- 1Department of Mathematical Sciences, College of Science, Princess Nourah bint Abdulrahman University, Riyadh, Saudi Arabia
- 2College of Engineering, Northern Border University (NBU), Arar, Saudi Arabia
- 3Department of Physics, Faculty of Sciences, University of Monastir, Monastir, Tunisia
- 4Faculty of Science, Department of Mathematics, Zagazig University, Zagazig, Egypt
- 5Faculty of Science, Department of Mathematics, Helwan University, Cairo, Egypt
- 6Arab Academy for Science, Technology and Maritime Transport, Alexandria, Egypt
- 7Faculty of Computer Science, Future University, New Cairo, Cairo, Egypt
In the present work, the semiconductor material is used to study the moisture diffusivity when a modified Moore–Gibson–Thompson (MGT) model is taken into account. The influence of moisture concentration is included in the governing equations throughout the photothermal transfer process. Based on the dissimilar relaxation durations of the coupled optoelectronic and thermoelastic waves, the MGT model is used to investigate the issue at hand. The method of the Laplace transform is used to obtain analytical solutions for the physical quantities, constitutive relationships, elastic waves, carrier density, heat equation conduction, and moisture diffusivity for the thermo-elastic medium. To extract the primary physical quantities in the space–time domain, the boundary conditions, temperature, plasma, displacement, and mechanical stress are inverted numerically using the Laplace transform. The effect of the new parameter like the reference moisture parameter with various values is discussed graphically on the primary physical quantities. The comparison between silicon and germanium is taken into account to achieve numerical computations.
1 Introduction
The stress field is responsible for producing the temperature field, and the stress field modulates the strain and stress fields. Force loads and thermal stresses are common sources of damage to structural parts. A crack may occur if the strains are great enough or if the strains combine with mechanical stresses from external loads. Recently, many scientists have been concerned with semiconductor materials; this is due to their many modern applications, such as aircraft electronics and sensors. In semiconductors, some materials have unique properties like highly conductive materials such as copper. In semiconductors, the most important effect property in modern industries is the photothermal (PT) excitation process that happens when temperature increases to release electrons to the surface of the material, which makes the material a good conductor of electricity. The process of electrons gaining energy because of increasing temperature is called electronic deformation (plasma), and this process causes an electric current. Light absorbed by the material causes a local increase in temperature and pressure, and a proportional increase in volume, according to the PT effect.
Biot [1] was the first to highlight the solution for the coupled thermo-elasticity. The Fourier heat conduction theory is considered the basis for the conventional dynamic (CD) theory of the thermo-elasticity theory. The CD assumes that wave propagation can travel at an unlimited speed because of the parabolic form found in the governing equations, and this theory was unacceptable for the physical experiments. Because of this inconsistency, Lord and Shulman (LS) [2] introduced a new model by putting one relaxation time in the equations, which makes the system of equations take the hyperbolic form, making the thermal waves propagate at a finite speed. Green–Lindsay (GL) [3] modified a new model of thermoelasticity containing two relaxation times, which makes many researchers utilize this model to conduct numerous studies. Many authors [4, 5] have used the GL theory known as the generalized thermoelasticity theory. After adding the relaxation factor to the suggested heat equation to Green–Naghdi III (GN-III) by Abouelregal et al. [6], many authors tend to utilize the modified thermoelastic theory in the context of the MGT equation because of its importance in many applications and also it was derived using a third-order differential equation. Othman et al. [7] studied the transient disturbance according to the moving heat source in the generalized magneto-thermoelasticity theory. Quintanilla [8, 9] has developed thermoelastic MGT heat conduction. Marin et al. [10–13] analyzed the thermoelasticity theory in the context of the MGT model’s starting values, as set by the dipolar elastic property. Recent evidence [14] shows that the MGT equation may be used in a wide range of contexts. Using a thermoelastic semiconductor material, Lotfy et al. [15, 16] employed the MGT model to prove the stability of their analytical solutions.
We argue that the fundamental ideas behind heat transmission and moisture transport are similar. Mechanically induced stresses may have significant effects on how heat and moisture are distributed. Understanding the relationship between mechanical deformation and diffusion caused by temperature and moisture is so crucial. There are a wide variety of engineering problems where the correlation between humidity, temperature, and deformation may be seen. When a solid is subjected to both moisture and heat, a phenomenon known as hygro-thermoelasticity takes place. Szekeres [17, 18] published research discussing moisture’s impact on conventional heat transmission. More so than mechanical loadings, Gasch et al. [19] discussed temperature and moisture fluctuations. Szekeres and Engelbrecht [20] established a fundamental analogy between heat and moisture before proceeding with creating equations governing coupled hygro-thermoelasticity.
Semiconducting materials found widespread use in contemporary engineering because of technological advancements. There is both theoretical and practical usefulness in learning more about how waves travel through a semiconducting material. Unfortunately, the author was unable to find any previous documentation of the wave propagation issue in semiconducting media during a PT process. The fundamental principle shared by all PT techniques is the detection of short-lived thermal waves generated in the sample upon its absorption of modulated light. When an appropriate transducer picks up these pressure fluctuations in the surrounding gaseous medium, we obtain the photoacoustic (PA) signal. This happens because the absorbed energy is transformed into heat both in the bulk and on the surface of the sample. The PA technique uses a PA signal obtained experimentally to determine where the heat is coming from that is causing the thermal waves. So, in addition to the optical characteristics of the sample, we may also learn about its thermal parameters, structural formations, and inhomogeneities from the PA response. Several authors have created cutting-edge approaches to investigate the laser–semiconductor interaction in photoacoustic spectroscopy [21, 22]. Several physical studies using PT techniques [23–27] confirmed the accurate temperatures, internal displacements, thermal diffusion, and other electrical features of nano-composite semiconductor materials. Elastic oscillations in the atomic lattices of a material are directly responsible for the electronic deformation induced by light. Hobiny and Abbas [28] used a semiconductor-filled cylinder cavity to investigate PT waves in free space. When a semiconducting material is subjected to PT waves with hydrostatic stress, moisture diffusivity with non-local parameters, two temperatures, laser pulses, and the resulting strain stresses become problematic [29, 30]. Applying the photo-thermoelasticity hypothesis to the case of the Moore–Gibson–Thompson (MGT) stability model in a photonic semiconductor material subject to a two-temperature theory, Chteoui et al. [31] found support for their theory. On the other hand, Hobiny and Abbas [32–34] used a theoretical analysis to obtain the effect of a moving heat source with laser irradiation on skin tissue during thermal damage. Many applications according to the bioheat model based on the thermoelasticity theory are studied for living tissue [35–38].
In recent years, the MGT equation has gained a lot of attention because it may be used in a variety of contexts. Recent years have seen a rise in the profile of research into PT phenomena within the context of the subject of material science. It may be used in the evaluation of the thermal, optical, and electrical properties of various materials. In this research, moisture diffusivity is used to analyze the moisture and heat equation that occurs during the PT MGT process in one dimension when the mechanical force and moisture diffusivity are both in play. The issue is posed at the free surface of a semi-infinite semiconducting material in its most general form. To solve the system and obtain an analytical solution for the primary physical fields, the Laplace transform is used. To declare the physical numbers, the numerical inverse of the Laplace transform must be executed by utilizing a computer language. In conclusion, the results of all calculations regarding the distribution of temperature, carrier intensity, normal displacement, normal force stress, and moisture concentration are visually depicted.
2 Main equations
During the PT transport phase, the medium is analyzed with the overlapping processes of plasma–thermal and moisture diffusion in mind if the thermo-elastic semiconductor material exhibits linear elastic properties and is homogeneously transversely anisotropic. In this problem, the fundamental distributions in this problem are the carrier density (intensity)
In tensor form, the motion equation is similar to [1–3]:
Both the displacement and strain tensor may be represented using the same equation:
With increasing humidity, the tensor form of stress, displacement, and plasma temperature is similar to the following equation:
In the aforementioned equations, the diffusivity parameters are
When the surface boundary conditions are thermally insulated, the rod representing the semiconductor elastic media is released from the constraints of the electrical short (closed circuit), isothermal, and stress loads. To that purpose, all analyses are performed along the
The following are the 1D descriptions of the physical quantities [30]:
For Eq. 4, we have
Here,
In one dimension, the constitutive equation is similar to the following equation:
The MGT model according to the PT excitation can be expressed as a general form of the LS and GN-III models. In this case, the principal models of the photo-thermoelasticity theory under the MGT effect (
(i) When
(ii) When
(iii) When
(iv) When
3 The mathematically formulized problem
The following non-dimensional variables are provided for convenience:
To simplify Eq. 7, Eq. 8, Eq. 9, Eq. 10, and Eq. 11, we may use Eq. 12 to remove the dashes and obtain
The 1D stress component takes the following form in the non-dimensional form:
where
The coupled parameter
According to the properties of homogeneity of the problem, the following initial conditions to solve the problem analytically are presented:
4 The solution to the problem
Laplace transforms used, which are defined for any function
Applying Eq. 19 to the main aforementioned Eqs 13–17, the following equations are obtained:
where
Solving the converted Eqs 20–22 and Eq. 23 by the elimination technique between
where the main coefficients of Eq. 25 are given as follows:
To solve the differential Eq. 25, the factorization method is given as follows:
The quantities
The other linear solutions of remain quantities are expressed in the following form:
Here, the parameters
The foregoing values provide the domain solution for Laplace’s main variable transformations in terms of unknown parameters
5 Boundary conditions
Assume that the elastic semiconductor medium is subjected to mechanical, plasma, and thermal stresses, with the loss of control over these variables (
(I) For
Accordingly,
(II) Application of the Laplace transformation to the condition of mechanical normal stress (pressure) components at the free surface
Therefore,
(III) When the carrier density is diffusively transported and photosynthesized during recombination processes, the plasma boundary condition at the free surface (
The following equation is obtained:
(IV) The free-surface displacement boundary condition is given as follows:
On the other hand, the following relation is obtained:
The quantities (
6 Inversion of the Fourier–Laplace transforms
Dimensionless physical fields in the time domain may be obtained by inversion of the Laplace transform. In this case, the Laplace transform may be approximated numerically using the Riemann sum method [39].
In the Laplace domain, the inverse of the function
In this case,
The following relation is obtained by expanding the Fourier series for the function
Here,
7 Numerical results and discussion
To create the numerical simulation, the numerical parameters of the physical fields are used. These factors include temperature, moisture, normal stress, displacement, and carrier density. The simulation is carried out by using substances known as silicon (Si) and germanium (Ge). The following table presents the physical constants with their SI unit representations according to Table 1 [27–31]:
7.1 The moisture reference influence
Figure 1 (the first group) shows the semiconductor constants of silicon utilized to obtain the graph of the main physical quantities: thermal waves (thermal temperatures), normal stress (mechanical waves), plasma waves (carrier density), elastic waves (displacement distribution), and moisture field against the
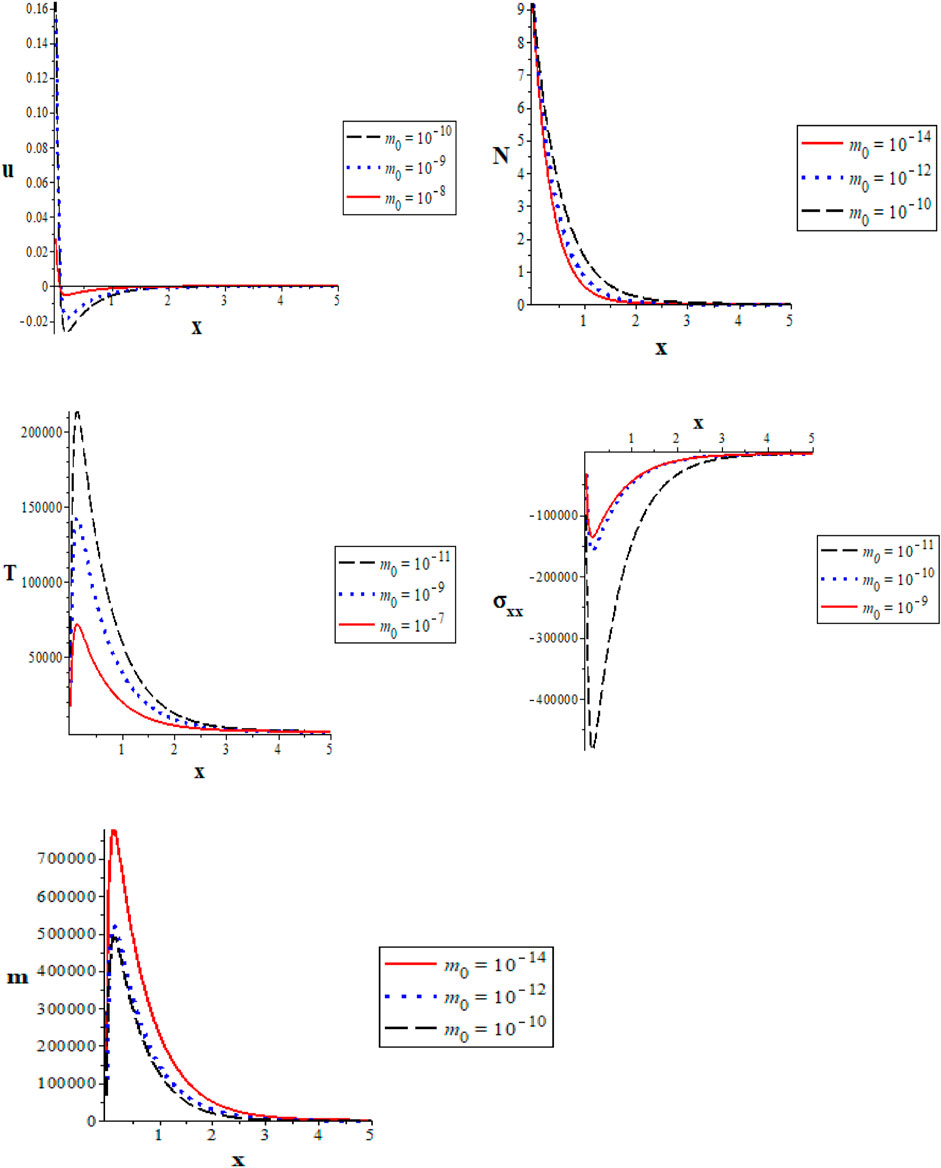
FIGURE 1. Representation of the variations of physical quantities with the x-axis (distance) under the effect of moisture diffusion at different values of reference moisture
7.2 The photo-thermoelastic model effect
The second kind of model depicts changes in photo-thermoelasticity models with increasing vertical distance, which may be used to investigate the effects of these variations on the basic dimensionless physical fields. Four different theories of photo-thermoelasticity are shown in Figure 2 (the second group) by showing the variations of the main physical field variables with distance (thermoelastic and photoelastic models). The outcomes fall within a range
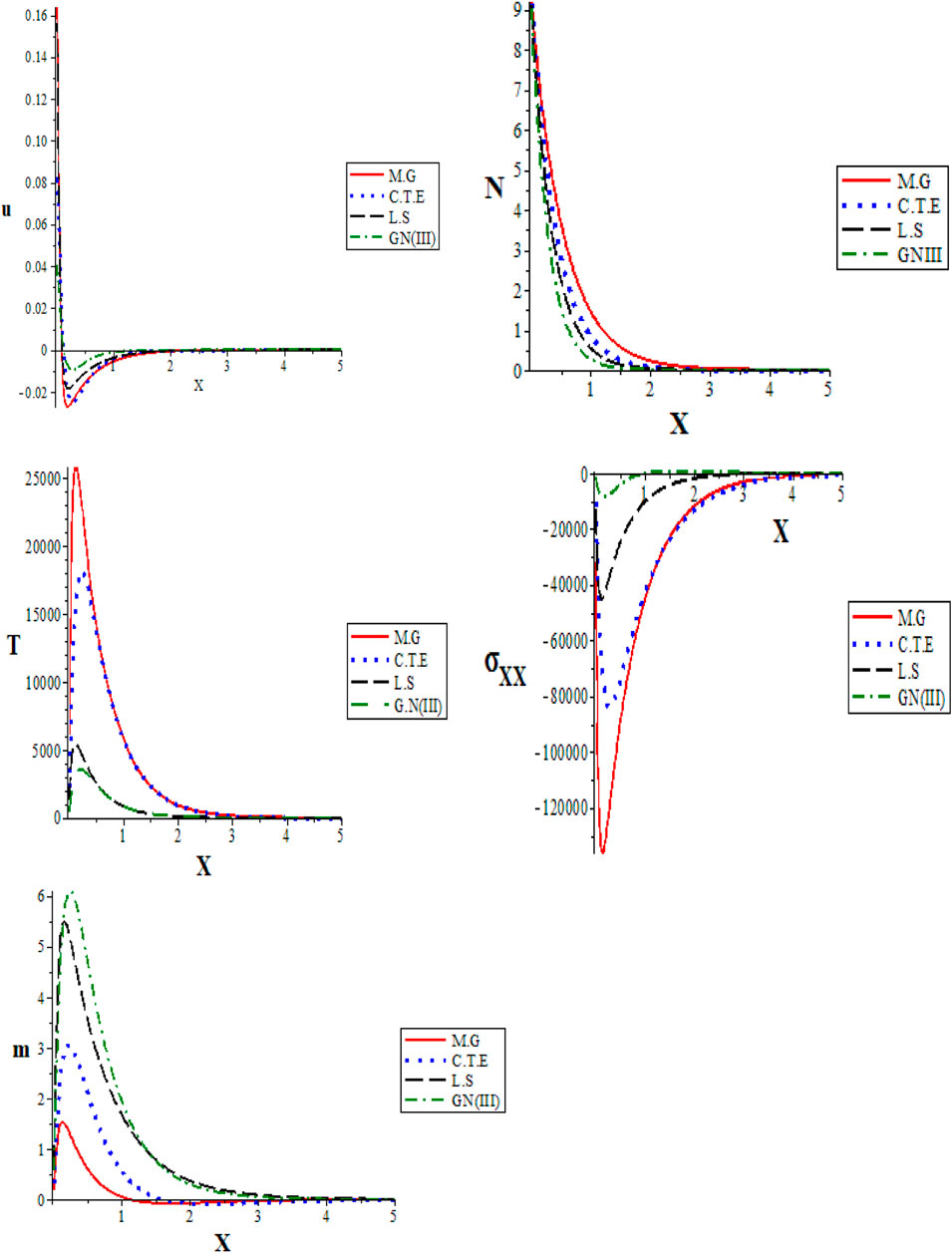
FIGURE 2. Representation of the variations of physical quantities with the x-axis (distance) for different photo-thermoelastic theories.
7.3 The comparison between two semiconductor materials
Silicon (Si) and germanium (Ge) are both semiconductor materials, and Figure 3 demonstrates the comparison when their physical constants are employed in the computations. All calculations are prepared according to the MGT model when
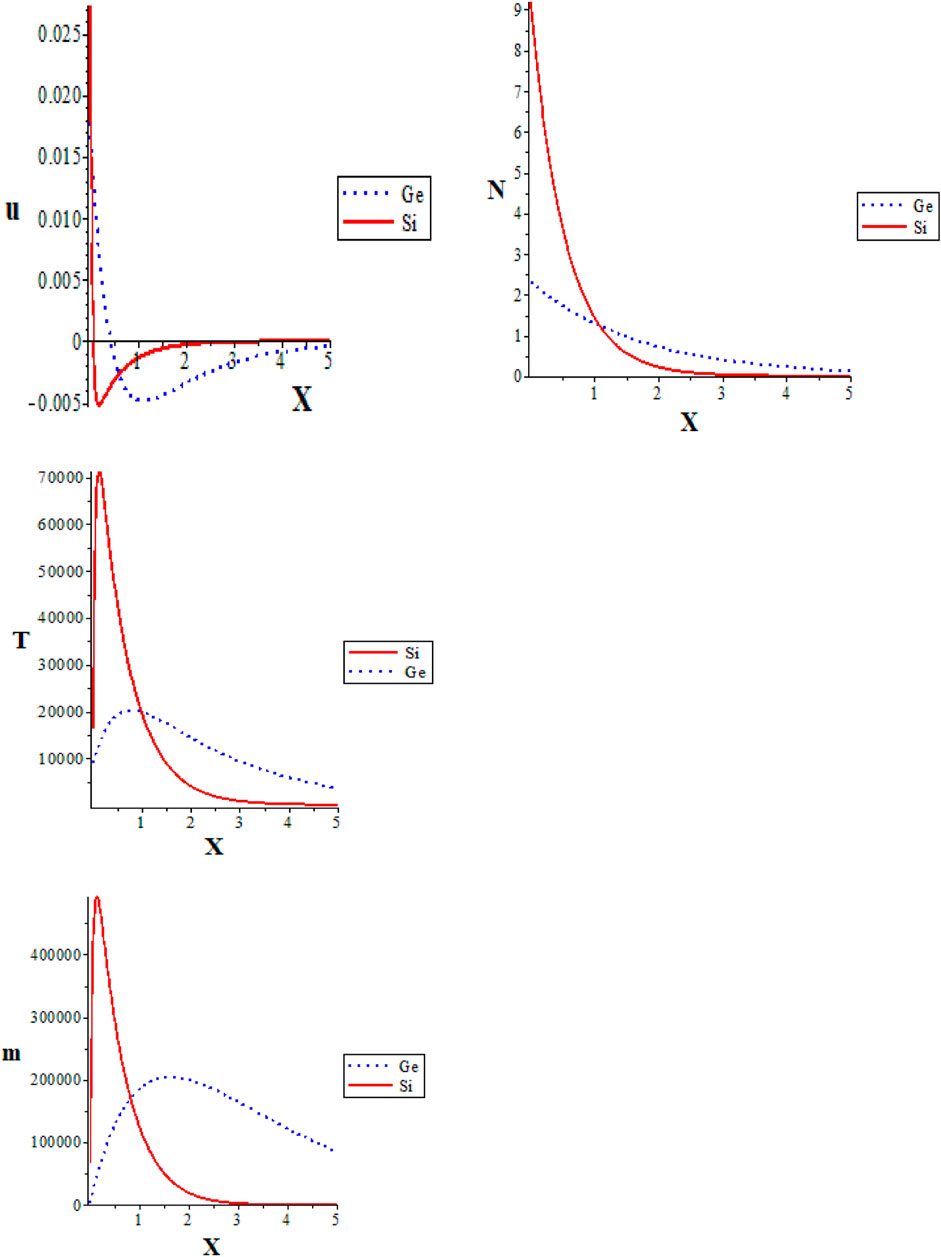
FIGURE 3. Representation of the variations of the main field with the x-axis (distance) for two different semiconductors.
8 Conclusion
This study offers an original account of the thermal and elastic relaxation time-dependent model applications (MG, GN(III), CTE, and LS) used to characterize the interference of elastic, thermal, and plasma waves in a semiconductor medium. Under the framework of MGT’s elasticity theory, the photo-thermoelastic interactions in an infinite semiconducting material have been investigated. A high quantity of moisture affects the semiconductor media. As various models have been developed to represent photo-thermoelasticity issues, the MGT model is a natural progression. The photo-thermoelastic models and the moisture diffusivity have drastically different standard deviations. The value of the moisture diffusivity parameter has a significant impact on the rate of change of the primary distribution variation. This means that the moisture content is a better indicator of heat transfer than it formerly was. The comparison of the wave propagations shows that the value of the physical parameters of the medium significantly affects the patterns of field distributions in this study. The physical assumptions are consistent with the notion that waves travel at limited speeds, as predicted by the MGT model and other photo-thermoelastic models.
Data availability statement
The raw data supporting the conclusion of this article will be made available by the authors, without undue reservation.
Author contributions
KL: Conceptualization, Methodology, and Supervision. MS and ALB: Software, Data curation. AE-D: and Writing-Original draft preparation. SE-S: Visualization, Investigation, Software, Validation. NB and HC: Writing-Reviewing and Editing. All authors contributed to the article and approved the submitted version.
Acknowledgments
The authors extend their appreciation to Princess Nourah bint Abdulrahman University for fund this research under Researchers Supporting Project number (PNURSP2023R154) Princess Nourah bint Abdulrahman University, Riyadh, Saudi Arabia. The authors extend their appreciation to the Deanship of Scientific Research at Northern Border University, Arar, KSA for funding this research work through the project number “NBU-FFR-2023-0028”.
Conflict of interest
The authors declare that the research was conducted in the absence of any commercial or financial relationships that could be construed as a potential conflict of interest.
Publisher’s note
All claims expressed in this article are solely those of the authors and do not necessarily represent those of their affiliated organizations, or those of the publisher, the editors, and the reviewers. Any product that may be evaluated in this article, or claim that may be made by its manufacturer, is not guaranteed or endorsed by the publisher.
References
1. Biot MA. Thermoelasticity and irreversible thermodynamics. J Appl Phys (1956) 27:240–53. doi:10.1063/1.1722351
2. Lord H, Shulman Y. A generalized dynamical theory of thermoelasticity. J.Mech Phys Sol (1967) 15:299–309. doi:10.1016/0022-5096(67)90024-5
4. Abo-Dahab S, Lotfy K. Generalized magneto-thermoelasticity with fractional derivative heat transfer for a rotation of a fibre-reinforced thermoelastic. J Comput Theor Nanoscience (2015) 12(8):1869–81. doi:10.1166/jctn.2015.3972
5. Othman M, Lotfy K. Two-dimensional problem of generalized magneto-thermoelasticity with temperature dependent elastic moduli for different theories. Multidiscipline Model Mater Structures (2009) 5(3):235–42. doi:10.1163/157361109789016961
6. Aboueregal A, Sedighi H, Shirazi A, Malikan M, Eremeyev V. Computational analysis of an infinite magnetothermoelastic solid periodically dispersed with varying heat flow based on non-local Moore–Gibson–Thompson approach. Contin Mech Thermodyn (2022) 34:1067–85. doi:10.1007/s00161-021-00998-1
7. Othman M, Lotfy K, Farouk R. Transient disturbance in a half-space under generalized magneto-thermoelasticity with internal heat source. Acta Physica Pol A (2009) 116(2):185–92. doi:10.12693/aphyspola.116.185
8. Quintanilla R. Moore-Gibson-Thompson thermoelasticity. Math Mech Sol (2019) 24:4020–31. doi:10.1177/1081286519862007
9. Quintanilla R. Moore-Gibson-Thompson thermoelasticity with two temperature. Appl Eng Sci (2020) 1:100006. doi:10.1016/j.apples.2020.100006
10. Vlase S, Năstac C, Marin M, Mihălcică M. A method for the study of the vibration of mechanical bars systems with symmetries. Acta Tech Napocensis, Ser Appl Math Mech Eng (2017) 60(4):539–44.
11. Abouelregal A, Marin M. The size-dependent thermoelastic vibrations of nanobeams subjected to harmonic excitation and rectified sine wave heating. Mathematics (2020) 8(7):1128. doi:10.3390/math8071128
12. Abouelregal A, Marin M. The response of nanobeams with temperature-dependent properties using state-space method via modified couple stress theory. Symmetry (2020) 12(8):1276. doi:10.3390/sym12081276
13. Scutaru ML, Vlase S, Marin M, Modrea A. New analytical method based on dynamic response of planar mechanical elastic systems. Bound Value Problem (2020) 2020:104. doi:10.1186/s13661-020-01401-9
14. Kaltenbacher B, Lasiecka I, Marchand R. Wellposedness and Exponential decay rates for the Moore–Gibson–Thompson equation arising in high intensity ultrasound. Control Cybernet (2011) 40:971–88.
15. Lotfy K, Seddeek M, Hassanin W, El-Dali A. Analytical solutions of photo generated moore–gibson–thompson model with stability in thermoelastic semiconductor excited material. Silicon (2022) 14:12447–57. doi:10.1007/s12633-022-01927-w
16. Lotfy K, Elidy E, Tantawi R. Piezo-photo-thermoelasticity transport process for hyperbolic two-temperature theory of semiconductor material. Int J Mod Phys C (2021) 32(7):2150088. doi:10.1142/S0129183121500881
17. Szekeres A. Analogy between heat and moisture. Comput Structures (2000) 76:145–52. doi:10.1016/s0045-7949(99)00170-4
18. Szekeres A. Cross-coupled heat and moisture transport: Part 1 theory. J Therm Stresses (2012) 35(1-3):248–68. doi:10.1080/01495739.2012.637827
19. Gasch T, Malm R, Ansell A. A coupled hygro-thermo-mechanical model for concrete subjected to variable environmental conditions. Int J Sol Structures (2016) 91:143–56. doi:10.1016/j.ijsolstr.2016.03.004
20. Szekeres A, Engelbrecht J. Coupling of generalized heat and moisture transfer. Periodica Polytechnica Ser Mech Eng (2000) 44(1):161–70.
21. Gordon JP, Leite RCC, Moore RS, Porto SPS, Whinnery JR. Long-transient effects in lasers with inserted liquid samples. Bull Am Phys Soc (1964) 119:501. doi:10.1063/1.1713919
22. Kreuzer LB. Ultralow gas concentration infrared absorption spectroscopy. J Appl Phys (1971) 42:2934–43. doi:10.1063/1.1660651
25. Tam AC. Photothermal investigations in solids and fluids. Boston: Academic Press (1989). p. 1–33.
26. Todorovic DM, Nikolic PM, Bojicic AI. Photoacoustic frequency transmission technique: Electronic deformation mechanism in semiconductors. J Appl Phys (1999) 85:7716–26. doi:10.1063/1.370576
27. Song YQ, Todorovic DM, Cretin B, Vairac P. Study on the generalized thermoelastic vibration of the optically excited semiconducting microcantilevers. Int J Sol Struct (2010) 47:1871–5. doi:10.1016/j.ijsolstr.2010.03.020
28. Mahdy A, Lotfy K, El-Bary A, Sarhan H. Effect of rotation and magnetic field on a numerical-refined heat conduction in a semiconductor medium during photo-excitation processes. Eur Phys J Plus (2021) 136(5):553–63. doi:10.1140/epjp/s13360-021-01552-3
29. El-Sapa S, Lotfy K, El-Bary A, Ahmed M. Moisture diffusivity and photothermal excitation in non-local semiconductor materials with laser pulses. Silicon (2023). doi:10.1007/s12633-023-02333-6
30. Lotfy K. Photothermal waves for two temperature with a semiconducting medium under using a dual-phase-lag model and hydrostatic initial stress. Waves Ran Comp Med (2017) 27(3):482–501. doi:10.1080/17455030.2016.1267416
31. Chteoui R, Lotfy K, Seddeek M, El-Dali A, Hassanin W. Moore–gibson–thompson stability model in a two-temperature photonic semiconductor excited medium affected by rotation and initial stress. Crystals (2022) 12(12):1720. doi:10.3390/cryst12121720
32. Hobiny A, Abbas I. Theoretical analysis of thermal damages in skin tissue induced by intense moving heat source. Int J Heat Mass Transf (2018) 124:1011–4. doi:10.1016/j.ijheatmasstransfer.2018.04.018
33. Hobiny A, Abbas I. Nonlinear analysis of dual-phase lag bio-heat model in living tissues induced by laser irradiation. J Therm Stresses (2020) 43:503–11. doi:10.1080/01495739.2020.1722050
34. Hobiny A, Abbas I. Analytical solutions of fractional bioheat model in a spherical tissue. Mech Based Des Struct Mach (2021) 49:430–9. doi:10.1080/15397734.2019.1702055
35. Ghanmi A, Abbas I. An analytical study on the fractional transient heating within the skin tissue during the thermal therapy. J Therm Biol (2019) 82:229–33. doi:10.1016/j.jtherbio.2019.04.003
36. Zenkour A, Abbas I. Nonlinear transient thermal stress analysis of temperature-dependent hollow cylinders using a finite element model. Int J Struct Stab Dyn (2014) 14(7):1450025. doi:10.1142/s0219455414500254
37. Alzahrani F, Abbas I. Analytical estimations of temperature in a living tissue generated by laser irradiation using experimental data. J Therm Biol (2019) 85:102421. doi:10.1016/j.jtherbio.2019.102421
38. Saeed T, Abbas I. Finite element analyses of nonlinear DPL bioheat model in spherical tissues using experimental data. Mech Based Des Struct Mach (2020) 50:1287–97. doi:10.1080/15397734.2020.1749068
39. Honig G, Hirdes U. A method for the numerical inversion of Laplace Transforms. Comp Appl Math (1984) 10(1):113–32. doi:10.1016/0377-0427(84)90075-x
40. Brancik L. Programs for fast numerical inversion of Laplace transforms in MATLAB language environment. In: Proceedings of the 7th Conference. MATLAB’99; November 10, 1999; Czech Republic Prague (1999). p. 27–39.
Keywords: semiconductor, optoelectronic, moisture diffusivity, Moore–Gibson–Thompson, waves, photocarrier
Citation: El-Sapa S, Becheikh N, Chtioui H, Lotfy K, Seddeek MA, El-Bary AA and El-Dali A (2023) Moore–Gibson–Thompson model with the influence of moisture diffusivity of semiconductor materials during photothermal excitation. Front. Phys. 11:1224326. doi: 10.3389/fphy.2023.1224326
Received: 17 May 2023; Accepted: 06 June 2023;
Published: 22 June 2023.
Edited by:
Mahmoud Abdelrahman, Mansoura University, EgyptReviewed by:
Ibrahim A. Abbas, Sohag University, EgyptAbdulkafi Mohammed Saeed, Buraydah, Saudi Arabia
Adnan Jahangir, COMSATS University Islamabad, Wah Campus, Pakistan
Copyright © 2023 El-Sapa, Becheikh, Chtioui, Lotfy, Seddeek, El-Bary and El-Dali. This is an open-access article distributed under the terms of the Creative Commons Attribution License (CC BY). The use, distribution or reproduction in other forums is permitted, provided the original author(s) and the copyright owner(s) are credited and that the original publication in this journal is cited, in accordance with accepted academic practice. No use, distribution or reproduction is permitted which does not comply with these terms.
*Correspondence: Nidhal Becheikh, bmlkaGFsLmJlY2hlaWtoQG5idS5lZHUuc2E=; Kh. Lotfy, a2hsb3RmeV8xQHlhaG9vLmNvbQ==