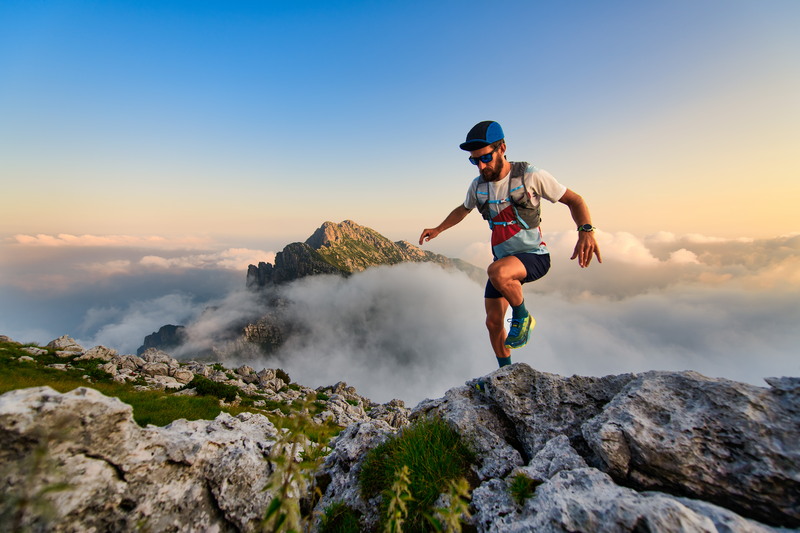
94% of researchers rate our articles as excellent or good
Learn more about the work of our research integrity team to safeguard the quality of each article we publish.
Find out more
ORIGINAL RESEARCH article
Front. Membr. Sci. Technol. , 28 June 2024
Sec. Membrane Applications - Liquid
Volume 3 - 2024 | https://doi.org/10.3389/frmst.2024.1407819
This article is part of the Research Topic Celebrating 1 Year of Frontiers in Membrane Science and Technology View all 10 articles
Acrylamide is an important chemical in great global demand for the synthesis of polyacrylamide. A facile and benign approach of concentrating high osmotic acrylamide aqueous solution at a low temperature is needed to replace the current energy-intensive and cost-expensive thermal flash evaporation process. For the first time, a multi-stage forward osmosis (FO) process has been developed to concentrate acrylamide solution from 200 g/L to 600 g/L. Thin-film composite (TFC) membrane was fabricated and used for the multi-stage FO process. Acrylamide feed solution (FS) with various concentrations was systematically characterized in terms of viscosity and osmotic pressure (OP). Draw solutes including NaCl and MgCl2 were tested, and their reverse salt fluxes were measured with the quantification of their accumulative contents in the resultant concentrated acrylamide solution. Different operation modes including AL-FS (active layer facing FS) and AL-DS (active layer facing DS) were explored to optimize the system efficiency of the FO concentration process. Both single- and multi-stage FO operations were investigated, and their performances were quantified to assess the efficiency of the concentration of acrylamide solution. The results demonstrate that the multi-stage FO operation could dramatically improve the system efficiency for the concentration of acrylamide solution better than the single-stage FO process, and the draw concentration renewal at Stages II, III, and IV led to a water flux increase of 18.56%, 17.52%, and 18.43%, respectively. Moreover, the accumulated MgCl2 in the final 600 g/L acrylamide solution was below 3.7 g/L, less than 0.62 wt% impurity in the product of acrylamide. Our work provides a practical insight into the viability and optimization of a multi-stage FO process for concentrating high osmotic chemicals.
• The potential of multi-stage forward osmosis in concentrating acrylamide was demonstrated.
• The acrylamide solution could be concentrated from 200 to 600 g/L during the FO process.
• MgCl2 was used as a more effective draw solute than NaCl with a very low reverse salt flux.
• The AL-FS mode was favored for concentrating acrylamide at a high concentration (> 200 g/L).
• The multi-stage FO operation could dramatically improve both water flux and concentration time.
Acrylamide holds significant industrial importance; it is primarily utilized in creating polyacrylamide, which accounts for approximately 90% of its usage (Smith and Oehme, 1991; Braun et al., 2022). Polyacrylamide is extensively used as a coagulant or flocculant for water treatment, with growing demand being driven by increasingly stringent environmental regulations (Seybold, 2008; Nath and Pande, 2020). Polyacrylamide also works as a water-soluble thickener for enhanced oil recovery, shale strengthening, and shale gas extraction (Xudong et al., 2004; Li et al., 2017; Al-Kindi et al., 2022). Thanks to numerous applications of polyacrylamide, its global demand is expected to grow continuously (Xiong, Loss, Shields, et al., 2018). Currently, acrylamide is synthesized through acrylonitrile (ACN) hydrolysis with nitrile hydratase (Lee et al., 1991; Raj et al., 2006; Asano et al., 2014), and it needs further concentration into a highly concentrated acrylamide solution for the synthesis of polyacrylamide. However, the present practical upper limit of produced acrylamide solution is only approximately 150 g/L−250 g/L (James Munch, 1975), and the high concentration of acrylamide severely decreases the stability and activity of the nitrile hydratase catalysts. It can especially cause a rapid catalyst deactivation when the acrylamide concentration is higher than 300 g/L (Watanabe, 1982; Nagasawa et al., 1993). Therefore, an enhanced concentration process for acrylamide product solution is imperative for meeting the necessary polymerization conditions required for polyacrylamide synthesis.
Thermal flash evaporation is a widely employed technique for concentrating acrylamide solution by removing water under the reduced-pressure of 1 bar at 50 °C–55 °C (Watanabe et al., 1989). However, this process is energy-intensive and is accompanied by high installation and maintenance expenses due to the complexity of the equipment (Wade, 1993; McGinnis and Elimelech, 2007). In addition, the relatively high operating temperature for the flash evaporation technique often causes the undesired free-radical polymerization of acrylamide, thereby inducing impurity (Ogata, 1960; Smith and Oehme, 1991). Therefore, a benign process of concentrating acrylamide aqueous solution at a low temperature is needed to improve purity, save energy, and reduce cost.
As an emerging concentration process, forward osmosis (FO) has been developed to concentrate high osmotic solution (Qi, Hu, Chai & Wang, 2019; An, Hu, Wang, Zhou & Liu, 2019; (Hu, 2023). During the FO process, osmosis drives water through a semipermeable membrane from feed to DS, thus concentrating a solute in the feed solution (FS) (Chekli et al., 2016; She et al., 2016). Therefore, selecting an appropriate draw solution (DS) with a higher osmotic pressure (OP) than that of the FS is key to sustaining the osmotic driving force through the FO membrane to concentrate the solute in FS (Zhao et al., 2012). In contrast, in counteracting the OP of FS, the pressure-driven membrane process of reverse osmosis has a limiting performance and does not work for concentrating high-osmotic FS (Rastogi, 2016). Meanwhile, FO membrane is also a core element in the FO system; recently, the gold standard for FO application has been thin-film composite (TFC) membrane, which exhibits relatively high permeability-selectivity far exceeding those cellulose-acetate-based FO membranes. Notably, the FO process provides the great advantage of membrane process of concentrating the high-osmotic FS at ambient conditions without extra pressure or heat (McGinnis and Elimelech, 2007; Zhao et al., 2012). Thus, with a high-performance membrane and suitable draw solutes, the FO process should have greater benefits than thermal concentration for concentrating acrylamide solution in terms of final product quality and energy demand. However, no work has been done to investigate the forward osmosis membrane process for concentrating high osmotic acrylamide solution.
The single-stage forward osmosis (FO) process requires a draw solution of initially higher concentration to generate an adequate driving force which can lead to inefficient resource utilization and higher reverse salt flux (Giagnorio et al., 2022; Truong and Chong, 2024). To overcome such limitations inherent in single-stage membrane processes, multi-stage membrane systems have been developed which have been theoretically proven to enhance the efficiency of separation or concentration operations (Zhu et al., 2009; Alshehri and Lai, 2014; Truong and Chong, 2024). Additionally, multi-stage membranes offer the advantage of maintaining a more uniform water flux across entire modules. This is achieved by adjusting the applied pressure at various stages to counteract the increasing osmotic pressure of the concentrated feed solution (Lin and Elimelech, 2015; Giagnorio et al., 2022). Therefore, multi-stage membrane processes have the potential to significantly reduce the overall economic costs of separation or concentration operations by reducing any unnecessary consumption of energy and resources. In this study, a multi-stage FO system is developed and evaluated for concentrating 200 g/L acrylamide solution with high OP (71.49 bar) for the first time. The current advanced TFC polyamide membrane is fabricated and evaluated in the FO process. Different concentrations of acrylamide solution are methodically studied for viscosity and OP and employed as FS. Draw solutes including representative monovalent salt sodium chloride (NaCl) and divalent salt magnesium chloride (MgCl2) were tested for the concentration of acrylamide solution; their reverse salt fluxes were measured, and their accumulative contents were quantified in the resultant concentrated acrylamide solution. Different operation modes including the AL-FS (active layer facing FS) and the AL-DS (active layer facing DS) were also studied to optimize the system efficiency of the FO concentration process. Both single- and multi-stage operations were then carried out, and their performances were quantified and compared to assess the efficiency of the FO process for the concentration of acrylamide solution. Our work provides a practical insight into the viability and optimization of multi-stage FO process for concentrating high-osmotic chemicals.
Polysulfone (PSf, Mn: 21,000 g/mol) was sourced from Solvay (Brussels, Belgium). M-phenylenediamine (MPD) and trimesoyl chloride (TMC) were obtained from Sigma-Aladdin (United States). Sodium chloride (NaCl), magnesium chloride (MgCl2), acrylamide, N-methyl-2-pyrrolidinone (NMP), and n-hexane were purchased from Sinopharm (China). All chemicals were utilized in their received state without further modification.
TFC FO membrane was fabricated via a two-step method according to our previous work (Liu and Hu, 2016): preparation of PSf support membrane through non-solvent-induced phase separation and the fabrication of the top PA layer through interfacial polymerization (IP) (Hao et al., 2023a; Hao et al., 2023b). In brief, 12 wt% PSf/NMP casting solution was cast on an NMP-prewetted PET nonwoven fabric using a casting knife with a gap of 150 μm and was immersed in deionized (DI) water (25 ± 1°C) overnight to produce the PSf support. The PA layer was then prepared on top of the PSf support using 3.4 wt% MPD aqueous solution and 0.15 wt% TMC organic solution in hexane. The obtained TFC membrane was immersed in 90 °C water bath for 120 s and then transferred in 4 °C DI water for further use.
The morphologies of the TFC membranes were observed using a Hitachi scanning electron microscope (SEM, S-4800). The contact angle of polyamide surface was determined using the Data Physics optical instrument (OCA20, Germany) with a digital camera. The surface charge of the sample was determined through Anton Paar electrokinetic analyzer (SurPASS™ 2, Austria) with 1.0 mmol/L KCl buffer solution, with 3–10 pH. The FO performance (details in Supporting Information, S1) of the fabricated TFC membrane was measured via a cross-flow custom-designed FO system at 25.0°C ± 0.5°C using a circulating cooling system (SDC-6, Scientz Biotechnology, China) (Supplementary Figure S1) according to Tiraferri et al. (2013). The effective surface area of the membrane cell was 38.52 cm2 and the crossflow velocity of both feed and draw solution was maintained at 7 cm/s. The water flux and reverse salt flux were determined following our previous work (Liu and Hu, 2016) and tested under the AL-DS and AL-FS operation modes, respectively.
OP of solutions was determined using a YASN freezing-point osmometer (Osmopro3250, United Kingdom). The viscosities of NaCl, MgCl2, and acrylamide solutions with various concentrations were determined using a Brookfield viscometer (DVS+, United States) under 25 °C. The concentration of acrylamide solution was determined using Persee UV-Vis spectrometer (TU-1810, China) at 198 nm based on the calibration curve shown in Supplementary Figure S2.
The concentration process of acrylamide solution was carried out in the above-mentioned crossflow FO system; draw solutions were 4 mol/L (M) and 5 M MgCl2, respectively. For each run, the initial acrylamide and DSs were performed at a crossflow velocity of 0.7 cm/s and kept at a constant volume of 1 L. The continuous flux was monitored via a Mettler digital balance (ME104E, Switzerland) and a Eutech conductivity meter (CON2700, United States) according to our previous work (Liu and Hu, 2016).
The PA active layer of the TFC membrane was formed on a PSf support membrane via the IP method. As illustrated in Figure 1A, the polyamide surface of the TFC membrane presents a characteristic ridge and valley morphology and exhibits good hydrophilicity with a relative low water contact angle (WCA) of 44° ± 4°. The average surface roughness of the polyamide layer was measured by AFM to be 90 ± 5 nm (Figure 1C), comparable with other reported TFC membranes (Han et al., 2012; Tian et al., 2013; Sun et al., 2014). In addition, the morphology of the cross-sectional TFC FO membrane revealed a thin polyamide layer of approximately 300 nm, crafted atop the porous PSf support exhibiting a finger-like pore structure (Figure 1B); this is expected to have a much lower mass transport resistance and, thereby, a suppressed internal concentration polarization (ICP) effect (Yip et al., 2010). Furthermore, TFC polyamide membrane exhibits a typical high water permeability coefficient (A) as 1.32 ± 0.11 LMH/bar, a very low solute permeability coefficient of NaCl (B) as 0.11 ± 0.08 LMH, and a characteristic structure parameter (S) of 421 ± 80 μm (Figure 1D), close to those of the previous reported TFC FO membranes (Zhang et al., 2021; Ibraheem et al., 2023), but much higher water permeability and NaCl selectivity than the well-used commercial TFC membrane or cellulose triacetate membrane from HTI (Tiraferri et al., 2013; Long et al., 2016) (Supplementary Table S1).
Figure 1. Surface and cross-section morphologies of the TFC membrane, including SEM images (A, B) and AFM image (C) of the TFC membrane; the insert in the SEM image A is a water drop on the membrane surface and its average water contact angle (WCA), and intrinsic transport parameters (A, B, S) of the TFC membrane (D).
The viscosity and OP of acrylamide solution with various concentrations were measured since they may have significant impacts on the FO concentration process and determine the selection of DS. As shown in Figure 2A, acrylamide solution exhibits a slightly increased viscosity with its concentration but presents a relatively low viscosity below 10 cP, even at a high concentration of 600 g/L. The increased viscosity often leads to a decreased solution diffusivity and subsequent intensified concentration polarization in FO. Compared to the viscosity of DI water (2.61 cP), results show that acrylamide solution has a comparably low viscosity. The OP of acrylamide solution with various concentrations exhibits a linear increase from 71.49 bar to 187.28 bar, with its concentration increasing from 200 g/L to 600 g/L (Figure 2B). Such a high OP of the acrylamide solution requires an appropriate DS with a much higher OP to concentrate the acrylamide solution in the FO process.
Figure 2. Viscosity (A) and OP (B) of acrylamide solution with various concentrations 200 g/L–600 g/L in water at 25 °C.
NaCl and MgCl2 were selected as a typical monovalent and divalent draw solute owing to the popularity and high OP. As presented in Figure 3A, the OPs of NaCl and MgCl2 solutions increase almost linearly with their concentrations following the Van ‘t Hoff law. The OP of 5 M MgCl2 solution is 413.81 bar, dramatically higher than 232.86 bar of 5 M NaCl solution. Nonetheless, NaCl DS is selected for many FO studies due to its abundance, low cost, and high solubility. In addition, as the concentration of NaCl DS rises from 3 M to 5 M, the water flux escalates from 3.65 LMH to 7.20 LMH in the AL-DS mode. Simultaneously, the salt flux displays a significantly accelerated rising pattern, surging from 12.65 gMH to 26.95 gMH (Figure 3B). When MgCl2 was selected as DS with the concentration increasing from 3 M to 5 M, the water flux increased rapidly from 3.88 LMH to 10.22 LMH in the AL-FS mode, which is greater than that with the NaCl DS owing to higher OP of MgCl2 solution. Moreover, the reverse salt flux was higher when the MgCl2 concentration increased and reached ∼20 gMH when operated in AL-FS operation mode with 5 M MgCl2, which was obviously lower than that when using the same NaCl draw concentration. Moreover, the special reverse salt flux (SRSF, Js/Jw, g/L) was calculated to ascertain the mass loss of the draw solute, which diffused across the TFC polyamide membrane since little water permeates through the membrane, which is lower for higher performance of FO membrane with the better selectivity-permeability. Results in Figure 3C illustrate that the SRSF of the TFC membrane is obviously lower under MgCl2 DS than under NaCl DS. For example, with the increasing MgCl2 draw concentration from 3 M to 5 M, the corresponding SRSF of the TFC membrane changed from 1.32 g/L to 1.54 g/L in the AL-FS mode; however, with NaCl DS, it increased from 2.48 g/L to 2.94 g/L, indicating a much less loss of MgCl2 than NaCl in the FO process (Hancock and Cath, 2009).
Figure 3. OPs (A) of NaCl and MgCl2 solutions with various concentrations 1 M–5 M at 25 °C. Water flux (Jw), reverse salt flux (Js) (B), and SRSF (Js/Jw) (C) of the TFC polyamide membrane with different concentrations of NaCl and MgCl2 solutions as DS, respectively, under the AL-FS mode. Here, 200 g/L acrylamide solution was used as the feed solution.
Therefore, the MgCl2 would be an appropriate draw solute for the concentration experiment of acrylamide solution during the FO process. The high concentration of MgCl2 solutions from 4 M to 5 M would be appropriate DSs for providing high osmotic driving force for TFC membranes with a water flux higher than 5 LMH.
With 4 M MgCl2 DS, the performance of the TFC membrane in terms of water and salt permeabilities was investigated using different feed solutions. The result in Figure 4A shows that the water flux of the TFC membrane was obviously lower in the AL-FS than that in the AL-DS mode when using 50 g/L and 100 g/L acrylamide solution as FS. For example, with 50 g/L acrylamide FS, the water fluxes of the TFC membrane were 15.06 LMH in AL-FS and 18.37 LMH in AL-DS, respectively, which is characteristic because there is less ICP of the TFC polyamide membrane in AL-DS than that in AL-FS mode (Tiraferri et al., 2013; Liu et al., 2017). However, when the acrylamide feed concentration was increased to 200 g/L, the water flux of the TFC membrane under the AL-DS mode was 7.29 LMH, which is lower than 10.49 LMH under the AL-FS mode. This is because of the severe ICP also occurring at the AL-DS operation mode when the support layer faced high concentration acrylamide solutions. In addition, with the increasing feed concentration from 50 g/L to 300 g/L, the corresponding SRSF of the TFC membrane increased slowly from 0.06 g/L to 1.16 g/L when operated under the AL-FS mode, but it increased rapidly from 0.50 g/L to 5.17 g/L when using the AL-DS as the operation mode, signifying considerably lesser and slower draw solute loss in the AL-FS mode than in the AL-DS mode (Figure 4B). This result suggests that AL-FS would be an appropriate operation orientation for the concentration experiment of acrylamide solution (Conc. >200 g/L) during the FO process.
Figure 4. Water flux, reverse salt flux (A), and SRSF (Js/Jw) (B) of the TFC polyamide membrane with different concentrations of acrylamide solutions as feed solution, respectively, under AL-FS and AL-DS modes. Here, 4 M MgCl2 solution was used as draw.
The impact of the concentration of acrylamide feed solution was investigated on the membrane performance, and 4 M and 5 M MgCl2 solutions were chosen as DS when operating the FO process in the AL-FS mode. Figure 5 shows the decrease of Jw and the increase of both Js and the Js/Jw with increasing concentration of acrylamide FS using 4 M and 5 M MgCl2 DS. For example, with 4 M MgCl2 DS, Jw decreased rapidly from 10.49 LMH to 4.43 LMH, and Js simultaneously increased from 4.00 gMH to 18.77 gMH with increasing acrylamide feed concentration from 200 to 600 g/L (Figure 5A). The same trend of Jw and Js also occurred when 5 M MgCl2 was used as a DS (Figure 5B), such as the decreasing Jw from 11.05 LMH to 4.68 LMH and the increasing Js from 13.07 gMH to 33.97 gMH, with the concentration of acrylamide FS increasing from 200 to 600 g/L. This was because the OP of the FS dramatically increased from 71.49 bar to 187.28 bar with the increasing acrylamide FS from 200 to 600 g/L, and the resulting driving force of the OP difference between feed and draw solutions significantly decreased from 342.32 bar to 226.53 bar at the initial operation. Moreover, the high salt permeability at the high osmotic FS may be related to a weakened Donnan potential in the negatively charged polyamide surfaces (Bartels et al., 2005).
Figure 5. When using different concentrations of acrylamide solutions as FS, water flux (Jw), reverse salt flux (Js) (A,B), and SRSF (Js/Jw) (C) under the AL-FS mode with 4 M and 5 M MgCl2 DS, respectively.
The SRSF (Js/Jw) value presents an increasing trend with the increasing acrylamide FS and MgCl2 DS (Figure 5C). For example, the SRSF (Js/Jw) value obviously increased from 0.38 g/L to 4.24 g/L with the increasing acrylamide concentration from 200 to 600 g/L when employing 4 M MgCl2 DS. In addition, with the same acrylamide FS, the SRSF (Js/Jw) value was higher employing a 5 M MgCl2 than that employing 4 M MgCl2 as DS. These results illustrate that both the loss of draw solutes and the ICP of the AL-FS operation were aggravated with the increasing concentration of feed and draw solutions. This is due to the decreased diffusion rate of salt solutes and increased salt passage in the TFC membrane with the increasing concentrations of DS and FS (Bartels et al., 2005; Song et al., 2011).
All of these results demonstrate that the concentrations of both FS and DS significantly affect the water flux and reverse salt flux and thus impact the long-term FO operation efficiency and the quality of the concentrated acrylamide product.
In order to more highly concentrate the acrylamide FS, the long-term FO process was operated and the long-term performance of FO membrane was investigated. Both 4 M and 5 M MgCl2 draw solution were used to concentrate the acrylamide solution from 200 g/L to 400 g/L; the final accumulated salt concentration in the acrylamide solution and the operation time were measured as two important parameters to evaluate the FO performance during the concentration of acrylamide solution. Figure 6 shows that the water flux of the FO membrane decreased rapidly in the initial stage and then slowly when the acrylamide solution was concentrated gradually from 200 g/L to 400 g/L. Moreover, the membrane water flux was higher when using 5 M MgCl2 DS than when using 4 M MgCl2 solution, while the flux difference between using 5 M and 4 M MgCl2 DSs became smaller with the increasing acrylamide solution during the concentration process. This is because of the greater dilution for higher concentration of DS when drawing the same amount of water, thus inducing the fast flux decline. In addition, higher concentrations of Mg2+ ions may also increase the scale on the membrane surface, possibly aggravating membrane fouling and causing a decrease in flux (Sun et al., 2016; Almoalimi and Liu, 2022). Importantly, it took 32.42 h to concentrate acrylamide solution from 200 g/L to 400 g/L with 5 M MgCl2 DS, which is much shorter than 48.79 h with 4 M MgCl2 DS (Figure 6). The accumulated salt in the acrylamide solution was 1.77 g/L when using 5 M MgCl2 solution as the DS, which is slightly higher than that of 1.74 g/L when using 4 M MgCl2 solution as the DS. Therefore, considering the FO process efficiency and the quality of concentrated product, 5 M MgCl2 is a better selection as the DS.
Figure 6. Water flux of the TFC polyamide membrane (left) and operation time (right) during the concentration of acrylamide solution from 200 g/L to 400 g/L and the accumulative salt content (bottom) in the final 400 g/L acrylamide solution when using 200 g/L acrylamide solution as an initial FS and different concentrations of MgCl2 as DS. The TFC polyamide membrane was operated in the AL-FS mode.
In order to improve the FO efficiency for the concentration of acrylamide solution, a multi-stage operation system was introduced to compensate for the dilution of DS and thus maintain the high flux. Here, the solute of MgCl2 was supplemented in the DS to remain at 5 M at the end of each stage when the acrylamide concentration was increased by 100 g/L. The results shown in Figure 7 and Table 1 indicate that the concentration efficiency can be effectively improved via multi-stage operation. For example, at the end of Stage I, the declined water flux was 6.83 LMH. By updating the draw concentration to 5 M, the water flux at the beginning of Stage II was increased 18.56% to 8.89 LMH. Additionally, the increased percentages of water flux were 17.52% and 18.43% at the beginning of Stages III and IV, respectively, compared with the water fluxes at the end of Stages II and III. This improved performance was achieved by renewing the draw concentration, demonstrating the efficiency of multi-stage operation and highlighting its potential for real FO applications.
Figure 7. Water flux profile of the TFC polyamide membrane and accumulative salt content during the concentration of acrylamide solution from 200 g/L to 600 g/L when using 5 M MgCl2 as the DS. The TFC polyamide membrane was operated in the AL-FS mode.
Moreover, the initial flux at each stage decreased gradually with the increase of the acrylamide concentration. For example, the initial water flux dropped significantly from 11.06 LMH (Stage I) to 6.07 LMH (Stage IV), while the initial concentration of acrylamide FS increased from 200 g/L (Stage I) to 500 g/L (Stage IV) and caused the decreased driving force of the FO process. Noticeably, the initial water fluxes at Stages II, III, and IV were very close to the membrane flux (Figure 5B) when operated at the same condition of the FO process but without the accumulative effect from the former stage. In addition, the flux decline percentage at each stage was also calculated to be 38.23% (Stage I), 37.29% (Stage II), 40.30% (Stage III), and 50.11% (Stage IV), respectively (Table 1). This observation further suggests that the flux decline accelerated at the later stage with the concentration increase of acrylamide FS because of the intensified ICP effect at the higher concentration of FS.
The accumulated salt in the final product was considered to be another critical factor for the concentration process of FO. As shown in Figure 7, the accumulated salt in the resultant acrylamide solution increased from 1.5 g/L to 3.7 g/L with an increase in the concentration factor from 1.5 to 3.0 when the acrylamide FS was concentrated from 300 g/L to 600 g/L. The concentration of MgCl2 in the final concentrated acrylamide solution (600 g/L) was only 3.7 g/L, less than the 0.62 wt% impurity in the product of acrylamide. Additionally, our results also suggest that the concentration of acrylamide solution can be further increased to be higher than 600 g/L since there was approximately 4.69 LMH of flux when 600 g/L acrylamide was used as FS (Figure 5B).
Furthermore, we summarized the FO performances of single- and multi-stage FO processes in Table 1. The results illustrate that the multi-stage process helped increase the average flux and save the concentration time compared with the single-stage FO process during the concentration of acrylamide FS from 200 g/L to 400 g/L. The flux increment and time-saving percentages were up to 14.61% and 13.91%, respectively, relative to the single-stage process. In addition, it took less time for the later stage to increase the acrylamide concentration by 100 g/L because of the decreasing volume of the FS. All results indicate that the multi-stage FO process would be preferred for the chemicals’ concentration because of high system efficiency, including high water flux and short operation time.
In comparison to the conventional multi-stage evaporation process (described in US patents US3887425A and US5922912A), the multi-stage FO process presents distinct advantages, including the elimination of high-temperature operations and enhanced concentration efficiency. According to these patents (Munch, 1975; Kambara et al., 1999), the conventional evaporation process typically requires operation at temperatures nearing 100 °C, accompanied by substantial energy consumption. In addition, high temperatures may cause acrylamide to polymerize to form insoluble polymers, reducing product quality. Furthermore, conventional evaporation methods typically achieve concentration limits of approximately 40–50 wt%. In contrast, our multi-stage FO process operates at a significantly lower temperature of 25 °C for the feed liquid, thereby reducing the demand for thermal energy during concentration. Moreover, our multi-stage FO process achieves higher concentrations (up to 600 g/L, equivalent to a mass concentration of 57.58%), surpassing the concentration thresholds necessary for various applications of acrylamide (Zheng et al., 2010).
Our work demonstrates that the multi-stage FO process provides an efficient way to concentrate high-osmotic acrylamide solution at room temperature. The high performance TFC polyamide membrane was used in the FO process to concentrate the acrylamide solution from 200 g/L to 600 g/L, and the AL-FS mode was demonstrated to be a more efficient operation orientation than AL-DS to concentrate a high concentration acrylamide solution (>200 g/L) during the FO process. A measure of 5 M divalent MgCl2 solution was used as an effective draw solute to provide high OP and suppress the ICP of the TFC membrane with a very low reverse salt flux. The results also illustrate that the multi-stage FO operation could dramatically improve the system efficiency for acrylamide concentration, and the draw concentration renewal at Stage II led to a water flux increase by 14.61% and to a 13.91% saving of concentration time. Moreover, the accumulated MgCl2 in the final 600 g/L acrylamide solution was below 3.7 g/L, less than 0.62 wt% impurity in the product of acrylamide. Our research demonstrates the great potential of the multi-stage FO process for concentrating high osmotic chemicals with high system efficiency. Further investigation of regenerating draw solution is needed to achieve a sustainable operation of the FO process for scale-up operation, and membrane distillation may provide a facile approach for keeping a constant concentration of the draw solution and maintaining a stable water flux of the FO process. The integrated FO-MD system effectively harnesses the inherent strengths of both processes, enabling the production of highly concentrated acrylamide along with high-purity purified water while also achieving energy savings.
The original contributions presented in the study are included in the article/Supplementary Material; further inquiries can be directed to the corresponding author.
SH: writing–original draft and methodology. ZZ: formal analysis, methodology, and writing–original draft. XZ: data curation, methodology, and writing–review and editing. XA: data curation and writing–original draft. YH: funding acquisition, resources, and writing–review and editing.
The author(s) declare that no financial support was received for the research, authorship, and/or publication of this article.
The authors gratefully acknowledge the support of the National Natural Science Foundation of China (No. 21978215).
The authors declare that the research was conducted in the absence of any commercial or financial relationships that could be construed as a potential conflict of interest.
The author(s) declared that they were an editorial board member of Frontiers, at the time of submission. This had no impact on the peer review process and the final decision.
All claims expressed in this article are solely those of the authors and do not necessarily represent those of their affiliated organizations, or those of the publisher, the editors and the reviewers. Any product that may be evaluated in this article, or claim that may be made by its manufacturer, is not guaranteed or endorsed by the publisher.
The Supplementary Material for this article can be found online at: https://www.frontiersin.org/articles/10.3389/frmst.2024.1407819/full#supplementary-material
Al-Kindi, S., Al-Bahry, S., Al-Wahaibi, Y., Taura, U., and Joshi, S. (2022). Partially hydrolyzed polyacrylamide: enhanced oil recovery applications, oil-field produced water pollution, and possible solutions. Environ. Monit. Assess. 194 (12), 875. doi:10.1007/s10661-022-10569-9
Almoalimi, K., and Liu, Y.-Q. (2022). Fouling and cleaning of thin film composite forward osmosis membrane treating municipal wastewater for resource recovery. Chemosphere 288, 132507. doi:10.1016/j.chemosphere.2021.132507
Alshehri, A., and Lai, Z. (2014). Attainability and minimum energy of single-stage membrane and membrane/distillation hybrid processes. J. Membr. Sci. 472, 272–280. doi:10.1016/j.memsci.2014.08.056
Asano, Y., Yasuda, T., Tani, Y., and Yamada, H. (2014). A new enzymatic method of acrylamide production. Agric. Biol. Chem. 46 (5), 1183–1189. doi:10.1080/00021369.1982.10865240
Bartels, C., Franks, R., Rybar, S., Schierach, M., and Wilf, M. (2005). The effect of feed ionic strength on salt passage through reverse osmosis membranes. Desalination 184 (1-3), 185–195. doi:10.1016/j.desal.2005.04.032
Braun, O., Coquery, C., Kieffer, J., Blondel, F., Favero, C., Besset, C., et al. (2022). Spotlight on the life cycle of acrylamide-based polymers supporting reductions in environmental footprint: review and recent advances. Molecules 27 (1), 42. doi:10.3390/molecules27010042
Chekli, L., Phuntsho, S., Kim, J. E., Kim, J., Choi, J. Y., Choi, J.-S., et al. (2016). A comprehensive review of hybrid forward osmosis systems: performance, applications and future prospects. J. Membr. Sci. 497, 430–449. doi:10.1016/j.memsci.2015.09.041
Giagnorio, M., Morciano, M., Zhang, W., Hélix-Nielsen, C., Fasano, M., and Tiraferri, A. (2022). Coupling of forward osmosis with desalination technologies: system-scale analysis at the water-energy nexus. Desalination 543, 116083. doi:10.1016/j.desal.2022.116083
Han, G., Zhang, S., Li, X., Widjojo, N., and Chung, T.-S. (2012). Thin film composite forward osmosis membranes based on polydopamine modified polysulfone substrates with enhancements in both water flux and salt rejection. Chem. Eng. Sci. 80, 219–231. doi:10.1016/j.ces.2012.05.033
Hancock, N. T., and Cath, T. Y. (2009). Solute coupled diffusion in osmotically driven membrane processes. Environ. Sci. Technol. 43 (17), 6769–6775. doi:10.1021/es901132x
Hao, S., Wang, J., Wang, Z., An, X., Liu, T., Qin, Y., et al. (2023a). Impact of hPG molecular size on the separation properties and antifouling performance of hPG-modified thin-film composite nanofiltration membrane. Desalination 548, 116296. doi:10.1016/j.desal.2022.116296
Hao, S., Xiao, J., Liu, L., Qin, Y., Li, S., and Hu, Y. (2023b). High flux and highly fouling-resistant polyamide reverse osmosis membrane having inner and outer zwitterion-like layers. Desalination 565, 116823. doi:10.1016/j.desal.2023.116823
Hu, Y. (2023). Grand challenge in membrane applications: liquid. Front. Membr. Sci. Technol. 2, 1177528. doi:10.3389/frmst.2023.1177528
Ibraheem, B. M., Aani, S. A., Alsarayreh, A. A., Alsalhy, Q. F., and Salih, I. K. (2023). Forward osmosis membrane: review of fabrication, modification, challenges and potential. Membranes 13 (4), 379. doi:10.3390/membranes13040379
Kambara, Y., Matsumura, M., Umeno, M., Uehara, Y., and Asao, K. (1999). Concentration method of aqueous acrylamide solution. U.S. Pat. Appl. 5 (922), 912.
Lee, C. Y., Hwang, Y. B., and Chang, H. N. (1991). Acrylonitrile adaptation of Brevibacterium sp. CH1 for increased acrylamide production. Enzyme Microb. Technol. 13 (1), 53–58. doi:10.1016/0141-0229(91)90188-g
Li, J., Guo, M., Jiao, S., Wang, Y., Luo, G., and Yu, H. (2017). A kinetic study of the biological catalytic hydration of acrylonitrile to acrylamide. Chem. Eng. J. 317, 699–706. doi:10.1016/j.cej.2017.02.100
Lin, S., and Elimelech, M. (2015). Staged reverse osmosis operation: configurations, energy efficiency, and application potential. Desalination 366, 9–14. doi:10.1016/j.desal.2015.02.043
Liu, X., Wu, J., Liu, C., and Wang, J. (2017). Removal of cobalt ions from aqueous solution by forward osmosis. Sep. Purif. Technol. 177, 8–20. doi:10.1016/j.seppur.2016.12.025
Liu, Z., and Hu, Y. (2016). Sustainable antibiofouling properties of thin film composite forward osmosis membrane with rechargeable silver nanoparticles loading. ACS Appl. Mater Interfaces 8 (33), 21666–21673. doi:10.1021/acsami.6b06727
Long, Q., Qi, G., and Wang, Y. (2016). Evaluation of renewable gluconate salts as draw solutes in forward osmosis process. ACS Sustain. Chem. Eng. 4 (1), 85–93. doi:10.1021/acssuschemeng.5b00784
McGinnis, R. L., and Elimelech, M. (2007). Energy requirements of ammonia–carbon dioxide forward osmosis desalination. Desalination 207 (1-3), 370–382. doi:10.1016/j.desal.2006.08.012
Nagasawa, T., Shimizu, H., and Yamada, H. (1993). The superiority of the third-generation catalyst, Rhodococcus rhodochrous J1 nitrile hydratase, for industrial production of acrylamide. Appl. Microbiol. Biotechnol. 40 (2-3). doi:10.1007/bf00170364
Nath, A., and Pande, P. P. (2020). Polyacrylamide based polymers: smart materials used in wastewater treatment. Adv. Sci. Eng. Med. 12 (1), 105–107. doi:10.1166/asem.2020.2531
Ogata, N. (1960). The transition polymerization of acrylamide. I. On the polymerization condition and the property of polymer. Bull. Chem. Soc. Jpn. 33 (7), 906–912. doi:10.1246/bcsj.33.906
Raj, J., Prasad, S., and Bhalla, T. C. (2006). Rhodococcus rhodochrous PA-34: a potential biocatalyst for acrylamide synthesis. Process Biochem. 41 (6), 1359–1363. doi:10.1016/j.procbio.2006.01.022
Rastogi, N. K. (2016). Opportunities and challenges in application of forward osmosis in food processing. Crit. Rev. Food Sci. Nutr. 56 (2), 266–291. doi:10.1080/10408398.2012.724734
Seybold, C. A. (2008). Polyacrylamide review: soil conditioning and environmental fate. Commun. Soil Sci. Plant Analysis 25 (11-12), 2171–2185. doi:10.1080/00103629409369180
She, Q., Wang, R., Fane, A. G., and Tang, C. Y. (2016). Membrane fouling in osmotically driven membrane processes: a review. J. Membr. Sci. 499, 201–233. doi:10.1016/j.memsci.2015.10.040
Smith, E. A., and Oehme, F. W. (1991). Acrylamide and polyacrylamide: a review of production, use, environmental fate and neurotoxicity. Rev. Environ. Health 9 (4), 215–228. doi:10.1515/reveh.1991.9.4.215
Song, X., Liu, Z., and Sun, D. D. (2011). Nano gives the answer: breaking the bottleneck of internal concentration polarization with a nanofiber composite forward osmosis membrane for a high water production rate. Adv. Mater 23 (29), 3256–3260. doi:10.1002/adma.201100510
Sun, Y., Tian, J., Zhao, Z., Shi, W., Liu, D., and Cui, F. (2016). Membrane fouling of forward osmosis (FO) membrane for municipal wastewater treatment: a comparison between direct FO and OMBR. Water Res. 104, 330–339. doi:10.1016/j.watres.2016.08.039
Sun, Y., Xue, L., Zhang, Y., Zhao, X., Huang, Y., and Du, X. (2014). High flux polyamide thin film composite forward osmosis membranes prepared from porous substrates made of polysulfone and polyethersulfone blends. Desalination 336, 72–79. doi:10.1016/j.desal.2013.12.036
Tian, M., Qiu, C., Liao, Y., Chou, S., and Wang, R. (2013). Preparation of polyamide thin film composite forward osmosis membranes using electrospun polyvinylidene fluoride (PVDF) nanofibers as substrates. Sep. Purif. Technol. 118, 727–736. doi:10.1016/j.seppur.2013.08.021
Tiraferri, A., Yip, N. Y., Straub, A. P., Romero-Vargas Castrillon, S., and Elimelech, M. (2013). A method for the simultaneous determination of transport and structural parameters of forward osmosis membranes. J. Membr. Sci. 444, 523–538. doi:10.1016/j.memsci.2013.05.023
Truong, V.-H., and Chong, T. H. (2024). Development of a diafiltration-nanofiltration-reverse osmosis (DiaNF-RO) process for ion fractionation towards resource recovery in seawater desalination. Desalination 583, 117684. doi:10.1016/j.desal.2024.117684
Wade, N. M. (1993). Technical and economic evaluation of distillation and reverse osmosis desalination processes. Desalination 93 (1-3), 343–363. doi:10.1016/0011-9164(93)80113-2
Watanabe, I. (1982). Process for the production of acrylamide using microorganism. U. S. Pat., US4343900.
Watanabe, I., Ogawa, Y., and Seki, S. (1989). Method for producing acrylamide using a microorganism. U. S. Pat., US4851342.
Xudong, S., Yue, S., Huimin, Y., and Zhongyao, S. (2004). Bioconversion of acrylnitrile to acrylamide using hollow-fiber membrane bioreactor system. Biochem. Eng. J. 18 (3), 239–243. doi:10.1016/j.bej.2003.09.001
Yip, N. Y., Tiraferri, A., Phillip, W. A., Schiffman, J. D., and Elimelech, M. (2010). High performance thin-film composite forward osmosis membrane. Environ. Sci. Technol. 44 (10), 3812–3818. doi:10.1021/es1002555
Zhang, K., An, X., Bai, Y., Shen, C., Jiang, Y., and Hu, Y. (2021). Exploration of food preservatives as draw solutes in the forward osmosis process for juice concentration. J. Membr. Sci. 635, 119495. doi:10.1016/j.memsci.2021.119495
Zhao, S., Zou, L., Tang, C. Y., and Mulcahy, D. (2012). Recent developments in forward osmosis: opportunities and challenges. J. Membr. Sci. 396, 1–21. doi:10.1016/j.memsci.2011.12.023
Zheng, R.-C., Zheng, Y.-G., and Shen, Y.-C. (2010). “Acrylamide, microbial production by nitrile hydratase,” in Encyclopedia of industrial Biotechnology, 1–39.
Keywords: forward osmosis, multi-stage, high osmotic pressure, acrylamide, concentration
Citation: Hao S, Zhang Z, Zhao X, An X and Hu Y (2024) Investigation of multi-stage forward osmosis membrane process for concentrating high-osmotic acrylamide solution. Front. Membr. Sci. Technol. 3:1407819. doi: 10.3389/frmst.2024.1407819
Received: 27 March 2024; Accepted: 20 May 2024;
Published: 28 June 2024.
Edited by:
Maria Giovanna Buonomenna, Ordine dei Chimici e Fisici della Campania and MIUR, ItalyReviewed by:
Yuan Liao, Nankai University, ChinaCopyright © 2024 Hao, Zhang, Zhao, An and Hu. This is an open-access article distributed under the terms of the Creative Commons Attribution License (CC BY). The use, distribution or reproduction in other forums is permitted, provided the original author(s) and the copyright owner(s) are credited and that the original publication in this journal is cited, in accordance with accepted academic practice. No use, distribution or reproduction is permitted which does not comply with these terms.
*Correspondence: Yunxia Hu, eXVueGlhaHVAdGlhbmdvbmcuZWR1LmNu
Disclaimer: All claims expressed in this article are solely those of the authors and do not necessarily represent those of their affiliated organizations, or those of the publisher, the editors and the reviewers. Any product that may be evaluated in this article or claim that may be made by its manufacturer is not guaranteed or endorsed by the publisher.
Research integrity at Frontiers
Learn more about the work of our research integrity team to safeguard the quality of each article we publish.