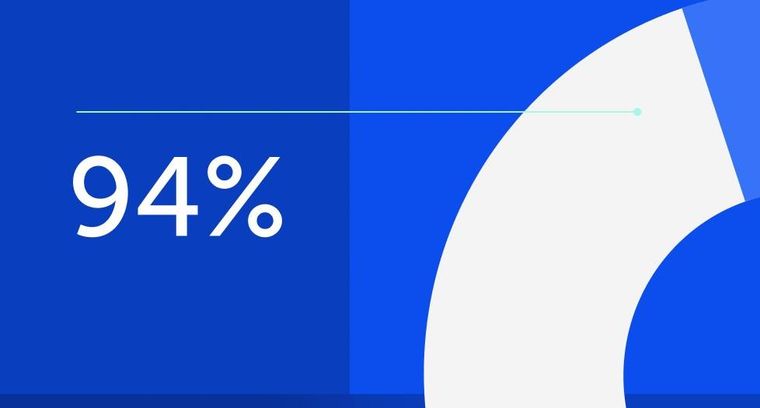
94% of researchers rate our articles as excellent or good
Learn more about the work of our research integrity team to safeguard the quality of each article we publish.
Find out more
ORIGINAL RESEARCH article
Front. Manuf. Technol., 31 October 2024
Sec. Material Forming and Removal
Volume 4 - 2024 | https://doi.org/10.3389/fmtec.2024.1410292
This article is part of the Research TopicExploring New Frontiers in Cryogenic MachiningView all articles
New supercritical carbon dioxide (
New cooling and lubrication methods for machining processes are under investigation to improve tool life and the quality of machined parts. These methods aim to reduce both friction and heating phenomena at chip/tool and tool/part contact zones. The application of supercritical
As an example, Supekar et al. (2012) used soybean oil dissolved in sc
These studies showed that sc
This work aims to investigate the influence of sc
Several components are selected to be paired with sc
Different types of components have been chosen based on previously numbered reasons. The components are described below and summarized in Table 1.
First, ionic liquids (ILs) have been reported by Sahab et al. (2017) to improve lubrication in reducing wear scar diameter (13%) during a tribological four-ball wear test. Davis et al. (2015) also noticed a better decrease of cutting forces when comparing IL-based MQL to water-based MQL during titanium machining. Their attractive properties, such as low melting point, negligible volatility, high thermal stability, and non-flammability, make them interesting lubricants for machining applications. Ionic liquids are soluble in sc
Another leverage of sustainability in machining assistance techniques is the use of vegetable-based oils. Commercial sunflower (S) and rapeseed (R) oils have been chosen because they are available, soluble in sc
Polyethylene glycol (PEG) from ThermoFisher (molecular weight: 200 g/mol) is also tested in this study. As reported by Goindi et al. (2018), it can be used as a lubricant although it is expected to decrease tool wear less than ionic liquids. The influence of dissolved droplets of water in sc
The lubricants selected in this study offer greater availability and are less health-threatening than traditional emulsions due to their biological composition. Pereira et al. (2016) have already highlighted the sustainability of cryo-MQL cooling methods over conventional flood coolants, considering environmental factors such as toxicity, power consumption, and ozone depletion.
However, the chosen lubricants here would not be suitable for machining applications where cleanliness is crucial, such as in the biomedical and agri-food industries.
A research-dedicated setup (Figure 1) was designed and manufactured to produce sc
The machine is fed in
A nozzle diameter of 0.25 mm was used for this study. The flow rate of sc
The pressure was limited to 100 bar, and the temperature was set to 40°C. This choice was made to guarantee a supercritical state and sufficient flow rate while minimizing
A pin-on-cylinder tribometer was used to reproduce the pressure at the chip/tool contact and chip sliding velocities. As illustrated in Figure 3, the tribometer screwed on a dynamometer (KISTLER 9121) was mounted on a SOMAB T500 lathe for the friction tests. A Hedenqvist-type tribometer (cylindrical pin on a cylindrical bar) was chosen for easy and quick execution (Hedenqvist and Olsson, 1991). The normal load
The
Only two sliding velocities of 20 m/min and 100 m/min (rotation of Ti6Al4V bar), based on a previous study by Courbon et al. (2020) on Ti6Al4V, were retained to reduce the number of experiments. These values cover the range of chip sliding velocities in machining difficult-to-cut alloys such as Ti6Al4V or Inconel718 (Courbon et al., 2013). Remember here that the main purpose is to investigate the comparative performance of the chosen mixtures (sc
For the normal load, a contact pressure of 1,300 MPa based on the experimental results of Outeiro et al. (2015) was used as the benchmark for a mechanical indentation FEM simulation to find corresponding tribological forces to use in the experiments, in association with chosen sliding velocities. Three values of forces, 100 N, 250 N, and 400 N, were selected and are presented in Table 1.
The recorded normal
All measured forces remained constant throughout each test (above 60 s), as well as the temperature, apart from the quick transition increase at the beginning of the friction. The average values of the apparent friction coefficient are computed for all the tested lubrication methods and compared in Figure 5.
Figure 5. Evolution of the friction coefficient for the two sliding speeds and lubricant flow rates.
The values for the apparent coefficient of friction reported here for dry tests at 100 m/min are higher than those obtained in tests with a spherical tip carbide (Courbon et al., 2020). For similar studies using the pin-on-cylinder tribological test at a 500 N load, the 0.25 value obtained by Courbon et al. (2020) is lower than those observed here with similar conditions of 400 N and 100 m/min. This could be due to our lower load conditions and the influence of the cylinder-on-cylinder contact (which has a larger surface area than spherical-tip-on-cylinder contact), potentially reducing the applied loads. As Courbon et al. (2020) cited from Meier et al. (2017), the friction coefficient is higher at lower loads. We assume these reasons could explain the differences between our results and their findings. Nevertheless, they reported no influence of the sliding speed on the coefficient of friction.
The main idea here is rather to check whether the selected lubricants can improve the contact when paired with sc
For the 20 m/min sliding tests, even if the addition of lubricants to sc
Nevertheless, a mean decrease of 0.1 in the apparent friction coefficient value was observed for the tests at 100 m/min. When increasing the lubricant flow rate from 1 mL/min to 4 mL/min, reductions of µ values occurred at 100 m/min. The lubricating effect of the used ionic liquids (PF6 and BF4), cited from previous literature (Section 2), could be depicted for the 100 m/min conditions with significant friction decreases at 4 m/min and 400 N. Even if it is well known that lower friction at higher speed could be due to material softening (Rech et al., 2013), the decrease of
It is also important to notice that “cheap” lubricants, such as water or rapeseed oils, were similar to commonly used machining mineral oil (MQL) when paired with sc
Ti6Al4V is known for adhesive behavior on the countermaterial in friction tests. The friction zone is then observed under an optical microscope after each test (meaning the application of all loads for the considered cooling conditions) to relate the area of sticking on the pin to the evolution of the apparent coefficient through all tests. Hedenqvist and Olsson (1991) used image post-processing to obtain the sticking area. Here, the observed zone is assimilated to an ellipse, and its area is calculated from the two measured half-axis. Though this method is less accurate than the one from Hedenqvist and Olsson (1991), it allows a comparison of the influence of the lubricating strategies on the sticking zone. This is summarized in Figure 6.
As seen for the apparent friction coefficient, no gain regarding friction was recorded at 20 m/min by adding the lubricants in sc
Examples of sticking patterns are presented in Figure 7 to show the effect of the ionic liquids paired with sc
The cooling abilities of sc
In this study, different lubricants (ionic liquids, vegetable and mineral oil, water, and PEG) were paired to sc
The original contributions presented in the study are included in the article/Supplementary Material; further inquiries can be directed to the corresponding author.
KK: writing–original draft, writing–review and editing, data curation, formal analysis, validation, and visualization. CB-D: data curation, formal analysis, investigation, methodology, validation, visualization, and writing–review and editing. HE-B: project administration, supervision, and writing–review and editing. FR: data curation, methodology, project administration, supervision, and writing–review and editing. GP: project administration, supervision, and writing–review and editing.
The author(s) declare that financial support was received for the research, authorship, and/or publication of this article. This study is part of the French research project
The authors declare that the research was conducted in the absence of any commercial or financial relationships that could be construed as a potential conflict of interest.
All claims expressed in this article are solely those of the authors and do not necessarily represent those of their affiliated organizations, or those of the publisher, the editors, and the reviewers. Any product that may be evaluated in this article, or claim that may be made by its manufacturer, is not guaranteed or endorsed by the publisher.
The Supplementary Material for this article can be found online at: https://www.frontiersin.org/articles/10.3389/fmtec.2024.1410292/full#supplementary-material
Bergs, T., Pušavec, F., Koch, M., Grguraš, D., Döbbeler, B., and Klocke, F. (2019). “Investigation of the solubility of liquid co2 and liquid oil to realize an internal single channel supply in milling of ti6al4v,” in Sustainable Manufacturing for Global Circular Economy: Proceedings of the 16th Global Conference on Sustainable Manufacturing, Lexington Kentucky, United States, October 2–4, 2018(Procedia Manufacturing), 33 200–207. doi:10.1016/j.promfg.2019.04.024
Cai, C., Liang, X., An, Q., Tao, Z., Ming, W., and Chen, M. (2021). Cooling/lubrication performance of dry and supercritical CO2-based minimum quantity lubrication in peripheral milling Ti-6Al-4V. Int. J. Precis. Eng. Manuf.-Green Tech. 8, 405–421. doi:10.1007/s40684-020-00194-7
Courbon, C., Pusavec, F., Dumont, F., Rech, J., and Kopac, J. (2013). Tribological behaviour of Ti6Al4V and Inconel718 under dry and cryogenic conditions—application to the context of machining with carbide tools. Tribol. Int. 66, 72–82. doi:10.1016/j.triboint.2013.04.010
Courbon, C., Sterle, L., Cici, M., and Pusavec, F. (2020). Tribological effect of lubricated liquid carbon dioxide on TiAl6V4 and AISI1045 under extreme contact conditions. Procedia Manuf. 47, 511–516. doi:10.1016/j.promfg.2020.04.139
Dang, J., Zhang, H., An, Q., Ming, W., and Chen, M. (2021). Surface modification of ultrahigh strength 300M steel under supercritical carbon dioxide (scCO2)-assisted grinding process. J. Manuf. Process. 61, 1–14. doi:10.1016/j.jmapro.2020.11.001
Davis, B., Schueller, J. K., and Huang, Y. (2015). Study of ionic liquid as effective additive for minimum quantity lubrication during titanium machining. Manuf. Lett. 5, 1–6. doi:10.1016/j.mfglet.2015.04.001
Fan, X., Wang, Y., Zhou, Y., Chen, J., Huang, Y., and Wang, J. (2018). Experimental study of supercritical co2 leakage behavior from pressurized vessels. Energy 150, 342–350. doi:10.1016/j.energy.2018.02.147
Goindi, G. S., Jayal, A. D., and Sarkar, P. (2018). Application of ionic liquids in interrupted minimum quantity lubrication machining of plain medium carbon steel: effects of ionic liquid properties and cutting conditions. J. Manuf. Process. 32, 357–371. doi:10.1016/j.jmapro.2018.03.007
Gross, D., Appis, M., and Hanenkamp, N. (2019). Investigation on the productivity of milling Ti6al4v with cryogenic minimum quantity lubrication. MM Sci. J. 2019, 3393–3398. doi:10.17973/mmsj.2019_11_2019098
Hedenqvist, P., and Olsson, M. (1991). Sliding wear testing of coated cutting tool materials. Tribol. Int. 24, 143–150. doi:10.1016/0301-679X(91)90020-A
Hyatt, J. A. (2002). Liquid and supercritical carbon dioxide as organic solvents. Archive Location: ACS Publications world Publisher: American Chemical Society. doi:10.1021/jo00200a016
Jiménez, A. E., and Bermúdez, M. D. (2010). Ionic liquids as lubricants of titanium–steel contact. Part 3. Ti6Al4V lubricated with imidazolium ionic liquids with different alkyl chain lengths. Tribol. Lett. 40, 237–246. doi:10.1007/s11249-010-9633-1
McHugh, M. A., and Krukonis, V. J. (1994) “Supercritical fluid extraction: principles and practice,” in Butterworth-Heinemann series in chemical engineering. 2nd edn. Boston: Butterworth-Heinemann.28708798
Meier, L., Schaal, N., and Wegener, K. (2017). In-process measurement of the coefficient of friction on titanium. 16th CIRP Conference on Modelling of Machining Operations (16th CIRP CMMO). Procedia CIRP 58, 163–168. doi:10.1016/j.procir.2017.03.212
Meier, T., Gross, D., and Hanenkamp, N. (2021). Investigation of lubricating oils from renewable resources for cryogenic minimum quantity lubricatio. mm Sci. J. 2021, 5069–5076. doi:10.17973/MMSJ.2021_11_2021154
Outeiro, J. C., Umbrello, D., M’Saoubi, R., and Jawahir, I. S. (2015). Evaluation of present numerical models for predicting metal cutting performance and residual stresses. Mach. Sci. Technol. 19, 183–216. Publisher: Taylor and Francis _eprint. doi:10.1080/10910344.2015.1018537
Pereira, O., Rodriguez, A., Fernandez-Abia, A., Barreiro, J., and Lopez de Lacalle, L. (2016). Cryogenic and minimum quantity lubrication for an eco-efficiency turning of aisi 304. J. Clean. Prod. 139, 440–449. doi:10.1016/j.jclepro.2016.08.030
Pušavec, F., Sterle, L., Kalin, M., Mallipeddi, D., and Krajnik, P. (2020). Tribology of solid-lubricated liquid carbon dioxide assisted machining. CIRP Ann. 69, 69–72. doi:10.1016/j.cirp.2020.04.033
Rahim, E., Rahim, A., Ibrahim, M., and Mohid, Z. (2016). Experimental investigation of supercritical carbon dioxide (SCCO2) performance as a sustainable cooling technique. Procedia CIRP 40, 637–641. doi:10.1016/j.procir.2016.01.147
Rech, J., Arrazola, P. J., Claudin, C., Courbon, C., Pusavec, F., and Kopac, J. (2013). Characterisation of friction and heat partition coefficients at the tool-work material interface in cutting. CIRP Ann. 62, 79–82. doi:10.1016/j.cirp.2013.03.099
Sahab, A. S. A. S., Rahim, E. A., and Samion, S. (2017). Tribological performance of modified jatropha oil containing oil-miscible ionic liquid for machining applications. J. Mech. Sci. Technol. 31, 5675–5685. doi:10.1007/s12206-017-1108-y
Supekar, S., Clarens, A., Stephenson, D., and Skerlos, S. (2012). Performance of supercritical carbon dioxide sprays as coolants and lubricants in representative metalworking operations. J. Mater. Process. Technol. 212, 2652–2658. doi:10.1016/j.jmatprotec.2012.07.020
Tapoglou, N., Taylor, C., and Christos, M. (2021). Milling of aerospace alloys using supercritical CO2 assisted machining. Procedia CIRP 101, 370–373. doi:10.1016/j.procir.2020.06.008
Watanabe, S., Takiwatari, K., Nakano, M., Miyake, K., Tsuboi, R., and Sasaki, S. (2013). Molecular behavior of room-temperature ionic liquids under lubricating condition. Tribol. Lett. 51, 227–234. doi:10.1007/s11249-013-0130-1
Wu, W., Zhang, J., Han, B., Chen, J., Liu, Z., Jiang, T., et al. (2003). Solubility of room-temperature ionic liquid in supercritical CO2 with and without organic compounds. Chem. Commun., 1412–1413. doi:10.1039/B302311G
Yu, W., Chen, J., Ming, W., An, Q., and Chen, M. (2022). Feasibility of supercritical CO2-based minimum quantity lubrication to improve the surface integrity of 50% Sip/Al composites. J. Manuf. Process. 73, 364–374. doi:10.1016/j.jmapro.2021.11.022
Yuan, Y., Wang, C., Yang, J., Zheng, L., and Weiqiang, X. (2018). Performance of supercritical carbon dioxide (scCO2) mixed with oil-on-water (OoW) cooling in high-speed milling of 316L stainless steel. Procedia CIRP 77, 391–396. doi:10.1016/j.procir.2018.08.301
Zhang, H., Dang, J., An, Q., Ming, W., Chen, M., and Zhang, J. (2021). Investigation of machinability in milling of Inconel 718 with solid Sialon ceramic tool using supercritical carbon dioxide (scCO2)-based cooling conditions. Ceram. Int. S0272884221034398 48, 4940–4952. doi:10.1016/j.ceramint.2021.11.032
Keywords: tribology, cryogenic cutting, supercritical CO2, ionic liquids, minimum quantity lubrication
Citation: Koulekpa KS, Benked-Dar C, Elias-Birembaux H, Rossi F and Poulachon G (2024) Investigating the efficiency of mixtures based on supercritical
Received: 31 March 2024; Accepted: 30 September 2024;
Published: 31 October 2024.
Edited by:
Vincent Wagner, École Nationale d’Ingénieurs de Tarbes, FranceReviewed by:
Tom Slatter, Loughborough University, United KingdomCopyright © 2024 Koulekpa, Benked-Dar, Elias-Birembaux, Rossi and Poulachon. This is an open-access article distributed under the terms of the Creative Commons Attribution License (CC BY). The use, distribution or reproduction in other forums is permitted, provided the original author(s) and the copyright owner(s) are credited and that the original publication in this journal is cited, in accordance with accepted academic practice. No use, distribution or reproduction is permitted which does not comply with these terms.
*Correspondence: Koffi Samuel Koulekpa, a29mZmkua291bGVrcGFAZW5zYW0uZXU=
Disclaimer: All claims expressed in this article are solely those of the authors and do not necessarily represent those of their affiliated organizations, or those of the publisher, the editors and the reviewers. Any product that may be evaluated in this article or claim that may be made by its manufacturer is not guaranteed or endorsed by the publisher.
Research integrity at Frontiers
Learn more about the work of our research integrity team to safeguard the quality of each article we publish.