- 1Yunnan Provincial Key Laboratory of Civil Engineering Disaster Prevention, Kunming University of Science and Technology, Kunming, China
- 2Department of Civil Engineering, Yunnan Minzu University, Kunming, China
- 3Chengguan Land and Resources Office, Yichuan County Land and Resources Bureau, Luoyang, China
- 4College of Civil Engineering, Hunan University, Changsha, China
In this study, a new fiber: polyoxymethylene fiber (POMF), was added into cement mortar to make a POM fiber-reinforced mortar (POMF-RM) material. When designing the mix proportion of POMF-RM, two factors were considered: fiber length (4, 8 and 12 mm) and dosage of POMF (volume fraction 0.24, 0.72 and 1.45%). When making the POMF-RM material, it was found that POMFs were easily dispersed into the mortar. Cubic and disc-shaped specimens of the POMF-RM material were made to conduct compression and Brazilian splitting experiments, respectively. It was found that, with increases in fiber length and volume content, the mechanical properties of the POMF-RM material were improved. Compared with the plain mortar, the elastic modulus, compressive and tensile strengths of the POMF-RM material significantly increased by 6.01, 13.18 and 5.34% at least, respectively. Among these two factors, the length of POMF played a more positive role. It was observed that the POMFs could effectively prevent the expansion of tensile cracks and significantly inhibit the complete disintegration of mortar fragments. This study showed that POMF was an excellent reinforcement material worthy of further research and application in practical engineering.
Introduction
Cementitious composites have been widely used in various engineering constructions. Although cementitious composites have excellent engineering properties, they exhibit adverse mechanical performances, such as brittleness, poor tensile resistance and cracking behaviors [1] due to their unequal strengths in tension and compression. These defects harm the durability and workability of engineering structures. In order to overcome these shortcomings, some techniques have been used, including adjusting mix proportion and addition of admixtures [2].
In addition to the above techniques, reinforcements are also a useful method to improve the mechanical properties of cementitious composites. The reinforcements added into the cementitious composites can be in the form of fibers [3], fabrics [4,5] and filling aggregates [6]. Among them, fibers can more effectively improve the tensile strengths and ductility of cementitious composites. In practical engineering, fiber-reinforced cementitious composites are easily available. They have been successfully used in various structures like underground mining pillar support [7] and composite columns [8].
On the other hand, the fiber-reinforced cementitious composites have attracted more attention from researchers. Recently, many experiments have investigated the mechanical characterizations of cementitious composites reinforced with polymer fibers, such as polyvinyl alcohol fiber (PVAF) [9], polypropylene fiber (PPF) [10], polyolefin fiber [11] and polyethylene fiber [12]. The experiments showed that the fibers enhance the ductility of cementitious composites and improve the brittle instability failure.
Polyoxymethylene (POM) fiber is a new fiber material characterized by high strength, high modulus, wear resistance, alkali resistance and long-term stability [13]. POM fiber (POMF) is a high-performance fiber with excellent comprehensive properties, which has potential application in enhancing the toughness and crack resistance of cementitious composites [5,14]. However, compared with the polymer fibers mentioned above, there are few reports on the experimental research of the POMF-reinforced cementitious composites.
As a brief preliminary study, this paper aims to investigate the mechanical characterizations of a POMF-reinforced mortar (POMF-RM) material. In this study, three lengths of POMFs were added into the cement mortar to make the POMF-RM specimens. Then, compression and Brazilian splitting tests were carried out on the POMF-RM specimens. By analyzing the test results, the deformation, strength and failure behaviors of the POMF-RM material were investigated. The interactive mechanism between the POMFs and the mortar matrix was analyzed.
Experiment Program
Materials
(1) POMF
In this study, POMF was used as reinforcement added into the mortar. POMF is a white organic polymer material with a smooth surface. Geometrically, a POMF is in a shape of short linear rod. The section diameter of a POMF is 0.2 mm, and its density is 1.41 g/cm3. POMF has excellent physical and mechanical properties. Its elastic modulus and fracture strength are in ranges of 8–10 GPa and 890–1000 MPa, respectively. It has good tensile ductility, and its elongation at break is 15%. POMFs are easy to disperse and add into cement mortar materials.
(2) Fine aggregate
This study used machine-made sand as the fine aggregates of cementitious composites. The rock for making this machine-made sand is hard limestone. The apparent density and packing densities of the machine-made sand are 2614 kg/m3 and 1569 kg/m3, respectively, and its fineness modulus is 2.92.
Mix Design and Specimen Preparation
Portland cement P. O. 52.5 had been used as the binder. The investigation emphasis was put on the influences of two factors: the length and dosage of POMF on the mechanical properties of cementitious composites. Therefore, all specimens used in the experiments adopt the same water binder ratio, 0.46.
Table 1 shows the mix proportion for making the POMF-reinforced mortar (POMF-RM) material. Two factors: three lengths of fibers and three dosages in quality content are completely orthogonally mix-designed. Therefore, nine kinds of cement mortars containing POMF were prepared in this study. In order to carry out the reference experiment, plain mortar (PM) material without any POMF was made. In Table 1, this PM material is represented by a quality content of 0 g.
Three different POMF lengths (4, 8 and 12 mm) and three dosages in quality content (1, 3 and 6 g) were used in making the POMF-RM material. The average density of the POMF-RM specimens prepared using the mix proportion in Table 1 is about 2.39 g/cm3. In this case, the volume fractions of the POMF in the prepared POMF-RM specimens are 0.24, 0.72 and 1.45%, respectively, corresponding to the three dosages in quality content (1, 3 and 6 g). Specific symbols are used to identify these mixes for simplicity and clarity. For example, POM8-RM_0.72 indicates that this group of POM-RM specimens was made of POMFs with a length of 8mm, and the POMF volume fraction is 0.72%. Other mixes have the same naming rules.
In this experimental investigation, two types of specimens were made. One is the standard cubic specimen with side lengths 70.7 mm × 70.7 mm × 70.7 mm. The cubic specimens were made for conducting the compression tests to obtain the compressive strengths of the POMF-RM material. Making cubic specimens and testing were conducted according to the Chinese standard GB/T 50,081-2019 Standard for Test Methods of Concrete Physical and Mechanical Properties.
Brazilian splitting test is an indirect testing method widely used to measure the tensile strengths of rock materials. In this study, this testing method was adopted to measure the tensile strengths of the POMF-RM material. By referring to the Chinese standard DL/T 5368-2015 Code for rock tests of hydroelectric and water conservancy engineering, disc-shaped specimens of the POMF-RM material with a cross-sectional diameter of 100 mm and a height of 50 mm were made for conducting the Brazilian splitting tests.
Test Apparatus and Testing Procedures
A microcomputer-controlled servo testing machine performed the compression and Brazilian splitting tests. The microcomputer of the testing machine can read and record the test data. By analyzing these data, the stress-strain curves of the specimen can be obtained.
This study adopted the displacement-controlled loading mode for conducting the tests. The loading rate was set to 0.1 mm/min. Then, a test started. Continuously applied load on a specimen to the residual deformation stage with a slow change in load, stopped loading, and then unloaded. So far, an experiment has been completed. Then, the loading device was adjusted to a proper position and removed the specimen.
Repeat the above steps for the next experiment. Three repeated procedures were conducted for the same experiment, and the average value was taken as the experimental result. In the experiment, the experimental data that is quite different from the general results should be discarded to reduce the influence of error on the experimental results.
Test Results and Analysis
Deformation Behavior
The cubic specimens with side lengths 70.7 mm × 70.7 mm × 70.7 mm were used to conduct the compression tests. The mean stress
where
Using Eq. 1 to analyze the test data of vertical forces and displacements, the stress-strain curves of the cubic specimens can be obtained and plotted in Figure 1. Like the rock materials [15,16], the stress-strain curves of the POMF-RM material (see Figure 1) can be roughly divided into four stages by characteristic stress thresholds, as schematically illustrated in Figures 1C. They can be marked with the initial crack closure stress
(1) From
(2) From
where,
(3) From
(4) From
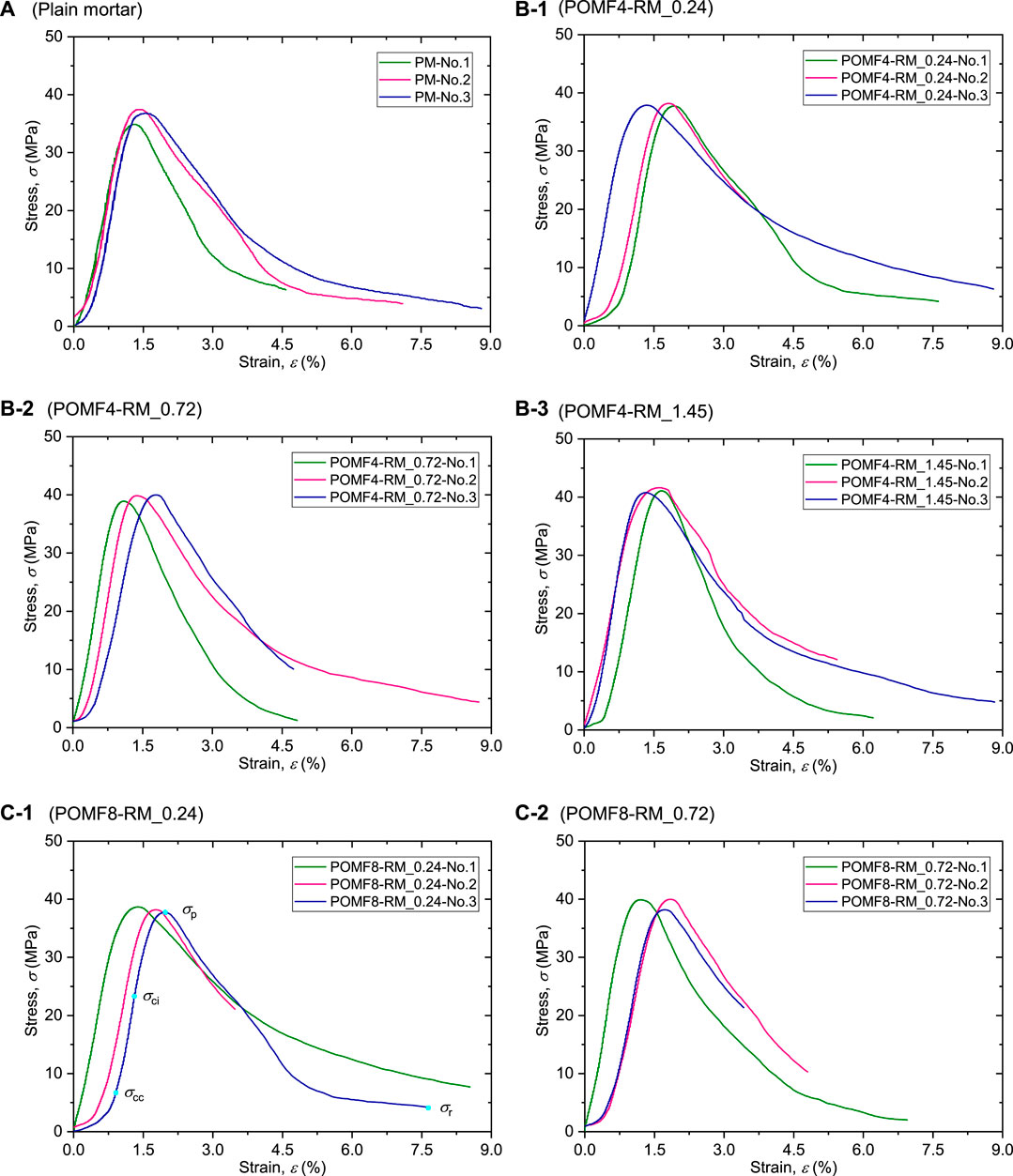
FIGURE 1. Testing stress-strain curves of the studied materials (A) Reference group of PM without POMFs (B) Group of POMF4-RM (C) Group of POMF4-RM (D) Group of POMF12-RM.
Based on Eq. 2, the test data in the linear elastic deformation stage were adopted to calculate the elastic moduli of the studied materials, which are given in Table 2. When the POMF volume fraction is 0.24%, the elastic moduli of the POMF-RM material with POMFs of different lengths (4, 8 and 12 mm) are 4.24, 4.43 and 4.76 GPa, increasing by 1.92, 6.49 and 14.42% respectively compared with that (4.16 GPa) of the PM material.
When the POMF volume fraction is 0.72%, the elastic moduli of POMF4-RM, POMF8-RM and POMF12-RM are 4.33, 4.48 and 4.73GPa, increasing by 4.09, 7.69 and 13.70% higher than that of PM, respectively. When the POMF volume fraction is 1.45%, the elastic moduli of POMF4-RM, POMF8-RM and POMF12-RM are 4.41, 4.51 and 4.55GPa, increasing by 6.01, 8.41 and 9.37% compared to that of PM, respectively.
It is observed from Table 2 that, under the same POMF volume fraction, the elastic stiffness of POMF12-RM significantly improves than that of POMF4-RM and POMF8-RM. This is because the addition of POMF inhibits the micro-crack propagation in the mortar matrices. Within the dosage range used in this study, the maximum elastic modulus is 4.76GPa, belonging to POMF12-RM_0.24. In this case, the benefit of POMFs on the improvement of the mortar’s elastic modulus is the most significant.
By analyzing the data in Table 2, among the two factors: fiber length and content, the effect of fiber length on the elastic properties of POM-RM is stronger than that of fiber content. Compared with the volume content, the length of POMF has advantages in strengthening the elastic modulus of mortar material. Therefore, POMF with a longer length is preferred under the exact dosage, achieving better mechanical properties.
Compressive Strength
Table 2 and Figure 2A show the effects of POMF length and dosage on the compressive strength of the POMF-RM material. The mean compressive strength of the PM material is 36.36 MPa. When the POMF volume fraction is 0.24%, the mean compressive strengths of POMF4-RM, POMF8-RM and POMF12-RM are 37.93, 38.20 and 42.62MPa, which increase by 4.31, 5.05 and 17.19% than that of PM specimens, respectively. When the POMF volume fraction is 1.45%, POMF has the most significant effect on improving the compressive strength. In this dosage condition, the mean compressive strengths of POMF4-RM, POMF8-RM and POMF12-RM are 41.16, 43.55 and 46.79MPa, respectively. Compared with the mean compressive strength 36.36 MPa of the PM material, their compressive strengths significantly increase by 13.18, 19.77 and 28.67%, respectively.
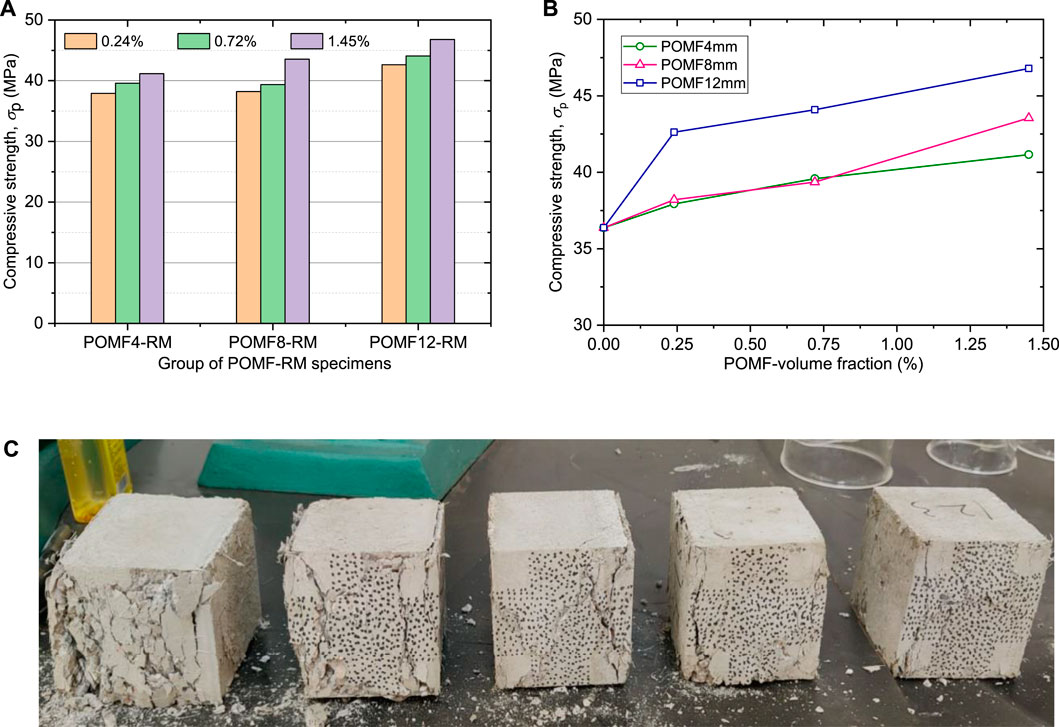
FIGURE 2. (A) Histogram showing the compressive strength of the POMF-RM material (B) Effects of POMF volume fraction on the compressive strength of the POMF-RM material (C) A photo showing the failed mortar specimens.
Figure 2B shows that the compressive strengths of the POMF-RM material raise linearly with the increase of the POMF volume fraction from 0.24 to 1.45%. Meanwhile, in the range from 0 to 0.24%, the strengthening effects of 12 mm-length POMFs on the compressive strength is greater than that of POMFs with lengths of 4 and 8 mm. Overall, within the range of POMF volume fractions adopted in this study, the compressive strength differences between POMF4-RM and POMF8-RM are relatively small. The 12 mm-length POMF has a significant advantage over POMFs with the other two lengths.
The enhancing effects of POMF on mortar strength are attributed to the POMFs embedded into the cement mortar matrices, hindering the transverse expansion of the vertical cracks in the specimens caused by splitting tension. The bonding and interlocking forces between fibers and mortar matrices are enhanced by increasing the POMF volume content and length. This mechanism significantly improves the compressive strength of mortar materials.
Splitting Tensile Strength
In the Brazilian splitting test, the tensile strength
where,
Brazilian splitting tests are used to measure the tensile strengths of POMF8-RM material, as listed in Table 2. It shows that the mean tensile strength of PM material is 1.31 MPa. Overall, with the increase of the volume contents of the 8 mm-length POMFs, the tensile strengths of the POMF8-RM material significantly improve. When the volume content reaches 1.45%, the tensile strength of the POMF8-RM material is 1.38MPa, which is slightly increased by 5.34% compared with the PM material.
Table 2 indicates that POMF has a positive effect on the tensile strength of mortar material. The mechanism may contribute to that POMFs alleviate the stress concentration at the crack tips and delay the initiation and propagation of tensile cracks in the cement mortar matrices. If POMFs are employed in practical engineering, they would effectively improve the tensile bearing capacity of structural members.
Post-Peak Failure Behavior
Method of Evaluating Brittleness
Using the method of evaluating rock brittleness proposed by Tarasov and Potvin [17], the effect of POMF on the failure brittleness of mortar material can be evaluated. Referring to Tarasov and Potvin [17] and by analyzing the stress-strain curves of the POMF-RM material, the post-peak stability behaviors of the POMF-RM material are regulated as Class Ⅰ.
For the Class Ⅰ instability behavior of a material, Tarasov and Potvin [17] proposed a brittleness index
Brittleness of the POMF-RM Material
Using the method mentioned above, the brittleness index values of the POMF-RM and PM materials in the post-peak deformation stage are estimated, as listed in Table 2. The brittleness index
For POMF4-RM material, when the POMF volume fraction increases from 0.24 to 1.45%, the brittleness index increases from 2.37 to 2.43. For POMF8-RM material, as the POMF volume fraction increases from 0.24 to 0.72%, the brittleness index increases from 2.69 to 2.71. However, as the POMF volume fraction increases from 0.72 to 1.45%, the brittleness index decreases to 2.67. For POMF12-RM, when the POMF volume fraction increases from 0.24 to 1.45%, the brittleness index decreases from 2.60 to 2.53.
Therefore, for 12 mm- and 8 mm-length POMFs, the addition of fibers does improve the brittleness of mortar material. However, the increase of volume fraction cannot ensure the continuous improvement of ductility of POMF12-RM and POMF8-RM materials. In fact, within the mix proportion range of this study, when the volume fraction of 8 mm-length POMF is 0.72%, the POMF-RM material reaches the maximum brittleness index, which is 2.71.
This indicates that POMF8-RM_0.72 is the optimal content to achieve the best ductility of mortar material. When the mortar material is loaded to damage in the post-peak deformation stage, the crack width is easy to expand beyond 4mm, so 4 mm-length POMFs cannot effectively prevent the expansion of the mortar cracks. Under the same dosage, the number of 12 mm-length POMFs is less than 8 mm-length POMFs, which cannot be densely distributed in the mortar matrices to prevent the generation of microcracks. POMF8-RM_0.72 is an intermediate state of mixed proportions, which can make up for the deficiencies in two aspects, so it has a significant effect on improving the ductility of the mortar material.
Failure Modes of the POMF-RM Material
The photo in Figure 2C shows the failed specimens of the POMF-RM material. From left to right, these failed specimens are POMF4-RM_1.45, POMF12-RM_0.24, two of POMF12-RM_0.72 and POMF12-RM_1.45. Overall, these cubic POMF-RM specimens exhibit severe failures, with fractures running vertically through the specimens along the loading direction. The fracture directions indicate that these POMF-RM specimens encounter severe splitting-tension failures. However, these damaged POMF-RM specimens were not completely dispersed. POMFs can be seen in the splitting-tension cracks connected to mortar fragments, preventing them from completely disintegrating.
It is observed that the crack densities and sizes decrease with the increase of POMF volume content. When the POMF volume content is small, the damage degree is more severe. For instance, POMF12-RM_0.24 is more destructive than POMF12-RM_1.45. The increase of POMF volume content is conducive to inhibiting the failure of POMF-RM material.
Conclusions
This study experimentally investigates the mechanical characterizations of a POMF-RM material under different mix proportions. The conclusions can be summarized as follows:
1. Increases in POMF length and volume content can improve the elastic properties of the mortar material. Under the condition of POMF12-RM_0.24, the elastic modulus of POMF-RM material reaches the maximum, which is 4.76GPa, increasing significantly by 14.42% higher than that of PM material.
2. With the increase of POMF length and volume content, the compressive and tensile strengths of the POMF-RM material increase significantly. POMFs can jointly work with the mortar matrix and block the transverse expansion of cracks, thus improving the strengths of the POMF-RM material.
3. The PM and POMF-RM materials exhibit semibrittle failure behaviors in the post-peak deformation stage. The POMF8-RM_0.72 material has the maximum brittleness index, which is 2.71. This is a significant ductility improvement compared to plain mortar material.
4. Under compression testing conditions, POMF-RM specimens exhibit a splitting-tension failure behavior. It is observed that the POMFs connect the mortar fragments and prevent the complete disintegration of the POMF-RM material. This indicates that POMF can effectively prevent the expansion of tensile cracks in the mortar material and inhibit the final damage.
Data Availability Statement
The raw data supporting the conclusions of this article will be made available by the authors, without undue reservation.
Author Contributions
Conception and design of study was mainly contributed by SZ and RG. Experimental implementation was mainly contributed by TL, BD and JZ. Drafting the manuscript was mainly contributed by JZ and TL.
Funding
This study is financially supported by China Postdoctoral Science Foundation (Grant No. 2020M673589XB).
Conflict of Interest
The authors declare that the research was conducted in the absence of any commercial or financial relationships that could be construed as a potential conflict of interest.
Publisher’s Note
All claims expressed in this article are solely those of the authors and do not necessarily represent those of their affiliated organizations, or those of the publisher, the editors and the reviewers. Any product that may be evaluated in this article, or claim that may be made by its manufacturer, is not guaranteed or endorsed by the publisher.
References
1. Gehri N, Mata-Falcón J, Kaufmann W. Refined Extraction of Crack Characteristics in Large-Scale concrete Experiments Based on Digital Image Correlation. Eng Structures (2022) 251:113486. doi:10.1016/j.engstruct.2021.113486
2. José Oliveira M, Ribeiro AB, Branco FG. Combined Effect of Expansive and Shrinkage Reducing Admixtures to Control Autogenous Shrinkage in Self-Compacting concrete. Construction Building Mater (2014) 52:267–75. doi:10.1016/j.conbuildmat.2013.11.033
3. Afroughsabet V, Geng G, Lin A, Biolzi L, Ostertag CP, Monteiro PJM. The Influence of Expansive Cement on the Mechanical, Physical, and Microstructural Properties of Hybrid-Fiber-Reinforced concrete. Cement and Concrete Composites (2019) 96:21–32. doi:10.1016/j.cemconcomp.2018.11.012
4. Bernat-Maso E, Gil L, Mercedes L, Escrig C. Mechanical Properties of Pre-stressed Fabric-Reinforced Cementitious Matrix Composite (PFRCM). Construction Building Mater (2018) 191:228–41. doi:10.1016/j.conbuildmat.2018.09.210
5. Zhang W, Xu X, Wang H, Wei F, Zhang Y. Experimental and Numerical Analysis of Interfacial Bonding Strength of Polyoxymethylene Reinforced Cement Composites. Construction Building Mater (2019) 207:1–9. doi:10.1016/j.conbuildmat.2019.02.122
6. Kaur G, Pavia S. Physical Properties and Microstructure of Plastic Aggregate Mortars Made with Acrylonitrile-Butadiene-Styrene (ABS), Polycarbonate (PC), Polyoxymethylene (POM) and ABS/PC Blend Waste. J Building Eng (2020) 31:101341. doi:10.1016/j.jobe.2020.101341
7. Cao S, Zheng D, Yilmaz E, Yin Z, Xue G, Yang F. Strength Development and Microstructure Characteristics of Artificial concrete Pillar Considering Fiber Type and Content Effects. Construction Building Mater (2020) 256:119408. doi:10.1016/j.conbuildmat.2020.119408
8. Ke X, Xu D, Cai M. Experimental and Numerical Study on the Eccentric Compressive Performance of RAC-Encased RACFST Composite Columns. Eng Structures (2020) 224:111227. doi:10.1016/j.engstruct.2020.111227
9. Zhou Y, Huang J, Yang X, Dong Y, Feng T, Liu J. Enhancing the PVA Fiber-Matrix Interface Properties in Ultra High Performance concrete: An Experimental and Molecular Dynamics Study. Construction Building Mater (2021) 285:122862. doi:10.1016/j.conbuildmat.2021.122862
10. Karimipour A, Ghalehnovi M, de Brito J, Attari M. The Effect of Polypropylene Fibres on the Compressive Strength, Impact and Heat Resistance of Self-Compacting concrete. Structures (2020) 25:72–87. doi:10.1016/j.istruc.2020.02.022
11. Rucka M, Wojtczak E, Knak M, Kurpińska M. Characterization of Fracture Process in Polyolefin Fibre-Reinforced concrete Using Ultrasonic Waves and Digital Image Correlation. Construction Building Mater (2021) 280:122522. doi:10.1016/j.conbuildmat.2021.122522
12. Ye J, Cui C, Yu J, Yu K, Dong F. Effect of Polyethylene Fiber Content on Workability and Mechanical-Anisotropic Properties of 3D Printed Ultra-high Ductile concrete. Construction Building Mater (2021) 281:122586. doi:10.1016/j.conbuildmat.2021.122586
13. Cao L, Wang Y, Wang Y. The Development and Application of Polyoxymethylene Fiber. Synth Techn Appl (2008) 23:38–41. in Chinese.
14. Liu L, Hou S, Jing W, Luo-xing W. Study on the Flexural Performance of Polyoxymethylene Fiber Reinforced Concrete. J Wuhan Textile Univ (2013) 26:35–8. in Chinese.
15. Cai M, Kaiser PK, Tasaka Y, Maejima T, Morioka H, Minami M. Generalized Crack Initiation and Crack Damage Stress Thresholds of Brittle Rock Masses Near Underground Excavations. Int J Rock Mech Mining Sci (2004) 41:833–47. doi:10.1016/j.ijrmms.2004.02.001
16. Eberhardt E, Stead D, Stimpson B. Quantifying Progressive Pre-peak Brittle Fracture Damage in Rock during Uniaxial Compression. Int J Rock Mech Mining Sci (1999) 36:361–80. doi:10.1016/s0148-9062(99)00019-4
Keywords: polyoxymethylene fiber, POMF-reinforced mortar, mechanical characterizations, brittleness evaluation, experimental investigation
Citation: Zhang J, Liu T, Dong B, Zhou S and Guo R (2022) Experimental Investigation of Mechanical Characterizations of a POM Fiber-Reinforced Mortar Material. Front. Phys. 10:837355. doi: 10.3389/fphy.2022.837355
Received: 16 December 2021; Accepted: 14 February 2022;
Published: 03 March 2022.
Edited by:
Qingxiang Meng, Hohai University, ChinaReviewed by:
Chuanqing Fu, Zhejiang University of Technology, ChinaGuojian Liu, Suzhou University of Science and Technology, China
Copyright © 2022 Zhang, Liu, Dong, Zhou and Guo. This is an open-access article distributed under the terms of the Creative Commons Attribution License (CC BY). The use, distribution or reproduction in other forums is permitted, provided the original author(s) and the copyright owner(s) are credited and that the original publication in this journal is cited, in accordance with accepted academic practice. No use, distribution or reproduction is permitted which does not comply with these terms.
*Correspondence: Rongxin Guo, Z3VvcnhAa211c3QuZWR1LmNu