- 1Institute of Technology and Exact Sciences, Federal University of Amazonas – UFAM, Itacoatiara, Brazil
- 2Department of Chemistry, Environment, and Food – DQA, Manaus Center Campus, Federal Institute of Education, Science, and Technology of Amazonas – IFAM, Manaus, Brazil
- 3Electrochemistry and Energy Laboratory – LEEN, Department of Chemistry, Federal University of Amazonas – UFAM, Manaus, Brazil
This work presents a comparative study of three synthesis methods for PtRu/C catalysts for use in polymer electrolyte fuel cells, investigating their activity in methanol oxidation. The evaluated methods were formic acid reduction (FAM), methanol reduction (ARM), and ethylene glycol reduction (ARE). XRD analysis confirmed the formation of a Pt-Ru binary alloy in all syntheses. Electrochemical tests indicated that all catalysts were properly prepared, with the PtRu/CARE catalyst standing out as having the best performance, achieving a power density of 74,88 mW cm−2 at 90°C and an oxygen pressure of 3 atm on the cathode. These results highlight the potential of PtRu/CARE for application in direct methanol fuel cells, surpassing the catalysts obtained through the other methods.
1 Introduction
Concerns over potential energy crises and environmental issues have become increasingly prominent in international discussions, driving the search for solutions to improve both energy storage and conversion. A clear example of this is the growing amount of research dedicated to the development of batteries, fuel cells, and supercapacitors. In this context, direct methanol fuel cells (DMFCs) are considered promising alternatives, as they convert the chemical energy of methanol into electricity through electrochemical processes, specifically through the methanol oxidation reaction (MOR) within the device (Zuo et al., 2022; Peng et al., 2023).
The search for more efficient catalysts for DMFCs involves developing materials that offer higher catalytic activity and operational durability. It is known that platinum-group metals (Ir, Os, Pt, Pd, Ru, and Rh), as well as other noble metals (such as Au and Ag), are chemically stable, making them suitable for reactions that require high catalytic activity, such as the MOR. However, despite many precious metal-based catalysts exhibiting desirable electrochemical performance, their high cost still limits their widespread large-scale application. As a result, researchers have devoted substantial efforts to improving the performance of these devices and making them more viable. Various strategies are employed to enhance the performance of DMFC catalysts, including adjustments in catalyst morphology, composition, architecture, and alloy degree (Tian et al., 2021; Zuo et al., 2022).
Pt-based materials are widely used in the catalysis of electrochemical reactions, including MOR. However, Pt’s catalytic activity faces certain challenges, such as the poisoning of active sites by strongly adsorbed intermediates, which reduces its effectiveness. To mitigate these issues, one of the main strategies is alloying Pt with other transition metals (Peng et al., 2023; Wang et al., 2024).
Binary and ternary catalysts have proven to be excellent options for improving methanol oxidation (Zuo et al., 2022). Among them, carbon-supported Pt and Ru-based catalysts (PtRu/C) stand out for their superior performance. This improvement is due to PtRu/C catalysts promoting methanol oxidation at low potentials and exhibiting greater resistance to CO poisoning. This occurs through the bifunctional mechanism, in which Pt adsorbs and dissociates methanol, while Ru oxidizes the adsorbed residues (Petrii, 2008; Yaqoob et al., 2021).
For instance, in the study by Sahin and Kivrak (2013), the authors synthesized catalysts combining Pt and Ru in different proportions using ethylene glycol as the reducing agent. They concluded that the Pt-Ru (25:1) catalyst showed higher activity and resistance to CO poisoning, as well as greater long-term stability compared to Pt-Ru (3:1), Pt-Ru (1:1), and Pt. Wang et al. (2021) synthesized PtRu/C using sodium borohydride (NaBH4) as the reducing agent. They observed that the PtRu/C catalyst synthesized with surfactant assistance exhibited catalytic activity about 1.8 times higher than the commercial PtRu/C catalyst. Xie et al. (2016) developed core-shell-type catalysts with different combinations of Pt and Ru. When applied to MOR in half-cell studies and single-fuel cell tests, the authors identified that the Ru@Pt0.5/C catalyst demonstrated better performance in terms of current density and greater tolerance to CO poisoning than other compositions tested (Xie et al., 2016). Regarding ternary catalysts, Kang et al. (2010) synthesized Pt-Ru-M (M = Ni, Sn, Mo) catalysts using NaBH4 as the reducing agent. In the electrochemical tests, the Pt5Ru4Ni catalyst showed the highest specific activity and methanol oxidation capacity compared to the PtRu and Pt catalysts, with activity 2.2 times higher than PtRu. While Pt5Ru4Sn and Pt5Ru4Mo performed worse than Pt5Ru4Ni, they still outperformed PtRu (Kang et al., 2010).
In addition to the atomic composition of the alloys, the synthesis methodology of the catalysts also plays a crucial role. In general, aqueous-phase synthesis methods, where water acts as the solvent for precursors, complexing agents, and reducing agents, are more widely used to obtain high-quality materials. However, the major challenge of these processes is maintaining highly dispersed and size-controlled PtRu nanoparticles on carbon supports, in addition to achieving the desired atomic ratio and alloy degree. Several methodologies, such as impregnation-reduction methods and colloidal routes, are employed for PtRu/C synthesis, using reducing agents like formic acid, methanol, ethanol, and ethylene glycol, with the latter two particularly suitable for obtaining electrocatalysts with uniform size and good distribution (Yaqoob et al., 2021; Wang et al., 2021; Liu et al., 2022).
In this context, the objective of this work was to synthesize and characterize PtRu/C catalysts using three different reducing agents: formic acid, methanol, and ethylene glycol. The performance of the catalysts for MOR was evaluated using voltammetry and chronoamperometry techniques, as well as potential and current measurements and polarization curves in a single fuel cell, aiming to correlate the electrochemical performance of methanol oxidation with the characteristics of the electrode surface.
2 Materials and methods
2.1 Synthesis of PtRu/C catalysts
Formic Acid Method (FAM): The synthesis of PtRu/C catalysts using formic acid as a reducing agent was performed by adding an appropriate amount of high surface area carbon powder (Vulcan XC-72, Cabot) to a 0.5 mol L−1 formic acid solution. (Salgado et al., 2013). To optimize ruthenium incorporation, the pH of the solution was adjusted to values around 14 using a 1.0 M KOH solution, favoring the conversion of RuCl3 to Ru(OH)3, thus improving reduction by the formate ion (dos Santos et al., 2006). The mixture was heated to 80°C, and then solutions of chloroplatinic acid (H2PtCl6.6H2O, Aldrich) and ruthenium chloride (RuCl3.6H2O, Aldrich) were added. After the reaction was complete, the pH was adjusted to 7, and the catalysts were vacuum-filtered and washed with ultrapure water. Notably, the reaction time was set to 1 h, and the platinum reduction process was confirmed through the potassium iodide test. Finally, the material was dried at 80°C for 2 h. The metal loading (PtRu) was 40%.
Alcohol Reduction Method: Two solvents and reducing agents were used: ethylene glycol (ARE) and methanol (ARM). Metal precursor salts were dissolved in ethylene glycol:H2O (3:1, v/v) or methanol:H2O (1:3, v/v) solutions, using Vulcan XC-72 as support. The mixtures were subjected to reflux heating for 3 h, at 90°C (methanol) or 130°C (ethylene glycol). After synthesis, the materials were washed with ultrapure water while being filtered and then dried at 80°C for 2 h (Spinacé et al., 2004; Sarma et al., 2005). In the methanol reduction process, the surfactant SB-12 was used for particle size control. In the case of ethylene glycol, its structure stabilizes the colloid, eliminating the need for surfactants (Spinacé et al., 2004; de Araujo et al., 2018; Marinho et al., 2021). The metal loading (PtRu) was 40%.
2.2 Catalyst characterization
The atomic composition of the catalysts was determined using energy dispersive X-ray spectroscopy (EDX) with an EDX-700A spectrometer (SHIMADZU). X-ray diffraction (XRD) analyses were performed using a D5000 diffractometer (SIEMENS) with Cu Kα radiation (1.5406 Å–potential of 40 mV and current of 30 mA). The diffraction angles (2θ) ranged from 10° to 90°, using a 0.05° step size and a scanning speed of 2°/min. Scanning electron microscopy (SEM) measurements were performed using a VEGA 3 – TESCAN electron microscope.
2.3 Electrochemical measurements
Electrochemical measurements were conducted in a half-cell setup with three electrodes, using a BAS CV 50W potentiostat/galvanostat (Bioanalytical System). A glassy carbon electrode (0.23 cm2) was used as the working electrode, a reversible hydrogen electrode (RHE) as the reference electrode, and a platinum plate as the counter-electrode. Before measurements, the working electrode was polished with alumina of different particle sizes (3.0 μm, 1.0 μm, and 0.3 μm). For catalyst deposition, inks were prepared by mixing 1 mg of the catalyst, 200 μL of isopropyl alcohol, and 10 μL of a 5% Nafion® solution. The suspension was ultrasonicated for 30 min, and 15 μL of the ink was applied to the glassy carbon electrode to ensure full coverage (Marinho et al., 2021). The results obtained were normalized by the geometric area of the working electrode.
2.4 Measurements in single fuel cell
The gas diffusion electrodes, composed of the diffusion and catalyst layers, were prepared using a combination of the painting and deposition methods (Paganin et al., 1996). The methodology is briefly presented below: the diffusion layer was fabricated from a homogeneous aqueous suspension of carbon powder (Vulcan XC-72, Cabot) and PTFE (PTFE T-30, DuPont), which was applied and filtered on both sides of a carbon cloth (PWB-3, Stackpole). After application, the structure was dried at 280°C for 30 min, followed by sintering at 350°C for another 30 min. The PTFE content in the diffusion layer was maintained at 15 wt% on both sides of the cloth for all electrodes.
The catalyst layer on the cathode side was prepared by mixing the PtRu/C catalyst obtained by the previously described methods with a 5% Nafion® solution (DuPont) and isopropanol as the solvent. The resulting mixture formed an ink, which was painted onto one side of the diffusion layer. Subsequently, the sample was heated to 80°C for 1 h. The catalyst loading was 1 mg cm−2, and the Nafion® content was 1.1 mg cm−2 for all electrodes. The same procedure was followed for the anode side using a Pt/C catalyst (20%, E-TEK).
For the Membrane-Electrode Assembly (MEA), a Nafion® N117 (DuPont) membrane was used. The MEA was fabricated by hot pressing under 5 tons of pressure at 125°C for 5 minutes. For comparison purposes, a commercial PtRu/C catalyst (40%, E-TEK) was also used. Experimental tests were conducted on an ELECTROCELL workstation (ETC-500P), with methanol feeding the anode and oxygen feeding the cathode (Antolini et al., 2007; Salgado et al., 2013). The methanol and oxygen flow rates were 2.5 mL min−1 and 70 mL min−1, respectively. The oxygen feed pressure at the cathode ranged from 1 atm to 3 atm, and the cell operating temperature was adjusted between 30ºC and 90°C.
3 Results and discussion
3.1 Catalyst characterization
Figure 1 presents the X-ray diffraction patterns of the PtRu/C catalysts prepared by the three methods: formic acid reduction (PtRu/CFAM), methanol reduction (PtRu/CARM), and ethylene glycol reduction (PtRu/CARE). These diffraction patterns are compared with that of the commercial PtRu/C catalyst (E-TEK). Regardless of the preparation method, all catalysts exhibited four diffraction peaks related to the face-centered cubic (FCC) structure, around 40°, 47°, 67°, and 82°, which correspond to the crystalline planes (111), (200), (220), and (311) of polycrystalline Pt, respectively. No diffraction peak characteristic of metallic ruthenium was identified in any of the samples, suggesting that Ru was fully incorporated into the Pt crystal lattice. This behavior is also evidenced by the shift of 2θ values to higher angles compared to those attributed to the Pt (FCC) planes as specified by the JCPDS 01–1,194 card (Wang et al., 2021; Wang et al., 2024; Chen et al., 2022).
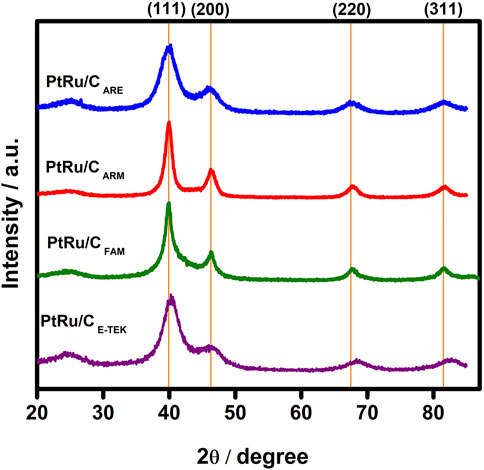
Figure 1. X-ray diffraction patterns of the synthesized electrocatalysts, compared to the commercial E-TEK catalyst and the Pt reference pattern from JCPDS 01–1,194 (orange lines).
An indication of the insertion of Ru atoms into the Pt crystalline lattice, beyond the shift in diffraction angles, is the reduction of lattice parameters (Table 1), since Ru has a smaller atomic radius than Pt. As a result, the electronic properties of Pt are modified with the formation of this solid solution (alloy), which is expected to improve the catalytic performance of these materials. In the Pt-Ru alloy, there is a suggestion that the incorporation of Ru reduces the adsorption of intermediates such as CO on the Pt surface, thereby increasing catalytic activity and the durability of the electrocatalysts (Radmilović et al., 1995).
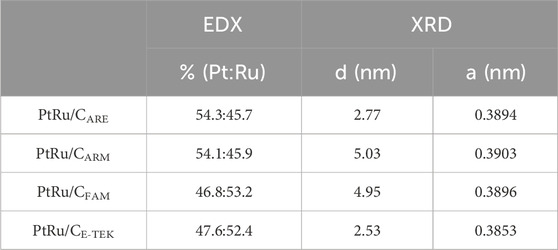
Table 1. Elemental composition in percentage (%) determined by EDX, crystallite size (d) determined by Scherrer’s equation, and Pt lattice parameter (a).
To calculate the crystallite size (d), Scherrer’s Equation was applied to the (220) plane. A proportionality constant “K” of 0.9 was adopted, assuming that the particles predominantly have a spherical shape. The value of “λ” was 0.15406 nm, as the equipment used Cu Kα radiation (Ferreira Frota et al., 2017; de Araujo et al., 2018). The reflection adjustment was performed using the Lorentz function. The crystallite sizes ranged between 2.5 and 5.0 nm. The XRD results, along with the elemental composition data obtained from EDX are summarized in Table 1.
This variation in crystallite size indicates the impact of the synthesis method on the catalyst’s crystalline structure. The values followed the increasing order: ARE < FAM < ARM, with the commercial PtRu E-TEK catalyst presenting the smallest value. Considering that smaller crystallite sizes are often associated with a higher specific surface area, it is expected that this material would also exhibit a greater density of active sites available for catalysis.
The lattice parameter values (Table 1) were determined using the Unitcell program. The obtained values were smaller than the reference for Pt/C (0.3931 nm, JCPDS, sheet 4–802), confirming the greater insertion of ruthenium into the Pt crystalline lattice. Similar results were observed by other authors using different preparation methods (Radmilović et al., 1995; Aricò et al., 1996), indicating that Ru incorporation into the lattice depends on the synthesis method used. This means that a Pt-Ru alloy was formed, and in this case, these materials are expected to exhibit greater synergy, leading to improved catalytic performance.
In summary, the XRD data confirm the formation of Pt-Ru alloys across all synthesis methods. The synthesis method directly influences the structural properties of the catalysts, as evidenced by variations in crystallite size and lattice parameters. Based on these results, catalysts synthesized by ethylene glycol reduction (ARE) are expected to show superior performance in fuel cell applications due to their smaller crystallite size and higher Ru insertion, characteristics that enhance both catalytic activity and resistance to poisoning by reaction intermediates.
Figure 2 shows the SEM images of the prepared PtRu/C catalysts. It can be observed in the micrographs that the PtRu/C catalysts showed considerable superficial similarity. That is, the synthesis methods compared in this study are not sufficiently significant to provide substantial morphological changes. In general, all samples exhibited a morphology of rounded, predominantly globular agglomerates. However, as can be observed in the diffractograms of Figure 1, the methods provided significant changes in the orientations of the Pt FCC planes. Thus, the difference in activities for electrochemical catalysis can be observed precisely because one method or another provides more reactive and more stable planes for methanol oxidation. The works developed by Jarvi et al. (1998), Tremiliosi-Filho et al. (1999), and Housmans et al. (2006) demonstrated long ago that different crystallographic orientations of Pt present distinct catalytic activities for the oxidation of methanol, with emphasis, for example, on the Pt (100) plane. This fact justifies the differences in electroactive surface area (ECSA) values calculated for the catalysts (Table 2), as well as the observed differences in catalytic activity for MOR in electrochemical analyses and unit cell studies.
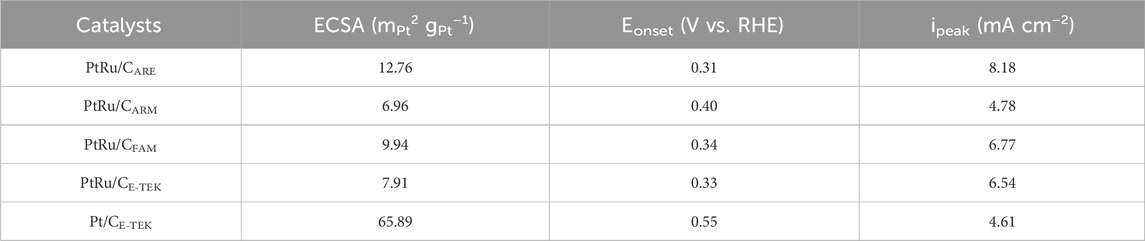
Table 2. Methanol oxidation parameters on PtRu/CE-TEK, PtRu/CFAM, PtRu/CARM, PtRu/CARE, and Pt/CE-TEK: electroactive surface area of Pt (ECSA), onset oxidation potential (Eonset) and peak current (ipeak).
3.2 Electrochemical measurements
With the assistance of voltammetric analyses, it was possible to determine the ECSA values of the catalysts (Table 2), which were calculated using the ratio of the charge related to the hydrogen desorption region (measured in μC) to the charge density required to reduce a monolayer of protons on a polycrystalline Pt surface (210 μC cmPt−2) (Trasatti and Petrii, 1991).
The synthesized catalysts were used for the methanol electro-oxidation reaction (MOR). The MOR electro-oxidation measurements were performed in an electrolyte of 0.5 mol L−1 H2SO4 with a methanol concentration of 1.0 mol L−1. In the anodic scan linear voltammetry (Figure 3), it is observed that, between potentials of 0.05–0.4 V (V vs. RHE), there is no significant difference between the catalysts regarding methanol electro-oxidation, indicating a sensitive blockage in the hydrogen region, suggesting that methanol adsorption occurs at very low potentials. The first indications of effective alcohol oxidation can be observed around 0.4 V–0.5 V, a potential region where a significant current increase is noted. In this process, the main adsorbate, carbon monoxide (CO), appears as an intermediate of methanol oxidation. Its oxidation to carbon dioxide occurs due to the presence of oxygenated species, usually adsorbed on the surface of the second metal at low potentials (Wang et al., 2021).
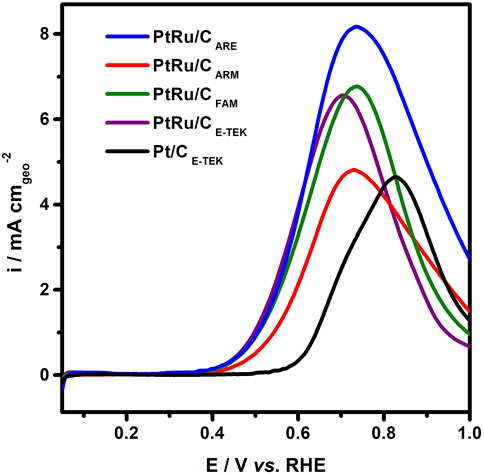
Figure 3. Linear sweep voltammograms for PtRu/C catalysts compared with Pt/CE-TEK. Scan rate: 2 mV s−1. Electrolyte: 0.5 mol L−1 H2SO4 + 1.0 mol L−1 methanol.
In general, under the applied experimental conditions (electrolyte: 0.5 mol L−1 H2SO4 + 1.0 mol L−1 methanol), it is observed that PtRu/CE-TEK, PtRu/CFAM, PtRu/CARM, and PtRu/CARE exhibit lower onset oxidation potentials (Eonset) than Pt/CE-TEK (Table 2). This means that, during the anodic linear sweep, the current values for PtRu/C begin to increase more prominently at lower potentials compared to Pt/C. The PtRu/CFAM catalyst showed a peak of 6.77 mA cm−2 at a potential of 0.74 V. PtRu/CARM reached 4.78 mA cm−2 at 0.73 V, while PtRu/CARE exhibited 8.18 mA cm−2 at 0.74 V. PtRu/CE-TEK, on the other hand, presented its peak current at 0.70 V with a magnitude of 6.54 mA cm−2.
The PtRu/CARM, PtRu/CARE, and PtRu/CFAM catalysts demonstrated an enhancement of approximately 0.2 V in the electro-oxidation of methanol compared to Pt/CE-TEK. This phenomenon is commonly reported in various academic works, as platinum alone becomes less efficient in the methanol oxidation reaction (MOR). Due to the bifunctional mechanism, the addition of Ru promotes greater efficiency in the removal of intermediates generated during the reaction, allowing for increased catalytic activity of the Pt sites (Petrii, 2008; Yaqoob et al., 2021; Wang et al., 2024).
Among the synthesized catalysts, it is observed that PtRu/CARM exhibited inferior performance compared to the other Pt-Ru catalysts, despite the chemical composition (loadings of ruthenium and platinum) being considerably similar. In addition to having a higher Eonset, PtRu/CARM developed a lower current peak related to methanol oxidation. This may be directly related to the synthesis methodology of this material. As previously emphasized regarding the XRD data, there is a close relationship between the electrochemical performance and the morphology of catalysts, which may be associated with particle size and crystallographic orientations that can be more effective for MOR catalysis (Kakati et al., 2014; Peng et al., 2023).
In a general overview, aiming for a possible application in direct methanol fuel cells (DMFC), the best catalyst is characterized by the highest potential shift in the electro-oxidation of methanol (Kakati et al., 2014; Peng et al., 2023). Therefore, as observed in Figure 3, the material prepared through ethylene glycol reduction (PtRu/CARE) stands out as the most promising for application in MOR catalysis.
The study of the stability of the catalysts through chronoamperometric tests is represented in Figure 4, in which a stationary condition of 0.6 V vs. RHE was applied. The initial behavior, characterized by a rapid drop in current, can be attributed to the accumulation of adsorbates on the catalyst surface, which compromises the subsequent steps of methanol oxidation (Wang et al., 2024). Among the evaluated catalysts, PtRu/CARE exhibited superior performance, showing comparable results to PtRu/CE-TEK. On the other hand, the catalyst synthesized by reduction with methanol (PtRu/CARM) demonstrated inferior performance, likely due to morphological differences or greater susceptibility to poisoning by reaction intermediates.
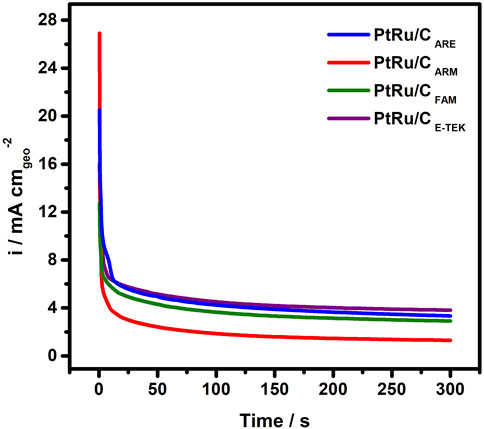
Figure 4. Comparative graph of chronoamperometric tests for methanol oxidation on the PtRu/C catalysts at 0.6 V for 300 s. Electrolyte: H2SO4 0.5 mol L−1 + methanol 1.0 mol L−1.
After 250 s, it was observed that the currents stabilized, with minor variations, indicating an almost stationary behavior for all the electrodes. This result suggests that, after the initial phase of intermediate adsorption, the catalysts reach a balance zone where the catalytic activity remains constant for a more extended period.
3.3 Measurements in single fuel cell
Studies on single fuel cells operating with methanol indicate that improvements in cell performance are directly related to factors such as the catalysts used, the preparation of the MEA, and the operational parameters and conditions, including gas feed and operating temperature (Yaqoob et al., 2021; Ahmed et al., 2022).
In general, all synthesized catalysts exhibited increasing catalytic activity with rising temperatures, achieving performance comparable to that of PtRu/CE-TEK, especially at temperatures between 70°C and 90°C (Figure 5). In these temperature ranges, no significant differences were observed in the high current density region. However, this behavior was not repeated under conditions where the temperature was close to ambient (30°C).
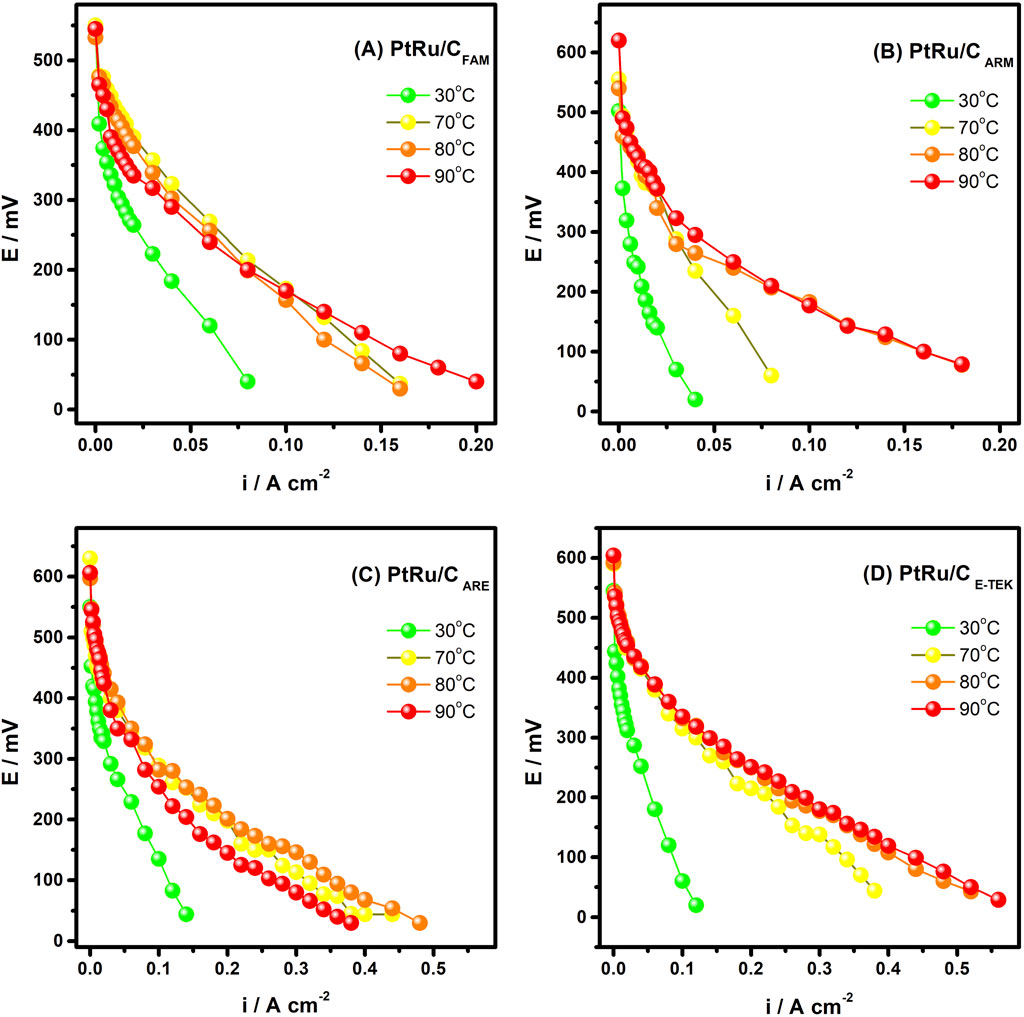
Figure 5. Polarization curves (E vs. i) for single cell tests using the catalysts: (A) PtRu/CFAM (B) PtRu/CARM, (C) PtRu/CARE, and (D) PtRu/CE-TEK at different operating temperatures.
In the region of low current densities, where activation losses occur due to the slow kinetics of electrons at the electrolyte/catalyst interface, higher performance is typically observed at elevated temperatures, with performance expected to improve beyond 90°C. However, it is important to note that as the temperature increases, the phenomenon of methanol crossover through the Nafion® membrane becomes more pronounced, which can interfere with the oxygen reduction reaction (ORR). Knowing that the Nafion® membrane is not completely impermeable, this crossover effect can lead to a greater loss of cell potential, as methanol oxidation will compete with the ORR at the cathode during this process (Velázquez-Palenzuela et al., 2011; Yaqoob et al., 2021).
In the current density region close to 0.1 A cm−2 (Figure 5), where ohmic losses occur, it is observed that the effect of temperature is quite significant, directly influencing the potential measured in the cell. The potentials obtained for PtRu/CFAM (Figure 5A), PtRu/CARM(Figure 5B) and, PtRu/CARE (Figure 5C) at a temperature of 80°C were 282, 183, and 282 mV, respectively. These potentials are lower compared to the commercial PtRu/CE-TEK (Figure 5D), which achieved 332 mV at the same temperature.
At a temperature of 90°C, the potentials obtained for a current density of 0.1 A cm−2 were equal to or lower than those obtained at 80°C, further evidencing the crossover effect, which is favored by the increase in temperature. Additionally, at 90°C, it is noticeable that the Nafion® membrane begins to dry out, which impairs its proton conductivity. As a result, the increased flow of methanol toward the cathode becomes more pronounced, competing with the electroosmotic drag of protons through the membrane (Velázquez-Palenzuela et al., 2011; Sahin and Kivrak, 2013; Yaqoob et al., 2021).
At 90°C, the potential versus current density (E vs. i) and power versus current density (P vs. i) curves, presented in Figure 6, reveal similar electrochemical performance between the electrocatalysts PtRu/CARM and PtRu/CFAM. Both achieved maximum power densities of 18.06 mW cm−2 and 16.8 mW cm−2, respectively, indicating that under more aggressive operating conditions (at 90°C), these two materials behave similarly in terms of electrocatalytic efficiency and overall performance.
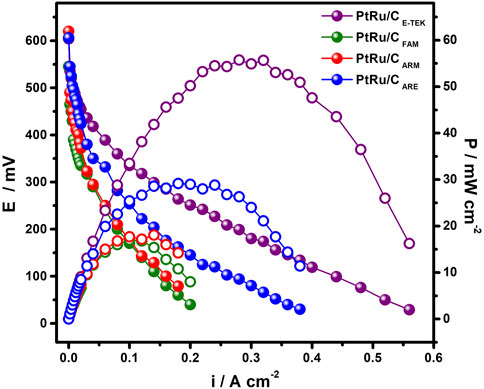
Figure 6. Polarization (E vs. i) and power density (P vs. i) curves for the PtRu/CFAM, PtRu/CARM, and PtRu/CARE, compared to the commercial PtRu/CE-TEK catalyst, measured at an operating temperature of 90°C.
However, when analyzing the behavior of the catalysts PtRu/CARE and PtRu/CE-TEK, a greater performance divergence was observed as the current density increased. This difference became more pronounced at high current densities, resulting in a significant variation of approximately 26 mW cm−2 between the two catalysts. This behavior suggests that while the performance of the catalysts is similar at low current densities, PtRu/CARE exhibits competitive advantages under high load conditions, even surpassing PtRu/CE-TEK.
As we have previously seen, this difference may be strongly associated with structural and morphological factors of the catalysts, such as particle distribution, nanoparticle size, and dispersion on the carbon support, which directly affect the efficiency of the catalytic process, especially at high current densities. Additionally, PtRu/CARE seems to handle better the limitations imposed by reactant diffusion and water management, which contributes to its superior performance compared to the other catalysts.
Therefore, when evaluating the efficiency of electrocatalysts under more severe operating conditions, such as at 90°C, PtRu/CARE is more active, especially at higher currents, where reaction kinetics become more limiting and ohmic resistance plays a more critical role in the overall performance (Shrivastava et al., 2015). These operating conditions were confirmed in the studies of Neto et al. (2009), focusing on the activity of PtRu/C prepared using citric acid as a reducing agent and OH− ions as a stabilizing agent.
The highest power densities were obtained under a cathode pressure of 3 atm and at 90°C, with the exception of PtRu/CARM, which exhibited a distinct behavior. As shown in Figure 7, PtRu/CARM reached its peak power output of 13.86 mW cm−2 at 80°C, in contrast to the other electrocatalysts tested, which achieved their best performance at 90°C. This result suggests that PtRu/CARM has a different sensitivity to temperature, possibly due to its specific structure or composition, which limits its efficiency at higher temperatures.
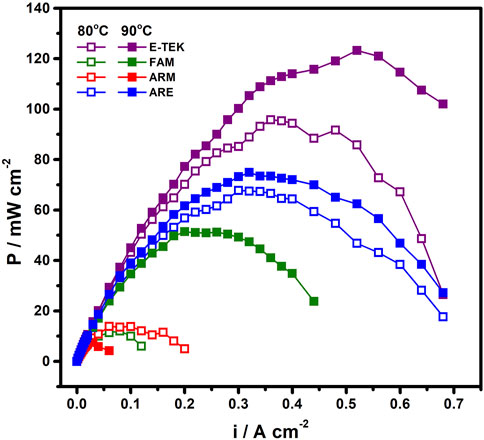
Figure 7. Power curves (P vs. i) at 80°C and 90°C for the PtRu/CFAM, PtRu/CARM, PtRu/CARE, and PtRu/CE-TEK catalysts. Operating condition: 3 atm pressure at the cathode.
The PtRu/CFAM, PtRu/CARE, and PtRu/CE-TEK electrocatalysts exhibited more typical behaviors, with significantly higher maximum power outputs at 90°C: 51.22 mW cm−2 for PtRu/CFAM, 74.88 mW cm−2 for PtRu/CARE, and 123.24 mW.cm-2 for PtRu/CE-TEK. Although these values highlight the superiority of PtRu/CE-TEK, it is not possible to fully compare this catalyst with the others, as the synthesis route for this electrocatalyst is not specified, making it difficult to establish a fair comparison that accounts for the preparation method. Nonetheless, this catalyst appears to be more efficient in maximizing electrochemical reactions, allowing for higher current densities and, consequently, greater power generation.
On the other hand, PtRu/CARE demonstrated a more consistent performance across different operating parameters, standing out particularly under the more severe conditions of high pressure and temperature. These data confirm that PtRu/CARE, from the initial results in both XRD analyses and electrochemical tests, exhibited an optimized structure that enhances its performance, especially at high current densities and under conditions of high pressure and temperature.
In Figure 8, the polarization curves corresponding to the test evaluating the combined effects of oxygen pressure at the cathode and operating temperature on the performance of the PtRu/CARE catalyst are presented. In Figure 7A, under 1 atm pressure conditions, a moderate effect of temperature on cell performance is observed. At low current densities, there is a small increase in potential with increasing temperature, suggesting an improvement in catalytic activity with heating. However, this difference is not very significant, indicating that under lower oxygen pressure (1 atm), temperature does not have a substantial impact on the overall electrochemical behavior of the cell.
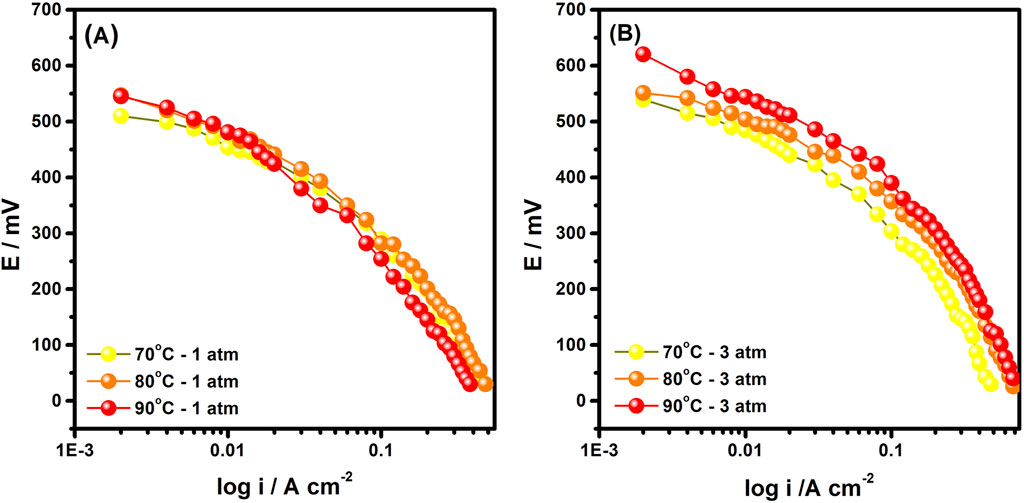
Figure 8. Polarization curves (E vs. i) for the PtRu/CARE catalyst at temperatures of 70, 80, and 90°C with varying oxygen feed pressure at the cathode: (A) 1 atm and (B) 3 atm.
In contrast, at high current densities, a slight increase in the Tafel coefficient is observed at 90°C, which may be associated with structural changes and dynamics in the gas diffusion electrode at the cathode. This behavior indicates a greater resistive effect at the cathode, likely due to higher methanol concentration, resulting in methanol crossover to the cathode. This phenomenon contributes to additional resistance, reducing the overall efficiency of the fuel cell (Velázquez-Palenzuela et al., 2011; Sahin and Kivrak, 2013; Wang et al., 2021).
In Figure 8B, under 3 atm pressure, the influence of temperature becomes more evident. As the temperature increases, both the performance at low current densities and at high current densities improve more significantly. This suggests that the combination of high oxygen pressure and elevated temperature enhances reaction kinetics, facilitating the transport of reactants and oxygen diffusion in the cathode electrode. In this case, the crossover effect seems to be mitigated by the higher pressure, reducing the impact of methanol presence at the cathode, allowing the cell to operate more efficiently.
The difference in behavior between 1 atm and 3 atm pressure reflects the importance of controlling operating conditions, such as pressure and temperature, to maximize the performance of electrocatalysts. Higher pressure facilitates oxygen diffusion, compensating for the adverse effects of crossover and minimizing the limitations imposed by ohmic resistance. This shows that to optimize the performance of fuel cells based on PtRu/C, it is essential to adjust oxygen pressure in conjunction with operating temperature.
In summary, when comparing all these results, it is clear that the performance of the catalysts is strongly influenced by the synthesis method and operating conditions, such as pressure and temperature. The increase in oxygen pressure at the cathode plays a crucial role in improving the efficiency of the oxygen reduction reaction (ORR), as it promotes greater availability of reactants at the catalytic site. However, it is important to note that as pressure and temperature increase, the methanol crossover effect also intensifies, as observed mainly in the FAM and ARM electrocatalysts. This phenomenon tends to increase internal resistance losses in the cell, limiting performance, as was observed with the drop in power at high current densities.
4 Conclusion
The synthesis methods analyzed proved to be simple and efficient for obtaining carbon-supported catalysts with high surface area. Among the tested catalysts, PtRu/CARE, prepared by the alcohol reduction method using ethylene glycol as a reducing agent, exhibited the best electrochemical performance, standing out particularly under more severe operating conditions, such as temperature of 90°C and 3 atm oxygen pressure at the cathode. This superior performance was observed in comparison to the PtRu/CARM and PtRu/CFAM catalysts, prepared by the methanol and formic acid reduction methods, respectively, whose performances were more limited, especially at high current densities and under higher pressure conditions.
Additionally, it was observed that operating conditions of temperature and pressure had a significant impact on the behavior of the catalysts. PtRu/CARE proved to be particularly efficient under high pressure and temperature, outperforming the commercial PtRu/CE-TEK under conditions close to 80°C and 1 atm. However, operating at 90°C with 3 atm pressure at the cathode resulted in the maximum power density for PtRu/CARE, although the methanol crossover effect caused resistive losses at the cathode, highlighting the need for further optimization in gas diffusion materials and membranes to minimize this effect.
Thus, it is concluded that PtRu/CARE stands out as a promising candidate for applications in direct methanol fuel cells (DMFCs), particularly under optimized operating conditions. However, mitigating the crossover effect and improving the efficiency of gas diffusion materials remain important challenges for maximizing the system’s performance and durability under real operating conditions.
Data availability statement
The original contributions presented in the study are included in the article/supplementary material, further inquiries can be directed to the corresponding author.
Author contributions
ES: Conceptualization, Investigation, Methodology, Writing–original draft. RS: Conceptualization, Data curation, Formal Analysis, Writing–original draft. DG: Supervision, Validation, Visualization, Writing–review and editing. LP: Formal Analysis, Resources, Supervision, Visualization, Writing–review and editing. RP: Conceptualization, Data curation, Formal Analysis, Funding acquisition, Methodology, Project administration, Resources, Supervision, Validation, Visualization, Writing–original draft, Writing–review and editing.
Funding
The author(s) declare that financial support was received for the research, authorship, and/or publication of this article. The authors thank CNPq (Grants #553988/2006-2, #554613/2010–7, and #456336/2013-3), FAPEAM (Grants #062.01163/2019-PAMEQ/2019, and #01.02.016301.03391/2021-90-EDITAL N. 010/2021-CT & I PRIORITY AREAS). This study was financed in part by the Coordination for the Improvement of Higher Education Personnel—Brazil (CAPES)—Finance Code 001.
Acknowledgments
The authors also thank Prof. Auro Tanaka for providing access to the potentiostat at the Electrochemistry Laboratory, Federal University of Maranhão (UFMA), São Luís/MA.
Conflict of interest
The authors declare that the research was conducted in the absence of any commercial or financial relationships that could be construed as a potential conflict of interest.
Generative AI statement
The author(s) declare that no Generative AI was used in the creation of this manuscript.
Publisher’s note
All claims expressed in this article are solely those of the authors and do not necessarily represent those of their affiliated organizations, or those of the publisher, the editors and the reviewers. Any product that may be evaluated in this article, or claim that may be made by its manufacturer, is not guaranteed or endorsed by the publisher.
References
Ahmed, A. A., Al Labadidi, M., Hamada, A. T., and Orhan, M. F. (2022). Design and utilization of a direct methanol fuel cell. Membr. (Basel) 12, 1266. doi:10.3390/membranes12121266
Antolini, E., Colmati, F., and Gonzalez, E. R. (2007). Effect of Ru addition on the structural characteristics and the electrochemical activity for ethanol oxidation of carbon supported Pt-Sn alloy catalysts. Electrochem. Commun. 9, 398–404. doi:10.1016/j.elecom.2006.10.012
Aricò, A. S., Cretì, P., Kim, H., Mantegna, R., Giordano, N., and Antonucci, V. (1996). Analysis of the electrochemical characteristics of a direct methanol fuel cell based on a Pt-Ru/C anode catalyst. J. Electrochem. Soc. 143, 3950–3959. doi:10.1149/1.1837321
Chen, L., Liang, X., Wang, D., Yang, Z., He, C. T., Zhao, W., et al. (2022). Platinum-ruthenium single atom alloy as a bifunctional electrocatalyst toward methanol and hydrogen oxidation reactions. ACS Appl. Mat. Interfaces 14, 27814–27822. doi:10.1021/acsami.2c02905
de Araujo, V. M. F., Antolini, E., Pocrifka, L. A., and Passos, R. R. (2018). Electro-oxidation of glycerol on carbon supported Pt75CoxNi25-x (x = 0, 0.9, 12.5, 24.1 and 25) catalysts in an alkaline medium. Electrocatalysis 9, 673–681. doi:10.1007/s12678-018-0475-1
dos Santos, L., Colmati, F., and Gonzalez, E. R. (2006). Preparation and characterization of supported Pt-Ru catalysts with a high Ru content. J. Power Sources 159, 869–877. doi:10.1016/j.jpowsour.2005.12.086
Ferreira Frota, E., Silva de Barros, V. V., de Araújo, B. R. S., Gonzaga Purgatto, Â., and Linares, J. J. (2017). Pt/C containing different platinum loadings for use as electrocatalysts in alkaline PBI-based direct glycerol fuel cells. Int. J. Hydrogen Energy 42, 23095–23106. doi:10.1016/j.ijhydene.2017.07.125
Housmans, T. H. M., Wonders, A. H., and Koper, M. T. M. (2006). Structure sensitivity of methanol electrooxidation pathways on platinum: an on-line electrochemical mass spectrometry study. J. Phys. Chem. B 110, 10021–10031. doi:10.1021/jp055949s
Jarvi, T. D., Sriramulu, S., and Stuve, E. M. (1998). Reactivity and extent of poisoning during methanol electrooxidation on platinum (100) and (111): A comparative study. Colloids Surfaces A Physicoehemical Eng. Aspects 134, 145–153. doi:10.1016/S0927-7757(97)00313-0
Kakati, N., Maiti, J., Lee, S. H., Jee, S. H., Viswanathan, B., and Yoon, Y. S. (2014). Anode catalysts for direct methanol fuel cells in acidic media: do we have any alternative for Pt or Pt-Ru? Chem. Rev. 114, 12397–12429. doi:10.1021/cr400389f
Kang, D. K., Noh, C. S., Kim, N. H., Cho, S. H., Sohn, J. M., Kim, T. J., et al. (2010). Effect of transition metals (Ni, Sn and Mo) in Pt5Ru4M alloy ternary electrocatalyst on methanol electro-oxidation. J. Ind. Eng. Chem. 16, 385–389. doi:10.1016/j.jiec.2009.09.067
Liu, H., Zhao, J., and Li, X. (2022). Controlled synthesis of carbon‑supported Pt‑based electrocatalysts for proton exchange membrane fuel cells. Electrochem. Energy Rev. 5, 13. doi:10.1007/s41918-022-00173-3
Marinho, V. L., Antolini, E., Giz, M. J., Camara, G. A., Pocrifka, L. A., and Passos, R. R. (2021). Ethylene glycol oxidation on carbon supported binary PtM (M = Rh, Pd an Ni) electrocatalysts in alkaline media. J. Electroanal. Chem. 880, 114859. doi:10.1016/j.jelechem.2020.114859
Neto, A. O., Verjulio-Silva, R. W. R., Linardi, M., and Spinacé, E. V. (2009). Preparation of PtRu/C electrocatalysts using citric acid as reducing agent and OH- ions as stabilizing agent for direct alcohol fuel cell (DAFC). Int. J. Electrochem. Sci. 4 (7), 954–961. doi:10.1016/S1452-3981(23)15198-4
Paganin, V. A., Ticianelli, E. A., and Gonzalez, E. R. (1996). Development and electrochemical studies of gas diffusion electrodes for polymer electrolyte fuel cells. J. Appl. Electrochem. 26. doi:10.1007/BF00242099
Peng, K., Liu, L., Bhuvanendran, N., Lee, S. Y., Xu, Q., and Su, H. (2023). Efficient one-dimensional Pt-based nanostructures for methanol oxidation reaction: an overview. Int. J. Hydrogen Energy 48, 29497–29517. doi:10.1016/j.ijhydene.2023.04.119
Petrii, O. A. (2008). Pt-Ru electrocatalysts for fuel cells: a representative review. J. Solid State Electrochem. 12, 609–642. doi:10.1007/s10008-007-0500-4
Radmilović, V., Gasteiger, H. A., and Ross, P. N. (1995). Structure and chemical composition of a supported Pt-Ru Electrocatalyst for methanol oxidation. J. Catal. 154, 98–106. doi:10.1006/jcat.1995.1151
Sahin, O., and Kivrak, H. (2013). A comparative study of electrochemical methods on Pt-Ru DMFC anode catalysts: the effect of Ru addition. Int. J. Hydrogen Energy 38, 901–909. doi:10.1016/j.ijhydene.2012.10.066
Salgado, J. R. C., Paganin, V. A., Gonzalez, E. R., Montemor, M. F., Tacchini, I., Ansón, A., et al. (2013). Characterization and performance evaluation of Pt-Ru electrocatalysts supported on different carbon materials for direct methanol fuel cells. Int. J. Hydrogen Energy 38, 910–920. doi:10.1016/j.ijhydene.2012.10.079
Sarma, L. S., Lin, T. D., Tsai, Y. W., Chen, J. M., and Hwang, B. J. (2005). Carbon-supported Pt-Ru catalysts prepared by the Nafion stabilized alcohol-reduction method for application in direct methanol fuel cells. J. Power Sources 139, 44–54. doi:10.1016/j.jpowsour.2004.07.016
Shrivastava, U. N., Tajiri, K., and Chase, M. (2015). Current density and ohmic resistance distribution in the land-channel direction of a proton exchange membrane fuel cell. J. Power Sources 299, 189–194. doi:10.1016/j.jpowsour.2015.08.099
Spinacé, E. V., Neto, A. O., Vasconcelos, T. R. R., and Linardi, M. (2004). Electro-oxidation of ethanol using PtRu/C electrocatalysts prepared by alcohol-reduction process. J. Power Sources 137, 17–23. doi:10.1016/j.jpowsour.2004.05.030
Tian, H., Yu, Y., Wang, Q., Li, J., Rao, P., Li, R., et al. (2021). Recent advances in two-dimensional Pt based electrocatalysts for methanol oxidation reaction. Int. J. Hydrogen Energy 46, 31202–31215. doi:10.1016/j.ijhydene.2021.07.006
Trasatti, S., and Petrii, O. A. (1991). Real surface area measurements in electrochemistry. Int. Union Pure Appl. Chem. 63, 711–734. doi:10.1351/pac199163050711
Tremiliosi-Filho, G., Kim, H., Chrzanowski, W., Wieckowski, A., Grzybowska, B., and Kulesza, P. (1999). Reactivity and activation parameters in methanol oxidation on platinum single crystal electrodes 'decorated' by ruthenium adlayers. J. Electroanal. Chem. 467, 143–156. doi:10.1016/S0022-0728(99)00078-9
Velázquez-Palenzuela, A., Centellas, F., Garrido, J. A., Arias, C., Rodríguez, R. M., Brillas, E., et al. (2011). Kinetic analysis of carbon monoxide and methanol oxidation on high performance carbon-supported Pt-Ru electrocatalyst for direct methanol fuel cells. J. Power Sources 196, 3503–3512. doi:10.1016/j.jpowsour.2010.12.044
Wang, K., Zhou, T., He, J., Cao, Z., and Jiang, Z. (2024). Regulating the atomic ratio of Pt/Ru to enhance CO anti-poisoning of Pt based electrocatalysts toward methanol oxidation reaction. Mol. Catal. 556, 113927. doi:10.1016/j.mcat.2024.113927
Wang, Q., Zhou, Y. W., Jin, Z., Chen, C., Li, H., and Cai, W. B. (2021). Alternative aqueous phase synthesis of a ptru/c electrocatalyst for direct methanol fuel cells. Catalysts 11, 925. doi:10.3390/catal11080925
Xie, J., Zhang, Q., Gu, L., Xu, S., Wang, P., Liu, J., et al. (2016). Ruthenium-platinum core-shell nanocatalysts with substantially enhanced activity and durability towards methanol oxidation. Nano Energy 21, 247–257. doi:10.1016/j.nanoen.2016.01.013
Yaqoob, L., Noor, T., and Iqbal, N. (2021). Recent progress in development of efficient electrocatalyst for methanol oxidation reaction in direct methanol fuel cell. Int. J. Energy Res. 45, 6550–6583. doi:10.1002/er.6316
Keywords: direct methanol fuel cells, PtRu/C, ethylene glycol reduction, electrochemical oxidation, bimetallic catalysts, electrocatalyst synthesis
Citation: Souza EAD, Silva RN, Gonçalves DA, Pocrifka LA and Passos RR (2024) Comparative performance of PtRu/C catalysts synthesized by different methods for direct methanol fuel cells under various operating conditions. Front. Nanotechnol. 6:1515034. doi: 10.3389/fnano.2024.1515034
Received: 22 October 2024; Accepted: 29 November 2024;
Published: 12 December 2024.
Edited by:
Ramireddy Boppella, Colorado State University, United StatesReviewed by:
Balamurugan Mani, Seoul National University, Republic of KoreaVenkata Sai Sriram Mosali, University of South Carolina, United States
Copyright © 2024 Souza, Silva, Gonçalves, Pocrifka and Passos. This is an open-access article distributed under the terms of the Creative Commons Attribution License (CC BY). The use, distribution or reproduction in other forums is permitted, provided the original author(s) and the copyright owner(s) are credited and that the original publication in this journal is cited, in accordance with accepted academic practice. No use, distribution or reproduction is permitted which does not comply with these terms.
*Correspondence: Raimundo Ribeiro Passos, cnJwYXNzb3NAdWZhbS5lZHUuYnI=