- 1Pacific Northwest National Laboratory, Richland, WA, United States
- 2National Renewable Energy Laboratory, Golden, CO, United States
- 3Los Alamos National Laboratory, Los Alamos, NM, United States
Separation technologies currently used in U.S. manufacturing industries are estimated to account for more than 20% of plant energy consumption. However, accurately determining the impact of new separation technology solutions can sometimes be difficult, especially when evaluating a slate of new candidate separation technologies, each of which has its own separation performance, energy demand, and capital cost. In these cases, a typical approach is to assess each new separation technology by collecting performance and cost information and then using that information to develop a techno-economic analysis to identify overall benefits. While this approach is thorough, it can be time consuming and can hinder reaching a critical understanding of the potential of a given separation challenge, especially when there is no known solution. To address these issues, we developed an assessment methodology, using industrial screening processes, that can be used to better understand the potential impacts of addressing a given separation challenge. This paper presents an overview of our separation challenge stream assessment methodology. The methodology involves defining an “ideal” separator and deriving the associated minimum separation energy. The “ideal” separator represents the most optimistic outlook of a given opportunity so the maximum impact from existing and not-yet-developed solutions can be assessed. Using established biorefinery models, we applied the methodology to 10 different separation challenge streams from two different biomass conversion platforms to identify the type of information that can be obtained. Three of the ten challenge streams assessed had maximum possible cost savings predictions >20%, and associated reductions in process energy carbon intensity ranging from 0 to 54%. Two streams had cost and energy savings potential that were < 5%. Some of the opportunity drivers from the various assessments include higher product yields, reduction or elimination of downstream equipment, new co-products, and cost savings associated with raw materials and energy consumption. The information from these assessments can help guide the selection or development of new separation technology solutions based on the various potential factors that drive the projected benefits.
Introduction
Separation technologies used in current U.S. manufacturing industries are estimated to account for more than 20% of plant energy consumption. As a result, there is a significant need for more efficient separation technology solutions. In manufacturing processes, separation challenges are defined when the separation of products or intermediates is difficult, energy-intensive, or expensive (Oak Ridge National Laborator., 2005). However, the impact of a new separation technology can sometimes be difficult to ascertain, especially when evaluating a slate of new candidate technologies, each of which has its own separation performance, energy demand, and capital cost. In these cases, a typical approach is to assess each new technology by collecting performance and cost information and then using that information to conduct a techno-economic analysis (TEA) to assess overall benefits. This approach is thorough but can be time-consuming and hinder the development of a critical understanding of the possible opportunity for a given separation challenge, especially when there is no known solution.
To address this issue, we developed an assessment methodology that can be used to reach a better, more comprehensive understanding of the potential impacts of a given separation challenge. Our methodology, which leverages steps commonly used in industrial screening, was refined within the Separations Consortium Program, under the U.S. Department of Energy's Bioenergy Technologies Office (BETO), to help guide applications for separation technologies currently under development (Bioprocessing Separations Consortium., 2017).
In our methodology, we used optimistic values for energy and capital costs to evaluate the maximum potential impact with an ideal separation technology under the optimal scenario (Yamamoto et al., 2000; Tsiropoulos et al., 2022). The strength of our approach vs. an approach that assesses a specific separation technology is that it recognizes and addresses underlying costs and performance factors that can potentially confound the true impact of one particular separation challenge. Indeed, if a known separation technology were assessed, the economic and energy impacts may not be overly compelling. However, an advanced separation technology solution, potentially even one that has not been developed yet, could have a major impact on economic and energy metrics. Compared to the conventional TEA approach, our methodology does not depend on the details of the separation technology to generate economic and energy consumption data; instead, an ideal scenario will be assumed to evaluate the maximum potential impact of any separation technology. While we developed this methodology to address bioprocessing challenges, it can easily be extended to other processing platforms.
Methodology
Assumptions
The aim of our assessment methodology was to determine the maximum potential opportunity of a given separation challenge while not being bound to the constraints of a given technical solution. Note that to apply the elements of this methodology, an established process model must exist.
• We assumed an “ideal” separation technology in all cases. Here, the separation energy for the “ideal” separator was assumed to require only two times (2×) the minimum theoretical separation energy as the lower bound (see the section below for the associated justification). If the minimum theoretical separation energy could not be estimated, a value of zero was assumed.
• To represent the optimal equipment costs for the “ideal” separation technology, we assumed the overall associated capital for the technology to be zero ($0). The motivation for this extreme assumption is that if the economic benefit is not sufficient based on a minimum separation energy assumption only, the addition on capital cost will only worsen the conclusion.
• Besides energy, some “ideal” separators may produce a sellable co-product, which can be accounted for in higher-level economic analysis.
• Some “ideal” separators may significantly impact downstream equipment needs, thereby reducing or eliminating those costs.
• The carbon intensity associated with process energy impacts (e.g., electricity and natural gas) must be normalized to a primary energy basis for comparison purposes. For the bioprocessing cases discussed in this paper, any electricity obtained from outside sources was assumed to come from natural gas-fired power generation.
Certain elements shown in the above assumptions are not necessarily new and leverage assumptions commonly used in industrial screening approaches. However, the overall methodology offers a uniform and consistent means of assessing a broader set of separation challenges streams compared to typical one-off assessments.
The following section describes the specific derivation of the minimum separation energy and 2 × minimum determination. This section is followed by sections that apply the overall methodology to a series of bioprocessing examples.
Determination of the separation energy for an “ideal” separation technology
To calculate the minimum theoretical separation energy of a given stream, a perfect membrane separator is first assumed (see Figure 1). Here, the feed stream enters the membrane, and a product stream exits with the target chemical purified to a certain required level. A residue stream with a composition based on the mass balance and recovery rate also is generated. Using this outline, the minimum theoretical separation energy is equal to the difference between the Gibbs free energies (G) of the outlet streams (product and residue) and the inlet stream (feed) (House et al., 2011).
For non-ideal mixtures, deviations from ideality are considered by including activity coefficients, and the minimum theoretical separation energy can be determined as follows:
where R is the gas constant, T is the temperature in K, X is the mole fraction, γ is the activity coefficient, and N is the mole flow rate (House et al., 2011).
It is important to point out that the minimum theoretical separation energy using the above methodology is a “work” value from a thermodynamic perspective. As such, it needs to be converted to primary energy before it can be compared with the heat duty calculated in many process models (Schwab, 2016). For example, if an aqueous stream has 10 wt% (4.2 mol%) ethanol that then is concentrated to 99.99 wt% (99.97 mol%), the minimum estimated theoretical separation energy is 6.8 kJ (work)/mol ethanol. If a natural gas power generation efficiency of 42% is applied, the primary energy value is 16.2 kJ (heat)/mol ethanol. The calculated minimum theoretical separation energies for all the products studied in this paper are summarized in Supplementary Table S1.
Because no technology can realistically perform at its minimum theoretical separation energy, the next parameter to understand is a reasonable multiplier for an “ideal” (but feasible) separation technology. Figure 2 shows the actual energy vs. the corresponding theoretical energy for several important commercial separation technologies (Leeper, 1992). This ratio ranges from 3× to 20×. Therefore, for purposes of the current evaluation methodology, a 2 × multiplier on the minimum theoretical energy was considered to be the best, yet feasible, case for an “ideal” separation technology.
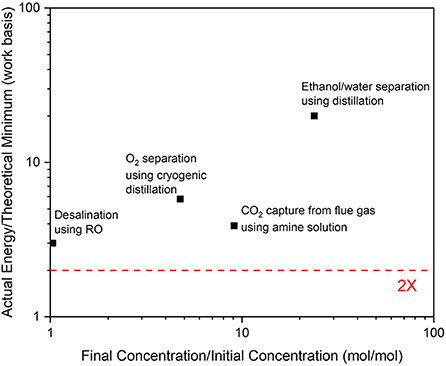
Figure 2. Commercial separation energies divided by the corresponding minimum theoretical separation energy plotted against the concentration ratio (final/initial). The data for ethanol distillation (Leeper, 1992), desalination (Abou Rayan and Khaled, 2003), O2 separation (Singh et al., 2003), and CO2 capture from flue gas (Ansolobehere et al., 2007) were obtained from the literature.
Limitations of the methodology
There are certain limitations in our challenge stream assessment methodology. For example, if the true opportunity to address a separation challenge is an extensive process reconfiguration, beyond the separation step, it may not be captured well. Furthermore, energy impacts are shown only as carbon intensity associated with the process energy. A more comprehensive greenhouse gas impact would include life-cycle elements on raw materials, products, etc. These elements could be built into the assessment methodology or included as part of a specific assessment associated with an actual candidate separation technology. Reductions in cost and carbon intensity obtained from the methodology only represent an ideal case and are not justified for any specific separation technology.
Energy and capital costs are not completely isolated from one another, so the best-scenario analysis may overestimate the results of economic evaluation (Briggs, 1999). Finally, the application of some reasonable probability assumptions for model inputs could reduce the uncertainty in the predictions (Li et al., 2021).
Even with the above limitations, the methodology here stands to provide key insight into the maximum potential economic impact for identified separation challenge streams.
Challenge streams examples in bioprocessing
The assessment methodology described above was next applied to a subset of bioprocessing challenge streams to better illustrate the efficacy of the approach. Here, two sets of bioprocessing conversion pathways were assessed: (1) hydrothermal liquefaction (HTL) of both wet wastes and algae and (2) biochemical conversion of biomass using the biological (fermentative) conversion of hydrolysate sugars to an intermediate fuel precursor, namely, short-chain carboxylic acid (butyric acid) or 2,3-butanediol intermediates. Note that the second pathway includes alkaline and mechanical refining pretreatment, enzymatic saccharification, and subsequent catalytic upgrading to final fuel products. These two pathway sets are among a number of priority pathways that are the focus of current BETO research and development efforts, each with a leading technology solution or design case (Bioprocessing Separations Consortium., 2017). The design cases encompass the full associated biorefinery, and detailed models of the overall process are well developed and studied by the national laboratories and are regularly updated in State-of-Technology (SOT) reports (Schwab, 2016).
First, candidate challenge streams were identified for the two targeted conversion platform sets through discussions with the associated technology development teams. Next, the technology teams were asked to rank the streams based on their perceived impact on energy/cost savings, with High (H) representing the highest perceived impact and Low (L) having the lowest impact, with Medium (M) falling between H and L impacts. This ranking process was based primarily on expert judgment, which provided insight into challenges that could have the most significant possible impacts on overall processing economics and energy reduction. The resulting set of challenge streams for the two targeted conversion platforms and their associated priority rankings are shown in Table 1. Note that the streams shown do not include downstream upgrading steps.
Table 1 shows 28 challenge streams across the two pathway sets. Of those streams, 15 streams received H impact rankings. A subset of these H-ranked separation challenge streams was subsequently assessed in more detail to quantify the magnitude of their impact on cost and energy consumption as part of the assessment methodology outlined here. The details of those assessments are described in sections “Assessments of separation challenge stream examples—hydrothermal liquefaction” and “Assessments of separation challenge stream examples—low-temperature conversion (fermentation) via BDO and mixed acid intermediates”.
Assessments of separation challenge stream examples—hydrothermal liquefaction
This section describes the assessments for all six of the H-ranked priority HTL challenge streams in Table 1. The process diagram for the wet-waste HTL process and the locations of the separation streams were shown in Figure 3. The models used for these assessments were the existing design case models and cost spreadsheets, which are regularly updated every year (Snowden-Swan et al., 2021). Each of the challenge streams was assessed using the “ideal” separator approach described above. In addition to the capital cost and energy cost of the process, values of co-products (if any) were accounted in the calculation of the minimum fuel selling price (MFSP). The individual assessments are described in the following subsections. A summary of all the HTL assessments is provided in section “Summary of HTL challenge stream assessments”.
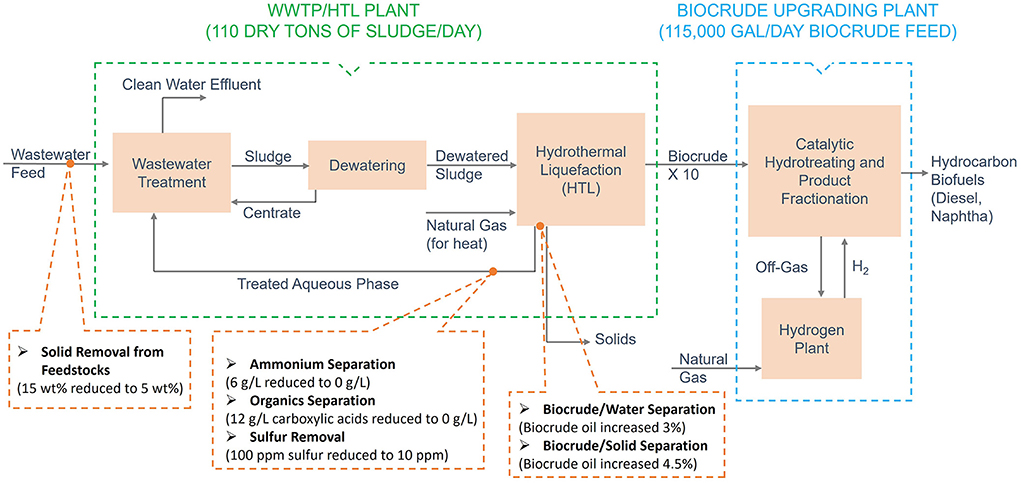
Figure 3. Process diagram for wet-waste HTL, with the locations of the assessed separation challenge streams.
Ammonium separation from the HTL aqueous stream
Aqueous streams from certain wet wastes (e.g., sewage sludge) can have high ammonium () concentrations, which can impede the ability to discharge to the associated wastewater treatment operations. The current approach for these cases is to remove the by first adding calcium hydroxide (lime) to shift the compounds to ammonia (NH3) and then airstrip and treat the resulting gas in a natural-gas-fired thermal oxidation unit (THROX). Each of these process steps represents significant energy and capital expense.
An “ideal” separator for from an HTL aqueous feed stream would need to be highly selective to reduce water recycling and the need for any lime additions, etc. (US Environmental Protection Agency., 2020). For the challenge stream assessment, the “ideal” separator for this stream was represented using the approach described above. Data from the 2020 SOT were used as the baseline case, and the current separation technology (lime addition, sludge recovery, NH3 stripping, and THROX) was replaced with the “ideal” separator (Snowden-Swan et al., 2021). The concentration of (on an NH3 basis) in the aqueous stream for the baseline case is 6 g/L. Based on this concentration, the calculated minimum theoretical separation energy is 18.2 kJ (work)/mol, or 43.3 kJ (heat)/mol of NH3 using the method described in the previous section. While the separated could ideally be a valuable co-product (most likely if it is present as NH3), no such value was accounted for in the estimate because appreciable organics would likely be present in the purified stream.
Techno-economic estimates for the “ideal” separator case are shown in Table 2. Based on these estimates, the HTL biocrude selling price can be reduced from $2.79/gge (gasoline gallon equivalent) to $2.40/gge by using an “ideal” separator to remove . This equates to a maximum possible overall cost reduction of ~14% compared to data in the SOT. The major cost savings are from operating and capital costs associated with the lime addition, pH control, and the THROX unit. As stated earlier, the biocrude selling price could be further decreased if pure NH3 were produced and sold as a co-product, but the likely presence of organics in the stream affects that option (this is addressed in the following case).
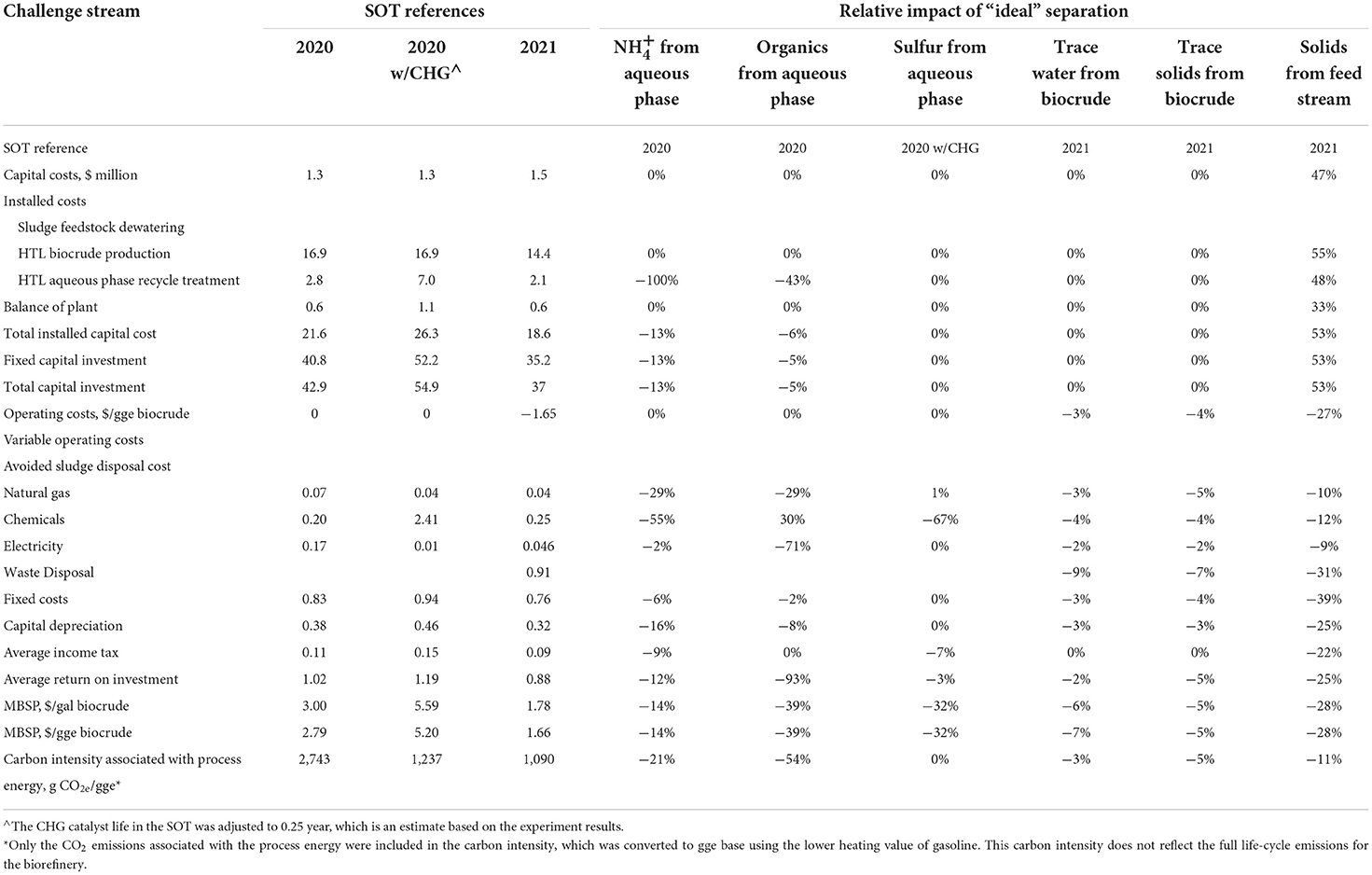
Table 2. Techno-economic estimates for the wet-waste HTL process separation challenge streams using the “ideal” separator approach.
Separation from the HTL aqueous stream
Aqueous streams from HTL reactors often contain dilute organics (1–3 wt%) in the form of carboxylic acids, such as acetic acid and propanoic acid, and can represent up to 25% of the overall carbon balance (Elliott et al., 2015; Maddi et al., 2017). If is removed from the aqueous stream by converting to NH3 and air stripping (as described in the previous section), significant amounts of organics also would be stripped in the process, leading to an impure NH3 stream that then only can be decomposed in the THROX. Further, if organics were removed prior to NH3 stripping, a pure NH3 stream could potentially be generated and sold as a co-product.
However, because of the low concentrations of the individual organic species in a typical HTL aqueous stream, conventional separation technologies are not economically viable, especially with the large amounts of water involved (Sherwood et al., 1975). For the purposes of the challenge stream assessment, data from the 2020 SOT again was used, and “ideal” separation of organics before the NH3 stripper was assumed. The complete removal of organics then was assumed to enable their use as a sellable co-product. Similarly, the pure NH3 recovered also was considered co-product quality because there would be no organic contaminants in that stream. The NH3 separation also eliminated the need for the THROX unit and its associated capital and operating costs.
The assumed concentration of the carboxylic acids (i.e., acetic acid, propanoic acid, and butanoic acid) in the aqueous stream was assumed to be 12 g/L or ~1.2 wt% (Maddi et al., 2017), with the theoretical minimum separation energy estimated to be 18.6 kJ (work)/mol acetic acid.
Techno-economic estimates for the ideal separator case are shown in Table 2. Based on these estimates, the HTL biocrude selling price can be reduced from $2.79/gge to $1.70/gge with an “ideal” organic separator. This equates to an overall cost reduction of ~39%. The major cost savings are from eliminating the THROX thermal oxidizer and recovering acetic acid and NH3 sulfate as co-products.
Sulfur removal from HTL aqueous stream
One current commercial solution for valorizing the organics in HTL aqueous streams is catalytic hydrothermal gasification (CHG) into methane (Elliott et al., 2015; Maddi et al., 2017). However, sulfur (including both inorganic and organic sulfur) present in nominal concentrations of 100 ppm in HTL aqueous streams can poison the ruthenium catalyst used in the CHG process (Anderson et al., 2019). The cost of replacing the CHG catalyst ranges from $0.56–0.63/gge for the biocrude from the wet-waste HTL process (Snowden-Swan et al., 2021). Sulfur concentrations < 10 ppm are needed to allow reasonable lifetimes for CHG catalysts. Guard beds and precipitation methods are potential ways to remove inorganic sulfur and sulfates, but those solutions can be expensive (Elliott and Oyler, 2013; Jones et al., 2014). Adsorption is another possible method for removing organic sulfur, but interference from other salts can be a factor.
Use of an “ideal” separator for sulfur removal was assumed to precede the CHG system, thereby increasing the CHG catalyst life from 4 to 12 months. The improved CHG efficiencies, in turn, enabled a fertilizer co-product stream to be removed. The theoretical minimum separation energy to reduce 100 ppm sulfur (e.g., thiophenol) to 10 ppm in water was estimated to be 25.5 kJ (work)/mol sulfur.
The TEA used data from the 2020 SOT with the CHG option, which represents a potential technology to treat the HTL aqueous stream and has an issue of sulfur positioning of catalyst, as the baseline case. The resulting estimates for the “ideal” separator case are shown in Table 2. Based on these estimates, the HTL biocrude selling price can be reduced from $5.20/gge to $3.53/gge using an “ideal” sulfur separator. This equates to an overall cost reduction of ~32%. The major cost savings are from the lowered catalyst replacement. Note, however, that the absolute biocrude selling price in the baseline for this case is much higher than that obtained in HTL without the CHG option. This means that the projected reductions are artificially high. Indeed, if sulfur removal were applied to the prior case (ideal organic separations), there would be a little overall economic benefit.
Removal of trace HTL biocrude from the aqueous stream
Water removal from the HTL biocrude is currently performed using decantation or centrifugation. These methods result in biocrude losses to the aqueous stream of ~3%. An improved separation technique could boost the biocrude yield and reduce the chemical oxygen demand for wastewater disposal.
The “ideal” separator for the trace biocrude would result in the complete removal of trace biocrude from the aqueous stream and its rerouting to the primary biocrude stream. Data from the 2021 SOT were used as the comparison baseline for the “ideal” separator. The complete removal of trace biocrude was assumed to reduce the chemical oxygen demand in the aqueous stream such that the wastewater discharge fee could be eliminated (Elliott and Oyler, 2013). Note that the 2021 SOT reports a lower minimum biofuel selling price (MBSP) ($1.66/gge of biocrude) than the 2020 SOT. This lower price was driven by a sludge feedstock credit and higher feed solids contents (Snowden-Swan et al., 2022).
Techno-economic estimates for the “ideal” separator case are shown in Table 2. Based on these estimates, the HTL biocrude selling price can be reduced from $1.66/gge to $1.55/gge. This equates to a maximum overall cost reduction of ~7%. The major cost savings are from the additional biocrude recovery and reduced wastewater discharge fee.
Removal of trace solids from the HTL biocrude
Solid residues need to be removed from the bio-crude oil after the HTL reaction. Currently, a filter is used in bench-scale operations, which results in biocrude oil losses from the associated blowdowns. If this biocrude were fully recovered, a 4.5% increase in biocrude oil production would be realized. Further, the contamination of solids in the biocrude oil could lead to additional solid waste disposal fees.
The “ideal” separator for trace solids in HTL biocrude would completely remove oil from the solid waste, thus potentially reducing the solid waste disposal fee. Data from the 2021 SOT were used for the baseline comparison. Here, the recovered biocrude is recycled, thereby increasing the overall biocrude yield by 4.5%. Techno-economic estimates for the “ideal” separator case are shown in Table 2. Based on these estimates, the HTL biocrude selling price can be reduced from $1.66/gge to $1.57/gge. This equates to a maximum overall cost reduction of ~5%. The major cost savings are from the additional biocrude recovery.
Removal of solids from the HTL feedstocks
In the 2021 SOT for wet waste HTL, the ash content in wastewater sludge feedstocks is as high as 15%, with manures having even higher ash contents. Because of solids-handling limitations with HTL, many manure feedstocks cannot be processed practically without significant pretreatment. Indeed, if novel ash-content separation processes were available, many feedstocks could be viable for HTL processing. The quantity of available manure in the United States is ~3 × that of U.S. wastewater sludge (on an energy content basis). Furthermore, 27% of available manure in the United States can be collected at the cost of -$76.35/wet metric ton (including a credit earned to remove manure waste), with a $50/wet metric ton fee to transport the manure within 100 miles (Milbrandt et al., 2018).
The “ideal” solid separator for HTL wet waste feeds would reduce the ash contents to 5% so they could be easily processed. This reduction would enable a broader supply of lower-cost feedstocks (e.g., manures, etc.). Data from the 2021 SOT were used in the baseline case and an “ideal” separator was applied to the feed stream to reduce the ash content. The theoretical minimum separation energy for removing solids is very low and hard to quantify. Therefore, it was assumed to be zero for the current estimates.
Techno-economic estimates for the “ideal” separator case are shown in Table 2. Based on these estimates, the HTL biocrude selling price can be reduced from $1.66/gge to $1.19/gge. This equates to a maximum overall cost reduction of ~28%. The major cost savings are from the ability to process less expensive feedstocks.
Summary of HTL challenge stream assessments
Table 2 shows the “ideal” separator estimates from all of the above HTL separation challenge streams. The predicted reductions in the total cost and overall process energy also are plotted in Figure 4. Here, MBSPs were updated to minimum fuel selling prices (MFSP) with an assumed conversion cost adder of about $1.1/gge. Based on the estimates shown, the “ideal” organic separation from the HTL aqueous stream was determined to represent the largest possible cost savings opportunity (up to 39%). That opportunity was driven by enhancing NH3 recovery, removing the gasification step, and forming sellable co-products. Separation technologies that could potentially capture some of the opportunities identified in the “ideal” separation case include selective adsorption (including ion exchange) and membrane-based separations, but considerable development would be required to make these technologies economically viable.
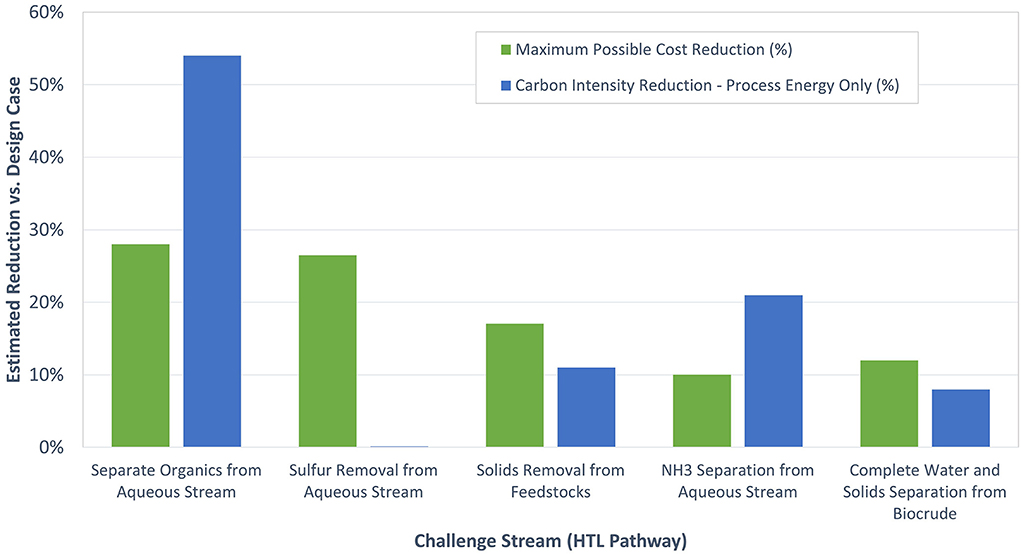
Figure 4. Estimated cost and energy reductions for the HTL separation challenge stream assessments. The cost and CO2 emission reduction for the trace water and trace solid removal from biocrude oil were combined.
The next highest “ideal” separator cost reduction was with the sulfur reduction case. However, the estimates for that case are artificially high because the baseline cost was higher due to the incorporation of commercial organic treatment technology that requires desulfurization. Indeed, this challenge stream would be irrelevant on its own if the organic separations could be achieved in a different way.
The next highest projected “ideal” separator cost reduction (up to 28%) was the stream associated with solids removal from a broader set of less expensive HTL feedstocks, including manures. However, this separation is technically challenging because of the overall nature of these materials. The remaining cases had maximum cost savings projections between 5 and 14%. The highest of these was removal at 14%, which was driven by the possibility of treatment cost compared to the baseline.
Table 2 and Figure 4 also show the corresponding carbon intensity reductions associated with “ideal” separations. A 54% reduction in process energy on a carbon intensity basis was predicted for recovering organics from the HTL aqueous stream. In the case of removal from the aqueous stream, about a 21% reduction in the process energy on a carbon intensity basis was estimated compared to the baseline. Reductions of carbon intensity in other cases were predicted to be small (i.e., < 5%).
Assessments of separation challenge stream examples—low-temperature conversion (fermentation) via BDO and mixed acid intermediates
This section describes assessments for four of the H-ranked, low-temperature conversion (fermentation) challenge streams shown in Table 1. Here again, the models used for these assessments were from the existing design case models and cost spreadsheets. Each challenge stream was assessed using the “ideal” separator approach. In addition to the capital cost and energy cost of the process, values of co-products (if any) were accounted in the calculation of the minimum fuel selling price (MFSP). The process diagram for the biochemical process through the 2,3-butanediol and acids pathways and the locations of the separation streams are shown in Figure 5. Similarly, the process diagram and the location of the separation stream for the sugar production are shown in Figure 6. The individual assessments are described in the following subsections and a summary of all the individual assessments is provided in section “Summary of biochemical challenge stream assessments.”
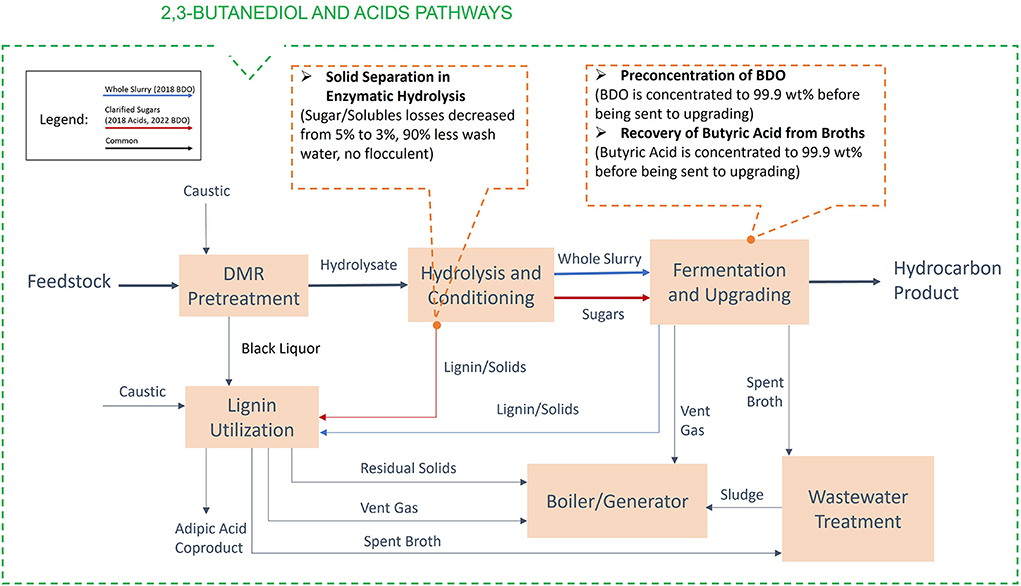
Figure 5. Process diagram for the biochemical process through the 2,3-butanediol and acids pathways, with the locations of the assessed separation challenge streams.
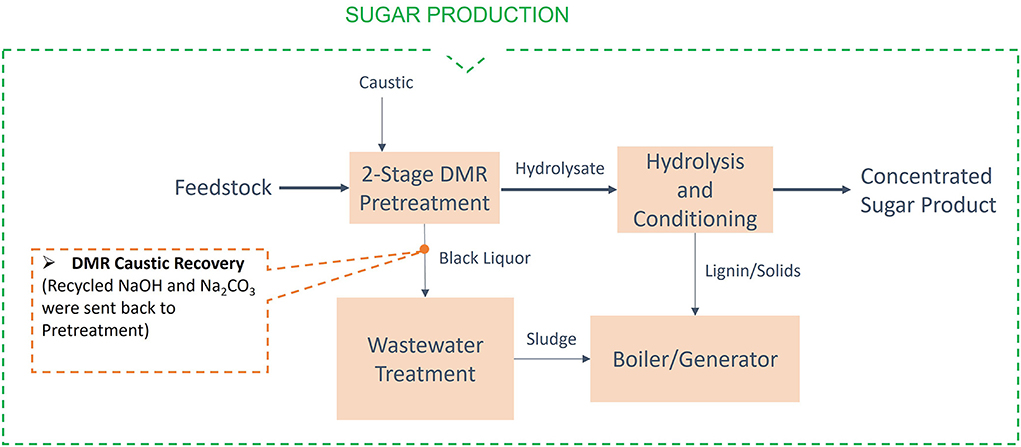
Figure 6. Process diagram for the sugar production with the locations of the separation challenge streams.
Recovery/recycling of caustic (NaOH or other) required in deacetylation
Representing a wide range of bioprocesses, a concentrated sugar production model was chosen to analyze a two-stage deacetylation and mechanical refining (DMR) pretreatment process developed by NREL. For processes that use DMR pretreatment sodium carbonate (Na2CO3) is added to help offset the use of NaOH (for deacetylation) by neutralizing acidic components released from biomass that would otherwise require more sodium hydroxide caustic (Chen et al., 2021). A 20% excess of both NaOH and Na2CO3 is assumed in this case to ensure a complete reaction. This means that unreacted caustic must be neutralized using sulfuric acid in the wastewater treatment process. An “ideal” separator for this process would fully recover and recycle the excess caustic, which is not realistic today. For the separation challenge stream assessment, an “ideal separator” was specifically inserted between DMR pretreatment and wastewater treatment unit operations to separate the residual caustic from the black liquor. In the black liquor stream, excess NaOH makes up ~0.32 wt% of the stream flow, while Na2CO3 makes up ~0.89 wt%. As with the other challenge stream cases, the capital cost of the separation process was assumed to be zero, and the separation energy was assumed to be 2 × the theoretical minimum. The neutralization equipment was left in place to control the pH of wastewater by taking care of any residual caustic or chemicals from other streams.
Techno-economic estimates for the “ideal” separator case are shown in Table 3. The cost basis for the design case comparison was assumed to be the minimum sugar selling price (MSSP). Here, the baseline case has an MSSP of $0.23 per pound. The “ideal” separator case, with fully recovered caustic, has an estimated MSSP of $0.22/lb, or a 3.5% improvement. Contributions from NaOH and Na2CO3 recovery are around 45 and 55% of the cost decrease, respectively. The major contributors to the predicted decrease are less purchased caustic and sulfuric acid and a reduction in wastewater treatment capital. Furthermore, the estimated carbon intensity process energy was 4% lower than the baseline case.
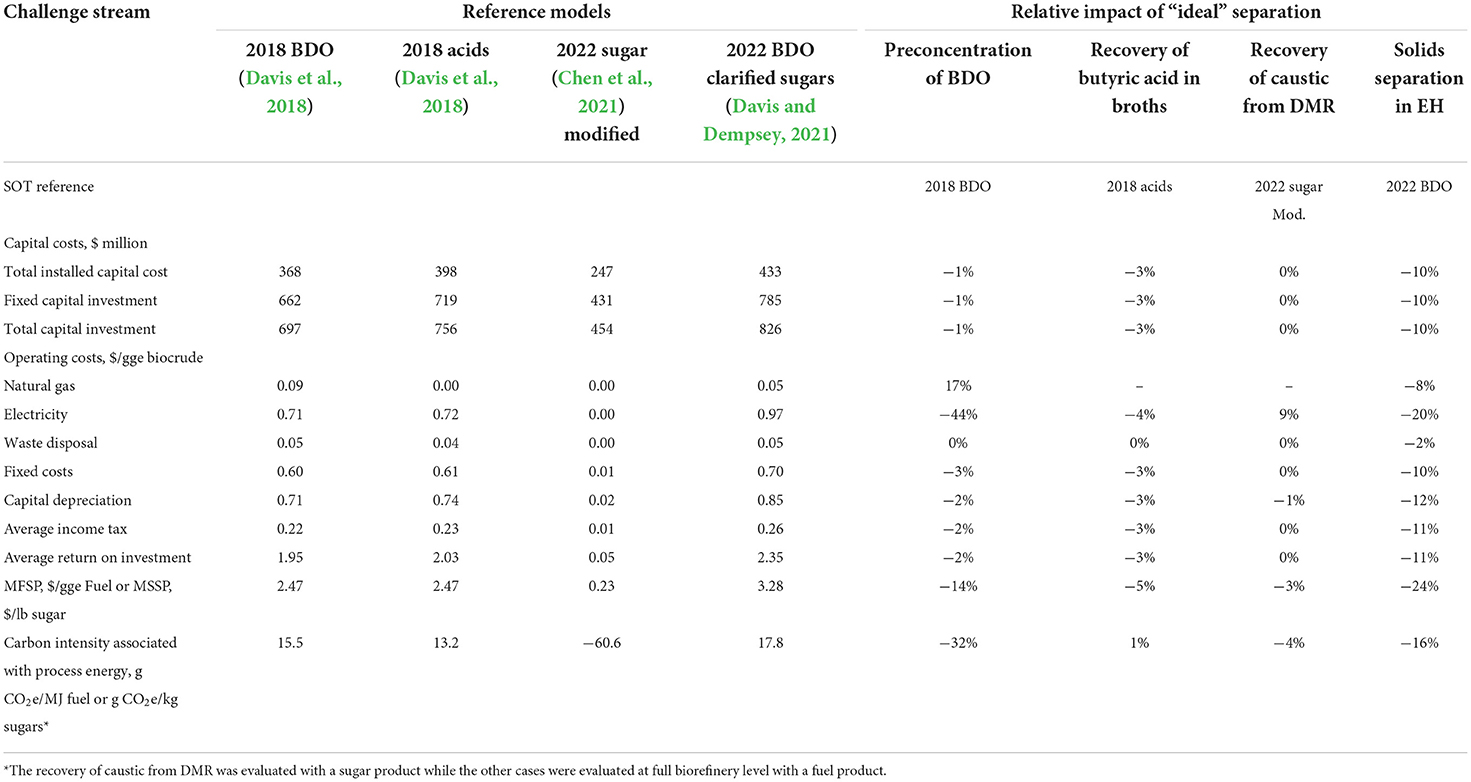
Table 3. Techno-economic estimates for the biochemical separation challenge streams using the “ideal” separator approach.
Recovery or concentration of highly water-soluble alcohols or diols in broths
2,3-Butanediol (BDO) is a common product target for a number of fermentation-based biochemical processes. However, BDO is produced only at low concentrations (~10 wt%) in the fermentation broths (Davis et al., 2018). A leading option is to directly convert BDO to butenes, which then can be more easily separated (Davis et al., 2018). However, if preconcentration of BDO were economically feasible, it could lower the cost of the associated catalytic upgrading systems via smaller reactors and lower energy. Here, an “ideal” separator would be implemented immediately following fermentation. The separator would remove water without vaporizing it, thereby concentrating the BDO to as high as 99.9%.
The core assumptions for the “ideal” separator were the same as with other cases. Techno-economic estimates are shown in Table 3. Because benefits could be realized with preconcentration to levels lower than 99.9%, scenarios were evaluated down to 25% preconcentration. Nevertheless, we determined that the maximum possible improvement was indeed represented at a BDO preconcentration of 99.9 wt%. This case yielded an MFSP of $2.11/gge, which was a ~14% improvement over the design case value of $2.47/gge. The lower cost drivers were the capital cost of downstream equipment (including the distillation column) and decreased electricity consumption. The overall process energy reduction led to a ~32% reduction in carbon intensity.
Recovery of short-chain carboxylic acids from broths
In the 2018 Butyric Acid Design Case (Davis et al., 2018), butyric acid is separated from the fermentation broth via an extractive membrane (pertraction) system using an organic solvent (e.g., trioctylphosphine oxide), followed by distillation to separate the organic acid product and recover the solvent. Here, the butyric acid is concentrated to 99.9 wt% before it is sent to the ketonization reactor. The core assumptions for the “ideal” separator were the same as with other cases.
Techno-economic estimates for the “ideal” separator case are shown in Table 3. The MFSP for the “ideal separator” case was determined to be $2.35/gge, which is a ~5% improvement over the 2018 design case reference of $2.47/gge. The lower associated process energy (i.e., 4% lower electricity demand; see Table 3) is equivalent to a 1% lower carbon intensity. Despite the significant capital cost savings with the “ideal” separator, the relative impact against the design case was less than a 5% reduction in MFSP and less than a 1% reduction for the process energy carbon intensity. This result suggests that the separation technologies used in the current design case are relatively optimized from a cost and energy standpoint. Note that the current design case basis for that operation also may err on the optimistic side, and further room exists to refine the details around cost and energy usage for that step moving forward, which may indicate a further opportunity for improvement relative to the current basis.
Separation of solids following enzymatic hydrolysis
Another high-priority challenge stream for biochemical processing involves the sugar losses from post-enzymatic hydrolysis (EH) and purification. In one of the current NREL BDO models, a vacuum filter press is used to separate solids from the post-EH stream (Davis and Dempsey, 2021). The recovered solids are then washed and sent, with 5% residual sugars/solubles, to the lignin upgrading train, where an adipic acid co-product is made. The loss of sugar/solubles to the co-product negatively affects the overall economics of the process. Increases in wash water flow rates could help overall adipic acid efficiency but would further dilute the main product stream from the EH unit.
An “ideal” separator would reduce the soluble/sugar losses from post-enzymatic hydrolysis from 5 to 1%, significantly decreasing wash-water usage and reducing or eliminating flocculent usage. Because there was recognition that an optimum loss may exist between 5 and 1%, additional intermediate cases were run.
Techno-economic estimates for the “ideal” separator case are shown in Table 3. The case shown represents a sugar/solubles loss of 3.3% (vs. 5%). Although the lower losses (i.e., 1%) were expected to represent the cost optimum, the ratio of adipic acid co-product production to fuel yield appeared to reach a tipping point. The predicted MFSP for the “ideal” separator case was $2.51/gge, which is a ~24% improvement over the design case value of $3.28/gge. Two significant contributors to the overall cost reduction were a 95% reduction in wash-water usage (a small amount is still required) and zero flocculent usage. These two factors equated to 8% and 6% decrease in overall costs for water and flocculent usages, respectively. Other significant drivers included lower electricity requirements from the wash water, reduced capital for solids separation, and higher fuel product flow rate as a result of improved sugar recovery. The “ideal” separator case also resulted in a predicted process energy reduction, as reflected in the ~16% improvement in the associated carbon intensity. Note that the MFSP of $3.28/gge from the current model is higher than $2.47/gge in the design case (Davis et al., 2018) as the result of the replacement of the lignin press with a vacuum filter and sugars in the form of “clarifier sugars” as opposed to the “whole slurry.”
Summary of biochemical challenge stream assessments
Table 3 shows the “ideal” separator economic and energy estimates from the above biochemical separation challenge streams. The predicted reductions in the total cost and overall process energy also are plotted in Figure 7. As seen from the figure, the challenge stream that yielded the largest predicted economic improvement was on the “Separation of solids from Deacetylation Mechanical Refining,” with a ~24% maximum predicted savings opportunity. This cost reduction was driven by lower associated wash-water and flocculent usage, as well as enhanced sugar recovery leading to higher product yields. The process energy carbon intensity for the “ideal” separator on this stream was predicted to be ~16% lower.
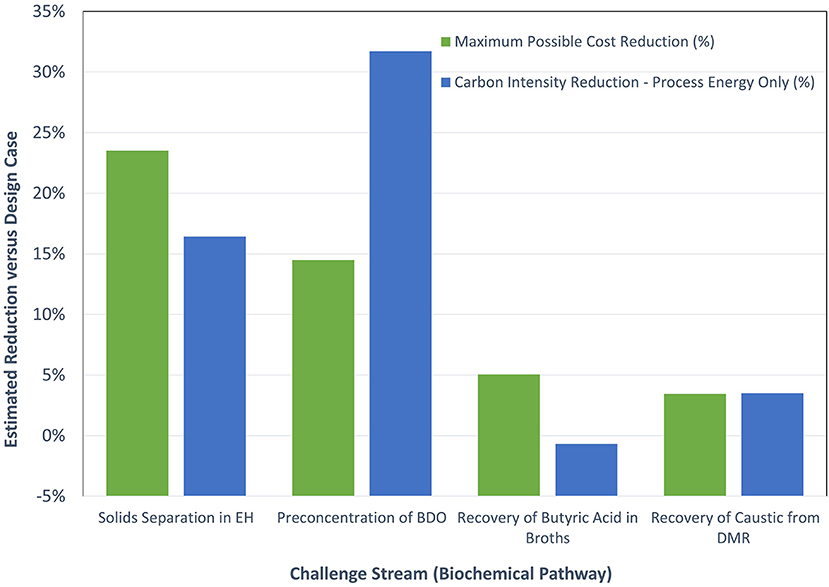
Figure 7. Estimated cost and process energy reductions for the biochemical separation challenge stream assessments.
The next largest predicted cost savings in Table 3 was the challenge stream associated with preconcentrating BDO. Here, the maximum economic impact was estimated to be 14% on an MFSP basis. The main contributors to this projected improvement were the decreased capital costs and lower electricity usage realized by preconcentration. A ~32% reduction in process energy on a carbon intensity basis also was predicted.
The two other challenge stream cases, “Recovery/recycling of caustic (NaOH or other) required in deacetylation” and “Recovery of butyric acid from broths,” each predicted costs savings of <5% and associated predicted process energy carbon intensity reduction <4%. For the challenged stream associated with butyric acid recovery, the lower opportunity in cost and energy savings is largely due to prior technology investments in that separation, which indicate a nearly optimized solution in the design case.
Conclusions
Our objective for the study presented here was to demonstrate how separation challenges in bioprocessing and other industries can be assessed in a way that helps understand the maximum possible opportunities for separation solutions from economic and energy standpoints. The approach uses baseline techno-economic models and applies “ideal” separators for identified separations challenges. The “ideal” separators represent the most optimistic outlook for potential technologies (e.g., 2 × theoretical separation energies, no associated capital cost, etc.) so the maximum possible impact from existing and not-yet-developed solutions could be assessed.
Example assessments were shown for ten different high-priority separation challenges streams to convey the type of information that can be gleaned. These examples were based on conversion pathways currently under development by BETO, each with established biorefinery design case models. Three of the ten challenge streams assessed had maximum possible cost savings predictions that were >20%, and associated reductions in process energy carbon intensity ranging from 0 to 54%. Two of the challenge streams had predicted impacts of < 5% for both maximum possible cost savings and process energy carbon intensity. For a number of the assessments, critical opportunity areas were found in which gains were identified, including reductions or eliminations of downstream equipment, new co-products, raw material savings, and certainly energy savings. These factors can help guide the selection of potential separation technology solutions that capitalize on the identified gains. In some cases, entirely new technologies may be deemed necessary to capture the largest amount of the identified opportunity. Here, the assessment information can potentially justify and guide the associated technology development.
Data availability statement
The calculated minimum theoretical separation energies for all the cases in the study are included in the article/Supplementary material, further inquiries can be directed to the corresponding author/s.
Author contributions
CF provided the conceptual framework. JL and CF designed and conducted the HTL challenge stream assessments. JD and ET designed and conducted the biochemical separation challenge streams. WK provided some input toward the separation challenge stream survey. LS-S, SL, and YJ provided baseline HTL models and inputs toward assessment. All authors contributed to the article and approved the submitted version.
Funding
This work was sponsored by the Department of Energy (DOE), BETO, Bioprocessing Separations Consortium program. Funding was provided by the DOE Office of Energy Efficiency and Renewable Energy.
Acknowledgments
The authors would like to thank the support from the DOE BETO and their support to the Separations Consortium. This work was authored in part by Alliance for Sustainable Energy, LLC, the manager and operator of the National Renewable Energy Laboratory (NREL) for DOE under Contract No. DE-AC36-08GO28308. Pacific Northwest National Laboratory is operated for the U.S. Department of Energy by Battelle Memorial Institute under Contract DE-AC05-76RL01830. The authors would also like to acknowledge support provided by DOE BETO and their support to the Separations Consortium. JD and ET thank Ryan Davis (NREL) for providing helpful insights into the biochemical separation streams.
Conflict of interest
The authors declare that the research was conducted in the absence of any commercial or financial relationships that could be construed as a potential conflict of interest.
Publisher's note
All claims expressed in this article are solely those of the authors and do not necessarily represent those of their affiliated organizations, or those of the publisher, the editors and the reviewers. Any product that may be evaluated in this article, or claim that may be made by its manufacturer, is not guaranteed or endorsed by the publisher.
Author disclaimer
The views expressed in the article do not necessarily represent the views of the DOE or the U.S. Government. The U.S. Government retains and the publisher, by accepting the article for publication, acknowledges that the U.S. Government retains a nonexclusive, paid-up, irrevocable, worldwide license to publish or reproduce the published form of this work or allow others to do so, for U.S. Government purposes.
Supplementary material
The Supplementary Material for this article can be found online at: https://www.frontiersin.org/articles/10.3389/frsus.2022.1056580/full#supplementary-material
References
Abou Rayan, M., and Khaled, I. (2003). Seawater desalination by reverse osmosis (case study). Desalination 153, 245–251. doi: 10.1016/S0011-9164(02)01143-8
Anderson, D., Schmidt, A., Hallen, R., Billing, J., Hart, T., Olarte, M., et al. (2019). “PNNL hydrothermal processing of biomass,” in Paper Presented at: DOE Bioenergy Technologies Office (BETO) 2019 Project Peer Review 2.2.2.301. Denver, CO.
Ansolobehere, S., Beer, J., Deutch, J., Ellerman, A. D., Friedman, J., Herzog, H., et al. (2007). MIT Interdisciplinary Study Report. Cambridge, MA: Massachusetts Institute of Technology.
Bioprocessing Separations Consortium. (2017). Available online at: https://bioesep.org/ (accessed September 10, 2022).
Briggs, A. (1999). Economics notes - handling uncertainty in economic evaluation. Br. Med. J. 319, 120. doi: 10.1136/bmj.319.7202.120
Chen, X., Davis, R., Tan, E., and Dempsey, J. (2021). Achieve at Least 90% Fermentable Monomeric Sugar Yields at an Enzyme Loading of 10 mg/g Cellulose (or less) with Cost-effective Chemical and Mechanical DMR Process Options. Internal NREL milestone report. Boulder, CO: National Renewable Energy Laboratory (US).
Davis, R., and Dempsey, J. (2021). TEA Screening for Optimal BDO Fermentation Approaches. Internal NREL milestone report. Boulder, CO: National Renewable Energy Laboratory (US).
Davis, R. E., Grundl, N. J., Tao, L., Biddy, M. J., Tan, E. C., Beckham, G. T., et al. (2018). Process Design and Economics for the Conversion of Lignocellulosic Biomass to Hydrocarbon Fuels and Coproducts: 2018 Biochemical Design Case Update; Biochemical Deconstruction and Conversion of Biomass to Fuels and Products via Integrated Biorefinery Pathways. Boulder, CO: National Renewable Energy Laboratory (US). doi: 10.2172/1483234
Elliott, D. C., Biller, P., Ross, A. B., Schmidt, A. J., and Jones, S. B. (2015). Hydrothermal liquefaction of biomass: developments from batch to continuous process. Bioresour. Technol. 178, 147–156. doi: 10.1016/j.biortech.2014.09.132
Elliott, D. C., and Oyler, J. R. (2013). Methods for Sulfate Removal in Liquid-phase Catalytic Hydrothermal Gasification of Biomass. US Patent No 8, 877.098 B2. Washington, DC: U.S. Patent and Trademark Office.
House, K. Z., Baclig, A. C., Ranjan, M., van Nierop, E. A., Wilcox, J., Herzog, H. J., et al. (2011). Economic and energetic analysis of capturing CO2 from ambient air. Proc. Natl. Acad. Sci. U. S. A. 108, 20428–20433. doi: 10.1073/pnas.1012253108
Jones, S., Zhu, Y., Anderson, D., Hallen, R., Elliott, D., Schmidt, A., et al. (2014). Process Design and Economics for the Conversion of Algal Biomass to Hydrocarbons: Whole Algae Hydrothermal Liquefaction and Upgrading. Richland (WA): Pacific Northwest National Laboratory (US). PNNL-23227. doi: 10.2172/1126336
Leeper, S. (1992). “Membrane separations in the recovery of biofuels and biochemicals: an update review,” in Separation and Purification Technology, ed N Li (Boca Raton, FL, CRC Press), 99–194.
Li, S. Y., Jiang, Y., Snowden-Swan, L. J., Askander, J. A., Schmidt, A. J., Billing, J. M., et al. (2021). Techno-economic uncertainty analysis of wet waste-to-biocrude via hydrothermal liquefaction. Appl. Energy 283, 116340. doi: 10.1016/j.apenergy.2020.116340
Maddi, B., Panisko, E., Wietsma, T., Lemmon, T., Swita, M., Albrecht, K., et al. (2017). Quantitative characterization of aqueous byproducts from hydrothermal liquefaction of municipal wastes, food industry wastes, and biomass grown on waste. ACS Sustain. Chem. Eng. 5, 2205–2214. doi: 10.1021/acssuschemeng.6b02367
Milbrandt, A., Seiple, T., Heimiller, D., Skaggs, R., and Coleman, A. (2018). Wet waste-to-energy resources in the United States. Richland, WA: Pacific Northwest National Laboratory (US). doi: 10.1016/j.resconrec.2018.05.023
Oak Ridge National Laborator. (2005). Materials for Separation Technologies: Energy and Emission Reduction Opportunities. Oak Ridge, TN.
Schwab, A. (2016). Bioenergy Technologies Office Multi-Year Program Plan. 2016. Washington, DC: United States. doi: 10.2172/1245338
Sherwood, T. K., Pigford, R. L., and Wilke, C. R. (1975). Mass Transfer Operations. New York, NY: McGraw-Hill.
Singh, D., Croiset, E., Douglas, P. L., and Douglas, M. A. (2003). Techno-economic study of CO2 capture from an existing coal-fired power plant: MEA scrubbing vs. O2/CO2 recycle combustion. Energy Convers. Manage. 44, 3073–3091. doi: 10.1016/S0196-8904(03)00040-2
Snowden-Swan, L. J., Billing, J., Thorson, M. R., Schmidt, A. J., Jiang, Y., Santosa, D. M., et al. (2021). Wet Waste Hydrothermal Liquefaction and Biocrude Upgrading to Hydrocarbon Fuels: 2020 State of Technology. Richland, WA: Pacific Northwest National Lab. (PNNL). doi: 10.2172/1771363
Snowden-Swan, L. J., Li, S., Jiang, Y., Thorson, M. R., Schimdt, A. J., Seiple, T. E., et al. (2022). Wet Waste Hydrothermal Liquefaction and Biocrude Upgrading to Hydrocarbon Fuels: 2021 State of Technology. Richland, WA: Pacific Northwest National Laboratory (US). doi: 10.2172/1863608
Tsiropoulos, I., Siskos, P., De Vita, A., Tasios, N., and Capros, P. (2022). Assessing the implications of bioenergy deployment in the EU in deep decarbonization and climate-neutrality context: a scenario-based analysis. Biofuel. Bioprod. Biorefin. 16, 1196–1213. doi: 10.1002/bbb.2366
US Environmental Protection Agency. (2020). Wastewater Technology Fact Sheet Ammonia Stripping. EPA 832-F-00-019. Washington, DC.
Keywords: bioenergy, separation, methodology, biomass conversion, techno-economic analysis
Citation: Liu J, Dempsey JW, Li S, Jiang Y, Snowden-Swan LJ, Kubic WL, Tan ECD and Freeman CJ (2022) Methodology for assessing the maximum potential impact of separations opportunities in industrial processes. Front. Sustain. 3:1056580. doi: 10.3389/frsus.2022.1056580
Received: 29 September 2022; Accepted: 31 October 2022;
Published: 23 November 2022.
Edited by:
Bing Shen How, Swinburne University of Technology Sarawak Campus, MalaysiaReviewed by:
Jaya Prasanth Rajakal, Swinburne University of Technology Sarawak Campus, MalaysiaJiuan Jing Chew, Swinburne University of Technology Sarawak Campus, Malaysia
Copyright © 2022 Liu, Dempsey, Li, Jiang, Snowden-Swan, Kubic, Tan and Freeman. This is an open-access article distributed under the terms of the Creative Commons Attribution License (CC BY). The use, distribution or reproduction in other forums is permitted, provided the original author(s) and the copyright owner(s) are credited and that the original publication in this journal is cited, in accordance with accepted academic practice. No use, distribution or reproduction is permitted which does not comply with these terms.
*Correspondence: Jian Liu, amlhbi5saXVAcG5ubC5nb3Y=; Eric C. D. Tan, ZXJpYy50YW5AbnJlbC5nb3Y=; Charles J. Freeman, Y2hhcmxlcy5mcmVlbWFuQHBubmwuZ292