- 1Department of Mechanical Engineering, Jeddah King Abdelaziz University, Jeddah, Saudi Arabia
- 2Institute of Graduate Studies and Research, Alexandria University, Alexandria, Egypt
The purpose of this study is to experimentally enhance the heat exchange rate of the shell and helical coil tube heat exchanger by mixing water with aluminum oxide (Al2O3) nanoparticles, as well as to explore the effect of inlet thermal parameters on the performance of the heat exchanger. A test rig was constructed to investigate the influence of particle concentration, and inlet temperatures on the performance of nano-fluid. Parameters such as Nusselt number, pressure drop, performance evaluation criteria (PEC) are considered to rate the performance of the nano-particle with the heat exchanger. In this study a wider range of particle concentration is considered, which varies from 0.0%–0.75%. Experiments with and without nanoparticles are carried out under identical working conditions. By analyzing the experimental data, it was found that nanoparticles significantly improve the coefficient of heat transfer inside the helically coiled tube. From sensitivity analysis, it is obseerved that there is a slight decrease in Nusselt number of the nano-fluid with increase in inlet temperatures of the nano-fluid and the cooling water. Furthermore, it is concluded that an 8.5% increase in PEC value is observed with increase in particle concentration from 0.15% to 0.75%.
1 Introduction
Heat exchangers are implemented in many engineering applications such as nuclear power plants, aerospace industries, air conditioning systems, chemical plants, oil refineries, refrigeration systems, power systems (Azadi et al., 2023; Carvajal-Mariscal et al., 2023; Khargotra et al., 2023; Maithani et al., 2023; Kumar A. P. et al., 2024; Luo et al., 2024; Moghadam et al., 2024). The design, application, space constraints, and fluid flow patterns in such applications influence the shape and size of heat exchangers, which are devices that transport or exchange heat between two fluids without mixing them. Every heat exchanger has a barrier that keeps the fluids apart while still enabling heat transmission. Hydraulic and thermal performance of heat exchangers have been upgraded in the last decades (Huminic and Huminic, 2016; Salilih and Abu-Hamdeh, 2021; Abu-Hamdeh and Salilih, 2022; Asiri et al., 2022; Salilih et al., 2023). Shell and helically coiled heat exchangers exceed the conventional heat exchangers for high temperature applications and outperform straight tube heat exchangers with regard to heat transfer coefficient (Prabhanjan et al., 2002). The flowing of the heat transfer fluid in a coiled tube results a centrifugal force in comparison to a straight tube, resulting in an eddy flow that augments heat transfer capabilities while also raising a drop in pressure (Dravid et al., 1971; Alimoradi and Veysi, 2016).
Traditional liquids like water and air have weak thermal conductivity, which restricts the rate of heat transfer. Nano-fluids are the new generation state of the art heat transfer fluids for heat exchangers, which have engrossed considerable attention in various research as a result of their reported high effectiveness in various heat transfer applications (Abu-Hamdeh et al., 2021a; Alsaady, 2021; Awais et al., 2021; Anggono et al., 2023; Kumar et al., 2023; Liu et al., 2023; Kumar A. et al., 2024; Rana et al., 2024). Dispersing nanoparticles across standard heat transfer liquids can increase the thermal conductivity of the working fluids without significantly altering their chemical and physical properties, which increases the rate of heat transfer. As a result, the heat transfer coefficient of the heat transfer fluids has risen significantly due to the implementation of nano-fluids rather than pure fluid in heat exchanger tubes, although there has been a moderate pressure drop (Hashim et al., 2019; Alazwari et al., 2021; Ghazanfari et al., 2023). The viscosity of the solution increases along with the volume percentages of nanoparticles. Using nano-fluids causes a greater pressure drop, and correspondingly higher energy input (Saidur et al., 2011; Kumar and Chandrasekar, 2020). To get high heat conductivity while keeping low viscosity, a number of research investigations have been done to explore the thermos-physical properties of nano-fluids (Das et al., 2007; Fsadni et al., 2018).
Numerous studies have shown that steady wall heat flux and steady wall heat increased because of the use of nano-fluids inside the coil tube (Tohidi et al., 2015). Palanisamy and Kumar (2019) investigated the pressure loss and heat transfer properties in a cone helically coiled tube subjected to turbulent flow with MWCNT/water nano-fluid at particle concentrations of 0.5, 0.3, and 0.1 percent. The studies’ findings demonstrated that water has a 0.5 total heat transfer coefficient, which is 52% lower than that of nano-fluids. At 0.5 percent, 0.3 percent, and 0.1 percent the heat transfer coefficient was increased above water by 41%, 30%, and 14%, respectively, in the case of employing a MWCNT/water nano-fluid. When MWCNT/water nano-fluids at concentrations of 0.5%, 0.3%, and 0.1% were compared to water, the Nusselt values rose to 68, 52, and 28 percent, respectively. According to reports, pressure drops in nano-fluids of 0.1%, 0.3%, and 0.5% are 16%, 30%, and 42% bigger than water, when using SiO2/water nano-fluids. Niwalkar et al. (2019) examined the increase in coefficient of heat transfer in a helically tube. The results of the experiment show that pressure drop, friction factor and the heat transfer coefficient of the nano-fluid increase with increasing mass flow rates and particle volume concentrations. In comparison to other concentrations (0.05, 0.1, 0.15, and 0.2 percent), 0.25 percent was shown to have the highest heat transfer coefficient due to its high viscosity. SiO2/water nano-fluids have larger heat transfer coefficients, pressure drops, and friction factors than demineralized water by 28.71%, 62.60%, and 52.61%, respectively. Peng et al. (2007) investigated the factors affecting the stability of nano-fluids. The test results showed that concentration, dispersant, base liquid viscosity, and nanoparticle Ph value were the key factors influencing the stability of suspensions. Additionally, the diameter, nanoparticle density, and ultrasonic vibration all have an impact on the stability of nano-fluids. Srinivas and Vinod (2016) used Al2O3, CuO, and TiO2 to evaluate the effectiveness of a disturbed shell and helical coil heat exchanger. Numerous coil-side fluid flow rates, stirring rates, temperatures and nano-fluid concentration were utilized in the experimentation. It was revealed that raising the nano-fluid concentration increased the rate of heat transfer. The efficiency of the heat exchange was also improved by increasing fluid temperature in the shell side and the concentration of the nano-fluids. By employing nano-fluids in a laminar flow environment, G. Huminic and Huminic (2011) performed numerical analysis and examined the heat transfer characteristics of a shell and helical coil heat exchanger. As particle volume concentrations increase, the temperature of the chilly fluid rises, improving its ability to absorb heat. Wu et al. (2013) investigated a shell and helical coil tube heat exchanger. The Al2O3-water nanofluid’s pressure drops and convection heat transfer properties were the focus of the inquiry. Since the thermal characteristics of the nanoparticles have the greatest influence on convective heat transmission, Al2O3-water nanoparticles can be viewed as a homogeneous solution. Farajollahi et al. (2010) found a different enhancement in heat transfer of a heat exchanger when two different nano-fluids are employed, the authors specifically considered TiO2- and Al2O3-water nanoparticles to carry out certain tasks. There has been an improvement for both nano-fluids at low and high concentration. The rivalry between the two types of nano-materials for conductivity and particle size may be the origin of these discrepancies in thermophysical characteristics. Kumar et al. (2013) used a variable percentage of Al2O3/water nano-fluid to study the frictional factor and the heat transmition of the shell and helical coil tube heat exchangers in a laminar stream environment. The better heat transfer coefficient is resulted due to the higher conductivity of nanoparticles and the randomized motion of the particles. Additionally, the viscosity of nano-fluids surges along with the increase in nanoparticle concentration, increasing the friction factor. Finally, the current part has attempted to offer insight into the older work that has been produced on this topic. From the aforementioned, it is clear that the researchers used both coil and tube and shell and tube heat exchangers in their research analyse the nano-fluids. Maghrabie et al. (2021) performed experimental investigation on shell and helically coiled heat exchanger with Al2O3 and SiO2 based nano-fluid for particle concentration of 0.1%, 0.2%, and 0.3%. The study is also carried out for different inclination angle of the heat exchanger, which is 0 o, 30 o, 60 o, and 90 o. Thermo-hydraulic performance of the nano-fluid was investigated and discussed in the paper. It was found that increasing the angle of inclination enhances the thermal performance of the heat exchanger. Elsaid et al. (2023) performed experimental and numerical study on shell and helically coiled heat exchanger with Al2O3, TiO2, MgO based nano-fluid. The study is carried out for different inclination of the heat exchanger as well for different cross sectional geometry of the tube.
Computational and experimental investigations on heat transfer aspects of nano-fluid have been considered in early studies in the shell and helical coil tube heat exchanger. However, the effect of inlet temperatures of the working fluids on heat transfer performance of the nano-fluids due to the change in physical property of the nano-fluids were not consider in researches. In this study, sensitivity analysis on thermal performance of Al2O3 nano-fluid is carried out to investigate the effect of the inlet temperature of the nano-fluid to the coil and the inlet temperature of the cooling water to the shell side, both on thermal performance of the nano-fluid. Furthermore, the experimental study is carried out for wider range of particle volume of concentration of the nano-fluid which ranges from 0.0% to 0.75%. As a result, this study has significance in understanding the property of the nano-fluid in a wider particle volume concentration, which can provide valuable insights for the scientific community. The findings of this research have the potential to benefit various industries and applications that rely on efficient heat transfer processes.
2 Experimental setup and data analysis
To perform the experiment, helical coil made of copper tube and heat exchanger’s shell pipe made of a thermoplastic material were constructed using materials from a local vendor. The nano-fluids materials are mixed with hot water in the hot water tank and flow inside the helical tube. The temperature of hot water at inlet range between (65–75oC). The cold water will be in the shell with temperature between (20–30oC), while it is mass flow rate is at 0.2 kg s-1. Figure 1 shows the experimental setup.
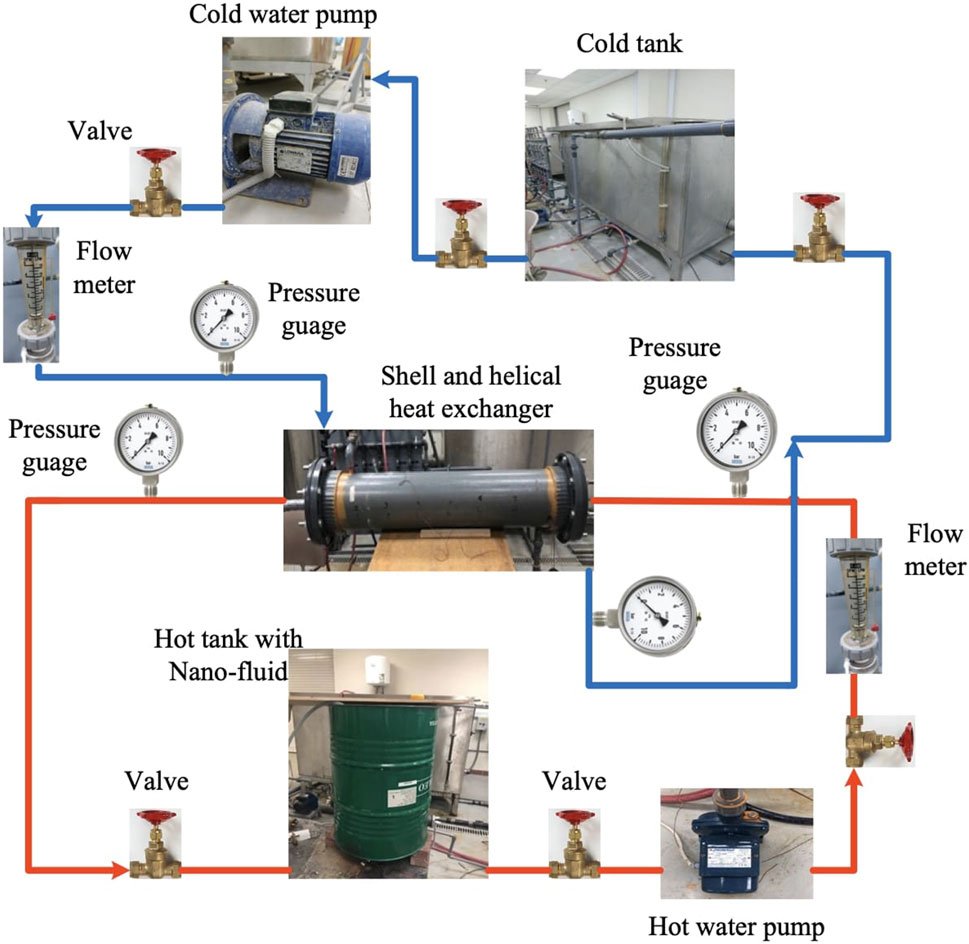
Figure 1. Schematic illustration of the experiment setup (Shabi et al., 2023).
Experiments are carried out with tap hot and cold water without nanoparticles; after recording the data, Different particle concentrations of nano-fluid (0.15%–0.75%) has been prepared by adding nano-particle to the hot water tank and mixing it properly, then experiments are performed again to record the required date. Finally, data from all experiments are analyzed and matched to show the impact of adding nanoparticles in enhancing heat transmission. Figure 2 depicts the geometry of the considered shell and helically coiled tube heat exchanger. The dimensional parameters of the heat exchanger, such as the internal and external diameters of the tube and the shell, are presented.
2.1 Physical property of the nano-fluid
Al2O3 nanomaterial was set up by diffusing its nanoparticles in 15 L of filtered water at different particle concentrations ranging from 0.15% to 0.75% with a 0.15% step. The Sodium dodecyl benzoic sulfate (SDBS) surfactant is added and dynamically stirred. Afterward, the appropriate Al2O3 nanoparticles quantity was added and stirred for around 4 h.
Particle volume concentration (
Where
The properties of Al2O3 nanoparticles are calculated utilizing the formulas for specific. heat (
Where the subscripts
The theoretic model for calculating the solid-liquid mixtures thermal conductivity is given as (Elsaid et al., 2023).
The nanoparticles materials with the percentage listed in Table 1 are mixed with hot water.
2.2 Data reduction and heat exchanger parameter
For the analysis, the parameters which are considered include the thermal conductivity of the tube, nanoparticle concentrations, inlet and outlet temperatures for the coil and the shell side, and the mass flow rate of the nanoparticle solution (i.e., Reynolds number of the nano-fluid). Furthermore, dimensions and thermal conductivity for shell and helically coiled heat exchanger are listed in Table 2 below.
Moreover, the thermo-physical characteristics of water and nano-particles have also been included. Following the experimental operation and data collecting, the nano-fluids’ rate of heat transfer in the internal tube can be calculated using the relations.
Then for the cold fluid (water), the heat transfer rate in the outer tube will be estimated using:
Afterward, the average heat transfer will be calculated by (Maghrabie et al., 2021):
Moreover, for the multiplication of the overall heat transfer coefficient (
Where the logarithmic mean temperature difference (
For estimating the total heat transfer coefficient, the equation used is (Maghrabie et al., 2021):
Where the heat exchanger area (
To compute the external convective coefficients (i.e.,
Where
The heat transfer coefficient of the shell side flow will also be computed from the Nusselt number as [49]:
Where
The Nusselt number of the nanofluid flowing in the coil tube can be given with (Abu-Hamdeh et al., 2021a; Abu-Hamdeh et al., 2021b; Milyani et al., 2022):
The performance evaluation criterion (PEC) of the nano-fluid in the helical coil can be given with the following equation (Attalla et al., 2016; Abdul Hamid et al., 2019):
Where
2.3 Experimental procedure
1- The cold and hot water tanks are filled.
2- The required volume of the nanoparticles is measured for the volume of hot water in the tank.
3- The measured nanoparticle is poured in the hot water tank and mixed with the water.
4- The mixture in the hot water tank is heated with a fire stove till it reaches the needed temperature.
5- The cold and hot water flow speeds are adjusted by using the flowmeter.
6- The experiment is started after the temperature of the mixture in the hot tank gets the desired value.
7- The first step of the experiment is started by opening the valves the working fluids streams into the heat exchanger.
8- In parallel with opening the water valves, the motors are turned on.
9- The testing is kept operating for 20–25 min.
10- The motor is turned off after the time is up.
11- The valves are shut off.
12- The readings is kept and saved.
Repeat from point 2 to point 13 till the end of the tests for the desired percentages of the nanomaterials.
Table 3 presents the uncertainty of the experimental measurements due to replication of the experiment.
3 Result and discussion
Figure 3 displays the effects of nanofluid concentration and the Reynolds number on the average Nusselt number with mass flow rate of 0.2 kg/s cooling water at the shell side and for different inlet temperatures of the hot nano-fluid, which are 65°C, 70°C, and 75°C; while the temperature of the cooling water kept at the value of 20°C. The nano-fluid mix has a considerable consequence on the average Nusselt-number; raising the particle concentration tended to increase the Nusselt-number meaningfully. The increase in average Nusselt number of the hot water in the coil increases by around 17.8% due to addition of 0.75% Al2O3 nano-particle.
Furthermore, as the inlet temperature of the nano-fluid (
Figure 4 shows the effect of particle concentration to drop in pressure of the nano-fluid. The figures shows the drop in pressure for 70°C entrance temperature of the nano-fluid, and 25°C inlet temperature of the cold water at the shell side. The particle concentration is varied from 0% to 0.75%. The flow rate of the cooling water kept at 0.2 kg s-1, while flow rate of the nano-fluid increased from 0.041 kg s-1 to 0.0825 kg s-1. Generally, there is a slight increase in drop in pressure due to increase in particle concentration for all considered flow rate of the nano-fluid. Up to 1.5% increase in drop in pressure is observed due to increase in nano particle concentration. However, the pressure drop of the nano-fluid with rise in flow rate is significant.
Figure 5 shows the effect of particle concentration to friction factor of the nano-fluid. The figures shows the friction factor for 70°C entrance temperature of the nano-fluid, and 25°C inlet temperature of the cold water at the shell side. The particle concentration is varied from 0% to 0.75%. The flow rate of the cooling water kept at 0.2 kg s-1, while flow rate of the nano-fluid increased from 0.041 kg s-1 to 0.0617 kg s-1. Similarly, there is a slight increase in friction factor due to increase in particle concentration for all considered flow rate of the nano-fluid. However, in the contrary the friction factor of the nano-fluid decreases with increase in its mass flow rate. The friction factor decreases from 0.0133 to 0.0096, for 0.041–0.0617 kg s-1 increase in mass flow rate of the nano-fluid.
Figure 6 shows the effects of nanofluid concentration and the Reynolds number on the performance evaluation criteria of the nano-fluid (PEC). The presented result is for 0.2 kg/s mass flow rate and 25°C entrance temperature of the cold water at shell side, and 70°C inlet temperature of the nano-fluid,. Overall, the PEC value of the nano-fluid is increased with increase in concentration of the nano-particle. The PEC value for 0.15% concentration is around 1.06, while the value increased to 1.15 for 0.75% concentration of the nano-fluid, which is an 8.5% increase in PEC. However, the change in the PEC value of the nano-fluid with change in its Reynold number is insignificant.
Figure 7 presents a comparison of this work against Dittus–Boelter data. The Dittus–Boelter data represent the Nusselt number’s relation with the Reynolds number of pure water in a straight tube. The comparison shows that the results of this study are close to the Dittus–Boelter data. Although the Dittus–Boelter data represent the relationship between the Nusselt number and the Reynolds number of pure water in a straight tube, it can be used to compare experimental results of flow in a helically coiled tube in many literature sources (Hardik et al., 2015).
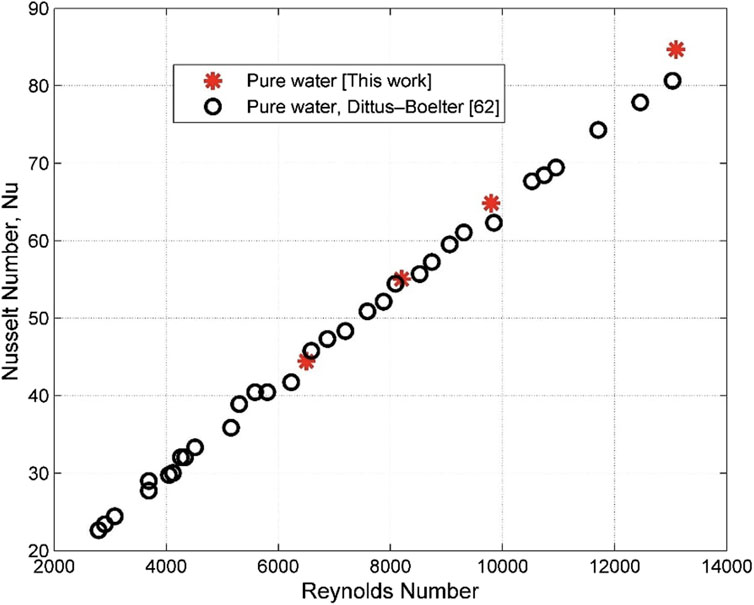
Figure 7. Reynolds number versus average Nusselt number comparison of this work with Dittus-Boelter data.
4 Conclusion
In this study a coil and shell type heat exchanger is tested in a laboratory. Our experimental data clearly demonstrate that the presence of Al2O3 nanoparticles greatly enhances the coefficient for the heat transfer inside the coil tube. The increase in flow rate of the nano-fluid inside the tube (measured by Reynolds number) increases its heat transmission performance (which is measured by Nusslet number). Furthermore, our data also reveal that the increase in mass flow rate of the nano-fluid rises its pressure drop in the tube. The following conclusions can be considered from this study:
• The average Nusselt number of the hot water in the coil is increased by around 17.8% due to addition of 0.75% Al2O3 nano-particle.
• As the inlet temperature of the nano-fluid increases, its Nusselt number of nano-fluid drops slightly due to change in its physical property.
• As the inlet temperature of the cooling water increases, its Nusselt number of the nan-fluid drops slightly due to change in physical property of the nano-fluid in the coil.
• The PEC value of the nano-fluid increases with increase in particle concentration of the nano-fluid. An 8.5% increase in PEC value is observed with increase in particle concentration from 0.15% to 0.75%.
Data availability statement
The raw data supporting the conclusion of this article will be made available by the authors, without undue reservation.
Author contributions
OS: Conceptualization, Data curation, Methodology, Resources, Software, Writing–original draft, Writing–review and editing. MA: Supervision, Writing–original draft, Writing–review and editing. El-N: Investigation, Supervision, Writing–original draft, Writing–review and editing. KE: Writing–original draft, Writing–review and editing.
Funding
The author(s) declare that no financial support was received for the research, authorship, and/or publication of this article.
Acknowledgments
We would like to express our gratitude to Engineer Osama Ahmed Elzoghaly, Head of the Tests and Projects Sector, Ministry of Electricity and Energy, Egypt, for his specific contribution in this research.
Conflict of interest
The authors declare that the research was conducted in the absence of any commercial or financial relationships that could be construed as a potential conflict of interest.
Publisher’s note
All claims expressed in this article are solely those of the authors and do not necessarily represent those of their affiliated organizations, or those of the publisher, the editors and the reviewers. Any product that may be evaluated in this article, or claim that may be made by its manufacturer, is not guaranteed or endorsed by the publisher.
References
Abdul Hamid, K., Azmi, W. H., Mamat, R., and Sharma, K. V. (2019). Heat transfer performance of TiO2–SiO2 nanofluids in a tube with wire coil inserts. Appl. Therm. Eng. 152, 275–286. doi:10.1016/j.applthermaleng.2019.02.083
Abu-Hamdeh, N. H., Alazwari, M. A., Salilih, E. M., Sajadi, S. M., and Hatamleh, R. I. (2021a). Efficiency enhancement of a solar collector by examine Graphene-Silica/water mixture: a comprehensive study based on the empirical/numerical results. Sustain. Energy Technol. Assessments 48, 101604. doi:10.1016/j.seta.2021.101604
Abu-Hamdeh, N. H., Alsulami, R. A., Aljinaidi, A. A., Alazwari, M. A., Eltaher, M. A., Almitani, K. H., et al. (2021b). Numerical investigation of molten salt/SiO2 nano-fluid in the solar power plant cycle and examining different arrangements of shell and tube heat exchangers and plate heat exchangers in these cycles. J. Taiwan Inst. Chem. Eng. 124, 1–8. doi:10.1016/j.jtice.2021.05.018
Abu-Hamdeh, N. H., and Salilih, E. M. (2022). A case study in the field of sustainability energy: transient heat transfer analysis of an ice thermal storage system with boiling heat transfer process for air-conditioning application. Energy Rep. 8, 1034–1045. doi:10.1016/j.egyr.2021.12.036
Alazwari, M. A., Abu-Hamdeh, N. H., and Salilih, E. M. (2021). Exergetic performance analysis on helically coiled tube heat exchanger-forecasting thermal conductivity of SiO2/EG nanofluid using ANN and RSM to examine effectiveness of using nanofluids. J. Therm. Anal. Calorim. 144, 2721–2733. doi:10.1007/s10973-021-10644-2
Alimoradi, A., and Veysi, F. (2016). Prediction of heat transfer coefficients of shell and coiled tube heat exchangers using numerical method and experimental validation. Int. J. Therm. Sci. 107, 196–208. doi:10.1016/j.ijthermalsci.2016.04.010
Alsaady, M. (2021). Modeling and multi-objective optimization of thermophysical parameters of hybrid nanodiamond–Ni-based nanofluids via response surface methodology. Front. Mech. Eng. 7, 675511. doi:10.3389/fmech.2021.675511
Anggono, A. D., Riswanto, D., Ismoen, M., Masyrukan, A. H., Hariyanto, A., and Sedyono, J. (2023). Effect of flow rate and CNM concentration in nanofluid on the performance of convective heat transfer coefficient. Front. Mech. Eng. (Web) 9, 1174185. doi:10.3389/fmech.2023.1174185
Asiri, S. A., Salilih, E. M., Alfawaz, K. M., Alogla, A. F., Sajadi, S. M., and Nusier, O. K. (2022). Heat transfer analysis of a water/lithium-bromide vapor generator system used for battery thermal development. J. Energy Storage 53, 105118. doi:10.1016/j.est.2022.105118
Attalla, M., Maghrabie, H. M., and Specht, E. (2016). An experimental investigation on fluid flow and heat transfer of rough mini-channel with rectangular cross section. Exp. Therm. Fluid Sci. 75, 199–210. doi:10.1016/j.expthermflusci.2016.01.019
Awais, M., Bhuiyan, A. A., Salehin, S., Ehsan, M. M., Khan, B., and Rahman, M. H. (2021). Synthesis, heat transport mechanisms and thermophysical properties of nanofluids: a critical overview. Int. J. Thermofluids 10, 100086. doi:10.1016/j.ijft.2021.100086
Azadi, S., Abjadi, A., Vahdat Azad, A., Ahmadi Danesh Ashtiani, H., and Afshar, H. (2023). Enhancement of heat transfer in heat sink under the effect of a magnetic field and an impingement jet. Front. Mech. Eng. 9, 1266729. doi:10.3389/fmech.2023.1266729
Carvajal-Mariscal, I., León-Ruiz, D., Belman-Flores, J. M., Martínez-Espinosa, E., and José-Pineda, O. (2023). Experimental assessment and semi empirical estimation of frost accretion—a case study on a spine-finned inverted-V tube array evaporator. Front. Mech. Eng. 9, 1101425. doi:10.3389/fmech.2023.1101425
Das, S. K., Choi, S. U., Yu, W., and Pradeep, A. T. (2007). Nanofluids: science and technology. John Wiley & Sons.
Dravid, A. N., Smith, K. A., Merrill, E. W., and Brain, P. L. T. (1971). Effect of secondary fluid motion on laminar flow heat transfer in helically coiled tubes. AICHE J. 17 (5), 1114–1122. doi:10.1002/aic.690170517
Elsaid, A. M., Ammar, M., Lashin, A., and Assassa, G. M. R. (2023). Performance characteristics of shell and helically coiled tube heat exchanger under different tube cross-sections, inclination angles and nanofluids. Case Stud. Therm. Eng. 49, 103239. doi:10.1016/j.csite.2023.103239
Farajollahi, B., Etemad, S. G., and Hojjat, M. (2010). Heat transfer of nanofluids in a shell and tube heat exchanger. Int. J. Heat. Mass Transf. 53 (1–3), 12–17. doi:10.1016/j.ijheatmasstransfer.2009.10.019
Fsadni, A. M., Whitty, J. P. M., Adeniyi, A. A., Simo, J., and Brooks, H. L. (2018). “A review on the application of nanofluids in coiled tube heat exchangers,” in Micro and nanomanufacturing volume ii (Springer), 443–465.
Ghazanfari, V., Imani, M., Shadman, M. M., Amini, Y., and Zahakifar, F. (2023). Numerical study on the thermal performance of the shell and tube heat exchanger using twisted tubes and Al2O3 nanoparticles. Prog. Nucl. Energy 155, 104526. doi:10.1016/j.pnucene.2022.104526
Hardik, B. K., Baburajan, P. K., and Prabhu, S. V. (2015). Local heat transfer coefficient in helical coils with single phase flow. Int. J. Heat Mass Transf. 89, 522–538. doi:10.1016/j.ijheatmasstransfer.2015.05.069
Hashim, W. M., Hoshi, H. A., and Al-Salihi, H. A. (2019). Enhancement the performance of swirl heat exchanger by using vortices and NanoAluminume. Heliyon 5 (8), e02268. doi:10.1016/j.heliyon.2019.e02268
Huminic, G., and Huminic, A. (2011). Heat transfer characteristics in double tube helical heat exchangers using nanofluids. Int. J. Heat. Mass Transf. 54 (19–20), 4280–4287. doi:10.1016/j.ijheatmasstransfer.2011.05.017
Huminic, G., and Huminic, A. (2016). Heat transfer and flow characteristics of conventional fluids and nanofluids in curved tubes: a review. Renew. Sustain. Energy Rev. 58, 1327–1347. doi:10.1016/j.rser.2015.12.230
Incropera, F., DeWitt, D., Bergman, T., and Lavine, A. (2007). Fundamental of heat and mass transfer. sixth ed. New York: John Wiley & Sons.
Khargotra, R., Kumar, R., Nadda, R., Dhingra, S., Alam, T., Dobrota, D., et al. (2023). A review of different twisted tape configurations used in heat exchanger and their impact on thermal performance of the system. Heliyon 9 (6), e16390. doi:10.1016/j.heliyon.2023.e16390
Kumar, A., Ali, M. A., Maithani, R., Gupta, N. K., Sharma, S., Kumar, S., et al. (2023). Experimental analysis of heat exchanger using perforated conical rings, twisted tape inserts and CuO/H2O nanofluids. Case Stud. Therm. Eng. 49, 103255. doi:10.1016/j.csite.2023.103255
Kumar, A., Kunwer, R., Donga, R. K., Kumar, S., Alam, T., Siddiqui, M. I. H., et al. (2024b). Effect of oval rib parameters on heat transfer enhancement of TiO2/water nanofluid flow through parabolic trough collector. Case Stud. Therm. Eng. 55, 104080. doi:10.1016/j.csite.2024.104080
Kumar, A. P., Kumar, S., Maithani, R., Sharma, S., Alam, T., Haque Siddiqui, M. I., et al. (2024a). Influence of 45oV-type with collective ring turbulence promoters parameters of thermal performance of flat plate heat collector. Case Stud. Therm. Eng. 55, 104113. doi:10.1016/j.csite.2024.104113
Kumar, P. C. M., and Chandrasekar, M. (2020). A review on helically coiled tube heat exchanger using Nan-fluid. Mater. Today Proc. 21, 137–141. doi:10.1016/j.matpr.2019.04.199
Kumar, P. C. M., Kumar, J., and Suresh, S. (2013). Experimental investigation on convective heat transfer and friction factor in a helically coiled tube with Al 2 O 3/water nanofluid. J. Mech. Sci. Technol. 27 (1), 239–245. doi:10.1007/s12206-012-1206-9
Liu, S., Liu, Y., Gu, H., Tian, R., Huang, H., and Yu, T. (2023). Experimental study of the cooling performance of γ-Al2O3/heat transfer fluid nanofluid for power batteries. J. Energy Storage 72 (Part C), 108476–152X. doi:10.1016/j.est.2023.108476
Luo, J., Alghamdi, A., Aldawi, F., Moria, H., Mouldi, A., Loukil, H., et al. (2024). Thermal-frictional behavior of new special shape twisted tape and helical coiled wire turbulators in engine heat exchangers system. Case Stud. Therm. Eng. 53, 103877. doi:10.1016/j.csite.2023.103877
Maghrabie, H. M., Attalla, M., and Mohsen, A. A. A. (2021). Performance assessment of A shell and helically coiled tube heat exchanger with variable orientations utilizing different nanofluids. Appl. Therm. Eng. 182, 116013. doi:10.1016/j.applthermaleng.2020.116013
Maithani, R., Kumar, A., Ali, M. A., Gupta, N. K., Sharma, S., Alam, T., et al. (2023). Exergy and sustainability analysis of a solar heat collector with wavy delta winglets as turbulent promoters: a numerical analysis. Case Stud. Therm. Eng. 49, 103293. doi:10.1016/j.csite.2023.103293
Milyani, A. H., Salilih, E. M., Ajour, M. N., Alhumade, H. A., Abu-Hamdeh, N. H., and Karimipour, A. (2022). Increasing electricity generation—installing photovoltaic cells coupled to a battery pack, to provide the electricity. J. Energy Storage 54, 105264. doi:10.1016/j.est.2022.105264
Moghadam, F. N., Izadpanah, E., Shekari, Y., and Amini, Y. (2024). Experimental evaluation of shell geometry impact on thermal and exergy performance in helical coiled tube heat exchanger with phase change material. J. Energy Storage 83, 110790. doi:10.1016/j.est.2024.110790
Niwalkar, A. F., Kshirsagar, J. M., and Kulkarni, K. (2019). Experimental investigation of heat transfer enhancement in shell and helically coiled tube heat exchanger using SiO2/water nanofluids. Mater. Today Proc. 18, 947–962. doi:10.1016/j.matpr.2019.06.532
Palanisamy, K., and Kumar, P. C. M. (2019). Experimental investigation on convective heat transfer and pressure drop of cone helically coiled tube heat exchanger using carbon nanotubes/water nanofluids. Heliyon 5 (5), e01705. doi:10.1016/j.heliyon.2019.e01705
Peng, X., Yu, X., Xia, L., and Zhong, X. (2007). Influence factors on suspension stability of nanofluids. Journal-Zhejiang Univ. Eng. Sci. 41 (4), 577.
Prabhanjan, D. G., Raghavan, G. S. V., and Rennie, T. J. (2002). Comparison of heat transfer rates between a straight tube heat exchanger and a helically coiled heat exchanger. Int. Commun. Heat Mass Transf. 29 (2), 185–191. doi:10.1016/S0735-1933(02)00309-3
Rana, S., Zahid, H., Kumar, R., Bharj, R. S., Rathore, P. K. S., and Ali, H. M. (2024). Lithium-ion battery thermal management system using MWCNT-based nanofluid flowing through parallel distributed channels: an experimental investigation. J. Energy Storage 81, 110372. 2352-152X. doi:10.1016/j.est.2023.110372
Saidur, R., Leong, K. Y., and Mohammed, H. A. (2011). A review on applications and challenges of nanofluids. Renew. Sustain. Energy Rev. 15 (3), 1646–1668. doi:10.1016/j.rser.2010.11.035
Salilih, E. M., and Abu-Hamdeh, N. H. (2021). Charging process of thermal energy storage system under varying incident heat flux: interaction the fluid neighbour nodes and particles in order to heat transfer. J. Therm. Analysis Calorim. 144, 1588–2926. doi:10.1007/s10973-020-10539-8
Salilih, E. M., Khan, M. N., Bamaga, O., Ahmed, I., Albeirutty, M., Almatrafi, E., et al. (2023). Thermal analysis of integrated hydrate-based desalination system with intermediate fluid type LNG vaporizer. J. Clean. Prod. 420, 138405. doi:10.1016/j.jclepro.2023.138405
Salimpour, M. R. (2009). Heat transfer coefficients of shell and coiled tube heat exchangers. Exp. Therm. Fluid Sci. 33 (2), 203–207. doi:10.1016/j.expthermflusci.2008.07.015
Shabi, O. A., Alhazmy, M., and Negeed, E. R. (2023). Analysis of shell and helically coiled tube heat exchanger performance with TiO2 nanofluid. Int. J. Mech. Eng. 8 (4), 38–58. doi:10.56452/2023-04/004
Srinivas, T., and Vinod, A. V. (2016). Heat transfer intensification in a shell and helical coil heat exchanger using water-based nanofluids. Chem. Eng. Process. Process Intensif. 102, 1–8. doi:10.1016/j.cep.2016.01.005
Tohidi, A., Ghaffari, H., Nasibi, H., and Mujumdar, A. S. (2015). Heat transfer enhancement by combination of chaotic advection and nanofluids flow in helically coiled tube. Appl. Therm. Eng. 86, 91–105. doi:10.1016/j.applthermaleng.2015.04.043
Wu, Z., Wang, L., and Sundén, B. (2013). Pressure drop and convective heat transfer of water and nanofluids in a double-pipe helical heat exchanger. Appl. Therm. Eng. 60 (1–2), 266–274. doi:10.1016/j.applthermaleng.2013.06.051
Nomenclature
Keywords: heat exchanger, nano-fluids, performance evaluation criteria (PEC), pressure drop, heat transfer, Reynolds number
Citation: Shabi OA, Alhazmy M, Negeed E-SR and Elzoghaly KO (2024) Experimental investigation of shell and helical coiled heat exchanger with Al2O3 nano-fluid with wide range of particle concentration. Front. Mech. Eng 10:1386254. doi: 10.3389/fmech.2024.1386254
Received: 14 February 2024; Accepted: 09 April 2024;
Published: 29 April 2024.
Edited by:
Xj Jing, City University of Hong Kong, Hong Kong SAR, ChinaReviewed by:
Tabish Alam, Central Building Research Institute (CSIR), IndiaMuneer Ismael, University of Basrah, Iraq
Copyright © 2024 Shabi, Alhazmy, Negeed and Elzoghaly. This is an open-access article distributed under the terms of the Creative Commons Attribution License (CC BY). The use, distribution or reproduction in other forums is permitted, provided the original author(s) and the copyright owner(s) are credited and that the original publication in this journal is cited, in accordance with accepted academic practice. No use, distribution or reproduction is permitted which does not comply with these terms.
*Correspondence: Khaled O. Elzoghaly, ay5vc2FtYS5lbHpvZ2hhbHlAZ21haWwuY29t