- 1Department of Mechanical Engineering, The Global CO2 Initiative, University of Michigan, Ann Arbor, MI, United States
- 2Department of Civil and Environmental Engineering, Center for Low Carbon Built Environment, University of Michigan, Ann Arbor, MI, United States
From technology to policy, the US is thinking about construction differently. The federal government is motivated to address the aging infrastructure across the country, and policy proposals are surfacing that seek green methods of performing this construction. This paper reviews the current status of concrete technology and policy to provide insight into the current state of the art. The scale of CO2 emissions from concrete production and use is elucidated. Current embodied emissions reduction methods show that action can be taken today in small and large projects alike. Additionally, developing concrete technologies offers pathways to reuse and rely on concrete for longer service lifetimes and reduce their lifetime embodied emissions. These concrete technologies must be implemented, and public procurement proves a unique tool to develop a nationwide demand signal for low embodied carbon building materials. Local governments closely interact with concrete producers, state governments oversee large infrastructure projects, and the federal government invests massively in construction. All three levels of government must coordinate for the effective rollout of low embodied carbon construction practices. Disparate policy approaches show successes and pitfalls to developing an effective construction policy that is aligned with climate. Importantly, approaches to addressing the twin challenge of climate change and crumbling infrastructure must consider the whole lifetime of the concrete. Throughout this paper, we examine the sector to highlight current practices and provide a vision for effective implementation.
Introduction
Achieving sustainable construction and operation of the built environment must be a priority to address climate change concerns. The US arena where this is most prominent is replacing deteriorating buildings, roads, bridges, and other infrastructure. The renewal of infrastructure entails the usage of enormous quantities of construction materials, namely concrete and steel. While concrete is a versatile and widely available construction material worldwide, the colossal amount consumed (over 3 tons per person annually) represents a significant concern for global CO2 emissions. At the same time, traditional concrete materials have limitations in their lifetime and performance. As a result, 50% of already repaired infrastructure fails again and requires re-repair (Mather and Warner, 2003).
Furthermore, conventional procurement policies, building codes, and regulations have been slow to prioritize climate over construction expediency. Significant climate impact and worldwide leadership can be achieved by reimagining the materials used in infrastructure regeneration while simultaneously rethinking the methods of procuring and utilizing such materials. This paper will discuss societal needs, technical details, and regulatory considerations needed to simultaneously address the twin challenge of climate change and crumbling infrastructure.
Concrete surrounds us daily, but concrete-related CO2 emissions occur far offsite making them easy to overlook. Cement, the binding element in concrete, is a good example. In 2019, the IEA showed that cement production accounted for 7-8% of global anthropogenic CO2 emissions (Miller et al., 2016; IEA, 2020). Concrete is the second most used resource on earth after water, with a globally estimated 26 billion tons produced annually (Curry and USGS, 2020). Projections show no significant slowdown until 2050 (Czigler et al., 2020). Given the scale of this industry and its emissions, serious consideration must occur on how emerging technologies can reshape this industry.
In the United States, infrastructure is the most prominent place where concrete is used. The American Society of Civil Engineers (ASCE) has produced an infrastructure report card and given the US a C-in its current infrastructure. For example, they specifically show that a majority of the 600,000 bridges are in fair condition, but 8% are in poor condition and are structurally deficient (ASCE, 2021). Now, infrastructure renewal could emit 200 million tons of CO2 (Dell, 2020).
Recent developments demonstrate opportunities to turn CO2 into a valuable resource for concrete production and leverage permanent carbon sequestration through the expanding construction sector (Fernández Bertos et al., 2004). Along with this thinking, innovations are sprouting in academia and industry that attempt to maximize concrete CO2 uptake while addressing technical needs in various markets (Zhang et al., 2017). The science behind concrete carbon sequestration is built on a series of thermodynamic downhill processes that mineralize CO2 from gas or liquid form into solid carbonates, thus forming an integral part of the final material. By intervening in multiple stages of the conventional product line, concrete carbon sequestration shows the viability of partially offsetting material embodied carbon and has been demonstrated at lab/pilot scale and emerging commercially.
Beyond conventional concrete, R&D efforts are undertaken on utilizing CO2 to facilitate more durable applications for lowering operations and maintenance (O&M) emissions. The immense need for the built infrastructure renewal is driven partially by the expected natural aging, but more commonly and aggressively by premature deteriorations occurring ahead of their designed service life. Breakdown occurs due to unforeseen cracking and the entrance of harmful species. The lack of infrastructure durability drives persistent demands for repetitive repair and rebuild that consume significant cement produced globally. Therefore, deploying materials that are not only more environmentally friendly but also last longer becomes unprecedentedly crucial. In this context, novel materials, particularly Engineered Cementitious Composites (ECC), open a new avenue to make use of CO2 for enhanced infrastructure durability (Li, 2019). ECC can take up CO2 like conventional concrete; however, ECC also uses captured carbon to assist in material crack control, damage tolerance, healing, and restoring its engineering functions during its lifetime. Implementing carbon-sequestered ECC as a highly durable concrete facilitates a zero-maintenance infrastructure system and simultaneously addresses embodied carbon and maintenance emissions.
To produce the desired reductions in embodied emissions requires a journey along a pathway. An illustrative roadmap is shown in Figure 1. Several of the key factors are shown in the figure that are pivotal to reach the ultimate goal of reduced emissions. Research provides methods of reducing emissions. Partnerships are needed to bring new methods out of the laboratory and into practice. Communication is needed to share new and successful methods and gain buy-in more broadly. The following steps lead to the development of policies that incentivize or mandate the use of lower embodied carbon construction methods. Finally, with policies and technologies in place, embodied emissions can be reduced at scale.
Concrete Technology
The Scale of Concrete Embodied Emissions
The global concrete industry emits 2.7 billion tons of CO2 every year, equating to 7-8% of anthropogenic CO2 emissions (Miller et al., 2016; IEA, 2020). Among the necessary ingredients for making concrete, Portland cement (PC) accounts for more than 90% of the total carbon and energy footprints. The carbon emissions of Portland cement production originate in two comparable sources: (1) calcination of limestone that releases CO2 from the calcium carbonate, and (2) fuel consumption for heating kilns to up to 1,450°C. Both sources are challenging to lower substantially in a short timeframe. As the expanding construction market drives concrete production to grow steadily, concrete as the most used construction material faces a pressing challenge for emission reduction.
Efforts have occurred in past decades for reducing the use of PC in concrete. This is commonly associated with the incorporation of supplementary cementitious materials (SCMs) as partial PC substitution (Lothenbach et al., 2011). Most SCMs are from industrial byproducts or low-cost natural minerals and have notably lower emission footprints than PC. Their chemical interaction with PC's hydration products, known as a pozzolanic reaction, could lead to comparable concrete strength even at a lowered PC usage. Byproduct-derived SCMs may be subjected to the variation of composition and property, and their availability may become uncertain as the upstream industry evolves. For example, coal fly ash as a commonly used SCMs is faced with an increasing shortage as less coal is burned for energy in certain regions. In this context, virgin materials from natural resources are being developed for SCMs, such as the blend of limestone and calcined clay (Scrivener et al., 2017). Despite the efforts in promoting increasing percentages of SCM incorporation, PC is still the cornerstone for concrete formulations due to the well-established experience, standards, and market confidence.
Another major emission source in the concrete industry is the drastic maintenance-related carbon dioxide through the use phase. Relative to the lengthy design service life of the built environment, concrete is not as durable as desired. This incurs repeated repair, thus significant intensities of resources, energy, and carbon emissions. The lack of durability stems from the unpredictable concrete cracking. Large cracks ubiquitously found in concrete structures create accessible pathways for harmful species (e.g., chloride and sulfate) to migrate into the concrete interior, thus accelerating concrete deterioration and steel rebar corrosion. Unfortunately, due to the intrinsic brittleness of concrete, there is a lack of strategies that effectively control cracks. As a result, the growing market for repair and reconstruction accounts for over half of total concrete consumption (EPA, 2018), representing a significant hurdle for sustainable infrastructure renewal.
Currently Available Technology
It is becoming more apparent that concrete can actually serve as a carbon sink. In the past years, technologies are thriving at different scales for turning CO2 into solid products and permanently sequestering CO2 in concrete. The precast industry is taking the lead based on the development of carbonation curing (Zhang et al., 2017). Under the designed condition, CO2 from industrial waste flue gas reacts with the metal cations in cementitious materials and forms mineral carbonates in concrete. This process accelerates the strength gain of hydraulic binders (such as PC) and thus speeds up the precast manufacturing by utilizing CO2. Carbonation curing provides additional opportunities for certain latent binders that do not gain sufficient strength by hydration alone. Their latent cementing ability can be activated by CO2 and turned into carbonate-based PC-free products. This includes the technologies from Carbon Built and Solidia based on hydrated lime and calcium silicate, respectively.
Beyond the precast industry, innovations occur in the cast-in-place applications via two routes, (1) pre-carbonation of concrete ingredients and (2) mixing fresh concrete with CO2 gas. The former is based on carbon mineralization in alkaline waste streams and natural minerals, such as steel slags and cement pastes contained in waste concrete. The carbonated materials have been used as non-cementing ingredients (e.g., coarse/fine aggregates) for new concrete production. Emerging companies, such as Carbon8 system, Carbon Free, and Blue Planet, are leading commercial developments in this domain. The second approach is based on CO2 mixing by injecting CO2 gas into a mixing truck where the fresh concrete is mixed steadily. CO2 reacts with cement to precipitate calcium carbonate that improves concrete strength. Consequently, the cement usage could be lowered for achieving the same grade of concrete compressive strength. Carbon Cure Technologies is driving the commercial efforts of CO2 mixing.
It can be seen from the current concrete CCUS technologies that the intrinsic concrete brittleness and lack of durability leading to repeated infrastructure repairs persist even though CO2 could be sequestered. This means that the lifecycle performance is uncertain regarding the infrastructure renewal based on current CCUS technologies (Ravikumar et al., 2021). The opportunity of renewing the large-volume material-flow infrastructure for a more sustainable built environment may be lost.
Ongoing Research/Carbon-Sequestered ECC
Engineered cementitious composites (ECC) is a novel class of fiber-reinforced concrete (Li, 2019). It is known as bendable concrete for its metal-like behavior under bending. In stark contrast to traditional concrete, ECC has two orders of magnitude higher tensile ductility and an intrinsic ability to control the crack width. ECC exhibits multiple hairline cracks when loaded in tension instead of few large cracks commonly found in traditional concrete. The incorporation of microfibers induces the fiber bridging across the microcracks, which continue carrying loads even in a cracked state. Over the past decades, ECC has been used in a broad realm spanning high-rise buildings, bridges, highways, and repair applications.
ECC differs from conventional concrete in its outstanding durability led by the robust crack width control. The tight crack width is a built-in material property irrespective of the imposed load. This quality means that no steel reinforcement is necessary for crack control for ECC infrastructure. As the ingress of harmful water-borne species is governed by the crack width, ECC shows low permeability and superior longevity for structures under mechanical and environmental loads. The tight cracks also promote self-healing, an intrinsic ability of cementitious materials to seal crack damages with mineral precipitates and to regain its mechanical properties. Lifecycle assessments on a concrete bridge show that ECC may lower use phase CO2 emissions by 50% due to the reduced need for repeated repairs and the associated traffic interruptions (Keoleian et al., 2005).
ECC offers an opportunity for CO2 sequestration. Ongoing studies at the University of Michigan's Center for Low Carbon Built Environment (CLCBE) demonstrated that ECC permanently sequesters 30% CO2 by cement mass through precast carbonation curing and 4% CO2 by ECC mass by incorporating carbonated ingredients for cast-in-place applications. The CO2-sequestered ECC exhibited comparable crack control capability and durability to regular ECC, while lowering the embodied carbon substantially. These studies demonstrate a solution of converting CO2 into durable construction materials and reducing embodied and maintenance carbon simultaneously for the built environment.
Concrete End of Life
Infrastructure renewal incurs another challenge associated with the construction and demolition wastes (CDW), among which more than 65% is attributed to crushed concrete (EPA, 2018). As a human-made geomaterial, concrete is non-degradable and persists in the natural environment. Efforts have been made in recycling crushed concrete as aggregate for new concrete production to divert this large-volume waste stream into a valuable resource. The recycled concrete aggregate (RCA) comprises of cementitious pastes and the aggregate initially mixed into the concrete. The former contains hydrated CaO-bearing phases (e.g., calcium hydroxide and calcium silicate hydrates) that can be carbonated for CO2 sequestration. Recent studies show that after carbonation RCA develops a denser paste-aggregate interfacial transition zone, thus a stronger bond with the new cement paste (Tam et al., 2020).
Beyond crushing and recycling concrete debris, ideally, concrete end-of-life could be wholly avoided by re-utilizing the structural components for new construction. This idea prompted ongoing research of the ECC-based Reco-Blox for next-generation zero-waste construction at CLCBE (Bao and Li, 2020). The ECC Reco-Blox is inspired by Lego blocks that assemble standard unit pieces into any type of structure. Steel bolts may be needed to secure mechanical connections between adjacent blocks to ensure structural integrity and loading-carrying capacity. The Reco-Blox is designed to be dissembled after the structural end-of-life and reassembled for another structure, such that no material waste is generated. This concept has been demonstrated by the assembly, load-testing, and disassembly of a prototype footbridge. Subsequently, the blocks were reconfigured and assembled into a prototype building frame. Traditional concrete as a brittle material is difficult to fulfill the requirement for Reco-Blox and tends to fail by uncontrolled cracks at the bolted connections. The use of ductile ECC can resolve this issue and thus extend the block lifetime profoundly. The ECC Reco-Blox can be 3D printed and assembled using robotic systems, which offer a solution for construction automation (Yu et al., 2021).
Concrete Policy
A technically feasible technology is often hampered by regulatory slowdown and lack of local knowledge, thus preventing progress. Recent advances and pilot projects illustrate successes and pitfalls in implementing lower embodied carbon building materials. US city and county governments are taking the first steps because construction is an inherently local endeavor. That is why low embodied carbon concrete (LECC) legislation has appeared nationwide in different local governments. Led by local advocates and experts, these efforts have sprouted activism networks to scale suitable policy activity rapidly. State-level policy initiatives impacting low-carbon concrete are similarly beginning to grow. Proposed policies provide price discounts or set thresholds for permitted embodied carbon in projects. Finally, the federal government can align construction with climate when addressing America's crumbling federally-managed infrastructure. Forthcoming federal action could fundamentally reframe the construction industry's role in addressing climate, and further bolster current policies that support CCUS.
These three levels of government are interdependent and highlight the different methods needed to adopt carbon-sequestering concretes. These three levels and their interactions are illustrated in Figure 2. Additionally, existing policies have provided data about implementing advanced concrete technologies that could significantly reduce the climate impact of the construction sector. This paper will provide best practices from ongoing policy initiatives nationwide and outline how ECC technology offers a unique opportunity for climate action. Governments can serve as market drivers and early adopters of low embodied carbon construction; however, there is a distinct need for creative thinking in how to spur the rapid adoption of low embodied carbon building materials. The following sections of the manuscript will outline the significant existing US-based policies that support methods to, directly and indirectly, support (LECC). Table 1 provides an overview of the highlighted policies across the local, state, and national levels.
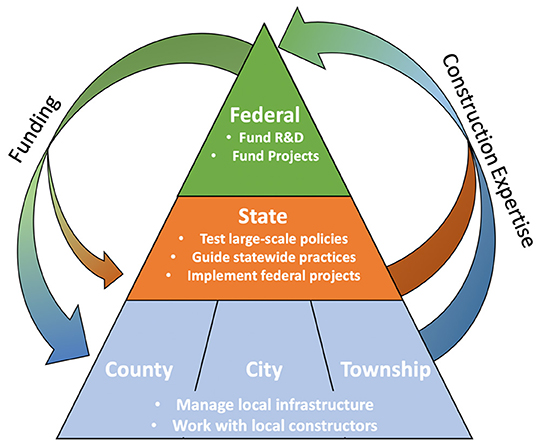
Figure 2. Hierarchy of government interaction surrounding construction. Highlighting the bi-directionality of federal, state, and local policy related to construction.
Private Construction
The government spends about a quarter of the total construction spending in the US, but this leaves significant private construction spending (The U.S. Census Bureau, 2021). This private construction is made up of residential and non-residential (business) development. Between April 2020 and April 2021, residential construction has increased by 29.5%, while non-residential has decreased by 4.8%. This drastic change in construction is mainly due to the COVID-19 pandemic and its influence on the housing market. Addressing non-governmental construction is vital, but this is more challenging because private construction spending is not centralized. Large corporations have begun adopting these practices, and the widespread availability of low carbon concretes will permit the private sector to adapt. Multi-national organizations can also support the dissemination of low carbon concretes worldwide.
Fortunately, several large organizations have become conscious of the embodied carbon footprint of their construction. These organizations have begun developing methods that use LECC for construction projects and consider the embodied emissions in their overall carbon footprints. For example, Microsoft plans to use Carbon Cure Technology's carbon-sequestering concretes to construct their HQ2 in Virginia. Organizations have started investing in the R&D of technologies that reduce embodied emissions. For example, the Durst Organization has developed a public-private partnership called the Building Product Ecosystem that works to popularize low embodied carbon concretes through the use of ground glass pozzolan (Krstic and Davalos, 2019; Kaminsky et al., 2020). Another method for investments into LECC has been corporate purchases of carbon sequestered in concrete. Stripe, an online payment company, has begun making multi-million dollar purchases of carbon as investments into developing carbon removal companies, which have included companies such as Carbon Cure Technology and Carbon Built. Having large corporations begin to invest, procure, and implement low embodied carbon concrete is vital in getting private construction to transition.
Local Government Policy
Construction is innately local. While the cement industry is consolidated with a small group of organizations; concrete producers usually operate within fifty miles of the construction site, given the curing nature of the concrete and the cost of transporting bulk materials. This regionality means that local policies will play a vital role in the deployment of LECC. The challenges of implementing LECC are that there are no universal solutions, and the local availability of materials and expertise must be used to tailor a viable solution. Therefore, local governments must collaborate with local concrete producers, architects, and engineers to support LECC. As illustrated in this section, successful local policies bring local stakeholders together to find viable solutions. This section outlines successful policies that can be adapted to other local governments.
Open Source Sidewalks (Hastings-on-Hudson)
One method to effectively support the adoption of LECC takes the form of a resolution promoting these technologies. However, since this policy method provides no incentives for utilizing LECC, it requires the participation of construction stakeholders and coordination by local decision-makers or activists. A recent example of this is the village of Hastings-on-Hudson in New York State. The “resolution for low-embodied carbon concrete for building and infrastructure projects in the village of Hastings-on-Hudson” states that the village would promote and utilize low embodied carbon concretes where utilization doesn't significantly impact the cost of the construction project and doesn't negatively impact the construction integrity (Hastings on Hudson City Council, 2020).
This resolution has resulted in the creation of a low embodied carbon concrete resources webpage, utilization of LECC for upcoming construction, and the development of a local concrete best practice that will be shared with neighboring villages. This resolution publicly announced the support of the village, but the work of activists with village engineers and local concrete producers has permitted the utilization of these technologies in upcoming RFPs in the village. Also, civil engineers and local stakeholders collaborated to create a concrete mix that uses locally available supplementary cementitious materials (SCMs) and cement mixes to reduce the embodied emissions of concrete. This mix can be used for flatwork, such as sidewalks, and significantly reduce CO2 emissions. The village has continued to highlight these projects in meetings and is working to gain the support of other nearby municipalities. This resolution demonstrates how small local efforts can grow beyond their original limitations.
Low Embodied Carbon Projects (Portland)
Action on low embodied carbon concrete can result once local officials recognize the scale of construction emissions. For example, a 2016 sustainable supply chain analysis of Portland, Oregon, identified construction services as the most significant source of GHG emissions in the city (Trucost, 2016). The analysis outlined goals to develop and implement tactics to reduce city-wide emissions. In 2019, the city developed a low carbon concrete initiative to reduce the global warming potential of concrete used in city construction. The initiative outlined three steps to reducing emissions in construction. Firstly, the city requires the submission of third-party verified environmental product declarations (EPDs) of concrete for city projects with over 50 yd3 of concrete. Secondly, the city performed a pilot project using different low-carbon concrete mixes to obtain performance data. Finally, the resulting data would facilitate the development of a policy that outlines a maximum emissions threshold for all city construction projects. The pilot tested granulated blast furnace slag replacement for cement between 30 and 50% and saw results that suggested that it could be effectively used for sidewalks and other construction purposes. These cement replacements reduced the global warming potential of poured concrete by 23–34% (Foreman and Palmeri, 2020).
Low Embodied Carbon Code (Marin)
In 2018, the county of Marin, California received grant funds from the Bay Area Air Quality Management District. This funding was aimed at determining effective policy methods to reduce embodied emissions in the built environment. An extensive set of stakeholders across the concrete implementation domain were assembled to address this issue (Community Development Agency, 2019). The team created a set of upper thresholds of embodied emissions of concretes that could be reached with cement reduction or cement substitution (Marin County, 2019). The task force showed that often overdesigned structures would heavily increase the carbon footprint of a project.
In 2019, the Marin County Board of Supervisors adopted the updated building codes, which set a threshold both in the embodied emissions and quantity of cement permitted per cubic yard. The outlined policy is shown in Figure 3. The policy requires the submission of verified EPDs for all county construction, and will use the submitted data to update the thresholds. The method implemented in Marin county permits builders to develop their own method of reducing global warming potential without having the county prescribe the mix design.
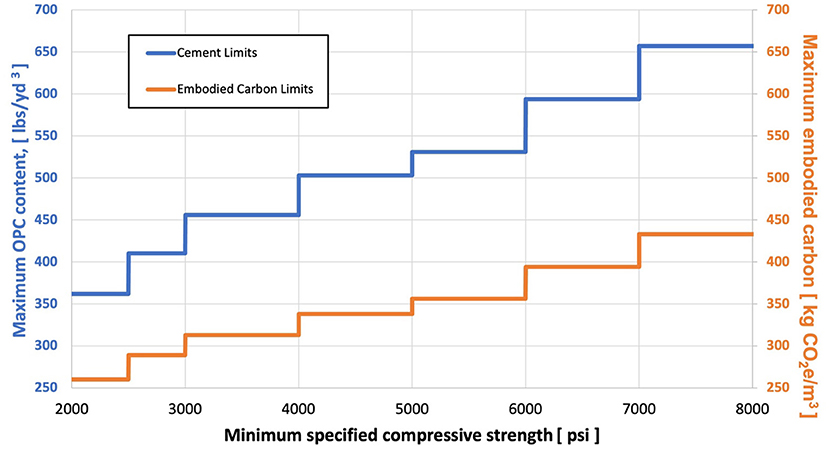
Figure 3. Illustration of Marin County concrete code with both cement limits and embodied carbon limits against the minimum compressive strengths (OPC, Ordinary Portland Cement).
State Government Policy Landscape
Local governments are well-situated to interact with architects, engineers, and constructors at a municipal level, but state governments are often charged with overseeing large-scale infrastructure construction and regulating statewide construction. State-level policies address the construction and repair of roads, bridges, dams, and other infrastructure. State-level Department of Transportations (DOTs) often provide construction guidelines on acceptable construction practices and typically maintain approved construction material lists, continually guiding construction statewide. Therefore, state-level LECC policies can significantly impact the embodied emissions of concrete from public and private construction occurring in a state. Additionally, successful state action can spread to neighboring or allied states and prompt federal action (Rabe, 2018). This spreading of policy ideas remains the case for LECC, as shown in the following sections.
States are in a unique position to implement federal construction projects; they work with local constructors and understand the local limitations of construction. For example, construction seasons in states with cooler climates often have best practices with concrete admixtures that allow construction to occur during seasons where material flow and performance are negatively affected (U.S. Department of Transportation, 2016). Likewise, certain cement substitutes, e.g., SCMs like coal fly ash and granulated blast furnace slag are more widely available in certain regions. This means that state government will be the proving ground for large-scale policies of low embodied carbon concrete.
Buy Clean California
In 2017, the Buy Clean California Act (BCCA) was signed into law (California Legislature, 2017). BCCA was the first of its kind policy that established a method to regulate the embodied emissions of certain construction products for state projects. The policy does not consider concrete as a component of its construction products, but it currently considers structural steel, concrete reinforcing steel, flat glass, and mineral wool board insulation. However, BCCA is implemented such that modifications would permit it to add more materials, such as concrete and wood products.
In 2020, the policy required the submission of EPDs in the procurement process for all outlined materials. This permitted the government to assemble a dataset of the GWP of all requested materials to determine the bounds. In 2021, California used its collected data to publish maximum acceptable GWP limits across the various product categories. These policy efforts have been replicated and introduced as legislation in Washington (Doglio et al., 2018; University of Washington, 2019), Oregon, and Minnesota (Hornstein and Ecklund, 2019), but have not been signed into law. Some of these newly introduced bills extend the eligible materials to include concrete. BCCA and other buy clean policies allow the state government to react to the locally available materials to reduce embodied emissions. The enforcing agency can update the GWP thresholds intermittently to continually reduce embodied emissions.
Low Embodied Carbon Concrete Leadership Act
New York state has taken a leadership role in addressing climate change through state action. This became clear when New York state enacted comprehensive policies to address climate change in the Climate Leadership and Community Protection Act of 2019 (Kaminsky, 2019). This policy did not address embodied emissions in materials. Concurrently, a 2019 policy, the Low Embodied Carbon Concrete Leadership Act (LECCLA), was introduced to address the embodied emissions of concrete. LECCLA creates an incentive structure for reducing emissions for all state-funded construction projects. Similar to previous policies, LECCLA requires the submission of EPDs to evaluate the GWP of different construction. However, LECCLA creates a discount, up to 5%, based on the lowest GWP submissions, rather than setting upper GWP limits. This discount provides an economic advantage for contractors to reduce CO2 intensity, and creates competition between the contractors bidding for a project. Since contractors are unaware of other bids, they can develop the lowest embodied emissions to receive the highest price discount. Additionally, there is a secondary discount, up to 3%, given for new concrete technologies that use CCUS. This second discount provides additional opportunities for concrete producers to invest in implementing and using carbon-sequestering concretes. This policy proposal offers a way for state-funded projects to assign a value to the embodied emissions of concrete. Legislation similar to New York's LECCLA has been introduced in New Jersey (Zwicker, 2021).
Federal Government Policy Landscape
Federal procurement spent $186.5 billion on non-defense contracts in 2018 (Hasanbeigi and Khutal, 2021). In 2012, the US Bureau of Economic Analysis reported about $2.3 billion just for the purchase of concrete, and estimates suggest that this has increased to around $5.2 billion in concrete purchases (Hasanbeigi and Khutal, 2021). The federal government is the single largest purchaser of concrete. However, federal policies occur at such a large scale that they prohibit involvement at the micro-level, where issues of carbon accounting, practices, and implementation can be more challenging. To circumvent this, federal funding is often distributed to state and local governments to perform construction projects; 68% of non-defense funding on goods and services was distributed to state and local governments as grants. Therefore, an effective policy at the federal level must be designed at the purchasing level and allow complementary state and local efforts to facilitate the implementation of low carbon concrete.
Additionally, research and development funding through research agencies such as the Department of Energy, the National Science Foundation, and the Advanced Research Projects Agency-Energy provides significant funding for research into advanced concrete technologies. This provides the federal government a significant lever to influence the climate-responsible construction agenda. One component currently overlooked in the policy realm is the durability of new construction. As outlined in the concrete technology section, federally-funded research has created the development of ultra-durable concretes which can outlast and outperform current practices. These more durable concretes are essential because the elimination of repeated repairs will reduce the lifetime embodied carbon of construction. This suggests that large-scale investment, such as legislation to address infrastructure renewal, could significantly reduce lifetime cost and environmental impact by prioritizing low embodied and durable concrete construction.
Recent policies have provided methods to economically stimulate the development and usage of carbon-storing concretes, and upcoming policy plans to repair federally managed infrastructure strongly highlight low-impact materials. Ongoing research funding for carbon-sequestering concretes and research into the CCU field supports developing these technologies at scale. This section outlines existing and proposed legislation that strongly supports low embodied carbon concretes.
IRS Tax Code: Section 45(Q)
In 2018, the Federal US Government passed the Bipartisan Budget Act of 2018 (Larson, 2018), which included a significant change to Section 45(Q) of the Internal Revenue Service's tax code (Department of the Treasury Internal Revenue Service, 2021). This change modified an existing incentive for the capture and storage of CO2. The newly revised code provides a significant tax credit across three categories of stored or utilized CO2. The framework of the Section 45(Q) policy is illustrated in Figure 4, and are described here in further detail. Firstly, permanent underground storage in saline aquifers gains a credit of $50 per ton. Secondly, the CO2 can be used in enhanced oil recovery, where it has a credit of $35 per ton. Finally, CO2 utilized in beneficial use products earns a credit of $35 per ton. These credits can be received as long as the facility stores more than a specified amount of CO2 per year, as outlined in the tax code. The credit can be claimed for 12 years from the beginning of the carbon capture plant operation.
The beneficial use of CO2 permits large-scale utilization of carbon sequestering concretes to claim a $35 per ton tax credit as long as a single entity stores at least 25,000 tons of CO2 in products every year. This large-scale support could provide an economic stimulus that would ease the adoption of carbon sequestering concrete but will only be accessible to large concrete producers. Large companies such as Carbon Cure have sold technology that has captured almost 100,000 tons since operating with their CO2 sequestering of ready mix concrete (Monkman, 2018). However, a single company would need to verify this utilization to reach the necessary threshold to obtain the 45(Q) credit. Challenges in distributing this quantity of captured carbon and calculating utilized carbon could make verification cumbersome. Economic analysis of the 45(Q) policy suggests that alone it does not provide a large enough incentive to give capture and use CO2 cost-parity with traditional materials (Friedmann et al., 2020). Nonetheless, this policy provides a significant price signal for CO2 and lends itself to cheapen the carbon sequestering concrete technologies.
Another significant challenge is that carbon capture projects must begin construction before January 1st, 2026. Since final regulations were not released until January of 2021, this short time horizon makes it unlikely that many viable projects will materialize in time. This is the case because investors with a significant tax appetite are needed to use the federal tax credit. Bills extending the project timeline, simplifying the monetization of the credit, and increasing the credit value have been introduced in amendment bills (Ryan, 2021), and these amendments are included in the legislation outlined in the proposed legislation section below.
Proposed Legislation
Climate Leadership and Environmental Action for Our Nation's (CLEAN) Future Act
In March 2021, the House Committee on Energy and Commerce introduced the CLEAN Future Act; legislation that seeks to comprehensively address climate issues in the United States (Pallone, 2021). This plan outlines goals to bring US emissions to net-zero greenhouse-gas emissions by 2050. One of the central components of the legislation is a plan to address emissions across the industrial sector, and does so by establishing a federal Buy Clean Program. This version, inspired by state efforts like BCCA, would require the submission of EPDs for all federally funded projects across all federally contracting agencies. This program would initially require EPDs for the following product categories: aluminum, iron, steel, flat-glass, insulation, unit masonry, wood products, and concrete/cement. Following data collection, GWP thresholds will be designated for all the product categories. Given the influence of federal procurement in state and local construction projects, this would rapidly accelerate the use of EPDs and methods to reducing embodied emissions.
Additionally, this bill provides grant funding to reequip industrial facilities with renewable energy and carbon capture technologies. This type of funding could permit cement producers to reduce their industrial emissions and lower the embodied energy of cement. These investments in reducing industrial emissions provide pathways to decarbonize the source cement while providing incentives to reduce cement utilization and support carbon utilization.
Storing CO2 and Lowering Emissions (SCALE) Act
In March 2021, Senators and Representatives re-introduced the SCALE Act, which was initially introduced in the previous congress (Veasey, 2021). This bill addresses three critical aspects of the deployment of CCUS in the United States. Firstly, the SCALE Act supports the deployment of transport CO2 infrastructure, namely through pipelines. This investment is needed to make CO2 feedstock available, which will be important in spreading the use of carbon sequestering concretes. This investment works in conjunction with the 45(Q) tax credit to facilitate the development of large CO2 sequestration and utilization projects. Secondly, this policy supports the development of regional hubs for geologic carbon sequestration in saline aquifers. Finally, this policy supports state, local, and public utility investment in CCU products through a grant program. These grants allow the purchase of goods that are derived from anthropogenic emissions. The proposal offers upwards of $64 million yearly to purchase these goods to grant applicants. Carbon sequestering concrete is one available good derived from CO2, and this grant will support local and state governments to invest in this technology.
American Jobs Plan
The presented American Jobs Plan (AJP) outlines President Biden's plan to address infrastructure and reimagine the American economy (White House, 2021). This plan provides a holistic view of how the Biden administration hopes to address the crumbling infrastructure. Still, political realities make it unlikely to pass as introduced by the White House. Nonetheless, the Biden Administration's work in highlighting low embodied carbon concretes and supporting the CCUS field merit discussion. The proposal aims to repair 10 of the most economically significant bridges and modernize 20,000 miles of highways, roads, streets across the country. This proposal outlines the usage of massive amounts of concrete to fix and replace this infrastructure. The proposal also prioritizes procurement of US-made low-carbon and innovative building materials in service of these replacements.
Additionally, the AJP expands the Section 45(Q) tax credit to provide a direct payment option and simplifying methods of receiving the credit for hard-to-abate sectors. The plan also creates a new government agency known as the Advanced Research Projects Agency—Climate (ARPA-C), which will fund R&D for utility-scale renewables, CCUS, advanced nuclear, hydrogen, and other valuable research areas needed to address climate. Both of these investments facilitate the deployment of carbon sequestering concretes.
While the political viability of the AJP remains in question at the time of the writing of this manuscript, the plan highlights a consciousness of the importance of considering low embodied carbon building materials and provides significant funding to procure these materials. Additionally, the investment builds a nationwide network of constructors familiar with LECC as they service federal jobs. While bi-partisan legislative action may be hard to accomplish, methods described within the AJP can be directly implemented into the executive agencies. For example, practices to reduce embodied emissions could be implemented within the Department of Transportation provided guidance from the President.
Actionable Recommendations For Policy
Lessons From Local Government
Local government policy highlights the need to have a wide variety of ways to reduce embodied emissions. The mixed availability of different SCMs, carbonation curing technologies, well-graded aggregates, and low-carbon cements makes local considerations vital to widespread carbon reductions. Certain cities do not have access to affordable coal fly ash, slag cement, or ground glass pozzolan based on local industries; these cities must be provided alternative options to allow them to reduce embodied emissions. The most effective way of doing this is to regulate construction using performance-based building codes rather than prescriptive building codes. This allows different builders, designers, and engineers to reduce emissions using locally available materials and methods. This means setting embodied carbon as a priority, but not forcing the widespread use of a single method of carbon reduction. Inherent in this approach is the comprehension that nationwide efforts will rely on the expertise of local constructors.
One standardized tool needed nationwide is accounting for embodied carbon, and EPDs exist for this purpose. Initially, the use of EPDs may be difficult for municipalities to request. However, statewide and nationwide policies can assist in the adoption of EPDs across the construction sector. Because EPDs have a high initial cost, it may become necessary for policies to support initial investment costs, and to support the constructors as they implement these new practices. Tools, such as the Embodied Carbon in Construction Calculator (EC3), provide widespread access to EPDs for designers and builders.
Lessons From State Government
State governments have demonstrated leadership in tackling the issue of embodied emissions in materials. Both BCCA and LECCLA policies provide unique and effective policy frameworks to reduce embodied emissions of state government construction. BCCA allows the state to directly regulate embodied emissions thresholds, while LECCLA provides a bid advantage for the lowest embodied carbon concrete mixes. However, neither of these policies is currently implemented to reduce embodied emissions of concrete. Both of these policies have been introduced in other states and have the potential for federal implementation.
If implemented widely, these policies will stimulate the adoption of low embodied carbon materials in their respective states. Neither policy provides a strong tool that would incentivize private construction to adopt LECC. LECCLA bid discounts and BCCA thresholds only apply to state construction, but both help provide access to EPDs. These policies could be supplemented with policy incentives that support private adoption of low embodied carbon building practices.
Lessons From Federal Government
The federal government is the single largest purchaser of concrete in the United States. This gives it the potential to make a demand signal for LECC that will reshape the nationwide construction. However, federal policymakers have several additional levers to shape the development and adoption of new concrete technologies beyond federal procurement. Incentive policies such as Section 45(Q) highlight a policy framework that could be used to specifically support carbon-sequestering concretes and carbon capture of cement facilities. These incentives could be tailored to directly work carbon utilizing products, such as concrete, by lowering annual carbon thresholds and providing direct payment. Since a single entity must reach the threshold, they may find it too onerous to distribute CO2 to a network of distributed concrete producers for the small tax credit. Federal funding for R&D in CCUS and concrete also provides a pathway to develop new technologies rapidly, and upcoming research funding centered around CCUS shows that these technologies are strongly supported.
Green procurement is an important piece that policymakers can modify to move LECC from the laboratory to the field quickly. The requirement of nationwide submission of EPDs for federally funded construction would force constructors to take on this practice widely and would allow private constructors to have access to these tools.
For federal infrastructure renewal, there is a strong potential to utilize new concrete technologies to lessen the climate impact of construction and permit for an infrastructure renewal that will not need to be replaced for quite some time. Concrete technologies, such as the engineered cementitious composites, could increase the durability of infrastructure projects while realizing climate goals. Durability needs to be prioritized in infrastructure projects because repeated repairs can prove challenging to perform and continue to increase the amount of maintenance carbon committed to a project, as seen in Figure 5. Since repaired infrastructure often needs further repair, this continuous process continues to add embodied emissions through the project's lifetime. Repairing the bridges, roads, dams is costly both in time and carbon. To extend the lifetime of procured concrete, policymakers can consider methods to make contractors provide a warranty or extend their producer responsibility beyond the completion of construction. Federal contracts would provide a small price increase to assure that producers would stand by their work for a certain product lifetime, and contractors would be responsible for repairs made before the end of the design product lifetime. This would allow contractors to find solutions that would reduce the need for repairs.
CONCLUSION
Sustainable construction methods must be a priority to address climate change concerns. Cement production contributes 7-8% of anthropogenic CO2 emissions, and addressing these hard-to-abate industrial emissions will be vital for a nationwide response to climate change. Additionally, the United States can demonstrate how to rapidly implement next-generation construction technologies with climate-conscious policy. This document provides a comprehensive review of the available concrete technology and policies across the United States to demonstrate the pathways to tackle construction challenges. This issue has become significant in reference to proposed US federal investments into federally managed infrastructure. Trillion-dollar investments into infrastructure are needed to improve their health, but they will have significant associated carbon emissions.
Currently available technologies demonstrate ways to reduce the embodied emissions today. Supplementary cementitious materials, reduced cement utilization, and CO2 sequestration could reduce embodied carbon in concrete. A main technical limitation lies at the lifetime improvement of the low-embodied-carbon materials, particularly considering the emissions associated with the maintenance and repair. Combining low embodied carbon technology with recent developments in extremely durable concrete would reduce the need for repeated repairs while extending construction lifetimes, which would reduce the maintenance emissions of concrete. These technologies are available, but require scaling up and standardization to support industrial adoption. Public policy promoting the reduction in embodied carbon of concrete and operation carbon of concrete infrastructure is needed to bring these technologies to fruition in the United States.
The three levels of government have a significant influence on the construction sector, demonstrating the need for policy to facilitate the adoption of LECC. Additionally, the creation of a collaborative policy environment between the local, state, and national policymakers will be needed to scale low embodied carbon construction quickly. Local governments are well-placed to interact closely with local concrete producers to find what is available regionally. Therefore, local policy can develop expertise needed to realize low embodied carbon projects. These local stakeholders work to promote LECC within their communities in private construction and share best-practices with nearby municipalities. State governments provide a proving ground for LECC because they coordinate large-scale infrastructure projects within their states, and they provide guidance on construction best practices statewide. Two distinct state policy approaches have developed across the United States that directly focus on LECC, and both provide methods to accounting for and gradually reducing embodied emissions in concrete. Finally, the federal government is the single largest purchaser of concrete in the US. This gives it incredible leverage to promoting low embodied carbon practices across its projects. Existing national policy proposals address low carbon materials by promoting CCUS technologies, EPD requirements, and federal carbon thresholds. These inter-dependent levels must develop methods in lockstep because large federal policy initiatives aimed at reducing carbon intensity in construction still require local implementation.
One area of future focus for US policies that has gained less attention in policy proposals is maintenance carbon. The opportunity to create durable construction is of particular importance when addressing a generational rebuild of deteriorating infrastructure. Rebuilding infrastructure is a protracted process, and doing so with methods that require repeated repairs could be costly to the budget, economy, and the environment. R&D surrounding concrete technology, often federally funded, has developed concretes that can resist extreme climates, perform for a longer lifetime, and reduce overall embodied emissions. These technologies should be utilized when replacing crumbling physical capital. Therefore, policymakers should include methods to promote durable concrete utilization in policy proposals; these could include methods such as incentives or federal warranty programs for construction lifetimes.
Author Contributions
LH did most of the background work and analysis of policies while DZ provided most of the sections on concrete materials. VL and VS contributed to all sections. All authors contributed to the conception of the paper and the writing.
Funding
This work was supported by Global CO2 Initiative and the Blue Sky Program by the College of Engineering, and the Department of Civil and Environmental Engineering (for the UM Center for Low Carbon Built Environment). VL and DZ are grateful for the funding support by the US Department of Energy ARPA-e (Award No. DE-AR0001141) at the University of Michigan.
Conflict of Interest
The authors declare that the research was conducted in the absence of any commercial or financial relationships that could be construed as a potential conflict of interest.
Publisher's Note
All claims expressed in this article are solely those of the authors and do not necessarily represent those of their affiliated organizations, or those of the publisher, the editors and the reviewers. Any product that may be evaluated in this article, or claim that may be made by its manufacturer, is not guaranteed or endorsed by the publisher.
References
ASCE (2021). 2021 Report Card for America's Infrastructure. Available online at: https://infrastructurereportcard.org/ (accessed June 15, 2021).
Bao, Y., and Li, V. C. (2020). Feasibility study of lego-inspired construction with bendable concrete. Autom. Constr. 113:103161. doi: 10.1016/j.autcon.2020.103161
Communit Development Agency (2019). Bay Area Low-Carbon Concrete Codes Project. Marin County. Available online at: https://www.marincounty.org/depts/cd/divisions/sustainability/low-carbon-concrete-project (accessed June 15, 2021).
Czigler, T., Reiter, S., Schulze, P., and Somers, K. (2020). Laying the Foundation for Zero-Carbon Cement. McKisney and Company.
Dell, R. (2020). What's at Stake with Buy Clean. Climeworks Foundation Blog. Available online at: https://www.climateworks.org/blog/whats-at-stake-with-buy-clean/ (accessed June 15, 2021).
Department of the Treasury and Internal Revenue Service (2021). Credit for Carbon Oxide Sequestration 4728–4773. Department of the Treasury and Internal Revenue Service.
Doglio, B., DeBolt, R., Macri, N., and Ormsby, T. (2018). State House Bill 2412: Buy Clean Washington Act. Washington Legislature.
Fernández Bertos, M., Simons, S. J. R., Hills, C. D., and Carey, P. J. (2004). A review of accelerated carbonation technology in the treatment of cement-based materials and sequestration of CO2. J. Hazard. Mater. 112, 193–205. doi: 10.1016/j.jhazmat.2004.04.019
Foreman, S., and Palmeri, J. (2020). 2020 Low Carbon Concrete Sidewalk Pilot. Carbon Leadership Forum.
Friedmann, B. Y. S. J., Ochu, E. R., and Brown, J. D. (2020). Capturing Investment: Policy Design To Finance Ccus Projects in the Us Power Sector. SIPA.
Hasanbeigi, A., and Khutal, H. (2021). Scale of Government Procurement of Carbon-Intensive Materials in the U.S. Global Efficiency Intelligence.
Hastings on Hudson City Council. (2020). Resolution for Low-Embodied Carbon Concrete for Building and Infrastructure Projects in the Village of Hastings-on-Hudson. Hastings on Hudson City Council.
Hornstein, F., and Ecklund, R. (2019). State House Bill 0726: Buy Clean Minnesota Act. Minnesota Legis.
Kaminsky, A. (2019). State Senate Bill 6599: New York State Climate Leadership and Community Protection Act. New York State Senate.
Kaminsky, A., Krstic, M., Rangaraju, P., Tagnit-Hamou, A., and Thomas, M. D. A. (2020). Ground-glass pozzolan for use in concrete. Concr. Int. 42, 24–32.
Keoleian, G. A., Kendall, A., Dettling, J. E., Smith, V. M., Chandler, R. F., Lepech, M. D., et al. (2005). Life cycle modeling of concrete bridge design: comparison of engineered cementitious composite link slabs and conventional steel expansion joints. J. Infrastruct. Syst. 11, 51–60. doi: 10.1061/(ASCE)1076-0342(2005)11:1(51)
Krstic, M., and Davalos, J. F. (2019). Field application of recycled glass pozzolan for concrete. ACI Mater. J. 116, 123–131. doi: 10.14359/51716716
Li, V. C. (2019). Engineered Cementitious Composites (ECC): Bendable Concrete for Sustainable and Resilient Infrastructure. Berlin: Springer.
Lothenbach, B., Scrivener, K., and Hooton, R. D. (2011). Supplementary cementitious materials. Cem. Concr. Res. 41, 1244–1256. doi: 10.1016/j.cemconres.2010.12.001
Mather, B., and Warner, J. (2003). Why do concrete repairs fail. Interview held at Univ. of Wisconsin, Dept. of Engrg. Professional Development, MD, WI.
Miller, S. A., Horvath, A., and Monteiro, P. J. M. (2016). Readily implementable techniques can cut annual CO2 emissions from the production of concrete by over 20% Environ. Res. Lett. 11:074029. doi: 10.1088/1748-9326/11/7/074029
Monkman, S. (2018). Sustainable ready mixed concrete production using waste CO2: a case study. Am. Concr. Ins. 330, 163–174.
Rabe, B. (2018). Can We Price Carbon. Cambridge, MA: MIT Press. doi: 10.7551/mitpress/11316.001.0001
Ravikumar, D., Zhang, D., Keoleian, G., Miller, S., Sick, V., and Li, V. (2021). Carbon dioxide utilization in concrete curing or mixing might not produce a net climate benefit. Nat. Commun. 12, 1–13. doi: 10.1038/s41467-021-21148-w
Ryan, T. (2021). House Bill 3538: Coordinated Action to Capture Harmful Emissions Act. US House of Representatives.
Scrivener, K., Martirena, F., Bishnoi, S., and Maity, S. (2017). Calcined clay limestone cements (LC3). Cem. Concr. Res. 114, 49–56. doi: 10.1016/j.cemconres.2017.08.017
Tam, V. W. Y., Butera, A., Le, K. N., and Li, W. (2020). Utilising CO2 technologies for recycled aggregate concrete: a critical review. Constr. Build. Mater. 250:118903. doi: 10.1016/j.conbuildmat.2020.118903
U.S. Department of Transportation. (2016). Use of Supplementary Cementitious Materials (SCMs) in Concrete Mixtures.
Yu, K., McGee, W., Ng, T. Y., Zhu, H., and Li, V. C. (2021). 3D-printable engineered cementitious composites (3DP-ECC): fresh and hardened properties. Cem. Concr. Res. 143:106388. doi: 10.1016/j.cemconres.2021.106388
Zhang, D., Ghouleh, Z., and Shao, Y. (2017). Review on carbonation curing of cement-based materials. J. CO2 Util. 21, 119–131. doi: 10.1016/j.jcou.2017.07.003
Keywords: carbon utilization, infrastructure, concrete, policy, embodied emissions
Citation: Henrion L, Zhang D, Li V and Sick V (2021) Built Infrastructure Renewal and Climate Change Mitigation Can Both Find Solutions in CO2. Front. Sustain. 2:733133. doi: 10.3389/frsus.2021.733133
Received: 29 June 2021; Accepted: 25 October 2021;
Published: 19 November 2021.
Edited by:
Stefano Stendardo, Italian National Agency for New Technologies, Energy and Sustainable Economic Development (ENEA), ItalyReviewed by:
Balkrishna Narkhede, National Institute of Industrial Engineering, IndiaWenqin Li, United States Department of Energy (DOE), United States
Copyright © 2021 Henrion, Zhang, Li and Sick. This is an open-access article distributed under the terms of the Creative Commons Attribution License (CC BY). The use, distribution or reproduction in other forums is permitted, provided the original author(s) and the copyright owner(s) are credited and that the original publication in this journal is cited, in accordance with accepted academic practice. No use, distribution or reproduction is permitted which does not comply with these terms.
*Correspondence: Volker Sick, dnNpY2tAdW1pY2guZWR1