- Chair of Supply Chain Management, Faculty of Business and Economics, University of Kassel, Kassel, Germany
Although interest in green and sustainable supply chains has been growing for over a decade in the academic discourse, the textile industry still embraces numerous examples of non-sustainable behavior (i.e., environmental damage, poor working conditions, or modern slavery). While there is a general agreement that stakeholder pressure can lead to more sustainable SCs, a lot remains for a more differentiated stakeholder perspective in sustainable supply chain management (SSCM). Thus, this study aims for theory elaboration by structuring relationships between SSCM and stakeholder constructs through an exploratory single case study design on the Otto Group, a German apparel frontrunner. It enables an in-depth investigation of the complexity of both stakeholder engagement/relationships and SSCM. As key results, sustainability managers and employees are important facilitators to realize win-win situations. Further, most progress is nowadays made in participating in multi-stakeholder-initiatives (MSI) and with standards to tackle sustainability issues in SCs. Furthermore, this study shows the importance of a shift from the perspective of sustainable products toward sustainable values, and it outlines best practices regarding the integration of stakeholders' expectations in SSCM.
Introduction
Although interest in green and sustainable supply chains has been growing for over a decade in the academic discourse (Ansari and Kant, 2017), the apparel industry embraces numerous examples of non-sustainable behavior. For example, clothing production is associated with myriad environmental damages, such as the contamination of rivers by chemicals used to dye the textiles. Moreover, working conditions, especially in manufacturing countries like China, Bangladesh, or Cambodia, are anything but sustainable – some even speak of modern slavery (Hasan, 2019). Most companies strive to achieve classical business targets rather than a genuine orientation toward sustainability (Gold and Schleper, 2017). Many companies have their own (in contrast to industry-wide) instruments and standards, which are not always applied comprehensively. Although anchoring sustainable and responsible supply chain management (SCM) on a strategic level and in corporate values is considered as essential (Beske and Seuring, 2014), the impact of stakeholders on sustainable supply chains (SCs) should not be underestimated (Wolf, 2014). One example is the Clean Clothes Campaign which advocates for workers' rights and improved working conditions in the international apparel industry and successfully calls for transparency in global SCs (Robledo and Triebich, 2020). Given that stakeholders come from different contexts, they have diverse expectations of a company. In addition to profit-oriented stakeholders, others are also concerned with social or environmental issues and therefore aim for sustainability in SCs. This stakeholder approach can lead to a shift in focus from the single economic view toward a holistic view of the value chain and potentially lead to a more ambitious and sustainable SCM approach (e.g., Gold and Schleper, 2017).
As most companies' SCs are very complex and not always clearly transparent, it is challenging to determine which stakeholder has a relevant role and can actively influence the company's approach toward more sustainability (Fritz et al., 2018). While there is a general agreement that stakeholder pressure can lead to more sustainable SCs (e.g., Wolf, 2014; Meixell and Luoma, 2015), a lot remains for a more differentiated stakeholder perspective in SSCM (Parmigiani et al., 2011; Siems and Seuring, 2021).
In many cases, stakeholder groups are described as pressure groups of companies and are thus seen as drivers toward sustainability (Meixell and Luoma, 2015). For example, Meixell and Luoma (2015) investigated stakeholder pressure toward the awareness, adoption, and integration of SSCM owing to a literature review. Fritz et al. (2018) developed a SC oriented iterative process to identify stakeholders in order to understand and address their concerns. This process includes, inter alia, stakeholder's engagement to spot other stakeholders. While apart from stakeholders as drivers or receivers of measures, other roles remain vague, Liu et al. (2018) attempted to explore additional possible stakeholder roles in the SSCM context. According to them, stakeholder groups can also act as facilitators or inspectors and thereby contribute to a more sustainable SC (Liu et al., 2018). Nevertheless, their study results are limited to supplier development which is just one part of SSCM (Beske and Seuring, 2014). In this context, the consideration of further SSCM constructs can be a valuable contribution. However, to the best of our knowledge, no empirical study has analyzed stakeholders in different roles in the context of SSCM. Thus, the following research question can be established:
How are stakeholders and their roles related to SSCM in the apparel industry?
To address this research question, an explorative case study on the textile division of Otto Group was conducted. As a large family-owned company with over 70 years of history they have experienced and initiated a transition toward a more sustainable SC. This transition was triggered by external pressure and stakeholders, but also actively driven by the company itself – not least because of the person at the top of the company. For example, the Otto Group was one of the first companies which introduced a Code of Conduct in Germany and can therefore be classified as a frontrunner (Otto Group, 2019). Further, environmental protection has been anchored as a corporate goal since the 1980's which is why the incorporation of stakeholders along the SC is an essential issue. The Otto Group is also member and co-founder of several alliances and MSIs to implement environmental and social standards for the apparel industry (Otto Group, 2020).
Thus, this research is relevant for the following reasons at least. First, several researchers called for more best practice case studies to learn from commendable companies in order to share SSCM practices (e.g., Silvestre, 2015, Köksal et al., 2017). Second, according to Khurana and Ricchetti (2016) further research is needed to evaluate current developments in SSCM for the apparel industry. In this respect, following similar case study designs, e.g., Brix-Asala et al. (2018)'s study (2018) which analyzed practices in relation to sustainability tensions of the frontrunner Fairphone, this paper aims to contribute by identifying stakeholders in different roles of SSCM.
The following chapter lays the theoretical background using literature on both SSCM in general and on the influence that stakeholders have in this respect in particular in order to create a link between SSCM and stakeholders' contributions to sustainability. Subsequently, the methodology is outlined. Here it should be noted that the results of a case study of a single company cannot, of course, be applied to an entire industry, but it can be advantageous to approach a phenomenon on a small scale in order to then examine it at the next larger level. Therefore, the case study uses mainly publicly available data, which was enriched with primary data, and thus strives for a higher method variety in qualitative research, as demanded by Eisenhardt et al. (2016) and Bansal et al. (2018). The following chapter shows the results of the analysis from the Otto Group's material and the interview by bringing together the previously theorized concepts of SSCM and stakeholder roles. In the discussion, the significance of the results is highlighted and the extent to which the case study brings value is elaborated. Finally, it will be shown how the results can be integrated into existing (scientific) discourses and where there is a need for further research.
Theoretical Background
Stakeholder and SSCM Terminology
The ongoing globalization led to more globalized SCs, which results in sustainability issues beyond national and company boundaries. Manufacturing processes have been relocated to countries with lower labor and environmental standards, and suppliers fulfill these processes in a multi-tier SC (Khurana and Ricchetti, 2016). Thus, the triple bottom line approach (TBL) (Elkington, 1998)– aiming to achieve simultaneously social, ecological, and economic business objectives – has become increasing attention. In the same line of argument -i.e., shifting attention toward a more differentiated business perspective – the stakeholder theory emphasizes that despite classical shareholders, other stakeholders, e.g., supplier, employees, or communities along with the SC, also require to be integrated into business decisions. Otherwise, a company may lose the legitimacy to do business. Parmar et al. (2010) define stakeholders as “any group or individual that can affect or be affected by the realization of an organization's purpose.”
Following to Mitchell et al. (1997), stakeholders can be differentiated by three attributes: power, legitimacy, and urgency. Other studies distinguish stakeholders according to their relationship to a specific company. Therefore, Clarkson (1995) differs between primary and secondary stakeholders. For primary stakeholders, companies themselves “can be defined as a system of primary stakeholder groups, a complex set of relationships between and among interest groups with different rights, objectives, expectations and responsibilities” (Clarkson, 1995). Secondary stakeholder groups can be defined as those who influence or affect a company or are influenced or affected by a company but are not engaged in transactions with the company and are not essential for its survival (Clarkson, 1995).
Seuring and Müller (2008) incorporated those considerations in the SCM context. They defined SSCM as “the management of material, information and capital flows as well as cooperation among companies along the SC while taking goals from all three dimensions of sustainable development, i.e., economic, environmental and social, into account which are derived from customer and stakeholder requirements” (Seuring and Müller, 2008).
In fact, not all sustainability dimensions can be considered equally, as there are different stakeholders (e.g., primary and secondary) with both different sustainability expectations and influence degrees (Meixell and Luoma, 2015).
SSCM and Stakeholder Roles
Research on sustainability in the SSCM context highlights, among other foci, which economic or social goals are triggered by pressures and incentives from external demands such as governments, customers, and other stakeholders (Seuring and Müller, 2008; Köksal et al., 2017). In this concern Meixell and Luoma (2015) state to what extent stakeholders can influence sustainability in SCs. They identify a positive correlation between stakeholder pressure in SCM and sustainability awareness, adoption of sustainability goals and/or implementation of sustainability practices.
According to Seuring and Müller (2008), two different fields require attention to achieve a more sustainable SC: (a) supplier management for risks and performance and (b) SCM for sustainable products. To improve sustainability in SCs and of products, focal firms have to find ways to manage quality and sustainability criteria through the whole SC in order to guarantee a certain sustainability level. Thus, enhancing the SCs overall sustainability performance incorporates the selection of a reduced but reliable supplier base and thus the assessment and (self-) evaluation of their performance (Siems et al., 2021). Implementing environmental and social standards, e.g., SA 8000 or ISO 14001, is a popular way to ensure a minimum performance and to manage risks along with the SC where the suppliers' involvement can facilitate the required exchange of information and coordination (Hofmann et al., 2014; Köksal et al., 2017; Yawar and Seuring, 2017). In addition to enhanced coordination and communication with suppliers, supplier development and life-cycle assessment of products contribute to further sustainability improvements and facilitate joint (product) developments (Beske and Seuring, 2014; Siems et al., 2021). This can ultimately lead to more efficient business operations while realizing win-win scenarios (Seuring and Müller, 2008; Rodríguez et al., 2016). Due to complexity, transparency issues, and limited resources, the focal firm has limited access to its suppliers (Busse et al., 2017). Thus, it sometimes faces trade-off decisions because goals of all three sustainability dimensions cannot be achieved simultaneously (Seuring and Müller, 2008; Brix-Asala et al., 2018). These trade-off decisions affect the SC performance and require agreeing to the lowest common thread to minimize risks and improve the SCs conditions as much as possible (Beske and Seuring, 2014; Seuring et al., 2019). Therefore, they can sometimes not solve an issue despite their willingness to tackle it (Carter et al., 2015).
However, the cooperation with non-traditional SC members such as NGOs, competitors or research institutes, and universities with a broad knowledge about different topics might be a suitable strategy to solve these complex issues (Rodríguez et al., 2016; Roscoe et al., 2020; Siems and Seuring, 2021). Liu et al. (2018) state that stakeholders can contribute to sustainable SCs as drivers, facilitators or inspectors within the process of supplier development at least. According to their study, drivers could be defined as actors “that provide pressure and/or incentives to initiate SDS [supplier development for sustainability] practices” (Liu et al., 2018). Facilitators provide knowledge and/or resources for practices; and inspectors provide a neutral and scientific ground for SDS practices (Liu et al., 2018). The fact that the role of drivers is mentioned more often in different studies than other roles is an interesting starting point for subsequent research. Other studies e.g., such as Köksal et al. (2017), mention stakeholders' role as drivers and characterize them as initiating and motivating factors in implementing SSCM practices. According to Siems and Seuring (2021), stakeholders can be integrated into SSCM practices at the internal and external dimensions of a focal firm to achieve true stakeholder orientation. Furthermore, Busse et al. (2017) illustrate how companies could identify SC sustainability risks with stakeholders' help. To monitor these risks, “gatekeeper instruments” such as Code of Conducts and processes (e.g., supplier selection) are in place, which can influence suppliers' behavior (Busse et al., 2017). Busse et al. (2017) assume that many industries (above all the apparel industry) only have low SC visibility—e.g., not enough information about suppliers—is therefore an interesting field to conduct further research. Consequently, it is crucial to take a look at the apparel industry and identify its nature.Together, these studies indicate the requirement to unravel the various contribution of stakeholders within SSCM.
Table 1 shows the identified deductive constructs of stakeholder roles mentioned in the reviewed literature on SSCM (Seuring and Müller, 2008; e.g., Liu et al., 2018; Seuring et al., 2019) and illustrates the underlying coding scheme. The table is derived from the SSCM construct of Seuring and Müller (2008) and the stakeholder constructs of Liu et al. (2018) and is furthermore enriched by the aforementioned current debate in SSCM literature.
Methodology
As there is insufficient evidence in previous publications on which stakeholders can influence corporate sustainability efforts and in which way, the Otto Group's SC is examined more closely in order to find out what impact stakeholders have on the implementation of sustainability in this area. However, we do not look at the individual steps of the Otto Group's SC because it is not fundamentally different in comparison to other companies, but rather at the complexity and structure of the SC in general to elaborate existing theory. Thus, the study aimed for theory elaboration by structuring relationships between SSCM and stakeholder constructs through a single exploratory case study design. It enables an in-depth investigation of the complexity of both stakeholder engagement/relationships and SSCM.
According to Stuart et al. (2002) a case study is helpful when the research question asks why or how things happen (Stuart et al., 2002; Saunders et al., 2009; Yin, 2018). Besides, it looks at a real-world phenomenon, which means that the case's context is crucial and cannot be controlled (Yin, 2018). In this respect, case-based research cures a “weak and limited understanding of the body of knowledge as a whole” (Stuart et al., 2002). Case studies not only serve to capture a phenomenon and develop from their richness of observation, but they also allow to refute or extend existing theories. Since exploratory research seeks to define an identified problem (Sreejesh et al., 2014), this case study aimed to explore stakeholders' influence by bringing together theoretical assumptions of both stakeholder theory and SSCM. As a case study should contain a transparent research process, the suggestions from Stuart et al. (2002) were followed with minor modifications: (1) Development of research instrument, (2) Data gathering, (3) Data analysis, and (4) Dissemination (see Figure 1).
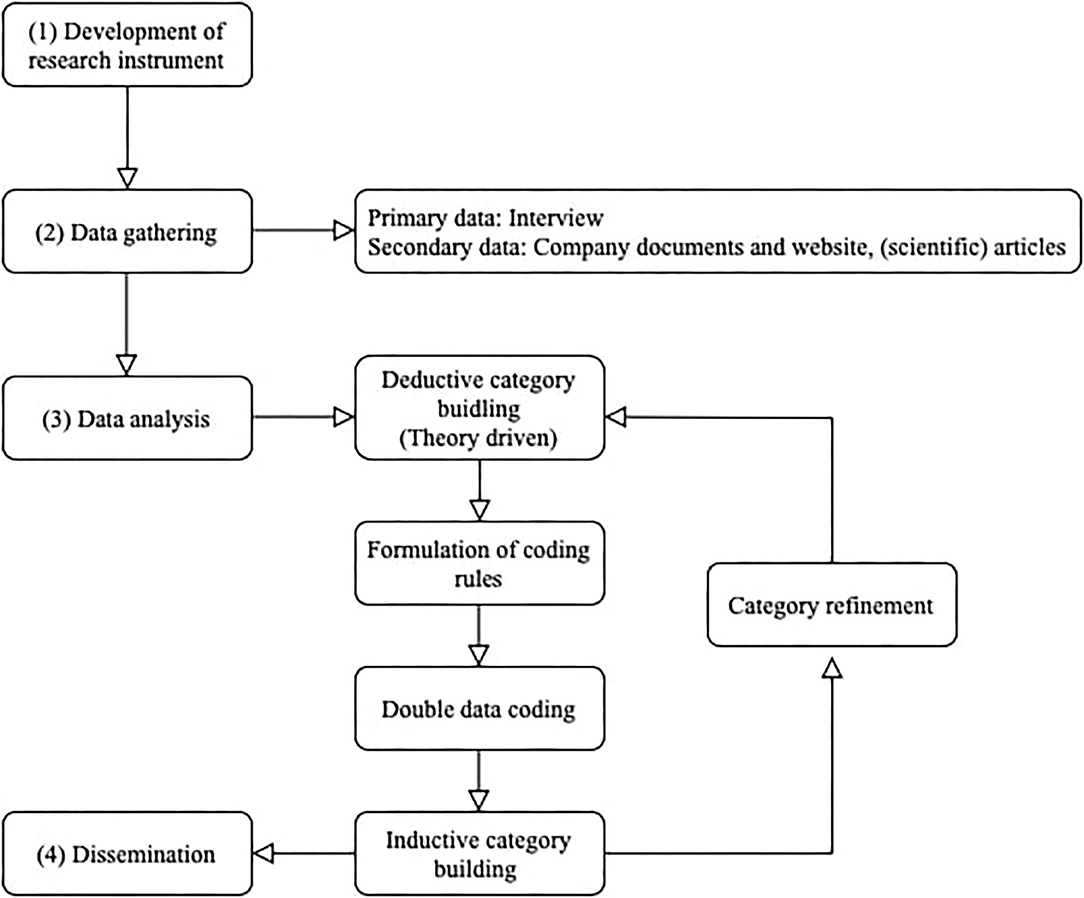
Figure 1. Applied research process (based on Stuart et al., 2002).
Development of Research Instrument: A Case Study
The apparel industry is an interesting field to research as it is one of the biggest industries with ~€1.5 trillion annual revenue (Shahbandeh, 2021). As mentioned before, the industry is characterized by the complexity of their SCs and the existence of multiple stakeholders, some of which are loud, others are in the background. Further, it is very susceptible to disruption and often subject to criticism, especially regarding sustainability-related aspects.
The industry's development toward fast response to consumer demands and permanently changing trends (Christopher et al., 2004) has led to lower producing costs resulting in bad environmental and poor labor conditions in SCs in producing countries (Masson et al., 2007). Although some apparel companies have addressed sustainability for many years (Khurana and Ricchetti, 2016), the industry is still known for incidents like Rana Plaza and environmental problems in their factories (Köksal et al., 2017). Therefore, it seems necessary to conduct further research on the factors that could counteract these adverse events and consequences. In this context, it is crucial to consider the social conditions in SCs—especially in upstream tiers—as they have not been sufficiently appreciated in previous research compared to environmental and economic aspects.
SSCM in the apparel industry takes into account both internal company measurements and industry-wide practices for a sustainable value chain. This includes stakeholders who can act as primary and secondary drivers, enablers or barriers; but also technological improvements and cost-driven decisions can influence a company's business decisions (Köksal et al., 2017). Khurana and Ricchetti (2016) describe the integration of SC sustainability into core business practices and the implementation of transparency in SCs as important instruments for more sustainability along the value chain of the apparel industry. The theoretical approaches cited above regarding a higher SC sustainability performance underline that a case study in the apparel industry is an appropriate approach to question theoretical hypotheses and identify challenges and methods for sustainability in SCM.
Regarding responsibility toward suppliers, Awaysheh and Klassen (2010) summarize four dimensions of socially responsible practices: supplier human rights, supplier labor practices, supplier codes of conduct and supplier social audits. In addition, Code of Conducts and Code of Ethics, and third party-audits that monitor compliance with the codes of the firms, can contribute to the implementation of sustainability in SCs (Köksal et al., 2017). By taking into account these lines of argumentation, a case study on the apparel industry might be a suitable approach to question theoretical hypotheses and identify challenges and methods for sustainability in SCM.
With almost 50,000 employees, more than €15.5 billion in revenue, and more than 120 group companies (Otto Group, 2021), the Otto Group is an outstanding example of a company in the apparel sector, primarily because of its long-standing focus on sustainability. The various group companies are linked to a highly complex SC. Against the background of this complexity, it is particularly interesting to identify and analyse the influences of different stakeholders and the mechanisms to manage them better.
As already outlined, the Otto Group's SC with the involved stakeholders as a frontrunner in the apparel industry offers an intriguing framework for this research due to the special conditions in a family-owned business and the company's long-standing sustainability orientation. This setting represents a different case compared to most apparel companies and could lead to a benchmark for the entire industry.
As already mentioned, the Otto Group can be seen as a role model/frontrunner in the apparel industry in terms of sustainability. Since the 1980's, environmental protection was implemented as a company goal. The Otto Group has been involved in the development of worldwide guidelines for social and environmental improvement. In order to increase their sustainable impact and to achieve sustainability goals, the Otto Group enters cooperation with different stakeholders along with the SC (Otto Group, 2019). As a further instrument, the Otto Group uses financial incentives for its chair members with regard to variable remuneration that depends on the extent to which sustainability targets and goals are fulfilled (CSR in Deutschland, 2014).
Beyond its long-term internal engagement on sustainability, the Otto Group is a member or co-founder of several alliances and MSIs to implement environmental and social standards for the apparel industry and in SCs (Otto Group, 2020). The combination of the different alliances and methods to tackle sustainability issues leads to a variety of stakeholder involvement and thus an interesting angle for this case study.
In this respect, this paper does not conduct a multi-case study with the integration of several generic companies, but focuses only on the Otto Group to show what they do as a frontrunner and can thus be understood as a best practice example – as requested e.g., by Silvestre (2015) and Köksal et al. (2017).
Data Gathering
According to material analysis, the case study was based on primary and secondary data (see Figure 1). As a starting point, the website of the Otto Group was scanned to get a first overview regarding the research scope. Two Otto Group annual reports (2018/2019 and 2019/2020) were used as secondary data in order to get an impression on the company's approach to sustainability. Furthermore, two articles about the Otto Group's sustainability strategy with a special focus on marketing opportunities but also the orientation and positioning of the company toward sustainable sourcing were used (Riekhof, 2013; Brock and Streubig, 2014). As a final secondary source that should not be forgotten, existing research on SSCM and stakeholder management was included in the analysis.
To validate and complete the first analysis's insights, a semi-structured interview with an SSCM expert from the Otto Group was conducted. A guideline developed by the research team served as the basis for the interview questions. On the one hand, the interview allowed to elaborate on some of the issues that have been identified as of particular interest and, on the other hand, tried to generate information about the existence and importance of stakeholders. The advantage of semi-structured interviews compared to open discussions is that the respondent can answer in their own words and has sufficient time and space. Still, the interviewer ensures that the answers are focused on the relevant topic (Sreejesh et al., 2014). Further, it allows going more into details on questions that appear during the interview and allows to ask further questions (Saunders et al., 2009).
The questions for the interview were chosen based on the underlying theoretical constructs and supplemented during the discussion with further researchers. The interview was conducted in a video conference and by both researchers in order to be able to analyse it as neutral as possible. In addition, the transcription was carried out on the basis of already proven scientific rules by the research team. Internal validity was achieved by offering to return the interview summary to the interviewee and offering his consent.
The combination of both data from the company and external information gained in a direct dialogue results in a more complete picture of the phenomena (Stuart et al., 2002).
Data Analysis
The case study aimed at theory elaboration, which define Fisher and Aguinis (2017, p. 441) as “the process of conceptualizing and executing empirical research using pre-existing conceptual ideas or a preliminary model as a basis for developing new theoretical insights by contrasting, specifying, or structuring theoretical constructs and relations to account for and explain empirical observations.” The research started with an existing conceptual model; then, data was collected to refine theory and gain new insights (see Figure 1). As there is also potential to collect additional data, this method seemed appropriate (Fisher and Aguinis, 2017). Both the interview and the secondary material were analyzed using the qualitative content analysis as it allows to analyse texts and draw conclusions (Kassarjian, 1977). In this analysis, the procedure of structuring was used. The aim is to assess the material based on defined criteria in order to filter out certain aspects (Mayring, 2015). According to Fisher and Aguinis (2017), the structuring approach is appropriate if the study's primary focus is to improve an existing theory's explanatory and predictive adequacy (Fisher and Aguinis, 2017). Which contents are to be extracted from the material will be developed by theory-guided categories (Mayring, 2015). Therefore, an abductive approach was chosen which allows both the application of an established interpretative rule—which in this case is existing in theory—and the observation of an empirical phenomenon. This results in a re-interpretation of existing theory (Alvesson and Kärreman, 2007). The advantage is that researchers can critically assess alternative ways of framing empirical material.
Therefore, the material to be analyzed was first condensed. As most of the material was published by the company, it is not neutral or scientific and consciously addresses certain aspects, while others are not mentioned. After an initial screening of the material, a first categorization was created based on the screened literature. The first draft of the category system was renewed in a next step by merging and omitting some of the categories according to Seuring and Müller (2008). According to Gioia et al. (2013), the reduction of categories helps to make the categories more manageable, so that in a second-order analysis it is easier to assess whether the categories are helpful to answer the research question. This was followed by a coding with the help of the software MAXQDA. In order to achieve as much neutrality as possible, the authors used a double coding by ensuring that two researcher analyzed the material and that only those factors were considered that coincided. Further, the authors see that the existing explanation is incomplete and therefore must be widened to unite stakeholder theory with literature on sustainable SCs.
Dissemination
According to Stuart et al. (2002) a case study must reflect the phenomena they are intended to, and must be repeatable and conclude with the same results. Thus, Table 2 condenses different validity and reliability measurements to disseminate the conducted qualitative research.
Findings
Within the analyzed material, different stakeholders were identified. These stakeholder groups have one or several stakes in the Otto Group's activities and can influence or were influenced by the Otto Group's actions (see Table 3). This fact often results in mutual relationships. Therefore, according to the definition of Parmar et al. (2010), these stakeholders are relevant for the Otto Group and are listed below in different functions. The distinction of stakeholder groups into primary and secondary stakeholders (Table 3) is based on Busse et al. (2017).
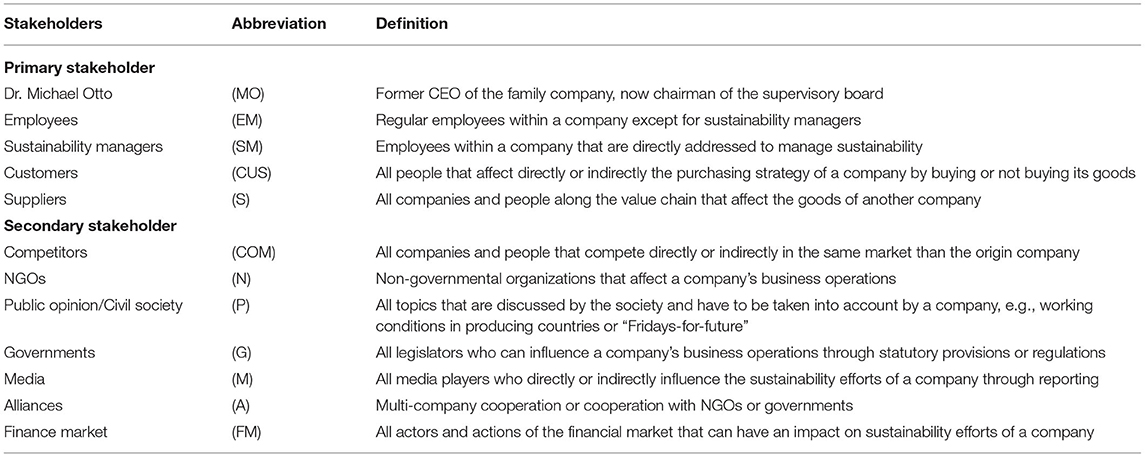
Table 3. Inductively identified stakeholders with definitions based on Busse et al. (2017).
In the next step, the respective actors are assigned to the three roles (drivers, facilitators, and inspectors) according to Liu et al. (2018) that have been extracted through the material analysis. Within the categories, a further distinction is made between primary and secondary stakeholders to illustrate their influence. According to Table 1, the stakeholders and their roles were then linked to the SSCM categories in terms of their influence on SSCM of the Otto Group. The coding allows categorizing and analyzing stakeholders' influence more precisely by revealing recurring patterns in individual stakeholder roles that relate to and influence sustainability in the Otto Group's SC. The extent to which these groups can affect the Otto Group's operations is outlined in the following chapters using the Otto Group's SSCM in combination with several stakeholder groups or response to pressure from stakeholder groups. Overall, it is a combination of different stakeholder groups that can influence the Otto Group's actions about sustainability in SCs in different ways.
Drivers
In order to assign the various stakeholder groups to their most frequent roles, MO and customers as primary stakeholders and secondary stakeholders such as NGOs, civil society, and media are identified as drivers (see Tables 3, 4). According to Busse et al. (2017), drivers are stakeholders that push awareness for sustainability. In line with the arguments of Table 1, the drivers were analyzed in combination with supplier management for risk and performance. In this regard, the implementation of standards is the most common way of the Otto Group to ensure a minimum SC performance also driven by stakeholder groups (Beske and Seuring, 2014).
Supplier Management
All analyzed sources describe MO, the chairman of the supervisory board, as a primary driver. As the CEO of the Otto Group, his engagement can be linked to supplier management. Since the 1980s, he has promoted the Otto Group's commitment to sustainability through his position as CEO from 1981 to 2007 by defining environmental protection as a corporate goal in 1986 (Otto Group, 2019). During this time, the Otto Group already implemented and pushed suppliers to incorporate environmental and social standards, e.g., child work restrictions or energy efficiency classes (Interview, 2020). While the implementation of standards is more a minimum requirement nowadays, it was a benchmark and not widely applied in the apparel sector or for large companies in general when the standards were implemented in the Otto Group. Therefore, MO's engagement has to be divided into two different stakeholder roles. The CEO's engagement can be classified as a driver and differs from his actual role, as he can be seen more as an inspector (see section Inspectors).
As a second stakeholder group identified as drivers concerning supplier management, customers play an essential role. In this context, the interviewee and several secondary sources mentioned the great relevance of customers. They do not directly reward positive, sustainable behavior and increasingly buy from such companies, but rather punish non-sustainable activities and then purchase from other companies. This means that any company must constantly be aware of and ensure compliance with specific standards. This expectation, combined with negative differentiation, makes positioning sustainability more difficult since positive differentiation does not have the expected effects on customers. Therefore, the Otto Group would welcome even greater commitment from customers so that a positive dedication to sustainability is also reflected in their purchasing behavior.
Nevertheless, customers in their role as drivers are granted a great deal of power, which, in conjunction with other secondary drivers, can often cause urgency. Urgency is, according to Mitchell et al. (1997), one of three crucial attributes (power and legitimacy) in order to identify stakeholder's salience. Especially the interaction with NGOs, the media, and the resulting public opinion can ensure that specific trends in sustainability arise, and that unsustainable behavior of companies is avoided and even punished.
Sustainable Performance Relationships
As an essential point for the engagement of MO, the foundations of MO, which cooperate closely with the Otto Group, target, in particular, the upstream stages of the SC and—through cooperation with producers and farmers—attempt to produce more sustainable materials right at the beginning of the value chain. Pagell and Wu (2009) suggested that working with non-traditional SC actors yields the potential to achieve (sustainable) win-win situations by combining efforts and resources. Even though foundations like the “Aid by Trade Foundation” or the “Stiftung 2°” serve as facilitators, the engagement of MO within the company and in combination with his position as founder of the initiatives mentioned above can be linked to his role as a driver. Thus, this example outlines how one stakeholder can trigger other stakeholders to work together to advance a particular goal that cannot be achieved alone.
Sustainable Risk Management
Furthermore, several secondary drivers influence the commitment to sustainability in the Otto Group on different levels (see Table 4). As far as social risks are concerned, the issue is being promoted by NGOs in particular. In the interview, they are described as a kind of “watchdog” who pays close attention to how the Otto Group behaves in this area and communicates misconduct accordingly. Since NGOs often address corporate violations, they also ensure that social risks, especially in production, must always be considered, and the social situation in SCs needs to be communicated to the public – especially as this issue is of public interest (Interview, 2020). When media, public opinion/civil society, and customers come together, a unique dynamic develops, which can pose economic risks for companies by causing much sensible attention. In particular, negative publicity, e.g., the accusation of greenwashing, can lead to a generally negative image and lower sales figures (Riekhof, 2013). This fact results in the Otto Group's strategy of not primarily targeting individual sales measures through sustainability, but rather to avoid customers perceiving the Otto Group as a non-sustainable company. The narrative has changed due to the possibility of differentiation through sustainability. While this used to be mainly positive, it now often happens that (some) customers ignore companies that are negatively associated with sustainability issues in their SC and do not buy products from them (Interview, 2020). Companies, including the Otto Group, must pay attention to this and recognize these trends through risk management and stakeholder dialogues in order to be able to react at an early stage so that the company is not negatively penalized by customers and potential customers (Riekhof, 2013; Interview, 2020).
SCM for Sustainable Products
At this point, a link can be drawn to SCM for sustainable products. According to Pagell and Wu (2009) and Seuring and Müller (2008), managing SCs for sustainable products requires enhanced coordination and communication and supplier development and joint innovation. According to Riekhof (2013) the Otto Group shifts the perspective from the narrative of sustainable products to values, where several stakeholders are co-producers of these values, and therefore, their roles and relationships must be reconfigured. This process can be seen as an outcome derived from customers as drivers regarding risk management. In this respect it is particularly striking that MO, in his role as a driver, is identified in all three risk dimensions. This can be explained by the early recognition of the social and ecological impact of companies which has led to a strong corporate focus on sustainability through MO since the 1980s. In addition, the company's name is automatically linked to his name, which is why unsustainable behavior is not only negatively linked to the company, but also to his person and family (Interview, 2020). As explained earlier, this stakeholder role is linked to his previous engagement with the company, and his current position may be more related to that of an inspector – also concerning risk management.
When it comes to SCM for sustainable products, the foundations are essential drivers to develop better solutions in SSCM. This can be seen, e.g., on the example of two foundations that were founded with the cooperation or under the initiative of MO – especially against the background that actors have not sufficiently addresses these issues. Despite sustainability measures focusing on the upstream SC stage, MO established the “Stiftung 2°,” a cross-market initiative for German companies to join forces for climate protection (Otto Group, 2019). Through the “Aid by Trade Foundation,” the initiative “Cotton made in Africa” (CmiA) was founded, which promotes sustainable and organic cotton in cooperation with small farmers. CmiA supports farmers in the sub-Saharan region to establish sustainable and ecological businesses that provide better income for families in the region and further improve the environmental footprint of the buying companies (Cotton made in Africa, 2021). With 86 million cotton articles, the Otto Group is a significant buyer from these farmers. For this reason, the Otto Group cooperates with foundations that tackle sustainability issues at different stages of the SC, e.g., through supplier development and joint innovations (CmiA) or improved coordination and communication, which is what the “Stiftung 2°” does.
Facilitators
When stakeholders act as facilitators, these stakeholder groups may provide the required know-how and resources to establish valuable measures for improving sustainable practices in companies (Busse et al., 2017). Among the primary stakeholder groups, sustainability managers and employees were most frequently mentioned in the role as facilitators, while among secondary stakeholder groups, alliances and suppliers were attributed this role. In addition, acceptance by suppliers and employees is necessary to establish effective methods and standards. Sustainability managers as primary stakeholders and alliances on the secondary side help communicate this approach more effectively and provide appropriate expertise. The interview clarified that—especially in cooperation with the alliances—a certain amount of power must be ensured to drive forward sustainability efforts.
Supplier Management for Risk and Performance
Supplier management for risk and performance is the first category, obtained from the Seuring and Müller (2008) framework. The analysis revealed that the Otto Group frequently uses both supplier involvement and implementation of standards. According to Beske and Seuring (2014), implementing standards can ensure a minimum performance; the participation in alliances with competitors, NGOs or governments, facilitates the implementation of standards in the SC for the Otto Group.
Sustainable Performance Relationships
Sustainability managers and employees are key facilitators for win-win situations in sustainable performance relationships. To strengthen the role of employees, the Otto Group implemented a Code of Ethics, providing employees with guidelines on how to act and work within the company. The idea is similar to a Code of Conduct for suppliers. Like the Code of Conduct, this instrument can be considered as a minimum requirement. According to Rodríguez et al. (2016), minimum criteria can be seen as the lowest common thread for risk-avoiding and improving conditions in the SC. Still, they can also be a starting point to aim for win-win situations. It is worth mentioning that this Code of Ethics is not introduced top-down but has been developed in a participatory manner. A more value-oriented company can strengthen the identification of employees with the company and improve the good external image. Above that, suggestions can be presented more easily by employees -site and implemented to improve the sustainability performance. In the past, more than 4,500 personal commitments of employees have been implemented, enhancing profitability, innovation, diversity, and sustainability (Brock and Streubig, 2014).
According to the SSCM expert interviews, this can be linked to suppliers in their role as facilitators with a win-win outcome in the sustainable performance relationship. The relationship to raw material suppliers is described with a push-pull effect. On the one hand, the Otto Group demands sustainable materials and can therefore be seen as a driver from the suppliers' perspective. On the other hand, suppliers rely on sustainability regarding the materials to receive better and stable contracts and establish a benchmark in the market so that the Otto Group must follow these trends accordingly to be perceived as sustainable. Besides, the interviewee also emphasized that it is a challenge not to fall into greenwashing attempts of suppliers but to build on long-term partnerships. With the possibility of achieving better orders, better acceptance, more extended collaboration, suppliers are incentivized to behave more sustainably. Despite the benefits for suppliers, this situation can be seen as a win-win situation because this also creates benefits for the Otto Group, as they can promote independent improvements and achieve higher SC sustainability performance (Interview, 2020).
The data revealed two different strategies to involve suppliers in progress toward a more sustainably SC. The first option is more direct and can lead to more holistic and more advanced sustainable solutions with a win-win outcome. Most outcomes in combination with competitors or alliances as drivers or facilitators led to minimum requirements as the environmental and social standards were implemented top-down in the SC. About the data, this led to joint innovation in the alliance and less supplier development and is used more for supplier assessment and supplier (self-) evaluation when it comes to supplier management (Otto Group, 2019; Weber et al., 2020). The second option addresses SCM for sustainable products and is later outlined.
Sustainable Risk Management
Concerning the avoidance and addressing of sustainability risks, sustainability managers act as facilitators since they provide know-how and resources to identify potential opportunities and risks in the impact process. These identification processes play an essential role both for the Otto Group's commitment to sustainability and for conducting materiality analyses in stakeholder dialogues (Interview, 2020; Otto Group, 2020), especially when it comes to internal management instruments. As a last instrument for sustainable performance relationships, the “impACT process” is an essential key tool to analyse and avoid sustainability risks with measures and training to improve sustainability in the SC. Therefore, it can be seen as the most critical gatekeeper instrument for supplier selection within the Otto Group. Furthermore, sustainability managers facilitate coordination and communication toward primary and secondary stakeholders to improve the necessity of SCM for more sustainable products (Otto Group, 2020). This can be linked to Pagell and Wu (2009), who suggested that enhanced coordination and communication with suppliers and other stakeholders can be used to manage SC for more sustainable products.
SCM for Sustainable Products
As already explained in the case of the win-win outcome with suppliers, this can, in turn, be linked to supplier involvement for supplier management and supplier development concerning SCM for sustainable products. Thus, Pagell and Wu (2009) suggest using supplier development to manage the SC for sustainable products. In combination with this stakeholder role, Beske and Seuring (2014) mention that supplier involvement can facilitate the necessary information exchange and coordination for minimum requirements. With the “EMPact Social” program, the Otto Group offers training in suppliers' factories for eight months to develop concrete improvement measures for several challenges. These workshops are held with factory representatives also to improve factory-specific topics (Otto Group, 2020).
Inspectors
As a third stakeholder role, inspectors can be named. In this role, stakeholder groups provide a neutral or scientific ground for sustainable supplier development and evaluate or assess the implementation of sustainability practices along with the SC (Liu et al., 2018). The results suggested governments as the key stakeholder for this role. Besides governments, MO as the primary inspector and NGOs as secondary inspectors were identified.
Supplier Management for Risk and Performance
Beske and Seuring (2014) suggested that implementing environmental and social standards is common to ensure minimum performance. The interviewee defined the role of governments to ensure a level playing field in which all companies can and must operate (Interview, 2020). Thus, governments defined social and environmental standards, which, in turn, served as a core component for supplier management for companies (Otto Group, 2019; Interview, 2020). Furthermore, in large MSIs where companies such as the Otto Group are involved, governments are in charge of coordination and communication to navigate the different companies and stakeholders and moderate the different opinions to reach a common perspective (Weber et al., 2020). This combination can also be extended to other categories from the framework, like sustainable performance relationships, so the focus on this combination will be deepened in the following paragraphs. The data indicated that, as governments, NGOs nowadays could also be defined as inspectors regarding implementing Codes of Conduct and environmental and social standards for supplier management (Riekhof, 2013).
Sustainable Performance Relationships
The implementation of standards and Codes of Conduct results in most cases in implementing minimum requirements that triggered two changes: on the one hand, to avoid the identified risks. On the other hand, the requirements lead to a general improvement of the SC's conditions, which is in line, for example, with Seuring and Müller (2008). Moreover, the interviewee suggested that standards must be developed for all market participants to ensure a neutral level playing field (Interview, 2020). Furthermore, the analysis revealed that another possibility for governments is to set up initiatives and alliances in which, under political pressure, companies agree to implement (more) sustainability practices within the SC (Otto Group, 2020).
The data indicate that legal frameworks as minimum requirements come into place when voluntary solutions do not work. According to the analyzed data, there is, for example, new legislation for the delivery sector since 2019 (Otto Group, 2020). This law is intended to improve working conditions in the distribution sector, as they have been massively criticized in recent years, especially in subcontractors. Furthermore, the German government plans a supply chain law that the European Union strives as a common regulation for the entire Union, aiming to make companies more responsible for their SCs (Interview, 2020). Thus, companies can also be held liable for infringements in the deeper SC. Initiatives like these often result in gatekeeper instruments such as Codes of Conduct or a suitable process for selecting suppliers to influence the suppliers' behavior (Busse et al., 2017).
In the Otto Group, this is manifested in the “amfori Business Social Compliance Initiative” (BSCI), which is used throughout the industry (Otto Group, 2019). According to the interviewee, the Otto Group wants to maintain long-term partnerships with suppliers and qualifies them through audits and training, which leads to a lack of consistency in non-compliance because so much has been invested in these partnerships (Interview, 2020). Nevertheless, it is still challenging to find suitable suppliers with very high sustainability standards because of the low margins, which already fulfill the supplier selection process and ambitious Codes of Conduct. In addition, the contracts with suppliers will be terminated if they do not comply with the Code of Conduct. For this reason, especially in earlier tiers of SCs, industry solutions or common standards are often developed as minimum requirements through alliances, as the selection of suppliers and training and education would require significantly higher resource input. Besides, these industry solutions offer more attractive margins for the suppliers to seriously and, on a large scale, align themselves with the customers' ideas (Interview, 2020).
Sustainable Risk Management
As mentioned in the chapter about the role of drivers, MO can also be seen as an inspector when it comes to economic risks because the name of the company is automatically linked to his name, which is why unsustainable behavior is not only negatively linked to the company, but also his person and family and can affect the financial situation of the company and the shareholders (Interview, 2020).
SCM for Sustainable Products
Within SCM for sustainable products, joint innovations and supplier development can be tackled with NGOs in regulatory functions. They participate in the construction of Codes of Conduct or standards and the development of certificate systems and support monitoring, and reporting activities of companies (Riekhof, 2013).
Synthesis of Detected Stakeholder Roles Within SSCM
Table 4 provides an overview which stakeholders could be assigned to which SSCM construct and what particular role they play. The identified stakeholders of the Otto Group are divided into primary and secondary stakeholders to allow further distinction. Together, the results yield meaningful insights into stakeholders' roles within the SSCM debate.
Discussion
Since little research focused on a more differentiated view regarding stakeholder roles in the context of SSCM, the aim of this case study was to have a broader look. In many SSCM studies (Wolf, 2014; e.g., Meixell and Luoma, 2015), stakeholders are described as drivers that force companies to establish or distance themselves from certain practices or products. By challenging this stigma, this research extends the debate on stakeholders' roles concerning SSCM and how a company responds to them by applying a single case study design.
In general, it is noticeable that various stakeholders exert their influence on different parts of the SC. In contrast to Meixell and Luoma's study (2015), which describes sustainability action mostly as top-down decisions, our findings show that sustainability is more present in the analyzed company's DNA, so various departments consequently implement different sustainability issues. In many cases, these actions are also relevant tasks for secondary groups of stakeholders like alliances, NGOs, or governments. The consequent and fast implementation of sustainability issues may be since sustainability has been part of the Otto Group's core business for a long time and is profoundly established in operational and strategic processes, which is why important issues regarding SSCM can quickly be identified and addressed.
Turning to Table 4, it is noticeable that inspectors were identified most for providing primary and minimum requirements. At the same time, drivers and facilitators were found in the context of more developed and in-depth sustainability issues. This finding might serve as a starting point for further research to scrutinize different stakeholders' allocation and their particular contributions. Other companies could adopt this approach when stakeholder groups are allocated to the various stakeholder roles and how often they occur.
Implementing industry-wide used standards can be seen rather as a complement to the already integrated sustainability practices/standards than an external stakeholder-driven requirement. This could be attributed to the fact that sector-wide standards may achieve greater comparability but do not improve further the processes in terms of content. On the one hand, this facilitates the process for suppliers to identify the criteria they have to meet to be accepted as a possible long-term partner, and shared knowledge within alliances or MSIs can be used to improve sustainability issues, which is in line with the current literature (e.g., Liu et al., 2018; Siems and Seuring, 2021). On the other hand, companies that use a uniform Code of Conduct are better positioned than companies applying individual standards to penetrate deeper SCs by putting pressure on suppliers through industry-wide uniformity.
Furthermore, the present study results could be compared to similar companies to identify similarities and differences and, thus, could serve as an interesting approach for further research. In the analyzed case, the Otto Group already achieved transparency for first-tier suppliers. Currently, the main effort lies in the extension beyond this directly visible horizon, as outlined by Busse et al. (2017). However, it must also be made clear which limitations exist regarding the possibilities for advanced transparency in the SC. First, there are limited resources possessed by a company and the direct suppliers to track the relationships to the suppliers in the next tiers; fostered by a high fluctuation of suppliers in the upstream SC due to prize-driven competition (e.g., Beske and Seuring, 2014). For this purpose, incentive systems could be developed to be able to develop long-term relationships in deeper SCs with the push-pull effect without reducing potential innovation through competition. Secondly, the inherent motivation of the company to reduce uncertainties within the SC could be discussed in further studies.
In line with established literature (e.g., Meixell and Luoma, 2015; Oelze et al., 2016), the analysis revealed that another possibility for governments to trigger more commitment regarding sustainability in the SC in specific sectors, is to set up initiatives and alliances in which, under political pressure, companies agree to implement (more) sustainability practices within the SC.
As a solution for low transparency in SCs and identifying possible risks in the apparel industry (e.g., Hasan, 2019), the results indicate that cooperating with different stakeholders at different stages of the SC provide more insights in several steps and improve the transparency of their own SC. For example, the analyzed company use knowledge and resources gained from cooperation with foundations and NGOs, in line with current papers in the field (Pagell and Wu, 2009; Roscoe et al., 2020; Siems and Seuring, 2021). In deeper SCs, they even cooperate with competitors in the form of alliances and with governments and further NGOs to implement standards like Codes of Conducts and training as well as possibilities to control implemented standards with audits. Further, the focal company faces/targets low levels of SC visibility and identifies sustainability risks with the help of its stakeholder network as described in Busse et al.'s (2017) framework.
The fact that sustainability is firmly anchored in the core business processes can also be traced back to MO. Since the former CEO is present throughout the analysis and assumes various roles, it is worth taking a closer look at his unique role. When MO was still CEO of the focal company, the focal company had not yet experienced any adverse effects from name-and-shame campaigns and has always presented itself as a driving force for the further development of sustainable practices. While the findings contained most of the SCM for sustainable products constructs, the life-cycle assessment was not identified as a relevant issue even outlined in the SSCM discussion (e.g., Beske and Seuring, 2014; Siems et al., 2021). As mentioned before, the focal company shifted the focus from sustainable products toward sustainable values to overcome challenges in the SC from a general perspective and not to deal with problems for single products periodically. For further research, it would be interesting to find out how this focus shifts toward a value orientation than on single products and the special role of MO differs from other companies and how the development of CSR is related to the upper echelons theory (Petrenko et al., 2016). Among other things, this theory attaches great importance to the personal values of management board members regarding the orientation of the company. However, the differences between family-owned companies and corporate groups must also be highlighted, as the loyalty and thus the motivation of top management are different.
In this respect, the philosophy of the Otto Group regarding SSCM can also be well illustrated by the quote, “alone you can go fast, together we can go far” (Interview, 2020, l). This makes it clear that the Otto Group wants to achieve possible successes through joint efforts and that the resources for this are being bundled. From this, it can be concluded that stakeholders can best influence the Otto Group through support in the form of cooperation, the provision of know-how and resources with regard to a more sustainable SC. Nevertheless, empirical qualitative research contains limitations on both the empirical and theoretical sides (Eisenhardt and Graebner, 2007).
On the one hand, there are limitations regarding the quantitative selection of the material. In particular, the fact that only one interview could be conducted could lead to an abbreviated view and result in limited generalization. Additional interviews with different managers, business partners and external stakeholders could have extended the studies insights. For example, the suppliers' point of view is particularly interesting to find out what the Otto Group's requirements mean to them. However, the study's research team conducted further interviews, but the company stated that more interviews were impossible due to limited personal resources.
Moreover, to address the issue of change over time, a comparison of several annual reports might have delivered interesting outcomes. Also, a direct comparison of different companies would have given more insights for further studies. It would also be helpful to conduct more interviews than just one. For that purpose, it would be particularly revealing to interview suppliers to find out how they understand their role. On the other hand, criticism can be made of the qualitative selection of the material, as many internal company materials were examined, which could lead to bias as these sources are not objective. Although we included other external sources (e.g., Riekhof, 2013; Brock and Streubig, 2014), the critic remains that mainly internal sources and perspectives were used, which does not reflect reality in a completely neutral way. In this respect, it would be interesting for a critical classification to include other external sources.
Furthermore, there are limitations to the comparability of stakeholder influence between companies. For example, the Otto Group has a special form of corporate philosophy with longstanding work in sustainability, which also includes the SC. Further, cooperation with stakeholders seems to play an important role. However, this situation cannot be fully transferred to companies with a different structure. Validating how beneficial the Otto Group's approach is for both stakeholders and companies, their way of stakeholder management could be compared to other, differently operating companies. Lastly, although the research was rooted in profound SSCM constructs (e.g., Seuring and Müller, 2008), applying different SSCM or stakeholder constructs might yield additional insights. The outlined papers' limitations provide a basis for further research, both to get a broader picture of possible stakeholder roles and to be able to make more precise predictions about how these can be more efficiently integrated.
Conclusion
The academic contribution of our paper lies in its relevance to the management field. In particular, our research project has highlighted the need for research about the influence of a company's management on sustainable practices and how SSCM practices can differ by implementing a (more differentiated) stakeholder perspective. This field has not gained much attention so far but contains further research potential. Thus, this study answers the research question of understanding which stakeholders and their roles are related to SSCM in the apparel industry. The case study has shown how the Otto Group interacts with its primary and secondary stakeholders at different SC stages to enhance the overall sustainability performance. Thus, this research provides best practices for integrating stakeholders that practitioners can learn from as called for (e.g., Silvestre, 2015, Köksal et al., 2017). For example, the Otto Group intensively communicates with their stakeholders in the whole SC, meets partners at eye level, and seeks to collaborate with non-traditional SC members. Additionally, the Otto Group takes different approaches to have an impact, particularly the upstream tiers, and, thus, takes a multi-tier approach, as suggested by Khurana and Ricchetti (2016). This approach can be a contribution to the debate on the multi-tier SCM field.
Since the case of the Otto Group represents a particular case, the generalizability of the results might be questionable. Thus, the particular results could serve as a starting point for further research on stakeholders and their roles toward a more sustainable SC and, therefore, putting forward the current SSCM debate. However, the described issues and applied practices might help managers achieving a more sustainable SC and follow the call by Wickert et al. (2021) to conduct more research with managerial implications.
Furthermore, the findings indicate that family-owned companies and corporate groups might operate differently, which is in line with Maloni et al.'s (2017) call for research on family businesses SCs. As already mentioned within the limitations, different perspectives from other stakeholders could give further insights. For example, the supplier perspective could be taken into account to validate or oppose the current state. Thus, both the study's limitations and results can serve as the basis for further research. Therefore, we suggest applying a more differentiated view regarding stakeholder roles in the SSCM context and encouraging companies to enhance their degree of stakeholder interaction.
Data Availability Statement
The raw data supporting the conclusions of this article will be made available on request by the authors, without undue reservation.
Ethics Statement
Ethical review and approval was not required for this study with human participants, in accordance with the local legislation and institutional requirements. The participants provided their informed consent to participate in this study.
Author Contributions
All authors have contributed equally to this work and approved it for publication.
Conflict of Interest
The authors declare that the research was conducted in the absence of any commercial or financial relationships that could be construed as a potential conflict of interest.
Publisher's Note
All claims expressed in this article are solely those of the authors and do not necessarily represent those of their affiliated organizations, or those of the publisher, the editors and the reviewers. Any product that may be evaluated in this article, or claim that may be made by its manufacturer, is not guaranteed or endorsed by the publisher.
References
Alvesson, M., and Kärreman, D. (2007). Constructing mystery: empirical matters in theory development. Acad. Manage. Rev. 2007, 1265–1281. doi: 10.5465/amr.2007.26586822
Ansari, Z. N., and Kant, R. (2017). A state-of-art literature review reflecting 15 years of focus on sustainable supply chain management. J. Clean. Prod. 142, 2524–2543. doi: 10.1016/j.jclepro.2016.11.023
Awaysheh, A., and Klassen, R. D. (2010). The impact of supply chain structure on the use of supplier socially responsible practices. Int. J. Op. Prod. Manage. 30, 1246–1268. doi: 10.1108/01443571011094253
Bansal, P., Smith, W. K., and Vaara, E. (2018). New ways of seeing through qualitative research. AMJ 61, 1189–1195. doi: 10.5465/amj.2018.4004
Beske, P., and Seuring, S. (2014). Putting sustainability into supply chain management. Supply Chain Manage. Int. J. 19, 322–331. doi: 10.1108/SCM-12-2013-0432
Brix-Asala, C., Geisbüsch, A.-K., Sauer, P., Schöpflin, P., and Zehendner, A. (2018). Sustainability tensions in supply chains: a case study of paradoxes and their management. Sustainability 10:424. doi: 10.3390/su10020424
Brock, C., and Streubig, A. (2014). “Nachhaltigkeitsmanagement am Beispiel der Otto Group – Herausforderungen, Strategie und Umsetzung,” in Sustainable Marketing Management, eds. H. Meffert, P. Kenning, and M. Kirchgeorg (Wiesbaden: Springer Fachmedien Wiesbaden) 339–357.
Busse, C., Schleper, M. C., Weilenmann, J., and Wagner, S. M. (2017). Extending the supply chain visibility boundary. IJPDLM 47, 18–40. doi: 10.1108/IJPDLM-02-2015-0043
Carter, C. R., Rogers, D. S., and Choi, T. Y. (2015). Toward the theory of the supply chain. J. Supply Chain Manag. 51, 89–97. doi: 10.1111/jscm.12073
Christopher, M., Lowson, R., and Peck, H. (2004). Creating agile supply chains in the fashion industry. Int. J. Retail Distrib. Mgt. 32, 367–376. doi: 10.1108/09590550410546188
Clarkson, M. E. (1995). A stakeholder framework for analyzing and evaluating corporate social performance. Acad. Manage. Rev. 20, 92–117. doi: 10.5465/amr.1995.9503271994
Cotton made in Africa (2021). Available online at: https://cottonmadeinafrica.org/ (accessed June 12, 2021).
CSR in Deutschland (2014). Die Preis-trä-ger 2014-Otto Group. Available online at: https://www.csr-in-deutschland.de/DE/CSR-Preis/Rueckblick/CSR-Preis-2014/Preistraeger-2014/Otto/otto.html (accessed June 22, 2021).
Eisenhardt, K. M., and Graebner, M. E. (2007). Theory building from cases: opportunities and challenges. AMJ 50, 25–32. doi: 10.5465/amj.2007.24160888
Eisenhardt, K. M., Graebner, M. E., and Sonenshein, S. (2016). Grand challenges and inductive methods: rigor without rigor mortis. AMJ 59, 1113–1123. doi: 10.5465/amj.2016.4004
Elkington, J. (1998). Partnerships fromcannibals with forks: the triple bottom line of 21st-century business. Environ. Qual. Manage. 8, 37–51. doi: 10.1002/tqem.3310080106
Fisher, G., and Aguinis, H. (2017). Using theory elaboration to make theoretical advancements. Org. Res. Methods 20, 438–464. doi: 10.1177/1094428116689707
Fritz, M. M., Rauter, R., Baumgartner, R. J., and Dentchev, N. (2018). A supply chain perspective of stakeholder identification as a tool for responsible policy and decision-making. Environ. Sci. Policy 81, 63–76. doi: 10.1016/j.envsci.2017.12.011
Gioia, D. A., Corley, K. G., and Hamilton, A. L. (2013). Seeking qualitative rigor in inductive research. Org. Res. Methods 16, 15–31. doi: 10.1177/1094428112452151
Gold, S., and Schleper, M. C. (2017). A pathway towards true sustainability: a recognition foundation of sustainable supply chain management. Eur. Manage. J. 35, 425–429. doi: 10.1016/j.emj.2017.06.008
Hasan, R. (2019). Modern Slavery in global apparel supply chain: an important research agenda. JTSFT. 3, 1–4. doi: 10.33552/JTSFT.2019.03.000559
Hofmann, H., Busse, C., Bode, C., and Henke, M. (2014). Sustainability-related supply chain risks: conceptualization and management. Bus. Strat. Environ. 23, 160–172. doi: 10.1002/bse.1778
Kassarjian, H. H. (1977). Content analysis in consumer research. J. Consum. Res. 4:8. doi: 10.1086/208674
Khurana, K., and Ricchetti, M. (2016). Two decades of sustainable supply chain management in the fashion business, an appraisal. J. Fashion Mark. Manage. 20, 89–104. doi: 10.1108/JFMM-05-2015-0040
Köksal, D., Strähle, J., Müller, M., and Freise, M. (2017). Social sustainable supply chain management in the textile and apparel industry—a literature review. Sustainability 9:100. doi: 10.3390/su9010100
Liu, L., Zhang, M., Hendry, L. C., Bu, M., and Wang, S. (2018). Supplier development practices for sustainability: a multi-stakeholder perspective. Bus. Strat. Env. 27, 100–116. doi: 10.1002/bse.1987
Locke, K., Golden-Biddle, K., and Feldman, M. S. (2008). Perspective—making doubt generative: rethinking the role of doubt in the research process. Organ. Sci. 19, 907–918. doi: 10.1287/orsc.1080.0398
Maloni, M. J., Hiatt, M. S., and Astrachan, J. H. (2017). Supply management and family business: a review and call for research. J. Purchas. Supply Manage. 23, 123–136. doi: 10.1016/j.pursup.2016.12.002
Masson, R., Iosif, L., MacKerron, G., and Fernie, J. (2007). Managing complexity in agile global fashion industry supply chains. Int. J. Logist. Manage. 18, 238–254. doi: 10.1108/09574090710816959
Mayring, P. (2015). Qualitative Inhaltsanalyse: Grundlagen und Techniken. Weinheim, Basel: Beltz Verlag.
Meixell, M. J., and Luoma, P. (2015). Stakeholder pressure in sustainable supply chain management. Int. J. Phys. Distrib. Logist. Manage. 45, 69–89. doi: 10.1108/IJPDLM-05-2013-0155
Mitchell, R. K., Agle, B. R., and Wood, D. J. (1997). Toward a theory of stakeholder identification and salience: defining the principle of who and what really counts. Acad. Manage. Rev. 22, 853–886. doi: 10.5465/amr.1997.9711022105
Oelze, N., Hoejmose, S. U., Habisch, A., and Millington, A. (2016). Sustainable development in supply chain management: the role of organizational learning for policy implementation. Bus. Strat. Env. 25, 241–260. doi: 10.1002/bse.1869
Otto Group (2021). Über Uns-Daten und Fakten. Available online at: https://www.ottogroup.com/de/ueber-uns/daten-fakten/Kennzahlen.php (accessed September 20, 2021).
Pagell, M., and Wu, Z. (2009). Building a more complete theory of sustainable supply chain management using case studies of 10 exemplars. J. Supply Chain Manage. 45, 37–56. doi: 10.1111/j.1745-493X.2009.03162.x
Parmar, B. L., Freeman, R. E., Harrison, J. S., Wicks, A. C., Purnell, L., Colle, S., and de (2010). Stakeholder theory: the state of the art. Acad. Manage. Ann. 4, 403–445. doi: 10.5465/19416520.2010.495581
Parmigiani, A., Klassen, R. D., and Russo, M. V. (2011). Efficiency meets accountability: performance implications of supply chain configuration, control, and capabilities. J. Operat. Manage. 29, 212–223. doi: 10.1016/j.jom.2011.01.001
Petrenko, O. V., Aime, F., Ridge, J., and Hill, A. (2016). Corporate social responsibility or CEO narcissism? CSR motivations and organizational performance. Strat. Manage. J. 37, 262–279. doi: 10.1002/smj.2348
Riekhof, H.-C. (2013). Retail Business: Perspektiven, Strategien, Erfolgsmuster. Mit Fallstudien und Praxisbeispielen von Aldi, Budnikowsky, Dell, Görtz, Hugo Boss, Keen On fashion, Kiehl's, Lush, Otto Group, Sport Scheck, Takko. Dordrecht: Springer.
Robledo, P., and Triebich, M. (2020). Position Paper on Transparency. Available online at: https://cleanclothes.org/file-repository/transparency_position_paper_ccc_2020-10-15.pdf/view (accessed September 20, 2021).
Rodríguez, J. A., Giménez Thomsen, C., Arenas, D., and Pagell, M. (2016). NGOs' initiatives to enhance social sustainability in the supply chain: poverty alleviation through supplier development programs. J. Supply Chain Manage. 52, 83–108. doi: 10.1111/jscm.12104
Roscoe, S., Subramanian, N., Prifti, R., and Wu, L. (2020). Stakeholder engagement in a sustainable sales and operations planning process. Bus. Strat. Env. 29, 3526–3541. doi: 10.1002/bse.2594
Saunders, M., Lewis, P., and Thornhill, A. (2009). Research Methods for Business Students. Harlow: Financial Times Prentice Hall.
Seuring, S., Brix-Asala, C., and Khalid, R. U. (2019). Analyzing base-of-the-pyramid projects through sustainable supply chain management. J. Clean. Prod. 212, 1086–1097. doi: 10.1016/j.jclepro.2018.12.102
Seuring, S., and Müller, M. (2008). From a literature review to a conceptual framework for sustainable supply chain management. J. Clean. Prod. 16, 1699–1710. doi: 10.1016/j.jclepro.2008.04.020
Shahbandeh, M. (2021). Global Revenue of the Apparel Market, 2012-2025. Available online at: https://www.statista.com/forecasts/821415/value-of-the-global-apparel-market (accessed June 22, 2021).
Siems, E., Land, A., and Seuring, S. (2021). Dynamic capabilities in sustainable supply chain management: an inter-temporal comparison of the food and automotive industries. Int. J. Prod. Econ. 236:108128. doi: 10.1016/j.ijpe.2021.108128
Siems, E., and Seuring, S. (2021). Stakeholder management in sustainable supply chains: a case study of the bioenergy industry. Bus. Strat. Env. doi: 10.1002/bse.2792. [Epub ahead of print].
Silvestre, B. S. (2015). A hard nut to crack! Implementing supply chain sustainability in an emerging economy. J. Clean. Prod. 96, 171–181. doi: 10.1016/j.jclepro.2014.01.009
Sreejesh, S., Mohapatra, S., and Anusree, M. R. (2014). Business Research Methods. Cham: Springer International Publishing.
Stuart, I., McCutcheon, D., Handfield, R., McLachlin, R., and Samson, D. (2002). Effective case research in operations management: a process perspective. J. Operat. Manage. 20, 419–433. doi: 10.1016/S0272-6963(02)00022-0
Weber, C., Rövekamp, G., Grewe-Salfeld, M., and Kruse, D. P. (2020). Kooperieren für die Nachhaltigkeit - Handbuch zu Strategien und Erfolgsfaktoren am Beispiel der Textilindustrie. Hamburg: Otto Group.
Wickert, C., Post, C., Doh, J. P., Prescott, J. E., and Prencipe, A. (2021). Management research that makes a difference: broadening the meaning of impact. J. Manage. Stud. 58, 297–320. doi: 10.1111/joms.12666
Wolf, J. (2014). The relationship between sustainable supply chain management, stakeholder pressure and corporate sustainability performance. J. Bus. Ethics 119, 317–328. doi: 10.1007/s10551-012-1603-0
Keywords: sustainable supply chain management (SSCM), stakeholder roles, collaboration, stakeholder engagement, sustainability practices, apparel industry, case study
Citation: Menke C, Hüsemann M and Siems E (2021) Stakeholder Influence on Sustainable Supply Chain Management: A Case Study of a German Apparel Frontrunner. Front. Sustain. 2:735123. doi: 10.3389/frsus.2021.735123
Received: 02 July 2021; Accepted: 10 September 2021;
Published: 12 October 2021.
Edited by:
Damjan Maletic, University of Maribor, SloveniaReviewed by:
Inga Lapina, Riga Technical University, LatviaMichał Adamczak, Poznan School of Logistics (WSL), Poland
Copyright © 2021 Menke, Hüsemann and Siems. This is an open-access article distributed under the terms of the Creative Commons Attribution License (CC BY). The use, distribution or reproduction in other forums is permitted, provided the original author(s) and the copyright owner(s) are credited and that the original publication in this journal is cited, in accordance with accepted academic practice. No use, distribution or reproduction is permitted which does not comply with these terms.
*Correspondence: Erik Siems, ZXJpay5zaWVtc0B1bmkta2Fzc2VsLmRl; orcid.org/0000-0003-4805-6540