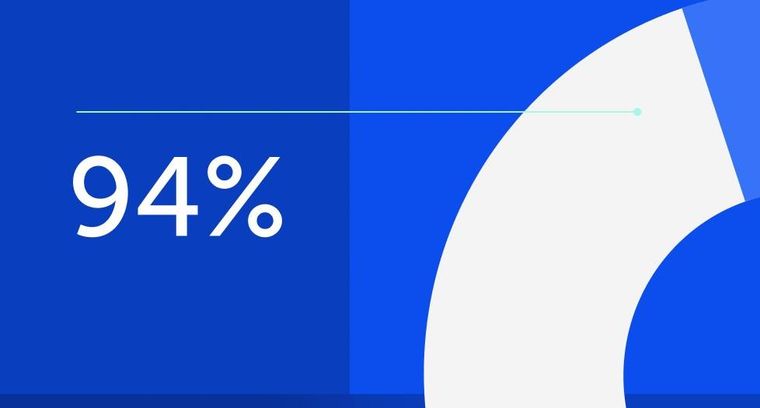
94% of researchers rate our articles as excellent or good
Learn more about the work of our research integrity team to safeguard the quality of each article we publish.
Find out more
ORIGINAL RESEARCH article
Front. Microbiol., 17 August 2023
Sec. Microbiological Chemistry and Geomicrobiology
Volume 14 - 2023 | https://doi.org/10.3389/fmicb.2023.1238853
This article is part of the Research TopicBioleaching and Biorecovery of Critical Raw Materials from Secondary SourcesView all 5 articles
The European Green Deal is proposed as the EU’s strategy to achieve climate neutrality. One key point is decoupling economic growth from resource use and shifting to a circular economy. Therefore, a circular economy of production processes is of high importance (European Commission, 2019). For example, by-products such as blast furnace dust are generated in the steel industry, containing valuable heavy metals such as zinc (Zn). Zn is an essential trace element for microorganisms, animals, humans, and plants. Zn is also the fourth most used metal in the world (e.g., in the galvanizing process) and plays a critical role in renewable energy technologies by preventing solar panels or wind turbines from rusting (International Zinc Association, 2022). Therefore, the recycling of Zn is in high demand to meet the Green Deal goals to minimize CO2 emissions and strengthen a circular economy.
In particular, biohydrometallurgical approaches that use microbes to extract metals from waste are becoming increasingly popular. Earlier bioleaching applications on primary sulfide ores are now being applied to wastes. Efficient solubilization of metals, such as iron (Fe), copper (Cu), or Zn, from secondary resources (e.g., waste incineration ashes and slags) by microbial activity has been recently reported (Kremser et al., 2021). Furthermore, the bioleaching of e-wastes, such as printed circuit boards (Yang et al., 2017; Utimura et al., 2019; Andrade et al., 2022) has been intensively investigated. The bioleaching of metal oxides is mainly accomplished by bacterial sulfuric acid production, Fe3+ regeneration, and the secretion of complexing agents (Kremser et al., 2020). Still, a crucial step after bioleaching is the metal recovery from the bioleachate.
Various metal recovery methods, such as biosorption, selective precipitation, electrowinning, or bioelectrochemical systems, are currently under investigation (Işıldar et al., 2019). Bioelectrochemical systems are an environmentally friendly platform technology for various applications such as wastewater treatment (Liu et al., 2004), hydrogen production (Hasibar et al., 2020), or the capture and conversion of CO2 into valuable products (Spiess et al., 2022).
Electroactive microorganisms employed in the anode chamber of bioelectrochemical systems can oxidize organic sources such as wastewater while generating an electrical current that can drive, in whole or in part (depending on the reduction potential), metal reduction at the cathode. Various metals such as chromium (Cr), cobalt (Co), nickel (Ni), Cu, or Zn have been investigated for their removal and recovery from metal-containing waste streams due to their potential toxic and carcinogen effects and to avoid environmental contamination (Nancharaiah et al., 2015). For instance, Cu (+0.34 V vs. SHE) was recovered at high rates with a microbial fuel cell (MFC) by concomitantly generating a current density of 23 A m−2 (Motos et al., 2015). On the other hand, to recover Zn (−0.76 V vs. SHE), a potential must be applied at microbial electrolysis cells (MEC) to enable cathodic reactions (Modin et al., 2017).
However, MECs offer several advantages compared to conventional Zn electrolysis. They can be operated at much lower energy consumption, cheaper anode materials can be used, and wastewater can be treated simultaneously. Furthermore, several studies have focused on the bioelectrochemical treatment and purification of acid mine drainage consisting of metal-rich solutions formed by the oxidative dissolution of sulfide minerals exposed to air, humidity, and acidophilic microbes during mining.
Recently, the reduction of Cu2+ to Cu0 from acid mine drainage in MFC mode, and also Fe, Ni, and tin (Sn) in subsequent MEC operation by applying a cathode potential of −0.7 V vs. Ag/AgCl, has been demonstrated (Leon-Fernandez et al., 2021). In another study, the complete precipitation of aluminum (Al), Zn, Cu, arsenic (As), Cr and almost complete precipitation of Fe, magnesium (Mg), calcium (Ca), manganese (Mn), Ni, Co, lead (Pb), and cadmium (Cd) was achieved using a two-cell bioelectrochemical process with continuous feed (Pozo et al., 2017). Furthermore, high sulfate and Zn concentrations were removed from acid wastewater by conversion of dissolved Zn ions into insoluble zinc sulfide and zinc hydroxide using an acidophilic and autotropic biocathode dominated by Desulfovibrio spp. (Teng et al., 2016).
However, no study has investigated the recovery of Zn from metal-laden bioleachate using a MEC. This study aimed to show the potential of combining both processes (bioleaching and bioelectrochemistry) to create a fully biotechnological metal recovery process. Furthermore, the Zn recovery efficiency from bioleachate as a catholyte was compared to the Zn recovery efficiency from the control zinc sulfate solution and the energy consumption under both conditions was evaluated. Furthermore, the anodic composition of the MEC was characterized after three months of operation. Additionally, selective metal precipitation of the bioleachate was investigated, and base consumption was monitored.
The experiments were performed in a two-chamber H-cell separated by a pretreated proton exchange membrane, as described elsewhere (Spiess et al., 2021). The working volume of each chamber was 220 mL. Carbon felt (projected surface area 12.5 cm2, AlfaAesar, Heysham, United Kingdom) was pretreated with isopropanol and hydrogen peroxide and used as anode material, as previously described (Spiess et al., 2021). Graphite foil (projected surface area 12.5 cm2, 99.8%, AlfaAesar, Heysham, United Kingdom) was used as cathode material, and titanium wires (0.25 mm, Alfa Aesar, Heysham, United Kingdom) were used to enable the external electrical connection. Each chamber was equipped with an Ag/AgCl reference electrode (3 M NaCl, +209 mV vs. SHE).
The anode chamber was filled with 200 mL of nutrient medium (pH 7.2) consisting of the following components (per liter): 3 g KH2PO4, 2.5 g K2HPO4, 0.13 g NaCl, 0.31 g NH4Cl, 6 g NaHCO3, 0.04 g MgSO4·7H2O, 12.5 mL trace element solution SL 10 (DSMZ 320), and 5 mL vitamin solution (DSMZ 141). Carbon sources with a chemical oxygen demand (COD) concentration of 675 mg L−1 were added to simulate wastewater consisting of the following ingredients (per liter): 0.138 g peptone/trypsin, 0.075 g yeast extract, 0.088 g sodium acetate, and 0.37 g glucose monohydrate. The nutrient medium thus prepared is hereafter referred to as synthetic wastewater. Further, the anode chamber was inoculated with 20 mL sewage sludge from a wastewater treatment plant, from which solid particles were first removed by centrifugation at 2,150 g for 10 min. The anode chamber was maintained under anaerobic conditions by flushing with pure CO2 at the beginning and after each feeding. A potential of −100 mV vs. Ag/AgCl (3 M NaCl) was applied at the anode using a SP-150 potentiostat (BioLogic Sciences Instruments, Seyssinet-Pariset, France).
The cathode chamber was filled with 220 mL of 36 mM phosphate buffer (pH 7.2) and a stable current flow was observed after 2 months. The cathode potential was monitored regularly with a Voltcraft VC880 multimeter (Hirschau, Germany). During the two-month adaptation period, the anode chamber was supplied with synthetic wastewater twice a week so that 50% of the anolyte and 100% of the catholyte were replaced at each feeding. An adaptation period was required to acclimate microorganisms on MEC conditions and lasted until a stable current flow was observed. All experiments were performed at room temperature with constant stirring of the anolyte and catholyte at 70 rpm with an IKA® RCT basic magnetic stirrer (Staufen, Germany).
After the adaptation period, the cathode solution was replaced with 220 mL of 7.65 mM zinc sulfate heptahydrate (corresponding to 0.5 g L−1 Zn2+) with pH adjusted to 3.0 by 1 M sulfuric acid. The electric conductivity of the control zinc sulfate solution thus prepared was 1.6 mS cm−1. MEC feeding took place twice a week. At each feeding, 50% of the anolyte was replaced by fresh synthetic wastewater. Simultaneously 100% of the catholyte was exchanged by a new zinc sulfate solution, and the graphite electrode was renewed by removing Zn depositions with 2 M HCl. Before each feeding, samples were collected from the anode and cathode chambers for further analysis. After 12 cycles, 220 mL of diluted filter-sterilized bioleachate was added to the cathode chamber instead of the zinc sulfate solution, and the experiments continued under the same conditions. Prior to use, the bioleachate was filtrated through a Nalgene bottle-top filter with a polyethersulfone membrane (Thermo Fisher Scientific, Waltham, United States) with a pore size of 0.22 μm. Afterwards, the filter-sterilized bioleachate (pH 3) was diluted with deionized water to achieve the same Zn concentrations as the zinc sulfate solution. After dilution, the filter-sterilized bioleachate had a pH of 3.4. Figure 1 depicts the laboratory setup of the MEC for Zn recovery operated in batch mode. The cathode chamber (on the right) was filled with filter-sterilized bioleachate.
Figure 1. Laboratory setup of the MEC for Zn recovery. A bioanodic chamber, oxidizing synthetic wastewater (left) and generating electrons, coupled to a cathode chamber, reducing metals from the bioleachate (right).
The experiments were carried out as an indirect bioleaching approach. In the first step, the microorganisms Acidithiobacillus thiooxidans (DSM 504) and Acidithiobacillus ferrooxidans (DSM 14882T) purchased from the German Collection of Microorganisms and Cell Cultures (DSMZ, Braunschweig, Germany) were cultivated in basal salts containing 10 g L−1 elemental sulfur as previously described (Wakeman et al., 2008) to produce sulfuric acid. In the second step, the produced biogenic sulfuric acid was filter-sterilized and used as a leaching agent to treat blast furnace dust from steel industry. Both steps were conducted at 30°C, 160 rpm stirring speed, and 75 L h−1 aeration. During indirect leaching, the average measured redox potential was 638 mV vs. SHE.
Selective precipitation was performed in duplicate by adjusting the pH to 4, 5, 6, 7, 8, and 9. The pH values were determined by a 765 Laboratory pH Meter control (Knick Elektronische Messgeräte GmbH & Co. KG, Berlin, Germany). For each pH value, 25 mL of undiluted bioleachate (pH 3) was continuously stirred using an IKA® C-MAG HS7 plate stirrer (Staufen, Germany) while 1 M NaOH was added until the desired pH was reached. Metal concentrations were determined by ICP-MS in the filtrates (0.22 μm) after six-day precipitation.
A COD test was used to determine the amount of degraded organic compounds, and then the COD removal efficiency and anodic coulombic efficiency (CEAn) were calculated as described elsewhere (Spiess et al., 2021).
The Zn recovery efficiency was calculated according to Equation (1), where Zn1 is the Zn concentration in the catholyte before electrolysis, and Zn2 is the Zn concentration in the catholyte after electrolysis.
Further, the coulombic efficiency of the cathode (CEZn) was calculated according to Equation (2), where ΔZn is the recovered amount of Zn (mol), n is the number of electrons needed for the reduction of Zn2+ to Zn0 (2 e−), F is the Faradays constant (96485.3 C mol −1), I represents the recorded current, and t is the time.
The energy consumption (ηE) (kWh kg−1 Zn) was calculated according to Equation (3), where ECell is the cell potential (V), and M is the molar mass of Zn (65.38 g mol −1).
The energy consumption for COD removal (kWh kg−1 COD) was calculated for standard conditions, as previously described (Zeppilli et al., 2019). Statistical analysis was performed using a t-test.
The metal concentrations in liquid samples were measured using an inductively coupled plasma mass spectrometer Agilent 7,900 (Agilent Technologies, Santa Clara, United States), as previously described (Kremser et al., 2021). Briefly, all samples were filter-sterilized and diluted with Milli Q water by a factor of 100 to minimize the matrix effect and to get the best LOD. A solution of Sc (400 g L−1) was used as an internal standard. A set of calibration solutions was prepared for quantification.
For measuring Fe2+ and total Fe, a microplate reader (Infinite 200 PRO, TECAN, Männedorf, Switzerland) using ferrozine solution was used. Prior to the measurements, samples were diluted as required using distilled water at pH 2. First, 228 μL of ferrozine solution was pipetted into a well of a Microplate 96 well-plate (Greiner, Kremsmünster, Austria), then 12 μL of sample was added. After 10 s of shaking, the first photometric measurements were conducted at 562 nm. Hereafter, 45 μL of hydroxylamine hydrochloride solution and 15 μL ammonium acetate buffer was added. After 20 min, the photometric measurement was repeated. Each measurement was conducted as a triplicate.
The bacterial DNA was isolated using the QIAamp BiOstic Bacteremia DNA Kit (Qiagen, Hilden, Germany), according to the manufacturer’s instructions. The highly variable V4 region was amplified with unique barcode primers and sequenced as described previously (Spiess et al., 2021). Briefly, PCR amplification was performed using Platinum II Taq Hot-Start DNA Polymerase (Thermo Fisher Scientific, Waltham, United States), as follows: initial DNA denaturation step at 94°C for 3 min, 35 cycles of DNA denaturation at 94°C for 45 s, annealing at 52°C for 60 s with a 50% thermal ramp, extension at 72°C for 90 s, and a final extension step at 72°C for 10 min. The library was purified by AMPure XP beads (Beckman Coulter, Brea, United States) and sequenced using a MiniSeq System (Illumina, San Diego, United States) with MiniSeq Mid Output Kit (300 cycles). Raw fastq reads were processed in R software (v4.2.2) using the open-source package DADA2 (v1.26) (Callahan et al., 2016). The DECIPHER package was used for multiple alignments with the phangorn package to build a phylogenetic tree, and the phyloseq package was used for subsequent phylogenetic analysis (Vítěz et al., 2020). A summary of all amplicon sequence variants (ASVs) is shown in the Supplementary material. The dataset generated and analyzed in this study is available in the NCBI Sequence Read Archive under project number BioProject ID: PRJNA950388.
Table 1 presents the metal composition of the diluted filter-sterilized bioleachate as prepared for further MEC usage. The bioleachate had the highest metal concentrations of Zn, followed by Al, Fe, Mg, and Mn. Furthermore, the measured electric conductivity of the diluted bioleachate was 3.8 mS cm−1 and the pH was 3.4.
A previous study investigated the thermophilic bioleaching of basic oxygen furnace dust with Acidianus manzaensis at an operation temperature of 64°C (Kölbl et al., 2022). Similar to the metal composition results from the bioleachate under mesophilic conditions in Table 1, the previous study reported high metal concentrations of Fe, Zn, Mn, and Al for the leached solution by A. manzaensis. These findings demonstrate the great potential of bioleaching and metal recovery from secondary waste products such as basic oxygen furnace dust or blast furnace dust.
Figure 2 shows the results of the Zn recovery from zinc sulfate solution (A) and bioleachate (B) over operation time using a MEC. All MEC performance parameters during these experiments are summarized in Table 2. With zinc sulfate solution 100% Zn recovery efficiency at all sampling points was achieved. In comparison, when bioleachate was used as catholyte for the MEC, Zn recovery efficiency fluctuated between 22 and 64%, averaging 41 ± 13%. This difference between the Zn recovery efficiency of zinc sulfate solution and bioleachate was significant (p < 0.001). Therefore, the CEZn was significantly lower with bioleachate (16 ± 3%) than with the zinc sulfate solution (39 ± 2%) (p < 0.001). However, the COD removal efficiency of the bioanode was not significantly different at both conditions, whether using zinc sulfate solution (63 ± 9%) or bioleachate (64 ± 11%) (p > 0.05). Also, the difference between zinc sulfate solution (2.2 ± 0.3 A m−2) and bioleachate (2.0 ± 0.3 A m−2) in current density per projected electrode surface area was insignificant (p > 0.05). As the COD removal efficiency remained stable under both conditions, the difference in calculated CEAn was insignificant for the zinc sulfate solution (76 ± 13%) compared to bioleachate (67 ± 10%) (p > 0.05).
Figure 2. Zn recovery efficiency (blue bars), COD removal efficiency (green bars), and current density (dark blue dots) versus MEC operating time with zinc sulfate solution (A) or bioleachate (B).
Table 2. Monitored performance parameters of MEC operated with zinc sulfate solution or bioleachate.
In a previous study, 98.5% Cu was removed from fly ash leachate using a MFC, and in the second step 95.4% Zn and 98.1% Pb were removed using an electrolysis reactor (Tao et al., 2014). In addition to the higher Zn recovery efficiency compared to this study, the reduction time was also faster (95.4% Zn removal in 10 h). However, in the previous study, a voltage of 6 V was applied to empower the recovery of Zn with an electrolysis reactor, which resulted in a high energy consumption of 450 kWh kg−1 metal. The present study required an energy consumption of 0.7 kWh kg−1 and 2.55 kWh kg−1 to recover Zn from zinc sulfate solution and bioleachate, respectively. Therefore, MECs may present a way to recover Zn from leachates at lower energy demands.
Summarizing, the Zn recovery efficiencies from bioleachate were approximately 60% lower than from the zinc sulfate solution. However, it must be considered that bioleachate has a more complex metal composition compared to the zinc sulfate solution. Therefore, the co-recovery of other metals in the bioleachate was also investigated. Figure 3 shows the concentration trends of the five most abundant metals in the bioleachate during MEC operation. Mg and Mn concentrations remained stable in bioleachate at 162 mg L−1 and 45 mg L−1 (day 4), respectively, and were not recovered during MEC operation. On the other hand, the concentrations of Zn, Al, and Fe in the catholyte decreased during MEC operation. The Zn concentration decreased continuously from 444 mg L−1 (day 0) to 354 mg L−1 (day 2) and finally to 245 mg L−1 (day 4). The Al concentration decreased rapidly from 270 mg L−1 (day 0) to 100 mg L−1 (day 2) and further to 10 mg L−1 (day 4). The Fe concentration decreased much slower than Zn and Al. After four days, 99 mg L−1 Fe from the initial 155 mg L−1 remained in bioleachate.
Figure 3. Trends in the concentration of Zn, Al, Mg, Fe, and Mn in the bioleachate used as catholyte over 4 days of MEC operation. Error bars indicate the standard deviation (n = 6).
The decrease in Fe concentration in the bioleachate could be due to metal reduction at the cathode. The reduction potential of Fe2+/Fe0 is −0.45 V vs. SHE, which is below the reduction potential of −0.76 V vs. SHE for Zn2+/Zn0. Recently, the reduction of Fe3+ to Fe2+ from acid mine drainage in MFC mode and the subsequent reduction of Fe2+ to Fe0 deposited on the cathode in MEC mode has been reported (Leon-Fernandez et al., 2021). The reduction of Fe3+ to Fe2+ took place spontaneously in the first stage (standard reduction potential 0.77 V vs. SHE), but to recover Fe in its elemental form, a potential of −0.7 V vs. Ag/AgCl was applied on the cathode, which led to a 60% Fe decrease after three days of operation (Leon-Fernandez et al., 2021). Similarly, in our experiments, a decrease in the Fe concentration of the bioleachate was observed. Therefore, Fe2+ was likely reduced to Fe0 at the cathode. On the other hand, the decrease in Al concentration in the bioleachate could be explained by precipitation mechanisms. Al3+ possibly precipitated to aluminum hydroxide as the pH increased from 3.4 to 4.4 during the electrolysis. These assumptions are consistent with previously published results (Wei et al., 2005) showing >75% Al precipitation from acid mine drainage when the pH rose from 3.5 to 4.5.
Figure 4 summarizes the recovery efficiencies of Zn, Al, Mg, Fe, and Mn. Al showed the highest recovery efficiency (93 ± 5%), possibly due to the precipitation of aluminum hydroxide. Moderate recovery efficiencies were achieved for Zn (41 ± 13%) and Fe (31 ± 11%) due to a reduction at the cathode. Mn and Mg were recovered with minimal efficiency, 3 ± 5 and 7 ± 6%, respectively.
Figure 4. Average recovery efficiency of Zn, Al, Mg, Fe, and Mn using bioleachate as catholyte in MEC operation. Error bars indicate the standard deviation (n = 12).
The Zn recovery from bioleachate was substantially lower than from zinc sulfate solution because the provided electrons were probably used for competing reactions such as Fe2+/Fe0 reduction. The MEC operation time probably needs to be expanded to increase the efficiency of Zn recovery from bioleachate. As observed earlier, the recovery time depends on the initial concentration and the applied current (Lim et al., 2021).
Table 3 summarizes the average energetic parameters from Zn recovery experiments using zinc sulfate solution or bioleachate of this study compared to literature. The difference between the energy consumptions for Zn recovery from zinc sulfate solution (0.70 kWh kg−1) and bioleachate (2.55 kWh kg−1) was significant (p < 0.001) due to the higher amount of Zn recovered from zinc sulfate solution than bioleachate. In addition, the difference between the average cell voltages (ECell) using zinc sulfate solution (−1.01 V) and bioleachate (−1.39 V) as the catholytes was significant (p < 0.05). On the contrary, the difference between the energy consumption for COD removal (0.20 and 0.22 kWh kg−1 COD) was insignificant (p > 0.05).
The calculated energy consumption of 0.7 kWh kg−1 Zn from zinc sulfate solution was lower compared to 2.4 kWh kg−1 of a previous study (Modin et al., 2017). Similar to this study, the MEC has been previously operated with controlled anode potential, and ZnSO4 served as the source for Zn2+. However, the lower amount of Zn recovered using bioleachate resulted in a higher energy consumption of 2.55 kWh kg−1 Zn. In another study, the electrowinning of Zn from zinc ash leachate was investigated with a PVC cell with an applied current density of 200 A m−2, consisting of an aluminum cathode and an iridium dioxide anode. The zinc-sulfate electrolyte was circulated, and Zn was stripped every 24 h. Compared to the MEC operated with zinc sulfate solution in this study, a five times higher energy consumption (3.51 kWh kg−1) was required to recover Zn with electrowinning (Ramachandran et al., 2004). The higher energy consumption for Zn electrowinning compared to the lower energy consumption using a MEC with zinc sulfate solution (0.70 kWh kg−1) or bioleachate (2.55 kWh kg−1) in this study profiles bioelectrochemical Zn recovery as a desirable candidate compared to electrowinning.
Figure 5 shows the genetic relationships of the anodic microbial community after three months of MEC operation, and Table 4 summarizes the relative abundances of the microbial community composition enriched on the MEC anode. The genus Enterococcus strongly dominated the anodic biofilm with a relative abundance of over 80%. The other four representatives were below 3%. Over 10% were represented by unknown genera or fell below the 1% threshold. The species diversity values obtained are similar to those previously observed under the same experimental conditions (Spiess et al., 2021). E. faecalis is an electroactive Gram-positive bacterium commonly identified on MFC anodes, capable of direct and mediated electron transport (Pankratova et al., 2018). E. faecalis forms dense biofilms in the presence of glucose (Pillai et al., 2004). Since the main carbon source in the synthetic wastewater in this study was glucose, this may explain why Enterococcus dominated the anode after the enrichment from sewage sludge. Similar observations were made when using glucose-rich synthetic wastewater as a substrate in a fully biocatalyzed MEC for methane production (Spiess et al., 2021).
Figure 5. Phylogenetic tree showing the genetic relationships of the anodic microbial community in the MEC. Only the 50 most abundant representatives are shown. The circle color represents phylum taxa, and the circle size corresponds to their abundance (number of reads). The tree is labeled by color-coded representatives identified in the taxa of the genus.
Furthermore, selective metal precipitation from the bioleachate was performed to investigate possible precipitation mechanisms due to the catholyte alkalization during MEC operation. For instance, Al3+ likely has been precipitated as aluminum hydroxide when the catholyte pH increased from 3.4 to 4.4 during MEC operation. Figure 6 shows tubes filled with bioleachate after performing selective precipitation at different pH values. As the pH grew, the proportion of precipitation products increased while the liquid fraction decreased. Furthermore, a color change was noticeable from pH 7, probably caused by the precipitation of Fe and Mn.
The dependence between the most precipitated metals and the base consumption to adjust different pH values in the bioleachate is shown in Figure 7. Fe (14 ± 0.6%) and Al (9 ± 0.5%) started precipitating at pH 4. Almost all Al was precipitated (97 ± 0.1%) with a base consumption of 135 ± 0.6 mL L−1 at pH 5, whereas Zn, Mg, and Mn remained largely in solution (<15% precipitation). This supports our findings that Al3+ probably precipitated as aluminum hydroxide during Zn electrolysis as the pH in the catholyte increased from pH 3.4 to 4.4. Hence, the selective recovery of Al from bioleachate at pH 5 before its filling into the MEC cathode chamber could be used to increase the selectivity of the bioelectrochemical Zn recovery. A further pH increase to pH 6 resulted in the precipitation of 48 ± 1.9% Zn, 100 ± 0.1% Al, 21 ± 1.0% Mg, 48 ± 0.5% Fe and 17 ± 0.7% Mn. Zn and Fe showed an almost simultaneous trend in precipitation from pH 6 to 9. At pH 7, almost all Zn (97 ± 1.0%) and Fe (96 ± 2.4%) were precipitated at a base consumption of 239 ± 3 mL L−1. In contrast, only 37 ± 0.3% Mg and 36 ± 2.3% Mn were precipitated. At pH 8, Zn and Fe precipitated 100%, and a further increase in pH to 9 with a total base consumption of 304 ± 4 mL L−1 resulted in precipitation of 92 ± 3.8% Mg and 99 ± 0.5% Mn.
Figure 7. Dependence of metal precipitation percentage on different pH and base consumption. The five metals with the highest concentrations from Zn, the most abundant one, up to Mn, are shown. Error bars indicate the standard deviation (n = 2).
The selective precipitation experiments revealed almost complete Al precipitation at pH 5, whereas the other metals remained widely dissolved. These findings coincide with a previous study in which 97% Al was recovered at pH 5, and Mn and Fe remained nearly stable in the solution (Kremser et al., 2022). However, the addition of base to adjust pH 5 in this study was substantially higher (135 ± 0.6 mL L−1 1 M NaOH) than in the previous one (46.8 mL L−1 1 M NaOH). However, it must be noted that in the previous study, a synthetic metal solution was used instead of bioleachate, which probably had a higher buffer capacity. At pH 7, more than 95% of Zn and Fe precipitated simultaneously, whereas pH 9 is required to precipitate most of Mg and Mn. These results are consistent with the previously described coprecipitation of Zn2+ and Fe2+ from industrial wastewater at pH 6.5–8.5 (Wang and Chen, 2019). Fe speciation of the used bioleachate in this study revealed a differentiation of 91% Fe2+ and 9% Fe3+ species. As reported earlier, Fe3+ precipitates at pH 3, whereas Fe2+ precipitation needs higher pH-values (Kremser et al., 2022), as also observed in this study. This finding was also supported by the dark blue-green color of the precipitate (Figure 6). The precipitation of metal ions can be influenced by various factors such as temperature (Cao et al., 2009) or initial concentrations. Especially the latter is of great importance because the higher the metal ion’s initial concentration, the lower the pH at which it starts to precipitate (Wang and Chen, 2019), which could explain why 48 ± 1.9% Zn was already precipitated at pH 6. Furthermore, sulfide and hydroxide precipitation mechanisms have previously been distinguished by adding NaOH until pH 4 to precipitate Fe selectively from synthetic metal solution (Santaolalla et al., 2021). Subsequently, Na2S was added to precipitate Cu, Zn, and Ni at pH 6. However, Cu (20.7%) and Ni (9.2%) have coprecipitated with Fe during the first step (Santaolalla et al., 2021).
To increase the selectivity of Zn recovery from bioleachate using MECs, pre-precipitation of Al (approximately at pH 5) by adding NaOH and subsequent filtration before entering the MEC cathode outlines a possible way. Furthermore, impurities such as Fe could be separated from bioleachate by oxidation of Fe2+ to Fe3+ using H2O2 (Wang and Chen, 2019) or biooxidation (Nurmi et al., 2010), followed by Fe3+ precipitation at pH 3 prior to bioelectrochemical Zn recovery. Therefore, to increase the selectivity of metal recovery from bioleachate, a combination of selective precipitation of leachate impurities, such as Al and Fe, with the subsequent operation of a Zn recovering MEC, must be further investigated and carefully evaluated for potential application. In addition, the composition of precipitates and purity of deposited cathode metals should be determined in the future.
This study investigated the recovery of Zn from bioleachate using a MEC for the first time. During Zn recovery, a constant potential of −100 mV vs. Ag/AgCl was applied at a synthetic wastewater-treating bioanode. First, the recovery of Zn from the control zinc sulfate solution and then from bioleachate was examined. Despite decreased Zn concentration from 444 mg L−1 to 245 mg L−1 during MEC operation with bioleachate, the Al concentration dropped from 270 mg L−1 to 10 mg L−1 after four days of operation. The drop in Al concentration was probably due to the precipitation of aluminum hydroxide because of an increase in the catholyte pH from 3.4 to 4.4. As the selective precipitation experiments confirmed, Al is precipitated almost completely at pH 5. Furthermore, during Zn recovery from bioleachate, the simultaneous reduction of Fe was observed. Moreover, the energy consumption for a Zn recovering MEC, whether operated with zinc sulfate solution or bioleachate, was substantially lower than electrowinning. In principle, Zn recovery from bioleachate using a MEC is feasible. Still, lower Zn recovery efficiency (41 ± 13%) and energy consumption (2.55 kWh kg−1) were achieved compared to zinc sulafate solution due to a more complex composition of the bioleachate. After three months of MEC operation, Enterococcus was enriched on the anode with 81.45% from sewage sludge. The predominance of this electroactive species is consistent with MEC operating and growth conditions that include glucose as the primary carbon source.
The datasets presented in this study can be found in online repositories. The names of the repository/repositories and accession number(s) can be found in the article/Supplementary material.
SS: conceptualization, methodology, investigation, visualization, and writing—original draft. JK: data analysis, visualization, and writing—original draft. TV: data acquisition and analysis. LB: providing dust samples and writing—review and editing. CH: investigation. ASC: writing—review and editing. MM: statistical analysis, funding, and writing—review and editing. MH: project administration, supervision, funding, conceptualization, and writing—review and editing. All authors contributed to the article and approved the submitted version.
The project was supported by the European fund for regional development, the program Interreg V-A Austria—Czech Republic, project ATCZ291, OPTIMO (Optimierung einer nachhaltigen Schwefelsäureproduktion für (Bio)Leaching-Prozesse im Abfallsektor). The financial support of the Province Styria and the Styrian Business Promotion Agency (“Zukunftsfonds Steiermark”) within the project INNOMET (PN 1507) is gratefully acknowledged. Further, the authors acknowledge the funding support of K1-MET GmbH, metallurgical competence center. K1-MET is a COMET Centre within the COMET – Competence Centers for Excellent Technologies Program and funded by the Federal Ministry for Climate Action, Environment, Energy, Mobility, Innovation and Technology; the Federal Ministry for Labor and Economy; the provinces Upper Austria, Styria and Tyrol; the Styrian Business Promotion Agency, and the Standortagentur Tyrol. This work was supported by a subsidy for the development of the research institution and by the Masaryk University Program, project no. MUNI/A/1313/2022.
SS, CH, ASC, and MH were employed by K1-MET GmbH. LB was employed by Voestalpine Stahl GmbH.
The remaining authors declare that the research was conducted in the absence of any commercial or financial relationships that could be construed as a potential conflict of interest.
All claims expressed in this article are solely those of the authors and do not necessarily represent those of their affiliated organizations, or those of the publisher, the editors and the reviewers. Any product that may be evaluated in this article, or claim that may be made by its manufacturer, is not guaranteed or endorsed by the publisher.
The Supplementary material for this article can be found online at: https://www.frontiersin.org/articles/10.3389/fmicb.2023.1238853/full#supplementary-material
Andrade, L. M., Botelho Junior, A. B., Rosario, C. G. A., Hashimoto, H., Andrade, C. J., and Tenório, J. A. S. (2022). Copper recovery through biohydrometallurgy route: chemical and physical characterization of magnetic (m), non-magnetic (nm) and mix samples from obsolete smartphones. Bioprocess Biosyst. Eng. 46, 1121–1131. doi: 10.1007/s00449-022-02775-z
Callahan, B. J., McMurdie, P. J., Rosen, M. J., Han, A. W., Johnson, A. J. A., and Holmes, S. P. (2016). DADA2: high-resolution sample inference from Illumina amplicon data. Nat. Methods 13, 581–583. doi: 10.1038/nmeth.3869
Cao, J., Zhang, G., Mao, Z., Fang, Z., and Yang, C. (2009). Precipitation of valuable metals from bioleaching solution by biogenic sulfides. Miner. Eng. 22, 289–295. doi: 10.1016/j.mineng.2008.08.006
European Commission. (2019). The European green Deal. Available at: https://ec.europa.eu/info/sites/default/files/european-green-deal-communication_en.pdf
Hasibar, B., Ergal, İ., Moser, S., Bochmann, G., Rittmann, S. K. M. R., and Fuchs, W. (2020). Increasing biohydrogen production with the use of a co-culture inside a microbial electrolysis cell. Biochem. Eng. J. 164, 107802–107806. doi: 10.1016/j.bej.2020.107802
International Zinc Association. (2022). Zinc recycling 2050 demand + supply. Available at: https://www.zinc.org/wp-content/uploads/sites/30/2022/10/2050-Demand-Supply_VF_11_22.pdf
Işıldar, A., van Hullebusch, E. D., Lenz, M., Du Laing, G., Marra, A., Cesaro, A., et al. (2019). Biotechnological strategies for the recovery of valuable and critical raw materials from waste electrical and electronic equipment (WEEE) – a review. J. Hazard. Mater. 362, 467–481. doi: 10.1016/j.jhazmat.2018.08.050
Kölbl, D., Memic, A., Schnideritsch, H., Wohlmuth, D., Klösch, G., Albu, M., et al. (2022). Thermoacidophilic bioleaching of industrial metallic steel waste product. Front. Microbiol. 13, 1–14. doi: 10.3389/fmicb.2022.864411
Kremser, K., Thallner, S., Schoen, H., Weiss, S., Hemmelmair, C., Schnitzhofer, W., et al. (2020). Stirred-tank and heap-bioleaching of shredder-light-fractions (SLF) by acidophilic bacteria. Hydrometallurgy 193:105315. doi: 10.1016/j.hydromet.2020.105315
Kremser, K., Thallner, S., Spiess, S., Kucera, J., Vaculovic, T., Všiansk, D., et al. (2022). Bioleaching and selective precipitation for metal recovery from basic oxygen furnace slag. PRO 10, 1–12. doi: 10.3390/pr10030576
Kremser, K., Thallner, S., Strbik, D., Spiess, S., Kucera, J., Vaculovic, T., et al. (2021). Leachability of metals from waste incineration residues by iron-and sulfur-oxidizing bacteria. J. Environ. Manag. 280:111734. doi: 10.1016/j.jenvman.2020.111734
Leon-Fernandez, L. F., Medina-Díaz, H. L., Pérez, O. G., Romero, L. R., Villaseñor, J., and Fernández-Morales, F. J. (2021). Acid mine drainage treatment and sequential metal recovery by means of bioelectrochemical technology. J. Chem. Technol. Biotechnol. 96, 1543–1552. doi: 10.1002/jctb.6669
Lim, S. S., Fontmorin, J. M., Pham, H. T., Milner, E., Abdul, P. M., Scott, K., et al. (2021). Zinc removal and recovery from industrial wastewater with a microbial fuel cell: experimental investigation and theoretical prediction. Sci. Total Environ. 776:145934. doi: 10.1016/j.scitotenv.2021.145934
Liu, H., Ramanathan, R., and Logan, B. E. (2004). Production of electricity during wastewater treatment using a single chamber microbial fuel cell. Environ. Sci. Technol. 38, 2281–2285. doi: 10.1021/es034923g
Modin, O., Fuad, N., and Rauch, S. (2017). Microbial electrochemical recovery of zinc. Electrochim. Acta 248, 58–63. doi: 10.1016/j.electacta.2017.07.120
Motos, P. R., Weijden, R. V., ter Heijne, A., Saakes, M., Buisman, C. J., and Sleutels, T. H. (2015). High rate copper and energy recovery in microbial fuel cells. Front. Microbiol. 6, 1–8. doi: 10.3389/fmicb.2015.00527
Nancharaiah, Y. V., Venkata Mohan, S., and Lens, P. N. L. (2015). Metals removal and recovery in bioelectrochemical systems: a review. Bioresour. Technol. 195, 102–114. doi: 10.1016/j.biortech.2015.06.058
Nurmi, P., Özkaya, B., Sasaki, K., Kaksonen, A. H., Riekkola-Vanhanen, M., Tuovinen, O. H., et al. (2010). Biooxidation and precipitation for iron and sulfate removal from heap bioleaching effluent streams. Hydrometallurgy 101, 7–14. doi: 10.1016/j.hydromet.2009.11.004
Pankratova, G., Leech, D., Gorton, L., and Hederstedt, L. (2018). Extracellular Electron transfer by the gram-positive bacterium Enterococcus faecalis. Biochemistry 57, 4597–4603. doi: 10.1021/acs.biochem.8b00600
Pillai, S. K., Sakoulas, G., Eliopoulos, G. M., Moellering, R. C., Murray, B. E., and Inouye, R. T. (2004). Effects of glucose on fsr-mediated biofilm formation in Enterococcus faecalis. J. Infect. Dis. 190, 967–970. doi: 10.1086/423139
Pozo, G., Pongy, S., Keller, J., Ledezma, P., and Freguia, S. (2017). A novel bioelectrochemical system for chemical-free permanent treatment of acid mine drainage. Water Res. 126, 411–420. doi: 10.1016/j.watres.2017.09.058
Ramachandran, P., Nandakumar, V., and Sathaiyan, N. (2004). Electrolytic recovery of zinc from zinc ash using a catalytic anode. J. Chem. Technol. Biotechnol. 79, 578–583. doi: 10.1002/jctb.1007
Santaolalla, A., Lens, P. N. L., Barona, A., Rojo, N., Ocio, A., and Gallastegui, G. (2021). Metal extraction and recovery from mobile phone PCBs by a combination of bioleaching and precipitation processes. Minerals 11, 1004. doi: 10.3390/min11091004
Spiess, S., Conde, A. S., Kucera, J., Novak, D., Thallner, S., Kieberger, N., et al. (2022). Bioelectrochemical methanation by utilization of steel mill off-gas in a two-chamber microbial electrolysis cell. Front. Bioeng. Biotechnol. 10:972653. doi: 10.3389/fbioe.2022.972653
Spiess, S., Kucera, J., Seelajaroen, H., Sasiain, A., Thallner, S., Kremser, K., et al. (2021). Impact of carbon felt electrode pretreatment on anodic biofilm composition in microbial electrolysis cells. Biosensors 11, 170. doi: 10.3390/bios11060170
Tao, H. C., Lei, T., Shi, G., Sun, X. N., Wei, X. Y., Zhang, L. J., et al. (2014). Removal of heavy metals from fly ash leachate using combined bioelectrochemical systems and electrolysis. J. Hazard. Mater. 264, 1–7. doi: 10.1016/j.jhazmat.2013.10.057
Teng, W., Liu, G., Luo, H., Zhang, R., and Xiang, Y. (2016). Simultaneous sulfate and zinc removal from acid wastewater using an acidophilic and autotrophic biocathode. J. Hazard. Mater. 304, 159–165. doi: 10.1016/j.jhazmat.2015.10.050
Utimura, S. K., Arevalo, S. J., Rosario, C. G. A., Aguilar, M. Q., Tenório, J. A. S., and Espinosa, D. C. R. (2019). Bioleaching of metal from waste stream using a native strain of Acidithiobacillus isolated from a coal mine drainage. Can. J. Chem. Eng. 97, 2920–2927. doi: 10.1002/cjce.23519
Vítěz, T., Novák, D., Lochman, J., and Vítězová, M. (2020). Methanogens diversity during anaerobic sewage sludge stabilization and the effect of temperature. Processes 8, 822. doi: 10.3390/pr8070822
Wakeman, K., Auvinen, H., and Johnson, D. B. (2008). Microbiological and geochemical dynamics in simulated-heap leaching of a polymetallic sulfide ore. Biotechnol. Bioeng. 101, 739–750. doi: 10.1002/bit.21951
Wang, L. P., and Chen, Y. J. (2019). Sequential precipitation of Iron, copper, and zinc from wastewater for metal recovery. J. Environ. Eng. 145, 1–11. doi: 10.1061/(asce)ee.1943-7870.0001480
Wei, X., Viadero, R. C., and Buzby, K. M. (2005). Recovery of iron and aluminum from acid mine drainage by selective precipitation. Environ. Eng. Sci. 22, 745–755. doi: 10.1089/ees.2005.22.745
Yang, C., Zhu, N., Shen, W., Zhang, T., and Wu, P. (2017). Bioleaching of copper from metal concentrates of waste printed circuit boards by a newly isolated Acidithiobacillus ferrooxidans strain Z1. J. Mater. Cycl. Waste Manag. 19, 247–255. doi: 10.1007/s10163-015-0414-7
Keywords: microbial electrolysis cell, metal recovery, zinc recovery, bioleaching, selective precipitation
Citation: Spiess S, Kucera J, Vaculovic T, Birklbauer L, Habermaier C, Conde AS, Mandl M and Haberbauer M (2023) Zinc recovery from bioleachate using a microbial electrolysis cell and comparison with selective precipitation. Front. Microbiol. 14:1238853. doi: 10.3389/fmicb.2023.1238853
Received: 12 June 2023; Accepted: 01 August 2023;
Published: 17 August 2023.
Edited by:
Ruiyong Zhang, Chinese Academy of Sciences (CAS), ChinaReviewed by:
Ana Laura Santos, Natural History Museum, United KingdomCopyright © 2023 Spiess, Kucera, Vaculovic, Birklbauer, Habermaier, Sasiain Conde, Mandl and Haberbauer. This is an open-access article distributed under the terms of the Creative Commons Attribution License (CC BY). The use, distribution or reproduction in other forums is permitted, provided the original author(s) and the copyright owner(s) are credited and that the original publication in this journal is cited, in accordance with accepted academic practice. No use, distribution or reproduction is permitted which does not comply with these terms.
*Correspondence: Sabine Spiess, c2FiaW5lLnNwaWVzc0BrMS1tZXQuY29t
Disclaimer: All claims expressed in this article are solely those of the authors and do not necessarily represent those of their affiliated organizations, or those of the publisher, the editors and the reviewers. Any product that may be evaluated in this article or claim that may be made by its manufacturer is not guaranteed or endorsed by the publisher.
Research integrity at Frontiers
Learn more about the work of our research integrity team to safeguard the quality of each article we publish.