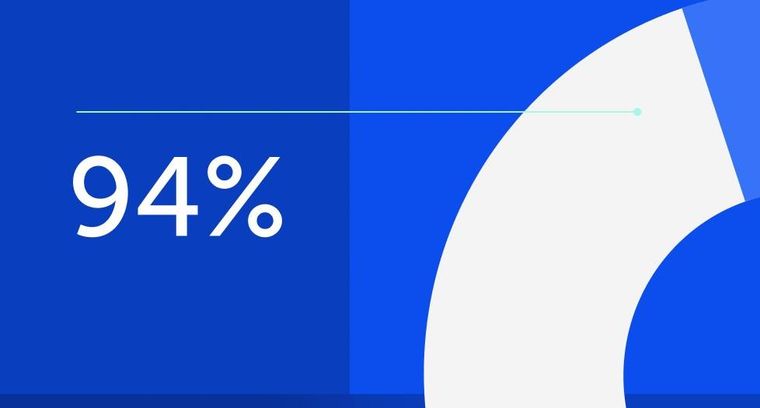
94% of researchers rate our articles as excellent or good
Learn more about the work of our research integrity team to safeguard the quality of each article we publish.
Find out more
ORIGINAL RESEARCH article
Front. Microbiol., 30 March 2022
Sec. Microbiotechnology
Volume 13 - 2022 | https://doi.org/10.3389/fmicb.2022.861918
This article is part of the Research TopicAdvanced Microbial Biotechnologies For Sustainable Agriculture, Volume IIView all 18 articles
Corn fiber, a by-product from the corn-processing industry, is an attractive feedstock for cellulosic ethanol because of its rich carbohydrate content (mainly residual starch, cellulose, and hemicellulose), abundant reserves, easy collection, and almost no transportation cost. However, the complex structure and components of corn fiber, especially hemicellulose, make it difficult to be effectively hydrolyzed into fermentable sugars through enzymatic hydrolysis. This study developed a simple and easy industrialized process without detoxification treatment for high-yield ethanol produced from corn fiber. Corn fiber was pretreated by dilute acid under the conditions optimized by Box-Behnken design (0.5% H2SO4 at 105°C for 43 min), and 81.8% of total sugars, including glucose, xylose, and arabinose, could be recovered, then the mixture (solid and hydrolysates) was directly used for semi-simultaneous saccharification and fermentation without detoxification, and ethanol yield reached about 81% of the theoretical yield.
Bioethanol, being a kind of fuel made from organic matter resulting from agriculture or forestry, is a sustainable resource with the advantages, such as cleanliness, renewable, and reduced dependence on petroleum imports (Lovett et al., 2011; Toor et al., 2020). In addition, as a fuel octane enhancing additive, bioethanol can diversify energy supplies while contributing significantly to reducing carbon and particle emissions (Moore et al., 2017). Currently, commercial bioethanol is mainly first-generation ethanol produced from starch- or sugar-containing feedstocks, such as corn, other grains, and sugar cane, which require huge cultivatable land while directly competing with the food supply (Nigam and Singh, 2011; Searchinger et al., 2018). The second-generation fuel ethanol uses renewable lignocellulose as raw materials, such as corn stover and other agricultural and forestry residues, but its commercial production has been limited by high production costs, including raw material costs, pretreatment costs, enzyme costs, and investment costs. The cost of raw materials is one of the most important factors affecting the commercial production of second-generation ethanol. Corn fiber is mainly composed of residual starch, cellulose, and hemicellulose. As a residue of the corn processing industry, it is estimated that the annual output of corn fiber reached 10.9 million tons in China (Jiang et al., 2018). In traditional corn ethanol facilities, corn fiber commonly passes through the fermentation and distillation stages and ends up in the distiller’s dried grains with solubles (DDGS) rather than being converted to ethanol, which reduces the total output of corn ethanol (Kurambhatti et al., 2018). Corn fiber is expected to become an attractive feedstock for cellulosic ethanol because of rich carbohydrates, abundant reserves, easy collection, and almost no transportation cost. According to reports, if corn fiber can be economically converted into ethanol, it will increase the total corn ethanol production by up to 13% on the existing basis while improving the protein content of DDGS (Bothast and Schlicher, 2005).
Unlike other lignocellulose, such as corn stover, hemicellulose is the most abundant component of corn fiber (about 40% of dry corn fiber weight), mainly composed of glucuronoarabinoxylan substituted by various side chains (Saha, 2003; Beri et al., 2020). It covers the surface of cellulose, thus affecting the accessibility of cellulase to cellulose. In contrast, because of the complex sugar compositions and structure of hemicellulose in corn fiber and the interaction between different components, it requires a complex hemicellulase system for completing the thorough degradation of hemicellulose (Agger et al., 2010). All the factors make corn fiber difficult to be effectively hydrolyzed into fermentable sugars by direct enzymatic hydrolysis. Therefore, pretreatment before enzymatic hydrolysis has been proposed to improve the enzymatic digestibility of corn fiber for obtaining high fermentable sugar yield (Kumar et al., 2009; Brodeur et al., 2011; Zhang et al., 2021). Till now, some methods used for pretreating corn fiber have been reported. For example, Bura et al. (2002) treated corn fiber by the steam explosion in a batch reactor at various degrees of severity and found that maximum total sugar yields of 81% could be obtained when corn fiber was pretreated at 190°C for 5 min with addition of 6% SO2, and using the pretreated corn fiber as substrate, the ethanol concentration reached 6.9 g/L by enzymatic hydrolysis and fermentation at 2% solid content, but the conversion of hemicellulose sugar is lower than 60%. Juneja et al. (2021) performed a two-step pretreatment of corn fiber separated from whole stillage, including liquid hot water pretreatment (LHW) and disk milling. It was shown that, under optimal conditions, the yields of glucose, xylose, and arabinose after enzymatic hydrolysis were 96.18, 72.39, and 66.33%, respectively, but only 21.54 g/L of ethanol concentration was reached after fermentation at 20% solid content. Both steam explosion and LHW require high temperature and pressure, as well as pressure equipment, but the conversion of hemicellulose in pretreated corn fiber was still low. In contrast, the pretreatment conditions of high temperature and high pressure also led to the formation of fermentation inhibitors through further degradation of sugar products.
Many literature showed that dilute acid pretreatment could effectively degrade hemicellulose of lignocellulose materials (Noureddini and Byun, 2010; Jiang et al., 2015; Mikulski and Kłosowski, 2018; Santos et al., 2018), thus the method has been used for pretreating corn fiber to obtain the high conversion of cellulose and hemicellulose, but the monosaccharides would be further degraded during the pretreatment to form inhibitors, such as furfural and 5-hydroxymethylfurfural (HMF). For example, Iram et al. (2019) pretreated DDGS with dilute acid, and the yield of total reducing sugar (TRS) reached 0.382 g/g DDGS; besides TRS, furfural and HMF were also produced during the acid pretreatment. Li et al. (2019) used the combination of acid pretreatment with distillation to in situ pretreat whole stillage containing corn fiber and recycled it to the liquefaction step, which improved the ethanol yield by 6.3% compared to the traditional process, and the cellulose conversion was 77.5%, but similarly, many inhibitors were also produced, which led to incomplete fermentation. Noureddini and Byun (2010) used dilute sulfuric acid to treat corn fiber and found that the highest yield of monosaccharides (63.1 g sugar/100 g corn fiber) was obtained when the pretreatment was conducted at 5% of biomass loading (w/w), 1.5% of sulfuric acid concentration (v/v), and 140°C, but the concentration of furfural in pretreatment liquor was also high (3.8 mg/ml) after pretreatment under the conditions. Besides, their results also showed that the formation of furfural could be significantly decreased when pretreatment temperature dropped from 140 to 120°C during the dilute sulfuric acid pretreatment of corn fiber.
Although the inhibitors produced by the dilute acid pretreatment, for example, acetic acid, formic acid, furfural, HMF, and phenolic compounds, limit the applicability of the hydrolysate for subsequent biotransformation (Hendriks and Zeeman, 2009; Yemiş and Mazza, 2011; Lee et al., 2017), and detoxification treatment must be conducted before fermentation to decrease their adverse effects on subsequent saccharification and fermentation, the dilute acid pretreatment is still an attractive approach for improving enzymatic digestibility of corn fiber because of high content and complex structure of hemicellulose in corn fiber. However, the pretreatment process still needs to be further improved to more effectively improve the enzymatic digestibility of corn fiber while minimizing sugar loss and inhibitors formation. To achieve this goal, in this study, we optimized dilute sulfuric acid pretreatment conditions, including temperature, acid concentration, and reaction time, by using the response surface method (RSM), then, the pretreated corn fiber with hydrolysates was directly used for the production of ethanol without detoxification by semi-simultaneous saccharification and fermentation (semi-SSF) process to assess the feasibility of the integrated process for ethanol production using corn fiber as feedstock. In the semi-SSF process, the cellulase from Penicillium oxalicum, which has more abundant hemicellulase activities than the cellulase from Trichoderma reesei (Gao et al., 2021), was used in the pre-hydrolysis of corn fiber-rich in hemicellulose components and subsequent SSF process, and Saccharomyces cerevisiae LF2, an engineered strain with glucose and xylose metabolism, was used in the fermentation of hydrolysates for obtaining high ethanol yield by simultaneous conversion of glucose and xylose to ethanol.
Corn fiber was obtained from Juneng Golden Corn Co. Ltd., (Shouguang, China). It was ground using an MF 10 basic Microfine grinder (IKA, Germany) with a 2.0-mm-hole diameter sieve, then stored in a sealed polyethylene bag at −20°C before use.
The liquid chromatography standards, including glucose, galactose, arabinose, xylose, mannose, galacturonic acid, glucuronic acid, furfural, HMF, and acetic acid, were purchased from Sigma-Aldrich Co. LLC (St. Louis, MO, United States). Reagent grade sulfuric acid (98%), anhydrous sodium acetate, sodium hydroxide, and ethanol were obtained from Sinopharm Chemical Reagent Co. Ltd. (Shanghai, China).
Penicillium oxalicum MCAX, an engineered strain in our laboratory (Gao et al., 2021), was used to produce cellulases.
Saccharomyces cerevisiae LF2 is capable of metabolizing xylose and glucose was maintained in our group. It was provided by Professor Xiaoming Bao from Qilu University of Technology, Shandong.
The chemical compositions of corn fiber were determined according to the National Renewable Energy Laboratory (NREL) protocols. The extractives were quantified according to the analytical method NREL/TP-510-42619 (Sluiter et al., 2005a), and the ash was determined by the incineration method described by Sluiter et al. (2005b). The contents of cellulose, hemicellulose (xylose, arabinose, and galactose), lignin, and acetyl group were determined by two-step hydrolyzing corn fiber with H2SO4 of 72% (w/w) and 4% (w/w), respectively, according to the analytical method NREL/TP-510-42618 (Sluiter et al., 2008a). The starch was quantified according to the analytical method NREL/TP-510-42619 (Sluiter and Sluiter, 2005). The protein was quantified according to the analytical method NREL/TP-510-42625 (Hames et al., 2008). The sample collected during the determination of acetyl group content was filtered by 0.22 μm Millipore Syringe Filters (Jinteng, China), and the filtrate was used to analyze glucuronic acid by high-performance liquid chromatography (HPLC) (Shimadzu, Japan), which was equipped with Shimadzu’s 20A refractive index detector. An Aminex HPX-87H column (300 × 7.8 mm) (Bio-Rad, Richmond, CA, United States) was used to separate the compounds at 60°C. The mobile phase was 0.005 M H2SO4 with a 0.5 ml/min flow rate.
The cellulase used in this study was produced by P. oxalicum MCAX according to the method suggested by Gao et al. (2021). The strain MCAX was cultivated in 50 ml of seed medium [g/L, wheat bran: 20, peptone: 10, glucose: 10, (NH4)2SO4: 2, KH2PO4: 3, and MgSO4: 0.5] in 300 ml Erlenmeyer flasks for 24 h at 30°C and 200 rpm on a rotary shaker. Then, the culture was inoculated into a fermentation medium [g/L, wheat bran: 30, bean cake powder: 15, microcrystalline cellulose: 30, (NH4)2SO4: 2, KH2PO4: 5, and MgSO4: 0.5] with an inoculation ratio of 10% (v/v) and incubated at 30°C and 200 rpm for 6 days. After fermentation, the supernatant was obtained by centrifugation at 10,000 rpm for 10 min and used as crude cellulase. The hydrolytic activities of the crude cellulase were as follows: filter paper activity (FPA) 6 stocktickerFPU/ml, xylanase 783 IU/ml, arabinofuranosidase 5 IU/ml, and β-xylosidase 1 IU/ml.
Pretreatment of corn fiber with dilute sulfuric acid was performed in a laboratory-scale vertical pressure steam sterilizer (Deqiang, China). A total of 4 g of corn fiber and dilute acid solution was thoroughly mixed in 50 ml flasks with 12 ml of reaction volume. Based on preliminary experiments, the following experimental conditions were tested: temperature of 105–125°C, H2SO4 concentration of 0.2–0.5% (w/v), and time of 10–60 min. The experiments were designed by a Box-Behnken RSM using Design-Expert version 8.0.6.1 software and are shown in Table 2.
For the significance analysis of different factors in the pretreatment, p-value was obtained by ANOVA and used for determining statistically significant. p > 0.05 indicates that the factor is not significant; p ≤ 0.05 indicates that it is significant; and p ≤ 0.01 indicates that it is very significant.
After pretreatment, the flasks were cooled down to room temperature. A part of the pretreated corn fiber slurries was collected to analyze the contents of furfural, HMF, formic acid, and acetic acid.
The saccharification was performed at 5% (w/v) substrate concentration in 50 ml flasks with a reaction volume of 20 ml. The pretreated corn fiber slurries were first adjusted to pH 5.0 with 10 M NaOH solution, mixed well with crude cellulase solution and acetate buffer of pH 4.8 in flasks, and incubated at 48°C in a thermostat air bath shaker set at 150 rpm. The samples were taken at reaction times of 0, 12, 24, and 48 h, respectively, and 72 h to analyze the concentrations of monomeric sugars in the enzymatic hydrolysates.
All experiments were performed in triplicate, and the average values are given in this study.
The hydrolysate of corn fiber was treated with dilute acid under the optimum pretreatment conditions, which contains 4.60 g/L glucose, 3.92 g/L xylose, 0.44 g/L furfural, 1.04 g/L formic acid, and 1.62 g/L acetic acid. For acclimation of the yeast, four different acclimation media were used. One of the media consisted of hydrolysate that was not diluted. The three other media were prepared by diluting hydrolysate to a concentration of 25, 50, and 75% (v/v), respectively. In each acclimation medium, 15.0 g/L glucose, 0.40 g/L (NH4)2SO4, and 1.00 g/L yeast extract were added. S. cerevisiae LF2 was first inoculated into YPD medium for activation of 24 h at 30°C, then take 2 ml of inoculum, centrifuge, and transfer the yeast cells to a 50 ml Erlenmeyer flask containing 20 ml of the acclimation medium with the lowest inhibitors concentration and incubated at 30°C to the glucose content in the medium less than 90% of the initial glucose content. After that, the strain was further transferred to the next acclimation medium with a higher inhibitors’ concentration and cultured according to the procedure above until the highest inhibitors concentration. To make the yeast better adapt to the change of inhibitor concentration, the acclimation of yeast in each inhibitor concentration was repeated more than four times.
The inoculum was prepared by growing S. cerevisiae LF2 in a YPD medium containing 20 g/L glucose, 20 g/L peptone, and 10 g/L yeast extract at 30°C, 200 rpm for 24 h in a thermostat air bath shaker. The inoculum with an OD of 2.0 at 600 nm was used as seed culture, and the inoculation volume was 5% (v/v).
The semi-SSF experiment was performed in a 50 ml sealed Erlenmeyer flask by a rubber plug with a needle. First, the pretreated corn fiber slurries were adjusted to pH 5.0 with 10 M NaOH, and the pre-hydrolysis was conducted at 20% (w/v) solid consistency, 48°C, pH 5.0 for 12 h using cellulase of 10 FPU/g (DM). After pre-hydrolysis, the reaction system temperature was adjusted to 30°C, and 5% (v/v) of seed was inoculated to the reaction system. Fermentation was carried out in a thermostat air bath shaker with a rotation rate of 200 rpm. The samples were taken periodically to determine the concentrations of glucose, xylose, and ethanol.
The FPA and the activities of xylanase, β-xylosidase (pNPXase), and α-arabinofuranosidase (pNPAase) of culture supernatants were measured using a Whatman No.1 filter paper, insoluble xylan (beech), p-nitrophenyl-β-D-xylopyranoside, and p-nitrophenyl-α-L-arabinofuranoside as the substrates, respectively, according to the methods presented by Gao et al. (2021). One unit (U) of enzyme activity was defined as the amount of enzyme that liberates 1 μmol of reducing sugars (for FPA and xylanase) equivalent or p-nitrophenol (for pNPAase and pNPXase) per minute under the assay conditions.
The samples collected in the pretreatment, enzymatic hydrolysis, and fermentation stages, respectively, were centrifuged at 10,000 rpm for 10 min. The supernatants were used for analyzing the contents of glucose, xylose, formic Acid, acetic acid, furfural, HMF, and ethanol using HPLC (LC-20AT, refractive index detector RID-20A, Shimadzu, Kyoto, Japan) With an Aminex HPX-87H column (Bio-Rad, Hercules, CA, United States) at 60°C using a mobile phase of 5 mM H2SO4 at a rate of 0.5 ml/min (Sluiter et al., 2008b). For the samples from the enzymatic hydrolysis and fermentation stage, the supernatants were first boiled for 10 min for inactivating enzyme. The sugar yields (%) were calculated according to the following formula:
where CHPLC is the concentration of sugar as determined by HPLC, mg/ml; V is the volume of the reaction system, ml; CF (conversion factor) is 0.9 for C-6 sugars and 0.88 for C-5 sugars; W is the weight of the substrate in the reaction system, g; and ContentSugar is the percentage of the polymeric sugar in corn fiber.
Table 1 provides the chemical compositions of corn fiber. The corn fiber contains starch, cellulose, and hemicellulose with a total carbohydrate content of 71.22 ± 1.27%. The major components were hemicellulosic sugars (xylose, arabinose, and galactose), and their total contents reached about 40%. These data were consistent with the previously reported results (Kim et al., 2008; Eylen et al., 2011). Compared with the chemical components of corn stover and corn cob (Eylen et al., 2011), the corn fiber had similar total glucan content to corn stover (30.6%) and corn cob (34.8%) and similar xylan content to corn stover (19%). But unlike corn cob and corn stover, a considerable part of the glucose in corn fiber was derived from starch, not just cellulose. In contrast, the contents of other hemicellulose sugars in corn fiber were significantly higher than that in corn stover and corn cob, which means that the degradation of corn fiber may require a more complex enzyme system with more abundant hemicellulase components.
Table 2. Pretreatment factors and experiment results in the experiments designed by the central composite design from response surface methodology.
From batch kinetics studies, it was found that the factors affecting acid pretreatment included the type of biomass, the type of acid, acid concentration, reaction time, and reaction temperature (Rahman et al., 2006). Among them, the operating conditions, including reaction time, temperature, and acid concentration, would significantly affect the efficiency of dilute acid pretreatment (López-Arenas et al., 2010). In this study, RSM incorporating variables of temperature, time, and acid concentration was used to optimize the pretreatment process parameters for maximizing the enzymatic conversion of carbohydrate in corn fiber to monosaccharides and minimizing the formation of inhibitors. The complete list of runs and responses is provided in Table 2. Five experimental runs were replicated at the center point of the design to confirm any differences in the estimation procedure as a measure of precision. Table 2 shows the yields of formic acid, acetic acid, and furfural after pretreatment and the yields of glucose, xylose, and arabinose after pretreatment and following enzymatic hydrolysis. Figure 1 shows the response surface plots of glucose, xylose, and arabinose yields under different pretreatment conditions. ANOVA of the models for glucose, xylose, arabinose, furfural, formic acid, and acetic acid is given in Table 3. The regression equations of different products were as follows, respectively.
Figure 1. Response surface plots of yields of glucose (A–C), xylose (D–F), and arabinose (G–I) (mg/g corn fiber) obtained from the Box-Behnken design of RSM.
Table 3. ANOVA Table of the adjusted models from dilute sulfuric acid pretreated and enzyme hydrolyzed corn fiber.
Glucose = + 334.95 – 0.49 × Temp. + 4.69 × Time + 8.45 × Acid conc. – 9.53 × Temp. × Time – 6.38 × Temp. × Acid conc. – 2.60 × Time × Acid conc.
Xylose = + 132.21 + 19.61 × Temp. + 14.86 × Time + 19.06 × Acid conc. – 0.64 × Temp. × Time + 1.19 × Temp. × Acid conc. – 0.66 × Time × Acid conc. + 1.56 × Temp.2 – 7.19 × Time 2 – 3.91 × Acid conc.2
Arabinose = + 110.82 + 5.20 × Temp. + 4.97 × Time + 6.71 × Acid conc. – 4.23 × Temp. × Time −3.00 × Temp. × Acid conc. – 2.97 × Time × Acid conc. – 0.62 × Temp.2 – 4.26 × Time 2 – 2.29 × Acid conc.2
Furfural = + 3.07 + 0.57 × Temp. + 0.19 × Time – 0.14 × Acid conc. – 0.24 × Temp. × Time – 7.500E-003 × Temp. × Acid conc. + 0.018 × Time × Acid conc. + 0.061 × Temp.2 – 0.014 × Time 2 – 0.39 × Acid conc.2
Formic acid = + 5.30 + 0.33 × Temp. + 0.14 × Time + 0.23 × Acid conc. + 0.16 × Temp. × Time + 0.17 × Temp. × Acid conc. + 0.047 × Time × Acid conc.
Acetic acid = + 8.25 + 2.90 × Temp. + 1.69 × Time + 2.65 × Acid conc. + 0.73 × Temp. × Time + 0.93 × Temp. × Acid conc. + 1.10 × Time × Acid conc.
where sugars and inhibitors appear as yield (mg/g) and the variables are Temp. (temperature, °C), Time (in min), and Acid conc. (acid concentration, %, w/v).
It is shown in Figure 1 and p-values in ANOVA that the yield of glucose obtained from the enzymatic hydrolysis of pretreated corn fiber was sensitive to acid concentration (p = 0.0372 ≤ 0.05) but not to pretreatment time (p = 0.2119 > 0.05) and temperature (p = 0.8922 > 0.05), but the yield of xylose was significantly very sensitive to reaction time (p < 0.0001), temperature (p < 0.0001), and acid concentration (p < 0.0001). Initially, the increase in pretreatment temperature is in favor of the conversion of xylan to xylose in subsequent enzymatic hydrolysis, but a high pretreatment temperature led to the dehydration reaction of xylose accelerated, thus decreased xylose production but increased furfural content (Table 2), which is similar to the results reported in some literature (Kabel et al., 2007; Noureddini and Byun, 2010).
In contrast, it was found that the yields of glucose and xylose (based on the original content in corn fiber) were 10.5 and 38.3%, respectively, in the pretreatment stage, and the yields of glucose and xylose were 95.5 and 72.4% after enzymatic hydrolysis, indicating that xylan was more dissolved out in the pretreatment stage. Avci et al. (2013) also reported the difference in production behavior between glucose and xylose. They found that after being treated with dilute sulfuric acid a considerable part of xylan was directly hydrolyzed into xylose, while glucose was mostly produced by enzymatic hydrolysis. This is similar to our results. In the study, maximum xylose of 171 mg/g corn fiber was obtained by pretreatment at 125°C for 35 min using 0.5% (m/v) H2SO4. Similar to xylose, as shown in Figure 1I, the yield of arabinose was also sensitive to pretreatment temperature (p = 0.0011 ≤ 0.01), time (p = 0.0014), and acid concentration (p = 0.0002).
Overall, for three main sugars in corn fiber (glucose, xylose, and arabinose), the highest yield of total sugars was produced by pretreatment at 125°C for 35 min using 0.5% (w/v) H2SO4 and enzyme hydrolysis, including glucose of 340 mg, xylose of 171 mg, and arabinose of 117 mg, respectively, on the basis of per gram corn fiber. This amount was approximately 85.4% of the three sugars present in the corn fiber.
Furfural and HMF were generated from xylose and glucose in the pretreatment process through a further dehydration reaction, respectively (Jönsson and Martín, 2016). It was found that furfural formation was also most sensitive to pretreatment temperature (p < 0.0001), but not to acid concentration (p = 0.949 > 0.05), maybe because sulfuric acid only acts as a catalyst to provide an acidic environment. The highest furfural content of 3.93 mg/g corn fiber was found after pretreatment at 125°C for 10 min with 0.35% sulfuric acid (Table 2). Extending pretreatment time from 10 min to 60 min under conditions of 0.35% sulfuric acid and 125°C, furfural content in pretreatment liquid decreased, maybe due to further decomposition of furfural. It was also found that the yield of formic acid, a degradation product of furfural (Yang et al., 2012), increased (Table 2). In addition, Yemiş and Mazza (2011) also reported that the too-long reaction time could cause the condensation reaction of furfural to form other products. However, no HMF was detected in any hydrolysate from the acid pretreatment process, possibly because little glucose was degraded during the acid pretreatment under pretreatment conditions used in the paper. Acetic acid was also detected in hydrolysates after the acidic pretreatment (Table 2), which comes from the shedding of acetyl groups in hemicellulose (Ibbett et al., 2011), and its content was also sensitive to reaction time (p < 0.0001), temperature (p < 0.0001), and acid concentration (p < 0.0001). Longer reaction time, higher reaction temperature, and acid concentration can promote acetic acid formation.
It was found that, although the pretreatment can obtain the highest amounts of sugars at 125°C for 35 min using 0.5% H2SO4, there was also the higher production of formic acid (5.97 mg/g corn fiber), acetic acid (14.5 mg/g corn fiber), and furfural (3.11 mg/g corn fiber), which may result in the inhibitory effect on microbial growth in subsequent ethanol fermentation. To obtain the maximum sugars while minimizing the formation of inhibitory compounds as much as possible, based on the RSM analysis (Figure 1 and Tables 2, 3), it was determined that the suitable pretreatment conditions for the corn fiber were the acid concentration of 0.5%, reaction temperature of 105°C, and reaction time of 43 min. Under this condition, the yield of glucose, xylose, and arabinose reached 354 mg/g corn fiber, 133 mg/g corn fiber, and 114 mg/g corn fiber, respectively, which is equivalent to 81.8% of the total amount of the three sugars present in the corn fiber. Although the yield (81.8%) was slightly lower than the highest sugar yield (85.4%) obtained at 125°C for 35 min using 0.5% H2SO4, the amounts of inhibitors produced in the mild pretreatment significantly decreased, for example, decreased by 25.7% for furfural, 45.6% for acetic acid, and 14.2% for formic acid, respectively.
According to the reports from the literature, furfural concentration greater than 0.2 mg/ml or acetic acid concentration greater than 5 mg/ml could be severely toxic to the growth of S. cerevisiae (Sanchez and Bautista, 1988; Larsson et al., 1999; Kim et al., 2013). In the system of multiple inhibitors coexisting, the interaction of these inhibitors could enhance the toxicity, leading to the greater inhibition of microbial growth and fermentation than any single inhibitor (Palmqvist and Hahn-Hägerdal, 2000; Hou et al., 2018). To high efficiently produce ethanol using the pretreated corn fiber as substrate, in this study, using two hydrolysates from corn fiber pretreated by dilute acid under optimum conditions (0.5% H2SO4, 105°C for 43 min) and the conditions for obtaining the highest total sugars yields (0.5% H2SO4, 125°C for 35 min), respectively, we first assessed the inhibition effect of hydrolysates on the growth of S. cerevisiae LF2 by investigating the effect on ethanol fermentation. The hydrolysates were preadjusted to pH 5.0 with 10 M NaOH solution, and S. cerevisiae LF2 was inoculated into the hydrolysates. It was shown in Figure 2 that the growth of S. cerevisiae LF2 was obviously inhibited in the hydrolysates, in which the growth of S. cerevisiae LF2 was strongly inhibited in the hydrolysate from pretreated corn fiber at 125°C using 0.5% (w/v) H2SO4 for 35 min, and almost no ethanol was produced in the whole fermentation period. For the hydrolysate from corn fiber pretreated in optimum conditions, ethanol was just produced after about 60 h of fermentation.
Figure 2. Changes in concentrations of ethanol, glucose, and xylose during fermentation of pretreated corn fiber by dilute acid under different pretreatment conditions for assessing inhibitors’ effect on fermentation. Ethanol, square; glucose, circle; xylose, triangle; pretreatment with 0.5% H2SO4 at 105°C for 43 min, solid; and pretreatment with 0.5% H2SO4 at 125°C for 35 min, hollow.
To shorten the lag growth period of S. cerevisiae LF2 during semi-SSF of hydrolysate, strain domestication was conducted by continuously and gradually increasing hydrolysate concentration in acclimation medium for making the S. cerevisiae LF2 adapt to this environment with inhibitors. After multiple habituated cultures, the tolerance of S. cerevisiae LF2 to inhibitors was greatly improved. The performances of the domesticated strain and parent strain were compared by cultivation in the acclimation media with the highest concentration of inhibitors, in which glucose was supplemented to 50.0 g/L in the media. As shown in Figure 3, using the domesticated strain, the ethanol concentration in fermentation liquid was significantly increased compared to the parent strain (23.5 g/L vs. 18.8 g/L), and the lag period decreased from 60 to 12 h, which could meet the requirements of semi-SSF, thus, in the following experiments, the domesticated strain was directly applied to ethanol fermentation of pretreated corn fiber without pre-detoxification treatment.
Figure 3. Changes in concentrations of ethanol, glucose, and xylose of parent strain (solid) and domesticated yeast (hollow) in acclimation medium with the highest inhibitors concentration supplemented with glucose. Ethanol, square; glucose, circle; xylose, triangle.
Semi-simultaneous saccharification and fermentation was used to evaluate ethanol production potential using corn fiber as substrate under the best pretreatment conditions. Compared to the SSF process, a pre-hydrolysis step was first carried out prior to SSF under the optimal conditions of enzymatic hydrolysis, which help to promote enzymatic hydrolysis and liquefaction of cellulosic substrate. The pretreated corn fiber was pre-hydrolyzed with the cellulase preparation for 12 h at 48°C and pH 5.0 before yeast was inoculated. Figure 4 shows the changes in glucose, xylose, and ethanol concentrations concerning time during the semi-SSF. It was shown that traces of ethanol in fermentation liquid (0.20 g/L) began to be detected at 24th hour, and after that, glucose was continuously consumed up to the concentration of 0 at 96th hour. Xylose concentration started decreasing when its concentration was close to that of glucose, and it was consumed completely at the end of fermentation. Finally, the ethanol concentration of 40.14 g/L was obtained, and ethanol yield was approximately 81% of the theoretical yield. However, in this study, the total fermentation time was long (about 144 h), and the rate of xylose conversion was still low. Thus, in further work, the S. cerevisiae LF2 will be further improved to decrease the lag period of strain, and the enzyme system will be modified to improve the rate of xylose conversion.
Figure 4. Time courses of sugar utilization and ethanol production during semi-SSF with S. cerevisiae LF2 and corn fiber pretreated at 105°C; 0.5% H2SO4 for 43 min; fermentation conditions: 20% (w/v) of solid content, 30°C and pH 5.0.
Some results from literature about cellulosic ethanol production using corn fiber as feedstock through different pretreatment and saccharification-fermentation process are summarized in Table 4. It was shown that, in the existing research, detoxification treatments, such as water washing, biodetoxification, and overliming, were usually used after acidic and alkaline pretreatment. For example, Shrestha et al. (2010) used water washing to detoxify the mild NaOH or steam pretreated corn fiber, and the ethanol concentration of 3.30 and 2.66 g/L, respectively, was obtained after fermentation under the condition of 4.3% solid content. However, its solid content and final ethanol concentration were too low for practical application. Gáspár et al. (2007) also used water washing for detoxification of corn fiber pretreated by KOH. The ethanol concentration reached 12.50 g/L after fermentation at 5% solid content by semi-SSF process. However, because most of the hemicellulose was dissolved in the alkali pretreatment process and wasted after water washing, the ethanol yield was very low, only 0.062 g/g initial corn fiber. Bura et al. (2002) reported that the inhibitors in the hydrolysate could be completed removed by detoxifying steam explosion-pretreated corn fiber with overliming treatment, but fermentation was conducted at only 2% of solid content, which was too low to be suitable for practical application. Although water washing and overliming can remove inhibitors, they also increase process steps and costs while generating problems, such as wastewater and the loss of sugars. Different from this, Zhang et al. (2021) adopted biodetoxification by inoculating Paecilomyces variotii to remove inhibitors produced by citric acid pretreatment, and the ethanol concentration reached 70.2 g/L using semi-SSF at 25% of solid content, and ethanol production reached 0.280 g/g initial corn fiber. Although less wastewater is produced due to biological detoxification rather than water washing and overliming, high citric acid dosage (4%) and reaction temperature (165°C) during pretreatment and too-long biodetoxification as strain growth and inactivation after detoxification influenced the economy of the process. Li et al. (2019) used the combination of acid pretreatment with distillation to in situ pretreat whole stillage containing corn fiber. The pretreated stillage was recycled to the liquefaction step with the addition of cellulase, or hydrolyzed using cellulase and then recycled to the liquefaction step, or hydrolyzed using cellulase followed by C6/C5 sugar co-fermentation. Compared with the traditional dry milling process, the highest ethanol yield increased by 6.3%, and the conversion of cellulose reached 77.5%. However, a large number of inhibitors in the pretreatment liquid resulted in incomplete fermentation. Myat and Ryu (2014) used thermal-mechanical extrusion to pretreat corn fiber, which reduced the crystallinity and polymerization degree of cellulose in corn fiber, and the final ethanol concentration reached 29.08 g/L. Juneja et al. (2021) used the combination of liquid hot water pretreatment with wet disk milling to pretreat corn fiber, resulting in a final ethanol concentration of 21.54 g/L at 20% of solid content. Due to the lack of chemical pretreatment, there were fewer inhibitors in these two pretreatments so that ethanol fermentation could be carried out without detoxification. But these pretreatments required higher energy consumption because of mechanical milling and high temperature compared to the process used in this study, and the final ethanol concentration was also lower than that in this study.
Overall, this study proposed a simple and low-cost process used to produce ethanol from corn fiber. In this process, mild pretreatment with dilute acid can enable the saccharification and fermentation process to directly be conducted without detoxification while ensuring the low loss of sugars during pretreatment, which was conducive to ensure the high ethanol yield, high final ethanol concentration (as high solid content after pretreatment), and no wastewater problem in pretreatment stage. These advantages show that this process has a good prospect of industrial application.
This study developed a simple production process for cellulosic ethanol using corn fiber. In this process, an optimized mild dilute acid pretreatment process ensured the high sugar recovery and fewer inhibitor production while high enzymatic digestibility of substrate, and the mixtures of solid and hydrolysates from pretreatment were directly transported into subsequent enzymatic hydrolysis and fermentation process without detoxification treatment for achieving high-efficiency conversion of sugar to ethanol and obtaining high ethanol yield at 20% of solid content through the semi-SSF process using acclimated yeast. This process could be easily industrialized with low equipment investment, fewer process steps, and no pretreatment wastewater problem.
The raw data supporting the conclusions of this article will be made available by the authors, without undue reservation.
YG and JZ designed the study. YG performed the experiment, analyzed the data, and wrote the manuscript. JH, NX, and HJ participated in part of the experiments. YQ revised the manuscript. JZ and XL conceived the study and edits for the manuscript. All authors contributed to the creation of the manuscript.
This study was financially supported by grants from the National Natural Science Foundation of China (No. 31870562), Natural Science Foundation of Shandong Province, China (ZR2019ZD19), and the Key Research and Development Project of Shandong Province (2019GSF107009).
The authors declare that the research was conducted in the absence of any commercial or financial relationships that could be construed as a potential conflict of interest.
All claims expressed in this article are solely those of the authors and do not necessarily represent those of their affiliated organizations, or those of the publisher, the editors and the reviewers. Any product that may be evaluated in this article, or claim that may be made by its manufacturer, is not guaranteed or endorsed by the publisher.
We would like to thank Xiangmei Ren from the State Key Laboratory of Microbial Technology of Shandong University for help and guidance in HPLC.
Agger, J., Viksø-Nielsen, A., and Meyer, A. S. (2010). Enzymatic xylose release from pretreated corn bran arabinoxylan: differential effects of deacetylation and deferuloylation on insoluble and soluble substrate fractions. J. Agric. Food Chem. 58, 6141–6148. doi: 10.1021/jf100633f
Avci, A., Saha, B. C., Dien, B. S., Kennedy, G. J., and Cotta, M. A. (2013). Response surface optimization of corn stover pretreatment using dilute phosphoric acid for enzymatic hydrolysis and ethanol production. Bioresour. Technol. 130, 603–612. doi: 10.1016/j.biortech.2012.12.104
Beri, D., York, W. S., Lynd, L. R., Peña, M. J., and Herring, C. D. (2020). Development of a thermophilic coculture for corn fiber conversion to ethanol. Nat. Commun. 11:1937. doi: 10.1038/s41467-020-15704-z
Bothast, R. J., and Schlicher, M. A. (2005). Biotechnological processes for conversion of corn into ethanol. Appl. Microbiol. Biotechnol. 67, 19–25. doi: 10.1007/s00253-004-1819-8
Brodeur, G., Yau, E., Badal, K., Collier, J., Ramachandran, K. B., and Ramakrishnan, S. (2011). Chemical and physicochemical pretreatment of lignocellulosic biomass: a review. Enzyme Res. 2011:787532. doi: 10.4061/2011/787532
Bura, R., Mansfield, S. D., Saddler, J. N., and Bothast, R. J. (2002). SO2-catalyzed steam explosion of corn fiber for ethanol production. Appl. Biochem. Biotechnol. 98-100, 59–72. doi: 10.1007/978-1-4612-0119-9_5
Eylen, D. V., Dongen, F., Kabel, M., and Bont, J. (2011). Corn fiber, cobs and stover: enzyme-aided saccharification and co-fermentation after dilute acid pretreatment. Bioresour. Technol. 102, 5995–6004. doi: 10.1016/j.biortech.2011.02.049
Gao, L., He, X., Guo, Y., Wu, Z., Zhao, J., Liu, G., et al. (2021). Combinatorial engineering of transcriptional activators in Penicillium oxalicum for improved production of corn-fiber-degrading enzymes. J. Agric. Food Chem. 69, 2539–2548. doi: 10.1021/acs.jafc.0c07659
Gáspár, M., Kálmán, G., and Réczey, K. (2007). Corn fiber as a raw material for hemicellulose and ethanol production. Process Biochem. 42, 1135–1139. doi: 10.1016/j.procbio.2007.04.003
Hames, B., Scarlata, C., and Sluiter, A. (2008). Determination of Protein Content in Biomass; Jan, Report No. TP-510-42625. Golden, CO: National Renewable Energy Laboratory.
Hendriks, A. T. W. M., and Zeeman, G. (2009). Pretreatments to enhance the digestibility of lignocellulosic biomass. Bioresour. Technol. 100, 10–18. doi: 10.1016/j.biortech.2008.05.027
Hou, J., Qiu, Z., Han, H., and Zhang, Q. (2018). Toxicity evaluation of lignocellulose-derived phenolic inhibitors on Saccharomyces cerevisiae growth by using the QSTR method. Chemosphere 201, 286–293. doi: 10.1016/j.chemosphere.2018.03.008
Ibbett, R., Gaddipati, S., Davies, S., Hill, S., and Tucker, G. (2011). The mechanisms of hydrothermal deconstruction of lignocellulose: new insights from thermal–analytical and complementary studies. Bioresour. Technol. 102, 9272–9278. doi: 10.1016/j.biortech.2011.06.044
Iram, A., Cekmecelioglu, D., and Demirci, A. (2019). Optimization of dilute sulfuric acid, aqueous ammonia, and steam explosion as the pretreatments steps for distillers’ dried grains with solubles as a potential fermentation feedstock. Bioresour. Technol. 282, 475–481. doi: 10.1016/j.biortech.2019.03.009
Jiang, K., Li, L., Long, L., and Ding, S. (2018). Comprehensive evaluation of combining hydrothermal pretreatment (autohydrolysis) with enzymatic hydrolysis for efficient release of monosaccharides and ferulic acid from corn bran. Ind. Crops Prod. 113, 348–357. doi: 10.1016/j.indcrop.2018.01.047
Jiang, L., Zheng, A., Zhao, Z., He, F., Li, H., and Liu, W. (2015). Obtaining fermentable sugars by dilute acid hydrolysis of hemicellulose and fast pyrolysis of cellulose. Bioresour. Technol. 182, 364–367. doi: 10.1016/j.biortech.2015.01.032
Jönsson, L., and Martín, C. (2016). Pretreatment of lignocellulose: formation of inhibitory by-products and strategies for minimizing their effects. Bioresour. Technol. 199, 103–112. doi: 10.1016/j.biortech.2015.10.009
Juneja, A., Noordam, B., Pel, H., Basu, R., Appeldoorn, M., and Singh, V. (2021). Optimization of two-stage pretreatment for maximizing ethanol production in 1.5G technology. Bioresour. Technol. 320, 124380. doi: 10.1016/j.biortech.2020.124380
Kabel, M. A., Bos, G., Zeevalking, J., Voragen, A. G. J., and Schols, H. A. (2007). Effect of pretreatment severity on xylan solubility and enzymatic breakdown of the remaining cellulose from wheat straw. Bioresour. Technol. 98, 2034–2042. doi: 10.1016/j.biortech.2006.08.006
Kim, S. K., Park, D. H., Song, S. H., Wee, Y., and Jeong, G. (2013). Effect of fermentation inhibitors in the presence and absence of activated charcoal on the growth of Saccharomyces cerevisiae. Bioprocess Biosyst. Eng. 36, 659–666. doi: 10.1007/s00449-013-0888-4
Kim, Y., Mosier, N. S., Hendrickson, R., Ezeji, T., Blaschek, H., Dien, B., et al. (2008). Composition of corn dry-grind ethanol by-products: DDGS, wet cake, and thin stillage. Bioresour. Technol. 99, 5165–5176. doi: 10.1016/j.biortech.2007.09.028
Kumar, P., Barrett, D. M., Delwiche, M. J., and Stroeve, P. (2009). Methods for pretreatment of lignocellulosic biomass for efficient hydrolysis and biofuel production. Ind. Eng. Chem. Res. 48, 3713–3729. doi: 10.1021/IE801542G
Kurambhatti, C. V., Kumar, D., Rausch, K. D., Tumbleson, M. E., and Singh, V. (2018). Increasing ethanol yield through fiber conversion in corn dry grind process. Bioresour. Technol. 270, 742–745. doi: 10.1016/j.biortech.2018.09.120
Larsson, S., Palmqvist, E., Hahn-Hägerdal, B., Tengborg, C., Stenberg, S., Zacvhi, G., et al. (1999). The generation of fermentation inhibitors during dilute acid hydrolysis of softwood. Enzyme Microb. Technol. 24, 151–159. doi: 10.1016/S0141-0229(98)00101-X
Lee, J. E., Vadlani, P. V., and Faubion, J. (2017). Corn bran bioprocessing: development of an integrated process for microbial lipids production. Bioresour. Technol. 243, 196–203. doi: 10.1016/j.biortech.2017.06.065
Li, X., Xu, Z., Yu, J., Huang, H., and Jin, M. (2019). In situ pretreatment during distillation improves corn fiber conversion and ethanol yield in the dry mill process. Green Chem. 21:1080. doi: 10.1039/C8GC03447H
López-Arenas, T., Rathi, P., Ramírez-Jiménez, E., and SalesCruz, M. (2010). Factors affecting the acid pretreatment of lignocellulosic biomass: batch and continuous process. Comput. Aided Chem. Eng. 28, 979–984. doi: 10.1016/S1570-7946(10)28164-6
Lovett, J. C., Hards, S., Clancya, J., and Snell, C. (2011). Multiple objectives in biofuels sustainability policy. Energy Environ. Sci. 4, 261–268. doi: 10.1039/C0EE00041H
Mikulski, D., and Kłosowski, G. (2018). Efficiency of dilute sulfuric acid pretreatment of distillery stillage in the production of cellulosic ethanol. Bioresour. Technol. 268, 424–433. doi: 10.1016/j.biortech.2018.08.005
Moore, R., Thornhill, K., Weinzierl, B., Sauer, D., D’Ascoli, E., Kim, J., et al. (2017). Biofuel blending reduces particle emissions from aircraft engines at cruise conditions. Nature 543, 411–415. doi: 10.1038/nature21420
Mosier, N. S., Hendrickson, R., Brewer, M., Ho, N., Sedlak, M., Dreshel, R., et al. (2005). Industrial scale-up of pH-controlled liquid hot water pretreatment of corn fiber for fuel ethanol production. Appl. Biochem. Biotechnol. 125, 77–97. doi: 10.1385/abab:125:2:077
Myat, L., and Ryu, G. H. (2014). Characteristics of destarched corn fiber extrudates for ethanol production. J. Cereal Sci. 60, 289–296. doi: 10.1016/j.jcs.2014.06.006
Nigam, P. S., and Singh, A. (2011). Production of liquid biofuels from renewable resources. Prog. Energy Combust. Sci. 37, 52–68. doi: 10.1016/j.pecs.2010.01.003
Noureddini, H., and Byun, J. (2010). Dilute-acid pretreatment of distillers’ grains and corn fiber. Bioresour. Technol. 101, 1060–1067. doi: 10.1016/j.biortech.2009.08.094
Palmqvist, E., and Hahn-Hägerdal, B. (2000). Fermentation of lignocellulosic hydrolysates. II: inhibitors and mechanisms of inhibition. Bioresour. Technol. 74, 25–33. doi: 10.1016/S0960-8524(99)00161-3
Rahman, S. H. A., Choudhury, J. P., and Ahmad, A. L. (2006). Production of xylose from oil palm empty fruit bunch fiber using sulfuric acid. Biochem. Eng. J. 30, 97–103. doi: 10.1016/j.bej.2006.02.009
Saha, B. C. (2003). Hemicellulose bioconversion. J. Ind. Microbiol. Biotechnol. 30, 279–291. doi: 10.1007/s10295-003-0049-x
Sanchez, B., and Bautista, J. (1988). Effects of furfural and 5-hydroxymethylfurfural on the fermentation of Saccharomyces cerevisiae and biomass production from Candida guilliermondii. Enzyme Microb. Technol. 10, 315–318. doi: 10.1016/0141-0229(88)90135-4
Santos, V. T. O., Siqueira, G., Milagres, A. M. F., and Ferraz, A. (2018). Role of hemicellulose removal during dilute acid pretreatment on the cellulose accessibility and enzymatic hydrolysis of compositionally diverse sugarcane hybrids. Ind. Crops Prod. 111, 722–730. doi: 10.1016/j.indcrop.2017.11.053
Searchinger, T. D., Wirsenius, S., Beringer, T., and Dumas, P. (2018). Assessing the efficiency of changes in land use for mitigating climate change. Nature 564, 249–253. doi: 10.1038/s41586-018-0757-z
Shrestha, P., Khanal, S. K., Pometto, A. L. III, and van Leeuwen, J. H. (2010). Ethanol production via in situ fungal saccharification and fermentation of mild alkali and steam pretreated corn fiber. Bioresour. Technol. 101, 8698–8705. doi: 10.1016/j.biortech.2010.06.089
Sluiter, A., Ruiz, R., Scarlata, C., Sluiter, J., and Templeton, D. (2005a). Determination of Extractives in Biomass; Jan, Report No. TP-510-42619. Golden, CO: National Renewable Energy Laboratory.
Sluiter, A., Hames, B., Ruiz, R., Scarlata, C., Sluiter, J., and Templeton, D. (2005b). Determination of Ash in Biomass; Jan, Report No. TP-510-42622. Golden, CO: National Renewable Energy Laboratory.
Sluiter, A., Hames, B., Ruiz, R., Scarlata, C., Sluiter, J., Templeton, D., et al. (2008a). Determination of Structural Carbohydrates and Lignin in Biomass; Jan, Report No. TP-510-42618. Golden, CO: National Renewable Energy Laboratory.
Sluiter, A., Hames, B., Ruiz, R., Scarlata, C., Sluiter, J., and Templeton, D. (2008b). Determination of Sugars, Byproducts, and Degradation Products in Liquid Fraction Process Samples; Jan, Report No. TP-510-42632. Golden, CO: National Renewable Energy Laboratory.
Sluiter, A., and Sluiter, J. (2005). Determination of Starch in Solid Biomass Samples by HPLC; Jan, Report No. TP-510-42624. Golden, CO: National Renewable Energy Laboratory.
Toor, M., Kumar, S. S., Malyan, S. K., Bishnoi, N. R., Mathimani, T., Rajendran, K., et al. (2020). An overview on bioethanol production from lignocellulosic feedstocks. Chemosphere. 242, 125080. doi: 10.1016/j.chemosphere.2019.125080
Yang, W., Li, P., Bo, D., and Chang, H. (2012). The optimization of formic acid hydrolysis of xylose in furfural production. Carbohydr. Res. 357, 53–61. doi: 10.1016/j.carres.2012.05.020
Yemiş, O., and Mazza, G. (2011). Acid-catalyzed conversion of xylose, xylan and straw into furfural by microwave-assisted reaction. Bioresour. Technol. 102, 7371–7378. doi: 10.1016/j.biortech.2011.04.050
Keywords: corn fiber, dilute sulfuric acid pretreatment, optimization, semi-simultaneous saccharification and fermentation, ethanol
Citation: Guo Y, Huang J, Xu N, Jia H, Li X, Zhao J and Qu Y (2022) A Detoxification-Free Process for Enhanced Ethanol Production From Corn Fiber Under Semi-Simultaneous Saccharification and Fermentation. Front. Microbiol. 13:861918. doi: 10.3389/fmicb.2022.861918
Received: 25 January 2022; Accepted: 01 March 2022;
Published: 30 March 2022.
Edited by:
Christopher Rensing, Fujian Agriculture and Forestry University, ChinaReviewed by:
Binod Parameswaran, National Institute for Interdisciplinary Science and Technology (CSIR), IndiaCopyright © 2022 Guo, Huang, Xu, Jia, Li, Zhao and Qu. This is an open-access article distributed under the terms of the Creative Commons Attribution License (CC BY). The use, distribution or reproduction in other forums is permitted, provided the original author(s) and the copyright owner(s) are credited and that the original publication in this journal is cited, in accordance with accepted academic practice. No use, distribution or reproduction is permitted which does not comply with these terms.
*Correspondence: Xuezhi Li, bGl4ekBzZHUuZWR1LmNu; Jian Zhao, emhhb2ppYW5Ac2R1LmVkdS5jbg==
Disclaimer: All claims expressed in this article are solely those of the authors and do not necessarily represent those of their affiliated organizations, or those of the publisher, the editors and the reviewers. Any product that may be evaluated in this article or claim that may be made by its manufacturer is not guaranteed or endorsed by the publisher.
Research integrity at Frontiers
Learn more about the work of our research integrity team to safeguard the quality of each article we publish.