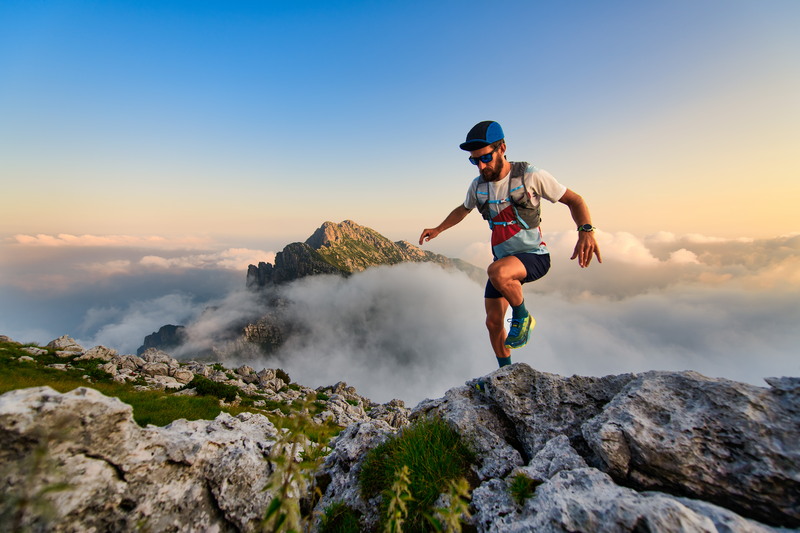
95% of researchers rate our articles as excellent or good
Learn more about the work of our research integrity team to safeguard the quality of each article we publish.
Find out more
MINI REVIEW article
Front. Phys. , 22 November 2022
Sec. Physical Acoustics and Ultrasonics
Volume 10 - 2022 | https://doi.org/10.3389/fphy.2022.1068838
This article is part of the Research Topic Programmable Elastic Metamaterials for Wave Control and Device Applications View all 11 articles
As an important tool for monitoring the marine environment, safeguarding maritime rights and interests and building a smart ocean, underwater equipment has developed rapidly in recent years. Due to the problems of seawater corrosion, excessive deep-sea static pressure and noise interference in the marine environment and economy, the applicability of manufacturing materials must be considered at the beginning of the design of underwater equipment. Piezoelectric metamaterial is widely used in underwater equipment instead of traditional materials because the traditional materials can not meet the application requirements. In this paper, according to the application range of piezoelectric metamaterials in underwater equipment, the current application of piezoelectric metamaterials is reviewed from the aspects of sound insulation and energy conversion. On this basis, the future development prospect of piezoelectric metamaterials in underwater equipment is introduced.
In recent years, with the rapid development of the world economy, land resources are becoming more and more scarce. Researchers have turned their attention to the ocean for resource exploitation. The development of marine resource exploration has become more and more rapid. Many marine technologies and underwater equipment (UE) have been rapidly developed. As UE continues to operate in the ocean for longer periods, researchers have found that a large number of equipment cannot meet the requirements because the equipment is made of traditional materials. The emergence of piezoelectric metamaterials (PMs) has solved many problems with their unique properties, so it has been rapidly applied to UE.
Metamaterial is a kind of artificially designed material with special structure, which can achieve singular or anomalous properties that ordinary materials do not have through a certain spatial arrangement. Metamaterials generally have such characteristics as band gap, waveguide, negative refraction, negative modulus, negative density, hyperlens, acoustic focusing, acoustic stealth and topological states [1, 2]. In the past few decades, left-handed materials [3], photonic crystals, phononic crystals [4], time crystals and even metasurfaces [5] can be classified as metamaterials. They have a very promising future in many fields such as communication, medicine, defense and military, aerospace and remote sensing. Metamaterials generally select existing materials and design new microstructures to achieve superior and anomalous functions. The selection of materials should follow the following rules. High modulus generally corresponds to high operating frequency, low modulus generally corresponds to low operating frequency and the large impedance difference between different component phases generally corresponds to a wider bandwidth gap. In order to carry out active control, intelligent materials such as piezoelectric material and shape memory alloy are generally selected. Compared with other smart materials, piezoelectric materials have outstanding advantages such as fast response speed, high control precision, small size and large market. The excellent electro-mechanical coupling effect of piezoelectric materials makes it possible to use different external circuits to change the mechanical properties of piezoelectric materials and then regulate and control various aspects of metamaterials [6].
The structure of PM is a kind of intelligent structure and its local resonance band gap has the characteristics of active tunability, which can meet the requirements of structural vibration frequency changing with the environment. The structure of PM has the characteristics of small additional mass and intelligently tunable band gap, which makes it have obvious advantages compared with other types of materials [7]. PM is a kind of acoustic metamaterial, and acoustic metamaterial is a medium composed of multiple materials with negative mass density, negative bulk modulus and other properties designed based on the principle of local resonance [8]. When the elastic wave in a specific frequency range propagates in the structure, it will cause the resonance phenomenon in the local resonance unit [9], which hinders the propagation of the elastic wave and generates a band gap. The band gap properties of PMs can be used to make sound insulation materials for UE. At the same time, the band gap characteristic is used to collect the vibration energy of elastic waves within a specific frequency range, and the vibration energy is confined to the local resonance unit and converted into electric energy by piezoelectric materials. The piezoelectric conversion properties of this PM can be used for piezoelectric sensors, underwater transducers, hydrophones and other equipment.
This paper is organized as follows. Section 2 introduces the band gap properties and piezoelectric conversion properties of PMs; Section 3 presents the research on the use of PMs as sound insulation and energy conversion functions in UE; Section 4 concludes and discusses the future directions of PMs in UE.
Acoustic metamaterial is a kind of artificial composite structure material, which is obtained by combining a variety of materials with different elastic modulus. It is a new functional material. When the elastic wave in a specific frequency range propagates in the structure, the elastic wave band gap will be generated as shown in Figure 1 [10]. The band gap can inhibit and absorb the elastic wave propagation in the relevant frequency range. The elastic band gap of acoustic metamaterial is generated by two main mechanisms, Bragg scattering mechanism and local resonance mechanism respectively. According to the different principles of band gap generation, acoustic metamaterial can be divided into Bragg scattering phononic crystals and local resonance acoustic metamaterial. Bragg scattering phononic crystals due to the Bragg reflection of the structure. When the wavelength of the propagating elastic wave is close to the lattice coefficient of the structure, the band gap will be generated, which has a strong inhibition and absorption effect on the elastic wave. For the local resonance metamaterial, the band gap is mainly generated by the local resonance element inside it. When the frequency of the elastic wave propagating in the local resonance element is close to its resonance frequency, the local resonance element will resonate under the action of the vibration energy of the elastic wave. Resonance will absorb vibration energy, so that elastic waves cannot continue to propagate forward and form band gap [11–15].
FIGURE 1. (A) phononic crystal (B) The contour of the phononic crystal is composed of Helmholtz resonator (C) Low resonant frequency band gap showing negative stiffness (D) Frequency position corresponding to band gap.
The PM is a type of acoustic metamaterial, so it has the properties of an acoustic metamaterial. This will cause resonance phenomenon in its local resonance unit, resulting in band gap that hinder the propagation of elastic waves. PMs are smart materials with excellent electro-mechanical coupling effect that allow the band gap of PMs to be regulated by changing the mechanical properties of the PM with different external circuits [6].
The tunable band gap of PMs allows them to better adapt to environmental changes, broaden the operating frequency range and overcome the serious drawbacks of passive metamaterials working at a single frequency or narrow band [16]. According to the material and structural characteristics, the bandgap performance of metamaterial structures can be generally classified into fixed bandgap characteristics and tunable bandgap characteristics [17]. Fixed bandgap metamaterial structures have been studied for many years [18–22]. The materials and structures required are some common ones, such as beam-plate composite metamaterial structures [23] and rod-beam composite metamaterial structures [24]. However, once the structure and model parameters of the metamaterial are determined, the position and width of the band gap are determined, which greatly limits its application in UE. Therefore, the metamaterial structure must have band gap tunability and this property is also very useful in practice.
Tunable band gap of metamaterial structures has been studied. Generally, the stiffness or inertia of the metamaterial structure is adjusted by special technical means and thus the position and width of the band gap can be adjusted. The first studies on tunable metamaterials started by Goffaux and Vigneron [25], who proposed to rotate a non-axisymmetric solid scatterer by a certain angle to change the band gap width for fluid-solid phonon crystals. In addition to adjusting the mechanical properties of metamaterials by rotating scatterers [26–28], changing the stiffness or shape of structures by applying external loads is also an effective method [29–32]. For example, Wang et al. [33] used post-buckling deformation to realize the regulation of the local resonance type band gap. Bertoldi et al. [34, 35] increased the bandgap width by compression of porous soft material structures with negative Poisson’s ratio. As shown in Figure 2, Shan et al. [36] studied the porous structure of triangular circular hole array and effectively tuned the elastic wave propagation in the structure by controlling the loading direction to enhance the tunability of the system’s dynamic response. Meaud [37] studied the propagation of elastic waves in a lattice with alternating linear and nonlinear springs.
FIGURE 2. Schematic of the basic folding mechanisms in a rigid kagome network. The basic unit cell for each folding mechanism is outlined in black. The color of the triangles corresponds to their rotation. (A) Mode with a basic cell of size 1 × 1; (B) Mode with a basic cell of size 2 × 1; (C) Mode with a basic cell of size 4 × 1; (D) Mode with a basic cell of size 2 × 2; (E) Mode with a basic cell of size 2 × 2 [36].
The band gap can also be controlled indirectly through the properties of the piezoelectric material. Active control of the band gap of a nonlinear piezoelectric spring model using positive and negative proportional control strategies is proposed. Nimmagadda proposed a composite structure composed of periodic lattice and local resonators. The two element structures have different dependence on temperature. The opening and closing of the band gap can be controlled by controlling the temperature, because the elastic modulus of the two element structures will change with temperature. Xia et al. [38] studied the effect of water temperature on the local resonance band gap and negative bulk modulus of acoustic metamaterials, and the local resonance band gap and negative bulk modulus were regulated by adjusting the water temperature.
PMs are metamaterials that use piezoelectric materials to design metamaterial structures. Metamaterials with the desired bandgap position and width can be obtained by an active control strategy. Piezoelectric materials not only give metamaterials intelligence but also expand the functional scope of metamaterials, so that related equipment has a variety of superior properties at the same time, which can effectively promote the multi-functionalization of equipment.
Among many intelligent materials, piezoelectric materials have a special electro-mechanical coupling effect and the equivalent circuit of piezoelectric materials is shown in Figure 3. They can be found in alloys or piezoelectric ceramics, soft polymers and conductors or semiconductors. There is no doubt that it is the most well-researched, the most mature and the most widely used intelligent material [39]. Common piezoelectric materials can be divided into three categories: piezoelectric crystals (such as quartz crystals), piezoelectric ceramics and piezoelectric polymers. They are used in different fields and play different values according to their different properties and states. The electro-mechanical coupling effect of piezoelectric materials is that under the action of mechanical pressure, surface charges will appear and form an electric field in the body, which is called the positive piezoelectric effect. Piezoelectric materials can also deform in response to an electric field, which is called the inverse piezoelectric effect. The electro-mechanical coupling effect of piezoelectric materials is that surface charges will appear under the action of mechanical pressure and an electric field will be formed in the body, which is called the positive piezoelectric effect and it can also deform under the action of the electric field, which is called the inverse piezoelectric effect. The mechano-electric coupling characteristics give piezoelectric materials the ability to convert electrical energy and mechanical energy, which can be used in applications such as transducers, sensors and actuators [6].
The excellent electro-mechanical coupling effect of piezoelectric materials makes it possible to use different external circuits to modify the mechanical properties of the piezoelectric material and thus modulate various aspects of the metamaterial. The key is to find a way to control the vibration of the structure. Piezoelectric shunt technology is an important means of vibration suppression, especially in the vibration control of smart structures. Because of the advantages of relatively low added mass, it is widely used in the field of vibration and noise control. According to the operating characteristics, piezoelectric shunt circuits can be divided into linear circuits and nonlinear circuits [7].
For linear circuits, the piezoelectric shunt damping technique was first proposed in 1979 and this technique [40] uses a resistive-inductive (RL) shunt circuit for vibration damping. If the resonance of the circuit is equal to the resonance of the mechanical system, the circuit is in the resonant state and will generate a considerable control force against the vibration of the mechanical system. The simplicity and ease of implementation of RL-based piezoelectric shunt damping techniques have attracted more and more attention [41–43]. The circuit control effect mainly depends on RL resonance. The traditional RL resonant shunt circuit has the following problems. For example, the vibration attenuation capability of the circuit under the condition of multi-modal vibration is not ideal [44], the realization of low-frequency vibration requires a hundred Henry-level inductance [45] and the circuit control effect is very sensitive to the change of circuit parameters [46]. In addition to the RL piezoelectric shunt damping circuit, the negative capacitive damping technology can also effectively avoid the narrow band gap and achieve the effect of broadband vibration control. On the one hand, the negative capacitance shunt circuit can effectively change the equivalent stiffness of piezoelectric materials [47], and on the other hand, it can produce a good damping effect [48, 49]. In particular, changes in the environment may cause dramatic changes in the structural resonance frequency. At the same time, the temperature will also change the capacitance in the control circuit, which will affect the performance of the shunt circuit. Based on the proposal of an accurate model for constructing piezoelectric materials, the problem of how to reduce or avoid the instability of the negative capacitance piezoelectric shunt damping circuit is solved [50].
In terms of nonlinear circuits, the most representative one is the synchronous switch damping (SSD) shunt circuit [51–54]. The synchronous switch damping shunt circuit is a semi-active control method, which is equivalent to providing a nonlinear impact load. The voltage of the piezoelectric material will continuously flip with the change of the structural displacement under the action of the nonlinear switch of the SSD circuit. Among SSD circuits, synchronous switched inductive damping circuit (SSDI) has attracted wide attention because of its excellent stability and good low-frequency vibration suppression effect without very large inductors [55, 56]. However, the manufacturing process and other factors will affect the quality factor of the inductor, which will affect the vibration suppression effect of SSDI circuit. To reduce this detrimental effect, Xu et al. [57] improved the vibration suppression effect of the circuit by adding negative capacitance to the circuit to improve the electromechanical coupling coefficient of the piezoelectric element. In addition, a voltage source is connected in series in the SSDI circuit to form the enhanced SSDV, which can also effectively improve the vibration suppression of the circuit. However, this method tends to cause circuit instability and a synchronous switching damping circuit based on a negative capacitance (SSDNC) structure has also been developed. This circuit can counteract the equivalent capacitance value of piezoelectric material by adjusting the value of negative capacitance, so as to improve the electromechanical coupling coefficient of piezoelectric material, increase the flipping voltage of piezoelectric material, and achieve better vibration suppression effect. This shunt circuit does not require precise system identification of the controlled structure. The vibration control effect is better and more stable. Changes in the external environment have a low impact on the control system. Most importantly, the control system is simple and can be implemented with only a few electronic components [58].
At present, PMs has been widely used in UE, including underwater gliders, hydrophones, underwater robots, offshore drilling platforms, submarines and underwater communication equipment [59–61]. It is also used to improve ultrasonic sensors and special equipment for detecting underwater explosives and underwater pollution [62, 63]. PMs has a very broad application prospect. For underwater equipment, the most prominent feature is that the hard boundary of sound field meets the need for hydrostatic pressure. The sound wave in the underwater equipment flows from the seawater environment to the underwater equipment. The water to equipment here is the hard boundary. The hard boundary condition is that the normal sound pressure is zero. Hydrostatic pressure refers to the pressure exerted by static liquid on adjacent contact. The band gap characteristics of PMs can be used for sound insulation of UE. To sum up, the application of piezoelectric metamaterial in underwater equipment can be developed in two directions. First, the band gap characteristics are used for sound insulation of underwater equipment. Second, piezoelectric conversion characteristics are used for energy harvesting in underwater devices. The application prospect of PMs in UE will be very broad.
The following describes the research content and research progress of PMs in terms of sound insulation and piezoelectric conversion of UE.
PM structures have good applications in the field of sound insulation and vibration damping due to their unique elastic wave band gap properties, i.e., elastic waves cannot propagate in their band gap frequency range [64, 65].
Zhou et al. [66] used a new method to verify and deduce a new type of piezoelectric composite metamaterial, which has both viscoelastic and piezoelectric properties. The viscosity of the viscoelastic material dissipates the mechanical energy of vibration and absorbs the sound waves to achieve passive noise reduction. The properties of piezoelectric materials can achieve the effect of active noise cancellation, by emitting the opposite phase of the sound wave to a known sound source to cancel out the sound wave. This material is applied to the coating of submarines. The reflection is eliminated by applying a controlled periodic voltage to the piezoelectric material layer to create a corresponding stress, which in turn emits sound waves that are in the opposite phase of the vibration. The concealment of submarine is improved, and the feasibility of using this new material for UE sound insulation is discussed theoretically. Yi et al. [67] proposed a general method for designing multi-resonant PMs, as shown in Figure 4. This metamaterial contains periodically distributed piezoelectric patches bonded to the surface of the main structure, the shunt circuit works with the patches in a self-inductive mode. By studying the effective bending stiffness of the multi-resonance metamaterial plate, the mechanism of multi-band gap generated by the transfer function is explained. When the effective bending stiffness becomes negative, the transfer function induces multiple frequency ranges, resulting in multiple band gaps The characteristics of these bandgaps can be studied, and their coupling and merging phenomena can be observed and analyzed. The elastic wave isolation effect of the material in multiple frequency bands is verified by numerical results in the frequency domain, which proves the functionality of the material and provides a new choice for sound insulation and vibration reduction of underwater equipment.
He et al. [68] designed a tunable thin-film metamaterial based on piezoelectric materials for the isolation of low-frequency noise. The material is made of a piezoelectric mass embedded in an elastic film, and it is verified by experiments that the material has good sound insulation performance in the frequency range of 20–1,200 Hz. Moreover, the external circuit of the piezoelectric mass block is explored to form an LC oscillating circuit, and the resonant frequency of the circuit can be adjusted by changing the parameters of the external circuit to realize the adjustability of the sound insulation performance. The results of this study provide a reference for the design of sound-insulating tunable PMs and support for the material to be used in UE.
To realize the sound insulation and vibration reduction of UE, Wang et al. [7] overcome the shortcoming of the relatively narrow band gap of PM structures by externally connecting different shunt circuits, and realized the adjustment of the band gap of metamaterials. The synthetic impedance technology is proposed, and the synthetic impedance equivalent control loop is designed. Through simulation research, it is shown that the method can flexibly adjust the band gap range of PMs using software programming, which provides a new way for the vibration and sound insulation of PMs in UE. With its unique piezoelectric properties, the PM is used in the sound insulation of UE, overcoming the problem of poor isolation of low-frequency sound by traditional materials, reducing the impact of underwater noise on UE and improving the data accuracy of the equipment.
Vibration energy in water mostly exists in the form of low frequency and broadband sound waves, and the vibration energy in water can be converted into electric energy through piezoelectric conversion characteristics.
The PM structure is designed to capture the underwater vibration energy of broadband and low frequency. The model of elastic wave propagation in PM structure is established, and then the characteristics of elastic wave propagation are solved by simulation. The band gap of the PM structure is solved and analyzed, and the energy output of PMs using different piezoelectric materials is simulated and experimentally analyzed to demonstrate the effectiveness of the material structure [8]. Experiments show that the PM structure can effectively absorb elastic wave vibration energy in a specific frequency range and convert it into electrical energy, which can realize energy storage and power supply for underwater robots and other equipment. Khan et al. [69] studied and proposed a modeling framework based on micromechanical finite element, which was used to calculate the electromechanical characteristics of 3–3 PMs based on honeycomb structural variants. The hydrostatic quality factor of the longitudinal polarization network is increased by four orders of magnitude and the acoustic impedance is reduced by one order of magnitude, which is very suitable for the design of hydrophones. Hydrophones are made of new PMs with higher hydrostatic quality factors. An active gradient metamaterial based on the composite structure of conventional piezoelectric materials was proposed to achieve acoustic impedance matching and underwater acoustic focusing [70]. The active focusing and broadband focusing behaviors of this PM are demonstrated by simulation and experiments, which can replace acoustic metamaterials used in UE.
To solve the power problem of underwater low-power wireless sensors, Zhang et al. [71] organically combined elastic wave fluctuation characteristics with piezoelectric energy-harvesting structures to improve the vibration energy capture efficiency of broadband low-frequency environments. As shown in Figure 5, a local resonant piezoelectric metamaterial thin sheet is designed and manufactured for test verification. The test results show that the optimized circuit can effectively improve the energy harvesting efficiency and provide a choice for long-term uninterrupted power supply of underwater low-power equipment. Sayed Saad Afzal et al. [72] proposed to create a completely battery-free and scalable underwater sensor network. By developing a backscattering underwater sensor using PMs, backscattering sensors can simply collect energy from environmental signals in the environment and then reflect them to communicate with near-zero power consumption, which is called piezoelectric acoustic backscattering. It is an underwater backscatter network system that uses underwater transducers to provide energy for communication and has made great progress in power-free underwater communication.
FIGURE 5. (A) Schematic diagram of the structural plane of the local resonance type PM sheet (B) Schematic diagram of the structure of the local resonance type PM resonant subunit.
Figure 6 is a structural diagram of a PM, which is used to fabricate a mechanical antenna that can be used for UE communication. The antenna has high radiation efficiency, multiple frequency bands and small size [73]. Through the structural parameters and materials of the piezoelectric radiation unit, the three operating frequency bands of 22, 24, and 26 kHz can be independently adjusted and the modulation range exceeds 15 kHz. The experimental results show that the proposed piezoelectric metamaterial antenna has great application potential in underwater communication equipment.
Xiao et al. proposed a two-dimensional local resonance metamaterial acoustic energy collector for the problem of sound energy harvesting. The acoustic energy density and conversion efficiency are improved by studying and utilizing piezoelectric energy harvesting technology of acoustic metamaterials. The sound energy conversion and sound insulation performance of the plate are studied from the acoustic point of view, so that the utilization rate of sound energy into electric energy can reach the highest [74]. Ma et al. designed a single cavity underwater acoustic metasurface unit with subwavelength thickness that simultaneously achieves high refractive index in underwater environment. By arranging several metasurface elements with gradient refractive index distribution along the radial direction, a 3D planar underwater acoustic lens with gradient refractive index is constructed. In addition, a lens-based acoustic concentrator is proposed to greatly increase the acoustic energy gain over a wide frequency range. It has potential application value in acoustic energy harvesting [75]. Kim et al. designed spherical and ellipsoidal metamaterial lenses based on Luneburg lenses and transform optics for underwater ultrasound imaging. It can enhance the signal over a wide frequency range and detect objects at wide angles. The lens has a wide frequency characteristic and can achieve the half maximum of focal length and full width in the frequency range of 60–160 kHz.These lenses can be used in sound-guided ranging, offering the possibility of detecting underwater at higher resolution at broadband and wide angles [15].
The emergence of PMs improves the efficiency of underwater elastic wave vibration energy harvesting, so they are mostly used to improve the traditional underwater energy harvesting equipment. The emergence of PMs provides a new option for the fabrication of UE, thus improving the performance of UE. In conclusion, the emergence of PMs has greatly promoted the development of UEs.
PMs can be widely used in UE due to their bandgap characteristics and piezoelectric conversion characteristics. The band gap characteristics are mainly related to the absorption of elastic waves. Under water, PMs are mainly used to absorb sound waves, play the role of sound insulation, noise reduction, vibration reduction and so on. The vibrational energy of elastic waves can be converted into electric energy by piezoelectric conversion. Under water, PMs can convert the vibrational energy to electricity to power UE. In addition, PM has excellent electro-mechanical coupling effect. The external shunt circuit is easy to be adjusted and designed in various ways, so that the PM has controllable characteristics, which can meet the different requirements of the functional design and application of acoustic equipment. In practical engineering, the application of PM can reduce noise and vibration of UE, which is helpful to improve the accuracy of hydrophones. The energy conversion efficiency of PM can be improved by changing its piezoelectric structure through the design of external shunt circuit. In general, the application of PM in UE extends the application range of UE.
So far, few piezoelectric metamaterial have been used underwater, or even acoustic metamaterial for underwater equipment. In recent years, the research of piezoelectric metamaterials has attracted great interest and attention of many researchers. At the same time, a lot of scientific research achievements have been made, but there is still a big gap with the actual demand and application. In the future, researchers still need to strengthen the corresponding theoretical, numerical and experimental research. Most of the existing related research is still based on basic research, and there is still a great lack of corresponding applied research. The research results of piezoelectric metamaterial are transformed into practical technology to make structures, components and equipment suitable for practical application. This requires the cooperation and efforts of theoretical researchers and technicians engaged in the field of applied research and technology development.
Based on the current research status, there is still room for future development as follows: 1) The mature application of PMs in UE is relatively small, and most of them are still in the theoretical and simulation stage. Experimental research on PMs should be accelerated, and more applications should be applied to UE. 2) Piezoelectric materials with better performance should be developed to power energy storage for larger UEs. 3) With the rapid development of artificial intelligence, the structure of PM can be designed by artificial intelligence algorithm. For example, it can be intelligently designed according to the range and function of use. 4) The properties of piezoelectric materials are fully exploited by UE, and researchers also need to develop equipment that can accurately process mechanical signals and design better external control circuits.
JZ, the author of the article, was responsible for the design and writing of the article. NH provided valuable advice on the design and writing of the article. JW offered advice on the use of metamaterials in underwater devices. WL was in charge of literature research. ZZ provided valuable advice on the design and writing of the article. MW, YZ and HD are coordinating the authors
This research was supported by the Zhejiang Science and Technology Plan Project (No. 2022C01199), and the Zhejiang science and technology project (No. GK219909299001-021). The funders had no role in the design of the study; in the collection, analyses, or interpretation of data; in the writing of the manuscript, or in the decision to publish the results.
Author JW was employed by Sanmen Sanyou Technology Inc.
The remaining authors declare that the research was conducted in the absence of any commercial or financial relationships that could be construed as a potential conflict of interest.
All claims expressed in this article are solely those of the authors and do not necessarily represent those of their affiliated organizations, or those of the publisher, the editors and the reviewers. Any product that may be evaluated in this article, or claim that may be made by its manufacturer, is not guaranteed or endorsed by the publisher.
1. Liu J, Guo H, Wang T. A review of acoustic metamaterials and phononic crystals. Crystals (2020) 10(4):305. doi:10.3390/cryst10040305
2. Liao G, Luan C, Wang Z, Liu J, Yao X, Fu J. Acoustic metamaterials: A review of theories, structures, fabrication approaches, and applications. Adv Mater Technol (2021) 6(5):2000787. doi:10.1002/admt.202000787
3. Grzegorczyk TM, Kong JA. Review of left-handed metamaterials: Evolution from theoretical and numerical studies to potential applications. J Electromagn Waves Appl (2012) 20(14):2053–64. doi:10.1163/156939306779322620
4. Kushwaha MS, Halevi P, Dobrzynski L, Djafari-Rouhani B. Acoustic band structure of periodic elastic composites. Phys Rev Lett (1993) 71(13):2022–5. doi:10.1103/PhysRevLett.71.2022
5. He Q, Sun S, Xiao S, Zhou L. High-efficiency metasurfaces: Principles, realizations, and applications. Adv Opt Mater (2018) 6(19):1800415. doi:10.1002/adom.201800415
6. Yuan Y, You Z, Chen W. PMs and wave control: Status quo and prospects. Chin J Theor Appl Mech (2021) 53(08):2101–16. doi:10.6052/0459-1879-21-198
7. Bo WL. Research on vibration control based on PMs northwestern. London: Polytechnical University (2019).
8. Dong C. Vibration energy collection system based on one-dimensional PMs master of engineering. China: Harbin Engineering University (2021).
9. Li Z, Wang Y, Ma T, Zhang C. Smart piezoelectric phononic crystals and metamaterials:state-of-the-art review and outlook. Chin Sci Bull (2022) 67(12):1305–25. doi:10.1360/TB-2021-1265
10. Lu M-H, Feng L, Chen Y-F. Phononic crystals and acoustic metamaterials. Mater Today (2019) 12(12):34–42. doi:10.1016/S1369-7021(09)70315-3
11. Ma F, Huang Z, Liu C, Wu JH. Acoustic focusing and imaging via phononic crystal and acoustic metamaterials. J Appl Phys (2022) 131(1):011103. doi:10.1063/5.0074503
12. Ji Y, Luan C, Yao X, Fu J, He Y. Recent progress in 3d printing of smart structures: Classification, challenges, and trends. Adv Intell Syst (2021) 3(12):2000271. doi:10.1002/aisy.202000271
13. Maldovan M. Sound and heat revolutions in phononics. Nature (2013) 503(7475):209–17. doi:10.1038/nature12608
14. Ma F, Wang C, Liu C, Wu JH. Structural designs, principles, and applications of thin-walled membrane and plate-type Acoustic/elastic metamaterials. J Appl Phys (2021) 129(23):231103. doi:10.1063/5.0042132
15. Kim J-W, Hwang G, Lee S-J, Kim S-H, Wang S. Three-dimensional acoustic metamaterial Luneburg lenses for broadband and wide-angle underwater ultrasound imaging. Mech Syst Signal Process (2022) 179:109374. doi:10.1016/j.ymssp.2022.109374
16. Tian Y, Ge H, Lu M-H, Chen Y-F. Research advances in acoustic metamaterials. Acta Phys Sin (2019) 68(19):194301. doi:10.7498/aps.68.20190850
17. Ren T. Investigations on bandgap tuning and sound insulation characteristics of metamaterial structures doctor of engineering. China: Harbin Engineering University (2021).
18. Guo Z, Li F. Advances in active tuning of elastic wave band gaps in metamaterial structures. Chin Sci Bull (2021) 67(12):1249–63. doi:10.1360/tb-2021-0483
19. Martínez J, Coves Á, Bronchalo E, San Blas ÁA, Bozzi M. Band-pass filters based on periodic structures in siw technology. AEU - Int J Elect Commun (2019) 112:152942. doi:10.1016/j.aeue.2019.152942
20. Taniker S, Yilmaz C. Phononic gaps induced by inertial amplification in bcc and fcc lattices. Phys Lett A (2013) 377(31-33):1930–6. doi:10.1016/j.physleta.2013.05.022
21. Hajhosseini M, Rafeeyan M, Ebrahimi S. Vibration band gap analysis of a new periodic beam model using gdqr method. Mech Res Commun (2017) 79:43–50. doi:10.1016/j.mechrescom.2017.01.002
22. Abueidda DW, Jasiuk I, Sobh NA. Acoustic band gaps and elastic stiffness of pmma cellular solids based on triply periodic minimal surfaces. Mater Des (2018) 145:20–7. doi:10.1016/j.matdes.2018.02.032
23. Li Y, Chen T, Wang X, Xi Y, Liang Q. Enlargement of locally resonant sonic band gap by using composite plate-type Acoustic metamaterial. Phys Lett A (2015) 379(5):412–6. doi:10.1016/j.physleta.2014.11.028
24. Al Ba'ba'a HB, Nouh M. Mechanics of longitudinal and flexural locally resonant elastic metamaterials using a structural power flow approach. Int J Mech Sci (2017) 122:341–54. doi:10.1016/j.ijmecsci.2017.01.034
25. Goffaux C, Vigneron JP. Theoretical study of a tunable phononic band gap system. Phys Rev B (2001) 64(7):075118. doi:10.1103/PhysRevB.64.075118
26. Tian Y, Tan Z, Han X, Li W. Phononic crystal lens with an asymmetric scatterer. J Phys D Appl Phys (2019) 52(2):025102. doi:10.1088/1361-6463/aae679
27. Lin S-CS, Huang TJ. Tunable phononic crystals with anisotropic inclusions. Phys Rev B (2011) 83(17):174303. doi:10.1103/PhysRevB.83.174303
28. Wu F, Liu Z, Liu Y. Acoustic band gaps created by rotating square rods in a two-dimensional lattice. Phys Rev E (2002) 66(4):046628. doi:10.1103/PhysRevE.66.046628
29. Ning S, Yang F, Luo C, Liu Z, Zhuang Z. Low-frequency tunable locally resonant band gaps in acoustic metamaterials through large deformation. Extreme Mech Lett (2020) 35:100623. doi:10.1016/j.eml.2019.100623
30. Chen Y, Wu B, Li J, Rudykh S, Chen W. Low-frequency tunable topological interface states in soft phononic crystal cylinders. Int J Mech Sci (2021) 191:106098. doi:10.1016/j.ijmecsci.2020.106098
31. Huang Y, Shen XD, Zhang CL, Chen WQ. Mechanically tunable band gaps in compressible soft phononic laminated composites with finite deformation. Phys Lett A (2014) 378(30-31):2285–9. doi:10.1016/j.physleta.2014.05.032
32. Huang Y, Li J, Chen W, Bao R. Tunable bandgaps in soft phononic plates with spring-mass-like resonators. Int J Mech Sci (2019) 151:300–13. doi:10.1016/j.ijmecsci.2018.11.029
33. Wang P, Casadei F, Shan S, Weaver JC, Bertoldi K. Harnessing buckling to design tunable locally resonant acoustic metamaterials. Phys Rev Lett (2014) 113(1):014301. doi:10.1103/PhysRevLett.113.014301
34. Bertoldi K, Boyce MC. Mechanically triggered transformations of phononic band gaps in periodic elastomeric structures. Phys Rev B (2008) 77(5):052105. doi:10.1103/PhysRevB.77.052105
35. Bertoldi K, Boyce MC, Deschanel S, Prange SM, Mullin T. Mechanics of deformation-triggered pattern transformations and superelastic behavior in periodic elastomeric structures. J Mech Phys Sol (2008) 56(8):2642–68. doi:10.1016/j.jmps.2008.03.006
36. Shan S, Kang SH, Wang P, Qu C, Shian S, Chen ER, et al. Harnessing multiple folding mechanisms in soft periodic structures for tunable control of elastic waves. Adv Funct Mater (2014) 24(31):4935–42. doi:10.1002/adfm.201400665
37. Nimmagadda C, Matlack KH. Thermally tunable band gaps in architected metamaterial structures. J Sound Vibration (2019) 439:29–42. doi:10.1016/j.jsv.2018.09.053
38. Xia B, Chen N, Xie L, Qin Y, Yu D. Temperature-controlled tunable acoustic metamaterial with active band gap and negative bulk modulus. Appl Acoust (2016) 112:1–9. doi:10.1016/j.apacoust.2016.05.005
39. Katzir S. The discovery of the piezoelectric effect the beginnings of piezoelectricity. Berlin, Germany: Springer (2006). p. 15–64.
40. Forward RL. Electronic damping of vibrations in optical structures. Appl Opt (1979) 18(5):690–7. doi:10.1364/ao.18.000690
41. Hollkamp JJ. Multimodal passive vibration suppression with piezoelectric materials and resonant shunts. J Intell Mater Syst Structures (2016) 5(1):49–57. doi:10.1177/1045389x9400500106
42. Behrens S, Moheimani SOR, Fleming AJ. Multiple Mode current flowing passive piezoelectric shunt controller. J Sound Vibration (2003) 266(5):929–42. doi:10.1016/s0022-460x(02)01380-9
43. Thomas O, Ducarne J, Deü JF. Performance of piezoelectric shunts for vibration reduction. Smart Mater Struct (2012) 21(1):015008. doi:10.1088/0964-1726/21/1/015008
44. Wu S-y. Method for multiple-mode shunt damping of structural vibration using a single pzt transducer. In: Conference of Smart structures and materials 1998: passive damping and isolation; 16 June 1998; San Diego, CA, United States. Bellingham, Washington, United States: SPIE (1998). p. 1–5.
45. Moheimani SR, Fleming AJ. Piezoelectric transducers for vibration control and damping. Berlin, Germany: Springer (2006).
46. Berardengo M, Manzoni S, Vanali M. The behaviour of mistuned piezoelectric shunt systems and its estimation. Shock and Vibration (2016) 2016:1–18. doi:10.1155/2016/9739217
47. Date M, Kutani M, Sakai S. Electrically controlled elasticity utilizing piezoelectric coupling. J Appl Phys (2000) 87(2):863–8. doi:10.1063/1.371954
48. Imoto K, Nishiura M, Yamamoto K, Date M, Fukada E, Tajitsu Y. Elasticity control of piezoelectric lead zirconate titanate (pzt) materials using negative-capacitance circuits. Jpn J Appl Phys (2005) 44(9):7019–23. doi:10.1143/jjap.44.7019
49. Beck BS, Cunefare KA, Ruzzene M, Collet M. Experimental analysis of a cantilever beam with a shunted piezoelectric periodic array. J Intell Mater Syst Structures (2011) 22(11):1177–87. doi:10.1177/1045389x11411119
50. Richard C, Guyomar D, Audigier D, Ching G. Semi-passive damping using continuous switching of a piezoelectric device. In: Conference of Smart Structures and Materials 1999: Passive Damping and Isolation; 12 July 1999; San Diego, CA, United States. Bellingham, Washington, United States: SPIE (1999). p. 1–8.
51. Lin Q, Ermanni P. Semi-active damping of a clamped plate using pzt. Int J Sol Structures (2004) 41(7):1741–52. doi:10.1016/j.ijsolstr.2003.11.023
52. Lefeuvre E, Badel A, Petit L, Richard C, Guyomar D. Semi-passive piezoelectric structural damping by synchronized switching on voltage sources. J Intell Mater Syst Structures (2006) 17(8-9):653–60. doi:10.1177/1045389x06055810
53. Muhammad BB, Wan M, Feng J, Zhang W-H. Dynamic damping of machining vibration: A review. Int J Adv Manuf Technol (2016) 89(9-12):2935–52. doi:10.1007/s00170-016-9862-z
54. Neubauer M, Han X, Schwarzendahl SM. Enhanced switching law for synchronized switch damping on inductor with bimodal excitation. J Sound Vibration (2011) 330(12):2707–20. doi:10.1016/j.jsv.2011.01.003
55. Faiz A, Guyomar D, Petit L, Buttay C. Wave transmission reduction by a piezoelectric semi-passive technique. Sensors Actuators A: Phys (2006) 128(2):230–7. doi:10.1016/j.sna.2006.02.021
56. Tang W, Wang B, Bao B, Cao JJ. Experimental comparisons of two detection methods for semi-passive piezoelectric structural damping. J Vib Eng Technol (2017) 5(4):367–79.
57. Han X, Neubauer M, Wallaschek J. Improved piezoelectric switch shunt damping technique using negative capacitance. J Sound Vibration (2013) 332(1):7–16. doi:10.1016/j.jsv.2012.08.001
58. Zhang S. A study on semi-active noise control by using synchronized switch damping method master of engineering. China: Nanjing University of Aeronautics and Astronautics (2016).
59. Hu G, Tang L, Banerjee A, Das R. Metastructure with piezoelectric element for simultaneous vibration suppression and energy harvesting. J Vib Acoust (2017) 139(1):4034770. doi:10.1115/1.4034770
60. Apaydin N, Sertel K, Volakis JL. Nonreciprocal leaky-wave antenna based on coupled microstrip lines on a non-uniformly biased ferrite substrate. IEEE Trans Antennas Propag (2013) 61(7):3458–65. doi:10.1109/tap.2013.2257646
61. Erb RM, Libanori R, Rothfuchs N, Studart AR. Composites reinforced in three dimensions by using low magnetic fields. Science (2012) 335(6065):199–204. doi:10.1126/science.1210822
62. Bisoffi M, Hjelle B, Brown DC, Branch DW, Edwards TL, Brozik SM, et al. Detection of viral bioagents using a shear horizontal surface acoustic wave biosensor. Biosens Bioelectron X (2008) 23(9):1397–403. doi:10.1016/j.bios.2007.12.016
63. Courjal N, Bernal MP, Ulliac G, Dahdah J, Benchabane S, Merolla JM. Linbo3 acousto-optical and electro-optical micromodulators. J Eur Opt Soc Rapid Publications (2009) 4:09018. doi:10.2971/jeos.2009.09018
64. Wang Y-Z, Li F-M, Kishimoto K, Wang Y-S, Huang W-H. Band gaps of elastic waves in three-dimensional piezoelectric phononic crystals with initial stress. Eur J Mech - A/Solids (2010) 29(2):182–9. doi:10.1016/j.euromechsol.2009.09.005
65. Lebon F, Rizzoni R. Higher order interfacial effects for elastic waves in one dimensional phononic crystals via the Lagrange-Hamilton's principle. Eur J Mech - A/Solids (2018) 67:58–70. doi:10.1016/j.euromechsol.2017.08.014
66. Zou S. Analysis of the acoustic concealing from the underwater polymer matrix piezoelectric composites. Beijing, China: Huazhong University of Science & Technology (2009).
67. Yi K, Liu Z, Zhu R. Multi-resonant metamaterials based on self-sensing piezoelectric patches and digital circuits for broadband isolation of elastic wave transmission. Smart Mater Struct (2021) 31(1):015042. doi:10.1088/1361-665X/ac3b1f
68. He Z-H, Zhao J-B, Yao H, Jiang J-N, Chen X. Sound insulation performance of thin-film AcousticMetamaterials based on piezoelectric materials. Acta Phys Sin (2019) 68(13):134302–90. doi:10.7498/aps.68.20190245
69. Khan KA, Khan MA. 3-3 piezoelectric metamaterial with negative and zero Poisson’s ratio for hydrophones applications. Mater Res Bull (2019) 112:194–204. doi:10.1016/j.materresbull.2018.12.016
70. Li Z, Zhao J, Hou C, Fei C, Zheng C, Lou L, et al. High-frequency self-focusing ultrasonic transducer with piezoelectric metamaterial. IEEE Electron Device Lett (2022) 43(6):946–9. doi:10.1109/led.2022.3170613
71. Zhang F. Study on coupling modeling and structural topology optimization method of local resonance PM vibration energy capture system master of engineering. Changsha, China: National University of Defense Technology (2018).
72. Afzal SS. Battery-free subsea internet of things. XRDS: Crossroads, ACM Mag Students (2020) 27(2):62–5. doi:10.1145/3436203
73. Xu J, Cao J, Guo M, Yang S, Yao H, Lei M, et al. Metamaterial Mechanical Antenna for Very Low Frequency Wireless Communication. Adv Compos Hybrid Mater (2021) 4(3):761–7. doi:10.1007/s42114-021-00278-1
74. Xiao H, Li T, Zhang L, Liao W-H, Tan T, Yan Z. Metamaterial Based Piezoelectric Acoustic Energy Harvesting: Electromechanical Coupled Modeling and Experimental Validation. Mechanical Systems and Signal Processing (2023) 185:109808. doi:10.1016/j.ymssp.2022.109808
Keywords: piezoelectric metamaterials, underwater equipment, band gap, sound insulation, piezoelectric conversion
Citation: Zhao J, Hu N, Wu J, Li W, Zhu Z, Wang M, Zheng Y and Dai H (2022) A review of piezoelectric metamaterials for underwater equipment. Front. Phys. 10:1068838. doi: 10.3389/fphy.2022.1068838
Received: 13 October 2022; Accepted: 03 November 2022;
Published: 22 November 2022.
Edited by:
Lingyun Yao, Southwest University, ChinaReviewed by:
Fuyin Ma, Xi’an Jiaotong University, ChinaCopyright © 2022 Zhao, Hu, Wu, Li, Zhu, Wang, Zheng and Dai. This is an open-access article distributed under the terms of the Creative Commons Attribution License (CC BY). The use, distribution or reproduction in other forums is permitted, provided the original author(s) and the copyright owner(s) are credited and that the original publication in this journal is cited, in accordance with accepted academic practice. No use, distribution or reproduction is permitted which does not comply with these terms.
*Correspondence: Ning Hu, aG9vbmluZ0BoZHUuZWR1LmNu; Zhenjing Zhu, c2hvY2twaWdAaGR1LmVkdS5jbg==; Maofa Wang, d2FuZ21mbDYwMEAxNjMuY29t; Yongju Zheng, am9hbnkwMjA0QDE2My5jb20=; Huajie Dai, cWlubG9uZ2NyY2NAZm94bWFpbC5jb20=
Disclaimer: All claims expressed in this article are solely those of the authors and do not necessarily represent those of their affiliated organizations, or those of the publisher, the editors and the reviewers. Any product that may be evaluated in this article or claim that may be made by its manufacturer is not guaranteed or endorsed by the publisher.
Research integrity at Frontiers
Learn more about the work of our research integrity team to safeguard the quality of each article we publish.