- Engineering Technology Research Institute of Southwest Oil and GasField Company, PetroChina, Chengdu, China
Unconventional reservoirs have strong heterogeneity, with significant differences in the distribution of porosity and permeability. Fracturing is an important technology for increasing natural gas production in unconventional oil and gas reservoirs. For unconventional reservoirs with high temperature and low permeability, the rapid increase in acid rock reaction rate leads to a significant decrease in the effective distance of acidic fluids and fracture conductivity, especially the inability to obtain effective support at the fracture tip, which restricts the increase in production of high-temperature unconventional oil and gas reservoirs. To address the above issues, a composite fracturing method is proposed, which first uses a proppant to support the crack tip, and then uses gelled acid to corrode the middle and rear parts of the crack. According to the fracture conductivity achievement test experiment and proppant migration experiment, when 40/70 mesh ceramsite and 100 mesh ceramsite are mixed at a mass ratio of 1:4, the fracture conductivity can reach 21.8 μm·cm2 under the effective closing pressure of 60 MPa, which is 123% higher than the fracture conductivity of cementitious acid corrosion. The gel is used to carry 40/70 mesh and 100 mesh ceramsite, and the Equilibrium level of the sand embankment can reach 38 cm. At the same time, the sand dike formed by different particle sizes of ceramic particles is smoother than the sand vein formed by a single particle size of proppant, and the migration ability of ceramic particles to the fracture tip is better. The composite stimulation technology has been applied to 9 wells in carbonate and shale oil and gas reservoirs. After fracturing, the production of oil and gas wells is 210% higher than that of gelled acid fracturing, and the composite stimulation technology has achieved good stimulation effects.
1 Introduction
The unconventional reservoirs is rich in oil and gas resources, which is an important field to ensure the world energy security [1–3]. In the past 20 years, China has successively discovered several large carbonate oil and gas fields in the Tarim Basin and Sichuan Basin, such as Tahe Oilfield and Shunbei Oilfield in the Tarim Basin, Puguang Oilfield and Anyue Oilfield in the Sichuan Basin [4–7]. The burial depth of reservoirs in Shunbei Oilfield in Tarim Basin and Qixia Formation in Sichuan Basin even exceeds 8,000 m, and the reservoir temperature is as high as 160°C–180°C [8–11]. Acid fracturing stimulation mainly depends on the formation of conductivity of fracture wall corroded by acid fluid, so as to establish oil and gas migration channel from formation to wellbore. The acid rock reaction speed increases sharply with the rise of reservoir temperature [12]. Under ultra-high temperature conditions, the acid solution reacts quickly after contacting the rock. The high temperature environment intensifies the consumption of acid solution, resulting in a very short effective action distance of acid solution in ultra-high temperature formation [13, 14], which affects the acid etching fracture length and oil and gas production.
Improving the length and conductivity of acid etched fractures is an important goal of acid fracturing in carbonate reservoirs, Aljawad et al. [15] indicated that different acid fluid systems should be selected according to the formation feature for improved fracture conductivity. Hou Bing et al. [16] investigated the fracture initiation and propagation in limestone formations under acid fracturing treatment. Lufeng Zhang et al. [17] proposed a new method to raise acid fracture conductivity under high closure stress and provided an insight into optimizing acid propped fracturing design and predicting well performance. Yang Wang et al. [18] proposed a technical method to improve the acid etching fracture length and conductivity of low permeability carbonate reservoirs by alternating injection of authigenic acid and gelling acid. Yang Wang et al. [19] carried out the visual test experiment of alternating injection acid fracturing and studied the influence of parameters such as injection displacement, acid ratio and injection stage on acid fingering morphology. Ye Jiexiao et al. [20], the influence of different injection stages, different liquid combinations and different displacement on the conductivity of acid corrosion fractures was studied by numerical scanning technology. Shahvir Pooniwala et al. [21] successfully performed proppant fracturing treatment for the first time in the Cretaceous carbonate formation of Kuwait. Lurui Dang et al. [22] established an acidizing fluid flow and reaction model taking the multiple leak-off effect of natural fracture, wormhole and matrix into account. Rencheng Dong et al. [23] developed a 3D acid transport model to compute the geometry of acid fracture for acid fracturing treatments with viscous fingering. The developed model couples the acid fluid flow, reactive transport and rock dissolution in the fracture. Daobing Wang et al. [24] proposed a simple iterative procedure to handle the non-linear characteristic of the hydraulic fracturing problem. Numeral validation illustrates that the results of PGD match well with these of standard fifinite element method in terms of fracture opening and fluid pressure in the hydro-fracture.
An Na et al. [25] developed a new type of solid granular acid which was prepared by taking sulfonic acid as the core material and using organic sulfonic acid/ethyl cellulose composite as capsule materials, and it could be solidified and granulated by adopting a spray drying process. Yang Wang et al. [26] established a kind of autogenic acid system through the hydrolysis of ester to acetic acid in situ, and the autogenic acid system possesses the desired characteristic in which hydrolysis can generate a small amount of acetic acid below 120°C and a large amount of acid above 140°C in 2 h. Zhiheng Zhao et al. [27] evaluated compatibility, temperature resistance, friction reduction of the high-temperature-resistant diverting acid (HTRDA), and the peak viscosity of the HTRDA can still reach 31 mPas at the temperature of 170 °C, which is higher than that of conventional diverting acid with about 10 mPas. Sui Yu et al. [28] developed a new high-temperature-resistant gelled acid system with modified xanthan gum, and the viscosity of the acid system at 160°C remains 21 mPas. Juan Du et al. [29] synthesized a high-temperature autogenic acid system with formaldehyde and ammonium and chloride as the matrix, and the effective acid rock reaction time of this autogenic acid can reach 6 h.
At present, there are a lot of researches on acid fracturing technology and high-temperature resistant acid fluid of carbonate rock oil and gas reservoirs. However, there are few researches on acid fracturing technology of such ultra deep and ultra-high temperature carbonate rock oil and gas reservoirs with a buried depth of more than 7,000 m and a reservoir temperature of 180°C. In order to improve the recovery of ultra deep and ultra high temperature carbonate reservoirs, it is very necessary to study targeted acid fracturing stimulation technology.
In order to solve the technical problem of acid fracturing in ultra deep and ultra-high temperature wells, the author has developed high-temperature resistant gelling acid, which can meet the acid fracturing requirements of 180°C ultra-high temperature reservoirs. At the same time, a new acid fracturing technology combined with hydraulic fracturing and acid fracturing is proposed, which greatly improves the length and conductivity of fracturing fractures. The field test has achieved good application results, which has certain reference significance for the technology of improving oil recovery in ultra deep and ultra-high temperature carbonate rock reservoirs.
2 Results and discussion
Acid fracturing forms grooves on the rock wall through acid rock reaction, thus establishing a channel for natural gas to flow from the reservoir to the wellbore. The length and conductivity of acid etched fractures determine the drainage area and control range of gas wells. For low permeability oil and gas reservoirs, the ultimate goal of acid fracturing is to improve the length and conductivity of acid etched fractures. However, the reaction speed of acid rock increases exponentially under ultra-high temperature environment, resulting in a significant reduction in the length of acid etched fractures and a rapid reduction in fracture conductivity, which is difficult to meet the requirements of ultra-high temperature and low permeability oil and gas reservoirs.
It can be seen from Figure 1 that the acid rock reaction rate at 160°C is 2.73 times that at 120°C, and the acid rock reaction rate increases sharply with temperature. This article uses FRACPRO to simulate the extension of acid corrosion fractures at different temperatures. FRACPRO is an acid fracturing design software. The single well geomechanical model is established by inputting parameters such as porosity, permeability, Young’s modulus and crustal stress in the FRACPRO, and then the acid fluid performance is customized according to the experimental results such as acid rock reaction rate, so as to simulate the fracture length results under the same fluid volume and displacement. From the simulation results of the FRACPRO, it can be seen that under the same displacement and fluid scale, the length of acid corrosion cracks at 160°C is reduced by more than 20% compared to 120°C.
2.1 Technical principles
Under high temperature, acid rock reaction is fast, acid fluid is difficult to reach the fracutre tip, and acid fluid cannot effectively dissolve the fracutre tip. To solve the above problems, a new method of combined hydraulic fracturing and acid fracturing is proposed, and the schematic diagram of composite stimulation technology is shown in Figure 2. The process steps of compound acid compression are as follows: First, hydraulic fracturing is injected to open the formation to form artificial fractures; then, sand carrying fluid is injected to carry ceramsite to support the fracture tip; finally, acid is injected to corrode the fracture wall. The ceramsite is used to support the fracutre tip, and the acid solution is used to dissolve the fracutre wall, so as to produce a high conductivity fracutre that can effectively support and corrode from the tip to the tail. This acid fracturing process combines the technical advantages of acid fracturing and hydraulic fracturing. It not only maintains the advantages of good effect of hydraulic fracturing to support fractures and high conductivity, but also forms high conductivity grooves on the fracture wall with the aid of acid solution to, etch the rock. The acid fracturing and hydraulic fracturing stimulation technologies complement each other well, and the compound acid fracturing technology greatly improves the fracture length and conductivity.
The core of the compound acid fracturing process is how to carry the proppant to the fracture tip, so as to improve the fracture length and conductivity. The transport of proppant in the fracture is affected by gravity, viscosity and other factors [30], and the proppant is distributed as a sand embankment in the fracture [31]. The equilibrium height of the sand dike and the position of the front edge of the sand dike are the key parameters to evaluate the transport of proppant [32].
In this paper, unconventional reservoir cores were selected to carry out acid corrosion fracture conductivity and hydraulic fracture conductivity tests. It can be seen from Figure 3 that hydraulic fracture conductivity is significantly higher than acid corrosion fracture conductivity, mainly because ceramsite in hydraulic fractures can play a better supporting role under high closure stress, and grooves and bulges in acid etching fractures are easy to be crushed and deformed under high closure stress. The above experiment further proves that using ceramic particles to support the fracture tip can improve the fracture conductivity.
This article selected 70/140 mesh ceramic particles and 40/70 mesh ceramic particles to conduct proppant transport and fracture conductivity tests. The density of 70/140 mesh ceramic particles and 40/70 mesh ceramic particles is 2.7 g/cm3, and the proppant transport is mainly studied through the proppant plate transport experiment device. The fracture conductivity is tested using high-temperature and high-pressure conductivity equipment according to API standards.
2.2 Proppant transport evaluation
In this paper, the proppant plate transport experiment device was used to simulate the transport process of ceramicites with different particle sizes and different concentrations in fractures. At the same time, the shape of sand embankment is quantitatively characterized by digital method.
A visual evaluation device for proppant transport was designed to study proppant placement in fractures during fracturing. The equipment is mainly composed of sand mixing container, displacement pump and tempered glass plates (Figure 4). The tempered glass plates is the main part of the device. The fracture is simulated by two transparent tempered glass plates placed in parallel. The length of the tempered glass plate is 7 m and the height is 0.7 m.

FIGURE 4. Schematic diagram of the composition of the visualization evaluation device for proppant transportation.
Compared with the current conventional proppant transport evaluation equipment, the size of the experimental device designed in this study is larger. The length of the traditional transport evaluation device is about 3 m [33], and the length of this device is as high as 7 m. At the same time, the power of the displacement pump is larger, which can pump the sand carrying fluid with high displacement. At the same time, the inner wall of the tempered glass plate is rough, which can more truly simulate the transport of proppant in the fracture.
In the experiment, the fracturing fluid and ceramsite were mixed in the sand mixing container. The fracturing fluid was then displaced into the tempered glass plates by the displacement pump. The proppant in simulated fractures will fall under gravity, and during the experiment, a high-speed camera was used to record the shape of the sand embankment in real time, and the final shape of the sand embankment was described by digital method. In this experiment, the clean fracturing fluid with viscosity of 40 mPas is used as the sand carrying fluid, and the particle size of ceramsite is 40/70 mesh and 100 mesh. The injection displacement is constant at 50 L per minute.
The equilibrium height and non-uniform coefficient of sand embankment are used to describe the sand embankment [34]. The equilibrium height of the sand embankment is the height of the sand embankment when the proppant particles are in equilibrium. The non-uniformity coefficient is calculated by the variance of the sand embankment height per unit section length. The non-uniformity coefficient is used to measure the uniformity of the distribution of the sand embankment in the height direction. The smaller the non-uniformity coefficient, the more uniform the proppant placement.
It can be seen from Figure 5 that with the increase of 40/70 mesh ceramsite concentration, the transport length of ceramsite in the simulated fracture length direction gradually becomes shorter, and it is difficult for high concentration ceramsite to be transported to the fracture tip. The total length of sand embankment formed by ceramsite with the concentration of 80 kg/cm3 is 5,780 mm, which is about 28% longer than that formed by ceramsite with the concentration of 140 kg/cm3.
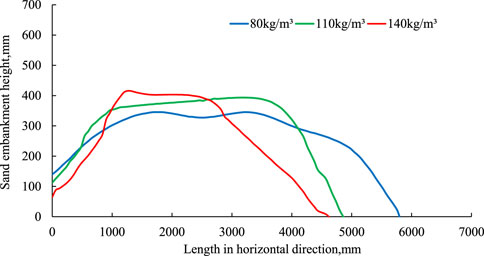
FIGURE 5. Digital map of sand embankment formed by transport of 40/70 mesh ceramsite with different concentrations.
During the transport process in the simulated fracture, the proppant will gradually sink and accumulate at the bottom of the fracture, thus forming a sand embankment and gradually increasing the height of the sand dike. When the settlement speed of proppant and the forward speed of proppant carried by fracturing fluid balance each other, the height of sand embankment will not increase any more. At this time, the height of sand embankment is called the equilibrium height of sand embankment [35, 36]. The greater the equilibrium height of the sand embankment is, the better the proppant can support the fracture height. However, since the total amount of proppant is certain, the height and length of the sand embankment always show a trend of trade-off. Therefore, the height and length of the sand embankment should be taken into account when optimizing the concentration of proppant.
As shown in Figure 6 with the increase of 100 mesh ceramsite concentration, the transport length of ceramsite in the simulated fracture length direction gradually becomes shorter, but the difference in the length of sand embankment formed by ceramsite with different concentrations is very small. The total length of sand embankment formed by ceramsite with 80 kg/cm3 concentration is only about 7% longer than that formed by ceramsite with 140 kg/cm3 concentration.
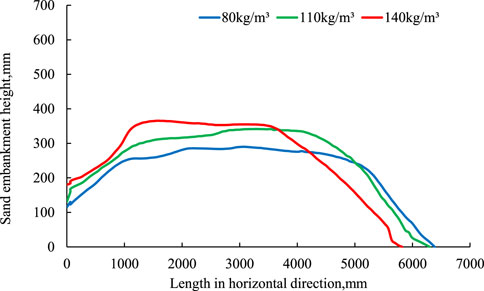
FIGURE 6. Digital map of sand embankment formed by transport of 100 mesh ceramsite with different concentrations.
It can be seen from Table 1 that with the increase of proppant particle size, the equilibrium height and non-uniformity coefficient of sand embankment gradually increase, and the overall length of sand embankment gradually decreases. This is because the ceramsite with small particle size is easy to carry, and it can move a large distance in the fracture. When the particle size of ceramsite increases, the increase of ceramsite settlement speed will lead to the sharp increase of the non-uniformity of the sand embankment at the same time.
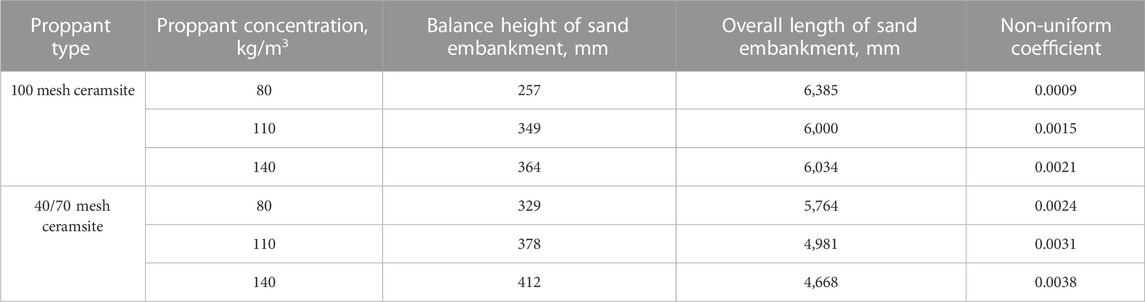
TABLE 1. Comparison of the sand embankment formed by ceramsite transportation with different concentration and particle size.
The effective closure pressure of ultra deep carbonate reservoirs in China is approximately 50 MPa [37]. Small particle size proppant is difficult to obtain high conductivity under high closure pressure. Although large particle size proppant can provide higher fracture conductivity, the addition of large particle size proppant in ultra deep carbonate fracturing is easy to cause sand plug [38]. In order to effectively support the fracture tip, it is necessary to study the characteristics of proppant transport morphology and conductivity formed by mixing large and small particle size proppants.
In this paper, 40/70 mesh ceramsite and 100 mesh ceramsite are mixed according to the mass ratio of 1:4 and 2:3 to test the transport form and conductivity of the proppant with combined particle size in the fracture. The experimental goal is to optimize the proppant combination that can not only transport to the fracture tip, but also provide high conductivity.
It can be seen from Figures 7, 8 that the transport patterns of ceramsite with mixed particle size in the fractures are roughly the same. With the increase of proppant concentration, the horizontal transport distance of the sand embankment gradually decreases, and the time period for the sand embankment to maintain the equilibrium state gradually decreases.
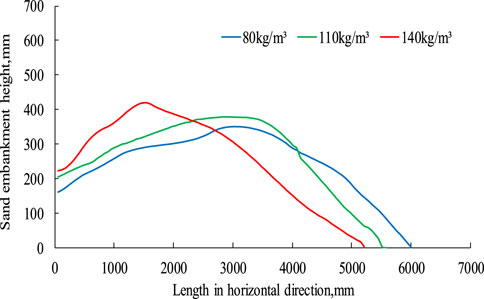
FIGURE 7. Digital map of sand embankment formed by 40/70 mesh and 100 mesh ceramsite transportation with 1:4 mass ratio.
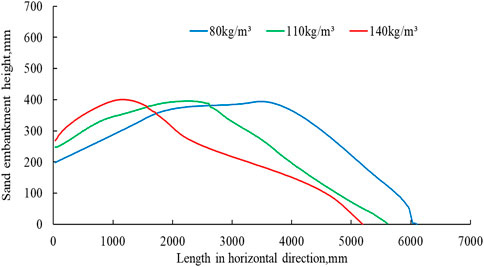
FIGURE 8. Digital map of sand embankment formed by 40/70 mesh and 100 mesh ceramsite transportation with 2:3 mass ratio.
It can be seen from Table 2 that with the increase of the mass proportion of 100 mesh ceramsite in the proppant, the nonuniformity coefficient of the sand embankment formed by the proppant with the same concentration is lower, indicating that a more balanced sand embankment shape can be obtained by using a large number of small particle size ceramsite.
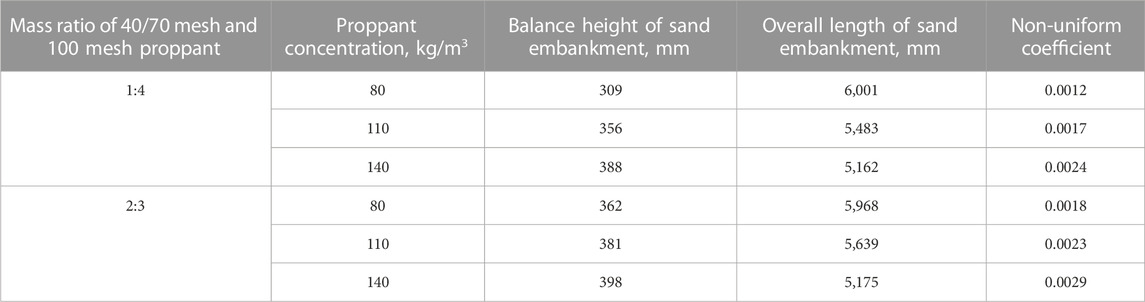
TABLE 2. Comparison of the sand embankment formed by ceramsite transportation with different concentration and particle size.
There are many fractures and corrosion cavities in carbonate reservoir, so the fluid loss during stimulation is relatively large, which leads to sand plugging during fracturing [39]. Because the essence of compound acid fracturing is to support the fracture tip with proppant, and other parts of the fracture are etched with acid to form conductivity, it is unnecessary to add too much proppant to compound acid fracturing [40].
The purpose of compound acid fracturing is to deliver proppant to the fracture tip and form effective support at the fracture tip. In this way, the sand embankment not only has a large length and height, but also has a relatively small non-uniform coefficient [41]. It can be seen from Figure 9 that when only 100 mesh ceramsite is added or the mass ratio of 100 mesh ceramsite to 40/70 mesh ceramsite is 4:1, the non-uniform coefficient of sand dike formed by proppant transport is small and the height and length of sand dike are large.
2.3 Fracture conductivity test
When only 100 mesh ceramsite or the mass ratio of 100 mesh ceramsite to 40/70 mesh ceramsite is 4:1, the shape of the sand embankment is relatively balanced, and the height and length of the sand embankment have good extension effects. The concentration and combination of proppant are optimized according to the experimental results of compound acid fracturing conductivity test. This paper focuses on the fracture conductivity when adding different concentrations of 100 mesh ceramsite or 40/70 mesh ceramsite and 100 mesh ceramsite with a mass ratio of 4:1, so as to select the best proppant combination and concentration.
The FCES-100 fracture conductivity meter produced by American Core Lab Company is used for the conductivity test. The maximum loading closure pressure of the instrument can be 120 MPa, and the ambient temperature can be heated to 160°C. The instrument meets the stress and temperature characteristics of ultra-deep and high-temperature carbonate reservoirs, and it can test the conductivity of proppant or the conductivity of acid etched fractures.
In order to ensure the reliability of the experimental results, carbonate rock slabs with the same rock mineral composition are used to carry out the experiment. First, drive the acid solution to corrode the surface of the carbonate rock slab, then pave ceramsite on the surface of the acid etched rock slab, and finally test the fracture conductivity.
We put 100 mesh ceramsite of three concentrations on the etched rock plate to test the fracture conductivity, so as to evaluate the change of the acid etched fracture conductivity after adding 100 mesh ceramsite. It can be seen from Figure 10 that with the increase of closure pressure, the fracture conductivity is generally declining. The fracture conductivity formed by acid + proppant is significantly higher than that of acid etched fractures. The fracture conductivity when the proppant concentration is 140 kg/m3 is 64% higher than that of acid etched fractures.
The fracture conductivity with the proppant concentration of 140 kg/m3 is only 5% more than that with the proppant concentration of 110 kg/m3. This is mainly because some proppant are filled into the grooves of acid etched fracture, which not only cannot improve the fracture conductivity, but may reduce the fracture conductivity [42].
We laid 40/70 mesh ceramsite and 100 mesh ceramsite on the etched rock slab in a 1:4 mass ratio to test the fracture conductivity, so as to evaluate the change of the fracture conductivity after adding 40/70 mesh ceramsite and 100 mesh ceramsite.
It can be seen from Figure 11 that the conductivity of proppant is greater than that of acid etched fracture. When the proppant concentration reaches 110 kg/m3, increasing the proppant concentration will not significantly improve the fracture conductivity.
It can be seen from Figure 12 that when the proppant concentration is also 110 kg/m3, the conductivity of 100 mesh ceramsite is significantly different from that of combined particle size ceramsite, and the combined particle size ceramsite is composed of 40/70 mesh and 100 mesh ceramsite in a 1:4 mass ratio. When the closure pressure is 50 MPa, the conductivity of composite ceramsite is 28.4% higher than that of 100 mesh ceramsite. When the closure pressure rises to 60 MPa, the conductivity of composite ceramsite is 43.0% higher than that of 100 mesh ceramsite, and 123% higher than the conductivity of gelling acid etched fracture.
2.4 Field application
The average buried depth of KL oil and gas field reservoir in China is 7,400 m, the reservoir temperature is 168°C, the average porosity is 2.7%, and the average permeability is 0.47 mD. The reservoir is characterized by ultra deep, ultra high temperature and low permeability. In the early stage, KL Oilfield used gelling acid fracturing technology, and after acid fracturing, the gas well produced only about 40,000 m3 of natural gas per day. Six wells in KL Oilfield with similar reservoir physical properties were selected for field test of composite acid fracturing technology. On average, 100 mesh ceramsite with a weight of 600 kg, 40/70 mesh ceramsite with a weight of 150 kg and 700 m3 gelled acid were used in a single well, and the maximum injection displacement was 6 m3/min. After the completion of acid fracturing, the fracturing software is used to analyze the acid fracturing fracture parameters. The analysis results show that the fracture length of composite acid fracturing is 38% higher than that of gelled acid fracturing, and the fracture conductivity is 118% higher than that of gelled acid fracturing. The composite stimulation technology has been applied to 9 wells in carbonate and shale oil and gas reservoirs. After fracturing, the production of oil and gas wells is 210% higher than that of gelled acid fracturing, and the composite stimulation technology has achieved good stimulation effects.
3 Conclusion
(1) By combining the advantages of hydraulic fracturing and acid fracturing, using proppant to fill the fracture tip that cannot be corroded by acid fluid, and using retarded acid to corrode the rest of the fracture. The compound acid fracturing can achieve full support of the fracture, especially improve the acid fracturing effect of the fracture tip.
(2) Through the visualization experiment of proppant migration, it can be seen that the shape equilibrium height and migration length of sand dike formed by single particle size proppant are not ideal, and larger equilibrium height and migration length can be obtained by using combined particle size proppant.
(3) When 100 mesh ceramsite and 40/70 mesh ceramsite are mixed, the fracture conductivity is significantly improved, especially 123% compared with the gelled acid etching fracture. The composite acid fracturing technology has achieved good application effect in ultra deep, high temperature and low permeability oil and gas fields, which can improve the gas production of such gas fields.
(4) Compared to the existing acid fracturing and hydraulic fracturing technologies, the composite stimulation technology proposed in this article combines the advantages of the acid fracturing and hydraulic fracturing technology, which not only improves the conductivity and length of fractures, but also reduces the risk of sand plugging in low-permeability reservoir fracturing.
(5) In order to accurately describe the migration of ceramic particles in rough fractures, it is recommended to combine PIV particle imaging technology to further finely describe the migration mechanism and influencing factors of ceramic particles in different viscosity fracturing fluids.
Data availability statement
The original contributions presented in the study are included in the article/supplementary material, further inquiries can be directed to the corresponding author.
Author contributions
YW: Conceptualization, funding acquisition, project administration, resources, writing—original draft and software. Data curation, formal analysis, methodology. ZL: writing—review & editing. All authors contributed to the article and approved the submitted version.
Funding
This work was financially supported by the project of the PetroChina Southwest Oil and Gas Field Company (Grant Nos. 20200302-14, 20210302-19, 20220302-11). The funder was not involved in the study design, collection, analysis, interpretation of data, the writing of this article, or the decision to submit it for publication.
Conflict of interest
Authors YW and ZL were employed by PetroChina Southwest Oil and Gas Field Company.
Publisher’s note
All claims expressed in this article are solely those of the authors and do not necessarily represent those of their affiliated organizations, or those of the publisher, the editors and the reviewers. Any product that may be evaluated in this article, or claim that may be made by its manufacturer, is not guaranteed or endorsed by the publisher.
References
1. Wang Y, Zhou C, Yi X, Li L, Chen W, Han X. Technology and application of segmented temporary plugging acid fracturing in highly deviated wells in ultradeep carbonate reservoirs in southwest China. ACS omega (2020) 5(39):25009–15. doi:10.1021/acsomega.0c01008
2. Wang Y, Fan Y, Zhou C, Luo Z, Chen W, He T, et al. Research and application of segmented acid fracturing by temporary plugging in ultradeep carbonate reservoirs. ACS omega (2021) 6(43):28620–9. doi:10.1021/acsomega.1c03021
3. Ningning Z, Dengfa H, Yanpeng S, Haowu L. Distribution patterns and controlling factors of giant carbonate rock oil and gas fields worldwide[J]. China Pet Exploration (2014) 19(6):54.
4. Lu YUN. Controlling effect of NE strike slip fault system on reservoir development and hydrocarbon accumulation and its geological significance in the eastern Shunbei area, Tarim Basin[J]. China Pet Exploration (2021) 26(3):41.
5. Li J, Wang X, Zhou K, Wang Y, Li N, Wu Y, et al. Characteristics of ultra-deep shale reservoir of marine-continental transitional facies[J]. Pet Geology Exp (2022) 44(1):72–82.
6. Haitao L, Geng F, Shang K. Key factors and directions of exploration in the Cambrian pre-salt sequence,Tarim Basin[J]. Oil Gas Geology (2022) 43(5):1049–57.
7. Xinhua MA, Haijun YAN, Jingyuan C. Development patterns and constraints of superimposed karst reservoirs in Sinian Dengying Formation, Anyue gas field, Sichuan Basin[J]. Oil Gas Geology (2021) 42(6):1281–94.
8. Wang Y, Zhou C, Zhang H, He T, Tang X, Peng H, et al. Research and application of segmented acid fracturing technology in horizontal wells of ultra deep carbonate gas reservoirs in southwest China[C]. In: Proceeding of the International Petroleum Technology Conference; Virtual. OnePetro (2021).
9. Jianzhong LI, Bin B, Ying B, Lu X, Zhang B, Shengfei Q, et al. Fluid evolution and hydrocarbon accumulation model of ultra-deep gas reservoirs in Permian Qixia Formation of northwest Sichuan Basin, SW China[J]. Pet Exploration Dev (2022) 49(4):719–30.
10. Xiao D, Cao J, Luo B, Zhang Y, Xie C, Shuangling C, et al. Mechanism of ultra-deep gas accumulation at thrust fronts in the Longmenshan Mountains, lower Permian Sichuan Basin, China. J Nat Gas Sci Eng (2020) 83:103533. doi:10.1016/j.jngse.2020.103533
11. Qi L, Structural characteristics and storage control function of the Shun I fault zone in the Shunbei region, Tarim Basin. J Pet Sci Eng (2021) 203:108653. doi:10.1016/j.petrol.2021.108653
12. Li N, Feng Y, Liu P, Luo Z, Zhao L. Study of acid–rock reaction kinetics under high temperature and pressure conditions based on the rotating disk instrument. Arabian J Sci Eng (2015) 40(1):135–42. doi:10.1007/s13369-014-1504-x
13. Xue H, Huang Z, Zhao L, Wang H, Kang B, Liu P, et al. Influence of acid-rock reaction heat and heat transmission on wormholing in carbonate rock. J Nat Gas Sci Eng (2018) 50:189–204. doi:10.1016/j.jngse.2017.12.008
14. Deng J, Mou J, Hill AD, Zhu D. A new correlation of acid-fracture conductivity subject to closure stress. SPE Prod Operations (2012) 27(02):158–69. doi:10.2118/140402-pa
15. Aljawad MS, Zhu D, Hill AD. Modeling study of acid fracture fluid system performance. In: Proceeding of the SPE 179109 presented at the Hydraulic Fracturing Technology Conference; Texas, USA. The Woodlands (2016).
16. Hou B, Zhang R, Chen M, Kao J, Liu X. Investigation on acid fracturing treatment in limestone formation based on true tri-axial experiment. Fuel (2019) 235:473–84. doi:10.1016/j.fuel.2018.08.057
17. Zhang L, Zhou F, Mou J, Xu G, Zhang S, Li Z. A new method to improve long-term fracture conductivity in acid fracturing under high closure stress. J Pet Sci Eng (2018) 171:760–70. doi:10.1016/j.petrol.2018.07.073
18. Wang Y, Fan Y, Wang T, Ye J, Luo Z. A new compound staged gelling acid fracturing method for ultra-deep horizontal wells. [J] Gels (2022) 8(7):449. doi:10.3390/gels8070449
19. Wang Y, Yang J, Wang T, Hu Q, Lv Z, He T. Visualization experiment of multi-stage alternating injection acid fracturing. Energ Rep (2022) 8:9094–103. doi:10.1016/j.egyr.2022.07.031
20. Ye JX, Li L, Han HF, Zhang SQ, Xue H, Zhang ZC, et al. Optimization research of multistage alternating acid fracturing: A case study of reservoir reconstruction for longwangmiao Formation in moxi-longnvsi area[J]. Reservoir Eval Dev (2018) 8(3):46–50.
21. Wu Y, Hu W, Wang M, Yao L, Fang H, Jia X, et al. Composite acid fracturing technology based on flow conductivity evaluation experiments[J]. Science Technology and Engineering (2018) 20(31):12276–12780.
22. Dang L, Zhou C, Huang M, Jiang D. Simulation of effective fracture length of prepad acid fracturing considering multiple leak-off effect. Nat Gas Industry B (2019) 6(1):64–70. doi:10.1016/j.ngib.2019.01.009
23. Dong R, Wheeler MF, Ma K, Su H. A 3D acid transport model for acid fracturing treatments with viscous fingering[C]. In: SPE Annual Technical Conference and Exhibition. Virtual. OnePetro (2020).
24. Wang D, Zlotnik S, Díez P, Ge H, Zhou F, Yu B. A numerical study on hydraulic fracturing problems via theProper generalized decomposition method. CMES: Comput Model Eng Sci (2020) 122(2):703–20. doi:10.32604/cmes.2020.08033
25. Na AN, Luo P, Yongshou LI, Fang Y, Jiao K. Development of solid granular acid for the deep acid-fracturing of carbonate reservoirs[J]. Pet drilling Tech (2020) 48(2):93–7.
26. Wang Y, Zhou C, Yi X, Li L, Zhou J, Han X, et al. Research and evaluation of a new autogenic acid system suitable for acid fracturing of a high-temperature reservoir. ACS omega (2020) 5(33):20734–8. doi:10.1021/acsomega.0c00336
27. Zhao Z, Sun C, Liu Y. High-temperature-resistant diverting acid for carbonate formation fracturing in sichuan basin: a property evaluation and field study[J]. Geofluids (2022).
28. Sui Y, Cao G, Guo T, Li Z, Bai Y, Li D, et al. Development of gelled acid system in high-temperature carbonate reservoirs. J Pet Sci Eng (2022) 216:110836. doi:10.1016/j.petrol.2022.110836
29. Du J, Guo G, Liu P, Xiang G, Cheng P, Liu J, et al. Experimental study on the autogenic acid fluid system of a high-temperature carbonate reservoir by acid fracturing. ACS omega (2022) 7(14):12066–75. doi:10.1021/acsomega.2c00259
30. Qingzhi W, Yingtao Y, Feng W. Experimental study on an innovative proppant placement method for channel fracturing technique[J]. J China Univ Pet (Edition Nat Science) (2016) 40(5):112–7.
31. Wen Q, Jinjian GAO, Hua LIU, Liu X, Wang S, Wang F. Dynamic experiment on slick-water prop-carrying capacity[J]. Oil Drilling Prod Tech (2015) 37(2):97–100.
32. Barboza BR, Chen B, Li C. A review on proppant transport modelling. J Pet Sci Eng (2021) 204:108753. doi:10.1016/j.petrol.2021.108753
33. Desheng Z, Zheng Z, Feng HUI, Yuhan S, Chaoneng Z, Yuan Z. Experiment and numerical simulation on transportation laws of proppant in major fracture during slick water fracturing[J]. Oil Drilling Prod Tech (2017) 39(4):499–508.
34. Zhang K, Zhang T, Wu S, Li N, He S. Simulation of proppant transport in fracture with different combinations of particle size[J]. Reservoir Eval Dev (2019) 9(6):72–7.
35. Liu X, Zhang X, Wen Q, Zhang S, Liu Q, Zhao L. Experimental research on the proppant transport behavior in nonviscous and viscous fluids. Energy and Fuels (2020) 34(12):15969–82. doi:10.1021/acs.energyfuels.0c02753
36. Suri Y, Islam SZ, Hossain M. Effect of fracture roughness on the hydrodynamics of proppant transport in hydraulic fractures. J Nat gas Sci Eng (2020) 80:103401. doi:10.1016/j.jngse.2020.103401
37. Tingxue J, Jun Z, Wenfeng J, Linbo Z. Deep penetration acid-fracturing technology for ultra-deep carbonate oil and gas reservoirs in the Shunbei Oil and Gas Field[J]. Pet Drilling Tech (2019) 47(3):140–7.
38. Yudi G, Linbo Z, Yang W. High conductivity acid fracturing technology in ultra-deep carbonate reservoir[J]. Reservoir Eval Dev (2019) 9(6):56–60.
39. Liu M, Zhang S, Mou J, Zhou F. Wormhole propagation behavior under reservoir condition in carbonate acidizing. Transport in porous media (2013) 96(1):203–20. doi:10.1007/s11242-012-0084-z
40. Zhu W, Liu Q, Yue M, Zhang L. Calculation of fracture conductivity considering proppant influence and simulation of proppant transport in fracture[J]. Chem Eng Oil Gas (2019) 48(2):75–8.
41. Zhou J, Zhou L, Jiang T, Zhang J. Experimental study on the fracture conductivity of ultra-deep carbonate reservoirs by channel sanding acid fracturing[J]. Chem Eng Oil Gas (2019) 48(2):75–8.
Keywords: fracture length, conductivity, unconventional reservoirs, low permeability, high temperature
Citation: Wang Y and Lv Z (2023) Composite stimulation technology for improving fracture length and conductivity of unconventional reservoirs. Front. Phys. 11:1181302. doi: 10.3389/fphy.2023.1181302
Received: 07 March 2023; Accepted: 02 May 2023;
Published: 22 May 2023.
Edited by:
Chengyuan Xu, Southwest Petroleum University, ChinaReviewed by:
Xiaopeng Yan, Changzhou University, ChinaShuyu Sun, King Abdullah University of Science and Technology, Saudi Arabia
Copyright © 2023 Wang and Lv. This is an open-access article distributed under the terms of the Creative Commons Attribution License (CC BY). The use, distribution or reproduction in other forums is permitted, provided the original author(s) and the copyright owner(s) are credited and that the original publication in this journal is cited, in accordance with accepted academic practice. No use, distribution or reproduction is permitted which does not comply with these terms.
*Correspondence: Yang Wang, d2FuZ3lhbmcwOTk2QHBldHJvY2hpbmEuY29tLmNu