- 1College of Logistics Engineering, Shanghai Maritime University, Shanghai, China
- 2Institute of Rail Transit, Tongji University, Shanghai, China
Cranes are widely used in the field of construction, logistics, and the manufacturing industry. Cranes that use wire ropes as the main lifting mechanism are deeply troubled by the swaying of heavy objects, which seriously restricts the working efficiency of the crane and even cause accidents. Compared with the single-pendulum crane, the double-pendulum effect crane model has stronger nonlinearity, and its controller design is challenging. In this paper, cranes with a double-pendulum effect are considered, and their nonlinear dynamical models are established. Then, a controller based on the radial basis function (RBF) neural network compensation adaptive method is designed, and a stability analysis is also presented. Finally, the hardware-in-the-loop experimental results show that the neural network compensation control can effectively improve the control performance of the controller in practice.
Introduction
Cranes are normally utilized to lift or move cargo in the field of construction, logistics, the manufacturing industry, etc. Cranes come in a variety of forms, and most cranes work by utilizing wire ropes to suspend cargo. With crane motion or external disturbances, cargo will sway owing to the flexibility of the wire ropes, and active and passive methods are taken to carry the cargo to the desired position. The swaying of the cargo is a kind of simple harmonic vibration. When the cargo carried by the cranes begins to sway, it needs several periods to be suppressed, which is time-consuming and even lead to working efficiency problems. Therefore, the swaying problem has become an urgent subject, especially for the port industry. More than that, the swaying problem will cause safety problems when carrying cargo of great mass, and it may even influence the design of the crane structure greatly.
Anti-swaying technology for cranes has been studied in the last 20 years. Attention was paid to both single-pendulum and double-pendulum effect cranes by using mechanical and automatic anti-swaying technology. When the mass of the spreader for the crane is big enough, the double-pendulum effect of the cranes cannot be neglected. In order to eliminate this double-pendulum effect, which brings stronger nonlinearity caused by interactions between the spreader and the payload into the system, controllers are designed to handle the swaying. A lot of research has been done to design such controllers for solving the double-pendulum effect. Kamal (Moustafa and Ebeid, 1988) et al. derived the nonlinear dynamical model of cranes, and, in 1988, a feedback control method was also presented to eliminate the swaying of the cargo. M. Guitierrez et al. (Gutierrez and Solo, 1998) proposed a fuzzy logic controller for an overhead crane prototype model that had obtained excellent control performances in simulations and experiments. Z Nowacki et al. (Nowacki et al., 1996) presented a PD controller with two feedback loops for an overhead crane and robustness analysis of the system was also proposed. Chwa et al. (Dongkyoung, 2017) presented a tracking control method based on a sliding mode control method for a three-dimensional overhead crane system to suppress the sway angels of the trolley, and the control performance was proved to be excellent. H.H Lee et al. (Cho and Lee, 2002) presented a novel fuzzy anti-swing control scheme combined with a position servo control and fuzzy logic control for an overhead crane prototype and the effectiveness of the proposed control strategy is proved by experiments.
Owing to the excellent approximation capability of the neural network method, researchers have presented several studies to solve the swaying problem of the cranes. Chunshien Li and Chun-yi Lee et al. (Li and Lee, 2001a; Li and Lee, 2001b) proposed a composite method combined with a neural network adaptive control method with fuzzy control for an overhead crane with high capacity to resist disturbance. Park et al. (Park and Le, 2012) had proposed a virtual prototype co-simulation by MATLAB and ADAMS to study the floating container crane. Zhang et al. (Zhang et al., 2016) proposed an adaptive tracking controller based on double-pendulum overhead cranes with uncertainties and disturbances by building a new sliding function as the desired trajectory. Ouyang et al. (Ouyang et al., 2019) presented a novel adaptive hierarchical sliding mode controller for overhead cranes with a double-pendulum effect, which can make the states of the system enter the desired sliding surface faster and even improve the precision of cart tracking. Ning Sun et al. (Sun et al., 2020a) established a dynamic model of a cooperative dual rotary crane system based on Lagrange’s method. Considering the actuator constraints, an output feedback control method that helps to increase the dual-boom positioning accuracy was also presented. Also, the control method mentioned in (Sun et al., 2020a) was extended to the positioning and tracking control for a pneumatic artificial muscle system (Sun et al., 2020b). Chen H et al. presented a new control strategy for a kind of under-actuated system by treating different constraints, and the proposed method was applied to a double-pendulum crane system with superior performances (Chen et al., 2019; Chen and Sun, 2020). Yang T et al. (Yang et al., 2020) designed an adaptive control method based on the neural network to solve the positioning problems for a ship-mounted crane system.
Based on the previous analysis, the elimination of the double-pendulum effect of cranes plays an important role to ensure the safety and effectiveness of cranes during operation. The main contribution of this work is as follows:
1. The proposed controller can realize fast positioning and anti-swing function for the crane system with a double swing effect.
2. The adaptive controller based on RBF neural network compensation has an online learning function and is not sensitive to the change of parameters. Even if there are some missing items in the controller, it can still get a better control effect through online learning compensation.
3. Experiment results show that the positioning accuracy and response speed are better than the traditional sliding mode controller.
In this paper, an overhead crane with a double-pendulum effect is chosen as the research object. Firstly, the mathematical model of the double-pendulum effect crane is established. Base on the mathematical model, an adaptive controller based on a radial basis function neural network compensation method is designed where the core of the controller is the robust controller, and the neural network is worked as an additional system to output compensation force. Then, the Lyapunov stability analysis is performed to testify the stability of the neural network controller crane system. Finally, hardware in a loop experimental platform is utilized to verify the proposed controller. A comparison between the sliding mode controller and the neural network controller is also presented to verify the effectiveness and feasibility of the control strategy.
Modeling of Double-Pendulum Effect Cranes
The structure of the overhead crane with a double-pendulum effect is composed of a trolley, a spreader with a large mass (first-order payload), and a payload (second-order payload). Connections between the spreader, trolley, and payload are made of wire ropes, which are shown in Figure 1.
This assumes that the trolley, spreader, and payload of the crane are working on a two-dimensional plane, and the track of the trolley is horizontal. It considers the spreader and payload as particles, and the connection point of the wire rope is on the centroid of the spreader and payload. The transient wind disturbances and friction among the trolley, spreader, and payload connection point are ignored. The simplified model is shown in Figure 2.
In Figure 2, the positive direction for the x axis is pointed to the right; F denotes the driving force of the trolley; f represents the friction force between the trolley and the track; M denotes the mass of the trolley; m1 and m2 represent the mass of the spreader and the payload, respectively; l1 and l2 denote the wire rope length among the centroid of the spreader, trolley, and the payload, respectively; x represents the displacement of the trolley; θ1 and θ2 denote the swing angle of the spreader and payload, respectively.
According to Lagrange equation of the second kind, the dynamic equation set of the crane with double-pendulum can be obtained:
where b denotes the damping coefficient;
Adaptive Controller Based on RBF Neural Network Compensation Method
Owing to the development of neural network technology (Hunt et al., 1992; Feng, 1995), a great process had been made in the field of automatic control, signal processing, and pattern recognition. In this case, the neural network method had been introduced into the crane system, and the model of the double-pendulum crane follows Eq. 2:
where
The control purpose of the double-pendulum crane is to help the trolley stop at the desired position while the first and second payloads which is set below the trolley keeps still. The tracking signal is defined as
The calculated traction is utilized to control the double-pendulum crane system. The controller is composed of a traction calculation method and a neural network compensation method. An RBF neural network correction controller is defined as an additional to recognize the online model error of the crane. As shown in Figure 3.
Calculated Traction Controller
The calculated traction control method is defined as a kind of robust controller (Weiping et al., 2004). According to the dynamic Eq. 2 of the crane, the control law can be designed as follows:
where
The systematic error is defined as follows:
where
RBF Neural Network Controller and Stability Analysis
RBF neural network method is adopted to approximate
where the input of the network is defined as
The adaptive control law can be designed as follows:
where γ > 0;
The Lyapunov function is designed as follows:
where γ > 0.
The matrix P is Symmetric and positive definite. Moreover, P should satisfy the Lyapunov equation as follows:
where Q ≥ 0.
where
V is derived with respect to time, and we can get the following:
where
Due to
According to the known conditions, it can be concluded that
where λmax(P) denotes the maximum eigenvalue of matrix P, λmin(Q) denotes the minimum eigenvalue of matrix Q.
In this case, as long as
At this time, the system satisfies the stability in the sense of Lyapunov.
According to the stability analysis criteria, if the matrix P is Symmetric and positive definite, in order to keep the system stable, the Lyapunov equation PA + ATP = −Q should be satisfied, where Q ≥ 0.
According to Eq. 2 and Eq. 3 and combining the approximation result
MATLAB is utilized to establish the crane system and the control system. Suitable control parameters are tuned and the results of the adaptive control system based on neural network compensation are shown in Figure 4 and Figure 5.
It can be depicted from Figure 4 that the neural network compensation can track the position accurately and suppress the swing angle very well. It is also shown in Figure 5 that the final state of the neural network controller is convergent to zero which proved the effectiveness of the controller.
Experiments
The hardware in the loop (HIL) simulation is introduced into the experiment, which is known as an advanced method in scientific research. In this experiment, the HIL is mainly composed of PC, the controller, and the mechanical structure. The PC had already been installed with the MATLAB/Simulink software and was used as a host computer. The motion control card is driven and communicated with the PC. The mechanical structure is driven by the motion card, and the motion parameters of the mechanical structure are collected by the motion control card and passed to the PC. The experimental physical prototype is shown in Figure 6.
In order to testify the performance of the presented neural network-based controller, the well-performed sliding mode controller in (Tuan and Lee, 2013) is also presented as a comparison group. The input of the sliding mode controller is defined as follows:
where K denotes the amplitude of the control switch gain; λ, α, β represent the designed parameters; sgn(·) denotes the sign function.
Controller Positioning Anti-swing Control Experiments
The sliding mode controller is established in MATLAB/Simulink and the control parameters are tuned to adapt to the experimental facilities. The experimental facility at the original point is static. With the control of the controller, the motion of the trolley follows the target position and the response results are obtained.
It depicts in Figure 7 that the sliding mode control-based method can eliminate the swing angular velocity very quickly in the wide range, and the amplitude of the swing angle is quite small. However, the switch character of the swing angle with high frequency, especially for the swing angles around 0°, will lead to oscillation.
With the same control object, the results of the RBF neural network compensation controller is shown as follows:
From Figure 8, the adaptive controller based on RBF neural network compensation has no chattering problem of the sliding mode controller, and the process is smoother than the sliding mode controller.
Anti-disturbance Control Experiment
This experiment is starting with a static trolley and the payload does not have a swing angle. After that, the payload is given a force that makes the payload swing, and the experiment is utilized to evaluate the anti-disturbance performances of the presented controller.
It is shown in Figure 9 that after external excitation the spreader or the payload can go back to the original position very quickly by using a sliding mode controller; the effect of the anti-swing is significant, and the final state is a high-frequency swing state. When the swing angle is big enough, the control effect is better.
The performance of the neural network-based controller is shown in Figure 10. Compared to the sliding mode-based controller, the neural network-based controller can control a greater swing angle. Additionally, with the bigger excitation, the maximum swing angle can reach 30°. It is proved that the proposed neural network-based controller can control a greater swing angle, which would make a quicker response with the same disturbances, and the working performance is superior in harsh situations.
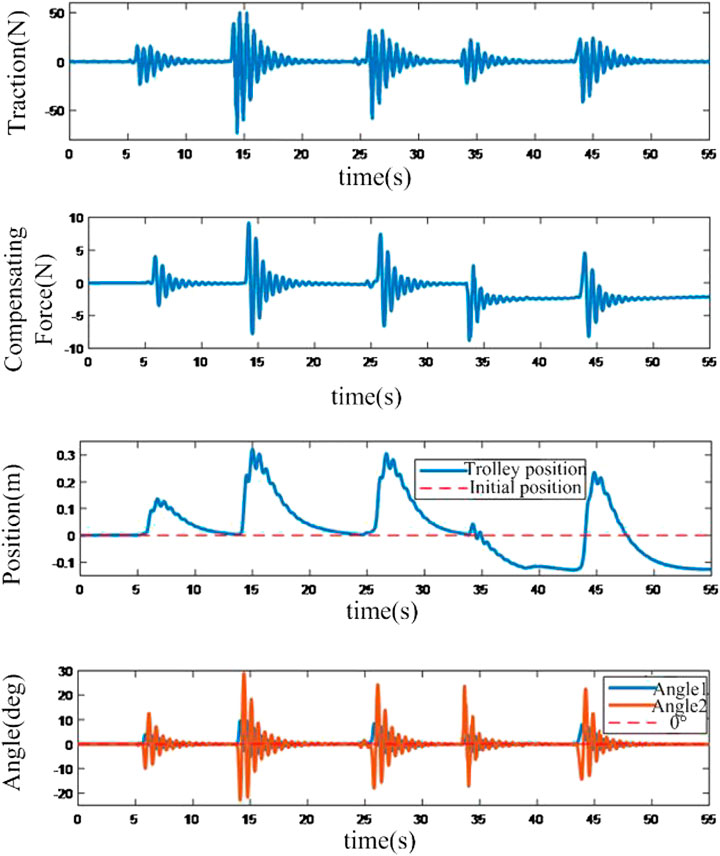
FIGURE 10. Response of anti-disturbance system based on neural network based compensation controller.
Conclusion
The overhead crane with the double-pendulum effect is chosen as the research object in this paper. A dynamic model of the crane has been established first. Then, an RBF-based neural network compensation adaptive controller is proposed, and simulations with MATLAB are also performed to verify the stability of the system. Finally, experiments with HIL are presented to test the presented controller where a comparison with a sliding mode based controller is also presented. The experimental results show that compares with the traditional sliding mode based controller, the neural network-based controller has a superior performance and better ability to anti-disturbances and without oscillation. Moreover, the proposed controller is also proved to be adequate for real-time control by experimental results.
Data Availability Statement
The original contributions presented in the study are included in the article/Supplementary Material, further inquiries can be directed to the corresponding author.
Author Contributions
H-YQ designed the controller and drafted the paper. Y-gS performed the simulations. J-cL and D-sD help stability analysis and carried out the experiments. All authors have read and agreed to the published version of the manuscript.
Conflict of Interest
The authors declare that the research was conducted in the absence of any commercial or financial relationships that could be construed as a potential conflict of interest.
References
Chen, H., and Sun, N. (2020). Nonlinear control of underactuated systems subject to both actuated and unactuated state constraints with experimental verification. IEEE Trans. Ind. Electron. 67 (9), 7702–7714. doi:10.1109/tie.2019.2946541
Chen, H., Xuan, B., and Yang, P. (2019). A new overhead crane emergency braking method with theoretical analysis and experimental verification. Nonlinear Dyn. 98 (3), 2211–2225. doi:10.1007/s11071-019-05318-6
Cho, S.-K., and Lee, H.-H. (2002). A fuzzy-logic antiswing controller for three-dimensional overhead cranes. ISA Trans. 41 (2), 235–243. doi:10.1016/s0019-0578(07)60083-4
Dongkyoung, C. (2017). Sliding-mode-control-based robust finite-time antisway tracking control of 3-D overhead cranes. IEEE Trans. Ind. Electron. 64, 6775–6784. doi:10.1109/TIE.2017.2701760
Feng, G. (1995). A compensating scheme for robot tracking based on neural networks. Robot. Auton. Syst. 15 (3), 199–206. doi:10.1016/0921-8890(95)00023-9
Gutierrez, M., and Solo, R. (1998). “Fuzzy control of a scale prototype overhead crane,” in Proceedings of the 37th IEEE Conference on Decision and Control, Tampa, FL, December 18–18, 1998, New York, NY: IEEE, 18.
Hunt, K. J., Sbarbaro, D., Żbikowski, R., and Gawthrop, P. J. (1992). Neural networks for control systems—a survey. Automatica 28 (6), 1083–1112. doi:10.1016/0005-1098(92)90053-I
Li, C., and Lee, C. Y. (2001a). Fuzzy motion control of an auto-warehousing crane system. IEEE Trans. Ind. Electron. 48 (5), 983–994. doi:10.1109/41.954563
Li, C., and Lee, C. Y. (2001b). “Soft computing system for motion control,” in 2001 IEEE Intelligent Transportation Systems, Oakland, CA, August 25–29, 2001.
Moustafa, K. A. F., and Ebeid, A. M. (1988). Nonlinear modeling and control of overhead crane load sway. J. Dynamic Syst. Meas. Control 110 (3), 266–271. doi:10.1115/1.3152680
Nowacki, Z., Owczarz, D., and Wozniak, P. (1996). “On the robustness of fuzzy control of an overhead crane,” in IEEE International Symposium on Industrial Electronics, Warsaw, Poland, June 17, 1996, New York, NY: IEEE.
Ouyang, H., Wang, J., Zhang, G., Mei, L., and Deng, X. (2019). Novel adaptive hierarchical sliding mode control for trajectory tracking and load sway rejection in double-pendulum overhead cranes. IEEE Access 7 , 1. doi:10.1109/ACCESS.2019.2891793
Park, H.-S., and Le, N.-T. (2012). Modeling and controlling the mobile harbour crane system with virtual prototyping technology. Int. J. Control Autom. Syst. 10 (6), 1204–1214. doi:10.1007/s12555-012-0615-y
Sun, N., Liang, D., Wu, Y., Chen, Y., Qin, Y., and Fang, Y. (2020a). Adaptive control for pneumatic artificial muscle systems with parametric uncertainties and unidirectional input constraints. IEEE Trans. Ind. Inf. 16(2):969–979. doi:10.1109/tii.2019.2923715
Sun, N., Fu, Y., Yang, T., Zhang, J., Fang, Y., and Xin, X. (2020b). Nonlinear motion control of complicated dual rotary crane systems without velocity feedback: design, analysis, and hardware experiments. IEEE Trans. Autom. Sci. Eng. 17 (2), 1017–1029. doi:10.1109/tase.2019.2961258
Tuan, L. A., and Lee, S.-G. (2013). Sliding mode controls of double-pendulum crane systems. J. Mech. Sci. Technol. 27 (6), 1863–1873. doi:10.1007/s12206-013-0437-8
Weiping, G., Diantong, L., Jianqiang, Y., and Dongbin, Z. (2004). Passivity-based-control for double-pendulum-type overhead cranes[C]//2004 IEEE Region 10 Conference TENCON 2004. IEEE 500, 546–549.
Yang, T., Sun, N., Chen, H., and Fanf, Y. (2020). Neural network-based adaptive antiswing control of an underactuated ship-mounted crane with roll motions and input dead zones. IEEE Trans. Neural Netw. Learn. Syst. 31 (3), 901–914. doi:10.1109/tnnls.2019.2910580
Keywords: double-pendulum, neural network, adaptive control, anti-sway and positioning, hardware in the loop
Citation: Qiang H-y, Sun Y-g, Lyu J-c and Dong D-s (2021) Anti-Sway and Positioning Adaptive Control of a Double-Pendulum Effect Crane System With Neural Network Compensation. Front. Robot. AI 8:639734. doi: 10.3389/frobt.2021.639734
Received: 09 December 2020; Accepted: 01 February 2021;
Published: 19 April 2021.
Edited by:
He Chen, Hebei University of Technology, ChinaCopyright © 2021 Qiang, Sun, Lyu and Dong. This is an open-access article distributed under the terms of the Creative Commons Attribution License (CC BY). The use, distribution or reproduction in other forums is permitted, provided the original author(s) and the copyright owner(s) are credited and that the original publication in this journal is cited, in accordance with accepted academic practice. No use, distribution or reproduction is permitted which does not comply with these terms.
*Correspondence: You-gang Sun, MTk4OXlvZ2FAdG9uZ2ppLmVkdS5jbg==