- Laboratory for Manufacturing Systems and Automation, Department of Mechanical Engineering and Aeronautics, University of Patras, Rio Patras, Greece
Digital Twins, as a technological pillar of Industry 4.0, correspond to the virtual representation and bi-fold a real-time communication of a digital counterpart of a process or a physical object. As the industrial and manufacturing landscape is shifting towards Industry 5.0, huge investments focusing on enhancing interactions between Operators and Cyber-Physical Systems (CPS) occur. Yet, Metaverse strengthens these interactions as it enables human immersion into a virtual world. Furthermore, it examines the very promising relationships between the CPS, through the digital twins of these CPS. Therefore, this short review presents the concept of the Digital Twin inception in Industrial Metaverse. Additionally, a service-oriented digital twin architecture with Metaverse-enabled platforms for added value creation and interactions with CPS towards achieving Industry 5.0 challenges and beyond is proposed.
1 Introduction
Over the past few decades, digital manufacturing has significantly benefited the entire industry with considerable values (Mourtzis, 2022a). Digital manufacturing creates models and simulates the development of products and processes by virtually simulating factories, resources, labor forces, and their skills, among others (Chryssolouris et al., 2009). The development of manufacturing has been significantly aided by the advancement of Information and Communication Technologies (ICTs). Computer-aided technologies, such as Computer Aided Design (CAD), Computer Aided Engineering (CAE), Computer Aided Manufacturing (CAM), Finite Element Analysis (FEA) among others. Furthermore, technological pillars of Industry 4.0 such as Big Data, Internet of Things (IoT), Artificial Intelligence (AI), Cloud Computing, Edge Computing, fifth-generation cellular networks (5G), Wireless Sensor Networks (WSN) are rapidly developed and show great potential in most of the societal and industrial aspects (Chen et al., 2018; Wang et al., 2018; Mourtzis et al., 2021a; Liu et al., 2021). The integration of the physical and digital worlds is made possible by all these technologies, which is a inevitable trend to meet the high market demands and growing complexity (Mourtzis et al., 2019). However, the full strategic potential of this integration is not fully realized. The integration process still needs a lot of work, and the most recent developments are focused on digital twins. Based on the abovementioned, the majority of smart industries have partnered with 3D content developers (e.g., Unity) (Unity Technologies, 2023) to create roadmaps for the creation of new metaverse platforms. Such platforms would turn smart factories into virtual metafactories, allowing them to test cases in the metaverse. Although the digital twin technology has received a lot of attention as an emerging paradigm lately, significant problems still need to be solved. Such challenges include the integration of digital twins with metaverse-supported frameworks, the use of digital clones in smart industries, and virtual interactions with digital clones (Jagatheesaperunal et al., 2022). This short review discusses the current state of digital twin technology in relation to cyber-physical systems (CPS) with metaverse for industry 5.0 and beyond.
2 Digital twins
Smart manufacturing is a strategic priority shared by all major manufacturing initiatives, such as Industry 4.0 and the Industrial Internet of Things (Kusiak, 2018). Sensors and data transmission technologies are increasingly being used to collect data at various stages of the lifecycle of a product, such as design, manufacturing, distribution, maintenance, and recycling. Big data analytics can fully utilize data to identify failure causes, streamline a supply chain, optimize product performance, and increase production efficiency (Grieves and Vicker, 2017). The concept of the digital twin (DT) extends the concept of conventional simulation by supporting the creation of virtual representations of physical systems, including processes, and enabling real-time communication between the digital and physical entities. However, the role of simulation in this process needs to be better developed, particularly in relation to the behavior of physical objects and humans in simulated environments (Tao and Qi, 2019; Zacharewicz et al., 2020). This is an important aspect of defining DT for services and the corresponding methodology which facilitates the implementation of CPS (Zacharewicz et al., 2020). Thus, one of the crucial challenges of smart manufacturing is to connect the physical and virtual spaces. Greater interactions between the physical and virtual spaces have resulted from the quick development of simulation (Mourtzis, 2020), data acquisition, data communication, and other advanced technologies (Qi and Tao, 2018; Tao et al., 2019). The value of Digital Twins (DT), which is characterized by the CPS-based integration, is emphasized both by academia and industry (Tao et al., 2019; Mourtzis et al., 2020; Stavropoulos and Mourtzis, 2022). A huge volume of data that can be processed by advanced analytics is produced by the ability of DT to integrate the physical and virtual data throughout the lifecycle of a product. The insights derived, can be then applied to improve the performance of the physical counterpart (product or process) (Li and Tao, 2018). Industry 5.0 can achieve a significant technological advancement by connecting the physical and digital worlds. In fact, digital twin technology significantly contributes to this convergence. Additionally, such technology enables international industries to create digital replicas of their operations, goods, and assets to improve performance and maintenance. The following basic characteristics are integrated into the digital twin technology: a) Connectivity (Wu et al., 2021), b) Homogenization (Khan et al., 2022), c) Digital Traces (Susila et al., 2020), d) Re-programmability (Parmar et al., 2020), and e) Modularity (Rasheed et al., 2020). As technology develops and converges, submerging us in new virtual worlds, the industry is at an inflection point. For example, the authors in have focused on the servitization aspect of digital twins and have also proposed a conceptual strategy for the development of digital twin solutions for services. The authors suggest that service-based digital twin architectures/strategies can benefit service industries by improving service quality, reducing costs, and enhancing customer satisfaction. However, the importance of collaboration and the existence of communication channels between stakeholders in the development of such architectures is imperative. Huge investments are taking place as more businesses invest to the vast realm of emerging opportunities. Subsequently, financial and research efforts are increasingly being put on the improvement of the interaction between humans and CPS, with a focus on the development process for digital twins for the integration of human entities (Zacharewicz et al., 2020; Kuo et al., 2021). For example, Facebook changed its name to Meta and pledged $10 billion to the development of metaverse technology. Activision Blizzard, a producer of well-known multiplayer online games, has been acquired by Microsoft in a record-breaking US$69 billion deal (KPMG, 2022). There is no doubt that many businesses will find opportunities for change as the metaverse continues to develop.
3 How does metaverse work?
The concept of Metaverse, so far, has proven to be very beneficial towards the co-existence of the physical world and the digital/virtual world through the integration of digital twins. However, its distinctive definition remains in its infancy (Mystakidis S., 2022). A large percentage of Metaverse is still unbuilt and consequently there is little agreement on the principles of operation. As per the MIT Platform Strategy Summit (2022) three possible scenarios for metaverse are outlined:
• Large competing ecosystems that have limited interoperability, (e.g., Apple and Android) dominate the metaverse.
• Similar to the internet but in three dimensions, the metaverse is a dynamic, open, and interoperable ecosystem.
• Consumers continue to use the metaverse for entertainment and gaming purposes, but it still falls far short of becoming a fully immersive virtual reality.
The technological pillars or Metaverse Transformers that will power Metaverse are illustrated in Figure 1. More specifically, the following seven technologies will have the biggest impact on metaverse development over the next decade: 1) Artificial Intelligence, 2) Internet of Things (IoT), 3) Extended Reality (XR), 4) Spatial and edge computing, 5) Blockchain, 6) Brain-computer Interfaces, 7) 3D modelling and reconstruction (Hackl et al., 2022).
4 Applications of digital twins and metaverse in smart manufacturing
Some key indicative applications of digital twin and Metaverse in Smart Manufacturing are summarized as follows:
• Manufacturing and Automotive industry: Digital twins can be used by manufacturers to duplicate physical processes. By analyzing the trace of the digital twin, the interaction between virtual and physical objects is improved and contributes towards addressing errors or problems in the physical process. Automotive industries create digital twins of their vehicles to demonstrate how actual vehicles work. They can investigate new features using digital twins in order to improve the model performance of the actual vehicle (Bhatti et al., 2021; Renault Group, 2022)
• Logistics and supply chain: Companies can virtualize packages using digital twins before they are actually packaged, which reduces packaging errors and allows for more accurate material feasibility analysis, workable logistics networks, and dependable warehouse layouts (Yu et al., 2022). The end-to-end supply chain network may be mapped with the aid of the metaverse, which would improve visibility of all supply chain stages. This can provide more precise, current information on a) Product Lead Times, b) Logistic Costs, and c) Delays and deliveries (Maersk, 2022)
• Urban planning: Experts can use DTs and Metaverse to model data for urban cities and plan smart cities. By integrating the developed project with its corresponding digital replica, this can further improve the digitization of related tasks such as urban project operation, maintenance, and construction, leading to optimal performance (Allam et al., 2022; Wang M. et al., 2022b).
• Healthcare: Using digital twins of patients or organs to practice crucial procedures (instead of actual patients) allows health professionals to create personalized models that will improve patient care (Mourtzis et al., 2021b). Additionally, the development, prototyping, evaluation, regulation, translation, and improvement of AI-based medical practice, particularly medical imaging-guided diagnosis and therapy, can be facilitated by a metaverse of “medical technology and AI (MeTAI)” (Wang G. et al., 2022a). Consequently, the healthcare field has made significant strides towards the creation of digital twins of both patients and medical devices, and thus it is important to improve the definition of DT in this context (Erol T. et al., 2020).
• Transactions: Blockchain technology contributes to intelligent manufacturing with the following three ways: a) the protection of data validity, b) the organization of communication between and within organizations, and c) the efficiency enhancement of manufacturing processes. Additionally, as Society 5.0, also known as a super intelligent societal model, and the industrial metaverse become the new reality in manufacturing, the need for greater cybersecurity is highlighted. Modern, secure information technology like blockchain fosters commercial and industrial innovation (Mourtzis et al., 2023)
5 Cyber physical systems for personalized value creation in industrial metaverse
Understanding the characteristics of the industrial landscape as emerging components for Industry 5.0 depends on the use of cutting-edge and industry-standard CPS architecture. Additionally, a service-oriented digital twin architecture with Metaverse-enabled platforms can create added value and facilitate interactions with CPS, supporting the move towards Industry 5.0 (Souad R. et al., 2022). On the contrary, the primary drawback of traditional CPS architectures is that it does not consider vertical and horizontal diversification with human, physical, and cyber components.
• 3C architecture: The 3C CPS architecture integrates computation, communication, and control as key elements to help meet the goals of smart industries. These 3C CPS components are crucial for integrating human, physical, and cyber components in smart industries (Kayan et al., 2022).
• 5C architecture: The 5C CPS architecture consists of levels for smart connection, conversion, cyber, cognition, and configuration. In the production environment, it combines the sensors and actuators. Cognitive modules and higher levels of automation support intelligent decision-making. (Mourtzis et al., 2022b). Few of the key protocols implemented in 5C CPS Architectures are listed as follows: Profibus/Profinet. Open Platform Communication -Unified Architecture (OPC-UA) Fieldbus, Ethernet Powerlink. For more details, please see Table 1.
• (Process Field Net) International (PI) and OPC Foundation are playing the key functioning role in an integrated manner since long time.
• Self-Adaptiveness: The self-adaptive CPS can function in dynamic and uncertain environments. This group of architectures deploys adaptation logic, which picks up information from the environment as it runs and adjusts to deal with adverse circumstances and uncertainties (Mourtzis D., 2022b; Petrovska et al., 2022).
• Fog computing: Compared to traditional cloud servers, fog gateways can process more samples successfully under high load, enabling quick evaluation. Predictive models can be integrated with intelligent machinery using industrial CPS based on the fog computing paradigm (Wang and Zao, 2022).
• Reference Architecture Model: The reference architecture model of Industry 4.0 (RAMI 4.0) was commissioned with the standardization of the International Electrotechnical Commission to adapt with earlier standards and to mature information and communication sharing strategies in smart industries. Additionally, it permits interoperability between various technologies that link business processes with suppliers and clients (Zhang, 2022).
• Industrial Internet Reference Architecture: The adoption of the Industrial Internet Reference Architecture (IIRA) is essential when looking at industrial process automation from the computing, control, and networking perspectives. The cascaded model of the reference architecture, in particular, starts the robust and trustworthy integration of IIoT and CPS (Mourtzis et al., 2022a).
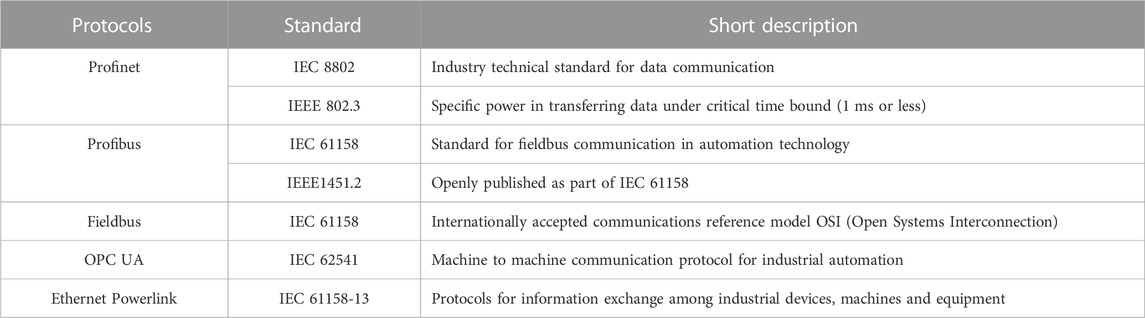
TABLE 1. Protocols and standards in CPS in industry 4.0 (Ahmadi et al., 2019).
The year 2020 marked a turning point in the development of spatial computing. Software platforms can be thought of as the foundational technology for creating and running application programs (Valaskova et al., 2022). To the best of our knowledge a limited number of publications have been published in the field of software platforms for Metaverse. Indicatively, the five layers of the Extended Reality (XR) software platforms for Metaverse are discussed by Mourtzis et al. (2022a). These layers are as follows: 1) Enabling platforms, 2) Content platforms, 3) Human-centered platforms, 4) Utility platforms, and 5) Platforms for Applications. Similarly, a framework of Metaverse as mediating design space between high value-added case studies and technology trends in society and business is discussed by Rehm et al. (2015). Additionally, the Metaverse is considered as an embodied version of the Internet that combines shardless, immersive, and interoperable virtual ecosystems that can be explored by user-controlled avatars. A detailed review outlining the layers of the Metaverse architecture is presented by Lim et al. (2022).
6 Discussion and outlook
6.1 Challenges for digital twins and metaverse implementation for industry 5.0 and beyond
Even though DTs have gained significant attention by both, academia and industry, the concurrent challenges especially in its integration with frameworks that support the metaverse are listed below (Anderson and Rainie, 2022):
• Limited immersive virtual interactions with digital clones and remote access for monitoring and control of the CPS.
• Difficult estimation techniques regarding the deficiencies of the DTs
• Accessibility constraints via Extended Reality (XR) apps and Internet of Everything (IoE) devices.
• Concerns raised about the evaluation of the feedback from the digital copies of industrial machinery and equipment, especially for the workforce focused on other priorities and tasks.
• Privacy and security issues as CPS will be also deployed in the Industry 5.0 landscape.
• Progress and research on open governance, interoperability and standardization issues is still in its infancy
In the following list, the main identified challenges of Metaverse Implementation are summarized as follows (Smaili et al., 2022).
6.1.1 Identity management
Ongoing Web 2.0 applications struggle to verify ID as the products and services in the Metaverse more frequently.
6.1.2 Security, safety, and privacy (SSP)
As connectivity between people and technology increases and more data is generated, concerns about privacy, safety, and security increase as well. This will accelerate the expansion of Metaverse to a rate comparable to the physical Universe.
6.1.3 Finance in metaverse
Using cryptocurrencies is challenging. Doing so in the Metaverse will make an already unreliable payment system even more difficult.
6.1.4 Laws, regulations, and protections
Metaverse users and their intellectual property as well, have to be protected within the virtual environment. As such newly discovered business like Non-Fungible Tokens (NFTs) will have to be integrated to the virtual ecosystem.
6.1.5 Living in metaverse causes emotional and mental impact
Mental problems caused by continuous social media usage and gaming will spread to the Metaverse on a large scale. This could provoke mental health issues in real world and create a blurred border between the real and the virtual world.
6.1.6 Standardization of the metaverse
By the time every stakeholder wants to establish the “standard” and dominate the market, this is one of the most difficult stages in the early lifecycle of any new technology. Interoperability will be a crucial aspect of the design and execution of the Metaverse because standards will apply to all procedures, protocols, hardware, and software.
6.1.7 Interoperability in the metaverse
Interoperability requires standards for the following four components:
o Identity for connecting individuals to assets and rights
o 3D rendering for visualization purposes
o Behaviors for object characterization
o Data Sharing for sharing ownership and permissions
Based on the abovementioned identified solutions and challenges, and even though the DT technology has received a lot of attention as an emerging paradigm lately, significant problems still need to be solved. Among these difficulties are the integration of digital twins with frameworks that support the metaverse, the use of digital clones in smart industries, and virtual interactions with digital clones. As such, a framework for Metaverse as a Service (MaaS) for service-oriented DTs towards Industry 5.0 is proposed in Figure 2.
6.2 How will metaverse impact the future
The current vision of metaverse is considered as a novel digital realm, a shared interactive and immersive AR that combines key technologies such as VR, AI, Cloud and Blockchain in virtual ecosystems. The metaverse concept was popularized during the pandemic and is seen as a good solution to the connectivity problem. The metaverse may offer a variety of tools to help with routine work tasks, socializing, and even shopping, all within a realistic virtual environment linked to the blockchain. The rapid development of XR and the creation of more sophisticated and immersive 3D online worlds, is likely to have positive effects on all facets of society, including education, healthcare, gaming and entertainment, the arts, social life, and other pursuits. However, as per all new digital technologies, there are concerns about the implications of these new spaces for health, safety, security, privacy, and the economy. This has led to a lot of speculation regarding how XR and the metaverse will develop and what that will entail for society. In research conducted by Pew Research Center and Elon University’s Imagining the Internet Center interviewed a large pool of technology experts to share their insights on the impact of metaverse for society. The results of the survey indicated the following (Anderson, J. and Rainie, L., 2022):
• By 2040, according to 54% of these experts, the metaverse will be a much more developed, fully immersive, and functional aspect of daily life for at least a half billion people worldwide. Of course, there are worries about the implications of these new spaces for health, safety, security, privacy, and the economy, just as there are with all digital technology. This has led to a lot of speculation regarding how XR and the metaverse will develop and what that will entail for society.
• By 2040, 46% of respondents predicted that the metaverse will not be a much more developed, fully immersive, and functional component of daily life for at least a half billion people worldwide.
Based on the abovementioned survey, the following challenges are pending to be addressed:
• How will the behavior be shared in Metaverse?
• How do companies be profitable while opening and maintaining opportunities for all stakeholders?
• How will engineers govern the technical differences between several enterprises in the metaverse?
It has to be stressed out that whatever shape the metaverse takes, cybersecurity and privacy regulations pose serious problems. There are many risks for businesses and users due to the current lack of privacy regulations for the metaverse, including the following: a) Misapplication and applicability of current privacy regulations, such as General Data Protection Regulation (GDPR), b) Extensive and intrusive data gathering, c) Issues related to data ownership and rights, and d) User-to-user privacy.
7 Conclusion
The key feature of the Industrial Metaverse system is that it improves the real-time interaction with physical objects, improves visualization in the configuration layer of the CPS, and is regarded as a digital twin of the workspace. The workforce groups and remote industrial managers who use the CPS models should have access to metaverse-enabled solutions. As a result, Industry 5.0 operations and beyond will increasingly rely on the metaverse to plan their operations, manufacturing, assembly, supply chain, marketing, and other relationships with stakeholders. Metaverse is not about escaping the physical world but is about embracing and augmenting it with virtual experiences that can lead to enhanced connectivity among the users, improved productivity in work and the creation of new knowledge derived from the insights produced by the autonomous digital agents that will be able to cooperate and create new knowledge without human intervention. However, this difficult challenge can be achieved with semantic communication and edge computing. There disruptive solutions can be used to address emerging requirements of big data sets, bandwidth efficiency and low latency data processing in Metaverse. With the proposed Metaverse as a Service model for service-oriented DTs towards Industry 5.0, this review aims to enhance communication, education, research, and control. Furthermore, it enables smart industries to implement cutting-edge changes in digital clones for the creation of new products and adopt cutting-edge marketing techniques for their goods. As it regards future research directions, by 2030 brain computer interfaces (BCIs), which allow for the tracking, recording, and sharing of human thought, are predicted to become commonplace. We might actually be able to experience memories and moments from other peoples’ lives thanks to XR technology. Meanwhile, it is possible that artificial data derived from simulated environments will direct robots in problem-solving and the replacement of humans in hazardous jobs. Cui et al., 2022.
Author contributions
DM Conceptualization, Writing, Literature Investigation.
Conflict of interest
The author declares that the research was conducted in the absence of any commercial or financial relationships that could be construed as a potential conflict of interest.
Publisher’s note
All claims expressed in this article are solely those of the authors and do not necessarily represent those of their affiliated organizations, or those of the publisher, the editors and the reviewers. Any product that may be evaluated in this article, or claim that may be made by its manufacturer, is not guaranteed or endorsed by the publisher.
References
Ahmadi, A., Sodhro, A. H., Cherifi, C., Cheutet, V., and Ouzrout, Y. (2019). “Evolution of 3C cyber-physical systems architecture for industry 4.0,” in Service orientation in holonic and multi-agent manufacturing: Proceedings of SOHOMA 2018 (Singapore: Springer International Publishing), 448–459.
Allam, Z., Sharifi, A., Bibri, S. E., Jones, D. S., and Krogstie, J. (2022). The metaverse as a virtual form of smart cities: Opportunities and challenges for environmental, economic, and social sustainability in urban futures. Smart Cities 5 (3), 771–801. doi:10.3390/smartcities5030040
Anderson, J., and Rainie, L. (2022). The metaverse in 2040. Washington, United States: Pew Research Centre.
Bhatti, G., Mohan, H., and Singh, R. R. (2021). Towards the future of smart electric vehicles: Digital twin technology. Renew. Sustain. Energy Rev. 141, 110801. doi:10.1016/j.rser.2021.110801
Boucher, N., and Renault Group, (2022). Vehicle digital twin: When physical and digital models unite. Last accessed on 26/01/2023 Available at: https://www.renaultgroup.com/en/news-on-air/news/vehicle-digital-twin-when-physical-and-digital-models-unite/.
Chen, B., Wan, J., Celesti, A., Li, D., Abbas, H., and Zhang, Q. (2018). Edge computing in IoT-based manufacturing. IEEE Commun. Mag. 56 (9), 103–109. doi:10.1109/mcom.2018.1701231
Chryssolouris, G., Mavrikios, D., Papakostas, N., Mourtzis, D., Michalos, G., and Georgoulias, K. (2009). Digital manufacturing: History, perspectives, and outlook. Proc. Institution Mech. Eng. Part B J. Eng. Manuf. 223 (5), 451–462. doi:10.1243/09544054jem1241
Cui, Y., Idota, H., and Ota, M. (2022). “Reforming supply chain systems in metaverse,” in Proceedings of the 9th Multidisciplinary International Social Networks Conference, Matsuyama, Japan, October 2022, 39–43.
Erol, T., Mendi, A. F., and Doğan, D. (2020). “The digital twin revolution in healthcare,” in 2020 4th International Symposium on Multidisciplinary Studies and Innovative Technologies (ISMSIT), Istanbul, Turkey, October 2020, 1–7.
Grieves, M., and Vickers, J. (2017). “Digital twin: Mitigating unpredictable, undesirable emergent behavior in complex systems,” in Transdisciplinary perspectives on complex systems: New findings and approaches (Singapore: Springer), 85–113.
Hackl, C., Lueth, D., and Di Bartolo, T. (2022). Navigating the metaverse: A guide to limitless possibilities in a Web 3.0 world. New Jersey, United States: John Wiley & Sons.
Jagatheesaperumal, S. K., and Rahouti, M. (2022). Building digital twins of cyber physical systems with metaverse for industry 5.0 and beyond. IT Prof. 24 (6), 34–40. doi:10.1109/mitp.2022.3225064
Kayan, H., Nunes, M., Rana, O., Burnap, P., and Perera, C. (2022). Cybersecurity of industrial cyber-physical systems: A review. ACM Comput. Surv. (CSUR) 54 (11), 1–35. doi:10.1145/3510410
Khan, L. U., Saad, W., Niyato, D., Han, Z., and Hong, C. S. (2022). Digital-twin-enabled 6G: Vision, architectural trends, and future directions. IEEE Commun. Mag. 60 (1), 74–80. doi:10.1109/mcom.001.21143
Kpmg, (2022). The future of the metaverse and Extended Reality. Last accessed on: 30/01/2023. Available online at: https://kpmg.com/xx/en/home/insights/2022/04/the-future-of-the-metaverse.html.
Kuo, Y. H., Pilati, F., Qu, T., and Huang, G. Q. (2021). Digital twin-enabled smart industrial systems: Recent developments and future perspectives. Int. J. Comput. Integr. Manuf. 34 (7-8), 685–689. doi:10.1080/0951192x.2021.1959710
Kusiak, A. (2018). Smart manufacturing. Int. J. Prod. Res. 56 (1-2), 508–517. doi:10.1080/00207543.2017.1351644
Lim, W. Y. B., Xiong, Z., Niyato, D., Cao, X., Miao, C., Sun, S., et al. (2022). Realizing the metaverse with edge intelligence: A match made in heaven. IEEE Wirel. Commun, 1–9. doi:10.1109/mwc.018.2100716
Liu, M., Fang, S., Dong, H., and Xu, C. (2021). Review of digital twin about concepts, technologies, and industrial applications. J. Manuf. Syst. 58, 346–361. doi:10.1016/j.jmsy.2020.06.017
Maersk, (2022). 3 ways the metaverse will transform your supply chain. Last accessed on 27/01/2023 Available online at: https://www.maersk.com/insights/digitalisation/how-the-metaverse-will-transform-supply-chain-management.
Mourtzis, D. (2022a). Design and operation of production networks for mass personalization in the era of cloud technology. Amsterdam, Netherlands: Elsevier, 1–393. Book.
Mourtzis, D. (2022b). Advances in adaptive scheduling in industry 4.0. Front. Manuf. Technol. Sec. Softw. Technol. 2. doi:10.3389/fmtec.2022.937889
Mourtzis, D., Angelopoulos, J., and Panopoulos, N. (2023). Blockchain integration in the era of industrial metaverse. Appl. Sci. 13 (3), 1353. doi:10.3390/app13031353
Mourtzis, D., Angelopoulos, J., and Panopoulos, N. (2022a). “Digital Manufacturing: The evolution of traditional manufacturing toward an automated and interoperable Smart Manufacturing Ecosystem,” in The digital supply chain (Amsterdam, Netherlands: Elsevier), 27–45.
Mourtzis, D., Angelopoulos, J., and Panopoulos, N. (2020). Intelligent predictive maintenance and remote monitoring framework for industrial equipment based on mixed reality. Front. Mech. Eng. 6, 578379. doi:10.3389/fmech.2020.578379
Mourtzis, D., Angelopoulos, J., Panopoulos, N., and Kardamakis, D. (2021b). A smart IoT platform for oncology patient diagnosis based on ai: Towards the human digital twin. Procedia CIRP 104, 1686–1691. doi:10.1016/j.procir.2021.11.284
Mourtzis, D., Angelopoulos, J., and Panopoulos, N. (2021a). Smart manufacturing and tactile internet based on 5G in industry 4.0: Challenges, applications and new trends. Electronics 10 (24), 3175. doi:10.3390/electronics10243175
Mourtzis, D., Fotia, S., Boli, N., and Vlachou, E. (2019). Modelling and quantification of industry 4.0 manufacturing complexity based on information theory: A robotics case study. Int. J. Prod. Res. 57 (22), 6908–6921. doi:10.1080/00207543.2019.1571686
Mourtzis, D., Panopoulos, N., and Angelopoulos, J. (2022b). “Production management guided by industrial internet of things and adaptive scheduling in smart factories,” in Design and operation of production networks for mass personalization in the era of cloud technology (Amsterdam, Netherlands: Elsevier), 117–152.
Mourtzis, D. (2020). Simulation in the design and operation of manufacturing systems: State of the art and new trends. Int. J. Prod. Res. 58 (7), 1927–1949. doi:10.1080/00207543.2019.1636321
Parmar, R., Leiponen, A., and Thomas, L. D. (2020). Building an organizational digital twin. Bus. Horizons 63 (6), 725–736. doi:10.1016/j.bushor.2020.08.001
Petrovska, A., Kugele, S., Hutzelmann, T., Beffart, T., Bergemann, S., and Pretschner, A. (2022). Defining adaptivity and logical architecture for engineering (smart) self-adaptive cyber–physical systems. Inf. Softw. Technol. 147, 106866. doi:10.1016/j.infsof.2022.106866
Qi, Q., and Tao, F. (2018). Digital twin and big data towards smart manufacturing and industry 4.0: 360 degree comparison. Ieee Access 6, 3585–3593. doi:10.1109/access.2018.2793265
Rasheed, A., San, O., and Kvamsdal, T. (2020). Digital twin: Values, challenges and enablers from a modeling perspective. Ieee Access 8, 21980–22012. doi:10.1109/access.2020.2970143
Rehm, S. V., Goel, L., and Crespi, M. (2015). The metaverse as mediator between technology, trends, and the digital transformation of society and business. J. Virtual Worlds Res. 8 (2). doi:10.4101/jvwr.v8i2.7149
Smaili, N., and de Rancourt-Raymond, A. (2022). Metaverse: Welcome to the new fraud marketplace. J. Financial Crime. ahead-of-print. doi:10.1108/jfc-06-2022-0124
Souad, R., Zacharewicz, G., and Chapurlat, V. (2022). “Digital twin for services (DT4S): Conceptual strategy,” in 10th IFAC Conference on Manufacturing Modelling, Management and Control (MIM) 2022, Nantes, France, Jun 2022, 3256–3261. IMT Atlantique.
Stavropoulos, P., and Mourtzis, D. (2022). “Digital twins in industry 4.0,” in In Design and operation of production networks for mass personalization in the era of cloud technology (Amsterdam, Netherlands: Elsevier), 277–316.
Summit, (2022). MIT platform strayegy Summit. Last Accessed on 30/01/2023. Available online at: https://www.yumpu.com/en/document/view/67215236/mit-platform-report-2022.
Susila, N., Sruthi, A., and Usha, S. (2020). Impact of cloud security in digital twin. Adv. Comput. 117 (1), 247–263.
Tao, F., and Qi, Q. (2019). Make more digital twins. Nature 573 (7775), 490–491. doi:10.1038/d41586-019-02849-1
Tao, F., Qi, Q., Wang, L., and Nee, A. Y. C. (2019). Digital twins and cyber–physical systems toward smart manufacturing and industry 4.0: Correlation and comparison. Engineering 5 (4), 653–661. doi:10.1016/j.eng.2019.01.014
Tao, F., Zhang, H., Liu, A., and Nee, A. Y. (2018). Digital twin in industry: State-of-the-art. IEEE Trans. industrial Inf. 15 (4), 2405–2415. doi:10.1109/tii.2018.2873186
Valaskova, K., Vochozka, M., and Lăzăroiu, G. (2022). Immersive 3D technologies, spatial computing and visual perception algorithms, and event modeling and forecasting tools on blockchain-based metaverse platforms. Analysis Metaphys. 21, 74–90.
Wang, G., Badal, A., Jia, X., Maltz, J. S., Mueller, K., Myers, K. J., et al. (2022a). Development of metaverse for intelligent healthcare. Nat. Mach. Intell. 4, 922–929. doi:10.1038/s42256-022-00549-6
Wang, J., Ma, Y., Zhang, L., Gao, R. X., and Wu, D. (2018). Deep learning for smart manufacturing: Methods and applications. J. Manuf. Syst. 48, 144–156. doi:10.1016/j.jmsy.2018.01.003
Wang, W., Guo, H., Li, X., Tang, S., Li, Y., Xie, L., et al. (2022b). BIM information integration based VR modeling in digital twins in industry 5.0. J. Industrial Inf. Integration 28, 100351. doi:10.1016/j.jii.2022.100351
Wang, Y., and Zhao, J. (2022). Mobile edge computing, metaverse, 6G wireless communications, artificial intelligence, and blockchain: Survey and their convergence. arXiv preprint arXiv:2209.14147 Available at: https://arxiv.org/abs/2209.14147.
Wu, Y., Zhang, K., and Zhang, Y. (2021). Digital twin networks: A survey. IEEE Internet Things J. 8 (18), 13789–13804. doi:10.1109/jiot.2021.3079510
Unity Technologies (2023). Unity-Unity. [online] Unity. Available at: https://unity.com/.
Zacharewicz, G., Daclin, N., Doumeingts, G., and Haidar, H. (2020). Model driven interoperability for system engineering. Modelling 1, 94–121. doi:10.3390/modelling1020007
Keywords: digital twin, metaverse, industry 4.0, industry 5.0, cyber-physical systems
Citation: Mourtzis D (2023) Digital twin inception in the Era of industrial metaverse. Front. Manuf. Technol. 3:1155735. doi: 10.3389/fmtec.2023.1155735
Received: 07 February 2023; Accepted: 03 April 2023;
Published: 12 April 2023.
Edited by:
Jiewu Leng, Guangdong University of Technology, ChinaReviewed by:
Greg Zacharewicz, Mines-Telecom Institute Alès, FranceCopyright © 2023 Mourtzis. This is an open-access article distributed under the terms of the Creative Commons Attribution License (CC BY). The use, distribution or reproduction in other forums is permitted, provided the original author(s) and the copyright owner(s) are credited and that the original publication in this journal is cited, in accordance with accepted academic practice. No use, distribution or reproduction is permitted which does not comply with these terms.
*Correspondence: Dimitris Mourtzis, bW91cnR6aXNAbG1zLm1lY2gudXBhdHJhcy5ncg==