- 1Advanced Energy Systems Graduate Program, Colorado School of Mines, Golden, CO, United States
- 2Mechanical Engineer Department, Colorado School of Mines, Golden, CO, United States
Electrified aircraft have gained traction as a promising approach to emissions abatement in the aviation sector. This transition will require overcoming numerous technical challenges related to increasing battery energy density, as well as logistic challenges related to the lithium supply chain, which is already stressed due to high demand for electric vehicles. We have estimated that lithium demand for electrified aviation may raise lithium demand in the range of 10–250%. The uncertainty in these estimates show the importance of quantifying the impacts of electrified aviation and designing batteries to mitigate additional demand. In addition, most reviews on electrified aviation do not include information on the localized social and environmental impacts caused by lithium demand, despite their importance to enabling technology necessary for emissions reductions. This review seeks to fill this gap by presenting an overview of environmental and social research in context with one another to encourage researchers in the field to consider these dynamics as part of electrified aircraft design. Given that the high energy density batteries necessary to enable large-scale electrification of aircraft are still under development, continued progress in this field should emphasize sustainable governance for lithium extraction and a circular battery economy to reduce social and environmental stressors.
Introduction
The projected growth of the aviation sector, combined with high energy density fuel requirements, make it a challenging industry to decarbonize. Currently, 2.5% of global greenhouse gas (GHG) emissions are attributed to the aviation sector; however, if current technology is not replaced, it will account for 11% of emissions within the next 20 years (Adu-Gyamfi and Good, 2022). This translates to around 900 Tg of CO2 equivalent (CO₂eq) per year or around 125–220 gCO₂eq per revenue passenger kilometer (Liu et al., 2016a; Gray et al., 2021; Lee et al., 2021). Furthermore, emissions at altitude result in radiative forcing, where it is estimated that emissions impacts are three times greater than for associated emissions at sea level (Lee et al., 2021). These concerns have led to the creation of ambitious emissions targets, worldwide, including the Advisory Council for Aviation Research and Innovation in Europe’s (ACARE) flightpath strategy and the NASA N+3 program (Adu-Gyamfi and Good, 2022). In addition, many airlines have voluntarily opted for more stringent targets via participation in Airlines for America (A4A) and the International Air Transport Association (IATA) (Airlines for America, 2021; International Air Transport Association, 2022).
Figure 1 presents an overview of the needs, challenges, and opportunities related to decarbonized aviation. Aircraft electrification via battery energy storage is often seen as a long-term favorable solution, as alternative fuels such as biofuels or hydrogen would still produce noise and contrails at low altitudes (Gnadt et al., 2019; Schwab et al., 2021). In recent years, electric aviation has received increased attention, and designs have been proposed by academic institutions (Cambridge-MIT), industry leaders (Airbus and Boeing), and governmental organizations (NASA) (Adu-Gyamfi and Good, 2022). Eviation’s Alice is powered by lithium-ion batteries (LIBs) and can reach distances of 440 nautical miles (nmi) with 9 passengers (Adu-Gyamfi and Good, 2022). The hybridized ZUNUM Aero’s ZA10 can carry twelve people and travel 700 nmi (Adu-Gyamfi and Good, 2022). Commercial aviation emissions, however, are primarily attributed to larger aircraft with higher passenger counts. Successful development of battery-electric air vehicles (EAVs) depends on the development of new battery approaches (chemistries, pack designs) to significantly increase the energy density. Projected requirements for single-aisle aircraft range from 800 Wh kg−1 for 600 nmi to 1,400 Wh kg−1 for 900 nmi (Pornet et al., 2015; Gnadt et al., 2019; Scholz et al., 2022), while current LIB energy density is roughly 250–270 Wh kg−1 (Eshetu et al., 2021; Adu-Gyamfi and Good, 2022). Proposed “beyond Li ion” chemistries for high energy density lithium batteries, such as Li-metal anodes, and Li-sulfur and Li-air cathodes, along with their theoretical energy densities, are described in Figure 1. In addition to improved energy density, next-generation batteries for EAVs must attain high cyclability, high specific power, low cost, and fast charging rates, among other targets. While Al and Zn-air batteries are projected to meet capacity requirements, lithium-based batteries have received the bulk of research relating to aviation.
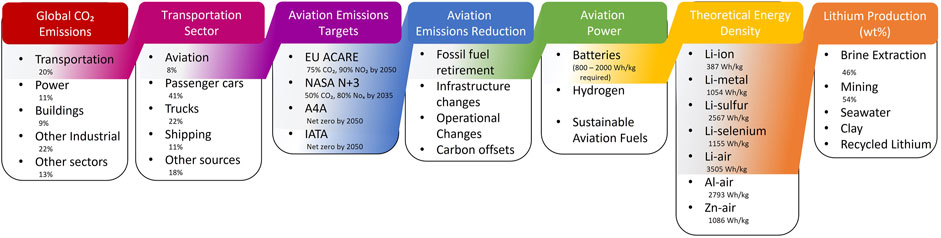
FIGURE 1. The connection between global CO₂ emissions, aviation emissions targets, and increased lithium production. Sources for global CO₂ (Crippa et al., 2021), transportation sector (International Energy Agency, 2020), aviation emissions targets (Airlines for America, 2021; Adu-Gyamfi and Good, 2022; International Air Transport Association, 2022), theoretical energy density (Bruce et al., 2012; Yang et al., 2015; Gnadt et al., 2019), and lithium production distribution (Stringfellow and Dobson, 2021).
While many reviews cover the technical aspects of lithium battery integration into aircraft (Adu-Gyamfi and Good, 2022; Hizarci et al., 2022; Yilmaz and Atmanli, 2022), this review focuses on the localized social and environmental impacts related to aircraft electrification. Successful deployment of lithium batteries for aviation will put additional burden on the supply chain for required raw materials. These impacts are often overlooked when developing climate targets and related policies to achieve them. The demand for lithium products, caused in part by electric vehicles (EV), has been projected to exceed lithium production by 100% by 2035 (Hersh, 2019). As lithium production is regionally concentrated, this demand puts pressures on local communities and ecosystems. Few papers are dedicated to this topic and this review seeks to familiarize researchers with impacts of increased Li consumption, so they can more readily quantify the ecological and social impacts associated with any particular battery design.
Tracing and allocating the lithium supply chain
Just as lithium production is regionally concentrated, LIB production and EV sales have global hotspots. This concept is demonstrated in Table 1, which compares the steps of the supply chain. In this table, “resources” refers to quantifiable lithium presence and “reserves” refers to lithium whose extraction cost are estimated to an acceptable error margin (Hersh, 2019). While this list is not exhaustive, the disconnect between resources and reserves demonstrates the limited number of countries currently producing lithium. The next column shows that Chinese companies have a plurality of the automotive LIB manufacturing share, and therefore must purchase lithium mined in other global regions, such as Chile and Australia (Mayyas et al., 2019). Finally, the “EV sales” column shows that demand for EVs and lithium come from countries that do not have significant lithium production. Countries which contributed to the demand for Li may exacerbate social and environmental concerns in lithium mining countries, while simultaneously receiving net environmental benefits of electrification (Anlauf, 2017). While Table 1 deals with automotive electrification and aviation electrification is in the early stages of development, these trends will likely follow similar patterns and therefore merit consideration.

TABLE 1. The lithium resources, lithium reserves, automotive LIB manufacturing share, and EV sales for different countries. In this case, a blank row means that the reference gives no data, rather than zero. References were published in 2019.
Lithium production and battery manufacturing
Though lithium is abundant in the earth’s crust, it does not exist in a pure state, and extraction can be energy intensive (Hersh, 2019). The majority of lithium is extracted from high concentration lithium brines and lithium mineral deposits, such as spodumene (Prior et al., 2013). The projected demand for electrified transport and energy storage has placed strain on the entire lithium supply chain, prompting investigations into extraction from seawater or clay. These processes are currently cost-prohibitive but may become necessary as demand increases (Hersh, 2019). The lithium carbonate equivalent (LCE) metric, as in Table 1, allows for comparison between resources (e.g., lithium oxide vs. lithium carbonate) (Prior et al., 2013).
Lithium brines produce lithium carbonate, which is more likely to be used in batteries, making them particularly important to transportation electrification. The “lithium triangle” in Latin America refers to salt flats in Bolivia, Chile, and Argentina, which contain around 75% of the world’s known lithium reserves (Seefeldt, 2020). Of these, Chile is the largest producer and currently provides around 35% of the world’s lithium (Mayyas et al., 2019). The Salton Sea, Smackover, Silver Peak, and Clayton Valley in the USA; East and West Taijinars, Zabuye, Yiliping, and Da Qaidam in China; and Fox Creak in Canada are all brine locations with over 0.01 wt% lithium concentration (Stringfellow and Dobson, 2021). The location, lithium concentration in solution, and presence of other elements all drive the cost and environmental impacts of lithium extracted from these sites. In the case of lithium brines, high ratios of SO₄ and Mg can severely limit resource development (Hersh, 2019). In China, for example, high concentrations of Mn in the Tibetan lakes have led to several project failures (Scholz et al., 2022).
Lithium mining typically produces lithium oxide, which is predominantly used in ceramics, but can also be upgraded to lithium carbonate (Champion, 2019; Mayyas et al., 2019). Lithium mines in Portugal typically supply the ceramic industry, while a significant portion of Li mined in Australia is bought by China for use in battery production (Prior et al., 2013; Dorn, 2021). Australia currently accounts for roughly 40–45% of the world’s lithium supply.
Life cycle analysis (LCA) quantifies and allocates environmental impacts to different steps of a process and can help understand how location and process type impact a battery’s total lifetime environmental impact. Figure 2 provides LCA results for lithium resource extraction and battery production. Figure 2A shows the GHG emissions associated with lithium hydroxide derived from brine and mining and Li₂CO₃ from seawater (Stamp et al., 2012; Chordia et al., 2022). In addition, the GHG emissions from lithium metal batteries are included (using results from ecoinvent 3.7.1), as this is a candidate for next generation high energy density anodes (Wernet et al., 2016). Figure 2B shows the GHG emissions attributed to lithium extraction and battery processing for a range of battery chemistries, including lithium ion, lithium-sulfur (Deng et al., 2017; Benveniste et al., 2019), lithium-air (Wang et al., 2020), and lithium metal batteries (Wu and Kong, 2018). The first four entries demonstrate how changing the lithium source (brine vs. mining) can vary its contribution to GHG (5% of the total emissions for brine, vs. 15% for mining) (Chordia et al., 2022). The lithium-sulfur and lithium-air batteries estimates assume sourcing is evenly split between mining and brines. With the exception of lithium-metal batteries, the lithium contribution to GHG emissions from a given source are similar and may show similar responses to fluctuations in sourcing.
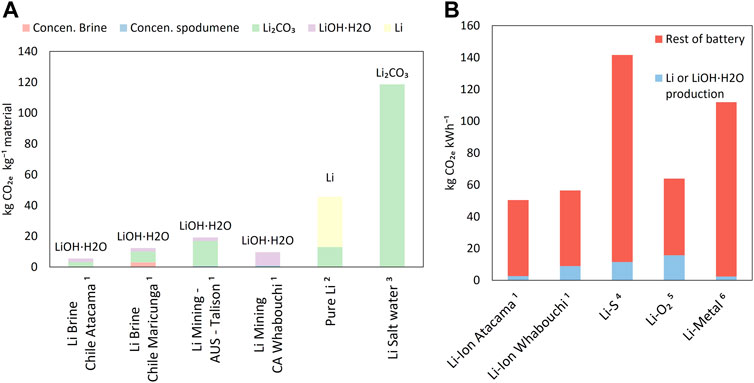
FIGURE 2. GHG emissions related to LIB production. (A) equivalent GHG emissions for lithium production for use in batteries, where the produced resource is shown above the bar and (B) GHG emissions for Li-ion batteries and alternatives. Values have been scaled to remove impacts from battery cooling and management systems, as these values are not available for chemistries at lower technology readiness levels. References: 1 (Chordia et al., 2022), 2 (Wernet et al., 2016), 3 (Stamp et al., 2012), 4 (Deng et al., 2017), 5 (Wang et al., 2020), 6 (Wu and Kong, 2018).
Applications to aviation
The net environmental benefits of electrified aviation broadly depend on the size of the aircraft, the energy density of the battery, and the composition of grid energy used to charge the battery. Modern LIB are already used to power small aircraft for short durations, as short haul flights by smaller aircraft have 50% less fuel efficiency. Electrified aircraft can provide reduced fuel costs and CO₂ emissions on flights less than 300 miles even if coal power is used (Schwab et al., 2021). These CO₂ reductions are enhanced by charging with solar power; however, this use case is limited to 6-9 passengers. Planes the size of regional jets (30–100 seats) or fewer make up only 5% of aviation emissions (National Academies of Sciences, 2016).
The development of electrified single-aisle aircraft (100–200 seats) would impact 43% of total global aviation emissions but depends on development of new battery technology (National Academies of Sciences, 2016; Adu-Gyamfi and Good, 2022). A study of an aircraft with a 1,000 kWh kg−1 battery and hybridization degree of 0.3, or where 30% of the thrust is provided by electricity, shows the overall environmental impact, using the ReCiPe 2008 endpoint method, was increased, relative to current technology. In addition, the operation costs increased by 41%, partially due to higher electricity costs. Through renewable energy production and negative incentives on emissions, the environmental impact is reduced, but operational costs remain higher (Scholz et al., 2022). An analysis of all-electric aircraft (AEA) demonstrates the CO2 emissions break-even point depends on the battery capacity and grid energy composition (Gnadt et al., 2019). Using the 100-year Absolute Global Warming Potential (AGWP100) method, if direct CO2 emissions are considered, high renewable energy scenarios show high capacity 800 Wh kg−1 and 2000 Wh kg−1 batteries outperforming conventional aircraft by 2043 and 2025, respectively. In this same analysis, direct non-CO2 emissions are not predicted to pass break-even thresholds until 2045 and 2040, respectively (Gnadt et al., 2019). Grids with high renewable energy penetration and high energy density batteries are essential for making AEA advantageous (Pornet et al., 2015; Gnadt et al., 2019). For hybridized aircraft, the battery is predicted to contribute to just 1% of lifecycle CO2 emissions; however, in the AEA case, with the current US grid, a battery would account for 7–12% of lifecycle emissions (Gnadt et al., 2019).
The variation in break-even points shows the importance of updating LCA with the best available information on battery capacity, energy mix, and composition. Furthermore, as accessible lithium sources are exhausted, the battery may constitute a larger percentage of GHG emissions in the future. The time frame for development of larger electrified aircraft ranges from 2030 to 2045 (Adu-Gyamfi and Good, 2022); without lithium recycling the environmental impacts of lithium extraction and depletion of lithium sources may intensify. This is especially true for next generation batteries, as the composition and capacity can depend greatly on the experimental design. The GHG emission benefits from electric aviation should be quantitatively examined before their adoption.
Estimating lithium demand
Estimating lithium demand due electrified aviation is difficult, as battery technology and future consumer demand are both speculative. Equation 1 provides a simple means to estimate Li demand related to aviation electrification:
where
Following this approach, Figure 3 estimates the strain on lithium sourcing and production posed by converting the global air fleet to AEAs. The total battery capacity, specific capacity, and lithium content of future aviation batteries are difficult to predict. The lithium content of beyond Li-ion batteries (Dai et al., 2019) such as lithium-sulfur (Deng et al., 2017; Schwich et al., 2020) and lithium-air batteries (Wang et al., 2020) can shift dramatically (3–22%) based on their design, as shown in Figure 3A. In Figure 3B, Eq. 1 is used to estimate the % of global lithium production [as of 2021 (Seiner et al., 2014)] required to convert the global single-aisle fleet to AEA. Three separate projections are included for AEA battery requirements: 1) a 32.3 MWh system with a battery energy density of 2000 Wh kg−1 (Gnadt et al., 2019), a 2) 60.31 MWh system with a 2000 Wh kg−1 battery (Seiner et al., 2014), and 3) a 28.8 MWh system with an 800 Wh kg−1 battery (Gnadt et al., 2019). According to Boeing, the global single-aisle fleet had 16,530 aircraft in 2019. This is projected to rise to 30,880 aircraft by 2041 (Mounir, 2022). In Figure 3B, values are given for a battery with 4wt% and 22wt% lithium, and with 2019 and projected 2041 fleet sizes. These projections are based on battery desities which exceed the current state of the art and are more typical of beyond Li-ion chemistries, such as Li-S and Li-O₂. It is worth nothing that these batteries do not exist at commercial scale and reaching this Li demand will require considerable advances in Li battery density. These calculations are intended to reflect the uncertainty in the demands electrified aviation will place on the lithium supply chain. In the most optimistic estimate, single-aisle AEA will increase the global lithium demand by 10% by 2041. In the worst-case scenario, lithium demand due to aircraft electrification would be more than double current lithium production.
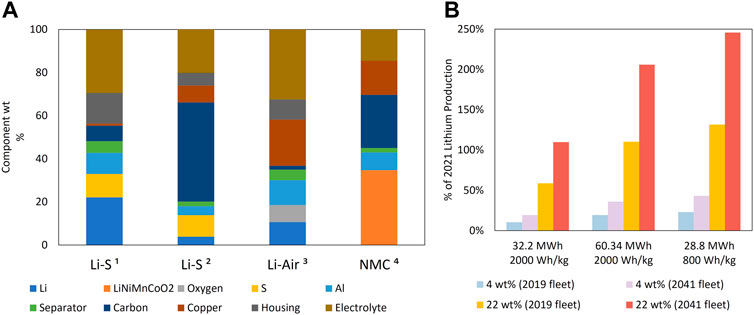
FIGURE 3. Estimated lithium demand for AEAs. (A) composition by wt% of different materials in lithium-based batteries. References: 1 (Schwich et al., 2020), 2 (Deng et al., 2017), 3 (Wang et al., 2020), 4 (Dai et al., 2019). (B) projected lithium demand as a percent of current production. The three series represent three proposed battery requirements (total battery energy and energy density) for single-aisle AEA. For each proposed battery, the lithium required is modeled for batteries that are 4 wt% and 22 wt% lithium, with the number of AEAs required to meet 2019 fleet size and anticipated 2041 fleet size (Mounir, 2022). Lithium demand is presented as a percentage of global 2021 production. Results show significant uncertainty in increased lithium demand, depending on advances in battery technology and actual aircraft energy demand.
Localized environmental and social impacts of lithium sourcing
The wholistic approach of LCA is essential to verify that pursuing a particular solution is worthwhile, but it should be considered in conjunction with other localized environmental stressors, and the social problems which stem from them (Süsser et al., 2022). Electrified aviation researchers should be aware of how these factors are impacted by, and will impact, their work. In this section, the localized environmental impacts, and their relationship with social discourse are discussed by mining type.
Lithium brines
In the case of lithium brines, water is often pumped from subterranean reserves into (polyvinyl chloride) PVC-lined evaporation ponds and partially evaporated, with the resulting high-salinity brine transported off site (Stamp et al., 2012; Kaunda, 2020). In the case of Salar de Atacama, two companies Soquimich (SQM) and Albermarle are permitted to draw 1,600 L/s and 400 L/s, respectively. Additional fresh water is needed to wash the lithium carbonate; the production of 17,500 tons of lithium carbonate from Salar de Olaroz required 240 L/s of salt brine and 201 L/s of fresh water (Anlauf, 2017). In the case of Salar de Olaroz in Argentina, subterranean water often plays a crucial role in local ecosystems, and the water pumped out in brine may be fossil water, or nonrenewable (Hizarci et al., 2022). Furthermore, the brine interacts with freshwater systems, and its extraction may lower groundwater levels (Hizarci et al., 2022). In the case of Salar de Atacama in Chile, water consumption from local mining operations is over 2x times greater than domestic use (Liu and Agusdinata, 2020). As a result, regional water storage has decreased by an average of 1.16 mm each year from 2002 to 2017 (Anlauf, 2017; Liu and Agusdinata, 2020). Analysis of satellite imagery shows reduced vegetation associated with increasing mine size, as well as changes in land surface temperature and soil moisture index (Liu et al., 2019). As seen in Figure 4, the Salar de Uyuni in Bolivia is within one of Conservation International’s 36 identified biological hotspots, the tropical Andes (Sanchez-Lopez, 2019; Critical ecosystem Partnership Fund, 2021). In the Salar de Atacama, the extraction of water has negatively impacted the population of two flamingo species (Guterrez et al., 1970; Garjadro and Redon, 2019). This region is a staging area for migratory birds and home to a delicate food web. The lack of baselines in these areas make it difficult to determine if other species are or will be impacted (Garjadro and Redon, 2019). If the PCV lining is ruptured or local high winds lead to spread of their contents, the altered soil alkalinity could damage both farms and local ecosystems (Sanchez-Lopez, 2019; Kaunda, 2020).
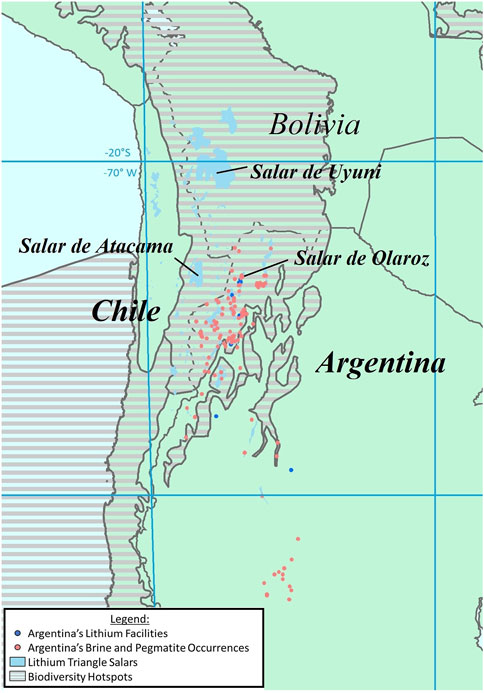
FIGURE 4. The geographic proximity of the lithium salars, Argentina’s lithium facilities and Argentina’s brine and pegmatites occurrences (Mihalasky et al., 2020) with Conservational International’s biodiversity hotspots (Hoffman et al., 2016). Figure produced using ArcGIS (ESRI, 2011).
The economic power of foreign companies and investments creates power differentials in the region, especially as engineering expertise is usually provided and retained by those companies (Valle and Holmes, 2013). In the case of Argentina, the Olaroz lithium project is facilitated by Australian mining company, Orocobre, and funded by US investors. The Toyota Tsusho Corporation gave financial assistance to surveys on the Olaroz project and China has invested in development of Bolivia’s mining industry (Valle and Holmes, 2013; Anlauf, 2017). Recently, Tianqui Lithium bought a 24% stake in the Chilian company SQM (Garjadro and Redon, 2019). The investment from international companies introduces fear that once the resources are extracted, companies will not take responsibility for cleaning up waste (Abelvik-Lawson, 2019). Furthermore, the profits made by mining resources may not translate to local communities, with projections that a local community in Bolivia, Nor Lipez, will only receive 2% of profits (Abelvik-Lawson, 2019).
Environmental impacts and industrial development can be directly tied to changes in the community, which can be sidestepped by companies looking to quickly develop lithium production sites. In the case of the lithium triangle, many communities located near salt flats depend on subsistence farming and quinoa agriculture (Anlauf, 2017). Mining is a controversial topic, as development of mines can bring employment and other economic benefits into the region (Valle and Holmes, 2013; Chaves et al., 2021). The relationship between mining companies and the community is complicated by companies that give the pretense of stakeholder engagement. In the past, the process for mine approval has been complicated by document inaccessibility, allotting less time to community speakers, or getting approval without the majority of community members present (Valle and Holmes, 2013; Excosteguy et al., 2022). Furthermore, companies do not demonstrate sustained community involvement. For example, Salar de Jujuy in Argentina provided free transportation and health care to local communities near Salar de Olaroz during the project approval but ended the assistance program shortly after project approval (Anlauf, 2017).
Just as water loss impacts local wetlands, it can uproot traditional ways of life by encroaching on land previously used for farming (Abelvik-Lawson, 2019; Liu et al., 2019). The development of industrial zones in rural areas also leads to an influx of laborers, putting additional pressure on water systems and diverting money away from the local economy if those laborers do not remain in the community (Liu and Agusdinata, 2020). In Argentina, there are 33 indigenous groups which oppose development near Salinas Grandes, (Dorn, 2021), while in Bolivia, the majority of lithium is located near the Quechua people (Valle and Holmes, 2013). An integrated model of the environmental and social dynamics near Salar de Atacama shows that stressed communities have led to protests and lawsuits against mining companies (Figure 5) (Liu and Agusdinata, 2021). Social resistance can ultimately delay development projects, which impacts reliable supply chains required for electrification and decarbonization (Süsser et al., 2022). These environmental impacts are compounded by battery GHG emission dependence on the location where lithium is extracted. In addition to compelling moral/ethical concerns, environmental benefits from aviation electrification are therefore also linked to the stress and approval of local populations.
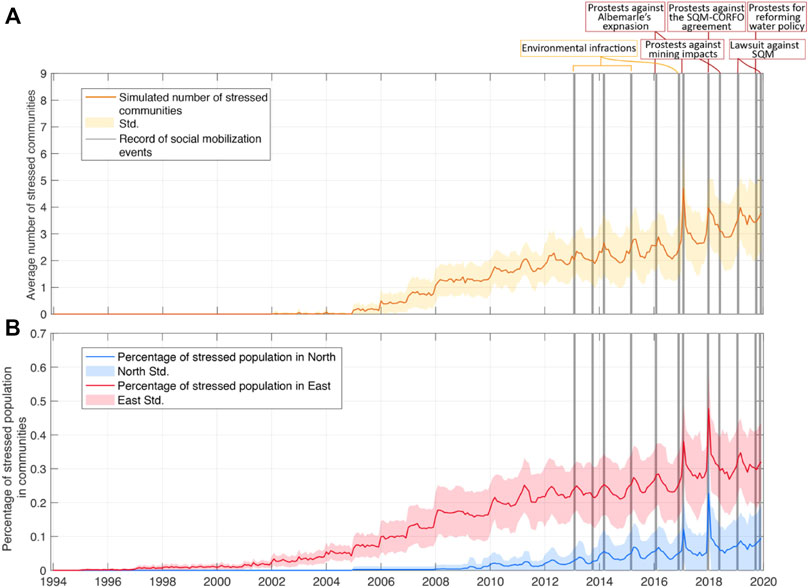
FIGURE 5. The correlation between population stress and disruptions in lithium extraction where (A) shows number of stressed communities and (B) the percentage of stressed communities in the northern and eastern regions. Reprinted from “The Extractive Industries and Society”, vol. 8, i.3, Wenjuan Liu and Datu B. Agusdinata, “Dynamics of local impacts in low-carbon transition: Agent-based modeling of lithium mining-community-aquifer interactions in Salar de Atacama, Chile”, Pages100927, Copyright (2021), with permission from Elsevier (Liu and Agusdinata, 2021).
Lithium mines
Lithium extraction from ore is often regarded as more expensive and energy intensive than from brines; however, responsible environmental stewardship could increase interest in constructing additional mine facilities. Mine tailings, disturbed areas, and waste rock are the main ecological threats from mineral mining. Mine tailings are usually stored in tailings storage facilities (TSF), the failure of which can lead to environmental contamination (Karrech et al., 2021). Extraction of lithium from ore is more expensive due to high transportation costs and small deposits that limit economy of scale benefits (Chaves et al., 2021). These production costs have caused several mines to close when lithium extraction from brines became prominent; however, Prior et al. points out that Australia can justify higher prices on lithium by developing and emphasizing sustainable practices (Prior et al., 2013). An annual compliance report from the Talison site demonstrated how mines can minimize their social and environmental impacts by detailing tracking of environmental impacts, restoration after resource depletion, and community complaints (Talison Lithium Australia PTY LTD, 2021).
The success of local mines does not mean communities welcome additional business. A study on one of Portugal’s lithium mines examined soil, water, and air quality, and found no difference between upstream and downstream water samples. The study detected higher amounts of nitrogen dioxide and particulate matter (PM1, PM2.5 and PM10) while mining occurred; however, they were still below acceptable limits (Rodrigues et al., 2019). Despite this, development of new mines in Portugal spurs debate as it intrudes on rural areas, which depend on farming and ecotourism (Dorn, 2021). Pereira (2018) notes that reports on potential lithium mining locations provide little discourse around environmental protections (Pereira, 2018). The region of Barroso is a Globally Important Agricultural Heritage system, providing habitat for endangered species. Furthermore, eight identified locations for lithium mining are in Natura 2000 areas, areas designated for protection by the European Union, and one is in a natural park (Pereira, 2018). Communities are hesitant to allow new mines, and several demonstrations against their construction have occurred (Chaves et al., 2021; Dorn, 2021). These community reservations should be addressed before additional projects proceed.
Discussion
Given that stable and ethical lithium extraction depends on policies which provide social and environmental protections (Prior et al., 2013), research and funding bodies should support both equitable lithium sourcing and efforts to develop and maintain the circular economy. To be certain, these concerns are salient for all Li-dependent industries, including battery EVs. However, while manufacturing techniques and supply chains for EV are highly defined, the lower technology readiness of next generation batteries required to support EAVs presents an opportunity. Incorporating the information in Sections 2 and 3 into EAV design decisions can have significant impact on the burgeoning electrified aviation field and its associated socio-environmental impacts. The following subections describe how these solutions relate to the sustainable aviation.
Sustainable governance
While similarities exist between countries extracting lithium from brine and countries extracting lithium from ore, the reality is that communities require tailored regulatory frameworks to address concerns at multiple levels of society and government (Petavratzi et al., 2022). This nexus of concepts is often referred to as environmental, social, and corporate governance (ESG) (Petavratzi et al., 2022). Transparency and structure are essential to monitor social and environmental outcomes (Petavratzi et al., 2022). Loosely defined licensing processes can result in environmental licenses that are issued for legal compliance, rather than environmental preservation (Sanchez-Lopez, 2019). The lack of faith in current legislation and protections should lead to development of more robust practices, including baseline surveys and consistent site monitoring.
There are several promising pathways to encourage responsible and transparent mineral extraction. The Extractive Industries Transparency Initiative (EITI) has developed standards for transparent governance of natural resources (EITI International Secretariat, 2019). Argentina has made commitments through the EITI standard, and the federal government has made a resolution to develop the Sistema de Información Abierta a la Comunidad sobre la Actividad Minera en Argentina (SIACAM), an open information system related to resource extraction (Extractive Industries Transparency Initiative, 2022). Petavratzi et al. recommend the development of Strategic Environmental and Social Assessment through the World Bank specific to lithium mining (Petavratzi et al., 2022). Süsser et al. discuss the need for social and environmental factors to be incorporated into energy (Süsser et al., 2022). These efforts should be supported by countries, companies, and researchers interested in sustainable lithium consumption and sourcing (Prior et al., 2013).
The circular economy
For further emphasis on sustainability, entities in all stages of the lithium life cycle should participate in the circular economy. For brine extraction, this could involve better water and waste management procedures (Liu and Agusdinata, 2021). For battery production, this involves ensuring longevity and energy efficiency during manufacturing (Prior et al., 2013). For aviation, the battery end of life (EOL) may be the highest area of interest. Currently, 95% lithium batteries are sent to landfills; however, as the demand for electric vehicles (EV) and AEA grows this will no longer be sustainable (Mayyas et al., 2019). The lack of clear recycling procedures for lithium batteries has led to some of them being processed in lead acid battery plants, causing equipment damage (Mayyas et al., 2019). In around 10 years, the first large fleet of EVs will be retired, and large amounts of critical resources will be wasted if recycling processes are not enacted (Gaines, 2014; Mayyas et al., 2019). The first electronic aircraft are just entering the fleet, but unlike lead or nickel-based batteries, recycling is limited by lack of direct guidelines or incentive programs. Progress in this field would reduce pressure on other nations to expand their extractive operations (Mayyas et al., 2019).
Figure 6 provides an overview of lithium-ion battery recycling technology, applicable to smaller electrified aircraft. The complex composition of lithium batteries, which contain lithium, cobalt, nickel, aluminum, and graphite makes recovering individual components difficult (Mayyas et al., 2019). Currently, two main processes are used for recycling: hydrometallurgy and pyrometallurgy, but both are only considered economic for the recovery of cobalt and nickel, rather than lithium (Gaines, 2014; Mayyas et al., 2019). Supercritical CO2 extraction is less common but allows recovery of solvents and most cathode materials. Unfortunately, there are concerns over the quality of the resulting products, which means they may be more suitable for other supply chains.
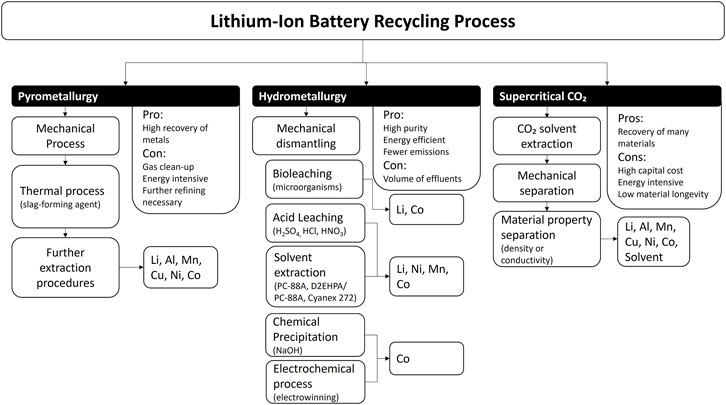
FIGURE 6. An overview of recycling methods for lithium batteries and their potential products (Gaines, 2014; Bertuol et al., 2016; Nowak and Winter, 2017; Swain, 2017; Mayyas et al., 2019; Zhang and Azimi, 2022).
As larger aircraft require batteries with higher energy densities, new recycling processes must be developed. The structure and composition of lithium-sulfur, lithium-metal, and lithium-air batteries are all different. In contrast to lithium-ion batteries, lithium may become the key driver by value (Schwich et al., 2020). Schwich et al. has developed a hydrometallurgy recycling procedure for lithium-sulfur batteries, which results in the precipitation of lithium carbonate (Schwich et al., 2020). In addition to developing and implementing recycling procedures, preliminary action can be taken by developing batteries with recyclable components (Zhang et al., 2020) or implementing recycled materials in battery design (Hu et al., 2015). As these resources should be allocated to both developing materials and recovery of materials at EOL.
Reducing manufacturing waste
An additional burden to battery supply chains involves materials lost during battery manufacturing. This scrap material could be integrated with recycling chains, but additional effort should be placed on reducing waste. The battery manufacturing process has an estimated 2,100 interdependencies, where small variations in physical cell properties can lead to significant differences in the quality of electrochemical performance (Kenny et al., 2012; Komas et al., 2019; Thiede et al., 2019; Schmidt et al., 2020; Duquesnoy et al., 2021; Turetskyy et al., 2021; Gonçalves et al., 2022). To demonstrate this complexity, Figure 7 shows some of the processing steps, their parameters, and impacted structural properties, as well as metrics for electrochemical cell. The examples are not exhaustive but give a broader picture of the challenges in determining how to link variations in electrochemical parameters to a specific process parameter or step. This causes 5–40% of commercial batteries to be discarded as ‘defective’ or ‘needing attention’ after production, increasing both waste and material demand (Silva et al., 2021; Turetskyy et al., 2021).
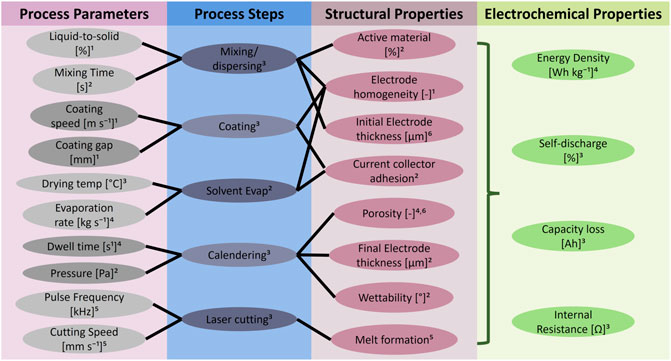
FIGURE 7. The link between process parameters, process steps, structural properties, and electrochemical parameters. In this figure, a maximum of two processing steps and three structural properties are linked to process parameters. This is to demonstrate some of the process complexity, without overcrowding the diagram. References: 1 (Duquesnoy et al., 2021), 2 (Gonçalves et al., 2022), 3 (Turetskyy et al., 2021), 4 (Schmidt et al., 2020), 5 (Thiede et al., 2019), 6 (Kenny et al., 2012).
In next generation battery research, emphasis has been placed on cathode material type, while design parameters crucial to Li-sulfur battery commercialization, such as areal sulfur loading and electrolyte/sulfur ratio, are often ignored (Fang et al., 2017). Furthermore, most experimental designs for both Li-sulfur and Li-O₂ have high variation in the resulting battery performance; however, this variability is rarely reported in literature (Liu et al., 2016b; Fang et al., 2017). Investment in new manufacturing techniques, such as continuous slurry processing and automation, are projected to reduce waste (Li et al., 2022). Within automation, machine learning and models which examine correlations between manufacturing procedures, improved cathode performance, and defect creation has become increasingly popular (Duquesnoy et al., 2021; Mistry et al., 2021; Turetskyy et al., 2021). These studies can discern which combination of inputs can lead to homogeneous electrodes and develop sensitivity indices for input variables, discerning complex non-linear relationships. As research into high density batteries continues, experimentalists should emphasize result consistency and intensive exploration of links between manufacturing procedures and electrochemical deficiencies.
Conclusion
Aviation is a difficult-to-abate sector and electrification of aircraft via lithium batteries has the potential to reduce these emissions. However, climate targets should not be met at the expense social and environmental justice. Implementation of lithium batteries for flight power will put extra stress on the lithium supply chain, with larger aircrafts requiring anywhere from 10 to 200% of current lithium production for their batteries. Before this technology is developed or implemented, design should be guided by the technical, social, and environmental challenges associated with meeting future demand. Sustainable practices do not just include technology implementation, but concern for supply chain impacts and responsible EOL practices. Many locations for lithium mining rest within delicate environmental systems. It has been shown that civil unrest in lithium mining locations has led to protests and backlash against mine development. As environmental damage and water scarcity have intensified, protests intensify in turn.
Researchers in this field have a responsibility to be familiar with the impacts of their work and corporations should be responsible for the ethics of their supply chain. On a broader scale, this entails performing LCA to determine that designs align with prefaced values of environmental impact reduction. Furthermore, supporting positive ESG conditions and circular economy development is an important research consideration. The design of high-capacity batteries has not been finalized, so an emphasis on recyclable materials and components should be strongly considered during development.
Author contributions
MC-G: Conceptualization, writing–original draft, investigation, data curation. SD: Writing–review and editing, supervision, funding acquisition.
Funding
Financial support provided by US National Science Foundation, Award 1903440, Program Manager Dr. Raymond Adomaitis.
Conflict of interest
The authors declare that the research was conducted in the absence of any commercial or financial relationships that could be construed as a potential conflict of interest.
Publisher’s note
All claims expressed in this article are solely those of the authors and do not necessarily represent those of their affiliated organizations, or those of the publisher, the editors and the reviewers. Any product that may be evaluated in this article, or claim that may be made by its manufacturer, is not guaranteed or endorsed by the publisher.
References
Abelvik-Lawson, H. (2019). Indigenous environmental rights, participation and lithium mining in Argentina and Bolivia: A socio-legal analysis. Essex, UK: University of Essex.
Adu-Gyamfi, B. A., and Good, C. (2022). Electric aviation: A review of concepts and enabling technologies. Transp. Eng. 9, 100134. doi:10.1016/j.treng.2022.100134
Airlines for America (2021). Airlines fly green. Available: https://www.airlines.org/airlines-fly-green/ (Accessed September 12, 2022).
Anlauf, A. (2017). “Greening the imperial mode of living? Socio- ecological (in)justice, electromobility, and lithium mining in Argentina,” in Fairness and justice in natural resource politics (Argentina: Taylor&Francis Group), 164–180.
Barke, A., Thies, C., Popien, J.-L., Melo, S. P., Cerdas, F., Herrmann, C., et al. (2021). Life cycle sustainability assessment of potential battery systems for electric aircraft. Procedia CIRP 98, 660–665. doi:10.1016/j.procir.2021.01.171
Benveniste, G., Sadok, R., Canals, L., Corchero, C., and Amante, B. (2019). “Life cycle assessment of Li-sulphur batteries for electric vehicles,” in 32nd electric vehicle symposium (Lyon: France).
Bertuol, D. A., Machado, C. M., Silva, M., Calgaro, C. O., Dotto, G. L., and Tanabe, E. (2016). Recovery of cobalt from spent lithium-ion batteries using supercritical carbon dioxide extraction. Waste Manag. 51, 245–251. doi:10.1016/j.wasman.2016.03.009
Bruce, P. G., Freunberger, S., Hardwick, L. J., and Tarascon, J.-M. (2012). Li–O2 and Li–S batteries with high energy storage. Nat. Mat. 11, 19–29. doi:10.1038/nmat3191
Chaves, C., Pereira, E., Ferreira, P., and Dias, A. G. (2021). Concerns about lithium extraction: A review and application for Portugal. Extr. Ind. Soc. 8 (3), 100928. doi:10.1016/j.exis.2021.100928
Chordia, M., Wickerts, S., NordelOf, A., and Arvidsson, R. (2022). Life cycle environmental impacts of current and future battery-grade lithium supply from brine and spodumene. Resour. Conserv. Recycl. 187, 106634. doi:10.1016/j.resconrec.2022.106634
Crippa, M., Guizzardi, M., Solazzo, E., Muntean, M., Schaaf, E., Monforti-Ferrario, F., et al. (2021). GHG emissions of all world countries. Luxembourg: Publications Office of the European Union.
Critical ecosystem Partnership Fund (2021). Tropical Andes biodiversity update. Arglinton, VA, USA: Conservation International.
Dai, Q., Spagenberger, J., Ahmed, S., Gaines, L., Kelly, J. C., and Wang, M. (2019). EverBatt: A closed-loop battery recycling cost and environmental impacts model. Oak Ridge, TN, USA: Argonne National Laboratory.
Deng, Y., Li, J., Li, T., Gao, X., and Yuan, C. (2017). Life cycle assessment of lithium sulfur battery for electric vehicles. J. Power Sources 343, 284–295. doi:10.1016/j.jpowsour.2017.01.036
Dorn, F. M. (2021). Inequalities in resource-based global production networks: Resistance to lithium mining in Argentina (Jujuy) and Portugal (região norte). J. für Entwicklungspolitik JEP 37 (4), 70–91. doi:10.20446/JEP-2414-3197-37-4-70
Duquesnoy, M., Boyano, I., Ganborena, L., Cereijo, P., Ayerbe, E., and Franco, A. A. (2021). Machine learning-based assessment of the impact of the manufacturing process on battery electrode heterogeneity. Energy AI 5, 100090. doi:10.1016/j.egyai.2021.100090
EITI International Secretariat (2019). The EITI standard 2019. Oslo, Norway: EITI International Secretariat.
Eshetu, G. G., Zhang, H., Judez, X., Adenusi, H., Armand, M., Passerini, S., et al. (2021). Production of high-energy Li-ion batteries comprising silicon-containing anodes and insertion-type cathodes. Nat. Commun. 12, 5459. doi:10.1038/s41467-021-25334-8
ESRI (2011). ArcGIS desktop: Release 10. Redlands, CA, USA: Environmental Systems Research Institute..
Excosteguy, M., Clavijo, A., Paz, W. F. D., Hufty, M., and Seghezzo, L. (2022). We are not allowed to speak”: Some thoughts about a consultation process around lithium mining in Northern Argentina. Extr. Ind. Soc. 11, 101134. doi:10.1016/j.exis.2022.101134
Fang, R., Zhao, S., Sun, Z., Wang, D.-W., Cheng, H.-M., and Li, F. (2017). More reliable lithium-sulfur batteries: Status, solutions and prospects. Adv. Mat. 29 (48), 1606823. doi:10.1002/adma.201606823
Federal Aviation Administration (2021). FAA Aerospace forecast fiscal years 2022–2042. Washington, DC, USA: Federal Aviation Administration.
Gaines, L. (2014). The future of automotive lithium-ion battery recycling: Charting a sustainable course. Sustain. Mater. Technol. 1-2, 2–7. doi:10.1016/j.susmat.2014.10.001
Garjadro, G., and Redon, S. (2019). Andean hypersaline lakes in the Atacama Desert, northern Chile: Between lithium exploitation and unique biodiversity conservation. Conserv. Sci. Pract. 1 (9), e94. doi:10.1111/csp2.94
Gnadt, A. R., Speths, R. L., Sabnis, J. S., and Barrett, S. R. (2019). Technical and environmental assessment of all-electric 180-passenger commercial aircraft. Prog. Aerosp. Sci. 105, 1–30. doi:10.1016/j.paerosci.2018.11.002
Gonçalves, R., Lanceros-Méndez, S., and Costa, C. (2022). Electrode fabrication process and its influence in lithium-ion battery performance: State of the art and future trends. Electrochem. Commun. 135, 107210. doi:10.1016/j.elecom.2022.107210
Gray, N., McDonagh, S., O'Shea, R., Smyth, B., and Murphy, J. D. (2021). Decarbonising ships, planes and trucks: An analysis of suitable low-carbon fuels for the maritime, aviation and haulage sectors. Adv. Appl. Energy 1, 100008. doi:10.1016/j.adapen.2021.100008
Guterrez, J. S., Moore, J. N., Donnelly, J. P., Dorador, C., Navedo, J. G., and Senner, N. R. (1970). Climate change and lithium mining influence flamingo abundance in the Lithium Triangle. Proc. Biol. Sci. 289, 20212388. doi:10.1098/rspb.2021.2388
Hersh, E. S. (2019). Latin America’s diverse lithium opportunity and a sustainable energy future. Golden, CO: The Payne Institute for Public Policy.
Hizarci, H., Demirel, O., Kalayci, K., and Arifoglu, U. (2022). “An overview of aircraft electric power system for sustainable aviation,” in New Frontiers in sustainable aviation (Cham, Switzerland: Springer), 113–146.
Hoffman, M., Koenig, K., Bunting, G., Costanza, J., and Williams, K. J. (2016). Biodiversity hotspots. Avaliable at: http://legacy.cepf.net/SiteAssets/hotspots_2016_1.zip.
Hu, Y., Zhang, T., Cheng, F., Zhao, Q., Han, X., and Chen, J. (2015). Recycling application of Li–MnO2 batteries as rechargeable lithium–air batteries. Angew. Chem. Int. Ed. Engl. 54 (14), 4412–4417. doi:10.1002/ange.201411626
International Air Transport Association (2022). Net-zero carbon emissions by 2050. Available: https://www.iata.org/en/pressroom/2021-releases/2021-10-04-03/ (Accessed September 12, 2022).
International Energy Agency (2019). Global EV Outlook 2019: Scaling-up the transition to electric mobility. Paris: France.
International Energy Agency (2020). Energy technology perspectives 2020. Paris, France: International Energy Agency.
Karrech, A., Dong, M., Skut, J., Elchalakani, M., and Shahin, M. (2021). Management and valorisation of delithiated β-spodumene and its processing stream. Case Stud. Constr. Mater. 15, e00671. doi:10.1016/j.cscm.2021.e00671
Kaunda, R. (2020). Potential environmental impacts of lithium mining. J. Energy & Nat. Resour. Law 38 (3), 237–244. doi:10.1080/02646811.2020.1754596
Kenny, B., Darcovich, K., MacNeil, D. D., and Davidson, I. J. (2012). Modelling the impact of variations in electrode manufacturing on lithium-ion battery modules. J. Power Sources 213, 391–401. doi:10.1016/j.jpowsour.2012.03.065
Komas, T., Daub, R., Karamat, M. Z., Thiede, S., and Herrmann, C. (2019). “Data-and expert-driven analysis of cause-effect relationships in the production of lithium-ion batteries,” in IEEE 15th International Conference on Automation Science and Engineering, Vancouver, BC, Canada, 22-26 August 2019 (IEEE), 380–385.
Lee, D., Fahey, D., Skowron, A., Allen, M., Burkhardt, U., Chen, Q., et al. (2021). The contribution of global aviation to anthropogenic climate forcing for 2000 to 2018. Atmos. Environ. X. 244, 117834. doi:10.1016/j.atmosenv.2020.117834
Li, J., Fleetwood, J., Hawley, W. B., and Kays, W. (2022). From materials to cell: State-of-the-Art and prospective technologies for lithium-ion battery electrode processing. Chem. Rev. 122, 903–956. doi:10.1021/acs.chemrev.1c00565
Liu, H., Xu, Y., Stockwell, N., Rodgers, M. O., and Guensler, R. (2016). A comparative life-cycle energy and emissions analysis for intercity passenger transportation in the U.S. by aviation, intercity bus, and automobile. Transp. Res. Part D Transp. Environ. 48, 267–283. doi:10.1016/j.trd.2016.08.027
Liu, J., Rahimian, S. K., and Monroe, C. E. (2016). Capacity-limiting mechanisms in Li/O2 batteries. Phys. Chem. Chem. Phys. 18 (33), 22840–22851. doi:10.1039/c6cp04055a
Liu, W., and Agusdinata, D. B. (2020). Interdependencies of lithium mining and communities sustainability in Salar de Atacama, Chile. J. Clean. Prod. 260, 120838. doi:10.1016/j.jclepro.2020.120838
Liu, W., Agusdinata, D. B., and Myint, S. W. (2019). Spatiotemporal patterns of lithium mining and environmental degradation in the Atacama Salt Flat, Chile. Int. J. Appl. Earth Obs. Geoinf. 80, 145–156. doi:10.1016/j.jag.2019.04.016
Liu, W., and Agusdinata, D. (2021). Dynamics of local impacts in low-carbon transition: Agent-based modeling of lithium mining-community-aquifer interactions in Salar de Atacama, Chile. Extr. Ind. Soc. 8 (3), 100927. doi:10.1016/j.exis.2021.100927
Mayyas, A., Steward, D., and Mann, M. (2019). The case for recycling: Overview and challenges in the material supply chain for automotive li-ion batteries. Sustain. Mater. Technol. 19, e00087. doi:10.1016/j.susmat.2018.e00087
Mihalasky, M., Briggs, D., Baker, M., Jaskula, B., Cheriyan, K., and DeLoach-Overton, S. (2020). Lithium occurrences and processing facilities of Argentina, and salars of the lithium triangle central south America. USA: U.S. Geological Survey data release.
Mistry, A., Franco, A. A., Cooper, S. J., Roberts, S. A., and Viswanathan, V. (2021). How machine learning will revolutionize electrochemical Sciences. ACS Energy Lett. 6 (4), 1422–1431. doi:10.1021/acsenergylett.1c00194
Mounir, I. (2022). Commercial market outlook 2022-2041. Available at: https://www.boeing.com/resources/boeingdotcom/market/assets/downloads/CMO_2022_Report_FINAL_v02.pdf.
National Academies of Sciences (2016). Engineering, and medicine, commercial aircraft propulsion and energy: Reducing global carbon emissions. Washington, DC, USA: National Academies Press.
Nowak, S., and Winter, M. (2017). The role of sub- and supercritical CO2 as “processing solvent” for the recycling and sample preparation of lithium ion battery electrolytes. Molecules 22 (3), 403. doi:10.3390/molecules22030403
Pereira, E. T. S. (2018). Lithium in Portugal. From an opportunity to a (hidden) threat? Porto, Portugal: Repositório Aberto da Universidade do Porto.
Petavratzi, E., Sanchez-Lopez, D., Hughes, A., Stacey, J., Ford, J., and Butcher, A. (2022). The impacts of environmental, social and governance (ESG) issues in achieving sustainable lithium supply in the Lithium Triangle. Min. Econ. 35, 673–699. doi:10.1007/s13563-022-00332-4
Pornet, C., Gologan, C., Vratny, P., Seitz, A., Schmitz, O., Isikveren, A., et al. (2015). Methodology for sizing and performance assessment of hybrid energy aircraft. J. Aircr. 52 (1), 341–352. doi:10.2514/1.c032716
Prior, T., Wager, P. A., Stamp, A., Widmer, R., and Giurco, D. (2013). Sustainable governance of scarce metals: The case of lithium. Sci. Total Environ. 461-462, 785–791. doi:10.1016/j.scitotenv.2013.05.042
Rodrigues, P. M. S. M., Antao, A. M. M. C., and Rodrigues, R. (2019). Evaluation of the impact of lithium exploitation at the C57 mine (Gonçalo, Portugal) on water, soil and air quality. Environ. Earth Sci. 78, 533. doi:10.1007/s12665-019-8541-4
Sanchez-Lopez, D. (2019). Sustainable governance of strategic minerals: Post-neoliberalism and lithium in Bolivia. Environ. Sci. Policy Sustain. Dev. 61 (6), 18–30. doi:10.1080/00139157.2019.1662659
Schmidt, O., Tomizek, M., Röder, F., Thiede, S., Herrmann, C., and Krewer, U. (2020). Modeling the impact of manufacturing uncertainties on lithium-ion batteries. J. Electrochem. Soc. 167 (6), 060501. doi:10.1149/1945-7111/ab798a
Scholz, A. E., Trifonov, D., and Hornung, M. (2022). Environmental life cycle assessment and operating cost analysis of a conceptual battery hybrid-electric transport aircraft. CEAS Aeronaut. J. 13, 215–235. doi:10.1007/s13272-021-00556-0
Schwab, A., Thomas, A., Bennett, J., Robertson, E., and Cary, S. (2021). Electrification of aircraft: Challenges, barriers, and potential impacts. Golden, CO: NREL.
Schwich, L., Sabarny, P., and Friedrich, B. (2020). Recycling potential of lithium–sulfur batteries—a first concept using thermal and hydrometallurgical methods. Metals 10 (11), 1513. doi:10.3390/met10111513
Seefeldt, J. L. (2020). Lessons from the lithium triangle: Considering policy explanations for the variation in lithium industry development in the “lithium triangle” countries of Chile, Argentina, and Bolivia. Polit. Policy 48 (4), 727–765. doi:10.1111/polp.12365
Seiner, H.-J., Vratny, P. C., Gologan, C., Wieczorek, K., Isikveren, A., and Hornung, M. (2014). Optimum number of engines for transport aircraft employing electrically powered distributed propulsion. CEAS Aeronaut. J. 5, 157–170. doi:10.1007/s13272-013-0096-6
Silva, G. V., Thomitzek, M., Abraham, T., and Herrmann, C. (2021). “Simulation-based assessment of energy demand and costs associated with production scrap in the battery production,” in Simulation in Produktion und Logistik 2021 (Göttingen: Cuvillier Verlag), 103–112.
Stamp, A., Lang, D. J., and Wager, P. A. (2012). Environmental impacts of a transition toward e-mobility: The present and future role of lithium carbonate production. J. Clean. Prod. 23 (1), 104–112. doi:10.1016/j.jclepro.2011.10.026
Stringfellow, W. T., and Dobson, P. F. (2021). Technology for the recovery of lithium from geothermal brines. Energies 14 (20), 6805. doi:10.3390/en14206805
Süsser, D., Martin, N., Stavrakas, V., Gaschnig, H., Talens-Peiró, L., Flamos, A., et al. (2022). Why energy models should integrate social and environmental factors: Assessing user needs, omission impacts, and real-word accuracy in the European Union. Energy Res. Soc. Sci. 92, 102775. doi:10.1016/j.erss.2022.102775
Swain, B. (2017). Recovery and recycling of lithium: A review. Sep. Purif. Technol. 172, 388–403. doi:10.1016/j.seppur.2016.08.031
Thiede, S., Tureskyy, A., Kwade, A., Kara, S., and Herrmann, C. (2019). Data mining in battery production chains towards multi-criterial quality prediction. CIRP Ann. 68 (1), 463–466. doi:10.1016/j.cirp.2019.04.066
Turetskyy, A., Wessel, J., Herrmann, C., and Thiede, S. (2021). Battery production design using multi-output machine learning models. Energy Storage Mat. 38, 93–112. doi:10.1016/j.ensm.2021.03.002
U.S. Geological Survey (2022). Mineral commodity summaries 2022 - lithium. Available: https://pubs.usgs.gov/periodicals/mcs2022/mcs2022-lithium.pdf (Accessed Sept 29, 2022).
Valle, V. M., and Holmes, H. C. (2013). Bolivia's energy and mineral resources trade and investments with China: Potential socioeconomic and environmental effects of lithium extraction. Lat. Am. Policy 4 (1), 93–122. doi:10.1111/lamp.12007
Wang, F., Deng, Y., and Yuan, C. (2020). Life cycle assessment of lithium oxygen battery for electric vehicles. J. Clean. Prod. 264, 121339. doi:10.1016/j.jclepro.2020.121339
Wernet, G., Bauer, C., Steubing, B., Reinhard, J., Moreno-Ruiz, E., and Weidema, B. (2016). The ecoinvent database version 3 (part I): Overview and methodology. Int. J. Life Cycle Assess. 21 (9), 1218–1230. doi:10.1007/s11367-016-1087-8
Wu, Z., and Kong, D. (2018). Comparative life cycle assessment of lithium-ion batteries with lithium metal, silicon nanowire, and graphite anodes. Clean. Technol. Environ. Policy 20, 1233–1244. doi:10.1007/s10098-018-1548-9
Yang, C. P., Yin, Y. X., and Guo, Y. G. (2015). Elemental selenium for electrochemical energy storage. J. Phys. Chem. Lett. 6, 256–266. doi:10.1021/jz502405h
Yilmaz, N., and Atmanli, A. (2022). Sustainable alternative fuels in aviation. Energy 140, 1378–1386. doi:10.1016/j.energy.2017.07.077
Zhang, J., and Azimi, G. (2022). Recycling of lithium, cobalt, nickel, and manganese from end-of-life lithium-ion battery of an electric vehicle using supercritical carbon dioxide. Resour. Conserv. Recycl. 187, 106628. doi:10.1016/j.resconrec.2022.106628
Keywords: sustainability, lithium batteries, electrified aviation, social justice, supply chain
Citation: Chen-Glasser M and DeCaluwe SC (2022) A review on the socio-environmental impacts of lithium supply for electric aircraft. Front. Aerosp. Eng. 1:1058940. doi: 10.3389/fpace.2022.1058940
Received: 30 September 2022; Accepted: 10 November 2022;
Published: 02 December 2022.
Edited by:
Matthew Oehlschlaeger, Rensselaer Polytechnic Institute, United StatesReviewed by:
Rajendra Singh, Clemson University, United StatesRafal Kowalik, Polish Air Force University, Poland
Lucjan Setlak, Polish Air Force University, Poland
Copyright © 2022 Chen-Glasser and DeCaluwe. This is an open-access article distributed under the terms of the Creative Commons Attribution License (CC BY). The use, distribution or reproduction in other forums is permitted, provided the original author(s) and the copyright owner(s) are credited and that the original publication in this journal is cited, in accordance with accepted academic practice. No use, distribution or reproduction is permitted which does not comply with these terms.
*Correspondence: Steven C. DeCaluwe, ZGVjYWx1d2VAbWluZXMuZWR1