the chemicals industry and that CO2 was captured from a bioethanol plant using renewable power.
Figure 6. The WTW carbon footprint of DME production and use plotted against: (A) the carbon intensity of the different electricity sources modeled. All assume CO2 was captured from a bioethanol plant using renewable power and heat for DME production was from steam derived from the chemicals industry. Dotted lines indicate the fossil fuel footprint of 94 g CO2eq/MJ and the 70% reduction target specified by RED II. (B) The CO2 capture footprint. Assumes using offshore wind and heat from steam derived from the chemicals industry. CO2 capture used: (A) DAC powered by EU grid electricity; (B) bioethanol plant flue-gas capture powered by EU grid electricity; (C) DAC powered by renewable energy; (D) flue-gas capture powered by renewables. (C) The heat footprint from steam from the chemicals industry, natural gas and waste heat from MWI. Assumes using offshore wind and CO2 captured from a bioethanol plant using renewable energy.
Figure 6A reveals that in order to achieve the WTW footprint of 28 g CO2eq/MJ DME (i.e., the 70% reduction over fossil fuels specified by RED II) the carbon intensity of the electricity used to produce DME needs to be 37 g CO2eq/kWh or lower. In practice, this means that the electricity needs to be generated by wind, neither the low-carbon electricity supplied by the nuclear-dominated French national grid nor that supplied by solar PV (according to the carbon intensity assumed by Ecoinvent) are low enough. This value assumes that the heat required for SEDMES and DSP was derived from steam arising from the chemicals industry and that the CO2 needed was captured using renewable power from a bioethanol plant.
Figure 6B plots the WTW DME footprint against the footprint of the CO2 capture step (for DAC and bioethanol flue-gas captured CO2 using EU grid electricity and renewables), allowing us to observe the relationship between the two. The modeling assumes DME production is powered by offshore wind and heat is supplied by steam from the chemicals industry. To achieve the desired WTW footprint of 28 g CO2eq/MJ DME, the CO2 capture footprint must be −835 g CO2eq/kg captured CO2 (or −56 g CO2eq/MJ DME). This means in practice that if DAC is to be used it has to use renewable heat and power, whereas if the CO2 is captured from a concentrated industrial flue-gas such as that from a bioethanol plant, then the capture process can use grid electricity so long as the DME production uses wind power.
Figure 6C plots the WTW DME footprint against the third variable, heat—modeled as being provided by steam from the chemicals industry, natural gas and waste heat from a municipal waste incinerator (MWI). Using waste heat from MWI halves the footprint compared to using steam from the chemicals industry. So long as the electricity used is derived from offshore wind, the source of the heat required for SEDMES and DSP is not crucial in terms of meeting the 70% emissions reduction target defined by RED II. However, once low-carbon electricity is used, there is the potential to reduce emissions from 17.8 to 8.1 g CO2eq/MJ DME, which amounts to a further reduction of 54% leading to an overall emissions reduction of 91% compared to fossil fuels.
The SEDMES Power-to-X technology has the potential to reduce life-cycle GHG emissions of transport fuel by up to 91% compared to fossil fuels. To achieve this level of reduction, the electricity used for both CO2 capture and DME production (including H2 production) needs to be derived from offshore wind and the heat required must be waste heat from municipal waste incineration. However, even if the heat used is steam from the chemicals industry or from natural gas, and if European average grid electricity is used to capture the required CO2 from a bioethanol plant, the emissions reductions achieved by using SEDMES would be enough to meet the 70% emissions reduction target specified in RED II, so long as electricity from offshore wind is used for DME (including H2) production.
In this study, data for the CO2 capture unit was taken from the literature and therefore the carbon intensity for CO2 capture could not be changed in the same way as was done for the DME production unit by changing the electricity source. Whilst this could be considered a limitation of the study, this approach does reflect reality as it is quite likely that CO2 capture will be conducted by the emitting facility which will be operated by a separate company than the DME production facility. Whilst it is clear that the Power-to-X facility will have to be supplied solely with renewable power in order to achieve the levels of emissions reductions required by RED II, it is more likely that the facility supplying captured CO2 will be supplied by electricity from the local electricity grid and that this will be used for CO2 capture.
As the overall process footprint is reduced by the use of renewable electricity, the footprint of the heat required becomes relatively more important. When using electricity from offshore wind, the carbon footprint of the DME purification step is 21% of the overall DME production process when heat is provided by steam. System engineering to improve heat integration could potentially enable the utilization of heat arising from the SEDMES reaction to supply the heat required for DME purification. Whilst this may not be a game-changer on its own, further evaluation of the utilization of waste heat from the exothermic SEDMES reaction to simultaneously reduce the cooling required as well as reduce the heating requirements of other parts of the process would potentially be a significant step toward further reduction of the carbon footprint.
As a carbon footprint assessment based upon data modeled for a demonstration plant, the results of this study have high levels of uncertainty. However, as an indication of its ability to reduce transport fuel carbon footprints to the levels required by European legislation to enable financial support, it should give Power-to-X developers confidence that this technology is heading in the right direction.
The original contributions presented in the study are included in the article/Supplementary material, further inquiries can be directed to the corresponding author.
PWS was the principal author of the paper. IG was a Masters (MEng) project student who carried out the main analyses. PS was principal investigator and contributed to the writing and editing of the manuscript. All authors contributed to the article and approved the submitted version.
This project has received funding from the Interreg 2 Seas programme 2014–2020 co-funded by the European Regional Development Fund under subsidy contract no 2S03–019 E2C. Additional funding for the work was provided by the Engineering and Physical Sciences Research Council (EP/V011863/1) as part of the UKRI interdisciplinary Center for Circular Chemical Economy.
The authors declare that the research was conducted in the absence of any commercial or financial relationships that could be construed as a potential conflict of interest.
All claims expressed in this article are solely those of the authors and do not necessarily represent those of their affiliated organizations, or those of the publisher, the editors and the reviewers. Any product that may be evaluated in this article, or claim that may be made by its manufacturer, is not guaranteed or endorsed by the publisher.
The Supplementary Material for this article can be found online at: https://www.frontiersin.org/articles/10.3389/frsus.2022.1057190/full#supplementary-material
Bareiß, K., de la Rua, C., Möckl, M., and Hamacher, T. (2019). Life cycle assessment of hydrogen from proton exchange membrane water electrolysis in future energy systems. Appl. Energy 237, 862–872. doi: 10.1016/j.apenergy.2019.01.001
Bongartz, D., Dor,é, L, Eichler, K., Grube, T., Heuser, B., Hombach, L. E., et al. (2018). Comparison of light-duty transportation fuels produced from renewable hydrogen and green carbon dioxide. Appl. Energy 231, 757–767. doi: 10.1016/j.apenergy.2018.09.106
Boon, J., van Kampen, J., Hoogendoorn, R., Tanase, S., van Berkel, F. P. F., and van Sint Annaland, M. (2019). Reversible deactivation of γ-alumina by steam in the gas-phase dehydration of methanol to dimethyl ether. Catal. Commun. 119, 22–27. doi: 10.1016/j.catcom.2018.10.008
De Falco, M., Capocelli, M., and Centi, G. (2016). Dimethyl ether production from CO2 rich feedstocks in a one-step process: thermodynamic evaluation and reactor simulation. Chem. Eng. J. 294, 400–409. doi: 10.1016/j.cej.2016.03.009
European Commission (2021). Commission Presents Renewable Energy Directive revision. Available online at: https://ec.europa.eu/info/news/commission-presents-renewable-energy-directive-revision-2021-jul-14_en (accessed September 27, 2022).
European Environment Agency (2020). Greenhouse Gas Emission Intensity of Electricity Generation. Data Visualization. Available online at: https://www.eea.europa.eu/data-and-maps/daviz/co2-emission-intensity-6#tab-chart_2 maps/daviz/co2-emission-intensity-6#tab-chart_2 (accessed September 27, 2022).
European Parliament (2018). Directive (EU) 2018/2001/EC of the European Parliament and of the Council of 11 December 2018 on the Promotion of the Use of Energy from Renewable Sources (Recast). EUR-Lex. Available online at: https://eur-lex.europa.eu/legal-content/EN/TXT/?uri=uriserv%3AOJ.L_.2018.328.01.0082.01.ENG&toc=OJ%3AL%3A2018%3A328%3ATOC (accessed September 27, 2022).
Hansen, J. B., Voss, B., Joensen, F., and Sigurð*ardóttir, I. D. (1995). Large scale manufacture of Dimethyl Ether—a new alternative diesel fuel from natural gas. SAE Trans. 104, 70–79. doi: 10.4271/950063
Khadzhiev, S. N., Ezhova, N. N., and Yashina, O. V. (2017). Catalysis in the dispersed phase: Slurry technology in the synthesis of dimethyl ether Pet. Chem. 57, 553–570. doi: 10.1134/S0965544117070040
Liuzzi, D., Peinado, C., Peña, M., van Kampen, J., Boon, J., and Rojas, S. (2020). Increasing dimethyl ether production from biomass-derived syngas via sorption enhanced dimethyl ether synthesis. Sustain. Energy Fuels 4, 5674–5681. doi: 10.1039/D0SE01172J
Matzen, M., and Demirel, Y. (2016). Methanol and dimethyl ether from renewable hydrogen and carbon dioxide: alternative fuels production and life-cycle assessment. J. Clean. Prod. 139, 1068–1077. doi: 10.1016/j.jclepro.2016.08.163
Michailos, S., McCord, S., Sick, V., Stokes, G., and Styring, P. (2019). Dimethyl ether synthesis via captured CO2 hydrogenation withinthe power to liquids concept: a techno-economic assessment. Energy Conv. Manag. 184, 262–276. doi: 10.1016/j.enconman.2019.01.046
Müller, L., Kätelhön, A., Bringezu, S., McCoy, S., Suh, S., Edwards, R., et al. (2020). The carbon footprint of the carbon feedstock CO2. Energy Environ. Sci. 13, 2979–2992. doi: 10.1039/D0EE01530J
Müller, M., and Hübsch, U. (2020). “Dimethyl Ether,” in Ullmann's Encycl. Ind. Chem. Wiley-VCH Verlag GmbH & Co. KGaA. doi: 10.1002/14356007.a08_541
Park, S. H., and Lee, C. S. (2013). Combustion performance and emission reduction characteristics of automotive DME engine system. Progress Energy Comb. Sci. 39, 147–168. doi: 10.1016/j.pecs.2012.10.002
Parvez, A. M., Wu, T., Li, S., Miles, N., and Mujtaba, I. M. (2018). Bio-DME production based on conventional and CO2-enhanced gasification of biomass: a comparative study on exergy and environmental impacts. Biomass Bioenergy 110, 105–113. doi: 10.1016/j.biombioe.2018.01.016
Semelsberger, T. A., Borup, R. L., and Greene, H. L. (2006). Dimethyl ether (DME) as an alternative fuel. J. Power Sourc. 156, 497–511. doi: 10.1016/j.jpowsour.2005.05.082
Sheldon, D. (2017). Methanol production-a technical history. Johnson Matthey Technol. Rev. 61, 172–182. doi: 10.1595/205651317X695622
Skorikova, G., Saric, M., Sluijter, S. N., van Kampen, J., Sanchez-Martinez, C., and Boon, J. (2020). The techno-economic benefit of sorption enhancement: evaluation of sorption-enhanced dimethyl ether synthesis for CO2 utilization. Front. Chem. Eng. 2,594884. doi: 10.3389/fceng.2020.594884
Sun, C., and Hsiau, S. (2019). Effect of electrolyte concentration difference on hydrogen production during PEM electrolysis. J. Electrochem. Sci. Technol. 9, 99–108. doi: 10.33961/JECST.2018.9.2.99
Szybist, P., McLaughlin, J., and Iyer, S. (2014). Emissions and Performance Benchmarking of a Prototype Dimethyl Ether Fuelled Heavy-Duty Truck. Oak Ridge National Laboratory. Available online at: https://afdc.energy.gov/files/u/publication/ornl_dme_tm-2014-59.pdf (accessed September 27, 2022).
Tomatis, M., Parvez, A. M., Afzal, M. T., Mareta, S., Wu, T., He, J., et al. (2019). Utilization of CO2 in renewable DME fuel production: A life cycle analysis (LCA)-based case study in China. Fuel 254, 115627. doi.org/10.1016/j.fuel.2019.115627. doi: 10.1016/j.fuel.2019.115627
Van Kampen, J., Boon, J., van Berkel, F., and van Sint Annaland, M. (2021). Separation enhanced methanol and dimethyl ether synthesis. J. Mater. Chem. A. 9 14627–14629. doi: 10.1039/D1TA03405G
Van Kampen, J., Boon, J., van Berkel, F., Vente, J., and van Sint Annaland, M. (2019). Steam separation enhanced reactions: review and outlook. Chem. Eng. J. 374, 1286–1303. doi: 10.1016/j.cej.2019.06.031
Keywords: Power-to-X, e-fuel, sorption-enhanced, dimethyl ether, carbon footprint, lifecycle, CO2 utilization, CCU-policy
Citation: Styring P, Sanderson PW, Gell I, Skorikova G, Sánchez-Martínez C, Garcia-Garcia G and Sluijter SN (2022) Carbon footprint of Power-to-X derived dimethyl ether using the sorption enhanced DME synthesis process. Front. Sustain. 3:1057190. doi: 10.3389/frsus.2022.1057190
Received: 29 September 2022; Accepted: 09 November 2022;
Published: 29 November 2022.
Edited by:
Laxman Singh, Siddharth University Kapilvastu, IndiaReviewed by:
Qingchun Yang, Hefei University of Technology, ChinaCopyright © 2022 Styring, Sanderson, Gell, Skorikova, Sánchez-Martínez, Garcia-Garcia and Sluijter. This is an open-access article distributed under the terms of the Creative Commons Attribution License (CC BY). The use, distribution or reproduction in other forums is permitted, provided the original author(s) and the copyright owner(s) are credited and that the original publication in this journal is cited, in accordance with accepted academic practice. No use, distribution or reproduction is permitted which does not comply with these terms.
*Correspondence: Peter Styring, cC5zdHlyaW5nQHNoZWZmaWVsZC5hYy51aw==
Disclaimer: All claims expressed in this article are solely those of the authors and do not necessarily represent those of their affiliated organizations, or those of the publisher, the editors and the reviewers. Any product that may be evaluated in this article or claim that may be made by its manufacturer is not guaranteed or endorsed by the publisher.
Research integrity at Frontiers
Learn more about the work of our research integrity team to safeguard the quality of each article we publish.