- 1Department of System Dynamics and Friction Physics, Technische Universität Berlin, Berlin, Germany
- 2Center of Advanced Studies in Mechanics, Tribology, Bio- and Nanotechnologies, Samarkand State University, Samarkand, Uzbekistan
The entry and propagation of pores inside an adhesive interface between an elastomer and a rigid sphere were studied experimentally and simulated numerically. It was shown that mutually interacting events involving attachment–detachment of different segments of the elastomer to the indenter resulted in non-trivial patterns of spatially distributed contacts between them, which were additionally influenced by air penetration of the pores.
1 Introduction
One of the actively developing areas in contact mechanics is associated with the study of adhesive contacts (Brörmann et al., 2013; Sahli et al., 2018; Liu et al., 2024; Siniscalco et al., 2024). There is increasing interest regarding the study of adhesion because adhesion phenomena are easily observable in daily life. However, complex processes occur within adhesive contacts related to restructuring of the contact boundaries when the contacting surfaces shift mutually. These could be a combination of propagation of elastic waves in the contact zone, hysteresis phenomena, etc. Adhesion also has high significance in various applications, including robotics (Weston-Dawkes et al., 2021; Singh and Gupta, 2022), medicine (Ge and Chen, 2020; Zemljič-Jokhadar et al., 2021), biology (Gorb et al., 2019; van den Boogaart et al., 2022; Phiri et al., 2023), and other areas (Chernov et al., 2014; da Silva et al., 2018; Lyashenko and Liashenko, 2020).
This work is devoted to the experimental study of an intriguing phenomenon like the propagation of elastic waves that are generated in the adhesive contact zone when a solid indenter slides along the surface of a soft elastomer. Analogous waves were first observed in a classical work (Schallamach, 1971) and were therefore named as Schallamach waves. It has been shown that adhesion leads to complex processes caused by restructuring of the contact during tangential movements (Schallamach, 1971; Brörmann et al., 2013). The specificity of the present work is the consideration of quasistatic contacts since the indenter moves along the surface of the elastomer at a very low speed. Despite this, the passage of elastic waves is observed within the contact. The present work also proposes a dynamic model that allows description of the occurrences of the observed waves and their propagation using relatively simple and clearly observed dynamics with two-dimensional representations. Our experiment reveals a highly interesting feature: changes in the friction mode and characteristics of elastic wave propagation resulting from contamination of the friction surfaces and decrease in adhesion. Since the contact characteristics rely heavily on adhesive strength that varies over time, building a general theory or model of tangential adhesive contact presents a fundamentally difficult challenge. This implies that a different theory should be developed or adapted for each experimental system.
2 Experimental results
Using the experimental setup detailed in Lyashenko et al. (2024), we conducted an experiment in which a steel sphere of radius
An important feature of this experiment is the possibility of direct observation of the contact area as an optically transparent elastomer is used. This enables real-time observation of the dynamic processes inside the continuously restructuring contact zone. Figure 1 shows the experimental time dependences of the normal
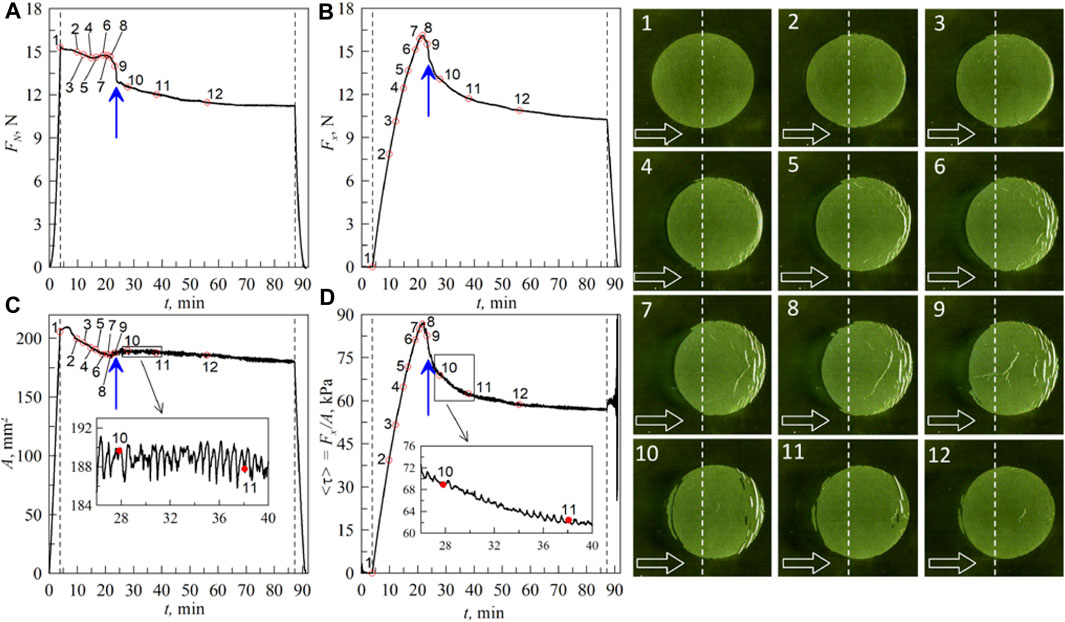
Figure 1. Experimental dependences of the (A) normal
The value
where μ is the friction coefficient. However, our experiments demonstrated that the adhesive properties decrease during sliding, consequently decreasing
The point 1 in Figure 1 corresponds to the final moment of normal indentation. Up to this point, the contact area can be approximated as
The frictional force in the contact is
The observed folds propagation represents Schallamach waves (Schallamach, 1971; Viswanathan and Chandrasekar, 2022) in adhesive contacts. An interesting feature of the case considered here is that over time, the propagation of folds in the contact stops completely (photo 12 in Figure 1). Surprisingly, this occurs in the same experimental run and indicates a transition to a different friction regime.
It is noted that before the experiment, the indenter surface was briefly treated with a FeCl3 solution, which greatly increased the adhesive strength of the contact against pull-off, meaning that the contact also becomes stronger to shearing. The properties of the indenter surface prepared in this manner degrade quickly upon contact with the elastomer and especially upon sliding. During sliding, the average stress
Another important feature is the specific character of elastic wave propagation. In our case, these waves are visualized as the propagation of folds from the leading to trailing edges of the contact. However, the waves propagate intermittently. After the next slip of the fold, further propagation stops since it is fixed in another place of the indenter where the position is stable. This is because the stresses must reach a maximum value
This is clearly visible in Supplementary Video S1, even though the video speed is 24 times faster than that of the original experiment. Note that even if the indenter moves with an extremely low speed, local slips occur with speeds that are many times higher. Therefore, to numerically simulate the process of fold propagation, it is necessary to construct a dynamic model with viscoelasticity and elastomer relaxation (Carbone et al., 2022; Papangelo and Ciavarella, 2023; Khudoynazarov, 2024). The processes under consideration are quite complex, so we limited our initial efforts to a simplified 1 + 1-dimensional model that allows us to trace the main features of fold propagation in the presence or absence of air in the folds.
3 Numerical model
The model essentially exploits the same numerical technique as in Lyashenko et al. (2023), where the elastic foundation was constructed from a set of interacting movable automata powered by a combination of short-range repulsion and long-range attraction. This allows the automata to naturally form a medium that maintains an elastically fixed distance between the neighbors. In the present work, we considered the contact between a rigid sphere and a planar elastic substrate. This is a standard tribological configuration characterized by adhesion, pressure, tangential shift, and other standard parameters (Stojanovic and Ivanović, 2014).
Formally one can treat the array of movable automata as a system of
In the majority of practically interesting cases, it is convenient to represent the interaction by a pair of potentials:
where
To simulate the elastic system, we define the initial positions of the automata on an ordered grid, where node of the grid is connected to its neighbors by an elastic force, tending to conserve the initial distances between the nodes in the original structure. This interaction is caused by the potential
which leads to linear elastic forces at small deviations and automatically ensures that the nodes are connected to each other at the equilibrium distance
The equations of motion can be written in standard form (Landau and Lifshitz, 1976) as
An analogous numerical approach and similar equations were recently used in Filippov et al. (2024a, 2024b). However, to simulate the effect of adhesion realistically, it has to be completed using a condition that specifies the circumstances where a segment of the substrate follows the sphere and is practically glued to it by adhesion. Thus, a given segment of the substrate is attached to the spherical surface when the distance between them is small enough
To proceed with this model, we applied an external load
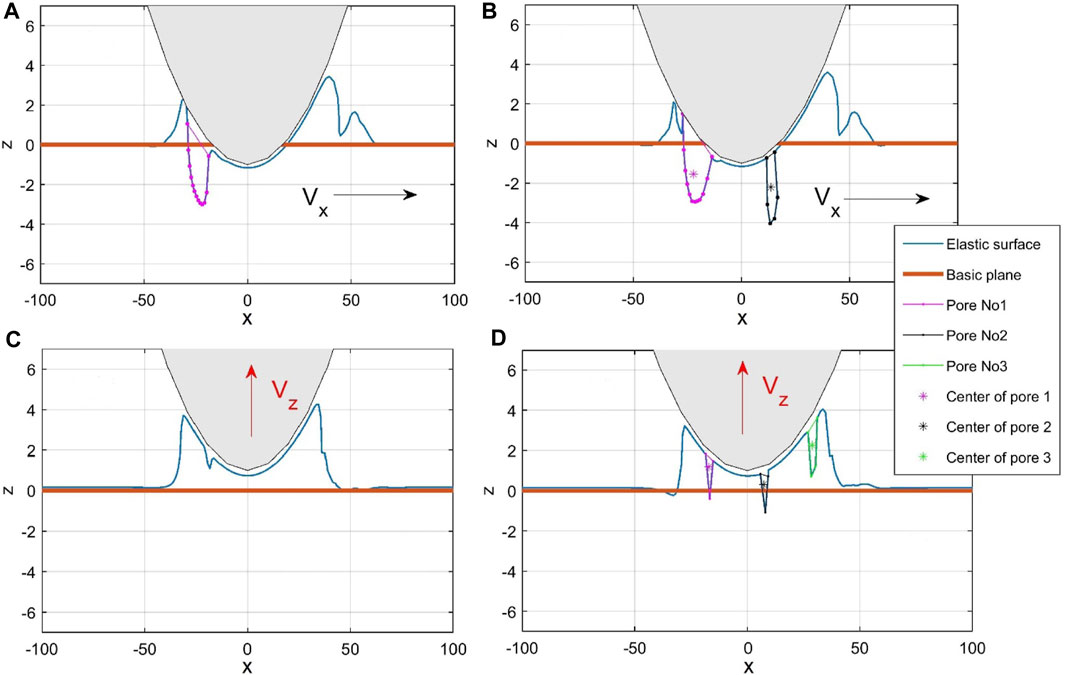
Figure 2. General sketch of the problem (A) without and (B) with air. (C) and (D) depict the same curves as in (A) and (B) at the final stage when the ball is gradually lifted from the substrate.
It is useful to apply this model to clarify the role of air in the real experiments, where air always exists (Koudine et al., 1997; Rand and Crosby, 2006). Air enters the pores and remains within them if the pores close after being formed. The trapped air produces a pressure that varies depending on the pore-size variations; this pressure grows inversely with the pore’s volume, such that the pressure decreases and slows the rate of expansion when it expands. When the pore shrinks, the air pressure increases and prevents collapse; hence, it is expected that the presence of air should stabilize the pores.
To incorporate air into the model, we added it as follows. In
Below, we present all the results as comparisons between the cases with and without air while maintaining all the other conditions constant. As a rule,
Slow vertical lifting of the indenter at the final stage of the routine is shown by the red arrow
The dynamic processes for the cases with and without air are demonstrated in Supplementary Video S2. Moreover, to enable direct visualization of the process in the form close to that in Figure 2, Supplementary Video S2 simultaneously shows data accumulation for the history of the processes, which are used to further depict them in static form as time–space maps in Figure 3.
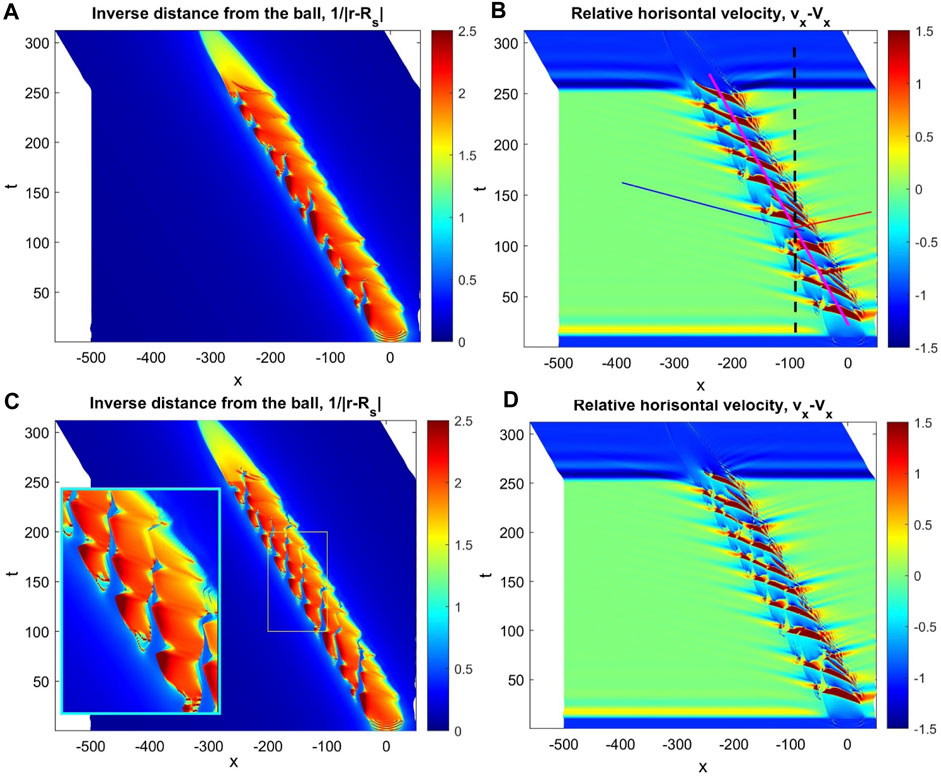
Figure 3. Time–space maps reproducing the recorded histories of inverse distance
In particular, these maps reproduce the histories recorded for the inverse distance
We also note the fine structures of the time-dependent distance between the sphere and elastic surface as well as mutual velocities in Figure 3C and Figure 3D, respectively. These complex structures of the depicted values are caused by the simultaneous presence of numerous pores. To elucidate the propagation of the chain of pores inside the system, we show a magnified fragment in Figure 3C marked by the rectangle. Integral information regarding the time-dependent volumes of the pores with and without air is shown in Figure 4A and Figure 4B, respectively. The different colors in the plots correspond exactly to the sequence of different pores shown in the instants in Figure 2. The numerical simulation supports the original idea that the pores exist (and coexist) longer upon being stabilized by the air pressure and that their individual curves overlap in time thereof (in other words, some of the pores exist simultaneously).
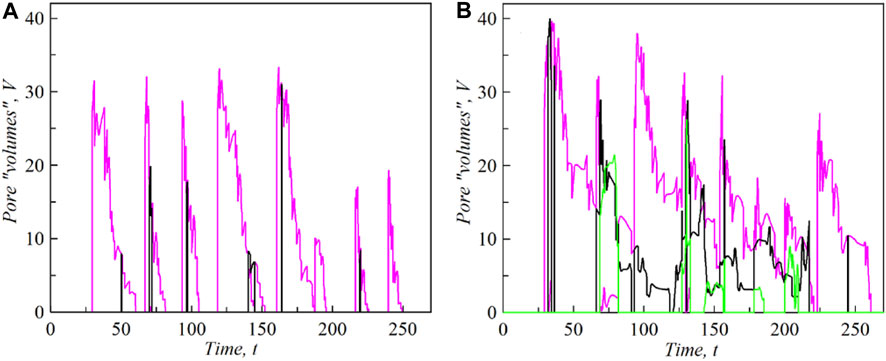
Figure 4. Time dependencies of the volumes of the pores
Moreover, if the vertical velocity is not too high, some of the pores survive through the support of the air inside when the sphere starts to move out of the surface. They exist for a while inside the adhesive “bridge,” which connects the elastic foundation to the gradually receding sphere. To demonstrate this, we specially removed the sphere slowly at the rate of
4 Conclusion
This work presents an experiment on elastic wave propagation in adhesive contacts. Initially, the adhesive strength was increased via surface chemical treatment of the indenter. However, contamination reduced the adhesive strength over time, altering the friction mode visibly. Wrinkles formed during the initial sliding but ceased over time due to the diminished influence of adhesion. This highlights the absence of a universal adhesive friction mode, necessitating unique theoretical models for specific cases. The present study proposes a model detailing wrinkle formation and propagation under shear stress. We provide valuable insights to researchers on adhesive friction by showing the lack of a universal behavior in adhesive contacts despite existing studies aimed at establishing such behaviors.
Data availability statement
The original contributions presented in the study are included in the article/Supplementary Material, and any further inquiries may be directed to the corresponding author.
Author contributions
IL: Formal analysis, Investigation, Methodology, Software, Validation, Visualization, Writing–original draft. AF: Formal analysis, Investigation, Methodology, Software, Validation, Visualization, Writing–original draft. VP: Conceptualization, Funding acquisition, Project administration, Supervision, Writing–review and editing.
Funding
The authors declare that financial support was received for the research, authorship, and/or publication of this article. The authors acknowledge financial support from the Deutsche Forschungsgemeinschaft (DFG PO 810/55-3).
Conflict of interest
The authors declare that the research was conducted in the absence of any commercial or financial relationships that could be construed as a potential conflict of interest.
The author(s) declare that they were an editorial board member of Frontiers at the time of submission. This had no impact on the peer review process and final decision.
The reviewer QL declared a shared affiliation with the author(s) to the handling editor at the time of review.
Publisher’s note
All claims expressed in this article are solely those of the authors and do not necessarily represent those of their affiliated organizations or those of the publisher, editors, and reviewers. Any product that may be evaluated in this article or claim that may be made by its manufacturer is not guaranteed or endorsed by the publisher.
Supplementary material
The Supplementary Material for this article can be found online at: https://www.frontiersin.org/articles/10.3389/fmech.2024.1400366/full#supplementary-material
SUPPLEMENTARY VIDEO S1 | Video of the experiment (see description in the text of the article).
SUPPLEMENTARY VIDEO S2 | Video of the simulation results (see description in the text of the article).
References
Berardo, A., Costagliola, G., Ghio, S., Boscardin, M., Bosia, F., and Pugno, N. M. (2019). An experimental-numerical study of the adhesive static and dynamic friction of micro-patterned soft polymer surfaces. Mater. Des. 181, 107930. doi:10.1016/j.matdes.2019.107930
Brörmann, K., Barel, I., Urbakh, M., and Bennewitz, R. (2013). Friction on a microstructured elastomer surface. Tribol. Lett. 50, 3–15. doi:10.1007/s11249-012-0044-3
Carbone, G., Mandriota, C., and Menga, N. (2022). Theory of viscoelastic adhesion and friction. Extreme Mech. Lett. 56, 101877. doi:10.1016/j.eml.2022.101877
Carpick, R. W., and Salmeron, M. (1997). Scratching the surface: fundamental investigations of tribology with atomic force microscopy. Chem. Rev. 97 (4), 1163–1194. doi:10.1021/cr960068q
Chernov, S. V., Makukha, Z. M., Protsenko, I. Y., Nepijko, S. A., Elmers, H. J., and Schönhense, G. (2014). Test object for emission electron microscope. Appl. Phys. A 114 (4), 1383–1385. doi:10.1007/s00339-013-8010-y
da Silva, L. F. M., Öchsner, A., and Adams, R. D. (2018). Handbook of adhesion technology (Cham: Springer). doi:10.1007/978-3-319-55411-2
Degrandi-Contraires, E., Poulard, C., Restagno, F., and Léger, L. (2012). Sliding friction at soft micropatterned elastomer interfaces. Faraday Discuss. 156, 255–265. doi:10.1039/C2FD00121G
Derjaguin, B. (1934). Molekulartheorie der äußeren Reibung. Z. Phys. 88, 661–675. doi:10.1007/BF01333114
Filippov, A. E., Nadein, K., Gorb, S. N., and Kovalev, A. (2024a). Bio-bearings: numerical model of the solid lubricant in the leg joints of insects. Tribol. Lett. 72 (1), 11. doi:10.1007/s11249-023-01815-3
Filippov, A. E., Nadein, K., Gorb, S. N., and Kovalev, A. (2024b). Large-scale numerical simulation of the solid lubricant behavior in the leg joints of insects. Adv. Theory Simul. 7, 2301236. doi:10.1002/adts.202301236
Ge, L., and Chen, S. (2020). Recent advances in tissue adhesives for clinical medicine. Polymers 12, 939. doi:10.3390/polym12040939
Gorb, S. N., Koch, K., and Heepe, L. (2019). Biological and biomimetic surfaces: adhesion, friction and wetting phenomena. Beilstein J. Nanotechnol. 10, 481–482. doi:10.3762/bjnano.10.48
Hertz, H. (1881). Ueber die Berührung fester elastischer Körper. für reine Angew. Math. 92, 156–171. doi:10.1515/9783112342404-004
Khudoynazarov, K. (2024). Longitudinal-radial vibrations of a viscoelastic cylindrical three-layer structure. Facta Univ. Ser. Mech. Eng. doi:10.22190/FUME231219010K
Koudine, A. A., Lambert, M., and Barquins, M. (1997). Some new experimental results on the Schallamach waves propagation by space-time analysis. Int. J. Adhes. Adhes. 17, 359–363. doi:10.1016/S0143-7496(97)00036-5
Liu, Y., Wang, H., Li, J., Li, P., and Li, S. (2024). Gecko-inspired controllable adhesive: structure, fabrication, and application. Biomimetics 9, 149. doi:10.3390/biomimetics9030149
Lyashenko, I. A., Filippov, A. E., and Popov, V. L. (2023). Friction in adhesive contacts: experiment and simulation. Machines 11, 583. doi:10.3390/machines11060583
Lyashenko, I. A., Khomenko, A. V., and Metlov, L. S. (2011). Nonlinear thermodynamic model of boundary friction. J. Frict. Wear 32, 113–123. doi:10.3103/S1068366611020061
Lyashenko, I. A., and Liashenko, Z. M. (2020). Influence of tangential displacement on the adhesion force between gradient materials. Ukr. J. Phys. 65 (3), 205–216. doi:10.15407/ujpe65.3.205
Lyashenko, I. A., Pham, T. H., and Popov, V. L. (2024). Effect of indentation depth on friction coefficient in adhesive contacts: experiment and simulation. Biomimetics 9, 52. doi:10.3390/biomimetics9010052
Lyashenko, I. A., and Popov, V. L. (2021). Hysteresis in an adhesive contact upon a change in the indenter direction of motion: an experiment and phenomenological model. Tech. Phys. 66, 611–629. doi:10.1134/S1063784221040113
Mergel, J. C., Scheibert, J., and Sauer, R. A. (2021). Contact with coupled adhesion and friction: computational framework, applications, and new insights. J. Mech. Phys. Solids. 146, 104194. doi:10.1016/j.jmps.2020.104194
Papangelo, A., and Ciavarella, M. (2023). Detachment of a rigid flat punch from a viscoelastic material. Tribol. Lett. 71, 48. doi:10.1007/s11249-023-01720-9
Phiri, R., Rangappa, S. M., Siengchin, S., and Marinkovic, D. (2023). Agro-waste natural fiber sample preparation techniques for bio-composites development: methodological insights. Facta Univ. Ser. Mech. Eng. 21 (4), 631–656. doi:10.22190/FUME230905046P
Rand, C. J., and Crosby, A. J. (2006). Insight into the periodicity of Schallamach waves in soft material friction. Appl. Phys. Lett. 89 (26), 261907. doi:10.1063/1.2408640
Sahli, R., Pallares, G., Ducottet, C., Ben Ali, I. E., Al Akhrass, S., Guibert, M., et al. (2018). Evolution of real contact area under shear and the value of static friction of soft materials. Proc. Natl. Acad. Sci. U. S. A. 115 (3), 471–476. doi:10.1073/pnas.1706434115
Singh, K., and Gupta, S. (2022). Controlled actuation, adhesion, and stiffness in soft robots: a review. J. Intell. Robot. Syst. 106, 59. doi:10.1007/s10846-022-01754-6
Siniscalco, D., Pessoni, L., Boussonnière, A., Castanet, A.-S., Billon, L., Vignaud, G., et al. (2024). Design of an azopolymer for photo-switchable adhesive applications. Coatings 14, 275. doi:10.3390/coatings14030275
Stojanovic, B., and Ivanović, L. (2014). Tribomechanical systems in design. J. Balk. Tribol. 20 (1), 25–34.
van den Boogaart, L. M., Langowski, J. K. A., and Amador, G. J. (2022). Studying stickiness: methods, trade-offs, and perspectives in measuring reversible biological adhesion and friction. Biomimetics 7, 134. doi:10.3390/biomimetics7030134
Viswanathan, K., and Chandrasekar, S. (2022). Fifty years of Schallamach waves: from rubber friction to nanoscale fracture. Phil. Trans. R. Soc. A 380, 20210339. doi:10.1098/rsta.2021.0339
Viswanathan, K., Mahato, A., and Chandrasekar, S. (2015). Nucleation and propagation of solitary Schallamach waves. Phys. Rev. E 91 (1), 012408. doi:10.1103/PhysRevE.91.012408
Weston-Dawkes, W. P., Adibnazari, I., Hu, Y.-W., Everman, M., Gravish, N., and Tolley, M. T. (2021). Gas-lubricated vibration-based adhesion for robotics. Adv. Intel. Syst. 3 (7), 2100001. doi:10.1002/aisy.202100001
Yan, C., Chen, H. Y., Lai, P. Y., and Tong, P. (2023). Statistical laws of stick-slip friction at mesoscale. Nat. Commun. 14, 6221. doi:10.1038/s41467-023-41850-1
Yashima, S., Romero, V., Wandersman, E., Frétigny, C., Chaudhury, M. K., Chateauminois, A., et al. (2015). Normal contact and friction of rubber with model randomly rough surfaces. Soft Matter 11, 871–881. doi:10.1039/c4sm02346c
Zemljič-Jokhadar, Š., Kokot, G., Pavlin, M., and Derganc, J. (2021). Adhesion and stiffness of detached breast cancer cells in vitro: Co-treatment with metformin and 2-Deoxy-d-glucose induces changes related to increased metastatic potential. Biology 10, 873. doi:10.3390/biology10090873
Keywords: adhesion, friction, shear stress, contact area, elastomer, Schallamach waves
Citation: Lyashenko IA, Filippov AE and Popov VL (2024) Propagation of elastic waves in adhesive contacts: experiment and numerical model. Front. Mech. Eng 10:1400366. doi: 10.3389/fmech.2024.1400366
Received: 13 March 2024; Accepted: 18 June 2024;
Published: 12 August 2024.
Edited by:
Noshir Sheriar Pesika, Tulane University, United StatesReviewed by:
Qiang Li, Technical University of Berlin, GermanyMilan Bukvic, University of Kragujevac, Serbia
Varvara Romanova, Institute of Strength Physics and Materials Science (ISPMS SB RAS), Russia
Copyright © 2024 Lyashenko, Filippov and Popov. This is an open-access article distributed under the terms of the Creative Commons Attribution License (CC BY). The use, distribution or reproduction in other forums is permitted, provided the original author(s) and the copyright owner(s) are credited and that the original publication in this journal is cited, in accordance with accepted academic practice. No use, distribution or reproduction is permitted which does not comply with these terms.
*Correspondence: Iakov A. Lyashenko, aS5saWFzaGVua29AdHUtYmVybGluLmRl