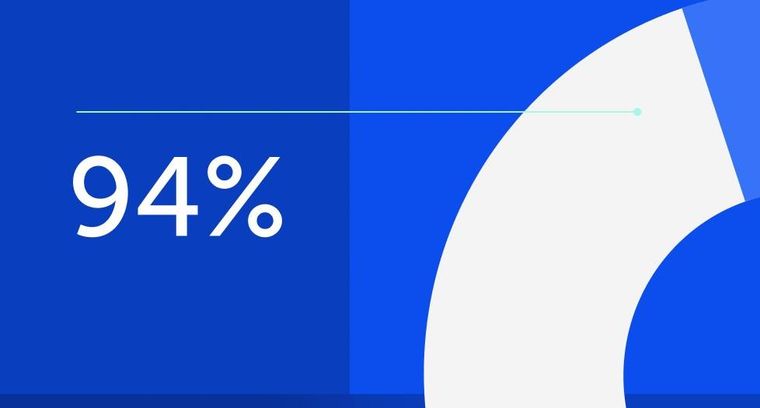
94% of researchers rate our articles as excellent or good
Learn more about the work of our research integrity team to safeguard the quality of each article we publish.
Find out more
REVIEW article
Front. Space Technol., 26 January 2022
Sec. Microgravity
Volume 2 - 2021 | https://doi.org/10.3389/frspt.2021.779696
This article is part of the Research TopicTechnologies for handling, preparation, and liquid-based analysis of fluidic samples in spaceView all 6 articles
Fluid transport and handling in extraterrestrial conditions, i.e. microgravity, require significantly different system engineering than here on Earth. On Earth, a notable part of fluid processing units inherently relies on buoyancy to transport and handle fluids. In space, however, buoyancy effects are negligible due to the strong diminishment of gravity, resulting in the domination of surface tension forces. Surface tension forces are also dominating micro-scale processes in gravity, making microfluidics a promising technology for fluidic transport and handling in microgravity. Recently, three different microfluidics-suitable fluid behavior phenomena have been studied on the ISS that might further facilitate the manipulation of fluids in space: capillary-driven flow, thermocapillary Marangoni forces, and electrolytic gas evolution-driven flow. Furthermore, attention is drawn for strategies to eliminate unwanted bubbles from liquid bodies in space, as they can damage sensitive equipment: Mesh-screen capillarity and open wedge channels have been identified as promising approaches. Finally, the relevance of fluid handling in space is illustrated with everyday activities during space missions, such as drinking, plant watering, and gathering biometric data.
On Earth, fluid handling often relies on gravity-induced effects such as buoyancy and natural convection. Such fluid processing units include apparatuses like bubbles columns, trickle bed reactors, cooling towers, but also phase separators such as decanters or flash drums. However, when moving away from the Earth’s surface, the terrestrial gravitational forces are diminishing with increasing distance to the Earth. The Bond number, a measure for the ratio of gravitational forces to surface forces decreases until the Bond number is <<1. At that point, a fluid system is dominated by surface forces instead of body forces—making gravity and density effects negligible in space and for fluid handling.
For example, the stratification of gases and liquids does not occur spontaneously anymore. This occurrence dramatically complicates fluid handling in space, making a lot of working principles for fluid manipulation useless for space application. Fluid processing apparatuses have to be conceptionally revised in order to be functional for space travel. Effects that come of importance for fluid handling are thermosolutal, phase-change, surface/interfacial tension, and electric/magnetic field forces (Grodzka and Bannister, 1974; Kassemi and Ostrach, 1992). The task of designing appropriate fluid handling equipment might further be complicated due to the fact that the gravitational acceleration experienced in a spacecraft varies with its location, acceleration, and rotation. Variability is also induced by altitude control maneuvers and vibrations from machinery (Kassemi and Ostrach, 1992).
The fluctuating microgravity makes the use of large vessels as well as pipe diameters undesirable, which is also unpopular due to the fact that first, usable volume in a space shuttle is limited, and second, additional weight drastically increases the overall system operating costs and the shuttle launching costs. Recent launch prices (2017) range from roughly 1,500 $USD per kg for the Falcon Heavy (SpaceX) to 3,000–4,000 $USD per kg for many of NASA’s cargo launchers (Zapata, 2017). Therefore, minimizing the volume and weight of the engineered system is certainly required to suppress the overall cost, but also a low power consumption is desirable.
A solution to the requirement of minimizing weight can be derived from learnings about the chemical industry here on Earth in the past decades, where “process intensification” has gained significant interest (Charpentier, 2007; Babi et al., 2016). Combining certain processing steps into one can reduce equipment weight and volume but will also increase overall system complexity. It is to be expected that both in-situ resource utilization and process intensification are of interest for long-term space missions (Hessel et al., 2020; Hessel et al., 2021). Other requirements for chemical systems related to human space travel are those of safety and flexibility. All of these are overcome by microfluidic applications on Earth already. While microfluidics allows for reliable processing of micro-volumes, major problems for a whole space exploration may arise when microfluidics do not function as expected. Furthermore, the high surface-to-volume ratio of small-scale piping ensures efficient mixing of fluids, higher reproducibility of chemical experiments, and increased heat transfer and cooling. It enables reactions to be operated in an enhanced chemical reaction space: at high pressure and temperature (Hessel et al., 2004).
Taking all this into consideration, it becomes clear that microfluidics is potentially a very interesting technology for handling fluids during space travel. Furthermore, applying microfluidic concepts as well as simplifying the overall fluid handling system will suppress the overall cost. Simplifying could be done by aiming for passive fluid handling concepts. A passive liquid delivery method will also drastically reduce the number of contaminable moving parts, all while providing a high-reliability operation.
A combination of active and passive liquid handling would allow to manage different gravitational conditions during space travel. The terrestrial, lunar, and Martian environments are managed in a “gravity-dominated mode”, while the low-gravity transit and orbit environments are managed in a “capillary fluidics mode”, where the role of gravity is replaced by the equally passive effects of surface tension, conduit shape, and wettability.
Density-driven convection does not take place in micro-gravity. Therefore, this effect cannot be relied upon for the mixing of liquids. Mechanical stirring or carefully designed flow reaction chambers need to be used instead. Also, convective heat transport will be inefficient in space, influencing thus heating and cooling process, and altering temperature gradients in liquid bodies. There is still limited data on these issues, which is why many of the current experiments onboard the ISS are designed to further investigate the effect of microgravity on physical and chemical processes. In this context, crewed space stations in low Earth orbit, such as the ISS, are invaluable for investigating the effects of long-term exposure to microgravity, for testing new technologies and devices for monitoring astronauts’ health, but also to translate current Earthly fluid handling applications to space.
As mentioned above, gravity and density effects (e.g., buoyancy) are negligible in space, so other forces such as surface tension and capillary and viscous forces become important, which also makes bubble management challenging. Bubbles can form under various circumstances such as gas being dissolved in a solution, gas being produced by chemical reactions, the evaporation of liquids, or the diffusion of air through seals or porous materials. Bubbles can be a serious hazard in space, as they can damage important equipment. Therefore, bubble management must be considered when designing devices for space application.
This paper, therefore, discusses several interesting fluidic handling concepts that have been tried and tested aboard the ISS in the past. This review consists of concepts which are both micro- and macro-fluidic related as it is meant to introduce the difficulties and opportunities that arise from moving to a low-g environment and the corresponding fluid handling concepts therein. The macro-fluidity arises from the type of experiments done in the ISS. However, all concepts are thought to be applicable in a microfluidic setting. The review starts with a more theoretical discussion on capillary flow, thermocapillary Marangoni forces, electrolytic gas evolution, and bubble entrapment. The second part of this paper moves the focus towards the application of these theories to prove the applicability of said theories and microfluidics. This section will touch on passive gas removal, drinking in microgravity, watering plants in space, biosensors, and electrowetting heat pipes.
Capillary flow occurs both in Space and on Earth when a body of liquid comes into contact with a cavity of a sufficiently small diameter. The resulting capillary force pulls the liquid into and up the cavity due to an interplay of surface tension of the liquid and adhesion between the liquid and the walls of the cavity. As long as the cavity fulfills the diameter prerequisite, the capillary flow occurs spontaneously and without the need for an external force. Microfluidics benefit largely from this effect, decreasing the overall required pumping requirements. For a more fundamental derivation and discussion on microfluidics and capillarity, the reader is referred to “Theoretical Microfluidics” (Bruus, 2006). The capillary flow comes to a halt once the mass of the liquid column results in a gravitational force equal to the capillary force. As the gravitational force is comparatively high on the Earth, the height of a liquid column in a cavity of appropriate diameter is usually within the order of millimeters. On contrary, due to the minimal or negligible gravitational forces and therefore, minimal or negligible hydrostatical pressure in space, the capillary rise of liquid columns of the same diameter can potentially extend over meters. In a perfect weightless environment, the capillary flow could continue indefinitely (given an infinite amount of water and length of capillary, and adhesion). However, in reality, true weightlessness cannot be achieved, and the infinitesimal gravitational forces are further impacted by g-jitter. Furthermore, the lack of gravitational forces also allows capillary flow in cavities of larger diameters than on Earth, thus making this flow principle more versatile in a microgravitational environment than on Earth. Realizing a spontaneous fluid movement of several meters without the use of pumps opens a range of potential applications for capillary flow in microgravity:
1) Capillary forces can be used to drive fluid flow through small wedges and corners, allowing for example the complete drainage of spacecraft fuel tanks to become an effortless process, thereby also increasing the efficiency of propellant resources and easing its management.
2) Capillary structures can be used for life support systems alike water recycling, carbon dioxide removal, and beverage cups, allowing for increased crew health and living comfort (Viestenz et al., 2018; Weislogel and Jenson, 2019).
3) Capillary forces might be beneficial for the design of passive liquid-gas separators, which will further be elaborated on in chapter 3.
Overall, using capillarity as a passive fluid transport and control method can save significant weight and therefore, investment.
However, a few considerations need to be acknowledged before implementing capillary flow in space. First, as shown above, the resulting capillary pull is strongly dependent on the present gravitational acceleration. During a space mission, the shuttle and its crew are exposed to a varying degree of gravitational acceleration due to constant change of the spacecraft’s location, acceleration, and rotation as well as altitude control maneuvers, vibrations from machinery, all resulting in g-jitter (Kassemi and Ostrach, 1992).
Secondly, the systems need to be carefully designed, as so to prevent bubble formation. For illustration, the example of spacecraft fuel tanks mentioned above is utilized. In the ideal case, capillary techniques are employed herein to obtain and preserve a continuous and bubble-free flow from the inlet (bulk) to the outlet (thrusters). Such an application uses vanes for guiding the liquid and can be viewed, albeit a little more abstract, as an open capillary channel with free liquid surfaces. These free liquid surfaces are curved according to the Young-Laplace equation to balance the pressure difference between the flowing liquid and external gas pressure. A change in flowrate will result in a change in free surface curvature. A critical flow rate exists above which the curvature is unable to balance the pressure difference. Above this critical flowrate, the surface collapses, and gas bubbles are ingested in the liquid phase (Canfield et al., 2013). Therefore, to avoid gas ingestion, it is essential to avoid operating conditions at and above a critical flow rate.
To improve the understanding of capillary flow in microgravity for potential spacecraft applications, three capillary channel geometries (parallel plates: PP, groove-shaped channel: GR, and wedge-shaped channel: WE) have been studied in different microgravitational environments. Short-time microgravitational studies include a drop tower (approximately 4.7 s μg) (Dreyer et al., 1994; Rosendahl et al., 2002) and rockets from the TEXUS program (over 5 min μg) (Rosendahl et al., 2004; Rosendahl and Dreyer, 2007; Rosendahl et al., 2010), while long-term studies have been conducted in the ISS, starting in late 2010.
The ISS studies are based on the “Capillary Channel Flow (CCF)” experimental setup, as reported by Canfield et al. (2013) and Conrath et al. (2013a): specific test channels with different cross-sectional shapes (PP, WE, GR) were employed, which allowed obtaining a single free surface by closing one of the sides of the PP setup. The open surface channel length could furthermore be altered by a slide bar. The setup is shown in Figure 1. Using this setup, the critical flow rates for bubble ingestion for steady-state conditions were determined with channel lengths ranging from 1 to 48 mm. The results showed a decrease in critical flowrate with an increase of channel length. Moreover, Canfield et al. also discussed the bubble volumes and ingestion frequencies compared to supercritical flowrates. The results suggested that the ingested volume per bubble is independent of flow rate, while the ingestion frequency displays a strong dependence on flow rate.
FIGURE 1. Several different configurations of capillary channels that have been studied aboard the ISS. (A) Parallel plates, (B) groove, and (C) wedge. The channels have a width a, height b, and a length of free surface l. Reprinted from Conrath et al. (2013a) with permission from APS.
Conrath et al. used data retrieved from the CCF experiments to develop a 1D-model for the steady-state flow between parallel plates (Conrath et al., 2013a). Their model predicts the free surface contours for a parallel plate set-up as well as the critical flowrate for a parallel plate flow. This model agrees well with experimental data for sub-critical flowrates in long channels. A comparison between experimental and modeled critical flowrates is shown in Figure 2. Grah et al. developed a model for the transient capillary channel flow stability and confirmed the accuracy of steady-state models (Grah et al., 2014). They confirmed that numerical predictions of critical steady-state flow rates are possible with high accuracy. For a 3D-model in OpenFOAM, an error of about 5% was observed. The 1D-model resulted in a similar accuracy within a channel length range of 8–19.2 mm, where the error was about 2%. For lengths shorter than 6 mm it was found that the error exceeds 6%. The advantage of the 1D-model over a 3D-model is the computing time. Grah et al. mentioned that the 1D-model is 106 times faster than 3D computations (Grah et al., 2014). Next, a new stability model was provided to reliably predict transient surface stability: A transient model, unlike a steady-state model, also takes the inertia of the accelerated liquid into account.
FIGURE 2. Experimental (diamond) and numerical (lines) results for the dependence of critical flowrate on open channel length. Results from a parallel plate channel set-up. Reprinted from Conrath et al. (2013a) with permission from APS.
In short, the capillary flow phenomenon is of great use for transporting and handling liquids in near weightlessness as it allows for a controllable flow. Also, significant research has been done on Earth and accurate modeling software is becoming available. Using capillary flow can reduce the need for pumps, resulting in a significant decrease of weight, volume, and investment required for system designs. Though, several drawbacks exist. For one, overdesigning of fluidic systems is required as g-jitter is inevitable. Moreover, capillary flow is related to the shape of, and thus pressure difference across, the liquid surface; this means that liquid flow will change if the surface tension and/or shape is altered for any reason. Think of, for example, the addition of a surfactant or a change in temperature (discussed in Section 2.2). It is necessary to take precautions against unwanted and unexpected surface tension changes. Next, capillary flow through an open channel has a critical flowrate above which bubble ingestion will occur, which can wreak havoc on sensitive equipment (discussed in Section 3). Overall, these drawbacks can be overcome by proper design of fluid handling systems.
In general, the Marangoni effect describes a mass transfer that is induced by a surface tension gradient. As the surface tension decreases with increasing temperature, a temperature gradient along the liquid-gas interface can be sufficient to generate a Marangoni effect: The surface tension increases at the lower temperature spots and the liquid will be “pulled” towards this side (Figure 3). When the Marangoni effect is caused by a temperature gradient, it is also referred to as the thermocapillary Marangoni effect. On Earth, however, it is comparatively difficult to observe the thermocapillary Marangoni forces. This as natural convection, caused by changing densities along the temperature gradient, usually predominates the mass transfer. Therefore, the thermocapillary Marangoni effect can best be observed in space, where with diminishing buoyant forces, the thermocapillary Marangoni effect becomes the driving force for convection in presence of a temperature gradient.
FIGURE 3. Schematic overview of a liquid bridge between two plates. (A) shows a small temperature difference and stable flow pattern, whereas (B) has a larger temperature difference resulting in a random flow pattern throughout the liquid bridge.
The thermocapillary Marangoni forces might become of special interest for certain space manufacturing approaches. For example, the semiconductor and rare metals industries might be able to utilize this effect to generate crystals of extremely high purity, as flow disturbances induced by gravitational forces can occur during production on Earth which leads to degradation of the crystal’s quality (Rainey, 2017).
A possible application of Marangoni forces might be impacted by the fact that at high Marangoni numbers, i.e., where mass transport caused by Marangoni forces predominated mass transport caused by diffusion, the flow becomes instable. This will result in temperature instability in the liquid. Effects like these are especially of importance and interest for high Prandtl number fluids, where the momentum diffusivity dominates thermal diffusivity. It is important to understand this behavior when oscillations and fluctuations are unwanted. Referring to the example of producing high purity crystals: Oscillations and fluctuations can induce premature crystal formation in supersaturated fluids or interfere with the desired crystal growth.
As mentioned above, long-term and pure-Marangoni-driven experiments are difficult to properly execute on Earth due to natural convection. Therefore, a series of microgravitational experiments have been performed onboard the ISS, called Dynamic Surf, from September 2013 to November 2016 (Yano et al., 2018a). The Dynamic Surf experiments were designed to understand the role of heat transfer at the liquid-gas interface and its influence on instability mechanisms of the Marangoni convection. The experimental setup consisted of a large-scale liquid bridge (LB) of high-Pr fluids and allowed the realization of pure Marangoni convection without buoyancy effects. During these experiments, the temperatures of the hot disk, cold disk, and ambient gas were changed and changes in the free surface were recorded. Thus, observed dynamic surface deformations could be directly related to instability mechanisms arising from Marangoni convection. Furthermore, the impact of heat transfer at the liquid-gas interface on the Marangoni fluid transport was studied (Yano et al., 2018b).
Yano et al. (2018b) reported that an increase in heat loss due to liquid surface heat transfer to the gas environment destabilizes the Marangoni convection. Furthermore, it was found that both this instability as well as g-jitter affect the free surface deformations, where the Marangoni instability results in oscillation and g-jitter in a much more dynamic motion.
Shitomi et al. (2019) investigated the effect of radiative heat transfer on thermocapillary convection in long liquid bridges of high-Pr fluids in a numerically simulated microgravitational environment using the commercial solver STAR-CCM+. It was found that large heat-loss and large heat-gain conditions generate a secondary flow pattern roll near the cold- and hot disk, respectively. This is shown in Figure 4. This result was obtained with a cold disk temperature of Tc = 27.5°C, a hot disk temperature of TH = 28.9 oC and a wall temperature ranging between TW = 22.5–32.5 oC.
FIGURE 4. Steamlines and temperature color contours for a high-Pr fluid with varying wall temperatures. TC = 27.5°C, TH = 28.9°C. The wall temperatures are (A) Tw = 32.5°C, (B) Tw = 28.9°C, and (C) Tw = 22.5°C. A secondary roll is present in (A) and (C). Reprinted from Shitomi et al. (2019) with permission from Elsevier.
The numerical results of the large heat-loss condition were compared with an experiment performed aboard the ISS. For this, both a liquid bridge with and without radiation effects was numerically investigated, this is shown in Figure 5. Figure 5A shows the temperature distribution of the liquid-bridge free surface as measured by an IR-camera, as well as the particle trajectories measured by a side-view camera. These trajectories were time-averaged and superimposed over 6 min. A cold band and the associated secondary roll, both like those observed in the experiment, were reproduced in the simulation with radiation effects included. Both the cold band and secondary roll were not observed in the simulation without radiation, indicating the importance of the effect of radiative heat loss from the liquid-bridge free surface (Shitomi et al., 2019).
FIGURE 5. Surface temperature distributions (left) and particle trajectories (right) for a high-Pr fluid. The results are obtained in (A) an experiment and (B) a simulation (1) with radiation and (2) without radiation. TC = 27.5°C, TH = 28.9°C, and TW = 25.0°C. Reprinted from Shitomi et al. (2019) with permission from Elsevier.
A better understanding of the Marangoni-force has been gained from experiments performed in low-g environments. Understanding and grasping the Marangoni force is useful for flow applications where temperature differences across surfaces exist. Temperatures affect surface tensions and thus flow through tubes and along walls; hence it affects the previously described capillary phenomenon. The Marangoni force also gives rise to new space manufacturing applications, as briefly touched in this section. Interesting, albeit novel, mixing/transport concepts are possible. However, employing the concept of the Marangoni force -in open channels-appears to be disturbed by flow instability at high Marangoni numbers. Ultimately, this force, seen on Earth as peculiar and somewhat unimportant, can give rise to interesting concepts and opportunities in low-g environments.
Besides altering surface tension for flow, it is also possible to create pressure to force fluid flow. One such idea is the possibility of bubble growth via electrolytic gas evolution.
Charge transfer in the electrolysis experiments takes place at a three-phase interface where the electrolytic gas, electrolyte, and electrode meet. On Earth, these bubbles readily detach from the electrode surface due to buoyancy. This detachment in turn induces macro-convection, complicating the analysis of ion transfer close to the electrode. Even with the lack of macro-convection, fresh electrolyte is constantly presented at the electrode due to micro-convection induces by bubble growth (Matsushima et al., 2003).
One application of electrolytic gas evolution in space could be to generate bubbles to create pressure differentials in microfluidic devices, thereby initiating fluid transport. However, an appropriate bubble removal technology might be required in order to protect sensitive equipment later down the line. Another interesting application of electrolysis in space is of course to produce oxygen for use in spacecraft and future human habitations on the Moon and Mars. Increased understanding of the effects of gravity will help better the design of gas-producing systems, overcoming possible problems. One such problem is that gas bubbles do not readily depart the electrode surface due to the lack of buoyancy forces, which might hinder the practicability of electrolysis equipment. Yet, the lack of buoyancy enables a better investigation into ion transfer and surface effects at the electrode.
Matsushima et al. published several papers about electrolysis under microgravity in the early 2000s (Matsushima et al., 2003; Matsushima et al., 2006). Here, a drop tower was used to obtain the wanted microgravitational environment. This lack of gravity, however, only lasted for 8 s. It was seen that bubble sizes in the microgravity experiments were larger than in terrestrial gravity, due to longer residence time at the electrode. The (time-) limitations of the drop tower can be overcome on the ISS.
Electrolytic gas evolution studies have been performed on the ISS from October 2019 to October 2020. Investigators conducted a comparative study, subjecting samples both on Earth and aboard the ISS to the same electrical conditions. By comparing the Earth and ISS experiments, researchers will gain a better understanding of the contribution of multiple competing effects on gas evolution, such as gravity and buoyancy. However, results have apparently not been published yet, and all information provided in this section is retrieved from the NASA website (Ge, 2020). An image from the Electrolysis Measurement investigation is given in Figure 6.
Rather than purely altering surface tensions, as described in previous sections, this section gave a short insight into how bubble creation can be beneficial for fluid flow. Using electrolysis to create bubbles is considered as an interesting concept to create gases and force flow through equipment. Bubble growth in low-g environments is different from that on Earth due to the, for example, difficulty of bubble detachment and the lack of macro-convection. However, introducing bubbles into liquid streams will require removal of said bubbles later down the line (discussed in Section 3).
Unfortunately, not much has been published yet from the ISS-experiments. We strongly hope that publications of the recently done experiments will become available soon. The mentioning of this idea and short discussion in this sub-section is still of use to have one consider that fluid flow can be altered by not just surface tension effects but also by creating pressure.
To highlight the importance of gas bubble removal, the danger of gas bubbles is shown using the example of storage and transport of fuel. Regarding the storage of fuel, gas and liquid are usually both present in fuel tanks. On Earth, liquid in a tank settles on the bottom to minimize the gravitational potential energy. In space, where the gravitational effects are minimal, the liquid can be distributed within the whole space of the tank and will not always be at the tank outlet. This could mean that gas can pass through the exit, leading to the ingestion of bubbles into equipment. Gas bubbles within a liquid stream can wreak havoc on equipment, in this case specifically pumps that are required to transport the fuel from the tank to the engine can be damaged. The gas bubbles can collapse when they pass from the eye of the pump to the higher-pressure side of the impeller, leading to mechanical deterioration. Furthermore, bubble ingestion will severely lower the capacity of the pump. This example underlines how simple, everyday technologies need to be designed conceptionally differently to be safely applied in space. Other systems affected by a decrease in efficiency due to bubble ingestion are thrusters, life support systems, and other apparatuses. Therefore, understanding when gas ingestion occurs in open channel flow is key. Next to preventive approaches, strategies for bubble-liquid separation need to be developed.
As mentioned above, gravitational forces are negligible compared to surface tension forces, which is characterized by a Bond number of Bo << 1. Therefore, an artificial body force must be employed to achieve gas-liquid separation for an active bubble removal approach. One way to create an artificial body force could be by firing the thrusters in short intervals, however, this will lead to a change in the object’s trajectory and can therefore be unpractical. Another option could be to install a centrifuge on board, yet, centrifuges are known to be heavy, complex, expensive, and will most probably require maintenance during their lifetime, which makes this approach unsuitable for space. Other options for artificial body forces include but are not limited to the likes of electro-magnetic manipulation (Martin and Holt, 2000; Marchetta and Winter, 2010), or manipulating liquids acoustically (Oeftering et al., 2003; Marston and Thiessen, 2004). The last two methods seem viable but do require electronics and hardware, which can fail over time.
A more elegant, space-suitable solution for bubble-liquid removal could consist of a passive approach, as it forgoes an additional, external force and heavy, space-consuming devices. Again, capillary forces can be employed to separate phases (gas-liquid and liquid-liquid, provided the according system parameters are met). To realize capillary flow-driven phase separation, an appropriate combination of system geometry, surface tension, and wetting characteristics need to be found.
When combining the capillary forces with the Young-Laplace pressure, one can see that a small mesh screen could be used to passively separate gas and liquid (Dodge, 1990; Fries and Odic, 2007). An important characteristic of such mesh screens is that the design can withstand a pressure differential from the gas to the liquid side when the mesh is wet. When wet, the mesh will stop the gas flow as long as the pressure difference over the screen is lower than the capillary pressure in the largest pores of its mesh. The gaseous phase is thus blocked by the pressure jump across the curved liquid-gas interphase in the small pores (Pingel and Dreyer, 2019). The gas breakthrough-point is known as the “bubble point pressure”. This capillary pressure can be retrieved from the well-known Young-Laplace equation. Assuming cylindrical pores and good wettability (small contact angle): Pbp = 4γ/D0. Where D0 is the largest pore diameter and γ is the surface tension value. Figure 7 shows a schematic for an apparatus for bubble point pressure testing of mesh screens. It must be noted that not every mesh is suitable for such application, a “Dutch Twilled” mesh is often mentioned as favorable due to its very fine pore size (Conrath et al., 2013b; Hartwig et al., 2014; Camarotti et al., 2019; Pingel and Dreyer, 2019). Figure 8 shows a CAD model of the Dutch Twilled mesh structure. An expected value for bubble point breakthrough pressure is in the range of several hundred to thousands of Pa, this would result in the bubble point diameter of tens of μm, strongly depending on the surface tension (Camarotti et al., 2019; Pingel and Dreyer, 2019).
FIGURE 8. CAD model of a Dutch Twilled mesh structure. Reprinted from Conrath et al. (2013b) with permission from Elsevier.
It is thus important that the mesh stays wet. With storable, nonvolatile liquids this is not a problem. However, keeping the mesh wet with easily evaporating liquids such as cryogens is more arduous. For certain cases, one must consider the screen’s ability to wick liquid from wet to dry areas. Dodge provides an equation for the wicking velocity of a liquid, which implies that there is a maximum possible evaporation rate for the screen that can be compensated by wicking (Dodge, 1990). This wicking, however, results in a decrease of the mesh’s bubble point (Bingham and Tegart, 1977). Moreover, these cryogenic liquids have low surface tension and require a finer mesh to counteract the surface tension (Young-Laplace equation). A finer mesh is accompanied by an increased flow-through-screen pressure drop and likelihood to be clogged by particulate matter, which are both disadvantageous (Hartwig et al., 2014). Overall, factors to consider for mesh-screen phase separation include bubble point pressure, flow-through-screen pressure drop, and wicking rate, but also so-called screen compliance and the material compatibility (Hartwig and Darr, 2014).
Conrath et al. proposed and investigated using a double mesh-screen set-up to block the liquid flow, rather than blocking the gas flow (Conrath et al., 2013b). A model was developed, and experiments were performed. Here, two mesh-screens are suspended in a tube at a distance L apart, both screens are connected by wicking aids such that both screens will wet when liquid contacts the first screen. This creates a gas plug between the two screens which results in a blocked liquid flow. Figure 9 shows a two-screen setup. The model proposed by Conrath et al. accounts for both cases of microgravity and terrestrial conditions where the capillary transport can be against gravity or gravity-assisted. Their predicted closure time (complete mesh wetting time) was 1.8x smaller than the experimentally observed time. Furthermore, the pressure breakthrough pressure was overpredicted, the experimental value was 57% of the predicted value. The values of the complete screen(s) wetting are in the range of several seconds, whereas the pressures are in the range of several hundred to thousands of Pa. Lastly, the leakage flow was strongly underpredicted (Conrath et al., 2013b). Pingel et al. have shown experimentally that a bubble enclosed between two screens can shrink over time (Pingel and Dreyer, 2019). Overall, a double mesh-screen can stop the liquid flow and thus be used to avoid liquid entering vents. However, it will not be able to stop liquid perfectly nor will it stop liquid indefinitely.
FIGURE 9. “Liquid from below”-test. (A) shows a dry screen. Once contact is established (B) the screen wets and traps gas. When pressure is increased, (C) the liquid rises but gas is trapped until (D) the trapped gas breaks through the top screen. Reprinted from Conrath et al. (2013b) with permission from Elsevier.
Jenson et al. examined passive phase separation in open wedge channels in μg for both zero-flow and axial flow and compared results to experiments conducted on the ISS (Jenson et al., 2014). Moreover, test conditions for 100% passive phase separations were given. A 48 mm long open surface in a wedge-shaped conduit has been described to passively separate phases. For a detailed mathematical description of fluid movement within such geometries, the reader is referred to publications of Metz et al. (2009), Weislogel et al. (2011), Weislogel et al. (2015).
The passive phase separation occurs by flows wicking along the walls of the wedge into the vertex, displacing the (in this case) gas bubble away from the vertex. This is shown schematically in Figure 10. Several interesting variations of bubble and separation phenomena were observed during the ISS experiments: In Figure 11A, a stable train of bubbles results from injecting small bubble volumes at low frequency and high liquid flow rate. In Figure 11B, the gas bubbles merge to larger bubbles which can migrate farther from the vertex to the free surface, leading to proper phase separation. This occurs when the bubble injection frequency is increased and/or the liquid flow rate is reduced. In Figure 11C, the bubble volume is large and frequency low. Nevertheless, the bubbles do not leave the liquid stream if the liquid velocity is above a threshold value. Though, these gas bubbles would reach the free surface if the channel length was increased, or injection was closer to the free surface. In Figure 11D, the bubble volume is high and injection frequency low, resulting in complete separation. Of course, operation modes were observed where any number of bubbles might remain or leave the wedge channel. In general, a higher liquid flow rate lowers the chance of the bubbles reaching the free surface within a predetermined channel length.
FIGURE 10. Time series of low-g capillary-dominated bubble migration in the presence of a free surface in an acute wedge-sectioned conduit of length L with a forced liquid flow through the duct. Reprinted from Jenson et al. (2014) with permission from Elsevier.
FIGURE 11. Visual results from onboard ISS experiments on bubble separation phenomena for fixed Ql = 1.75 ml/s: (A) non-separating low volume single bubble trains, (B) Bubbles that merge with each other and then coalesce with the free surface within the given channel length, (C) large volume single bubbles that do not reach free surface within the given channel length, and (D) larger volume single bubbles that coalesce with the free surface within the channel length. Reprinted from Jenson et al. (2014) with permission from Elsevier.
Jenson et al. (2014) provide five statements for aiding in the design of bubble separation processes in acute polygonal conduits:
1) Bubble volumes with Vb < (4π/3) {H sin(α)/[1 + sin(α)]}3 are unlikely to contact the free surface. Where H is the height from the wedge vertex to the free surface and α half of the polygonal (wedge) angle.
2) At low liquid and gas flowrates, a range of small bubbles with volumes smaller than those described in point 1 can reach the free surface due to inertial-capillary effects resulting from wake vortices.
3) When Vb is above the minimum volume threshold, all bubbles will eventually separate provided a low enough liquid flowrate and ample channel length. Also provided in this paper is an approximation for the required inertial-capillary bubble migration separation length mentioned in point 2.
4) Small bubble volumes at high gas flow rates combined with low liquid velocity will enable bubbles to merge, which in turn increases the bubble volumes and increases separation.
5) Characteristic bubble migration velocities have been identified for both viscous- and inertia-dominated conditions and are provided in said paper. 100% phase separation maps have also been provided for specific flow rate ranges and ratios: 0–1.6 ml/s gas and 0–3 ml/s liquid flowrate.
The concepts presented in the previous two sub-sections focus on separation of (gas-)bubbles from liquid. In a low-g environment, such devices would find use near the exit of a tank or tube where bubbles absolutely must be removed. Taking one step back into the equipment/tank, Propellant Management Devices (also known as Liquid Acquisition Devices) are present. These devices are used to separate liquid and gas phases within a tank and to transfer these gas-free liquids to, for example, a thruster or pump. Thus, these PMDs should be designed and built such that there is always a fluid link between the PMD entrance in the tank and the tank outlet (Hartwig, 2017).
These PMDs and their description are related to macro-fluidics. However, the underlying ideas and principles are of importance to grasp and modify to one’s personal fluid handling system design. Therefore, this sub-section will give some examples of capillary and non-capillary type PMDs and their advantages and disadvantages. The reader is referred to Hartwig for a more thorough and historical review of low-g PMDs (Hartwig, 2017).
The simplest PMD is a hole located at the bottom of a tank. However, it is clear that this approach is not sufficient in a low-g environment. More specialized PMDs include those based on a non-capillary approach. These devices are also known as positive expulsion devices. They make use of a barrier between the liquid and gas phase to avoid the gas entering said liquid. Examples of such systems are bladders/balloons, diaphragms, and pistons (Lark, 1967; Ballinger et al., 1995). These non-capillary variants are effective at keeping the liquid and gas separate. Furthermore, these systems are effective at controlling slosh within a tank and avoid reactions between gas and liquid (Lenahen et al., 2013). Contrary to these advantageous qualities, pistons are prone to leaking and bladders and diaphragms PMDs are impractical in large scale applications as they span the entire surface volume, resulting in significant additional weight (Hartwig, 2017).
More appropriate concepts for fluid handling include those based on capillarity, this phenomenon is explained in Section 2.1. Capillary PMDs include screens (as described in Section 3.1), throughs, baffles, vanes, screen channels, and sponges. The first three applications are considered partial communication PMDs as these are unable to reacquire fluid contact once it is broken. The latter three are considered total communication capillary driven PMDs as these are designed such that they can reconnect with liquid present in a tank.
Of these, vanes are the simplest in design and production; they are often constructed from thin sheet metal. Vanes are lightweight, cheap, and reliable. However, vanes have limited flow (capillary) flow capacity and can ingest bubbles at higher flowrates (as discussed in Section 2.1) (Tegart, 1997). A more complex LAD is that of a screen channel. Such device consists of an enclosed liquid flow path open to one side via a mesh-screen. Such screen channel allows for higher flowrates, blocks gas bubbles from entering (as discussed in Section 3.1), but is more complex and expensive to design. These have been used for cryogenic applications (Burge et al., 1973). An intermediate complex total communication PMD is a sponge. Sponges generally consist of perforated angled plates in contact with an outlet. These applications can be specially designed to drive bubbles away from the outlet by applying the knowledge discussed in Section 3.2. The size and number of plates is optimized to achieve the required flowrate (Jaekle, 1993). Sponges are in between vanes and full-on screen channels with respect to robustness, liquid control, weight, expense, etcetera. A major downside of sponges (and vanes) is the inability to test and verify their performance here on Earth.
Many types of PMDs exist and each has advantages and disadvantages. PMDs are essential for fluid handling systems to acquire and continue feeding liquid for processing. As seen in this section, many applications rely on capillarity for fluid flow and bubble separation. Several applications of fluid/gas separation and flow have thus been discussed so far. The next section will provide more examples of fluid flow and chemistry related to the theory discussed before.
The previous sections described theoretical approaches of manipulating and handling liquids in space, including potential and current technical applications. Section 3 was mostly related to separation of gas and liquid phases. The following section will give complemental applications of the presented concepts/theories in the area of food science, biology, diagnostics, and heat transfer, which have been proven to work on the ISS (and thus in space) to underline the universal importance of fluid transport and handling for everyday life in space.
Even a simple, daily activity like drinking a beverage can become difficult in a microgravitational environment. After all, opening a bottle or can and pouring the liquid into one’s mouth is not possible. Therefore, NASA currently relies on non-transparent sealed plastic pouches for transport and as a consumption method of pre-manufactured beverages. The range of beverages includes fruit drinks, tea, coffee, and water. The pouches come with a specifically designed straw that prevents the accidental spill of droplets into the space shuttle environment, as freely moving bubbles can represent a serious safety hazard (Smith et al., 2019). A potential disadvantage of this system is that aroma molecules released to a headspace above the bulk liquid cannot be accessed by the consumer, thereby potentially reducing the overall perceived taste.
To overcome this disadvantage and to improve the drinking experience, the “Capillary Effects of Drinking in the Microgravity Environment (Capillary Beverage)” experiment applied several of the previously discussed concepts to design cups to drink from in space (Weislogel, 2016). These specially designed cups use geometry and the resulting capillary forces to move liquid from the bulk along a narrow wedge to the cup’s lip (Pettit et al., 2009). Capillary forces reach an equilibrium at the top lip, and the flow stops. Sipping the liquid from the lip will disrupt the equilibrium and more liquid will be moved along the wedge to the user’s mouth until the liquid contents of the cup are exhausted.
The surface tension forces in the cup, as shown in Figure 12, were sufficiently strong to keep tea from spilling during normal motions (Pettit et al., 2011). Furthermore, flexible cup walls allow the cup to be used with different liquids: by squeezing the walls, the contact angle for the wedge is decreased and the capillary forces are amplified—resulting in a stronger fluid motion.
FIGURE 12. Astronaut Don Pettit moves the 0-G cup about the cabin without spillage while Steve Bowen takes a sip of tea in the background. Credits: NASA.
Studying the effects of surface tension, wetting, and geometrical shapes has the potential to make not just drinking easier, but also reduce the weight and volume of drinking bags that are sent to space. Furthermore, the results can be used to design new cups or even passive fluid control systems (Weislogel) For example, bubbles can effectively be removed from the liquid flowing through this cup by changing the geometry. Combining this cup with ample nucleation sites along the liquid flow path could possibly, although highly unlikely, even allow for a layer of foam on beer. However, it needs to be noted that the taste and drinking experience of carbonated beverages in space is vastly different than on Earth. The lack of buoyancy prevents carbon dioxide bubbles from rising to the liquid’s surface, therefore not causing the sparkling sensation in the oral cavity for which carbonated beverages are popular on Earth. Ingesting large amounts of gas will further lead to an unpleasant feeling in the digestive system of the astronaut, as a microgravitational environment makes it also more difficult for human bodies to separate gas from liquids.
As plants are an absolutely critical aspect of the complete life support system on Earth, the realization of reliable and efficient plant growth in space will be substantial to enable the long-term, independent survival of humans in an environment that is hostile to life. Considering space food systems, growing plants for food production is also beneficial for short and medium-long space missions, as it reduces the required freight and decreases the continued logistical burden of sending stored food items to the ISS. Moreover, plants convert carbon dioxide to oxygen via photosynthesis and create relatively clean water from wastewater as a result of evapotranspiration. Interestingly, plants utilize the capillary effect themselves to transport water from the roots to the stem and towards the leaves.
Over-saturation of the root zone and inadequate aeration often hinder proper plant growth in the microgravitational environment. In addition, the reduced gravitational environment and its resulting lack of convection reduces the overall diffusion of waste products and CO2 away from the cell. The lack of natural convection also results in a thicker boundary layer around plant leaves, reducing gas exchange, heat transfer, and water vapor transpiration; all resulting in a decreased uptake of water and nutrients through the roots (Stutte et al., 2011; Poulet et al., 2016; Carillo et al., 2020).
Consequently, NASA addresses these challenges in form of the “Plant Water Management” research project, which is expected to refine the fundamental understanding of the interaction of microgravity with respect to water and nutrient delivery to various plant configurations (Hatch et al., 2020). Of special interest is the plant spacing distance and its effect on water delivery, plant evaporation, and environmental condensation. Felt fabric, foam, and sponges were used to create the artificial plants with a mirrored root system and an evaporation rate of a real plant (Schabel, 2021). This omitted many of the complexities of a real plant. The ultimate outcome of this project is hoped to be a “pick-and-eat” food-production system in space.
Furthermore, both soil-based and hydroponics systems (i.e., plant roots directly suspended in water) are investigated on-board the ISS. A hydroponics test cell setup is shown in Figure 13. The overarching scientific objectives of these experiments are, as listed by Hatch et al. (2020) and Mungin et al. (2019), as follows:
• Demonstrate the role of surface tension, geometry, and wetting in a low-g environment and how it can replace the gravitational requirement in certain terrestrial plant growth systems
• Test and demonstrate a routine including priming, start-up, and steady and transient operation of the experiment
• Provide water and air to the root zone of plants throughout the complete plant life cycle
• Provide sufficient water and air to single or multi-plant set-ups
• Provide sufficient water to equal the needs arising from plant growth and evapotranspiration
• Provide water and air using a geometry that is applicable to all gravitational environments
• Using capillary forces to control water inventory in an open or half-open container
FIGURE 13. The set-up of the PWM Hydroponics Test Cell used to determine how to provide adequate aeration and hydration to grow plants in space. Credits: NASA.
Experiments aboard the ISS have shown that plants can be grown in microgravity. However, these set-ups have sub-optimal operations. The VEGGIE module demonstrated evidence of both insufficient and excess water in the plant root zone (Massa et al., 2017). Other systems such as the Advanced Plant Habitat (APH) (Massa et al., 2016) and the Passive Orbital Nutrient Delivery System (PONDS) (Massa et al., 2019) modules have been based and improved on the VEGGIE experiments. Yet, these modules have sub-par growth performances with issues still related to the water/nutrient-delivery system used, among others (Burgner et al., 2019).
On-site medical diagnostics are of high importance in space, as a swift return to Earth in case of medical emergency is not possible, which is especially true for long-term deep space exploration. Additionally, long-duration space flights themselves pose health concerns for astronauts, resulting from the microgravitational environment as well as from long-term exposure to high-energy cosmic rays. Proper crew health maintenance and performance will rely on prevention, early diagnoses, condition management, and in-situ medical interventions (Roda et al., 2018). Until now, only a couple of medical diagnostic devices have been used on the ISS. One of which is the i-STAT analyzer (Love, 2001): a compact and automated instrument used to test a 65-microliter sample of blood utilizing disposable assay cartridges and electrochemical detection techniques. A disadvantage of this device is the limited shelf life of the cartridges (Smith et al., 1997). Also, fouling of the electrodes can decrease the devices’ performance. It is of interest to expand the range of biological and biophysical biomarkers that can be measured in space. This is accompanied by an interest in highly sensitive methods for accurate and reliable results.
Space-related diagnostic devices and biosensors, in contrast to terrestrial apparatuses, are required to be reliably operatable in a microgravitational environment. Chemical and biochemical reactions should only be minimally affected by the absence of gravity. Yet another stringent requirement in developing biosensors for space application is the safety of the spacecraft environment. Appropriate multi-level containment and safe disposal must be ensured to avoid the release of potentially dangerous chemicals and contaminated biological samples during operation or unexpected events. Furthermore, in anticipation of long-term space missions, the devices are required to have extended shelf life and operation life while being stored in a high-radiation environment. Also, the sensors should be compact, light-weight, and of restricted power consumption (Roda et al., 2018).
An ideal microfluidic concept for space application would be paper-based chemistry. In paper-based analytical devices, small fluid volumes are manipulated via capillarity phenomenon. They usually are simple, inexpensive, and lightweight—all of which are favorable characteristics for space application (Hu et al., 2014; Zangheri et al., 2019). One of these paper-based techniques is the Lateral Flow Immunoassay (LFIA). In LFIAs, a nitrocellulose membrane is fitted with specific immunoreagents immobilized in a predetermined layout. A liquid sample is then transported by capillary forces along this membrane, ultimately completing the biological assessment (Posthuma-Trumpie et al., 2008).
The “IN SITU Bioanalysis” project was active onboard the ISS during the second half of 2017. During this time, a chemiluminescence-based LFIA biosensor, as shown in Figure 14, was tested for cortisol measurements in oral fluid. Taking cortisol as a model analyte enables non-invasive sampling. However, cortisol levels in saliva are extremely low at nanomolar levels, and thus require highly sensitive measurement methods. The materials, channel sizes, and geometry of this biosensor were chosen in a way that the most common problems of handling fluids (bubble formation, surface wetting impairment, and solutions mixing) in space were avoided (Zangheri et al., 2019). Via this experiment, the feasibility of performing ultrasensitive immunological chemistry directly onboard the ISS was demonstrated. However, it was shown that further improvements are possible. Ideas such as reusable cartridges, cartridge miniaturization, and process automation were suggested (Zangheri et al., 2019).
FIGURE 14. Principle of a cortisol assay with loading of oral fluid and HRP-cortisol conjugate. Reprinted from Zangheri et al. (2019) with permission from Elsevier.
Furthermore, the environment in the space shuttle needs to be constantly monitored, as the environment is vital to the survival of the astronauts. Water and air are continuously recycled and high quality needs to be ensured. On top of that, onboard food production will be required for long-term deep space exploration, which will require additional biosensors to watch food quality and safety.
In July 2019, the Spacecraft Atmosphere Monitor (S.A.M.) was flown to the ISS to monitor air quality. S.A.M. employs a gas chromatograph mass spectrometer (GCMS) to continuously and autonomously monitor the majority of components found in the air: oxygen, carbon dioxide, nitrogen, methane, but also humidity. A new version is being developed to also include monitoring trace gases (Hill, 2019). However, more of interest to this review are sensors that allow a more expedient, low-cost, and in-flight method to detect and identify microbes. Between 2006 and 2009, the Lab-on-a-chip application development portable test system (LOCAD-PTS) was tested aboard the ISS (Maule et al., 2009). This system could quantify specific bacteria and fungi by employing several methods, including surface tension, to keep the required sample volume. Other tested systems included the WETLAB-2 and RAZOR EX system (NASA, 2017; NASA, 2021).
Most sensors do not employ microfluidics at this point. However, it is clear that a great interest exists for biosensors in space. Microfluidics, such as paper-based chemistry, provides a great opportunity to increase the efficiency and efficacy of sensors and can overcome other limitations imposed by space.
Heat pipes transport heat by evaporating a working fluid at a heat source (evaporator) and rejecting it at a condenser. The liquid is then transported back to the evaporator to close the loop. Heat pipes are effective devices for transmitting heat over considerable distances with small temperature drops, simple construction, and without the need for external pumping (Faghri, 1995). Heat pipes can transfer significant heat over small temperature ranges due to exploiting the latent heat related to phase change. This feat is highly desirable in space. Though, the capacity of condensate transport back to the evaporator is limited by the wicking ability of the mesh/wick used in older heat pipe designs. When the capillary wick in the heat pipe is replaced by electrical pumping of condensate, it is called an electrowetting heat pipe. This concept is based on the electrical altering of droplet surface tension. A schematic overview is shown in Figure 15. Two discrete microchannels exist where one pumps the condensate to the evaporator, while the other channel allows vapor to move to the condenser.
FIGURE 15. (A) Schematic top view of an EHP, showing the liquid and vapor channels, and (B) side view of a two-plate device for EW-induced movement of droplets.
Electrowetting heat pipes are not influenced by the capillary limitations imposed by an adiabatic wick. First-order models predict that these EHPs (multiple channel set-up) with a total cross-section of 10 cm × 4 mm (W × H) can transport approximately 1.5 kW over distances exceeding 1 m using water. Furthermore, this concept benefits from ultralow power consumption (microwatts), a wide range of working fluids, and the absence of moving parts (Hale and Bahadur, 2015). Hale et al. compared electrowetting-based heat pipes with several other heat pipes of similar dimensions and found that electrowetting can transport more than twice the maximum heat capacity while offering a low thermal resistance (Hale and Bahadur, 2015). These other pipes were based on the following techniques: a sintered powder heat pipe, an axial groove heat pipe, a loop heat pipe, and a thermosyphon.
The electrical pumping of droplets is a promising technology for heat load transport. It has been extensively tested on Earth. In 2018, a study was done on the ISS to relate investigate the role of gravity on e.g. contact line friction and hysteresis (Wikramanayake et al., 2019). The results show that electrowetting experiments could be conducted in space and that any safety, reliability, and compactness-related challenges could be overcome.
Space exploration will increase in the near future. Many technologies for handling fluids on Earth must be redesigned for the microgravitational environment. For this, understanding surface tension and how to alter it is key. Interesting applications of micro- and macro-fluidic concepts are being researched aboard the ISS. This review provided several of these concepts for manipulating surface tension. We report the use of capillary flow, thermocapillary Marangoni forces, electrolytic gas evolution techniques in space. It moved on to tested applications of these theories such as passive gas bubble removal techniques, drinking in microgravity, and biosensors.
Knowledge about handling and transporting liquids is ever increasing with the research done aboard the ISS. When wanting to settle on the Moon or Mars, more chemical engineering concepts have to be redesigned for low-g environments; especially reactor designs and separation techniques. This as a long-term settlement has many more necessities to sustain life. Fluid handling in space requires new designs for fluid handling apparatuses. Microfluidics is a strong candidate for moving chemical plants to space as it allows for combining reliable fluid handling concepts with safety and flexibility. Furthermore, microfluidic concepts on Earth are based on surface-dominated effects, meaning that they are (almost) directly translatable to the microgravitational environment. Understanding surface effects is key to successful fluid chemistry and engineering for omni-gravitational applications. Yet, many (fundamental) questions remain for space agencies and industry to research. The remainder of this outlook will state some of the questions posed by these space agencies. It is by no means an exhaustive list of these questions and the reader is encouraged to read the ESA and NASA sites for a complete overview (ROADMAPS FOR FUTURE RESEARCH, 2016; 2020 NASA Technology Taxonomy, 2020).
Space agencies such as ESA and NASA have set strategic goals which the experiments and publications described in this review touch. Their research goals are given in the so-called roadmaps for future research and the technology taxonomy as written by the ESA and NASA, respectively. An example, as given in the ESA roadmaps, is related to the fluid/wall interaction—which is of importance for capillary-driven flows. Questions here are related to the influence of different parameters on wettability and how this wettability can be predicted. Also, how does wettability influence the contact line dynamics in the absence of gravity?
Next, the thermocapillary Marangoni force, or two-phase heat and mass transfer in more general, is of interest. Stated research interests include questions such as: what is the contribution of convection mechanisms in mixed convection regimes? What is the contribution of the Marangoni convection to the total energy transport at the two-phase interface? And what triggers instabilities in the fluid-vapor interface and how does this instability influence the heat transfer? Next, space is also of interest for fundamental questions related to the briefly touched metal nucleation and crystallization. Here, the ESA roadmap mentions space research interest towards, for example, the dependence of nucleation on convection in liquid metals and alloys and the relation between chemical diffusion coefficients and self-diffusion coefficients of metals and alloys.
The low-g environment is suitable to disentangle the multitude of influences related to mass and heat transfer in space. As mentioned several times before, microgravity avoids buoyancy-driven flows. These often overshadow underlying physical phenomena as touched upon in this review. Phenomena such as the Marangoni force, bubble induced convection, and capillarity/bubble removal in an open wedge channel can therefore be researched in greater detail in space.
Furthermore, both ESA and NASA have an interest in researching human health, life support, and habitation systems. This can also be interpreted as supporting life in hostile environments. Extended knowledge is required to sustain biological processes in a closed ecological system. Especially when space factors such as low-g and radiation are present. This review touched these subjects with the discussion on watering plants and flow in biosensors in space. More general questions remain with respect to subjects such as the metabolic behavior of (micro)organisms and plants in space, water and solute transport, and genetic stability in a space environment. For human physiology, many fundamental questions related to the heart, lung, and kidneys, bone and muscles, the immune system, and the effects of radiation remain, to name just a few themes.
Space research is thus not just important but a necessity for acquiring a deep understanding and extensive knowledge of the themes related to space exploration and the advancement of human civilization.
This manuscript is an outcome of joint global collaboration between researchers from different countries and continents; each being specialised in a specific kind of expertise. Central to it is VH, being renowned as leading microfluidics researcher and ambassador for the field of micoreactors/flow chemistry. Central is JN as emerging young researcher, JN is a remote post-master student in the Hessel group, who worked and published on self-priming micro-flow chips on satellites. SS makes PhD on dispersed liquid/liquid systems in space and NT co-supervises several researches in space technology for human space exploration. In the past few years, these researchers attached have published several papers in high IF journals, like Chemical Society Reviews, Angewandte Chemie, ACS Sustainable Chemistry and Engineering, Chemical Engineering Journal, IECR, Chemical Engineering Science, Reaction Chemistry and Engineering, and more. In our opinion, the current manuscript demonstrates a similar level of novelty as these previous papers, since we report about the use of microfluidics in space, both from the fundamental and applied side.
The authors declare that the research was conducted in the absence of any commercial or financial relationships that could be construed as a potential conflict of interest.
All claims expressed in this article are solely those of the authors and do not necessarily represent those of their affiliated organizations, or those of the publisher, the editors and the reviewers. Any product that may be evaluated in this article, or claim that may be made by its manufacturer, is not guaranteed or endorsed by the publisher.
The authors acknowledge financial support from the Andy Thomas Centre for Space Resources, University of Adelaide, Australia
2020 NASA Technology Taxonomy, (2020). Available at: https://www.nasa.gov/sites/default/files/atoms/files/2020_nasa_technology_taxonomy.pdf (Accessed December 3, 2021).
Babi, D. K., Cruz, M. S., and Gani, R. (2016). “Fundamentals of Process Intensification: A Process Systems Engineering View,” in Process Intensification in Chemical Engineering: Design Optimization and Control. Editors J. Segovia-Hernández, and A. Bonilla-Petriciolet (Cham: Springer), 7–33. doi:10.1007/978-3-319-28392-0_2
Ballinger, I., Lay, W., and Tam, W. (1995). Review and History of PSI Elastomeric Diaphragm Tanks. arc.aiaa.org. 1995, undefined, 1–3. doi:10.2514/6.1995-2534
Bingham, P., and Tegart, J. (1977). “Wicking in fine Mesh Screens,” in 13th Propulsion Conference, Orlando, FL, July 11–13, 1977 (AIAA). doi:10.2514/6.1977-849
Bruus, H. (2006). Theoretical Microfluidics. Editor H. Bruus. 3rd ed. (Oxford, United Kingdom: Oxford University Press).
Burge, G., Blackmon, J., and Castle, J. (1973). “Design of Propellant Acquisition Systems for Advanced Cryogenic Space Propulsion Systems,” in 9th Propulsion Conference, Las Vegas, NV, November 5–7, 1973 (AIAA). doi:10.2514/6.1973-1287
Burgner, S. E., Mitchell, C., Massa, G., Romeyn, M. W., Wheeler, R. M., and Morrow, R. (2019). “Troubleshooting Performance Failures of Chinese Cabbage for Veggie on the ISS,” in 49th International Conference on Environmental Systems, Boston, MA, July 7–11, 2019. Available at: https://ttu-ir.tdl.org/handle/2346/84553.
Camarotti, C., Deng, O., Darr, S., Hartwig, J., and Chung, J. N. (2019). Screen Compliance Experiments for Application of Liquid Acquisition Device in Space. Microgravity Sci. Technol. 31 (1), 109–122. doi:10.1007/S12217-018-9671-0
Canfield, P. J., Bronowicki, P. M., Chen, Y., Kiewidt, L., Grah, A., Klatte, J., et al. (2013). The Capillary Channel Flow Experiments on the International Space Station: Experiment Set-Up and First Results. Exp. Fluids 54, 1–14. doi:10.1007/S00348-013-1519-1
Carillo, P., Morrone, B., Fusco, G. M., De Pascale, S., and Rouphael, Y. (2020). Challenges for a Sustainable Food Production System on Board of the International Space Station: A Technical Review. Agronomy 10, 687. doi:10.3390/AGRONOMY10050687
Charpentier, J.-C. (2007). In the Frame of Globalization and Sustainability, Process Intensification, a Path to the Future of Chemical and Process Engineering (Molecules into Money). Chem. Eng. J. 134, 84–92. doi:10.1016/J.CEJ.2007.03.084
Conrath, M., Canfield, P. J., Bronowicki, P. M., Dreyer, M. E., Weislogel, M. M., and Grah, A. (2013a). Capillary Channel Flow Experiments Aboard the International Space Station. Phys. Rev. E 88, 063009. doi:10.1103/PhysRevE.88.063009
Conrath, M., Smiyukha, Y., Fuhrmann, E., and Dreyer, M. (2013b). Double Porous Screen Element for Gas-Liquid Phase Separation. Int. J. Multiphase Flow 50, 1–15. doi:10.1016/J.IJMULTIPHASEFLOW.2012.10.003
Dodge, F. T. (1990). “Fluid MAnagement in Low Gravity,” in Low-Gravity Fluid Dynamics and Transport Phenomena. Editors J. N. Koster, R. L. Sani, and A. R. Seebas (Washington, DC: American Institute of Aeronautics and Astronautics), 3–14. Available at: https://www.google.com/search?q=Dodge%2C+F.T.%2C+1990.+Low-Gravity+Fluid+Dynamics+and+Transport+Phenomena%2C+vol.+130.+Aeronautics+and+Astronautics%2C+Washington%2C+DC%2C+pp.+3%E2%80%9314+(Chapter+1).&rlz=1C1ONGR_enNL932NL932&oq=Dodge%2C+F.T.%2C+1990.+Low-Gravity+Fluid+Dynamics+and+Transport+Phenomena%2C+vol.+130.+Aeronautics+and+Astronautics%2C+Washington%2C+DC%2C+pp.+3%E2%80%9314+(Chapter+1).&aqs=chrome.69i57j69i60l2.226j0j7&sourceid=chrome&ie=UTF-8 (Accessed August 3, 2021).
Dreyer, M., Delgado, A., and Path, H.-J. (1994). Capillary Rise of Liquid between Parallel Plates under Microgravity. J. Colloid Interf. Sci. 163, 158–168. doi:10.1006/JCIS.1994.1092
Faghri, A. (1995). Heat Pipe Science and Technology. 1st ed. Abingdon, Oxon, United Kingdom: Taylor & Francis Group. Available at: https://books.google.nl/books?hl=nl&lr=&id=9QpQAQAAQBAJ&oi=fnd&pg=PR15&dq=A.+Faghri,+1995+%22Heat+pipe+science+and+technology,%22+Taylor+%26+Francis.&ots=MSCAQRBSKh&sig=Rk_kbplfmHmplAEnGEC2qvhV5Bs&redir_esc=y#v=onepage&q=A.%20Faghri%2C%201995%20%22Heat%20pipe%20science%20and%20technology%2C%22%20Taylor%20%26%20Francis.&f=false (Accessed September 1, 2021).
Fries, N., and Odic, K. (2007). “Wicking of Perfectly Wetting Liquids into a Metallic Mesh,” in Proceedings of the 2nd International Conference on Porous Media and its Applications in Science and Engineering ICPM2, Kauai, HI, June 17–21, 2007. Available at: https://www.zarm.uni-bremen.de/2forschung/grenzph/papers/fries2007.pdf (Accessed August 4, 2021).
Ge, Z. (2020). Electrolytic Gas Evolution under Microgravity. Available at: https://www.nasa.gov/mission_pages/station/research/experiments/explorer/Investigation.html?#id=1939 (Accessed September 13, 2021).
Grah, A., Canfield, P. J., Bronowicki, P. M., Dreyer, M. E., Chen, Y., and Weislogel, M. M. (2014). Transient Capillary Channel Flow Stability. Microgravity Sci. Technol. 26 (6), 385–396. doi:10.1007/S12217-014-9403-Z
Grodzka, P., and Bannister, T. (1974). “Natural Convection in Low-G Environments,” in 12th Aerospace Sciences Meeting, Washington, DC, January 30–February 1, 1974 (Washington: American Institute of Aeronautics and Astronautics AIAA). doi:10.2514/6.1974-156
Hale, R. S., and Bahadur, V. (2015). Electrowetting Heat Pipes for Heat Transport over Extended Distances. IEEE Trans. Compon., Packag. Manufact. Technol. 5, 1441–1450. doi:10.1109/TCPMT.2015.2472363
Hartwig, J., and Darr, S. (2014). Influential Factors for Liquid Acquisition Device Screen Selection for Cryogenic Propulsion Systems. Appl. Therm. Eng. 66, 548–562. doi:10.1016/J.APPLTHERMALENG.2014.02.022
Hartwig, J., Adin Mann, J., and Darr, S. R. (2014). Parametric Analysis of the Liquid Hydrogen and Nitrogen Bubble point Pressure for Cryogenic Liquid Acquisition Devices. Cryogenics 63, 25–36. doi:10.1016/J.CRYOGENICS.2014.05.013
Hartwig, J. W. (2017). Propellant Management Devices for Low-Gravity Fluid Management: Past, Present, and Future Applications. J. Spacecraft Rockets 54, 808–824. doi:10.2514/1.A33750
Hatch, T. R., Weislogel, M. M., Mungin, R. M., and Hernandez, M. A. (2020). “Plant Water Management in Microgravity,” in International Conference on Environmental Systems, Lisboa, Portugal, July 12–16, 2020. Available at: https://ttu-ir.tdl.org/bitstream/handle/2346/86415/ICES-2020-28.pdf?sequence=1&isAllowed=y (Accessed August 31, 2021).
Hessel, V., Löwe, H., and Hardt, S. (2004). Chemical Micro Process Engineering: Fundamentals, Modelling and Reactions. Available at: https://books.google.com/books?hl=nl&lr=&id=C9VnUZjTC-gC&oi=fnd&pg=PR5&dq=Chemical+micro+process+engineering:+fundamentals,+modelling+and+reactions+V+Hessel,+H+L%C3%B6we,+S+Hardt+John+Wiley+%26+Sons&ots=nxuGFqNaMH&sig=qK2c8JngUrUuJUqw5GlFAQwFZSs (Accessed September 16, 2021).
Hessel, V., Sarafraz, M. M., and Tran, N. N. (2020). The Resource Gateway: Microfluidics and Requirements Engineering for Sustainable Space Systems. Chem. Eng. Sci. 225, 115774. doi:10.1016/J.CES.2020.115774
Hessel, V., Tran, N. N., Orandi, S., Asrami, M. R., Goodsite, M., and Nguyen, H. (2021). Continuous‐Flow Extraction of Adjacent Metals-A Disruptive Economic Window for In Situ Resource Utilization of Asteroids? Angew. Chem. Int. Ed. 60, 3368–3388. doi:10.1002/ANIE.201912205
Hill, D. (2019). SAM Goes to Work Aboard ISS | NASA. Available at: https://www.nasa.gov/feature/nasas-spacecraft-atmosphere-monitor-goes-to-work-aboard-the-international-space-station (Accessed September 7, 2021).
Hu, J., Wang, S., Wang, L., Li, F., Pingguan-Murphy, B., Lu, T. J., et al. (2014). Advances in Paper-Based point-of-care Diagnostics. Biosens. Bioelectron. 54, 585–597. doi:10.1016/J.BIOS.2013.10.075
Jaekle, D. E. (1993). “Propellant Management Device Conceptual Design and Analysis: Sponges,” in AIAA/SAE/ASME/ASEE 29th Joint Propulsion Conference and Exhibit, Monterey, CA, June 28–30, 1993. Available at: http://www.pmdtechnology.com/pdfs/AIAA93-1970.pdf (Accessed November 23, 2021). doi:10.2514/6.1993-1970
Jenson, R. M., Wollman, A. P., Weislogel, M. M., Sharp, L., Green, R., Canfield, P. J., et al. (2014). Passive Phase Separation of Microgravity Bubbly Flows Using Conduit Geometry. Int. J. Multiphase Flow 65, 68–81. doi:10.1016/J.IJMULTIPHASEFLOW.2014.05.011
Kassemi, S. A., and Ostrach, S. (1992). Nature of Buoyancy-Driven Flows in a Reduced-Gravity Environment. AIAA J. 30, 1815–1818. doi:10.2514/3.11141
Lark, R. F. (1967). Cryogenic Positive Expulsion Bladders. J. Macromolecular Sci. B 1, 623–637. doi:10.1080/00222346708212353
Lenahen, B., Gangadharan, S., and Desai, M. (2013). “A Computational and Experimental Analysis of Spacecraft Propellant Tanks Implemented with Flexible Diaphragms,” in 54th AIAA/ASME/ASCE/AHS/ASC Structures, Structural Dynamics, and Materials Conference, Boston, MA, April 8–11, 2013. doi:10.2514/6.2013-1886
Love, J. (2001). Portable Clinical Blood Analyzer - I-STAT. Available at: https://www.nasa.gov/mission_pages/station/research/experiments/explorer/Investigation.html?#id=364 (Accessed September 7, 2021).
Marchetta, J. G., and Winter, A. P. (2010). Simulation of Magnetic Positive Positioning for Space Based Fluid Management Systems. Math. Comput. Model. Int. J. 51, 1202–1212. doi:10.1016/J.MCM.2010.01.002
Marston, P. L., and Thiessen, D. B. (2004). Manipulation of Fluid Objects with Acoustic Radiation Pressure. Ann. N. Y Acad. Sci. 1027, 414–434. doi:10.1196/ANNALS.1324.034
Martin, J., and Holt, J. B. (2000). Magnetically Actuated Propellant Orientation experiment, Controlling Fluid Motion with Magnetic fields in a Low-Gravity Environment. ntrs.nasa.gov. Available at: https://ntrs.nasa.gov/api/citations/20000036592/downloads/20000036592.pdf (Accessed August 1, 2021).
Massa, G. D., Wheeler, R. M., Morrow, R. C., and Levine, H. G. (2016). Growth chambers on the International Space Station for Large Plants. Acta Hortic. 1134, 215–222. doi:10.17660/ACTAHORTIC.2016.1134.29
Massa, G. D., Dufour, N. F., Carver, J. A., Hummerick, M. E., Wheeler, R. M., Morrow, R. C., et al. (2017). VEG-01: Veggie Hardware Validation Testing on the International Space Station. Open Agric. 2, 33–41. doi:10.1515/OPAG-2017-0003
Massa, G., Romeyn, M., Spencer, L., Mickens, M., Poulet, L., and Wheeler, R. (2019). NCERA-101 Station Report from Kennedy Space center. FL, USA (April 2019). Available at: https://ntrs.nasa.gov/api/citations/20190002588/downloads/20190002588.pdf (Accessed September 1, 2021).
Matsushima, H., Nishida, T., Konishi, Y., Fukunaka, Y., Ito, Y., and Kuribayashi, K. (2003). Water Electrolysis under Microgravity. Electrochimica Acta 48, 4119–4125. doi:10.1016/S0013-4686(03)00579-6
Matsushima, H., Fukunaka, Y., and Kuribayashi, K. (2006). Water Electrolysis under Microgravity. Electrochimica Acta 51, 4190–4198. doi:10.1016/J.ELECTACTA.2005.11.046
Maule, J., Wainwright, N., Steele, A., Monaco, L., Morris, H., Gunter, D., et al. (2009). Rapid Culture-Independent Microbial Analysis Aboard the International Space Station (ISS). Astrobiology 9, 759–775. Available at: https://home.liebertpub.com/ast. doi:10.1089/AST.2008.0319
Metz, T., Paust, N., Zengerle, R., and Koltay, P. (2009). Capillary Driven Movement of Gas Bubbles in Tapered Structures. Microfluid Nanofluid 9 (2), 341–355. doi:10.1007/S10404-009-0551-1
Mungin, R. M., Weislogel, M. M., Hatch, T. R., and M C Quillen, J. B. (2019). “Omni-gravity Hydroponics for Space Exploration,” in 49th International Conference on Environmental Systems, Boston, MA, July 7–11, 2019. Available at: https://ttu-ir.tdl.org/bitstream/handle/2346/84457/ICES-2019-242.pdf?sequence=5&isAllowed=y (Accessed August 31, 2021).
NASA (2017). WetLab-2 | NASA. Available at: https://www.nasa.gov/ames/research/space-biosciences/wetlab-2 (Accessed September 7, 2021).
NASA (2021). Water Monitoring Suite. Available at: https://www.nasa.gov/mission_pages/station/research/experiments/explorer/Investigation.html?#id=1847 (Accessed September 7, 2021).
Oeftering, R. C., Chato, D. J., and Mann, A. I. (2003). Liquid Propellant Manipulated Acoustically. Cleveland, OH: NASA Glenn Research Center. Research and Technology 2002. Available at: https://ntrs.nasa.gov/citations/20050215041.
Pettit, D., Weisloge, M., Concus, P., and Finn, R. (2009). Beverage Cup for Use in Spacecraft or Weightless Environments. Available at: https://patentimages.storage.googleapis.com/3c/e9/a5/a70219d667f155/US20110101009A1.pdf (Accessed August 31, 2021).
Pettit, D. R., Weislogel, M., Concus, P., and Finn, R. (2011). A Zero-Gravity Cup for Drinking Beverages in Microgravity. Houston, TX: Lyndon B. Johnson Space Center. NASA Tech Briefs.
Pingel, A., and Dreyer, M. E. (2019). Phase Separation of Liquid from Gaseous Hydrogen in Microgravity Experimental Results. Microgravity Sci. Technol. 31, 649–671. doi:10.1007/S12217-019-09727-5
Posthuma-Trumpie, G. A., Korf, J., and van Amerongen, A. (2008). Lateral Flow (Immuno)assay: its Strengths, Weaknesses, Opportunities and Threats. A Literature Survey. Anal. Bioanal. Chem. 393 (2), 569–582. doi:10.1007/S00216-008-2287-2
Poulet, L., Fontaine, J.-P., and Dussap, C.-G. (2016). Plant's Response to Space Environment: a Comprehensive Review Including Mechanistic Modelling for Future Space Gardeners. Bot. Lett. 163, 337–347. doi:10.1080/23818107.2016.1194228
Rainey, K. (2017). Exploring the Wonders of Fluid Motion: Improving Life on Earth through Understanding the Nature of Marangoni Convection. Available at: https://www.nasa.gov/mission_pages/station/research/benefits/marangoni_convection/ (Accessed September 14, 2021).
ROADMAPS FOR FUTURE RESEARCH (2016). A Redefinition of Strategic Goals for Future Space Research on the ISS and Supporting Research Platforms. Available at: https://indico.gsi.de/event/6401/images/751-Roadmap_v6.pdf (Accessed December 3, 2021).
Roda, A., Mirasoli, M., Guardigli, M., Zangheri, M., Caliceti, C., Calabria, D., et al. (2018). Advanced Biosensors for Monitoring Astronauts' Health during Long-Duration Space Missions. Biosens. Bioelectron. 111, 18–26. doi:10.1016/J.BIOS.2018.03.062
Rosendahl, U., and Dreyer, M. E. (20072007). Design and Performance of an experiment for the Investigation of Open Capillary Channel Flows. Exp. Fluids 42 (5), 683–696. doi:10.1007/S00348-007-0274-6
Rosendahl, U., Ohlhoff, A., Dreyer, M. E., and Rath, H. J. (2002). Investigation of Forced Liquid Flows in Open Capillary Channels. Microgravity Sci. Technol. 13 (4), 53–59. doi:10.1007/BF02881681
Rosendahl, U., Ohlhoff, A., and Dreyer, M. E. (2004). Choked Flows in Open Capillary Channels: Theory, experiment and Computations. J. Fluid Mech. 518, 187–214. doi:10.1017/S0022112004001041
Rosendahl, U., Grah, A., and Dreyer, M. E. (2010). Convective Dominated Flows in Open Capillary Channels. Phys. Fluids 22, 052102. doi:10.1063/1.3379847
Schabel, A. (2021). Project Examines How to Water Plants in Space. Available at: http://www.nasa.gov/feature/glenn/2021/project-examines-how-to-water-plants-in-space (Accessed August 31, 2021).
Shitomi, N., Yano, T., and Nishino, K. (2019). Effect of Radiative Heat Transfer on Thermocapillary Convection in Long Liquid Bridges of High-Prandtl-Number Fluids in Microgravity. Int. J. Heat Mass Transfer 133, 405–415. doi:10.1016/J.IJHEATMASSTRANSFER.2018.12.119
Smith, S. M., Davis-Street, J. E., Fontenot, T. B., and Lane, H. W. (1997). Assessment of a Portable Clinical Blood Analyzer during Space Flight. Clin. Chem. 43, 1056–1065. Available at: https://academic.oup.com/clinchem/article/43/6/1056/5640939 (Accessed September 7, 2021). doi:10.1093/clinchem/43.6.1056
Smith, S. M., Lane, H. W., and Zwart, S. R. (2019). “Chapter 13: Spaceflight Metabolism and Nutritional Support,” in Principles of Clinical Medicine for Space Flight. Editors Mi. R. Barratt, E. S. Baker, and S. L. Pool (New York: Springer), 412–416.
Stutte, G., Wheeler, R., Morrow, R., and Newsham, G. (2011). “Operational Evaluation of VEGGIE Food Production System in the Habitat Demonstration Unit,” in 41st International Conference on Environmental Systems, Portland, OR, July 17–21, 2011 (ICES 2011). doi:10.2514/6.2011-5262
Tegart, J. (1997). “A Vane Type Propellant Management Device,” in 33rd Joint Propulsion Conference and Exhibit, Seattle, WA, July 6–9, 1997. doi:10.2514/6.1997-3028
Viestenz, K. J., Jenson, R. M., Weislogel, M. M., and Sargusingh, M. J. (2018). “Capillary Structures for Exploration Life Support Payload Experiment,” in 48th International Conference on Environmental Systems ICES-2018-241, Albuquerque, NM, July 8–12, 2018. Available at: https://ttu-ir.tdl.org/bitstream/handle/2346/74194/ICES_2018_241.pdf (Accessed September 15, 2021).
Weislogel, M. M., and Jenson, R. M. (2019). “Passive No Moving Parts Capillary Solutions for Spacecraft Life Support Systems,” in 49th International Conference on Environmental Systems ICES-2019-203, Boston, MA, July 7–11, 2019. Available at: https://ttu-ir.tdl.org/bitstream/handle/2346/84433/ICES-2019-203.pdf (Accessed September 15, 2021).
Weislogel, M. M., Baker, J. A., and Jenson, R. M. (2011). Quasi-steady Capillarity-Driven Flows in Slender Containers with interior Edges. J. Fluid Mech. 685, 271–305. doi:10.1017/JFM.2011.314
Weislogel, M. M., Wollman, A. P., Jenson, R. M., Geile, J. T., Tucker, J. F., Wiles, B. M., et al. (2015). Capillary Channel Flow (CCF) EU2-02 on the International Space Station (ISS): An Experimental Investigation of Passive Bubble Separations in an Open Capillary Channel. Cleveland. Available at: https://ntrs.nasa.gov/api/citations/20160001341/downloads/20160001341.pdf (Accessed November 16, 2021).
Weislogel, M. (2016). Capillary Effects of Drinking in the Microgravity Environment. Available at: https://www.nasa.gov/mission_pages/station/research/experiments/explorer/Investigation.html?#id=1768 (Accessed August 31, 2021).
Wikramanayake, E., Hale, R., Elam, J., Shahriari, A., Bahadur, V., Alvarez-Hernandez, A. R., et al. (2019). “Characterizing Microfluidic Operations Underlying an Electrowetting Heat Pipe on the International Space Station,” in Proceedings of the ASME 2018 International Mechanical Engineering Congress and Exposition IMECE2018, Pittsburgh, PA, November 9–15, 2018. doi:10.1115/IMECE2018-86223
Yano, T., Nishino, K., Matsumoto, S., Ueno, I., Komiya, A., Kamotani, Y., et al. (2018a). Overview of “Dynamic Surf” Project in Kibo–Dynamic Behavior of Large-Scale Thermocapillary Liquid Bridges in Microgravity. Int. J. Microgravity Sci. Appl. 35, 350102. doi:10.15011/JASMA.35.1.350102
Yano, T., Nishino, K., Matsumoto, S., Ueno, I., Komiya, A., Kamotani, Y., et al. (2018b). Report on Microgravity Experiments of Dynamic Surface Deformation Effects on Marangoni Instability in High-Prandtl-Number Liquid Bridges. Microgravity Sci. Technol. 30, 599–610. doi:10.1007/S12217-018-9614-9
Zangheri, M., Mirasoli, M., Guardigli, M., di Nardo, F., Anfossi, L., Baggiani, C., et al. (2019). Chemiluminescence-based Biosensor for Monitoring Astronauts' Health Status during Space Missions: Results from the International Space Station. Biosens. Bioelectron. 129, 260–268. doi:10.1016/J.BIOS.2018.09.059
Zapata, E. (2017). The State of Play US Space Systems Competitiveness: Prices, Productivity, and Other Measures of Launchers & Spacecraft. Available at: https://ntrs.nasa.gov/search.jsp?R=20170012517 (Accessed November 22, 2019).
Keywords: microgravity, microfluidics, capillary flow, marangoni forces, electrolytic gas evolution, bubble removement
Citation: Nijhuis J, Schmidt S, Tran NN and Hessel V (2022) Microfluidics and Macrofluidics in Space: ISS-Proven Fluidic Transport and Handling Concepts. Front. Space Technol. 2:779696. doi: 10.3389/frspt.2021.779696
Received: 19 September 2021; Accepted: 14 December 2021;
Published: 26 January 2022.
Edited by:
Florian Kehl, University of Zurich, SwitzerlandReviewed by:
Mark Weislogel, IRPI, LLC, United StatesCopyright © 2022 Nijhuis, Schmidt, Tran and Hessel. This is an open-access article distributed under the terms of the Creative Commons Attribution License (CC BY). The use, distribution or reproduction in other forums is permitted, provided the original author(s) and the copyright owner(s) are credited and that the original publication in this journal is cited, in accordance with accepted academic practice. No use, distribution or reproduction is permitted which does not comply with these terms.
*Correspondence: Volker Hessel, dm9sa2VyLmhlc3NlbEBhZGVsYWlkZS5lZHUuYXU=
Disclaimer: All claims expressed in this article are solely those of the authors and do not necessarily represent those of their affiliated organizations, or those of the publisher, the editors and the reviewers. Any product that may be evaluated in this article or claim that may be made by its manufacturer is not guaranteed or endorsed by the publisher.
Research integrity at Frontiers
Learn more about the work of our research integrity team to safeguard the quality of each article we publish.