- 1Department of Electric Electronic and Information Engineering (DIEEI), University of Catania, Catania, Italy
- 2Naval Information Warfare Center Pacific, San Diego, CA, United States
Energy Harvesting strategies coupled with the improvement of electronics and the progressive reduction of power requirements have been widely recognized as fundamental to enable self-powered (or autonomous) devices. Among all the potential energy sources, kinetic energy stemming from mechanical vibrations has been particularly extensively investigated for EH purposes due to its characteristics of heterogeneity and ubiquity. To exploit such energy sources, a suitable coupling mechanism to convert vibrations into electric charge is required; it must take into account the wide frequency bandwidth of mechanical vibrations as encountered in everyday scenarios. This review offers an overview of linear vs. non-linear strategies for EH, with a specific focus on different approaches to implement efficient coupling mechanisms; the performances of the specific solutions covered in this work are discussed.
1 Introduction
The possibility of scavenging unused energy available in the surrounding environment, to power electronics or to prolong the battery longevity, has long attracted the attention of researchers, and has become a more pressing problem in an era where reliance on batteries (which need proper disposal) is decreasing, coupled with the increased miniaturization of devices. Hence, Energy Harvesting (EH) strategies together with the improvement of electronics and the progressive reduction of device power requirements have been widely recognized as fundamental to enable self-powered (or autonomous) devices, for the spread of new technological solutions in different fields and the reduction of maintenance costs (mainly associated with the need for batteries [1]). Wireless sensor networks and the Internet of Things are two main examples of areas that would largely benefit from novel EH solutions [1].
Kinetic energy from mechanical vibrations has been largely investigated for EH purposes due to its characteristics of heterogeneity, ubiquity, continuity and, in some cases, periodicity [2]. To exploit such energy sources, a suitable coupling mechanism capable of converting vibrations to electric charge is required [3]. The literature is replete with EH systems exploiting different conversion mechanisms or exploiting the properties of specific materials. A classification of all the proposed solutions for energy harvesting from vibrations can be done according to different points of view based on the feature highlighted. Some possible classifications are:
1.1 Sources of vibrations
Deterministic (periodic) vibrations, non-deterministic (stochastic or aperiodic) vibrations, noisy vibrations superimposed to a periodic vibration [3, 4].
1.2 Conversion mechanisms
Magnetic, electrostatic, electromagnetic, triboelectric, piezoelectric, magnetostrictive [3, 5].
1.3 Intrinsic material properties used to generate electric charge
Piezoelectrics, magnetostrictive compounds coupled with piezoelectrics, ferroelectric, multiferroic, macro-fiber composites and metamaterials, the latter category includes photonic crystals, acoustic/electromagnetic metamaterials [6–8].
1.4 Coupling mechanism
Linear (resonant) mechanisms, non-linearized mechanisms, intrinsically non-linear mechanisms (e.g., Duffing non-linearity and other higher-order polynomial springs, bistable, and multi-stable oscillators, parametric oscillators, stochastic resonance, mechanical frequency converters, self-tuning mechanisms, non-oscillatory mechanisms) [7, 8].
Independently of the mechanical to electrical conversion pathway, the coupling mechanism should have suitable characteristics in terms of 1) sensitivity to “fit” with the magnitude of the vibrations and 2) an appropriately wideband frequency response allowing energy to be harvested in a wide range of frequencies compliant with the specific application under consideration. In fact, apart from some specific cases where vibrations are periodic, in general the energy of vibrations is distributed over a wide range of frequencies and in some cases the bandwidth can also be variable in time [4].
Generally, the coupling mechanism is an oscillator. Depending on their mechanical behavior, oscillators fall into two main classes: Linear and nonlinear oscillators. These two classes of oscillators are briefly discussed in the following sections. From an application point of view, both classes have advantages and drawbacks, as highlighted in Table 1.
2 Fundamental concepts, issues, and problems
2.1 The linear oscillator
The simplest coupling mechanism for EH is the linear resonant oscillator, generally implemented by a one-end-fixed cantilever beam. The mechanical to electrical transduction can be performed via different strategies such as: electromagnetic, piezoelectric, electrostatic, magnetostrictive, and recently electret and triboelectric phenomena [2, 7]. The main advantages of this setup are the structural simplicity and suitability for miniaturization and integration. However, its resonant behavior permits the extraction of only a limited fraction of the overall energy from wide spectrum vibrational sources. The linear EH solution is very efficient in cases wherein the resonant frequency of the linear oscillator matches the frequency of the mechanical input vibrations, or the latter is concentrated in a limited band around it [2].
In general, the oscillator can be tuned to maximize its power output or to broaden its frequency bandwidth, but these two outcomes are mutually exclusive [8]. Higher power outputs can be obtained by increasing the quality factor of the oscillator. On the other hand, increasing the quality factor significantly reduces the frequency bandwidth exploitable for the sake of EH. To overcome this limitation and broaden the operational bandwidth of linear energy harvesters, different solutions have been proposed. Among the main strategies are: Arrays of linear oscillators with different resonance frequencies, frequency tuning by using different methods acting on the geometry of the oscillator or the amount or position of the proof mass or by modifying the oscillator’s stiffness, and non-linearization of linear oscillators by exploiting several strategies e.g., mechanical stoppers, magnetic or electrical forces, frequency-up conversion techniques etc.
A comprehensive review of the main principles and strategies for increasing the operating bandwidth can be found in [7]. As an example, in [9, 10] the use of mechanical stoppers to limit the displacement amplitude in one or both directions of oscillations are investigated. The proposed mechanism allows for inducing the bandwidth broadening with respect to the original linear behavior, due to a non-linear resonant peak flattening and extension towards the higher frequency range. However, the quality factor of the resonator concomitantly decreases with a consequent reduction of the generated power. Moreover, mechanical stoppers introduce mechanical fatigue. The latter drawback can be resolved by using other solutions, like soft mechanical stoppers, magnetic forces, or air springs such as the squeeze film damping adopted in [11]. It should also be observed that, although frequency tuning is very engaging, it is not always convenient or easy to be implemented. For example, if the frequency of the vibrations is variable in time, a mechanism for continuous tuning would be required. This, in turn, would need a non-negligible power that can be comparable or higher than the energy scavenged, thus nulling the effectiveness of the harvester, as a function of the system complexity [7]. Attempts to implement no extra-power demanding self-tuning mechanisms have been performed. A representative example is the doubly clamped beam with a proof mass free to slide along the beam, investigated in [12, 13]. As shown, the device self-tunes towards the source frequency, as the mass self-slides along towards the most favorable position.
2.2 Non-linear solutions for vibrational energy harvesting
In the past 15 years, a different approach to face the limitations of linear oscillators highlighted in the previous section has emerged: The design of energy harvesters exploiting intrinsically non-linear device properties. The interest in such a class of systems arises mainly from the absence of resonant behaviors (as in the case of linear oscillators), but their geometrical and mechanical parameters can be designed to harvest energy with a quasi-constant efficiency [3, 14] in a wider range of frequencies and in the presence of a (non-deterministic) noisy vibrational background [15].
However, non-linear vibrational harvesters also have their drawbacks and challenges that can limit the expected advantages. First, the wider operational bandwidth is obtained at cost of a lower power efficiency if compared to the behavior of linear solutions at their resonance frequency. Moreover, non-linear solutions in some cases show more sophisticated architectures, that make their design and fabrication more difficult or require extra elements (e.g., magnets, stoppers, etc.) to be assembled with a consequent increment of the required volume.
Two examples aimed at demonstrating the capability of non-linear solutions to provide some advantages if employed in vibrational energy harvesters are given in [16, 17]. Spring hardening non-linearities obtained by atypical stress distributions in the structure to improve the performance of an electromagnetic vibration energy harvester have been investigated in [16]. The authors demonstrated an enhancement of the bandwidth of the EH which makes it suitable for extracting mechanical energy from real-world wideband vibrations and the capability of the developed prototype to power a wireless sensor node including a temperature and humidity sensor and Bluetooth connectivity. These results have been obtained by using a suitable complex spring design and manufacturing.
A statically balanced compliant mechanism for applications in piezoelectric EH, based on the concept of stiffness compensation between a linear component with positive-stiffness and a non-linear component has been proposed in [17]. The non-linear part of the system consists of two sets of post-buckled fixed-guided compliant beams in parallel showing negative-stiffness. Although the authors demonstrated acceptable performances in terms of beams displacements on a large prototype (with dimensions on the order of some tens of centimeters), the compliant mechanism appears to be quite difficult to scale down.
This paper is focused on this class of (non-linear) solutions and aims to provide the reader a brief review of two of the main non-linear principles used in vibrational EH. In particular, we consider the Duffing non-linearity and bistability.
It is important to note that this paper does not aim to be a complete and exhaustive review of the state of the art on non-linear solutions for EH from vibrations. Other works can be considered as valuable references for researchers and are available in the literature [2, 8].
2.3 Non-linear principles in vibrational energy harvesting
A common way to treat a vibrational energy harvester is to look at it as an oscillator and model it as a second-order underdamped mass-spring-damper system subject to external vibrations [2, 8, 18]. The general form of the governing equation is:
where m is the mass, d is the damping coefficient, ẍ, ẋ and x are, respectively, the acceleration, the velocity, and the displacement of the mass. F(t) represents the mechanical force due to the vibrations, while the differential term
where a is the strength of the nonlinearity, and b the linear spring constant. For the sake of our discussion, the latter parameter can be expressed as
2.4 Duffing non-linearity
Duffing type non-linearities are ubiquitous in the non-linear EH literature. One of the main representative approaches exploits a linear resonator (in general a cantilever beam) with an added magnetic mass (typically placed on the tip) and external magnets placed nearby in different positions to modulate the magnetic coupling, thus inducing a spring softening or hardening effect [19, 20].
Alternatively, hardening or softening of a spring can be induced by axial pre-stress or pre-compliance [21]. Duffing nonlinearities can also be observed in linear resonators if driven into the high amplitude oscillation regime, as demonstrated by [22]. A different approach is to use magnetic levitation as proposed in [23, 24], where a permanent magnet is kept in suspension inside a tube by two other magnets positioned at the ends and exerting an opposing force. Electrostatic pre-stress or specific topological designs have been adopted in [25, 26] to observe Duffing non-linearities in MEMS.
However, many studies concluded that Duffing oscillators do not have a fundamental performance advantage (in terms of accumulated power) over linear oscillators, when subjected to broadband noise, apart from a bandwidth enhancement [8, 23, 27].
2.5 Bistable oscillators
As mentioned earlier, bistable oscillators have attracted the attention of researchers for their particular behavior. The presence of two (stable) potential wells separated by an energy barrier (corresponding to an unstable state) permits the oscillator to scavenge energy by two operating conditions: while vibrating when the oscillator is trapped in one of the two stable states (also known as intra-well oscillations) and when the oscillator has sufficient energy to cross the potential barrier and switch from one stable state to the other (also known as inter-well or snap-through oscillations). It is interesting to note that the input energy needed to activate the snap-through behavior should be just sufficient to cross the inherent system potential energy barrier, regardless of the frequency of the mechanical input. Effectively, this means that the system spends negligible time around the unstable fixed point of the potential energy function, i.e., the transitions between stable steady states are near-instantaneous. This property, together with other factors like the high switching velocity and the generally higher displacements with respect to linear oscillators, make this class of non-linear systems good candidates to improve the performance of vibrational energy harvesters in the presence of wideband noise [28, 29].
Bistability can be realized via different approaches. It can be a designed intrinsic characteristic of the system or can be forced by mechanical stress exerted by external forces or constraints (e.g., the buckled beam in [14]). Examples of suitably designed bistable oscillators are the carbon fibre-piezoelectric composite plate in [30], the composite laminates in [31] and bistable morphing composites in [32]. Other examples are discussed in [33].
Magnetic coupling is an example of a different approach used to realize bistable oscillators for EH. Typical configurations proposed in the literature adopt a linear oscillator like a cantilever beam with an added magnetic mass at its tip and an opposing magnet in the zero-displacement position to generate a repulsive force and to push the magnetic proof mass toward one of the stable states as in [15, 28, 29, 34, 35] or two attractive magnets placed at a suitable distance from the end of the beam to prevent the beam from residing in its stable position for too long, as in [15, 19, 20], or two or more cantilevers next to each other with an opposing magnetic mass each to force each other into bistable states [34]. It must be observed that suitable similar configurations have been exploited to realize multi-stable oscillators for EH [36–38].
The use of external mechanical forces or applied stress is another common route to introducing bistability, as in the case of the rotational system in [39] where the centripetal acceleration is exploited, or in the case of axial loading applied to a clamped–clamped beam to force it into a buckling configuration [3, 15]. Many works have investigated the advantages arising from the Snap-Through Buckling (STB) configuration for vibrational energy harvesters [40–43].
Buckling is defined as a deformation (a change in the shape) of a structural component subject to load exceeding a well-defined critical value [44]. Snap-Through Buckling is used to refer to systems that can jump from an equilibrium state to another through a non-destructive externally induced mechanical deformation. Buckling of beams can be obtained in various ways e.g., axial compression, heating expansion, or residual stresses [45].
In the following, a brief review of the activity performed at the Sensor Lab of the DIEEI-University of Catania, aimed at investigating different STB based EH solutions, is given. A first basic prototype was investigated and discussed in [46]. The architecture was re-designed, improved with the use of high-performance piezoelectric transducers, and presented in [14]. The prototype, whose schematization is shown in Figure 1, consists of a polymeric PolyEthylene Terephthalate (PET) flexible clamped-clamped beam, constrained in the STB configuration. The beam is of dimensions 6.1 cm by 1 cm with thickness 140 μm. A pre-compression (Δy) of 1 mm obtained by moving the beam clamping along the main dimension (y-axis in Figure 1) leads the beam in the STB configuration with two stable positions 9 mm apart (Δx in Figure 1) from each-other. A mass of 5.3 g is placed in the middle of the beam. As demonstrated in previous works [3, 14, 46, 47], the pre-compression and proof-mass make the device suitable for energy harvesting from wideband low amplitude vibration sources. Two piezoelectric transducers, Volture V21BL by Mide, placed close to the two beam stable positions and clamped at one end, have been used to convert the mechanical energy into electrical energy. Each time the beam switches from one stable position to the other under the effect of the external forces generated by vibrations, the proof mass hits one of the piezoelectric transducers which vibrates at its natural frequency.
The performance of the harvester has been investigated in terms of the frequency response and power conversion efficiency, for mechanical inputs with different characteristics. In [14] the bistable system has been investigated under a periodic impulsive input in the horizontal direction, while its response when subject to a bandlimited noise input was presented in [47]. The results are summarized in Tables 2, 3, respectively.

TABLE 2. The energy conversion efficiency of the harvester investigated in [14], for the range of frequencies 0.5–5 Hz (©2017 IEEE).
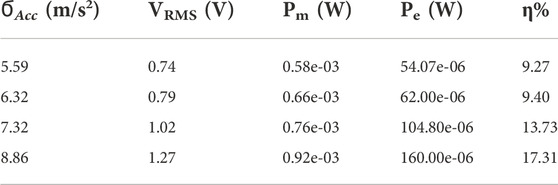
TABLE 3. The standard deviation, ϭAcc, of the (supra-threshold) acceleration generated by a bandlimited noise input, the RMS piezoelectric output voltage, the mechanical and electrical powers and the energy conversion efficiency of the harvester discussed in [47] (©2017 IEEE).
Mechanical input signals were generated by an electrodynamical shaker TV 51110 by TIRA GmbH, driven by the amplifier BAA 120 and a 33120A function generator by Agilent Technologies. To perform an independent measurement of the input acceleration the reference accelerometer, MMA7331L by Freescale Semiconductor, with a sensitivity S = 83.6 mV/g (configured in the operating range of ±12 g), has been used. The following quantities have been investigated and quantified: the frequency of the input signal, f, the maximum, Amax, and the Root Mean Square (RMS), ARMS, accelerations (in Table 2) measured by the reference accelerometer or the noise standard deviation (σAcc in Table 3) of the measured acceleration signal. Other relevant quantities are: the RMS piezoelectric output voltages, VRMS, the electrical, Pe, and mechanical, Pm, powers and the percentage power conversion efficiency, η%. The power conversion efficiency has been evaluated as the ratio between the output electrical power and the input mechanical power:
where
In [48] a STB configuration has been investigated for the case of a periodic acceleration applied along the vertical direction. In this case, the weight of the proof mass load introduces an asymmetry in the force required to switch the beam from the bottom stable state to the opposite position. Actually, when the beam with the mass is in the bottom position, the external applied force (due to the vibrations) must overcome the weight of the proof mass in addition to the beam’s restoring force, at least for the time required to activate the snap-through buckling mechanism [14]. If the force has a lower intensity the STB beam remains in its bottom stable state where it can undergo intra-well vibrations. In other words, it behaves like a non-linear monostable dynamical system whose potential can still be “rocked” through the application of the time-dependent (e.g., time-sinusoidal) signal. In this case the potential is not parabolic, hence the dynamics are non-linear; in the presence of a dissipative term one can, in fact, observe a very rich behavior in the system with the state-point switching between two attractors (albeit in a single well but non-parabolic potential).
To restore the symmetry in its dynamic bistable behavior, a compensation strategy exploiting a magnetic repulsion mechanism together with a magnetic proof mass on the beam was proposed in [48]. A schematization of the STB harvester with the repulsive permanent magnet placed at the optimal distance Lm = 29 mm from the upper state position of the beam is shown in Figure 2. The position of the repulsive magnet has been experimentally fixed by measuring the repulsive magnetic force exerted by the magnet on the proof mass through a dedicated setup which exploits a load cell (Transducer Techniques GSO-10) and the dedicated conditioning electronic. The setup and the measurement methodology are discussed in [48].
To demonstrate the advantages of the magnetic compensation strategy, the device’s EH performance was characterized as a function of the device tilt. Its behavior has been compared with that shown by the same device without the repulsion mechanism, as reported in Table 4 [48]. In particular, the RMS acceleration and the related mechanical power, the electrical power generated, and the estimated power conversion efficiency in the frequency range 0.5–5 Hz in both the cases the prototype is operated with and without the repulsive mechanism, are shown in Table 4, respectively. We readily see the benefit of the asymmetry compensation in terms of minimum acceleration required to switch the beam between its stable states and, consequently, the improvement in terms of conversion efficiency.
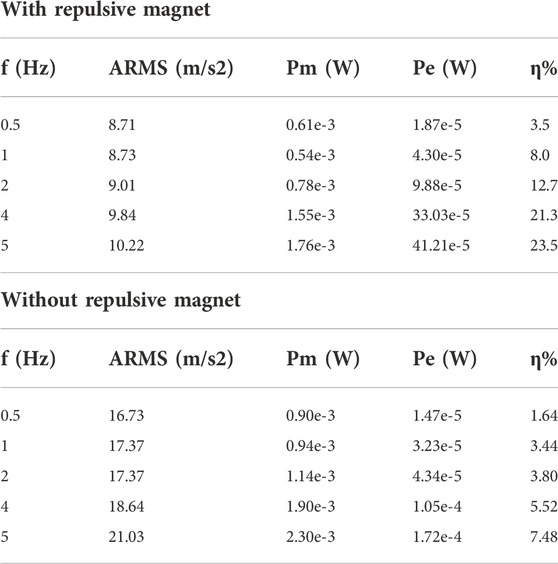
TABLE 4. The estimated efficiency, η, the RMS acceleration, ARMS, and the electrical, Pe, and mechanical, Pm, powers for the harvester presented in [47], a) with and b) without the repulsive magnet (©2018 IEEE).
The response of the non-linear vibrational energy harvester, in the presence of noisy vibrations superimposed on a subthreshold deterministic input signal was investigated in [49]. In particular, the analysis was concentrated on a specific operating regime in which the noise-mediated cooperative behavior, Stochastic Resonance [50, 51], can be exploited in signal detection scenarios. A further improvement of the performance of the STB energy harvester presented in [47], has been demonstrated in [52]. There, a new “constrained” bistable configuration with the two stable positions placed closer has been discussed, and experimentally investigated; this is schematized in Figure 3. The new configuration was obtained by moving the two piezoelectric transducers from the position of the two stable minima toward the inflection points of the potential energy function [53] that underpins the dynamics of the bistable beam.
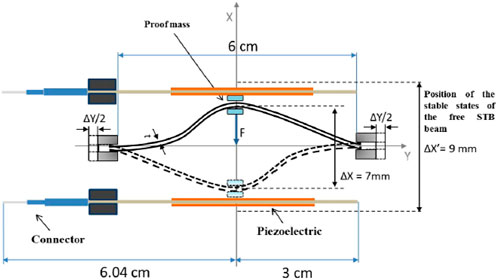
FIGURE 3. Schematization of the “constrained” bistable STB EH (top view) investigated in [52] (©2019 IEEE).
As demonstrated in [52], the main advantages of the new configuration are a reduction of the input acceleration required to activate the switching process, thus making the beam more sensitive to the external vibrations, hence an increase of the power conversion efficiency and, finally, an enlargement of the range of frequencies where the bistable system operates at its maximum switching rate with accelerations compatible with the applications of interest. For the sake of completeness, the results of the experimental investigation in case of a periodic input, are repeated in Table 5. To demonstrate the above stated advantages of the new configuration, the results of the characterization of the STB energy harvester (not “constrained”) obtained in the same operating conditions, have been repeated in Table 5, for comparison. It is worth noting here that, although the configuration of the (not “constrained”) STB harvester is the same as in [14], a different deterministic mechanical input, sinusoidal instead of impulsive, has been used during the characterization, hence the difference of results in Tables 2, 5. The response of the harvester under a band limited noise input has been also investigated in [52] and compared to the STB. The results are reported in Table 6, respectively. An analytical model describing the dynamics of the “constrained” EH harvester has been discussed in [53].
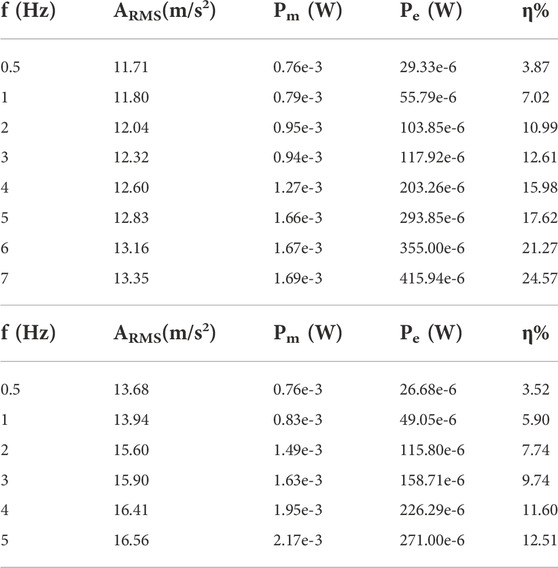
TABLE 5. Estimated efficiency, the RMS acceleration, ARMS, and the electrical and mechanical powers, Pe and Pm, for a) the “constrained” STB and b) the STB nonlinear harvester, discussed in [52], (©2019 IEEE).

TABLE 6. Estimated efficiency, the standard deviation of the acceleration ϬA, and the electrical and mechanical powers, Pe and Pm, for a) the “constrained” STB and b) the STB harvester discussed in [52], (©2019 IEEE).
It is worth noting that enhanced bandwidth performance in the bistable EH has already been demonstrated [28]. In fact, given the dynamics of the STB, it makes perfect sense to model it as a 2-state system with, effectively, a very rapid time-constant (the system does not linger near the unstable fixed point of the potential energy function).
The above STB based EHs have been demonstrated to be capable of generating enough energy to power a low-power 2.4 GHz wireless transceiver embedded in the TI eZ430-RF2500 development tool exploiting the TI MSP430 microcontroller [54]. The ac power generated by the piezoelectric transducers has been converted to dc power via a power management module LTC3588 by Linear Technology with supercapacitors for energy storage.
In [55] the “constrained” STB energy harvester has been investigated in the case of a bi-directional (clockwise-counterclockwise) uniform circular motion in the range of angular positions (45°–135°). The power generated has been experimentally observed to be sufficient to power a wireless sensor node employing a dedicated power management module and a very low power Bluetooth low energy (BLE) module based on the STM IC blueNRG-1 system-on-chip.
Finally, starting from the analysis in [49] the authors investigated the possibility of exploiting the non-linear STB harvester to implement an “autonomous” sensor for the measurement of target vibrations. The main idea was to use the same device as a sensor for the measurement of vibrations and as an energy harvester to extract the energy, required to power the conditioning electronics, from the target mechanical signal and the noise background. The architecture of the device, the developed signal processing methodology aimed to extract from the sensor output the information about the input vibration and the experimental results are described in [56]. More in detail, the non-linear harvester has been operated in the presence of noisy vibrations (band-limited random vibrations) superimposed on a subthreshold deterministic (sinusoidal) input signal. In other words, the sinusoidal signal had an amplitude lower than the switching threshold of the STB beam (depending on the inherent potential barrier), thus not sufficient to activate the switching process without the noise background. Such an operating condition can be found in real scenarios e.g., everyday appliances, cars, flying vehicles, machinery, etc. The paper was mainly focused on the signal processing methodology, supported by experimental evidence, to extract from the sensor output the information about the noise level (in terms of the standard deviation) and the RMS amplitude of the deterministic component. The methodology removes the contribution to the overall piezoelectric output voltage due to the deterministic component using a thresholding and windowing algorithm. The remaining contribution to the output voltage (due to the noise) can be used to unambiguously estimate the noise level. Moreover, an analytical model to estimate the RMS amplitude of the deterministic input and the noise-related component from the measurement of the output voltage has been proposed. Due to the subthreshold deterministic periodic signal, this sensor exploits the Stochastic Resonance [50] effect.
3 A look ahead
There have been significant advances in harvester technology, however too little attention is paid to actually mating the harvester to a device, in the optimally efficient way. Partly this is because often different entities fund and develop the device and harvester, with the device always geared to a specific application (e.g., seismic sensing). The assumption is that clever people can, somehow, “slap” them together. However, a careful “mating” of the two usually requires some really careful/clever circuit design, parameter optimization, etc. So possibly, in the future the way to go about this would be to 1) define one or more important sensor applications (e.g., microsensors to implant/emplace on bridges to detect structural issues) and 2) design the sensor and EH as one composite unit with the EH integrated onto the board and capable of powering the sensor as well as all required readout/communications etc.
From a modeling standpoint, this amounts to writing down (for instance) two coupled non-linear differential equations representing the sensor and the harvester with the coupling carefully chosen and characterized depending on actual engineering/physics considerations in that particular application. They would both have the same (external) source terms (input signals + noise). Then the idea would be to define the measure of the sensor response (e.g., Signal-to-Noise Ratio, SNR, other signal analyses statistics, etc.) and optimize it with respect to coupling/system/EH parameters. In other words, this would be a “holistic” approach which takes careful count of engineering the composite system for maximum efficiency.
The above approach assumes separate entities for the sensor and EH, but requires one to couple them in a really clever manner for optimal performance. However, the philosophy “any EH can function as a sensor and vice versa” could be followed; this is the backbone of our autonomous sensor concept outlined in Section 2. In this approach one has an application involving a reasonably wideband sensor which is required to detect target signals in a relatively narrow band of interest but is also subject to other signals (and noise) across its entire operational bandwidth, which it harvests for energy. This can become somewhat delicate. If you have e.g., a vibrational detection sensor and the ambient signals and noise are vibrational, it should be possible (this is the autonomous sensor described in Section 2). In other sensing cases (e.g., magnetic) in the presence of ambient noise, some extremely clever engineering would be needed, and the optimizing of the composite unit (a “magnetic autonomous sensor”) could be quite challenging. However, one might simplify the problem by coupling the magnetic field sensor to a super-capacitor which is charged through a vibrational energy harvester that is tuned to e.g., low frequency seismic vibrations. This is, of course, the somewhat “inelegant” (by comparison) solution proposed in the preceding paragraph.
The important issue in either scenario is: how can we optimize the sensor for signal detection and simultaneous energy harvesting given that the target signals are in a particular bandwidth and the noise (possibly also having deterministic time-dependent components) could encompass the entire sensor bandwidth? If one uses some non-linear effect like stochastic resonance to optimize signal detection, how will it affect the EH section? Note that in either of the above scenarios, the existence of a tested physics model of the sensor/EH is of paramount importance.
4 Conclusion
Solutions for energy harvesting from vibrations present in the environment or generated by humans during walking, running etc., machineries, fixtures and work tools are expected to become widely used to directly power or recharge batteries for electronics and autonomous sensing systems. Of the numerous strategies, architectures and materials investigated in the literature, non-linear mechanical systems have been demonstrated to be suitable to enhance the performances of vibrational energy harvesters by overcoming the limits of traditional linear oscillators. This paper has aimed to provide the reader a brief review (without the claim of being complete and exhaustive) of two of the main non-linear principles used in vibrational EH: Duffing non-linearity and bistability. A specific focus has been put on vibrational energy harvesters exploiting the advantages of the non-linear bistable STB configuration, addressed by the authors in the last decade. To provide the reader with a rapid an easily accessible summary of the contents of this work, the linear and non-linear solutions discussed in the paper are summarized in Table 7 together with the relative references.
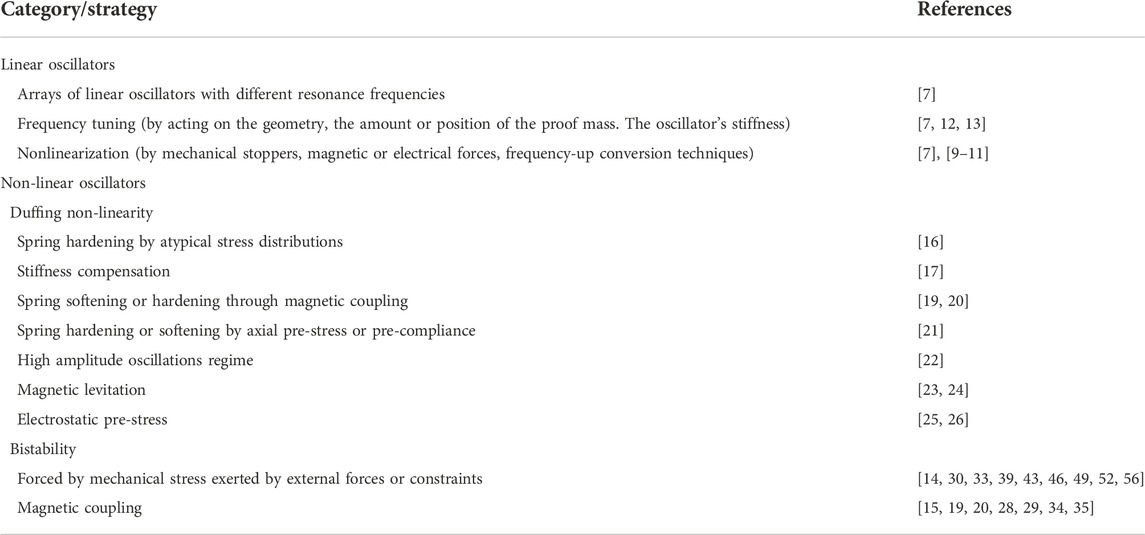
TABLE 7. Strategies to overcome limitations of linear oscillators and non-linear principles used in vibrational Energy Harvesting reported in this work.
It is worth reiterating the important (and usually constructive) role played by background noise. In the absence of deterministic signals, the noise (if wideband) will provide a good energy source provided the system parameters are adjustable so that the crossing rate (over the energy barrier) is increased. In the presence of the deterministic signal, additional scenarios such as stochastic resonance can come into play to further improve the performance of the energy harvester. We note that there can occur scenarios wherein the bistable system discussed above is not overdamped, meaning the dynamics includes a dissipative term. In this case, the interplay between noise and dissipation can be exploited to yield a stochastic resonance like behavior that is mediated by the dissipation; in fact, a modified stochastic resonance effect occurs also at low noise, with the dissipation playing an important role [56]. Hence, an adjustment of the harvester configuration could exploit this behavior even in the presence of weak signals and noise. While we have not, specifically, considered such a system (in an energy harvesting role), the point to be made here is that a plethora of configurations of non-linear (bistable) dynamic systems exist; their energy harvesting performance can be optimized with a good a priori knowledge of the system and environmental parameters in which they will operate, as well as a good understanding of the underlying physics of the device.
Author contributions
Conceptualization, BA, AB, and VM; methodology, VM and SB; validation VM; writing—original draft preparation, VM; revision, BA and AB. All authors have read and agreed to the published version of the manuscript.
Conflict of interest
The authors declare that the research was conducted in the absence of any commercial or financial relationships that could be construed as a potential conflict of interest.
Publisher’s note
All claims expressed in this article are solely those of the authors and do not necessarily represent those of their affiliated organizations, or those of the publisher, the editors and the reviewers. Any product that may be evaluated in this article, or claim that may be made by its manufacturer, is not guaranteed or endorsed by the publisher.
References
1.Energy Harvesting Technologies for IoT”. Energy efficiency policy brief. IEA 4E Publications (2020).
2. Yildirima T, Ghayeshb MH, Lia W, Alicia G. A review on performance enhancement techniques for ambient vibration energy harvesters. Renew Sust Energ Rev (2017) 71:435–49. doi:10.1016/j.rser.2016.12.073
3. Marletta V. A review of vibrational energy harvesters underpinned by a flexible snap-through buckling beam. IEEE Instrum Meas Mag (2020) 23(1):34–41. doi:10.1109/MIM.2020.8979521
4. Roundy S, Wright P, Rabaey J. A study of low level vibrations as a power source for wireless sensor nodes. Comput Commun (2003) 26(11):1131–44. doi:10.1016/s0140-3664(02)00248-7
5. Ullah Khan F, Ahmad I. Review of energy harvesters utilizing bridge vibrations. Shock and Vibration (2016) 2016:21. doi:10.1155/2016/1340402
6. Chen Z, Guo B, Yang Y, Cheng C. Metamaterials-based enhanced energy harvesting: A review. Physica B: Condensed Matter (2014) 438:1–8. doi:10.1016/j.physb.2013.12.040
7. Zhu D, Tudor M, Beeby S. Strategies for increasing the operating frequency range of vibration energy harvesters – A review. Meas Sci Technol (2010) 21(2):022001. doi:10.1088/0957-0233/21/2/022001
8. Jia Y. Review of non-linear vibration energy harvesting: Duffing, bistability, parametric, stochastic and others. J Intell Mater Syst Structures (2020) 31(7):921–44. doi:10.1177/1045389x20905989
9. Soliman M, Abdel-Rahman E, El-Saadany E, Mansour R. A design procedure for wideband micropower generators. J Microelectromech Syst (2009) 18(6):1288–99. doi:10.1109/jmems.2009.2031695
10. Le CP, Halvorsen E. MEMS electrostatic energy harvesters with end-stop effects. J Micromech Microeng (2012) 22(7):074013. doi:10.1088/0960-1317/22/7/074013
11. Chen ST, Du S, Arroyo E, Jia Y, Seshia A. Shock reliability enhancement for MEMS vibration energy harvesters with nonlinear air damping as a soft stopper. J Micromech Microeng (2017) 27(10):104003. doi:10.1088/1361-6439/aa82ed
12. Gregg CG, Pillatsch P, Wright PK. Passively self-tuning piezoelectric energy harvesting system. J Phys : Conf Ser (2014) 557:012123. doi:10.1088/1742-6596/557/1/012123
13. Miller LM, Pillatsch P, Halvorsen E, Wright PK, Yeatman EM, Holmes AS. Experimental passive self-tuning behavior of a beam resonator with sliding proof mass. J Sound Vib (2013) 332(26):7142–52. doi:10.1016/j.jsv.2013.08.023
14. Andò B, Baglio S, Bulsara AR, Marletta V, Pistorio A. Investigation of a nonlinear energy harvester. IEEE Trans Instrum Meas (2017) 66(5):1067–75. doi:10.1109/tim.2017.2663178
15. Harne RL, Wang KW. A review of the recent research on vibration energy harvesting via bistable systems. Smart Mater Struct (2013) 22:023001. doi:10.1088/0964-1726/22/2/023001
16. Kankana P, Andreas A, Saibal R. Tapered nonlinear vibration energy harvester for powering Internet of Things. Appl Energ (2021) 283:116267. doi:10.1016/j.apenergy.2020.116267
17. Liang H, Hao G, Olszewski OZ, Pakrashi V. Ultra-low wide bandwidth vibrational energy harvesting using a statically balanced compliant mechanism. Int J Mech Sci (2022) 219:107130. doi:10.1016/j.ijmecsci.2022.107130
18. Andò B, Baglio S, Marletta V, Bulsara AR. Modeling a nonlinear harvester for low energy vibrations. IEEE Trans Instrum Meas (2019) 68(5):1619–27. doi:10.1109/tim.2018.2882901
19. Erturk A, Hoffmann J, Inman D. A piezomagnetoelastic structure for broadband vibration energy harvesting. Appl Phys Lett (2009) 94(25):254102. doi:10.1063/1.3159815
20. Stanton S, McGehee C, Mann B. Reversible hysteresis for broadband magnetopiezoelastic energy harvesting. Appl Phys Lett (2009) 95(17):174103. doi:10.1063/1.3253710
21. Marinkovic B, Koser H. Smart sand – A wide bandwidth vibration energy harvesting platform. Appl Phys Lett (2009) 94(10):103505. doi:10.1063/1.3097207
22. Ramlan R, Brennan MJ, Mace BR, Kovacic I. Potential benefits of a non-linear stiffness in an energy harvesting device. Nonlinear Dyn (2010) 59(4):545–58. doi:10.1007/s11071-009-9561-5
23. Daqaq M. Response of uni-modal Duffing-type harvesters to random forced excitations. J Sound Vib (2010) 329(18):3621–31. doi:10.1016/j.jsv.2010.04.002
24. Mann B, Sims N. Energy harvesting from the nonlinear oscillations of magnetic levitation. J Sound Vib (2009) 319(1–2):515–30. doi:10.1016/j.jsv.2008.06.011
25. Tvedt LGW, Nguyen DS, Halvorsen E. Nonlinear behavior of an electrostatic energy harvester under wide- and narrowband excitation. J Microelectromech Syst (2010) 19(2):305–16. doi:10.1109/jmems.2009.2039017
26. Halvorsen E. Fundamental issues in nonlinear wideband-vibration energy harvesting. Phys Rev E (2013) 87:042129. doi:10.1103/physreve.87.042129
27. Langley R R. Bounds on the vibrational energy that can be harvested from random base motion. J Sound Vib (2015) 339:247–61. doi:10.1016/j.jsv.2014.11.012
28. Cottone F, Vocca H, Gammaitoni L. Nonlinear energy harvesting. Phys Rev Lett (2009) 102:080601. doi:10.1103/physrevlett.102.080601
29. Gammaitoni L, Neri I, Vocca H. Nonlinear oscillators for vibration energy harvesting. Appl Phys Lett (2009) 94:164102. doi:10.1063/1.3120279
30. Arrieta AF, Hagedorn P, Erturk A, Inman DJ. A piezoelectric bistable plate for nonlinear broadband energy harvesting. Appl Phys Lett (2010) 97(10):104102. doi:10.1063/1.3487780
31. Fuhong D, Pan D. Piezoelectric energy harvesting based on Bi-stable composite laminate. In: Manyala R, editor. Energy harvesting. London, UK: IntechOpen (2018).
32. Elsheikh A. Bistable morphing composites for energy-harvesting applications. Polymers (2022) 14:1893. doi:10.3390/polym14091893
33. Betts DN, Kim HA, Bowen CR, Inman DJ. Optimal configurations of bistable piezo-composites for energy harvesting. Appl Phys Lett (2012) 100:114104. doi:10.1063/1.3693523
34. Lin J, Lee B, Alphenaar B. The magnetic coupling of a piezoelectric cantilever for enhanced energy harvesting efficiency. Smart Mater Struct (2010) 19(4):045012. doi:10.1088/0964-1726/19/4/045012
35. Stanton S, McGehee C, Mann B. Nonlinear dynamics for broadband energy harvesting: Investigation of a bistable piezoelectric inertial generator. Physica D: Nonlinear Phenomena (2010) 239(10):640–53. doi:10.1016/j.physd.2010.01.019
36. Zhou S, Lallart MN, Erturk A. Multistable vibration energy harvesters: Principle, progress, and perspectives. J Sound Vibration (2022) 528:116886. doi:10.1016/j.jsv.2022.116886
37. Litak G, Margielewicz J, Gąska D, Wolszczak P, Zhou S. Multiple solutions of the tristable energy harvester. Energies (2021) 14:1284. doi:10.3390/en14051284
38. Zhang Y, Duan X, Shi Y, Yue X. Response analysis of the tristable energy harvester with an uncertain parameter. Appl Sci (Basel) (2021) 11:9979. doi:10.3390/app11219979
39. Horne J, Snowdon M, Jia Y. Using artificial gravity loaded nonlinear oscillators to harvest vibration within high g rotational systems. J Phys : Conf Ser (2018) 1052(1):012096. doi:10.1088/1742-6596/1052/1/012096
40. Xie Z, Kwuimy CAK, Wang Z, Huang W. A piezoelectric energy harvester for broadband rotational excitation using buckled beam. AIP Adv (2018) 2018:015125. doi:10.1063/1.5018077
41. Zhang J, Zhang J, Shu C, Fang Z. Enhanced piezoelectric wind energy harvesting based on a buckled beam. Appl Phys Lett (2017) 110:183903. doi:10.1063/1.4982967
42. Jung S-M, Yun K-S. Energy-harvesting device with mechanical frequency-up conversion mechanism for increased power efficiency and wideband operation. Appl Phys Lett (2010) 96:111906. doi:10.1063/1.3360219
43. Han D, Yun K-S. Piezoelectric energy harvester using mechanical frequency up conversion for operation at low-level accelerations and low-frequency vibration. Microsyst Technol (2015) 21:1669–76. doi:10.1007/s00542-014-2261-1
44. Vangbo M. An analytical analysis of a compressed bistable buckled beam. Sensors Actuators A: Phys (1998) 69(3):212–6. doi:10.1016/s0924-4247(98)00097-1
45. Hussein H, Younis MI. Analytical study of the snap-through and bistability of beams with arbitrarily initial shape. J Mech Robot (2020) 12(4):041001. doi:10.1115/1.4045844
46. Andò B, Baglio S, Bulsara AR, Marletta V. A bistable buckled beam based approach for vibrational energy harvesting. Sensors Actuators A: Phys (2013) 211:153–61. doi:10.1016/j.sna.2013.12.027
47. Andò B, Baglio S, Bulsara AR, Marletta V, Pistorio A. Performance investigation of a nonlinear energy harvester with random vibrations and sub-threshold deterministic signals. IEEE Trans Instrum Meas (2017) 66(5):992–1001. doi:10.1109/tim.2017.2649998
48. Andò B, Baglio S, Marletta V, Pistorio A, Bulsara AR. A measurement methodology for the characterization of a compensated nonlinear energy harvester for vertical operation. IEEE Trans Instrum Meas (2019) 68(8):3032–41. doi:10.1109/tim.2018.2869182
49. Andò B, Baglio S, Bulsara AR, Marletta V. A nonlinear energy harvester operated in the stochastic resonance regime for signal detection/measurement applications. IEEE Trans Instrum Meas (2020) 69(8):5930–40. doi:10.1109/tim.2019.2957913
50. Bulsara AR, Gammaitoni L. Tuning in to noise. Phys Today (1996) 49(3):39–45. doi:10.1063/1.881491
51. Andò B, Graziani S. Adding noise to improve measurement. IEEE Instrum Meas Mag (2001) 4(1):24–31. doi:10.1109/5289.911170
52. Andò B, Baglio S, Marletta V, Pistorio A, Bulsara AR. A low-threshold bistable device for energy scavenging from wideband mechanical vibrations. IEEE Trans Instrum Meas (2019) 68(1):280–90. doi:10.1109/tim.2018.2840587
53. Andò B, Baglio S, Marletta V, Bulsara AR. A wireless sensor node powered by nonlinear energy harvester. In: Proc. Of the 13th IEEE Sensors Conf; Valencia, Spain. IEEE (2014). p. 1583–6.
54. Andò B, Baglio S, Marletta V, Rosa RL, Bulsara AR. A nonlinear harvester to scavenge energy from rotational motion. In: Proceeding of the IEEE International Instrumentation and Measurement Technology Conference (I2MTC); Auckland, New Zealand. IEEE (2019). p. 1–6.
55. Andò B, Baglio S, Bulsara AR, Marletta V. Toward a self-powered vibration sensor: The signal processing strategy. Energies (2021) 14:754. doi:10.3390/en14030754
Keywords: non-linear energy harvesting, snap-through buckling, bistable systems, wideband vibrations, piezoelectric conversion
Citation: Andò B, Baglio S, Marletta V and Bulsara AR (2023) A comparison of linear and non-linear strategies for energy harvesting from mechanical vibrations. Front. Phys. 10:1032978. doi: 10.3389/fphy.2022.1032978
Received: 31 August 2022; Accepted: 28 November 2022;
Published: 06 January 2023.
Edited by:
Fernando A. Oliveira, University of Brasilia, BrazilReviewed by:
Fabrizio Bonani, Politecnico di Torino, ItalyMofeed Turky Rashid, University of Basrah, Iraq
Copyright © 2023 Andò, Baglio, Marletta and Bulsara. This is an open-access article distributed under the terms of the Creative Commons Attribution License (CC BY). The use, distribution or reproduction in other forums is permitted, provided the original author(s) and the copyright owner(s) are credited and that the original publication in this journal is cited, in accordance with accepted academic practice. No use, distribution or reproduction is permitted which does not comply with these terms.
*Correspondence: Bruno Andò, YnJ1bm8uYW5kb0B1bmljdC5pdA==