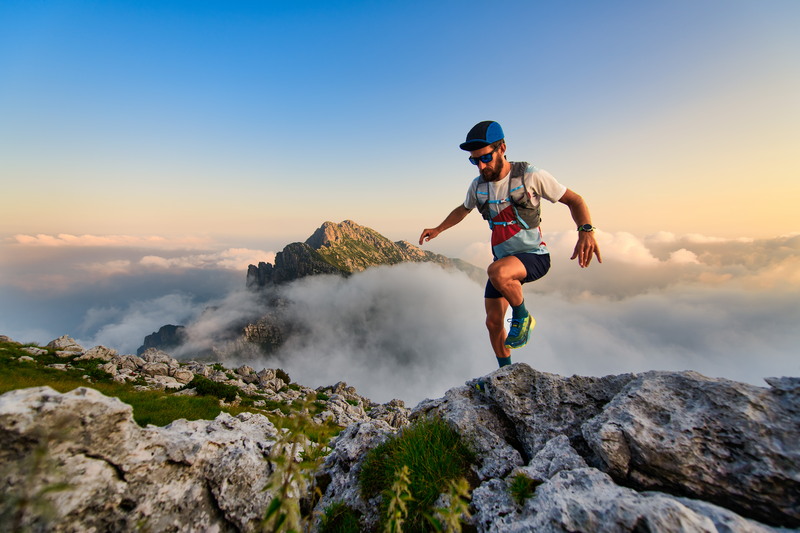
95% of researchers rate our articles as excellent or good
Learn more about the work of our research integrity team to safeguard the quality of each article we publish.
Find out more
POLICY AND PRACTICE REVIEWS article
Front. Sustain. , 30 November 2022
Sec. Circular Economy
Volume 3 - 2022 | https://doi.org/10.3389/frsus.2022.1038323
This article is part of the Research Topic Sustainability Assessment of Chemicals in Consumer Products View all 5 articles
The production and consumption of textile products traditionally follows a largely linear (take, make, use, discard) economic model. Textiles are currently being produced in greater volumes than ever before, even after accounting for population growth, and unwanted products are discarded in mass quantities, most of which ends up in landfills or incinerated. This model causes serious social and environmental impacts and, thus, a transition to a more circular economic model – where materials and products are kept within the economy through reuse, repair, and recycling – is necessary. However, many challenges face a circular economy (CE) for textiles. Herein we discuss challenges and opportunities with the current textiles recovery system in the United States and outline activities and resources necessary to facilitate the transition to a CE in the U.S. Specifically, we describe the overarching need for collaboration, system harmonization, and data and information exchange. We further outline necessary actions in terms of standards development, labeling advancements, design characteristics, alternative business models for brands and retailers, end market development for recyclers, community engagement and educational programs, research and development, and the role of policy and regulation.
The traditional life of textile products has followed a largely linear path, where raw materials are extracted/harvested, manufactured, distributed, used, and then disposed, typically in either landfills or incinerators. Interest and momentum are growing for a transition to a circular economy (CE) to keep products and materials cycling within the economy and out of unwanted sinks (e.g., land, air, and water systems) (Ellen MacArthur Foundation, 2017; Piribauer and Bartl, 2019; Oregon State Legislature, 2021; European Commission, 2022). Unlike the linear economy, a circular economy aims to eliminate waste entirely by designing products that are durable, reusable, and repairable using materials that can be recovered and recycled at end-of-life (EoL) (NIST, 2022). As a result, public and private organizations at the national and global scale are urging increased circularity to address climate change, conserve limited natural resources, reduce pollution, and lessen supply chain disruptions (e.g., Ellen MacArthur Foundation, 2017; European Commission, 2018, 2022; United Nations, 2022).
The textiles' manufacturing industry is global and fragmented, and while collection for resale (e.g., thrift stores, donation bins) is practiced to some extent in the U.S., the majority of EoL textile products are discarded in landfills and burnt in incinerators (Adler, 2020; SMART, 2022). This represents a significant loss of material and economic value and causes acute social and environmental impacts. Progress is being made in the transition to a CE for textiles, but many challenges persist. Recent academic research has applied multi-modal methods to assess and prioritize challenges facing the circular textiles industry in Taiwan (Huang et al., 2021). Others have established a conceptual framework to tackle barriers to CE supply chains for textiles in select economies (Kazancoglu et al., 2020). Several other recent review articles (Jia et al., 2020; Bressanelli et al., 2022a) have applied thorough literature analysis, expert surveys, and convened panels of experts in an effort to identify the greatest challenges impacting circularity in the textiles industry, some at a regional level, and some more broadly.
The U.S. National Institute of Standards and Technology (NIST) has recently undertaken a research effort to identify the technical and economic barriers inhibiting a CE for textiles in the U.S., and methods of addressing those barriers domestically. The focus of this effort included extending beyond the literature to directly engage with stakeholders in the industry to identify these needs and potential next steps to address them. This paper begins with a background on textiles, their production and waste generation, and the social and environmental impacts associated with the current industry. We then discuss challenges and opportunities with the current recovery system, diving into the various practices (e.g., collection, sorting, grading, repair, and recycling) associated with textiles circularity as well as overarching aspects that influence circularity, for better or worse (e.g., economics and the direct relationship between plastics and textiles). NIST conducted a workshop to engage with this stakeholder community and better understand their needs (Schumacher and Forster, 2022). To the authors' knowledge this manuscript is the first comprehensive publication to evaluate the circularity of the textiles system in the U.S. based on insight from experts in the field to identify concrete steps that may facilitate a circular economy for textiles.
Textiles are a broad category of flexible materials made through spinning raw fibers into long and twisted lengths that are interlocked into bundles of yarns or threads and then woven, knitted, matted, or otherwise bound together into fabrics (The Textile Museum, 2021). Fibers generally are categorized by their chemical origin, falling into two classifications: natural and manmade/manufactured/synthetic (Figure 1). Textiles can be comprised of single fiber types or a blend of two or more fiber types depending on the desired product characteristics (stretch, stain and/or water resistance, durability, expense, etc.). Many products utilize textiles, and several (e.g., mattresses) have developed individual supply chains and management programs at EoL. For this reason, textiles herein refers to those used in clothing and apparel, outdoor equipment (e.g., tents), home and hospitality (e.g., towels, linens, etc.), upholstery fabrics, stuffed toys, and post-industrial textiles such as manufacturer clippings, overstock, deadstock, off-spec, and returns.
Figure 1. Classification by fiber type [as defined in Morton and Hearle (2001); Code of Federal Regulations (2022)].
Textile production has increased dramatically over the last two decades, reaching nearly 100 million metric tons (Mt) produced in 2020, nearly double that produced in 2000 and quadruple the production of 1970 (Niinimäki et al., 2020). While demand for cotton, wool, and cellulosics has remained fairly constant over the decades, demand for synthetics, especially polyester, has increased tremendously (Textile Exchange, 2021). It is estimated that today 60% of clothing and 70% of household textiles comprise synthetic fibers, and this trend is expected to increase into the future as consumers in emerging economies adopt Western lifestyles and attire (Niinimäki et al., 2020; Mortensen, 2021). Currently, 60% of global fiber produced is destined for the fashion industry, with the remainder used for interiors, industrial textiles, geotextiles, agrotextiles, and hygienic textiles, among other uses (Niinimäki et al., 2020).
The textile manufacturing sector is a complex industry due to its fragmented and heterogeneous nature that is dominated by small and medium enterprises (SMEs) (Hasanbeigi and Price, 2012). In the current linear model (Figure 2), the value chain of textiles is characterized by vertical disintegration and global dispersion of successive processes that span several industries including agriculture (natural fibers) and petrochemicals (synthetic fibers) as well as manufacturing, distribution logistics, and retail (Niinimäki et al., 2020).
Figure 2. Current linear supply chain of textile products with associated natural capital inputs and environmental impacts [adapted from Niinimäki et al. (2020); European Environment Agency (2021)].
Growing production of textiles has aligned with a global shift of textile and garment production from developed to developing countries, which generally have a competitive advantage in manufacturing and labor costs. China now dominates the production market, annually exporting an estimated $109.9 billion worth of textiles and $158.4 billion worth of apparel (Lu, 2021). Other major textile and garment producing countries include India, Turkey, South Korea, Bangladesh, Pakistan, and Vietnam (Bevilacqua et al., 2014; Niinimäki et al., 2020). Currently, more than 90% of apparel sold in the U.S. is imported from other countries (Yao, 2021). This global shift in production has led to increased complexity and reduced transparency of supply chains as each step of the supply chain often occurs in a different geographical region with unique labor, economic, and environmental policies (Niinimäki et al., 2020). The textile and clothing industry is a major contributor to economies around the world and is estimated to be worth over $3 trillion and employs 300 million people, many of them women (Hiller, 2021; UN Alliance for Sustainable Fashion, 2021).
The tremendous growth in textiles production, particularly since the mid-1990s, has been largely driven by the rise of fast fashion. Taxes on imports/exports diminished at that time, and manufacturing moved to countries with lower labor costs and reduced regulatory requirements (Niinimäki, 2021). The term fast fashion describes the mass manufacturing and marketing of low-cost clothing that is quickly transferred from a design concept to retail stores. It is thus “fast” in several ways: (1) rate of production, (2) number of fashion cycles, delivery, consumers' decision to purchase, and (3) rate at which garments are worn and disposed (Crumbie, 2021).
Social media has also been a driver of fast fashion, as higher visibility has increased the rate at which trends cycle. From a business model perspective, fast fashion has been exceptionally successful. However, it has caused negative social impacts on the workforce, and has resulted in a situation where cheap product prices lead to unsustainable consumption behavior and ultimately fuels a culture of consumption and disposal. Additionally, fast fashion products tend to be lower in quality and, therefore, are often not durable or suitable for resale, repair, or repurposing into alternative textile products (e.g., wiping rags) (Niinimäki et al., 2020).
Textile waste sources include clothing and apparel, home and hospitality textiles, contract textiles, uniforms and workwear, and upholstery fabrics as well as manufacturer or retailer overstock, deadstock, off-spec, damages, and returns (Adler, 2021). Distinctions are made between pre-consumer (often referred to as post-industrial) waste, which is generated during the manufacturing process (i.e., before it reaches the consumer), and post-consumer waste, which is generated by the consumer after use (Federal Trade Commission, 2012). The former tends to be the cleanest and easiest stream to identify material compositions, while the latter represents the highest volume stream that includes blends of all fiber types and often contain contaminants (Wang, 2010; Johnson et al., 2020).
The rate of both pre- and post-consumer textile waste generation has increased significantly over the last several decades. Figure 3 presents the percent change since 1960 of post-consumer textile waste generation and total municipal solid waste (MSW) generation, per U.S. EPA data (US EPA, 2020). Textile waste generation increased 868 % during the reported timeframe while total MSW increased 232%. On a per capita basis, textile waste grew 55% between 2000 and 2018, indicating that the increased textile waste generation is not only due to population growth but also increased affluence (Adler, 2021). Each American discarded an average of 47 kg (104 lbs) of textiles in 2018. By comparison, the annual per capita discard rates in Finland and Sweden are 17 kg per capita and 24 kg per capita, respectively (Niinimäki, 2021). In 2018, textiles comprised 5.83% of the total municipal solid waste (MSW) stream generated in the U.S. (roughly 15.5 million metric tons) (US EPA, 2021a). It must be noted, however, that the U.S. EPA does not track or measure the volumes of textiles donated to non-profits or charities for reuse, which potentially comprises a large, unrepresented segment of the total volume of discarded textiles. Additionally, insufficient data exists to confidently measure pre-consumer textile waste generated through different supply chain production stages (e.g., fiber processing, textile production, garment manufacturing). That said, it is estimated that somewhere between 2 to 20% of all textiles produced are discarded as waste during garment production (Magruder, 2022).
Figure 3. Percent change since 1960 of textile waste and total municipal solid waste (MSW) generation in the U.S., based on EPA data (US EPA, 2020; Code of Federal Regulations, 2022).
The current recovery rate for textiles in the U.S. is approximately 15%, while the remaining 85% of discarded clothing and textiles are sent for landfill or incineration (King, 2021; US EPA, 2021b). The volume recovered are collected either through donation to thrift stores and charities or collected through curbside collection programs and retail store takebacks (Figure 4) (Adler, 2020). It is estimated that thrift stores sell approximately 20% of textile donations, while the remainder are sold to sorters-graders who assess and sort the textiles based on quality, condition, and format to be sold to appropriate downstream markets, such as reuse/resale in domestic or international markets, down cycled to rags or stuffing, or sent for disposal (Adler, 2021; King, 2021). Industry experts claim that a significant amount of textiles are not sorted or graded before being exported and sold internationally (Magruder, 2022). Currently, less than 1% of textiles collected go to fiber-to-fiber recycling (Adler, 2021).
Figure 4. Current fate of used textiles in the United States. Question marks indicate flows for which reliable data are unavailable. Shoddy is made from shredded fibers and used for insulation and stuffing. Based on data from Adler (2021), US EPA (2021b), Magruder (2022).
The cost of managing textile waste in the U.S. is significant. In 2020, it was estimated that textile collection and disposal cost Americans over $4 billion based on average disposal fees and collection costs (Adler, 2021). This cost will likely increase as transportation costs rise and available landfill capacity is reduced.
Export of used clothing to low-income regions is a common practice for garments that do not have a market in wealthier nations. The major importing countries are in Africa, Asia, and Central America and the benefits and detriments of importing used textiles are a subject of significant debate (Adler, 2021). Several countries in Eastern Africa have collectively banned the import of used textiles to protect their own domestic textile industries (United Nations, 2018).
The textile industry is rife with negative social and environmental impacts due to the high usage of energy, water, and chemicals; the leakage of pollutants to environmental sinks; and the lack of sound and enforced environmental and social regulations in nations where production and manufacturing currently takes place. Figure 2 displays the resource inputs and resulting emissions along the textiles supply chain. Natural fibers, especially cotton, require large amounts of land, water, and agrochemicals for production. By comparison, synthetic fibers such as polyester and nylon rely heavily on petroleum feedstocks and therefore have high climate change impacts, but have low demand for land and mineral resources, and low toxicity during production. Ultimately, all textile materials have environmental impacts and shifting away from one to another may only serve to shift the environmental burden; therefore, efforts should focus on reducing the impacts of all fiber types.
The textile industry consists of many production and manufacturing facilities that together consume a significant amount of energy (Niinimäki et al., 2020). Many of these facilities are in regions of the world where fossil fuels dominate the energy supply and as a result are a substantial source of greenhouse gas (GHG) emissions. Further, the global distribution of the textiles supply chain requires substantial transportation, which itself is a significant source of carbon emissions (European Environment Agency, 2021). Therefore, reducing GHG emissions associated with textiles production is necessary to address climate change.
Additionally, the textile industry is a major water consumer and source of water pollution. Quantifying the global water consumption used by the industry is challenging, and estimates range from 20 trillion liters (L) to 215 trillion L (World Bank, 2019; Niinimäki et al., 2020; Hiller, 2021; UN Alliance for Sustainable Fashion, 2021). Nearly all phases of the supply chain utilize water in some capacity, and water demand of textiles use, particularly for clothing, is high due to laundering. Furthermore, some areas where fibers and textiles are produced are already facing water stress, which is exemplified by the fact that many of these regions do not have the water purification infrastructure in place to properly treat and recirculate water (Niinimäki et al., 2020; Hiller, 2021). The amount of water used in the textiles industry is expected to increase, which combined with population growth, will further stress water availability.
Chemicals are used or applied in nearly every stage of the textile supply chain. While agrochemicals are used on natural fiber crops, synthetic fiber production is a complex industrial chemical process with many petrochemical inputs. Textile manufacturing processes such as spinning and weaving utilize lubricants, accelerators, and solvents and wet processing of fabrics use chemicals such as bleaches, dyes, water, and stain repellents, among others (Niinimäki et al., 2020). Some of these chemicals can be harmful to the environment, factory workers and local communities, and consumers. For example, per- and polyfluoroalkyl substances (PFAS) are widely used synthetic chemicals that make clothing, carpets, and other products to impart water or stain repellent properties yet are of concern because of their persistence in the environment, solubility in groundwater, and potential adverse health effects (Peaslee et al., 2020; US EPA, 2021c).
Microplastic fibers (MPF), also known as microfibers, are small (less than 5 millimeters in length) plastic threadlike fibers that are increasingly being recognized as a source of environmental pollution. The predominant leakage pathway is expected to be through the laundering of synthetic clothing, where abrasion causes the shedding of MPF to the water effluent. While many modern wastewater treatment plants can effectively capture MPF, they generally do so in the sewage sludge which, in the U.S. and Europe, is then often used on agricultural soils, thus directly releasing the MPF to the environment (Cai et al., 2020). Furthermore, as discussed above, many low-income countries do not have modern wastewater treatment facilities and, thus, untreated wastewater is often directly discharged to waterways (WWAP, 2017). Other sources of MPF leakage are expected to be through textiles production (wastewater effluent from production facilities) as well as the degradation or fragmentation of textiles during use and EoL (i.e., in landfills) (Henry et al., 2019; Lynch, 2021). Discarded fishing nets, which are made of synthetic fibers, are also expected to be a significant source of MPF in the oceans (Lynch, 2021).
While any country producing textiles and textile products experiences negative social impacts, the globalization of the textile and fashion industry has resulted in the uneven distribution of environmental consequences. Low-income countries are largely responsible for producing textiles and clothing and, thus, most exposed to the impacts associated with production. As such, they bear the burden for wealthy countries, who represent the largest share of consumers.
Working conditions and labor rights should also be included in a discussion about the social impacts of the textiles industry. Undeniably, the textiles industry is a major source of employment, particularly for women. However, producing nations often lack occupational health and safety regulations, minimum wage requirements, or child labor restrictions, making labor justice an issue. The collapse of the Rana Plaza building in Dhaka, Bangladesh that housed five garment factories resulted in the death of over 1,100 people. The event has become a symbol of the working conditions of garment manufacturers and spurred movements to improve labor standards, although many still face resistance (Bair et al., 2020).
Transitioning to a CE for textiles has the potential to address many of these impacts and impart social and environmental benefits. Extending the life of products and recycling at EoL reduces the resource demands and emissions and pollution associated with the production of new garments. At present these environmental benefits are difficult to quantify, as they are process and location dependent and necessitate sufficient and reliable data and lifecycle assessments. Additional work is needed to measure these benefits. Textile circularity also has social benefits particularly through the donation of used products to charities for resale. The donation and resale ecosystem provides reliable jobs (often to marginalized populations), supports charities' fundraising efforts and social missions, and enables such organizations to extend the life and value of textiles (Schumacher and Forster, 2022). Additionally, textile repair and recycling industries have the potential to provide many job opportunities domestically and abroad.
This section presents current practices employed, challenges, and opportunities for advancement regarding the collection, sorting-grading, and recycling of textiles, with a primary focus on the U.S. system. Furthermore, the complex market relationship between the plastics and textile industries, particularly with respect to the demand for recycled polyethylene terephthalate (PET), is also discussed.
Current textile collection generally includes thrift stores and charities, drop-off centers, curbside collection programs, donation bins, and retail store takeback programs. However, availability of these programs differs greatly across the U.S. As mentioned previously, only 15% of textile waste is currently recovered in the U.S., with the remainder going to incineration/landfill. This represents a significant need to educate consumers on the value of post-use textile products and available collection alternatives. Further, products not sold through resale are sorted and graded for cascading uses and end markets (such as wiping materials, shoddy, fiber recycling). Specific challenges and opportunities facing textiles collection, sorting, and grading are identified in Table 1.
Table 1. Challenges and opportunities for textiles collection (Schumacher and Forster, 2022).
Widespread access to consistent collection services is essential to support downstream markets for used textiles. Textiles cannot be readily added to existing recycling services due to contamination and because municipal recycling facilities are not typically equipped to separate out textiles. Textiles could potentially be collected separately as part of waste/recycling collection services (e.g., in a separate container), but this comes with increased cost and logistics (Brasch, 2021). It is argued that if the downstream processes and end markets are improved, waste management haulers can readily extend collection services to include textiles but implementing collection programs before end markets are ready for large volumes can be damaging for local programs (Brasch, 2021).
That said, recyclers are hesitant to invest in large-scale infrastructure without major improvements in collection to provide reliable, high-volume feedstock streams. For example, a major recycler will not invest the required $20 million to $25 million to construct a recycling facility without knowing it can collect 34,000 to 45,000 metric tons (75 million to 100 million pounds) of textiles. Increasing collection to warrant this investment requires a combination of brands and retailer takeback programs, charity, for profit, and municipal collection programs as well as legislation to stimulate the investment needed to transition from a linear to circular economy.
Currently, approximately 20% of collected textiles are reused through domestic resale (Figure 4) and some is directly exported and sold internationally (Adler, 2021; Magruder, 2022). Textiles not sent for resale are sorted and graded for alternative uses and markets. This involves the identification and categorization of textiles based on quality, condition, and format for sale in downstream markets (Adler, 2021). While some sorting and grading is done in the U.S. (namely in Texas and California), much of it is done in the United Arab Emirates, India, Pakistan, and Central America where labor costs are lower (King, 2021). However, freight costs for overseas shipping have increased significantly in recent years along with decreased availability of shipping containers. These factors, together with the import bans discussed previously could influence the export of textiles for these practices.
At present, sorting and grading is primarily performed manually, although technologies are increasingly being employed, particularly to aid in fiber identification. Near-infrared (NIR)-spectroscopy is one such technology, which is widely used in automated sorting applications for other segments of the recycling industry, such as PET recycling (Barker, 2021). Challenges ensue, however, as post-consumer textiles increasingly consist of different fiber blends. At present, the margin of error for fiber identification technologies is still too large for many recyclers (namely chemical recyclers) who require very pure feedstock (e.g., 80 to 95% purity) (Schumacher and Forster, 2022). As a result, many identification technologies on the market still require some level of human labor.
A need exists for the development and expansion of high-speed automated sortation systems. This is necessary to reduce the cost of manual labor, especially given the volume of textiles required to support large-scale textile-to-textile recycling as well as rapid fiber identification. Such a system would ideally combine NIR spectroscopy, artificial intelligence, and robotics; the former to identify fiber types and provide percentages of polymer/material compositions, and the latter two to separate the textiles based on desired categories (e.g., fiber composition, color, etc.). Efforts are underway in this regard (Fibersort, 2021) and necessitate the simultaneous expansion in collection of feedstock as well as growth in demand of outputs. Automated sorting systems could be included in domestic textile sorting facilities (e.g., textile material recovery facilities, MRFs) distributed across the country to allow for the development of regional textile recovery hubs and increased waste diversion (Adler, 2021).
Digital identifiers (IDs) such as Quick Response (QR) codes or Radio Frequency Identification (RFID) tags on textile products have the potential to increase the speed and efficiency of textile sorting. Rapid attribute identification such as fiber composition, chemical additives, etc., would greatly enhance the sorting-grading process. This topic is discussed in further detail in the Section Labeling.
Reuse of used textile products is the highest value approach when compared to alternative pathways (e.g., repurposing or recycling) and offers the lowest impact from an environmental standpoint (King, 2021). However, several challenges currently face reuse and repair industries, which are outlined in Table 2.
Table 2. Challenges and opportunities for textiles reuse and repair (Schumacher and Forster, 2022).
As previously mentioned, 85% of post-consumer textiles are currently discarded in the municipal waste stream, eliminating the potential for circularity. This signifies a lack of consumer knowledge about the continued value and reuse capabilities. Furthermore, today's consumers lack the ability, interest, or time to repair broken or damaged products and choose to discard and buy new rather than seek repair support.
The repair sector is integral to the circularity of textiles, forming partnerships and collaborations may take additional effort. Furthermore, large-scale, franchised garment repair is not economical in the current system due to increasing transportation costs, time consuming processes, decreasing quality of clothing due to Fast Fashion trends, and the relatively low cost of new garments. Efforts must be made to educate consumers on the value and pathways for used products, as well as build industry acceptance for reused and repaired garments (e.g., brand takeback and resell programs). Some brands have recently launched a repair service for consumers to send in damaged garments for repair and have reported significant consumer participation with this model (Feitelberg, 2018).
Recycling is the next approach to retain value in textile products after reuse and repair. In general, textile recycling involves reprocessing post-industrial or post-consumer textiles into new products, but several classifications of textile recycling routes exist that require defining. The term recycling refers to the conversion of textile waste into something approximating the same value (e.g., recovery of fibers back into fibers), but is often also used as the catch-all for all forms of recovery pathways. Upcycling refers to turning discarded textile material into something of higher value (e.g., making new garments or products with materials from waste textiles). Downcycling is the turning of waste textile material into something of lower value such as rags. In closed-loop recycling, the material from a product is recycled and used in a similar or identical product, whereas in open-loop recycling material from a product is recycled and used in different products (often referred to as cascade recycling).
Textile recycling generally includes mechanical and/or chemical processes that turn textile fabrics back into their fiber components to then be remanufactured into fabrics. Mechanical recycling processes generally include shredding waste textiles into small fractions, carding to release the fibers, bleaching, and then re-spinning those fibers into new yarns. This process is best suited for mono-fiber materials (e.g., acrylic, pure cotton, and wool) due to their fiber yield. That said, mechanical recycling shortens the staple fiber length, compromising the strength and softness of recycled fibers. As a result, fabrics that include mechanically recycled fibers can generally only use 20 to 30% of recycled fibers before the quality of the fabric is reduced (Johnson et al., 2020). Post-consumer waste results in lower-quality recycled fiber due to degradation during wear, therefore, only pre-consumer waste is typically recycled mechanically (Johnson et al., 2020).
Chemical recycling refers to the process of using chemical methods to disassemble textiles back to their basic chemical components. Most chemical recycling technologies are in the start-up research and development phase (between technology readiness levels 3 to 7) with only a few operating at scale (e.g., Aquafil Global, 2022; Lenzing, 2022). Chemical recycling approaches for synthetic, polymer-based textiles, typically include depolymerization to reclaim the monomer or oligomer constituents which can then be repolymerized and re-spun into new, virgin-like fibers (Wang, 2010). Natural or cellulosic fiber approaches include dissolution in solvent systems or derivatization into viscose compounds. The former produces cotton fibers that can be re-spun into recycled fibers while the latter produces viscose products that can be used for fiber production as well as other applications (Johnson et al., 2020). It is worth noting that, due to the nature of chemical recycling, where recycled polymers become indistinguishable from their virgin counterparts, accounting tools such as Mass Balance Accounting (MBA) will be required to trace recycled content through the process (Beers et al., 2022).
Table 3 presents challenges and opportunities facing the mechanical and chemical recycling of textiles. Recycling routes often consist of a combination of mechanical and chemical processes. For example, garments are first subjected to mechanical pretreatment to remove items such as zippers and buttons, then ground or shredded and, in some cases (e.g., carpet recycling), separation and debonding of components using mechanical methods (e.g., loop-clipping, density separation, centrifugation) is needed (Wang, 2010). In this regard, chemical recycling still requires pre-processing for most raw materials to meet input specifications and material handling requirements, which generally include mechanical processes.
Table 3. Challenges and opportunities for textiles recycling (Schumacher and Forster, 2022).
Both chemical and mechanical recycling processes are sensitive to feedstock purity. Current recycling technologies cannot process mixed material inputs (e.g., garments made from two or more fibers) nor can they process chemicals and finishes applied to garments. As such, un-processable fractions, or low-purity, low-value feedstocks must be removed and disposed of properly, which represents considerable waste by itself (Wang, 2022). In general, the higher the feedstock purity, the lower the availability, and vice versa, and lower feedstock purity generally results in higher processing costs. Purity requirements of feedstock for chemical recycling range from 80 to 95%, depending on the method employed (Bender, 2021). Color-independent processes naturally increase the feedstock availability. This reinforces the need for identification and composition of fiber types and blends (e.g., percent of fiber composition).
Modern consumers have expressed a preference for comfort and stretch in their clothing, thus increasingly products include small amounts of elastane. This practice is problematic for recycling as elastane is difficult to separate from other fibers, and current technologies are not capable of recovering elastane. Therefore, a need exists for processes to separate out and recycle elastane.
Currently, post-industrial (or pre-consumer) streams are the most successful for mechanical recycling because they comprise a designated stream with known characteristics and have not lost quality due to wear and laundering. However, they also represent a smaller volume than post-consumer waste streams that comprise a mixture of garment types, fiber types/blends and quality, colors, additives, and finishes/coatings. However, as discussed previously, the post-consumer textile supply chain is currently not capable of supplying future recycling plants (namely chemically recycling plants) with the volume needed to drive circularity. Further, due to high processing costs, recycled fibers are often more expensive than their virgin-based counterparts. Therefore, to increase the uptake of recycled textiles requires market acceptance of a premium cost associated with recovered textiles, increased support and demand for recycled content from brands, and/or subsidies to support the development and expansion of recycling infrastructure.
While “fiber-to-fiber” recycling is not yet widely practiced, “bottle-to-fiber” is common practice, in which PET bottles are mechanically recycled into polyester textiles. Nearly all recycled polyester is derived from PET bottles and, as a result, textiles are currently the largest outlet for recycled PET, greater than bottle-to-bottle recycling. This is largely due to the more forgiving fiber market and favorable cost structure compared to food-grade end markets (Adler, 2020). Polyester currently constitutes the most widely used fiber in the apparel industry and while only 14% of polyester currently comes from recycled inputs, industry stakeholders would like that to increase to 45% by 2025 (Textile Exchange, 2022). However, as more food and beverage brands commit to recycled content targets, and regulation of packaging companies increases, competition for recycled PET will increase and recycled content for textile and apparel brands will be harder to achieve. This tremendous crossover between recycled polyester and PET packaging must be considered holistically to ensure adequate supply for all end uses and selection of the most efficient circular pathway for all materials.
Circularity for textiles is not economical in the current system. As indicated above, large-scale textile reuse and repair is hindered by high transportation and labor costs and decreasing quality and cost of new clothing due to fast fashion. Similarly, the cost to collect and recycle textiles exceeds the price that end users are willing to pay for the product. Often, consumers are unwilling to pay “the circular premium”, that is, the difference in price for a circular product (e.g., made from bio-based or recycled materials) than a traditionally manufactured product (D'Adamo and Lupi, 2021). Even if the U.S. were to expand collection systems, processing systems, and market demand, the economics do not currently support the business model (Bender, 2022). Options to address this concern include industry or public policy requirements for mandatory post-consumer recycled content, or policies such as Extended Producer Responsibility (EPR). The latter might allow for a funding mechanism that supports circular business models through options such as eco-modulated fees, which are varying levels of fees on virgin raw materials and products that do not meet different thresholds of minimum recycled content criteria, that could drive design for recyclability. Consumer-driven initiatives, such as sustainable fashion driven by pop culture and social media could also influence the economics of textiles circularity.
The globalization of the textiles industry has resulted in the shift of garment production from developed countries in the West to developing countries, primarily in southeast Asia. While this shift has complicated supply chain logistics and transparency therein, it may also be viewed as an opportunity to revitalize former textile industrial districts in the West to expand CE practices. As experienced in the industrial district of Prato, Italy, historically a center for textile production of international relevance, has become recognized for its reorganization and revitalization with a focus on circular textiles, primarily the recovery and recycling of woolen products (Bressanelli et al., 2022a,b). Similar opportunities for enhanced circularity have also been identified other geographic regions (Kazancoglu et al., 2020; Huang et al., 2021). In this sense, the traditional labor market, supply chain structure and relationships, and political environment can be utilized and adapted to support the transition of industrial districts to a CE.
The challenges described above closely align with those identified in several recent research reviews. Bressanelli et al. (2022a) discerned design, legislation, and labor competences as key challenges preventing a CE for the textile industry in Prato, Italy. Kazancoglu et al. (2020) recognized the primary challenges facing circularity were management and decision-making (the business decision to pursue circularity), high labor intensity (e.g., for collection, sorting, and repair of textiles), design challenges, materials (the inclusion of non-recyclable materials, chemicals, and additives in textiles), rules and regulation, knowledge and awareness of circularity, integration and collaboration, cost, and technical infrastructure. Jia et al. (2020) described organization barriers, meaning those related to a particular company's policies, such as internal support for circularity, metrics for performance, access to resources such as training for employees, and adequate strategic planning. Next, they discussed financial barriers, given that cost is a major obstacle to adopting new practices, and finally they named policy barriers, such as a lack of regulations and laws surrounding sustainable practices that extend beyond waste management and consider the full value chain for textiles. Similar barriers were also explored by Huang et al. (2021) who found governmental and regulatory issues, economic and financial issues, technological issues, societal issues, organizational and managerial issues, and infrastructural, supply chain, and market issues, many of which were also identified by the other reviews and discussed herein. This indicates that there is general consensus amongst the community regarding the biggest challenges facing a CE for textiles and the next section will discuss some methods to address them.
Addressing the challenges and fostering the opportunities identified above necessitates several actions. Collaboration across the textiles value chain can support system harmonization and the collection and exchange of data and information, which are all necessary for circularity. The following section explains each of these steps in greater detail. Note that all the steps discussed below are deemed necessary to realize a circular economy for textiles and thus are not presented in any prioritized order.
Transitioning to a circular economy for textiles requires an uncommon amount of cross-sectoral collaboration. Increased communications between stakeholders throughout the value chain and reverse logistics are necessary to understanding the many different dimensions of the issue and recognizing and serving the diverse perspectives and needs of various stakeholders. Innovative strategic partnerships including public-private partnerships can be powerful tools in developing recovery systems, advancing successful business models, and raising capital and financing for public and private infrastructure. Collaboration can drive information sharing, organizational learning, and technology exchange, and thus requires trust and transparency. As such, communication channels must be enabled and supported that are participatory and inclusive. Collaborations must include the stakeholders depicted in Figure 5.
Figure 5. Connections and collaborations needed between stakeholders to facilitate a CE for textiles.
Several challenges face this collaboration, particularly for select stakeholder groups. Some stakeholders are unable to participate in external events such as virtual meetings or workshops because they do not have the computing capability, access, or the time. Despite these challenges, collaboration with these communities is vital to the successful transition to circularity and as such, may require additional effort to connect with these stakeholders. For example, doing personal outreach, lessening restrictions, or providing access and translation services.
There is a significant need to harmonize many aspects of the textiles system including identifying and agreeing upon aspects such as a common language, definitions, classifications, industry tools, and standards. For example, the very definition of textiles, as well as what products are included is not well established. Definitions and classifications of waste, second-hand, and materials for recycling is particularly ambiguous across countries (e.g., in trade codes) and need to be further clarified (OECD, 2020). Similarly, agreement is needed on concepts such as biodegradable and bio-based polymers. Agreement is also needed regarding whether contamination includes chemicals introduced by design, stains and residue resulting from product use, or both. Classifications for waste audit studies must also be harmonized to enable comparisons and compilation.
Standards related to a circular economy for textiles are emerging at various levels around the world (e.g., Global Standard GmbH, 2021; ISO, 2022; Textile Exchange, 2022). Harmonization of these standards at the international level is needed to promote interoperability and facilitate trade for businesses with circular modes of operations (OECD, 2020).
Additionally, tools to characterize and model textiles circularity must be comprehensive, consistent, and transparent. Lifecycle assessment (LCA), techno-economic analysis (TEA), and material flow analysis (MFA) are examples of systems-level assessment tools that can serve as a baseline for environmental impacts, identify supply vulnerabilities, and support cost-benefit analysis, policy evaluations, supply-demand scenarios, and economic feasibility studies. However, to be accurate and useful, these tools need more consistency between data inputs, system boundaries, functional units, and assumptions. As a result, any comprehensive assessment of the circularity of textiles will require significant advances in the tools and data currently available to evaluate the entire economic, manufacturing (including design), social, and environmental landscape.
Significant data gaps currently inhibit the advancement of many CE efforts. Without quality and available data, it is not possible to reduce the industry's environmental footprint, design effective policy, or drive social change.
Acquiring or collecting reliable data is a significant challenge for several reasons, including opaque supply chains, proprietary information, lack of data tracking by brands, cost of data collection and reporting, lack of resources or knowledgeable personnel, inconsistent use of terms, and a general lack of transparency across the industry. Further, while many companies and organizations (e.g., Producer Responsibility Organizations) are collecting significant amounts of data, they are often proprietary, splintered, and/or not interoperable across the industry. Table 4 identifies some of the specific data needed to facilitate a CE.
A need exists for a unified infrastructure for collecting and managing significant amounts of data. Publicly available databases, repositories, and registries can be managed by private and/or public institutions for use by industry stakeholders, but they must be harmonized (e.g., consistent terminology) and interoperable. Data publishers and stewards should follow the FAIR Data Principles of Findability, Accessibility, Interoperability, and Reusability to ensure effective data discovery and application (Wilkinson et al., 2016). Additionally, access to data and databases needs to be available and affordable to all stakeholders, including resource-limited local governments.
Improving traceability and transparency has become a priority in the textile industry to manage supply chains more effectively and to identify and address social and environmental impacts. A garment is said to change hands 7 to 10 times in the supply chain, each time undergoing some level of alteration (Zaroff, 2021). Development of traceability platforms is necessary to track and trace products through development and provide the data necessary to enable downstream decision-making.
Transparent information exchange can enhance system performance, stimulate investment, and help strengthen relationships between stakeholders across the lifecycle of products and thereby promote circularity. However, strategies are needed to facilitate data transparency while protecting proprietary information. Such strategies could include the development of a data framework to guide establishment of data standards, auditable data protocols, and other data tools suited to the needs and integrity of the entire supply chain.
Information sharing also necessitates increased connectivity between stakeholders across the CE. This is necessary to understand different dimensions and recognize the diverse perspectives of various stakeholders. Communication channels must be enabled and supported that are participatory and inclusive.
Much of the data necessary to drive circularity could come in the form of improved labeling on textile products. In the U.S., Customs and Border Protection (CBP) and the Federal Trade Commission (FTC) enforce labeling laws and acts which, in general, require that textile and apparel products sold in the U.S. be labeled with the following information: fiber content, country of origin, manufacturer or dealer identity, and the care instructions (FTC, 2021, 2000; Office of Textiles and Apparel, 2021). Only fibers that comprise 5% or more of a product need to be identified (< 5% should be disclosed as “other fibers”) and non-fibrous materials such as plastic, glass, wood, paint, metal, or leather, do not have to be included on the label (FTC, 2014). While states and localities are preempted from implementing tag and label laws, they can require disclaimers for things like recycled content and toxic substances (Benson and Reczek, 2016).
Table 5 outlines challenges facing labeling for circularity and opportunities for improvement. Current labeling does not provide the data necessary to support decision making for appropriate reuse and recycling pathways. Despite fiber content requirements, more than 40% of garment labels contain inaccurate fiber composition information (Circle Economy, 2020). Additionally, current labeling is designed for the consumer, not circular partners, and are often removed prior to reaching post-consumer stakeholders.
Alternative labeling strategies are necessary to support and communicate textile traceability throughout the lifecycle of products. Such a strategy could include, for examples, digital product identification (often called a digital passport) in which a garment is equipped with a permanent digital identifier such as a QR code, RFID tag, watermark, or Near-field Communication (NFC) technology to allow access to data collected at each stage of the supply chain. Such identifiers could provide the necessary data to support reuse/recycling decision-making including brand identification, product characteristics (year, size, style, etc.), and production information (fiber origin and composition, chemicals/additives/dyes, certifications). Naturally, such digital identification requires an online database to host the data. Nascent efforts of this nature are already underway (EON, 2021; TextileGenesis, 2021), however, they have been criticized for their cost and network structure as being prohibitive to resource-limited stakeholders. Future research is necessary to explore appropriate hardware options for the digital identifier, for instance to understand how they can endure wear and tear and how they impact the recycling process. In addition, standards and policy development is needed to ensure accuracy and verifiability of the identifier information through conformity assessment.
Fashion and textile brands have a significant role in facilitating a CE for textiles. While many brands are taking steps to increase the circularity of their products through design for circularity, use of recycled materials, and zero waste production [see Moorhouse and Moorhouse (2017) for examples], these practices are not the mainstream and thus significant room for improvement remains. This section discusses design strategies that brands can employ to drive circularity as well as alternative business models that can help to curb textile waste generation and support their bottom line.
Fashion brand designers have a significant influence on the circularity of textile products, including upstream innovations and fiber sourcing, manufacturing processes and quality, as well as product durability and recyclability. However, in general, current design practices fail to consider the full lifecycle of products. Table 6 presents several circular design challenges and opportunities.
To support circularity, product design must balance the needs of quality, durability, and recyclability, with customer demand and cost. Design-for-recycling (DfR) entails that products are ideally 100% pure (not blended), contain only polymers, chemicals, additives, dyes, and finishes that do not contaminate the recycling system, and are easy to disassemble (e.g., removal of buttons, zippers). That said, these features are often what make garments (specifically outdoor apparel) durable and long-lasting. Improved data and decision tools would be useful to aid designers in prioritizing design characteristics. Similarly, design guidelines could help designers to incorporate DfR principles.
Increased communication between designers and the recovery industry is also necessary. This includes the need for feedback loops from recovery practitioners to designers with data pertaining to garment failure modes and recovery challenges and successes. Currently, the knowledge of sorters, graders, dismantlers, and recyclers is not codified to be used by designers for the re-design of products. As such, a need exists for practical guidelines to formalize information sharing between EoL service providers and designers. This necessitates agreed upon terminology, metrics, evaluations, and information sharing mechanisms.
Additionally, the design of textile materials themselves needs to be more sustainable and circular. As mentioned previously, modern textile materials are increasingly synthetic in nature, which causes significant environmental impact during production and use and can be difficult to recycle at EoL. The use of biomaterials and bioengineered polymers specifically is one area that has seen increased interest to address some of these challenges (e.g., Schiros et al., 2021), but materials engineers and designers must consider the lifecycle impacts of materials including compatibility with recycling infrastructure.
Brands can also facilitate circularity by advancing new business models such as repair, resell, renting, or even the application of artificial intelligence (AI) and on-demand manufacturing to optimize production and avoid excess. Some brands have initiated garment take-back programs (through mail-in or drop-off programs) in which they may sort and clean garments for direct resale, repair, or transformation into alternative textile products (e.g., Gama, 2021; Patagonia, 2022). Alternatively, some organizations (e.g., The Renewal Workshop, 2022) work on behalf of brands to clean, sort, and repair damaged or returned items for resale either on brand-specific online platforms or shared marketplaces. Ultimately, there is value in reuse applications for used textile products, and several ways brands can help keep their products in circulation while simultaneously supporting their bottom line.
Brand takeback and resale programs, together with the use of sustainable (e.g., recycled) textiles, could significantly influence consumer acceptance for reused/recycled products, a much-needed factor in transitioning to circularity. Takeback programs should be accessible to all customers and can include store drop-off or mail back. Brands can offer incentives for returning used garments, such as discounts, access to exclusive sets, or priority for the launch of special products. One challenge with takeback is ensuring that collected garments are appropriately processed through reuse, repair, and recycling channels.
Traditional recycling end markets include rag, shoddy, and mechanical fiber recycling while emerging recycling end markets include fiber-to-fiber (chemical) recycling. Traditional reuse end markets are thrift, donation, and export while re-commerce and resale are emerging reuse end markets. So, while there is a variety of end markets for textiles, they are at different stages of maturity. Further, most of these markets are distributed globally and the transport costs can be prohibitive. Thus, efforts are needed to identify and advance more opportunities for local markets.
Reuse markets, such as resale and rental, offer significant value and promise. For example, the clothing rental sector is expected to reach $2.5 billion by 2023, while resale is expected to grow eleven times faster than the broader retail clothing sector by 2025 (ThredUp, 2021; Zaroff, 2021). But this growth necessitates increasing consumer awareness and acceptance of used textiles as well as systems and infrastructure to support the market. Additionally, brands and retailers must continue to commit to circular sources, and industry and brands need to participate in pilot projects, partnerships, and engagement with recyclers.
Industry standards, specifications, and certification programs can establish requirements and consistency for products, feedstocks, and processes. Current standards generally support organic and sustainable production of natural fibers (e.g., cotton, wool, down), address social and environmental impacts of supply chains and manufacturing, and provide chain of custody verification tools of recycled content claims. Additional standards needed are outlined in Table 7.
The current linear model is highly incentivized for waste: it is less expensive to discard a textile product than it is to redirect it toward a circular business model. Further, the current system taxes labor, which is generally the highest cost for a company, and not waste (i.e., taxes the desired input rather than undesired output). Currently, circularity is considered additive (e.g., takeback and resell is an added business strategy for brands) rather than a replacement to the existing model.
Many argue that a CE for textiles is not possible without policy and legislation to serve as a catalyst. Designed thoughtfully, policy and legislation can create a level playing field, promote investment, incentivize textile recovery and infrastructure development, and ultimately encourage innovation and participation in recovery. Policy approaches need to be carefully crafted to lessen creation with new resources, disincentivize waste, and instead drive efficiency and reuse of materials. That said, textiles policies need to avoid material monopolies, deterrence from reuse/repair, and unfair access (Brasch, 2021). Table 8 presents several policy approaches that can be implemented at the local, state, and/or federal level that can aide in facilitating a circular economy for textiles.
Table 8. Policy approaches to facilitate a circular economy for textiles at the local, state, and/or federal level [adapted from Adler (2021), Brasch (2021), Hughes (2021)].
Outside of regulating landfills and waste-to-energy plants, the U.S. EPA does not currently have the regulatory authority to manage municipal solid waste (e.g., post-consumer material) as this responsibility is left to the state or municipality. As a result, several states are currently introducing bills to manage textile waste, most focused on carpet stewardship programs (e.g., Illinois General Assembly, 2021; Minnesota Legislature, 2021; Minnesota House of Representatives, 2021; Oregon State Legislature, 2021; The New York State Senate, 2021) and one state aiming to ban the disposal of textiles (MassDEP, 2021). To date, however, California has the only fiber recovery law in the U.S.: a carpet stewardship program which passed in 2011. The disparate nature of state and local initiatives may ultimately hinder the broad scale-up and distribution of recovery infrastructure. Rather, cohesive policy is needed that supports the timeline of scale-up and recovery capacities.
EPR is a comprehensive policy approach that extends a producer's financial and managerial responsibility for its products beyond the manufacturing stage – both upstream to product design and downstream to post-consumer reuse, recycling, or disposal (Cassel, 2021). In effect, this approach transitions away from taxpayers/governments funding recovery programs and internalizes these costs into the cost of manufacturing. To date, 33 U.S. states have passed 124 EPR laws covering 15 products, however no EPR laws cover textiles. Internationally, France currently has the only EPR law for textiles (Légifrance, 2007).
Recent European Union (EU) regulation includes the establishment of separate collection for textiles waste by January 1, 2025 (European Commission, 2018). Additionally, in 2022, the EU will introduce the Sustainable Textiles Strategy, laying the policy foundations aimed at making the EU textiles industry more sustainable. The strategy includes measures such as developing eco-design requirements, improving the business and regulatory environment for circular textiles in the EU, and boosting the sorting, reuse, and recycling of textiles with measures such as EPR (Šajn, 2021). These requirements will undoubtedly drive innovation and boost the competitiveness and resilience of the textiles industry in the EU and may influence the U.S. market.
Community engagement and education geared to all age ranges is critical to drive sustainable consumption and production of textiles and can take many forms. Table 9 provides several possible approaches to education and engagement activities that can help facilitate a CE.
Compelling outreach that drives engagement with consumers, brands, and communities is needed to drive textiles circularity. Repair skills should be introduced early in childhood education such as through crafting and home economics lessons. Sustainable consumption and production can be taught through cross-disciplinary activities throughout the education system. DIY courses, clubs, and repair cafes can allow the general public to engage in circularity. Further, consumer education campaigns can guide residents on where and how to donate used textiles, as well as what happens to textiles once they are donated or recycled. Controlled education and outreach campaigns can also help to address misconceptions about textile reuse and recycling, such as what happens to donated clothes or what can and should be donated. Such messaging needs to be clear, concise, and ongoing.
Education of workforces and training of experts in the field of CE is also critically needed. Educational program development should aim to strengthen and enhance the technical and practical skills of a workforce prepared to support the increased recovery and recycling of textile products. Academic programs could produce expertise tailored to the needs for circularity, including design strategies, technology innovation for collection, sorting, separation, and recycling, or business development to keep materials in the economy. Further, training programs should aim to promote the development of a skilled and distributed workforce focused on the growing field of circular materials.
Continued research is necessary to understand the current system and prioritize where and how advancements can be made. As displayed in Table 10, needed fields of research span from broader economic assessments and system-wide waste generation and social behavior studies to technical research and development.
Economic assessment is also necessary to evaluate the development of textile recovery and recycling infrastructure, including the feasibility of regional textile sorting facilities (MRFs). Such facilities could aide in domestic processing of textiles and dramatically increase the volume of textiles sorted for reuse and recycling, and thus reduce both export and landfill/incineration. But it is yet unknown if they are economically and practically feasible. Assessment should include partners, operators, suitable end markets for sorted materials, grade specifications, potential commodity value relative to collection and processing expenses, as well as potential public and private funding support for infrastructure development (e.g., low-interest loans, tax incentives, zoning allowances, etc.).
A need also exists for advanced and consistent waste composition audits to measure the volume of textiles that can be reused, repurposed, or recycled but are currently ending up in waste streams. Table 10 provides data that should be included in textile waste audits.
Consumer behavior studies are also necessary to collect qualitative data regarding behaviors and motivations around textile consumption, use, and disposal. This information can be used to direct information/outreach campaigns, design effective policy, and guide infrastructure development for collection.
Research and development must also be advanced on the technical aspects of sustainable textiles production and technological processes for textile sorting, separation, and recycling. In many cases, the transition from laboratory and bench-scale research to pilot projects and eventually commercialization is hindered by lack of investment. This is particularly the case for chemical recycling processes due to the low volume of materials collected for recycling which does not support significant investment. This situation is not justification for delayed research on recovery methods, but rather supports the need for government-funded research and development (R&D) in the field. Government-funded R&D could enable private investment in sectors of the CE by providing the data and information necessary to alleviate market uncertainties and thus prompting the development and deployment of cost-efficient reuse and recycling processes.
A transition to a CE for textiles will support economic growth, provide reliable jobs, as well as reduce the environmental impact of textiles and associated products. However, many challenges persist that must be addressed to facilitate textiles circularity in the United States. We discussed many of the technological, economic, and social barriers to a CE for textiles and identified specific data, tools, standards, R&D, and educational approaches to address them. This works reveals the need for harmonization of terminology, classifications, industry tools, and standards to unify approaches, increase interoperability of tools and resources, and promote broad adoption of CE strategies. Further, none of the opportunities identified can be pursued in isolation. Many factors, including economic, social, and environmental influence the motivation to shift toward a CE, and therefore moving toward circularity necessitates broad, multidisciplinary, multi-stakeholder collaboration. Through this cooperation, we can reach an optimized CE that depends on reciprocity, trust, transparency, and cooperation between all players.
KS wrote the first draft. AF revised and edited the draft. KS and AF were involved in the writing of this paper. Both authors approved the final version of the paper.
The authors are very grateful to Dr. Kathryn Beers, Director of the CE program at NIST, for supporting the textiles circular economy program at NIST.
The authors declare that the research was conducted in the absence of any commercial or financial relationships that could be construed as a potential conflict of interest.
All claims expressed in this article are solely those of the authors and do not necessarily represent those of their affiliated organizations, or those of the publisher, the editors and the reviewers. Any product that may be evaluated in this article, or claim that may be made by its manufacturer, is not guaranteed or endorsed by the publisher.
These opinions, recommendations, findings, and conclusions do not necessarily reflect the views or policies of NIST or the United States Government.
Adler, M. (2021). “Textile circularity in the US: current landscape, bottlenecks, and critical gaps,” in NIST Workshop: Facilitating a Circular Economy for Textiles.
Aquafil Global (2022). ECONYL® Pure. (Aquafil Global). Available online at: https://www.aquafil.com/econyl-pure/ (accessed December 28, 2021).
Bair, J., Anner, M., and Blasi, J. (2020). The political economy of private and public regulation in post-Rana Plaza Bangladesh. ILR Rev 73, 969–994. doi: 10.1177/0019793920925424
Barker, K. (2021). “Optical sorting advances are driving the MRF of the future,” in Recycling Product News.
Beers, K., Schumacher, K., Migler, K., Morris, K. C., and Kneifel, J. (2022). An Assessment of Mass Balance Accounting Methods for Polymers Workshop Report. NIST Special Public. 1500, 206. doi: 10.6028/NIST.SP.1500-206
Bender, D. (2021). “Challenges to mechanical and chemical recycling of textiles,” in NIST Workshop: Facilitating a Circular Economy for Textiles.
Benson, L. M., and Reczek, K. (2016). A guide to United States apparel and household textiles compliance requirements. Gaithersburg, MD: US Department of Commerce, National Institute of Standards and Technology. doi: 10.6028/NIST.IR.8115
Bevilacqua, M., Ciarapica, F. E., Mazzuto, G., and Paciarotti, C. (2014). Environmental analysis of a cotton yarn supply chain. J. Cleaner Prod. 82, 154–165. doi: 10.1016/j.jclepro.2014.06.082
Brasch, J. (2021). “Legal and regulatory barriers and opportunities for a textiles circular economy,” in NIST Workshop: Facilitating a Circular Economy for Textiles.
Bressanelli, G., Nesi, C., Saccani, N., and Visintin, F. (2022a). “Circular economy in the textile industry: evidence from the prato district,” in Role of Circular Economy in Resource Sustainability (Cham: Springer), 123–131. doi: 10.1007/978-3-030-90217-9_11
Bressanelli, G., Visintin, F., and Saccani, N. (2022b). Circular Economy and the evolution of industrial districts: A supply chain perspective. Int. J. Prod. Econ. 243, 108348. doi: 10.1016/j.ijpe.2021.108348
Cai, Y., Mitrano, D. M., Heuberger, M., Hufenus, R., and Nowack, B. (2020). The origin of microplastic fiber in polyester textiles: The textile production process matters. J. Cleaner Prod. 267, 121970. doi: 10.1016/j.jclepro.2020.121970
Cassel, S. (2021). “Extended producer responsibility for textiles,” in NIST Workshop: Facilitating a Circular Economy for Textiles.
Circle Economy (2020). Clothing Labels: Accurate or Not? Circle Economy. Available online at: https://www.circle-economy.com/resources/clothing-labels-accurate-or-not
Code of Federal Regulations (2022). 303.7 Generic names and definitions for manufactured fibers. (National Archives and Records Administration). Available online at: https://www.ecfr.gov/current/title-16/chapter-I/subchapter-C/part-303/section-303.7 (accessed April 5, 2022).
Crumbie, A. (2021). What is fast fashion and why is it a problem? Ethical Consumer, Available online at: https://www.ethicalconsumer.org/fashion-clothing/what-fast-fashion-why-it-problem#:~:text=Fast%20fashion%20is%20'fast'%20in,few%20times%20before%20being%20discarded (accessed December 15, 2021).
D'Adamo, I., and Lupi, G. (2021). Sustainability and resilience after COVID-19: A circular premium in the fashion industry. Sustainability 13:1861. doi: 10.3390/su13041861
European Commission (2018). Directive (EU) 2018/851 of the European Parliament and of the Council of 30 May 2018 amending Directive 2008/98/EC on waste. Office J. the European Union.
European Environment Agency (2021). Plastic in textiles: towards a circular economy for synthetic textiles in Europe.
Federal Trade Commission (2012). Guides for teh Use of Environmental Marketing Claims; Final Rule. U.S. FTC.
Fibersort (2021). Valvan Baling Systems introduces Fibersort. (Valvan Baling Systems). Available online at: http://www.valvan.com/products/equipment-for-used-clothingwipers/sorting-equipment/fibersort/ (accessed December 22, 2021).
FTC (2000, September 1). Care Labeling of Textile Wearing Apparel and Certain Piece Goods. (Federal Trade Commission). Available online at: https://www.ftc.gov/node/119456 (accessed December 29, 2021).
FTC (2014). Threading your way through the labeling requirements under the textile and wool acts. (Federal Trade Commission). Available online at: https://www.ftc.gov/tips-advice/business-center/guidance/threading-your-way-through-labeling-requirements-under-textile#except (accessed December 29, 2021).
FTC (2021). Textile Fiber Rule. (Federal Trade Commission). Available online at: https://www.ftc.gov/enforcement/rules/rulemaking-regulatory-reform-proceedings/textile-fiber-rule (accessed December 29, 2021).
Gama, C. (2021). “Eileen fisher renew: waste no more,” in NIST Workshop: Facilitating a Circular Economy for Textiles.
Global Standard GmbH (2021). Global Organic Textile Standard. Available online at: www.global-standard.org (accessed August 29, 2022).
Hasanbeigi, A., and Price, L. (2012). A review of energy use and energy efficiency technologies for the textile industry. Renew. Sustain. Energy Rev. 16, 3648–3665. doi: 10.1016/j.rser.2012.03.029
Henry, B., Laitala, K., and Klepp, I. G. (2019). Microfibres from apparel and home textiles: prospects for including microplastics in environmental sustainability assessment. Sci. Total Environ. 652, 483–494. doi: 10.1016/j.scitotenv.2018.10.166
Hiller, K. (2021). “The Environmental Impacts of the Fiber, Textiles, and Clothing (FTC) Industry,” in NIST Workshop: Facilitating a Circular Economy for Textiles.
Huang, Y. F., Azevedo, S. G., Lin, T. J., Cheng, C. S., and Lin, C. T. (2021). Exploring the decisive barriers to achieve circular economy: Strategies for the textile innovation in Taiwan. Sustain. Prod. Consumpt. 27, 1406–1423. doi: 10.1016/j.spc.2021.03.007
Hughes, J. (2021). “Facilitating a circular economy for textiles: legal and regulatory barriers and opportunities,” in NIST Workshop: Facilitating a Circular Economy for Textiles.
Illinois General Assembly (2021). SB0345: Carpet Stewardship Act. Available online at: https://www.ilga.gov/legislation/BillStatus.asp?DocNum=345andGAID=16andDocTypeID=SBandSessionID=110andGA=102 (accessed December 30, 2021).
ISO (2022). ISO/TC 323: Circular Economy. (International Organization for Standardization). Available online at: https://www.iso.org/committee/7203984.html (accessed August 29, 2022).
Jia, F., Yin, S., Chen, L., and Chen, X. (2020). The circular economy in the textile and apparel industry: A systematic literature review. J. Cleaner Prod. 259, 120728. doi: 10.1016/j.jclepro.2020.120728
Johnson, S., Echeverria, D., Venditti, R., Jameel, H., and Yao, Y. (2020). Supply chain of waste cotton recycling and reuse: A review. AATCC J. Res. 7, 19–31. doi: 10.14504/ajr.7.S1.3
Kazancoglu, I., Kazancoglu, Y., Yarimoglu, E., and Kahraman, A. (2020). A conceptual framework for barriers of circular supply chains for sustainability in the textile industry. Sustain. Develop. 28, 1477–1492. doi: 10.1002/sd.2100
King, J. (2021). “Textile reuse and recycling: A SMART perspective,” in NIST Workshop: Facilitating a Circular Economy for Textiles.
Légifrance (2007). Code de l'environnement - Article L541-10-3. Code de l'environnement. Available online at: https://www.legifrance.gouv.fr/codes/article_lc/LEGIARTI000043974919 (accessed December 30, 2021).
Lenzing (2022). Circular Economy. Available online at: https://www.lenzing.com/sustainability/sustainability-management/circular-economy (accessed December 28, 2021).
Lu, S. (2021). Changing trends in world textile and apparel trade. Available online at: https://www.just-style.com/features/changing-trends-in-world-textile-and-apparel-trade/ (accessed March 3, 2022).
Lynch, J. (2021). “Quantifying and characterizing plastic pollution in the ocean: a focus on textile sources,” in NIST Workshop: Facilitating a Circular Economy for Textiles.
MassDEP (2021). Solid Waste Master Plan. Massachusetts Department of Environmental Protection. Available online at: https://www.mass.gov/guides/solid-waste-master-plan (accessed December 30, 2021).
Minnesota House of Representatives (2021). HF1426: Carpet stewardship program established. Available online at: https://www.house.leg.state.mn.us/bills/Info/HF1426/92/2021/0 (accessed December 30, 2021).
Minnesota Legislature (2021). SF 959: Omnibus environment and natural resources policy and finance bill. Available online at: https://www.revisor.mn.gov/bills/bill.php?b=senateandf=SF0959andssn=0andy=2021 (accessed December 30, 2021).
Moorhouse, D., and Moorhouse, D. (2017). Sustainable design: circular economy in fashion and textiles. Design J. 20, S1948–S1959. doi: 10.1080/14606925.2017.1352713
Mortensen, L. (2021). “Environment and climate impacts from textiles – an EU perspective,” in NIST Workshop: Facilitating a Circular Economy for Textiles.
Morton, W., and Hearle, J. (2001). Physical Properties of Textile Fibres. 4th ed., Oxford: The Textile Institute and Woodhead Publishing.
Niinimäki, K. (2021). “Textiles in CE: Challenges and Opportunities,” in NIST Workshop: Facilitating a Circular Economy for Textiles.
Niinimäki, K., Peters, G., Dahlbo, H., Perry, P., Rissanen, T., and Gwilt, A. (2020). The environmental price of fast fashion. Nat. Rev. Earth Environ. 1, 189–200. doi: 10.1038/s43017-020-0039-9
NIST (2022). Circular Economy. National Institute of Standards and Technology. Available online at: https://www.nist.gov/circular-economy (accessed March 17, 2022).
OECD (2020). OECD Workshop on International Trade and the Circular Economy. OECD - Organization for Economic Cooperation and Development. Available online at: https://www.oecd.org/env/workshop-trade-circular-economy-summary-report.pdf
Office of Textiles Apparel (2021). U.S. Labeling Requirements for Textile, Apparel, Footwear and Travel Goods. Available online at: https://otexa.trade.gov/us_labeling.htm (accessed December 29, 2021).
Oregon State Legislature (2021). HB 3271: Establishes carpet stewardship program. Available online at: https://olis.oregonlegislature.gov/liz/2021R1/Measures/Overview/HB3271 (accessed December 30, 2021).
Patagonia (2022). Worn Wear. Available online at: https://wornwear.patagonia.com/ (accessed July 13, 2022).
Peaslee, G. F., Wilkinson, J. T., McGuinness, S. R., Tighe, M., Caterisano, N., Lee, S., et al. (2020). Another pathway for firefighter exposure to per-and polyfluoroalkyl substances: firefighter textiles. Environ. Sci. Technol. Lett. 7, 594–599. doi: 10.1021/acs.estlett.0c00410
Piribauer, B., and Bartl, A. (2019). Textile recycling processes, state of the art and current developments: A mini review. Waste Manage. Res. 37, 112–119. doi: 10.1177/0734242X18819277
Šajn, N. (2021). Legislative Train Schedule A European Green Deal: EU Strategy for Sustainable Textiles. European Parliament. Available online at: https://www.europarl.europa.eu/legislative-train/theme-a-european-green-deal/file-eu-textiles-strategy (accessed December 30, 2021).
Schiros, T. N., Mosher, C. Z., Zhu, Y., Bina, T., Gomez, V., Lee, C. L., et al. (2021). Bioengineering textiles across scales for a sustainable circular economy. Chem. 7, 2913–2926. doi: 10.1016/j.chempr.2021.10.012
Schumacher, K., and Forster, A. L. (2022). Facilitating a Circular Economy for Textiles Workshop Report. Gaithersburg, MD: National Institute of Standards and Technology. doi: 10.6028/NIST.SP.1500-207
Textile Exchange (2021). Preferred, Fiber and Materials Market Report. Textile Exchange. Available online at: https://textileexchange.org/wp-content/uploads/2021/08/Textile-Exchange_Preferred-Fiber-and-Materials-Market-Report_2021.pdf
Textile Exchange (2022). Standards. Available online at: https://textileexchange.org/standards/ (accessed August 29, 2022).
Textile Exchange (2022). 2025 Recycled Polyester Challenge (Textile Exchange). Available online at: https://textileexchange.org/2025-recycled-polyester-challenge/ (accessed December 28, 2021).
TextileGenesis. (2021). About Us. (TextileGenesis). Available online at: https://textilegenesis.com/ (accessed December 29, 2021).
The New York State Senate (2021). Senate Bill S5027A: Relates to establishing the carpet stewardship program. Available online at: https://www.nysenate.gov/legislation/bills/2021/s5027 (accessed December 30, 2021).
The Renewal Workshop (2022). Available online at: https://renewalworkshop.com/
The Textile Museum (2021). An Introduction to Textile Terms. The George Washington University Museum Archives. Available online at: https://web.archive.org/web/20060723073411/http://www.textilemuseum.org/PDFs/TextileTerms.pdf (accessed December 22, 2021).
UN Alliance for Sustainable Fashion. (2021). What is the UN Alliance for Sustainable Fashion? (United Nations). Available online at: https://unfashionalliance.org/ (accesed December 15, 2021).
United Nations (2018). Protectionist ban on imported used clothing. United Nations: Africa Renewal. Available online at: https://www.un.org/africarenewal/magazine/december-2017-march-2018/protectionist-ban-imported-used-clothing (accessed December 22, 2021).
United Nations (2022). Goal 12: Ensure sustainable consumption and production patterns. UN Sustainable Development Goals. Available online at: https://www.un.org/sustainabledevelopment/sustainable-consumption-production/ (accessed June 24, 2022).
US EPA (2020). Advancing Sustainable Materials Management: 2018 Tables and Figures. United States Environmental Protection Agency. Available online at: https://www.epa.gov/sites/default/files/2021-01/documents/2018_tables_and_figures_dec_2020_fnl_508.pdf (accessed March 21, 2022).
US EPA (2021a). National Overview: Facts and Figures on Materials, Wastes and Recycling. Available online at: https://www.epa.gov/facts-and-figures-about-materials-waste-and-recycling/national-overview-facts-and-figures-materials (accessed December 16, 2021).
US EPA (2021b). Textiles: Material-Specific Data. United State Environmental Protection Agency. Available online at: https://www.epa.gov/facts-and-figures-about-materials-waste-and-recycling/textiles-material-specific-data (accessed March 21, 2022).
US EPA (2021c). PFAS Explained. United States Environmental Protection Agency. Available online at: https://www.epa.gov/pfas/pfas-explained (accessed December 21, 2021).
Wang, P. Y. (2022). Interviewee, Professor, School of Materials Science and Engineering, Georgia Institute of Technology.
Wang, Y. (2010). Fiber and textile waste utilization. Waste Biomass Valoriz. 1, 135–143. doi: 10.1007/s12649-009-9005-y
Wilkinson, M. D., Dumontier, M., Aalbersberg, I. J., Appleton, G., Axton, M., Baak, A., et al. (2016). The FAIR Guiding Principles for scientific data management and stewardship. Sci. Data 3, 1–9. doi: 10.1038/sdata.2016.18
World Bank (2019). How Much Do Our Wardrobes Cost to the Environment? The World Bank. Available online at: https://www.worldbank.org/en/news/feature/2019/09/23/costo-moda-medio-ambiente (accessed December 17, 2021).
WWAP (2017). The United Nations World Water Development Report 2017: Wastewater, the Untapped Resource. Paris: United Nations World Water Assessment Programme, UNESCO.
Keywords: circular economy (CE), textiles, sustainability, recycling, circularity
Citation: Schumacher KA and Forster AL (2022) Textiles in a circular economy: An assessment of the current landscape, challenges, and opportunities in the United States. Front. Sustain. 3:1038323. doi: 10.3389/frsus.2022.1038323
Received: 06 September 2022; Accepted: 27 October 2022;
Published: 30 November 2022.
Edited by:
Idiano D'Adamo, Sapienza University of Rome, ItalyReviewed by:
Gianmarco Bressanelli, University of Brescia, ItalyCopyright © 2022 Schumacher and Forster. This is an open-access article distributed under the terms of the Creative Commons Attribution License (CC BY). The use, distribution or reproduction in other forums is permitted, provided the original author(s) and the copyright owner(s) are credited and that the original publication in this journal is cited, in accordance with accepted academic practice. No use, distribution or reproduction is permitted which does not comply with these terms.
*Correspondence: Kelsea A. Schumacher, S2Vsc2VhLnNjaHVtYWNoZXJAbmlzdC5nb3Y=
†ORCID: Kelsea A. Schumacher orcid.org/0000-0001-6104-4697
Amanda L. Forster orcid.org/0000-0001-7397-4429
Disclaimer: All claims expressed in this article are solely those of the authors and do not necessarily represent those of their affiliated organizations, or those of the publisher, the editors and the reviewers. Any product that may be evaluated in this article or claim that may be made by its manufacturer is not guaranteed or endorsed by the publisher.
Research integrity at Frontiers
Learn more about the work of our research integrity team to safeguard the quality of each article we publish.