- 1Key Laboratory of Molecular Medicine and Biotherapy, School of Life Science, Beijing Institute of Technology, Beijing, China
- 2Center for Infectious Disease Research, School of Medicine, Tsinghua University, Beijing, China
For decades, lignocellulosic biomass has been introduced to the public as the most important raw material for the environmentally and economically sustainable production of high-valued bioproducts by microorganisms. However, due to the strong recalcitrant structure, the lignocellulosic materials have major limitations to obtain fermentable sugars for transformation into value-added products, e.g., bioethanol, biobutanol, biohydrogen, etc. In this review, we analyzed the recent trends in bioenergy production from pretreated lignocellulose, with special attention to the new strategies for overcoming pretreatment barriers. In addition, persistent challenges in developing for low-cost advanced processing technologies are also pointed out, illustrating new approaches to addressing the global energy crisis and climate change caused by the use of fossil fuels. The insights given in this study will enable a better understanding of current processes and facilitate further development on lignocellulosic bioenergy production.
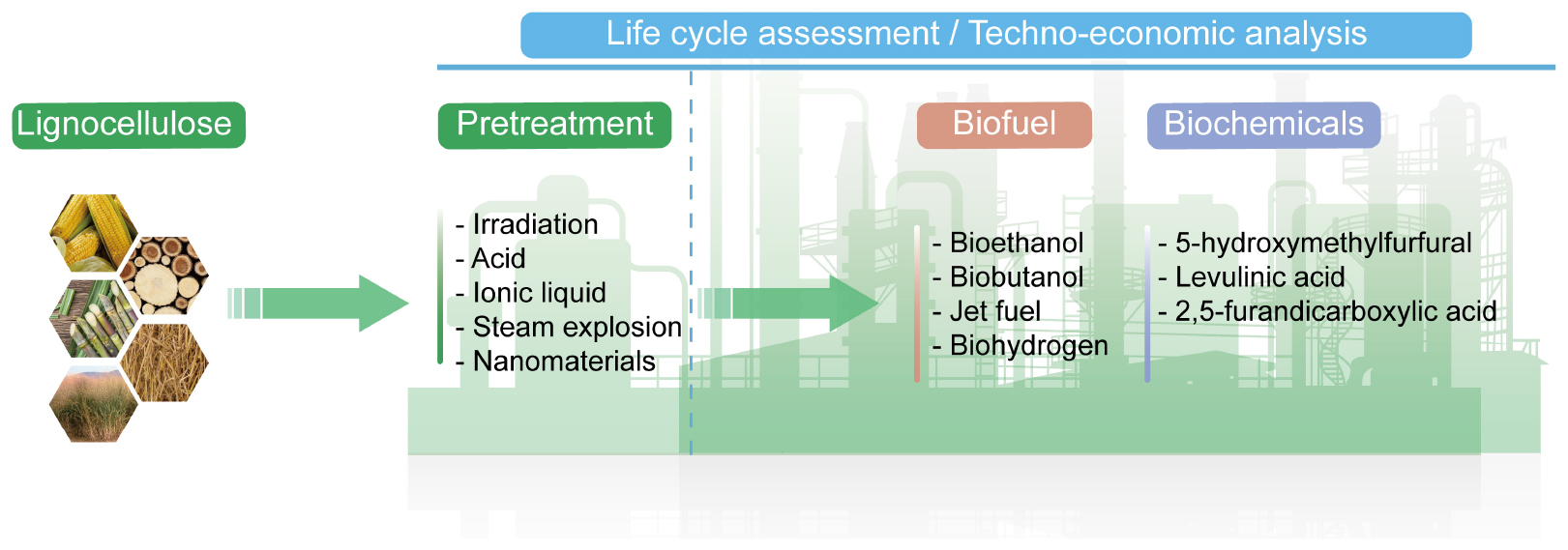
GRAPHICAL ABSTRACT. Overall schematic diagram of lignocellulosic biomass conversion into value-added products.
Introduction
Global primary energy consumption has expanded rapidly in the last decades and reached its fastest rate of 2.9% annual growth since 2010. Oil and coal remain the most wildly used fuels and account for around half of the global energy consumption. To a very large extent, an above-average growth of fossil fuel consumption directly leads to the fastest expansion (2.0%) of carbon emissions, with a historic high of 33.1 gigatons of energy-related CO2 emissions in 2018 (BP, 2019; Usmani et al., 2020). The vast amount of released CO2 from fossil fuels resulted in a persistent temperature anomaly above the average temperature of the last 19th century, particularly in the prominent low-carbon scenarios for 2050 (Heleniak, 2021). Owing to the chasm between fossil fuel-reserved status and stringent climate targets, multiple scenarios have suggested that additional efforts are required to limit global CO2 emissions (Rogelj et al., 2018; WESP, 2020). According to the current oil price, the global crude oil consumption in 2018 was up to 4.6 billion tons, the highest level since 2010 (Dudley, 2018; Chai et al., 2021). Therefore, developing and promoting low-carbon energy sources are urgently needed to reduce the global carbon footprint and meet the net-zero-emission target.
Nowadays, plant biomass provides approximately 10% of global primary energy and is expected to mitigate the energy and environmental challenges (Ahmad et al., 2020). Among various kinds of plant biomass, lignocellulosic biomass is thought to have the greatest potential since it is widely available and potentially has a lower-cost per-unit energy than petroleum (Lynd et al., 2017; Ufodike et al., 2020). Lignocellulosic biomass, also termed as lignocellulose, is a carbon-neutral bioenergy feedstock and the most abundant bio-renewable material on the earth, which is considered the most abundant carbon-neutral resource that can reduce CO2 emission and solve the energy crisis. As an example, wheat straw is considered typical lignocellulose and mainly consists of cellulose, hemicellulose, and lignin. Currently, wheat straw is being produced in ever greater quantities, with the growth of global agriculture, with China annually contributing over 900 million tons of straw, mainly derived from corn, rice, and wheat (Han et al., 2020; Ma et al., 2020). However, most of wheat straw is openly burnt in situ for the preparation of the farmland and agriculture cycle, which will not only cause a tremendous waste of lignocellulosic energy, and also emits a large amount of greenhouse gasses (GHG) (Chai et al., 2021).
Based on the renewable property and huge economic benefits, lignocellulosic has been utilized in the synthesis of various high-value compounds. This review concentrated on the pretreatment technologies of lignocelluloses, including physical, chemical, physicochemical, biological, and other pretreatments, and discussed the bottlenecks and challenges of different pretreatment methods, with a special focus on new strategies to overcome pretreatment barriers. In addition, the generation of high-value-added products, especially biofuels, biohydrogen, and biomaterials from lignocellulosic raw materials is an attractive method to achieve the sustainable development. The current status and application prospects of bioethanol, biobutanol, 5-hydroxymethylfurfural (HMF), and levulinic acid (LA), which is produced from lignocellulosic biomass, are summarized and reviewed herein. Moreover, a comprehensive assessment of the environmental sustainability and economic feasibility risks of current strategies has been discussed with life-cycle assessment (LCA) and techno-economic analysis (TEA). We also proposed the research directions for further development of economically and ecologically viable methods for the production of biofuels and other value-added biological products from lignocellulosic biomass.
Structural characteristics of lignocellulosic biomass
Some technological barriers still hinder the cost-effective pretreatment of lignocellulosic biomass, but robust research is going on to overcome those obstacles. Lignocellulosic biomass has evolved to protect plants from infertility and hydrolysis through the recalcitrant structure of cell walls. This robustness is mainly a result of the cross-linking between polysaccharides and lignin through complex linkages (Tarasov et al., 2018).
Lignocellulose is a complex matrix, consisting of polysaccharides, phenolic polymers, and proteins that, together, constitute the essential structure of the plant cell wall. In general, lignocellulosic materials from energy crops (e.g., corn) mainly consist of cellulose (35–50%), hemicelluloses (20–35%), and lignin (15–20%), as well as minor amounts of ash and extractive components (Zahoor, et al., 2021). Moreover, the lignin contents can reach 25% or higher in woody crops (e.g., willow) (Fonseca et al., 2020; Bonfiglio et al., 2021). However, these components are firmly intertwined and bonded together, forming a cross-linked three-dimensional polymer network of covalent or non-covalent bonds. Figure 1 shows the fundamental structure and composition of lignocellulosic biomass. Cellulose molecules are arranged in regular bundles or a random geometry, respectively, forming crystalline and amorphous regions. Cellulose and hemicellulose polymers in microfibrils are linked by hydrogen bonds and are protected by lignin. This stabilized structure confers lignocellulosic biomass with different degrees of resistance to various treatments, including enzymatic hydrolysis.
Cellulose
Cellulose is linear polysaccharides, in which glucose molecules are linked together through β–(1→4) glycosidic bonds. The cellulose chains form a crystalline structure via hydrogen bonds and Van der Waals interactions, consequently aggregating into microfibrils and then fibers (Ashokkumar et al., 2022). This is the common structural feature of the primary cell wall of green plants and algae. Cellulose is the most abundant and available organic polymer in nature, but its proportion varies considerably with sources, for example, 90% in cotton fiber and 40–50% in wood. The high degree of crystallinity provides sufficient strength to cellulose but requires relatively rigorous condition (320°C and 25 MPa) to observe the crystalline-to-amorphous transformation in water, which hampers the subsequent saccharification for the biorefinery production.
Hemicellulose
Hemicellulose is an amorphous and variable heteropolymer, containing approximately 500–3,000 sugar units of xylose, glucose, and galactose. It is cross-linked with either cellulose or lignin and further solidifies the cell wall (Figure 1). Of the hemicelluloses, the xylan (polymer of xylose) is predominated in hardwoods and cereal, whereas glucomannan is the major type occurring in softwoods. Although hemicellulose is widely available, the diversity of sugar units varies, depending on the source of lignocellulosic biomass, resulting in more challenging pretreatment compared to cellulose (Zoghlami and Paës, 2019). However, the differences in variability of the sugar unit, chain length, and structure of glycosyl side chains give hemicellulose a huge advantage over cellulose in aspect of for regioselective chemical and enzymatic modifications.
Lignin
Lignin is the third major component of lignocellulosic biomass, bound to hemicellulose through covalent bonds, contributing to the rigidity and compactness of the plant cell wall (Kang et al., 2019). Lignin is made up of three types of phenylpropanoid monomers: 4-propenyl phenol, 4-propenyl-2-methoxyphenol, and 4-propenyl-2,5-dimethoxyl phenol (del Río et al., 2020).
Although lignocellulosic biomass has great potential economic value, pretreatment is an inevitable step for bioconversion to obtain monomeric sugars, which greatly increase the cost of bioprocessing (Sindhu et al., 2016; Sun et al., 2016b). The first step in a lignocellulosic facility is pretreatment for increasing the fractions of cellulose, hemicellulose, and lignin in the following hydrolysis step. It has been estimated that the pretreatment step accounts for 18–20% of the total project expense for the production of lignocellulosic ethanol, more than any other single step (Zhang et al., 2021). Furthermore, the associated cost of enzymes also prevents the production of bioenergy on an industrial scale (Saldarriaga-Hernández et al., 2020). These obstacles have led to the liquidation of many advanced biofuel startups, and the surviving companies have mainly focused on high-value-added products instead of fuels. Even though the global investment in biofuels and biochemicals prefers chemicals rather than fuels, the bioconversion of lignocellulose is confronted with both opportunities and challenges.
Current technologies for the pretreatment of lignocellulosic
The industrial conversion of lignocellulosic biomass usually includes multiple steps, starting from the gathering and transportation of lignocellulose biomass, as well as the production of cellulase enzymes, followed by the pretreatment of lignocellulose biomass, hydrolysis of cellulose, fermentation of resulting monomer sugars, and, finally, treatment of effluent. Many pretreatment methods have been developed and optimized to maximally break down the cell walls, eliminate the hemicelluloses and/or lignin, increase the specific surface area, and so on, promoting the subsequent hydrolysis or depolymerization of cellulose. The main aim of the pretreatment is to deform the structure of lignin and reduce the crystallinity of cellulose to increase the contact area of the enzymes with cellulose during the process of hydrolysis. As shown in Figure 2, the recalcitrant structure of lignocellulose could be disrupted in the pretreatment process, resulting in easily hydrolyzed substrates for the subsequent enzymatic or microbial treatment.
The ideal pretreatment should be widely adaptable to different biomass sources, while also maintaining a low cost. The ideal pretreatment process should have (i) high-sugar yield and fermentation availability, (ii) minimal formation of toxic compounds and byproducts, as well as (iii) minimal energy requirements (Sindhu et al., 2016; Sun et al., 2016b; Bhutto et al., 2017). Several major pretreatment methods were compared in different ways and listed in Table 1.
Previous studies have developed different methods to pretreat lignocellulose with the aim to separate cellulose from lignocellulose and degrade lignocellulose to achieve a higher-sugar yield. The pretreatments should reduce the polymerization degree and crystallinity of cellulose, remove or degrade lignin and hemicellulose (or degraded lignin and hemicellulose), while also increasing the accessible surface area (Fei et al., 2020). Several selected methods are detailed below.
Physical pretreatment
The aim of physical pretreatment is to enhance the accessible surface area by reducing the crystallinity and polymerization degree of cellulose, and thereby enhance the effectiveness of enzymatic hydrolysis (Chuetor et al., 2017, 2019). Physical pretreatment methods mainly included mechanical comminution (chipping, grinding, or milling) and irradiation (gamma rays, electron beam, microwave, etc.) (Karimi et al., 2013; Sun et al., 2016b; Bichot et al., 2020).
Mechanical comminution pretreatment
Mechanical comminution (MC) pretreatment alters the intrinsic internal structure of lignocelluloses and the extent of crystallinity by converting lignocellulosic biomass into particles of different sizes that are more amenable to enzymes. The pattern of the pretreatment defines the final particles size. For example, after the process of chipping, milling, and grinding, the particle size can reach 10–30 and 0.2–2 mm, respectively (Witaszek et al., 2020). Furthermore, the final particle size of lignocellulosic feedstocks is highly depended on the energy consumption of active mechanical comminution (Sun et al., 2016b). The microstructural and thermo-optical characteristics of lignocellulosic Paulownia biomass were altered by ultrafine grinding, providing significant benefits for subsequent hydrolysis and hydrogen production (Yi et al., 2020). Recently, it has been reported that combined biological and mechanical treatments could boost the bioethanol yield by up to 83%, resulting in an improvement of the overall substrate conversion of up to 131%. Accordingly, the combination of dry biological–mechanical pretreatments has great application potential in the future (Motte et al., 2015). At present, the high cost of single mechanical pretreatment impedes its large-scale application, but it can be combined with other pretreatment methods to great benefit.
Irradiation pretreatment
The cellulose in the lignocellulose biomass can be converted into microfibers, oligosaccharides with a low degree of polymerization, and even disaccharide via irradiation pretreatment. New irradiation pretreatment methods have been developed recently, including gamma irradiation, electron beam irradiation, microwave, and ultrasonic energy (Kumar et al., 2020). The gamma rays from radioactive decay of cobalt-60 or cesium-137 can penetrate biomass materials and decompose cellulose as well as lignin. A high conversion rate up to 72.68% for subsequent enzymatic hydrolysis could be achieved from agricultural straw after gamma irradiation at 800 kGy (Wu et al., 2020).
Ultrasound is sound waves with frequencies above 20 kHz, and has promising effect on cell wall disruption and accessible surface area changes. A recent study has suggested that ultrasound pretreatment led to significant improvement in lignocellulosic biomass solubility and biofuel yield (Marta et al., 2020). However, irradiation pretreatment, when used alone, has different defects, such as the formation of inhibitors and high energy consumption, and is now often combined with other pretreatment options. Several studies incorporating the acid and alkaline-mediated ultrasound pretreatment for increased biofuel yield have been reported. The application of ultrasound-assisted dilute acid pretreatment demonstrated that the combined method can eliminate the formation of inhibitors and increase the substrate utilization efficiency as well as bioethanol yield (Paramasivan et al., 2021). Similarly, ultrasound-assisted alkaline pretreatment was performed to achieve a high sugar content, resulting in a considerable yield of glucose after enzymatic saccharification (Ong et al., 2021). The combination of chemical or physical pretreatment with microwave was also employed to enhance yield with low doses of gamma irradiation. As found by Liu et al. (2021), alkali pretreatment combined with microwave irradiation of wheat straw could significantly increase the purity of cellulose up to 90.66%, and temperature is the most efficient factor among the process conditions.
Chemical pretreatments
Acid pretreatment
The main objective of acid pretreatment is to decompose hemicellulose by disintegrating its bond with cellulose and partially degrade lignin, which can facilitate biomass fragmentation and production output (Mostofian et al., 2016). Both highly concentrated and dilute acids have been applied to preprocess a variety of lignocellulosic materials. However, pretreatments with concentrated acid require a large amount of acid, leading to corrosion of equipment, require additional recovery steps, and increase the cost (Kang et al., 2018). Even worse, low pH leads to unfavorable Pechmann reactions among lignin constituents, which leads to low lignin removal and can inhibit the subsequent enzymatic saccharification (Mostofian et al., 2016; Narron et al., 2016; Shuai et al., 2016). Therefore, diluted acid pretreatment is more widespread than the use of concentrated acid.
Pretreatment with diluted sulfuric acid with a concentration of 2–5% is usually carried out at a higher temperature in the range of 200–240°C, while a lower temperature is recommended for concentrated acid hydrolysis of biomass (Rezania et al., 2020). One study employed formic/acetic acid to pretreat beechwood at 104.2°C for 5 h and obtained 70.5% delignification. However, diluted acid pretreatment cannot remove the lignin, which was disadvantageous for subsequent steps (Martínez et al., 2015). These lignin droplets probably blocked the enzyme accessible to biomass or formed an ineffective combination with cellulose by intermolecular forces. A new bacteria-enhanced diluted acid pretreatment strategy has attempted to provide a solution to the above challenges. Using this approach, the enzymatic digestibility of rice straw was increased by 35–70 and 173–244% compared to diluted acid preprocessing and untreated biomass, respectively (Yan et al., 2017). This strategy was expected to be further developed to put into practical application. More attentions should be paid to reducing or eliminating inhibitors produced during the dilute acid pretreatment process.
Alkali pretreatment
Alkali pretreatment is the most frequently used method to get rid of lignin and hemicelluloses from lignocellulosic feedstocks and convert a large volume of lignocellulosic materials into lignocellulosic fibers. It was reported to have an advantage over acid pretreatment by causing less sugar loss and was shown to be more efficacious on agricultural residues than on wood biomass (Kim et al., 2016). The major aim of alkaline pretreatment is the disintegration of lignin, hemicellulose, and intermolecular ester bonds (Shi et al., 2021). Reagents, such as NaOH, Ca(OH)2(lime), Na2S, Na2CO3, NH4OH, and other alkaline reagents, have been employed to preprocess lignocellulosic feedstocks, whereby NaOH and Ca(OH)2 are the most commonly used (Sun et al., 2016b). Compared with liquid NaOH pretreatment, lime pretreatment is more cost-effective and environmentally friendly due to its easy separation with CO2 assistance. Moreover, lime pretreatment does not form inhibitors such as furfural and HMF (Mathew et al., 2011). The addition of an oxidant agent (O2/H2O2) in alkaline pretreatment [NaOH/Ca(OH)2] can optimize the results by increasing lignin elimination. Martínez et al. (2015) found that 90% (w/w) of glucan was converted into glucose by enzymatic action, and 50% of unwanted xylan was removed after pretreatment with NaOH. However, the main drawback of alkali pretreatment is the black liquor (wastewater containing unrecovered alkalis and dissolved lignin), as well as the high energy input for hydrolysis (Vu et al., 2020). To date, the combination of alkaline pretreatment with mechanical milling has been the most commonly used to improve the reactivity of lignocellulosic material and enhance the fermentable sugar yield (Schneider et al., 2017; Wang et al., 2018; Shen et al., 2020).
Ionic liquids pretreatment
Ionic liquid (ILs) is a kind of molten salt that is in liquid state at ambient temperature and consists of pairedions. ILs possess many advantaged characteristics, such as non-flammability, low vapor pressure, as well as good thermal and chemical stability (Bhutto et al., 2017). Since there is no toxic or flammable vapor generated, ILs are regarded as “green solvents” and have become rising stars in the field of lignocellulose pretreatment (Elgharbawy et al., 2016; Yoo et al., 2017; Das et al., 2021). ILs have a powerful ability to dissolve the inter- and intramolecular hydrogen bonds of lignocellulose, and their performance can be further improved by altering the negative ions as well as the alkyl residues of the positive ions (Xu et al., 2016). Some studies found that π-π bond can be formed between the imidazolium cation of the ILs and lignin, improving its degradation (Jiang et al., 2011; Shill et al., 2011). Furthermore, pretreating lignocellulose with certain ILs makes the biomass more accessible to enzymes due to structural and chemical alterations (Torr et al., 2016). A method using 1-ethyl-3-methylimidazolium acetate allowed the separation of lignocellulosic biomass into high-purity carbohydrate and lignin fractions, with an efficient ILs recovery (Chinwatpaiboon et al., 2021). In general, solvent recovery is usually complicated and requires high energy consumption, which limits the large-scale utilization of ILs. Further studies are, therefore, needed to optimize the process flow to drive economically feasible ILs methodologies for the pretreatment of lignocellulose.
Organosolv pretreatment
Organosolv (OS) fractionation was thought to be superior to other lignocellulose pretreatments methods as it efficiently generates pure products and uses an easily recovered solvent (Zhang et al., 2016). This process yields three independent components: water-free lignin, hydrous hemicellulose vapor, and a comparatively pure cellulose fraction (Zhao et al., 2017). Generally, various catalysts, such as formic, oxalic, acetylsalicylic, and salicylic acid, are added to enhance the performance of delignification and dissolution of the hemicellulose fractions (Li et al., 2016a; Zhang et al., 2016; Singh et al., 2022).
Ethanol is the most favored solvent for organosolv pretreatment due to its advantages, such as low cost, low boiling points, and easy recovery. However, for most low-boiling-point solvents, the pretreatment process is carried out at high pressure, which increases the operational costs (Bhutto et al., 2017). Conversely, employing violate organic solvents required exceedingly tight control due to intrinsic combustibility and explosion hazards (Bhutto et al., 2017). Previous studies have elucidated that the generation of undesired furfural and HMF can be reduced under mild pretreatment conditions at low temperature and pressure as well as neutral pH (Kim and Pan, 2010). Sun et al. (2016a) evaluated the commercial and industrial application of atmospheric glycerol organosolv pretreatment (AGO), and the results revealed good constituent selectivity, with the removal of approximately 70% lignin and hemicellulose, while preserving 94% of the overall cellulose. Based on the previous work, further research should focus on the optimization of pretreatment conditions for the final purpose of commercialization.
Oxidative pretreatment
Oxidative pretreatment is usually employed to bleach paper pulp (Sun et al., 2016b). In this process, nearly all lignin can be separated from lignocellulosic biomass without significant loss of cellulose and hemicelluloses, which optimizes the yield of fermentable sugars (Coca et al., 2016). Commonly used oxidation reagents include O3, O2, H2O2, ClO2, NaClO, and Cl2. The pretreatment is usually carried out at ambient temperature and pressure, thus avoiding the formation of toxic byproducts (Alvira et al., 2010). It was reported that the use of wet disk milling (WDM), followed by ozonolysis, was preferable for pretreating sugarcane bagasse and straw, resulting in a higher saccharification yield than WDM after ozonolysis (de Barros et al., 2013). Remarkably, a two-stage pretreatment enabled sugar recovery from corn stover with a low-enzyme loading (Li et al., 2016b). The pretreatment with diluted hydrochloric acid (0.7% wt hydrochloric acid at 120°C for 40 min), followed by Fenton oxidation (at room temperature for 12 h), resulted in the recovery of 81.0% xylose and 32.9% lignin. Ultimately, high sugar recovery was achieved with low-enzyme loading, but the large consumption of oxidation reagents made the process economically unviable (Travaini et al., 2016).
Physicochemical pretreatments
Steam explosion pretreatment
Steam explosion is the most commonly used thermo-mechanic-chemical preprocessing method for lignocellulosic feedstocks, which allows the opening of the lignocellulosic structure via the combination of mechanical forces and chemical function (Verardi et al., 2018). The most important factors that determine the results of steam explosion are section size, temperature, dwell time, and the joint effect of both temperature and time (Sarker et al., 2021). López-Linares et al. (2015) showed that the optimal conditions for the maximization of enzymatic hydrolysis yield were 215°C and 7.5 min, leading to a maximum glucose yield of 72.3% from rapeseed straw. Wang et al. found that autohydrolysis mainly occurred on the hemicelluloses and the amorphous region of cellulose at a shorter steam pretreatment time. Prolonged incubation time could benefit the depolymerization of the crystalline region of cellulose (Smichi et al., 2020). Due to large amount of fermentation inhibitors generated under the condition of violent steam explosion, various cleaners, such as SO2 and H2SO4, have been applied to enhance the separation of hemicelluloses under relatively mild conditions (Sun et al., 2016b).
Steam explosion pretreatment has several favorable characteristics, such as high energy efficiency, low environmental impacts, being suitable for large particle size, and requiring no external chemicals (Bhutto et al., 2017). Furthermore, high sugar recovery can be achieved because the material is quickly heated by steam so that only small amounts of fluid remain in the equipment. However, the numerous inhibitors from sugar and lignin degradation, such as furfural and phenolic compounds, are the main disadvantage of steam explosion pretreatment. These compounds can be removed by washing the pretreated biomass with large amounts of water but raising the issue of loss of sugar and reprecipitation of lignin. Nonetheless, steam explosion pretreatment has been proved to be an effective pretreatment process for the production of various bioproducts. A remaining challenge of this process is how to minimize the production of inhibitors.
Liquid hot water pretreatment
Liquid hot water (LHW) pretreatment is also a hydrothermal treatment method related to the steam explosion pretreatment, albeit using liquid hot water rather than steam to preprocess lignocellulose. As a consequence of high-level decomposition of cellulose when the temperature exceeds 240°C, the hydrothermal temperature is usually fluctuated in the range of 160–240°C (Cao et al., 2014; Sun et al., 2014). The primary purpose of the liquid hot water is to degrade the hemicellulose and make it more accessible to enzymes. To minimize the produce of inhibitors, the pH should be maintained between 4 and 7 during the pretreatment, as hemicellulosic sugar is mostly maintained at a low degree of polymerization under these conditions (Chen et al., 2014b). In recent studies, several catalytic agents have been tentatively applied to assist the separation of hemicelluloses or lignin, such as dilute alkali and H2SO4 (Yao et al., 2018; Yang et al., 2019; Ladeira Ázar et al., 2020).
Overall, liquid hot water pretreatments had the advantages of high productivity, no catalysts requirement, low-cost installation, relatively high hemicellulose recovery, and low formation of inhibitors. However, high water and energy demand due to the high temperature and pressure as well as the relatively limited output of fermentable sugars are remaining challenges, which required further exploration.
Ammonia fiber explosion pretreatment
Ammonia fiber explosion (AFEX) exposes lignocellulosic materials to liquid ammonia at 60–100°C and 250–300 psi for an unequal length of time, followed by a rapid pressure release (Zhao et al., 2020). This process can evidently enhance enzymatic hydrolysis because liquid ammonia causes the expansion of lignocellulose and alters the crystal structure of cellulose, while the rapid release of pressure ultimately results in the physical disintegration and crystallinity attenuated of lignocellulosic biomass (Sun et al., 2016b). However, this process cannot remove significant amounts of lignin and hemicellulose from lignocellulose. Accordingly, this method allows low lignin preservation, reducing the inhibition of enzymes and promoting enzyme accessibility, dramatically reducing enzyme loadings. AFEX was reported to produce 36-fold-less furans and 100-fold-less carboxylic acids than dilute acid pretreatment, allowing the direct delivery to fermentation without any detoxification (Chundawat et al., 2010). AFEX has achieved high conversion rates (80–97%) of various biomass sources, such as corn stover, wheat straw, and rice straw (Momayez et al., 2018; Qiao et al., 2018; Wang et al., 2019).
Ammonia fiber explosion is a forward-looking pretreatment process with several virtues, such as being harmless to the environment, having low energy consumption, mild-reaction conditions, and negligible production of inhibitors. Furthermore, most of the ammonia can be recycled back into the process reactor to reduce the operating input. Nevertheless, the expensive liquid ammonia is less competitive for industrial applications than some of the other commonly used solvents.
Nanobiotechnology pretreatment
Considering disadvantages of conventional lignocellulosic biomass pretreatment methods, such as the cumbersome and costly treatment process, serious environmental pollution, and the limitations in reducing the polymerization rate and crystallinity of cellulose (Chandel et al., 2022), it is crucial to develop economical and efficient pretreatment methods for lignocellulose. Recently, utilizing of nanobiotechnology for lignocellulosic biomass pretreatment has gained widespread attentions, which is considered to be an effective solution to overcome the bottlenecks. Nanomaterials with magnetic properties could be recovered from the reaction mixture for reuse by increasing the magnetic field, indicating a cost-effective and ideal pretreatment method (Sajid and Płotka-Wasylka, 2020). Due to the properties such as the high-specific surface area, thermal stability, and high specificity, nanomaterials have been utilized for the immobilization of enzymes, which could enhance their reusability and the production of immobilized proteins. Nanotechnology is mainly applied to the pretreatment of lignocellulosic biomass by acid-functionalized magnetic nanoparticles mediated and nano-shear hybrid alkaline (NSHA). It has been reported that the pretreatment of 500 mg g–1 of sugarcane bagasse with two types of acid-functionalized magnetic nanoparticles, alkyl sulfonic acid, and butyl hydroxy acid yielded 18.83 and 18.67 g L–1 sugar, respectively (Mahajan et al., 2020). Deng et al. utilized the NSHA method for pretreatment of corn stover biomass to improve biofuel production. Approximately, 70% of cellulose was converted, which significantly facilitates efficient biofuel production (Deng et al., 2018).
With rapid development of the global industry, fossil energy is becoming increasingly scarce. The acquisition of bioenergy from renewable resources plays a significant part in the eco-friendly society, which promotes green and sustainable development. At present, various nanomaterials, such as magnetic nanoparticles, zinc oxide nanoparticles, and magnesium oxide nanocatalysts, have been utilized in improving the production of renewable bioenergy from lignocellulosic biomass (Dey et al., 2022; Govarthanan et al., 2022).
In conclusion, the application of nanotechnology could effectively improve the efficiency of lignocellulosic pretreatment and reduce the environmental pollution. The utilization of magnetic nanoparticles for lignocellulosic biomass pretreatment or immobilization of enzymes is considered as a cost-effective solution. Meanwhile, nanobiotechnology shows great potential for efficient production of biofuels and other high-value-added compounds.
Biological pretreatment
Biological pretreatment is an environmentally friendly technique, and has attracted increasing interest for promoting the enzymatic digestion of lignocellulosic materials in ethanol production processes (Batog and Wawro, 2021). Commonly employed microorganisms, such as brown, white, and soft rot fungi, perform their function on depolymerizing lignin and hemicelluloses in lignocellulosic biomass (Saritha and Arora, 2012; Sindhu et al., 2016). Brown-rot fungi mainly digest cellulose, while the white- and soft-rot fungi utilize both cellulose and lignin (Meehnian et al., 2017; Couturier et al., 2018). Notably, white-rot fungi are the most popular choice for the biological pretreatment of lignocellulosic biomass (López-Abelairas et al., 2013; Machado and Ferraz, 2017). A comprehensive review has discussed various facets of biological pretreatment, related enzymes, factors influencing biological pretreatment, as well as future perspectives (Singh, 2021).
Although biological pretreatment offers many advantages, such as low-capital investment, using less energy, requiring no externally added chemicals, having no inhibitor production, and mild pretreatment conditions, it is hindered by the very long incubation time (several weeks) and the relatively low hydrolysis yields. Screening or engineering of more powerful microorganisms, as well as optimizing the fermentation methods, is certainly a worthwhile research direction for the future.
Other pretreatments
Novel and updated pretreatment methods for lignocellulose include CO2 explosion pretreatment, SO2 explosion pretreatment, N2 explosion pretreatment, supercritical fluid pretreatment, and wet oxidation and hydrogen peroxide-acetic acid pretreatment (Wi et al., 2015; Lee et al., 2020; Arumugham et al., 2022). However, ongoing efforts to apply these methods have not yet resulted in economically viable industrial processes.
A recent study has assessed the techno-economics of four different pretreatment processes, including steam explosion, dilute sulfuric acid, AFEX and biological pretreatments. The authors suggested that steam explosion and sulfuric acid pretreatment methods might be good alternatives at the present state of technology, but further research is needed to make them industrially competitive (Baral and Shah, 2017). Similarly, scenarios for dilute acid, liquid hot water, and AFEX methods were studied, and the results suggested the best scenarios, which achieved total annual costs reduction of 19.6%, as well as Minimum Bioethanol Selling Prices reduction of 30.2% (da Silva et al., 2016). Specifically, liquid hot water pretreatment (SCN-L3) achieved the best minimum bioethanol selling prices, with savings of 30%. However, these results should be used as guidelines and are not suitable as standards because the experimental designs and reporting results did not provide adequate consistency to allow comparison and identification of the best protocols.
High-value products from lignocellulosic biomass
In recent years, lignocellulosic has attracted increasing attentions biomass as a renewable and sustainable energy. The emerging technologies based upon the concept of biomanufacturing contribute a wide range of bioproducts, including biofuels, biohydrogen, biomaterials, and a series of biochemicals from fermentation and refining steps (Figure 3). Therefore, lignocellulosic biomass provides an attractive alternative for the production of biofuels and chemicals in a sustainable and eco-friendly society, which had led to its reorganization as a valuable commodity all over the world. Table 2 shows some value-added products that have been successfully produced from the different components of lignocellulosic biomass.
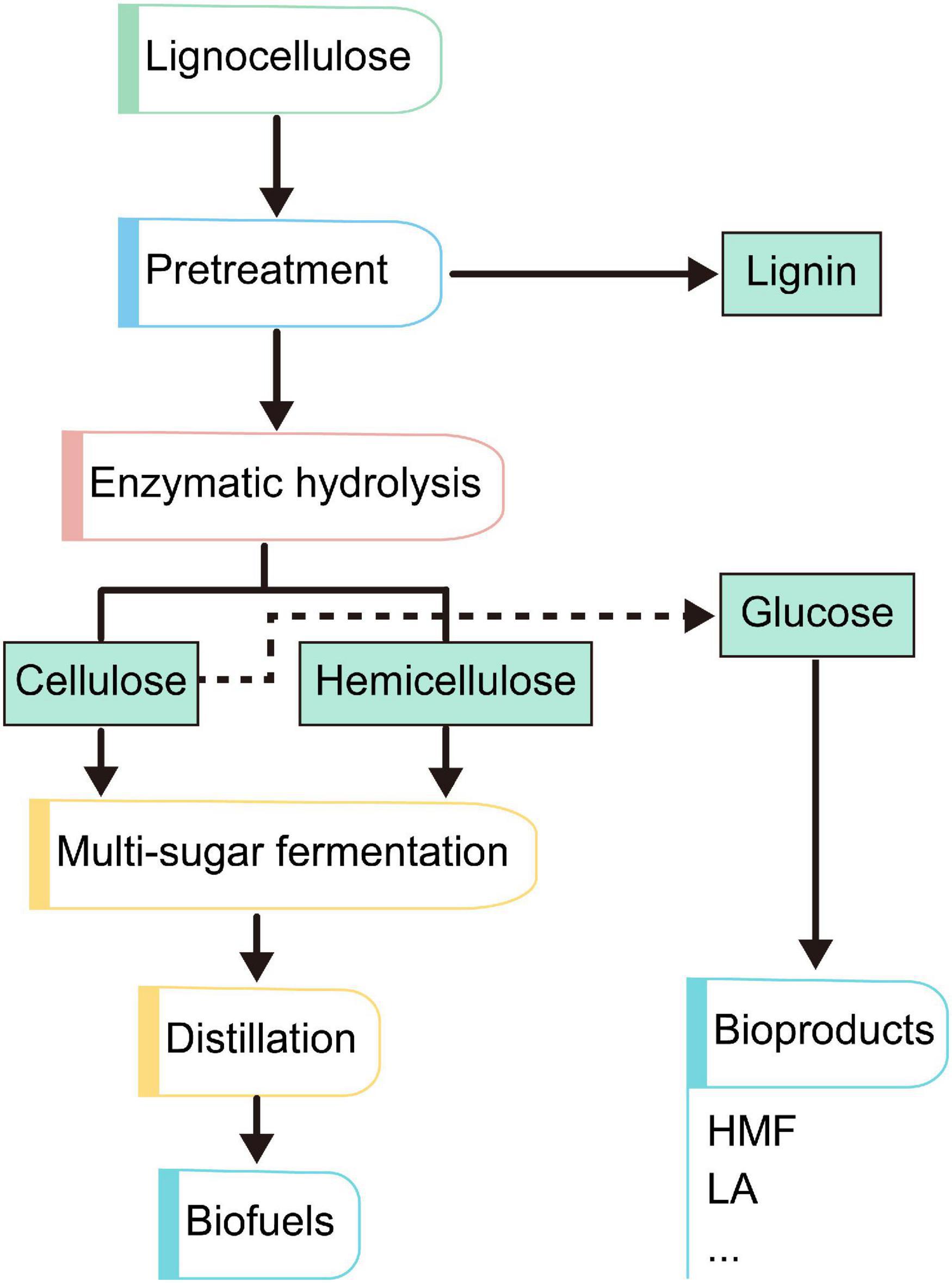
Figure 3. General routes of formation of different value-added products from lignocellulosic biomass.
Bioethanol is a well-known biofuel used in the transportation sector worldwide by far, which can be produced by fermentation of a variety of feedstocks. Studies focusing on the bioconversion of lignocellulose to bioethanol provide different strategies for improving the yield, aiming to pave the way for industrial-scale bioethanol production. Compared with bioethanol, biobutanol has a higher-energy content and a higher-octane number, resulting in a drop-in fuel alternative, which can be used alone or blend with gasoline in any concentration. Another important liquid biofuel is biodiesel, a form of diesel fuel generated by a chemical transesterifying process that combines vegetable oils, animal fats, and alcohol in the presence of a catalyst. To date, biodiesel has been studied extensively and has been produced on a commercial scale through numerous advancements in pretreatment, catalysts, and reactor optimization (Zhang et al., 2019; Mohiddin et al., 2021).
These liquid biofuels emit GHG upon combustion and, therefore, are not considered as preferable energy sources yet. Biohydrogen, as a fuel, has been seen as one of the cleanest energy carriers as it is renewable, carbon free, and has no emission of GHGs from combustion (Abdin et al., 2020). Usually, conversion of lignocellulosic biomass to hydrogen can be accomplished by thermochemical methods (gasification or pyrolysis) and the biological process (bio-photolysis, photo fermentation, or dark fermentation) (Singh et al., 2021). Apart from these routes, nanotechnology has begun to gain interest for promoting the biohydrogen production. Many studies have been reported to investigate the effect of different nanoparticles on biohydrogen production, and have revealed that nanoparticles help the cell to transfer electron faster during redox reaction (Tahir et al., 2021).
Although bioethanol is the main product in acetone-butanol-ethanol (ABE) fermentation by Clostridium species, other products, such as 2,3-butanediol, xylitol, lactic acid, and butyric acid, can be obtained by metabolic engineering and adaptive evolution of candidate strains (Araújo et al., 2021; Lee et al., 2021; Zou et al., 2021; Fu et al., 2022).
In addition, different enzymes used during the hydrolysis process of lignocellulosic biomass could be obtained from various microbes (Table 3). For example, Lignicell Refining Biotechnologies Ltd. (formally Laihe Rockley Bio-chemicals Co. Ltd., a sino-foreign joint venture company) reported an annual production of 40,000 tons of ABE in 2012 (Jiang et al., 2015). Moreover, compared with the fossilized one, the price of n-butanol ($1.32 kg–1) was very competitive compared to the price of the petrochemical alternative ($1.52 kg–1).
Novel value-added products, such as HMF, LA, and 2,5-furandicarboxylic acid (FDCA), have recently been produced from lignocellulosic biomass via advanced reaction systems and selective catalytic processes. HMF is produced industrially on a modest scale, and is mainly used as a flavoring agent in the food industries. Important derivatives, such as furfuryl alcohol and 2-methyltetrahy-drofuran, have great potential in the synthesis of furan resins. It was reported that lignocellulose can be directly converted into HMF with an approximate 49% yield in a seawater-tetrahydrofuran biphasic medium (Guo et al., 2018). As a keto acid generated mainly from HMF, LA has high reactivity and wide functionality due to the presence of ketone and carboxylic functional groups, and was recognized as an important precursor for the synthesis of biofuels. In 2015, GF Biochemicals began the large-scale commercial synthesis of LA based on the acid catalysis process. The commercial production of FDCA was first initiated at a pilot plant scale in 2011 by Avantium, using catalytic oxidation processes with a yield of approximately 50%.
However, most of startup companies have been shut down because of financial issues caused by the price depreciation of n-butanol. Those that have survived still struggled with various problems, such as less cost-effective pretreatment, troublesome inhibitors, as well as low-yield productions. In this section, we have summarized the recent advancement and challenges of converting lignocellulose to high-value products, including bioethanol, biobutanol, HMF, and LA.
Bioethanol
Ethanol (C2H5OH) is the most abundant biofuel and is being considered as a potential substitute in petroleum-derived transportation industries. First-generation commercial ethanol production was based on starch and sugar-derived feedstocks, which resulted in the food-versus-fuel debate over bioethanol and a consequent food price crisis. The conversion of lignocellulosic biomass into bioethanol is of great interest and is considered the second generation of bioethanol due to its low environmental impacts and wide available resources that do not compete with food production. Generally, the production of bioethanol from lignocellulosic biomass can be achieved via biochemical and thermochemical conversion. Both routes result in simple oligomers of lignin, hemicellulose, and cellulose via degradation, but the subsequent conversion technologies are not similar. The Fischer-Tropsch process is a heterogeneous catalytic reaction that can gasify biomass to produce syngas (CO and H2), which can be chemically converted into ethanol, butanol, and green diesel (Snehesh et al., 2017). An enzymatic hydrolysis process was integrated with the fermentation of reducing sugars in the same device, termed as simultaneous saccharification and fermentation (SSF), resulting in the biological transformation of sugars (produced in the procedure of the enzymatic hydrolysis of cellulose) into ethanol. Therefore, the final product inhibition of cellulase caused by the accumulation of sugars was neutralized due to the presence of yeast and the cellulolytic enzyme complex. In addition, the entire process demanded a single fermenter, thereby economizing the investment costs. However, there was one highlighted problem that the optimal conditions of saccharification and fermentation were not compatible. Research on superior reactor installation allowed the fermentation to the ethanol process based on the technology of fed-batch seemingly to be a prospective means to enhance the end output of ethanol. To this end, various studies optimized the simultaneous saccharification and fermentation process.
Paschos et al. proposed a semi-consolidated process involving two microorganisms (Saccharomyces cerevisiae and Fusarium oxysporum) for the fermentation of a highly viscous liquefied material via an in-house free-fall mixing reactor. The authors claimed that the addition of solid Fusarium oxysporum culture resulted in an ultimate ethanol concentration of 58 g L–1, an increase of up to 19% compared to the control (Paschos et al., 2015). Choudhary et al. (2017) isolated ten yeast strains from diverse sources and evaluated their production potentials, among which S. cerevisiae JRC6 showed the best fermentation performance, providing a promising alternative for simultaneous saccharification and fermentation processes. However, the pre-hydrolysis time was not systematically assessed in most studies, which is an important step before SSF and impacts on yield, productivity as well as ethanol concentration. A recent study has evaluated a pre-hydrolysis and SSF performance and maximized the ethanol concentration via multi-criteria optimization, resulting in 290 L of ethanol per ton of pretreated sugarcane straw (Pratto et al., 2020). In addition, a suitable microbial strain that is capable of converting lignocelluloses efficiently has been requested in the bioethanol production industry. The novel genetic manipulation strategies allow overexpression and editing of genes in different microbial candidates to gain enhancement of ethanol yield, productivity, and tolerance. Escherichia coli is one the most common model bacteria and has been engineered for the selective production of bioethanol via genetic manipulation. In recent years, different studies have been performed to optimize the substrate utilization, ethanol tolerance, and robustness of engineered strains through several different aspects. Recently, a metabolic engineered E. coli strain WDH-LF has been given the positive impact on ethanol production by the deletion of frdD and ldhA. Compared to the parental strain, the resultant strain redirected carbon flux to ethanol production and increased up to 167% higher-ethanol production from glucose (Lopez-Hidalgo et al., 2021). Moreover, other promising microorganisms, including Cyanobacteria, thermophilic bacteria, and Zymomonas mobilis, also have employed to improve ethanol production (Rahayu et al., 2020; Sarkar et al., 2020; Roussou et al., 2021).
Biobutanol
Butanol (C4H9OH) is an important chemical precursor in many industries, as well as a potential direct substitute for petrochemical gasoline. Butanol is a highly flammable straight-chain alcohol with a boiling potion of 117°C. Although biobutanol and bioethanol can be produced via similar fermentation of lignocellulosic biomass, biobutanol is a superior biofuel compared to bioethanol due to its good miscibility with gasoline, non-hygroscopic nature, low-Reid vapor pressures, lower volatility than other traditional fuels, fewer emission, and higher-energy content than ethanol (Pugazhendhi et al., 2019). The leading biobutanol producers, such as Butamax and Gevo, have been devoting significant research efforts to the replacement of fossil fuels (Wang et al., 2017).
The most common microorganisms for biobutanol synthesis are anaerobic spore-forming bacteria, including Clostridium acetobutylicum, Clostridium beijerinckii, and Clostridium saccharobutylicum, Clostridium saccharoperbutylacetonicum (Das and Maiti, 2022). Generally, solventogenic Clostridia can synthesize butanol via the ABE fermentation process from renewable lignocellulosic feedstocks, but this route has been characterized byproduct inhibition. A recent study has revealed that overexpression of the efflux pump gene srpB boosted robustness of C. saccharoperbutylacetonicum, resulting in the growth capability in the high concentration of butanol and inhibitors (e.g., furfural and ferulic acid) (Jiménez-Bonilla et al., 2020). The biobutanol production via the ABE route faces high-economic risk due to the overproduction of acetone, which is lower boiling points and corrosive byproducts (Cai et al., 2022). This unfavored compound can be substantially converted into isopropanol through the isopropanol-butanol-ethanol pathway in C. beijerinckii strain, or be eliminated in engineered acetone-free producers, such as S. cerevisiae and E. coli (Ferreira dos Santos Vieira et al., 2020; Nawab et al., 2020; Veza et al., 2021).
However, the key challenges affecting the large-scale synthesis of biobutanol are mainly attributed to pretreatment costs, low yield, and downstream recovery costs. To bridge the gap between current production efficiency and that required for commercial viability of biobutanol, further research efforts should be focused on improving the production strains using novel numerous molecular tools.
The evolution of bioinformatics, high-throughput methods, and CRISPR/Cas9 system could overcome the barriers to pretreatment processing and improve the generation of bioproducts from lignocellulose biomass. Luo et al. (2020) elucidated the physiological mechanism of Clostridium acetobutylicum ATCC824 in response to phenolic inhibitors, which generated in hydrolysates during the lignocellulosic biomass pretreatment process by the combination of kinetic and transcriptional analysis, and explored the influence of phenolic stress on the production of butanol. Meanwhile, the transcriptional analysis revealed that the genes expression profile related to membrane transporters has been affected by phenolics, which has important guiding significance for achieving efficient synthesis of biobutanol from lignocellulose. Furthermore, genetic engineering of host strain proves to be an important research direction to produce high-value products from lignocellulosic biomass. Recently, different target genes have been modified in several species to improve the efficiency of saccharification and enhance the recalcitrance (Va et al., 2021). The butyrate fermentative supernatant has been utilized to produce butanol in Clostridium acetobutylicum/Saccharomyces cerevisiae co-culture system, and the increment reached 46.8% compared to control (Luo et al., 2017). Zhang et al. (2018) developed an inducible endogenous CRISPR-Cas9 platform, which generated mutant Δcat1::adhE2, revealing great potential of economic butanol production.
5-Hydroxymethylfurfural
5-Hydroxymethylfurfural (C6H6O3) has been investigated as a versatile biobased C5 and C6 platform molecule for the biorefinery, but high-production costs have hindered its development on an industrial scale (Delbecq et al., 2018). HMF is one of the most important C6-platform molecules for the production of numerous industrial chemicals, including LA, furfuryl alcohol, and furandicarboxylic acid (Li et al., 2019; Xu et al., 2020). HMP is produced industrially via the degradation of hexoses or through acid-catalyzed dehydration of cellulose (Li et al., 2019; Portillo Perez et al., 2019). The primary reason for the low yield of HMF is the rapid conversion to LA in aqueous solvents. Accordingly, recent studies have attempted to promote the synthesis of HMF and related products by employing homogenous and heterogeneous catalysts. Many studies investigating the heterogeneous acid-catalyzed conversion of fructose into HMF suggested that the high selectivity to HMF is controlled by the acid type, fructose tautomer distribution, and the solvent type (Svenningsen et al., 2018). A high-HMF yield from glucose approaching 60% was achieved by regulating the ratio of Lewis-to-Brønsted acid sites, with an optimal ratio of 0.3 (Swift et al., 2016). A higher selectivity of HMF (90%) synthesis from fructose, reaching 90%, was attained by using a sulfonic acid-functionalized acidic catalyst in dimethyl sulfoxide solvent at 120°C (Chen et al., 2014a). However, the separation process of HMF from solvent, such as DMSO, is the main drawback due to its high-boiling point, and, hence, alternative solvents (e.g., tetramethylene sulfone) or biphasic solvent systems are actually being explored to simplify the extraction of HMF (Agarwal et al., 2018). Sodium chloride in abiphasic system of water-based solvents has crucial benefits for the selective formation of HMF. An HMF yield of 53% was obtained using a biphasic solvent, comparing AlCl3/HCl as the aqueous phase and methyl isobutyl ketone as the organic phase, with the yield reaching 66.2% by adding 20 wt% NaCl (Guo et al., 2020). HMF is, arguably, the most versatile bio-derived platform molecule, but further efforts are needed to increase the yield of low environmental impact strategies.
Levulinic acid
Levulinic acid (C5H8O3) has been listed as one of the 12 key sugar-derived platform chemicals that can be produced mainly from HMF via a rehydration step. It can be used to produce a variety of biochemicals, including biofuels, flavoring agents, plasticizers, polymers, and antifreeze, through different reactions (Liu et al., 2018). Considering the promising potentials of various market applications, the sustainable production of LA from lignocellulosic biomass feedstock via biorefinery approaches has attracted significant interest. However, the synthesis of LA from lignocellulosic material subunits usually faces challenges, such as low yield, high equipment costs, severe environmental pollution, and undesired byproducts. The most wildly used pathway for LA production through consecutive one-pot transformation constitutes several steps: (i) the pretreatment of lignocellulosic biomass, (ii) hydrolysis of cellulose to glucose, (iii) isomerization of glucose to fructose, (iv) dehydration of hexoses (glucose and fructose) to HMF, and (v) rehydration of HMF to LA (Deng et al., 2015; Mukherjee et al., 2015). The inevitable formation of humins in these processes can significantly affect the efficiency of biomass. Homogeneous catalysis using SnCl4 allows the efficient production of LA from corncob residue, with a 64.6 mol% yield of LA after 60 min at 180°C (Zhao et al., 2019). However, concerns related to limited catalyst recyclability, reactor corrosion, and waste generation have inspired the development of heterogeneous catalysts (e.g., alkaline-treated zeolites Y) for the produce of LA and its derivatives (Bounoukta et al., 2022). Nevertheless, the production of LA and its derivatives is a promising area that merits further research to economically optimize the whole biorefinery process.
Current strategies for assessing the feasibility of a lignocellulosic biorefinery
The biofuels produced from various lignocellulosic biomass sources are generally considered clean and eco-friendly energy that can reduce GHG emissions. It is wildly accepted that biofuels and other chemicals derived from biomass residues present a promising route for solving climate change and an energy crisis, and several advanced biofuel companies are working worldwide to seize market share from fossil fuels (Lynd et al., 2017). However, this is not necessarily true due to the tradeoffs among positive and negative effects on the environment (Zucaro et al., 2016). Moreover, many of the biorefinery techniques require further technological innovation, funding, marketing, and lignocellulosic biomass valorization, which still precludes their feasibility on an industrial and commercial scale (Burg et al., 2018; Singhvi and Gokhale, 2019; Bora et al., 2020; Singhania et al., 2022). For this reason, it is necessary to develop a comprehensive assessment framework for the reliable and quantitative evaluation of environmental sustainability.
Life-cycle assessment is a scientifically accepted tool for assessing the possible environmental impacts of a specific product through qualitative, quantitative, confirmable, and manageable information (Singh and Olsen, 2011; Hiloidhari et al., 2017). There are many LCA methods and commercial software available to assess the direct environmental impact and indirect natural resource costs of a defined product or system. Typically, an LCA study consists of four stages. The first stage is the definition of goal and scope, aiming to identify the objective, limits, context, the functional unit, and environmental effects of the system. The second step is life cycle inventory, in which the life cycle of a product is simulated by quantifying all inputs (e.g., materials and energy), outputs (e.g., products and byproducts), and environmental releases (e.g., gas/particle emissions and wastewater). The third step, also known as life-cycle inventory analysis, is a technical process that assesses the potential effects of the inputs and outputs of a defined product. The final step, the interpretation, is an evaluation of all results related to the product, leading to conclusions and recommendations for minimizing the environmental burden. In practice, the type of lignocellulosic raw materials, the applicability of conversion technology, and optimal productivity should be carefully considered to maximize the product yield and profit. Espada et al. (2021) evaluated the environmental feasibility of a cardoon-to-bioethanol process using LCA, suggesting that steam explosion-based processes present the best environmental performance, with a dramatic reduction of primary energy demand (80%) and GHG emissions (45%). Bello et al. (2019) stated that solvents and energy demand are the critical points in the case of producing 2,5-furandicarboxylic acid and HMF from lignocellulosic feedstock. Compared to the conventional thermochemical process, the renewable electricity pathway has lower-energy intensity and a milder environmental impact. Accordingly, Patel et al. (2022) concluded that the processes of HMF production is the most significant factor in overall environmental impact in many categories. A similar study focusing on microalgae biomass, the most promising feedstock for third-generation biofuel production, demonstrated its great potential for bioethanol production, with a favorable net energy ratio (0.45) and net energy balance (–2,749.6 GJ y–1), as well as low water and land footprints in bioethanol production plants (Hossain et al., 2019).
A successful biorefinery not only requires promising and eco-friendly process technology but must also include optimized capital investment and operating costs. Techno-economic analysis (TEA) is a crucial approach for the commercialization of bioproducts from lignocellulosic biomass, enabling informed decision-making for process scale-up (Scown et al., 2021). TEA consists of several elements, including process design, process modeling, equipment sizing, a capital cost estimate, and an operating cost estimate, with the aim to recognize the crucial factors, such as the payback period and operating cost. The first TEA of HMF production was performed in 2010, in which the authors claimed that the high price of fructose cannot support a profitable scenario for HMF production from lignocellulosic biomass, no matter how much the other costs are minimized (Davidson et al., 2021). Numerous studies conducted detailed TAE by introducing different strategies, models, and types of biomass material to investigate the economic feasibility and production of biofuels on the industrial scale (Naveenkumar and Baskar, 2020; Aui et al., 2021; Thoppil and Zein, 2021). TEA of bioethanol production from wheat straw revealed that 20 million liters of ethanol could be obtained annually with a sale price equal to or greater than $2.57 L–1 (Hasanly et al., 2018). Chong et al. (2020) conducted TEA of third-generation bioethanol production from macroalgae cellulosic residue, finding that 15,833.3 kgh–1 of biomass material was required to produce 7,626 kgh–1 of bioethanol, leading a net energy ratio of 0.53 and a minimum selling price of $0.54 kg–1. The economic analysis of utilization of soybean straw for biofuel production suggested a minimum selling price of $1.94 kg–1biohydrogen, with a considerable payback period of 2.5 years (Okolie et al., 2021).
Life-cycle assessment and TEA are both powerful tools to optimize the process configuration and evaluate the potential risks when designing an industrialized biorefinery system. Further investigations are still needed to build a reliable and efficient framework that can ensure the practical application of lignocellulosic biomass and its valorization.
Conclusion and future perspectives
The low price and broad availability of a wide range of lignocellulosic materials can promote the expansion of the international biofuel market and help reduce carbon dioxide emissions on a global scale.
Nevertheless, an economically and ecologically viable processing methodology has not been fully developed to date. To overcome diverse bottlenecks, further research should consider the following facets: (i) opting for easily converted lignocellulosic materials, (ii) understanding the properties and synergy mechanism of different feedstocks to adopt a proper pre-treatment method, (iii) designing large-scale integration to reduce energy consumption and avoiding unnecessary losses, (iv) optimizing and rationalizing the equipment to enhance process economics, (v) efficient conversion and utilization of hemicellulosic sugars to increase ethanol production; (vi) effective separation and utilization of byproducts and maximization of the recovery of reaction reagents; (vii) promoting vigorous economic and political support to give a competitive edge to the fledgling businesses for the bioconversion of lignocellulose.
Author contributions
Y-XH conceived the topic. BZ reviewed the literature and prepared the first-draft manuscript. ZC, SY, and Y-XH revised the manuscript. ZC reviewed and edited the content. All authors contributed to the article and approved the submitted version.
Funding
We would like to acknowledge the financial support of the National Natural Science Foundation of China (Grant No. 21908007), the National Key R&D Program of China (Grant No. 2019YFA0904104), the Innovation Team Project of Colleges and Universities in Jinan (Grant No. 2019GXRC033), and the Fundamental Research Funds for the Central Universities.
Conflict of interest
The authors declare that the research was conducted in the absence of any commercial or financial relationships that could be construed as a potential conflict of interest.
Publisher’s note
All claims expressed in this article are solely those of the authors and do not necessarily represent those of their affiliated organizations, or those of the publisher, the editors and the reviewers. Any product that may be evaluated in this article, or claim that may be made by its manufacturer, is not guaranteed or endorsed by the publisher.
References
Abdin, Z., Zafaranloo, A., Rafiee, A., Mérida, W., Lipiński, W., and Khalilpour, K. R. (2020). Hydrogen as an energy vector. Renew. Sustain. Energy Rev. 120:109620. doi: 10.1016/j.rser.2019.109620
Agarwal, B., Kailasam, K., Sangwan, R. S., and Elumalai, S. (2018). Traversing the history of solid catalysts for heterogeneous synthesis of 5-hydroxymethylfurfural from carbohydrate sugars: a review. Renew. Sustain. Energy Rev. 82, 2408–2425. doi: 10.1016/j.rser.2017.08.088
Ahmad, E., Khan, T. S., Alam, M. I., Pant, K. K., and Ali Haider, M. (2020). Understanding reaction kinetics, deprotonation and solvation of brønsted acidic protons in heteropolyacid catalyzed synthesis of biorenewable alkyl levulinates. Chem. Eng. J. 400:125916. doi: 10.1016/j.cej.2020.125916
Alvira, P., Tomás-Pejó, E., Ballesteros, M., and Negro, M. J. (2010). Pretreatment technologies for an efficient bioethanol production process based on enzymatic hydrolysis: a review. Bioresour. Technol. 101, 4851–4861. doi: 10.1016/j.biortech.2009.11.093
Ammar, E. M., Martin, J., Brabo-Catala, L., and Philippidis, G. P. (2020). Propionic acid production by Propionibacterium freudenreichii using sweet sorghum bagasse hydrolysate. Appl. Microbiol. Biotechnol. 104, 9619–9629. doi: 10.1007/s00253-020-10953-w
Araújo, D., Costa, T., and Freitas, F. (2021). Biovalorization of lignocellulosic materials for xylitol production by the yeast Komagataella pastoris. Appl. Sci. 11:5516. doi: 10.3390/app11125516
Ariaeenejad, S., Kavousi, K., Mamaghani, A. S. A., Motahar, S. F. S., Nedaei, H., and Salekdeh, G. H. (2021). In-silico discovery of bifunctional enzymes with enhanced lignocellulose hydrolysis from microbiota big data. Int. J. Biol. Macromol. 177, 211–220. doi: 10.1016/j.ijbiomac.2021.02.014
Arumugham, T., AlYammahi, J., Rambabu, K., Hassan, S. W., and Banat, F. (2022). Supercritical CO2 pretreatment of date fruit biomass for enhanced recovery of fruit sugars. Sustain. Energy Techn. 52:102231. doi: 10.1016/j.seta.2022.102231
Ashokkumar, V., Venkatkarthick, R., Jayashree, S., Chuetor, S., Dharmaraj, S., Kumar, G., et al. (2022). Recent advances in lignocellulosic biomass for biofuels and value-added bioproducts - a critical review. Bioresour. Technol. 344:126195. doi: 10.1016/j.biortech.2021.126195
Aui, A., Wang, Y., and Mba-Wright, M. (2021). Evaluating the economic feasibility of cellulosic ethanol: a meta-analysis of techno-economic analysis studies. Renew. Sustain. Energy Rev. 145:111098. doi: 10.1016/j.rser.2021.111098
Baral, N. R., and Shah, A. (2017). Comparative techno-economic analysis of steam explosion, dilute sulfuric acid, ammonia fiber explosion and biological pretreatments of corn stover. Bioresour. Technol. 232, 331–343. doi: 10.1016/j.biortech.2017.02.068
Batog, J., and Wawro, A. (2021). Chemical and biological deconstruction in the conversion process of sorghum biomass for bioethanol. J. Nat. Fibers 1–12. doi: 10.1080/15440478.2021.1889444
Bello, S., Salim, I., Méndez-Trelles, P., Rodil, E., Feijoo, G., and Moreira, M. T. (2019). Environmental sustainability assessment of HMF and FDCA production from lignocellulosic biomass through life cycle assessment (LCA). Holzforschung 73, 105–115. doi: 10.1515/hf-2018-2100
Bhutto, A. W., Qureshi, K., Harijan, K., Abro, R., Abbas, T., Bazmi, A. A., et al. (2017). Insight into progress in pre-treatment of lignocellulosic biomass. Energy 122, 724–745. doi: 10.1016/j.energy.2017.01.005
Bichot, A., Lerosty, M., Radoiu, M., Méchin, V., Bernet, N., Delgenès, J.-P., et al. (2020). Decoupling thermal and non-thermal effects of the microwaves for lignocellulosic biomass pretreatment. Energy Convers. Manage. 203:112220. doi: 10.1016/j.enconman.2019.112220
Bonfiglio, F., Cagno, M., Yamakawa, C. K., and Mussatto, S. I. (2021). Production of xylitol and carotenoids from switchgrass and Eucalyptus globulus hydrolysates obtained by intensified steam explosion pretreatment. Ind. Crops Prod. 170:113800. doi: 10.1016/j.indcrop.2021.113800
Bora, R. R., Lei, M., Tester, J. W., Lehmann, J., and You, F. (2020). Life cycle assessment and technoeconomic analysis of thermochemical conversion technologies applied to poultry litter with energy and nutrient recovery. ACS Sustain. Chem. Eng. 8, 8436–8447. doi: 10.1021/acssuschemeng.0c02860
Bounoukta, C. E., Megías-Sayago, C., Ivanova, S., Ammari, F., Centeno, M. A., and Odriozola, J. A. (2022). Pursuing efficient systems for glucose transformation to levulinic acid: Homogeneous vs. heterogeneous catalysts and the effect of their co-action. Fuel 318:123712. doi: 10.1016/j.fuel.2022.123712
Burg, V., Bowman, G., Haubensak, M., Baier, U., and Thees, O. (2018). Valorization of an untapped resource: energy and greenhouse gas emissions benefits of converting manure to biogas through anaerobic digestion. Resour. Conserv. Recy. 136, 53–62. doi: 10.1016/j.resconrec.2018.04.004
Burhanoğlu, T., Sürmeli, Y., and Şanlı-Mohamed, G. (2020). Identification and characterization of novel thermostable α-amylase from Geobacillus sp. GS33. Int. J. Biol. Macromol. 164, 578–585. doi: 10.1016/j.ijbiomac.2020.07.171
Cai, D., Wen, J., Zhuang, Y., Huang, T., Si, Z., Qin, P., et al. (2022). Review of alternative technologies for acetone-butanol-ethanol separation: principles, state-of-the-art, and development trends. Sep. Purif. Technol. 298:121244. doi: 10.1016/j.seppur.2022.121244
Cao, X., Peng, X., Sun, S., Zhong, L., and Sun, R. (2014). Hydrothermal conversion of bamboo: identification and distribution of the components in solid residue, water-soluble and acetone-soluble fractions. J. Agric. Food Chem. 62, 12360–12365. doi: 10.1021/jf505074d
Chai, W. S., Bao, Y., Jin, P., Tang, G., and Zhou, L. (2021). A review on ammonia, ammonia-hydrogen and ammonia-methane fuels. Renew. Sustain. Energy Rev. 147:111254. doi: 10.1016/j.rser.2021.111254
Chandel, H., Kumar, P., Chandel, A. K., and Verma, M. L. (2022). Biotechnological advances in biomass pretreatment for bio-renewable production through nanotechnological intervention. Biomass. Convers. Bior. 1–23. doi: 10.1007/s13399-022-02746-2740
Chen, J., Li, K., Chen, L., Liu, R., Huang, X., and Ye, D. (2014a). Conversion of fructose into 5-hydroxymethylfurfural catalyzed by recyclable sulfonic acid-functionalized metal-organic frameworks. Green Chem. 16, 2490–2499. doi: 10.1039/C3GC42414F
Chen, J., Zhang, W., Zhang, H., Zhang, Q., and Huang, H. (2014b). Screw extrude steam explosion: a promising pretreatment of corn stover to enhance enzymatic hydrolysis. Bioresour. Technol. 161, 230–235. doi: 10.1016/j.biortech.2014.02.043
Chinwatpaiboon, P., Saejao, C., Boonsombuti, A., and Luengnaruemitchai, A. (2021). Optimization of ionic liquid 1-ethyl-3-methylimidazolium acetate pretreatment of Napier grass combined with acetic acid and ferric chloride under microwave radiation by response surface methodology. Biomass Convers. Bior. 1–12. doi: 10.1007/s13399-021-01901-1903
Chong, T. Y., Cheah, S. A., Ong, C. T., Wong, L. Y., Goh, C. R., Tan, I. S., et al. (2020). Techno-economic evaluation of third-generation bioethanol production utilizing the macroalgae waste: a case study in Malaysia. Energy 210:118491. doi: 10.1016/j.energy.2020.118491
Choudhary, J., Singh, S., and Nain, L. (2017). Bioprospecting thermotolerant ethanologenic yeasts for simultaneous saccharification and fermentation from diverse environments. J. Biosci. Bioeng. 123, 342–346. doi: 10.1016/j.jbiosc.2016.10.007
Chuetor, S., Barakat, A., Rouau, X., and Ruiz, T. (2017). Analysis of ground rice straw with a hydro-textural approach. Powder Technol. 310, 74–79. doi: 10.1016/j.powtec.2016.12.072
Chuetor, S., Champreda, V., and Laosiripojana, N. (2019). Evaluation of combined semi-humid chemo-mechanical pretreatment of lignocellulosic biomass in energy efficiency and waste generation. Bioresour. Technol. 292:121966. doi: 10.1016/j.biortech.2019.121966
Chundawat, S. P. S., Vismeh, R., Sharma, L. N., Humpula, J. F., da Costa, Sousa, L., et al. (2010). Multifaceted characterization of cell wall decomposition products formed during ammonia fiber expansion (AFEX) and dilute acid based pretreatments. Bioresour. Technol. 101, 8429–8438. doi: 10.1016/j.biortech.2010.06.027
Coca, M., González-Benito, G., and García-Cubero, M. (2016). Chemical oxidation with ozone as an efficient pretreatment of lignocellulosic materials. Environ. Technol. 2016, 409–429. doi: 10.1080/09593330.2021.1903565
Couturier, M., Ladevèze, S., Sulzenbacher, G., Ciano, L., Fanuel, M., Moreau, C., et al. (2018). Lytic xylan oxidases from wood-decay fungi unlock biomass degradation. Nat. Chem. Biol. 14, 306–310. doi: 10.1038/nchembio.2558
da Silva, A. R. G., Ortega, C. E. T., and Rong, B.-G. (2016). Techno-economic analysis of different pretreatment processes for lignocellulosic-based bioethanol production. Bioresour. Technol. 218, 561–570. doi: 10.1016/j.biortech.2016.07.007
Das, L., Achinivu, E. C., Barcelos, C. A., Sundstrom, E., Amer, B., Baidoo, E. E. K., et al. (2021). Deconstruction of woody biomass via protic and aprotic ionic liquid pretreatment for ethanol production. ACS Sustain. Chem. Eng. 9, 4422–4432. doi: 10.1021/acssuschemeng.0c07925
Das, M., and Maiti, S. K. (2022). Current knowledge on cyanobacterial biobutanol production: advances, challenges, and prospects. Rev. Environ. Sci. Biotechnol. 21, 483–516. doi: 10.1007/s11157-022-09618-z
Davidson, M. G., Elgie, S., Parsons, S., and Young, T. J. (2021). Production of HMF, FDCA and their derived products: a review of life cycle assessment (LCA) and techno-economic analysis (TEA) studies. Green Chem. 23, 3154–3171. doi: 10.1039/D1GC00721A
de Barros, R. D. R. O., de Sousa Paredes, R., Endo, T., da Silva, Bon, E. P., and Lee, S.-H. (2013). Association of wet disk milling and ozonolysis as pretreatment for enzymatic saccharification of sugarcane bagasse and straw. Bioresour. Technol. 136, 288–294. doi: 10.1016/j.biortech.2013.03.009
de Santana, J. S., da Silva, J. L., Dutra, E. D., Menezes, R. S. C., de Souza, R. B., and Pinheiro, I. O. (2021). Production of 1,3-propanediol by Lactobacillus diolivorans from agro-industrial residues and cactus cladode acid hydrolyzate. Appl. Biochem. Biotech. 193, 1585–1601. doi: 10.1007/s12010-021-03513-z
del Río, J. C., Rencoret, J., Gutiérrez, A., Elder, T., Kim, H., and Ralph, J. (2020). Lignin monomers from beyond the canonical monolignol biosynthetic pathway: another brick in the wall. ACS Sustain. Chem. Eng. 8, 4997–5012. doi: 10.1021/acssuschemeng.0c01109
Delbecq, F., Wang, Y., Muralidhara, A., El Ouardi, K., Marlair, G., and Len, C. (2018). Hydrolysis of hemicellulose and derivatives—a review of recent advances in the production of furfural. Front. Chem. 6:146. doi: 10.3389/fchem.2018.00146
Deng, R., Yue, J., Qu, H., Liang, L., Sun, D., Zhang, J., et al. (2018). Glucose-bridged silver nanoparticle assemblies for highly sensitive molecular recognition of sialic acid on cancer cells via surface-enhanced raman scattering spectroscopy. Talanta 179, 200–206. doi: 10.1016/j.talanta.2017.11.006
Deng, W., Zhang, Q., and Wang, Y. (2015). Catalytic transformations of cellulose and its derived carbohydrates into 5-hydroxymethylfurfural, levulinic acid, and lactic acid. Sci. China Chem. 58, 29–46. doi: 10.1007/s11426-014-5283-5288
Dey, N., Kumar, G., Vickram, A. S., Mohan, M., Singhania, R. R., Patel, A. K., et al. (2022). Nanotechnology-assisted production of value-added biopotent energy-yielding products from lignocellulosic biomass refinery - a review. Bioresour. Technol. 344:126171. doi: 10.1016/j.biortech.2021.126171
Du, C., Li, Y., Zong, H., Yuan, T., Yuan, W., and Jiang, Y. (2020). Production of bioethanol and xylitol from non-detoxified corn cob via a two-stage fermentation strategy. Bioresour. Technol. 310:123427. doi: 10.1016/j.biortech.2020.123427
Du, L., Cui, X., Li, H., Wang, Y., Fan, L., He, R., et al. (2021). Enhancing the enzymatic hydrolysis efficiency of lignocellulose assisted by artificial fusion enzyme of swollenin-xylanase. Ind. Crops Prod. 173:114106. doi: 10.1016/j.indcrop.2021.114106
Elgharbawy, A. A., Alam, M. Z., Moniruzzaman, M., and Goto, M. (2016). Ionic liquid pretreatment as emerging approaches for enhanced enzymatic hydrolysis of lignocellulosic biomass. Biochem. Eng. J. 109, 252–267. doi: 10.1016/j.bej.2016.01.021
Espada, J. J., Villalobos, H., and Rodríguez, R. (2021). Environmental assessment of different technologies for bioethanol production from Cynara cardunculus: a life cycle assessment study. Biomass Bioenerg. 144:105910. doi: 10.1016/j.biombioe.2020.105910
Fei, X., Jia, W., Wang, J., Chen, T., and Ling, Y. (2020). Study on enzymatic hydrolysis efficiency and physicochemical properties of cellulose and lignocellulose after pretreatment with electron beam irradiation. Int. J. Biol. Macromol. 145, 733–739. doi: 10.1016/j.ijbiomac.2019.12.232
Ferreira dos Santos Vieira, C., Maugeri Filho, F., Maciel Filho, R., and Pinto Mariano, A. (2020). Isopropanol-butanol-ethanol (IBE) production in repeated-batch cultivation of Clostridium beijerinckii DSM 6423 immobilized on sugarcane bagasse. Fuel 263:116708. doi: 10.1016/j.fuel.2019.116708
Fonseca, B. G., Mateo, S., Roberto, I. C., Sánchez, S., and Moya, A. J. (2020). Bioconversion in batch bioreactor of olive-tree pruning biomass optimizing treatments for ethanol production. Biochem. Eng. J. 164:107793. doi: 10.1016/j.bej.2020.107793
Fu, H., Zhang, H., Guo, X., Yang, L., and Wang, J. (2022). Elimination of carbon catabolite repression in Clostridium tyrobutyricum for enhanced butyric acid production from lignocellulosic hydrolysates. Bioresour. Technol. 357:127320. doi: 10.1016/j.biortech.2022.127320
George, A., Brandt, A., Tran, K., Zahari, S. M. S. N. S., Klein-Marcuschamer, D., Sun, N., et al. (2015). Design of low-cost ionic liquids for lignocellulosic biomass pretreatment. Green Chem. 17, 1728–1734. doi: 10.1039/C4GC01208A
Giap, V. D., Duc, H. T., Huong, P. T. M., Hanh, D. T., Nghi, D. H., Duy, V. D., et al. (2022). Purification and characterization of lignin peroxidase from white-rot fungi Pleurotus pulmonarius CPG6 and its application in decolorization of synthetic textile dyes. J. Gen. Appl. Microbiol. Online ahead of print doi: 10.2323/jgam.2022.05.005
Govarthanan, M., Manikandan, S., Subbaiya, R., Krishnan, R. Y., Srinivasan, S., Karmegam, N., et al. (2022). Emerging trends and nanotechnology advances for sustainable biogas production from lignocellulosic waste biomass: a critical review. Fuel 312:122928. doi: 10.1016/j.fuel.2021.122928
Grubišić, M., Mihajlovski, K., Gruičić, A. M., Beluhan, S., Šantek, B., and Ivančić Šantek, M. (2021). Strategies for improvement of lipid production by yeast Trichosporon oleaginosus from lignocellulosic biomass. J. Fungi 7:934. doi: 10.3390/jof7110934
Guo, T., Li, X., Liu, X., Guo, Y., and Wang, Y. (2018). Catalytic transformation of lignocellulosic biomass into arenes, 5-Hydroxymethylfurfural, and furfural. Chem. Sus. Chem. 11, 2758–2765. doi: 10.1002/cssc.201800967
Guo, W., Heeres, H. J., and Yue, J. (2020). Continuous synthesis of 5-hydroxymethylfurfural from glucose using a combination of AlCl3 and HCl as catalyst in a biphasic slug flow capillary microreactor. Chem. Eng. J. 381:122754. doi: 10.1016/j.cej.2019.122754
Hämäläinen, V., Barajas-López, J. D. D., Berlina, Y., Álvarez-Rafael, R., and Birikh, K. (2021). New thermostable endoglucanase from Spirochaeta thermophila and its mutants with altered substrate preferences. Appl. Microbiol. Biotechnol. 105, 1133–1145. doi: 10.1007/s00253-020-11077-x
Han, Y., Ma, W., Zhou, B., Yang, X., Salah, A., Li, C., et al. (2020). Effects of straw-return method for the maize-rice rotation system on soil properties and crop yields. Agronomy 10:461. doi: 10.3390/agronomy10040461
Hasanly, A., Khajeh Talkhoncheh, M., and Karimi Alavijeh, M. (2018). Techno-economic assessment of bioethanol production from wheat straw: a case study of Iran. Clean Technol. Envir. Policy 20, 357–377. doi: 10.1007/s10098-017-1476-1470
Heleniak, T. (2021). The future of the Arctic populations. Polar Geography 44, 136–152. doi: 10.1080/1088937X.2019.1707316
Hiloidhari, M., Baruah, D. C., Singh, A., Kataki, S., Medhi, K., Kumari, S., et al. (2017). Emerging role of Geographical Information System (GIS), Life Cycle Assessment (LCA) and spatial LCA (GIS-LCA) in sustainable bioenergy planning. Bioresour. Technol. 242, 218–226. doi: 10.1016/j.biortech.2017.03.079
Hossain, N., Zaini, J., and Indra Mahlia, T. M. (2019). Life cycle assessment, energy balance and sensitivity analysis of bioethanol production from microalgae in a tropical country. Renew. Sustain. Energy Rev. 115:109371. doi: 10.1016/j.rser.2019.109371
Hsu, T.-C., Guo, G.-L., Chen, W.-H., and Hwang, W.-S. (2010). Effect of dilute acid pretreatment of rice straw on structural properties and enzymatic hydrolysis. Bioresour. Technol. 101, 4907–4913. doi: 10.1016/j.biortech.2009.10.009
Jiang, M., Zhao, M., Zhou, Z., Huang, T., Chen, X., and Wang, Y. (2011). Isolation of cellulose with ionic liquid from steam exploded rice straw. Ind. Crops Prod. 33, 734–738. doi: 10.1016/j.indcrop.2011.01.015
Jiang, Y., Liu, J., Jiang, W., Yang, Y., and Yang, S. (2015). Current status and prospects of industrial bio-production of n-butanol in China. Biotechnol. Adv. 33, 1493–1501. doi: 10.1016/j.biotechadv.2014.10.007
Jiménez-Bonilla, P., Zhang, J., Wang, Y., Blersch, D., de-Bashan, L.-E., Guo, L., et al. (2020). Enhancing the tolerance of Clostridium saccharoperbutylacetonicum to lignocellulosic-biomass-derived inhibitors for efficient biobutanol production by overexpressing efflux pumps genes from Pseudomonas putida. Bioresour. Technol. 312:123532. doi: 10.1016/j.biortech.2020.123532
Kang, S., Fu, J., and Zhang, G. (2018). From lignocellulosic biomass to levulinic acid: a review on acid-catalyzed hydrolysis. Renew. Sustain. Energy Rev. 94, 340–362. doi: 10.1016/j.rser.2018.06.016
Kang, X., Kirui, A., Dickwella Widanage, M. C., Mentink-Vigier, F., Cosgrove, D. J., and Wang, T. (2019). Lignin-polysaccharide interactions in plant secondary cell walls revealed by solid-state NMR. Nat. Commun. 10:347. doi: 10.1038/s41467-018-08252-8250
Karimi, K., Shafiei, M., and Kumar, R. (2013). “Progress in physical and chemical pretreatment of lignocellulosic biomass,” in Biofuel Technologies, eds V. K. Gupta and M. G. Tuohy (Berlin: Springer), 53–96.
Karnaouri, A., Asimakopoulou, G., Kalogiannis, K. G., Lappas, A., and Topakas, E. (2020). Efficient d-lactic acid production by Lactobacillus delbrueckii subsp. bulgaricus through conversion of organosolv pretreated lignocellulosic biomass. Biomass Bioenerg. 140:105672. doi: 10.1016/j.biombioe.2020.105672
Kim, D.-E., and Pan, X. (2010). Preliminary study on converting hybrid poplar to high-value chemicals and lignin using organosolv ethanol process. Industrial Eng. Chem. Res. 49, 12156–12163.
Kim, D. G., Yoo, S. W., Kim, M., Ko, J. K., Um, Y., and Oh, M.-K. (2020). Improved 2,3-butanediol yield and productivity from lignocellulose biomass hydrolysate in metabolically engineered Enterobacter aerogenes. Bioresour. Technol. 309:123386. doi: 10.1016/j.biortech.2020.123386
Kim, J. S., Lee, Y., and Kim, T. H. (2016). A review on alkaline pretreatment technology for bioconversion of lignocellulosic biomass. Bioresour. Technol. 199, 42–48. doi: 10.1016/j.biortech.2015.08.085
Kuglarz, M., Gunnarsson, I. B., Svensson, S.-E., Prade, T., Johansson, E., and Angelidaki, I. (2014). Ethanol production from industrial hemp: effect of combined dilute acid/steam pretreatment and economic aspects. Bioresour. Technol. 163, 236–243. doi: 10.1016/j.biortech.2014.04.049
Kumar, B., Bhardwaj, N., Agrawal, K., Chaturvedi, V., and Verma, P. (2020). Current perspective on pretreatment technologies using lignocellulosic biomass: an emerging biorefinery concept. Fuel Process. Technol. 199:106244. doi: 10.1016/j.fuproc.2019.106244
Ladeira Ázar, R. I. S., Bordignon-Junior, S. E., Laufer, C., Specht, J., Ferrier, D., et al. (2020). Effect of lignin content on cellulolytic saccharification of liquid hot water pretreated sugarcane bagasse. Molecules 25:623. doi: 10.3390/molecules25030623
Lappe, A., Jankowski, N., Albrecht, A., and Koschorreck, K. (2021). Characterization of a thermotolerant aryl-alcohol oxidase from Moesziomyces antarcticus oxidizing 5-hydroxymethyl-2-furancarboxylic acid. Appl. Microbiol. Biotechnol. 105, 8313–8327. doi: 10.1007/s00253-021-11557-11558
Lee, J. T. E., Khan, M. U., Tian, H., Ee, A. W. L., Lim, E. Y., Dai, Y., et al. (2020). Improving methane yield of oil palm empty fruit bunches by wet oxidation pretreatment: Mesophilic and thermophilic anaerobic digestion conditions and the associated global warming potential effects. Energy Convers. Manage. 225:113438. doi: 10.1016/j.enconman.2020.113438
Lee, J. W., Lee, Y.-G., Jin, Y.-S., and Rao, C. V. (2021). Metabolic engineering of non-pathogenic microorganisms for 2,3-butanediol production. Appl. Microbiol. Biotechnol. 105, 5751–5767. doi: 10.1007/s00253-021-11436-11432
Li, M.-F., Yang, S., and Sun, R.-C. (2016a). Recent advances in alcohol and organic acid fractionation of lignocellulosic biomass. Bioresour. Technol. 200, 971–980. doi: 10.1016/j.biortech.2015.10.004
Li, W., Liu, Q., Ma, Q., Zhang, T., Ma, L., Jameel, H., et al. (2016b). A two-stage pretreatment process using dilute hydrochloric acid followed by Fenton oxidation to improve sugar recovery from corn stover. Bioresour. Technol. 219, 753–756. doi: 10.1016/j.biortech.2016.08.025
Li, X., Xu, R., Yang, J., Nie, S., Liu, D., Liu, Y., et al. (2019). Production of 5-hydroxymethylfurfural and levulinic acid from lignocellulosic biomass and catalytic upgradation. Ind. Crops Prod. 130, 184–197. doi: 10.1016/j.indcrop.2018.12.082
Li, Y., Yoo, K., Lee, D.-K., Kim, J. Y., Kim, H., Kim, B., et al. (2013). Photovoltaic properties of high efficiency plastic dye-sensitized solar cells employing interparticle binding agent “nanoglue”. Nanoscale 5, 4711–4719. doi: 10.1039/C2NR33352J
Liu, C., Wang, X., Lin, F., Zhang, H., and Xiao, R. (2018). Structural elucidation of industrial bioethanol residual lignin from corn stalk: a potential source of vinyl phenolics. Fuel Process. Technol. 169, 50–57. doi: 10.1016/j.fuproc.2017.09.008
Liu, Q., He, W.-Q., Aguedo, M., Xia, X., Bai, W.-B., Dong, Y.-Y., et al. (2021). Microwave-assisted alkali hydrolysis for cellulose isolation from wheat straw: influence of reaction conditions and non-thermal effects of microwave. Carbohyd. Polym. 253:117170. doi: 10.1016/j.carbpol.2020.117170
Liu, Y., Zhou, H., Wang, L., Wang, S., and Fan, L. (2016). Improving Saccharomyces cerevisiae growth against lignocellulose-derived inhibitors as well as maximizing ethanol production by a combination proposal of γ-irradiation pretreatment with in situ detoxification. Chem. Eng. J. 287, 302–312. doi: 10.1016/j.cej.2015.10.086
López-Abelairas, M., Álvarez Pallín, M., Salvachúa, D., Lú-Chau, T., Martínez, M. J., and Lema, J. M. (2013). Optimisation of the biological pretreatment of wheat straw with white-rot fungi for ethanol production. Bioprocess Biosystems Eng. 36, 1251–1260. doi: 10.1007/s00449-012-0869-z
Lopez-Hidalgo, A. M., Balderas Hernandez, V. E., and De Leon-Rodriguez, A. (2021). Scale-up of hydrogen and ethanol co-production by an engineered Escherichia coli. Fuel 300:121002. doi: 10.1016/j.fuel.2021.121002
López-Linares, J. C., Ballesteros, I., Tourán, J., Cara, C., Castro, E., Ballesteros, M., et al. (2015). Optimization of uncatalyzed steam explosion pretreatment of rapeseed straw for biofuel production. Bioresour. Technol. 190, 97–105. doi: 10.1016/j.biortech.2015.04.066
Luo, H., Zeng, Q., Han, S., Wang, Z., Dong, Q., Bi, Y., et al. (2017). High-efficient n-butanol production by co-culturing Clostridium acetobutylicum and Saccharomyces cerevisiae integrated with butyrate fermentative supernatant addition. World J. Microbiol. Biotechnol. 33:76. doi: 10.1007/s11274-017-2246-2241
Luo, H., Zheng, P., Bilal, M., Xie, F., Zeng, Q., Zhu, C., et al. (2020). Efficient bio-butanol production from lignocellulosic waste by elucidating the mechanisms of Clostridium acetobutylicum response to phenolic inhibitors. Sci. Total Environ. 710:136399. doi: 10.1016/j.scitotenv.2019.136399
Lynd, L. R., Liang, X., Biddy, M. J., Allee, A., Cai, H., Foust, T., et al. (2017). Cellulosic ethanol: status and innovation. Curr. Opin. Biotechnol. 45, 202–211. doi: 10.1016/j.copbio.2017.03.008
Ma, Y., Shen, Y., and Liu, Y. (2020). State of the art of straw treatment technology: challenges and solutions forward. Bioresour. Technol. 313:123656. doi: 10.1016/j.biortech.2020.123656
Machado, A. D. S., and Ferraz, A. (2017). Biological pretreatment of sugarcane bagasse with basidiomycetes producing varied patterns of biodegradation. Bioresour. Technol. 225, 17–22. doi: 10.1016/j.biortech.2016.11.053
Mahajan, R., Chandel, S., Puniya, A. K., and Goel, G. (2020). Effect of pretreatments on cellulosic composition and morphology of pine needle for possible utilization as substrate for anaerobic digestion. Biomass Bioenerg. 141:105705. doi: 10.1016/j.biombioe.2020.105705
Maleki, M., Shahraki, M. F., Kavousi, K., Ariaeenejad, S., and Hosseini Salekdeh, G. (2020). A novel thermostable cellulase cocktail enhances lignocellulosic bioconversion and biorefining in a broad range of pH. Int. J. Biol. Macromol. 154, 349–360. doi: 10.1016/j.ijbiomac.2020.03.100
Marta, K., Paulina, R., Magda, D., Anna, N., Aleksandra, K., Marcin, D., et al. (2020). Evaluation of ultrasound pretreatment for enhanced anaerobic digestion of sida hermaphrodita. BioEnergy Res. 13, 824–832. doi: 10.1007/s12155-020-10108-10109
Martínez, P. M., Bakker, R., Harmsen, P., Gruppen, H., and Kabel, M. (2015). Importance of acid or alkali concentration on the removal of xylan and lignin for enzymatic cellulose hydrolysis. Ind. Crops Prod. 64, 88–96. doi: 10.1016/j.indcrop.2014.10.031
Mathew, A. K., Chaney, K., Crook, M., and Humphries, A. C. (2011). Alkaline pre-treatment of oilseed rape straw for bioethanol production: evaluation of glucose yield and pre-treatment energy consumption. Bioresour. Technol. 102, 6547–6553. doi: 10.1016/j.biortech.2011.03.067
Meehnian, H., Jana, A. K., and Jana, M. M. (2017). Pretreatment of cotton stalks by synergistic interaction of Daedalea flavida and Phlebia radiata in co-culture for improvement in delignification and saccharification. Int. Biodeterior. Biodegrad. 117, 68–77. doi: 10.1016/j.ibiod.2016.11.022
Mesa, L., López, N., Cara, C., Castro, E., González, E., and Mussatto, S. I. (2016). Techno-economic evaluation of strategies based on two steps organosolv pretreatment and enzymatic hydrolysis of sugarcane bagasse for ethanol production. Renew. Energ. 86, 270–279. doi: 10.1016/j.renene.2015.07.105
Mohiddin, M. N. B., Tan, Y. H., Seow, Y. X., Kansedo, J., Mubarak, N. M., Abdullah, M. O., et al. (2021). Evaluation on feedstock, technologies, catalyst and reactor for sustainable biodiesel production: a review. J. Ind. Eng. Chem. 98, 60–81. doi: 10.1016/j.jiec.2021.03.036
Momayez, F., Karimi, K., and Horváth, I. S. (2018). Enhancing ethanol and methane production from rice straw by pretreatment with liquid waste from biogas plant. Energy Convers. Manage. 178, 290–298. doi: 10.1016/j.enconman.2018.10.023
Mondal, S., Santra, S., Rakshit, S., Kumar Halder, S., Hossain, M., and Chandra Mondal, K. (2022). Saccharification of lignocellulosic biomass using an enzymatic cocktail of fungal origin and successive production of butanol by Clostridium acetobutylicum. Bioresour. Technol. 343:126093. doi: 10.1016/j.biortech.2021.126093
Mostofian, B., Cai, C. M., Smith, M. D., Petridis, L., Cheng, X., Wyman, C. E., et al. (2016). Local phase separation of co-solvents enhances pretreatment of biomass for bioenergy applications. J. Am. Chem. Soc. 138, 10869–10878. doi: 10.1021/jacs.6b03285
Motte, J.-C., Sambusiti, C., Dumas, C., and Barakat, A. (2015). Combination of dry dark fermentation and mechanical pretreatment for lignocellulosic deconstruction: an innovative strategy for biofuels and volatile fatty acids recovery. Appl. Energy 147, 67–73. doi: 10.1016/j.apenergy.2015.02.042
Mukherjee, A., Dumont, M.-J., and Raghavan, V. (2015). Review: sustainable production of hydroxymethylfurfural and levulinic acid: challenges and opportunities. Biomass Bioenerg. 72, 143–183. doi: 10.1016/j.biombioe.2014.11.007
Narron, R. H., Kim, H., Chang, H.-M., Jameel, H., and Park, S. (2016). Biomass pretreatments capable of enabling lignin valorization in a biorefinery process. Curr. Opin. Biotechnol. 38, 39–46. doi: 10.1016/j.copbio.2015.12.018
Naveenkumar, R., and Baskar, G. (2020). Optimization and techno-economic analysis of biodiesel production from Calophyllum inophyllum oil using heterogeneous nanocatalyst. Bioresour. Technol. 315:123852. doi: 10.1016/j.biortech.2020.123852
Nawab, S., Wang, N., Ma, X., and Huo, Y.-X. (2020). Genetic engineering of non-native hosts for 1-butanol production and its challenges: a review. Microbial Cell Fact. 19:79. doi: 10.1186/s12934-020-01337-w
Okolie, J. A., Nanda, S., Dalai, A. K., and Kozinski, J. A. (2021). Techno-economic evaluation and sensitivity analysis of a conceptual design for supercritical water gasification of soybean straw to produce hydrogen. Bioresour. Technol. 331:125005. doi: 10.1016/j.biortech.2021.125005
Ong, V. Z., Wu, T. Y., Chu, K. K. L., Sun, W. Y., and Shak, K. P. Y. (2021). A combined pretreatment with ultrasound-assisted alkaline solution and aqueous deep eutectic solvent for enhancing delignification and enzymatic hydrolysis from oil palm fronds. Ind. Crops Prod. 160:112974. doi: 10.1016/j.indcrop.2020.112974
Paramasivan, S., Sankar, S., Senthil Velavan, R., Krishnakumar, T., Batcha, R. S. I., and Muthuvelu, K. S. (2021). Assessing the potential of lignocellulosic energy crops as an alternative resource for bioethanol production using ultrasound assisted dilute acid pretreatment. Mater. Today Proc. 45, 3279–3285. doi: 10.1016/j.matpr.2020.12.470
Paschos, T., Xiros, C., and Christakopoulos, P. (2015). Simultaneous saccharification and fermentation by co-cultures of Fusarium oxysporum and Saccharomyces cerevisiae enhances ethanol production from liquefied wheat straw at high solid content. Ind. Crops Prod. 76, 793–802. doi: 10.1016/j.indcrop.2015.07.061
Patel, P., Schwartz, D., Wang, X., Lin, R., Ajao, O., and Seifitokaldani, A. (2022). Technoeconomic and life-cycle assessment for electrocatalytic production of furandicarboxylic acid. ACS Sustain. Chem. Eng. 10, 4206–4217. doi: 10.1021/acssuschemeng.1c08602
Portillo Perez, G., Mukherjee, A., and Dumont, M.-J. (2019). Insights into HMF catalysis. J. Ind. Eng. Chem. 70, 1–34. doi: 10.1016/j.jiec.2018.10.002
Pratto, B., dos Santos-Rocha, M. S. R., Longati, A. A., de Sousa Júnior, R., and Cruz, A. J. G. (2020). Experimental optimization and techno-economic analysis of bioethanol production by simultaneous saccharification and fermentation process using sugarcane straw. Bioresour. Technol. 297:122494. doi: 10.1016/j.biortech.2019.122494
Pugazhendhi, A., Mathimani, T., Varjani, S., Rene, E. R., Kumar, G., Kim, S.-H., et al. (2019). Biobutanol as a promising liquid fuel for the future - recent updates and perspectives. Fuel 253, 637–646. doi: 10.1016/j.fuel.2019.04.139
Qiao, X., Zhao, C., Shao, Q., and Hassan, M. (2018). Structural characterization of corn stover lignin after hydrogen peroxide presoaking prior to ammonia fiber expansion pretreatment. Energy Fuels 32, 6022–6030. doi: 10.1021/acs.energyfuels.8b00951
Radveikienė, I., Vidžiûnaitė, R., Meškienė, R., Meškys, R., and Časaitė, V. (2021). Characterization of a yellow laccase from Botrytis cinerea 241. J. Fungi 7:143. doi: 10.3390/jof7020143
Rahayu, F., Tajima, T., Kato, J., Kato, S., and Nakashimada, Y. (2020). Ethanol yield and sugar usability in thermophilic ethanol production from lignocellulose hydrolysate by genetically engineered Moorella thermoacetica. J. Biosci. Bioeng. 129, 160–164. doi: 10.1016/j.jbiosc.2019.08.008
Rai, N., Yadav, M., and Yadav, H. S. (2020). Purification and characterization of versatile peroxidase from citrus sinensis leaf extract and its application in green chemistry. Anal. Chem. Lett. 10, 524–536. doi: 10.1080/22297928.2020.1833751
Rezania, S., Oryani, B., Cho, J., Talaiekhozani, A., Sabbagh, F., Hashemi, B., et al. (2020). Different pretreatment technologies of lignocellulosic biomass for bioethanol production. an overview Energy 199:117457. doi: 10.1016/j.energy.2020.117457
Rogelj, J., Popp, A., Calvin, K. V., Luderer, G., Emmerling, J., Gernaat, D., et al. (2018). Scenarios towards limiting global mean temperature increase below 1.5 °C. Nat. Climate Change 8, 325–332. doi: 10.1038/s41558-018-0091-93
Roussou, S., Albergati, A., Liang, F., and Lindblad, P. (2021). Engineered cyanobacteria with additional overexpression of selected Calvin-Benson-Bassham enzymes show further increased ethanol production. Metab. Eng. Commun. 12:e00161. doi: 10.1016/j.mec.2021.e00161
Sajid, M., and Płotka-Wasylka, J. (2020). Nanoparticles: synthesis, characteristics, and applications in analytical and other sciences. Microchem. J. 154:104623. doi: 10.1016/j.microc.2020.104623
Saldarriaga-Hernández, S., Velasco-Ayala, C., Leal-Isla Flores, P., de Jesús Rostro-Alanis, M., Parra-Saldivar, R., Iqbal, H. M. N., et al. (2020). Biotransformation of lignocellulosic biomass into industrially relevant products with the aid of fungi-derived lignocellulolytic enzymes. Int. J. Biol. Macromol. 161, 1099–1116. doi: 10.1016/j.ijbiomac.2020.06.047
Saratale, G. D., and Oh, M.-K. (2015). Improving alkaline pretreatment method for preparation of whole rice waste biomass feedstock and bioethanol production. RSC Adv. 5, 97171–97179. doi: 10.1039/C5RA17797A
Saritha, M., and Arora, A. (2012). Biological pretreatment of lignocellulosic substrates for enhanced delignification and enzymatic digestibility. Indian J. Microbiol. 52, 122–130. doi: 10.1007/s12088-011-0199-x
Sarkar, P., Mukherjee, M., Goswami, G., and Das, D. (2020). Adaptive laboratory evolution induced novel mutations in Zymomonas mobilis ATCC ZW658: a potential platform for co-utilization of glucose and xylose. J. Ind. Microbiol. Biotechnol. 47, 329–341. doi: 10.1007/s10295-020-02270-y
Sarker, T. R., Pattnaik, F., Nanda, S., Dalai, A. K., Meda, V., and Naik, S. (2021). Hydrothermal pretreatment technologies for lignocellulosic biomass: a review of steam explosion and subcritical water hydrolysis. Chemosphere 284:131372. doi: 10.1016/j.chemosphere.2021.131372
Schneider, L., Haverinen, J., Jaakkola, M., and Lassi, U. (2017). Pretreatment and fractionation of lignocellulosic barley straw by mechanocatalysis. Chem. Eng. J. 327, 898–905. doi: 10.1016/j.cej.2017.06.175
Scown, C. D., Baral, N. R., Yang, M., Vora, N., and Huntington, T. (2021). Technoeconomic analysis for biofuels and bioproducts. Curr. Opin. Biotechnol. 67, 58–64. doi: 10.1016/j.copbio.2021.01.002
Shen, F., Xiong, X., Fu, J., Yang, J., Qiu, M., Qi, X., et al. (2020). Recent advances in mechanochemical production of chemicals and carbon materials from sustainable biomass resources. Renew. Sustain. Energy Rev. 130:109944. doi: 10.1016/j.rser.2020.109944
Shi, S., Guan, W., Blersch, D., and Li, J. (2021). Improving the enzymatic digestibility of alkaline-pretreated lignocellulosic biomass using polyDADMAC. Ind. Crops Prod. 162:113244. doi: 10.1016/j.indcrop.2021.113244
Shill, K., Padmanabhan, S., Xin, Q., Prausnitz, J. M., Clark, D. S., and Blanch, H. W. (2011). Ionic liquid pretreatment of cellulosic biomass: enzymatic hydrolysis and ionic liquid recycle. Biotechnol. Bioeng. 108, 511–520. doi: 10.1002/bit.23014
Shuai, L., Amiri, M. T., Questell-Santiago, Y. M., Héroguel, F., Li, Y., Kim, H., et al. (2016). Formaldehyde stabilization facilitates lignin monomer production during biomass depolymerization. Science 354, 329–333. doi: 10.1126/science.aaf7810
Sindhu, R., Binod, P., Mathew, A. K., Abraham, A., Gnansounou, E., Ummalyma, S. B., et al. (2017). Development of a novel ultrasound-assisted alkali pretreatment strategy for the production of bioethanol and xylanases from chili post harvest residue. Bioresour. Technol. 242, 146–151. doi: 10.1016/j.biortech.2017.03.001
Sindhu, R., Binod, P., and Pandey, A. (2016). Biological pretreatment of lignocellulosic biomass–an overview. Bioresour. Technol. 199, 76–82. doi: 10.1016/j.biortech.2015.08.030
Singh, A., and Olsen, S. I. (2011). A critical review of biochemical conversion, sustainability and life cycle assessment of algal biofuels. Appl. Energy 88, 3548–3555. doi: 10.1016/j.apenergy.2010.12.012
Singh, S., Dhillon, A., and Goyal, A. (2020). Enhanced catalytic efficiency of Bacillus amyloliquefaciens SS35 endoglucanase by ultraviolet directed evolution and mutation analysis. Renew. Energ. 151, 1124–1133. doi: 10.1016/j.renene.2019.11.105
Singh, S., Sinha, R., and Kundu, S. (2022). Role of organosolv pretreatment on enzymatic hydrolysis of mustard biomass for increased saccharification. Biomass Convers. Bior. 12, 1657–1668. doi: 10.1007/s13399-020-01251-1256
Singh, S. K. (2021). Biological treatment of plant biomass and factors affecting bioactivity. J. Clean. Prod. 279:123546. doi: 10.1016/j.jclepro.2020.123546
Singh, T., Alhazmi, A., Mohammad, A., Srivastava, N., Haque, S., Sharma, S., et al. (2021). Integrated biohydrogen production via lignocellulosic waste: opportunity, challenges & future prospects. Bioresour. Technol. 338:125511. doi: 10.1016/j.biortech.2021.125511
Singhania, R. R., Patel, A. K., Raj, T., Chen, C.-W., Ponnusamy, V. K., Tahir, N., et al. (2022). Lignin valorisation via enzymes: a sustainable approach. Fuel 311:122608. doi: 10.1016/j.fuel.2021.122608
Singhvi, M. S., and Gokhale, D. V. (2019). Lignocellulosic biomass: hurdles and challenges in its valorization. Appl. Microbiol. Biotechnol. 103, 9305–9320. doi: 10.1007/s00253-019-10212-10217
Smichi, N., Messaoudi, Y., Allaf, K., and Gargouri, M. (2020). Steam explosion (SE) and instant controlled pressure drop (DIC) as thermo-hydro-mechanical pretreatment methods for bioethanol production. Bioprocess Biosystems Eng. 43, 945–957. doi: 10.1007/s00449-020-02297-2296
Snehesh, A. S., Mukunda, H. S., Mahapatra, S., and Dasappa, S. (2017). Fischer-tropsch route for the conversion of biomass to liquid fuels - technical and economic analysis. Energy 130, 182–191. doi: 10.1016/j.energy.2017.04.101
Soltaninejad, A., Jazini, M., and Karimi, K. (2022). Biorefinery for efficient xanthan gum, ethanol, and biogas production from potato crop residues. Biomass Bioenerg. 158:106354. doi: 10.1016/j.biombioe.2022.106354
Sun, F. F., Zhao, X., Hong, J., Tang, Y., Wang, L., Sun, H., et al. (2016a). Industrially relevant hydrolyzability and fermentability of sugarcane bagasse improved effectively by glycerol organosolv pretreatment. Biotechnol. Biofuels 9, 1–13. doi: 10.1186/s13068-016-0472-477
Sun, S., Sun, S., Cao, X., and Sun, R. (2016b). The role of pretreatment in improving the enzymatic hydrolysis of lignocellulosic materials. Bioresour. Technol. 199, 49–58. doi: 10.1016/j.biortech.2015.08.061
Sun, S., Cao, X., Sun, S., Xu, F., Song, X., Sun, R.-C., et al. (2014). Improving the enzymatic hydrolysis of thermo-mechanical fiber from Eucalyptus urophylla by a combination of hydrothermal pretreatment and alkali fractionation. Biotechnol. Biofuels 7, 1–12. doi: 10.1186/s13068-014-0116-118
Svenningsen, G. S., Kumar, R., Wyman, C. E., and Christopher, P. (2018). Unifying mechanistic analysis of factors controlling selectivity in fructose dehydration to 5-hydroxymethylfurfural by homogeneous acid catalysts in aprotic solvents. ACS Catal. 8, 5591–5600. doi: 10.1021/acscatal.8b01197
Swift, T. D., Nguyen, H., Erdman, Z., Kruger, J. S., Nikolakis, V., and Vlachos, D. G. (2016). Tandem Lewis acid/Brønsted acid-catalyzed conversion of carbohydrates to 5-hydroxymethylfurfural using zeolite beta. J. Catal. 333, 149–161. doi: 10.1016/j.jcat.2015.10.009
Taha, M., Shahsavari, E., Al-Hothaly, K., Mouradov, A., Smith, A. T., Ball, A. S., et al. (2015). Enhanced biological straw saccharification through coculturing of lignocellulose-degrading microorganisms. Appl. Biochem. Biotech. 175, 3709–3728. doi: 10.1007/s12010-015-1539-1539
Tahir, N., Nadeem, F., and Zhang, Q. (2021). Optimisation of photo-fermentative biohydrogen production from corn stover through the synergetic effect of ultrafine grinding and SnO2 nanomaterials. J. Clean. Prod. 328:129631. doi: 10.1016/j.jclepro.2021.129631
Tarasov, D., Leitch, M., and Fatehi, P. (2018). Lignin-carbohydrate complexes: properties, applications, analyses, and methods of extraction: a review. Biotechnol. Biofuels 11:269. doi: 10.1186/s13068-018-1262-1261
Thoppil, Y., and Zein, S. H. (2021). Techno-economic analysis and feasibility of industrial-scale biodiesel production from spent coffee grounds. J. Clean. Prod. 307:127113. doi: 10.1016/j.jclepro.2021.127113
Torr, K. M., Love, K. T., Simmons, B. A., and Hill, S. J. (2016). Structural features affecting the enzymatic digestibility of pine wood pretreated with ionic liquids. Biotechnol. Bioeng. 113, 540–549. doi: 10.1002/bit.25831
Travaini, R., Martín-Juárez, J., Lorenzo-Hernando, A., and Bolado-Rodríguez, S. (2016). Ozonolysis: an advantageous pretreatment for lignocellulosic biomass revisited. Bioresour. Technol. 199, 2–12. doi: 10.1016/j.biortech.2015.08.143
Ufodike, C. O., Eze, V. O., Ahmed, M. F., Oluwalowo, A., Park, J. G., Liang, Z., et al. (2020). Investigation of molecular and supramolecular assemblies of cellulose and lignin of lignocellulosic materials by spectroscopy and thermal analysis. Int. J. Biol. Macromol. 146, 916–921. doi: 10.1016/j.ijbiomac.2019.09.214
Usmani, Z., Sharma, M., Karpichev, Y., Pandey, A., Chandra Kuhad, R., Bhat, R., et al. (2020). Advancement in valorization technologies to improve utilization of bio-based waste in bioeconomy context. Renew. Sustain. Energy Rev. 131:109965. doi: 10.1016/j.rser.2020.109965
Va, A., Rv, B., Sj, C., Sc, D., Sd, E., Gkf, G., et al. (2021). Recent advances in lignocellulosic biomass for biofuels and value-added bioproducts - a critical review. Bioresource Technol. 344:126195.
Verardi, A., Blasi, A., Marino, T., Molino, A., and Calabrò, V. (2018). Effect of steam-pretreatment combined with hydrogen peroxide on lignocellulosic agricultural wastes for bioethanol production: analysis of derived sugars and other by-products. J. Energy Chem. 27, 535–543. doi: 10.1016/j.jechem.2017.11.007
Veza, I., Muhamad Said, M. F., and Latiff, Z. A. (2021). Recent advances in butanol production by acetone-butanol-ethanol (ABE) fermentation. Biomass Bioenerg. 144:105919. doi: 10.1016/j.biombioe.2020.105919
Vu, H. P., Nguyen, L. N., Vu, M. T., Johir, M. A. H., McLaughlan, R., and Nghiem, L. D. (2020). A comprehensive review on the framework to valorise lignocellulosic biomass as biorefinery feedstocks. Sci. Total Environ. 743:140630. doi: 10.1016/j.scitotenv.2020.140630
Wang, D., Xin, Y., Shi, H., Ai, P., Yu, L., Li, X., et al. (2019). Closing ammonia loop in efficient biogas production: recycling ammonia pretreatment of wheat straw. Biosys. Eng. 180, 182–190. doi: 10.1016/j.biosystemseng.2019.02.010
Wang, H.-M., Wang, B., Wen, J.-L., Wang, S.-F., Shi, Q., and Sun, R.-C. (2018). Green and efficient conversion strategy of Eucalyptus based on mechanochemical pretreatment. Energy Convers. Manage. 175, 112–120. doi: 10.1016/j.enconman.2018.09.002
Wang, Y., Ho, S.-H., Yen, H.-W., Nagarajan, D., Ren, N.-Q., Li, S., et al. (2017). Current advances on fermentative biobutanol production using third generation feedstock. Biotechnol. Adv. 35, 1049–1059. doi: 10.1016/j.biotechadv.2017.06.001
Wi, S. G., Cho, E. J., Lee, D.-S., Lee, S. J., Lee, Y. J., and Bae, H.-J. (2015). Lignocellulose conversion for biofuel: a new pretreatment greatly improves downstream biocatalytic hydrolysis of various lignocellulosic materials. Biotechnol. Biofuels 8, 1–11. doi: 10.1186/s13068-015-0419-414
Witaszek, K., Pilarski, K., Niedbała, G., Pilarska, A. A., and Herkowiak, M. (2020). Energy efficiency of comminution and extrusion of maize substrates subjected to methane fermentation. Energies 13:1887. doi: 10.3390/en13081887
Wu, X., Chen, L., He, W., Qi, H., Zhang, Y., Zhou, Y., et al. (2020). Characterize the physicochemical structure and enzymatic efficiency of agricultural residues exposed to γ-irradiation pretreatment. Ind. Crops Prod. 150:112228. doi: 10.1016/j.indcrop.2020.112228
Xu, C., Alam, M. A., Wang, Z., Peng, Y., Xie, C., Gong, W., et al. (2021). Co-fermentation of succinic acid and ethanol from sugarcane bagasse based on full hexose and pentose utilization and carbon dioxide reduction. Bioresour. Technol. 339:125578. doi: 10.1016/j.biortech.2021.125578
Xu, C., Paone, E., Rodríguez-Padrón, D., Luque, R., and Mauriello, F. (2020). Recent catalytic routes for the preparation and the upgrading of biomass derived furfural and 5-hydroxymethylfurfural. Chem. Soc. Rev. 49, 4273–4306. doi: 10.1039/D0CS00041H
Xu, H., Guo, M.-Y., Gao, Y.-H., Bai, X.-H., and Zhou, X.-W. (2017). Expression and characteristics of manganese peroxidase from Ganoderma lucidum in Pichia pastoris and its application in the degradation of four dyes and phenol. BMC Biotechnol. 17:19. doi: 10.1186/s12896-017-0338-335
Xu, J., Xiong, P., and He, B. (2016). Advances in improving the performance of cellulase in ionic liquids for lignocellulose biorefinery. Bioresour. Technol. 200, 961–970. doi: 10.1016/j.biortech.2015.10.031
Yamada, R., Nakashima, K., Asai-Nakashima, N., Tokuhara, W., Ishida, N., Katahira, S., et al. (2017). Direct ethanol production from ionic liquid-pretreated lignocellulosic biomass by cellulase-displaying yeasts. Appl. Biochem. Biotech. 182, 229–237. doi: 10.1007/s12010-016-2322-2322
Yan, X., Wang, Z., Zhang, K., Si, M., Liu, M., Chai, L., et al. (2017). Bacteria-enhanced dilute acid pretreatment of lignocellulosic biomass. Bioresour. Technol. 245, 419–425. doi: 10.1016/j.biortech.2017.08.037
Yang, H., Shi, Z., Xu, G., Qin, Y., Deng, J., and Yang, J. (2019). Bioethanol production from bamboo with alkali-catalyzed liquid hot water pretreatment. Bioresour. Technol. 274, 261–266. doi: 10.1016/j.biortech.2018.11.088
Yang, J., Xu, H., Jiang, J., Zhang, N., Xie, J., Zhao, J., et al. (2020). Itaconic acid production from undetoxified enzymatic hydrolysate of bamboo residues using Aspergillus terreus. Bioresour. Technol. 307:123208. doi: 10.1016/j.biortech.2020.123208
Yao, K., Wu, Q., An, R., Meng, W., Ding, M., Li, B., et al. (2018). Hydrothermal pretreatment for deconstruction of plant cell wall: Part II. Effect Cell. Struct. Bioconversion AICHE J. 64, 1954–1964. doi: 10.1002/aic.16106
Yi, W., Nadeem, F., Xu, G., Zhang, Q., Joshee, N., and Tahir, N. (2020). Modifying crystallinity, and thermo-optical characteristics of Paulownia biomass through ultrafine grinding and evaluation of biohydrogen production potential. J. Clean. Prod. 269:122386. doi: 10.1016/j.jclepro.2020.122386
Yoo, C. G., Pu, Y., and Ragauskas, A. J. (2017). Ionic liquids: promising green solvents for lignocellulosic biomass utilization. Curr. Opin. Green Sust. 5, 5–11. doi: 10.1016/j.cogsc.2017.03.003
Zahoor, Wang, W., Tan, X., Imtiaz, M., Wang, Q., Miao, C., et al. (2021). Rice straw pretreatment with KOH/urea for enhancing sugar yield and ethanol production at low temperature. Ind. Crops Prod. 170:113776. doi: 10.1016/j.indcrop.2021.113776
Zhang, H., Han, L., and Dong, H. (2021). An insight to pretreatment, enzyme adsorption and enzymatic hydrolysis of lignocellulosic biomass: experimental and modeling studies. Renew. Sustain. Energy Rev. 140:110758. doi: 10.1016/j.rser.2021.110758
Zhang, H., Zhang, J., and Bao, J. (2016). High titer gluconic acid fermentation by Aspergillus niger from dry dilute acid pretreated corn stover without detoxification. Bioresour. Technol. 203, 211–219. doi: 10.1016/j.biortech.2015.12.042
Zhang, J., Zong, W., Hong, W., Zhang, Z.-T., and Wang, Y. (2018). Exploiting endogenous CRISPR-Cas system for multiplex genome editing in Clostridium tyrobutyricum and engineer the strain for high-level butanol production. Metab. Eng. 47, 49–59. doi: 10.1016/j.ymben.2018.03.007
Zhang, K., Xu, R., Abomohra, A. E.-F., Xie, S., Yu, Z., Guo, Q., et al. (2019). A sustainable approach for efficient conversion of lignin into biodiesel accompanied by biological pretreatment of corn straw. Energy Convers. Manage. 199:111928. doi: 10.1016/j.enconman.2019.111928
Zhao, C., Shao, Q., and Chundawat, S. P. S. (2020). Recent advances on ammonia-based pretreatments of lignocellulosic biomass. Bioresour. Technol. 298:122446. doi: 10.1016/j.biortech.2019.122446
Zhao, P., Zhou, C., Li, J., Xu, S., and Hu, C. (2019). Synergistic effect of different species in stannic chloride solution on the production of levulinic acid from biomass. ACS Sustain. Chem. Eng. 7, 5176–5183. doi: 10.1021/acssuschemeng.8b06062
Zhao, X., Li, S., Wu, R., and Liu, D. (2017). Organosolv fractionating pre-treatment of lignocellulosic biomass for efficient enzymatic saccharification: chemistry, kinetics, and substrate structures. Biofuel. Bioprod. Bior. 11, 567–590. doi: 10.1002/bbb.1768
Zhou, P., Yao, R., Zhang, H., and Bao, J. (2019). Unique glucose oxidation catalysis of Gluconobacter oxydans constitutes an efficient cellulosic gluconic acid fermentation free of inhibitory compounds disturbance. Biotechnol. Bioeng. 116, 2191–2199. doi: 10.1002/bit.27020
Zhuang, X., Wang, W., Yu, Q., Qi, W., Wang, Q., Tan, X., et al. (2016). Liquid hot water pretreatment of lignocellulosic biomass for bioethanol production accompanying with high valuable products. Bioresour. Technol. 199, 68–75. doi: 10.1016/j.biortech.2015.08.051
Ziaei-Rad, Z., Fooladi, J., Pazouki, M., and Gummadi, S. N. (2021). Lignocellulosic biomass pre-treatment using low-cost ionic liquid for bioethanol production: an economically viable method for wheat straw fractionation. Biomass Bioenerg. 151:106140. doi: 10.1016/j.biombioe.2021.106140
Zoghlami, A., and Paës, G. (2019). Lignocellulosic biomass: understanding recalcitrance and predicting hydrolysis. Front. Chem. 7:874. doi: 10.3389/fchem.2019.00874
Zou, L., Ouyang, S., Hu, Y., Zheng, Z., and Ouyang, J. (2021). Efficient lactic acid production from dilute acid-pretreated lignocellulosic biomass by a synthetic consortium of engineered Pseudomonas putida and Bacillus coagulans. Biotechnol. Biofuels 14:227. doi: 10.1186/s13068-021-02078-2077
Keywords: lignocellulosic biomass, pretreatment, bioenergy, biorefinery, biofuels
Citation: Zheng B, Yu S, Chen Z and Huo Y-X (2022) A consolidated review of commercial-scale high-value products from lignocellulosic biomass. Front. Microbiol. 13:933882. doi: 10.3389/fmicb.2022.933882
Received: 01 May 2022; Accepted: 27 July 2022;
Published: 23 August 2022.
Edited by:
Jun Feng, University of Wisconsin-Madison, United StatesReviewed by:
Nadeem Tahir, Henan Agricultural University, ChinaMadan L. Verma, Indian Institute of Information Technology, India
Nitin Verma, Meerut Institute of Engineering and Technology, India
Copyright © 2022 Zheng, Yu, Chen and Huo. This is an open-access article distributed under the terms of the Creative Commons Attribution License (CC BY). The use, distribution or reproduction in other forums is permitted, provided the original author(s) and the copyright owner(s) are credited and that the original publication in this journal is cited, in accordance with accepted academic practice. No use, distribution or reproduction is permitted which does not comply with these terms.
*Correspondence: Zhenya Chen, Y2hlbnpoZW55YUBiaXQuZWR1LmNu; Yi-Xin Huo, aHVveWl4aW5AYml0LmVkdS5jbg==
†These authors have contributed equally to this work