- 1ICT4SM, Institute of Mechanical Engineering, École Polytechnique Fédérale de Lausanne, Lausanne, Switzerland
- 2Whirlpool Europe S. R. L., Cassinetta di Biandronno, Italy
Digital Twin is one of the fundamental enabling technologies for Industry 4.0 as it allows the convergence between a physical system and its digital representation. A proper modelling method is the prerequisite for successful digital twin implementation. The manufacturing process determines critically the quality of the manufactured products. The influential elements need to be systematically organized when modelling a manufacturing process. This paper proposes a semantic modelling method named RMPFQ (Resource, Material, Process, Function/Feature, Quality) aiming to interlink the main influential factors related to product quality during manufacturing processes. The proposed RMPFQ model is formalized with an application ontology following the IOF-Core middle-level and BFO top-level ontologies. Based on this ontology, a semantic-driven digital twin architecture is designed and mapped to the recently proposed Cognitive Digital Twin concept. A correlation matrix is designed to quantify the relationships among RMPFQ elements thus to facilitate the industrial applications. A case study based on the assembly process of a washing machine is conducted to demonstrate the implementation procedures of the proposed RMPFQ method.
1 Introduction
Digital Twin (DT) is a virtual, digital equivalent to a physical product (Grieves, 2014). It is a concept fostered by various advanced technologies such as Cyber-Physical Production Systems (CPPS), Industrial Internet of Things (IIOT), Artificial Intelligence (AI), 3D modelling, system simulation, digital prototyping etc. (Chavarría-Barrientos et al., 2018; Wang et al., 2019). DT is one of the fundamental enabling technologies for Industry 4.0, as it makes possible of the convergence between a physical system and its digital representation (Wang et al., 2015; Schleich et al., 2017). Aiming at modelling complex structures and processes, DTs enables to detect physical problems sooner, predict outcomes more accurately, and create higher quality products (Stavropoulos and Mourtzis, 2022). The concept of DT has been evolving rapidly in recent years and has been widely applied in various industrial scenarios such as system modelling and simulation (Jinjiang Wang et al., 2018), design validation (Detzner and Eigner, 2018), manufacturing process optimization (Wang et al., 2019) etc. The modelling of DT plays a critical role in its practical applications. An appropriate DT model should be capable of ensuring a correct match with the original physical system and representing its actual conditions. However, it remains a challenging task to build a feasible DT model for manufacturing systems and processes due to their complexity in industrial applications. The manufacturing processes can significantly affect the quality of a product. In the manufacturing phase, the designed quality of a product is expected to be realized by machining or assembling materials according to certain production processes (Foehr et al., 2013b).
Zero-Defect-Manufacturing (ZDM) (Psarommatis et al., 2020) is one of the important targets of Industry 4.0 and DT is expected to empower this vision. When designing a DT model for a manufacturing system, all the relevant factors, such as production design, machining processes, and the inbound logistic purchasing all necessary materials, as well as the interactions among them need to be taken into consideration. This leads to the interoperability issues among different stakeholders from inside or outside of a company. It is due to the fact that data from different sources usually have heterogeneous syntax, schema, or semantics, making different stakeholders difficult to interoperate. Semantic engineering provides solutions to achieve semantic interoperability in a heterogeneous information system by defining formal models for domain knowledge.
The main research questions this study aims to address are: 1) how to formally describe a manufacturing system with semantic engineering approaches? 2) How to integrate semantic technologies with DTs to enhance their cognitive capabilities? 3) What are the available tools enabling the implementation of knowledge modelling for manufacturing systems? Targeting at these research questions, this paper proposes a semantic modelling method for manufacturing processes with special focus on the quality perspective. It covers the main elements that can impact product quality in the manufacturing phase, including manufacturing resource, materials, production processes, product features and functions. The proposed model is further used as the basis for a semantic-driven digital twin architecture which is the first step towards the recently proposed Cognitive Digital Twin (CDT) paradigm (Zheng et al., 2021).
The rest of the paper is arranged as follows: Section 2 introduces some existing studies related to this paper. Section 3 describes the proposed RMPFQ model, as well as an enabling correlation matrix and an application ontology structure. Section 4 presents the architecture of the semantic-driven DT architecture and its relations with CDT. Section 5 introduces a case study extracted from an industrial application scenario to demonstrate the implementation procedures of the proposed RMPFQ model. Finally, Section 6 summarizes the paper with a conclusion about the preliminary contributions of the proposed approach and the outlook into the future work.
2 Literature Review
This section reviews the core concepts mentioned in this study including Digital Twin, semantic modelling and the recently emerged Cognitive Digital Twin. Considering multiple topics are involved, it would be overloaded to conduct thorough systematic literature reviews. Therefore, only some of the most pertinent studies of each topic are introduced in this section.
2.1 Digital Twin
After a decade of rapid development, DT has become an essential enabling technology for advanced manufacturing. A basic DT is composed of three main elements including the physical entity in real space, virtual representations in virtual space, and the connections of data and information that tie the virtual and real spaces together (Grieves, 2014). Based on this three-dimension definition, Tao et al. (2017) proposed a five-dimension DT model to promote the further applications of DT by adding two more dimensions, i.e. DT data and services. During the past decade, DT and relevant technologies have been widely applied in many different domains such as prognostics and health management (Tao et al., 2018), operation state monitoring of complex equipment (Gockel et al., 2012; Seshadri and Krishnamurthy, 2017).
DT has also been broadly adopted in the manufacturing domain covering different production systems. Tao et al. (2017) developed a DT model for a shop-floor and proposed a reference architecture with operating mechanism to facilitate the implementation of the shop-floor DT concept. Focusing on the additive manufacturing, Knapp et al. (2017) developed a DT model for typical additive manufacturing processes and analyzed its main components. A DT reference model was developed by Wang et al. (2019) aiming at improving the fault diagnosis capabilities of rotating machinery. In order to achieve autonomous manufacturing, a DT-based Cyber-Physical Production System (DT-CPPS) was proposed in (Ding et al., 2019) to create smart shop floors by combing CPPS and DT technologies. Aiming at ZDM, Psarommatis (2021) proposed a methodology for developing DT models for modeling a production system, and used the created DT model to create ZDM performance maps. Mourtzis et al. (2021) integrated DT with a ZDM framework aiming to optimize equipment design using data derived from industrial environments. Their framework covers data acquisition, data processing and the simulation. Both historical data and simulation data were used for DT construction.
With the rapid deployment of advanced technologies, such as IIOT and CPPS, modern manufacturing systems are getting increasingly complex. Such a complex system can be treated as a system of systems consisting of various subsystems and components. Moreover, different stakeholders are involved during different lifecycle phases of the manufacturing system. When developing DTs for such a complex system, it is a challenging task to cope with the heterogeneity brought by different stakeholders and subsystems thus to achieve high level of interoperability. A semantic model can provide possible solutions to this challenge.
2.2 Semantic Modelling
An information model of a system can enable to abstract different types of data and information of the system, and to provide an understanding of how the data elements are related (Calero et al., 2006). A common information model makes possible of data and information sharing with unambiguous, shared meaning, thus to achieve semantic interoperability at the system level (Hildebrandt et al., 2020). A semantic model is a type of information model that supports the modelling of entities and their relationships. The total set of entities in a semantic model comprises the taxonomy of classes that can be used to represent the real world. The main objective of semantic modelling is to abstract different kind of data within the context of its correlation, and to model the domain world at the abstract level. The main benefits of such semantic models include avoiding misunderstanding, enhancing interoperability, enabling reasoning and leveraging resources, among others (Calero et al., 2006).
Ontology engineering is one of the prominent approaches to create such semantic models. It includes a set of activities, methodologies, tool suites and languages that concern the ontology development and management (Gómez-Pérez and Suárez-Figueroa, 2009). Feilmayr and Wöß (2016) defines ontology as “a formal, explicit specification of a shared conceptualization that is characterized by high semantic expressiveness required for increased complexity.” Ontology enables capturing and instantiating knowledge persistently so that it can be reused in a tool-agnostic way. It can be used as a rusted source of knowledge to provide a unified and coherent view over existing systems (El Kadiri and Kiritsis, 2015).
To assure the interoperability and reusability of different ontologies, a hierarchical methodology should be followed, i.e. using upper-level ontologies to unify the lower-level application ontologies. The existing ontologies can be categorized into at least three levels: top-level ontology, middle-level ontology and application ontology.
• A top-level ontology contains a set of general vocabularies commonly used across all domains. These vocabularies are properly structured and formally defined according to certain methodology. Examples of popular top-level ontologies include the Basic Formal Ontology (BFO) (Arp and Smith, 2008) and the Descriptive Ontology for Linguistic and Cognitive Engineering (DOLCE) (Borgo et al., 2022).
• A middle-level ontology focuses on certain application domains such as manufacturing, material, chemistry, biology etc. Manufacturing is one of the main application areas of ontology. For example, Lemaignan et al. (2006) developed the MASON (MAnufacturing’s Semantics ONtology) as a preliminary upper ontology aims to create a common semantic net for the manufacturing domain; and explored its possible applications in automatic cost estimation and semantic-aware multi-agent manufacturing system. Negri et al. (2015) created the MSO (Manufacturing System Ontology) focusing on the discrete manufacturing, process production and the logistics domains. The Industrial Ontologies Foundry (IOF) (IOF, 2021) is an ongoing initiative aims to co-create a set of open domain-level ontologies to support the manufacturing for industrial needs and to promote data interoperability. Depending on its scope, a middle-level ontology can be further narrowed down to certain domain and sub-domain ontologies.
• An application ontology is developed for a specific application scenario with customized vocabularies and relationships. It can be developed on the basis of a middle-level ontology. The relevant data sources can be added to an application ontology to construct a knowledge graph and to conduct certain specific tasks. For example, Foehr et al. (2013a) proposed the MPFQ-model (Material, Production Processes, Product Functions/Features, Product Quality) to organize the main factors during production that can impact product quality. Based on this model they developed an application Ontology to support quality optimization of discrete manufacturing processes.
2.3 Semantic-Driven and Cognitive Digital Twin
Modern industrial systems are highly complex involving heterogeneous data, information and knowledge across different lifecycle phases and various industrial domains. Cross-domain and cross-lifecycle integration is a main challenge for DT applications in to such complex systems. Previous studies (Banerjee et al., 2017; Kharlamov et al., 2018; Gómez-Berbís and de Amescua-Seco, 2019) have explored the feasibility of using semantic modelling to address the data heterogeneous problem due to different protocols and specifications follows by different stakeholders, therefore to enhance the interoperability of DTs. The adoption of semantic technologies enhances the cognitive capabilities of the current DTs and makes possible of integrating multiple related DTs. Based on these studies, the CDT concept has been attracting much attention recently (Zheng et al., 2021).
The CDT concept is first proposed in 2016 (Adl, 2016) along with the cognitive evolution of IoT technologies. It is further explored from the perspectives of cognitive computing and artificial intelligence in 2017 (Fariz Saracevic, 2017), as well as from the angle of hybrid human-machine cognitive capabilities (Fernández et al., 2019). Some studies (Abburu et al., 2020b; Lu et al., 2020; Ali et al., 2021) have tried to define CDT by extending DTs with extra semantic capabilities, model and twin management capabilities, as well as autonomous decision-making capabilities.
A recent study (Zheng et al., 2021) reviews existing studies about CDT and defines CDT as “a digital representation of a physical system that is augmented with certain cognitive capabilities and support to execute autonomous activities; comprises a set of semantically interlinked digital models related to different lifecycle phases of the physical system including its subsystems and components; and evolves continuously with the physical system across the entire lifecycle.” CDT is considered as the next generation of DT (Boschert et al., 2018) as it will enable different cognitive capabilities, such as attention, perception, comprehension, memory, reasoning, prediction, decision-making, problem-solving, reaction and so on, making it possible to deal with complex and unpredicted behaviours with optimization strategies dynamically (Kokar and Endsley, 2012; Fernández et al., 2019; Al Faruque et al., 2021; Zheng et al., 2021).
Despite of the promising future of CDT and other semantic-driven DT methods, there are many gaps need to be bridged. A functional and comprehensive knowledge base is the core for this capability. Knowledge representation and acquisition are among the most challenging task for CDT development (Zheng et al., 2021). Due to the heterogeneity and ambiguity of domain knowledge, it is difficult to specify, formalize and transfer it into a machine understandable format (Abburu et al., 2020a). Semantic technologies such as ontology and knowledge graphs have been widely adopted for knowledge management.
Targeting at the challenges of knowledge representation and acquisition, this paper proposes a semantic modelling method for manufacturing systems focusing on the quality perspective. The aim is to push forward the application of semantic-driven DTs in manufacturing domain proceeding towards the CDT paradigm.
3 The RMPFQ Model
To deal with the complex quality requirements in the Factories of the Future (FoF), a project named “inteGration of pRocess and quAlity Control using multi-agEnt technologies” (GRACE) founded by European Union was created. It mainly focused on the provision of a new multi-agent architecture, combined with a methodology for quality assurance and improvement to provide suitable solutions for plant operators (Foehr et al., 2013b). The MPFQ-model was developed in this project to provide integrated consideration of factors related to product quality in manufacturing phase, i.e. material, production process, and product functions (Foehr et al., 2013a). The simplified elements of the MPFQ-model and their interrelations are as shown in Figure 1.
The MPFQ-model was developed based on the processes of assembly manufacturing. As shown in Figure 1, during an assembly Process (k), two or more Materials (x, y) are assembled to form a Function (m) which impacts Quality (n). This model can properly describe some typical assembly processes. However, in many cases the manufacturing resources can also affect the manufactured product quality. For example, during a machining process, usually only one workpiece is machined, and it interacts directly with a machine tool. The status of the machine and machine tool can directly affect the quality of the workpiece. Even for assembly processes, the status of the production resources, such as fixture and tooling, can also impact the final product quality. Therefore, the MPFQ-model needs to be extended to fit more manufacturing scenarios.
This study extends the MPFQ-model by adding the Resource element to represent the manufacturing resources. Figure 2 shows the elements of the proposed RMPFQ model and their interrelations, as well as some exemplary data related to these elements.
Based on the definition of MPFQ-model (Foehr et al., 2013a), we define the elements of the proposed RMPFQ model as follows:
• Manufacturing Resource, according to ISO 15531, represents the devices, tools and means, at the disposal of the enterprise to produce goods and services, but except raw material and final product components.
• Material represents the entities that are needed to produce a certain product or product component, which may include raw materials, pre-products, consumables, operating supplies, product components and assemblies (O’Sullivan and Sheffrin, 2007).
• Manufacturing Processes are defined as processing and transforming materials into the final goods by using machines, tools and human labour. This process is defined within the plant engineering (Gibovic and de Ciurana, 2008).
• Product Functions/Features represent the distinguished characteristics of a product item, which may include functionalities like specific tasks, actions or processes that the product is able to perform; and/or other features like performance (Foehr et al., 2013a).
• Product Quality (Q) is defined as, according to DIN EN ISO 9000, the degree of conformance of final product functions and features to designed requirements.
For the definition of Resource, we followed the ISO 15531 standard as it is close to the purpose of the proposed RMPFQ model, although there exist several different definitions as reviewed by Emilio et al. (Sanfilippo et al., 2019). The elements of the RMPFQ model may have different emphasis for assembly and machining processes, although they might share the same names. The output of an assembly process is usually either the final product or main components of it. In this case, the quality (Q) directly interacts with the customers’ requirements, and the function (F) is the core to fill such requirements, which then requires qualified components/parts/materials (M) being assembled through proper Processes (P). In contrast, the output of a machining process is usually a workpiece manufactured by a supplier. The quality (Q) of the part mainly refer to the conformance of workpiece features to the designed requirements. It does not necessarily interact with the customers requirements, and the F element emphasizes more on the Features of the part although it may impact the Function of the product in the assembly process.
The proposed RMPFQ model can be used to model different phases of a product lifecycle, i.e. product part machining process and components assembly process. In addition to the interactions between different elements inside a RMPFQ model, relationships also exits between different RMPFQ models corresponding to different manufacturing processes. Figure 3 depicts a typical application scenario including two machining processes followed by an assembly process. The two machining processes are executed by two different suppliers producing two parts, which are then assembled through the assembly process.
There are several types of interrelations in this simplified scenario.
• A given material (Ma, Mb) is machined by manufacturing resources (Ra, Rb) (e.g. fixture and associated tooling and a cutting tool) through a planned machining process (Pa, Pb). This composes the RPM interactions (marked with orange lines).
• The machining process (Pa, Pb) uses input material (Ma, Mb) and resources (Ra, Rb) to produce one or more features (Fa, Fb), composing the RMPF interactions (marked with blue lines).
• All the RMPF elements may also have straightforward impact on the quality (Qa, Qb) of the machined workpiece (marked with green lines).
• For the assembly process, the machining process is replaced by assembly process and the input includes multiple materials instead of one single workpiece. The interactions among the elements remain the same.
It is worth to note that there also exist relations among different resources, i.e. machine, setup, and cutting tool, which is not reflected in the proposed model; and a machining process may generate multiple features as described by Najam et al. (Anjum et al., 2012).
3.1 RMPFQ Correlation Matrix
To better evaluate the relationships among different elements, a correlation matrix is designed as shown in Figure 4. It enables quantifying the impacts of RMPF elements on quality (Q). It is composed of three dimensions corresponding to the RMPF entities, Quality entities, and quality inspection Stations. Station is added to reflect the quality control procedures in a physical manufacturing system. It is not included in the RMPFQ model since it only inspects product quality but does not impact the quality directly. Details about each dimension of the correlation matrix are explained as follows:
• Bottom-left matrix: Correlation between RMPF entities, i.e. Resource (R1, Ri, RNr), Material (M1, Mj, MNm), Process (P1, Pk, PNp), Function (F1, Fl, FNf), and Quality (Q1, Qn, QNq) entities. Each of them represents the impact level of a RMPF entity on a Quality entity. Nr, Nm, Np, Nf, Nq are the total numbers of RMPFQ entities respectively; and rq, mq, pq, fq represent the correlation values between RMPF and Quality entities.
• Bottom-right matrix: Correlation between each of the RMPF entities and inspection Station (S1, Sm, SNs). Each of them represents the possibility of a RMPF entity been inspected by a certain station. Ns denotes the total number of stations; and rs, ms, ps, fs are the correlation values between RMPF and each station.
• Top matrix: Correlation between each of the Quality and Stations entities. It represents the capability of each station to inspect a certain quality indicator.
During industrial applications, the correlation values between RMPF-Quality, and between RMPF-Station are directly given by experts based on their knowledge. The correlations values can be measured by positive rational numbers in a predefined range. For example, multiple experts can evaluate separately for each correlation and categorize them into four levels, i.e. No correlation, low correlation, medium correlation and high correlation. Then the evaluation results can be averaged and mapped into a range such as [0−4] representing the four levels.
In contrast, the correlation between Quality-Station can be calculated based on the previous evaluation results since a station does not impact quality directly. The correlation value (Cmn) of a station Sm with a quality Qn can be calculated using the following Eq. 1:
To better indicate the performance of a certain station for measuring a quality entity, the above correlation can be further transformed into percentage (Pmn) divided by the values of all stations for this quality entity. It can be calculated with the following Eq. 2:
Once the above correlation matrix is completed, the results can be stored into a graph database enabled by semantic modelling. The value of each correlation can be used as a property of a relationship in the graph database. More details will be introduced in the following sections.
4 RMPFQ Application for Semantic-Driven Digital Twin
The proposed RMPFQ model can be used to supported semantic modelling for DT applications. This section first introduces the development of application ontologies based on RMPFQ; and them presents a semantic-driven DT architecture based on the application ontology.
4.1 RMPFQ for Ontology Development
The feasibility of using such a model to develop application ontologies has been verified by previous studies. The aforementioned MPFQ model was used to create the GRACE Ontology (Leitão et al., 2012) aiming to optimize discrete manufacturing processes. In a previous study (Zheng et al., 2020a), the proposed RMPFQ model was adopted to support the development of an application ontology for knowledge management of aircraft assembly system design.
To improve the interoperability, the application ontology needs to follow commonly used upper-level ontologies. In this study, the middle-level IOF-Core ontology1 is adopted as the basis of the application ontology. IOF-Core itself refers to the BFO as the top-level ontology. It contains a set of formally defined vocabularies that can be used for creating application ontologies in the manufacturing domain. Figure 5 illustrates the structure of the application ontology. All the RMPFQ elements can be integrated to predefined classes in IOF-Core.
• The RMPFQ-Resource entities refer to tangible manufacturing resources. Therefore, they can be inserted as sub-classes of the Material Resource in IOF-Core. The Resource defined in IOF-Core has a wider range than manufacturing resources. It includes also intangible resources and human resources.
• The RMPFQ-Material entities can be inserted as sub-classes of Material Artifacts in IOF-Core, which traces back to material entity in BFO.
• The RMPFQ-Process entities cover both Assembly Process and Manufacturing Operation in IOF-Core, which trace back to process in BFO.
• The RMPFQ-Function/Feature entities can be mapped to Product Design, Requirement and Function which are sub-classes of Directive Information Content Entity and Dispostion in IOF-Core. They can further trace back to generically dependent continuant and specifically dependent continuant in BFO.
• The RMPFQ-Quality entities can be directly mapped as subclass quality which is defined in BFO.
The interrelations between RMPFQ elements can be transferred to object properties in the application ontology, such as Process(Pk) − requiresResource → Resource(Ri) and Process(Pk) − relizesFunction → Function(Fm). More specific examples will be introduced in the case study section. The formal definitions and descriptions of the mentioned IOF-Core classes can be found in the source file of the IOF-Core ontology1. It is worth to notice that the IOF-Core ontology is an ongoing project. There are still pending issues to be fixed in the future versions, for example, the location of Product and Resource. They are currently positioned at the same level of BFO entities such as generically dependent continuant and independent continuant. It will be rearranged in the new version which is expected to be released in the near future.
The adoption of IOF-Core and BFO assures the interoperability of the developed application ontology with other ontologies that follows the same top-level ontology. It is worth to mention that BFO is not the only top-level ontology. Other ones such as DOLCE (Borgo et al., 2022) are also widely adopted by many application ontologies. It remains a challenging task to assure interoperability across these top-level ontologies. There are some ongoing efforts aiming to address this challenge by integrating or connecting different top-level ontologies. For example, the OntoCommons project2 aims to create an Ontology Commons EcoSystem (OCES) for data documentation, including a set of ontologies and tools, covering the manufacturing and material domains.
4.2 Semantic-Driven Digital Twin Architecture
To facilitate industrial applications, a semantic-driven digital twin architecture is designed based on the aforementioned application ontology and the proposed RMPFQ model. In a previous study (Zheng et al., 2020c), a multi-agent digital twin architecture for manufacturing processes using the MPFQ model has been proposed. The digital twin architecture in this study, as shown in Figure 6, is an extended version of the previous MPFQ-based model.
As shown in Figure 6, the overall semantic-driven digital twin architecture is divided into real space, virtual space and the connections between them. More specifically, the real space represents the physical manufacturing system in reality; the virtual space includes a data management layer, a model management layer, a service layer and a user interaction layer. The details and functions of each layer are introduced as follows.
• Physical manufacturing system represents the physical elements that compose a manufacturing system, including resources (e.g. machines, fixture, facilities), materials (e.g. raw materials, workpieces, assemblies) and other relevant elements such as the environment of the workshop. The physical elements provide data sources for the virtual space through embedded sensors, measurement equipment and inspection stations and so on.
• Data management layer includes all functions related to data ingesting, integration, storage and analysis etc. It is the core of the proposed semantic-driven architecture. Its main components and functions are introduced as follows:
– Ontology-based graph database: The application ontology is used to create a graph database to integrate all the data related to the digital twin. The adoption of upper-level ontologies such as IOF-Core and BFO enables semantic interoperability among heterogeneous data sources. In terms of development tools, the open source ontology editor Protégé can be used to edit and validate the ontology schema. It supports Web Ontology Language (OWL) and includes deductive classifiers to validate that models. It has an easy connection with agent development frameworks such as Java Agent Development Framework (JADE). The developed application ontology can then be imported to a graph database such as Neo4j3 which provides more capabilities to allow linking different data sources to the ontology classes and object properties. It also makes possible of more advanced queries and reasoning by combining query languages with other programming languages. For example, Neo4j provides the Cypher4 query language whcih can be integrated with Python and Java etc. to perform more complex query and reasoning tasks.
– Data sources: several types of data are involved corresponding to the elements of the proposed RMPFQ model. For a typical manufacturing process, the data about the manufacturing resource, material, features and quality indicators are usually generated on-line by embedded sensors or off-line by external measurement equipment. The process, function and quality requirement data are usually obtained from data repositories of the production management systems like Product Data Management (PDM) or Enterprise Resource Planning (ERP) systems.
– Data storage and sharing: Depending on the demand of the application scenarios, different data storage and sharing solutions can be utilized, such as centralized enterprise data server, private or public cloud storage and decentralized distributed file system etc. Considering the data heterogeneity of a modern company, the system needs to support both structural and non-structural data storage and sharing. There is a trend adopt blockchain and distributed ledger technology to cope with data privacy/security and trust issues during data sharing, especially for inter-enterprise interoperations. In case of large data volumes, distributed peer-to-peer data storage systems like InterPlanetary File System (IPFS) provide proper solutions. Technical details can be found in previous studies (Shangping Wang et al., 2018; Naz et al., 2019; Ordieres-Meré et al., 2019; Zheng et al., 2020b; Sun et al., 2020). To produce the information for desired services, data analysis needs to be conducted with the support of data mining and machine learning technologies, which has been extensively studied in data science field, thus not introduced in this study.
– Data interoperability: to enable the data flow and exchange across different system components, existing standards and specifications need to be considered. A recent report (Meyer et al., 2020) investigated popular standards and specifications adopted by some European manufacturing enterprises, including communication protocols, such as OPC-UA, MQTT, MTconnect, HTTP/REST, Modbus, PPMP, and AMQP etc.; and semantic specifications such as B2MML, CAEX, PLCOpen, COLLADA, AutomationML, MTConnect, and MIMOSA etc.
• Model management layer aims to store and manage different types of virtual models such as product design model, resource model and process model among others. A model manager can be created based on the graph database to provide functions such as version management, traceability management, consistency management, co-design and co-simulation etc. This layer is added to cope with the high complexity of some manufacturing systems following the CDT reference architecture proposed by Zheng et al. (2021). It makes possible of extending a single digital twin model to multiple federated models to cover different hierarchical levels of a complex manufacturing system, for example from a single assembly station to an assembly line and further to the entire factory or multiple factories.
• Service management layer orchestrates and presents different business services such as data-driven services and model-driven services to the end user according to the requirements of the application scenarios. Typical examples of such service include fault diagnosis and prognosis, predictive maintenance, manufacturing process optimization and decision-support for physical entities; and calibration of the parameters of the virtual models during the running to sustain its high performance.
• User interaction layer enables stakeholders to interact with different services provided by the digital twin through certain user interfaces.
As shown in Figure 6, the proposed semantic-driven DT architecture can be mapped to the functional layers of the CDT reference architecture proposed in (Zheng et al., 2021), which was designed based on the Reference Architecture Model Industrie 4.0 (RAMI4.0) (Adolphs et al., 2015).The physical manufacturing system can be mapped to the Physical Entities layer of CDT: and the four virtual layer can be mapped to the Data Ingestion and Processing layer, Model Management layer, Service Management layer, and User Interface layers of CDT correspondingly. There is no Twin Management layer included in the proposed DT architecture because this study currently covers only a single manufacturing system without dealing with multiple DT models.
5 Case Study
In order to demonstrate the feasibility of the proposed RMPFQ model for knowledge modelling, a case study is conducted based on a dummy dataset extracted from an washing machine assembly line. This section first introduces the application scenario. Then it explains the implementation of the RMPFQ model based on this case including the development of an application ontology, the construction of an ontology-based graph database, and semantic-driven services. A short discussion is presented in the end to summarize the application achievements and limitations.
5.1 Application Scenario
An assembly line of washing machine is composed of a set of assembly processes corresponding to different functional units of the machine, such as washing unit, hydraulic unit, drum unit, heat pump unit and chassis unit etc. The data used in this case study are extracted from a real assembly line. The information about the RMPFQ elements has been anonymized and no sensitive data are included. The processes and materials are commonly used in most washing machine assembly lines of different manufacturers.
As shown in Table 1, this case study involves seven entities of material, process and function, as well as five entities of resource, quality and station. Most of them are extracted from the drum unit assembly process. The relationships among these entities can be identified according to the RMPFQ model and inserted to the application ontology. Some of the relations are illustrated in Figure 7. The impacts of RMPF entities on quality and stations can be evaluated using the correlation matrix as introduced previously. More details will be introduced in the following sections.
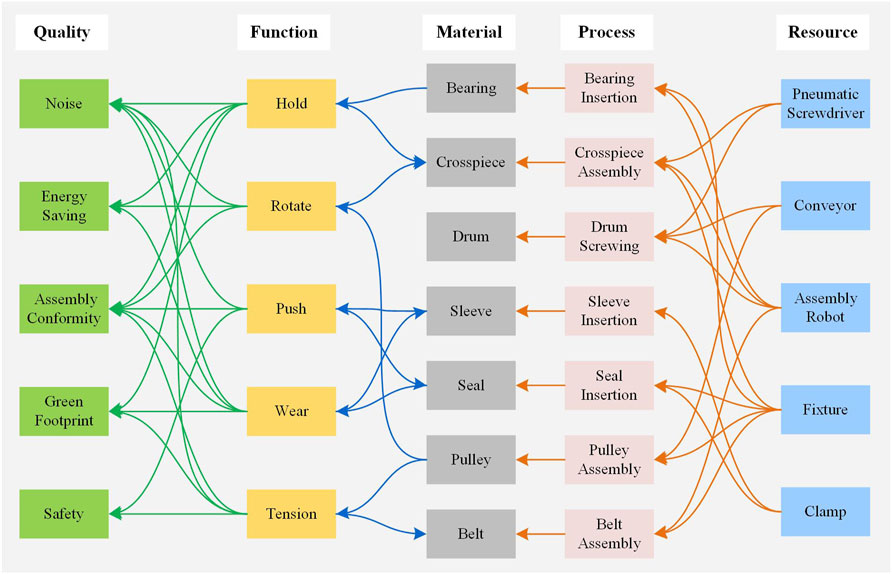
FIGURE 7. Exemplary RMPFQ elements and their relationships (the meaning of lines are the same as in Figure 2)
5.2 Implementation and Results
5.2.1 Development of Application Ontology
An application ontology is developed based on the IOF-Core ontology and the RMPFQ modelling approach for the case study. As shown in Figure 5, based on the BFO framework, the IOF-Core ontology defines a set of commonly used vocabularies in different industry. According to the application scenario, new classes and individuals, such as the aforementioned RMPFQ elements, can be added to the IOF-Core ontology to create a more specific application ontology.
The Protégé software is used to support ontology development. The source code of the IOF-Core ontology is open available1, which can be imported to Protégé and used as basis to create the application ontology. Some of the main classes of the application ontology related to the case study are shown in Figure 8. The source file of the application ontology is available online5.
As shown in Figure 8, the classes on the left are mostly defined in IOF-Core which provides the basic structure of the application. New classes corresponding to the RMPFQ elements and stations related to the application scenario are added as shown in the right side of Figure 8.
5.2.2 Ontology-Based Graph Database
The developed application ontology is used as basis to construct a knowledge graph enabled by Neo4j graph database. It can be deployed locally or on a cloud server to enable remote access by different stakeholders. Neo4j provides a plugin named Neosemantics6, which enables using RDF data in Neo4j graph database. It allows importing and exporting ontologies in various formats, such as OWL, RDF, XML, and Turtle etc. Once imported to Neo4j, different querying and reasoning can be executed based on tailored query conditions and reasoning rules.
Some of the entities listed in Table 1 and their interrelationships are presented in Figure 9. The figure is generated by the Neo4j Browser plugin. As shown in Figure 9, all the entities in Neo4j can be categorized into Node (colored circles) and Relationship (arrow lines). Different properties can be added to each of the nodes and relationships, such as id, name, label, and uri, among others. The relationships in Neo4j can be generally mapped to the object properties in OWL ontologies. The main difference is that it is not possible to define properties for object properties in OWL ontologies. In contrast, Neo4j graph database allows define multiple customized properties for relationships, for example, the required quantity of a material, the cost of a manufacturing resource, the impact weight of a process on a quality indicator and so on. This advantage enables such a graph database to model manufacturing processes more comprehensively and flexibly.
As shown in Figure 9, six types of nodes (corresponding to the RMPFQ elements and stations listed in Table 1) and six types of relationships among the nodes are defined.
• The hasMaterial relationship defines the required materials of an assembly process, for example, (BearingInsertion) − [hasMaterial] → (Bearing).
• The hasResource relationship defines the required resources of an assembly process, for example, (BearingInsertion) − [hasResource] → (Fixture).
• The providesFunction and receivesFunction relationships define the provider and receiver of a function, for example, (Sleeve) − [providesFunction] → (Push) ← [receivesFunction] − (Seal).
• The impactsQuality relationship defines the impact of a RMPF entity on a quality entity, for example, (Pulley) − [impactsQuality] → (Noise).
• The hasCorrelation relationship defines if a RMPF entity can be measured or evaluated at a station, for example, (Crosspiece) − [hasCorrelation] → (VibrationTest).
Based on existing relationships, new relationship can be generated through reasoning according to certain rules. For example, the following rule in natural language: “if a Material (m) has impact on a Quality (q) and this Material (m) can be inspected at a Station (s), then this Quality (q) should has correlation with this Station (s),” can be defined in Neo4j Cypher query language:
The execution result of the above reasoning rule is shown in Figure 10. New relationships between quality and station entities are created according to the rules defined above. Similar rules can be defined for generating other relationships, for example, among processes, functions and stations. After the relationships are defined, certain properties can be added, for example the impact weights of RMPF entities on quality entities. The values of these weights are evaluated by domain experts using the RMPFQ correlation matrix as introduced previously.
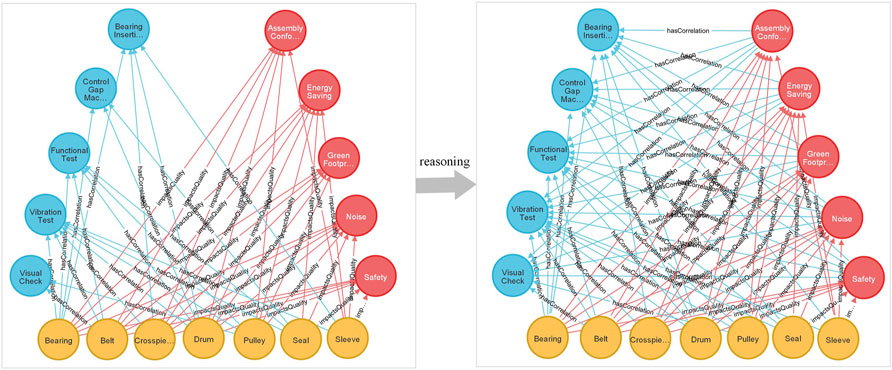
FIGURE 10. An example of generating new relationships between quality and station entities through reasoning.
An exemplary correlation matrix corresponding to the dummy dataset in Table 1 is created as shown in Table 2. All the correlation values between RMPF-Quality, and between RMPF-Station are provided by domain experts from the case owner. The correlation between Quality-Station (the bottom three rows in percentage) are calculated according to Eqs 1, 2. To reduce the size of the table, three entities of each category are selected. The presented values are the average of the results from three experts and some of them are modified to respect data privacy regulations of the case owner.
Once the correlation matrix is defined, the values can be used to update the corresponding relationship properties in the graph database. The Cypher excerpt below demonstrates an example of updating the weights of the relationships between Material (Bearing) - Quality (Noise) and Material (Bearing) - Station (Functional Test).
The Neo4j graph database provides drivers for multiple programming languages, e.g. Python and Java, making it possible to integrate Cypher queries into these languages thus to conduct more complex querying and reasoning tasks. Customized middleware can be developed to automatically execute the aforementioned property updating process.
With all the relevant properties added, the graph database is ready to be deployed for providing tailored semantic-driven services such as process monitoring and quality prediction. Real time data about resource, material and process are collected from inspection stations on the assembly line. After parsing and preprocessing, these data are further analyzed using manual feature extraction and machine learning algorithms. The knowledge captured in the graph database such as the interrelations among different RMPF entities and their influence on certain quality aspects. Summarized results can be presented to different stakeholders to dynamically monitor the assembly process and support decision-makings considering different key performance indicators (Papacharalampopoulos et al., 2020; Juhlin et al., 2021). Due to limited resource, the procedures of creating such semantic-driven services using the captured knowledge is not included in this paper. As a complementary, a previous study (Hu et al., 2022) has introduced the approach of querying information about assembly processes from the ontology-based graph database and use it to support simulations. Graph databases, such as Neo4j in this case, provide Application Programming Interfaces (APIs) enabling the development of tailored middleware for data retrieving and parsing.The retrieved data can be fed to corresponding discrete event simulation (DES) and 3D simulation engines. The simulation results can be further visualized and recommended to the end user.
5.3 Discussion
The objective of this case study is to demonstrate the implementation of the proposed RMPFQ model in industrial scenarios. An application ontology is developed to formalize the RMPFQ model, based on which a graph database is constructed to enable semantic-driven services. The aforementioned correlation matrix is used to quantify the impacts of resource, material and process entities on different quality indicators, which are stored in the graph database as relationship properties. Due to limited resource and efforts, this paper could not cover all aspects of the case study. There are several limitations:
• This paper covers mainly the semantic modelling part of the application case, whereas the topics about data collection and analysis, service generation mechanisms, as well as the result visualization and user interaction are not covered in this study. Existing studies have extensively investigated these topics and many verified solutions are available in the market.
• Due to limited resources, we are not able to implement the proposed framework to a complete industrial case in this study. The dataset used in the case study is a simplified dummy dataset containing limited number of resource, material and process entities. For a complete assembly line, more elements need to be considered and a larger correlation matrix is expected. Therefore, it is difficult to evaluate the performance of the proposed method in real industry applications. One of the future works will be testing the proposed approach in a lab environment with all the core components.
• In industrial applications, a critical task is to decompose a complete product into multiple function units and create function models for each unit thus to identify the relationships among different materials and processes. This task can be performed using methods such as Quality Function Deployment (QFD). In this case study, this task is not included since existing studies have provided sufficient solutions.
6 Conclusion
This paper proposes a knowledge modelling method for manufacturing systems with special focus on the quality perspective. It covers the main factors related to product quality including manufacturing resources, materials, processes, features and functions. To quantify the impacts of these elements on certain quality indicators, a correlation matrix is designed, which takes into account the quality inspection stations on the assembly line. Based on the RMPFQ modelling method, an application ontology structure is created following the IOF-Core middle-level and BFO top-level ontology to ensure cross-domain interoperability. By enriching the ontology with relevant object and relationship properties, a graph database is constructed facilitated by Neo4j platform. Inspired by the recently proposed CDT concept, a semantic-driven digital twin architecture is designed aiming to accelerate the application of the proposed modelling method in industry.
The implementation of the proposed semantic-driven digital twin architecture requires the support of various advanced technologies including semantic modelling, IIoT, machine learning, cloud and distributed computing, among others. This study mainly focused on the semantic modelling topic. There are still some gaps need to be bridged in future. Moreover, it is a challenging task for most small and medium-sized enterprises (SMEs) to implement such new solutions and they need to find the suitable technology suppliers. To address this challenge, several international projects and initiatives have been created involving manufacturing enterprises, relevant technology providers and research organizations aiming to build a platform to provide SMEs with suitable solutions. The work present in this paper is part of such projects focusing on zero-defect manufacturing and autonomous quality in the Industry 4.0. As future work, the proposed model will be further extended and validated in more manufacturing scenarios. Some of the future works are listed below.
• To extend the application scenario to multiple system levels, i.e. from a single assembly line to multiple connected lines, and further to include inter-organizational manufacturing systems such as the machining processes of materials and components from suppliers.
• To integrate multiple lifecycle phases such as product and system design, operation and maintenance etc. As an example, an application ontology was developed based on the proposed RMPFQ model targeting at the design phase of an aircraft assembly system (Zheng et al., 2020a).
• To explore the application of the proposed model in more semantic-driven services enabled by ontology engineering and graph databases.
• To integrate relevant technologies for implementing the proposed semantic-driven digital twin architecture thus to push forward the current digital twin to the cognitive digital twin paradigm.
Data Availability Statement
The original contributions presented in the study are included in the article/Supplementary Material, further inquiries can be directed to the corresponding author.
Author Contributions
XZ, PP, CT, and DK conceived of the presented idea and developed the theory. XZ implemented the idea with enabling technologies and wrote the manuscript with the support of JL, PP and CT provided information about the case study. All authors discussed the results and contributed to the final manuscript.
Funding
This study is supported by the EU Commission within the research projects QU4LITY Digital Reality in Zero Defect Manufacturing (EU H2020 825030) and FACTLOG-Energy-aware Factory Analytics for Process Industries (EU H2020 869951). Open access funding provided by École Polytechnique Fédérale de Lausanne.
Conflict of Interest
Author PP and CT were employed by Whirlpool Europe S. R .L.
The remaining authors declare that the research was conducted in the absence of any commercial or financial relationships that could be construed as a potential conflict of interest.
Publisher’s Note
All claims expressed in this article are solely those of the authors and do not necessarily represent those of their affiliated organizations, or those of the publisher, the editors and the reviewers. Any product that may be evaluated in this article, or claim that may be made by its manufacturer, is not guaranteed or endorsed by the publisher.
Footnotes
1https://github.com/NCOR-US/IOF-BFO.
4https://neo4j.com/developer/cypher/.
5https://github.com/zhengxiaochen/rmpfq_ontology.
6https://github.com/neo4j-labs/neosemantics.
References
Abburu, S., Berre, A. J., Jacoby, M., Roman, D., Stojanovic, L., and Stojanovic, N. (2020a). “Cognitive Digital Twins for the Process Industry,” in Proceeding of the COGNITIVE 2020, The Twelfth International Conference on Advanced Cognitive Technologies and Applications, Nice, France, October 2020 (Nice, France: Think Mind), 68–73.
Abburu, S., Berre, A. J., Jacoby, M., Roman, D., Stojanovic, L., and Stojanovic, N. (2020b). “Cognitwin-hybrid and Cognitive Digital Twins for the Process Industry,” in Proceeding of the 2020 IEEE International Conference on Engineering, Technology and Innovation (ICE/ITMC), Cardiff, UK, June 2020 (IEEE), 1–8. doi:10.1109/ice/itmc49519.2020.9198403
Adl, A. E. (2016). The Cognitive Digital Twins: Vision, Architecture Framework and Categories. Cambridge, MA, United States: Technical Report.
Adolphs, P., Bedenbender, H., Dirzus, D., Ehlich, M., Epple, U., Hankel, M., et al. (2015). Reference Architecture Model Industrie 4.0 (Rami4. 0). ZVEI and VDI, Status report. Online report.
Al Faruque, M. A., Muthirayan, D., Yu, S.-Y., and Khargonekar, P. P. (2021). “Cognitive Digital Twin for Manufacturing Systems,” in Proceeding of the 2021 Design, Automation & Test in Europe Conference & Exhibition (DATE), Grenoble, France, Feb. 2021 (IEEE), 440–445. doi:10.23919/date51398.2021.9474166
Ali, M. I., Patel, P., Breslin, J. G., Harik, R., and Sheth, A. (2021). Cognitive Digital Twins for Smart Manufacturing. IEEE Intell. Syst. 36, 96–100. doi:10.1109/mis.2021.3062437
Anjum, N., Harding, J. A., Young, R. I., and Case, K. (2012). Manufacturability Verification through Feature-Based Ontological Product Models. Proc. Institution Mech. Eng. Part B J. Eng. Manuf. 226, 1086–1098. doi:10.1177/0954405412437125
Arp, R., and Smith, B. (2008). Function, Role, and Disposition in Basic Formal Ontology. Nat. Preced., 1941 1. doi:10.1038/npre.2008.1941.1
Banerjee, A., Dalal, R., Mittal, S., and Joshi, K. P. (2017). Generating Digital Twin Models Using Knowledge Graphs for Industrial Production Lines. New York, United States: UMBC Information Systems Department.
Borgo, S., Ferrario, R., Gangemi, A., Guarino, N., Masolo, C., Porello, D., et al. (2022). Dolce: A Descriptive Ontology for Linguistic and Cognitive Engineering. Appl. Ontol. 17, 1–25. doi:10.3233/ao-210259
Boschert, S., Heinrich, C., and Rosen, R. (2018). “Next Generation Digital Twin,” in Proc. Tmce (Spain: Las Palmas de Gran Canaria), 209–218.
Calero, C., Ruiz, F., and Piattini, M. (2006). Ontologies for Software Engineering and Software Technology. Springer Science & Business Media.
Chavarría-Barrientos, D., Batres, R., Wright, P. K., and Molina, A. (2018). A Methodology to Create a Sensing, Smart and Sustainable Manufacturing Enterprise. Int. J. Prod. Res. 56, 584–603. doi:10.1080/00207543.2017.1386333
Detzner, A., and Eigner, M. (2018). “A Digital Twin for Root Cause Analysis and Product Quality Monitoring,” in DS 92: Proceedings of the DESIGN 2018 15th International Design Conference, 1547–1558. doi:10.21278/idc.2018.0418
Ding, K., Chan, F. T. S., Zhang, X., Zhou, G., and Zhang, F. (2019). Defining a Digital Twin-Based Cyber-Physical Production System for Autonomous Manufacturing in Smart Shop Floors. Int. J. Prod. Res. 57, 6315–6334. doi:10.1080/00207543.2019.1566661
El Kadiri, S., and Kiritsis, D. (2015). Ontologies in the Context of Product Lifecycle Management: State of the Art Literature Review. Int. J. Prod. Res. 53, 5657–5668. doi:10.1080/00207543.2015.1052155
Fariz Saracevic, I. (2017). Cognitive Digital Twin. Technical Report. Event held in Bosnia 2017 (Online report).
Feilmayr, C., and Wöß, W. (2016). An Analysis of Ontologies and Their Success Factors for Application to Business. Data & Knowl. Eng. 101, 1–23. doi:10.1016/j.datak.2015.11.003
Fernández, F., Sánchez, Á., Vélez, J. F., and Moreno, A. B. (2019). “Symbiotic Autonomous Systems with Consciousness Using Digital Twins,” in International Work-Conference on the Interplay between Natural and Artificial Computation (Springer), 23–32. doi:10.1007/978-3-030-19651-6_3
Foehr, M., Jäger, T., Turrin, C., Petrali, P., Pagani, A., and Leitão, P. (2013a). Implementation of a Methodology for Consideration of Product Quality within Discrete Manufacturing. IFAC Proc. Vol. 46, 863–868. doi:10.3182/20130619-3-ru-3018.00181
Foehr, M., Jäger, T., Turrin, C., Petrali, P., Pagani, A., and Leitão, P. (2013b). “Methodology for Consideration of System Quality within Manufacturing,” in Proceeding of the 2013 IEEE International Systems Conference (SysCon), Orlando, FL, USA, April 2013 (IEEE), 553–558. doi:10.1109/syscon.2013.6549936
Gibovic, D., and de Ciurana, J. (2008). Introduction and Applications of Din 8580. Girona, Spain: University of Girona, 978–984.
Gockel, B., Tudor, A., Brandyberry, M., Penmetsa, R., and Tuegel, E. (2012). “Challenges with Structural Life Forecasting Using Realistic Mission Profiles,” in Proceeding of the 53rd AIAA/ASME/ASCE/AHS/ASC structures, structural dynamics and materials conference 20th AIAA/ASME/AHS adaptive structures conference 14th AIAA, Honolulu, Hawaii, April 2012, 1813. doi:10.2514/6.2012-1813
Gómez-Berbís, J. M., and de Amescua-Seco, A. (2019). “Sedit: Semantic Digital Twin Based on Industrial Iot Data Management and Knowledge Graphs,” in International Conference on Technologies and Innovation (Springer), 178–188. doi:10.1007/978-3-030-34989-9_14
Gómez-Pérez, A., and Suárez-Figueroa, M. C. (2009). “Neon Methodology for Building Ontology Networks: a Scenario-Based Methodology,” in International Conference on SOFTWARE, SERVICES and SEMANTIC TECHNOLOGIES (Sofia, Bulgaria: Demetra EOOD), 160.
Grieves, M. (2014). Digital Twin: Manufacturing Excellence through Virtual Factory Replication. White Pap. 1, 1–7.
Hildebrandt, C., Köcher, A., Küstner, C., López-Enríquez, C.-M., Müller, A. W., Caesar, B., et al. (2020). Ontology Building for Cyber-Physical Systems: Application in the Manufacturing Domain. IEEE Trans. Autom. Sci. Eng. 17, 1266–1282. doi:10.1109/tase.2020.2991777
Hu, X., Arista, R., Zheng, X., Lentes, J., Sorvari, J., Lu, J., et al. (2022). Ontology-based System to Support Industrial System Design for Aircraft Assembly. IFAC-PapersOnLine 55, 175–180. doi:10.48550/ARXIV.2204.10636
IOF (2021). IOF Technical Principles. Technical Report. Available at: https://www.industrialontologies.org/technical-principles/.
Jinjiang Wang, J., Ma, Y., Zhang, L., Gao, R. X., and Wu, D. (2018). Deep Learning for Smart Manufacturing: Methods and Applications. J. Manuf. Syst. 48, 144–156. doi:10.1016/j.jmsy.2018.01.003
Juhlin, P., Schlake, J.-C., Janka, D., and Hawlitschek, A. (2021). “Metamodeling of Cyber-Physical Production Systems Using Automationml for Collaborative Innovation,” in Proceeding of the 2021 26th IEEE International Conference on Emerging Technologies and Factory Automation (ETFA), Vasteras, Sweden, Sept. 2021 (IEEE), 1–4. doi:10.1109/etfa45728.2021.9613560
Kharlamov, E., Martin-Recuerda, F., Perry, B., Cameron, D., Fjellheim, R., and Waaler, A. (2018). “Towards Semantically Enhanced Digital Twins,” in Proceeding of the 2018 IEEE International Conference on Big Data (Big Data), Seattle, WA, USA, Dec. 2018 (IEEE), 4189–4193. doi:10.1109/bigdata.2018.8622503
Knapp, G. L., Mukherjee, T., Zuback, J. S., Wei, H. L., Palmer, T. A., De, A., et al. (2017). Building Blocks for a Digital Twin of Additive Manufacturing. Acta Mater. 135, 390–399. doi:10.1016/j.actamat.2017.06.039
Kokar, M. M., and Endsley, M. R. (2012). Situation Awareness and Cognitive Modeling. IEEE Intell. Syst. 27, 91–96. doi:10.1109/mis.2012.61
Leitão, P., Rodrigues, N., Turrin, C., Pagani, A., and Petrali, P. (2012). “Grace Ontology Integrating Process and Quality Control,” in Proceeding of the IECON 2012-38th Annual Conference on IEEE Industrial Electronics Society, Montreal, QC, Canada, Oct. 2012 (IEEE), 4348–4353. doi:10.1109/iecon.2012.6389189
Lemaignan, S., Siadat, A., Dantan, J.-Y., and Semenenko, A. (2006). “Mason: A Proposal for an Ontology of Manufacturing Domain,” in Proceeding of the IEEE Workshop on Distributed Intelligent Systems: Collective Intelligence and Its Applications (DIS’06), Prague, Czech Republic, June 2006 (IEEE), 195–200.
Lu, J., Zheng, X., Gharaei, A., Kalaboukas, K., and Kiritsis, D. (2020). “Cognitive Twins for Supporting Decision-Makings of Internet of Things Systems,” in Proceedings of 5th International Conference on the Industry 4.0 Model for Advanced Manufacturing (Springer), 105–115. doi:10.1007/978-3-030-46212-3_7
Meyer, O., Knaak, C., and Ewald, T. (2020). D2.8 Standards Compliance and Interoperability Specification. Technical Report. Available at: https://ec.europa.eu/research/participants/documents/downloadPublic?documentIds=080166e5d401e605&appId=PPGMS.
Mourtzis, D., Angelopoulos, J., and Panopoulos, N. (2021). Equipment Design Optimization Based on Digital Twin under the Framework of Zero-Defect Manufacturing. Procedia Comput. Sci. 180, 525–533. doi:10.1016/j.procs.2021.01.271
Naz, M., Al-zahrani, F. A., Khalid, R., Javaid, N., Qamar, A. M., Afzal, M. K., et al. (2019). A Secure Data Sharing Platform Using Blockchain and Interplanetary File System. Sustainability 11, 7054. doi:10.3390/su11247054
Negri, E., Fumagalli, L., Macchi, M., and Garetti, M. (2015). “Ontology for Service-Based Control of Production Systems,” in IFIP International Conference on Advances in Production Management Systems (Springer), 484–492. doi:10.1007/978-3-319-22759-7_56
Ordieres-Meré, J., Villalba-Díez, J., and Zheng, X. (2019). Challenges and Opportunities for Publishing Iiot Data in Manufacturing as a Service Business. Procedia Manuf. 39, 185–193. doi:10.1016/j.promfg.2020.01.308
O’Sullivan, A., and Sheffrin, S. M. (2007). Prentice Hall Economics: Principles in Action. Boston, United States: Pearson/Prentice Hall.
Papacharalampopoulos, A., Giannoulis, C., Stavropoulos, P., and Mourtzis, D. (2020). A Digital Twin for Automated Root-Cause Search of Production Alarms Based on Kpis Aggregated from Iot. Appl. Sci. 10, 2377. doi:10.3390/app10072377
Psarommatis, F. (2021). A Generic Methodology and a Digital Twin for Zero Defect Manufacturing (Zdm) Performance Mapping towards Design for Zdm. J. Manuf. Syst. 59, 507–521. doi:10.1016/j.jmsy.2021.03.021
Psarommatis, F., May, G., Dreyfus, P.-A., and Kiritsis, D. (2020). Zero Defect Manufacturing: State-Of-The-Art Review, Shortcomings and Future Directions in Research. Int. J. Prod. Res. 58, 1–17. doi:10.1080/00207543.2019.1605228
Sanfilippo, E., Terkaj, W., and Borgo, S. (2019). “Resources in Manufacturing,” in Proceeding of the 10th International Workshop on Formal Ontologies meet Industry (FOMI), Graz, Austria.
Schleich, B., Anwer, N., Mathieu, L., and Wartzack, S. (2017). Shaping the Digital Twin for Design and Production Engineering. CIRP Ann. 66, 141–144. doi:10.1016/j.cirp.2017.04.040
Seshadri, B. R., and Krishnamurthy, T. (2017). “Structural Health Management of Damaged Aircraft Structures Using Digital Twin Concept,” in Proceeding of the 25th aiaa/ahs adaptive structures conference, Grapevine, Texas, January 2017, 1675. doi:10.2514/6.2017-1675
Shangping Wang, S., Zhang, Y., and Zhang, Y. (2018). A Blockchain-Based Framework for Data Sharing with Fine-Grained Access Control in Decentralized Storage Systems. Ieee Access 6, 38437–38450. doi:10.1109/access.2018.2851611
Stavropoulos, P., and Mourtzis, D. (2022). “Digital Twins in Industry 4.0,” in Design and Operation of Production Networks for Mass Personalization in the Era of Cloud Technology (Elsevier), 277–316. doi:10.1016/b978-0-12-823657-4.00010-5
Sun, S., Zheng, X., Villalba-Díez, J., and Ordieres-Meré, J. (2020). Data Handling in Industry 4.0: Interoperability Based on Distributed Ledger Technology. Sensors 20, 3046. doi:10.3390/s20113046
Tao, F., Zhang, M., Cheng, J., and Qi, Q. (2017). Digital Twin Workshop: a New Paradigm for Future Workshop. Comput. Integr. Manuf. Syst. 23, 1–9. doi:10.13196/j.cims.2017.01.001
Tao, F., Zhang, M., Liu, Y., and Nee, A. Y. C. (2018). Digital Twin Driven Prognostics and Health Management for Complex Equipment. Cirp Ann. 67, 169–172. doi:10.1016/j.cirp.2018.04.055
Wang, L., Törngren, M., and Onori, M. (2015). Current Status and Advancement of Cyber-Physical Systems in Manufacturing. J. Manuf. Syst. 37, 517–527. doi:10.1016/j.jmsy.2015.04.008
Wang, J., Ye, L., Gao, R. X., Li, C., and Zhang, L. (2019). Digital Twin for Rotating Machinery Fault Diagnosis in Smart Manufacturing. Int. J. Prod. Res. 57, 3920–3934. doi:10.1080/00207543.2018.1552032
Zheng, X., Lu, J., Arista, R., Hu, X., Lentes, J., Ubis, F., et al. (2020a). “Development of an Application Ontology for Knowledge Management to Support Aircraft Assembly System Design,” in FOMI 2021: 11th International Workshop on Formal Ontologies meet Industry, held at JOWO 2021: Episode VII The Bolzano Summer of Knowledge, Bolzano, Italy, September 2021.
Zheng, X., Lu, J., Sun, S., and Kiritsis, D. (2020b). “Decentralized Industrial Iot Data Management Based on Blockchain and Ipfs,” in IFIP International Conference on Advances in Production Management Systems (Springer), 222–229. doi:10.1007/978-3-030-57997-5_26
Zheng, X., Psarommatis, F., Petrali, P., Turrin, C., Lu, J., and Kiritsis, D. (2020c). A Quality-Oriented Digital Twin Modelling Method for Manufacturing Processes Based on a Multi-Agent Architecture. Procedia Manuf. 51, 309–315. doi:10.1016/j.promfg.2020.10.044
Keywords: digital twin, semantic modelling, ontology, assembly process, zero defect manufacturing
Citation: Zheng X, Petrali P, Lu J, Turrin C and Kiritsis D (2022) RMPFQ: A Quality-Oriented Knowledge Modelling Method for Manufacturing Systems Towards Cognitive Digital Twins. Front. Manuf. Technol. 2:901364. doi: 10.3389/fmtec.2022.901364
Received: 21 March 2022; Accepted: 04 May 2022;
Published: 24 May 2022.
Edited by:
Hongbae Jun, Hongik University, South KoreaReviewed by:
Panagiotis Stavropoulos, University of Patras, GreeceNikos Panopoulos, University of Patras, Greece
Maria Chiara Magnanini, Politecnico di Milano, Italy
Copyright © 2022 Zheng, Petrali, Lu, Turrin and Kiritsis. This is an open-access article distributed under the terms of the Creative Commons Attribution License (CC BY). The use, distribution or reproduction in other forums is permitted, provided the original author(s) and the copyright owner(s) are credited and that the original publication in this journal is cited, in accordance with accepted academic practice. No use, distribution or reproduction is permitted which does not comply with these terms.
*Correspondence: Xiaochen Zheng, eGlhb2NoZW4uemhlbmdAZXBmbC5jaA==