- 1Department of Management and Humanities, University of Technology Petronas, Tronoh, Malaysia
- 2Department of HRM, College of Administrative and Financial Science, Qatar University, Doha, Qatar
- 3Gulf University, Sanad, Bahrain
The main purpose of this research was to investigate the mediating role of safety communication (SCO) in the relationship between safety culture (SC) and safety performance (SP) amongst employees in the petrochemical industry. Safety communication methods not only enhance working conditions but also have a positive impact on employee's behaviors and attitudes toward safety leading toward reduced incidents in the workplace environment. A stratified sampling method was followed to collect data in the petrochemical industry in Malaysia. Structural equation modeling (SEM) was utilized to analyze the hypothesized model, using data from 320 participants. The findings reveal that safety communication partially mediates the association between safety culture and safety performance. Further, safety culture was found to have a significant and positive effect on safety performance. This -study makes a significant theoretical contribution by providing empirical evidence on the direct and indirect relationship between safety culture and safety performance in the petrochemical industry.
Introduction
Despite a wide variety of approaches and ideas throughout the years to enhance safety culture and occupational health and safety in the workplace, the petrochemical oil and gas industry has faced difficulties to diminish a high rate of fatalities and injuries amongst working staff (1, 2). In the United States alone there were 138 deaths, due to of the nature of work in the petrochemical industry (3), and this regrettable trend extended throughout the sector's operations around the world. By comparison, the industry's on-the-job fatality rate in the United States was ~7.6 times higher than the national average (4).
Many previous studies have examined the link between safety culture and safety outcomes (5–9). However, there is a lack of evidence in the literature on the essential role of safety communication in the relationship between safety culture and safety performance. Effective safety communication plays a vital role in reducing incidents of employees at the workplace. Safety communication is not only about the exchange of information on safety in the workplace; it is also about influencing staff behavior and attitudes toward safety (10). According to Noort, Reader, Shorrock, and Kirwan (11) effective safety communication positively affects safety performance. On the other hand, Mullen (12, 13), identified that poor communication often occurs among workers, particularly among employees and senior management, and may be due to a neglect of constructive communication and feedback regarding workplace safety. One of the reasons for poor safety communication is the lack of a positive safety culture (14). Therefore, the current study aims to fill this gap and contribute to safety literature, by investigating the role of safety communication as a mediating factor in the relationship between safety culture and employee safety performance.
This study focuses on the petrochemical and oil and gas industry since this entails high risks related to health and safety. The oil and gas sector is under public scrutiny like never before on a host of health, safety, and environmental problems (15). These concerns are already impacting how companies operate and interact with the public. A pilot program with nine companies called the SafeOCS Industry Safety Database managed by the Bureau of Transportation Statistics in the U.S, has selected three potential next steps for the use of this industry wide safety database. One of the main steps is: “Develop effective communication processes, including dashboards, to share lessons learned, review aggregated results, assess causal factors, network, and discuss potential actions to prevent recurrence and thereby improve safety” (16). According to Curlee et al. (17), all the petrochemical and oil and gas production and exploration activities, typically experience the highest fatality rates of all the major industries. In the same line, Cloughley and Thomas (18), stated thatpetrochemical activities tend to be harsh and hazardous as they take place within ahigh pressure and high temperature (HPHT) environment.
Based on the aforementioned argument, we hypothesize that safety communication will mediate the relationship between safety culture and employee safety performance. Safety culture, by reducing accidents, allows employers to invest their resources in obtaining and enhancing safety performance (19–21). The rest of the paper is structured as follows: Section 2 provides a review of the literature and develops the study hypotheses; Section 3 presents the methods and materials; Section 4 presents the data analysis and results, Sections 5 and 6 present the discussion and conclusion.
All in all, this study aims to provide new theoretical and practical insights in the relationship between safety culture and safety performance by exploring the key role of safety communication as a mediating variable. It also does so in a newly industrialized country context.
Literature Review
Personnel in the field have to deal with the instability of the drilling and production process. Activities such as overbalanced wells, gas leakages, and generally, the reactive nature of hydrocarbon resources tend to create life-threatening situations if not monitored well (22). That is why much of the literature has focused on the health safety environment (HSE) in the petrochemical, oil and gas sector.
Employers paid around “1 billion USD per week” for direct staff compensation costs according to National Safety Council statistics in 2010. The economic influence of workplace injuries in the U.S. were nearly 142 billion USD every year and the production loss because of accidents and injuries was equal to 80 million days lost every year (23). While deaths and injuries are irreversible effects, there are several financial and environmental effects involved as well. Indeed, if everybody behaved and performed safely, the production would certainly increase, or at least there would be no drop in production. A survey conducted by Liberty Mutual and cited by (24) found out amongst executives that:
❖ 9% indicated that a company's financial performance is greatly influenced by a safe workplace.
❖ 61% assumed that for each $1 for safety invested, a $3 or more return was observed.
❖ 13% stated that in each $1 invested in safety, $10 would be reimbursed.
❖ And 40% expected indirect costs between $3 and $5, for every $1 in direct costs of injuries or incidents.
From the devastating impact of the Bhopal tragedy in 1984 to the Macondo accident in the Gulf of Mexico in 2010, accidents have been proven to affect individuals, the environment, and the company's brand, as well as result in additional legal concerns such as criminal charges (25). The adverse effects of industrial incidents on societal loss have been evaluated in numerous studies (26).
There are three sectors in the petrochemical industry: upstream, midstream, and downstream. Employees in all three industries operate in high-risk conditions (Figure 1). The upstream sector is responsible for the production of fundamental raw materials, the midstream sector is for intermediates, and the downstream sector is in charge of the process and production of diverse byproducts (20).
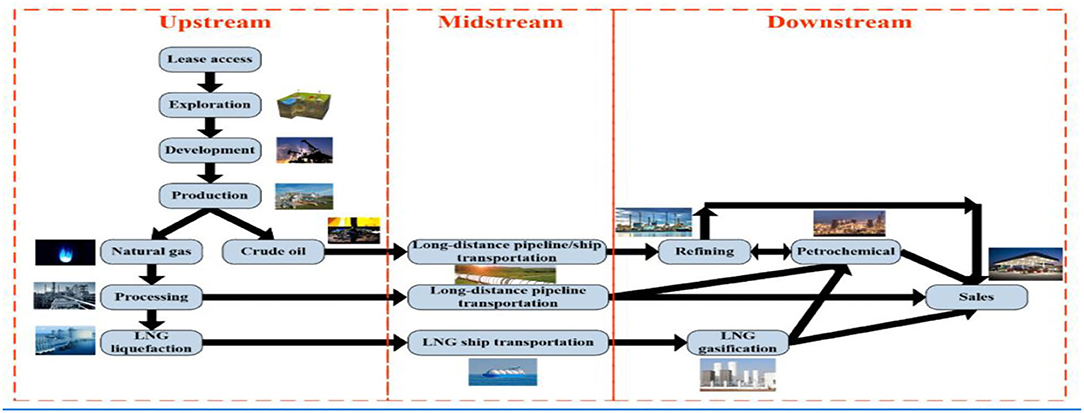
Figure 1. Upstream, midstream, and downstream operations in the oil and gas sector. Source (82).
Upstream Operations
The upstream operation is the initial step in the oil and gas production process, and it includes searching for crude oil and natural gas deposits, as well as recovering and producing them (27). Within the oil and gas industry, this stage is known as the E&P (exploration and production) stage (28). Searching for oil reserves, either underground or underwater, drilling exploratory wells, and, if deposits are discovered, operating these wells to bring found deposits to the surface are all common areas in the upstream process.
Midstream Operations
The natural gas and oil industry's midstream operation makes a significant contribution to everything needed to transport and store crude oil and natural gas before they are refined and processed into fuels and critical components for a long list of products used every day. Pipelines and all the infrastructure required to transport these resources over far distances, such as pumping stations, tank trucks, rail tank cars, and transcontinental tankers, are all part of the midstream industry (29, 30).
Downstream Operations
The final and most diversified stage of the oil and gas industry is downstream operations. This could include everything from crude oil refining to natural gas processing and purification, as well as sales, marketing, product distribution, and retail. The production of petrochemicals and plastics is also included. During the downstream stage, many products derived from crude oil are produced, including diesel oil, liquefied petroleum gas (LPG), petrol, fertilizers, antifreeze, pharmaceuticals, and even cosmetics (31). Downstream is without a doubt the part of the oil and gas business that has the most direct relationship to daily consumers, which means that jobs in this sector are in high demand and diverse (32, 33).
Safety Culture
Many companies throughout the world are becoming more interested in the concept of “safety culture” as a way to reduce the risk of large-scale disasters and accidents that occur during ordinary work. Its expanding relevance is evidenced by publicly declared goals in the offshore, shipping, and nuclear industries to achieve consistent global safety cultures (34–37). Companies are motivated to find solutions to prevent workplace injuries because of the costs connected with them and the time necessary for accident investigations (38, 39).
Improved culture and behaviors of operating personnel play a vital role in safe operations (40, 41). Visible leadership motivates personnel and enhances the performance of the company. It also enhances the commitment of the operating personnel. It has been observed that people are poor in assessing risks whilst performing operations as people tend to become acclimated to risk, i.e., “Used to Risk.” They unconsciously adjust their definition of acceptable risk. E.g., NASA Officials got used to living with small failures, the result-the catastrophic failure of the challenger. Overconfidence is also one of the main reasons for accidents–exposure to fairly fixed and no risk over a long period results in the underestimation of risk (42, 43). People have trouble imagining how small failings can lead to catastrophic disasters (Dominos Effect). Ignorance supplies fuel for accidents to happen. No matter how well defined a system is, someone will find a way to defeat the pro-active measures. A large number of cases are available in the industry (44). Many previous studies (45, 46), mentioned that there is a significant relationship between safety culture and safety communication.
As a result, the organizational culture, specifically the safety culture, is predicted to play a critical role in the mitigation of safety communication, hence hypothesis 1 was developed to investigate the link between safety culture and safety communication.
Hypothesis 1: Safety culture has a positive impact on safety communication.
Factors of Safety Cultures
Work Environment
Workplace environment (WE) refers to the procedures and policies that must be implemented to ensure the health and safety of employees. The first policy entails accident detection and control based on regulatory regulations, as well as staff safety training and education (47). The immediate context in which an individual conducts his task is referred to as the workplace environment. The setting in which employees work has a significant effect on the quality of their work and their performance. Improper surroundings present dangers, making the workplace environment dangerous and slowing the employee's production rate (48, 49). Furthermore, health and safety at work have professionals and legal obligations to provide employees with a workplace free of hazards that could result in significant physical injury or death. In addition, they must provide a safe and healthy working environment for their employees.
Organization Communication
Organizational communication (OC): is known as a productive relationship with others, understanding and listening to each other. Conveying ideas and communications obviously and consistently; expressing things comprehensibly and simply, in ways that others can understand, and showing sincere knowledge, interest, and concern; bringing these features together to make variation happen. Communication effectively sustains the development of optimistic relationships with all investors and can impact attitudes and behaviors regarding safety and health issues (50).
Leadership
Leadership (LS) is related to the process of social influence, which maximizes the effects of others, toward the achievement of a goal. Leaders are individuals who have great influence attitudes and behaviors of others. Usually, they do this through their normal character and by their influence. Leaders can be assigned at any position in an organization from the board and senior executives, through middle-level managers such as site managers, to front-line supervisors (19, 51–53). Safety and health improvement in an organization depends on positive leadership and competent management.
Safety Performance
Kucherov et al. (54), mentioned that safety performance occurs when front-line individuals improve their behaviors, however, behaviors on the front line will only change if there is a great leader to monitor their behaviors, make a different feeling of belonging in the teamwork. With this regard, oil and gas companies are increasingly developing and implementing safety leadership training programs. It aims to help leaders to create a personal and organizational safety imperative to be apart from their daily personnel behavior, provide Leaders to deliver the cultural and behavioral changes on the front line, and make safety leadership self-sustaining with the organization (55, 56). People, processes, tasks, and systems can interact purposefully and cooperatively to achieve health, safety, and environmental (HSE) goals through communication. The way we communicate with safety will have an impact on whether or not people accept and engage in the process, and the language we use will frequently indicate whether or not the method is accepted (9). Graphs representing lost time, medical procedures, employee's compensation rates, intensity and accident rates, and good performance measures can be used to communicate an organization's performance. These are used to enable continuous improvement and increase line employee's responsibilities for meeting an organization's HSE goals (57).
Safety incidents data have been collected and categorized by Oil and Gas Producers (OGP) and the international association of oil and gas producers since 1985. (IOGP) obtained the largest database of safety performance in the exploration and production industry. Around fifty participant organizations of the oil and gas industry contribute to annual benchmarking processes that focus mainly on incidents, accidents, and injuries in the oil and gas companies (58, 59).
According to Coday et al. (60), the process of extracting hydrocarbons in remote geographical locations and harsh environmental conditions is drastically increasing worldwide. Combined associations and established partnerships between giant oil producers on risky international projects are common. Sharing contracts with several investors must be managed properly. There is a high rate of non-productive time that requires swift and decisive action, and the overall equipment efficiency needs to grow (61, 62).
Human and environmental safety and health protection remain the number one priority for the oil and gas industry. These companies are used to dealing with stringent EHS regulations across the entire span of their activities, from exploration and production, to pipeline management and marketing (63, 64). These regulations are not only stringent but also constantly revised to take into consideration technological development and the more extreme conditions in which oil and gas companies operate (65). Previous research (9, 66, 67), hasrevealed that positive safety culture and safety communication were essential to enhanced safety performance. Therefore, the following hypotheses are established based on the preceding discussion.
Hypothesis 2: Safety communication has a positive impact on safety performance.
Hypothesis 3: Safety culture factors has a positive impact on safety performance.
Safety Communication
Today, a growing number of businesses are prioritizing safety communications as a key value. This emphasis on safe workplace benefits not only employee morale as well as the business line. According to the “Liberty Mutual Workplace Safety Index (68),” a company may expect a $4 return on investment for every $1 invested in workplace safety. Safety communication is the most influencing tool in all aspects of business, and the workplace is no exception. Safety hazards, regulations, goals, warnings, area guidelines, rules, and progress reports should be communicated to employees via a variety of media for a truly protected workplace to be implemented (69). Organizational safety culture, leadership, and group climates are all part of the bigger picture when it comes to safety communication (70). The use of researcher-based evaluation and feedback to operational and production workers to improve their daily oral safety communication with employees resulted in considerably higher levels of safety performance in the workplace environment (71, 72). In their conceptualizations and evaluations of the safety culture in various industries, several scholars have added safety communication (73–75). The term “safety culture” refers to a set of shared organizational ideals aimed at reducing risk. This is when most people in an organization, from top leadership to temporary workers, place high importance on ensuring a safe workplace (76). Poor safety culture and communication have been linked to infamous and large-scale health and safety catastrophes in the past, demonstrating why encouraging improved safer practices is a powerful strategy (77). Employee errors, however, are not the main source of blame. Poor management actions, such as ignoring the need to develop channels of communication with employees or ignoring employee feedback, can result in large financial losses (78). Improving health and safety communication systems, such as the channels you use, how you record essential information, and employee feedback techniques has the potential to improve your company's safety culture. You will encourage greater self-responsibility in your employees as a result of this, and health and safety will become a shared obligation rather than a separated one (79). According to the finding of earlier studies (80, 81), when operational workers in the petrochemical oil and gas exploration sector in Malaysia detect a positive safety culture at the workplace, they must concentrate their efforts on performing the project rather than on safety measures, as they risk being laid off. Thus, it hypothesized that:
Hypothesis 4: Safety communication mediates the relationship between safety culture and safety performance.
As illustrated in Figure 2, a framework was constructed in this study to clarify that good safety performance, safety communication, and safety are all related to safety culture. This framework has highlighted three key variables that the researcher is examining (safety culture, safety communication, and safety performance).
In this study, safety culture will be an independent variable and assumed to influence safety performance (dependent variable). The connection between safety culture and safety performance will be mediated through safety communication. This research will examine the importance of safety communication in mediating the link between safety culture and safety performance in Malaysian petrochemical and oil and gas industries. By verifying the framework elements in the context of Malaysia, this study will also look at several ways for safety reducing risk, and accident prevention. The finding of this study will target to contribute to a better understanding of the factors that affect an employee's safety performance and how to increase positive safety behaviors. As a result, the model of employee safety performance will aid in the improvement of the worker's productivity and well-being, as well as ensuring his or her safety at work in general. Exchanges and protection Questionnaires based on “social exchange theory” (SET) and measuring the efficiency of exchanges have been utilized in the areas of communication, safety culture, and safety performance (83, 84).
Methods and Materials
Procedure
The surveys were delivered to Malaysian employees working in the petrochemical, oil, and gas industries. The principal investigator remained in the workplace throughout the questionnaire's completion to answer any queries that respondents might have. Employees in the petrochemical oil and gas sector responded with a total of 320 replies. As a result, the total sample size was set at N = 320. Therefore, the sample size is sufficient for 95% CI with a 5% margin of error (85).
Measures Used
The WE, OC, LS, SCO, and SP research instruments were adapted from well-known and widely used measures by researchers in this area (attached as Appendix A). Cronbach Alpha was evaluated for all factors in a pilot test involving 60 employees. The statement was declared suitable for usage because it was over 0.70 for all the variables. The following are the instrument's specifications.
Safety Culture
For measuring (SC), the 16-items scale was adopted by (86, 87). It has three dimensions: work environment (WE), (6 items), organization communication (OC), (5 items), and leadership (LS), (5 items). For each factor of the safety culture scale, the reliability values were determined to be as follows: work environment (0.896), organization communication (0.872), and leadership (0.922). As a result, the items are measured using a five-point Likert scale (1 = Strongly Disagree; 2 = Disagree; 3 = Neutral; 4 = Agree; 5 = Strongly Agree).
Safety Communication
SCO was designed by Vinodkumar and Bhasi (88), to examine the level of safety communication. Comprised of five items and was used to measure safety communication at the workplace environment and enhanced the connection between safety culture and safety performance, where the reliability value was discovered (0.864). Each items were respondents answered on a five-points Likert scale (1 = Strongly Disagree; 2 = Disagree; 3 = Neutral; 4 = Agree; 5 = Strongly Agree).
Safety Performance
For measuring (SP), the 9-item scale was adopted by Wu et al. (89). For each dimension of the safety performance scale, we tested the reliability, and the result was (0.907). Items are measured using a five-point Likert scale (1 = Strongly Disagree; 2 = Disagree; 3 = Neutral; 4 = Agree; 5 = Strongly Agree).
Sampling and Data Collection Procedures
This research used a five-point Likert scale with 30 items as the survey questionnaire (90–92), which has been used in previous investigations (93, 94). Table 1 shows the structure of the research instruments.
The sample for this study was chosen using a stratified random sampling procedure from the study's population. “Stratified random sampling” is defined as a stratification or segregation procedure is followed by the selection of participants at random in every stratum (95). Total numbers of 423 questionnaires were distributed through the petrochemical oil and gas company in Malaysia. After invalid surveys were removed, 320 genuine questionnaires were obtained, with an 86.89 % response rate.
Table 2 shows the percentage of males and females as 318 (99.4%) and 2 (0.6%), respectively; the gender structure of the survey revealed a higher ratio of men than women, which is consistent with the following features of the petrochemical oil and gas companies in Malaysia.
Based on marital status, respondents were married at 82.81, 13.13 % were single, and 4.06% were divorced. In terms of educational background, 82.19% of respondents had completed secondary school. Furthermore, 13.75% of the respondents had completed a college degree. In addition, 2.81% of respondents had finished their primary education, and 1.25% had a degree of graduate or postgraduate. As a result, the proportion of people with secondary education was relatively high, which corresponds to the requirements for employment in petrochemical oil & gas companies in Malaysia.
According to the frequency of the age groups in the sample, 12.81% of the total respondents are between the age of 20–29 years, 49.06% are between the age of 30–39 years, and 24.69% are between the ages of 40–49 years, and 10.94% are between the ages of 50–59 years, and 2.50% are between the ages of 60 years and above. As a result, the age composition of the sample was predominantly middle-aged and younger, which is consistent with the age requirements for employees in the petrochemical oil and gas sector.
Structural Equation Modeling Using Partial Least Squares (PLS-SEM)
Structural equation modeling (SEM) is a multivariate method for assessing the validity of competing hypotheses and obtained samples in the context of a concept or theory (96, 97). “Partial Least Squares” & “Structural Equation Modeling” (PLS-SEM) and covariance-based structural equation modeling are the two main techniques to SEM (CB-SEM) (96, 98).
When it comes to defining the link between items and constructs for researchers, PLS-SEM is more versatile than CB-SEM (99, 100). In any sample size, PLS-SEM performswell, but it must meet the sample size's minimum criteria, which allows for the generation of variables having complex effects on particular model components. The constructs or latent variables that can be employed with both reflective and non-reflective (formative) measurement models are the focus of PLS-SEM (101).
SEM is useful in a variety of situations, including models with a large number of hidden variables and indicators. As a result, it strives for the most sparse models feasible (102, 103). SEM has been successfully applied in a variety of social science fields, including construction, industry, hotel management, competitive performance [93, 94], the environment, and organization (39).
Lastly, the four hypotheses provided in this study were evaluated using the PLS-SEM approach. Variance inflation factor (VIF) was utilized to investigate multicollinearity challenges to evaluate multi-collinearity, according to Bauer and Baumeister (104). This was performed by evaluating the measurement model's fitting and path analysis using the Smart-PLS v3.2.1 tool (105). To test common technique bias, Harman's single factor was tested using SPSS version 25.0 software.
Normality Test
To examine the normality of the data set, a skewness and kurtosis test was carried out for all study variables. It is recommended that skewness and kurtosis range values of the variables must fall between ±1.96 (106). Both positive and negative deviations from these values are the causes of non-normality. Therefore, data (n = 320) was estimated for the assessment of normality assumption. It was noted that the value of Skewness and Kurtosis of all scale items was within the range of ±1.96, which is significant at 0.05. So, these results explain that data is normally distributed as shown in the table below.
Results and Data Analysis
The suggested model was evaluated using the “Partial Least Square technique (Smart-PLS 3.2.7) software” (107). We used the recommended two-staged analytical approach to evaluate the measurement and structural models (108). “G* Power version 3.1.9.2” was used to calculate the suitable sample size (109). The study's total sample size of 320 employees, comfortably exceeded the minimal sample size requirement. The number of participants in this study exceeded the recommended sample size for (PLS-SEM) analysis, which is 100 (110).
Common Method Variance
When data is collected from a single source, it is referred to as “single-source data,” there is a possibility of common method variance (111), or if the study utilized a cross-sectional research approach (112). There is a problem with common method variance when a single component describes most of the variance in a set of data (113). Harmans' one-factor test was utilized to assess the probability of common method variance (CMV). A total of 33.54% was accounted for the single factor, showing that common factors such as technique (testing time, single sources) is not a concern for these data set. Bagozzi et al. (114) propose another method for assessing common method variance. They stated that, if the inter-correlations in a correlation matrix are much more than 0.90, there could be a problem with common method variance. Table 3 shows that the correlation matrix's values are all < 0.90. As a result, both techniques confirm that in this study, there is not a severe issue of common method variance.
Multicollinearity
According to Hair et al. (115), multicollinearity refers to whether independent variables (IV) in a regression model are significantly associated with each other or with the dependent variable (DV). Before hypothesis testing, multicollinearity must be established. The multicollinearity of the current investigation was confirmed using variance inflation factor (VIF) (116). There is a possibility of multicollinearity if the VIF value is larger than 3.33 (117). To investigate the issue of multicollinearity, VIF was calculated. The VIF values for safety culture and safety communication were 1.32 and 1.314, respectively, which were significantly lower than the 3.33 threshold values (117). This shows that there are no difficulties with multicellularity in the research.
Measurement Model and Validity
There are two types of validity in the measuring model: convergent validity (CV) and discriminant validity (DV). Convergent validity describes how elements that are conceptually related are converging on the structure with which they are linked (118). Items loadings, average variance extracted (AVE), composite reliability(CR), Cronbach's alpha(CA), standardized factor loadings (SFL) are all part of the convergent validity (115). If an item's loading is equal to or > 0.7 the validity of items is accepted. But, if the items loading is <0.4 the item should be eliminated (115, 119). The items loadings (0.699–0.905) were within the permissible range. The AVE was larger than 0.5, which is consistent with the literature's indicated threshold value (115, 120–122). Where the values of SIL, CA, CR should be > 0.70 (121, 123–125). The determination coefficient R2 represents the degree of endogenous variable explained variance (99). R2 can be used to determine a structural model's explanatory capacity (126). for the development of target structures, the R2 must be acceptable, with this rage (“weak 0.25, medium 0.50, substantial 0.75”). The reliability and R2 test results are shown in Table 4.
According to the table above, SIL values varied from (0.700 to 0.894) which are (>0.650), and CA values ranged from (0.863 to 0.908) above 0.700, CR values ranged from 0.901 to 0.924 which are (>0.650), and AVE value ranged from 0.573 to 0.726 (>0.50) (127). According to Falk and Miller (128), the R2 value ranged from 0.222 to 0.359 (≥0.10).
The degree to which constructs are different from each other is explained by discriminant validity. We used the “Fornell and Larcker”(129) criterion to determine discriminant validity. The AVE square root for all constructs must be bigger than the correlation among all other constructs (130). Table 3 reveals that all numerical values were bigger than the correlation values of all other variables, indicating that the model is discriminately valid.
Structural Model
According to the previous research (98, 131) mentioned that, R2 values (predictive power), t-values and β- values using a “bootstrapping technique of 5,000 samples” to evaluate the structural model. The effect size f2 and Q2 values should also be reported, based on Kaufmann and Gaeckler (132). While a “p-value” can inform the reader whether an important impact exists, the “p-value” will not reveal the extent of the impact as mentioned by Sullivan and Feinn (133). Both statistically significant (p-value) and substantive significance (effect size) are important results to report and understand in investigations. We also used a blindfolding test to look at the model's predictive relevance (Q2), which is exclusively computed for dependence variables (DV). Q2 confirms that the observed associations are not only statistically significant but also practical, and it is only used on endogenous (dependent) construct with one or more components (134).
Safety communication showed mediate predictive power (R2 = 0.358). safety performance (R2 = 0.223), work environment (R2 = 0.801), organization communication (R2 = 0.532), and leadership (R2 = 0.290). For the predictive relevance (Q2) for safety communication (0.102), safety performance (0.112), work environment (0.631), organization communication (0.347), and leadership (0.028), all of the variables were higher than zero, showing that the model is predictive (115). Table 5 demonstrates the size of the effect f2 for safety culture with significant safety performance and safety communication. SC with SCO is small to mediate. The effect size for other two associations, namely safety communication and safety culture and safety performance was found small to medium (135). Three constructs were identified as independent variables (IV) under safety culture, work environment (WE), organization communication (OC), and leadership (LS), and safety performance (SP), and safety communication was the mediating variable in the final structural model. The latent variables for all of these higher-order structures were determined using a redundant indicator technique (work environment, organization communication, leadership, and safety performance) as shown in Figure 3.
Hypothesis Results
We anticipated a positive relationship between safety culture and safety communication. Therefore, hypothesis 1 was supported by the results (β = 0.598, p < 0.001). hypothesis 2 predicated that safety communication would be positively correlated with safety performance. Hypothesis 2 was supported by the results (β = 0.315, p < 0.001). hypothesis 3 predicted a positive relationship between safety culture and safety performance (β = 0.210, p < 0.001), which was supported as shown in Table 5. We used the approach given by Preacher et al. (136), to conduct the mediation analysis. According to their perspective, the indirect effect should be prioritized to achieve mediation; if it is significant, the mediation is achieved; otherwise, there is no mediation (116). Hypothesis 4 predicted that safety communication would mediate the association between safety culture and safety performance as shown in Table 6 of mediation analysis.
Analysis of Mediation Effect
The bootstrapping method was present in this investigation to confirm the mediating impact (137). Previous research had analyzed such indirect impacts, also various researchers have used and advised this study approach (138–140). Furthermore, due to this method's aids in overcoming mediation difficulties and the lack of confidence interval of mediator and outcome variables, bootstrap findings are said to have more accurate probability estimations (141). As a result, there are two reasons why this strategy should be used. The first is that it provides a useful tool for determining the significance and confidence intervals (CI) in a variety of scenarios. When a 95% of confidence interval excludes zero, there is evidence of an indirect impact linking X to Y via a mediator, and the mediation is established. Another argument is that this method does not require a lot of assumptions. As a result, the results acquired using this method are more precise. Based on Table 6, presents the indirect effect data, which reveal that mediating hypotheses was supported.
Discussion
The main purpose of this research was to determine the impacts of safety culture on employee's safety performance via safety communication. Based on, Social Exchange Theory (SET) (142), we examined the effect of safety communication on safety performance after developing a direct hypothesis linking safety culture to employee safety communication. It was proposed that higher levels of safety culture would allow sufficient sources to be allocated to enhancing safety performance by reducing employee accidents and fatalities. As predicted, safety communication mediated the connection between safety culture and safety performance. Safety culture, by reducing accidents, allows workers to invest their saved resources in obtaining and enhancing safety performance. Our research makes a substantial contribution to the field of theory. Firstly, it advances SC theory in the literature on occupational safety (143, 144). By demonstrating that it improves individual safety performance by reducing workplace accidents and fatalities (145). Secondly, the findings highlight the importance of enhancing the overall safety culture rather than focusing on physical safety to encourage employee's safety performance (146). It has been recommended that future research should include both safety cultures measures to enhance our understanding of their roles in workplace safety environment (147, 148), and the findings of our study recommend that future researches may require both safety culture and safety performance measures to enhance our understanding of their safety rules and regulations in the workplace place safety. Safety culture and employee safety performance were found to minimize accidents and fatalities considerably, which is consistent with previous findings (38, 61, 149, 150).
Our research adds to the safety culture literature by demonstrating that a psychosocially safe culture can prevent psychological distress and fatality even in unsafe working environments. Only a few research have looked at this association in risky conditions such as accidents and fatalities (6, 151–153). In addition, most previous research on injuries served as a measure of workplace safety, and little research has been done on how safety communication affects safety performance between workers. Our research addresses a significant gap in the literature on occupational safety and health. Based on the safety performance concept (154, 155) our research found that employees' safety performance and safety culture improves when they are improving with safety communication. Although the assessment was focused on safety leadership, it emphasized the importance of addressing the context requirements of various businesses when it came to workplace safety. Our findings revealed that in high-risk oil and gas businesses, focusing on psychological issues is just as crucial as focusing on physical factors to enhance worker safety performance. It adds to the body of knowledge in the field of occupational safety by emphasizing the significance of taking a more holistic approach. In industries where working circumstances are stressful, such as the oil and gas sector, businesses need to focus on safety cultures variables to enhance employee's safety performance. Further research into strategies to increase safety should take into account both psychosocial and physical safety. The current research examined the impact of safety culture on safety performance as a result of safety communication. The study produced numerous significant additions to the literature on safety culture in general and safety culture in particular. The study's significant theoretical achievements are listed below.
By exploring the importance of safety culture on workplace safety, the current study added to the existing body of knowledge. A theoretically recognized and recommended role (9, 156), however, little empirical work had been done to test the theoretical assumptions. Therefore, the study made a significant addition by not only experimentally proving the relevance of safety culture in safety-critical businesses like the petrochemical oil and gas industry but also establishing that it has a greater impact than safety performance. Previous studies on safety culture have usually labeled it as having a relational meaning or combining it with safety outcome behaviors (157). Because of the lack of clarity surrounding leaders' safety culture actions, many people believe that this form of leadership is useless or even harmful.
As a result, the current work contributes significantly to the literature in this area. The study's findings revealed that the effectiveness of safety culture is influenced by the context of the organization. The findings demonstrated that the impact of safety culture was much bigger than the impact of safety outcomes. The study's findings confirm that the general adoption of effective development should be approached with caution. The study contributes to the body of knowledge and lays the groundwork for future research in this area, examining the effectiveness of management communication in various organizations and cultural settings to see whether the claim of universal applicability has any validity.
The theoretical approaches of this study will serve to expand existing research and aid in the exploration of various organizational cultural situations. The research backs up the theory that learning is a social process in which employees develop behaviors dependent on how rewarding those behaviors are. The current findings show that future research into different leadership styles depending on how acceptable certain proactive behavior are in a national or corporate environment could aid in the advancement of organization theory considerably.
Conclusion
Employee safety performances are influenced by the company's safety culture. This study verifies our assumptions that safety culture has a favorable impact on safety performance through safety communication, based on SET. The outcomes of this research add to the body of the knowledge not just in terms of the direct relationships between safety culture and safety communication, but also in terms of the indirect impact of safety culture and safety performance. This research is the first study to conceptualize and empirically examine the mediating role of safety communication between safety culture and safety performance. Furthermore, research on safety culture in Asian settings, especially in Southeast Asian countries i.e., Malaysia, is limited. This research provides strong guiding's that may be used by practitioners and academicians. These findings are explored in terms of safety interventions and future studies.
The findings have substantial consequences for professionals. Previously, positive safety culture was thought to be essential for maintaining workplace safety environments (45). However, the findings of our study suggest that to increase workplace safety organizations should focus on safety culture in addition to physical safety. Establishing a high level of safety culture at the managerial level is vital not only for psychosocial health but also for enhancing member safety performance. Constructing a work environment where workers feel their managements are committed to their psychological wellbeing, they are not overburdened with work requirements, and they are in a psychosocially safe environment reduces employee accidents, fatalities, and also stress and allows them to be more constructive inability to absorb safety information, participating in safety procedures, and putting them into action.
The safety culture literature (158, 159) explains the practical steps that must be taken to implement safety culture in organizations. Using legislation to ensure the proper application of safety culture in high-risk sectors like in oil and gas can be an efficient strategy to put safety culture rules into implementation (160). Other effective practices include safety culture in management performance appraisals and appointing people to senior roles based on their adherence to safety culture policy (161).
Finally, our findings show that high-risk companies such as oil and gas must prioritize workers' mental health such as accidents and fatalities over competing needs (such as production) to positively affect their safety performance.
The Study Implications
The main objective of this study was to assess the impact of safety culture on the workplace safety performance indicators, i.e., leading and lagging indicators with the mediation of psychosocial hazards. We investigated the impact of the psychosocial hazard on safety performance after developing direct hypotheses concerning safety culture and psychosocial hazard. It was proposed that a high level of safety culture would enable the provision of sufficient resources to contribute toward ensuring good safety performance by reducing employees' psychosocial hazard, based on the social exchange theory (162). As expected, psychosocial hazard mediated the relationship between safety culture and safety performance. It was obvious to find psychosocial hazard's interplay between safety culture and safety performance based on conservation of resources theory (163). In doing so, by reducing psychosocial hazards for the workforce, organizations will allow their workers to invest their saved resources in learning and improving their safety habits.
Our research contributes to the field of theory in a significant way. First, it confirmed that safety culture theory promotes individual safety performance by decreasing the psychosocial hazard (164, 165). In harmony with prior literature, safety culture dimensions such as management commitment, work environment, and involvement of workers collectively and positively impact safety performance (166). Second, the findings emphasize the need to enhance the entire safety culture to promote safety performance among employees (167). Finally, safety performance was improved by reducing their indicators (leading and lagging), which can prevent any accident occurring during the workplace environment (145, 168).
In the current study, four hypotheses were tested, three hypotheses were direct predictors, and the rest utilized safety communication as a mediating relationship between safety culture and safety performance.
Study Limitation
Because of the cross-sectional nature of our study, we must proceed with caution when interpreting our findings. A cross-sectional design was chosen for two reasons. To begin with, gathering data from the petrochemical oil and gas business was extremely challenging due to the process and time required to gain access to the local Malaysian industries. The second issue is Malaysia's lack of support for researchers prevented us from collecting data many times (169). While cross-sectional research can be useful in the early stages of a project (170), a longitudinal layout is essential to prove the causal flow and mediation. Other culture measures (particularly, safety culture) should be included in future studies to further understand their unique and comparative impacts on workplace injuries. A study on psychological wellbeing was undertaken similarly (171). The data for our analysis came from Malaysia's oil and gas industry. As a result, caution should be used when extrapolating these findings to other areas. It must be fascinating to discover if people in other industries and occupations with different levels of job requirements are affected in the same way by unsafe act unsafe conditions (UAUS). Our research did not directly assess employee resources, but it did test a theoretical framework based on the social exchange theory's premise. We suggest that a clear measure of personal resources maintained in a psychosocially and socially safe culture would contribute significantly to the safety literature and assist develop an understanding of SET. A comparative of safety performance in a safety culture “vs.” an unsafe culture could enhance safety theory while also having practical consequences for managers and organizations.
Data Availability Statement
The original contributions presented in the study are included in the article/supplementary materials, further inquiries can be directed to the corresponding author/s.
Author Contributions
All authors involved in the methodology design, data analysis, literature review, manuscript preparation, and have read and agreed to the published version of the manuscript.
Conflict of Interest
The authors declare that the research was conducted in the absence of any commercial or financial relationships that could be construed as a potential conflict of interest.
Publisher's Note
All claims expressed in this article are solely those of the authors and do not necessarily represent those of their affiliated organizations, or those of the publisher, the editors and the reviewers. Any product that may be evaluated in this article, or claim that may be made by its manufacturer, is not guaranteed or endorsed by the publisher.
Acknowledgments
The authors would like to thank Universiti Teknologi PETRONAS & Centre For Graduate Studies (CGS) for supporting this study.
References
1. Langley GJ, Moen RD, Nolan KM, Nolan TW, Norman CL, Provost LP. The Improvement Guide: A Practical Approach to Enhancing Organizational Performance. Massachusetts, MA: John Wiley and Sons (2009).
2. Mariana M, Sahroni TR, Gustiyana T. Fatigue and human errors analysis in petrochemical and oil and gas plant's operation. In: Proceedings of the International Conference on Industrial Engineering and Operations Management, Bandung, Indonesia (2018).
3. Perrons RK. How Innovation and Research and Development Happen in the Upstream Oil and Gas Industry: Insights from a Global Survey. (2018). p. 41–73. doi: 10.1201/b22353-3
4. Commission P. Review of Regulatory Burden On The Upstream Petroleum (oil and gas) Sector. Productivity Commission. Melbourne, NSW: Government of Australia Research Reports (2009).
5. Brondino M, Silva SA, Pasini M. Multilevel approach to organizational and group safety climate and safety performance: co-workers as the missing link. Saf Sci. (2012) 50:1847–56. doi: 10.1016/j.ssci.2012.04.010
6. Feng Y, Teo EAL, Ling FYY, Low SP. Exploring the interactive effects of safety investments, safety culture and project hazard on safety performance: an empirical analysis. Int J Proj Manag. (2014) 32:932–43. doi: 10.1016/j.ijproman.2013.10.016
7. Hon CK, Chan AP, Yam MC. Determining safety climate factors in the repair, maintenance, minor alteration, and addition sector of Hong Kong. J Constr Eng Manag. (2013) 139:519–28. doi: 10.1061/(ASCE)CO.1943-7862.0000588
8. Hsiang C. Safety culture, safety behavior and safety performance in railway companies In: Paper presented at the 9th World Congress on Railway Research. Lille (2011).
9. Kalteh HO, Mortazavi SB, Mohammadi E, Salesi M. The relationship between safety culture and safety climate and safety performance: a systematic review. Int J Occup Saf Ergon. (2021) 27:206–16. doi: 10.1080/10803548.2018.1556976
10. Shuen YS, Wahab SRA. The mediating effect of safety culture on safety communication and human factor accident at the workplace. Asian Soc Sci. (2016) 12:127–141. doi: 10.5539/ass.v12n12p127
11. Noort MC, Reader TW, Shorrock S, Kirwan B. The relationship between national culture and safety culture: implications for international safety culture assessments. J Occup Organ Psychol. (2016) 89:515–38. doi: 10.1111/joop.12139
12. Saleem MS, Isha ASNB, Yusop YM, Awan MI, Naji GMA. The role of psychological capital and work engagement in enhancing construction workers' safety behavior. Front Public Health. 91.
13. Rodríguez-Sánchez AM, Schaufeli W, Salanova M, Cifre E, Sonnenschein M. Enjoyment and absorption: an electronic diary study on daily flow patterns. Work Stress. (2011) 25:75–92. doi: 10.1080/02678373.2011.565619
14. Conchie SM, Moon S, Duncan M. Supervisors' engagement in safety leadership: Factors that help and hinder. Saf Sci. (2013) 51:109–17. doi: 10.1016/j.ssci.2012.05.020
16. Collina DV, Moreau RL. SafeOCS industry safety data: the value proposition for the oil and gas industry In: Paper presented at the Mary K O'Connor Process Safety Symposium Proceedings. Texas, TX (2019).
17. Curlee CK, Brouillard SJ, Marshall ML, Knode TL, Smith SL. Upstream onshore oil and gas fatalities: A review of OSHA's database and strategic direction for reducing fatal incidents. In: Paper presented at the SPE/EPA/DOE Exploration and Production Environmental Conference. (2005). doi: 10.2118/94416-MS
18. Cloughley T, Thomas I. Accident data for the upstream oil and gas industry. In: Paper presented at the SPE Health, Safety and Environment in Oil and Gas Exploration and Production Conference. (1996). doi: 10.2118/35904-MS
19. Aboramadan M, Dahleez KA. The impact of perceived servant leadership traits and safety climate on task performance and risk-taking behavior in times of crisis. Leadersh Health Serv. (2021). doi: 10.1108/LHS-05-2021-0049. [Epub ahead of print].
20. Çakit E, Jan Olak A, Murata A, Karwowski W, Alrehaili O, Marek T. Assessment of the perceived safety culture in the petrochemical industry in Japan: a cross-sectional study. PLoS ONE. (2019) 14:e0226416. doi: 10.1371/journal.pone.0226416
21. Zhou X, Rasool SF, Ma D. The relationship between workplace violence and innovative work behavior: the mediating roles of employee wellbeing. Healthcare. (2020) 8:332. doi: 10.3390/healthcare8030332
22. Davies HW, Gorman-Ng M. Development of a Web-based tool for risk assessment and exposure control planning of silica-producing tasks in the construction sector. Front Public Health. (2020) 8:371. doi: 10.3389/fpubh.0.2020.00371
23. Zhong Z, Zhu L, Young S. Approximation framework of embodied energy of safety: insights and analysis. Energies. (2020) 13:4230. doi: 10.3390/en13164230
24. Cramton CD. The mutual knowledge problem and its consequences for dispersed collaboration. Organ Sci. (2001) 12:346–71. doi: 10.1287/orsc.12.3.346.10098
26. Kim BK, Krams J, Krug E, Leaseburge M, Lemley J, Alkhawaldeh A, et al. Case study analysis of the financial impact of catastrophic safety events. (2012) 25:780–7. doi: 10.1016/j.jlp.2012.05.006
27. Zhan M, Yang W, Zhang F, Luo C, Wu H, Guo P, et al. Experimental investigation on the separation performance for a new oil-water separator. Front Energy Res. (2021) 8:409. doi: 10.3389/fenrg.2020.608586
28. He J, Zhong C, Yao Y, Yan P, Wang Y, Wan Z, et al. The exploration and production test of gas hydrate and its research progress and exploration prospect in the northern South China Sea. Mar Geol Front. (2020) 36:1–14. doi: 10.16028/j.1009-2722.2020.127
29. Fu J, Liu Y, Sun F. Identifying and regulating the environmental risks in the development and utilization of natural gas as a low-carbon energy source. Front Energy Res. (2021) 9:28. doi: 10.3389/fenrg.2021.638105
30. Mosly I, Makki AA. Safety climate perceptions in the construction industry of Saudi Arabia: the current situation. Int J Environ Res Public Health. (2020) 17:6717. doi: 10.3390/ijerph17186717
31. Al-Samhan M, Al-Fadhli J, Al-Otaibi AM, Al-Attar F, Bouresli R, Rana MS. Prospects of refinery switching from conventional to integrated: an opportunity for sustainable investment in the petrochemical industry. Fuel. (2022) 310:122161. doi: 10.1016/j.fuel.2021.122161
32. Mailan Arachchige Don RK, Hong S-C. Sri Lankan migrant worker perceptions of workplace hazard and safety awareness: case of the manufacturing industry in Korea. Int J Occup Saf Ergon. (2021) 1–7. doi: 10.1080/10803548.2021.1992158
33. Rahim KA, Liwan A. Oil and gas trends and implications in Malaysia. Energy Policy. (2012) 50:262–71. doi: 10.1016/j.enpol.2012.07.013
37. Yovi EY, Abbas D, Takahashi T. Safety climate and risk perception of forestry workers: a case study of motor-manual tree felling in Indonesia. Int J Occup Safety Ergon. (2021) 1–9. doi: 10.1080/10803548.2021.1986306
38. Al-Bayati AJ. Impact of construction safety culture and construction safety climate on safety behavior and safety motivation. Safety. (2021) 7:41. doi: 10.3390/safety7020041
39. Naji GMA, Isha ASN, Mohyaldinn ME, Leka S, Saleem MS, Rahman SMNBSA, et al. Impact of safety culture on safety performance; mediating role of psychosocial hazard: an integrated modelling approach. Int J Environ Res Public Health. (2021) 18:8568. doi: 10.3390/ijerph18168568
40. Waterson P. Patient safety culture and organisational behaviour. Patient Saf Culture. (2018). p. 70–93. doi: 10.1201/9781315599717
41. Zwetsloot G, Leka S. Corporate culture, health, and well-being. In: Leka S, Houdmondt J, editors. A Text Book for Occupational Health Psychology. Chicester: Wiley-Blackwell (2010). 250–68.
42. Leka S, Van Wassenhove W, Jain A. Is psychosocial risk prevention possible? deconstructing common presumptions. Saf Sci. (2015) 71:61–7. doi: 10.1016/j.ssci.2014.03.014
43. Verdoes JC, Punt PJ, Stouthamer AH, van den Hondel CAJG. The effect of multiple copies of the upstream region on expression of the aspergillus niger glucoamylase-encoding gene. Gene. (1994) 145:179–87. doi: 10.1016/0378-1119(94)90003-5
44. Binz C, Razavian NB, Kiparsky MJ. Of dreamliners and drinking water: developing risk regulation and a safety culture for direct potable reuse. Water Resour Manag. (2018) 32:511–25. doi: 10.1007/s11269-017-1824-1
45. He C, Jia G, McCabe B, Sun J. Relationship between leader–member exchange and construction worker safety behavior: the mediating role of communication competence. Int J Occup Saf Ergon. (2021) 27:371–83. doi: 10.1080/10803548.2019.1579484
46. Kao CS, Lai WH, Chuang TF, Lee JC. Safety culture factors, group differences, and risk perception in five petrochemical plants. Process Saf Prog. (2008) 27:145–52. doi: 10.1002/prs.10246
47. Kirwan M, Matthews A, Scott PA. The impact of the work environment of nurses on patient safety outcomes: a multi-level modelling approach. Int J Nurs Stud. (2013) 50:253–63. doi: 10.1016/j.ijnurstu.2012.08.020
48. Kodarlikar M, Umale V. A Healthy Workplace Environment: Impact on Employee and Organizational Performance (2020).
49. Rasool SF, Wang M, Tang M, Saeed A, Iqbal J. How toxic workplace environment effects the employee engagement: the mediating role of organizational support and employee wellbeing. Int J Environ Res Public Health. (2021) 18:2294. doi: 10.3390/ijerph18052294
50. Barbour JB, Gill R, Barge JKJCT. Organizational communication design logics: a theory of communicative intervention and collective communication design. Commun Theory. (2018) 28:332–53. doi: 10.1093/ct/qtx005
51. Stebbins P, Lees D, Ham D, Karabitsios J. Supportive leadership: Improving organisational health and preventing burnout in pastoral care managers and staff. Aust J Rehabil Couns. (2010) 16:99–118. doi: 10.1375/jrc.16.2.99
52. Wang B, Rasool SF, Zhao Y, Samma M, Iqbal J. Investigating the nexus between critical success factors, despotic leadership, and success of renewable energy projects. Environ Sci Pollut Res. (2021) 29:10388–98. doi: 10.1007/s11356-021-16441-6
53. Zhou X, Rasool SF, Yang J, Asghar MZ. Exploring the relationship between despotic leadership and job satisfaction: the role of self efficacy and leader–member exchange. Int J Environ Res Public Health. (2021) 18:5307. doi: 10.3390/ijerph18105307
54. Kucherov V, McDonald A, Ivanov I, Rose J. The application of the accelerative learning cycle to the design and delivery of safety leadership programs for personnel of onshore and offshore upstream oil assets. In: Paper presented at the SPE Annual Caspian Technical Conference and Exhibition Baku (2015).
55. Ajmal M, Isha ASN, Nordin SM, Kanwal N, Al-Mekhlafi A-BA, Naji GMA. A conceptual framework for the determinants of organizational agility: does safety commitment matters? Solid State Technol. (2020) 63:4112–9.
56. Naji GMA, Isha AN, Abd SMNBS. The role of HR strategy on safety culture and psychological stress among employees in the upstream oil and gas companies: a conceptual review. Solid State Technol. (2020) 63:9118–28.
57. Geordy R, Sridhar M, Sudhakumar J. Effect of communication patterns in safety performance of construction workers. In: Paper Presented at the National Conference on Structural Engineering and Construction Management. Cham (2020). doi: 10.1007/978-3-030-55115-5_72
58. Ajmal M, Isha ASN, Nordin SM, Sabir AA, Munir A, Al-Mekhlafi A-BA, et al. Safety management paradigms: COVID-19 employee well-being impact on occupational health and safety performance. J Hunan Univ Nat Sci. (2021) 48:128–142.
59. Penkey SP, Siddiqui NA. A Review on Accident Pyramid and its Empirical Interpretation in Oil and Gas Industry (Upstream). Pasel (2015). p. 1–3.
60. Coday BD, Almaraz N, Cath TY. Forward osmosis desalination of oil and gas wastewater: Impacts of membrane selection and operating conditions on process performance. J Membr Sci. (2015) 488:40–55. doi: 10.1016/j.memsci.2015.03.059
61. Maliha MN, Abu Aisheh YI, Tayeh BA, Almalki A. Safety barriers identification, classification, and ways to improve safety performance in the architecture, engineering, and construction (AEC) industry: review study. Sustainability. (2021) 13:3316. doi: 10.3390/su13063316
62. Ajmal M, Isha ASN, Nordin SM, Rasheed S, Al?Mekhlafi ABA, Naji GMA. Safety management and safety outcomes in oil and gas industry in Malaysia: Safety compliance as a mediator. Process Safety Prog. e12345. doi: 10.1002/prs.12345
63. Isha ASN. Occupational Health And Safety Practices In The Petrochemical Industries of Malaysia. Nottingham, UK: University of Nottingham (2012).
64. Shaikh SA. Impact of internal marketing and human resource management to foster customer oriented behavior among employees: a study on mega retail stores in Karachi. NICE Res J. (2018) 183–199. doi: 10.51239/nrjss.v0i0.11
66. Keffane S. Communication's role in safety management and performance of the road safety practices. Jordan J Civ Eng. (2015) 9:79–94. doi: 10.1260/2046-0430.3.1.79
67. Wadsworth E, Smith A. Safety culture, advice and performance. Policy Pract Health Saf. (2009) 7:5–31. doi: 10.1080/14774003.2009.11667726
69. Alcantara J, Whetten A, Alcantara J. Towards a safety culture in chiropractic: The use of the safety, communication, Operational Reliability, and engagement (SCORE) questionnaire. Complement Ther Clin Pract. (2021) 42:101266. doi: 10.1016/j.ctcp.2020.101266
70. Paolucci A, Sangiorgi S, Mariani MG. Non-technical skills in social networks: the spread of safety communication and teamwork in a warehouse. Int J Environ Res Public Health. (2021) 18:467. doi: 10.3390/ijerph18020467
71. Mambwe M, Mwanaumo EM, Thwala WD, Aigbavboa CO. Evaluating occupational health and safety management strategy success factors for small-scale contractors in Zambia. Sustainability. (2021) 13:4696. doi: 10.3390/su13094696
72. Rasool SF, Samma M, Wang M, Zhao Y, Zhang Y. How human resource management practices translate into sustainable organizational performance: the mediating role of product, process and knowledge innovation. Psychol Res Behav Manag. (2019) 12:1009. doi: 10.2147/PRBM.S204662
73. Cigularov KP, Chen PY, Rosecrance J. The effects of error management climate and safety communication on safety: a multi-level study. Accid Anal Prev. (2010) 42:1498–506. doi: 10.1016/j.aap.2010.01.003
74. Kim NK, Rahim NFA, Iranmanesh M, Foroughi B. The role of the safety climate in the successful implementation of safety management systems. Saf Sci. (2019) 118:48–56. doi: 10.1016/j.ssci.2019.05.008
75. Pinto A, Nunes IL, Ribeiro RA. Occupational risk assessment in construction industry–Overview and reflection. Saf Sci. (2011) 49:616–24. doi: 10.1016/j.ssci.2011.01.003
76. Lyndon A, Johnson MC, Bingham D, Napolitano PG, Joseph G, Maxfield DG, et al. Transforming communication and safety culture in intrapartum care: a multi-organization blueprint. J Obstet Gynecol Neonatal Nurs. (2015) 44:341–9. doi: 10.1111/1552-6909.12575
77. Vecchio-Sadus AM. Enhancing safety culture through effective communication. Saf Sci Monit. (2007) 11:1–10.
78. Johnsen S, Bakken T, Transeth A, Holmstrøm S, Merz M, Grøtli E, et al. Safety and security of drones in the oil and gas industry.In: Paper presented at the Proceedings of the 30th European Safety and Reliability Conference and the 15th Probabilistic Safety Assessment and Management Conference, Edited by Piero Baraldi, Francesco Di Maio and Enrico Zio, ESREL2020-PSAM15. Singapore: Research Publishing (2020). doi: 10.3850/978-981-14-8593-0_3924-cd
79. Boadu EF, Wang CC, Sunindijo RY. Characteristics of the construction industry in developing countries and its implications for health and safety: an exploratory study in Ghana. Int J Environ Res Public Health. (2020) 17:4110. doi: 10.3390/ijerph17114110
80. Abuashour AMB, Hassan Z. A Conceptual framework for enhancing safety performance by impact cooperation facilitation, safety communication and work environment: jordanian hospitals. Sains Humanika. (2019) 11:2. doi: 10.11113/sh.v11n2-2.1659
81. Haas EJ, Yorio PL. Behavioral safety compliance in an interdependent mining environment: supervisor communication, procedural justice and the mediating role of coworker communication. Int J Occup Saf Ergon. (2021) 1–13. doi: 10.1080/10803548.2021.1896140
82. Lu H, Huang K, Azimi M, Guo LJIA. Blockchain technology in the oil and gas industry: a review of applications, opportunities, challenges, and risks. (2019) 7:41426–44. doi: 10.1109/ACCESS.2019.2907695
83. Hofmann DA, Morgeson FP. Safety-related behavior as a social exchange: the role of perceived organizational support and leader–member exchange. J Appl Psychol. (1999) 84:286. doi: 10.1037/0021-9010.84.2.286
84. Hofmann DA, Morgeson FP, Gerras SJ. Climate as a moderator of the relationship between leader-member exchange and content specific citizenship: safety climate as an exemplar. J Appl Psychol. (2003) 88:170. doi: 10.1037/0021-9010.88.1.170
85. Suursalu S. Predictive Maintenance Using Machine Learning Methods In Petrochemical Refineries (2017).
86. Cox S, Cheyne A. Assessing safety culture in offshore environments. Saf Sci. (2000) 34:111–29. doi: 10.1016/S0925-7535(00)00009-6
87. Lu C-S, Yang C-S. Safety leadership and safety behavior in container terminal operations. Saf Sci. (2010) 48:123–34. doi: 10.1016/j.ssci.2009.05.003
88. Vinodkumar M, Bhasi M. Safety management practices and safety behaviour: Assessing the mediating role of safety knowledge and motivation. Accid Anal Prev. (2010) 42:2082–93. doi: 10.1016/j.aap.2010.06.021
89. Wu T-C, Chen C-H, Li C-C. A correlation among safety leadership, safety climate and safety performance. J Loss Prev Process Ind. (2008) 21:307–18. doi: 10.1016/j.jlp.2007.11.001
90. Ali F, Rasoolimanesh SM, Sarstedt M, Ringle CM, Ryu K. An assessment of the use of partial least squares structural equation modeling (PLS-SEM) in hospitality research. Int J Contemp Hosp Manag. (2018) 30:514–38. doi: 10.1108/IJCHM-10-2016-0568
91. Astrachan CB, Patel VK, Wanzenried G. A comparative study of CB-SEM and PLS-SEM for theory development in family firm research. J Fam Bus Strategy. (2014) 5:116–28. doi: 10.1016/j.jfbs.2013.12.002
92. Savic M, Ogeil RP, Sechtig MJ, Lee-Tobin P, Ferguson N, Lubman DI. How do nurses cope with shift work? a qualitative analysis of open-ended responses from a survey of nurses. Int J Environ Res Public Health. (2019) 16:3821. doi: 10.3390/ijerph16203821
93. Lei PW, Wu Q. Introduction to structural equation modeling: Issues and practical considerations. Edu Meas. (2007) 26:33–43. doi: 10.1111/j.1745-3992.2007.00099.x
94. Williams LJ, Vandenberg RJ, Edwards JR. 12 structural equation modeling in management research: a guide for improved analysis. Acad Manag Ann. (2009) 3:543–604. doi: 10.5465/19416520903065683
95. Aibinu AA, Al-Lawati AM. Using PLS-SEM technique to model construction organizations' willingness to participate in e-bidding. Autom Constr. (2010) 19:714–24. doi: 10.1016/j.autcon.2010.02.016
96. Kecklund L, Ingre M, Kecklund G, Söderström M, Åkerstedt T, Lindberg E, et al. The TRAIN-project: Railway safety and the train driver information environment and work situation-a summary of the main results. In: Paper presented at Signalling Safety 2001, (2001).
97. Reimer B, D'Ambrosio LA, Coughlin JF, Fried R, Biederman J. Task-induced fatigue and collisions in adult drivers with attention deficit hyperactivity disorder. Traffic Inj Prev. (2007) 8:290–9. doi: 10.1080/15389580701257842
98. Ghaleb EA, Dominic P, Fati SM, Muneer A, Ali RF. The assessment of big data adoption readiness with a technology–organization–environment framework: a perspective towards healthcare employees. Sustainability. (2021) 13:8379. doi: 10.3390/su13158379
99. MacKinnon DP. Integrating mediators and moderators in research design. Res Soc Work Pract. (2011) 21:675–81. doi: 10.1177/1049731511414148
100. Samma M, Zhao Y, Rasool SF, Han X, Ali S. Exploring the relationship between innovative work behavior, job anxiety, workplace ostracism, and workplace incivility: empirical evidence from small and medium sized enterprises (SMEs). Healthcare. (2020) 8:508. doi: 10.3390/healthcare8040508
101. Hamidun R, Hoong AW, Roslan A, Shabadin A, Jamil H. Characteristics of heavy goods vehicles (HGV) accidents in Malaysia. In: Paper Presented at the IOP Conference Series: Materials Science and Engineering. (2019). doi: 10.1088/1757-899X/512/1/012021
102. Bergh LIV, Leka S, Zwetsloot GI. Tailoring psychosocial risk assessment in the oil and gas industry by exploring specific and common psychosocial risks. Saf Health Work. (2018) 9:63–70. doi: 10.1016/j.shaw.2017.05.001
103. Saleem MS, Isha ASN, Mohd Yusop Y, Awan MI, Naji GMA. Agility and safety performance among nurses: the mediating role of mindful organizing. Nursing Rep. (2021) 11:666–79. doi: 10.3390/nursrep11030063
104. Vohs KD, Baumeister RF. Handbook of Self-Regulation: Research, Theory, and Applications. 2nd ed. New York, NY: Guilford Press (2011).
105. Saleem MS, Isha ASN, Yusop YM, Awan MI, Naji GMA. The whole nine yards of safety climate research. J Hunan Univ Nat Sci. (2021) 48:486–503.
106. Kim H-Y. Statistical notes for clinical researchers: assessing normal distribution (2) using skewness and kurtosis. Restor Dent Endod. (2013) 38:52–4. doi: 10.5395/rde.2013.38.1.52
107. Ringle CM, Wende S, Becker J-M. SmartPLS 3. SmartPLS GmbH, Boenningstedt. J Serv Sci Manag. (2015) 10. Available online at: http://www.smartpls.com
108. Anderson JC, Gerbing DW. Structural equation modeling in practice: a review and recommended two-step approach. Psychol Bull. (1988) 103:411. doi: 10.1037/0033-2909.103.3.411
109. Faul F, Erdfelder E, Buchner A, Lang A-G. G* Power Version 3.1. 7 [Computer Software]. Uiversität Kiel, Germany (2013).
110. Reinartz W, Haenlein M, Henseler J. An empirical comparison of the efficacy of covariance-based and variance-based SEM. Int J Res Market. (2009) 26:332–44. doi: 10.1016/j.ijresmar.2009.08.001
111. Podsakoff PM, MacKenzie SB, Lee J-Y, Podsakoff NP. Common method biases in behavioral research: a critical review of the literature and recommended remedies. J Appl Psychol. (2003) 88:879. doi: 10.1037/0021-9010.88.5.879
112. Audenaert M, Decramer A, Lange T, Vanderstraeten A. Setting high expectations is not enough: linkages between expectation climate strength, trust, and employee performance. Int J Manpower. (2016) 37:1024–41. doi: 10.1108/IJM-12-2015-0201
113. Podsakoff PM, Organ DW. Self-reports in organizational research: problems and prospects. J Manage. (1986) 12:531–44. doi: 10.1177/014920638601200408
114. Bagozzi RP, Yi Y, Phillips LW. Assessing construct validity in organizational research. Adm Sci Quart. (1991) 363:421–58. doi: 10.2307/2393203
115. Hair JF, Hult GTM, Ringle CM, Sarstedt M. A Primer On Partial Least Squares Structural Equation Modeling (PLS-SEM). Sage Publications (2021). doi: 10.1007/978-3-030-80519-7
116. Ramayah T, Cheah J, Chuah F, Ting H, Memon MA. Partial Least Squares Structural Equation Modeling (PLS-SEM) Using SmartPLS 3.0. Kuala Lumpur: Pearson (2018).
117. Kock N, Lynn G. Lateral collinearity and misleading results in variance-based SEM: An illustration and recommendations. J Assoc inf Syst. (2012) 13:546–80. doi: 10.17705/1jais.00302
118. Urbach N, Ahlemann F. Structural equation modeling in information systems research using partial least squares. J Inf Technol Theory Appl. (2010) 11:5–40.
119. Kock N. Advanced mediating effects tests, multi-group analyses, and measurement model assessments in PLS-based SEM. Int J e-Collab. (2014) 10:1–13. doi: 10.4018/ijec.2014010101
120. Alarcón D, Sánchez JA, De Olavide U. Assessing convergent and discriminant validity in the ADHD-R IV rating scale: User-written commands for Average Variance Extracted (AVE), Composite Reliability (CR), and Heterotrait-Monotrait ratio of correlations (HTMT). In: Paper Presented At The Spanish STATA Meeting. Seville (2015).
121. Chin WW. How To Write Up And Report PLS Analyses. In Handbook of Partial Least Squares. Springer (2010). p. 655–90. doi: 10.1007/978-3-540-32827-8_29
122. Henseler J, Ringle CM, Sarstedt M. A new criterion for assessing discriminant validity in variance-based structural equation modeling. J Acad Market Sci. (2015) 43:115–35. doi: 10.1007/s11747-014-0403-8
123. Aboelmaged M. The drivers of sustainable manufacturing practices in Egyptian SMEs and their impact on competitive capabilities: a PLS-SEM model. J Clean Prod. (2018) 175:207–21. doi: 10.1016/j.jclepro.2017.12.053
124. Mikalef P, Pateli A. Information technology-enabled dynamic capabilities and their indirect effect on competitive performance: findings from PLS-SEM and fsQCA. J Bus Res. (2017) 70:1–16. doi: 10.1016/j.jbusres.2016.09.004
125. Zeng F, Huang W-C, Hueng J. On Chinese government's stock market rescue efforts in 2015. Modern Econ. (2016) 7:411–8. doi: 10.4236/me.2016.74045
126. Barger LK, Cade BE, Ayas NT, Cronin JW, Rosner B, Speizer FE, et al. Extended work shifts and the risk of motor vehicle crashes among interns. N Eng J Med. (2005) 352:125–34. doi: 10.1056/NEJMoa041401
127. Love PE, Davis PR, Chevis R, Edwards DJ. Risk/reward compensation model for civil engineering infrastructure alliance projects. J Constr Eng Manag. (2011) 137:127–36. doi: 10.1061/(ASCE)CO.1943-7862.0000263
129. Fornell C, Larcker DF. Evaluating structural equation models with unobservable variables and measurement error. J Market Res. (1981) 18:39–50. doi: 10.1177/002224378101800104
130. Fornell C, Larcker DF. Structural Equation Models With Unobservable Variables And Measurement Error: Algebra And Statistics. Los Angeles, CA: Sage Publications Sage CA (1981). doi: 10.2307/3150980
131. Henseler J, Dijkstra TK, Sarstedt M, Ringle CM, Diamantopoulos A, Straub DW, et al. Common beliefs and reality about PLS: comments on rönkkö and evermann (2013). Organ Res Methods. (2014) 17:182–209. doi: 10.1177/1094428114526928
132. Kaufmann L, Gaeckler J. A structured review of partial least squares in supply chain management research. J Purchas Supply Manage. (2015) 21:259–72. doi: 10.1016/j.pursup.2015.04.005
133. Sullivan GM, Feinn R. Using effect size—or why the P value is not enough. J Grad Med Educ. (2012) 4:279–82. doi: 10.4300/JGME-D-12-00156.1
134. Geisser S. The predictive sample reuse method with applications. J Am Stat Assoc. (1975) 70:320–8. doi: 10.1080/01621459.1975.10479865
135. Cohen J. Statistical Power Analysis For The Social Sciences. 2nd ed. Hillsdale, NJ: Erlbaum (1988).
136. Preacher KJ, Rucker DD, Hayes AF. Addressing moderated mediation hypotheses: theory, methods, and prescriptions. Multivariate Behav Res. (2007) 42:185–227. doi: 10.1080/00273170701341316
137. Mooney CZ, Mooney CF, Mooney CL, Duval RD, Duvall R. Bootstrapping: A Nonparametric Approach To Statistical Inference. Sage (1993). doi: 10.4135/9781412983532
138. Al-Mekhlafi A-BA, Isha ASN, Naji GMA. The relationship between fatigue and driving performance: a review and directions for future research. J Crit Rev. (2020) 7:134–41. doi: 10.31838/jcr.07.14.24
139. Cheung GW, Lau RS. Testing mediation and suppression effects of latent variables: Bootstrapping with structural equation models. Organ Res Methods. (2008) 11:296–325. doi: 10.1177/1094428107300343
140. Preacher KJ, Hayes AF. SPSS and SAS procedures for estimating indirect effects in simple mediation models. Behav Res Method Instrum Computers. (2004) 36:717–31. doi: 10.3758/BF03206553
141. Ortiz C, Castro JJ, Alarcón A, Soler M, Anera RG. Quantifying age-related differences in visual-discrimination capacity: drivers with and without visual impairment. Appl Ergon. (2013) 44:523–31. doi: 10.1016/j.apergo.2012.11.006
142. Cropanzano R, Mitchell MS. Social exchange theory: an interdisciplinary review. J Manage. (2005) 31:874–900. doi: 10.1177/0149206305279602
143. Kortum E, Leka S, Cox T. Psychosocial risks and work-related stress in developing countries: health impact, priorities, barriers and solutions. Int J Occup Med Environ Health. (2010) 23:225–38. doi: 10.2478/v10001-010-0024-5
144. Wagner A, Schöne L, Rieger MA. Determinants of occupational safety culture in hospitals and other workplaces—results from an integrative literature review. Int J Environ Res Public Health. (2020) 17:6588. doi: 10.3390/ijerph17186588
145. Naji GMA, Isha ASN, Al-Mekhlafi A-BA, Sharafaddin O, Ajmal M. Implementation of leading and lagging indicators to improve safety performance in the upstream oil and gas industry. J Critic Rev. (2020) 7:265–9. doi: 10.31838/jcr.07.14.45
146. Naji GMA, Isha ASN, Alzoraiki M, Al-Mekhlafi A-BA, Sharafaddin O, Saleem MS. Impact of safety culture and psychosocial hazard on safety performance among upstream employees in malaysia at oil and gas industry. Solid State Technol. (2020) 63:4120–6.
147. Leka S, Jain A, Iavicoli S, Vartia M, Ertel M. The role of policy for the management of psychosocial risks at the workplace in the European Union. Saf Sci. (2011) 49:558–64. doi: 10.1016/j.ssci.2010.02.002
148. Tetzlaff EJ, Goggins KA, Pegoraro AL, Dorman SC, Pakalnis V, Eger TR. Safety culture: a retrospective analysis of occupational health and safety mining reports. Saf Health Work. (2021) 12:201–8. doi: 10.1016/j.shaw.2020.12.001
149. Arezes PM, Miguel AS. The role of safety culture in safety performance measurement. Meas Bus Excell. (2003) 7:20–8. doi: 10.1108/13683040310509287
150. Çakit E, Karwowski W, Murata A, Olak AJ. Application of structural equation modeling (SEM) and an adaptive neuro-fuzzy inference system (ANFIS) for assessment of safety culture: an integrated modeling approach. Safety. (2020) 6:14. doi: 10.3390/safety6010014
151. Mirza MZ, Isha ASN, Memon MA, Azeem S, Zahid M. Psychosocial safety climate, safety compliance and safety participation: The mediating role of psychological distress. J Manag Organ. (2019) 1–16. doi: 10.1017/jmo.2019.35
152. Rasool SF, Wang M, Zhang Y, Samma M. Sustainable work performance: the roles of workplace violence and occupational stress. Int J Environ Res Public Health. (2020) 17:912. doi: 10.3390/ijerph17030912
153. Zadow A, Dollard MF. Psychosocial safety climate. In: Clarke S, Probst TM, Guldenmund F, Passmore J, editors. The Wiley Blackwell Handbook of the Psychology of Occupational Safety and Workplace Health. 1st ed. John Wiley & Sons Ltd.
154. Stemn E, Bofinger C, Cliff D, Hassall ME. Examining the relationship between safety culture maturity and safety performance of the mining industry. Saf Sci. (2019) 113:345–55. doi: 10.1016/j.ssci.2018.12.008
155. Yang C-C, Wang Y-S, Chang S-T, Guo S-E, Huang M-F. A study on the leadership behavior, safety culture, and safety performance of the healthcare industry. World Acad Sci Eng Technol. (2009) 53:1148–55.
156. Weaver MD, Wang HE, Fairbanks RJ, Patterson D. The association between EMS workplace safety culture and safety outcomes. Prehosp Emerg Care. (2012) 16:43–52. doi: 10.3109/10903127.2011.614048
157. Tong R, Yang X, Parker T, Zhang B, Wang Q. Exploration of relationships between safety performance and unsafe behavior in the Chinese oil industry. J Loss Prev Proc Indus. (2020) 66:104167. doi: 10.1016/j.jlp.2020.104167
158. Cooper MD. Towards a model of safety culture. Saf Sci. (2000) 36:111–36. doi: 10.1016/S0925-7535(00)00035-7
160. Petitta L, Probst TM, Barbaranelli C, Ghezzi V. Disentangling the roles of safety climate and safety culture: Multi-level effects on the relationship between supervisor enforcement and safety compliance. Accid Anal Prev. (2017) 99:77–89. doi: 10.1016/j.aap.2016.11.012
161. Selvapatt N, Ward T, Bailey H, Bennett H, Thorne C, See L-M, et al. Is antenatal screening for hepatitis C virus cost-effective? A decade's experience at a London centre. J Hepatol. (2015) 63:797–804. doi: 10.1016/j.jhep.2015.05.015
163. Hobfoll SE. Conservation of resources: a new attempt at conceptualizing stress. Am Psychol. (1989) 44:513. doi: 10.1037/0003-066X.44.3.513
164. Guldenmund FW. The nature of safety culture: a review of theory and research. Saf Sci. (2000) 34:215–57. doi: 10.1016/S0925-7535(00)00014-X
165. Zadow AJ, Dollard MF, Mclinton SS, Lawrence P, Tuckey MR. Psychosocial safety climate, emotional exhaustion, and work injuries in healthcare workplaces. Stress Health. (2017) 33:558–69. doi: 10.1002/smi.2740
166. Tang DKH, Leiliabadi F, Olugu EU. Factors affecting safety of processes in the Malaysian oil and gas industry. Saf Sci. (2017) 92:44–52. doi: 10.1016/j.ssci.2016.09.017
167. Zohar D. Thirty years of safety climate research: Reflections and future directions. Accid Anal Prev. (2010) 42:1517–22. doi: 10.1016/j.aap.2009.12.019
168. Yang R. Safety in Construction: Connecting Safety Climate, Safety Performance, and Leading Indicators. University of Toronto (2021).
169. Ali H, Abdullah NAC, Subramaniam C. Management practice in safety culture and its influence on workplace injury: an industrial study in Malaysia. Disaster Prev Manag. (2009) 18:470. doi: 10.1108/09653560911003660
170. Barling J, Loughlin C, Kelloway EK. Development and test of a model linking safety-specific transformational leadership and occupational safety. J Appl Psychol. (2002) 87:488. doi: 10.1037/0021-9010.87.3.488
171. Idris MA, Dollard MF, Coward J, Dormann C. Psychosocial safety climate: Conceptual distinctiveness and effect on job demands and worker psychological health. Saf Sci. (2012) 50:19–28. doi: 10.1016/j.ssci.2011.06.005
Appendix
Keywords: safety culture, safety communication, safety performance, petrochemical sector, Malaysia
Citation: Naji GMA, Isha ASN, Alazzani A, Saleem MS and Alzoraiki M (2022) Assessing the Mediating Role of Safety Communication Between Safety Culture and Employees Safety Performance. Front. Public Health 10:840281. doi: 10.3389/fpubh.2022.840281
Received: 20 December 2021; Accepted: 31 January 2022;
Published: 10 March 2022.
Edited by:
Alberto Modenese, University of Modena and Reggio Emilia, ItalyReviewed by:
Erman Çakıţ, Gazi University, TurkeyMohammed Aboramadan, University of Insubria, Italy
Madeeha Samma, Shanghai University, China
Samma Faiz Rasool, Zhejiang University of Technology, China
Copyright © 2022 Naji, Isha, Alazzani, Saleem and Alzoraiki. This is an open-access article distributed under the terms of the Creative Commons Attribution License (CC BY). The use, distribution or reproduction in other forums is permitted, provided the original author(s) and the copyright owner(s) are credited and that the original publication in this journal is cited, in accordance with accepted academic practice. No use, distribution or reproduction is permitted which does not comply with these terms.
*Correspondence: Gehad Mohammed Ahmed Naji, Z2VoYWRuYWppLnV0cEBnbWFpbC5jb20=