- 1Department of Mechanical and Industrial Engineering, Manipal Institute of Technology, Manipal Academy of Higher Education, Manipal, India
- 2Department of Mechanical Engineering, Sri Sai Ram Institute of Technology, Chennai, India
- 3Department of Chemistry, Sri Sairam Engineering College, Chennai, India
- 4Department of Machining, Assembly and Engineering Metrology, Faculty of Mechanical Engineering, VSB-Technical University of Ostrava, Ostrava, Czechia
- 5Department of Mechanical Engineering, Sikkim Manipal Institute of Technology, Sikkim Manipal University, Gangtok, India
- 6Department of Physics, National Institute of Technology, Imphal, India
The present work shows the influence of deposition temperatures on the mechanical properties of silver (Ag)-doped diamond-like carbon (DLC) coating synthesized by the thermal chemical vapor deposition (CVD) technique. The deposited film showed excellent mechanical and tribological behavior with respect to the lower deposition temperatures. From the EDS analysis, it was confirmed that the percentage of Ag decreased from 9.8% to 8.4% as the deposition temperature increased. The nanoindentation tests at different loads were extensively carried out to observe the mechanical properties of the coating with respect to various deposition temperatures. The coating hardness (H) and Young’s modulus (E) decreased with the rise in furnace temperature, and the Hmax. and Emax. were observed as 29.71 and 251.19 GPa, respectively, for the Ag-DLC coating grown at 800°C at a load of 20 mN. In comparison to other Ag-DLC thin films made using different deposition techniques, the residual stress (σ) was significantly reduced, reaching 0.45 GPa, which is extremely low.
1 Introduction
DLC films possess both sp3-and sp2-bonded carbon and exhibit excellent mechanical, electrical, and optical properties. The applications of DLC coatings are widely spread in the biomedical sector due to their various biomedical properties, such as their hydrophobic, biocompatible, and functional surfaces and field emission properties. (Ţalu et al., 2019; Yang et al., 2020; Meng et al., 2023). However, it has been observed that this coating possesses poor thermal stability above 400°C, along with the presence of residual stress, which leads to poor adhesion to metal substrates and thus restricts its exposure to various domains. Earlier studies revealed that the presence of residual stress in DLC coatings can be reduced by doping various metals/non-metals or semiconductors without affecting the mechanical and tribological properties (Love et al., 2013). Over the past few years, Ag-doped DLC thin film coating has found major applications in many domains that are related to corrosion protection, wear, medicine, and optics (Jing et al., 2023). Wang et al. grew Ag-DLC coating over glass and 316L stainless steel substrates using the PVD (magnetron sputtering) technique and reported the crucial role of Ag segregation in the microstructure and chemical, mechanical, and biomedical properties of Ag-DLC films (Wang et al., 2018). Alloying of DLC thin film with metals such as Ag leads to improvement in coating toughness and improved adhesion due to the growth of soft crystals with enhanced ductility (Ţălu et al., 2020). Moreover, DLC thin film with Ag doping can reduce internal stresses and enhanced coating adhesion. (Jing et al., 2020). Wu et al. reported excellent tribological properties with higher hardness and lower residual stress of Ag-DLC thin film coating when doped with 0.35 atomic % in the DLC network (Wu et al., 2013). Manninen et al. found the deployment of Ag in DLC network leads to the reduction of surface free energy and internal stress, lower friction coefficient (µ), and enhanced wear resistance (WR) (Manninen et al., 2013).
Other than good tribological and mechanical properties, Ag-DLC coating has excellent biocompatibility. Pisarick et al. reported dual-pulsed laser-deposited Ag-DLC coating to be very suitable for biomaterials due to its excellent biomedical and mechanical properties (Písařík et al., 2017). Patnaik et al. discussed the comparison of cathodic arc-deposited AlCrN (ternary coating) and Ag-alloyed a-C (amorphous carbon base coating) over 316 LVM stainless steel. It was observed that a-C:Ag/CrN exhibited better tribological properties compared to AlCrN/CrN because of its good surface quality (Patnaik et al., 2021). Mazare et al. investigated the structural, biomedical, and corrosion resistance of Ag-DCL coatings deposited on titanium (Ti) substrates by using the thermionic vacuum arc technique and observed an improved corrosion resistance as compared to uncoated Ti substrate. Through this experiment, the authors reported higher antibacterial activity of Ag-DLC coating against Staphylococcus aureus (model Gram-positive bacteria) (Mazare et al., 2018). Zia et al. observed an increase in the hardness of DLC coating by 18% with the consecutive reduction of wear volume with a small amount of carbon particles embedded in the film. However, the increase in carbon content resulted in an enhanced friction coefficient by 20% with a consecutive decrease in hardness (Zia et al., 2017). Duta et al., 2018 investigated the biomedical properties of silver (Ag)- and silicon (Si)-incorporated DLC coating synthesized through the matrix-assisted pulsed laser evaporation technique. A bio-test revealed the non-cytotoxic nature of the coating for MG63 cells with poor antimicrobial activity when doped with Ag up to 1.85 at%. Other authors also observed improvement in antimicrobial activity when doped with 3.6 at% of Ag by keeping the adherence characteristics and cytotoxic action at acceptable levels. Past research work also reported an enhancement of Osseo integration properties of DLC coating when doped with 5.5 at% of Ag (Endrino et al., 2008). Talu et al. studied the surface microstructure of Ag-DLC grown through radio frequency plasma-enhanced CVD and reported a consecutive decrease in fractal dimension with an increase in deposition time (Ţalu et al., 2019). Ghadai et al. studied the effect of deposition temperature over the mechanical properties of thermal CVD-deposited Al-DLC thin film coating. Their results showed that deposition temperature had a significant effect on the structural and mechanical properties of the coatings (Ghadai et al., 2023).
From the aforementioned literature, it is observed that Ag-DLC thin films have a wide application in different fields. Most researchers have analyzed Ag-DLC coating either by using different substrates or by varying different precursor gases or by using different deposition techniques. Nevertheless, as far as is known, no research groups are involved in the analysis of physical and biomedical characteristics of Ag-DLC coating grown by the thermal chemical vapor deposition process. Moreover, deposition temperature is an important parameter regarding thin film growth over the substrate. Investigating the detailed mechanical properties of Ag-DLC coatings by varying the deposition temperature is thus crucial. Therefore, the present research article is focused on the following points:
(a) To analyze the influence of CVD temperature on the morphological properties of Ag-DLC coating.
(b) To study the compositional analysis of the DLC coating with respect to deposition temperature.
(c) To analyze the detailed mechanical properties of Ag-incorporated DLC coating for various indentation loads.
2 Experimental details
2.1 Coating preparation
The Ag-incorporated DLC thin films were grown over silicon (Si) substrates by using the thermal CVD technique shown in Figure 1. Prior to deposition, all samples were processed using the Radio Corporation of America (RCA) cleaning process for the removal of metallic and non-metallic contaminants. Then, 10 mM of AgNO3 and 5% HF solution were prepared separately. After the preparation of the individual solutions, both were mixed at a ratio of 1:1, and the cleaned Si substrates were dipped in the solution for 10 s. The dipped Si substrates were placed inside the CVD reactor tube for the synthesis of the DLC coating. To synthesize the Ag-DLC coating, the flow rates of N2 and C2H2 were kept constant at 20 sccm and 5 sccm, respectively, by varying the deposition temperature from 800°C to 950°C. The heating and cooling rate were kept 5°C minute and 3°C minute, respectively, and the deposition time was constant at 2 h.
2.2 Coating characterization
The morphological study of Ag-incorporated DLC coatings was characterized through SEM, with the instrument having the model no. JEOL JSM 7610F FEG-SEM. The elemental compositions of the coatings were carried out using Oxford EDS (X-act). The film thickness was observed through Dektak V 300 profilometer equipped with a 2.5 μm radius diamond stylus. For the thickness measurement, the diamond stylus was made to move from one end to other with a uniform rate at five different points, and the mean height was taken into account when assessing the total thickness. Innova SPM atomic force microscope (AFM) was used for evaluating the surface roughness of the Ag-DLC coatings. The nanoindentation test was conducted by using a CSM instrument, model no. NHTX 55–0019, fitted with a Berkovich diamond indenter tip (B-I 93; 20 μm curvature radius) at different loads ranging from 20 to 50 mN.
3 Result and discussion
3.1 Compositional analysis using EDS technique
Using the EDS technique, the elemental composition of the Ag-doped DLC coatings prepared at various process temperatures was analyzed. Table 1 shows the Ag-DLC coating composition grown under different temperatures obtained from the EDS results. It has been noted that the DLC films deposited at 800°C and 950°C exhibited the maximum and minimum atomic % (at%) of Ag. The % of Ag decreased with respect to the temperature due to the thermal evaporation of Ag from the surface at higher temperature. The findings showed that as process temperature increased, the coating’s carbon content increased. Meanwhile, in estimating the composition of various elements in the coatings, very small traces of magnesium (Mg) and nitrogen (N) were also found. However, the presence of higher C and Ag contents predominated the presence of Mg and N, and therefore, they were excluded from the EDS results.
3.2 Atomic force microscopy
Figure 2A shows the 2-D images of the Ag-DLC coating prepared at different temperatures ranging from 800°C to 950°C. The coating thickness was measured as 3.24
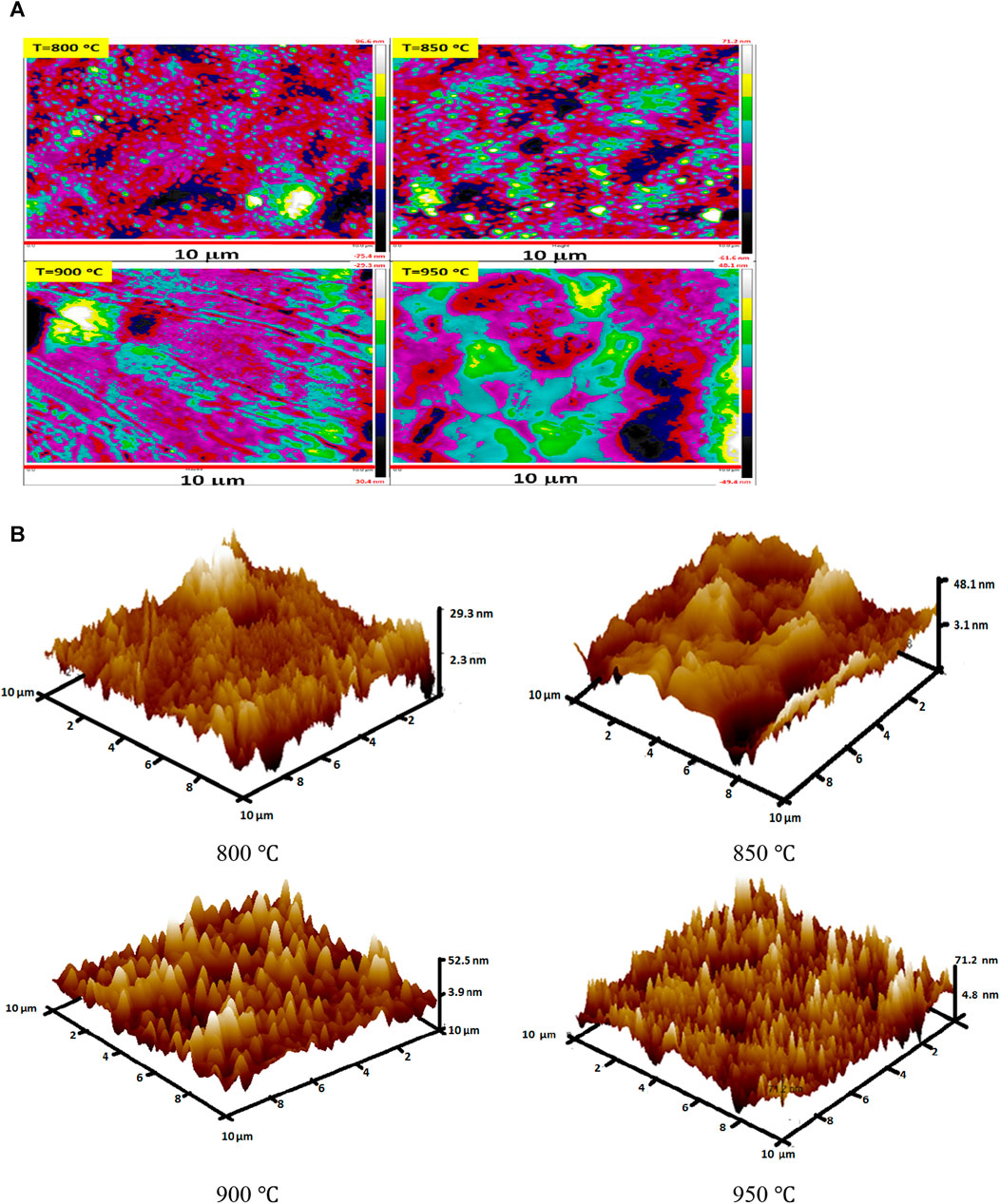
FIGURE 2. (A) 2-D AFM images of the Ag-DLC thin films deposited at different temperatures from 800 to 950°C. (B) 3-D AFM images of the Ag-DLC thin films deposited at different temperatures from 800 to 950°C.
3.3 Nanoindentation
Nanoindentation was carried out on the Ag-DLC coatings at different loads to evaluate the H, E, and the plasticity index parameters at various deposition temperatures. The load displacement curve of the Ag-DLC thin films at different loads between 20 and 50 mN is shown in Figure 3. The loading–unloading curve’s hysteresis can provide fundamental details regarding the anticipated plastic deformation of the Ag-DLC coatings. Furthermore, as the Ag-DLC thin film deposition temperature rose, the hysteresis under the loading-unloading curve increased for a given load. It is known that H (Hardness) α 1/hmax (maximum indentation): the higher the Hardness of the coating, the smaller the hmax. According to the figure, the film deposited at a lower temperature had the lowest hmax for a given load, while the film deposited at a higher temperature had the highest hmax. Therefore, the film deposited at 800
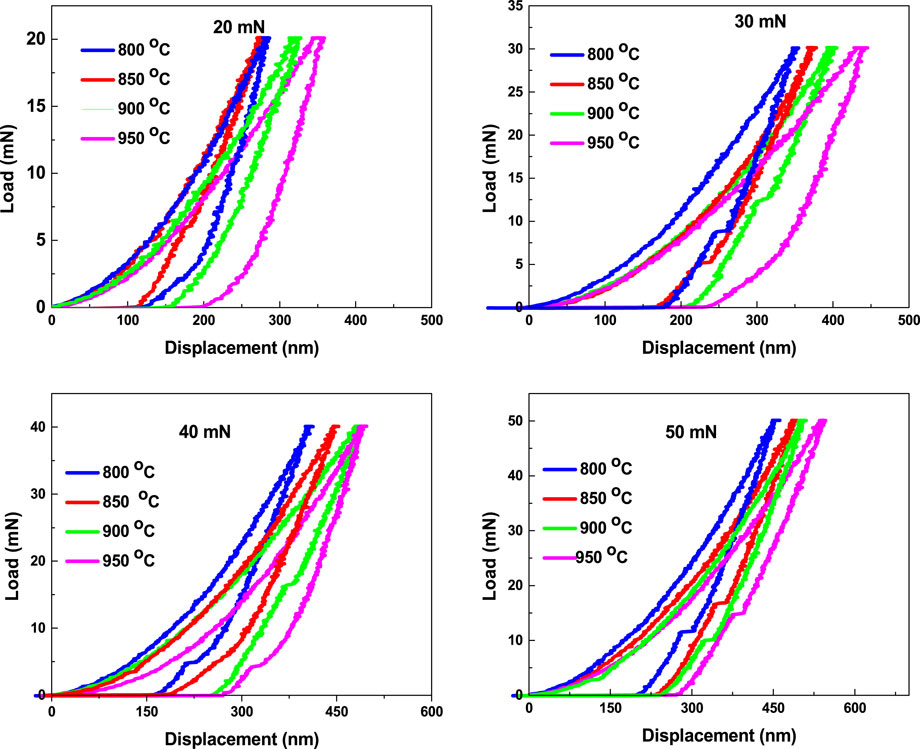
FIGURE 3. Load displacement curve of the Ag-DLC thin films deposited at different temperature at different loads from 20 mN to 50 mN.
Applying Oliver and Pharr’s method (Oliver and Pharr, 1992) for finding out the mechanical properties of the coatings, the E and H were measured by examining the unloading section of the load–displacement curve. The H was evaluated using Eq. 1.
Where Fmax is the maximum load over the sample, and A is the contact area of the indenter tip pointed over the substrate.
From Eq. 2 presented below, the stiffness (S) was calculated.
From Eq. 3, the calculation of elastic modulus (Ew) was carried out.
Regarding “S,” Oliver (Oliver and Pharr, 1992) developed the geometry independent Eq. 3, which is derived from the upper portion of the loading–unloading curve and represents the stiffness denoted by S. The Berkovich indenter’s constant β value is 1.034, and the reduced elastic modulus is represented by Er. The indenter and workpiece are indicated by the subscripts I and C, respectively.
Figure 4 represents the H and E of the Ag-DLC coating with different temperatures at different loads ranging from 20 mN to 50 mN. The amount of penetration by the indenter plays a crucial role for finding the type of coating. If the indenter penetrates one-10th of the thickness of the film, then the mechanical properties of the film can be influenced by the substrate. The H of the film may vary with respect to the penetration depth, and this result will give information about the types of film, such as hard film on soft substrate or soft film on hard substrate. It is known that if a soft film is deposited over a hard substrate, then the H of the film will increase with respect to the penetration depth. However, if a hard coating is coated over a soft substrate, then the H of the film will decrease with respect to the indentation depth. In the present work, the H of the film decreased with respect to the indentation depth, which means there was a hard coating over the soft substrate. From Figure 4, it is noticed that the H and E of the Ag-DLC coating decreased with increasing the temperature for a fixed load. The maximum H and E were 29.712 and 251.19 GPa for the Ag-DLC coating synthesized at 800°C at a constant load of 20 mN. From the EDS analysis, it was confirmed that the percentage of Ag decreased with the increase of the deposition temperature. Choi et al. analyzed the effect of Ag percentage over the H and E of the coating and observed that the hardness of the coating decreases with the increase of the Ag concentration (Jing et al., 2020). However, in the present work, the hardness of the film decreased with the decrease in the Ag concentration. This may be due to the effect of the higher deposition temperature. At a higher deposition temperature, the C-C bond is weaker, and this reduces the total sp3 fraction (Ghadai et al., 2023).
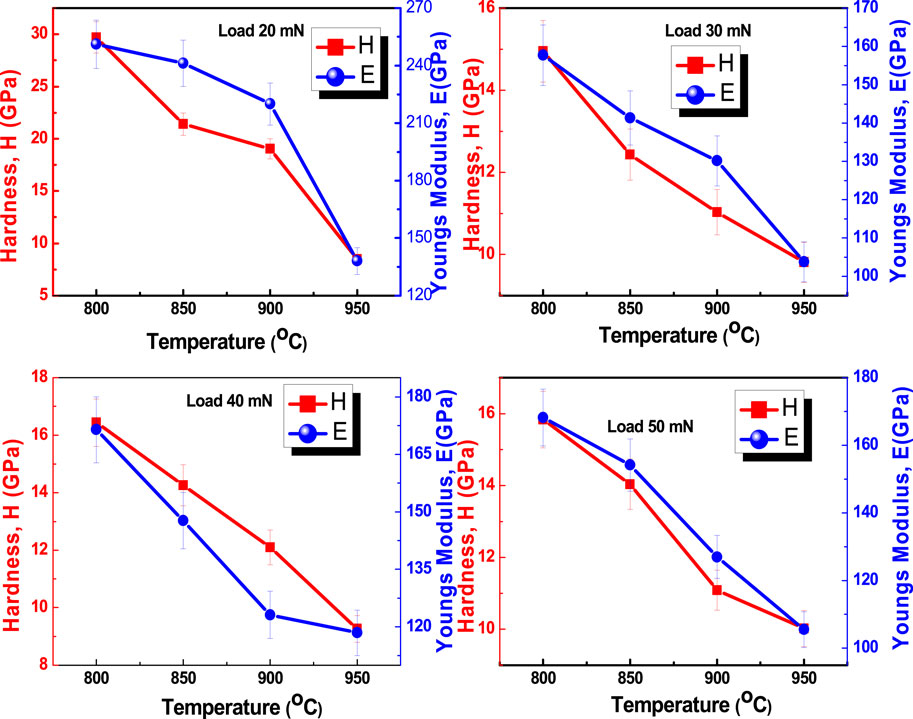
FIGURE 4. H and E of the Ag-DLC thin films deposited at different temperatures at different loads from 20 mN to 50 mN.
Incorporation of other elements such as Ag, Si, Mo, and Cu, etc., into the DLC coating gives an effective way to enhance the σ of the coating. Figure 5 shows the variation of the residual stress (σ) of the Ag-DLC films deposited at different deposition temperatures from 800 to 950°C. The σ of the coating was computed by the help of the Stoney equation, and it is presented in Eq. 4.
Where the thickness of the film and substrate is denoted as tf and ts, respectively. R1 and R2 are the film curvature and curvature of the substrate before the coatings, respectively. The ʋs and Es are the Poisson ratio and Young’s modulus of the substrate, and the values for the Silicon substrate are 0.27 and 127 GPa, respectively (Janssen et al., 2009; Ardigo et al., 2014). In the present case, the minimum σ of 0.45 GPa was achieved, which is the lowest compared to the other Ag-DLC films synthesized by PVD or PECVD techniques (Janssen et al., 2009; Wu et al., 2013; Ardigo et al., 2014). The σ is compressive in nature, and the decrease in the magnitude of σ was mainly due to the development of metallic silver amorphous phases, which act as an efficient buffer site to grasp the stress within the DLC films (Ghadai et al., 2023).
4 Conclusion
The Ag-DLC coating was successfully deposited by thermal CVD with the variation of deposition temperatures. From AFM and SEM, it was observed that the average Ra of the film increased with the increase in temperature. The minimum and maximum Ra were 4.8 and 71.2 nm for the Ag-DLC film at deposition temperatures of 800 and 950°C, respectively. The EDX results confirm that Ag decreases with the increase of deposition temperatures. Moreover, the H and E of the Ag-DLC coating decreased with the increase of temperature for a fixed load, and the maximum H and E were 29.712 and 251.19 GPa, respectively, for the Ag-DLC coating deposited at 800
Data availability statement
The original contributions presented in the study are included in the article/Supplementary material, further inquiries can be directed to the corresponding author.
Author contributions
RG: Conceptualization, Formal Analysis, Investigation, Methodology, Writing–original draft, Writing–review and editing. GS: Formal Analysis, Investigation, Visualization, Writing–original draft. MV: Formal Analysis, Investigation, Methodology, Software, Visualization, Writing–review and editing. RC: Funding acquisition, Supervision, Visualization, Writing–review and editing. SD: Investigation, Methodology, Software, Validation, Writing–review and editing. BS: Conceptualization, Supervision, Validation, Visualization, Writing–review and editing.
Funding
The author(s) declare that no financial support was received for the research, authorship, and/or publication of this article.
Conflict of interest
The authors declare that the research was conducted in the absence of any commercial or financial relationships that could be construed as a potential conflict of interest.
The author(s) declared that they were an editorial board member of Frontiers, at the time of submission. This had no impact on the peer review process and the final decision.
Publisher’s note
All claims expressed in this article are solely those of the authors and do not necessarily represent those of their affiliated organizations, or those of the publisher, the editors and the reviewers. Any product that may be evaluated in this article, or claim that may be made by its manufacturer, is not guaranteed or endorsed by the publisher.
References
Ardigo, M. R., Ardigo, M. R., Ahmed, M., and Besnard, A. (2014). Stoney formula: investigation of curvature measurements by optical profilometer. Adv. Mater. Res. 996, 361–366. doi:10.4028/www.scientific.net/amr.996.361
Duta, L., Ristoscu, C., Stan, G. E., Husanu, M. A., Besleaga, C., Chifiriuc, M. C., et al. (2018). New bio-active, antimicrobial and adherent coatings of nanostructured Carbon double-reinforced with Silver and Silicon by Matrix-Assisted Pulsed Laser Evaporation for medical applications. Appl. Surf. Sci. 441, 871–883. doi:10.1016/j.apsusc.2018.02.047
Endrino, J. L., Galindo, R. E., Zhang, H.-S., Allen, M., Gago, R., Espinosa, A., et al. (2008). Structure and properties of silver-containing a-C(H) films deposited by plasma immersion ion implantation. Surf. Coat. Technol. 202, 3675–3682. doi:10.1016/j.surfcoat.2008.01.011
Ghadai, R. K., Logesh, K., Čep, R., Chohan, J. S., and Kalita, K. (2023b). Influence of deposition time on titanium nitride (TiN) thin film coating synthesis using chemical vapour deposition. Materials 16 (13), 4611. doi:10.3390/ma16134611
Ghadai, R. K., Shanmugasundar, G., Cepova, L., Das, S., Mahto, P. K., and Kalita, K. (2023a). A temperature-based synthesis and characterization study of aluminum-incorporated diamond-like carbon thin films. Front. Mech. Eng. 9 (2023), 1325040. doi:10.3389/fmech.2023.1325040
Janssen, G. C. A. M., Abdalla, M. M., Keulen, F. V., Pujada, B. R., and Venrooy, B. V. (2009). Celebrating the 100th anniversary of the Stoney equation for film stress: developments from polycrystalline steel strips to single crystal silicon wafers. Thin Solid Films 517, 1858–1867. doi:10.1016/j.tsf.2008.07.014
Jing, P. P., Feng, Q. G., Lan, Q. H., Ma, D. L., Wang, H. Y., Jiang, X., et al. (2023). Migration and agglomeration behaviors of Ag nanocrystals in the Ag-doped diamond-like carbon film during its long-time service. Carbon 201, 648–658. doi:10.1016/j.carbon.2022.09.065
Jing, P. P., Gong, Y. L., Deng, Q. Y., Zhang, Y. Z., Huang, N., and Leng, Y. X. (2020). The formation of the “rod-like wear debris” and tribological properties of Ag-doped diamond-like carbon films fabricated by a high-power pulsed plasma vapor deposition technique. Vacuum 173, 109125. doi:10.1016/j.vacuum.2019.109125
Love, C. A., Cook, R. B., Harvey, T. J., Dearnley, P. A., and Wood, R. J. K. (2013). Diamond like carbon coatings for potential application in biological implants - a review. Tribol. Int. 63, 141–150. doi:10.1016/j.triboint.2012.09.006
Manninen, N. K., Ribeiro, F., Escudeiro, A., Polcar, T., Carvalho, S., and Cavaleiro, A. (2013). Influence of Ag content on mechanical and tribologicalbehavior of DLC coatings. Surf. Coat. Technol. 232, 440–446. doi:10.1016/j.surfcoat.2013.05.048
Mazare, A., Anghel, A., Surdu-Bob, C., Totea, G., Demetrescu, I., and Ionita, D. (2018). Silver doped diamond-like carbon antibacterial and corrosion resistance coatings on titanium. Thin Solid Films 657, 16–23. doi:10.1016/j.tsf.2018.04.036
Meng, K., Yu, L., Jing, S., Tan, X., Chen, X., and Wang, G. (2023). Microstructures, mechanical properties and surface wettability of La-doped diamond-like carbon films deposited by magnetron co-sputtering. J. Alloys Compd. 934, 167860. doi:10.1016/j.jallcom.2022.167860
Oliver, W. C., and Pharr, G. M. (1992). An improved technique for determining hardness and elastic modulus using load and displacement sensing indentation experiments. indentation Exp. 7, 1564–1583. doi:10.1557/jmr.1992.1564
Patnaik, L., Maity, S. R., and Kumar, S. (2021). Mechanical and tribological assessment of composite AlCrN or aC: Ag-based thin films for implant application. Ceram. Int. 47 (5), 6736–6752. doi:10.1016/j.ceramint.2020.11.016
Písařík, P., Jelínek, M., Remsa, J., Mikšovský, J., Zemek, J., Jurek, K., et al. (2017). Antibacterial, mechanical and surface properties of Ag-DLC films prepared by dual PLD for medical applications. Mater. Sci. Eng. C 77, 955–962. doi:10.1016/j.msec.2017.04.005
Ţălu, Ş., Abdolghaderi, S., Pinto, E. P., Matos, R. S., and Salerno, M. (2020). Advanced fractal analysis of nanoscale topography of Ag/DLC composite synthesized by RF-PECVD. Surf. Eng. 36, 713–719. doi:10.1080/02670844.2019.1710937
Ţalu, Ş., Stach, S., and Abdolghaderi, S. (2019). The effects of deposition time on the nanoscale patterns of Ag/DLC nanocomposite synthesized by RF-PECVD. Microsc. Res. Tech. 82 (5), 572–579. doi:10.1002/jemt.23203
Wang, L. J., Zhang, F., Fong, A., Lai, K. M., Shum, P. W., Zhou, Z. F., et al. (2018). Effects of silver segregation on sputter deposited antibacterial silver-containing diamond-like carbon films. Thin Solid Films 650, 58–64. doi:10.1016/j.tsf.2018.02.015
Wu, Y., Chen, J., Li, H., Ji, Li, Ye, Y., and Zhou, H. (2013a). Preparation and properties of Ag/DLC nanocomposite films fabricated by unbalanced magnetron sputtering. Appl. Surf. Sci. 284, 165–170. doi:10.1016/j.apsusc.2013.07.074
Wu, Y., Chen, J., Li, H., Ji, L., Ye, Y., and Zhou, H. (2013b). Preparation, and properties of Ag/DLC nanocomposite films fabricated by unbalanced magnetron sputtering. Appl. Surf. Sci. 284, 165–170. doi:10.1016/j.apsusc.2013.07.074
Yang, W., Gao, Y., Guo, P., Xu, D., Hu, L., and Wang, A. (2020). Adhesion, biological corrosion resistance and bio tribological properties of carbon films deposited on MAO coated Ti substrates. J. Mech. Behav. Biomed. 101, 103448. doi:10.1016/j.jmbbm.2019.103448
Keywords: DLC, EDS, Ag-DLC, cvd, residual stress, AFM
Citation: Ghadai RK, Shanmugasundar G, Vanitha M, Čep R, Das S and Swain BP (2024) Investigation of mechanical properties of silver-doped diamond-like carbon coating by varying deposition temperature. Front. Mech. Eng 10:1354903. doi: 10.3389/fmech.2024.1354903
Received: 13 December 2023; Accepted: 25 January 2024;
Published: 14 February 2024.
Edited by:
Lokeswar Patnaik, National Institute of Advanced Manufacturing Technology (Formerly NIFFT), IndiaReviewed by:
Viorel Paleu, Gheorghe Asachi Technical University of Iași, RomaniaSunil Kumar, Amrita Vishwa Vidyapeetham University, India
Copyright © 2024 Ghadai, Shanmugasundar, Vanitha, Čep, Das and Swain. This is an open-access article distributed under the terms of the Creative Commons Attribution License (CC BY). The use, distribution or reproduction in other forums is permitted, provided the original author(s) and the copyright owner(s) are credited and that the original publication in this journal is cited, in accordance with accepted academic practice. No use, distribution or reproduction is permitted which does not comply with these terms.
*Correspondence: Ranjan Kr. Ghadai, cmFuamFua3VtYXJibHNAZ21haWwuY29t
†ORCID: Ranjan Kr. Ghadai, orcid.org/0000-0001-6326-911X; G. Shanmugasundar, orcid.org/0000-0002-5608-7737; M. Vanitha, orcid.org/0000-0001-7539-126X