- Physical Sciences Division, Institute of Advanced Study in Science and Technology, An Autonomous Institute Under DST, Govt. of India, Guwahati, Assam, India
Cold atmospheric plasma (CAP) is a promising technology quite useful in many industries including biotechnology, biomedical, textiles, and food processing. The contrivance of plasma technology can be a potential game-changer to use in any possible way in these industries. This CAP technology is technically a green process with no generation of chemically harmful substances with more ecological and economic benefits. This review article will focus on the research done in the textile industry and food processing, how plasma brings in an effective change in these industrial sectors as well the as application of CAP in disinfection, sterilization, microbial inactivation, and surface modification to obtain desirable results. Recently, there have been reports of successful use of CAP technology for surface inactivation of SARS-CoV-2, plasma-activated water for disinfection of SARS-CoV-2. This article will streamline the innovations in textiles and food industries achieved using plasma technology and what gaps industries face while manufacturing. The focus will be on what research has already done while depicting the gaps and opportunities for using plasma technology in these industries and making use of it to achieve a circular economy, which is one of the major policies of the European countries. A circular economy enables manufactures to produce goods which can be reused, recycled, refurbished, and repaired rather than scrapping them after a single use. The reduction of harmful chemicals, wastewater treatment, and sterilization is achieved using plasma technology and allows reusing the resources which consequently helps to achieve most of the UN’s sustainable development goals and help society to live a sustainable and better life.
Introduction
Plasma, as regarded by all, is the fourth state of matter. It is a partially ionized gas comprising of electrons, ions, and neutral particles. Irving Langmuir first used the term plasma to this ionized gas in 1927 [1]. More than 99% of the matter of the visible universe is said to be in the plasma state. Plasma can be produced in laboratories by different techniques and predominantly by supplying electrical energy to a gas. When the voltage applied between two electrodes is high enough to cause a breakdown of the gas, a plasma is formed. Due to the very high mobility of the electrons, they can rapidly gain energy from the applied electric field and transfer their energy to the neutral particles through collisions. Once an electron hits another atom with sufficient energy, it can rip off another electron from an atom and thus will create a cascading effect, ending up with many electrons and ions, and a plasma is created. When the excited particles relax to low energy states, we see the plasma glow. Plasma breakdown voltage between the electrodes for a specific gas depends on the pressure and the distance between the electrodes, according to Paschen’s Law [2, 3] and with this breakdown voltage, electrons are generated that later contribute to electron avalanches and secondary electron emission processes [4]. Figure 1 shows the breakdown voltage for various gases as a function of the product of pressure and distance between the electrodes. As long as the applied voltage exceeds the breakdown voltage, which varies for different gases, plasma will continue to flow. Additionally, when this breakdown voltage is reached, gases lose their insulating properties and become conductors [5]. In gas plasma, breakdown voltage depends on pressure and electrode distance. Therefore, the breakdown voltage is high, when the product of pressure and electrode distance is low since few collisions will occur and the breakdown voltage is low when the product of pressure and electrode distance is high because of occurring many collisions [5]. Different gases have similar patterns of pressure and distance between electrodes, which yields a minimum product value between 130 and 1,300 Pa cm [6].
An electric field is applied to a neutral gas in order to create and maintain low-temperature plasmas in industrial and scientific settings [7].
The plasma can be classified on the ground of relative temperatures of electrons, ions, and neutrals. There are two main categories in which plasma can be classified—“thermal plasma” and “nonthermal plasma”. Thermal plasmas have electrons and heavy particles at the same temperature i.e., they are at thermal equilibrium. On the other hand, non-thermal plasmas have very high electron temperature, whereas the heavy particles i.e., ions and neutrals remain at a much lower temperature (sometimes room temperature). CAP is referred to as nonthermal plasma because electrons remain at a very high temperature than the heavy particles that are near room temperature [8]. In thermal plasma delivery, high pressures, beyond 105 Pa, require a power of around 50 MW, whereas cold plasma does not require high power for a generation [9]. The various methods to produce CAP in the lab include dielectric barrier discharge - DBD method, the Plasma Jet method, and the Corona discharge [10, 11]. Several different gases such as Argon, Helium, Air, and Nitrogen can be used to produce CAP. Various high voltage electrical excitation sources such as KHz frequency AC, DC, pulse DC, radio frequency (RF), and microwave (MW) sources are used to excite the plasma. Since the discharge occurs under atmospheric conditions, air can diffuse into the discharge regions and as a result, various reactive oxygen species (ROS) and reactive nitrogen species (RNS) such as O3, HO•, O2−, NO, N2O, NO2 is formed in the plasma phase. Also, these reactive species are formed by plasma-liquid interaction or by plasma-air interaction outside the discharge zone. These reactive species are biologically very important. Here, we will focus on the two most widely used techniques -DBD and Plasma Jet discharge in this review and we will highlight the recent advancements in plasma-activated water (PAW).
Dielectric Barrier Discharge–DBD Method: The plasma creation with the DBD method is gaining significance due to its economic benefits at the present time. It is probably one of the most valuable types of plasma technology because of its simple arrangements and adaptability for the electrodes shape and the dielectric material used [12]. DBD plasma is caused by the application of a high voltage in between two metal electrodes (high voltage terminal and ground electrode) as shown in Figure 2. One or both electrodes are surrounded by a dielectric material such as glass, quartz, polymer, mica, or artistic material [13]. Gaps in between them vary from 0.1 mm to a few centimeters and electron density in the argon plasma is in the order of 1014 cm −3 [14]. Gas pressures between 104 and 106 Pa are the normal range used in DBD activity, followed by recurrence bands fluctuating between 10 and 50 MHz and voltage adequacy fluctuating between 1 and 100 kVrms for alternating current [15].
Plasma Jet discharge: Plasma jets cover a variety of arrangements in which the plasma is generated using different gases [9, 16]. Coaxial electrodes are the most commonly used design, in which gas flows in between the electrodes. In this method, a discharge is produced between a ground electrode and a live electrode as shown in Figure 3. When power is applied to form a discharge, it ignites and operates on a feed gas that passes between an outer grounded electrode and a live electrode, consequently, a beam of discharge will be produced [5]. In this arrangement, free electrons are accelerated, which collide with molecules of gas to form reactive species. A high flow rate of gas is established between electrodes and the plasma formed between the electrode comes out into the open air with the gas flow. Plasma jets produce a constant, steady, and unvarying release of plasma at atmospheric pressure [5]. A collection of various cold plasma jet setups has been discussed in detail by Lu et. Al [17]. Typical values of plasma parameters such as electron density and temperature of CAP plasma devices vary in the 1013–1015 cm−3 and 1–10 eV ranges respectively [18–22]. Due to its simplistic model and production of cold plasma, it is highly used in the biomedical field, for example, KINPen, a CAP jet-based EU-certified medical device can reduce microbial burden significantly compared to the existing methods. KINPen uses Argon as feed gas to treat chronic wounds for patients [23].
Plasma Activated Water–PAW: The reactive species present in the plasma can be effectively used to produce PAW. The common sources to generate PAW are CAP- DBD and plasma jet. When CAP- DBD and plasma jet directly treated aqueous solutions like tap water, phosphate buffer saline, sodium chloride, and N-Acetylcysteine, then the aqueous solution is pronounced as plasma activated liquid (PAL) as shown in Figure 3. When only water is treated with plasma discharge sources pronounced as plasma-activated water (PAW) [24]. The various ROS and RNS produced in the plasma phase as well as during plasma-liquid interaction diffuse into the liquid sample during plasma treatment. Therefore, PAW also contains these reactive species, as CAP-DBD and plasma jet produce [24, 25]. Zhou et al. have demonstrated briefly the different mechanisms to generate PAW to make it more effective and the chemistry of the originated reactive species and its relative application in the biomedical field [23].
In this review, we will focus on the applications of the different plasma generating methods in some of the major industries such as food, textile, and disinfection. We will highlight the significance of utilizing plasma in these industries with a clear marking of the shortcomings in the present situation. Finally, the review will emphasize the ways of utilizing plasma in industries to achieve a circular economy as a way forward to contribute to the UN SDG.
CAP for food industry
In a busy life, people are willing to find fresh but long-lasting food. It could be possible by thermal and non-thermal technologies while preserving all the nutrients of the food. Though thermal technologies might reduce the microbes’ counts, they also degrade the quality by destroying the heat-sensitive vitamins and micronutrients [4]. Alternatively, irradiation, low-temperature plasma technique, pulsed electric field, high hydrostatic pressure, pulsed UV-light, and ultrasound processing are some non-thermal techniques for the inactivation or reduction of the microbial load on various food items. However, many issues exist with the non-thermal techniques such as in the case of microbial inactivation, irradiation can cause food poisoning, pulsed UV light has low penetrating power, pulsed electric field has a high initial cost with less effect on spores and enzymes, ultrasound can cause changes in the quality as well as physio-chemical properties of the food, high hydrostatic pressure denatures proteins and causes unfolding [26]. One of the non-thermal technologies is CAP in which high temperature is not required for microbial inactivation and ultimately preserves or has a minor effect on the color, smell, taste, and nutritional value of food [5]. CAP produced by the DBD method is an imminent technology to inactivate pathogens effectively in both cases under suitable conditions. Parameters that can affect the efficacy of CAP-DBD treatment in food processing could be factors involved in the operation-voltage, current, type of gas, relative humidity, temperature, flow rate, frequency, material, thickness, and spacing of electrodes and barrier, treatment, and storage time, headspace and volume ratio product in-package and product rolling, direct and remote exposure, hurdle treatment (synergism of different technologies); product features- surface characteristics, product type (plant or animal-based)and composition, and water content; microbiological factors- initial count, type of pathogen, growth rate [15].
The reduction of S. Typhimurium and L. monocytogenes microbes with CAP is more effective on the solid surface rather than in a liquid carrier because CAP reactive species need to diffuse within the liquid medium as the highly reactive species are not able to penetrate far into the liquid medium. However, the study by Smet et al. correspondingly shows that the food structure essentially impacts the inactivation conduct and viability of CAP [28]. The main components to inactivate the microbes in CAP are the reactive species-ROS and RNS. These reactive species attack the cell wall of the pathogens and intracellular components, making them rupture along with peptidoglycan or lipopolysaccharides oxidation [29]. Nevertheless, reactive species have been directly associated with the oxidative stress on the exterior surface of microbial cells where the cell membrane ruptures by peroxidation of lipids, inactivation of enzymes, denaturation of protein, and DNA cleavage [29]. Microbiologists use log reduction to express the relative number of living microbes that are eliminated by disinfection. Artificially injected Salmonella spp., Listeria monocytogenes, and E. coli strain O157:H7 on apples, cantaloupe, and iceberg lettuce reduces the strain by at least units by treating with atmospheric uniform glow discharge plasma [30]. If treated indirectly with gliding arc plasma, E. coli O157:H7 shows a reduction by 3 log units within 3 min of treatment [31]. In strawberries, the application of non-thermal cold plasma results in the minimal degradation of two main components: anthocyanin and ascorbic acid at 80 kV [32].
Cold plasma with the appropriate reactive species has been successfully used in meat industries to inactivate some undesirable bacteria including E. coli, Listeria monocytogenes, and salmonella spp [25]. Gorbanev et al. have applied cold atmospheric plasma to produce ready-to-use meat bresaola and achieved with the reduction of redness by 40–70% and bacteria L. innocua by up to 1.6 ± 0.5 log10 cfu/g (at 15.5–62 W for 2–60 s) [26]. Indirect plasma was also used for microbial inactivation in pork and achieved to hold bacteria for up to 20 days at 5°C; however, effects on other parameters like color and pH, were observed greater in more exposure time.
Fresh fruits and vegetables are prone to browning due to the chemical reaction that results in food wastage. The more fruits and vegetables get brown, the fewer vitamins they have. CAP successfully reduced the activity of two responsible enzymes—polyphenol oxidase and peroxidase for the browning effect on the freshly cut vegetables and fruits by approximately 90% (180 s treatment) and 85% (240 s) using, respectively as well as pH remains below the room temperature during plasma treatment [10]. A roller conveyor plasma device composed of rolling electrodes encompasses a plastic rod enveloped with silicon and aluminum sheet placed in between the high voltage electrode and the ground electrode and this device successfully inactivated the Xanthomonas campestris on a cabbage leaf [33]. Some agricultural products release ethylene gas, which reduces the freshness of the products. The plasma DBD has been used to decompose the ethylene gas by diluting it with a gas mixture of oxygen, nitrogen, and carbon dioxide, which can be further used in transportation containers. However, along with this process, the production of harmful gases such as ozone, carbon monoxide, and hydrogen was observed, but the DBD with Ag-Zeolite reduced the concentration of carbon monoxide with O3 reduction [34]. Ma et al. shows ambient result regarding enzymatic browning degradation and reduction in polyphenol oxidase activity in apple slices [35]. Surowsky et al. shows a reduction in the activity of polyphenol oxidase and peroxidase [36]. ROS, such as atomic oxygen and particularly OH radicals, can cleave peptide bonds, oxidize amino acid side chains and form protein–protein cross-linkages. Garofulić et al. demonstrated it is that evident longer exposure time of cold plasma reduce the content of anthocyanin [37]. But short treatment in large volumes causes no degradation as well as plasma-treated on sour cherry marasca juice found the highest content of anthocyanin as compared to untreated and pasteurized juice. Kovačević et al. also show that the content of anthocyanin in pomegranate juice is highest in plasma treated than in untreated one [38]. Botrytis cinerea causes fungus after mulberry harvest [39] shows CAP treatment at 0, 0.5, 1, 2, 3 min with 0, 2, 3 V on mulberry effectively reduce the growth of botrytis cinerea. CAP effectively shows auspicious results in the inactivation of S. enterica and bacillus spores on the surface of the black peppercorns and moreover, CAP does not affect the color, peperine, and oil content [40]. Degradation of Aspergillus spp. Spores on hazelnut increased with the applied reference voltage and the frequency [41]. Zahoranová et. al have shown the inhibition of different pathogens, Aspergillus flavus, Alternaria alternata, and Fusarium culmorum non the maize surface by cold atmospheric plasma and also gave surface finishing without the use of any chemicals [42]. CAP also effectively reduced the microbial count in dried herbal tea, which provides industrial relevance to CAP [43]. Table 1 comprehensively highlights the application of cold atmospheric plasma to various foods. Moreover, the inactivation of microbes is also induced by washing food with PAW which can replace the chemical sanitizer. PAW effectively disinfected the rocket salad [44], pesticide removal was observed on grapes dipped in PAW for 10 min [45], able to disinfect many meat products [46], seafood preservation and decontamination is also possible [47]. Hence, along with CAP technology, PAW io such effective to preserve and decontaminate food items.
CAP produces these reactive species at a time and synergizes all these reactive species responsible for the effective inactivation of microbes. The reactivity of these species transfers into physical and chemical processes such as particle collisions, mass transfer and complex chemical processes at the interface, and photolysis by absorbed UV photons.
Many inquiries regarding the types of species produced during plasma exposure and their particular role in the process of inactivation of the microbes actually still need to be considered. Moreover, complete knowledge of the inactivation process helps to make effective tools. In terms of cost CAP’s efficiency need to evaluate. The potential of cold plasma technology induces researchers to develop and modify all processes for nutritional, safer, and more beneficial products than conventional technology. Most eatables such as apples and strawberries are overloaded with chemicals/wax for increasing the shelf life which happens in conventional technology. CAP technology can not only sustain the structural and chemical composition of the product but also reduces the chemical release to the environment. Application of CAP to a wide range of food has been done but still, there is a lack of information regarding the physiochemical, sensorial, and nutritional properties of food. Researchers found that the CAP effect on food is very minimal, quality remains intact such as color, taste and pH. So far, it is showing positive results which increases CAP’s potential as an environment-friendly technology. Risk assessment of CAP must be conducted by authorities before it is been commercialized. Additionally, plasma in an aqueous solution generates ROS and RONS which are mainly responsible for the inactivation of pathogens and bacteria. The European Commission has no curtailments regarding the use of plasma technology to preserve organic food [60]. However, plasma also generates nitrates, nitrites, and hydrogen peroxide, which may react and produce toxins compounds such as peroxynitrous acid [34]. Hence, studies need to be done that no harmful byproducts are produced by CAP treatment and simultaneously maintain the nutritional and chemical qualities of the food. Ozone, which is one main reactive species is unstable and decomposes to a pure oxygen state and the half-life of ozone molecules varies from a few seconds to hours [61]. The unconsumed oxygen reverts to oxygen with no residuals. Ozone and NOX are produced in very low concentrations which one can find by quantification of species produced by CAP. Their production can be controlled by properly tuning the plasma reactor. Cold plasma can meet numerous expectations that the food industry requires, provided a complete knowledge of the process of operation is available. However, more studies on the utilization of CAP need to be carried out from a molecular perspective of proteins/enzymes present in both the microbes as well as the food.
CAP for disinfection
Disinfection/Sterilization of different kinds of equipment in the bio-medical field is necessary to avoid unnecessary secondary infections caused due to pathogens. Various techniques are used to sterilize medical equipment, such as the use of ethylene oxide, peracetic acid, hydrogen peroxide, formaldehyde, exposure to UV, treatment with gamma-ray, and autoclaving [4]. Table 2 signifies the different existing processes and the pros and cons of utilizing these techniques.
Plasma has broad benefits in the biomedical field. CAP effectively produces a mixture of various long-lived and short-lived reactive species which works synergistically in the plasma environment that increases its applicability. Plasma is now used prevalently to sterilize medical devices found without any alteration in the devices happen and also produce no chemical residues. However, to minimize the effect of ozone on any object or humans, the CAP device can be customized according to the requirement of the target to be treated. For example, by using an air pump activated charcoal and manganese dioxide pass through the plasma device to block or decrease the concentration of ozone [69]. It can be used to sterilize, and inactivate a large number of pathogens, and has great potential in dentistry and therapeutic also, disinfection of medical devices, beds, surgical masks, gloves, and floors [70, 71]. Hence, in comparison to the various disinfection methods CAP is a promising technology with fewer human interventions.
Recently, severe acute respiratory syndrome coronavirus 2 (SARS-CoV-2) has devastated the livelihood of many people and also led to the loss of human lives. As we are aware, this virus spreads through respiratory droplets from one person to the other and hence disinfection of the areas is highly important. According to the World health organization (WHO), there are some possible modes of transmission of SARS-COV-2 such as airborne transmission, contact and droplet transmission, and fomite transmission [72]. The most common method of disinfection is the use of sodium hypochlorite solution, but the repeated usage of huge quantities of this chemical affects the soil and human/animal health. An alternative to this chemical treatment can be achieved through CAP. Most studies found that SARS-CoV-2 virus surface inactivation is possible using CAP over many surfaces like desks and chairs. The important aspects of surface inactivation are the composition of the material, the roughness of the surface or material, and the absorptivity of the material. For example, treatment of argon-fed cold plasma on the metal surface shows higher discharge intensity at the interface which produced more species which are directly involved in the inactivation process and consequently increases the efficiency. On rough surfaces, however, the inactivation of microbes is low. Also, absorptivity plays a major role in surface inactivation like cardboard protects the SARS-CoV-2 virus from plasma discharge disrupting inactivation efficiency. So, material roughness and absorptivity are major factors which affect the surface inactivation process in the case of the SARS-CoV-2 virus and material composition is the second-most important factor. Unlike argon-fed plasma, helium-fed plasma was not able to achieve complete disinfection of SARS-COV-2 virus on metals, plastics, and cardboard even at higher treatment time [73]. The reason is Helium plasma a has much lower RONS concentration than Argon for the same working state. Therefore, the RONS concentration is also important in SARS-CoV-2 surface inactivation. No chemical is needed and Plasma is a safer method than alcohol, and UV radiation methods [73]. In addition, PAW also can be used to disinfect medical devices. Ganesh Subramanian et al. also reported the inactivation of Pseudomonas aeruginosa, bacteria which is responsible for the infection which originated in hospitals [74].
CAP-DBD can curb airborne transmission by completely inactivating the aerosols containing the virus or purifying SARS-CoV-2 RNA suspension [75]. Cortázar et al. have shown that using CAP and PAW, the SARS-CoV-2 and H1N1 influenza virus inactivation without any damage or alteration of the healthy cells [77]. Alternatively, PAW can also effectively repress the pseudovirus infection through S protein inactivation of the pseudo viruses with SARS-CoV-2 S protein used as a model [78]. The CAP is very helpful in the deactivation of SARS-CoV-2 on food or food packages and in addition, it can increase the shelf life of food [79]. Absolute deactivation of SARS-CoV-2 spike protein and RNA using CAP has been reported [80]. Disinfection of masks used to avoid SARS-CoV-2 virus achieved using hydrogen peroxide plasma [81]. Futuristic development is going on, and the need of the moment is to find the potential of CAP to curb the announced epidemic of SARS-COV-2.
CAP for textile industry
In terms of textiles and apparel, India is among the world’s most significant markets. Researchers need to analyze the limitations that this industry is facing, which not only benefits to enhance the potential of the textile industry but also helps in the economic development in India as well as throughout the world. Now, the stimulus of cold plasma technology in textiles gives a new direction to develop new finished products and improve the quality of already existing products which are ultimately beneficial to the industry as well as society also. In the future, the ecological and energy-saving complications demand for a steady substitution of numerous conventional wet science-based material handling which utilizes a lot of water, power, and releases effluents, by different types of low-alcohol and dry-completing cycles. The waste produced by the wet method is usually dumped into rivers and oceans leading to water pollution. Plasma technology also has the potential to reduce the water pollution generated by a wet chemical used in the manufacturing process. It is a completely dry process and does not release any toxins and harmful chemicals.
Plasma technology has many applications for textile advancement and modifying its properties according to the need, such as, it can enhance mechanical properties of textiles, can provide antistatic finishing, can improve surface wettability, can improve dyeing and printing sustainability, can convert normal into flame retardant fabrics, can improve adhesion [82]. With the increase in fiber production, the efforts to adopt environment-friendly production processes and technologies have been incentivized; for example, REACH (Registration, Evaluation, Authorization, and Restriction of Chemicals) initiation in European countries forced industries to tackle the environmental problem by innovation [83]. Plasma can be a game changer by modifying the conventional methods used in textile industries. In textile industries, dye lost in the effluents causes many environmental problems [84]. Here, plasma technology can remove grease or wax in fibers, which occurs in fibers naturally or synthetically. Also, it can facilitate the diffusion of dye molecules into the fiber making the dying process easier, and also results in improved intensity of the color and change in the color after washing off the textiles [85, 86]. Plasma technology can also improve dye exhaustion, the mass of the dye absorbed by the textile divided by the total initial mass of dye in the bath. In addition, enhancing dying consistency, cutting dye and water consumption, and enabling the reuse of effluents, can also significantly reduce operating costs and impact the environment [87–89]. The changes in the surface modification and chemical configuration of the dyed fabrics upon application of plasma have been studied [90–94]. The particular exposure time, applied voltage, feed gas, etc., contribute to the enhancement of dyeability [95–97]. When textiles are treated with plasma, it undergoes significant physical and chemical changes like changes in layers of the surface, structural, and physical properties. Some effects like plasma cleaning [98], plasma activation [99], plasma-assisted grafting [100], and plasma polymerization are majorly observed [101].
Antimicrobial efficiency of the fabric is usually achieved by a conventional process using salts, detergents and baths can be overcome by using DC sputtering in which no chemicals are used and the process duration is minimal. Antimicrobial efficiency sustains even after 30 cycles of laundry baths [102] for the plasma based sputtering process. Plasma technology is used to modify polypropylene fibers to increase the fixing of the copper particles on the surface of the fabric and enhance disinfection [103]. Using Argon, low-temperature plasma decolorization of denim fabrics can be achieved, with a smoother surface and is less time-consuming than the conventional process [104]. The hygroscopicity and dye adsorption ability of wool samples increased in which oxygen gas was used [105]. The space between warp and weft yarn is occluded when the surface of the fabric is first coated with aluminum and copper and then treated with low-temperature plasma without any alteration in the physical structure of the fabric [106]. The shrink-resistant and anti-felting effects on the wool fabrics were observed using low-temperature plasma [107].
Textile industries produce cotton, wool, and jute, among other materials, to provide customers with quality products at a reasonable price. Hence, they contribute significantly to economic development regarding output, employment, and foreign exchange. There are many severe problems with the textile industry worldwide concerning production. During the dyeing and printing process, workers are exposed to many toxic chemicals [108–110]. Many serious diseases, such as cancer, breathing, lung infections, and stomach infections, can be caused by the use of formaldehyde-releasing solvents. To make fire-resistant textiles, flame retardants are used [111], but they contain very harsh chemicals that harm not only people but also the environment since they do not decompose easily and become part of the food chain through the soil. Thereafter, the chemical waste produced by this industry is dumped into the rivers, disrupting aquatic life. Many developments have been made, such as replacing harmful chemicals with safer ones, using the same water again and again to avoid water wastage, etc. However, there is a dire need to find safer and cleaner technologies to reduce or diminish such severe issues which can be accomplished by using plasma technology. For example, by using the technique of plasma grafting to the surface of the polymer, the flame retardation properties can be achieved, and additionally, smoke reduction was observed [112], of the nylon fabric treated with atmospheric plasma jet increases surface roughness which enhanced dye intensity [113], thus it can help in reduced intake of dyes with enhanced color properties. Though many research works have shown that plasma technology reduces the use of chemicals in textile processing, a comprehensive evaluation of the various dyes in various water conditions (hard, soft) and pH conditions is essential to figuring out the right choice of technology and color impact on the fabrics.
Circular economy and plasma technology
The circular economy intends to depend on sustainable power, limits, tracks, and removes the utilization of poisonous chemical substances; and eliminate squandering through the cautious plan. Some simple principles effortlessly define the circular economy [114]. Some of the principles include designing waste reduction methods, building resilience through diversity and creating more think in “systems”. The main motto of the circular economy is to create products which are organic and easily eliminated from the waste cycle can help in the high-quality retention. The products should not be in the category of waste and should be able to recycle the products.
Plasma technology can be helpful in the goal of achieving a circular economy. Figure 5 shows the relationship between the plasma technology and circular economy, which achieves UNDP’s SDGS goals. Apart from being an eco-friendly technology, it is helpful in the development of manufacturing of many products which replace or reduce the inclusion of harmful chemical products. For example, in all the above-mentioned industries such as food, disinfection and textiles we can achieve circular economy provided we use plasma. CAP technology helps to use of less dye and increases absorptivity in textiles, can replace washing of food with harmful chemicals to improve shelf-life [115], can replace toxic chemical agents while synthesizing nanoparticles [116], can be utilized in wastewater treatment [117]. Plasma gasification, one of the plasma technology applications, can convert solid waste into monetary and social values for the circular economy [118], however, many research challenges do exist. The liquid plasma can convert vegetable oils into fuels [119] and thus minimizes the use of conventional sources of energy. Agriculture materials are prone to microbial hazards as they are exposed to dust, animals, and human waste, insects. The plasma technology can reduce these risk factors. The preface of plasma technology for the circular economy faces so many challenges. The best way to bring plasma technology to the circular economy is commercialization after thorough research. There should be a bridge between research and commercialization so that it is beneficial for the successful industrial future. The research should not be limited to the laboratories but should be in profit and money-oriented enterprises on a larger scale. Figure 4 compares the roles of circular economy and plasma technology in achieving the UNDP SDGs. Thus, we can achieve the UNDP SDGs goals if we can utilize plasma technology and cash upon the circular economy.
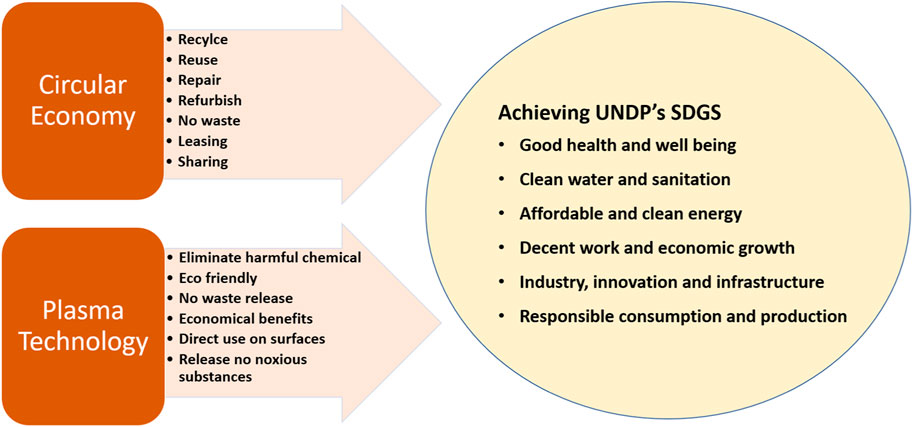
FIGURE 5. The relationship between the use of plasma technology and circular economy in achieving the UNDP’s SDGs.
Conclusion
This review explains briefly the potential of the CAP technology in the food, disinfection, and textile industries. These days, CAP is gaining attention because it is eco-friendly with no release of toxic residue and the main motive of this review is to synergize the underutilized plasma technology for the benefit of the circular economy and implementation in various industries after careful evaluation of the process parameters. A miniscule but active change can be beneficial for the society and environment where the industries can be eco-friendly with abundant financial gains. Especially, in the fast-moving consumer good (FMCG) sectors such as food and textiles, the minimal use of chemicals through plasma technology can help in organically extending the shelf-life and improve the quality of the textiles. Cost-benefit analysis determines whether the technology is effective in terms of economics. For example, compared to alternatives, plasma technology is more efficient than conventional flue gas treatment, which is a post-combustion treatment in terms of investment and operational cost. Moreover, plasma is used for various environmental applications such as air pollutant treatment, drinking water treatment, and waste treatment in terms of capital expenditure and operating costs plasma technology is more economically viable [120]. Though some ambiguities exist in the implementation of plasma technology in these industries, it is evident that these can be easily overcome with the research findings and cold plasma can be a ground-breaking and cost-effective technology.
Author contributions
KS conceptulaized the work, and KS, Re, HB, and RK have written the manuscript.
Acknowledgments
Author KS thanks DST-IASST, Guwahati for the In-house project grant and SERB, Govt. of India for the SRG grant (SRG/2020/001894 dt. 11.11.2020). Author Re thanks UGC, Govt. of India for the support for the Junior Research Fellowship.
Conflict of interest
The authors declare that the research was conducted in the absence of any commercial or financial relationships that could be construed as a potential conflict of interest.
Publisher’s note
All claims expressed in this article are solely those of the authors and do not necessarily represent those of their affiliated organizations, or those of the publisher, the editors, and the reviewers. Any product that may be evaluated in this article, or claim that may be made by its manufacturer, is not guaranteed or endorsed by the publisher.
References
1. Harry JE. Introduction to plasma technology: Science, engineering, and applications. John Wiley & Sons (2013).
2. Woo R. RF voltage breakdown and the Paschen curve. Proc IEEE (1974) 62:521. doi:10.1109/proc.1974.9459
3. Graves DB. Plasma processing. IEEE Trans Plasma Sci IEEE Nucl Plasma Sci Soc (1994) 22:31–42. doi:10.1109/27.281547
4. Garner AL, Loveless AM, Dahal JN, Venkattraman A. A tutorial on theoretical and computational techniques for gas breakdown in microscale gaps. IEEE Trans Plasma Sci IEEE Nucl Plasma Sci Soc (2020) 48:808–24. doi:10.1109/tps.2020.2979707
6. Bruggeman PJ, Iza F, Brandenburg R. Foundations of atmospheric pressure non-equilibrium plasmas. Plasma Sourc Sci Technol (2017) 26:123002. doi:10.1088/1361-6595/aa97af
7. Conrads H, Schmidt M. Plasma generation and plasma sources. Plasma Sourc Sci Technol (2000) 9:441–54. doi:10.1088/0963-0252/9/4/301
8. Boulos MI. Thermal plasma processing. IEEE Trans Plasma Sci IEEE Nucl Plasma Sci Soc (1991) 19:1078–89. doi:10.1109/27.125032
9. Coutinho NM, Silveira MR, Rocha RS, Moraes J, Ferreira MV, Pimentel TC, et al. Cold plasma processing of milk and dairy products. Trends Food Sci Technol (2018) 74:56–68. doi:10.1016/j.tifs.2018.02.008
10. Khanikar RR, Bailung H. Cold atmospheric pressure plasma technology for biomedical application. In: Plasma science and technology. London, United Kingdom: IntechOpen (2021). [Online]. Available: https://www.intechopen.com/chapters/77718 10.5772/intechopen.98895 (Accessed October 10, 2021).
11.Bermudez-Aguirre D, editor. Advances in cold plasma applications for food safety and preservation. Academic Press (2019).
12. Ziuzina D, Patil S, Cullen PJ, Keener KM, Bourke P. Atmospheric cold plasma inactivation of E scherichia coli in liquid media inside a sealed package. J Appl Microbiol (2013) 114:778–87. doi:10.1111/jam.12087
13. Chirokov A, Gutsol A, Fridman A. Atmospheric pressure plasma of dielectric barrier discharges. Pure Appl Chem (2005) 77:487–95. doi:10.1351/pac200577020487
14. Becker KH, Kogelschatz U, Schoenbach KH, Barker RJ. Non-equilibrium air plasmas at atmospheric pressure. Boca Raton: CRC Press (2004).
15. Feizollahi E, Misra NN, Roopesh MS. Factors influencing the antimicrobial efficacy of dielectric barrier discharge (DBD) atmospheric cold plasma (ACP) in food processing applications. Crit Rev Food Sci Nutr (2021) 61:666–89. doi:10.1080/10408398.2020.1743967
16. Scholtz V, Pazlarova J, Souskova H, Khun J, Julak J. Nonthermal plasma—a tool for decontamination and disinfection. Biotechnol Adv (2015) 33(6):1108–19. doi:10.1016/j.biotechadv.2015.01.002
17. Lu X, Laroussi M, Puech V. On atmospheric-pressure non-equilibrium plasma jets and plasma bullets. Plasma Sourc Sci Technol (2012) 21:034005. doi:10.1088/0963-0252/21/3/034005
18. Lu X, Naidis GV, Laroussi M, Reuter S, Graves DB, Ostrikov K. Reactive species in non-equilibrium atmospheric-pressure plasmas: Generation, transport, and biological effects. Phys Rep (2016) 630:1–84. doi:10.1016/j.physrep.2016.03.003
19. Keidar M, Shashurin A, Volotskova O, Ann Stepp M, Srinivasan P, Sandler A, et al. Cold atmospheric plasma in cancer therapy. Phys Plasmas (2013) 20(5):057101. doi:10.1063/1.4801516
20. Laroussi M, Lu X, Keidar M. Perspective: The physics, diagnostics, and applications of atmospheric pressure low temperature plasma sources used in plasma medicine. J Appl Phys (2017) 122(2):020901. doi:10.1063/1.4993710
21. Van Gessel B, Brandenburg R, Bruggeman P. Electron properties and air mixing in radio frequency driven argon plasma jets at atmospheric pressure. Appl Phys Lett (2013) 103(6):064103. doi:10.1063/1.4817936
22. Wang L, Cvetanović N, Obradović B, Ionita ER, Dinescu G, Leys C, et al. On the electron density of atmospheric pressure radio frequency dielectric barrier discharge and discharge with bare electrode. Jpn J Appl Phys (2020) 59. SHHB01.
23. Klebes M, Ulrich C, Kluschke F, Patzelt A, Vandersee S, Richter H, et al. Combined antibacterial effects of tissue‐tolerable plasma and a modern conventional liquid antiseptic on chronic wound treatment. J Biophotonics (2015) 8:382–91. doi:10.1002/jbio.201400007
24. Zhou R, Zhou R, Wang P, Xian Y, Mai-Prochnow A, Lu X, et al. Plasma-activated water: Generation, origin of reactive species and biological applications. J Phys D Appl Phys (2020) 53:303001. doi:10.1088/1361-6463/ab81cf
25. Suwal S, Coronel-Aguilera CP, Auer J, Applegate B, Garner AL, Huang JY. Mechanism characterization of bacterial inactivation of atmospheric air plasma gas and activated water using bioluminescence technology. Innovative Food Sci Emerging Tech (2019) 53:18–25. doi:10.1016/j.ifset.2018.01.007
26. Gorbanev Y, O'Connell D, Chechik V. Non‐thermal plasma in contact with water: The origin of species. Chem Eur J (2016) 22:3496–505. doi:10.1002/chem.201503771
27. Manas P, Pagán R. Microbial inactivation by new technologies of food preservation. J Appl Microbiol (2005) 98:1387–99. doi:10.1111/j.1365-2672.2005.02561.x
28. Smet C, Noriega E, Rosier F, Walsh JL, Valdramidis VP, Van Impe JF. Impact of food model (micro) structure on the microbial inactivation efficacy of cold atmospheric plasma. Int J Food Microbiol (2017) 240:47–56. doi:10.1016/j.ijfoodmicro.2016.07.024
29. Laroque DA, Seó ST, Valencia GA, Laurindo JB, Carciofi BA. Cold plasma in food processing: Design, mechanisms, and application. J Food Eng (2022) 312:110748. doi:10.1016/j.jfoodeng.2021.110748
30. Critzer FJ, Kelly-Wintenberg K, South SL, Golden DA. Atmospheric plasma inactivation of foodborne pathogens on fresh produce surfaces. J Food Prot (2007) 70:2290–6. doi:10.4315/0362-028x-70.10.2290
31. Niemira BA, Sites J. Cold plasma inactivates Salmonella stanley and Escherichia coli O157: H7 inoculated on golden delicious apples. J Food Prot (2008) 71:1357–65. doi:10.4315/0362-028x-71.7.1357
32. Misra NN, Pankaj SK, Frias JM, Keener KM, Cullen PJ. The effects of nonthermal plasma on chemical quality of strawberries. Postharvest Biol Technol (2015) 110:197–202. doi:10.1016/j.postharvbio.2015.08.023
33. Toyokawa Y, Yagyu Y, Misawa T, Sakudo A. A new roller conveyer system of non-thermal gas plasma as a potential control measure of plant pathogenic bacteria in primary food production. Food Control (2017) 72:62–72. doi:10.1016/j.foodcont.2016.07.031
34. Nishimura J, Takahashi K, Takaki K, Koide S, Suga M, Orikasa T, et al. Removal of ethylene and by-products using dielectric barrier discharge with Ag nanoparticle-loaded zeolite for keeping freshness of fruits and vegetables. Trans Mat Res Soc Jpn (2016) 41:41–5. doi:10.14723/tmrsj.41.41
35. Ma L, Zhang M, Bhandari B, Gao Z. Recent developments in novel shelf life extension technologies of fresh-cut fruits and vegetables. Trends Food Sci Technol (2017) 64:23–38. doi:10.1016/j.tifs.2017.03.005
36. Surowsky B, Fischer A, Schlueter O, Knorr D. Cold plasma effects on enzyme activity in a model food system. Innovative Food Sci Emerging Tech (2013) 19:146–52. doi:10.1016/j.ifset.2013.04.002
37. Garofulić IE, Jambrak AR, Milošević S, Dragović-Uzelac V, Zorić Z, Herceg Z. The effect of gas phase plasma treatment on the anthocyanin and phenolic acid content of sour cherry Marasca (Prunus cerasus var. Marasca) juice. LWT - Food Sci Technol (2015) 62(1):894–900. doi:10.1016/j.lwt.2014.08.036
38. Kovačević DB, Putnik P, Dragović-Uzelac V, Pedisić S, Jambrak AR, Herceg Z. Effects of cold atmospheric gas phase plasma on anthocyanins and color in pomegranate juice. Food Chem (2016) 190:317–23. doi:10.1016/j.foodchem.2015.05.099
39. Yinxin L, Can Z, Menglu H, Cui S, Jinping C, Jingyu W, et al. Effect of cold atmospheric plasma on the gray mold rot of postharvest mulberry fruit. Food Control (2022) 137:108906. doi:10.1016/j.foodcont.2022.108906
40. Hertwig C, Reineke K, Ehlbeck J, Knorr D, Schlüter O. Decontamination of whole black pepper using different cold atmospheric pressure plasma applications. Food Control (2015) 55:221–9. doi:10.1016/j.foodcont.2015.03.003
41. Dasan BG, Boyaci IH, Mutlu M. Nonthermal plasma treatment of Aspergillus spp. spores on hazelnuts in an atmospheric pressure fluidized bed plasma system: Impact of process parameters and surveillance of the residual viability of spores. J Food Eng (2017) 196:139–49. doi:10.1016/j.jfoodeng.2016.09.028
42. Zahoranová A, Hoppanová L, Šimončicová J, Tučeková Z, Medvecká V, Hudecová D, et al. Effect of cold atmospheric pressure plasma on maize seeds: Enhancement of seedlings growth and surface microorganisms inactivation. Plasma Chem Plasma Process (2018) 38(5):969–88. doi:10.1007/s11090-018-9913-3
43. Durek J, Fröhling A, Bußler S, Hase A, Ehlbeck J, Schlüter OK. Pilot-scale generation of plasma processed air and its influence on microbial count, microbial diversity, and selected quality parameters of dried herbs. Innovative Food Sci Emerging Tech (2022) 75:102890. doi:10.1016/j.ifset.2021.102890
44. Laurita R, Gozzi G, Tappi S, Capelli F, Bisag A, Laghi G, et al. Effect of plasma activated water (PAW) on rocket leaves decontamination and nutritional value. Innovative Food Sci Emerging Tech (2021) 73:102805. doi:10.1016/j.ifset.2021.102805
45. Zheng Y, Wu S, Dang J, Wang S, Liu Z, Fang J, et al. Reduction of phoxim pesticide residues from grapes by atmospheric pressure non-thermal air plasma activated water. J Hazard Mater (2019) 377:98–105. doi:10.1016/j.jhazmat.2019.05.058
46. Jung S, Lee J, Lim Y, Choe W, Yong HI, Jo C. Direct infusion of nitrite into meat batter by atmospheric pressure plasma treatment. Innovative Food Sci Emerging Tech (2017) 39:113–8. doi:10.1016/j.ifset.2016.11.010
47. Liao X, Su Y, Liu D, Chen S, Hu Y, Ye X, et al. Application of atmospheric cold plasma-activated water (PAW) ice for preservation of shrimps (Metapenaeus ensis). Food Control (2018) 94:307–14. doi:10.1016/j.foodcont.2018.07.026
48. Berardinelli A, Vannini L, Ragni L, Guerzoni ME. Impact of atmospheric plasma generated by a DBD device on quality-related attributes of “Abate Fetel” pear fruit. In Plasma for bio-decontamination, medicine and food security 2012. (2012) Dordrecht: Springer. 457–67.
49. Pankaj SK, Misra NN, Cullen PJ. Kinetics of tomato peroxidase inactivation by atmospheric pressure cold plasma based on dielectric barrier discharge. Innovative Food Sci Emerging Tech (2013) 19:153–7. doi:10.1016/j.ifset.2013.03.001
50. Misra NN, Patil S, Moiseev T, Bourke P, Mosnier JP, Keener KM, et al. In-package atmospheric pressure cold plasma treatment of strawberries. J Food Eng (2014) 125:131–8. doi:10.1016/j.jfoodeng.2013.10.023
51. Kim HJ, Yong HI, Park S, Choe W, Jo C. Effects of dielectric barrier discharge plasma on pathogen inactivation and the physicochemical and sensory characteristics of pork loin. Curr Appl Phys (2013) 13:1420–5. doi:10.1016/j.cap.2013.04.021
52. Zhuang H, Rothrock MJ, Hiett KL, Lawrence KC, Gamble GR, Bowker BC, et al. In-package air cold plasma treatment of chicken breast meat: Treatment time effect. J Food Qual (2019) 1–7. doi:10.1155/2019/1837351
53. Sarangapani C, O'Toole G, Cullen PJ, Bourke P. Atmospheric cold plasma dissipation efficiency of agrochemicals on blueberries. Innovative Food Sci Emerging Tech (2017) 44:235–41. doi:10.1016/j.ifset.2017.02.012
54. Los A, Ziuzina D, Akkermans S, Boehm D, Cullen PJ, Van Impe J, et al. Improving microbiological safety and quality characteristics of wheat and barley by high voltage atmospheric cold plasma closed processing. Food Res Int (2018) 106:509–21. doi:10.1016/j.foodres.2018.01.009
55. Yong HI, Kim HJ, Park S, Alahakoon AU, Kim K, Choe W, et al. Evaluation of pathogen inactivation on sliced cheese induced by encapsulated atmospheric pressure dielectric barrier discharge plasma. Food Microbiol (2015) 46:46–50. doi:10.1016/j.fm.2014.07.010
56. Gurol C, Ekinci FY, Aslan N, Korachi M. Low temperature plasma for decontamination of E. coli in milk. Int J Food Microbiol (2012) 157:1–5. doi:10.1016/j.ijfoodmicro.2012.02.016
57. Xu L, Garner AL, Tao B, Keener KM. Microbial inactivation and quality changes in orange juice treated by high voltage atmospheric cold plasma. Food Bioproc Tech (2017) 10:1778–91. doi:10.1007/s11947-017-1947-7
58. Noriega E, Shama G, Laca A, Díaz M, Kong MG. Cold atmospheric gas plasma disinfection of chicken meat and chicken skin contaminated with Listeria innocua. Food Microbiol (2011) 28:1293–300. doi:10.1016/j.fm.2011.05.007
59. Hajhoseini A, Sharifan A, Yousefi HR. Effects of atmospheric cold plasma on microbial growth of Listeria innocua and Staphylococcus aureus in ready-to-eat fish products. Iranian J Fish Sci (2020) 19:262–71.
60.European Commission. Plasma gas technique as electronic preservation practice of organic food and feed, EGTOP/2014, directorate-general for agriculture and rural development, directorate, B. Multilateral relations, quality policy, B. 4. Organics. (2022). Expert Group for Technical Advice on Organic Production EGTOP, Final Report on Food (III).
62. Mubarak MT, Ozsahin I, Ozsahin DU. IEEE (20192019). p. 1–4.Evaluation of sterilization methods for medical devicesAdv Sci Eng Technol Int Conferences (Aset)
63. Yadav MK, Modi A, Kedare SB. Solar autoclave for rural hospitals using aerogel as transparent insulation material. In: Proceedings of the 7th international conference on advances in energy research 2021. Singapore: Springer. (2021). 1667–77.
64. Iwaguch S, Matsumura K, Tokuoka Y, Wakui S, Kawashima N. Sterilization system using microwave and UV light. Colloids Surf B: Biointerfaces (2002) 25:299–304. doi:10.1016/s0927-7765(01)00324-1
65. Krishnamurthy K, Demirci AL, Irudayaraj J. Inactivation of Staphylococcus aureus by pulsed UV-light sterilization. J Food Prot (2004) 67:1027–30. doi:10.4315/0362-028x-67.5.1027
66. Vashkov VI, Kareev NV, Ramkova NV, Chudnova LB. A gaseous method for sterilizing medical instruments. Biomed Eng (Ny) (1974) 8:341–3. doi:10.1007/bf00566462
67. Von Woedtke T, Kramer A, Weltmann KD. Plasma sterilization: What are the conditions to meet this claim? Plasma Process Polym (2008) 5:534–9. doi:10.1002/ppap.200800013
68. Laroussi M. Sterilization of contaminated matter with an atmospheric pressure plasma. IEEE Trans Plasma Sci IEEE Nucl Plasma Sci Soc (1996) 24:1188–91. doi:10.1109/27.533129
69. Sung SJ, Huh JB, Yun MJ, Chang BM, Jeong CM, Jeon YC. Sterilization effect of atmospheric pressure non-thermal air plasma on dental instruments. J Adv Prosthodont (2013) 5(1):2–8. doi:10.4047/jap.2013.5.1.2
70. Sakudo A, Yagyu Y, Onodera T. Disinfection and sterilization using plasma technology: Fundamentals and future perspectives for biological applications. Int J Mol Sci (2019) 20:5216. doi:10.3390/ijms20205216
71. Martens PA, Galliani V, Graham G, Caputo RA. Sterilization of medical products using gas plasma technology. InSterilization of Drugs and Devices (2018) 157–95. CRC Press.
72.World Health Organization. Infection prevention and control during health care when novel coronavirus ( nCoV) infection is suspected: Interim guidance. NW, Washington, DC, United States: World Health Organization (2020). 25 January 2020.
73. Chen Z, Garcia G, Arumugaswami V, Wirz RE. Cold atmospheric plasma for SARS-CoV-2 inactivation. Phys Fluids (2020) 32:111702. doi:10.1063/5.0031332
74. Ganesh Subramanian PS, Harsha R, Manju DK, Hemanth M, Lakshminarayana R, Anand MS, et al. Characterization of plasma activated water for medical applications. Adv Mater Lett (2019) 10:919–23. doi:10.5185/amlett.2019.0041
75. Bisag A, Isabelli P, Laurita R, Bucci C, Capelli F, Dirani G, et al. Cold atmospheric plasma inactivation of aerosolized microdroplets containing bacteria and purified SARS‐CoV‐2 RNA to contrast airborne indoor transmission. Plasma Process Polym (2020) 17:2000154. doi:10.1002/ppap.202000154
76. Bisag A, Isabelli P, Laghi G, Laurita R, Dirani G, Taddei F, et al. Cold atmospheric plasma decontamination of SARS‐CoV‐2 bioaerosols. Plasma Processes and Polymers (2021). p. e2100133.
77. Cortázar OD, Megía-Macías A, Moreno S, Brun A, Gómez-Casado E. Vulnerability of SARS-CoV-2 and PR8 H1N1 virus to cold atmospheric plasma activated media. Sci Rep (2022) 12:263–2. doi:10.1038/s41598-021-04360-y
78. Guo L, Yao Z, Yang L, Zhang H, Qi Y, Gou L, et al. Plasma-activated water: An alternative disinfectant for S protein inactivation to prevent SARS-CoV-2 infection. Chem Eng J (2021) 421:127742. doi:10.1016/j.cej.2020.127742
79. Capelli F, Tappi S, Gritti T, de Aguiar Saldanha Pinheiro AC, Laurita R, Tylewicz U, et al. Decontamination of food packages from SARS-COV-2 RNA with a cold plasma-assisted system. Appl Sci (2021) 11:4177. doi:10.3390/app11094177
80. Khanikar RR, Kalita M, Kalita P, Kashyap B, Das S, Khan MR, et al. Cold Atmospheric Pressure Plasma for attenuation of SARS-CoV-2 Spike protein binding to ACE2 protein and the RNA deactivation. RSC Adv (2022) 12:9466–72. doi:10.1039/d2ra00009a
81. Ibáñez-Cervantes G, Bravata-Alcántara JC, Nájera-Cortés AS, Meneses-Cruz S, Delgado-Balbuena L, Cruz-Cruz C, et al. Disinfection of N95 masks artificially contaminated with SARS-CoV-2 and ESKAPE bacteria using hydrogen peroxide plasma: Impact on the reutilization of disposable devices. Am J Infect Control (2020) 48(9):1037–41. doi:10.1016/j.ajic.2020.06.216
83. Zille A. (2020). “Plasma technology in fashion and textiles,” in Sustainable technologies for fashion and textiles. Woodhead Publishing, 117–142.
84. Schneider K, Hafner C, Jäger I. Mutagenicity of textile dye products. J Appl Toxicol (2004) 24:83–91. doi:10.1002/jat.953
85. Karahan HA, Özdoğan E, Demir AS, Ayhan H, Seventekin NE. Effects of atmospheric plasma treatment on the dyeability of cotton fabrics by acid dyes. Coloration Technol (2008) 124:106–10. doi:10.1111/j.1478-4408.2008.00129.x
86. Hossain MM, Müssig J, Herrmann AS, Hegemann D. Ammonia/acetylene plasma deposition: An alternative approach to the dyeing of poly (ethylene terephthalate) fabrics at low temperatures. J Appl Polym Sci (2009) 111:2545–52. doi:10.1002/app.29289
87. Deshmukh RR, Bhat NV. Pretreatments of textiles prior to dyeing: Plasma processing. Rijeka, Croatia: Textile dyeing (2011).
88. Shah JN, Shah SR. Innovative plasma technology in textile processing: A step towards green environment. Res J Eng Sci (2013) 2:34–9.
89. Radetic M, Jovancic P, Puac N, Petrovic ZL. Environmental impact of plasma application to textiles. In: Journal of physics: Conference series, 71. Bristol, United Kingdom: IOP Publishing (2007). p. 012017. No. 1.
90. Ren Y, Deng J, Li ZH. Influence of the combined treatment of causticization and low temperature plasma on the properties of polyester fiber. In: Advanced materials research, 175. Bäch SZ, Switzerland: Trans Tech Publications Ltd (2011). p. 312–7.
91. Xiaoliang T, Gao Q, Xiaoli C, Zhongfu R. IEEE (20072007). p. 829.Dyeing behavior of atmospheric dielectric barrier discharge Ar-O2 plasma treated poly (ethylene terephthalate) fabricIEEE 34th Int Conf Plasma Sci (Icops)
92. El-Nagar K, Saudy MA, Eatah AI, Masoud MM. DC pseudo plasma discharge treatment of polyester textile surface for disperse dyeing. J Textile Inst (2006) 97:111–7. doi:10.1533/joti.2005.0169
93. Ghoranneviss M, Shahidi S, Anvari A, Motaghi Z, Wiener J, Šlamborová I. Influence of plasma sputtering treatment on natural dyeing and antibacterial activity of wool fabrics. Prog Org Coat (2011) 70:388–93. doi:10.1016/j.porgcoat.2010.11.017
94. Kamel MM, El Zawahry MM, Helmy H, Eid MA. Improvements in the dyeability of polyester fabrics by atmospheric pressure oxygen plasma treatment. J Textile Inst (2011) 102:220–31. doi:10.1080/00405001003672366
95. Yaman N, Özdoǧan E, Seventekin N. Atmospheric plasma treatment of polypropylene fabric for improved dyeability with insoluble textile dyestuff. Fibers Polym (2011) 12:35–41. doi:10.1007/s12221-011-0035-2
96. Carneiro N, Souto AP, Rios MJ. Evaluation of cotton fabric properties after mercerization using CORONA as a preparation step. (2021).
97. Carneiro N, Souto AP, Nogueira C, Madureira A, Krebs C, Cooper S. Preparation of cotton materials using corona discharge. J Nat Fibers (2006) 2:53–65. doi:10.1300/j395v02n04_04
98. Shahidi S, Ghoranneviss M, Moazzenchi B. New advances in plasma technology for textile. J Fusion Energ (2014) 33:97–102. doi:10.1007/s10894-013-9657-2
99. Gorjanc M, Bukošek V, Gorenšek M, Mozetič M. CF4 plasma and silver functionalized cotton. Textile Res J (2010) 80:2204–13. doi:10.1177/0040517510376268
100. Sinha E, Panigrahi S. Effect of plasma treatment on structure, wettability of jute fiber and flexural strength of its composite. J Compos Mater (2009) 43:1791–802. doi:10.1177/0021998309338078
101. Chinta SK, Landage SM, Kumar MS. Plasma technology and its application in textile wet processing. Int J Eng Res Technol (Ijert) (2012) 1:1–2.
102. Shahidi S, Ghoranneviss M, Moazzenchi B, Rashidi A, Mirjalili M. Investigation of antibacterial activity on cotton fabrics with cold plasma in the presence of a magnetic field. Plasma Process Polym (2007) 4:S1098–103. doi:10.1002/ppap.200732412
103. Shahidi S, Ghoranneviss M. Comparison between oxygen and nitrogen plasma treatment on adhesion properties and antibacterial activity of metal coated polypropylene fabrics. Fibers Polym (2012) 13(8):971–8. doi:10.1007/s12221-012-0971-5
104. Ghoranneviss M, Moazzenchi B, Shahidi S, Anvari A, Rashidi A. Decolorization of denim fabrics with cold plasmas in the presence of magnetic fields. Plasma Process Polym (2006) 3:316–21. doi:10.1002/ppap.200500061
105. Shahidi S, Ghoranneviss M, Moazzenchi B, Rashidi A, Dorranian D. Study of surface modification of wool fabrics using low temperature plasma. In: Proceedings of the 3rd international conference on the Frontiers of plasma physics and technology. (PC/5099). (2004).
106. Shahidi S, Ghoranneviss M, Moazzenchi B, Dorranian D, Rashidi A. Water repellent properties of cotton and PET fabrics using low temperature plasma of Argon. Eindhoven, Hollanda: XXVIIth ICPIG (2005). p. 18–22.
107. Shahidi S, Rashidi A, Ghoranneviss M, Anvari A, Wiener J. Plasma effects on anti-felting properties of wool fabrics. Surf Coat Technol (2010) 205:S349–54. doi:10.1016/j.surfcoat.2010.08.003
108. Husain I, Hussain J, Arif M. Environmental impact of dyeing and printing industry of Sanganer, Rajasthan (India). Turkish J Eng Env Sci (2014) 37:272–85. doi:10.3906/muh-1310-8
109. Mia R, Selim M, Shamim A, Chowdhury M, Sultana S, Armin M, et al. Review on various types of pollution problem in textile dyeing & printing industries of Bangladesh and recommandation for mitigation. J Textile Eng Fashion Technol (2019) 5:220–6. doi:10.15406/jteft.2019.05.00205
111. Weil ED, Levchik SV. Flame retardants in commercial use or development for textiles. J Fire Sci (2008) 26:243–81. doi:10.1177/0734904108089485
112. Shi L. An approach to the flame retardation and smoke suppression of ethylene–vinyl acetate copolymer by plasma grafting of acrylamide. Reactive Funct Polym (2000) 45:85–93. doi:10.1016/s1381-5148(00)00015-8
113. Wang CX, Qiu YP. Nylon dyeing using atmospheric pressure plasma technology [J]. Dyeing & Finishing. (2006) 16.
115. Pan Y, Cheng JH, Sun DW. Cold plasma‐mediated treatments for shelf-life extension of fresh produce: A review of recent research developments. Compr Rev Food Sci Food Saf (2019) 18:1312–26. doi:10.1111/1541-4337.12474
116. Boruah PJ, Kalita P, Bailung H. In-liquid plasma: A novel tool for nanofabrication. In: Plasma science and technology. London, United Kingdom: IntechOpen (2021).
117. Gururani P, Bhatnagar P, Bisht B, Kumar V, Joshi NC, Tomar MS, et al. Cold plasma technology: Advanced and sustainable approach for wastewater treatment. Environ Sci Pollut Res (2021) 28:65062–82. doi:10.1007/s11356-021-16741-x
118. Munir MT, Mardon I, Al-Zuhair S, Shawabkeh A, Saqib NU. Plasma gasification of municipal solid waste for waste-to-value processing. Renew Sustain Energ Rev (2019) 116:109461. doi:10.1016/j.rser.2019.109461
119. Meeprasertsagool P, Watthanaphanit A, Ueno T, Saito N, Reubroycharoen P. New insights into vegetable oil pyrolysis by cold plasma technique. Energ Proced (2017) 138:1153–8. doi:10.1016/j.egypro.2017.10.224
Keywords: cold atmosphere plasma, circular economy, food industry, disinfection, textile—clothing industry
Citation: Reema , Khanikar RR, Bailung H and Sankaranarayanan K (2022) Review of the cold atmospheric plasma technology application in food, disinfection, and textiles: A way forward for achieving circular economy. Front. Phys. 10:942952. doi: 10.3389/fphy.2022.942952
Received: 13 May 2022; Accepted: 15 August 2022;
Published: 13 September 2022.
Edited by:
Masaharu Shiratani, Kyushu University, JapanCopyright © 2022 Reema, Khanikar, Bailung and Sankaranarayanan. This is an open-access article distributed under the terms of the Creative Commons Attribution License (CC BY). The use, distribution or reproduction in other forums is permitted, provided the original author(s) and the copyright owner(s) are credited and that the original publication in this journal is cited, in accordance with accepted academic practice. No use, distribution or reproduction is permitted which does not comply with these terms.
*Correspondence: Kamatchi Sankaranarayanan, a2FtYXRjaGkuc2Fua2FyYW5AZ21haWwuY29t