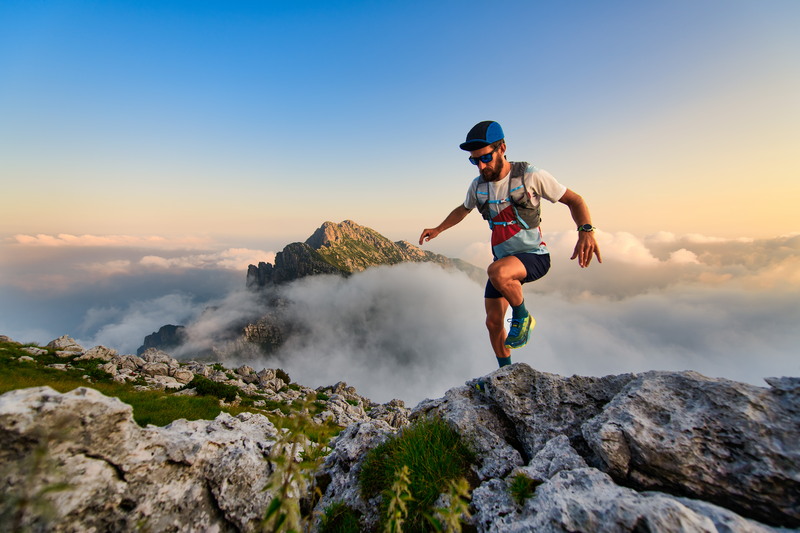
95% of researchers rate our articles as excellent or good
Learn more about the work of our research integrity team to safeguard the quality of each article we publish.
Find out more
REVIEW article
Front. Soft Matter , 14 November 2022
Sec. Liquid Crystals
Volume 2 - 2022 | https://doi.org/10.3389/frsfm.2022.1052037
This article is part of the Research Topic Editors' Showcase: Liquid Crystals View all 7 articles
Liquid crystal polymer networks (LCNs) have a great potential in soft actuator technologies. In contrast to other materials, LCNs offer a wide range of external stimuli which can trigger their actuation. These are for example based on changes of temperature, photo-induced or via the application of electric fields. We here discuss the main LCN actuation mechanisms and classify them into several groups based on the used stimulus. Specific recent examples are provided for liquid crystal actuators and several general applications of such materials in connection to actuation mechanisms are exemplary outlined.
Liquid crystals (LCs) are unique materials with an unusually rich phase diagram. Due to the anisotropic shape of their molecules (e.g., rod-like, disk-like), liquid crystals do not directly transition between the liquid and solid states, but go through one or several additional phases called liquid crystalline mesophases. Being in one of these states, matter exhibits properties of both liquids and solids: molecules can move freely, enabling a liquid-like flow; while at the same time their orientation is correlated, leading to the long-range orientational order observed in solids. Additionally, liquid crystals can exhibit low-dimensional positional order (1D—fluid smectics; 2D—hexatic smectics). Liquid crystalline mesophases differ in the type of orientational order and the order of the molecules’ centres of mass (Figure 1A). For example, in the nematic phase (N) on small scales molecules are oriented in the same direction on average, while there is no order in the positions of the centres of mass. Another very similar example is the cholesteric phase (N*), which is the chiral version of the nematic phase, the asterix “*” indicating chirality of the system, which often manifests itself through a helical superstructure. Similar to the nematic phase, the cholesteric molecules on small distances order parallel, but on larger scales they tend to form spiral structures, while the centre’s of mass exhibit no positional order. The fluid smectic state is also relatively similar to the nematic phase, but here this phase shows a long-range one-dimensional order of the centres of mass as the molecules are arranged in layers. The LC molecules can be parallel to the layer’s normal—the smectic A phase—or tilted relative to it—the smectic C phase. A number of other mesophases exist, information about which can be found in (Chandrasekhar, 1992; Stegemeyer, 1994; de Gennes and Prost, 1995; Blinov, 2011; Goodby et al., 2014; Collings and Goodby, 2019).
FIGURE 1. (A) Main liquid crystalline mesophases. The director n is shown with an arrow for each of the phases. (B) The architecture of a polymer network (left) and the gyration radii,
Liquid crystals are well known for their applications in display technologies (Lueder, 2010; Chen, 2011). The aim to improve display performance has been dictating the direction of LC research for many years. These efforts have resulted in LCD screens being integrated in numerous devices (Kawamoto, 2012). However, nowadays they start to be gradually replaced by the new, more efficient technology of organic light-emitting diodes (OLED) (Tsujimura, 2017). Therefore, other areas of LC research like biosensors (Luan et al., 2020), active matter (Zhang et al., 2021), optical devices (Jaroszewicz and Bennis, 2020), and soft actuators (Ula et al., 2018) started to attract more interest, promising new applications in the future.
This review is focused on liquid crystals in the context of actuators, devices which transform supplied energy into motion and changes of their shape. All actuators can be divided into two types: rigid and soft. The former, based on servomotors and MEMSs (micro–electro–mechanical systems), are well developed and used widely (in robotic manipulators on factories and building sites, microphones, scanning probe microscopes, etc.). At the same time, soft actuator technologies, based on soft and active materials (polymers, liquid crystals, colloids, shape memory alloys, etc.), only start to be actively investigated. This type of actuators is expected to provide several advantages over the rigid ones, such as smooth, complex, animal-like motions, a variety of external triggering stimuli that can be used as an energy source, a high adaptability to environment changes, biocompatibility as well as the possibility of the low-effort creation of sub-centimetres actuators (El-Atab et al., 2020). Applications in artificial muscles (Thomsen et al., 2001; Ambrogi et al., 2005), waste energy harvesting (Wei et al., 2018; Han et al., 2020), microfluidics (Chen et al., 2011, 2010; Lv et al., 2016), and soft robotics (Chang et al., 2021) are possible.
Among the materials used in soft actuator technologies, liquid crystal polymer networks play an important role because of the great variety of actuation-triggering stimuli. Except for few examples (Cheng et al., 2015; Lv et al., 2016), they are the only material used for liquid crystal-based actuators. That is the reason why this review is mainly concentrated on such materials. We will first explain the nature of LCNs and then discuss different mechanisms of their actuation, classifying them by the used external stimulus.
Liquid crystal polymer networks (Warner and Terentjev, 2003; de Jeu, 2012) are polymer networks (Figure 1B, left) with incorporated liquid crystal (or mesogenic) moieties (Figure 1C). Their existence was predicted by de Gennes in 1975 (de Gennes, 1975), while they were first synthesized by Finkelmann in 1981 (Finkelmann et al., 1981). The unique property of such systems is that the average orientation of mesogenic units, characterised by the vector
LCNs can be divided into liquid crystal elastomers (LCEs) and liquid crystal thermosets (LCTs, or duromers, or liquid crystal polymer networks as they are often referred to), which are lightly and highly cross-linked, respectively. Due to higher elasticity, enabling relatively large deformations, LCEs are more often investigated in the context of actuator technologies. Nevertheless, LCTs can also be used for this purpose.
The properties of building blocks used for the synthesis of LCNs (i.e., monomers, cross-linkers, mesogenic units, spacers), and the way the blocks are combined with each other significantly influence the liquid crystalline and mechanical properties of the networks and can be used to tune them. For example, mesogenic units determine the nature of liquid crystallinity of an LCN: thermotropic for rod- (Finkelmann et al., 1981) and disk-like (Kreuder et al., 1985) mesogens and less conventional lyotropic for amphiphilic mesogens (Löffer and Finkelmann, 1990) (lyotropic LCs (Neto and Salinas, 2005; Dierking and Martins Figueiredo Neto, 2020) exist in a certain range of LC unit concentrations instead of temperature ranges). The way mesogenic units are incorporated into a polymer network also plays an important role since it can determine the mesophase type. For example, LCNs can be divided into end-on LCNs (Figures 1Di,iii), for which LC units are connected with main- or side-chains of a polymer network along their long axis (for rods), and side-on LCNs (Figures 1Dii,iv), for which the connection is lateral. Notably, the former often form smectic phases (Brehmer et al., 1994; Nishikawa et al., 1997), while for the latter the nematic phase is more common (Thomsen et al., 2001). LCNs can also be divided into side-chain (Figures 1Di,ii) and main-chain (Figures 1Diii,iv) LCNs, depending on the LC units’ location in the network. Using monomers with chiral mesogens attached as side-chains helps to synthesise LCNs exhibiting the cholesteric and chiral smectic phases (Finkelmann et al., 1981; Zentel et al., 1987; Zentel, 1988; Kim and Finkelmann, 2001). The cross-linking density and the length of spacers which attach mesogens to main-chains in case of side-chain LCNs allow one to control the stiffness of the material (Kupfer et al., 1994). The creation of self-repairable systems is possible if special cross-linkers are used (Wang et al., 2017). There are numerous other ways to tune LCNs’ properties via their chemical design. Detailed information about them can be found in (Brömmel et al., 2012; Kularatne et al., 2017; Herbert et al., 2021).
Further, nematic LCNs will be used for the discussion and denoted just as LCNs, unless stated otherwise. However, almost all mechanisms can be realised in other LC phases as well.
Thermally induced actuation is based on the temperature dependence of the LCN order parameter,
where
FIGURE 2. (A) Temperature dependence of the order parameter S. (B) Schematic illustration of the thermally induced deformation of an LCN’s small element. (C) Schematic illustration of poly-domain and mono-domain LCNs. (D) Schematic illustration of the macroscopic, thermally induced deformation of a mono-domain LCN. (E) Bending of an LCN film with the so-called splay alignment (left) occurring due to the thermally induced contraction of its top side and elongation of the bottom side along the same direction (the elongation of the sides in the orthogonal direction does not contribute to the bending). Transformation into a cone for an LCN film with a concentric alignment with a +1 defect in the centre (right) occurring due to the thermally induced material expansion along the radial directions and contraction along the tangential directions. Polymer chains and changes in the thickness of the films are not shown.
However, the director is uniform only on a relatively small scale, inside domains into which a sample appears to be spontaneously split (Figure 2C, left). In this case, the LCN is called a poly-domain liquid crystal network. In the poly-domain state, domain shape changes do not result in the shape change of the whole network. In order to obtain a macroscopic deformation (Figure 2D), one needs to uniformly align LC units across the sample (Figure 2C, right), i.e., to prepare a mono-domain liquid crystal network. There are several alignment techniques used for this purpose, including mechanical stretching of a sample (Kupfer and Finkelmann, 1991), preparation in traditional LC cells with alignment layers (Thomsen et al., 2001), the alignment of LC units with magnetic (Buguin et al., 2006) or electric (Brehmer et al., 1994) fields, and others.
Controlled alignment patterning, which may be useful for some applications, can be achieved via the ink-jet printing technique (Gantenbein et al., 2018; Kotikian et al., 2018), by using LC cells with patterned alignment layers (Ware et al., 2016), and some other methods and results in more complex deformations, which often involve the 3D folding of a sample. Several examples of non-uniform LC units’ arrangements and corresponding thermally induced shape changes are shown in Figure 2E.
More information on alignment techniques can be found in comprehensive reviews by Kularatne et al. (2017) and Herbert et al. (2021). It should be noted that a predesigned LC molecules’ orientation is necessary for all mechanisms of LCN actuation and is realized using the same techniques mentioned above. Further, all discussed LCN systems will be mono-domain, unless stated otherwise.
Next, we will investigate different methods of changing the LCN’s temperature, which allow one to use the actuation mechanism for various purposes.
The simplest way to change the temperature of an LCN is to put it in a contact with an object of a different temperature. Choosing the environment as the object can be very beneficial as it allows one to create environmentally responsive and adaptive actuators. Such qualities can be used for biomedical applications, e.g., drug release systems (Jampani et al., 2018), low-grade waste heat harvesting (Han et al., 2020) and self-controlled technologies. However, from a technical point of view, it is difficult to use the thermal conduction method to perform a controlled actuation process, which can be desirable for applications in soft robotics. One of the approaches to overcome this problem, suggested by He et al. (2019a) and He et al. (2020), is the integration of water channels inside an LCN sample and channelling water of a desired temperature through the device. The authors demonstrated the feasibility of their actuator by animating an artificial skeleton (Figure 3A) (He et al., 2019b). However, the implementation of such a mechanism in technologies is still challenging, since it needs a water temperature control system, which is difficult to make compact enough. That is why other, semi-thermal methods, which still allow the use of the thermally induced actuation mechanism, are necessary.
FIGURE 3. (A) Arm bending by the contraction of biceps muscle and the elongation of triceps muscle made of mono-domain LCN films with integrated water channels. Reprinted with permission from He et al. (2019a). Copyright 2019 John Wiley and Sons. (B) LCN film deformations (i, ii, iii, iv) caused by irradiation with different VIS light patterns indicated in the top right corners (grey zones correspond to illuminated areas). The film bends due to the finite penetration of light into the LCN material which will be discussed further in the text. Reprinted with permission from Hauser et al. (2016). Copyright 2016 American Chemical Society. (C) Photo-thermally induced bending of a mono-domain LCN film caused by a finite light penetration depth. (D) Magnetic field strength dependence of magnetisation in case of a hysteresis.
Light can be employed to heat LCN if one introduces photo-thermal agents into the material (Dong and Zhao, 2018), which can convert light energy to thermal energy. Graphenes (Wei et al., 2016), carbon nanotubes (CNTs) (Ji et al., 2010; Camargo et al., 2011), metal nanoparticles (Sun et al., 2012; Hauser et al., 2016), dyes (de Haan et al., 2012; Guo et al., 2016; Gelebart et al., 2017; Liu L et al., 2017; Qin et al., 2020), and conjugated polymers (Liu et al., 2016) often serve as dopants due to their high light absorption and quantum yield of photo-thermal energy conversion for certain wavelengths (Dong and Zhao, 2018). Graphenes, CNTs, and metal nanoparticles are efficient at absorbing both visible (VIS) and near-infrared (NIR) light, while dyes are more specific (for instance, Lumogen IR788 (de Haan et al., 2012) and Dye 1002 (Kohlmeyer and Chen, 2013) are for NIR light; ABS407, ABS594, and ABS694 dyes (Qin et al., 2020) are for VIS light). Conjugated polymers are used for NIR light-responsive actuators.
This heating mechanism allows to control the actuation remotely (Dong and Zhao, 2018). This property can be employed in devices which work in dangerous conditions, e.g., in toxic environments or under high pressure. The creation of light-responsive actuators is possible and can be used, for example, in devices which monitor light conditions or light-harvesting technologies (Wei et al., 2018). Considering the fact that NIR light has a relatively high tissue penetration depth, and both VIS and NIR light are not harmful for biological systems, the discussed photo-thermal effect can also be used for bio-medical applications, e.g., telerobotic surgery. Another advantage is the possibility of a high-precision spatial control of light intensity, which allows one to perform shape deformations more complex than a simple contraction/elongation (Dong and Zhao, 2018) as was demonstrated by Hauser et al. (2016) (Figure 3B).
However, the photo-induced heating techniques encounter some challenges as well. Photo-thermal dopants are usually only poorly dispersible in LCNs, and thus achieving high concentrations, necessary to speed up switching-on actuation times, is often difficult and demands a special treatment of dopants. Additionally, high concentrations of dopants can make LCNs stiffer and in this way restrict deformation magnitudes. It also has to be taken into account that in the beginning of the irradiation process, a temperature gradient forms inside an LCN sample due to the finite light penetration depth. For a homogeneous film sample (i.e.,
The Joule heating effect can also be realised in LCN systems. For this purpose, conductive wires (Spillmann et al., 2007a; Petsch et al., 2014), layers (Greco et al., 2012), and nanoparticles (Chambers et al., 2009), channels filled with liquid metals (Kotikian et al., 2021), and liquid metal droplets (Ford et al., 2019; Kent et al., 2020; Ambulo et al., 2021) are added to LCNs. Using electricity to heat LCNs allows one to easily combine actuators with well-developed electronic technologies. However, for this approach heat transfer is often not efficient enough, while the incorporation of the external objects into LCNs often leads to the materials’ stiffening and relatively quick degradation due to the incompatibility of the objects with the LCNs. Furthermore, the degradation is also caused by large temperature gradients present in the system (Chambers et al., 2009).
In the presence of an alternating magnetic field (AMF) of a high enough frequency, the changes in the field and the magnetic dipole orientation of a ferromagnetic material can be not synchronised, leading to hysteresis (Figure 3D). Then, after one traversal, the work the magnetic field does on the system of a unit volume is
where
The advantage of this mechanism is the remote control of actuation. Moreover, AMFs with radio frequencies can be employed, which makes this heating mechanism very attractive in medicine. Biological tissues are mostly transparent for radio AMFs and so will not be heated by the fields (Dennis and Ivkov, 2013; Dutz and Hergt, 2013), while an actuator placed in a human body will be able to accept the signal. However, one can again expect problems related to the poor compatibility of the external objects with LCNs.
It is possible to induce the LC-isotropic phase transition without heating an LCN if photosensitive molecules, having rod-like and bent isomers, (most often azobenzene derivatives) are present in the system. While the molecules are in their extended rod-like form [called the trans-form for azobenzene derivatives (Figure 4C, left)], they stabilize liquid crystalline order in the LCN (Figure 4B, left). But if the sample is irradiated by light of a certain wavelength, these groups absorb photons and change their conformation to a bent form [the cis-form for azobenzene derivatives (Figure 4C, right)]. In this state, the molecules act like impurities and decrease the LC-isotropic transition temperature and thus lowering the degree of liquid crystalline order (Figure 4B, right, Figure 4A). This implies that by the illumination of a sample one can induce the actuation of an LCN isothermally, with the maximum contraction observed for
FIGURE 4. (A) The temperature dependence of the order parameter
This mechanism of actuation allows one to use light of a wide range of wavelengths as an external stimulus, namely UV, VIS and NIR light. Azobenzene derivatives normally need UV light to transform from the trans- to the cis-form (Figure 4C) (Pang et al., 2019). This part of the EM spectrum can be used for applications where actuators are not supposed to interact with living beings. However, if bio-medical applications are concerned, it is desirable to use VIS or NIR light as those are not harmful for biological substances. To shift the absorbance peak towards visible wavelengths, the use of azotolane instead of azobenzene derivatives was suggested (Figure 4D) (Yin et al., 2009; Zhao and Yu, 2014). NIR light can be used as an external stimulus if upconversion nanophosphors are incorporated into an LCN (Wu et al., 2011). An upconversion nanophosphor absorbs several NIR photons and then emits a single photon of a shorter wavelength in the UV or VIS range (Figure 4E), in a process known as upconversion luminescence. It is also possible to create a UV-VIS-NIR responsive actuator by incorporating both azobenzenes (for UV light-triggered photo-induced actuation) and graphene oxide (for VIS and NIR light-triggered photo-thermally induced actuation) (Cheng et al., 2015).
Azobenzene moieties can help to enhance mechanical properties if they are part of cross-linkers: they fold on light illumination and in this way pack polymer chains closer to each other, facilitating a contraction in the case of side-chain LCNs with the mutually orthogonal orientation of polymer chains and the director (Figure 5A) (Sánchez-Ferrer et al., 2011). Interesting concepts of actuation emerge if attention is paid to the incident light polarization. For example, Yu et al. (2003) showed that polydomain LCNs can also be effectively used for actuating devices. The authors irradiated a poly-domain LCN film with polarised light and observed a film bending along the polarisation direction (Figure 5B). The reason for such behaviour is that the light absorption efficiency of azobenzene derivatives is higher for light polarised along the
FIGURE 5. (A) Schematic illustration of the photo-induced contraction of a side-chain, mono-domain LCN, facilitated by the bending of azobenzene containing cross-linkers. (B) Poly-domain LCN film bending along different directions depending on light polarisation. Domains with the director
Disadvantages of such a mechanism include the limited number of suitable photosensitive molecules, the degradation of actuators caused by side reactions and photo-degradation, and sample bending due to the finite light penetration depth (Dong and Zhao, 2018).
Finally, it must be noted that the discussed photo-induced decrease in the liquid crystalline order and Weigert effect are well observed in liquid crystal elastomers but not in liquid crystal thermosets which are cross-linked too densely. Light-triggered actuation of the latter is mostly related to the change in photosensitive molecules length upon the transition from the rod-like to the bent state (White, 2018).
In the case of a special chemical design, LCNs can be forced to deform in response to the chemical composition of the environment. There are several concepts of creating such LCN systems. Let us consider several of them in somewhat more detail.
One of the concepts was suggested by Harris et al., 2007, Harris et al. (2005) and is based on LCNs in which the role of the mesogens is played by the polymer side-chains, paired in rod-like clusters via secondary bonds (Figure 6A, top). The bonds should be able to reversibly break or form in response to a certain chemical stimulus resulting in the change of the liquid crystalline order. The latter is expected to cause either LCN contraction along the director and its elongation perpendicular to it in case of decreasing order (bonds being broken) or the opposite behaviour in case of increasing order (bonds being formed).
FIGURE 6. (A) Mono-domain LCN, in which the role of mesogens is played by side-chains, paired in rod-like clusters by secondary bonds (top), and the shape change of the LCN caused by the breaking of the bonds after a certain change in the chemical composition of the environment (bottom). Reprinted with permission from Harris et al. (2005). Copyright 2005 American Chemical Society (B) The architecture of an LCN with the immobilized ureazse enzyme (top) and the scheme of the chemical reaction, leading to the creation of secondary bonds between side-chains (bottom). Reprinted with permission from Velasco Abadia et al. (2021). Copyright 2021 American Chemical Society. (C) Conformational change of a Bip-based derivative caused by its interaction with a metal ion (top) and the corresponding deformation of a mono-domain LCN. Reprinted with permission from Michal et al. (2015). Copyright 2015 American Chemical Society. (D) Schematic illustration of LCN actuation through the anisotropic swelling mechanism shown for a side-chain, mono-domain LCN.
With this idea in mind, the authors created a pH responsive LCN. The LCN’s polymer side-chains were caped with carboxylic acid units and paired in rod-like clusters via hydrogen bonds between the units. It was shown that the bonds could be effectively broken by LCN exposure to a high pH potassium hydroxide (KOH) solution which led to LCN actuation (Harris et al., 2005). In a later study on the same system (Harris et al., 2007), the authors demonstrated that instead of the expected contraction, an elongation along the director was observed, but the deformation was much smaller than the elongation in the plane orthogonal to the director and was attributed to network swelling in the KOH solution.
Other chemical stimuli can also be used to trigger LCN actuation. For example, Velasco Abadia et al. (2021) created an LCN responsive to urea. To achieve this, the authors immobilized the urease enzyme at the ends of some of the side-chains as it is shown in Figure 6B, top. In a water-urea solution, the enzyme catalysed a reaction between urea and water, which yielded ammonia as one of the products. The ammonia reacted with the acyl fluoride groups on the side-chains’ ends (which were not connected with the urease), generating benzamide groups (Figure 6B, bottom). In turn, the benzamide groups formed hydrogen bonds with each other, thus forming rod-like clusters and consequently increasing the liquid crystalline order. The latter resulted in LCN elongation along the director and contraction perpendicular to it (Velasco Abadia et al., 2021). The idea of using urease to trigger LCN actuation was further investigated and developed by the group in their later study (Abadia et al., 2022).
The discussed mechanism utilizing breakable mesogenic units can be tailored to other chemical reactions, giving a unique opportunity to broaden the range of chemical stimuli. The two studies by Velasco Abadia et al. (2021) and Abadia et al. (2022) made a significant step forward in this direction since there is the rich variety of enzymes in nature.
The second actuation concept is generally similar to the previous one, but in this case the change in liquid crystalline order results from the conformational change of mesogenic units in response to a chemical stimulus. A good illustration of this concept is the study by Michal et al. (2015) in which the authors prepared an LCN with mesogenic units sensitive to the presence of metal ions. In this study, a polymer network contained Bip-based derivatives as monomers (Bip: 2,6-bis (ben-zimidazolyl)-4-pyridine). In their usual configuration, the Bip-based derivatives are rod-like and tend to form an LC phase, whereas in the presence of metal ions, due to the ligand nature of Bip, they form a complex with the ions, and consequently bend, losing their liquid crystalline nature (Figure 6C, top). Therefore, when the LCN was exposed to a
This actuation concept exploits the ability of polymer networks to swell in response to a chemical stimulus and the ability of LC units to influence the alignment of polymer chains in a network. Indeed, in a mono-domain LCN, the coupling between the alignment of the LC units and polymer main-chains leads to the macroscopically anisotropic architecture of the network. Due to this fact, one can expect that the swelling process in LCNs should occur anisotropically as well, with network elongation being more pronounced in some particular direction (which would depend on the way the LC units are oriented relative to the main-chains), i.e., anisotropic LCN actuation should be observed (Figure 6D).
There are several mechanisms of polymer network swelling. One of them is based on the swelling of polyelectrolyte networks due to their ionization and can be illustrated on the same study by Harris et al. (2007), Harris et al. (2005) discussed earlier. In this work, the side-chain LCN exposure to a high pH KOH solution not only caused a decrease in LC order but also converted the carboxylic acid units into dissociable carboxylic acid salts of potassium and in this way made the network capable of ionization, i.e., transformed it into a polyelectrolyte. Therefore, in the presence of water, the salt units dissociated into ions, and the free
Boothby et al. (2017) exploited another swelling mechanism, which was based on LCN exposure to good solvents. By definition, a solvent is good for a given polymer if interactions between the polymer and the solvent are energetically beneficial. Due to this fact, polymer chains tend to expand in a good solvent in order to increase the amount of interaction. Therefore, an LCN exposed to a good solvent should swell. The authors demonstrated that their side-chain LCN indeed swelled in such organic solvents as tetrahydrofuran, acetone, dimethylformamide, and chloroform. Notably, the LCN did not expand in all directions as it was expected, yet with different efficiency. Instead, along the director a contraction was observed. It was hypothesized that the swelling related expansion in this direction was suppressed by the contraction due to the LC order decrease caused by the dilution of LC units which resulted from the increase in the sample volume.
In general, depending on the chemical design of a LCN and the chosen swelling mechanism, different solvents can be used as triggers, including water (Harris et al., 2005; de Haan et al., 2014; Liu Y et al., 2017), tetrahydrofuran, acetone, dimethylformamide, and chloroform (Boothby et al., 2017) as discussed above. Notably, the swelling of an LCN in a low molecular weight liquid crystals (LMWLCs) is a particularly interesting direction of research due to a rich variety of phenomena related to the orientational order of LMWLC in an LCN matrix (Yusuf et al., 2004b; 2004a; Matsuyama and Kushibe, 2010).
In general, chemically responsive LCNs have the advantage of a large variety of chemicals that can be used as triggers. At the same time, additional consideration should be given to the way of restoring the initial sample shape since this depends on the chemical reactions employed. The discussed actuation mechanisms can be used in drug technologies and various sensors (e.g., pH, humidity, metal ion sensors), while it seems to be difficult to use them in robotics.
Liquid crystals are often highly responsive to the electric fields, and this property gives an opportunity to use the latter to trigger LCN actuation. Let us consider the two main mechanisms of electrically induced actuation that have been suggested to date.
The electroclinic effect, first demonstrated by Garoff and Meyer (Garoff and Meyer, 1979; Garoff and Meyer, 1977), is a unique phenomena observed in chiral smectic phases and is most often described for the smectic A* (
FIGURE 7. (A) Shematic illustration of the electroclinik effect in a
The magnitude and direction of deformations (contraction/elongation) for such systems are independent of the electric filed polarity (Köhler et al., 2005; Spillmann et al., 2007b). The largest mechanical response to the electric field is usually observed at temperatures in the vicinity of the transition between
(see Figure 7A), where
Since this dependence is quadratic, this deformation is of electrostrictive nature (Damjanovic and Newnham, 1992), with
which corresponds to the piezoelectric effect (Damjanovic and Newnham, 1992). However, only the electrostrictive effect was confirmed in experiments (Lehmann et al., 2001; Köhler et al., 2005; Spillmann et al., 2007b), while for the second type of deformation the derived dependence does not hold (Spillmann et al., 2007b).
An advantage of this mechanism is the possibility of the remote control. Moreover, an electrostriction coefficient of up to
It should be noted that the same deformations can be induced by the transition between
It is well known that due to their non-zero dielectric anisotropy,
The discussed mechanism enables the remotely controlled actuation. However, as in the previous case, the electrically induced deformations are partially or completely suppressed in constrained films. (Qin and Yu 2017). Suspending films in silicon oil (Urayama et al., 2006; 2005a) or LMWLC (Zentel, 1986) is often used to prevent this effect. A theoretical consideration of actuation in constrained and unconstrained geometries can be found in (Terentjev et al., 1994).
Other deformation effects can be achieved if one changes an LCN architecture or the sign of LC units’ dielectric anisotropy in the network and the surrounding solution (Huang et al., 2003; Urayama et al., 2005b).
In this review, we provided an overview of the main LCN actuation mechanisms. The most popular and well-studied are the mechanisms of actuation based on thermal changes, which cause a change of the order parameter and therefore a change of the length of the LCN. This can be achieved by a range of different methods, for example heating through thermal conduction, photo-induced heating, electrically induced heating or magnetically induced heating. In any case it is preferable and simple from an applicational point of view to choose a method that is contactless, whenever possible, although this does obviously depend on the specific application and its performance requirements. For the latter reason, also the photo-induced actuation has been developed, which acts on the basis of trans-cis isomerisation of suitable mesogenic units, nearly exclusively containing azo-groups. Some actuators, mainly in the field of sensors, are required to react to chemical changes in the environment. In such actuators, mesogenic units used are often based on breakable bonds or are capable of conformational changes. Anisotropic swelling can also be employed to produce a chemoresponsive actuator. At last, a popular mechanism for actuation of liquid crystal networks is that via electrically induced shape- and order parameter changes. Here the electroclinic effect, which is electrostrictive in nature, is exploited, leading to a polarity independent, linear shape change of the LCN with applied electric field. Other electrical mechanisms are based on the realignment of the mesogens. To keep this review introductory, we considered only the basic principles of the described actuation mechanisms. However, theoretical and computer models, which quantitively describe the relation between stimulus and/or material parameters and the induced deformations, are being developed to facilitate the development of programable LCN devices. The recent overview of the results in this research direction can be found in (Soltani et al., 2021).
In order to provide a general idea (but by no means a comprehensive characterisation) of LCN mechanical performance, we have collected relative shape changes, actuation times, and exerted stresses from several discussed articles in Supplementary Table S1. From the table follows that the achieved length changes are of the order of several tens of percent (∼30%–50%) for average actuation time of the order of several seconds, up to minutes. Only the electrically induced actuation can occur at faster times of several milliseconds. It must be noted that in certain cases LCNs can change their dimensions by several hundred percent (Ahir et al., 2006). Stresses observed in the discussed articles range from tens to hundreds kPa although values of up to several GPa can also be achieved (White, 2018). In comparison to other types of soft actuators, which include electroactive, magnetoactive, ferroelectric, and shape memory polymers, hydrogels, shape memory alloys, and others, LCNs are generally slower but, at the same time, show large deformations. In terms of exerted stresses, these materials are comparable to other polymer-based soft actuators. Importantly, since the mechanical characteristics of an LCN actuator depend on its chemical and physical design, the proper tuning of the latter can often help to attain desired performance values. In addition to mechanical characteristics, such factors as production feasibility, the reversibility of deformations, material lifetime, and others should be considered when choosing a soft actuator type. A comprehensive comparison of different soft actuators in terms of various aspects can be found in (Apsite et al., 2022; Hao et al., 2022).
Today, LCN fabrication technologies and the understanding of the involved processes appear to have matured to a point suitable for the design of actual real devices. All actuation mechanisms have different advantages and disadvantages, and the prioritisation of one over the other needs to be based on the device requirements. A large range of different concepts of LCN actuators applications has already been suggested, e.g., in the fields of 1) waste-energy harvesting (Wei et al., 2018; Han et al., 2020), 2) microfluidics [pumps (Chen et al., 2010), valves (Chen et al., 2011), smart channels (Lv et al., 2016)], 3) smart surfaces (Nagai et al., 2016; Liu D et al., 2017; Ryabchun et al., 2021), 4) biomimetic technologies (Yang and Zhao, 2018; Zeng et al., 2018), 5) optical devices (Schuhladen et al., 2014; López-Valdeolivas et al., 2018), 6) soft robotics, and 7) medicine [drug technologies, artificial muscles (Thomsen et al., 2001; Ambrogi et al., 2005; Dong and Zhao, 2018)] (Figure 8). The results in this directions are summarised by a number of review articles (Jiang et al., 2013; Ula et al., 2018; Shang et al., 2019; Zhu et al., 2021). Investigations, aiming on more specific goals and supported by industry, could help to accelerate the development of technologies based on LCN actuators. In any case, this field of research is promising in materials design and will provide results and applications which will be useful in the future.
FIGURE 8. (A) Compact electrically controlled aperture, made of an LCN with conductive wires, for a phone camera. Reprinted with permission from Schuhladen et al. (2014). Copyright 2014 WILEY-VCH Verlag GmbH & Co. KGaA, Weinheim. (B) Griper, made of an LCN with conductive wires. Reprinted with permission from He et al. (2019b). Copyright 2019 AAAS. (C) Schematic illustration of a photo-controlled valve with an LCN membrane suggested in Chen et al. (2011). (D) Caterpillar-like walker powered by temporally modulated light. Reprinted with permission from Zeng et al. (2018). Copyright 2017 WILEY-VCH Verlag GmbH & Co. KGaA, Weinheim.
AG wrote the first draft of the review manuscript, which was critically revised by ID. The final manuscript was approved by all authors.
The authors declare that the research was conducted in the absence of any commercial or financial relationships that could be construed as a potential conflict of interest.
All claims expressed in this article are solely those of the authors and do not necessarily represent those of their affiliated organizations, or those of the publisher, the editors and the reviewers. Any product that may be evaluated in this article, or claim that may be made by its manufacturer, is not guaranteed or endorsed by the publisher.
The Supplementary Material for this article can be found online at: https://www.frontiersin.org/articles/10.3389/frsfm.2022.1052037/full#supplementary-material
Abadia, A. V., Herbert, K. M., White, T. J., Schwartz, D. K., and Kaar, J. L. (2022). Biocatalytic 3D actuation in liquid crystal elastomers via enzyme patterning. ACS Appl. Mat. Interfaces 14, 26480–26488. doi:10.1021/acsami.2c05802
Ahir, S. V., Tajbakhsh, A. R., and Terentjev, E. M. (2006). Self-assembled shape-memory fibers of triblock liquid-crystal polymers. Adv. Funct. Mat. 16, 556–560. doi:10.1002/adfm.200500692
Ambrogi, V., Giamberini, M., Cerruti, P., Pucci, P., Menna, N., Mascolo, R., et al. (2005). Liquid crystalline elastomers based on diglycidyl terminated rigid monomers and aliphatic acids. Part 1. Synthesis and characterization. Polymer 46, 2105–2121. doi:10.1016/j.polymer.2005.01.007
Ambulo, C. P., Ford, M. J., Searles, K., Majidi, C., and Ware, T. H. (2021). 4D-Printable liquid metal–liquid crystal elastomer composites. ACS Appl. Mat. Interfaces 13, 12805–12813. doi:10.1021/acsami.0c19051
Apsite, I., Salehi, S., and Ionov, L. (2022). Materials for smart soft actuator systems. Chem. Rev. 122, 1349–1415. doi:10.1021/acs.chemrev.1c00453
Blinov, L. M. (2011). Structure and properties of liquid crystals. Dordrecht, Heidelberg, London, New York: Springer.
Boothby, J. M., Kim, H., and Ware, T. H. (2017). Shape changes in chemoresponsive liquid crystal elastomers. Sensors Actuators B Chem. 240, 511–518. doi:10.1016/j.snb.2016.09.004
Brehmer, M., Zentel, R., Wagenblast, G., and Siemensmeyer, K. (1994). Ferroelectric liquid-crystalline elastomers. Macromol. Chem. Phys. 195, 1891–1904. doi:10.1002/macp.1994.021950601
Brömmel, F., Kramer, D., and Finkelmann, H. (2012). “Preparation of liquid crystalline elastomers,” in Liquid crystal elastomers: Materials and applications. Editor W. H. de Jeu (Berlin, Heidelberg: Springer), 1–48.
Buguin, A., Li, M.-H., Silberzan, P., Ladoux, B., and Keller, P. (2006). Micro-Actuators: When artificial muscles made of nematic liquid crystal elastomers meet soft lithography. J. Am. Chem. Soc. 128, 1088–1089. doi:10.1021/ja0575070
Camargo, C. J., Campanella, H., Marshall, J. E., Torras, N., Zinoviev, K., Terentjev, E. M., et al. (2011). Localised actuation in composites containing carbon nanotubes and liquid crystalline elastomers. Macromol. Rapid Commun. 32, 1953–1959. doi:10.1002/marc.201100578
Chambers, M., Finkelmann, H., Remškar, M., Sánchez-Ferrer, A., Zalar, B., and Žumer, S. (2009). Liquid crystal elastomer–nanoparticle systems for actuation. J. Mat. Chem. 19, 1524–1531. doi:10.1039/B812423J
Chang, K.-T., Liu, C.-Y., and Liu, J.-H. (2021). Bioinspired thermal/light-tunable actuators based on predesigned tilted liquid crystal actuators. J. Mat. Sci. 56, 12350–12363. doi:10.1007/s10853-021-06107-6
Chen, M., Huang, H., Zhu, Y., Liu, Z., Xing, X., Cheng, F., et al. (2011). Photodeformable CLCP material: Study on photo-activated microvalve applications. Appl. Phys. A 102, 667–672. doi:10.1007/s00339-010-6103-4
Chen, M., Xing, X., Liu, Z., Zhu, Y., Liu, H., Yu, Y., et al. (2010). Photodeformable polymer material: Towards light-driven micropump applications. Appl. Phys. A 100, 39–43. doi:10.1007/s00339-010-5853-3
Chen, R. H. (2011). Liquid crystal displays: Fundamental physics and technology. Hoboken, NJ: Wiley.
Cheng, Z., Wang, T., Li, X., Zhang, Y., and Yu, H. (2015). NIR–Vis–UV light-responsive actuator films of polymer-dispersed liquid crystal/graphene oxide nanocomposites. ACS Appl. Mat. Interfaces 7 (49), 27494–27501. doi:10.1021/acsami.5b09676
Collings, P. J., and Goodby, J. W. (2019). Introduction to liquid crystals: Chemistry and physics. 2nd edn. Boca Raton: CRC Press.
Damjanovic, D., and Newnham, R. E. (1992). Electrostrictive and piezoelectric materials for actuator applications. J. Intelligent Material Syst. Struct. 3, 190–208. doi:10.1177/1045389X9200300201
de Gennes, P. G., and Prost, J. (1995). The physics of liquid crystals. 2nd ed. Oxford, New York: Oxford University Press.
De Gennes, P. G. (1975). Reflexions sur un type de polymeres nematiques. C. R. Acad. Sci. Ser. B 281, 101–103.
De Haan, L. T., Sánchez-Somolinos, C., Bastiaansen, C. M. W., Schenning, A. P. H. J., and Broer, D. J. (2012). Engineering of complex order and the macroscopic deformation of liquid crystal polymer networks. Angew. Chem. Int. Ed. 51, 12469–12472. doi:10.1002/anie.201205964
De Haan, L. T., Verjans, J. M. N., Broer, D. J., Bastiaansen, C. W. M., and Schenning, A. P. H. J. (2014). Humidity-responsive liquid crystalline polymer actuators with an asymmetry in the molecular trigger that bend, fold, and curl. J. Am. Chem. Soc. 136, 10585–10588. doi:10.1021/ja505475x
De Jeu, W. H. (2012). Liquid crystal elastomers: Materials and applications. Berlin, Heidelberg: Springer.
Dennis, C. L., and Ivkov, R. (2013). Physics of heat generation using magnetic nanoparticles for hyperthermia. Int. J. Hyperth. 29, 715–729. doi:10.3109/02656736.2013.836758
Dierking, I., and Martins Figueiredo Neto, A. (2020). Novel trends in lyotropic liquid crystals. Crystals 10, 604. doi:10.3390/cryst10070604
Dong, L., and Zhao, Y. (2018). Photothermally driven liquid crystal polymer actuators. Mat. Chem. Front. 2, 1932–1943. doi:10.1039/C8QM00363G
Dutz, S., and Hergt, R. (2013). Magnetic nanoparticle heating and heat transfer on a microscale: Basic principles, realities and physical limitations of hyperthermia for tumour therapy. Int. J. Hyperth. 29, 790–800. doi:10.3109/02656736.2013.822993
El-Atab, N., Mishra, R. B., Al-Modaf, F., Joharji, L., Alsharif, A. A., Alamoudi, H., et al. (2020). Soft actuators for soft robotic applications: A review. Adv. Intell. Syst. 2, 2000128. doi:10.1002/aisy.202000128
Finkelmann, H., Kock, H.-J., and Rehage, G. (1981). Investigations on liquid crystalline polysiloxanes 3. Liquid crystalline elastomers — A new type of liquid crystalline material. Makromol. Chem. Rapid Commun. 2, 317–322. doi:10.1002/marc.1981.030020413
Ford, M. J., Ambulo, C. P., Kent, T. A., Markvicka, E. J., Pan, C., Malen, J., et al. (2019). A multifunctional shape-morphing elastomer with liquid metal inclusions. Proc. Natl. Acad. Sci. U. S. A. 116, 21438–21444. doi:10.1073/pnas.1911021116
Gantenbein, S., Masania, K., Woigk, W., Sesseg, J. P. W., Tervoort, T. A., and Studart, A. R. (2018). Three-dimensional printing of hierarchical liquid-crystal-polymer structures. Nature 561, 226–230. doi:10.1038/s41586-018-0474-7
Garoff, S., and Meyer, R. B. (1977). Electroclinic effect at theA−CPhase change in a chiral smectic liquid crystal. Phys. Rev. Lett. 38, 848–851. doi:10.1103/PhysRevLett.38.848
Garoff, S., and Meyer, R. B. (1979). Electroclinic effect at theA−Cphase change in a chiral smectic liquid crystal. Phys. Rev. A 19, 338–347. doi:10.1103/PhysRevA.19.338
Gelebart, A. H., Vantomme, G., Meijer, E. W., and Broer, D. J. (2017). Mastering the photothermal effect in liquid crystal networks: A general approach for self-sustained mechanical oscillators. Adv. Mat. 29, 1606712. doi:10.1002/adma.201606712
Goodby, J. W., Collings, P. J., Kato, T., Tschierske, C., Gleeson, H., Raynes, P., et al. (2014). Handbook of liquid crystals (8 vols). 2nd edn.Weinheim: Wiley VCH.
Greco, F., Domenici, V., Assaf, T., Romiti, S., and Mattoli, V. (2012). “Bending actuation of a composite liquid crystal elastomer via direct Joule heating,” in Proceedings of the 4th IEEE RAS EMBS International Conference on Biomedical Robotics and Biomechatronics (BioRob), Rome, Italy, 24-27 June 2012 (IEEE), 646–651. doi:10.1109/BioRob.2012.6290942
Guo, L.-X., Liu, M.-H., Sayed, S. M., Lin, B.-P., Keller, P., Zhang, X.-Q., et al. (2016). A calamitic mesogenic near-infrared absorbing croconaine dye/liquid crystalline elastomer composite. Chem. Sci. 7, 4400–4406. doi:10.1039/C6SC00758A
Han, Y., Jiang, C., Fu, H., Luo, C., Lin, H., and Peng, H. (2020). A flexible bilayer actuator based on liquid crystal network and PVDF–TrFE for low-grade waste heat harvesting. Energy Technol. 8, 2000612. doi:10.1002/ente.202000612
Hao, Y., Zhang, S., Fang, B., Sun, F., Liu, H., and Li, H. (2022). A review of smart materials for the boost of soft actuators, soft sensors, and robotics applications. Chin. J. Mech. Eng. 35, 37. doi:10.1186/s10033-022-00707-2
Harris, K. D., Bastiaansen, C. W. M., and Broer, D. J. (2007). Physical properties of anisotropically swelling hydrogen-bonded liquid crystal polymer actuators. J. Microelectromech. Syst. 16, 480–488. doi:10.1109/JMEMS.2006.886033
Harris, K. D., Bastiaansen, C. W. M., Lub, J., and Broer, D. J. (2005). Self-assembled polymer films for controlled agent-driven motion. Nano Lett. 5, 1857–1860. doi:10.1021/nl0514590
Hauser, A. W., Liu, D., Bryson, K. C., Hayward, R. C., and Broer, D. J. (2016). Reconfiguring nanocomposite liquid crystal polymer films with visible light. Macromolecules 49, 1575–1581. doi:10.1021/acs.macromol.6b00165
He, Q., Wang, Z., Song, Z., and Cai, S. (2019a). Bioinspired design of vascular artificial muscle. Adv. Mat. Technol. 4, 1800244. doi:10.1002/admt.201800244
He, Q., Wang, Z., Wang, Y., Minori, A., Tolley, M. T., and Cai, S. (2019b). Electrically controlled liquid crystal elastomer–based soft tubular actuator with multimodal actuation. Sci. Adv. 5, eaax5746. doi:10.1126/sciadv.aax5746
He, Q., Wang, Z., Wang, Y., Song, Z., and Cai, S. (2020). Recyclable and self-repairable fluid-driven liquid crystal elastomer actuator. ACS Appl. Mat. Interfaces 12, 35464–35474. doi:10.1021/acsami.0c10021
Herbert, K. M., Fowler, H. E., McCracken, J. M., Schlafmann, K. R., Koch, J. A., and White, T. J. (2021). Synthesis and alignment of liquid crystalline elastomers. Nat. Rev. Mat. 7, 23–38. doi:10.1038/s41578-021-00359-z
Hiraoka, K., Sagano, W., Nose, T., and Finkelmann, H. (2005). Biaxial shape memory effect exhibited by monodomain chiral smectic C elastomers. Macromolecules 38, 7352–7357. doi:10.1021/ma050642c
Huang, C., Zhang, Q. m., and Jákli, A. (2003). Nematic anisotropic liquid-crystal gels—self-assembled nanocomposites with high electromechanical response. Adv. Funct. Mat. 13, 525–529. doi:10.1002/adfm.200304322
Jampani, V. S. R., Mulder, D. J., De Sousa, K. R., Gélébart, A.-H., Lagerwall, J. P. F., and Schenning, A. P. H. J. (2018). Micrometer-scale porous buckling shell actuators based on liquid crystal networks. Adv. Funct. Mat. 28, 1801209. doi:10.1002/adfm.201801209
Ji, Y., Huang, Y. Y., Rungsawang, R., and Terentjev, E. M. (2010). Dispersion and alignment of carbon nanotubes in liquid crystalline polymers and elastomers. Adv. Mat. 22, 3436–3440. doi:10.1002/adma.200904103
Jiang, H., Li, C., and Huang, X. (2013). Actuators based on liquid crystalline elastomer materials. Nanoscale 5, 5225–5240. doi:10.1039/c3nr00037k
Kaiser, A., Winkler, M., Krause, S., Finkelmann, H., and Schmidt, A. M. (2009). Magnetoactive liquid crystal elastomer nanocomposites. J. Mat. Chem. 19, 538–543. doi:10.1039/B813120C
Kawamoto, H. (2012). “The history of liquid-crystal display and its industry,” in Proceedings of the 2012 Third IEEE HISTory of ELectro-Technology CONference (HISTELCON), Pavia, Italy, 05-07 September 2012 (IEEE), 1–6. doi:10.1109/HISTELCON.2012.6487587
Kent, T. A., Ford, M. J., Markvicka, E. J., and Majidi, C. (2020). Soft actuators using liquid crystal elastomers with encapsulated liquid metal joule heaters. Multifunct. Mat. 3, 025003. doi:10.1088/2399-7532/ab835c
Kim, S. T., and Finkelmann, H. (2001). Cholesteric liquid single-crystal elastomers (LSCE) obtained by the anisotropic deswelling method. Macromol. Rapid Commun. 22, 429–433. doi:10.1002/1521-3927(20010301)22:6<429::aid-marc429>3.0.co;2-#
Köhler, R., Stannarius, R., Tolksdorf, C., and Zentel, R. (2005). Electroclinic effect in free-standing smectic elastomer films. Appl. Phys. A 80, 381–388. doi:10.1007/s00339-003-2267-5
Kohlmeyer, R. R., and Chen, J. (2013). Wavelength-selective, IR light-driven hinges based on liquid crystalline elastomer composites. Angew. Chem. Int. Ed. Engl. 125, 9404–9407. doi:10.1002/ange.201210232
Kotikian, A., Morales, J. M., Lu, A., Mueller, J., Davidson, Z. S., Boley, J. W., et al. (2021). Innervated, self-sensing liquid crystal elastomer actuators with closed loop control. Adv. Mat. 33, 2101814. doi:10.1002/adma.202101814
Kotikian, A., Truby, R. L., Boley, J. W., White, T. J., and Lewis, J. A. (2018). 3D printing of liquid crystal elastomeric actuators with spatially programed nematic order. Adv. Mat. 30, 1706164. doi:10.1002/adma.201706164
Kreuder, W., Ringsdorf, H., and Tschirner, P. (1985). Liquid crystalline polymers with disc-like mesogens in the main chain. Makromol. Chem. Rapid Commun. 6, 367–373. doi:10.1002/marc.1985.030060513
Kularatne, R. S., Kim, H., Boothby, J. M., and Ware, T. H. (2017). Liquid crystal elastomer actuators: Synthesis, alignment, and applications. J. Polym. Sci. Part B Polym. Phys. 55, 395–411. doi:10.1002/polb.24287
Küpfer, J., and Finkelmann, H. (1991). Nematic liquid single crystal elastomers. Makromol. Chem. Rapid Commun. 12, 717–726. doi:10.1002/marc.1991.030121211
Küpfer, J., Nishikawa, E., and Finkelmann, H. (1994). Densely crosslinked liquid single-crystal elastomers. Polym. Adv. Technol. 5, 110–115. doi:10.1002/pat.1994.220050205
Lehmann, W., Skupin, H., Tolksdorf, C., Gebhard, E., Zentel, R., Krüger, P., et al. (2001). Giant lateral electrostriction in ferroelectric liquid-crystalline elastomers. Nature 410, 447–450. doi:10.1038/35068522
Liu D, D., Tito, N. B., and Broer, D. J. (2017). Protruding organic surfaces triggered by in-plane electric fields. Nat. Commun. 8, 1526. doi:10.1038/s41467-017-01448-w
Liu L, L., Liu, M.-H., Deng, L.-L., Lin, B.-P., and Yang, H. (2017). Near-infrared chromophore functionalized soft actuator with ultrafast photoresponsive speed and superior mechanical property. J. Am. Chem. Soc. 139, 11333–11336. doi:10.1021/jacs.7b06410
Liu, W., Guo, L.-X., Lin, B.-P., Zhang, X.-Q., Sun, Y., and Yang, H. (2016). Near-infrared responsive liquid crystalline elastomers containing photothermal conjugated polymers. Macromolecules 49, 4023–4030. doi:10.1021/acs.macromol.6b00640
Liu Y, Y., Xu, B., Sun, S., Wei, J., Wu, L., and Yu, Y. (2017). Humidity- and photo-induced mechanical actuation of cross-linked liquid crystal polymers. Adv. Mat. 29, 1604792. doi:10.1002/adma.201604792
Löffer, R., and Finkelmann, H. (1990). Amphiphilic liquid-crystalline elastomers. Makromol. Chem. Rapid Commun. 11, 321–328. doi:10.1002/marc.1990.030110704
López-Valdeolivas, M., Liu, D., Broer, D. J., and Sánchez-Somolinos, C. (2018). 4D printed actuators with soft-robotic functions. Macromol. Rapid Commun. 39, 1700710. doi:10.1002/marc.201700710
Luan, C., Luan, H., and Luo, D. (2020). Application and technique of liquid crystal-based biosensors. Micromachines 11, 176. doi:10.3390/mi11020176
Lueder, E. (2010). Liquid crystal displays: Addressing schemes and electro-optical effects. 2nd edn. Wiley.
Lv, J., Liu, Y., Wei, J., Chen, E., Qin, L., and Yu, Y. (2016). Photocontrol of fluid slugs in liquid crystal polymer microactuators. Nature 537, 179–184. doi:10.1038/nature19344
Matsuyama, A., and Kushibe, Y. (2010). Three stage-volume phase transitions of a side-chain liquid crystalline elastomer immersed in nematic solvents. J. Chem. Phys. 132, 104903. doi:10.1063/1.3353611
Michal, B. T., McKenzie, B. M., Felder, S. E., and Rowan, S. J. (2015). Metallo-Thermo-and photoresponsive shape memory and actuating liquid crystalline elastomers. Macromolecules 48, 3239–3246. doi:10.1021/acs.macromol.5b00646
Nagai, H., Liang, X., Nishikawa, Y., Nakajima, K., and Urayama, K. (2016). Periodic surface undulation in cholesteric liquid crystal elastomers. Macromolecules 49, 9561–9567. doi:10.1021/acs.macromol.6b01688
Neto, A. M. F., and Salinas, S. R. A. (2005). The physics of lyotropic liquid crystals: Phase transitions and structural properties. Oxford, New York: Oxford University Press.
Nishikawa, E., Finkelmann, H., and Brand, H. R. (1997). Smectic A liquid single crystal elastomers showing macroscopic in-plane fluidity. Macromol. Rapid Commun. 18, 65–71. doi:10.1002/marc.1997.030180201
Okamoto, T., Urayama, K., and Takigawa, T. (2011). Large electromechanical effect of isotropic-genesis polydomain nematic elastomers. Soft Matter 7, 10585–10589. doi:10.1039/C1SM06372C
Pang, X., Lv, J., Zhu, C., Qin, L., and Yu, Y. (2019). Photodeformable azobenzene-containing liquid crystal polymers and soft actuators. Adv. Mat. 31, 1904224. doi:10.1002/adma.201904224
Petsch, S., Rix, R., Reith, P., Khatri, B., Schuhladen, S., Ruh, D., et al. (2014). “A thermotropic liquid crystal elastomer micro-actuator with integrated deformable micro-heater,” in Proceedings of the 2014 IEEE 27th International Conference on Micro Electro Mechanical Systems (MEMS), San Francisco, 26-30 January 2014 (IEEE), 905–908. doi:10.1109/MEMSYS.2014.6765788
Qin, B., Yang, W., Xu, J., Wang, X., Li, X., Li, C., et al. (2020). Photo-actuation of liquid crystalline elastomer materials doped with visible absorber dyes under quasi-daylight. Polymers 12, 54. doi:10.3390/polym12010054
Qin, L., and Yu, Y. (2017). “Light-responsive surface: Photodeformable cross-linked liquid-crystalline polymers based on photochemical phase transition,” in Responsive polymer surfaces. Editors D. Liu, and D. J. Broer (Hoboken, New Jersey, United States: John Wiley & Sons), 1–34.
Ryabchun, A., Lancia, F., and Katsonis, N. (2021). Light-fueled nanoscale surface waving in chiral liquid crystal networks. ACS Appl. Mat. Interfaces 13, 4777–4784. doi:10.1021/acsami.0c20006
Sánchez-Ferrer, A., Merekalov, A., and Finkelmann, H. (2011). Opto-mechanical effect in photoactive nematic side-chain liquid-crystalline elastomers. Macromol. Rapid Commun. 32, 671–678. doi:10.1002/marc.201100005
Schuhladen, S., Preller, F., Rix, R., Petsch, S., Zentel, R., and Zappe, H. (2014). Iris-like tunable aperture employing liquid-crystal elastomers. Adv. Mat. 26, 7247–7251. doi:10.1002/adma.201402878
Shang, Y., Wang, J., Ikeda, T., and Jiang, L. (2019). Bio-inspired liquid crystal actuator materials. J. Mat. Chem. C 7, 3413–3428. doi:10.1039/C9TC00107G
Soltani, M., Raahemifar, K., Nokhosteen, A., Kashkooli, F. M., and Zoudani, E. L. (2021). Numerical methods in studies of liquid crystal elastomers. Polymers 13, 1650. doi:10.3390/polym13101650
Spillmann, C. M., Naciri, J., Martin, B. D., Farahat, W., Herr, H., and Ratna, B. R. (2007a). Stacking nematic elastomers for artificial muscle applications. Sensors Actuators A Phys. 133, 500–505. doi:10.1016/j.sna.2006.04.045
Spillmann, C. M., Ratna, B. R., and Naciri, J. (2007b). Anisotropic actuation in electroclinic liquid crystal elastomers. Appl. Phys. Lett. 90, 021911. doi:10.1063/1.2420780
Sun, Y., Evans, J. S., Lee, T., Senyuk, B., Keller, P., He, S., et al. (2012). Optical manipulation of shape-morphing elastomeric liquid crystal microparticles doped with gold nanocrystals. Appl. Phys. Lett. 100, 241901. doi:10.1063/1.4729143
Terentjev, E. M., Warner, M., and Bladon, P. (1994). Orientation of nematic elastomers and gels by electric fields. J. Phys. II Fr. 4, 667–676. doi:10.1051/jp2:1994154
Thomsen, D. L., Keller, P., Naciri, J., Pink, R., Jeon, H., Shenoy, D., et al. (2001). Liquid crystal elastomers with mechanical properties of a muscle. Macromolecules 34, 5868–5875. doi:10.1021/ma001639q
Ula, S. W., Traugutt, N. A., Volpe, R. H., Patel, R. R., Yu, K., and Yakacki, C. M. (2018). Liquid crystal elastomers: An introduction and review of emerging technologies. Liq. Cryst. Rev. 6, 78–107. doi:10.1080/21680396.2018.1530155
Urayama, K., Honda, S., and Takigawa, T. (2006). Deformation coupled to director rotation in swollen nematic elastomers under electric fields. Macromolecules 39, 1943–1949. doi:10.1021/ma052762q
Urayama, K., Honda, S., and Takigawa, T. (2005a). Electrooptical effects with anisotropic deformation in nematic gels. Macromolecules 38, 3574–3576. doi:10.1021/ma0503054
Urayama, K., Kondo, H., Arai, Y. O., and Takigawa, T. (2005b). Electrically driven deformations of nematic gels. Phys. Rev. E 71, 051713. doi:10.1103/PhysRevE.71.051713
Velasco Abadia, A., Herbert, K. M., Matavulj, V. M., White, T. J., Schwartz, D. K., and Kaar, J. L. (2021). Chemically triggered changes in mechanical properties of responsive liquid crystal polymer networks with immobilized urease. J. Am. Chem. Soc. 143, 16740–16749. doi:10.1021/jacs.1c08216
Wang, Z., Tian, H., He, Q., and Cai, S. (2017). Reprogrammable, reprocessible, and self-healable liquid crystal elastomer with exchangeable disulfide bonds. ACS Appl. Mat. Interfaces 9, 33119–33128. doi:10.1021/acsami.7b09246
Ware, T. H., Biggins, J. S., Shick, A. F., Warner, M., and White, T. J. (2016). Localized soft elasticity in liquid crystal elastomers. Nat. Commun. 7, 10781. doi:10.1038/ncomms10781
Warner, M., and Terentjev, E. M. (2003). Liquid crystal elastomers, international series of monographs on physics. Oxford, New York: Oxford University Press.
Wei, R., Wang, Z., Zhang, H., and Liu, X. (2016). Photo-responsive liquid crystalline elastomer with reduced chemically modified graphene oxide. Liq. Cryst. 43, 1009–1016. doi:10.1080/02678292.2016.1155773
Wei, W., Gao, J., Yang, J., Wei, J., and Guo, J. (2018). A NIR light-triggered pyroelectric-dominated generator based on a liquid crystal elastomer composite actuator for photoelectric conversion and self-powered sensing. RSC Adv. 8, 40856–40865. doi:10.1039/C8RA08491B
White, T. J. (2018). Photomechanical effects in liquid crystalline polymer networks and elastomers. J. Polym. Sci. Part B Polym. Phys. 56, 695–705. doi:10.1002/polb.24576
Winkler, M., Kaiser, A., Krause, S., Finkelmann, H., and Schmidt, A. M. (2010). Liquid crystal elastomers with magnetic actuation. Macromol. Symp. 291–292, 186–192. doi:10.1002/masy.201050522
Wu, W., Yao, L., Yang, T., Yin, R., Li, F., and Yu, Y. (2011). NIR-Light-Induced deformation of cross-linked liquid-crystal polymers using upconversion nanophosphors. J. Am. Chem. Soc. 133, 15810–15813. doi:10.1021/ja2043276
Yang, R., and Zhao, Y. (2018). Multitemperature memory actuation of a liquid crystal polymer network over a broad nematic–isotropic phase transition induced by large strain. ACS Macro Lett. 7, 353–357. doi:10.1021/acsmacrolett.8b00089
Yin, R., Xu, W., Kondo, M., Yen, C.-C., Mamiya, J., Ikeda, T., et al. (2009). Can sunlight drive the photoinduced bending of polymer films? J. Mat. Chem. 19, 3141–3143. doi:10.1039/B904973H
Yu, Y., Nakano, M., and Ikeda, T. (2003). Directed bending of a polymer film by light. Nature 425, 145. doi:10.1038/425145a
Yusuf, Y., Cladis, E. P., Brand, H. R., Finkelmann, H., and Kai, S. (2004a). Hystereses of volume changes in liquid single crystal elastomers swollen with low molecular weight liquid crystal. Chem. Phys. Lett. 389, 443–448. doi:10.1016/j.cplett.2004.04.003
Yusuf, Y., Ono, Y., Sumisaki, Y., Cladis, P. E., Brand, H. R., Finkelmann, H., et al. (2004b). Swelling dynamics of liquid crystal elastomers swollen with low molecular weight liquid crystals. Phys. Rev. E 69, 021710. doi:10.1103/PhysRevE.69.021710
Zeng, H., Wani, O. M., Wasylczyk, P., and Priimagi, A. (2018). Light-Driven, caterpillar-inspired miniature inching robot. Macromol. Rapid Commun. 39, 1700224. doi:10.1002/marc.201700224
Zentel, R., Reckert, G., and Reck, B. (1987). New liquid-crystalline polymers with chiral phases. Liq. Cryst. 2, 83–89. doi:10.1080/02678298708086640
Zentel, R. (1986). Shape variation of cross-linked liquid-crystalline polymers by electric fields. Liq. Cryst. 1, 589–592. doi:10.1080/02678298608086283
Zentel, R. (1988). Untwisting of the helical superstructure in the cholesteric and chiral smectic C∗phases of cross-linked liquid-crystalline polymers by strain. Liq. Cryst. 3, 531–536. doi:10.1080/02678298808086399
Zhang, R., Mozaffari, A., and de Pablo, J. J. (2021). Autonomous materials systems from active liquid crystals. Nat. Rev. Mat. 6, 437–453. doi:10.1038/s41578-020-00272-x
Zhao, J., and Yu, Y. (2014). Visible light induced bending behavior of crosslinked liquid crystal polymers containing azotolane with a longer spacer. Mol. Cryst. Liq. Cryst. 601, 134–141. doi:10.1080/15421406.2014.940566
Keywords: liquid crystal, elastomer, polymer network, actuator, actuation mechanisms, actuation triggers
Citation: Gruzdenko A and Dierking I (2022) Liquid crystal-based actuators. Front. Soft. Matter 2:1052037. doi: 10.3389/frsfm.2022.1052037
Received: 23 September 2022; Accepted: 31 October 2022;
Published: 14 November 2022.
Edited by:
Hiroshi Yokoyama, Kent State University, United StatesReviewed by:
Shaoting Lin, Massachusetts Institute of Technology, United StatesCopyright © 2022 Gruzdenko and Dierking. This is an open-access article distributed under the terms of the Creative Commons Attribution License (CC BY). The use, distribution or reproduction in other forums is permitted, provided the original author(s) and the copyright owner(s) are credited and that the original publication in this journal is cited, in accordance with accepted academic practice. No use, distribution or reproduction is permitted which does not comply with these terms.
*Correspondence: Ingo Dierking, aW5nby5kaWVya2luZ0BtYW5jaGVzdGVyLmFjLnVr
Disclaimer: All claims expressed in this article are solely those of the authors and do not necessarily represent those of their affiliated organizations, or those of the publisher, the editors and the reviewers. Any product that may be evaluated in this article or claim that may be made by its manufacturer is not guaranteed or endorsed by the publisher.
Research integrity at Frontiers
Learn more about the work of our research integrity team to safeguard the quality of each article we publish.