- 1Department of Water Conservancy and Civil Engineering, Tibet Agricultural and Animal Husbandry University, Linzhi, China
- 2Key Laboratory of Ministry of Education for Geomechanics and Embankment Engineering, Hohai University, Nanjing, China
- 3Jiangsu Research Center for Geotechnical Engineering Technology, Hohai University, Nanjing, China
To improve the stability of sand slopes in Southeast Tibet, the wet–dry cycle test, immersion test, and permeability test were carried out using polyvinyl alcohol (PVA) as the improving material. The improvement effect was evaluated by considering the unconfined compressive strength. The results have revealed that the unconfined compressive strength of the improved soil significantly increased with the PVA content, while the degradation of the improved soil by wet–dry cycling and water immersion weakened. However, the permeability of the improved soil slightly decreased compared with that of unmodified soil. Through scanning electron microscopy (SEM), it was found that PVA only forms an elastic network structure in the sand to wind and connect the soil particles, but pores remain in the sand. This indicates that the addition of PVA does not affect the permeability to a great extent but greatly increases the strength. The findings of this study provide a useful reference for the practical application of PVA.
Introduction
The engineering characteristics of sandy soil are poor, which increases the likelihood of various engineering geological problems. Specifically, sandy slopes are prone to deformation under rainfall conditions, which leads to slope instability [1, 2]. The permeability coefficient is an important physical index for measuring the soil’s permeability. The large permeability of sand causes local seepage deformation and damage to the soil by hydraulic erosion, in turn affecting the consolidation and stability of soil [3–6]. In recent years, as global warming increases, severe weather conditions, particularly heavy rainfall, frequently occur all over the world. Many natural disasters have been caused by heavy rainfall on roads in Nyingchi, Bomi, and Medog, Tibet. Heavy rainfall does not only erode the shallow soil of slopes but also raises the water levels of the Yarlung Zangbo River, Niyang River, Palong Zangbo River, and other rivers in Southeastern Tibet, thus accelerating the erosion caused by rivers to the soil of slopes, resulting in soil instability, which severely affects local traffic and development of the tourism industry.
Sand improvement and reinforcement have been the focus of studies in the field of engineering geology. Soil improvement and reinforcement technology refer to the addition of substances to the soil to exploit the interaction between the added substances and the soil and improve the soil’s engineering characteristics. The physical reinforcement materials are mainly geosynthetics, including geogrids, geotextiles, and various types of fiber. The interface forces between the reinforcement materials and the soil are used to enhance the compressive strength, shear strength, and tensile strength of the soil and improve the soil’s toughness. These reinforcement materials do not change the mineral composition of soil but do improve the strength of the soil through interface friction and a mesh overlapping structure. Fiber materials are dispersed in soil, and the connection between each unit is weak [7–10]. Chemical modification can also enhance the engineering characteristics of the soil. Traditional chemical modifiers, including cement, lime, and fly ash, can fill the pores between the soil particles and exert a bonding effect on the soil particles, which greatly improves the strength of the soil. However, such modified materials have a drastic reaction process and high alkalinity and change the mineral composition of the soil, which is harmful to the environment because the soil ecology is significantly affected. After reinforcement, the soil becomes brittle [11–13]. The polymer modifier is a new type of improved reinforcement material that uses polymer cross-linking to form a three-dimensional structure to wrap and cement soil particles. Some polymer modifiers have highly active groups and can be used for the reaction of active substances in soil to form new chemical groups and enhance the bonding strength of various soil parts. Some polymers do not react with soil particles and instead form a network structure after dehydration and drying. The film formed by polyvinyl alcohol (PVA) has good tensile strength and the polymers are uniformly distributed in the soil, which limits the soil particles to a certain position, increases the strength of the soil, and improves the soil’s durability [14, 15]. Most high-molecular polymers are used as auxiliary materials for improvement but cannot be separated from traditional curing agents such as cement [16–19].
In this study, the organic polymer PVA-20-99H was used as an improving material because it is capable of coating sand particles, increasing the interaction force between the particles, and changing the engineering characteristics of sand. The effects of the PVA content, wet–dry cycles, and soaking time on the engineering characteristics of the improved sand were investigated, and the reinforcement mechanism of PVA 20-99 was analyzed using scanning electron microscopy (SEM). The results can be useful as a reference in the development of engineering applications.
Experimental Schemes
Experimental Materials and Sample Preparation
Sand
The sand used in the test was obtained from the Palong-Tibet River in Southeast Tibet. Figure 1 shows the satellite map of the sampling site. The samples had an effective particle size of approximately 0.02 mm, a limited particle size of approximately 0.13 mm, an uneven coefficient of 6.23, and a curvature coefficient of 1.44. The particle size distribution was mainly in the range of 0–0.316 mm, and more than 50% of the particles with a particle size d > 0.075 mm were fine-grained sand with good gradation. Figure 2A shows the sand used in the test.
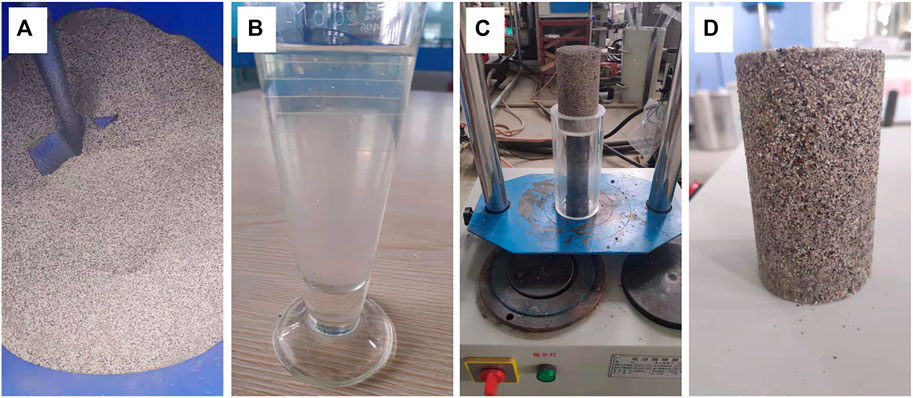
FIGURE 2. Test materials, sample preparation, and sample appearance: (A) sand used in test; (B) polyvinyl alcohol gel; (C) sample-making process; (D) sample appearance.
Polyvinyl Alcohol
The reinforcing material used in the test was an organic polymer curing agent called PVA 20-99 (PVA-20-99H). The PVA is a white floccule at normal temperature and insoluble in cold water. After being dissolved in boiling water, it forms a stable PVA gel, which is light yellow, as shown in Figure 2B. After being dissolved, it can be diluted with water, and after being dried and dehydrated, it is still insoluble in cold water. The basic properties of this polymer are listed in Table 1.
Sample Preparation
The sampled soil was air-dried and subsequently screened using a sieve with 2.5 mm square holes. According to the mass ratio of PVA gel to sand, four proportions of 6, 8, 10, and 12% were added, and the effective substance content of the used PVA solution was 5.34%. The sample was made using the static pressure method and demolded using an electric demolding machine. This process is shown in Figure 2C. The sample diameter was 50 mm and the height was 100 mm, as shown in Figure 2D. Each sample was set with three parallel samples to avoid test errors.
Test Apparatus and Procedures
After preparation and standing for 1 day, the samples were air-dried and cured under simulated natural conditions for 3, 7, 14, and 28 days. When the curing age reached 7 days, the samples were removed and subjected to wet–dry cycle testing and immersion testing. When the specified test times were reached, one sample of each ratio was reserved for a subsequent SEM experiment, and the remaining samples were subjected to unconfined compression testing using a triaxial testing machine with a loading rate of 1 mm/min.
Wet–dry cycling consists of two processes: saturation and drying. The saturation process of the sample was carried out as follows:
1) After placing a permeable stone at the bottom of the container, water was added to the container until the water surface was as high as the permeable stone, and the sample was then placed on the permeable stone.
2) Water was gradually added until the sample was completely submerged in water, and permeable stones were placed on top of the sample.
3) A certain amount of water was added to the container every 2 h to keep the water level in the container unchanged.
4) After 24 h of saturation, the sample was removed.
The drying process was carried out as follows:
1) The saturated sample was placed in a drying oven at 40°C.
2) The sample was weighed every 4 h during the drying process to ensure that the water content satisfied the test requirements.
3) When the moisture content stopped changing (after approximately 40 h), the drying ended. The entire process is shown in Figure 3.
In the immersion test, drying was carried out after immersion for 3, 5, 7, and 10 days to simulate the immersion process, which is longer than a single wet–dry cycle. Additionally, an unconfined compressive strength test was carried out.
Results Analysis and Discussion
Influence of Polyvinyl Alcohol on Unconfined Compressive Strength of Sand
Figure 4A shows the stress–strain curves of different PVA contents after curing for 3 days. As can be seen, the unconfined compressive strength of the stabilized sand increased with the PVA content. With 6% PVA content, the unconfined strength was 147.70 kPa; with 12% PVA content, the unconfined strength was only 320.86 kPa. Therefore, the strength did not improve as the PVA content increased. Additionally, the stress–strain curve fluctuates because some areas with high water content still existed in the samples cured for 3 days. In these areas, the PVA was not dehydrated to form an elastic screen that provides strength. As the strain increased, the PVA screen that provided strength appeared to separate from the soil particles or break, which resulted in a not raise in strength.
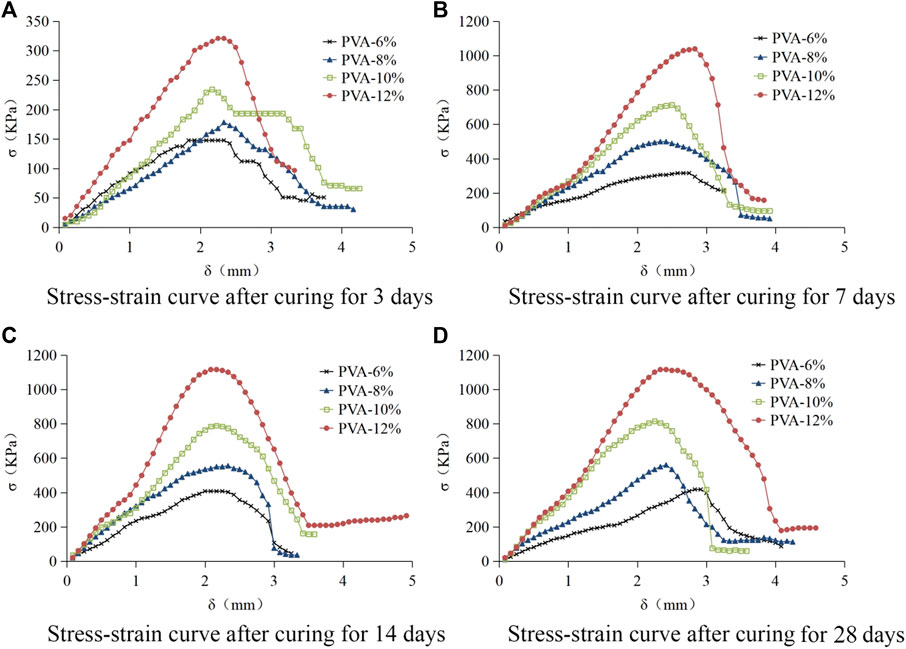
FIGURE 4. Stress–strain curves obtained under different curing ages: (A) curing for 3 days. (B) curing for 7 days. (C) curing for 14 days. (D) curing for 28 days.
In the curing process, the water content in the sample gradually became uniform and the PVA formed a complete network structure to provide strength. Figure 4B shows the stress–strain curve of different PVA contents under outdoor curing for 7 days. The unconfined compressive strength of the improved sand with 12% content increased to 1038.96 kPa, which is significantly higher than that obtained under curing for 3 days. Figure 4C shows the stress–strain curve obtained under air-dried curing for 14 days. Compared with curing for 7 days, the strength slightly increased because the unconfined compressive strength of PVA in the sample increased by continuous dehydration, and the unconfined strength obtained with 12% PVA content reached 1115.36 kPa. Figure 4D shows the stress–strain curve obtained after air-dried curing for 28 days. The strength is essentially the same as that obtained under curing for 14 days and did not obviously increase compared with that obtained under curing for 7 days. Figure 5 shows a typical photograph of the damage of the improved sample.
Figure 6A shows the change curve of the unconfined compressive strength of the improved soil and the PVA addition amount under different curing ages. As can be seen, when the sample was air-dried and cured for 3 days, the lubrication of water among the soil particles was the main controlling factor because the sample contained more water at this time and the strength increase was not obvious. After the water content became uniform, the PVA formed an elastic three-dimensional screen to provide strength, and the PVA content became the main controlling factor. As the PVA addition amount increased, the unconfined compressive strength of the improved soil obviously increased. Figure 6B shows the variation curve of the unconfined compressive strength with the curing time under different PVA contents. As can be seen from the graph, the strength of the air-dried curing rapidly increased in the 3–7-day stage, and the unconfined compressive strength of the improved soil slowly increased in the 7–14-day stage. After 14 days, the unconfined compressive strength of each content tended to be stable, and the unconfined compressive strength obtained under curing for 28 days was essentially the same as that obtained under curing for 14 days. Ling et al. [20] added PVA to improved soil and cured it for 28 days. They reported that the PVA fiber significantly improved the unconfined compressive strength. Zuanfeng Pan et al. [19] added PVA fiber directly to soil and reported that as the PVA fiber amount increased, the fiber agglomerated in the soil and affected the soil’s strength. Their test results revealed that this problem did not occur when PVA gel was used.
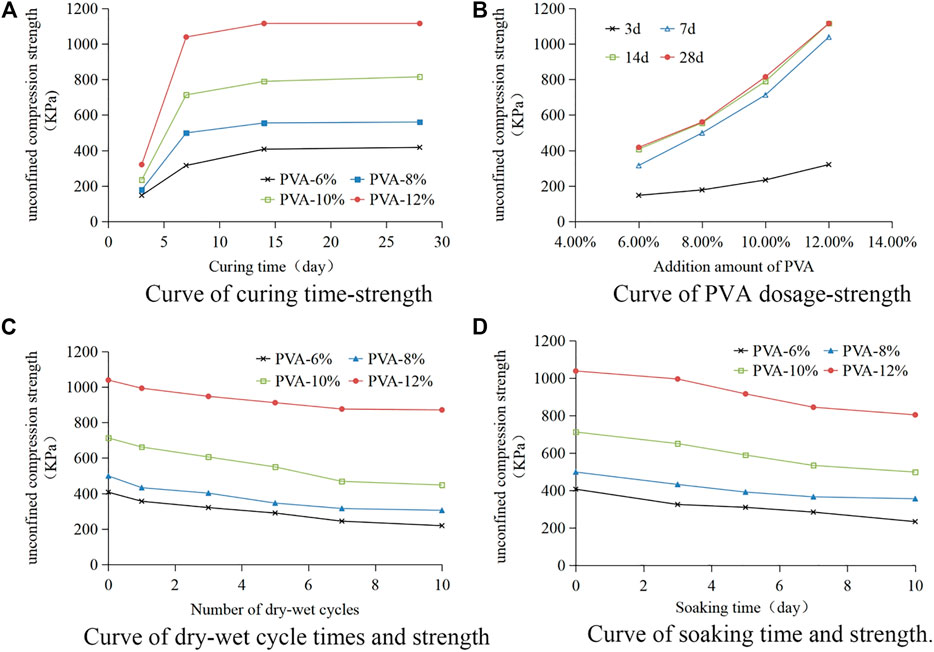
FIGURE 6. Unconfined compressive strength under different conditions: (A) curing time-strength. (B) PVA dosage-strength. (C) dry-wet cycle times and strength. (D) soaking time and strength.
Influence of Wet–Dry Cycles on Unconfined Compressive Strength of Improved Sand
Figure 6C shows the relationship between the unconfined compressive strength and the number of wet–dry cycles with different PVA contents. The non-stabilized soil sample disintegrated when immersed in water, but the PVA-stabilized soil sample did not break or peel after being immersed in water. The unconfined compressive strength essentially exhibited the same change trend as the number of wet–dry cycles increased. The unconfined compressive strength of the stabilized soil samples decreased with the increase of the wet–dry cycles. Moreover, after 10 wet–dry cycles, the unconfined compressive strength of the improved soil with 12% PVA content decreased from 1038.96 kPa to 875.99 kPa and was still much higher than the unconfined compressive strength of the non-stabilized soil samples cured for 7 days (10.19 kPa).
Cracks were not observed on the surface of the sample after the wet–dry cycles because the PVA gel lost water and clung to the surface of the soil particles during the drying process, which limited the displacement of soil particles and resulted in the closer arrangement of soil particles. Because the PVA gel is insoluble in water, the degradation of the improved soil caused by the wet–dry cycles slowed down. Ye et al. [21] reported that if the curing time is short, the unrestricted compressive strength first increases and then decreases with the increase of the wet–dry cycles. After 10 cycles, the unrestricted compressive strength tends to be stable. For samples with long curing times, as the wet–dry cycles increased, the unrestricted compressive strength always decreased. Kaveh Roshan reported that the addition of fibers reduced the uniaxial strength loss under wet–dry cycles [22].
Influence of Immersion on Unconfined Compressive Strength of Improved Sand
Figure 6D shows the relationship between the unconfined compressive strength and the soaking days under different PVA contents. As can be seen, the unconfined compressive strength of the stabilized sand gradually decreased with the increase of the soaking days, and the unconfined compressive strength of the stabilized sand with 6, 8, 10, and 12% PVA gel content after soaking for 10 days was 57.50, 71.43, 70.00, and 77.45%, respectively, under curing for 7 days.
With a PVA content of 6%, the strength ratio of the stabilized sand after immersion was smaller compared with that obtained with a PVA content of 12%, and the unconfined compressive strength was still 804.69 kPa after immersion for 10 days, indicating that the deterioration of soil by immersion diminishes with the increase of PVA content. Similar results have been obtained by Liu et al. [23], who reported that the polymer obviously enhanced the stability of the soil in water.
Effect of PVA Content on Permeability
Sand particles in contact with each other form a skeleton structure, and pores function as seepage channels. After being added to sand, PVA gel becomes uniformly distributed in the soil and wraps sand particles to form a three-dimensional network structure.
The constant head test uses the following formula to calculate the permeability coefficient:
where
As shown in Figure 7, according to the formula, the permeability coefficient of plain soil is 8.61E-03. When the PVA content was 6, 8, 10, and 12%, the permeability coefficients were 8.42E-03, 8.37E-03, 8.27E-03, and 8.20E-03, respectively. As the PVA content increased, the permeability coefficient slightly decreased, but the overall change was not significant. However, the unconfined compressive strength of the improved soil obviously increased, which indicates that the addition of PVA gel did not obviously fill or block the pores of the sample. Notably, the maximum content of PVA gel is 12%, but the effective substance content of the PVA gel is only 5.34%, which means that approximately 95% of PVA gel is water.
As the curing time increased, the PVA gel gradually dehydrated and its strength improved. Additionally, with the separation of water, the remaining effective substance accounted only for approximately 0.6% of the soil weight, at most. Because PVA does not react to produce new substances to fill the pores, it is obvious that such a small amount of PVA does not have an obvious effect on pore filling, and the change of the permeability coefficient conforms to the known law. Therefore, PVA gel with higher effective substance content should be added in a later stage. Sito Ismanti [24] used bamboo chips to reinforce sand and reported that the size and content of the bamboo chips had a significant effect on permeability. Cabalar [25] solidified sand with xanthan gum and reported that the permeability of sand decreased by 3–4 orders of magnitude. Huang [26] reported that the addition of latex and sand may lead to a small decrease in permeability. Chegenizadeh [27] reported that natural fiber can increase permeability.
Mechanism of PVA Curing Sand
Figure 8A shows a SEM photograph of the sand used in the test; the photograph was magnified 150 times. As can be seen, the sand used in the test was packed with loose particles with clear and obvious particle boundaries, and cementation did not exist between the sand particles. Figure 8B shows the SEM image after adding 6% PVA. At this time, the boundary of the soil particles was blurred, and there were filaments connecting the sand particles in the pores. The soil particles were cemented with PVA and were no longer loosely stacked but rather had a three-dimensional structure. Figure 8C shows the SEM image of the modified soil with 12% PVA. At this time, obvious cementation substances existed among the soil particles, and it can be seen that the network structure produced by the PVA gel was wrapped around the soil particles. Figure 8D shows an electron micrograph with 12% PVA addition at a magnification of 500 times, from which it can be clearly seen that PVA existed in the pores.
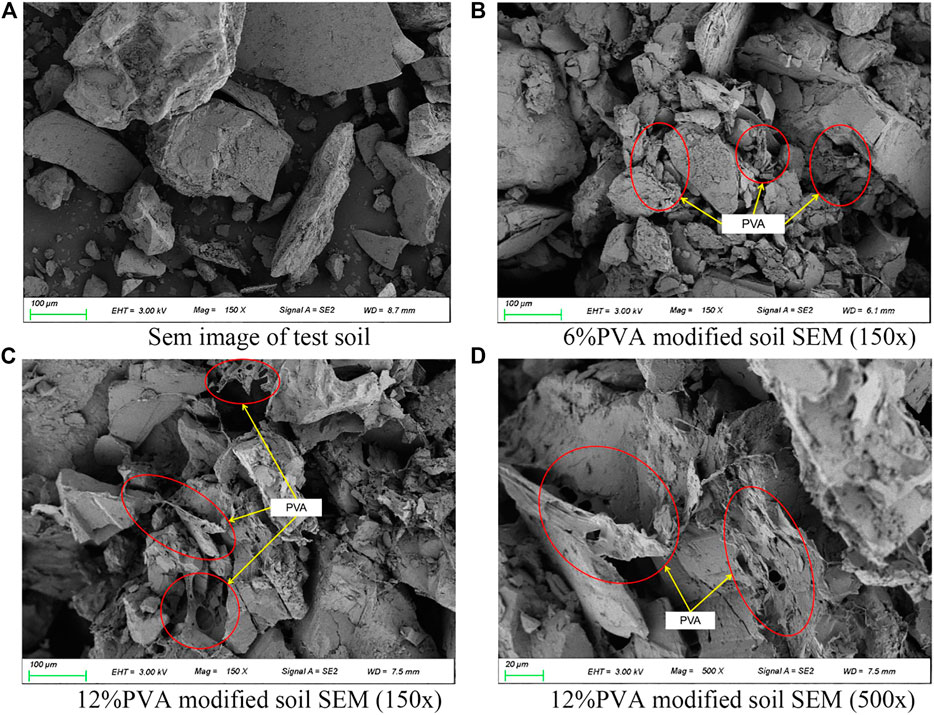
FIGURE 8. Scanning electron microscopy image: (A) test soil. (B) 6% PVA modified soil (150X). (C) 12% PVA modified soil (150X). (D) 12% PVA modified soil (500X).
As the PVA gel was added, the volume of PVA shrank with the loss of water and finally formed a complete three-dimensional network structure close to the surface of the sand particles, which limited the displacement of the soil particles and increased the strength of the soil through its own strength. However, a large number of pores still existed in the cured samples, and the density was low. The amount of PVA effective substances was still small and could only fill a few pores. After the PVA gel was added to the samples for dehydration, a complete three-dimensional network structure formed and connected the pores. The connected pores and the PVA only filled a few pores, which only slightly changed the permeability of the samples.
Conclusion
Based on the experimental data and the above discussion, the following conclusions can be drawn from this study:
1) The addition of PVA improved the unconfined compressive strength of sand, and the unconfined compressive strength of the sample with 12% PVA solution reached 1038.96 kPa, which is much higher than that of non-stabilized soil (10.19 kPa).
2) The strength of PVA-stabilized sand gradually decreased under wet–dry cycles, and the strength after 10 wet–dry cycles was approximately 80% of that obtained without wet–dry cycling.
3) As the soaking days increased, the unconfined compressive strength of the PVA-stabilized soil gradually decreased. After soaking for 10 days, the unconfined compressive strength with 12% PVA content was 804.69 KPa, which is still much higher than the 7-day strength of non-stabilized soil.
4) With the addition of PVA gel, the permeability coefficient slightly decreased, but the change was small. Additionally, the content of the PVA effective substances was only approximately 0.6% of the soil weight, which indicates that PVA can effectively improve the unconfined compressive strength of improved sand without changing the permeability.
5) After dehydration, the PVA wrapped and wound the sand particles, which interconnected to form a spatial three-dimensional network structure, thereby limiting the displacement of soil particles and significantly increasing the strength of soil through its own strength.
Data Availability Statement
The raw data supporting the conclusion of this article will be made available by the authors, without undue reservation.
Author Contributions
ZL contributed to the work concept or design, data collection, and drafting of papers, and approved the final manuscript to be published. ZZ was responsible for data collection and analysis and approved the final version of the manuscript to be published. HS contributed to data collection and approved the final manuscript to be published. WL conducted the data analysis and important revision of the paper and approved the final version of the manuscript to be published. BW and PW made important amendments to the manuscript and approved the final version to be published.
Funding
This work was financially supported by the Fourth Batch of Flexible Talent Introduction Project of Tibet Agriculture and Animal Husbandry College and Key Project of Natural Fund of Tibet Autonomous Region (XZ 2019 ZR G-56(Z)).
Conflict of Interest
The authors declare that the research was conducted in the absence of any commercial or financial relationships that could be construed as a potential conflict of interest.
Publisher’s Note
All claims expressed in this article are solely those of the authors and do not necessarily represent those of their affiliated organizations, or those of the publisher, the editors and the reviewers. Any product that may be evaluated in this article, or claim that may be made by its manufacturer, is not guaranteed or endorsed by the publisher.
References
1. Zhang FB, Yang MY, Li BB, Li ZB, Shi WY. Effects of Slope Gradient on Hydro-Erosional Processes on an Aeolian Sand-Covered Loess Slope under Simulated Rainfall. J Hydrol (2017) 553:447–56. ISSN 0022-1694. doi:10.1016/j.jhydrol.2017.08.019
2. Van Den Berg JH, Van Gelder A, Mastbergen DR. The Importance of Breaching as a Mechanism of Subaqueous Slope Failure in fine Sand. Sedimentology (2002) 49(1):81–95. doi:10.1111/j.1525-139x.2006.00168.x-i1
3. Sepah VA, Parveen S, Balraj S, Zand M. Comparative Evaluation of Infiltration Models[J]. Ksce J Civil Eng (2018) 22(10):4173–84. doi:10.1007/s12205-018-1347-1
4. Morbidelli R, Saltalippi C, Flammini A, Govindaraju RS. Role of Slope on Infiltration: A Review[J]. J Hydrol (2018) 557:878–86. doi:10.1016/j.jhydrol.2018.01.019
5. Sandoval G, Galobardes I, Teixeira RS, Toralles BM. Comparison between the Falling Head and the Constant Head Permeability Tests to Assess the Permeability Coefficient of Sustainable Pervious Concretes[J]. Case Stud Construction Mater (2017) 7:317–28. doi:10.1016/j.cscm.2017.09.001
6. Shin KJ, Bae W, Choi S-W, Son MW, Lee KM. Parameters Influencing Water Permeability Coefficient of Cracked concrete Specimens. Construction Building Mater (2017) 151:907–15. doi:10.1016/j.conbuildmat.2017.06.093
7. Mo Y-xin, Pang J-yong, Huang J-kun, Russo P. Dynamic Mechanical Properties and Fractal Characteristics of Polypropylene Fiber-Reinforced Cement Soil under Impact Loading[J]. Adv Mater Sci Eng (2019) 2019:1–14. doi:10.1155/2019/3735891
8. Duan X-lei, Zhang J-shuang, Šišková A. Mechanical Properties, Failure Mode, and Microstructure of Soil-Cement Modified with Fly Ash and Polypropylene Fiber[J]. Adv Mater Sci Eng (2019) 2019:1–13. doi:10.1155/2019/9561794
9. Aldeeky H, Al Hattamleh O, Abu Alfoul B. Effect of Sand Placement Method on the Interface Friction of Sand and Geotextile. Int J Civ Eng (2016) 14(2):133–8. doi:10.1007/s40999-016-0019-0
10. Yetimoglu T, Salbas O. A Study on Shear Strength of Sands Reinforced with Randomly Distributed Discrete Fibers. Geotextiles and Geomembranes (2003) 21(2):103–10. doi:10.1016/s0266-1144(03)00003-7
11. Horpibulsuk S, Chinkulkijniwat A, Cholphatsorn A, Suebsuk J, Liu MD. Consolidation Behavior of Soil-Cement Column Improved Ground. Comput Geotechnics (2012) 43:37–50. doi:10.1016/j.compgeo.2012.02.003
12. Chai J-C, Miura N. Cement/Lime Mixing Ground Improvement for Road Construction on Soft Ground - ScienceDirect[J]. Ground Improvement Case Histories (2005) 6: 279–303. doi:10.1016/b978-0-08-100191-2.00001-0
13. Song Z, Zhang D, Mao Y, Mu Y, Zhang K, Zhang Q. Behavior of Lime-Stabilized Red Bed Soil after Cyclic Wetting-Drying in Triaxial Tests and SEM Analysis. Adv Mater Sci Eng (2020) 2020:12. Article ID 4230519. doi:10.1155/2020/4230519
14. Zhang Z, Zhang Q. Matrix Tailoring of Engineered Cementitious Composites (ECC) with Non-oil-coated, Low Tensile Strength PVA Fiber. Construction Building Mater (2018) 161:420–31. doi:10.1016/j.conbuildmat.2017.11.072
15. Zhang LS, Wu WZ, Wang JL. Immobilization of Activated Sludge Using Improved Polyvinyl Alcohol (PVA) Gel. J Environ Sci (China) (2007) 19(011):1293–7. doi:10.1016/s1001-0742(07)60211-3
16. Zp A, Chang WB, Jl C, Wang W, Liu J. Study on Mechanical Properties of Cost-Effective Polyvinyl Alcohol Engineered Cementitious Composites (PVA-ECC)[J]. Construction Building Mater (2015) 78:397–404. doi:10.1016/j.conbuildmat.2014.12.071
17. Silva GGD, Sobral PJA, Carvalho RA, Bergo PVA, Mendieta-Taboada O, Habitante AMQB. Biodegradable Films Based on Blends of Gelatin and Poly (Vinyl Alcohol): Effect of PVA Type or Concentration on Some Physical Properties of Films. J Polym Environ (2008) 16(4):276–85. doi:10.1007/s10924-008-0112-9
18. Yu J, Yao J, Lin X, Li H, Lam JYK, Leung CKY, et al. Tensile Performance of Sustainable Strain-Hardening Cementitious Composites with Hybrid PVA and Recycled PET Fibers. Cement Concrete Res (2018) 107:110–23. doi:10.1016/j.cemconres.2018.02.013
19. Zhang P, Li Q-f., Wang J, Shi Y, Ling Y-f., Effect of PVA Fiber on Durability of Cementitious Composite Containing Nano-SiO2. Nanotechnology Rev (2019) 8(1):116–27. doi:10.1515/ntrev-2019-0011
20. Ling Y, Zhang P, Wang J, Chen Y. Effect of PVA Fiber on Mechanical Properties of Cementitious Composite with and without nano-SiO2[J]. Construction Building Mater (2019) 229:117068. doi:10.1016/j.conbuildmat.2019.117068
21. Ye H, Chu C, Xu L, Guo K, Li D. Experimental Studies on Drying-Wetting Cycle Characteristics of Expansive Soils Improved by Industrial Wastes[J]. Adv civil Eng (2018) 2018:2321361. doi:10.1155/2018/2321361
22. Roshan K, Choobbasti AJ, Kutanaei SS. Evaluation of the Impact of Fiber Reinforcement on the Durability of Lignosulfonate Stabilized Clayey Sand under Wet-Dry Condition. Transportation Geotechnics (2020) 23:100359. doi:10.1016/j.trgeo.2020.100359
23. Liu J, Bai Y, Li D, Wang Q, Qian W, Wang Y, et al. An Experimental Study on the Shear Behaviors of Polymer-Sand Composite Materials after Immersion. Polymers (2018) 10(8):924. doi:10.3390/polym10080924
24. Ismanti S, Yasufuku N. Effect of Bamboo Chips in Cemented Sand Soil on Permeability and Mechanical Properties in Triaxial Compression. Int J Geol Environ Eng (2016) 10:917–23.
25. Cabalar AF, Wiszniewski M, Skutnik Z. Effects of Xanthan Gum Biopolymer on the Permeability, Odometer, Unconfined Compressive and Triaxial Shear Behavior of a Sand. Soil Mech Found Eng (2017) 54(5):356–61. doi:10.1007/s11204-017-9481-1
26. Huang B, Wu H, Shu X, Burdette EG. Laboratory Evaluation of Permeability and Strength of Polymer-Modified Pervious concrete. Construction Building Mater (2010) 24(5):818–23. doi:10.1016/j.conbuildmat.2009.10.025
Keywords: sand, polyvinyl alcohol, wet–dry cycles, mechanical properties, permeability
Citation: Li Z, Zhao Z, Shi H, Li W, Wang B and Wang P (2021) Experimental Investigation of Mechanical, Permeability, and Microstructural Properties of PVA-Improved Sand Under Dry-Wet Cycling Conditions. Front. Phys. 9:761754. doi: 10.3389/fphy.2021.761754
Received: 20 August 2021; Accepted: 20 September 2021;
Published: 25 October 2021.
Edited by:
Wanqing Shen, Université de Lille, FranceCopyright © 2021 Li, Zhao, Shi, Li, Wang and Wang. This is an open-access article distributed under the terms of the Creative Commons Attribution License (CC BY). The use, distribution or reproduction in other forums is permitted, provided the original author(s) and the copyright owner(s) are credited and that the original publication in this journal is cited, in accordance with accepted academic practice. No use, distribution or reproduction is permitted which does not comply with these terms.
*Correspondence: Peiqing Wang, NDk3NDUwNzM0QHFxLmNvbQ==