- 1Institute for Nuclear Research (Atomki), Debrecen, Hungary
- 2Department of Theoretical Physics, Doctoral School of Physics, Faculty of Science and Technology, University of Debrecen, Debrecen, Hungary
- 3Diehl Aviation Hungary Kft, Debrecen, Hungary
We present an extension of fiber bundle models to describe the mechanical response of systems which undergo a sequence of stick-slip cycles taking into account the changing stiffness and the fluctuating number of slip events of local material elements. After completing all stick-slip cycles allowed, fibers can either ultimately break or can keep their final stiffness leading to softening or hardening of the bundle, respectively. Under the assumption of global load sharing we derive analytic expressions for the constitutive response of the bundle with both quenched and annealed disorder of the failure thresholds where consecutive slips occur. Our calculations revealed that on the macro-scale the bundle exhibits a plastic behavior, which gets more pronounced when fibers undergo a higher number of stick-slip cycles with a gradually degrading stiffness. Releasing the load a permanent deformation remains, which increases monotonically for hardening bundles with the maximum deformation reached before unloading starts, however, in the softening case a non-monotonous behavior is obtained. We found that the macroscopic response of hardening bundles is more sensitive to fluctuations of the number of stick-slip cycles allowed than of the softening ones. The quenched and annealed disorder of failure thresholds gives rise to the same qualitative macro-scale behavior, however, the plastic response is found to be stronger in the annealed case.
1 Introduction
Fibre bundle models (FBM) are one of the most important theoretical approaches to the damage and fracture of disordered materials [1]. In the framework of FBMs, the specimen is discretized as a bundle of parallel fibers which are subject to an external load along the fibers’ direction [2, 3]. The Young modulus of fibers is typically assumed to be constant so that materials’ heterogeneity is entirely represented by the randomness of the strength of fibers. Even in their simplest form, FBMs provided a deep insight into the process of damaging of heterogeneous materials [2, 4, 5] making also possible to embed fracture processes into the general framework of statistical physics [1, 6, 7] and to clarify its analogy to phase transitions and critical phenomena [8–13].
Soon after the introduction of the basic concept of FBMs by Peires in 1927 [14], the model had been extended to capture time dependence and fatigue effects [15]. During the past decades subsequent developments of the model have demonstrated that varying the mechanical response [16] (brittle, plastic) and rheological (visco-elastic) behavior [17–20] of individual fibers, furthermore, the degree of strength disorder [21–23], range of load sharing (local, global) [11, 24, 25] following breaking events, and the way of loading [19, 20, 26] (quasi-static, creep, fatigue) the model is able to capture a broad spectrum of materials’ behavior. Due to this flexibility, the model has gained a wide variety of applications from the fracture of fiber reinforced composites [25, 27], through granular materials, where force chains were treated as load bearing fibers [28, 29], to the rupture of biological materials [30].
Recently, we have proposed an extension of FBMs [31, 32] to describe the mechanical response of systems with a complex micro-structure which respond to external loading by local rearrangements, for instance, of particles like in granular materials [28, 33] and in agglomerates of dipolar particles [34], or by an activation of internal stored length such as spider silk [35]. A special area where stick-slip dynamics can be exploited for technological applications, is the development of nanocomposites, in particular carbon nanotube (CNT) composites, where CNTs are embedded in a polymeric matrix. One of the interesting properties of CNT nanocomposites is the ability to absorb vibrational energy which, together with high strength and fatigue tolerance, makes them perfect candidates for new multifunctional composite structures [36]. Recent experimental studies have revealed that the damping enhancement can be attributed to the CNT-matrix stick-slip caused by the severe elastic mismatch which leads to shear stress localization at the interfaces [37]. To represent the microscale complexity underlying stick-slip dynamics, fibers of our model were assumed to undergo a sequence of stick-slip events: when the local load reaches a failure threshold the fiber does not break, instead its load drops down to zero but the fiber has the ability of support load again. The model has been successfully applied to analyze the mechanical response of sheared granular materials [33] and the effect of root reinforcement on the stability of soils [29]. Complementing the stick-slip FBM with a healing mechanism it proved to be capable to describe the failure process of snow [38, 39].
In the basic setup of the model it is assumed that fibers keep their original stiffness during their entire damage history [31, 32], which is a crude simplification. It is reasonable to assume that restructuring events give rise to a degradation of the local stiffness or to hardening, e.g., due to damage or activating stored length inside the material, respectively. Additionally, fibers of the bundle are allowed to undergo the same number of slip events although in an extended sample the number of possible restructurings may have a spatial variation. To make the stick-slip FBM more realistic, in the present paper we resolve these limitations by allowing for the change of the stiffness of fibers as a result of slip events, and we capture the fluctuations of the number of stick-slip cycles allowed for fibers. Under the assumption of global load sharing, we derive analytic expressions for the macroscopic constitutive response of the bundle both for quenched and annealed disorder of failure thresholds where slip is activated. The stiffness change is treated in a multiplicative way which allows for a unified framework of stiffness degradation and stiffening. We demonstrate that the stick-slip dynamics results in a plastic behavior on the macro-scale and explore consequences of the new degrees of freedom of the model.
2 Stick-Slip Dynamics with Varying Stiffness
The model consists of N parallel fibers which are characterized by the same initial stiffness value
where
After the slip has been completed, the fiber gets sticked so that it can support load again described by the constitutive law
where ε denotes the strain of the fiber. Eq. 2 takes into account that the relaxed length of the fiber is extended with the strain threshold
which can be greater or lower than the initial value E, for
For the interaction of fibers we assume global load sharing in such a way that fibers are stretched between two hard loading plates which ensure a global response of the entire system following local slipping events. However, global load sharing does not imply equal load of fibers in our stick-slip system since fibers which suffered a different number of slips have different stiffnesses and relaxed lengths, hence, they keep different loads. After fixing the type of disorder the threshold strains of slips can be determined from the corresponding stress thresholds. A fiber which has slipped k times at the consecutive strain thresholds
where the sum of failure thresholds
2.1 Quenched Disorder of Failure Thresholds
Quenched disorder means that slips of a fiber always occur at the same stress threshold
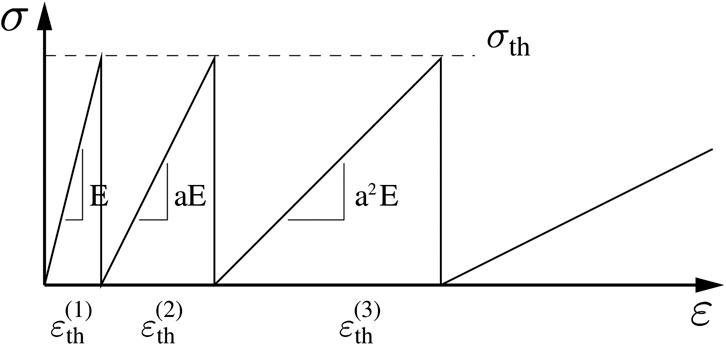
FIGURE 1. Mechanical response of a single fiber in the case of quenched disorder when the slipping threshold
The relaxed length
For the sum of the geometric series inside the brackets we introduce the shorthand notation
2.1.1 Derivation of the Constitutive Equation With Varying Stiffness
To obtain a closed analytic form for the constitutive equation, we assume strain controlled loading of the bundle between two hard plates. At a given strain ε during the loading process, the bundle is a mixture of subsets of fibers which are either intact (no slip), or have suffered different number of slip events k, where
where the failure index
The macroscopic constitutive response of the system can be obtained by summing up the load
The partial loads
where the first, second, and third terms provide the contribution of intact fibers, of the fibers which have suffered exactly
With the asymptotic stiffness
The constitutive behavior of the stick-slip bundle is illustrated in Figure 2 for several values of the maximum number K of slip events at a fixed value of the stiffness parameter
where the parameter λ is set to
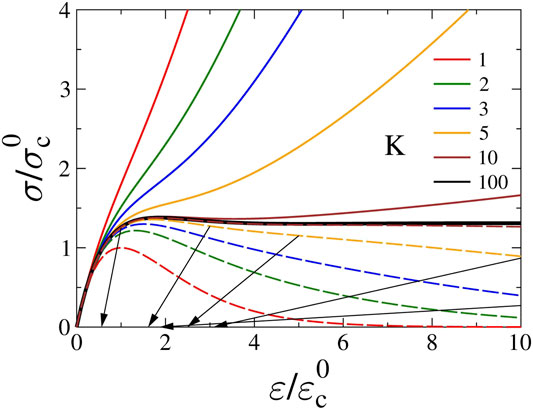
FIGURE 2. Constitutive behavior of the stick-slip bundle with quenched disorder of the sliding thresholds according to Eq. 8 including both cases of remaining stiffness (continuous lines) and ultimate failure of fibers (dashed lines) after completing K slip events. The arrows highlight unloading curves, which start at different strains
2.1.2 Effect of the Varying Fiber Stiffness on the Macroscopic Response of Stick-Slip Bundles
The value of the stiffness parameter a has an important effect on the overall behaviour of the system. It can be inferred from Eqs 5, 6 that for the stiffening case
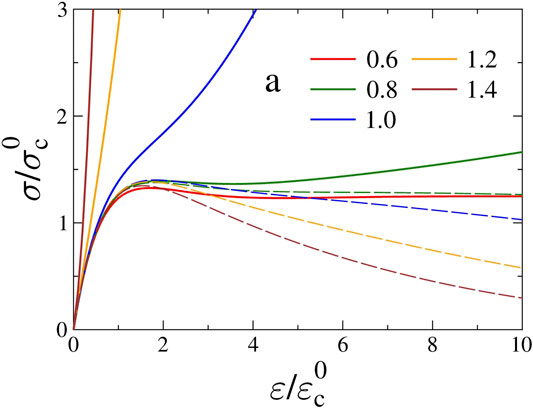
FIGURE 3. The effect of the value of the stiffness parameter a on the macroscopic behavior of a bundle where all fibers are allowed to perform
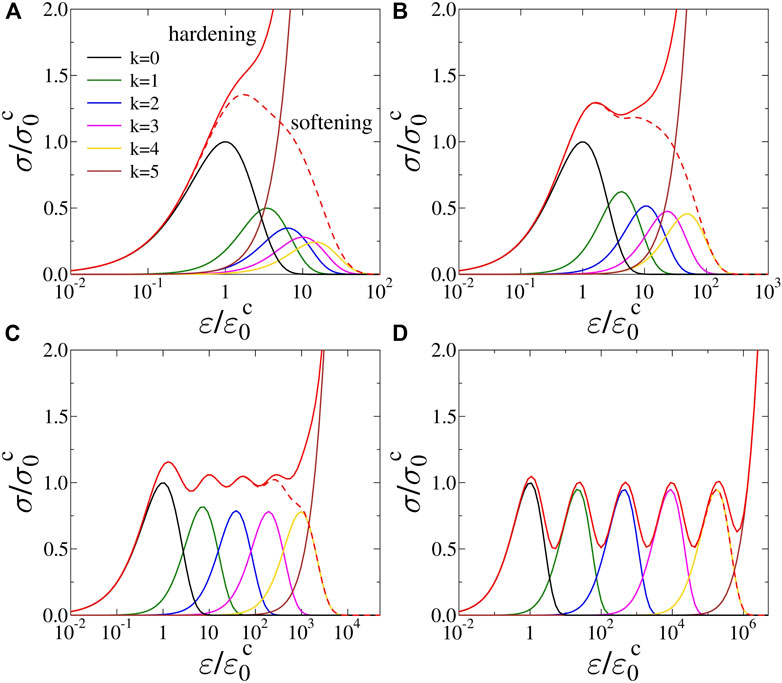
FIGURE 4. Emergence of the plateau regime as the stiffness parameter a decreases at a fixed value of the maximum number
The separation of the
It is a very important consequence of the stick-slip dynamics that upon unloading
For intermediate starting points
which converges to
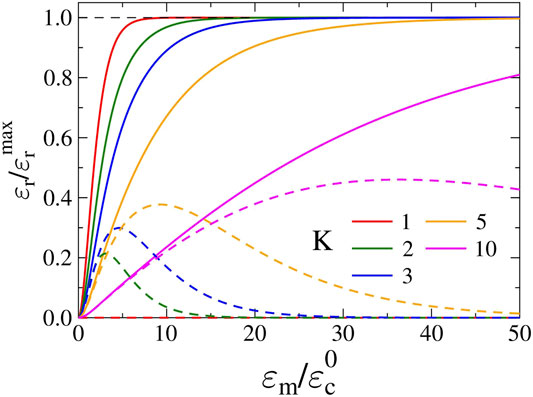
FIGURE 5. Permanent deformation
Examples of unloading curves are presented in Figure 2 for the case of softening bundles, where fibers break after K slips. Since no slip can occur under a decreasing load, the unloading curves are always straight lines and their slope, i.e. the unloading modulus decreases with increasing
The expression shows that the unloading modulus
For the unloading modulus of softening bundles the last term inside the brackets has to be skipped to take into account the ultimate breaking of fibers. It can also be inferred from Figure 2 that the permanent deformation of softening bundles is not monotonous, i.e. the
It follows from Figure 4 that once a plastique plateau can be identified, its extension is practically the same for hardening (no breaking) and softening (breaking after K slips) bundles. At a given parameter set
and hence, of the extension of the plateau, when fibers get stiffer after slip events. However, for the case of stiffness degradation
3 Fluctuating Maximum Number of Slip Events
Fiber bundle models with stick-slip dynamics can be applied to understand damage accumulation and fracture in a large variety of systems where micro-scale restructuring plays a dominating role. However, in the present form of the model the maximum number of allowed stick-slip cycles is fixed for all the fibers, which is a very strong constraint and limits the applicability of the model under realistic conditions. In this section we extend the model to capture the effect of the fluctuating slip number K.
We assume that K is a random variable which is sampled from a probability density function
Note that the possibility of fibers with
The constitutive equation
The first term of the right hand side of Eq. 3 represents the load kept by intact fibers taking into account that a fiber can be intact either because it can never slip
which we use for explicit calculations to demonstrate the outcomes of the generic derivations. Here the parameter
which yields
and
for the asymptotic Young modulus
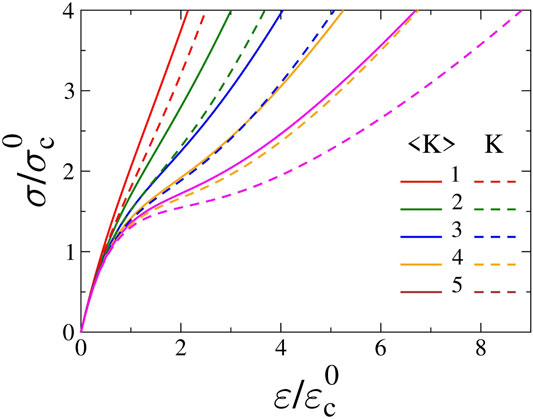
FIGURE 6. Comparison of the constitutive curves of stick-slip bundles with constant (dashed lines) and fluctuating (continuous lines) maximum number of slip events for the case of hardening at the stiffness parameter
The constitutive response of softening bundles with fluctuating maximum slip number can also be obtained from Eq. 3 by skipping the last term, which represents the contribution of fibers with failure index
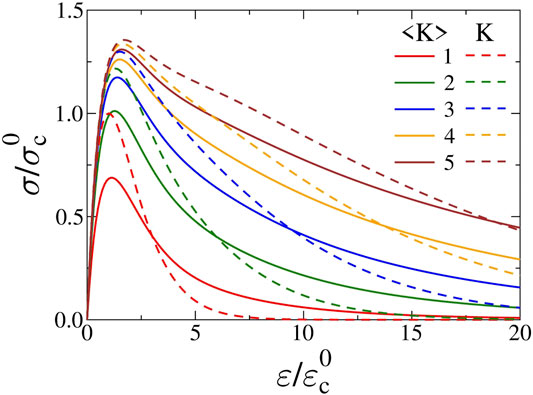
FIGURE 7. Comparison of the constitutive curves of stick-slip bundles with constant (dashed lines) and fluctuating (continuous lines) maximum number of slip events for the case of softening at the stiffness parameter
4 Annealed Disorder of Failure Thresholds
In materials with a complex micro-structure slip events may be followed by a change of the local material properties. In our fiber bundle model this behavior can be captured up to some extent by assigning a new threshold value to the fiber after each slip event from the same probability distribution
where
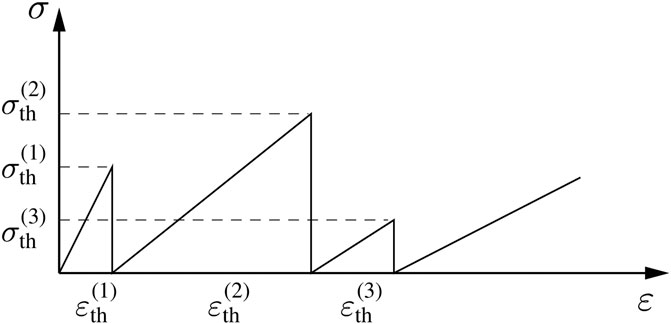
FIGURE 8. Constitutive behavior of a single fiber with annealed disorder of the slip thresholds. The value of the stiffness parameter is
Based on the above expressions the constitutive equation
where again the load bearing contributions of the subsets of fibers of different slip numbers
The constitutive responses of stick-slip bundles with quenched and annealed disorder are compared in Figure 9 for the case of hardening with fixed values of the number of slip events K. It can be observed that the two sets of curves have a qualitatively similar behavior. For
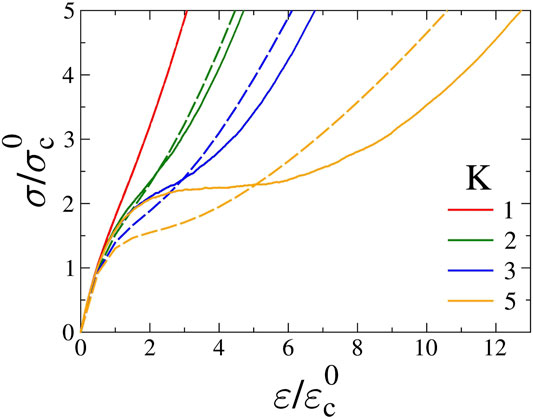
FIGURE 9. Comparison of the constitutive curves of hardening stick-slip bundles with quenched (dashed lines) and annealed (continuous lines) failure thresholds for several values of the fixed number of allowed slip events K at the stiffness parameter
5 Discussion
We presented an extension of fiber bundle models of stick-slip dynamics incorporating the effect of stiffness change of the fibers after slip events, and the fluctuations of the number of stick-slip cycles fibers can experience under an increasing external load. Stick-slip dynamics implies that when the load of a fiber exceeds its local strength the fiber does not break, instead it slips which increases its relaxed length. As a consequence, the load of the fiber drops down to zero, however, the fiber retains its load bearing capacity. The stick-slip FBM has a high degree of complexity making it flexible to describe various materials’ behaviors. In order to enhance the applicability of the model, we introduced a parameter which controls the change of fibers’ stiffness after slip events in a multiplicative way allowing for both gradual degradation and stiffening. During their loading history fibers can undergo a sequence of stick-slip cycles. In our model construction the failure thresholds where slip is activated can be either fixed for the entire failure process of the fiber (quenched disorder), or it can be sampled from a probability distribution (annealed disorder) representing fixed structural disorder of materials and the effect of the local change of the material’s behavior after slip events, respectively. As another novel element of our study, the maximum number of slip events is treated as a random variable inside the bundle sampled from a probability distribution. The total number of slip events allowed and the threshold loads where slip is activated are independent random variables. After completing all the stick-slip cycles a fiber can either keep its final stiffness or it can suffer ultimate breaking, which result in global hardening and softening of the bundle in the limit of high deformation, respectively.
We analyzed the model in the mean field limit, i.e. global load sharing (GLS) was assumed. However, in stick-slip FBMs GLS does not imply equal load on fibers, because at a given strain fibers of the bundle can have different relaxed lengths and stiffness values. We derived closed analytic forms for the macroscopic constitutive response of the bundle both for quenched and annealed disorder of the slip thresholds. These results showed that on the macro-scale the bundle exhibits a plastic behavior, i.e. the
Releasing the load on the bundle, a permanent deformations remains, which increases monotonically with the maximum deformation reached before unloading started for hardening bundles, while in the softening case a non-monotonous behavior is obtained. The permanent deformation of softening bundles proved to be smaller than that of their hardening counterpart. The asymptotic value of the permanent deformation of hardening bundles can be used to characterize the extension of the plateau regime at different stiffness parameters a. Our calculations revealed that increasing the number of allowed slips K the extension of the plateau has a finite limit for stiffening bundles
We showed that fluctuations of the number of stick-slip cycles allowed for fibers affect the behavior of both hardening and softening bundles. Comparing hardening bundles of constant and fluctuating slip numbers with the same average value revealed that larger fluctuations result in a narrower plastic regime affecting also the asymptotic stiffness and the permanent deformation of the bundle. For softening bundles the fluctuations of the slip number result in lower and higher load bearing capacities at small and large deformations, respectively, compared to their constant slip number counterparts.
Annealed disorder of slip thresholds results in a qualitatively similar macroscopic response to quenched disorder, however, its description involves a higher mathematical complexity.
Here we focused on the effect of the changing stiffness and fluctuating slip number of fibers on the macroscopic behavior of a stick-slip FBM, and demonstrated that varying its parameters the model is capable to capture several aspects of the macro-scale consequences of stick-slip dynamics. The constitutive curves with the softening regimes and oscillations along the plateau can only be realized in strain controlled experiments. Under stress controlled loading slip events are followed by a load redistribution inside the bundle which can induce further slips and eventually can trigger an entire avalanche of slipping fibers until the bundle gets stabilized. As to the next, we are going to explore the effect of the varying stiffness and fluctuating slip number on dynamics and statistics of slip avalanches, which can have a relevance for the understanding of restructuring avalanches of granular materials and of earthquakes.
Although, the model is complex, still it could be further extended to fit to specific applications. For instance, when consecutive slip events result in the accumulation of internal damage of fibers, the degradation of fibers’ stiffness may be accompanied by the reduction of fibers’ strength. This correlation of local strength and stiffness can be captured by the model in such a way that at slip events fibers get a new failure threshold (annealed disorder) from a distribution which has the same functional form as the original one, however, its average is gradually reduced. Due to its flexibility, the model can serve as a starting point to develop more realistic micro-mechanical models of carbon nanotube reinforced polimeric composites where the high damping ability of the material originates from the stick-slip occurring at the CNT-matrix interface. Our approach can complement recently developed micro-mechanical models of CNT nanocomposites [43–45] providing an efficient framework for the representation of two sources of disorder (local strength and slip number), degradation and stiffening after slip events, and softening or hardening after the maximum slip number is reached. Work in this direction is in progress.
Data Availability Statement
The raw data supporting the conclusions of this article will be made available by the authors, without undue reservation.
Author Contributions
ZH, IK, and FK carried out analytical derivations, ZH performed computer simulations. ZH and FK performed the data analysis, conceived and designed the study and drafted the manuscript. All authors read and approved the manuscript.
Funding
The project is co-financed by the European Union and the European Social Fund. This research was supported by the National Research, Development and Innovation Fund of Hungary, financed under the K-16 funding scheme Project no. K 119967. The research was financed by the Thematic Excellence Programme of the Ministry for Innovation and Technology in Hungary (ED_18-1-2019-0028), within the framework of the Vehicle Industry thematic programme of the University of Debrecen.
Conflict of Interest
The authors declare that the research was conducted in the absence of any commercial or financial relationships that could be construed as a potential conflict of interest.
Acknowledgments
The authors are grateful for discussions with Gergő Pál.
References
1.Herrmann HJ, and Roux S eds. Statistical models for the fracture of disordered media In: Random materials and processes. Amsterdam, Netherlands: Elsevier (1990).
2. Hansen A, Hemmer P, Pradhan S. The fiber bundle model: modeling failure in materials. In: Statistical physics of fracture and breakdown. Hoboken, New Jersey: Wiley (2015).
3. Kun F, Raischel F, Hidalgo RC, Herrmann HJ. Extensions of fiber bundle models. In: Bhattacharyya P, and Chakrabarti BK, editors. Modelling critical and catastrophic phenomena in geoscience: a statistical physics approach. Lecture notes in physics. Berlin, Germany: Springer-Verlag Berlin Heidelberg New York (2006). p. 57–92.
4. Hidalgo RC, Kun F, Kovács K, Pagonabarraga I. Avalanche dynamics of fiber bundle models. Phys Rev E—Stat Nonlinear Soft Matter Phys (2009) 80:051108. doi:10.1103/PhysRevE.80.051108
5. Danku Z, Kun F. Temporal and spacial evolution of bursts in creep rupture. Phys Rev Lett (2013) 111:084302. doi:10.1103/PhysRevLett.111.084302
6. Sinha S, Kjellstadli JT, Hansen A. Local load-sharing fiber bundle model in higher dimensions. Phys Rev E—Stat Nonlinear Soft Matter Phys (2015) 92:020401. doi:10.1103/PhysRevE.92.020401
7. Danku Z, Ódor G, Kun F. Avalanche dynamics in higher-dimensional fiber bundle models. Phys Rev E (2018) 98:042126. doi:10.1103/physreve.98.042126
8. Andersen JV, Sornette D, Leung K. Tricritical behavior in rupture induced by disorder. Phys Rev Lett (1997) 78:2140–3. doi:10.1103/physrevlett.78.2140
9. Yoshioka N, Kun F, Ito N. Kertész line of thermally activated breakdown phenomena. Phys Rev E—Stat Nonlinear Soft Matter Phys (2010) 82:055102. doi:10.1103/PhysRevE.82.055102
10. Karpas E, Kun F. Disorder-induced brittle-to-quasi-brittle transition in fiber bundles. Epl (2011) 95:16004. doi:10.1209/0295-5075/95/16004
11. Roy S, Biswas S, Ray P. Modes of failure in disordered solids. Phys Rev E (2017) 96:063003. doi:10.1103/PhysRevE.96.063003
12. Roy S, Ray P. Critical behavior in fiber bundle model: a study on brittle to quasi-brittle transition. Epl (2015) 112:26004. doi:10.1209/0295-5075/112/26004
13. Roy C, Manna SS. Brittle to quasibrittle transition in a compound fiber bundle. Phys Rev E (2019) 100:012107. doi:10.1103/PhysRevE.100.012107
14. Peires FT. Tensile tests for cotton yarns. V.-“The weakest link,” theorems on the strength of long composite specimens. J Textil Inst (1926) 17:T355–368.
15. Coleman BD. Time dependence of mechanical breakdown in bundles of fibers. III. The power law breakdown rule. Trans Soc Rheol (1958) 2:195–218. doi:10.1122/1.548830
16. Raischel F, Kun F, Herrmann HJ. Failure process of a bundle of plastic fibers. Phys Rev E—Stat Nonlinear Soft Matter Phys (2006) 73:066101. doi:10.1103/PhysRevE.73.066101
17. Nechad H, Helmstetter A, Guerjouma RE, Sornette D. Andrade and critical time-to-failure laws in fiber-matrix composites: experiments and model. J Mech Phys Solid (2005a) 53:1099. doi:10.1016/j.jmps.2004.12.001
18. Nechad H, Helmstetter A, Guerjouma RE, Sornette D. Creep ruptures in heterogeneous materials. Phys Rev Lett (2005b) 94:045501. doi:10.1103/PhysRevLett.94.045501
19. Kun F, Moreno Y, Hidalgo RC, Herrmann HJ. Creep rupture has two universality classes. Europhys Lett (2003) 63:347–53. doi:10.1209/epl/i2003-00469-9
20. Hidalgo RC, Kun F, Herrmann HJ. Creep rupture of viscoelastic fiber bundles. Phys Rev E—Stat Nonlinear Soft Matter Phys (2002a) 65:032502. doi:10.1103/PhysRevE.65.032502
21. Hidalgo RC, Kovács K, Pagonabarraga I, Kun F. Universality class of fiber bundles with strong heterogeneities. Europhys Lett (2008) 81:54005. doi:10.1209/0295-5075/81/54005
22. Roy C, Kundu S, Manna SS. Fiber bundle model with highly disordered breaking thresholds. Phys Rev E—Stat Nonlinear Soft Matter Phys (2015) 91:032103. doi:10.1103/PhysRevE.91.032103
23. Danku Z, Kun F. Fracture process of a fiber bundle with strong disorder. J Stat Mech (2016) 2016:073211. doi:10.1088/1742-5468/2016/07/073211
24. Hidalgo RC, Moreno Y, Kun F, Herrmann HJ. Fracture model with variable range of interaction. Phys Rev E—Stat Nonlinear Soft Matter Phys (2002b) 65:046148. doi:10.1103/PhysRevE.65.046148
25. Phoenix SL, Newman WI. Time-dependent fiber bundles with local load sharing. ii. general weibull fibers. Phys Rev E—Stat Nonlinear Soft Matter Phys (2009) 80:066115. doi:10.1103/PhysRevE.80.066115
26. Bhattacharyya P, Pradhan S, Chakrabarti BK. Phase transition in fiber bundle models with recursive dynamics. Phys Rev E—Stat Nonlinear Soft Matter Phys (2003) 67:046122. doi:10.1103/PhysRevE.67.046122
27. Curtin WA. Size scaling of strength in heterogeneous materials. Phys Rev Lett (1998) 80:1445. doi:10.1103/physrevlett.80.1445
28. Hidalgo RC, Grosse CU, Kun F, Reinhardt HW, Herrmann HJ. Evolution of percolating force chains in compressed granular media. Phys Rev Lett (2002c) 89:205501. doi:10.1103/PhysRevLett.89.205501
29. Michlmayr G, Or D, Cohen D. Fiber bundle models for stress release and energy bursts during granular shearing. Phys Rev E—Stat Nonlinear Soft Matter Phys (2012) 86:061307. doi:10.1103/PhysRevE.86.061307
30. Layton BE, Sastry AM. Equal and local-load-sharing micromechanical models for collagens: quantitative comparisons in response of non-diabetic and diabetic rat tissue. Acta Biomater (2006) 2:595. doi:10.1016/j.actbio.2006.05.013
31. Halász Z, Kun F. Fiber bundle model with stick-slip dynamics. Phys Rev E—Stat Nonlinear Soft Matter Phys (2009) 80:027102. doi:10.1103/PhysRevE.80.027102
32. Halász Z, Kun F. Slip avalanches in a fiber bundle model. Europhys Lett (2010) 89:26008. doi:10.1209/0295-5075/89/26008
33. Michlmayr G, Chalari A, Clarke A, Or D. Fiber-optic high-resolution acoustic emission (AE) monitoring of slope failure. Landslides (2017) 14:1139–46. doi:10.1007/s10346-016-0776-5
34. Furst EM, Gast AP. Micromechanics of dipolar chains using optical tweezers. Phys Rev Lett (1999) 82:4130. doi:10.1103/physrevlett.82.4130
35. Emile O, Foch AL, Vollrath F. Time-resolved torsional relaxation of spider draglines by an optical technique. Phys Rev Lett (2007) 98:167402. doi:10.1103/PhysRevLett.98.167402
36. Suhr J, Koratkar NA. Energy dissipation in carbon nanotube composites: a review. J Mater Sci (2008) 43:4370–82. doi:10.1007/s10853-007-2440-x
37. Zhou X, Shin E, Wang K, Bakis C. Interfacial damping characteristics of carbon nanotube-based composites. Compos Sci Technol (2004) 64:2425–37. doi:10.1016/j.compscitech.2004.06.001
38. Capelli A, Reiweger I, Lehmann P, Schweizer J. Fiber-bundle model with time-dependent healing mechanisms to simulate progressive failure of snow. Phys Rev E (2018) 98:023002. doi:10.1103/PhysRevE.98.023002
39. Capelli A, Reiweger I, Schweizer J. Studying snow failure with fiber bundle models. Front Phys (2020) 8:236. doi:10.3389/fphy.2020.00236
40. Pradhan S, Hansen A, Chakrabarti BK. Failure processes in elastic fiber bundles. Rev Mod Phys (2010) 82:499. doi:10.1103/revmodphys.82.499
41. Vollrath F, Porter D. Spider silk as archetypal protein elastomer. Soft Matter (2006) 2:377–85. doi:10.1039/b600098n
42. Yates R, Goodman D. Probability and stochastic processes: a friendly introduction for electrical and computer engineers. Hoboken, NJ: John Wiley & Sons (2005).
43. Huang Y, Tangpong X. A distributed friction model for energy dissipation in carbon nanotube-based composites. Commun Nonlinear Sci Numer Simulat (2010) 15:4171–80. doi:10.1016/j.cnsns.2010.01.017
44. Wang TY, Liu SC, Tsai JL. Micromechanical stick-slip model for characterizing damping responses of single-walled carbon nanotube nanocomposites. J Compos Mater (2016) 50:57–73. doi:10.1177/0021998315570371
Keywords: fiber bundle, stick-slip, plastic behaviour, varying stiffness, fluctuating slip number
Citation: Halász Z, Kállai I and Kun F (2021) Stick-Slip Dynamics in Fiber Bundle Models with Variable Stiffness and Slip Number. Front. Phys. 9:613493. doi: 10.3389/fphy.2021.613493
Received: 02 October 2020; Accepted: 04 January 2021;
Published: 04 March 2021.
Edited by:
Subhrangshu Sekhar Manna, S.N. Bose National Centre for Basic Sciences, IndiaCopyright © 2021 Halász, Kállai and Kun. This is an open-access article distributed under the terms of the Creative Commons Attribution License (CC BY). The use, distribution or reproduction in other forums is permitted, provided the original author(s) and the copyright owner(s) are credited and that the original publication in this journal is cited, in accordance with accepted academic practice. No use, distribution or reproduction is permitted which does not comply with these terms.
*Correspondence: Zoltán Halász, em9sdGFuLmhhbGFzekBhdG9ta2kuaHU=