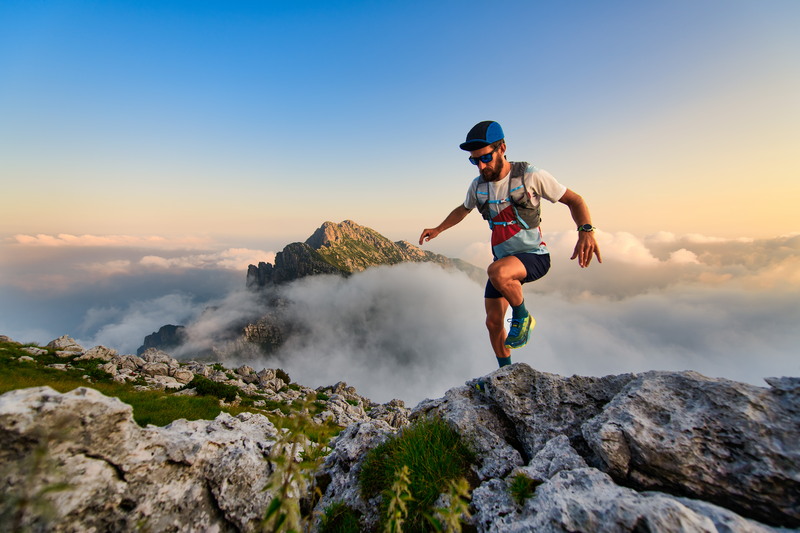
94% of researchers rate our articles as excellent or good
Learn more about the work of our research integrity team to safeguard the quality of each article we publish.
Find out more
ORIGINAL RESEARCH article
Front. Manuf. Technol. , 31 October 2022
Sec. Sustainable Life Cycle Engineering and Manufacturing
Volume 2 - 2022 | https://doi.org/10.3389/fmtec.2022.951643
This article is part of the Research Topic Digital Twins and Manufacturing in the era of Industry 4.0 and Industry 5.0 View all articles
There is a recognized need for mass personalization for sustainability at scale. Mass personalization is becoming a leading research trend in the latest Industrial Revolution, whereas substantial research has been undertaken on the role of Industry 4.0 enabling technologies. The world is moving beyond mass customization, while manufacturing has led to mass personalization ahead of other industries. However, most studies have not treated human capabilities, machines, and technologies as sustainable collaboration. This research investigates mass personalization as a common goal under the latest Industrial revolutions. Also, it proposes a Reference Architecture Model for achieving mass personalization that contributes to understanding how Industry 5.0 enhances Industry 4.0 for higher resilience and sustainability through a human-centric approach. The study implies that Human Capital 5.0 leads collaboration with machines and technologies, bringing more value-added and sustainable products.
Personalization makes customers feel more valued through memorable experiences. Individuals are increasing the demand for affordable, personalized products to meet their expectations. Some companies have adopted mass personalization as a competitive advantage in fulfilling individuals’ needs and supporting environmental milestones (Boër et al., 2018). Many disruptive technologies are undergoing rapid development under Industry 4.0 (Zheng et al., 2018) while often replacing humans with technology in the value lifecycle; therefore, a direction modification is arising under Industry 5.0.
Industry 5.0 is based on the observation or the assumption that Industry 4.0 focuses less on the original principles of social fairness and sustainability but more on digitalization and enabling technologies for increasing the efficiency and flexibility of production (Xu et al., 2021). However, the world of mass personalization and advanced manufacturing is experiencing a rapid transformation to a human-centric approach by actively involving customers in the co-creation process (Zheng et al., 2019). Using the workforce alongside technologies and machines makes mass personalization more feasible, motivating humans to work for more valuable products.
A strong motivation to increase productivity while not removing the workforce imposes challenges worldwide (Chin 2021). Industry 4.0 enables digital transformation and value creation processes but could raise several challenges for society in the future, such as mass unemployment. In addition, the recent pandemic has raised new concerns resulting in a shift toward mass personalization under a new Industrial Revolution (Sarfraz et al., 2021), which can be recognized as a post-pandemic recovery. This study outlines the primary features and concerns advantages of Industry 4.0 and Industry 5.0, where humans, technologies, and machines work as collaborators instead of competitors.
Society is transforming living environments (Vrchota et al., 2020) and experiencing a transition in the Digital and Green Economy, which are complementary to supporting sustainable development. While Industry 4.0 technologies bring significant value, they potentially can result in evolving global challenges. For instance, Blockchain is a revolutionary technology that contributes to the circular economy by enhancing the supply chain and reducing the carbon footprint across the entire value chain (Upadhyay et al., 2021). At the same time, Blockchain-enabled currency increases carbon footprint due to mining worldwide. Considerable research dedicated to Industry 5.0 was published only a decade since Industry 4.0 emerged, claiming to change the direction from industrial shareholders to society stakeholders (Breque, De Nul, and Petrides 2021).
The co-existence of the two Industrial Revolutions is mainly due to technological developments and the global demand for sustainable development. The former is recognized under Industry 4.0, and the latter is known as Industry 5.0. However, the debate over a call for a new Industrial Revolution is outside this article’s scope since this study attempts to discover Industry4.0’s capabilities and Industry5.0’s ambitions for achieving a high level of sustainability via mass personalization, a common goal of these two Industrial Revolutions. This study presents an outline for mass personalization based on the concepts of Industry 4.0. The research findings contribute to Industry4.0’s capabilities and Industry5.0’s development for achieving sustainability as a strategic goal.
The rest of this paper is organized as follows. Industrial Revolutions: Lifecycle and Value Propositions Section provides a review of the Industrial Revolution. Technology-driven mass personalization under Industry 4.0 is presented in Industry 4.0: Technology-Driven Mass Personalization Section, followed by human-centric mass personalization under Industry 5.0 in Industry 5.0: Human-Centric Mass Personalization Section. The proposed Mass Personalization as a Service (MPaaS) model is described in Mass Personalization - A Sustainable Business Model Under Industry 4.0 and Industry 5.0 Section. Challenges Under Industry 4.0 and Industry 5.0 Section provides a review of significant challenges. Finally, Conclusions and Future Works Under Industry 4.0 and Industry 5.0 Section concludes and points out future works.
The word"revolutio” specifies a fundamental and relatively sudden change, which has derived from the Latin word “revoluti”, meaning"a turn around”. Revolutions have varied widely in methods, duration, causes, and principles, but they often result in significant changes in response to challenges in an established system. Early studies of revolutions primarily analyzed events in European history. Similarly, the first Industrial Revolution shifted to new manufacturing processes in Great Britain, which produced a significant turning point in history. It is not surprising that Industry 4.0 was introduced in the centre of Europe by the German government.
Scholarly debates a new Industrial Revolution, while Industry 4.0 was coined a decade ago and has not matured enough due to ongoing development. Industry 4.0 is still in the early stages of expansion, with many years ahead in its technological evolution. Nevertheless, following the traditional decades’ cycle for the emerging new Industrial Revolution, the discovery that Industry 5.0 is already going ahead, led by Europe, is paving the way for sustainable development.
Figure 1 illustrates that the first Industrial Revolution was depicted by the age of mechanization with the advent of steam-driven machinery, which continued for over a century. The second introduced the concept of mass production through electric power. The shift from the second Industrial Revolution to the third took almost a century. The third resulted in the rise of advances in electronics and computers, indicating the start of Industry 3.0—the age of automation. Less than 40 years later, the fourth breakup emerged by Industry 4.0, known as the digitalization of manufacturing marked by cyber-physical systems and some cutting-edge technologies. It is the smart and cognitive machine age with little room for humans, which raised a big concern for the evolution of society beyond Industry 4.0. The pace of change is moving faster than ever in human history.
Industry growth is fundamentally related to social and economic development. Only a decade after Industry 4.0, the world has faced new global challenges and is seeking another Industrial Revolution. The next revolution, Industry 5.0, is on the horizon to bring back the human touch, which leverages the collaboration between human creativity and increasingly powerful and accurate machinery, which shows humankind is making a comeback. Technologies are converging more these days but iterating the current tech-driven Industrial Revolution may not have the desired impact if Industry 5.0 becomes an extended Industry 4.0. While the past Industrial Revolutions introduced significant technology shifts, Industry 5.0 would be the first Industrial Revolution with long-term impacts and fewer technology-driven approaches.
The world has seen tremendous changes in the industry 4.0 era. Advanced technologies have been introduced and globally adopted by industries in the past decade. A considerable effort has been dedicated to developing and implementing Industry 4.0 technologies. However, The European Commission announced Industry 5.0 to address global challenges and meet a more human-centric, sustainable, and resilient industry. Since forces are changing the world at an extraordinary rate, this study has investigated a shift from technology-driven to value-driven strategies. In addition, a conceptual model of transition to Industry 5.0 is proposed, along with a framework.
The real value of Industrial Revolutions, by definition, is human. Figure 2 shows how Industry 4.0 and Industry 5.0 cohesion creates scalable uniqueness with collaborations among technologies and humans. Cyberspace makes the cohesion between digital and physical worlds more feasible. Industry 4.0 technologies enable scalable uniqueness, and Industry 5.0 blends technology and humans for greater levels of sustainability. While Industry 4.0 offers enabling technologies for mass personalization, Industry 5.0 demands mass personalization by further collaboration between humans, machines, and digital technologies for resilience and sustainability.
Industrie 4.0 is the entirely digitalized and connected production paradigm that moves into the manufacturing industry, resulting in smart factories. Industry 4.0 is often used interchangeably with the fourth industrial revolution, Industrial IoT, cyber-physical systems, smart factories, smart manufacturing, advanced manufacturing, and RAMI 4.0-compliant. Regardless of different terms, companies find the opportunity to benefit from Industry 4.0-capable products to offer affordable and scalable personalization in the digital era. However, whether and when personalization will become the minimum product characteristic is unknown.
Personalization was not a big concern in the past, as most manufacturers operated under HenryFord’s philosophy that “you can have any color as long as it is black” Nevertheless, it took time since the unique value proposition of personalization describes how a business can offer a more tailored customer experience to address individuals needs. While mass personalization in digital media is obvious, the manufacturing industry has faced challenges in fulfilling individuals’ requirements. However, Industry 4.0 enables smart machines and augmented humans to create cognitive and physical improvements to close the gap between the physical and digital worlds (Kosch et al. 2022).
Industry 4.0 is a vision that evolved from an initiative to make the German manufacturing industry more competitive by enabling the digital transformation of industries, including manufacturing. Industry 4.0 is used interchangeably with the fourth Industrial Revolution and represents the intelligent networking of connected machines and processes with the help of information and communication technology. Industry 4.0 is the digital transformation of industries offering automation and data exchange in manufacturing technologies, including cyber-physical systems, IoT, Cloud manufacturing, smart manufacturing, and intelligent manufacturing for further value creation (Zhong et al. 2017). So, the technological advancement in the manufacturing industry has never been more substantial with massive demand. Also, the expectations to address global challenges have never been higher.
Industrial challenges are not limited to a single function, geography or business model. Historically they are related to customer preferences, affordability, and shorter delivery. Individual Industry 4.0 technologies are seen as the solution to many pain points. Table 1 lists some industry technologies such as IoT, AR, and Digital Twin with significant contributions. However, the most outstanding value of industry 4.0 comes from the improvements achieved when these technologies and capabilities are integrated and orchestrated at a value chain and product lifecycle.
The world is witnessing a trend where companies no longer force products to the market. Instead, they focus on what individuals want. This trend is evident in companies that invest in innovation. Personalization is more than a sales and marketing method for companies to stand out; it allows for a sustainable and long-term relationship, resulting in loyalty and longer-lasting products. Most customers are delighted when companies personalize their offerings Epsilon’s Digital Transformation Team 2018). However, there is a high demand for moving mass personalization beyond marketing messages, emails, and website content and towards long-lasting personalized products with a unique experience. Personalization is an unavoidable part of a modern user experience.
Being customer-centric and customer-focused is not the same. Similarly, humans, customers, consumers, and users are different, and understanding the differences can help develop a better mass personalization strategy. For instance, the consumer is a broader concept than the user as it refers to all members who use the same product despite only one family member purchasing the product. Also, customer-centred implies focusing on the customer, whereas customer-centric means thinking about the customer, but the processes, goals, and results are identical. The human-centred approach has significant advantages, including higher customer satisfaction, transparency, sustainability, productivity, long-lasting products, and customer lifetime value.
Data is the lifeblood of the mass personalization paradigm, and collaborative human-centric approaches provide the building blocks for a high level of sustainability. Mass personalization has proved hard to achieve profitability and affordability at scale since the fulfilment of individuals drives production costs and complexity up. The rapid development of Industry 4.0 technologies improves manufacturing efficiency, flexibility, agility, and productivity, in response to challenges that arise from manufacturers shifting to mass personalization. Therefore, the manufacturing objective has shifted from a manufacturer-led to a customer-led approach with a human-centred design and production process to fulfil individual satisfaction.
The forthcoming paradigm of mass personalization as a data-driven approach combines the low-cost advantage of the mass production paradigm with the individual need. The Data, Information, Knowledge, Wisdom (DIKW) hierarchy model was a decent idea when it was first proposed and explained the vertical integration of Industry 4.0. DIKW attempts to answer the life humans have lost in living, the wisdom humans have lost in knowledge, and the knowledge humans lost in information. DIKW model raised concerns due to the pyramid hierarchy. The knowledge results from applying finer-grained filters at each level can be misleading to the personalization production life cycle.
The shift from mass production to mass personalization concerns productivity and sustainability, while historically, some challenges are related to customer preferences, affordability, and delivery time. Industry 4.0 solves many pain points since technological advancements do not limit to one-size-fits-all products. Figure 3 shows and Table 1 lists Industry 4.0 enabling technologies, including Additive Manufacturing (AM), Augmented Reality (AR), Big Data, Blockchain, Cloud, Robotics, Digital Twin, and Internet of Things (IoT), with significant contributions to mass personalization under the Industry 4.0 umbrella. However, the most outstanding value of Industry 4.0 comes from the advanced capabilities for achieving scalable uniqueness for higher production when these technologies are orchestrated at a value chain.
Acknowledging the mass personalization paradigm requires innovations in identifying individual requirements, unique product design, on-demand product development, smart contract, e-supply chain, and service-oriented business strategies. Although modularization increases product variety with mass production efficiency, mass customization has some limitations: 1) Customers do not participate wholeheartedly in the design phase. 2) Designers predetermine potential combinations. 3) The concept of mass customization is not necessary to satisfy individual requirements. Industry 4.0 enables scalable and affordable personalization with adequate production time.
Scalable personalization is more feasible than ever but has not been developed adequately. Nevertheless, mass personalization is a severe challenge due to dependencies, data privacy, complexities, and a manufacturing resource pool. Mass Personalization as a Service (MPaaS) powers many services to continue functioning economically and socially with higher customer satisfaction. MPaaS is proposed to address on-demand requirements at reasonable costs and time despite uncertain needs and changes due to the service-oriented architecture and value proposition of Industry 4.0 enabling technologies (Aheleroff et al., 2021).
The principles of Industry 4.0, including autonomy, interoperability, decentralization, distribution, service-oriented, scaling, virtualization, transparency, seamless, and real-time capabilities, play a crucial role in the digital transformation of production and value creation processes with capabilities for enabling the mass personalization paradigm. The Industry 4.0 principles support innovation for creating value and changing experiences as, in the end, humans matter. The Reference Architectural Model for Industrie 4.0 (RAMI 4.0) has been developed as an architectural reference model that covers all areas of digital value creation, enabling stakeholders to understand Industry 4.0 design principles, including autonomy, automation, decentralization, integration, interconnection, transparency, and service-oriented (Hankel and Rexroth 2015).
Industry 4.0 brings autonomy to cyber-physical systems for flexibility in responding to uncertain personalization demands. Autonomous decision is essential in Industry 4.0 (Wilkesmann and Wilkesmann 2018). The interconnected Industry 4.0 and underlying digital technologies influence the design of ecosystems toward hybrids between centralization and decentralization of the global value chain (Schmidt et al., 2020). Industry 4.0 depicts the movement of phenomena in autonomous production systems, including Cobots. Not all decisions can be automated; therefore, human choices are still valuable in Cobots and the workforce collaboration to meet scalable and affordable personalization. The discussion on autonomy is far from over, certainly from the human and decision-making perspective. However, autonomy is not always achievable in practice. Autonomy is a recognized capability in Industry 4.0 and will have a value-added application in the Industry 5.0 era.
Automation under Industry 4.0 is not limited to conventional CNC machines but software-defined tools, devices, and machines. Utilizing AI, Big Data, Cobot, IoT, Cloud, and software for on-demand manufacturing products such as personalized medical products are becoming smarter and more innovative. Technology’s value advantages make design and manufacturing change affordable, scalable, and faster. Advanced automation autonomously calculates cost-effective operating with higher flexibility and prediction capabilities. The traditional image of automation is often similar to the DIKW pyramid looking at hierarchical levels in the Industry 4.0 vertical integration. However, IoT and connected systems moved automation to the next level through converged Cobot and Cloud computing with the ability to collect, generate and compute a massive amount of data. This data enables efficiency, reduces supply chain challenges in scheduling at a higher velocity, and offers Agile design for mass personalization production beyond traditional automation.
A decentralized system is a subset of a distributed system. The former means every node makes its own decision. The latter refers to no single data sharing, processing, and decision-making point. Decentralized manufacturing has become a distinguishing feature for resilience, agility, and servitization as the Industry targets mass personalization and further sustainability development. Utilizing global resources and manufacturing capabilities are made more feasible due to decentralization under Industry 4.0. Like the move to open-sourced software, decentralization allows more stakeholders access to capabilities and resources to enhance flexibility, resilience, efficiency, autonomy, and innovation for responding to personalization at scale, which can manage the complexity of mass personalization production.
The two integrations in Industry 4.0 enable mass personalization. The former integration concerning the automation pyramid: from field and control level in shop floor to production, operations, and enterprise planning level. Vertical integration makes seamless automation with minimum use of several systems and applications across automation pyramid levels due to IoT platforms supporting integrated and interoperability functionalities. Unlike vertical integration, the latter concerns the end-to-end value chain: from suppliers, processes, data flows and systems in the product development and production, distribution by logistics 4.0, and ultimately, the customer for a personalized product (Winkelhaus and Grosse 2020).
Achieving scalable personalization requires bridging the man and machine gap, which involves seamless and real-time data connections. Physical assets such as machines can communicate using smart sensors and technologies such as IoT to collaborate with humans. Interoperability is the ability to leverage connected data, connected assets, connected people, and communication technologies for collaboration between machines and humans in vertical and horizontal integration. The Internet of People (22) represents the mapping of social individuals and their interactions with smart devices on the Internet. It focuses on data collection and modeling for different Internet-based personal information applications.
Transparency implies openness, communication, and accountability for helping others realize what actions are performed. Transparency and virtualization can be extended under Industry 4.0 as the capability of cyber-physical systems to create digital representations of physical things in cyberspace. For scalable and affordable personalization, transparency should be put in context by Big Data to utilize the most appropriate resources and capabilities from the digital, cyber, and physical environments. Considering data privacy, transparency on the DIKW model is vital for mass personalization.
The manufacturing industry needs to be more tailored to individuals’ demand for value-added services, particularly mass personalization, instead of off-the-shelf production, which concerns the environment and sustainability worldwide. Most industries have adopted the as-a-service economy; However, transforming manufacturing into human-centricity and evolving customer demands seek new service-based revenue models that are yet to be achieved in practice. Industry 4.0 empowers companies to adopt service-oriented models by adding levels of smartness using advanced technologies such as Big Data analytics and IoT for offering distinguished services at scale.
Industry 5.0 is evolving to focus on individual needs, which requires better interaction among humans, machines, and advanced technologies. Industry 5.0 aspires to create reliable human-centric collaboration with autonomous robots, preferably at the same time, in the same workspace, in contrast to “automatio”, which uses technologies with restricted human intervention in processes. Individuals want to stand out and express their unique requirements through personalized products within reach for modest incomes. This desire for mass personalization forms the psychological and cultural driver behind Industry 5.0, which uses technology to return more value by humans to manufacturing, which could result in the latest wave of the industrial revolution.
The desire for mass personalization calls another assumption as there is a range of product types, such as drywall anchors, that can be made at a minimal cost, and often there is no need to consider such personalized products. In addition, the mass personalization trend raises a common concern that robots are taking over career opportunities. However, Industry 5.0 empowers people to realize basic human desires and fosters companies to deploy Cobots that need to employ a considerable workforce. Instead of replacing workers, Cobots help companies achieve unique value proposition.
Figure 4 shows that Industry 4.0 technologies significantly contribute to production efficiency. Industry 4.0 transforms the design, manufacture, operation, and production systems. Connectivity and interaction among parts, machines, and humans will make production systems faster and more efficient and elevate mass customization to new levels (Rubmann et al., 2015). In addition, Figure 2 illustrates the role of human-centric Industry 5.0 in leading production growth to a high level of sustainability. Therefore, Industry 4.0 focuses on “doing things right”, while Industry 5.0 is concerned about"doing the right things”, which results in sustainable development.
The fast-paced social evolution and globalization have raised prosperity worldwide. However, they have partially increased environmental pollution, regional inequality, and overused natural resources due to automation and digitization advancements. The emergence of increasingly promising technologies will speed up digital and technological innovations while society faces environmental threats. There is a debate about whether this is the time for a new Industrial Revolution. We may recall what was new when Industry 4.0 was coined to answer this provoking question. Artificial Neural Networks (1943), Industrial Robots (Unimate, 1961), The Internet (ARPAnet, 1969), PCs (IBM, 1981), the"We” (Tim Berners, 1990), wireless communication (Wi-Fi, 1997), the Internet of Things (Coke Ma-chine at CMU, the 1980s), and 3D printing (Stereolithography, 1985)? The response is quite evident that there existed years before 2011 when Industry 4.0 was introduced.
Industry 5.0 recognizes the Industry’s power to achieve the UN’s Sustainable Development Goals (SDGs) and become an active provider of prosperity to place well-being at the centre of the production process. This revolution hopes to improve the Industry’s position in society (30). Evolution is merely slow, reliable, and continuous changes in a given direction, applicable in many emerging technologies such as IoT, AR, and Digital Twin in the Industry 4.0 era. Cutting-edge technologies are developing with more advanced and real-life applications.
Moore’s Law states that the number of transistors on a microchip doubles every two years, though the cost of computers is halved. A similar state happened when Industry 4.0 was introduced. No new technology emerged except the affordability and accessibility of advanced technologies and capabilities such as 3D printers, digital data, affordable sensors, and high-speed Cloud-based services. Now, the world is more conscious of the environment, sustainability, and humans concerning increased waste, overusing natural resources, and a machines’ lifecycle under Industry 4.0 development. Many traditional machines retrofitted and transformed under Industry 4.0 into smart machines contribute to production but fail in response to the required sustainability, resilience, and workforce productivity during global challenges such as the pandemic.
Industry 5.0 is human-centric, focusing on mass personalization, resilience, and sustainability to embrace cross-disciplines and a broad spectrum of industries such as healthcare, financial, insurance, information technology, and the manufacturing industry, dominated by Industry 4.0. However, the true potential for Industry 5.0 progress lies in leveraging collaboration between humans, machines, and technologies. It is a collaboration between increasingly powerful and accurate machinery such as Smart CNC, Cobots, advanced technologies such as IoT, and the unique creative potential of the human being.
Table 2 highlights that Industry 5.0 covers a reasonable list of coherent and logical values for humans, society, and the planet. However, this does not mean the debate for value propositions under an emerging Industrial Revolution is over because small and medium-sized businesses can benefit from the advent of smaller, more affordable, and easy-to-use Cobots. Also, a considerable amount of research claims that adopting Industry 4.0 capabilities can result in what has recently been proposed under Industry 5.0. The world expects significant Industry 5.0 benefits, to include but not be limited to cost efficiency, greener revolution, innovation and personalization.
Industry 5.0 can take over developments and effective processes since the beginning of Industry 4.0. Most businesses use the least resources to make the most sustainable and resilient financial directions and obtain the highest profits.
Unlike the past Industrial Revolutions, Industry 5.0 focuses on protecting the environment as a priority, leading to the emergence of sustainability and resilience as new trends align with what consumers, most government regulations, and international organizations such as the United Nations have been increasingly demanding.
Industry 4.0 automation allows the workforce to utilize machines for repetitive tasks. However, technological innovation does not sufficiently allow focus on strategies to turn creative ideas into reality. Human Capital in Industry 5.0 will leverage the potential of machines and technology and lead to affordable personalization at scale.
Society 5.0 or “Super Smart Societ” is Japan’s concept of a technology-based, human-centric society, emerging through Industry 4.0. Society 5.0 was proposed as a future society for Japan, adopted by the Japanese Cabinet in January 2016, following the hunting society (Society 1.0), agricultural society (Society 2.0), industrial society (Society 3.0), and information society (Society 4.0). Society 5.0 aims to create a human-centric society for economic development and address societal challenges based on five strategic fields (Fukuyama 2018; Harayama 2018).
In response to globalization and the wave of digital transformation, the world realized a need for a direction change than further development. Different terms, such as Society 5.0 and Industry 4.0, were formed by focusing on a specific domain, such as society, manufacturing, smart cities, and connecting things worldwide. Industry 5.0 is not well established and seeking a reference architecture like Reference Architectural Model Industrie 4.0 (RAMI 4.0) for Industry 4.0 and Society 5.0 Reference Architecture (S5RA) for Society 5.0. However, it has exceptional potential for further research and development to improve resilience, sustainability, and human centricity beyond what has been developed.
Figure 5 shows that Society and Industrial Revolutions respond to individuals’ requirements and challenges by respecting environmental, social, and economic dimensions. Society 5.0 balances Industry 4.0, responsible economic development, and resolution of social problems. However, a gap has been identified between production and consumption, which involves sharing, leasing, reusing, repairing, refurbishing, and recycling existing materials and products as long as possible (Potočan, Mulej, and Nedelko 2021) - shaping a new Industrial Revolution focusing on sustainability. The concept of Industry 5.0 and Society 5.0 is not an alternative to Industry 4.0 or a developed version. Instead, these concepts want to create a prosperous human-centric society to address global challenges.
Industry 4.0 is shifting traditional automation to digitalization driven by cutting-edge technologies. However, it is realized that globalization will drive industrial needs toward high sustainability and resilience. Therefore, the next Industry Revolution is characterized by the return of the workforce to factories for achieving mass personalization. Digital transformation significantly impacts industries, such as data privacy issues, while increasing social complexity. Therefore, a tradeoff between society and economic growth motivates the creation of Industry 5.0 as a reaction to the vision of Industry 4.0.
In the digital era, AI will transform Big Data through IoT into wisdom according to the DIKW pyramid, helping humans have more fulfilling lives while balancing economic advancement with the resolution of social problems and creating a forward-looking human-centric society (Fukuda 2020). Digitalization is a means, but humans must remain the main actors. A massive amount of data is analyzed, and results are fed back to humans under Society 5.0. Similarly, Big Data and other advanced technologies are utilized for higher sustainability and fed back to humans. Figure 6 shows that humans remain central in Society 5.0 and Industry 5.0, aiming for a dedicated human-centric approach with a desire to cover each other due to a common goal (Fukuda 2020). Society 5.0 balances economic and social challenges by a system that integrates cyberspace and physical space, while Industry 5.0 exceeds the sustainability of the physical world. This cohesion is a response to smart societies under Society 5.0 as opposed to smart factories of Industry 4.0.
Resource conservation has emerged as a critical challenge in the digitalization era. At the same time, the technology-oriented approach increases the concern for global challenges, damaging the environment, wasting resources, and missing the value of humans in the workplace. Economic and social scientists use human capital to identify effective personal characteristics such as skills, knowledge, and health in the production process. Using human capital has been recognized innovation-driven approach to sustainability, resilience, and economic growth. Human resources can be transformed into highly productive Human Capital, reaching education, health and values.
The history of operators’ interactions with industrial revolutions follows a generational evolution. A human can take several forms, including in the loop (intervention), out of the loop (control), and on the loop (supervisor). While Operator 4.0 represents a smart and skilled operator, Human Operator 5.0 is more about Human-Machine collaboration focusing on the human side of manufacturing (Mourtzis, Angelopoulos, and Panopoulos 2022). Human Capital is essential for leading a sustainable transformation. The human-centric industrial revolution demands more Human Capital than previous industrial revolutions for higher flexibility, innovation, and scalable uniqueness. Recently, a human-centric perspective was shaped to foster a more balanced working relationship between increasingly innovative technologies, machines, and humans under Industry 5.0. This section defines Human Capital 5.0, contributing to mass personalization production toward further resilience and sustainability development.
This study proposes a new human-centric term to meet the future labor force. “Human Capital 5” is an intangible and autonomous physical asset with embedded values, including knowledge, skills, collaborations, creativity, and innovation to get the most out of technologies that achieve competitiveness and scalable personalization towards higher sustainability and resilience. The demand for Human Capital 5.0 is not a fad but an irreversible long-term plan. Human Capital 5.0 references the required competencies in the Industry 5.0 era. Therefore, companies that do not gain from Human Capital 5.0 cannot meet regulations and benefit from global opportunities.
Figure 7 illustrates the role of Human Capital 5.0 in achieving the three values, including personalization, resilience, and sustainability, in the Industry 5.0 era. In addition, these three values, personalization, empower Human Capital 5.0 to move beyond physiological and safety toward social, esteem, and self-actualization in Maslow’s hierarchy of needs. Last but not least, the mutual influence of Human Capital 5.0 and three values makes the UN Sustainable Development Goals more achievable.
Human Capital 5.0 brings the unique creativity of the human being to a production model, where the focus lies on humans using machines and enabling technologies to shift from buying off-the-shelf to making personalized products, resulting in higher sustainability. Industry 5.0 is not a replacement for Industry 4.0; Instead, a revolution in a more extended plan. Therefore, Human 5.0 still needs the advantages of enabling technologies to produce custom-made products at scale. Although some approaches and habits such as thrift, swapping, borrowing, and insisting on using working products support Industry 5.0 goals but may not be suitable for several people.
Figure 8 specifies that sustainability meets Maslow’s hierarchy of needs under Industry 5.0. Maslow extended observations of humans’ deficiency and growth needs, with uniqueness and the prioritization of needs as the two vital themes within the theory. Sustainability is often thought of as a long-term goal, and the sustainable development concept is recognized based on three fundamental pillars, including social, economic and environmental, which can be used at the global and individual levels. A meaningful bond between Maslow’s hierarchy and the sustainable development pathway shows that Industry 5.0 aims to shift from deficiency needs to meeting the needs of the present without compromising the ability of future generations to meet their own needs.
Human Capital 5,0 can help target higher levels in Maslow’s hierarchy and sustainability development by using enabling technologies and developing systems that measure changes across economic, social and environmental dimensions towards achieving sustainable development. Technology-enabled innovation has been responsible for social development. However, a revolution to focus on society and the environment with a willingness to reach self-actualization is demanded in the Industry 5.0 era because natural capital, e.g. environmental resources, cannot be replaced with human-made capital.
Industry 4.0 technologies such as IoT apply to monitor, control, and predict emissions from the combustion of fossil fuels to solve environmental problems. Nonetheless, once lost, natural resources cannot be recovered or repaired within a reasonable timescale, such as the loss of clean air, clean water, specific species, fertile soils, and climate regulation. So, Human Capital 5.0 can play a critical role in cohesion between the three major sustainable dimensions to address Industry 5.0 goals.
The influx of technology dramatically improves"industry, innovation, and infrastructure” as one of the United Nations Sustainable Development Goals aim to build resilient infrastructure, promote sustainable industrialization, and foster innovation. However, global challenges emerge the need for a human-centric industrial revolution, which requires a reference model with a focal point for understanding mass personalization production beyond technology-driven Industry 4.0 for higher sustainability and resilience with human-centric and social responsibilities alongside wealth creation.
The manufacturing industry makes the production process more efficient under Industry 4.0, and companies have automated processes that deliver scalable, consistent, and repeatable outcomes. Nevertheless, this does not address the necessity to ensure high resilience, sustainability, and personalized products. Human-machine collaboration is the key to unlocking these benefits, while one of Industry 5.0 challenges is to develop a reference model and adopt relevant human-centric processes.
A reference model is an abstract architecture representing components in simplified schematic form, while architecture is mainly defined as the fundamental structure of elements, interfaces, processes, principles, purposes, and properties. This study proposes a Reference Architecture Model for Industry 5.0 (RAMI 5.0) consisting of three crucial physical, digital, and cohesion layers. A reference is needed to support mass personalization under Industry 5.0. Using such a model can help break down complicated work into simple structured packages that align with crucial aspects of industrial resilience and sustainability to provide a shared understanding of the function of every layer and the interfaces between the layers.
Figure 9 brings a common understanding of Industry 5.0 for industrial use cases involving design, development, and deployment. This 3D layered model comprises a three-dimensional coordinate structure that describes all crucial aspects of Industry 5.0. This way, complex interrelations are broken into smaller clusters, including seven layers, four hierarchy levels, and a mass personalization value life cycle. Given increasing value and impact in the new Industry era, the proposed Reference Architecture Model for Industry 5.0 gives businesses a holistic framework for developing future products and business models using a three-dimensional map in a structured manner complemented by the Industry 5.0 components.
The vertical axis describes the six layers comprising an interlinked set of physical assets, sustainable, resilient, cohesion, enabling technologies, and business. The six layers on the vertical axis describe the decomposition of an asset into its properties, structured layer by layer. Such representations originate from sustainability, resilience, and cohesion to enabling technology for businesses under Industry 5.0, where properties of complex systems are broken down into layers.
The left horizontal axis represents the life cycle of value-added mass personalization for all vertical axis layers, from unique assets such as constructed wetlands to sustainable and resilient businesses. With the appropriate hierarchy levels on the right axis, every layer on the left can be joined through the product lifecycle development under the Industry 5.0 umbrella. Therefore, mass personalization complies with the six vertical and four layers on the right axis.
Industry 5.0 is a framework for the future of natural resources, energy, mobility, and manufacturing that builds upon the vision of Industry 4.0. Highly sustainable and resilient Industry 5.0 concepts can be explained and implemented using the proposed three-dimensional model for achieving a bigger purpose, the United Nations Sustainable Development Goals. All crucial aspects of Industry 5.0 can be mapped within this corresponding model. It describes all essential elements and provides a common understanding of what Industry 5.0 requires, the function of each component and the interfaces. The current"Industry 4.” manufacturing system characteristics are:
• Flexible systems and smart machines
• Distributed functions over the Internet
• Communication autonomy
• Technology-enabled mass personalization
The “New World: Industry 5.” characteristics are:
• Collaborate humans and machines seamlessly
• Creative, adaptive, innovative implementation
• Sustainable and resilient development worldwide
• Human-centric mass personalization
The word “sustainabilit” specifies the capacity to meet the needs of the present without compromising the needs of the next generations. It has derived from the origin of the Latin word “sus + tener”, broken down its meaning and translates to sus, to up and tenere, to hold. Nevertheless, change is the only constant, and industrial transformation is faster in the digital era. The world will be shifting from mass production to an era of mass personalization for meeting individuals’ requirements without compromising the effects on the environment, economy and society. A significant shift in tailored products will result in higher loyalty, resource utilization, and customer satisfaction.
Manufacturing evolution is affiliated with Industrial Revolutions, market, and customer demand. However, the manufacturing industry confronts new goals that are not only profit but aspirations for future generations and higher sustainability. This Industry 5.0 trend does not return to time-consuming and costly personalization, such as spending too much effort in knitting, carving, or creating by hand. So how to make affordable personalized products? Cobot is a big part of the answer. Cobots enhance human craftsmanship with the speed, accuracy, and precision required to make personalized products. The craftspeople use suitable technologies such as Cobot to make affordable products that meet individuals expected quality and specifications. Cobots bring the human touch to the assemblies that companies need to address individuals’ demands.
Automation brings higher productivity and efficiency while compromising individuals’ needs. Industry 4.0 has made mass personalization more feasible by enabling technologies with less human intervention to address this challenge. Although Industry 4.0 offers suitable technologies to address the growing demand for mass personalization, Industry 5.0 aims to amend this with humans back in production through a joint effort between people, machines, and technologies. While increasing automation can delegate hazardous tasks to machines, Industry 4.0 adoption concerns workforce reduction. Instead, Industry 5.0 objects to getting the human backbone of the production, creating a balanced mix of human intelligence and cognitive computing that promises mass personalization representing high-value-generating products resulting in higher sustainability.
A flexible layout and resource optimization for the mass personalization manufacturing model in smart manufacturing systems was proposed (Zhang, Ming, and Bao 2022). However, unlike technology advancement, Industry 5.0 is not recognized as an industry expansion, boosted automation, or incremental Industry 4.0 development. Cobot-enabled Industry 5.0 promises individuals the products they desire and, at the same time, secures a workforce with more meaningful employment than factory jobs by putting human beings back at the centre of industrial production. In an important sense, Industry 5.0 is enabled by the most advanced industrial automation technology, Cobots.
Architecture is mainly defined as a system and relationships to address the fundamental structure of elements, interfaces, processes, restrictions, principles, purposes, and physical and logical properties. The Reference Architecture Model for Industry 4.0 (RAMI 4.0) brings a common understanding of digitized industrial use cases involving the design, development, and deployment, which can be adopted as a model for almost all Industry 4.0 applications similar to the seven-layer ISO/OSI model, which is used as a reference for network protocols. The advantage of using such models is a shared understanding of a model. Furthermore, RAMI 4.0 defines a Service-Oriented Architecture (SoA). The basic principles of SoA are independent of vendors and products. Finally, RAMI 4.0 can help break complicated work into simple structured packages aligned with the crucial aspects of Industry 4.0 capabilities.
Figure 10 compares Industry 4.0 and Industry 5.0 architecture layers concerning digital weight over the physical. Both aim to offer mass personalization business while Industry 4.0 is technology-driven and Industry 5.0 is human-centric. Given the increasing impact in the Industry 4.0 era, the RAMI 4.0 was developed, including assets, integration, communication, information, function, and business, to support Industry 4.0 initiatives and give businesses a framework for developing future products (Heinz, Meik, and Birgit 2019).
Mass personalization flourished with the rise of Industry 4.0 development. Based on considerable studies, the mass personalization paradigm looks feasible in published scientific papers dating back over a decade, enabled by primary Industry 4.0 technologies. Still, it remains silent with limited industrial case studies. To address this concern, Industry 5.0 promises value to society when human-lead a blended machine and technology capabilities. It represents, to this extent, advanced technologies proved a potential to achieve mass personalization, and Industry 5.0 directs flawless production with minimum waste toward sustainable and resilient development.
The digital era implies significant shifts driven by technologies and their usage, similar to smartphones, social media, and video conferencing during the pandemic. In the Industry 4.0 era, technology fusion offers advanced manufacturing capabilities to achieve mass personalization like never before. However, adopting Industry 4.0 looks complex and costly but has the capabilities to enable novel approaches to develop flexibility for value-added products. Industry 4.0 can potentially address ecological and social challenges such as resource efficiency, environmental, and sustainability. So, the question is, what is the need for Industry 5.0?
Mass customization is not adequate as individuals have unique needs. Driven by a desire to make affordable products that give uniqueness to individuals, Industry 4.0 technologies and capabilities primarily enable mass personalization. The customer is not limited to making choices from a list of options in mass customization. Instead, it offers custom-made products based on what is strictly required. However, lowering costs while ensuring scalable product differentiation is not the ultimate goal. Manufacturing should provide more value to human life and society than using the workforce like machines, which operate for robots. They want sustainable mass personalization when humans engage in manufacturing, which can lead to mass personalization using value-adding human creativity and the ability to understand customers deeply.
Industry 5.0 is a vision introduced by Europe on a transition towards climate neutrality and digital leadership to keep Europe sustainable and competitive. The new vision has been labeled Industry 5.0 to minimize the unfavorable Industry 4.0 environmental impact. Industry 4.0 pioneers have discussed technology, data, smart machines, and intelligent connected things far more than humans, society, sustainability, resilience, and the environment. Table 3 highlights primary Industry 4.0 features and what is expected in the extended Industrial Revolution. Besides a shift in the direction, there is a synergy between Industry 4.0 capabilities and Industry 5.0 objectives. At least one common goal, mass personalization, can be identified, which is enabled by Industry 4.0 technologies and encouraged by Industry 5.0 but has not been successfully practiced in many industries.
The pandemic has changed and accelerated the priorities that the world expects in the following decades. Industry 5.0 gives consumers the desired products and gives workers more meaningful work. Placing humans back at the centre of production creates a skilled workforce. Although Industry 4.0 relies heavily on automation, Industry 5.0 will put humans back at the centre of production, making mass personalization more practical with several value-added advantages, including resilience, better user experience, responsiveness, and sustainability.
The lifecycle of Industrial Revolutions does not have a specific beginning and end. A transition from one to another shows an overlap over a period to make a successful transition, often with adequate knowledge, skill, and resources to embrace a new revolution. Industrial Revolutions are not evolution; to this extent, Industry 5.0 would be a significant shift concerning human-centric approaches rather than technology. While the world is still adopting digitization under the Industry 4.0 umbrella, the beginning of Industry 5.0—the age of personalization at scale is raised. The scope of the new Industrial Revolution will be to reinforce the human by utilizing cutting-edge technologies to meet personalized perception (Mourtzis, Angelopoulos, and Panopoulos 2021).
Industry 5.0 would value the workforce by blending humans and machines by utilizing brainpower that allows personalization. The capability to personalize at a scale beyond digital products could be one of the most significant benefits of Industry 5.0. For instance, mass personalization. It is already trendy in marketing, education, finance, and insurance and could manifest in the healthcare industry, where robotic-assisted surgery benefits complex and personalized surgical operations. “Industry 5.0 will be a synergy between humans and autonomous machines” (Demir, Döven, and Sezen 2019) with a human-centric approach. Humans are known for limits in the five classical senses of sight, hearing, taste, smell, and touch. At the same time, they are capable of empathy, flexibility, rapid adaptation to changes, practical communication skills and dealing with exceptions. Therefore, Cobots can assist with abilities when humans face constraints. Figure 11 illustrates that humans can lead by enabling technologies to produce mass personalization. As the most complex production paradigms, this combination maintains further agility, resilience, and flexibility for mass personalization.
Craft production results in long-lasting products. Since mass production could not meet individual requirements, manufacturers target clustering products and customer segmentation with mass production efficiency. However, customization is not what the citizens of the 21st century deserve. Therefore, one-of-a-kind production has been considered since Industry 4.0 emerged. However, mass personalization has faced challenges in practice resulting in a new Industrial Revolution. Industry 5.0 aims to increase collaboration between human cognitive, advanced technologies, and smart machines to oversee scalable personalization once believed impossible due to the limited manufacturing in predefined and repetitive processes.
Personalization has evolved due to market demand and the convergence of multiple Industry 4.0 technologies, including IoT, Big Data, Blockchain, Cobot, Cloud Manufacturing, and Additive Manufacturing. IoT and mass personalization are like two sides of a coin. The former deal with instant data, and the latter enables a human-centric model to engage purposefully and bring value-added with sustainability. There is proof that IoT and mass personalization match building meaningful, scalable, and unique experiences. However, IoT alone may not address mass personalization due to several challenges, including data privacy, service provisioning, multitenancy, human interaction, and iterative, incremental process."IoP2” refers to provisioning individuals’ requirements enabled by the Internet and other data-oriented technologies. IoP2 describes the convergence of enabling technologies for exchanging exclusive data over the Internet to fulfil a spectrum of scalable and affordable personalized products. IoP2 is not a technology similar to IoT. Instead, a service-oriented approach in which customer data and requirements are considered for service provisioning using crucial technologies. IoP2 enables value-added personalization, including but not limited to distinguished appearances, materials and features for creating an affordable and unique customer experience. However, there are serious concerns about the growth of IoP2, especially in data privacy.
Internet of Behaviours (IoB) is considered one of Gartner’s nine strategic technology trends to enable resilient businesses’ flexibility from pandemics. IoB can gather, combine and process data from many sources, including individuals, social media, private agencies, public sectors, location tracking, and facial, voice, and body gesture recognition deployments. IoB has ethical and societal implications similar to wearables that health insurance companies use to track activities and reduce compensations. The increasing sophistication of the technology that processes this data has grown this trend (Panetta 2020).
Figure 12 expresses a blend of humans, things, and the Internet, which introduces a new term for provisioning mass personalization production. The extension of IoT and IoB is the interconnection of smart products and humans that provides valuable insights into customer experience, interests, needs, and preferences toward personalization. IoT and IoB influence how individuals interact over the Internet, while IoP2 consolidates individuals and Things over the Internet.
IoP2 collects, integrates, combines, processes, and enriches data from many sources, including humans and machines. The increasing IoT-enabled systems and Big Data have permitted the mass personalization trend to grow significantly. IoP2 does have ethical and social implications depending on an individual’s aim. However, Blockchain would be an alternative to fill the gap with the ever-expanding services, including SaaS, PaaS, and IaaS. As the manufacturing industry improves under Industry 4.0, distributed manufacturing capabilities, the amount of captured data and how the data is integrated across different machines become more crucial for mass personalization production.
While technology emerges, new business paradigms become more popular due to the significant sustainability and added value for individuals in modern life. Uber, Netflix, Airbnb, and similar companies realized that digital transformation could offer mass personalization over the Internet when adopting cutting-edge technologies to create a much better customer experience. An ever-expanding IoT-enabled service model does not mean that the skills the workforce brings will not be needed. Instead, we will see Cobots become an extension of how emerging technologies and businesses, such as mass personalization, can involve third-party service providers using IoP2 under the Industry 4.0 umbrella toward Industry 5.0 sustainability goals.
As we approach the fifth Industrial Revolution, Cobots will play a significant role in handling repetitive tasks while humans focus on perception-driven decisions. Humans’ capabilities, such as creativity and the ability to use technology, drive Industry 5.0 to meet mass personalization for substantial value to individuals, the environment and society. Mutual collaboration between humans and Cobots is a win-win scenario in a value-added business model under Industry 5.0 umbrella (Müller 2020).
In addition to increasing productivity, efficiency, and quality, Cobots can help manufacturers become more sustainable, replacing large off-the-shelf products with personalized ones, creating more value from resources and reducing waste. Industry 5.0 is not replacing Industry 4.0. Instead, it introduces a revolution using technologies like IoT, Digital Twin, and Cobot for higher sustainability through a human-centric approach. Therefore, humans can dedicate effort to perception-driven work and delegate repetitive work to robots. Industry 5.0 is here to create innovations based on human-driven technology and machine (HTM) capabilities for higher sustainability.
How can Industry 5.0 concept turn into reality? How can Industry 4.0 capabilities support Industry 5.0 to achieve affordable mass personalization? Industry 5.0 recognizes the power of Industry 4.0 in designing, building, developing, and maintaining products in smart factories. Cobot is fundamental to the progression of Industry 5.0, which is becoming a resilient provider of prosperity by getting the most out of the relationship between machines, technology, and the human mind. The next generation of Cobots can provide a faster, more affordable, and highly flexible relationship between humans and machines to meet personalization at scale. For instance, Cobots are increasingly used to load and unload machines and provide highly personalized 3D-printed parts working as collaborators rather than competitors.
Figure 13 shows a move from industrial robots to Cobot-enabled automation, giving the workforce a high level of flexibility for taking advantage of machine capabilities. Cobots are designed to work alongside humans, while industrial robots do pre-programmed routine work independently. As a key Industry 5.0 enabling technology, Cobot produces a safer workplace because they have been designed to work alongside employees to support the workforce. A Cobot can assist employees in more meaningful tasks for producing custom-made products. By contrast, industrial robots often automate the manufacturing process without human intervention. Cobots are easy to program and capable of learning on the job, for instance, by moving the arm along the desired track than industrial robots. Unlike industrial robots, Cobots are not designed for heavy manufacturing.
Cobots consider humans for simple and intuitive interaction with humans and act as apprentices, capable of observing human actions and assisting operators. However, expanding other technologies such as Digital Twin and AI will be necessary. Furthermore, increasingly complex processes will require software development capable of Big Data, empowering the workforce to interact with machines and technology to transform a business and take the leap toward Industry 5.0.
Industry 5.0 envision the new goals as a step toward Industry 4.0 enhancement for human-centric mass personalization with higher resilience and sustainability. The impression behind Industry 4.0 concerns cyber and physical systems communication resulting in scalability and affordability in manufacturing, logistic, and management towards mass personalization. Industry 5.0 harnesses the benefits of Industry 4.0, putting technology to enable the transition but extending it by taking a human-centred approach. Industry 5.0 shifts from robots for automation to robots that collaborate with humans.
New technological developments shape user experience in the mass personalization era as crucial parts of the Industrial Revolution. It becomes essential to understand if a service should focus on automation or augmentation when moving from mass production to mass personalization. The former implies that machines take over the human task. The latter means that humans collaborate closely with technology-enabled machines to perform exceptional work. While augmentation and automation are not separated, combining both can bring extra value to simplify the complex mass personalization manufacturing paradigm.
Extreme automation and undervalued human have had additional consequences since Industry 4.0 emerged. Automation often desires short-term benefits, but augmentation aims for sustainable and resilient advantages. Industry 5.0 enhances Industry 4.0 automation by augmenting humans’ capabilities on top of speed, accuracy, scalability, predictive capabilities, and repetition in automation. Industry 5.0 extends into Industry 4.0 capabilities by adding humans’ agility, dexterity, creativity, improvisation, leadership, social talent, and soft skills.
What are the most significant long-term challenges facing humanity? Can threats be predicted and prevented? The answer may underline cohesion among humans, social, economic, and technological for innovations toward sustainability and resilience. Due to complex and costly implementation, SMEs often face difficulties adopting cutting-edge technologies and Industry 4.0 capabilities. New technologies can accelerate innovation to address global challenges in the right direction. Industry 4.0 technologies can bring substantial value if they revolutionize energy-consuming, empower scalable business models with a value proposition for local businesses, personalize user experience, and help products last longer. Therefore, a shift in the focus from shareholder value to stakeholder value, sustainability, and resilience has become a new global challenge.
The environment has been compromised globally by inappropriate consumption and production patterns since cutting-edge technologies emerged, not due to technological advancement. For instance, vehicle manufacturing significantly contributes to the economy, uses vast resources, and damages the environment yearly. So, how can the manufacturing industry reduce its carbon footprint? While technology development increases carbon dioxide and makes up the greenhouse gas emissions from manufacturing and using more petrol-run vehicles globally, technology revolutionized the vehicle industry with Electric Vehicles. Therefore, technology is not the source of the issue. Instead, using technology that damages the environment is the wrong direction.
Technology fundamentally changes the way we live and work. The past Industrial Revolution brought about new technologies with immense power, succeeded by further industrialization. The impact of the technology-driven approach on the environment has included misusage and damage to the earth. For instance, dams have many benefits, but building some large dams will significantly and irreversibly result in severe ecological damage. Similarly, cutting down trees is necessary to produce wood for construction, paper and other applications, but further industrialization potentially leads to a negative impact.
Further cohesion among technology and human-centric models should result in more environment-friendly products with higher sustainability as part of Industry 5.0 progress to address significant concerns, including economic, socio, technological, and cohesion among Industry 4.0 and Industry 5.0. Considerable challenges are mutually reinforcing and overlap, as indicated in Figure 14. The following sections discuss challenges of technology advancing in emerging economies, product differentiation, scale economies, and foresight social-economic.
Global challenges are identified under the United Nations Sustainable Development Goals. However, economic challenges are different worldwide, mainly in the US, Europe, Latin America, Africa, China, and India. For many developing countries, sustainable growth is limited by the size of the industries that can trade abroad and often do not grow by making more of the same that evolve their comparative advantage. Global companies that adopt Industry 4.0 dominate the market and reach significant economic growth but cause rising high unemployment rates, inequality, and poverty worldwide. Balancing Industry 4.0 economic development and resolving social problems requires intensifying learning over financial success, raising productivity and creativity, and leading to sustainable economic growth.
In the wake of the pandemic, addressing economic challenges and quick recovery with resilience will be essential. However, a new mindset could face challenges regarding cohesion in technology-driven and human-centric approaches for resilience and sustainable economic growth. Both technologies and humans are crucial to accomplishing resilience for meeting mass personalization, which could address individuals’ requirements and provide a sense of ownership with loyalty to products, resulting in higher sustainability and reducing various waste, including physical, digital, social, and process.
The world had moved from when humans had challenges to trust in technologies and machines. The Industry 4.0 development has increased the interest in industrial humanization, sustainability and resilience (Grabowska, Saniuk, and Gajdzik 2022). Promising Industry 4.0 has proved smart, reliable, scalable, and affordable capabilities beyond physical limitations. However, this does not mean humans have a healthier society than before. Often seen, humans and the environment are forgotten in technology-driven developments. Therefore, socio challenges become a severe concern across different industries.
The new normal can be extremely technology-driven, raising further socio challenges. The COVID-19 outbreak has swept through societies, including education, healthcare, economics, essential social interactions and everyday life, including flexibility with autonomy at work. Although physical, digital and cyberspace have become increasingly integrated. This does not look like sustainable healthy social prosperity regarding people’s relationships. Although people are getting used to the new normal, there is a doubt whether this situation is suitable and sustainable.
Society has already been impacted due to the absence of global agreement on sustainability. Feasible strategies and workable practices, including acceptance criteria for production and development, must be developed considering stakeholders’ sustainable value. It is no surprise that companies face resistance to digital transformation progress, especially in training the workforce to use advanced technologies. Therefore, A change in direction is required to address such challenges. Consequently, it is not humans that need to be forced to use new technologies. Instead, the technology should be developed for humans to embrace changes through a seamless process.
Scalable personalization faces severe challenges due to breaching privacy in the digital era. Utilizing advanced Industry 4.0 technologies made mass personalization feasible but has not been considered global sustainability. Transparency, trust, privacy, efficiency, scalability, and environment-friendly capabilities have yet to be achieved because every enabling technology, including IoT, Digital Twin, Cloud, and Blockchain, has consequences. A blend of Industry 4.0 capabilities and Industry 5.0 direction could address global sustainability and resilience challenges. For instance, Blockchain brings unique transparency and privacy advantages but has a significant environmental impact due to the mining process globally.
Industry 4.0 provides several values; nonetheless has raised various concerns. Several industries observe the development of cutting-edge technologies such as AI, which can reduce mass personalization costs by recognizing individuals’ requirements with minimum effort. However, privacy and trust have become a big challenge since AI algorithms require a massive scale of data to learn and improve the decision-making processes. Big Data and AI could enrich mass personalization to identify individual needs and expectations. Therefore, each technology has unmissable value and fundamental challenges in achieving mass personalization.
Leading companies reveal the limitations of advanced communications and the demand for 5G. It is faster than 4G, data carries without disruption, and higher accuracy is feasible as radio wavelength can be measured millimeters. However, the full impact of 5G on retrofitting long-standing factories and disrupting factory design with 5G cell layouts, machine placement, network connections and related concerns are yet to be practiced.
Lastly, personalization for critical industries such as healthcare has limitations. Technology-enabled metrics may not measure human conditions, unique requirements, and exceptional needs such as empathy and feelings. At the same time, it might be straightforward, directly measuring common sense needs such as size, weight, and temperature. The trend of mass personalization further complicates Industry 4.0 and Industry 5.0 cohesion. The latter focuses on human-machine interaction, assuming mutual communication, confidence, trust, freedom, and seamless communication with efficiency, flexibility, scalability, and productivity. However, transitioning from technology-driven to human-centric approaches may compromise established processes with financial consequences.
Industry 4.0 empowers further productivity, efficiency and cost savings. However, the world has faced global challenges, including increased natural resources and product waste since the affordable mass production growth. At the same time, Industry 4.0 offers a tool kit of cutting-edge technologies to measure, analyze, and track environmental impact. One of the biggest challenges is the cohesion between sustainable development and utilizing modern technologies. At best, the dilemma is that people pursue conflicting environmental quality and current economic trends. Since Industry 4.0 emerged, mass personalization has been more feasible.
Both individuals and companies wish to move beyond mass production. The former group is willing to have affordable personalized products. The former adopts a mass personalization business model as an advantage in the competitive market. The result can bring higher sustainability and customer satisfaction while significantly reducing waste. However, no research group, company, or particular Industry can play a role due to worldwide challenges. Instead, a group of influencers from academia, Industry and international organizations would be able to make a bold change. Therefore, this section summarizes critical challenges from economic, socio and technology adoption aspects when developing cohesion between Industry 4.0 and Industry 5.0.
The manufacturing industry is becoming more intelligent. However, it is not necessarily resilient, sustainable, and innovative enough to address the impact of global challenges. A shift from technology-enabled to human-centric mass personalization is a quest for today’s and future sustainability that has been barely studied. Though Industry 4.0 has delivered industrial automation and other significant production impacts, it sometimes has replaced the workforce. Therefore, Industry 5.0 aims to address that imbalance, using the concepts of human-centric and suitable technologies such as Cobot to ensure humans lead the digital transformation toward further resilience and sustainability worldwide.
Over the last decade, Industry 4.0 has focused on “doing things right” and raised concerns about “doing the right things,” resulting in Industry 5.0 being earlier than expected. Industry 5.0 originated as a scalable, transferrable, and universal industrial concept to move beyond national-level implementations, unlike Industry 4.0 adoption by several nations. Therefore, Industry 5.0 is not coined for a group of people, regions, and particular firms. Instead, it creates equity for the current and next generations rather than holding advantages for technology pioneers.
Highly technology-driven Industry 4.0 development may take longer to reach the plateau, but in the end, Industry 5.0 could outrun Industry 4.0 and Society 5.0 down the line. Nevertheless, most Industry 4.0 technologies have great potential to enable mass personalization for higher sustainability and resilience. The concern is not related to the value of Industry 4.0. Instead, a direction change requires to support the UN Sustainability Development Goals. The world has acknowledged the value of Industry 4.0 technologies and realized a revolution is required to achieve more sustainable development and resilience through human-centric approaches. Therefore, Industry 5.0 may not be an Industry 4.0 enhancement or extension.
This study proposed RAMI 5.0 and discussed Human Capital 5.0 with the capability to harness digital technologies for achieving higher sustainability and resilience. The argument running through this study concerns that Industry 4.0 consists of enabling technologies, while Industry 5.0 initiates rules to restore a human-centric vision for humanity rather than humans. Industry 5.0 and Industry 4.0 coexist to benefit society due to enabling Industry 4.0 technologies and a Human-centered approach under Industry 5.0 direction for higher sustainability and resilience. Most likely, Industry 5.0 will stay as an extension of Industry 4.0, following new technologies for achieving mass personalization production. In the future, it will be essential to explore and investigate the potential use of the proposed architecture and Cobot as a crucial technology under Industry 5.0 to meet higher sustainability with affordable and scalable personalization.
The raw data supporting the conclusion of this article will be made available by the authors, without undue reservation.
SA: Draft the article. XX: Provide direction and critical modification. RZ: Corrections and advice. HH: Discussion of ideas.
The authors would like to thank the Laboratory for Industry 4.0 Smart Manufacturing Systems at the University of Auckland for their support.
The authors declare that the research was conducted in the absence of any commercial or financial relationships that could be construed as a potential conflict of interest.
The handling editor [QM] declared a past co-authorship with the author [XX].
All claims expressed in this article are solely those of the authors and do not necessarily represent those of their affiliated organizations, or those of the publisher, the editors and the reviewers. Any product that may be evaluated in this article, or claim that may be made by its manufacturer, is not guaranteed or endorsed by the publisher.
Aheleroff, S., Mostashiri, N., Xu, X., and Zhong, R. (2021). Mass personalisation as a service in industry 4.0: A resilient response case study. Adv. Eng. Inf. 50, 101438. doi:10.1016/j.aei.2021.101438
Aheleroff, S., Zhong, R. Y., Xu, X., Feng, Z., and Goyal, P. (2020). “Digital Twin enabled mass personalization: A case study of a smart wetland maintenance system,” in Proceedings of the ASME 2020 15th International Manufacturing Science and Engineering Conference MSEC2020 (IEEE), 1–6. doi:10.1115/msec2020-8363
Anshari, M., Almunawar, M. N., Lim, S. A., and Al-Mudimigh, A. (2019). Customer relationship management and big data enabled: Personalization & customization of services. Appl. Comput. Inf. 15, 94–101. doi:10.1016/j.aci.2018.05.004
Boër, C. R., Redaelli, C., Boër, D., and Gatti, M. T. (2018). “Mass customization and personalization: A way to improve sustainability beyond a common paradox,” in Customization 4.0 (Cham: Springer), 237–250. doi:10.1007/978-3-319-77556-2_15
Breque, M., De Nul, L., and Petrides, A. (2021). Industry 5.0 - towards a sustainable, human- centric and resilient European industry. Europe: European Commission. doi:10.2777/308407
Chin, S. T. S. (2021). Influence of emotional intelligence on the workforce for industry 5.0. IBIMA Bus. Rev. 2021, 1–7. doi:10.5171/2021.882278
Demir, K. A., Döven, G., and Sezen, B. (2019). Industry 5.0 and human-robot Co-working. Procedia Comput. Sci. 158, 688–695. doi:10.1016/j.procs.2019.09.104
Epsilon's Digital Transformation Team (2018). New Epsilon research indicates 80% of consumers are more likely to make a purchase when brands offer personalized experiences. Available at: https://www.epsilon.com/us/about-us/pressroom/new-epsilon-research-indicates-80-of-consumers-are-more-likely-to-make-a-purchase-when-brands-offer-personalized-experiences (Accessed January 9, 2018).
Espinoza, P., Teresa, A., Rossit, D. A., Tohmé, F., and Cvásquez, O. (2022). Mass customized/personalized manufacturing in industry 4.0 and Blockchain: Research challenges, main problems, and the design of an information architecture. Inf. Fusion 79, 44–57. doi:10.1016/j.inffus.2021.09.021
Fei, L., Voegler, M., Claessens, M., and Dustdar, S. (2013). “Efficient and scalable IoT service delivery on Cloud,” in 2013 IEEE sixth international conference on cloud computing (IEEE), 740–747. doi:10.1109/CLOUD.2013.64
Fukuda, Kayano (2020). Science, technology and innovation ecosystem transformation toward society 5.0. Int. J. Prod. Econ. 220, 107460. doi:10.1016/j.ijpe.2019.07.033
Grabowska, S., Saniuk, S., and Gajdzik, B. (2022). Industry 5.0: Improving humanization and sustainability of industry 4.0. Budapest: Scientometrics. doi:10.1007/s11192-022-04370-1
Hankel, M., and Rexroth, B. (2015). The reference architectural model industrie 4.0 (RAMI 4.0). ZWEI Die Elektroindustrie 2 (2), 4–9.
Harayama, Y. (2018). Society 5.0: Aiming for a new human-centered society - Japan's science and technology policies for addressing global social challenges. Cover Story Collab. Creation through Glob. R&D TRENDS Hitachi Rev. 66 (6).
Heinz, B., Meik, B., and Birgit, B. (2019). Which criteria do industrie 4.0 products need to fulfil?, Budapest: Platform Industrie 4.0, 32. Available at: https://www.plattform-i40.de/PI40/Redaktion/EN/Downloads/Publikation/criteria-industrie-40-products.html.
Huang, S. H., Yang, Y. I., and Chu, C. H. (2012). Human-centric design personalization of 3D glasses frame in markerless augmented reality. Adv. Eng. Inf. 26 (1), 35–45. doi:10.1016/j.aei.2011.07.008
Kosch, T., Scholl, P. M., Schoen, D., Colley, A., Genç, C., Raudanjoki, O., et al. (2022). Augmenting human appearance through technological design layers. Front. Comput. Sci. 4, 755451. doi:10.3389/fcomp.2022.755451
Mourtzis, D., Angelopoulos, J., and Panopoulos, N. (2021). “A teaching factory paradigm for personalized perception of education based on extended reality (XR),” in Proceedings of the 12th conference on learning factories (CLF 2022) (IEEE). doi:10.2139/ssrn.4071876
Mourtzis, D., Angelopoulos, J., and Panopoulos, N. (2022). Operator 5.0: A survey on enabling technologies and a framework for digital manufacturing based on extended reality. J. Mach. Eng. 22 (1), 43–69. doi:10.36897/jme/147160
Müller, J. (2020). Enabling technologies for industry 5.0: Results of a workshop with europe's technology leaders. Europe: European Commission. doi:10.2777/082634
Panetta, K. (2020). Gartner top strategic technology trends for 2021. Budapest: Gartner. Available at: https://www.gartner.com/smarterwithgartner/gartner-top-strategic-technology-trends-for-2021 (Accessed October 19, 2020).
Potočan, V., Mulej, M., and Nedelko, Z. (2021). Society 5.0: Balancing of industry 4.0, economic advancement and social problems. Kybernetes 50 (3), 794–811. doi:10.1108/K-12-2019-0858
Rubmann, M., Lorenz, M., Gerbert, P., Waldner, M., Jan, J., Engel, P., et al. (2015). Industry 4.0: The future of productivity and growth in manufacturing industries. Budapest: The Boston Consulting Group.
Sarfraz, Z., Sarfraz, A., Iftikar, H. M., and Akhund, R. (2021). Is covid-19 pushing us to the fifth industrial revolution (society 5.0)? Pak. J. Med. Sci. 37 (2), 591–594. doi:10.12669/pjms.37.2.3387
Saxena, A., Saxena, A., Sharma, R., and Parashar, M. (2021). Emergence of futuristic HRM in perspective of human - cobot's collaborative functionality. Int. J. Eng. Adv. Technol. 10 (5), 292–296. doi:10.35940/ijeat.e2763.0610521
Schmidt, M. C., Veile, J. W., Müller, J. M., and Voigt, K. I. (2020). Ecosystems 4.0: Redesigning global value chains. Int. J. Logist. Manag. 32, 1124–1149. doi:10.1108/IJLM-03-2020-0145
Upadhyay, A., Mukhuty, S., Kumar, V., and Kazancoglu, Y. (2021). Blockchain technology and the circular economy: Implications for sustainability and social responsibility. J. Clean. Prod. 293, 126130. doi:10.1016/j.jclepro.2021.126130
Vayre, B., Vignat, F., and Villeneuve, F. (2012). Metallic additive manufacturing: State-of-the-Art review and prospects. Mech. Industry 13 (2), 89–96. doi:10.1051/meca/2012003
Vrchota, J., Martin, P., Rolínek, L., and Bednář, J. (2020). Sustainability outcomes of green processes in relation to industry 4.0 in manufacturing: Systematic review. Sustainability 12, 5968. doi:10.3390/su12155968
Wilkesmann, M., and Wilkesmann, U. (2018). Industry 4.0 – organizing routines or innovations? VINE J. Inf. Knowl. Manag. Syst. 48 (2), 238–254. doi:10.1108/VJIKMS-04-2017-0019
Winkelhaus, S., and Grosse, E. H. (2020). Logistics 4.0: A systematic review towards a new logistics system. Int. J. Prod. Res. 58, 18–43. doi:10.1080/00207543.2019.1612964
Xu, X. (2012). From Cloud computing to Cloud manufacturing. Robotics Computer-Integrated Manuf. 28 (1), 75–86. doi:10.1016/j.rcim.2011.07.002
Xu, X., Lu, Y., Vogel-Heuser, B., and Wang, L. (2021). Industry 4.0 and industry 5.0—inception, conception and perception. J. Manuf. Syst. 61 (10), 530–535. doi:10.1016/j.jmsy.2021.10.006
Zhang, X., Ming, X., and Bao, Y. (2022). A flexible smart manufacturing system in mass personalization manufacturing model based on multi-module-platform, multi-virtual-unit, and multi-production-line. Comput. Industrial Eng. 171 (9), 108379. doi:10.1016/j.cie.2022.108379
Zheng, P., wang, H., Sang, Z., Zhong, R. Y., Liu, Y., Liu, C., et al. (2018). Smart manufacturing systems for industry 4.0: Conceptual framework, scenarios, and future perspectives. Front. Mech. Eng. 13 (2), 137–150. doi:10.1007/s11465-018-0499-5
Zheng, P., Yuan, L., Chen, C. H., and Xu, X. (2019). Smart, connected open architecture product: An IT-driven Co-creation paradigm with lifecycle personalization concerns. Int. J. Prod. Res. 57 (8), 2571–2584. doi:10.1080/00207543.2018.1530475
Keywords: industrial revolutions, Industry 4.0, Industry 5.0, Human Capital 5.0, cobot, RAMI, mass personalization
Citation: Aheleroff S, Huang H, Xu X and Zhong RY (2022) Toward sustainability and resilience with Industry 4.0 and Industry 5.0. Front. Manuf. Technol. 2:951643. doi: 10.3389/fmtec.2022.951643
Received: 24 May 2022; Accepted: 13 October 2022;
Published: 31 October 2022.
Edited by:
Qiunan Meng, Dalian University of Technology, ChinaCopyright © 2022 Aheleroff, Huang, Xu and Zhong. This is an open-access article distributed under the terms of the Creative Commons Attribution License (CC BY). The use, distribution or reproduction in other forums is permitted, provided the original author(s) and the copyright owner(s) are credited and that the original publication in this journal is cited, in accordance with accepted academic practice. No use, distribution or reproduction is permitted which does not comply with these terms.
*Correspondence: Shohin Aheleroff, c2hvaGluLmFoZWxlcm9mZkBhdWNrbGFuZC5hYy5ueg==
Disclaimer: All claims expressed in this article are solely those of the authors and do not necessarily represent those of their affiliated organizations, or those of the publisher, the editors and the reviewers. Any product that may be evaluated in this article or claim that may be made by its manufacturer is not guaranteed or endorsed by the publisher.
Research integrity at Frontiers
Learn more about the work of our research integrity team to safeguard the quality of each article we publish.