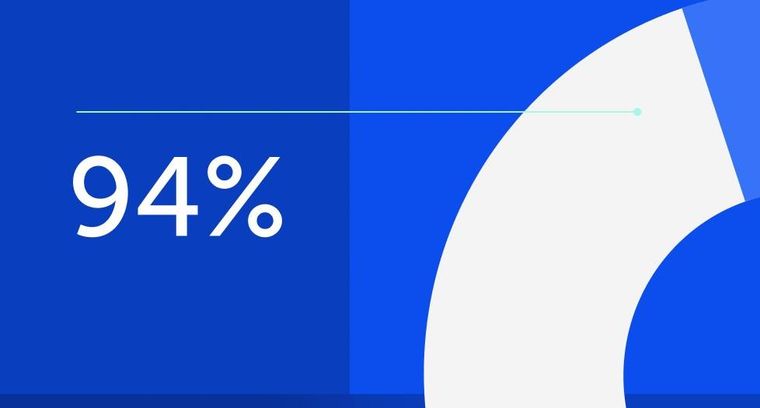
94% of researchers rate our articles as excellent or good
Learn more about the work of our research integrity team to safeguard the quality of each article we publish.
Find out more
BRIEF RESEARCH REPORT article
Front. Manuf. Technol., 09 May 2023
Sec. Sustainable Life Cycle Engineering and Manufacturing
Volume 3 - 2023 | https://doi.org/10.3389/fmtec.2023.1009633
The digital twin (DT) concept plays a crucial role in Industry 4.0 and the digitalization of manufacturing processes. A DT is a virtual representation of a physical object, system, or process, designed to accurately reflect its real-world counterpart. In manufacturing, existing process data are often incomplete and do not qualify as a DT. However, with the help of specialized communication frameworks and cheaper, easier-to-use sensors, it is possible to integrate the existing manufacturing execution system (MES) and enterprise resource planning (ERP) data with the missing data gathered from the shop floor to create a comprehensive DT. In this paper, we present a digital shop floor decision support system (DSS) for non-linear aluminum manufacturing production. The system is split into five main components: digitization of shop floor orders; merging and sorting of MES, ERP, and shop floor data; custom and genetic optimization algorithms for the aging furnace production step; layout construction mechanism for optimal placement and stacking of orders in the furnace; and a user-friendly graphical user interface (GUI). The system’s performance was evaluated through three tests. The first test measured the efficiency of digitization, the second aimed to quantify time saved in finding packets in the hall, and the last test measured the impact of the optimizer on furnace productivity. The results revealed a 23.5% improvement in furnace capacity, but limitations were identified due to usability and human intervention.
The current industrial production faces the challenge of manufacturing products “just in time,” with the number of production steps and complexity constantly increasing (Lennon Olsen and Tomlin, 2019; Habib et al., 2022). Depending on the product and the production method, many production steps can be arranged in an arbitrary sequence or in a predefined sequence combination. Customer requirements, the limitations of production sites, and the increasing number of products in circulation are complicating the tasks of operators. For the selected use case at Constellium, the aging furnaces represent a bottleneck in production, making it crucial to optimize or increase its capacity.
This paper aims to demonstrate the creation of a digital twin (DT) for existing products and processes, incorporating manufacturing requirements from the manufacturing execution system (MES) and enterprise resource planning (ERP) system and optimizing a specific production step through simulations. The decision support system (DSS) is dynamic, meaning it provides suggestions that the operator can evaluate and adapt on a case-by-case basis (Zhang et al., 2022).
Digitalization has been identified as the main growth vector for the future of industries worldwide (Marr, 2016). This led to the term “Industry 4.0” being coined (Lasi et al., 2014), and it quickly gained widespread popularity (Columbus, 2018). Separately, physical duplicates have long been used to drive complex systems. In the late 1960s, NASA’s Apollo program extensively used them for training and also during the Apollo 13 mission’s dramatic accident and return to Earth (David et al., 2018). Dr. Grieves first presented the two notions together, expanded the concept, and coined the term “digital twin” (Grieves, 2011; Grieves, 2016).
Because it is a relatively new and highly dynamic field, the current definition of DT is still evolving (Negri et al., 2017; Aheleroff et al., 2021). However, some key characteristics are undisputed:
1. There exists a physical system (PS) and its digital counterpart (Shafto et al., 2010; Glaessgen and Stargel, 2012)
2. There exists a level of granularity in the DT representation adequate with the application (Boschert and Rosen, 2016; Schleich et al., 2017; Matthews, 2018)
3. There exists a bidirectional (Brenner and Hummel, 2017; Deloitte, 2018; Madni et al., 2019) real-time association (Uhlemann et al., 2017; Guivarch et al., 2019; Stavropoulos and Papacharalampopoulos, 2022) between the PS and its DT
4. This real-time association endures throughout the life cycle of the PS (Tuegel, 2012; Tao et al., 2018; Stavropoulos, 2022)
5. Multiple source sensors and operation data allow the DT to constantly reflect the state of the PS, as best as possible (“The Mirroring”) (Cai et al., 2017; Haag and Anderl, 2018; Trauer et al., 2021)
6. Most importantly, the DT must include an intelligent agent able to further understand and learn from the DT’s past and present states. This agent is also able to reason, simulate, and predict future states of the PS based on the stimuli of potential controls and the physical environment of the system (Majumdar et al., 2013; Nikolakis et al., 2019). This aims toward autonomy and self-optimization of the system (Zhou et al., 2019)
7. Finally, the agent is able to feed optimal stimuli to the PS (Tao et al., 2018; Pickl et al., 2019; Zhou et al., 2019)
A DT is, therefore, valuable, not because it exists as a digital representation of the PS but owing to its existence as a whole: encompassing cyber-physical systems, data, and most importantly, its intelligent agent. As a result, DT has now been identified as a top disruptive trend (Pettey, 2017) that represents the largest opportunity for digitalization driving Industry 4.0 (Gartner, 2022).
To bring a generic and reusable DT onto the shop floor, multiple different problems need to be solved together. First, an appropriate use case was evaluated and found within Constellium, a major aluminum manufacturer for extruded aluminum products.
Aluminum extrusion components are essential in day-to-day life. They are used in planes, trains, cars, and many more applications. They help reduce the environmental impact of transportation and many other applications due to the fact that aluminum is a light, machinable but still strong and long-lasting material. In total, there are about 23 steps in the production process of aluminum extruded elements. In addition, aluminum has the unique ability of being indefinitely recyclable.
The aging furnace production step was identified as critical and has significant potential for optimization. To modify the physical characteristics of the aluminum profiles, we should artificially age the metal using a so-called aging furnace. The products stay inside these furnaces between 5 and 24 h. This is the reason why there is a multitude of furnaces on the shop floor. Smaller orders with a higher frequency cannot be combined and placed within these furnaces efficiently. Bottlenecks can, therefore, arise easily at this production step. Figure 1A shows the active furnaces for the year 2018, including the downtimes in between. The two big breaks around September at furnaces 67 and 49 were identified as furnace maintenance. The smaller gaps are weekends, and the even smaller breaks are unloading/loading operations as well as downtime. The data from 2018 were taken and used to calculate optimum planning. The loading and unloading operations were estimated to last 30 min. If the furnaces were used in a quasi-optimal setting, the full workload for 2018 could have been completed by September (Figure 1B). Another identified problem is the communication between work shifts.
FIGURE 1. Optimization possibilities of different aging furnaces. (A) Unoptimized and (B) optimized.
To resolve the mentioned problems, the DSS is split into three major components. Each contributes its part in creating a dynamic production planning. First, the products on the shop floor must be digitized and tracked in real-time. Second, the database created must be enhanced with additional metadata from the ERP and MES systems. Third, the optimizer can use this DT to run simulations to create the quasi-optimal product combination and furnace filling at a given time.
To provide information about the packets on the shop floor that are ready to be baked as well as their location, a pan-tilt-zoom (PTZ) camera, as well as Lidar, were used. Overhead cranes were equipped with multiple sensors facing the shop floor. Since the overhead cranes are used to transport all the products, they are constantly in use and perform a back-and-forth scan motion. The selected overhead crane covers an area of 3,780 m2 at a height of 7.15 m. Using this approach, the whole area was covered with only four scanners instead of 88, which were theoretically necessary.
The Lidar scanners were placed at a distance of 3.1 m from each other. This ensured that no product could cast a shadow onto another product without being covered by the next scanner. The scanner placement must be analyzed and adapted in each application case. It depends not only on the product to be digitized but also on the field of view (FoV) of the used scanners.
The x location of the scanners is known, and the y-axis (direction of the crane movement) can be read from the overhead crane system itself. The products to be digitized can be represented as boxes.
The data from all the scanners are merged, and a point cloud of the shop floor beneath is created. A noise filter algorithm runs in three steps: cutting out the envelope of the noise, filtering outliers, and, lastly, discriminating the points that are part of the ground from other points. For outlier smoothing, a custom algorithm based on a statistical approach is used.
Once the point cloud has been cleaned, a layer smoothing algorithm is used to further remove noise in the different z-axis layers. This algorithm is based on a statistical approach similar to the outlier smoothing algorithm. With the help of the aforementioned algorithms, ground plane and top product planes could be located.
The object detection is then performed in three additional steps: detecting planes with the random sample consensus (RANSAC) method, converting the point cloud to a 2D grayscale image for finally performing a bounding box algorithm. The resulting data are stored as a JavaScript Object Notation (JSON) object containing all x–y–z locations of the packets within the sensor area.
Since the overhead cranes perform a sweeping motion over the shop floor and the FoV of the sensors is limited to a small area, the temporal information needs to be combined to create a complete shop floor product map. Once the packets are isolated, the end of the packets will be detected to deduce the start and end position of any packet. Due to the FoV problems of the scanners, up to four products, depending on their size, can be stacked on top of each other. The scanners do not recognize the subpackets, but only the top plane.
This leads to another temporal condition to localize packets: there can be multiple products at any given location on the store floor. With each scan of the crane, the map is analyzed for each detected package, and whether and with which probability one of the following operations has taken place is determined:
• None: no change
• Insert: a new product has been added or an existing product has been repositioned to another pile
• Stack: a product has been stacked on top of another one
• Remove: a product was removed
• Unstack: a product was removed from a stack
For each operation, there are one to four possible scenarios, depending on whether there is already none, one, or multiple packets on the shop floor. Using this algorithm, a map of the store floor is created, which is continuously updated in real-time.
Five containers, here the furnaces, of different capacity are available to perform the aging process of the aluminum products. Each furnace can be configured individually with a specific aging curve. These aging curves, defined in terms of temperatures and durations, which we call “recipes,” are preconfigured in the machine and can be selected by an operator at the beginning of the process. On the other side of the problem, we have a certain number of items, here the aluminum products, which need to be aged in the furnaces with a specific recipe. Finally, each item has a predefined delivery date that needs to be adhered to, and one product can be aged with more than one recipe.
An algorithm for the optimization of the furnace’s usage has been developed and is presented in this paper. The specific problem we try to address is the container loading problem. It consists of packing a set of rectangular objects into a larger rectangular container in such a way so as to optimize some criteria while satisfying a set of constraints. In our case, the goal is to optimize the filling of the furnaces in order to maximize their efficiency. A dedicated and personalized solution has been implemented by incorporating the specific loading constraints and mechanics applied by Constellium during this process. Figure 2 shows the quasi-optimal loading of all five furnaces during the production trial.
The realization of the algorithm starts by modeling the problem and integrating the aforementioned definition and constraints. The first phase of the development has focused on the implementation of a genetic algorithm (GA). Before being treated by the algorithm, each product gets converted into a rectangular box with the dimensional characteristics of the recommended U-shaped support for that product and its original length. A list representing the recipes the product can be aged with is constructed and assigned to this list. The operation of the algorithm is essentially to group items sharing similar recipes and start the filling of the furnaces with the items that have only one recipe in the largest group. The items that could not be placed are generally those with more than one recipe and, thus, can be used in a second pass to fill the furnaces with another recipe, starting with the largest group of that recipe. Items with more than one recipe have less priority and can be considered stopgap elements. As the total number of possible recipes for a product does not exceed 2, the groups are big enough to easily fill the furnaces. We can achieve a quasi-optimal solution in very few seconds compared to our experience with the GA, which takes longer and does not necessarily provide better results. The choice of using a greedy algorithm over GA is further justified by the fact that there are generally many items available from which the algorithm can pick to fill the remaining space. The last step of the algorithm, namely, the scheduling of the furnaces with their contents, is realized by a scheduler. This ensures the sequential use of the furnaces by considering the delivery date of each product and its availability.
The final solution is implemented as a Python program that reads the products from a database periodically and constructs optimized planning of the furnaces. Communication with the program is made possible through a Message Queuing Telemetry Transport (MQTT) interface. During each run, the program sends the planning in JSON format in a retained MQTT topic that could be read any time by an external program. For an easy understanding of the solution, a 3D visual representation of the furnace and its content is attached to the message. The user can interact with the application to validate the solutions proposed by the algorithm or to specify when a product should not be considered by the algorithm. The proposed furnaces that are not fully filled can be discarded by the operators and treated another day when more products are available. Finally, for the usability of the program, the required input parameters such as the type of recipes and the configuration of the furnaces have been made available to the user through configuration files.
The complete DSS consists of five different main components. Four Lidar sensors are installed on the overhead crane and connected to two edge devices via Ethernet. All point cloud analyses are performed on site using the Robotic Operating System software framework.
Three different subprograms run on the central server. First, an MQTT broker is used to ensure communication between the crane system and the user’s tablet; second, the actual digital twin of the shop floor map; third, the optimizer with its connection to the ERP system. Figure 3 shows a schematic overview of the architecture.
The operator receives the information and controls the system using an industrial tablet computer. This allows the operator to interact with the DSS in a harsh environment, even when wearing gloves, with the help of a stylus. One part of the DSS is the interactive map with all the products that can be viewed. With the help of the built-in camera in the tablet computer, the map can be modified by scanning the QR code on the products. Thus, the employees can adapt the map subsequently. The current production schedule is communicated to the employee via a timetable. Here, too, the employee can independently plan or prevent the planning of products with the help of the built-in optimizer functions. The optimization algorithm is started automatically if the map or product information changes.
The system’s performance was evaluated in three independent manners. The component “product digitization” was evaluated with the Lidar sensors and the overhead cranes. This aimed to measure the efficiency of the digitization. The second component was the optimizer, and it was evaluated with existing real and artificial data. The last component was to measure the performance of the complete system. Therefore, at the end of the project, the system was deployed and used during production for a 4-week trial period. During that period, it was closely monitored and evaluated. The results from the tests are shown in Section 3.1 and Section 3.2.
The first test aimed to measure the efficiency of digitization. To do this, the system started from an empty representation of the test area and then performed various measurement maneuvers. The test location was covered by the biggest overhead crane of Constellium, reaching 3,780 m2. The result of this first test highlighted the difficulties of having reliable Lidar data. However, the test was, nevertheless, considered a success: above 80% of the products on the observed shop floor section were correctly identified. This made it possible to detect problematic situations. Errors in the map were all resolved by operator actions and the add, remove, and modify functions provided by the application.
The second test quantified the time saved in finding unknown products in the hall. As a case study, four workers received a set of three customer orders to be found in the hall. The average search time to find products without the map system was 15 min. Using our system, the average time to find an order was reduced to an average of 1 min 28 s, resulting in a 90% reduction in the time required.
The goal of the trial period was to use the system to optimize the use of five furnaces in parallel. The entire production plan was created using the DSS. The operators were instructed that the created plan must be followed as closely as possible. In event of deviations, these were noted. The generated raw data were compared with historical data. There are several fluctuations that can affect the results, such as
• Quantity: if the number of products is not high enough, the planning cannot be improved
• Part size: if the size of the products is in such a way that furnaces cannot be combined, the optimization gain will be diminished
• Bake recipes: only parts with the same or similar recipes can be combined
• Use by operators: the operators must be trained to use the system; wrong usage can slow or diminish the optimization effects.
To reduce the impact of these factors, the following points are considered:
• Quantity: the selected trial period is historically considered to be neither a weak nor a strong month in terms of product quantity processed
• Parts size: the parts have maximal sizes, and they fit predefined containers; thus, the baking furnaces have been chosen to be fed with multiples of those containers
• Bake recipes: testing is carried out on five different furnaces, so parts can be dispatched between furnaces; they also have a wide heating range, which means that many different recipes are possible
• Use by operators: the chief operator has followed the project, advising on the use of the system; prior to the beginning of the tests, the operators were informed about using the system.
Four data features were evaluated and represented hereafter:
• Weight per hour: this represents the productivity of the furnace. The bigger the value, the better the productivity
• Produced weight: in close relation with the filling percentage, it represents the weight of the parts being baked; the bigger the value, the better the furnace performance.
Figure 4A shows the weight per hour in the furnaces for the 4-week trial as well as the average of the years 2014–2020. A total of 3 out of the 4 weeks were ranked the highest in terms of “weight per hour in a furnace” over the last 7 years’ production data. Figures 4B–F show the processed products in tons per month of all five furnaces. The red line represents the values during the test period. We performed a one-tailed paired t-test (α = 0.05) on ovens 45, 49, 65, 67, and 68. We obtained a p-value = 0.0021 for increased weight per hour in a furnace and a p-value = 0.0043 for produced weight. This shows a statistically significant improvement.
FIGURE 4. (A) Comparison of furnace performance from the trial period to the years 2014–2020. (B–F) Processed load of the five furnaces historically; the red line shows the value of the trial period.
During the 4-week test, the average weight per load increased from 34.5 tons to 42.6 tons, an increase of 23.5%. All furnaces surpassed the third quartile in terms of processed products in tons.
The resulting application was integrated into the Constellium Cyber–Physical Production System (CPPS) and supports the operators in furnace planning. The system adapts to the needs of the operators. They can either accept and implement, only partially implement, or ignore the suggestions. The dynamically generated production plan can be influenced by delay and selection functions for the optimizer and with add, remove, or modify functions for the shop floor map. The system is currently used for production planning. Figure 2 shows a graphical representation of the production planning for all five furnaces at a specific time during the trial period.
The project was a success since the importance and savings of the project were demonstrated during the trial phase. The furnace capacity was increased by 23.5% in a historical comparison. The DSS is still used after the end of the project for daily planning of the furnaces. The advantage of such a system is to combine the knowledge and decision-making ability of the employees with the foresight and speed of the simulation of the digital twin.
Nevertheless, some limitations of both subsystems (optimizer and digitization) have been identified. In its current version, the optimizer is limited to one of twenty-three production steps. The optimization factor can be increased as soon as more steps are considered. As an example, the products could already be optimally placed in the hall for the next production step.
The sensors used for product digitization are working at their specified limit; during the trial period, many packages were not detected or were detected in a different form. Some of these detection problems could be traced back to reflections and noise which can be observed on the sensors.
Finally, the tablets’ use and interface were criticized by the operators.
The feedback from the operators showed that having a reliable digital twin alone does not result in increased production or capacity. Specific algorithms and a proper user interface must be developed and implemented to solve clearly defined problems. In addition, the operators must be trained correctly so that they do not fall back into old habits and the digital twin can achieve its full effect. Although the tablet can be used with a stylus pen, it has limitations when operated with gloves. In addition, both hands are used, which does not leave a free hand for crane control. Fixed operator stations or a transportation system adapted to their needs could solve the problem.
The results from the operator feedback indicate that simply having a dependable digital twin does not lead to improved production or capacity. To fully utilize the potential of a digital twin, specific algorithms and a user-friendly interface must be designed and implemented to tackle well-defined issues. Moreover, operators must receive proper training to avoid reverting to previous practices and maximize the benefits of the digital twin. The current tablet, while it can be used with a stylus pen, has limitations when operated with gloves.
Future work on this project includes exploring opportunities to further improve the usability of the system, which should emphasize operator training as an important factor in maximizing the potential of a digital twin, as well as investigating ways to minimize human intervention. Additionally, research will be conducted to integrate predictive maintenance techniques into the DSS to improve furnace productivity and efficiency. The scalability and adaptability of the DT concept in manufacturing will also be evaluated to determine its potential for wider implementation in the industry.
The raw data supporting the conclusion of this article will be made available by the authors, without undue reservation.
SZ is the project leader; JC and FC are technology advisors; DP, GMa, LF, GMo, SD, and AA are scientific collaborators. All authors contributed to manuscript revision, read, and approved the submitted version.
Innosuisse is the Swiss Innovation Agency. Its role is to promote science-based innovation in the interest of the economy and society in Switzerland. Nowadays, the key to economic success is a combination of knowledge, research, and development. Innosuisse especially promotes the partnership between academia and the market with innovation projects, networking, training, and coaching, laying the foundation for successful Swiss start-ups as well as innovative products and services. It provides considerable benefits for a prosperous and sustainable economy. Innosuisse is a federal entity under public law with a separate legal personality. It provides support in accordance with the subsidiarity principle: it only supports projects if the innovation could not be implemented and market potential would not be tapped into without funding.
The authors declare that the research was conducted in the absence of any commercial or financial relationships that could be construed as a potential conflict of interest.
All claims expressed in this article are solely those of the authors and do not necessarily represent those of their affiliated organizations, or those of the publisher, the editors and the reviewers. Any product that may be evaluated in this article, or claim that may be made by its manufacturer, is not guaranteed or endorsed by the publisher.
Aheleroff, S., Xu, X., Ray, Z., and Lu, Y. (2021). Digital twin as a service (DTaaS) in industry 4.0: An architecture reference model. Adv. Eng. Inf. 47, 101225. doi:10.1016/j.aei.2020.101225
Boschert, S., and Rosen, R. (2016). “Digital twin—the simulation aspect,” in Mechatronic futures. Editors P. Hehenberger, and D. Bradley (Cham: Springer International Publishing), 59–74. doi:10.1007/978-3-319-32156-1_5
Brenner, B., and Hummel, V. (2017). Digital twin as enabler for an innovative digital shopfloor management system in the ESB logistics learning factory at reutlingen - university. Procedia Manuf. 9, 198–205. doi:10.1016/j.promfg.2017.04.039
Cai, Y., Starly, B., Cohen, P., and Lee, Y. S. (2017). Sensor data and information fusion to construct digital-twins virtual machine tools for cyber-physical manufacturing. Procedia Manuf. 10, 1031–1042. doi:10.1016/j.promfg.2017.07.094
Columbus, L. (2018). 2018 roundup of internet of things forecasts and market estimates forbes. Available at: https://www.forbes.com/sites/louiscolumbus/2018/12/13/2018-roundup-of-internet-of-things-forecasts-and-market-estimates/ (Accessed June 14, 2019).
David, J., Lobov, A., and Lanz, M. (2018). “Leveraging digital twins for assisted learning of flexible manufacturing systems,” in 2018 IEEE 16th International Conference on Industrial Informatics (INDIN), Porto, Portugal, 18-20 July 2018 (IEEE), 529–535. doi:10.1109/INDIN.2018.8472083
Deloitte (2018). Industry 4.0 and the digital twin. Available at: https://www2.deloitte.com/cn/en/pages/consumer-industrial-products/articles/industry-4-0-and-the-digital-twin.html (Accessed May 10, 2019).
Gartner (2022). Emerging technologies: Revenue opportunity projection of digital twins gartner. Available at: https://www.gartner.com/en/documents/4011590 (Accessed January 24, 2023).
Glaessgen, E., and Stargel, D. (2012). “The digital twin paradigm for future NASA and U.S. Air force vehicles,” in 53rd AIAA/ASME/ASCE/AHS/ASC structures, structural Dynamics and materials Conference<BR>20th AIAA/ASME/AHS adaptive structures Conference<BR>14th AIAA (Honolulu, Hawaii: American Institute of Aeronautics and Astronautics). doi:10.2514/6.2012-1818
Grieves, M. (2016). Origins of the digital twin concept. Cocoa Beach, Florida: Space Coast Press. doi:10.13140/rg.2.2.26367.61609
Grieves, M. (2011). Virtually perfect: Driving innovative and lean products through product lifecycle management. Cocoa Beach, Florida: Space Coast Press.
Guivarch, D., Mermoz, E., Marino, Y., and Sartor, M. (2019). Creation of helicopter dynamic systems digital twin using multibody simulations. CIRP Ann. 68, 133–136. doi:10.1016/j.cirp.2019.04.041
Haag, S., and Anderl, R. (2018). Digital twin – proof of concept. Manuf. Lett. 15, 64–66. doi:10.1016/j.mfglet.2018.02.006
Habib, F. E., Bnouachir, H., Chergui, M., and Ammoumou, A. (2022). “Industry 4.0 concepts and implementation challenges: Literature Review,” in 2022 9th International Conference on Wireless Networks and Mobile Communications (WINCOM), Rabat, Morocco, 26-29 October 2022 (IEEE), 1–6. doi:10.1109/WINCOM55661.2022.9966456
Lasi, H., Fettke, P., Kemper, H. G., Feld, T., and Hoffmann, M. (2014). Industrie 4.0. WIRTSCHAFTSINFORMATIK 56, 261–264. doi:10.1007/s11576-014-0424-4
Lennon Olsen, T., and Tomlin, B. (2019). Industry 4.0: Opportunities and challenges for operations management. SSRN Electron. J. 22(1), 113–122. doi:10.2139/ssrn.3365733
Madni, A., Madni, C., and Lucero, S. (2019). Leveraging digital twin technology in model-based systems engineering. Systems 7, 7. doi:10.3390/systems7010007
Majumdar, P. K., FaisalHaider, M., and Reifsnider, K. (2013). “Multi-physics response of structural composites and framework for modeling using material geometry,” in 54th AIAA/ASME/ASCE/AHS/ASC structures, structural dynamics, and materials conference (Boston, Massachusetts: American Institute of Aeronautics and Astronautics). doi:10.2514/6.2013-1577
Marr, B. (2016). Why everyone must get ready for the 4th industrial revolution forbes. Available at:https://www.forbes.com/sites/bernardmarr/2016/04/05/why-everyone-must-get-ready-for-4th-industrial-revolution/ (Accessed January 15, 2019).
Matthews, S. (2018). Designing better machines: The evolution of a cognitive digital twin explained internet things blog. Available at: https://www.ibm.com/blogs/internet-of-things/iot-evolution-of-a-cognitive-digital-twin/ (Accessed May 10, 2019).
Negri, E., Fumagalli, L., and Macchi, M. (2017). A review of the roles of digital twin in CPS-based production systems. Procedia Manuf. 11, 939–948. doi:10.1016/j.promfg.2017.07.198
Nikolakis, N., Alexopoulos, K., Xanthakis, E., and Chryssolouris, G. (2019). The digital twin implementation for linking the virtual representation of human-based production tasks to their physical counterpart in the factory-floor. Int. J. Comput. Integr. Manuf. 32, 1–12. doi:10.1080/0951192X.2018.1529430
Pettey, C. (2017). Prepare for the impact of digital twins. Available at: https://www.gartner.com/smarterwithgartner/prepare-for-the-impact-of-digital-twins/ (Accessed May 9, 2019).
Pickl, S. W., Tao, B., Liao, T. W., and Tao, F. (2019). Editorial for the special issue on “intelligent computing and system towards smart manufacturing. J. Ambient. Intell. Humaniz. Comput. 10, 825–827. doi:10.1007/s12652-018-1073-z
Schleich, B., Anwer, N., Mathieu, L., and Wartzack, S. (2017). Shaping the digital twin for design and production engineering. CIRP Ann. 66, 141–144. doi:10.1016/j.cirp.2017.04.040
Shafto, M., Conroy, M., Doyle, R., Glaessgen, E., Kemp, C., LeMoigne, J., et al. (2010). DRAFT modeling, simulation, information technology & processing roadmap. Available at: https://www.researchgate.net/publication/280310295_Modeling_Simulation_Information_Technology_and_Processing_Roadmap (Accessed May 10, 2019).
Stavropoulos, P. (2022). Digitization of manufacturing processes: From sensing to twining. Technologies 10, 98. doi:10.3390/technologies10050098
Stavropoulos, P., and Papacharalampopoulos, A. (2022). Designing a digital twin for micromanufacturing processes. Adv. Mech. Eng. 14, 168781322210960. doi:10.1177/16878132221096004
Tao, F., Cheng, J., Qi, Q., Zhang, M., Zhang, H., and Sui, F. (2018). Digital twin-driven product design, manufacturing and service with big data. Int. J. Adv. Manuf. Technol. 94, 3563–3576. doi:10.1007/s00170-017-0233-1
Trauer, J., Pfingstl, S., Finsterer, M., and Zimmermann, M. (2021). Improving production efficiency with a digital twin based on anomaly detection. Sustainability 13, 10155. doi:10.3390/su131810155
Tuegel, E. (2012). “The airframe digital twin: Some challenges to realization,” in 53rd AIAA/ASME/ASCE/AHS/ASC structures, structural Dynamics and materials Conference<BR>20th AIAA/ASME/AHS adaptive structures Conference<BR>14th AIAA (Honolulu, Hawaii: American Institute of Aeronautics and Astronautics). doi:10.2514/6.2012-1812
Uhlemann, T. H. J., Lehmann, C., and Steinhilper, R. (2017). The digital twin: Realizing the cyber-physical production system for industry 4.0. Procedia CIRP 61, 335–340. doi:10.1016/j.procir.2016.11.152
Zhang, J., Chen, J., Yao, D., Li, J., and Guo, S. (2022). Numerical investigation on the low-frequency vibroacoustic response of an aluminium extrusion compounded with acoustic metamaterials. Compos. Struct. 259, 1–17. doi:10.1016/j.compstruct.2020.113460
Keywords: 3D packaging, shop floor optimization, genetic algorithms, user-center design, real-time monitoring, real-time optimization, greedy algorithms
Citation: Zahno S, Corre J, Petrovic D, Mottiez G, Fracheboud L, Amand A, Devènes S, Maître G and Carrino F (2023) Dynamic project planning with digital twin. Front. Manuf. Technol. 3:1009633. doi: 10.3389/fmtec.2023.1009633
Received: 02 August 2022; Accepted: 20 April 2023;
Published: 09 May 2023.
Edited by:
Shaun West, Lucerne University of Applied Sciences and Arts, SwitzerlandReviewed by:
Simon Züst, Lucerne University of Applied Sciences and Arts, SwitzerlandCopyright © 2023 Zahno, Corre, Petrovic, Mottiez, Fracheboud, Amand, Devènes, Maître and Carrino. This is an open-access article distributed under the terms of the Creative Commons Attribution License (CC BY). The use, distribution or reproduction in other forums is permitted, provided the original author(s) and the copyright owner(s) are credited and that the original publication in this journal is cited, in accordance with accepted academic practice. No use, distribution or reproduction is permitted which does not comply with these terms.
*Correspondence: Silvan Zahno, c2lsdmFuLnphaG5vQGhldnMuY2g=
Disclaimer: All claims expressed in this article are solely those of the authors and do not necessarily represent those of their affiliated organizations, or those of the publisher, the editors and the reviewers. Any product that may be evaluated in this article or claim that may be made by its manufacturer is not guaranteed or endorsed by the publisher.
Research integrity at Frontiers
Learn more about the work of our research integrity team to safeguard the quality of each article we publish.