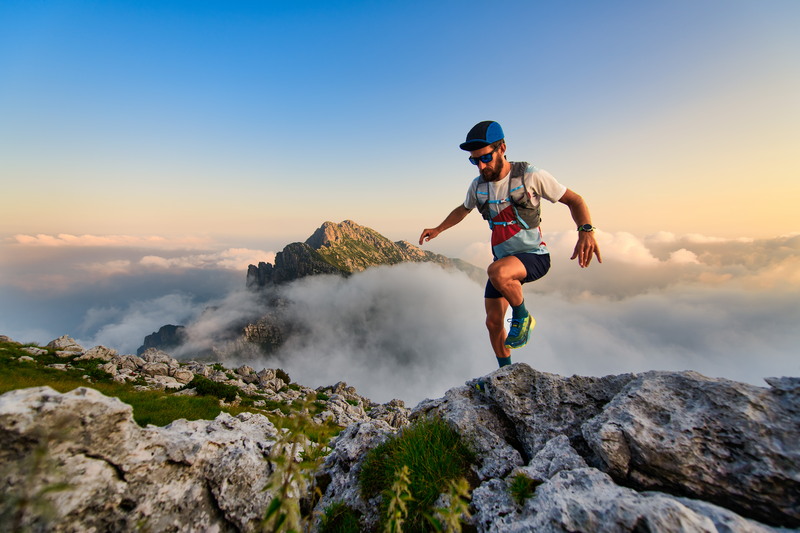
95% of researchers rate our articles as excellent or good
Learn more about the work of our research integrity team to safeguard the quality of each article we publish.
Find out more
SYSTEMATIC REVIEW article
Front. Mech. Eng. , 09 July 2024
Sec. Tribology
Volume 10 - 2024 | https://doi.org/10.3389/fmech.2024.1412137
This article is part of the Research Topic Visualization Techniques in Tribology View all 17 articles
Condition monitoring of machine elements becomes more important over the last years. Different approaches to detect failures in mechanical components have been developed. All these methods are located at a distance from the point of interest, the observed machine element. This leads to uncertainties in the data, which influences the data quality negatively. Using the electrical impedance for condition monitoring enables in situ measurement with reduced uncertainties and higher data quality. In the last years, research considering this topic was done, but a systematic overview is missing. In this article, a systematic literature research according to the PRISMA approach is fulfilled. The main questions are, what application fields for electrical impedance-based condition monitoring approaches exists and which research gaps are not addressed yet. At the end, 21 articles are categorized in their application fields. Analyzing their content, research questions are identified which have to be addressed in further investigations.
Rolling element bearings are one of the most important machine elements in mechanical engineering. They are widely used and a crucial component in most technical systems (Hamrock and Dowson, 1981; Harris, 2001; Kirchner, 2007). Therefore, a damaged rolling element bearing can cause critical damages in a machine or apparatus, which lead to unplanned downtimes and reduced reliability (Schaeffler Monitoring Services GmbH, 2019; Peng et al., 2022). Hence, there is an increasing interest in the detection of harmful bearing conditions and the identification of bearing damages.
The state of the art for damage detection in machine elements for rotary machines is vibration analysis (Davies and Davies, 1998; Jardine et al., 2006; Schenk, 2010; Randall, 2011; Lei, 2016; Schaeffler Monitoring Services GmbH, 2019). Other techniques are thermography, shaft speed analysis, endoscopy and lubricant analysis (Davies and Davies, 1998; Miller and Kitaljevich, 2000; Jardine et al., 2006; Schenk, 2010; Randall, 2011; Schaeffler Monitoring Services GmbH, 2019). Alternative condition monitoring approaches utilize the stator currents in electrical machines (Cameron et al., 1986; Thomson and Barbour, 1998). All these methods have the same disadvantage. They are located outside the point of interest, so the signal path from the damaged bearing to the sensor or observation point is affected by uncertainties (Engelhardt, 2012; Mathias, 2016; Vorwerk-Handing, 2020; Becker-Dombrowsky et al., 2023a). This influences the measurement results and reduces the information density. To increase information density. The usage of machine learning approaches for analyzing the sensor data is also common (Lei et al., 2008; Lei, 2016; Akpudo and Hur, 2020).
To avoid this disadvantage, sensory utilizable machine elements (SuME) can be used to enable in situ measurement. SuME use the electric properties of machine elements to enhance the functionalities of a component to become a sensor itself (Kraus et al., 2020; Kraus et al., 2021). One widespread measurement category of SuME is the electric impedance. Impedance-based condition monitoring approaches are already in use, e.g., for insulation observation (Jameson et al., 2017; Joseph and Krishnan, 2021; Zheng et al., 2021), condition monitoring of stator windings (Kohler et al., 2002; Zhang et al., 2022) and fuel cell observation (Beer et al., 2015; Boškoski et al., 2017; Mahlangu and Barendse, 2021; Jiang et al., 2023). By measuring the electric impedance of a rolling element bearing, different kinds of information can be achieved and the bearing becomes a sensor, which enables condition monitoring of itself and of the surrounding system (Becker-Dombrowsky et al., 2023a; Prashad, 1988; Schirra et al., 2018).
The idea of using the electric properties of machine elements is not new, e.g., Prashad already investigated their opportunities (Prashad, 1988). Many researchers study different kinds of applications for impedance measurement. A structured overview of the state of research in the context of impedance-based condition monitoring for machine elements such as rolling bearings is still missing. Therefore, the aim of this work is to get an overview of this topic and two answer the following two main questions:
1. What are applications of impedance based condition monitoring approaches?
2. Which research gaps exists for the identified approaches?
To do so, scientific literature will be investigated and summarized systematically. Other review articles in this field are focused on harmful currents in drivetrains and electrical induced bearing damages (Johns-Rahnejat et al., 2023; Schneider et al., 2022b) or on film thickness detection techniques (Peng et al., 2022). A broader application field for using the electric properties of bearings, e.g., to detect damages is not considered so far. This article is looking at the topic of impedance-based condition monitoring approaches in general.
In the following section, the fundamentals outlining the basics of the electrical impedance and the electric properties of rolling elements bearings will be addressed. Afterwards, the research method is presented. Then, the results are discussed and a conclusion will be drawn.
In this section, the fundamentals of electrical impedance and the elasto-hydrodynamic lubrication (EHL) contacts are given. In addition, the electric analogous model of rolling element bearings will be explained.
Electrical impedance is the impedance of an element through which alternating current flows. It is determined in the complex plane. The real part R represents the effective resistance, the imaginary part the circular frequency-dependent reactance X. The latter can have both capacitive and inductive components. Therefore, the impedance can be described completely via amplitude and phase (Keysight Technologies, 2014).
The impedance Z is calculated according to Hufschmid as follows in Eq. 1 (Hufschmid, 2021).
The amplitude of the impedance |Z| can be determined using Pythagoras' theorem written in Eq. 2. The phase angle φ results from the geometric observation of the impedance vector in the complex plane using the tangent in Eq. 3 (Hufschmid, 2021).
The reactance X can exhibit both capacitive and inductive behavior. In the case of inductive behavior, the reactance is calculated taking into account the angular frequency, where L is the inductance and ω is the electrical angular frequency shown in Eq. 4 (Rinderknecht, 2017).
The reactance is calculated in the case of capacitive behavior according to Eq. 5; the capacitance is described by the letter C (Rinderknecht, 2017).
The geometric relations describing the electric impedance are pictured in Figure 1.
Figure 1. The Pythagoras theorem explaining the electrical impedance according to (Keysight Technologies, 2014).
In general, components show a frequency dependent behavior under alternating current and can exhibit different behaviors. The phase angle for ideal capacitance is–90° until the natural resonant frequency is reached. The phase angle of ideal inductors, on the other hand, is +90° below the natural resonant frequency. Ideal resistors have an angle of 0°. The natural resonant frequency is the frequency at which the reactance of inductance and capacitance are equal and have a phase angle of φ = 0°. The components then exhibit resistive behavior. After the natural resonance frequency is exceeded, the sign of the respective phase angle changes and the components change their behavior (Keysight Technologies, 2014; Furtmann et al., 2016).
The theory of elasto-hydrodynamic lubricated contact (EHL contact) considers the elastic deformation of the contact partners in the rolling contact, taking into account Hertzian theory in combination with the influence of temperature and pressure on the lubricant viscosity in the lubrication gap. This is an extension of the theory of hydrodynamic contact (HD) (Brüser, 1972; Hamrock and Dowson, 1981; Hertz, 1881; Dahlke, 1994; Steinhilper and Sauer, 2012a).
The EHL theory can be used to determine the minimum lubricant film thickness in the rolling contact (Hamrock and Dowson, 1981). This is particularly interesting with regard to the question of sufficient lubricant supply, but also for the electrical properties of the rolling bearing, which will be discussed in more detail later.
The EHL theory is based on the use of several dimensionless parameters, which record the prevailing operating conditions in the rolling contact and thus enable the calculation of the lubrication gap height. Isothermal operating conditions and smooth surfaces of the contact partners are assumed (Hamrock and Dowson, 1981).
According to Hamrock/Dowson, the dimensionless minimum lubricant film thicknes
It is made up of the dimensionless parameters for load W, speed U and material G, as well as the ratio of the elliptical semi-axes of the Hertzian contact k (Hamrock and Dowson, 1981).
The EHL effect is created by the transportation of lubricant through the lubrication gap. On the inlet side, the lubricant adhering to the bodies is introduced into the lubrication gap. On the outlet side, the lubricant is pressed out of the gap by the prevailing load. Consequently, this is also where the maximum pressure acting in the lubrication gap is located. As a result of the movement and load on the lubricant, shearing of the lubricant occurs. This leads to friction and energy dissipation. This circumstance is not taken into account in the theory according to Hamrock/Dowson. This can be remedied by using correction factors to extend the equation of the minimum lubricant film thickness. However, these are not discussed further here, but reference is made to the relevant literature (Hamrock and Dowson, 1981).
As Furtmann explained, machine elements can exhibit different electrical behavior under alternating current and can be modeled accordingly as circuit elements. He regards shafts as electrical conductors whose electrical behavior corresponds to a serial connection of resistance and inductance between each machine element applied (Furtmann et al., 2016).
EHL contact area building machine elements such as rolling bearings and spur gears show a capacitive behavior under hydrodynamic lubrication. They can be modeled as a plate capacitor in case of liquid friction (Becker-Dombrowsky et al., 2023a; Furtmann et al., 2016; Prashad, 2006). Machine elements like housings, screws and shafts are modeled as a serial connection of inductance and ohmic resistance. This is based on the pure metallic structure of this components, which does not allow other electric behavior (Becker-Dombrowsky et al., 2023a; Furtmann et al., 2016). Figure 2 summarizes the central machine elements for rotating machinery and their equivalent electrical components.
Figure 2. Common machine elements and their equivalent electrical components according to (Becker-Dombrowsky et al., 2023a), modified by author.
As the results in Section 4 show, researchers in the field of impedance-based condition monitoring are focused on rolling element bearings. Therefore, only the electric analogous model of rolling element bearings will be presented in the next section.
Rolling bearings in an AC circuit can be described as series and parallel connections of capacitors and resistors. The arrangement of the elements and thus the overall electrical behavior change according to the lubrication conditions within the bearing (Prashad, 1988).
The rolling contact is electrically modeled as a plate capacitor with the capacitance
Figure 3. Electric model of the EHL contact in a ball bearing (Schirra, 2021).
The capacitance is calculated according to the equation for plate capacitors Eq. 7 as follows (Gemeinder, 2016).
This shows that the capacitance and consequently the impedance of the rolling contact depend on the lubricant properties (relative permittivity
As can be seen from Figure 3, the equation above does not take into account the boundary influence zone. Barz and Gemeinder use a correction factor
Schirra has already proposed an approach for the corresponding model extension. It replaces the static factors for considering the edge zone by calculating the capacity in this zone. In addition, the unloaded rolling elements are included in the analysis in a similar way. The calculations carried out by him correspond to the empirically determined values and therefore represent a sufficiently accurate model description (Schirra, 2021).
In case of the EHL contact, the contact partners are completely separated and the bearing exhibits capacitive behavior if a high-resistance lubricant is used. The capacitance of the contact depends on the contact geometry, the number of rolling elements, the lubricant film thickness and the electrical properties of the lubricant, which acts as a dielectric (Gemeinder, 2016; Bechev et al., 2020).
Figure 4 shows the exemplary replacement model of a rolling contact with a single rolling element in the bearing under alternating voltage
Figure 4. Equivalent model of a contact consisting of a rolling element and inner or outer ring (Furtmann, 2017).
Depending on the lubrication conditions in the rolling contact, three different electrical behaviors can be determined within the lubrication gap. These are primarily related to the lubrication gap height. Figure 5 illustrates this relationship.
Figure 5. Electric model of the EHL contact as a function of the lubrication film thickness (Martin, 2021).
In the area of solid-state friction, there is direct metallic contact between the rolling element and the respective raceway, so that the contact zone can be modeled as an ohmic resistance
As can be seen in the middle section of Figure 5, two different phenomena can occur with a thin lubricant film, which are related to the breakdown voltage. According to Gemeinder, the latter is the product of the breakdown field strength of the lubricant and the lubricant film height (Gemeinder, 2016). If the lubricant film height is sufficient or if the voltage at the rolling contact is below the breakdown voltage, the phenomenon described for the EHL contact of the parallel connection of capacitance
The bearing current density is decisive for the damaging effect of currents. The bearing current depends on the magnitude of the applied voltage and the bearing impedance (Prashad, 1988), which in turn is related to the contact conditions within the lubrication gap (Gemeinder, 2016). The bearing current density is defined as the quotient of the current and the effective Hertzian area (Muetze, 2003). A bearing current density below 0.1 A/mm2 is considered uncritical (Radnai et al., 2015). A damaging effect cannot be ruled out between 0.1 A/mm2 and 1 A/mm2. Larger bearing currents, on the other hand, have a damaging effect (Radnai et al., 2015). As soon as liquid friction is present, an insulating lubricating film forms between the contact partners and the EHL contact occurs with the behavior described above (Gemeinder, 2016).
As the fundamentals show, impedance measurement and capacitance calculation enable different monitoring approaches to machine elements and especially to rolling bearings. A systematic classification of the applications for impedance measurement in machine element observation has not been fulfilled yet. Also, analyzing possible research gaps and further opportunities of this technique is still missing. Therefore, a systematic literature research is fulfilled in this work to classify the different application fields in impedance based machine element observation and to find possible research questions. In the next section, the method of this literature research is presented.
The aim of this work is to get an overview of impedance-based condition monitoring methods. This includes all kinds of machine elements in mechanical engineering topic. The focus is on the observation of classic machine elements like spur gears and rolling element bearings. Specialized applications like fuel cell observation mentioned in Section 1 are not included. Articles about electrical induced damages in rolling element bearings and harmful bearing currents are not included as well. The topics are connected to each other, but electrical induced damages of machine elements are a specific and own field. A literature review according to the PRISMA approach is applied to check different databases about possible literature.
PRISMA is an abbreviation for “Preferred Reporting Items for Systematic Reviews and Meta-Analyses.” This approach is a systematic method to analyze different databases to get an overview of the state of research on a certain topic. PRISMA is already used for literature research in medical and clinical contexts (Liberati et al., 2009; Page et al., 2021).
The proceeding in this work is according to Fett et al. (2023), which also used the PRISMA approach for a review in a mechanical engineering topic. The investigated databases Inspec, ProQuest, TEMA and Web of Science are common in mechanical engineering. Additionally, articles found from other sources like Research Gate and Google Scholar are included as well. The databases are searched using their internal search engine. The results are saved in an internal database, where they are clustered manually.
As a search term for the title the following string was used. The restrictions to the title were included using Boolean operators. For the single database, some details had to be changed, but not in a significant manner. Only the titles are investigated to get a reasonable amount of articles. Otherwise, a lot of improper literature has to be investigated. In the first search, spur gears and other machine elements were included, but no literature was found. So, the search term was changed to reduce the amount of improper literature.
1. TITLE (“Impedance” or “Electrical Impedance” or “Impedance Measurement*” or “Real Part” or “Imaginary Part” or “Phase Angle” or “Absolute Value” or “Capacitance” or “Impedanz” or “Elektrische Impedanz” or “Impedanzmessung*” or “Impedanzmessverfahren” or “Realteil” or “Imaginärteil” or “Phasenwinkel” or “Impedanzbetrag” or “Betrag der Impedanz” or “Kapazität”)
2. TITLE (“Rolling Element Bearing*” or “Roll* Bearing” or “EHL” or “EHL contact” or “Machine Element*” or “Condition Monitoring” or “Lubrication Condition” or “Wälzlager” or “Maschinenelement” or “Zustandsüberwachung”)
After getting the title from the databases, the duplicates are removed and the remaining titles are screened. Titles that do not include condition monitoring using the electric properties of classic machine elements as their topic are excluded. Included are articles, which enable the usage of impedance-based condition monitoring of machine elements by fundamental research. After excluding improper titles, the proper articles are screened and read in detail. Improper articles, articles in unusual languages and not available articles have been removed. In the end, twenty articles are further investigated. Figure 6 summarizes the investigation process. The number of articles in every step is mentioned as well.
As mentioned in Section 3, twenty articles are identified as proper for this review. Analyzing the publication year, the increasing interest in the topic of impedance based condition monitoring techniques can be seen. In Figure 7 the trend is illustrated. The first article on this topic was published by Heemskerk et al. (1982). In the last years, the increase of interest in the electric impedance can be seen. As yet, the amount of publications has its maximum in 2023 with five articles.
Figure 7. Published articles to impedance based condition monitoring of machine elements over their publication years.
After analyzing the articles’ content, three main topics can be differentiated. The first one is about load measurement using the electrical impedance. Using load measurement as an instrument for condition monitoring is based on the idea of detecting the loads affecting a machine element and calculating the remaining useful life (Schirra et al., 2018; Schaeffler Monitoring Services GmbH, 2019; Schirra, 2021). It can be applied to machine elements with a fatigue limit such as spur gears (in case of pit load capacity) and rolling element bearings (Dahlke, 1994; Steinhilper and Sauer, 2012a; Steinhilper and Sauer, 2012b; Deutsches Institut für Normung e.V. Wälzlager, 2021). The second topic contains rolling bearing condition monitoring by analyzing electrical signals, e.g., for damage detection. The third and most commonly investigated topic addresses the lubrication condition monitoring. Further, it can be divided into lubrication film thickness detection and lubricant condition detection. All articles are focused on rolling element bearings as the observed machine element or the EHL contact itself. Other machine elements like spur gears are not part of the investigations. Furtmann described the electrical analogous models for different machine elements, but condition monitoring is not his scope (Furtmann et al., 2016; Furtmann, 2017).
In the following, the articles will be summarized shortly in their topic classes. Figure 8 gives an overview of the identified topics.
The idea of load measurement using the electrical impedance is initiated by Schirra et al. (2018). They investigate the opportunities of simultaneous load and failure monitoring. The basis is the analogous model of the rolling contact. From the impedance, the capacitance is calculated, which enables estimating the Hertzian area. Using the Hertzian area, the load and the resulting remaining useful lifespan of the rolling bearing can be estimated. For a real sensor application, further investigations are necessary as well as additional sensors, e.g., for temperature and speed gauging. Also, instationary operating conditions are not investigated (Schirra et al., 2018).
Some of the identified challenges of impedance based load measurement are considered by Schirra et al. (2021) in a subsequent publication. Their research is taking unloaded rolling elements and the undeflected area into account by enlarging the current models. Their experimental results show an improvement, but differences between measurement and calculation remain (Schirra et al., 2021).
The articles to impedance based load measurement are summarized in Table 1.
Yang et al. (2000) investigated a method to measure the rolling element skew in a tapered roller bearing. The installed two contact potential difference probes at the outer ring and gauged the capacitance between roller and ring. With this capacitance signal, they measure the skew. They were able to determine the correlation between skew, rotational speed and lubrication (Yang et al., 2000).
Tuomas and Isaksson developed an impedance based measurement technique to observe the buildup of the lubrication film in rolling element bearings to identify different operating conditions. Their investigation enables the differentiation between the run-in phase at the beginning of bearing life and the enclosing normal operating state. At the end of bearing life, they are able to identify changes in the signal behavior which indicates additional metallic contacts (Tuomas and Isaksson, 2009).
Schnabel et al. identify the run-in phase of EHL contacts. Further, they studied the correlation between surface roughness and impedance behavior at their ball on disk apparatus. They found out that the contact resistance depends on the surface roughness. The impedance in general was not affected by surface active additives (Schnabel et al., 2016).
Schirra et al. (2018) were already mentioned in Section 4.1. The idea behind the condition monitoring approach is to detect the bearing loads and to calculate the remaining useful lifetime of the observed bearing (Schirra et al., 2018).
Martin et al. (2022) used the impedance signals and changes in the signal to detect pitting damages in the surface. They measured the impedance using a shunt circuit at their rolling bearing test rig in fatigue tests under stationary operating conditions. They also investigate the impedance under artificial surface damages at the inner ring raceway. As a result, detecting and localizing the pitting damages was possible. Also, they are able to measure the pitting length in the raceway (Martin et al., 2022).
Chevallier et al. (2023) compare vibration measurement based condition monitoring to impedance-based condition monitoring approaches. They provide evidence for the possibilities of the impedance method. It can be seen that impedance based condition monitoring has opportunities to be investigated further (Chevallier et al., 2023).
Becker-Dombrowsky et al. (2023b) investigate the data generated by Martin et al. (2022). They identified indicators in the impedance signal using feature engineering approaches, which enables an early detection of pitting damages. The behavior of the identified features in time and frequency domain could be physically explained (Becker-Dombrowsky et al., 2023b).
The articles to impedance based rolling bearing condition monitoring are summarized in Table 2.
Lubrication condition monitoring is the biggest topic in impedance based condition monitoring. It can be divided into lubrication condition detection and the film thickness detection.
Zeng et al. (2020) use the electrical impedance to detect debris in the oil and other abnormalities. The developed sensor is able to detect metallic particles in the lubricant as well as water droplets and bubbles in the oil. Particles between 18 µm (iron) and 75 µm (copper) could be detected. So, the presented system is able to monitor lubricants and systems condition by detecting impurity (Zeng et al., 2020).
Shi et al. (2022) present a similar approach. They have developed an inductance-resistance and capacitance sensing micro sensor. With this sensor, they are able to detect metallic debris, moisture and air bubbles in the observed oil. This enables condition monitoring (Shi et al., 2022).
The articles to lubricant condition detection are summarized Table 3.
Heemskerk et al. (1982) investigate measuring the lubrication condition in rolling bearings using the electrical impedance. They were able to gauge the film thickness in case of separating lubrication film. They could predict the so-called lift-off speed at the end of the run-in for grease lubrication and named possible application fields (Heemskerk et al., 1982).
Tuomas and Isaksson measured the lubrication condition in rolling element bearings in a refrigerant environment using the electrical impedance. Due to the lower viscosity because of the refrigerant in the oil, a higher amount of metallic contacts in the run-in was expected. They could identify the run-in phase of the bearing by measuring the impedance and the higher amount of metallic contacts in the impedance signal at the bearing’s beginning and end of life (Tuomas and Isaksson, 2009).
Glovnea et al. (2012) already published a review about the evaluation of lubrication in EHL contacts using electrical methods. Most approaches were focused on experimental apparatus. They list advantages and disadvantages, but also discuss the opportunities of impedance measurement (Glovnea et al., 2012).
Clarke et al. (2016) investigate the mixed lubrication regime using the electrical contact resistance techniques. It can be shown that the measurement technique was able to monitor the contact conditions and the dependence of the signal from the lubrication film height. Also, the relation between contact resistance, high loads and surface roughness are examined (Clarke et al., 2016).
For lubrication film thickness measurement, Xie et al. (2016) developed an impedance based measurement approach avoiding slip rings and other common contact devices. Therefore, they used two electric field coupling paths. The error between the presented approach and the slip ring method is about 15%, which they declared as sufficient enough for film thickness measurements (Xie et al., 2016).
Jablonka et al. (2012) investigated the electrical analogous model of the ball to raceway contact for a ball on flat configuration. The measurement method based on the impedance is applicable to machine elements like rolling element bearings, but further research is needed. They identify the contact geometry model and the lubricant itself as another research topics (Jablonka et al., 2012).
In a subsequent contribution, Jablonka et al. (2018) transferred their knowledge to radially loaded deep-groove ball bearings. They implemented a quantitative measurement approach for film thickness detection. Modified rolling bearings with ceramic balls and one metallic ball were used to investigate the electric behavior of the single contact in the bearing. So, they were able to investigate lubricant composition, properties and supply, load, temperature and entrainment speed. It could be shown that impedance measurement in rolling bearings allows film thickness detection (Jablonka et al., 2018).
Maruyama and Nakano compared the impedance measurement approach for film thickness evaluation to optical interferometry on a ball-on-disc apparatus. They could confirm that the results of impedance based oil film thickness measurement agreed with the interferometry results. This allows the transfer of the impedance measurement approach to machine elements like ball bearings for EHL contact investigation (Maruyama and Nakano, 2018).
Later, Maruyama et al. (2019) picked up their results and developed an impedance based approach for film thickness monitoring and breakdown ratio of oil films in EHL contacts of ball bearings. It is shown that using the impedance, a parallel observation of breakdown ratio and lubrication film thickness is possible. Also, they compared the calculated film thickness after Hamrock and Dowson (1981) to the measured thickness. In the low-speed range, the measured values agreed with the calculated film heights satisfactorily. For higher speeds, the measured film thickness is thinner than the calculated one, which means that the models have to be optimized (Maruyama et al., 2019).
In 2023, Maruyama et al. (2019) transferred the approach of their research in 2019 to thrust needle roller bearings. The results were similar to the results for ball bearing, which suggests an independence of the measurement technique from the rolling element bearing type (Maruyama et al., 2023).
Cen et al. (2021) created a review on EHL film thickness in rolling element bearings using the capacitance method. Two main approaches for transforming the measured capacitance to an oil film thickness were identified. The first one calculates the capacitance in the Hertzian contact area. The second method uses calibration approaches to transfer the measured capacitance into a film thickness (Cen et al., 2021).
Schneider et al., 2022b present a new capacitance based analytical method for film thickness monitoring. The article includes an approach for measuring and calculating the capacitance of each rolling contact. The novelty of this publication is the calculation of the local lubricant film height of combined loaded bearings with point contact (Schneider et al., 2022a).
Manjunath et al. (2024) describe the Electrical Impedance Spectroscopy (EIS) as an instrument for film thickness measurement in line contact bearings. The research before is focused on film thickness detection in point contact building bearings. For analyzing the generated impedance data, impedance-based and capacitance-based approaches are used. The authors can show that the measured capacitance differs from the calculated capacitance by a factor of 3 up to 11, depending on the parameters like speed and temperature. The presented EIS approach enables to detect the transition from boundary to mixed lubrication and from mixed lubrication to EHL (Manjunath et al., 2024).
The articles to lubricant condition detection are summarized in Table 4.
Using the impedance to measure loads in machine elements, namely, rolling element bearings, works under certain conditions. Mainly, its accuracy depends on the electric analogous model of the EHL contact, which has to be investigated further. Schirra et al. (2021) were able to improve the model, but an error between measurement and calculation still remains (Schirra et al., 2021).
In case of impedance based rolling bearing condition monitoring, two basic topics could be identified. The initial idea was to detect the end of run-in phase and optimal lubrication condition in rolling element bearings to optimize the bearing lifespan (Tuomas and Isaksson, 2009; Schnabel et al., 2016). Later, Schirra et al. (2018) established the idea of condition monitoring over the bearing operational time in general and remaining useful life calculation using the electric analogous model of the EHL contact in combination with the Hertzian theory (Schirra et al., 2018). Martin et al. analyzed the complex impedance signal to find significant changes which leads to pitting damages in the bearings raceways (Martin et al., 2022). They are able to detect and to localize pitting damages and to measure their length in rolling direction. Rycerz et al. (2017); Kunzelmann et al. (2023) developed an approach for rolling contact fatigue prediction, which is based on mathematic models describing the pitting damage progression. They could show that their models can predict the damage progression properly, when the pitting damage has reached a certain dimension. Impedance measurement can detect and measure small pitting damages to use the models described in (Rycerz et al., 2017; Kunzelmann et al., 2023), which is not possible with vibration measurement (Kunzelmann et al., 2023) or ultrasonic reflectrometry (Peng et al., 2022). Becker-Dombrowsky et al. (2023a) continued analyzing the signals of Martin et al. (2022) and could find features in time and frequency domain, which enables the usage of machine learning approaches for damage early detection (Becker-Dombrowsky et al., 2023b; Chevallier et al., 2023) could identify further opportunities for impedance based condition monitoring compared to vibration measurement (Chevallier et al., 2023). Analyzing the different research articles, several open research question can be seen. In fact, the impedance measurement approach is still limited to rolling element bearings. Other machine elements are not taken into account, yet. A first research article to this topic is presented by Becker-Dombrowsky et al. (2023a), but a comparable level to impedance based rolling bearing condition monitoring is not reached. Furthermore, all research was done under stationary operating conditions. Besides, rolling bearings can be operated in mixed lubrication regime, which is not investigated yet. The experiments use standard lubricants without additives. There is the possibility that additives might influence the electric properties by mutating the raceway surfaces (Lugt et al., 2001; Prashad, 2006; Reibung and Schmierung und Verschleiß, 2015; Schnabel et al., 2016; Bukvić et al., 2024). The impedance of the lubricant near the raceway surface differs from the lubricant impedance between the raceways (Furtmann, 2017), which indicates changes in the electric properties of the bearing using surface mutating additives such as described in (Bukvić et al., 2024).
Investigations under varying loads and speeds are still missing, which is essential for an application in technical systems. Further research is needed here, especially how load and speed changes can influence the signals. It is not clear, if a condition detection can be realized under instationary operating parameters. Another aspect is, if health monitoring is possible under high dynamic conditions. A comparison between states of technique applications like vibration measurement and impedance measurement would be interesting as well.
All tests were carried out in hydrodynamic lubrication regime, but mixed lubrication is not investigated yet. This has to be addressed as well to apply the technique to, e.g., gearboxes. The influence of lubricant additives to the impedance signal is not considered. They can affect the contact partner surfaces, which may cause changes in the impedance signal.
The topic of impedance based lubrication condition monitoring is more investigated than the two topics before, especially film thickness detection. After measuring the lubrication film thickness in ball-on-disc apparatus and other test rigs for single contact investigation (Glovnea et al., 2012; Jablonka et al., 2012; Schnabel et al., 2016; Maruyama and Nakano, 2018), the impedance based approach is applied to rolling element bearings (Heemskerk et al., 1982; Tuomas and Isaksson, 2009; Xie et al., 2016; Maruyama et al., 2019; Schneider et al., 2022a; Maruyama et al., 2023). The results show that the application is transferable from the single contact to the bearing in general, independently from the bearing type with different contact conditions (Maruyama et al., 2019; Maruyama et al., 2023). Still, differences between calculation and measurement remain, which indicates that the contact models need to be improved further. Also, the influence of different lubricants is not investigated yet. Some additives have been researched regarding their influence on the contact impedance, but further research is necessary (Schnabel et al., 2016). A detection of mixed lubrication condition is possible (Heemskerk et al., 1982; Tuomas and Isaksson, 2009; Clarke et al., 2016; Schnabel et al., 2016), but a sufficient film thickness measurement out of the hydrodynamic lubrication regime is not researched as well as varying operation conditions.
For lubricant condition detection, it was shown that different kinds of oil soiling can be detected. This includes metallic particles, moisture and air bubbles (Zeng et al., 2020; Shi et al., 2022). However, tests for lubricant condition detection in machine elements like spur gears and rolling element bearings are still missing. This includes investigations under stationary and instationary operation conditions as well as experiments in the mixed and hydrodynamic lubrication regimes.
As mentioned in Section 4, the research field of impedance based condition monitoring techniques for machine elements can be separated in three main applications summarized in Figure 8. It can be seen that more research in the field of impedance based condition monitoring for machine elements is needed. Mostly, rolling element bearings are in the focus of this techniques. Other EHL contact building machine elements like spur gears are not investigated deeply in this research area. All in all, the presented approaches are investigated under laboratory conditions. In general, the impedance behavior under instationary operating conditions is not researched yet, independently of its use case. Also, other lubrication regimes beside the hydrodynamic lubrication are not investigated. A transfer to real applications is missing.
In this review, a systematic literature review according to the PRISMA approach was fulfilled to investigate the topic of electrical impedance based condition monitoring of machine elements. Different databases were studied for literature. The articles found were screened and at the end, 20 articles and their research content were presented.
The research topic of electrical impedance based condition monitoring can be divided in three main section, the load measurement, the rolling bearing condition monitoring and the lubrication condition monitoring. The last one can further be divided into the topics of lubricant condition detection and film thickness detection. It can be seen that the focus of research is on rolling element bearings. This is not surprising, because rolling bearings are one of the central components in drivetrains. The amount of subcategories for the single application fields is interesting, because the identified opportunities for this condition monitoring approach are greater than assumed.
In addition, several research gaps are identified. Other machine elements like spur gears are not taken into account. Based on their electric behavior in the EHL regime, a similar impedance signal behavior can be possible for surface induced damages. Also, the electric properties in the mixed lubrication regime have to be investigated. For rolling element bearings, different lubrication regimes beside the hydrodynamic lubrication are not considered yet. If a damage detection in case of mixed friction is possible has to be investigated further. The influence of surface mutating additives in oil and grease lubrication might change the electric behavior under mixed lubrications in positive or negative manner, which is not considered yet. Furthermore, the presented approaches are tested under stationary operating conditions. A generalization of impedance behavior for different rotational speeds and forces for condition monitoring is missing. Further research has to identify load and speed independent signal characteristic to ensure an overall usage of impedance-based condition monitoring.
In summary, for applying electrical impedance based condition monitoring approaches of machine elements beyond laboratory, further research is necessary. Both research questions are addressed and answered by the results of this literature research. Based on these results, further research regarding impedance-based condition monitoring can be fulfilled.
The original contributions presented in the study are included in the article/Supplementary Material, further inquiries can be directed to the corresponding author.
FB-D: Conceptualization, Formal Analysis, Investigation, Project administration, Supervision, Visualization, Writing–original draft. EK: Project administration, Resources, Supervision, Writing–review and editing.
The author(s) declare that no financial support was received for the research, authorship, and/or publication of this article.
The authors declare that the research was conducted in the absence of any commercial or financial relationships that could be construed as a potential conflict of interest.
All claims expressed in this article are solely those of the authors and do not necessarily represent those of their affiliated organizations, or those of the publisher, the editors and the reviewers. Any product that may be evaluated in this article, or claim that may be made by its manufacturer, is not guaranteed or endorsed by the publisher.
Akpudo, U. E., and Hur, J.-W. (2020). A feature fusion-based prognostics approach for rolling element bearings. J. Mech. Sci. Technol. 34 (10), 4025–4035. doi:10.1007/s12206-020-2213-x
Barz, M. (1996). Die schmierfilmbildung in fettgeschmierten schnellaufenden spindellagern. Diss. (Hannover: Gottfried Wilhelm Leibniz Universität).
Bechev, D., Weicker, M., Schwörer, K., Dellwo, U., and Arnold, D. (2020). “Schädlicher stromdurchgang 2 forschungsvorhaben nr. 650 II,” in Methodik zur praxisnahen Charakterisierung von elektrischen Schmierstoffeigenschaften zur Verbesserung der rechnerischen Vorhersage von Lagerströmen (Frankfurt: Forschungsvereinigung Antriebstechnik e.V).
Becker-Dombrowsky, F. M., Hausmann, M., Welzbacher, P., Harder, A., and Kirchner, E. (2023a). Systematic identification of disturbance factors on electric characteristics of mechanical gearboxes.
Becker-Dombrowsky, F. M., Koplin, Q. S., and Kirchner, E. (2023b). Individual feature selection of rolling bearing impedance signals for early failure detection. Lubricants 11 (7), 304. doi:10.3390/lubricants11070304
Beer, C. de, Barendse, P. S., and Pillay, P. (2015). Fuel cell condition monitoring using optimized broadband impedance spectroscopy. IEEE Trans. Industrial Electron. 62 (8), 5306–5316. doi:10.1109/TIE.2015.2418313
Boškoski, P., Debenjak, A., and Mileva Boshkoska, B. (2017). Fast electrochemical impedance spectroscopy. doi:10.1007/978-3-319-53390-2
Brüser, P. (1972). Untersuchungen über die elastohydrodynamische Schmierfilmdicke bei elliptischen Hertzschen Kontaktflächen. Braunschweig: Technische Universität Braunschweig.
Bukvić, M., Gajević, S., Skulić, A., Savić, S., Ašonja, A., and Stojanović, B. (2024). Tribological application of nanocomposite additives in industrial oils. Lubricants 12 (1), 6. doi:10.3390/lubricants12010006
Cameron, J. R., Thomson, W. T., and Dow, A. B. (1986). Vibration and current monitoring for detecting airgap eccentricity in large induction motors. IEE Proc. B Electr. Power Appl. doi:10.1049/ip-b.1986.0022
Cen, H., Bai, D., Chao, Y., Li, Y., and Li, R. (2021). EHL film thickness in rolling element bearings evaluated by electrical capacitance method: a review. Tribology-Materials, Surfaces Interfaces 15, 55–77. doi:10.1080/17515831.2020.1838098
Chevallier, E., Boudimbou, J. C., Bouzerar, R., Garcia, T., Bolaers, F., and Chiementin, X. (2023). Monitoring of roller bearings: electrical vs vibrational analysis 2023. doi:10.31224/3295
Clarke, A., Weeks, I., Evans, H. P., and Snidle, R. W. (2016). An investigation into mixed lubrication conditions using electrical contact resistance techniques. Tribol. Int. 93, 709–716. doi:10.1016/j.triboint.2014.10.010
Dahlke, H. (1994). Handbuch wälzlager-technik: bauarten, gestaltung, betrieb. 1994th ed. Wiesbaden: Springer Fachmedien.
Davies, A. (1998). “Handbook of condition monitoring,” in Techniques and methodology. Editor A. Davies (Netherlands: SpringerDordrecht).
Deutsches Institut für Normung e.V. Wälzlager (2021). Dynamische Tragzahlen und nominelle Lebensdauer.
Engelhardt, R. A. (2012). “Uncertainty Mode and Effects Analysis – heuristische Methodik zur Analyse und Beurteilung von Unsicherheiten in technischen Systemen des Maschinenbaus,” in Technische universität Darmstadt (Düsseldorf: VDI-Verlag).
Fett, M., Wilking, F., Goetz, S., Kirchner, E., and Wartzack, S. (2023). “Sensor selection and integration for Cyber-Physical Systems in context of Digital Twins – a systematic review of requirements,” in 18th Annual System of Systems Engineering Conference (SoSe), 1–7. doi:10.1109/SoSE59841.2023.10178669
Furtmann, A. (2017). Elektrisches Verhalten von Maschinenelementen im Antriebsstrang (Hannover: Gottfried Wilhelm Leibniz Universität Hannover).
Furtmann, A., Tischmacher, H., and Poll, G. (2016). “Extended HF equivalent model of a drive train,” in XXII international conference on electrical machines (ICEM): SwissTech convention center. Lausanne, Switzerland, 04-07 September, 2016 (Piscataway, NJ: IEEE), 2244–2250.
Gemeinder, Y. (2016). “Lagerimpedanz und Lagerschädigung bei Stromdurchgang in umrichtergespeisten elektrischen Maschinen,” in Technische universität darmstadt (Bonn: Ingenieurwissenschaftlicher Verlag).
Glovnea, R., Furtuna, M., Nagata, Y., and Sugimura, J. (2012). Electrical methods for the evaluation of lubrication in elastohydrodynamic contacts. Tribol. Online 7 (1), 46–53. doi:10.2474/trol.7.46
Hamrock, B. J., and Dowson, D. (1981). Ball bearing lubrication: the elastohydrodynamics of elliptical contacts. New York: Wiley.
Harder, A., Zaiat, A., Becker-Dombrowsky, F. M., Puchtler, S., and Kirchner, E. (2022). Investigation of the voltage-induced damage progression on the raceway surfaces of thrust ball bearings. Machines 10 (10), 832. doi:10.3390/machines10100832
Heemskerk, R. S., Vermeiren, K. N., and Dolfsma, H. (1982). Measurement of lubrication condition in rolling element bearings. A S L E Trans. 25 (4), 519–527. doi:10.1080/05698198208983121
Hertz, H. (1881). Über die Berührung fester elastischer Körper. J. für die reine und angewandte Math. 92, 156–171.
Hufschmid, M. (2021). Grundlagen der Elektrotechnik: Einführung für Studierende der Ingenieur-und Naturwissenschaften. Wiesbaden: Springer Vieweg.
Jablonka, K., Glovnea, R., and Bongaerts, J. (2012). Evaluation of EHD films by electrical capacitance. J. Phys. D Appl. Phys. 45, 385301. doi:10.1088/0022-3727/45/38/385301
Jablonka, K., Glovnea, R., and Bongaerts, J. (2018). Quantitative measurements of film thickness in a radially loaded deep-groove ball bearing. Tribol. Int. 119, 239–249. doi:10.1016/j.triboint.2017.11.001
Jameson, N. J., Azarian, M. H., and Pecht, M. (2017). Impedance-based condition monitoring for insulation systems used in low-voltage electromagnetic coils. IEEE Trans. Industrial Electron. 64 (5), 3748–3757. doi:10.1109/TIE.2017.2652359
Jardine, A. K., Lin, D., and Banjevic, D. (2006). A review on machinery diagnostics and prognostics implementing condition-based maintenance. Mech. Syst. Signal Process. 20, 1483–1510. doi:10.1016/j.ymssp.2005.09.012
Jiang, P., Chen, J., Jin, L., and Kumar, L. (2023). Adaptive condition monitoring for fuel cells based on fast EIS and two-frequency impedance measurements. IEEE Trans. Industrial Electron. 70 (8), 8517–8525. doi:10.1109/TIE.2022.3220843
Johns-Rahnejat, P. M., Rahmani, R., and Rahnejat, H. (2023). Current and future trends in tribological research. Lubricants 11 (9), 391. doi:10.3390/lubricants11090391
Joseph, J., and Krishnan, S. T. (2021). Development of severity and location indices based condition monitoring scheme for underground cables by impedance spectroscopy. IEEE Trans. Power Deliv. 36 (2), 533–543. doi:10.1109/TPWRD.2020.2984476
Keysight Technologies (2014). Impedance measurement handbook: a guide to measurement technology and techniques; Available at: https://www.keysight.com/de/de/assets/7018-06840/application-notes/5950-3000.pdf.
Kirchner, E. (2007). Leistungsübertragung in Fahrzeuggetrieben: Grundlagen der Auslegung, Entwicklung und Validierung von Fahrzeuggetrieben und deren Komponenten. Berlin, Heidelberg: Springer-Verlag Berlin Heidelberg.
Kohler, J. L., Sottile, J., and Trutt, F. C. (2002). Condition monitoring of stator windings in induction motors. I. Experimental investigation of the effective negative-sequence impedance detector. IEEE Trans. Ind. Appl. 38 (5), 1447–1453. doi:10.1109/TIA.2002.802935
Kraus, B., Neu, M., and Kirchner, E. (2020). Sensing machine elements as enablers of comprehensive digitization – a review.
Kraus, B., Schmitt, F., Steffan, K.-E., and Kirchner, E. (2021). A valve closing body as a central sensory-utilizable component.
Kunzelmann, B., Rycerz, P., Xu, Y., Arakere, N. K., and Kadiric, A. (2023). Prediction of rolling contact fatigue crack propagation in bearing steels using experimental crack growth data and linear elastic fracture mechanics. Int. J. Fatigue 168, 107449. doi:10.1016/j.ijfatigue.2022.107449
Lei, Y. (2016). Intelligent Fault diagnosis and remaining useful life prediction of rotating machinery. Oxford, United Kingdom: Elsevier.
Lei, Y., He, Z., and Zi, Y. (2008). A new approach to intelligent fault diagnosis of rotating machinery. Expert Syst. Appl. 35 (4), 1593–1600. doi:10.1016/j.eswa.2007.08.072
Liberati, A., Altman, D. G., Tetzlaff, J., Mulrow, C., Gøtzsche, P. C., Ioannidis, J. P. A., et al. (2009). The PRISMA statement for reporting systematic reviews and meta-analyses of studies that evaluate healthcare interventions: explanation and elaboration. BMJ 339, b2700. doi:10.1136/bmj.b2700
Loos, J., Bergmann, I., and Goss, M. (2021). Influence of high electrical currents on WEC formation in rolling bearings. Tribol. Trans. 64 (4), 708–720. doi:10.1080/10402004.2021.1909789
Lugt, P. M., Severt, R. W. M., Fogelströ, J., and Tripp, J. H. (2001). Influence of surface topography on friction, film breakdown and running-in in the mixed lubrication regime. Proc. Institution Mech. Eng. Part J J. Eng. Tribol. 215, 519–533. doi:10.1243/1350650011543772
Mahlangu, S., and Barendse, P. (2021). Online condition monitoring of fuel cells (FC) by implementing electrical impedance spectroscopy using a switch-mode DC-DC converter, 477–482. doi:10.1109/ECCE47101.2021.9595528
Manjunath, M., Hausner, S., Heine, A., Baets, P. de, and Fauconnier, D. (2024). Electrical impedance spectroscopy for precise film thickness assessment in line contacts. Lubricants 12 (2), 51. doi:10.3390/lubricants12020051
Martin, G. (2021). “Die Wälzlagerimpedanz als Werkzeug zur Untersuchung von Oberflächenabweichungen in Wälzlagern,” in Technische universität darmstadt (Darmstadt: Primary publication).
Martin, G., Becker, F. M., and Kirchner, E. (2022). A novel method for diagnosing rolling bearing surface damage by electric impedance analysis. Tribol. Int. 170, 107503. doi:10.1016/j.triboint.2022.107503
Maruyama, T., Maeda, M., and Nakano, K. (2019). Lubrication condition monitoring of practical ball bearings by electrical impedance method. Tribol. Online 14, 327–338. doi:10.2474/trol.14.327
Maruyama, T., and Nakano, K. (2018). In situ quantification of oil film formation and breakdown in EHD contacts. Tribol. Trans. 61 (6), 1057–1066. doi:10.1080/10402004.2018.1468519
Maruyama, T., Radzi, F., Sato, T., Iwase, S., Maeda, M., and Nakano, K. (2023). Lubrication condition monitoring in EHD line contacts of thrust needle roller bearing using the electrical impedance method. Lubricants 11 (5), 223. doi:10.3390/lubricants11050223
Mathias, J. (2016). “Auf dem Weg zu robusten Lösungen - Modelle und Methoden zur Beherrschung von Unsicherheit in den frühen Phasen der Produktentwicklung,” in Technische universität darmstadt (Düsseldorf: VDI Verlag GmbH).
Miller, J. L., and Kitaljevich, D. (2000). “In-line oil debris monitor for aircraft engine condition assessment,” in 2000 IEEE Aerospace Conference. Proceedings (Cat. No.00TH8484).
Muetze, A. (2003). “Bearing currents in inverter-fed AC-motors,” in Technische universität darmstadt (Darmstadt: Shaker-Verlag GmbH).
Page, M. J., Moher, D., Bossuyt, P. M., Boutron, I., Hoffmann, T. C., Mulrow, C. D., et al. (2021). PRISMA 2020 explanation and elaboration: updated guidance and exemplars for reporting systematic reviews. BMJ 372, n160. doi:10.1136/bmj.n160
Peng, H., Zhang, H., Shangguan, L., and Fan, Y. (2022). Review of tribological failure analysis and lubrication technology research of wind power bearings. Polym. (Basel) 14 (15), 3041. doi:10.3390/polym14153041
Prashad, H. (1988). Theoretical evaluation of impedance, capacitance and charge accumulation on roller bearings operated under electrical fields. Wear 125 (3), 223–239. doi:10.1016/0043-1648(88)90115-9
Radnai, B., Gemeinder, Y., Kiekbusch, T., Weber, J., Hering, J., and Arnold, D. (2015). Schädlicher Stromdurchgang: Untersuchung des Schädigungsmechanismus und der zulässigen Lagerstrombelastung von Wälzlagern in E-Motoren und Generatoren verursacht durch parasitäre hochfrequente Lagerströme (Frankfurt am Main: FVA-Heft 1127, Forschungsvorhaben Nr. 650 I, Forschungsvereinigung Antriebstechnik e.V.).
Randall, R. B. (2011). “Vibration-based condition monitoring: industrial,” in Aerospace and automotive applications (Chichester: Wiley).
Reibung Schmierung and Verschleiß (2015). Reibung, Schmierung und Verschleiß - Forschung und praktische Anwendungen. in Gesellschaft für Tribologie (Göttingen: GfT Gesellschaft für Tribologie e.V.).
Rycerz, P., Olver, A., and Kadiric, A. (2017). Propagation of surface initiated rolling contact fatigue cracks in bearing steel. Int. J. Fatigue 97, 29–38. doi:10.1016/j.ijfatigue.2016.12.004
Schaeffler Monitoring Services GmbH (2019). Condition Monitoring Praxis: Handbuch zur Schwingungs-Zustandsüberwachung von Maschinen und Anlagen. 1st ed. Mainz: Vereinigte Fachverlage GmbH.
Schenk, M. (2010). Instandhaltung technischer Systeme: Methoden und Werkzeuge zur Gewährleistung eines sicheren und wirtschaftlichen Anlagenbetriebs (Berlin: Springer-Verlag).
Schirra, T. (2021). Phänomenologische Betrachtung der sensorisch nutzbaren Effekte am Wälzlager – Einfluss unbelasteter Wälzkörper auf die elektrische Impedanz: UNSPECIFIED.
Schirra, T., Martin, G., Puchtler, S., and Kirchner, E. (2021). Electric impedance of rolling bearings - consideration of unloaded rolling elements. Tribol. Int. 158, 106927. doi:10.1016/j.triboint.2021.106927
Schirra, T., Martin, G., Vogel, S., and Kirchner, E. (2018). “ball bearings as sensors for systematical combination of load and failure monitoring,” in Design 2018: proceedings of the 15th international design conference, may 2018, dubrovnik, Croatia. Editors D. Marjanović, M. Štorga, S. Škec, N. Bojčetić, and N. Pavković (Zagreb: Fac: of Mechanical Engineering and Naval Architecture Univ), 3011–3022.
Schnabel, S., Marklund, P., Minami, I., and Larsson, R. (2016). Monitoring of running-in of an EHL contact using contact impedance. Tribol. Lett. 63 (3), 35. doi:10.1007/s11249-016-0727-2
Schneider, V., Bader, N., Liu, H., and Poll, G. (2022a). Method for in situ film thickness measurement of ball bearings under combined loading using capacitance measurements. Tribol. Int. 171, 107524. doi:10.1016/j.triboint.2022.107524
Schneider, V., Behrendt, C., Höltje, P., Cornel, D., Becker-Dombrowsky, F. M., Puchtler, S., et al. (2022b). “Electrical bearing damage,” in A problem in the nano- and macro-range.
Schneider, V., Liu, H.-C., Bader, N., Furtmann, A., and Poll, G. (2021). Empirical formulae for the influence of real film thickness distribution on the capacitance of an EHL point contact and application to rolling bearings. Tribol. Int. 154, 106714. doi:10.1016/j.triboint.2020.106714
Shi, H., Zhang, H., Huo, D., Yu, S., Su, J., Xie, Y., et al. (2022). An ultrasensitive microsensor based on impedance analysis for oil condition monitoring. IEEE Trans. Industrial Electron. 69, 7441–7450. doi:10.1109/tie.2021.3100982
Steinhilper, W., and Sauer, B. (2012a). Konstruktionselemente des Maschinenbaus 2: Grundlagen von Maschinenelementen für Antriebsaufgaben. 7th ed. (Berlin, Heidelberg: Springer Berlin Heidelberg).
Steinhilper, W., and Sauer, B. (2012b). Konstruktionselemente des Maschinenbaus 1: Grundlagen der Berechnung und Gestaltung von Maschinenelementen. 8th ed. (Berlin: Springer Vieweg).
Thomson, W. T., and Barbour, A. (1998). “On-line current monitoring and application of a finite element method to predict the level of static airgap eccentricity in three-phase induction motors,” in IEEE Transactions on Energy Conversion. (IEEE), 347–357.
Tischmacher, H. (2017). Systemanalysen zur elektrischen Belastung von Wälzlagern bei umrichtergespeisten Elektromotoren. Dissertation. (Hannover: Gottfried Wilhelm Leibniz Universität Hannover).
Tischmacher, H., and Gattermann, S. (2012). Multiple signature analysis for the detection of bearing currents and the assessment of the resulting bearing wear. in International Symposium on Power Electronics Power Electronics, Electrical Drives, Automation and Motion. 1354–1359.
Tuomas, R., and Isaksson, O. (2009). Measurement of lubrication conditions in a rolling element bearing in a refrigerant environment. Industrial Lubr. Tribol. 61, 91–99. doi:10.1108/00368790910940419
Vorwerk-Handing, G. (2020). “Erfassung systemspezifischer Zustandsgrößen – Physikalische Effektkataloge zur systematischen Identifikation potentieller Messgrößen,” in Technische universität darmstadt (Darmstadt: Publisher's Version).
Xie, K., Liu, L.-C., Li, X.-P., and Zhang, H.-L. (2016). Non-contact resistance and capacitance on-line measurement of lubrication oil film in rolling element bearing employing an electric field coupling method. Measurement 91, 606–612. doi:10.1016/j.measurement.2016.05.080
Yang, Y., Danyluk, S., and Hoeprich, M. (2000). A study on rolling element skew measurement in a tapered roller bearing with a specialized capacitance probe. J. Tribol. 122 (3), 534–538. doi:10.1115/1.555397
Zeng, L., Wang, W., Rogers, F., Zhang, H., Zhang, X., and Yang, D. (2020). A high sensitivity micro impedance sensor based on magnetic focusing for oil condition monitoring. IEEE Sensors J. 20 (7), 3813–3821. doi:10.1109/JSEN.2019.2958872
Zhang, P., Zheng, D., and Lu, G. (2022). The effect and compensation of phase angle deviation along the winding for the online stator insulation condition monitoring. IEEE Trans. Industrial Electron. 69 (8), 8440–8451. doi:10.1109/TIE.2021.3108730
Keywords: electrical impedance, condition monitoring, systematic review, load measurement, condition detection, electric properties, EHL
Citation: Becker-Dombrowsky FM and Kirchner E (2024) Electrical impedance based condition monitoring of machine elements–a systematic review. Front. Mech. Eng 10:1412137. doi: 10.3389/fmech.2024.1412137
Received: 04 April 2024; Accepted: 13 June 2024;
Published: 09 July 2024.
Edited by:
Steven Chatterton, Polytechnic University of Milan, ItalyReviewed by:
Saša Milojević, University of Kragujevac Faculty of Engineering, SerbiaCopyright © 2024 Becker-Dombrowsky and Kirchner. This is an open-access article distributed under the terms of the Creative Commons Attribution License (CC BY). The use, distribution or reproduction in other forums is permitted, provided the original author(s) and the copyright owner(s) are credited and that the original publication in this journal is cited, in accordance with accepted academic practice. No use, distribution or reproduction is permitted which does not comply with these terms.
*Correspondence: Florian Michael Becker-Dombrowsky, Zmxvcmlhbl9taWNoYWVsLmJlY2tlckB0dS1kYXJtc3RhZHQuZGU=
†ORCID: Florian Michael Becker-Dombrowsky, orcid.org/0000-0002-4272-861X; Eckhard Kirchner, orcid.org/0000-0002-7663-8073
Disclaimer: All claims expressed in this article are solely those of the authors and do not necessarily represent those of their affiliated organizations, or those of the publisher, the editors and the reviewers. Any product that may be evaluated in this article or claim that may be made by its manufacturer is not guaranteed or endorsed by the publisher.
Research integrity at Frontiers
Learn more about the work of our research integrity team to safeguard the quality of each article we publish.