- 1Control and Systems Engineering Department, University of Technology-Iraq, Baghdad, Iraq
- 2College of Computer and Information Sciences, Prince Sultan University, Riyadh, Saudi Arabia
- 3Automated Systems and Soft Computing Lab (ASSCL), Prince Sultan University, Riyadh, Saudi Arabia
- 4Faculty of Computers and Artificial Intelligence, Benha University, Benha, Egypt
The performance of the robotic manipulator is negatively impacted by outside disturbances and uncertain parameters. The system’s variables are also highly coupled, complex, and nonlinear, indicating that it is a multi-input, multi-output system. Therefore, it is necessary to develop a controller that can control the variables in the system in order to handle these complications. This work proposes six control structures based on neural networks (NNs) with proportional integral derivative (PID) and fractional-order PID (FOPID) controllers to operate a 2-link rigid robot manipulator (2-LRRM) for trajectory tracking. These are named as set-point-weighted PID (W-PID), set-point weighted FOPID (W-FOPID), recurrent neural network (RNN)-like PID (RNNPID), RNN-like FOPID (RNN-FOPID), NN+PID, and NN+FOPID controllers. The zebra optimization algorithm (ZOA) was used to adjust the parameters of the proposed controllers while reducing the integral-time-square error (ITSE). A new objective function was proposed for tuning to generate controllers with minimal chattering in the control signal. After implementing the proposed controller designs, a comparative robustness study was conducted among these controllers by altering the initial conditions, disturbances, and model uncertainties. The simulation results demonstrate that the NN+FOPID controller has the best trajectory tracking performance with the minimum ITSE and best robustness against changes in the initial states, external disturbances, and parameter uncertainties compared to the other controllers.
1 Introduction
The field of robotics mainly focuses on problems related to visualization, modeling, and control. Robots are used in many daily tasks and occupations in every aspect of modern life. Robotic manipulators are increasingly required in factories and industries as they play important roles in the operations instead of humans, especially when these operations involve risky, repetitive, and complex activities (Oleiwi et al., 2021). The use of robots has also become necessary to ensure efficient, quick, and accurate operations. Traditional robots are large and bulky since they contain stiff linkages throughout their construction; most industries need upgrades to the current classical robots to lower the building costs, minimize energy consumption brought on by the large actuators, and boost production (Alandoli and Tian, 2020). Since robotic manipulators are well-suited for many applications, particularly in the industrial field, they have been widely used for many years. The trajectory tracking control is an important issue from the viewpoint of automatic control because various applications, such as welding, screwing, moving cars or equipment parts, and painting, demand precise trajectory tracking to accomplish their objectives (Azar and Fernando, 2019). The complexity and non-linearity of a robotic manipulator make it impossible for proportional integral derivative (PID) controllers to provide effective trajectory tracking and constant force/twist control simultaneously. The robotic manipulator also experiences a number of uncertainties, external disturbances, payload variations, and parameter variations during operation (Dachang et al., 2020; Abdulameer and Mohamed, 2022). To design controllers that can handle the dynamics of the manipulator robot for controlling and trajectory tracking, many solutions have been proposed using traditional control systems (Ajeil et al., 2020; Ibraheem et al., 2020; Najm et al., 2020). Sharma et al. (2015) described the design and analysis of a fractional-order PID (FOPID) controller with two degrees of freedom (DOFs) based on the cuckoo search algorithm for a two-link rigid robot manipulator (2-LRRM) with a payload; their results indicated that the suggested strategy improves the performance of the closed-loop system by resolving robustness and disturbance rejection issues. Kumar (2017) proposed an interval type-2 fuzzy proportional derivative plus integral controller based on the genetic algorithm for a 5-DOF redundant robot manipulator. Cao et al. (2021) introduced an invariant control structure for manipulator robot trajectory tracking with input saturation and uncertainty by combining reinforcement learning and non-singular terminal sliding-mode control. Shuyang and John (2021) applied a neural network (NN) as a multilayer perceptron structure based on the iterative process of learning; here, the desired robot joint was employed as the input, and the desired robot motion was related to the output; the movement of the robot with respect to the intended set of joint paths is determined by the iterative learning control. Shojaei et al. (2020) suggested a specific performance-based adaptive neural control system for manipulator robots without considering the input current, acceleration, or velocity; this scheme includes the actuator dynamics under model uncertainty, and an acceleration velocity observer was coupled with a neural adaptive second-order PID controller. Nohooji (2020) addressed the unknown dynamics and outside disturbances of a manipulator robot to design a control approach utilizing NN-based radial basis activation functions and self-tuning PID control. Zhou et al. (2020) and Kareem et al. (2023) introduced fractional-order sliding-mode control using a deep convolutional NN for controlling trajectory tracking in manipulator robots; here, the controller switching gain decreased drastically since the NN corrects the uncertainty of the system without knowledge of the upper boundaries. Four distinguished non-linear control structures were studied by Jenhani et al. (2022) to address the problem of controlling and stabilizing robotic systems to predefined positions. To control the position and velocity of the 2-link robot, classical and adaptive sliding-mode controllers were introduced by Al-Hadithy and Hammoudi (2020) as well as Hameed and Hamoudi (2023). Hamoudi and Rasheed (2023) used particle swarm optimization to study the effectiveness of adaptive and classical backstepping control schemes for non-linear systems.
It is well-known in intelligent control that the NN controller can be used to solve various control issues, particularly when the controlled plant displays non-linearity and/or uncertainties in the model parameters. The advantage of the NN is that it has solid capability for mapping. Conversely, the PID controller is the most widely used controller in the industry because of its robust performance under numerous operating conditions and straightforward design. Therefore, in our proposed controllers, we merge the advantages of NNs with those of the PID and FOPID controllers to obtain hybrid controllers based on the zebra optimization algorithm (ZOA) to control a 2-LRRM.
The following are the main contributions of this work:
1. Six control structures are proposed based on NNs with PID/FOPID operations.
2. ZOA is used to adjust the gains of the proposed control structures on the basis of reducing the integral-time-square error (ITSE) performance index.
3. A comparative robustness study is conducted among the proposed control structures by altering the initial conditions, disturbances, and model uncertainties.
4. A new objective function is proposed for the tuning process to obtain controllers with minimal chattering in the control signals.
The remainder of this paper is structured as follows: the 2-LRRM’s mathematical model is described in Section 2. The proposed controller structures are discussed in Section 3. The ZOA is explained in Section 4. The simulation results are shown in Section 5; the robustness tests are presented in Section 6, and the conclusions are presented in Section 7.
2 Mathematical model of the 2-LRRM
The 2-LRRM structure is illustrated in Figure 1. It is composed of two links with lengths
The equations describing the x and y positions of
The conventional form can be applied to the manipulator dynamics as indicated in Eqs. (1-10)
where
The Coriolis/centrifugal vector denoted by V is of the form
The gravity vector
The 2-LRRM parameter specifications are as listed in Table 1 (Mohamed et al., 2023).
3 Structures of the proposed hybrid controllers
This section provides the descriptions of the proposed controllers below.
3.1 Set-point-weighted PID and FOPID controllers
This section discusses set-point-weighted PID and FOPID controllers. The block diagram of this feedback control system is indicated in Figure 2.
The equation describing the set-point-weighted PID (W-PID) controller is presented in Eq. (11):
where
Here,
where
In Eqs. (11, 12),
The set-point-weighted PID and FOPID controller structures are demonstrated in Figure 3.
3.2 Recurrent neural network (RNN)-like PID and FOPID controllers
In these two controllers, RNN-like PID and FOPID are adopted. The block diagram of the feedback control system for this type of hybrid controller is shown in Figure 4. The common structure of the RNN-PID and RNN-FOPID controllers is shown in Figure 5. For the conventional PID controller, the order variables have integer values
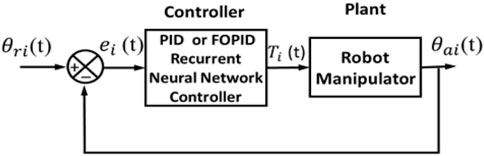
Figure 4. Recurrent-neural-network-like PID and FOPID controller block diagrams (RNN-PID and RNN-FOPID).
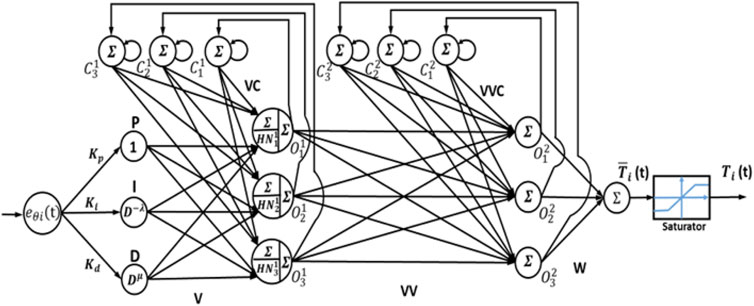
Figure 5. Recurrent-neural-network-like PID and FOPID structures (RNN-PID and RNN-FOPID controllers).
In the RNN-PID controller, the input layer has a single neuron
where, the feedback and processing elements in the second hidden layer are defined in Eqs. (16-17)
and
The output of the second hidden layer is given by Eq. (18):
The activation function used is a sigmoid function, as shown in Eq. (19):
where, the feedback elements in the third hidden layer are defined in Eq. (20)
The output of the third hidden layer is expressed in Eq. (21):
The output of the single neuron in the output layer is given in Eq. (22):
where
In the RNN-FOPID controller, the input layer again has a single neuron
3.3 NN-based PID and FOPID controllers
In this type of controller, the NN and PID/FOPID controllers both contribute to the production of the control signal. Figure 6 displays the feedback control system block diagram for this type of controller.
The common structure for these two controllers is indicated in Figure 7.
For the conventional PID controller, the order variables have integer values
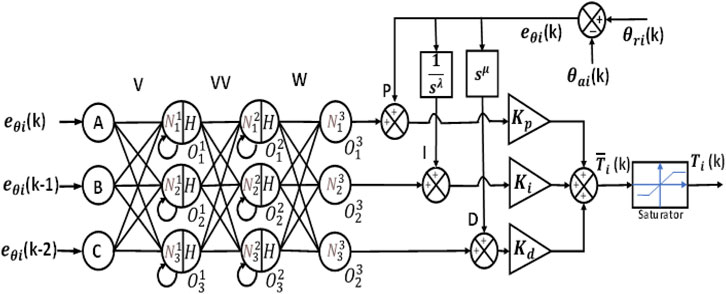
Figure 7. Neural network combined with PID and FOPID controller structures (NN + PID and NN + FOPID).
Thus, the first layer of hidden neurons is given by Eq. (26):
The output of the first hidden layer is given by Eq. (27):
The input and output of the second hidden layer are given by Eqs (28, 29), respectively.
The activation function used is a sigmoid function, as shown in Eq. (30):
The output of the third hidden layer is given by Eq. (31):
Equations (32–34) define the three control actions of the PID controller, and each of these control actions is added to one of the neuron outputs of the NN, as shown in Eqs. (35–37).
The equation of the control signal is expressed by Eq. (38):
The structure of the NN + FOPID controller is the same as that of the NN + PID controller, with the difference being fractional-order operations of the integral and derivative functions given by
The equation of the control signal is given by Eq. (45):
4 Zebra optimization algorithm
The ZOA is a nature-inspired metaheuristic algorithm and is presented mathematically in this section (Trojovská et al., 2022). The actions of zebras in the wild serve as the primary source of inspiration for the ZOA, where the foraging behaviors and defense mechanisms against predator attacks are simulated. The description is provided first, followed by the mathematical modeling of the ZOA steps. Effective real-world optimization issues can be resolved by the ZOA by achieving an appropriate balance between exploration and exploitation.
• Initialization
The population of zebras that provide a solution to the problem can be numerically modeled using a matrix, in addition to the plain where the zebras are located inside the search space. Within the search area, the zebras are positioned randomly at their starting positions. Equation (46) provides the structure of the ZOA population matrix.
where X is the population, N is the total number of initial solutions in the population, and m is the number of variables in each solution;
where F represents the vector of objective function values and Fi denotes the value of the objective function for the
Phase 1: Foraging behavior
Zebra behavior models through forage seeking are employed to update the population members during the first phase (Pastor et al., 2006). Equations (48, 49) can be used in the mathematical model to update the positions of the zebras during the foraging phase.
where
Phase 2: Predator defense strategies
The initial strategy for defense involves lions attacking the zebras, but the zebras move away from their current locations to escape (Pastor et al., 2006). Therefore, the mode S1 in Eq. (50) can be used to mathematically represent this strategy. In the second technique, when other predators attack one of the zebras, the other zebras in the herd move toward the attacked zebra in an attempt to confuse and intimidate the predator by forming a protective structure (Caro et al., 2014). Mode S2 in Eq. (50) is used to formally represent the zebra behaviors. When a zebra is updated, its new location is accepted if its objective function has a better value (Kennedy and Kennedy, 2013). This update scenario is represented using Eq. (51).
where Ps is the probability of choosing one of two randomly generated strategies in the interval [0, 1], AZ is the status of the attacked zebra and
4.1 Pseudocode of the proposed ZOA
Begin ZOA.
Input: Information regarding the optimization issue.
Calculate the population size (N) and total number of iterations (T).
Evaluate the objective function based on the initial solution.
For t = 1: T, update PZ.
For i = 1: N
Phase 1: Foraging behavior
Use Eq. (48) to determine the new
Use Eq. (49) to update the
Phase 2: Predator defense strategies
Ps = rand if Ps < 0.5.
Strategy one: Lion-fighting phase
Use mode S1 in Eq. (50) to determine the new
Else
Strategy two: Exploratory phase against other predators
Determine the
End if
Use Eq. (51) to update the
Ending for i = 1: N
Save the best possible candidate solution.
Ending for t = 1: T
Display the optimal ZOA solution as the output for the given optimization problem.
Stop
The five key components for tuning a PID controller are the fitness function,
5 Simulation and results
The performances of the 2-LRRM with the proposed controllers for trajectory tracking are examined and discussed in this section. The six proposed controllers, namely W-PID, W-FOPID, RNN-PID, RNN-FOPID, NN + PID, and NN + FOPID controllers, are compared against each other to minimize the performance index when the nominal model is used. Two starting points are used for
where
One of the important advantages of a NN is its flexibility to capturing complex underlying data structures. In the design of NN controllers, this allows production of the most complex control signals with high frequencies (i.e., chattering). In fact, a chattering signal cannot be applied practically, and the optimal solution obtained is not a feasible solution. Therefore, the objective function is modified as demonstrated in Eq. (53)
where Sn is the number of times that the control signal’s slope changes signs, and
This modified objective function excludes any solutions that contain high chattering control signals from among the candidate solutions. The desired trajectories
Now that all details about the simulation and nominal model are available and known, we start applying the ZOA optimizer to adjust the gains of all the suggested controllers based on the nominal model to minimize the ITSE. Since the ZOA is a stochastic algorithm, each controller is simulated 10 times to derive the best results. Table 2 shows the ITSE values for all proposed control structures when applied to a nominal plant and executed with two initial positions.
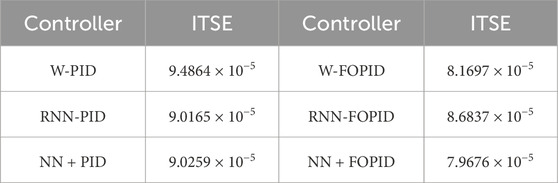
Table 2. ITSE values of the suggested controllers for a nominal plant when using two initial positions [0.1745, 0.1745] and [−0.1745, –0.1745].
Overall, the findings show that in terms of the ITSE, the suggested controllers with fractional-order integral and derivative actions perform better than those with corresponding integer-order actions. This is attributed to the fact that the tuning parameters of the controller are increased by the FOPID, which in turn increases the number of DOFs, controller capabilities, and robustness. Despite the results being very close to each other, as seen from Table 2, the findings indicate that the hybrid NN + FOPID structure has the highest ITSE of 7.9676 × 10−5 while the W-PID controller has the lowest ITSE of 9.4864 × 10−5. Figure 10 shows the trajectory tracking performances of
Based on the results, it is concluded that the NN + FOPID controller performs better than all the other suggested controllers and that it is the best controller among them.
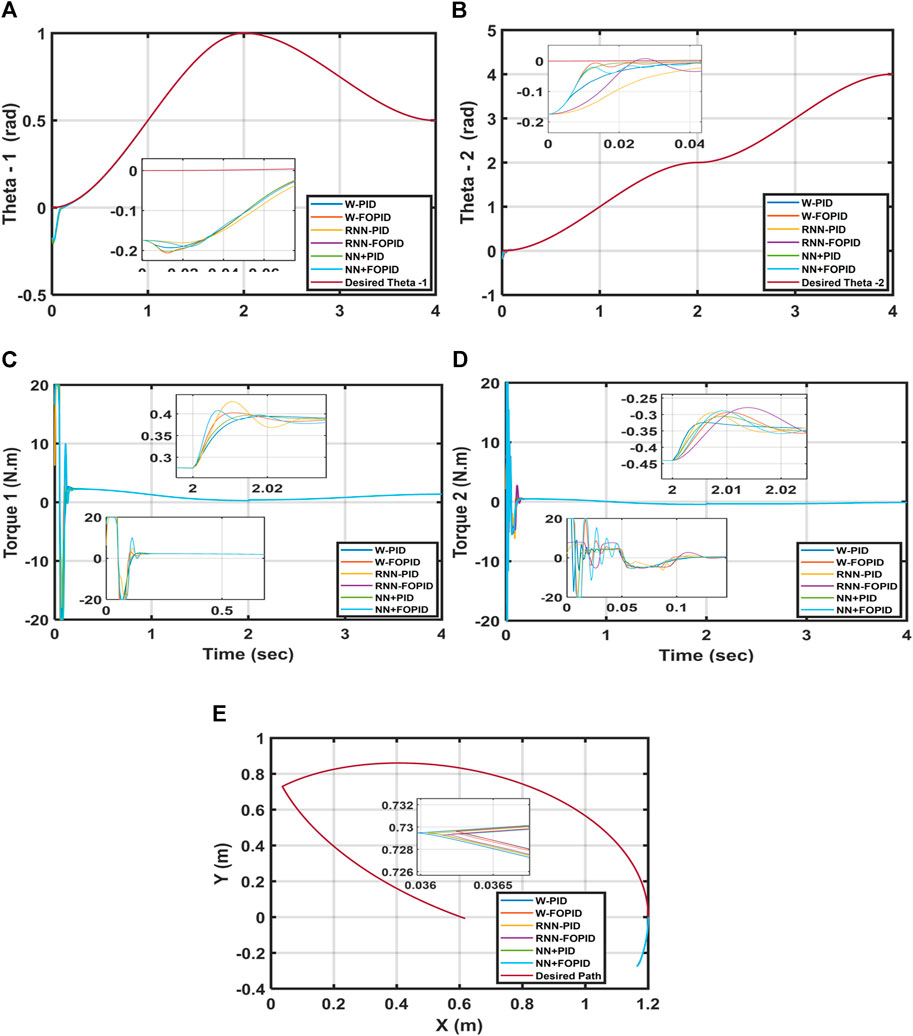
Figure 10. (A) Desired and calculated
6 Robustness tests
This section presents the results of the proposed controllers that are subjected to robustness tests. To show the capabilities of each controller, the following experiments are implemented in MATLAB without adjusting the gains or retuning the gains of the proposed controllers.
6.1 Initial condition changes
In this test, another set of initial conditions [0.15, 0.15] was considered for [
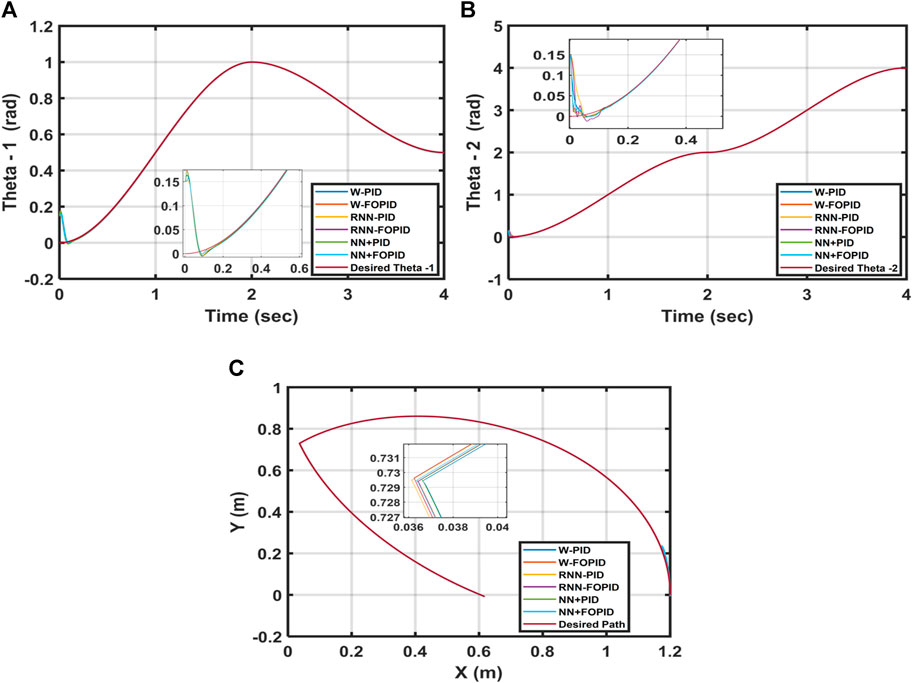
Figure 11. (A)Desired and calculated
Despite altering the starting position, the NN + FOPID controller performs better than the other suggested controllers, where the ITSE = 2.3871 × 10−5 of the NN + FOPID controller is the optimal among them. Furthermore, in the trajectory response, NN + FOPID has the least amount of overshoot and fastest settling time for
6.2 Parameter variations
In this test, the parameter variations of the 2-LRRM model are investigated for the suggested control structures by incrementing the mass of each link by 5%. Table 4 shows the ITSE value of each controller. The RNN-PID controller has the best performance index of ITSE = 0.1418 × 10−5, and the tracked trajectories for
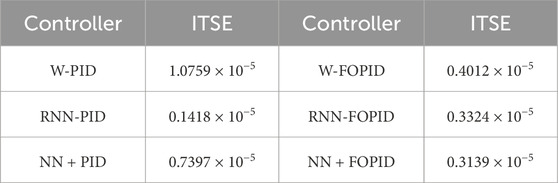
Table 4. ITSE values of the proposed controllers when adding 5% to the masses of both links and setting the starting position to [0.0, 0.0].
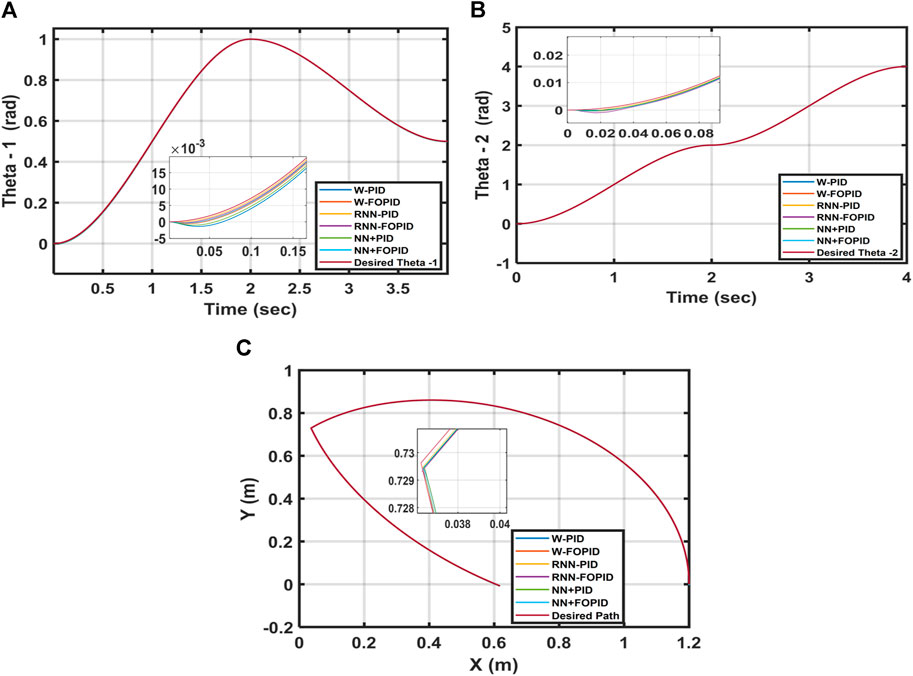
Figure 12. Desired and calculated trajectories for (A)
6.3 Disturbance addition
Another test was conducted to determine the robustness of the proposed control structures by increasing the disturbance terms [sin (50t), sin (50t)] in the control actions [
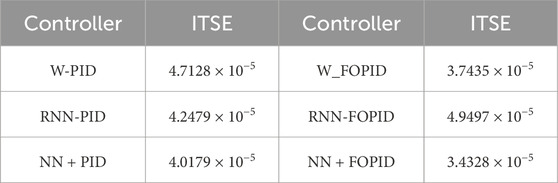
Table 5. ITSE values of the suggested controllers with added disturbance of sin(50t) to both links and a starting position of [0.15, 0.15].
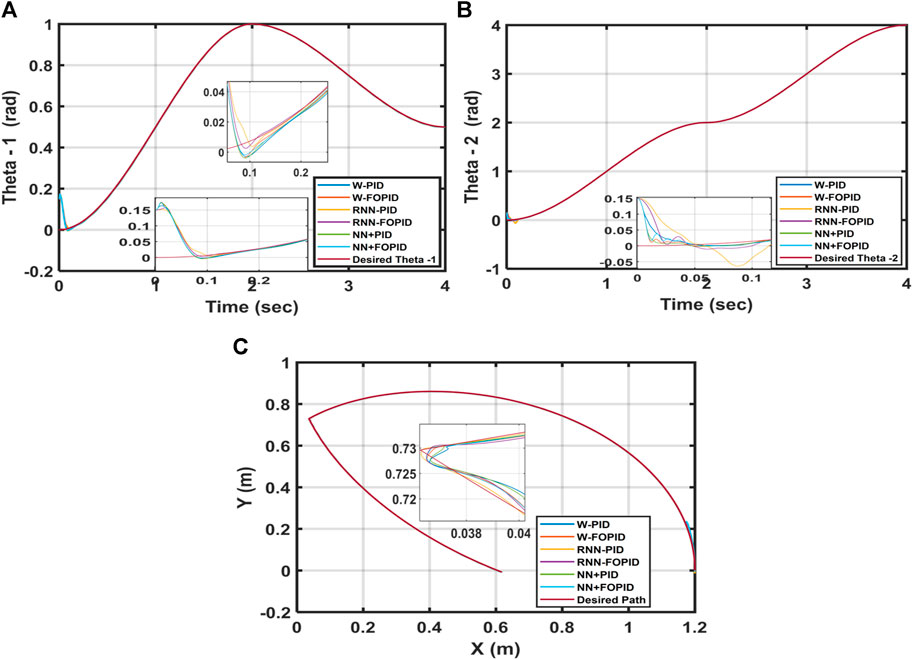
Figure 13. Desired and calculated trajectories for (A)
6.4 All tests conducted simultaneously
This combined test is crucial when evaluating robustness since it determines which of the proposed controllers can be used as the best controller. All suggested controllers are subjected to the combined impacts of added disturbance of sin(50t) to the control signals [
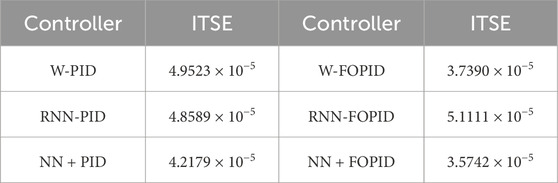
Table 6. ITSE between the desired and calculated paths when using a starting point of [0.15, 0.15] with added disturbances of [sin(50t), sin(50t)] and added masses of 5% to both links.
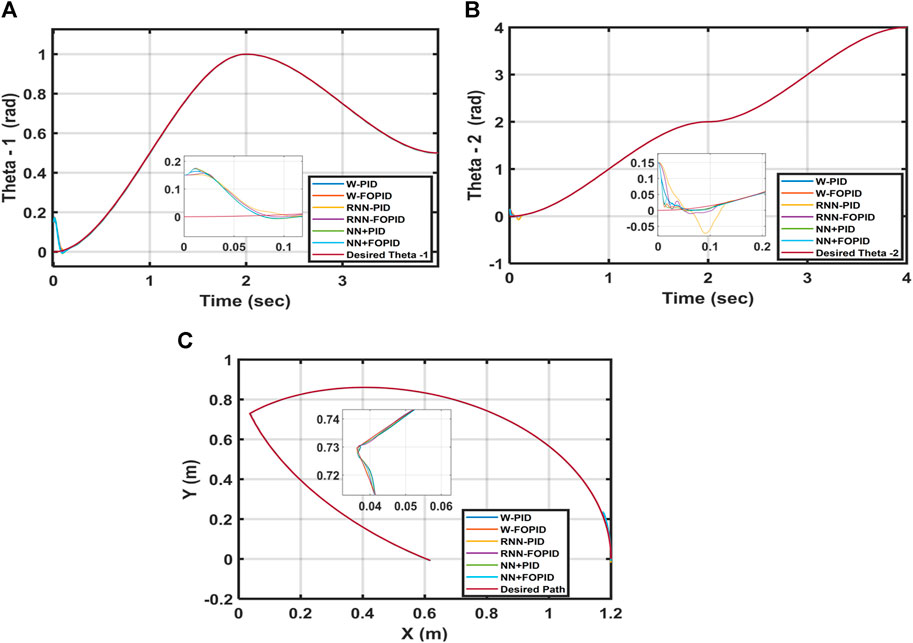
Figure 14. Desired and calculated trajectories for (A)
7 Conclusion
In this study, six PID- and FOPID-based control structures are proposed for a 2-LRRM for trajectory tracking; these are named W-PID, W-FOPID, RNN-PID, RNN-FOPID, NN + PID, and NN + FOPID controllers. To optimize the controller parameters, the ZOA was used offline to minimize the performance index ITSE. The MATLAB simulation results show that all proposed controllers have the ability to quickly reduce the errors between the real and desired paths before tracking the required path. By altering the initial state values, adding disturbances to the control signals, and increasing the masses of the two links, the robustness of each suggested controller was examined. According to the results of the nominal system tuning test and all robustness tests, the NN + FOPID has the best control structure among the suggested controllers. The combination of NN with fractional-order integration and differentiation affords high performance and efficient responses, which are reflected in the results. In addition, the modified objective or fitness function allowed ZOA-based tuning of the controller parameters to determine stable responses with fewer fluctuations in the control signals. The trajectory tracking responses for Theta-1 and Theta-2 have the smallest overshoots, shortest settling times, and lowest ITSE values. Moreover, the NN + FOPID controller outperformed all the other controllers in the robustness tests. This work also highlights the capacity of the ZOA for fine-tuning the controller parameters. Finally, as a future work, this study can be extended using other optimization techniques instead of the ZOA, such as the firebug swarm optimization algorithm, chimp optimization algorithm, mayfly optimization algorithm, and gazelle optimization algorithm to adjust the controller gains. In addition, a real robot manipulator equipped with all required hardware may be employed to practically implement and verify the suggested controllers.
Data availability statement
The original contributions presented in the study are included in the article/supplementary material; further inquiries can be directed to the corresponding author.
Author contributions
MJ: conceptualization, formal analysis, methodology, resources, software, writing–original draft, and writing–review and editing. BO: conceptualization, formal analysis, methodology, resources, software, validation, writing–original draft, and writing–review and editing. ATA: conceptualization, formal analysis, investigation, methodology, resources, validation, visualization, and writing–review and editing. AM: funding acquisition, investigation, methodology, resources, validation, visualization, and writing–review and editing.
Funding
The author(s) declare that financial support was received for the research, authorship, and/or publication of this article. This research was funded by Prince Sultan University, Riyadh, Saudi Arabia. This research was also supported by the Automated Systems and Soft Computing Lab (ASSCL), Prince Sultan University, Riyadh, Saudi Arabia.
Acknowledgments
The authors would like to thank Prince Sultan University, Riyadh, Saudi Arabia, for support with the article processing charges (APC) of this publication. The authors specially acknowledge the Automated Systems and Soft Computing Lab (ASSCL) at Prince Sultan University, Riyadh, Saudi Arabia. The authors wish to acknowledge the editor and reviewers for their insightful comments, which have improved the quality of this publication.
Conflict of interest
The authors declare that the research was conducted in the absence of any commercial or financial relationships that could be construed as a potential conflict of interest.
Publisher’s note
All claims expressed in this article are solely those of the authors and do not necessarily represent those of their affiliated organizations, or those of the publisher, the editors, and the reviewers. Any product that may be evaluated in this article, or claim that may be made by its manufacturer, is not guaranteed or endorsed by the publisher.
References
Abdulameer, H. I., and Mohamed, M. J. (2022). Fractional order fuzzy PID controller design for 2-Link rigid robot manipulator. Int. J. Intelligent Eng. Syst. 15 (3), 103–117. doi:10.22266/ijies2022.0630.10
Ajeil, F., Ibraheem, I. K., Azar, A. T., and Humaidi, A. J. (2020). Autonomous navigation and obstacle avoidance of an omnidirectional mobile robot using swarm optimization and sensors deployment. Int. J. Adv. Robotic Syst. 17 (3), 172988142092949–15. doi:10.1177/1729881420929498
Alandoli, E. A., and Tian, S. L. (2020). A critical review of control techniques for flexible and rigid link manipulators. Robotica 38 (12), 2239–2265. doi:10.1017/S0263574720000223
Azar, A. T., and Fernando, E. S. (2019). Fractional order two degree of freedom pid controller for a robotic manipulator with a fuzzy type-2 compensator. Proc. Int. Conf. Adv. Intelligent Syst. Inf. 845, 77–88. Springer International Publishing. doi:10.1007/978-3-319-99010-1_7
Baruh, A. M., and Nenkova, B. (2002). Adaptive neural control with integral-plus-state action. Cybern. Inf. Technol. 2 (1), 37–48. Sofia.
Cao, S., Sun, L., Jiang, J., and Zuo, Z. (2021). Reinforcement learning-based fixed-time trajectory tracking control for uncertain robotic manipulators with input saturation. IEEE Trans. Neural Netw. Learn. Syst. 34 (8), 4584–4595. doi:10.1109/TNNLS.2021.3116713
Caro, T., Izzo, A., Reiner, R. C., Walker, H., and Stankowich, T. (2014). The function of zebra stripes. Nat. Commun. 5 (1), 3535–10. doi:10.1038/ncomms4535
Dachang, Z., Baolin, D., Puchen, Z., and Shouyan, C. (2020). Constant force PID control for robotic manipulator based on fuzzy neural network algorithm. Complexity 2020, 1–11. Article ID 3491845. doi:10.1155/2020/3491845
Al-Hadithy, D., and Hammoudi, A. (2020). “Two- link robot through strong and stable adaptive sliding mode controller,” in IEEE 13th International Conference on Developments in eSystems Engineering (DeSE), Liverpool, United Kingdom, December 14-17, 2020.
Hameed, A. M., and Hamoudi, A. K. (2023). A 2-link robot with adaptive sliding mode controlled by barrier function. J. Eur. des Systèmes Automatisés 56 (6), 1105–1113. doi:10.18280/jesa.560620
Hamoudi, A. K., and Rasheed, L. T. (2023). Design and implementation of adaptive backstepping control for position control of propeller-driven pendulum system. J. Eur. des Systèmes Automatisés 56 (2), 281–289. doi:10.18280/jesa.560213
Ibraheem, G. A. R., Azar, A. T., Ibraheem, I. K., and Humaidi, A. J. (2020). A novel design of a neural network-based fractional PID controller for mobile robots using hybridized fruit fly and particle swarm optimization. Complexity 2020, 1–18. Article ID 3067024. doi:10.1155/2020/3067024
Jenhani, S., Gritli, H., and Carbone, P. G. (2022). Comparison between some nonlinear controllers for the position control of Lagrangian-type robotic systems. Chaos Theory Appl. 4, 179–196. doi:10.51537/chaos.1184952
Kareem, A. A., Oleiwi, B. K., and Mohamed, J. M. (2023). Planning the optimal 3D quadcopter trajectory using a delivery system-based hybrid algorithm. Int. J. Intelligent Eng. Syst. 16 (2), 427–439.
Kennedy, S., and Kennedy, V. (2013). Animals of the masai mara. Princeton, NJ, USA: Princeton Univ. Press.
Kumar, V. (2017). Evolving an interval type-2 fuzzy PID controller for the redundant robotic manipulator. Expert Syst. Appl. 73, 161–177. doi:10.1016/j.eswa.2016.12.029
Lewis, F. L., Dawson, D. M., and Abdallah, C. T. (2004). Robot manipulator control theory and practice. Florida, United States: CRC Press, 1–632. doi:10.1201/9780203026953
Mohamed, M. J., Oleiwi, B. K., Abood, L. H., Azar, A. T., and Hameed, I. A. (2023). Neural fractional order PID controllers design for 2-link rigid robot manipulator. Fractal Fract. 7 (9), 693. doi:10.3390/fractalfract7090693
Mohan, V., Chhabra, H., Rani, A., and Singh, V. (2018). An expert 2DOF fractional order fuzzy PID controller for nonlinear systems. Neural Comput. Appl. 31 (8), 4253–4270. doi:10.1007/s00521-017-3330-z
Najm, A. A., Ibraheem, I. K., Azar, A. T., and Humaidi, A. J. (2020). Genetic optimization-based consensus control of multi-agent 6-DoF UAV system. Sensors 20 (12), 3576. doi:10.3390/s20123576
Nohooji, H. R. (2020). Constrained neural adaptive PID control for robot manipulators. J. Frankl. Inst. 357 (7), 3907–3923. doi:10.1016/j.jfranklin.2019.12.042
Oleiwi, B. K., Al-Jarrah, R., Roth, H., and Kazem, B. I. (2015). Integrated motion planning and control for multi objectives optimization and multi robots navigation. IFAC-PapersOnLine 48 (10), 99–104. doi:10.1016/j.ifacol.2015.08.115
Oleiwi, B. K., Mahfuz, A., and Roth, H. (2021). “Application of fuzzy logic for collision avoidance of mobile robots in dynamic-indoor environments,” in Proceedings of the 2nd International Conference on Robotics, Electrical and Signal Processing Techniques (ICREST), Dhaka, Bangladesh, 5-7 January, 2021, 131–136.
Oleiwi, B. K., Roth, H., and Kazem, B. I. (2014). “Multi objective optimization of path and trajectory planning for non-holonomic mobile robot using enhanced genetic algorithm,” in Neural networks and artificial intelligence. ICNNAI 2014. Communications in computer and information science, vol 440. Editors V. Golovko, and A. Imada (Cham: Springer). doi:10.1007/978-3-319-08201-1_6
Pastor, J., Cohen, Y., and Hobbs, N. T. (2006). “The roles of large herbivores in ecosystem nutrient cycles,” in Large herbivore ecology ecosystem dynamics and conservation conservation biology (Cambridge, UK: Cambridge Univ. Press), 289–325.
Raafat, S. M., and Raheem, F. A. (2017). “Introduction to robotics-mathematical issues,” in Mathematical advances towards sustainable environmental systems (Springer), 261–289. doi:10.1007/978-3-319-43901-3_12
Sharma, R., Gaur, P., and Mittal, A. (2015). Performance analysis of two-degree of freedom fractional order PID controllers for robotic manipulator with payload. ISA Trans. 58, 279–291. doi:10.1016/j.isatra.2015.03.013
Shojaei, K., Kazemy, A., and Chatraei, A. (2020). An observer-based neural adaptive PID2 controller for robot manipulators including motor dynamics with a prescribed performance. IEEE/ASME Trans. Mechatronics 269 (3), 1689–1699. doi:10.1109/TMECH.2020.3028968
Shuyang, C., and John, T. W. (2021). Industrial robot trajectory tracking control using multi-layer neural networks trained by iterative learning control. Robotics 10 (1), 50. doi:10.3390/robotics10010050
Trojovská, E., Dehghani, M., and Trojovský, P. (2022). Zebra optimization algorithm: a new bio-inspired optimization algorithm for solving optimization algorithm. IEEE Access 10, 49445–49473. doi:10.1109/access.2022.3172789
Wilson, M., Hubel, T. Y., Wilshin, S. D., Lowe, J. C., Lorenc, M., Dewhirst, O. P., et al. (2018). Biomechanics of predator–prey arms race in lion zebra cheetah and impala. Nature 554 (7691), 183–188. doi:10.1038/nature25479
Keywords: neural network, recurrent neural network, set-point controller, proportional integral derivative controller, fractional-order PID controller, 2-link rigid robot manipulator, zebra optimization algorithm
Citation: Jasim Mohamed M, Oleiwi BK, Azar AT and Mahlous AR (2024) Hybrid controller with neural network PID/FOPID operations for two-link rigid robot manipulator based on the zebra optimization algorithm. Front. Robot. AI 11:1386968. doi: 10.3389/frobt.2024.1386968
Received: 16 February 2024; Accepted: 25 April 2024;
Published: 14 June 2024.
Edited by:
Yanan Li, University of Sussex, United KingdomReviewed by:
Chengzhi Zhu, South China University of Technology, ChinaHassène Gritli, Carthage University, Tunisia
Copyright © 2024 Jasim Mohamed, Oleiwi, Azar and Mahlous. This is an open-access article distributed under the terms of the Creative Commons Attribution License (CC BY). The use, distribution or reproduction in other forums is permitted, provided the original author(s) and the copyright owner(s) are credited and that the original publication in this journal is cited, in accordance with accepted academic practice. No use, distribution or reproduction is permitted which does not comply with these terms.
*Correspondence: Ahmad Taher Azar, YWF6YXJAcHN1LmVkdS5zYQ==, YWhtYWQuYXphckBmY2kuYnUuZWR1LmVn