- 1CONAHCYT-Corporación Mexicana de Investigación en Materiales, Saltillo, Mexico
- 2Tecnologico de Monterrey, Institute for the Future of Education, Monterrey, Mexico
- 3TecNM Campus Cuernavaca-CENIDET, Tecnológico Nacional de México (TecNM), Cuernavaca, Mexico
- 4TecNM Campus Minatitlán, Tecnológico Nacional de México (TecNM), Minatitlán, Mexico
- 5Facultad de Ciencias Químicas e Ingeniería (FCQel), Universidad Autónoma del Estado de Morelos, Cuernavaca, Mexico
- 6Coordinación Académica Región Altiplano, Universidad Autónoma de San Luis Potosí, Mexico
The dominant phenomenon in laser welding processes is heat transfer by conduction, making it crucial to gain insights into energy distribution within the heat-affected region, including the melt pool. Thermal analysis enables the description of thermo-mechanical, metallurgical aspects, and also addresses studies related to fluid flow and energy transfer. As research in welding processes has advanced, these models have evolved. This is why it is now efficient to use computational modeling techniques as it allows us to analyze the behavior of laser welding during the process. This underlines the importance of this work which has carried out an exhaustive theoretical literature review with the objective of classifying and describing the numerical simulations of laser welding based on the physics involved. In that sense, the mathematical models and strategies used in laser welding are explored in a general way. Therefore, two types of laser welding by conduction and deep penetration are defined from this point and they are categorized according to the phenomena involved in Model Heat Conduction and Model Integral Multiphysics. This comprehensive review article serves as a valuable resource for higher education students by providing a structured and detailed exploration of laser welding and its mathematical modeling. By classifying and describing numerical simulations based on the physics involved, it offers a framework for students to understand the complexities of this field. Additionally, this innovative approach to organizing and presenting research contributes to educational innovation by facilitating a more efficient and effective learning experience, helping students acquire the knowledge and research skills necessary for advancements in the laser welding domain.
1 Introduction
Throughout history, humans have instinctively adapted and shaped their surroundings. One crucial aspect of this evolution has been the necessity to invent and create tools, weapons, and implements for various tasks crucial to societal, economic, and industrial progress. A notable example of this is the emergence of metallurgy during the Bronze Age, particularly in Europe and the East, where the demand to forge metals spurred innovation and the development of metalworking techniques. Initially, forging fell within this paradigm; in the present day, characterized by industrial growth and productivity, the processes emphasizing efficiency, safety, and cost-effectiveness in metal joining are collectively referred to as welding (Josep and Wiliam, 1998). This process is present in all the manufacturing operations of vehicles, tools, instruments, etc. Based on scientific and technological progress, the welding process is not exclusive to joining identical materials or metals of similar composition and properties, however, the welding process can be performed not only on metals but also on different polymers and a wide range of dissimilar materials (materials with divergent composition and properties). When performing the process of joining metals, several processes should be considered, which should ensure the optimal conditions of the joint (resistance to mechanical wear, corrosion, oxidation, resistance to high temperatures, etc.) so that as a result of the welding process a joint with unique properties is obtained.
In 1856, James Joule laid the foundations for welding principles, and the subsequent evolution of welding metallurgy has paved the way for the emergence of innovative welding methods, contributing significantly to industrial advancements today. The replication of the welding process in a digital environment can exclusively be achieved through the application of computational techniques. However, the welding process is very complex as it includes heat source motion, material deposition, thermal dependence, transient heat transfer with complex boundary conditions, and phase change phenomena. Of course, the thermal field can be considered as a field that has a considerable impact on the mechanical and metallographic fields. The heat transferred to the metals during the welding process causes them to melt and blend with the filler material. Upon solidification, this amalgamation results in a metal possessing entirely distinct properties from its pre-welding state. Hence, it becomes imperative to comprehend their characteristics, encompassing both thermal and mechanical properties, to effectively analyze their performance. Hence, in response to the imperative to enhance welding techniques and facilitate the joining of diverse materials, a range of methods have been developed for welding processes. It would, therefore, be insightful to explore a comprehensive classification of welding techniques, enabling a thorough understanding of the unique attributes of each process and aiding in the selection of the most suitable method for specific industrial applications.
In the literature, some review studies are available that show the versatility of laser welding because they describe the laser welding process in different aspects, but emphasize the field of application and use of laser technology. Mackwood and Crafer (2005) published a review describing the thermal modeling and prediction of laser welding of metals. The authors noted that similar techniques are used for other types of welding such as arc, resistance, and friction stir welding. Later, Rao et al. (2011) published a review paper based on hybrid welding. The authors described the modeling works employing hybrid welding formed by LBW and GMAW welding. The authors also emphasized the importance of this type of hybrid welding because, at the time of modeling, it is of great complexity since the transport phenomena of each weld involved in the process are immersed. Years later, Svenungsson J. et al. (2015) presented modeling studies of keyhole welding, considering wavelength-analysis modeling of the energy transfer of the laser to the keyhole surface.
In that same period, Dal and Fabbro (2016) also performed a state of the art of laser welding simulation. The authors focused on the joining of dissimilar metals or materials under the laser welding process. In this review, most of the equations and assumptions needed to simulate laser welding are provided. Years later, Bappa Acherjee (2018) presented a very extensive literature review. In the first paper, the author presented the state of the art on hybrid welding (Laser-Arc), where the focus remained on the convergence of knowledge in the technical sense, research, and application of the welding process through a general description of hybrid laser arc welding, which includes the principle of operation. Consequently, a review of the process LBW of polymers was carried out by Bappa Acherjee (2020). This review was based on the following aspects: the fundamentals of welding operation and aspects of polymer welding strategies, and the application of process strategies, among others. Later, Bappa Acherjee (2021a) and (2021b) complemented the reviews outlined above with a review of LBW of polymers based on welding parameters, quality attributes, process monitoring, and laser irradiation strategies applied to laser transmission welding of polymers.
Other review papers were published, including Dave et al. (2021) in which the authors presented a critical review of laser transmission welding in semicrystalline polymers. The authors considered items such as interdiffusion and microstructural changes involved in the laser-polymer interaction and described an overview of the characterization process that determines weld quality. Among the laser parameters, the authors described laser power and welding speed. A comprehensive review was also performed by Bayat and Dong, (2021) to classify numerical simulations of metal additive manufacturing with the application of laser powder bed fusion (L-PBF). The authors rated the simulations according to the length scale and according to the physics involved in the process. Therefore, they provide insight into modeling strategies for different types of scales. In the same year, Riquelme and Rodrigo (2021) presented an outlook on laser cladding on magnesium alloys. The authors describe that magnesium-based alloys have poor mechanical properties. Therefore, this problem can be solved with coatings with optimum properties. That is why laser cladding is an option in coating manufacturing. Thus, the review was based on laser cladding on magnesium and investigated the effect of manufacturing parameters. In a later year, Jiang et al. (2022) described in their research work the relationship in recent years between neural networks and the development of fiber laser systems. The work of the authors points out recent research on fiber lasers aside from control of nonlinear effects and evaluation of laser properties.
A review article published by Nascimentos et al. (2023) gives a comprehensive overview of thermal models of heat sources for welding. However, the authors made an effort to organize a catalog and statistically describe the most important models in the last 20 years. This review of Ernandes is exhaustive in nature, as it encompasses a comprehensive exploration of the subject. Within this work, the authors meticulously detail the geometry and mathematical models pertaining to heat sources. They present these models in a chronological sequence, offering a systematic account of the various heat sources employed in modeling the welding phenomenon. In this sense, the review papers show the overview of the research on the welding process, covering aspects of the type of application material, industrial process, comparisons with other processes in the application, and all the source models that exist for the modeling of welding. Also, for the analysis of the phenomenon, experimental studies are essential to conceptualize the phenomenon.
Presently, within the industrial landscape, laser welding stands as an advanced and expanding technique. Its profound penetration capabilities and the extensive array of laser types have prompted the exploration of numerous phenomena and case studies enrich this field. In this context, this work specifically delineates an objective, focusing on the case study of penetration in laser welding.
Among the various phenomena associated with heat energy transfer, encompassing its three mechanisms (conduction, convection, and radiation), the predominant one in welding modeling is heat transfer via conduction. Consequently, welding processes, irrespective of their specific type, consistently involve the flow of multiple forms of energy, including kinetic, electrical, and thermal, all of which ultimately culminate in a heat flow affecting the material. This underscores the paramount significance of delving into this category of phenomena, with a particular emphasis on the modeling of laser welding, as it yields essential insights crucial for acquiring the requisite knowledge in this domain.
Hence, the primary objective of this work, which is the research contribution, is to classify and describe numerical simulations of laser welding based on the physics involved and the aspects of the heat source model that have been employed. In a general way, it explores the mathematical models employed in laser welding and provides readers with a comprehensive introduction, especially those keen on delving into laser welding modeling. It aims to acquaint them with the mathematical models employed to capture this phenomenon, along with the associated. The structure of the article includes multiple sections. Section 2 is dedicated to reviewing the current state-of-the-art in laser welding modeling, Section 3 is dedicated to mathematical modeling of laser modeling with a special focus on model heat conduction and integral multiphysics, Section 4 deals with heat source models that simulate laser welding, Section 5 is related to CFD tools for this analysis, Section 6 discusses the findings and Section 7 conclusions of the review art.
2 Current state of the art in laser welding modeling
To comprehensively grasp the landscape and evolutionary trajectory of welding in the domain of computational modeling and simulation, an initial prerequisite is a foundational understanding of the various welding methodologies and their operational mechanics. Nevertheless, it must be acknowledged that embarking upon a comprehensive exploration of the encompassing spectrum of welding, which involves an intricate web of concepts, laws, and principles, presents a formidable and extensive undertaking.
To establish an accurate classification of welding, it should be defined based on the specific process, conditions, or characteristics that each welding method employs. Some authors, such as De Azevedo et al. (2022), provide different types of welding classified based upon the type of process. Resistance welding, arc welding, oxyfuel gas welding, and solid-state welding are included within energy welding as this process uses a laser to generate the energy required in the joining of materials. However, Kou (2002) describes a classification by considering the type of energy and conceptualized fusion welding, including gas Welding or oxyacetylene, arc, and high-energy beam welding as subtypes of this procedure. High-energy beam welding is better known as laser welding, or it is also expressed as electron welding. As per this name, it uses a laser device through which it produces an ordered beam of light and in which it concentrates transitions to atomic dimensions (electrons) at higher energy levels. There are two subtypes of this type of welding classified according to the joining procedure (for experimental setup schematics, see Figures 1A, B) which are: electron beam welding (EBW) and laser beam welding (LBW), respectively. The difference between these procedures is that EBW uses a void environment with high energy, high welding speed, and a narrow Heat Affected Zone (HAZ) ((Zhang et al., 2014; Yang et al., 2020)).
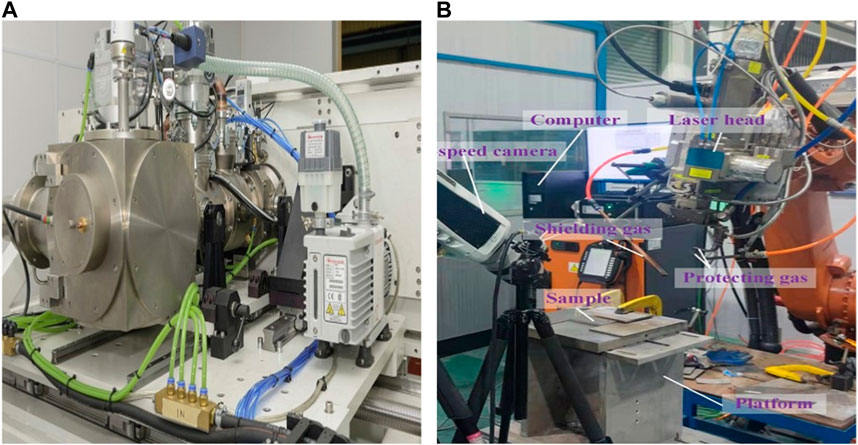
FIGURE 1. Schematic of the experimental setup of: (A) Electron Beam Welding (Feng et al., 2021) and (B) Laser Beam Welding (Tao et al., 2023). (The Figures are Under a Creative Commons license, Open Access).
In a laser welding system, the laser presents a synergy with the base material through the thermal energy since it must generate the energy (heat flow) necessary to melt and penetrate the surface of the base materials that interact in the welding process. In this process, a sort of fluid pool is created. It is in these processes where multiple phenomena occur and which require the knowledge of different areas of physics to fully interpret the phenomenology (Lienert, 2011; von Allmen, 1987). Such is the versatility of the laser welding process that it can use a variety of techniques, including the utilization of shielding gases, applied pressure, or a combination of both, throughout the welding procedure. The most common joining techniques such as arc and oxy-fuel welding have been replaced by LBW joining technology for different applications. This is because of the advantages of concentrating the energy, and ease of operation because it can be automated, so it is considered one of the modern techniques (Liu et al., 2018).
Among the diverse thermal-energy-utilizing welding techniques, experimental observation of the procedure presents complexity.
Thus, Ventrella, Berretta, and De Rossi (2010) developed an experimental case study and analyzed the effects of the operating parameters of the pulsed laser. In this way, they analyzed the characteristics and behavior of the joined parts in order to determine the mechanical properties. The authors concluded that the shape and dimension of the weld bead depend on the dimension of the separation of the spaces between the parts. In this sense, the width of the connection and the depth increase proportionally to the pulse energy. Thus, the range of power density required for laser welding is between 5×104 and 107 W/cm2. It may happen that the value is less than 105 W/cm2 and that the laser beam will be reflected by the medium. It is further possible that only 30% of the power will be absorbed (Fresnel phenomenon) by the surface (Svenungsson, Choquet, and Kaplan, 2015). This process is called conduction welding (so defined because the penetration depth is one-tenth of a millimeter). In the opposite case, where the power density operates with values greater than 106 W/cm2, the laser beam is absorbed until the base material starts to evaporate and a weld pool is formed which expands to allow the laser to penetrate, this process is known as keyhole welding (Ebrahimi and Hermans, 2023), Figures 2A, B describes both categories with the characteristic aspects, respectively.

FIGURE 2. Categories of laser welding: (A) Conduction Welding and (B) Keyhole Welding, (Ebrahimi and Hermans, 2023). (The Figures are Under a Creative Commons license, Open Access).
Thus, the difficulties associated with acquiring equipment that facilitates real-time observation and analysis of the heat source impinging on the joint region. In essence, it remains an intricate endeavor. Therefore, it is impossible to analyze the area affected by the heat in the weld puddle. Thus, observing the phenomenon physically and avoiding the risk to the eyes of the observer, due to the exposure to radiation during joining, is impossible so far.
For these reasons, modeling and computational simulation have been the main tools of the scientific community to try to understand, analyze, describe, and develop the laser welding phenomenon. Furthermore, it is essential to note that the development of a mathematical model that accurately represents the underlying physics of welding hinges on the specific case study of interest.
In addition, numerical modeling is complemented by experimental research to verify and understand the strengths or weaknesses of the welding process. The interest in fully understanding the physics involved in this process is driving the field of numerical modeling to perform more precise investigations of every aspect of laser welding under consideration. Miyamoto (2010) developed technology for fusion by using laser pulses with less repetition so that the laser energy is absorbed at the interface. It has been noted that modeling the phenomena that occur in welding involves simplifying some of the physics involved. Among those that occur, the pressure generated (recoil pressure) due to the evaporation of the medium causes the vapor to drive the molten metal and form a long, narrow cavity.
In this way, the laser will be able to penetrate through the vapor until it refracts again at another point in the cavity. Therefore, the changes caused in the morphological structure (Cunningham et al., 2019) of the material due to the absorptivity have generated interest when investigating the evolution of the weld pool (Wang et al., 2006; Cho et al., 2009; Pang et al., 2016; Huang et al., 2017; Li et al., 2019). Roy et al. (2006) developed a 3D thermal and hydrodynamic model for pulsed laser welding to numerically analyze the evolution of the temperature and velocity fields during the process.
Thus, when generating the weld puddle, the geometrical aspects as well as the behavior of the laser operating parameters are of great interest and studies have been conducted to determine the relationship between penetration and stability in the keyhole (Bedenko et al., 2010; Gao et al., 2018). Analysis of the dependence between stability and keyhole weld depth has been raised. In this regard, Fabbro (2020) presented a thermal model for a regime of the laser applied to macro welding considering the laser absorptivity and Savin et al. (2018) performed a numerical study of continuous laser welding and heat treatment, considering the modes of deep penetration and surface melting. The results showed that the maximum deformation and longitudinal strain due to tensile stress is in the elastic region.
The importance of the geometrical aspects of the weld puddle has been reported by Vaglio et al. (2023) who developed a thermo-geometrical model and predicted keyhole porosity. The difference in geometry and aspects in the evolution of the phenomenon can be avoided with keyhole analysis. In this way, we find the work done by Courtois et al. (2013) presents a new approach to calculating the laser reflections, treating them as a wave from Maxwell’s equations.
The modeling of the laser welding phenomenon is an emblematic topic because it requires considering a mathematical model of the process welding phenomenon and a mathematical model to determine the type of heat source, in order to determine the heat flux acting on the weld pool and the heat affected zone (HAZ). There exists a notable evolution in heat source models, which will be elaborated upon in a subsequent section. Specifically, within the context of laser welding, recent years have witnessed dedicated research endeavors aimed at refining the methodology for replicating the laser welding process.
As welding is a widely used process, a model that allows the simulation of the heat flow necessary and physically adequate for its study must be provided since the result of heat input is deformation and residual stresses in the structure. In numerical simulation studies, the contribution in the application of energy transport, momentum transport and matter transport improve the understanding of the laser welding process. However, the literature is very wide and versatile due to the studies that exist. Thus, not having a concise reference when approaching the development of a model for the simulation of laser welding can lead to errors of uncertainty in the calculations.
From the concepts and fundamentals of the laser welding process, there is a growing importance in understanding that the physical phenomena underlying these processes are remarkably intricate and, more significantly, intricately interrelated. In this sense, the most relevant phenomenon in the welding process is the interaction of energy and matter, in that the flow of energy passes through or impinges on a solid medium. It then triggers a series of transport phenomena, resulting in an increase of energy and as a consequence a change in the solid medium’s state of segregation. Therefore, in numerical modeling, the energy flow is represented as a volumetric heat source, which must be considered as a mobile aspect. Determining the transient thermal field in a solid medium is important because the mechanical properties and metallographic aspects depend only on the temperature. Among the subsequent phenomena, a dynamic process in the weld puddle occurs, which requires determining and analyzing the flow field in the weld as a consequence of the coexistence of fluids in different phases, under complex boundary conditions (evaporation and convective and radiative losses to the surrounding environment). In this aspect, the phenomena of keyhole dynamics, molten pool dynamics, tracking interface, and the occurrence of weld defects contribute to a comprehensive understanding of the subject (Yang et al., 2020).
Modeling and comprehensively addressing all facets of this phenomenon entail a substantial computational expenditure in terms of both time and effort. Additionally, grappling with the intricacies of the mathematical model poses a formidable challenge. The first category pertains to thermo-mechanical and metallurgical simulations, which are geared towards scrutinizing outcomes related to stress analysis, residual stresses, mechanical properties, metallurgical phase transitions, and mechanical deformations arising within the laser welding process. In this sense, Suárez et al. (2011) developed a transient thermo-metallurgical model through ANSYS software. The work was carried out considering the laser cladding technique. Therefore, due to the temperature field, the thermal and metallurgical effects, i.e., phase transformation, were observed, and the results were verified with experimental data. Furthermore, Vemanaboina et al. (2014) presented a study of a finite element based transient thermal model to simulate the welding process applied to stainless steel. The temperature in the heat-affected zone, which determines the deformations and stresses, was analyzed.
Later, Azizpour et al. (2015) developed a 3D numerical study of the finite element methodology (FEM) technique of laser beam welding of a Ti6Al4V sheet, to determine the temperature zone and subsequently to predict the mechanical property of hardness and weld geometry. By using SYSWELD software, the effect of focal position on the weld bead geometry was investigated and the results were compared with experimental results.
Sahoo and Chou (2016) studied the microstructure evolution in an electron beam additive manufacturing process. The authors developed a three-dimensional thermal model with ABAQUS software and analyzed the thermal behavior in the electron beam additive manufacturing process. Furthermore, they used a moving conical volumetric heat source combined with a horizontal Gaussian distribution source. In obtaining the thermal field, the phase-field method was employed to incorporate the temperature gradient and solidification rate as simulation parameters in a Fortran code.
Later, Su et al. (2017) performed a numerical simulation in 3D of transient laser welding to analyze the temperature and residual stress in aluminum parts. The model was considered plastic and thermo-elastic. They also analyzed the laser welding power and speed. Sebayang et al. (2018) evaluated the distortion and phase transformation in the heat affected zone during the laser welding process through finite element analysis with a thermos-structural and metallurgical model using MSC Marc/Mentat software. The authors used a conical Gaussian heat source distribution and the Seyyfarth-Kassatkin model for the estimation of the transformation phases. Years later, Zhang J. et al. (2018) conducted a two-dimensional study of grain structure growth in laser welding. The authors developed a model based on cell autonomy (CA) coupled with the finite element technique to determine the temperature distribution and evolution of the granular microstructure during metal solidification. Shapeev et al. (2019) conducted a study using 3D modeling of laser welding on dissimilar metals with the method of collocations and least squares. The geometrical parameters of laser welding were determined to avoid brittleness in the formation of intermetallic phases.
Nandy et al. (2019) presented a molecular dynamics simulation study to investigate the sintering mechanism of AlSi10Mg metal powders of different sizes. The authors employed Sandia National Laboratories’ MD LAMMPS (Large-scale Atomic/Molecular Massive Simulator) software. It was observed that nano-sized particles and interfacial atoms have higher mobility than surface atoms, resulting in higher part densification. In the multicomponent alloy case, the diffusion rate is higher than in pure metal.
Panda and Sahoo (2019) analyzed the effects of varying laser density and welding speed. The authors presented a transient 3D thermo-mechanical model and determined the stresses during powder bed laser melting of an AlSi10Mg built-up part using ANSYS software. In the model, the authors considered the effects of heat transfer, a moving Gaussian distribution heat source, and the process of direct laser sintering of metals.
Nazami and Sahoo (2020) analyzed the influence of hatch spacing and laser spot overlap during melting in an aluminum alloy under a 3D transient heat transfer model. The authors used ANSYS software and considered the mechanisms of conduction, convection, and radiation, as well as a Gaussian-distributed heat source. It was concluded that the dimension of the molten pool changes with varying hatch spacing and laser spot overlap.
Sahoo (2021a) performed a simulation of heat transfer and temperature distribution for different parameters of laser energy and welding speed using ANSYS software. A Gaussian heat source distribution was used in the model. In the same year, Sahoo (2021b) developed a thermo-mechanical model through finite element analysis to determine the residual stress and strain of the part built with AlSi10Mg. The author concluded that there is a decrease in residual stress in the built part with an increase in the gap between hatches.
Another study, by Giudice and Sili (2022), evaluated residual stresses in laser welding. The authors determined the longitudinal stress distribution through a multi-source model, which allowed for determining the temperature field in full penetration welding. The authors also concluded that the resolution of the thermal field helps to analytically determine the residual stresses through a combined process of the thermal profiles and the corresponding heating-cooling cycles.
More recent studies have reported the development of laser calibration, such that parametric studies contribute to optimizing the welding process. An example is Nisar et al. (2023) who developed a 3D transient thermal study using finite element in ABAQUS to optimize the parameters of the laser welding process on an aluminum alloy. In the study, they used a conical Gaussian heat source and a regression model to determine the optimal parameters. The results showed that the laser power has an influence on the weld bead width, while the welding speed has an influence on the temperatures. Also, (Liu et al., 2023), investigated the effect of laser welding parameters on ceramics. They determined the temperature field, speed and power of laser welding using ABAQUS software by finite element analysis. Furthermore, Chuang et al. (2023) proposed a study based on finite element-COMSOL Multiphysics simulations, regression analysis, and neural networks in order to obtain the power and speed parameters of laser welding to decrease angular distortion and improve mechanical properties. The authors successfully predicted the weld puddle geometry, cooling rate, and heat-affected zone dimensions as a function of laser power and welding speed.
The consequent effects on the parameters of the welding process were reported in the work by Wang et al. (2023) who performed a 3D numerical study through ANSYS of laser conduction welding between stainless steel and PET. The authors considered a surface type heat source in their model. They analyzed the effect of laser welding speed on the joint temperature field, weld morphology, pore distribution, interfacial microstructure, strength, and dissimilar joint fracture development. A study reported by Polonsky et al. (2023) performed a 3D study for the characterization of partial penetration laser welding of 304L stainless steel by finite element simulation. They used the code developed by Sandia National Laboratories called ESCULT and SCULPT. Another work was reported by Karlson et al. (2023) to determine the geometric characteristics of the weld on its strength and ductility under quasi-static tensile loads through 3D finite element simulations. The authors validated the model with experimental load-displacement results. The simulation was performed using the SIERRA/SolidMechanics (SIERRA/SM) code developed by the authors and the Sculpt and Cubit codes were used to generate the computational mesh. Another study was presented by Wu et al. (2023) which presented the theoretical-experimental study of damage in a titanium alloy joint during hot deformation in the laser welding process. Numerical simulation of uniaxial tension was performed by finite element with Abaqus software. The results showed that the error between the fracture deformation in the numerical study and the experimental one is less than 5%. In a case study, Zuo et al. (2023) presented the experimental and numerical study of laser welding of Al2O3 ceramic. In this regard, they analyzed the effects of laser welding parameters on crack morphology. During the experiment, it was observed that when the defocus distance was greater than 17 mm, free cracks were formed in the weld and in the base material. In the numerical study, it was determined through a thermo-elastoplastic model that the maximum stress is 1,576 MPa, so that the model developed with the ABAQUS software did not present defects due to cracks. The authors concluded that as long as the stress is less than 1,576 MPa, cracks do not occur.
In another theoretical-experimental analysis reported by Wasilewski et al. (2023), they studied the thermal cycles in laser welding processes at high speeds. In this sense, the authors analyzed the fields and temperature gradients through thermo-metallurgical numerical simulation using finite element and the results were validated with experimental data. The temperature field was obtained by means of a semi-analytical 3D transient model with a Gaussian surface heat source combined with a conical heat source, in a synchronous manner. The results showed that the heating rates are in the range of 2 × 104 K s-1 and 4 × 105 Ks-1. Among the thermo-mechanical studies, Zhang et al. (2023) determined the temperature field of the weld puddle to analyze the residual stress and strain. The authors performed a numerical simulation through the finite element technique of the welding process for a high-power laser. They employed a combined Gaussian and conical volumetric heat source model. The authors concluded that the Von Mises stress was unevenly distributed with a maximum value of 220 MPa. Subsequently, Li et al. (2023) developed a 3D finite element model of laser welding to determine the residual stress and weld deformations in a stainless-steel wall. The authors employed the thermal cycling curve method in conjunction with a combined surface Gaussian type heat source and a cylindrical volumetric heat source. The authors observed that the weld puddle morphology matched the experimental results, so the heat source model is accurate. On the other hand, Rehman et al. (2023) reported the results of finite element analysis of laser butt joint welding using SYSWELD software. A conical heat source and the double ellipsoidal model were considered in the study. The numerical results of the weld profile were validated with the experimental results and the model that showed correct accuracy was the conical model.
Apart from considering the geometric defects and dimensional accuracy, for the simulation of the keyhole and weld puddle, with the increase of energy in the medium a phase change was generated, therefore, three phases of the material coexist: a solid phase, liquid metal, and the vapor of the material. Therefore, the second category corresponds to the multi-physical simulations because they allow the observation and analysis of the thermal fields caused by the incidence of the energy beam on the weld bead, where the effects of laser-material interaction, heat, fluid flow, and solid-liquid are taken into account. Phase transformation by the incidence of the heat source energy, allows one to analyze multiple phenomena in the welding process, as well as the weld geometry, considering the superficial stress, the Marangoni effect, and pressure recoil during the process transition from superficial to keyhole welding and the distribution of the heat source.
Based on this reason, Amara et al. (2003) considered the ray tracing method and no multiple refraction in the numerical study of the vapor produced during laser welding through the finite volume method. The authors studied the effects of vapor pressure and ambient pressure and they observed that ray tracing allows an adequate absorbed intensity for the model, but it is important to consider the multiple refraction. Thus, it is required to consider the effects of surface tension, pressure recoil, and the effect of thermos-capillarity between the vapor and the molten metal as these aspects allow one to understand the dynamics of the weld puddle. Later, Amara & Fabbro (2008) presented a study in which they analyzed the effects of inert gas on liquid metal flow. The authors considered the effects of surface tension, annealing pressure on the evolution between the keyhole, weld pool, and surrounding air. They employed the VOF method to determine the ratio at the fluid interface using Fluent software. It was concluded that using gas injection during the process improves the fluid flow and therefore allows for better joints. Therefore, the interest in analyzing these effects allowed Saadlaoui et al. (2018) to propose a new methodology using finite elements. In order to perform a three-dimensional numerical study of the dynamics of the weld puddle and in the model, he proposed the concepts of back pressure, surface tension, and the thermo-capillary effect. The required energy source was obtained by combining the double ellipsoidal source and a Gaussian surface source for the modeling using the commercial software SYSWELD.
Mokrane et al. (2018) studied the selective laser sintering process as an additive manufacturing technique for material processing. The authors developed a computational tool to simulate the thermal processes. The authors described the modeling, simulation, and validation to optimize the laser sintering process, as well as a parametric analysis to have the reliability of the model represent the real physical phenomena. In the same year, Alter et al. (2018) presented a study using a frequency-doubled disk laser for high speeds. Through an analytical model, the authors determined the laser power at the melting and deep penetration interface. The authors observed that heat conduction welding for speeds >1 m/s achieves quality welds without spatter formation. Later on, Meng (2020) performed a numerical study of elements in laser beam welding with deposition material. The authors developed a three-dimensional fluid flow and transient heat transfer model, employed a ray tracing method with a mesh refinement algorithm to calculate the Fresnel absorption in the keyhole wall, and employed Ansys Fluent software to obtain the temperature, velocity fields, and free surface deformation. Also, Ghosh et al. (2021) presented a numerical study to determine the transient regime temperature distribution during the laser welding process. The model was resolved with COMSOL Multiphysics software and the study used a Hermit-Gaussian function as a continuous mode (CW) heat source of 300 W and a moving speed of 120 mm/min.
Guo et al. (2021) presented a theoretical analysis of keyhole welding, in which the authors considered the geometrical relationship that can be obtained with the ratio of the radius of curvature at the gas-liquid interface and the radius of the laser beam. Furthermore, Giudice et al. (2021) developed an analytical model of a parameterized moving linear heat source to determine the temperature field during the laser welding process. This developed model allows the expression of the thermal field as a function of the reference system of the heat source. The authors were able to analyze the temperature profiles during the welding process. Years later, Kang et al. (2022) developed a three-dimensional fluid flow coupled energy transfer model for the simulation of the weld pool dynamics. The authors considered the study in a laminar regime with the VOF method to calculate to tracking interface. In the model, they considered recoil pressure, surface tension as the moving forces, and a combined Gaussian distribution heat source. In this way, it was possible to establish a relationship between the stability of the keyhole and the stability of the weld pool, in order to avoid porosity defects. In this sense, analyses have also been carried out when considering the free surface of the fluid.
Chianese et al. (2022) presented a 3D numerical study with Flow 3D software. In this way, they analyzed the effect of inter-piece separation on the temperature field and on metal mixing. The multiphysics model considered beam oscillation with a Gaussian type profile, multiple reflection, evaporation, keyhole formation, solidification, diffusion, species conservation, and laser absorption as a function of temperature and VOF technique tracking at the liquid-vapor interface. The authors concluded that the separation between parts causes uncontrolled mixing of the metal. A year later, Chianese et al. (2023) reported the effect of laser beam shaping on metal mixing and molten bath dynamics. The study was performed using Flow 3D software and the multiphysics model considered convection and conduction heat transfer, as well as fluid flow dynamics, and the effect of the square column. The multiple reflection method was also implemented through ray tracing, the VOF method, and phase change. In their case, Tsai et al. (2023) analyzed the behavior of the keyhole and weld puddle with an artificial neural network (ANN) to predict the melt pool depth, melt pool width, and cooling rate for any combination of the parameters of laser power and welding speed. In a three-dimensional study, Fresnel absorption effect, back pressure, Marangoni force, buoyancy force, VOF method, surface tension, vapor column heat transfer induced by vapor, and laser beam energy density in Gaussian distribution results were obtained by Flow 3D software. A theoretical-experimental study presented by Ai et al. (2023) analyzed the influence of keyhole behavior on the asymmetry characteristics of laser welding in dissimilar materials. The authors presented a multiphase 3D model. In this sense, Unni and Vasudevan (2023) performed a three-dimensional numerical simulation in the transient of the hybrid laser-MIG welding (HLMW) for a 316 LN stainless steel plate of 0.01 m thickness. It was observed that the authors employed three volumetric heat sources (arc and laser heat source), double conical ellipsoid, double conical-cylindrical ellipsoid, and double rotating Gaussian ellipsoid. The authors analyzed the weld pool development and temperature distribution with ANSYS Fluent software and validated them with experimental results. The study by Fan et al. (2023) permits a comparison of laser welding and GMA-assisted high-power laser welding. In the 3D transient model, a hybrid heat source, i.e., a planar elliptical double heat source and a Gaussian conical heat source, was considered for arc and laser heat distribution respectively, Fresnel absorption. Furthermore, the effects of electromagnetic force, evaporation, recoil pressure, surface tension, Boussinesq approximation, and free surface tracking were examined using the VOF method. The results were obtained using Ansys Fluent software and showed that low current pulsed GMA increases the high-temperature region of the weld pool. On the other hand, a multiphase model was presented by Zhou et al. (2023) and they described the dynamics of the synergy of the keyhole and vertical laser mirror weld puddle with the upward direction of an aluminum alloy. Mass transfer, fluid flow, VOF method, and the effect of heat by a hybrid heat source, i.e., a Gaussian distribution heat source and a volumetric taper source, were considered in the model. Also, Jabeen et al. (2023) presented the development of a 3D numerical model to determine the welding efficiency of a fiber-reinforced thermoplastic composite. In the model, ray tracing was considered to quantify the effect of light scattering patterns. The COMSOL Multiphysics software was used to perform the analysis and the effect of fiber orientation on the reflection and refraction of light transmission during the laser welding process was observed. They also performed the validation of the welding geometry with experimental results.
Studies with higher complexity involve multiphysical, multiphase, and thermo-mechanical or metallurgical models, to study or prevent the formation of porosity, grains, or subsequent defects during the laser welding process. Thus, the research conducted by Xia and Wang, (2023) studied the formation of porosity induced by a keyhole in oscillating laser T-joint welding. They also considered observing the influence of laser oscillation and angle of incidence. They presented a 3D numerical model through Flow 3D software. In that sense, Yin et al. (2023) established a transient 3D model for the weld puddle and keyhole. In this way, they investigated the morphology and distribution of porosities by employing laser mirror welding on an aluminum alloy. Laser heat input, metal surface vaporization, and conjugate heat transfer were considered. The results were validated with experimental data. The melt flow behavior permits the analysis of the porosity evolution in different regions of the medium-thickness plate. Also, Xia and Xiong. (2023) performed a numerical simulation of molten pool flow behavior and keyhole evolution. In the study, the authors proposed bilateral synchronous oscillating double laser beam welding and synchronous double laser beam welding, with the aim of avoiding porosity in T-joint welding. The results were validated with experimental data, demonstrating that porosity is reduced with bilateral synchronous oscillating dual-beam synchronous welding. Li et al. (2023) investigated the keyhole dynamics and pore formation mechanisms in the annular laser welding process for a thickened aluminum alloy. The authors performed a numerical experimental study. The numerical model was 3D, transient, and considered heat transfer, fluid flow, Marangoni effect, back pressure, and laser beam tracing. In the experimental results, they found that the porosity can be reduced by combining a heat source with an annular laser beam and a source with a Gaussian beam. The case study presented by Kamat et al. (2023) developed a multiphysics model integrated into the process of laser welding of thin films. The model considered evaporation, the VOF method, weld puddle dynamics, in-pool absorption, and multiple reflection. The authors considered the analysis of the welding process by means of CFD through Flow 3D software and obtained the weld dimensions that were compared with the experimental data. They then employed a finite element analysis model with MSC-Simufact software to evaluate the structural performance of the CFD-simulated weld. The study reported by Huang et al. (2023) describes a numerical and experimental methodology. In this regard, it studies the effect of laser oscillation on metal mixing and weld puddle microstructure during the welding process of aluminum and copper. The numerical study was developed through CFD with Flow 3D software and they implemented Scheil’s model to predict the phase distribution in the weld. An alternative for the phenomenon of grain growth was reported by Lu et al. (2023) who performed a transient numerical simulation of the thermal flow dynamics in the oscillating laser welding process, so when the oscillation frequency (f) increased from 20 to 200 Hz, the temperature gradient decreased from 1,518 to 1067 K/mm. In their case, Han et al. (2024a) presented a theoretical - numerical macro-scale study with Flow 3D Software. The multiphysical study considered heat and mass transfer as well as laser beam oscillation to analyze the evolution of equiaxial grains in a medium-thickness Al-Li alloy. They employed Gaussian-type axisymmetric distribution to simulate the heat source of the laser beam. Another study by Han et al. (2024b) developed a study based on a 3D multiscale model to determine the microstructure change in the molten pool during the solidification process of laser welding. Through the Flow 3D software, they incorporated a multiphase model (phase change), using the VOF technique to track the free surface. The simulation result permitted them to observe the distance of the columnar grain growth. The authors provided the information to avoid microstructure defects and grain region reduction. Also, Ai et al. (2024a) developed a model with solidification conditions in transient state considering the shape of the molten bath, to determine the microstructure and evolution of the grain to improve the quality of laser welding. In the study, they used a phase field model to calculate grain growth during laser welding of an aluminum alloy. Another work by Ai et al. (2024b) presented a multiphase numerical model to analyze the process of forming the coating layer during additive laser manufacturing. In this way, the dynamic behavior of the molten metal and the evolution of the free surface of the coating layer were discussed.
To determine this aspect of the phenomenon, several studies have reported the methods that have been used such as considering a porous medium interface solid between liquid (Piekarska and Kubiak, 2011; Piekarska and Kubiak, 2013), volume fractional (VOF), Level Step, and Arbitrary Lagrangian-Eulerian (ALE), among others, to determine tracking interface (Flint et al., 2022; Huang et al., 2023). Table 1 lists in general terms the considerations that describe the characteristics of the nature of the phenomenon, in order to obtain a particular mathematical model and define a modeling strategy.
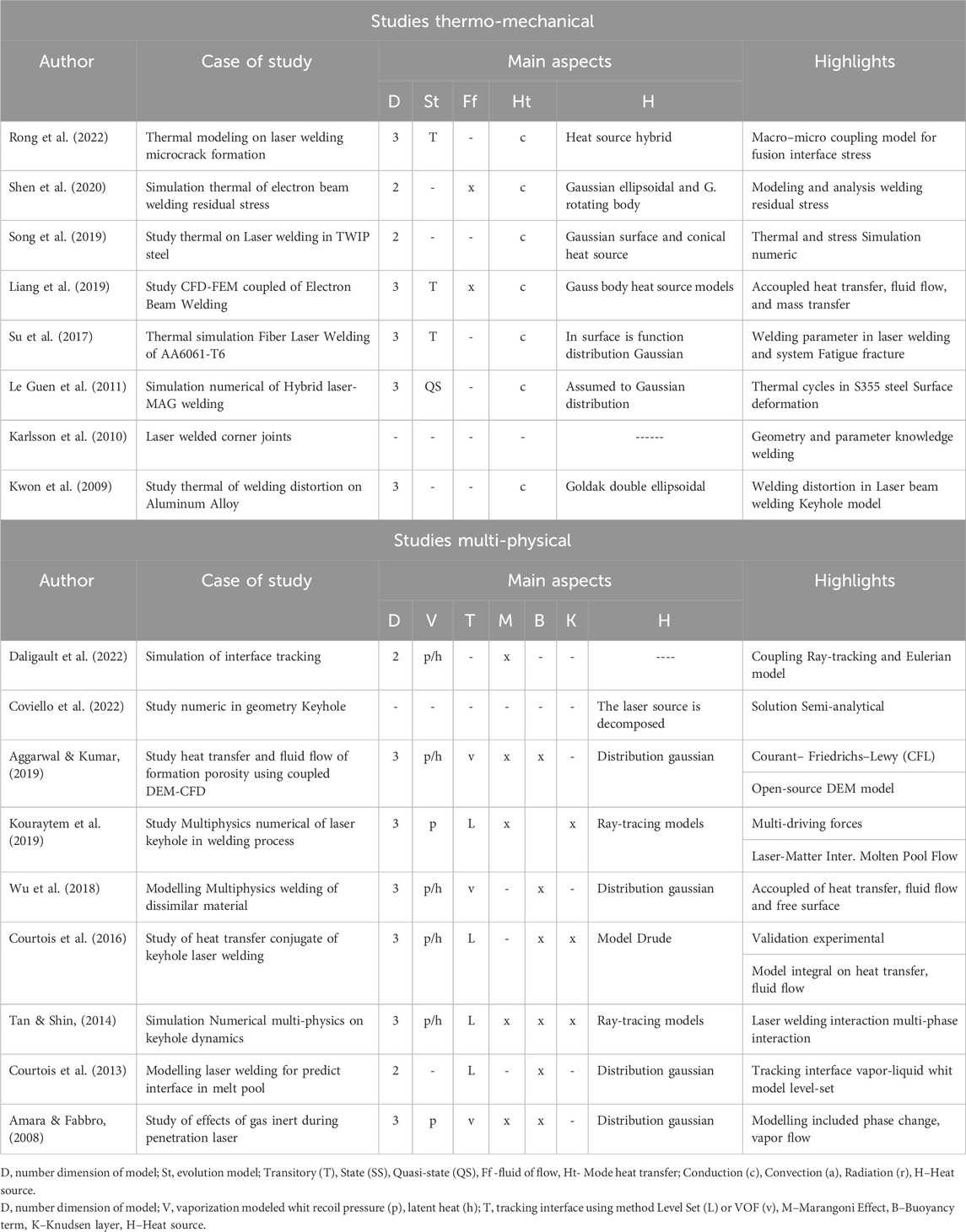
TABLE 1. Characteristics of the numerical simulations of thermo-mechanical and multi-physical studies.
The study performed by FEM or CFD represents the selected process considerations according to the laser welding application, however, they must provide the data of their results and information regarding the physics. In the welding process, the keyhole and the molten puddle present variations because of the welding speed and the cooling rate that does not permit the gas to escape completely by evaporation from the molten metal puddle. The formation of porosities in the weld are the defects that become cracks, therefore, research based on simulations to predict the deformations and residual stress, by means of process parameters, also involves the analysis of the microstructure and mechanical properties of the joint. If possible, some studies present an approach to fully integrate the attributes of the thermal field by coupling fluid dynamics with thermo-mechanical studies and determine the structural performance of the welded joint. In this way, they present data on residual stress and weld distortion by including aspects of weld puddle dynamics and keyhole evolution.
According to the discussion, the simulation according to its modeling strategy presents only conduction models and integral multi-physics models as a consequence of the multi-physical study through different CFD models. For both strategies, it is imperative to analyze the different laws that constitute them to consider the advantages or disadvantages of the model. Another aspect to analyze of the categorization in the simulations is the heat source models that have been used. In the literature, it is observed that Gaussian and double ellipsoidal distribution have been used in different simulations and even hybrid heat sources have been realized by joining two sources. It is important to know the details and justification for adopting this strategy.
This article lays the foundation for higher education students to embark on a journey of enhanced research skills and educational innovation in the realm of laser welding. By emphasizing the need for a structured classification and description of numerical simulations based on underlying physics, it provides a clear path for students to navigate the intricate world of laser welding modeling. The innovative approach of this review article not only facilitates a deeper understanding of the subject matter but also encourages students to embrace novel methodologies for comprehending complex topics, ultimately fostering their growth and proficiency in research skills within the field of laser welding.
3 Modeling of laser welding: Focus on model heat conduction and model integral multiphysics
There are two solution techniques for any type of phenomenon: experimental and theoretical. The first technique tries to reproduce the phenomenon of interest in its totality and looks for a way to do it under the same conditions, which becomes very complex due to the high cost of measurement equipment, problems of scale, and difficulty in the measurements. The other technique requires a mathematical interpretation of a physical system, which could be represented in its entirety or under certain considerations. This mathematical model is usually the solution of simple cases because it has certain restrictions such as geometry or linear phenomena. Within this technique, there are two categories, studies that are solved under an analytical solution and studies using mathematical modeling (numerical methods). This latter technique allows one to study and solve complex phenomena and obtain results in a short period of time, obtaining an approximate solution.
To develop the model of the laser welding phenomenon, it is important to remember as mentioned in previous sections that it depends entirely on the energy in which the process is performed and therefore the distribution or knowing the amount of energy required. So, it is only required to predict the temperature field in the medium during the process, because of the effects it has on the materials being joined. Then, to obtain this parameter, it is required to derive the heat diffusion equation (Villacis Ramón Mayra Elizabeth, 2022).
Then, considering a differential element in rectangular coordinates and in three dimensions, by means of the energy balance in Table 2, the relationship of the heat fluxes with the enthalpy change (E = TmCp) in the medium is expressed which is quantified by the internal energy. q(x,y,z,t) is the volumetric heat source and H(T) represents the change from solid to liquid or liquid to solid state. Convective and radiative flow are also considered as the heat lost by the medium. Finally, the expression of the conductive model is the general heat diffusion equation, for other authors the Fourier-Biot equation. This expression describes the amount of heat energy in a medium in a given period of time, i.e., the temperature of a medium as a function of time (transient).
The driving model was developed using a FEM where simulations are presented for stress, fatigue, distortion, and residual stress analysis induced by LBW and metallurgical phase transformations. Zhang X. et al. (2019) employed a FEM for thermal simulation during double-beam laser welding (transverse arrangement) to evaluate the effects of arrangement mode and laser power ratio. Also, Zain-ul-abdein et al. (2011) investigated the effect of residual stresses on metallurgical transformations in T-type joints for aircraft applications. Perulli et al. (2020) presented a FEM-based model for the thermo-mechanical study of stainless steel and dissimilarly evaluated metallurgical transformations for steel.
The advancement of computational modeling techniques allows for studying the thermo-mechanical/thermo-metallurgical problems of laser welding using the finite element technique (Deng et al., 2007; Barsoum and Lundbäck, 2009; Maekawa et al., 2013; Daneshgar and Daneshgar, 2016; Pu et al., 2017). The integral model is developed for the study of the laser welding phenomenon that contemplates other variables besides the temperature field.
Computational fluid dynamics allows the coupling of the physical phenomenon from the phase change of the materials, free surface, the effect of thermal capillarity, welding change by keyhole conduction, vaporization, ejection of the material, and chemical reactions. By means of the finite volume method (FVM), the Navier-Stokes equations coupled to the energy equation are solved. Table 3 expresses the governing equations used for the modeling. Tan et al. (2013) presented a transient and three-dimensional study to describe the dynamics in the keyhole, weld puddle, and vapor plume. They employed a model involving energy transport, hydrodynamics, and chemical species transport to analyze the aspect of metal vapor in the gas phase. Pang et al. (2011) investigated the keyhole and weld pool dynamics of laser welding through an integral model, coupling heat transfer, fluid flow, and keyhole-free surface. Of the works that can be considered complete because of the type of phenomena they consider is the one reported by Bayat et al. (2019), Bayat and Nadimpali, (2021) presents studies where the multi-physics model is integrated to conjugate heat transfer, multiphase flow, solidification/melting, evaporation, back pressure, capillary forces, Marangoni effect, buoyancy, and the effect of ray tracing. The versatility of the model allows it to address issues and elucidate conjectures about the phenomenon during the welding process. Zhou et al. (2023) analyze the keyhole dynamics by means of a three-dimensional multiphase model in a transient state that allowed them to accurately observe the evolution of the keyhole.
Since such case studies consider the relationships coupled to first equations, some authors include within their mathematical models the type of heat source, the input heat, laser power density, laser parameters, initial conditions, and boundary conditions, among others, since they depend entirely on the temperature field.
Laser welding research determines the temperature profile because temperature gradients and high cooling rates generate residual stress, which results in weld distortion. In order to determine an estimate of the weld joint stress, a thermo-elastic-plastics model is required since these models permit one to quantify the weld distortion caused by the energy caused by the fusion.
Therefore, it is important to perform research based on simulations to predict the deformations and residual stress, by means of process parameters, that also involves the analysis of the microstructure and mechanical properties of the joint.
Specifically, the research should analyze the fundamental physics driving fluid flow, heat transfer, metal mixing, and microstructure evolution during molten pool solidification. In laser welding, the keyhole and molten pool exhibit variations due to back pressure which can cause solidification behavior and microstructure evolution.
In this sense, the complexity of the model increases due to the multiscale aspects and in addition to computational fluid dynamics and thermo-mechanical analysis. Therefore, structural and morphological studies of laser welding must consider aspects of weld pool dynamics and keyhole evolution. In this way obtaining a more accurate model is only possible by performing a CFD study and including the volume of fluid (VOF) or next step (LS) model to observe the free flow surface necessary for the multiphase field, surface tension, evaporation, Marangoni force, and back pressure through which the oscillations in the weld puddle are caused and the keyhole is formed in addition to the laser-matter interaction, which in the case of deep penetration laser welding is by means of Fresnel absorption and multiple reflection.
4 Heat source model to simulate laser welding
The mathematical model of heat conduction considers the energy generation term, which represents the energy coming from the volumetric heat source and physically is the laser light beam on the material. The treatment and prediction of the heat source, in the LBW modeling or simulation, is of total importance, since knowing the temperature distribution is what will allow one to perform the thermo-mechanical and metallurgical analysis. In a case study, the material temperature allows one to determine the residual stress and distortion calculations. Therefore, the heat source is responsible for defining the temperature allocation in the melting zone and in the heat affected zone. Research on the heat source model dates back to the 1940s.
The particular interest in the treatment of the heat source in the laser welding process implies that any value cannot be considered randomly, but because the temperature field must be correctly predicted with certainty it is definitive that it must be done through a relationship or a value that allows the distribution of the heat density. Thus, over the years, heat source models have been developed initially as a heat source for the arc welding process, and subsequently, each model was adapted in order to use them in other welding processes, as in the case of laser welding. According to Kik (2020), it is possible to consider more than one model to describe the phenomenon of the heat source that gives rise to the weld pool. The typical models for the analysis of thermal cycles in welding modeling are the conical heat source model, Gaussian surface heat source model, and double ellipsoid heat source model. Such models are based on the general diffusion equation.
A pioneer in the field who developed a mathematical model was Rosenthal in 1941 (Näsström and Karlberg, 2014). From those years on, interest arose in modeling other welding processes, and the equation provided by Rosenthal, (1946) was used, where he defined the distribution of the welding power density. Initially, this theoretical development was generated for the arc welding process, however, in the research studies Rosenthal used a linear and point-type heat source. Also, Rykalin (1957) presented a model developed in an analytical way, where he made models for other processes since he considered the influence of the cooling rate on the mechanical properties of the welded parts. However, Pavelic et al. (1969) Friedman, (1975) was the first to develop a model different from the one presented by Rosenthal and Rykalin, since the author defined the heat source under a Gaussian distribution. Subsequently, a double ellipsoidal model for the heat source was developed and this model fits the weld pool geometry. This model was developed by Goldak et al. (1984), Goldak et al. (1986) and considered the displacement of the heat source based on functions describing the energy behavior during the process. In 1999, Jhon Dowden built a mathematical model for laser-assisted plasma arc welding, however, this model was limited in representing the evolution of the phenomenon over time Dowden (2001). Also, models of interest are those of Lukačević Z., (1998) and Samardžić I., (1996); the authors presented a mathematical model of an impulse heat source and a moving line heat source, respectively.
Stone et al. (2000) considered a heat source with a conical distribution combined with a Gaussian distribution with radial geometry. However, this has a uniform distribution and a double ellipsoidal heat source with a conical ellipse. Later, Nguyen et al. (2004) presented analytical transient state solutions for a semi-finite body through a moving heat source of semi-ellipsoidal and double ellipsoidal types. Some studies have considered modeling of the welding process for deep penetration, as in the case of electron beam welding and laser welding. Combining the double ellipsoidal with the elliptical cone yields a heat source suitable for modeling deep penetration processes such as electron beam welding. The model presented by Lundbäck & Runnemalm, (2005), had the versatility of combining the double ellipsoidal with the elliptical cone to obtain a heat source suitable for modeling deep penetration processes such as electron beam welding. This model estimates the fraction of heat (β) applied by each of the sources. A double ellipsoidal distribution model extended to a double elliptical conical heat distribution was proposed by Flint et al. (2017). This model calculates the temperature distribution in a transient regime and can be used for any type of welding. Based on the different models that exist, Figure 3 shows the timeline of the models that have been used for laser welding (Mokrov et al., 2019; Das et al., 2022).
Thus, it is possible to observe that there is a post-Rosenthal stage, where the model of the heat source has had a gradual change, allowing us to consider the geometry, the evolution in time, and the penetration of the power density, among other characteristics. This has allowed us to have a more complete model, i.e., greater accuracy in the calculations and an improvement in the development of the simulation of the laser welding phenomenon. So, it is possible to model from a point, linear, or flat heat source, for 1D, 2D, and 3D, respectively, to a volumetric heat source. Since the current studies use the volumetric heat source proposed by Goldak, it is due to the characteristics that relate each term of the mathematical model to the weld pool geometry and to the power density distribution shape.
The temperature field in a simulation for a given welding process is in essence the change of thermal energy in mechanical analysis. Put this way, the temperature field can be considered as a boundary condition where it can be calculated in a prescribed way or by a prescribed heat flux. If the prescribed temperature (Dirichlet condition) is considered in a simulation, it must be performed on the nodes and specific positions in the computational mesh domain. This method is used in 2D simulation and is the most common since the temperature increases linearly up to the prescribed value and remains constant. On the other hand, if a prescribed heat flow (Von Neumann condition) is considered, it is the most employed method at present, i.e., the input of the heat source in the simulation is performed in the same way on a specific position in the computational mesh. Therefore, the most commonly used heat source of this type has a Gaussian distribution and it must be considered that the source allows a distribution of the heat density. The double ellipsoidal model is considered a volumetric heat source since this model has two elliptical regions. Figure 4 shows the schematic of the double ellipsoidal model. This schematic shows the dimensions of the weld pool and the thermal gain and conceptualizes the dimensional aspect in which the energy enters through the arc or laser.
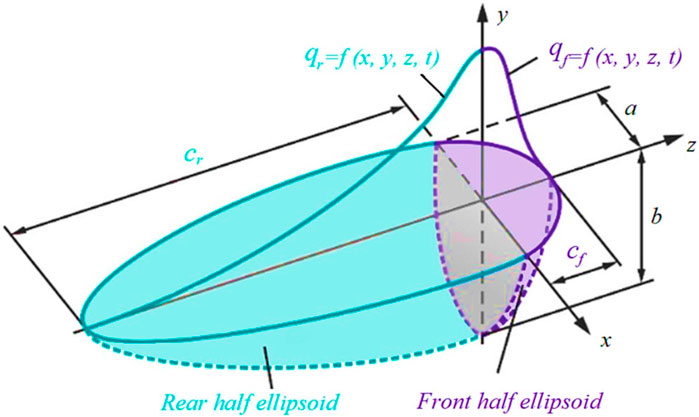
FIGURE 4. Geometric scheme of the Goldak model (Farahani et al., 2023) (The Figures are Under a Creative Commons license, Open Access).
Each of the terms has a relationship in the welding process, i.e., the term b represents half the width of the weld bead, c is the height of the bead. With a positive sense and in the direction of the z-axis should be expressed the welding speed, ws. af is the axis that represents the forward length of the weld in the front zone and the term ar represents the length in the rear zone of the weld bead while maintaining its speed. Finally, the goal is to obtain the value at the highest point of the ridge, since in that region is the energy flow required by the material to make the joint. The Goldak equation determines the energy flow with two calculations, one for the front region and the other for the back region (Goldak and Akhlaghi, 2005).
Therefore, the term qi in Eqs (1, (4 is the laser power intensity in order to determine the temperature distribution in the material. Goldak et al. describe that through computational mechanics of welding it is possible to optimize welding processes, for the modeling they used a moving double ellipsoid lateral heat source. Furthermore, it is possible to obtain an accurate temperature field by employing three heat sources for different aspects. On the surface of the medium, they used a double elliptical disk. To represent the incidence of the direct energy coming from the plasma arc they used a double ellipsoidal source and for the stirring effects of the liquid metal it was also possible to model by means of a double ellipsoidal heat source (Jhon and Mahyar, 2011). Another aspect to consider is that the geometric constants of the Goldak model must be chosen in order to correctly describe the most important zones, the melting zone and the heat affected zone. In the model, the function of the ellipse is to cause heat input for any point on the x, y, and z-axes, although it decreases in proportion as it moves away from the origin. Therefore, the maximum value of the input heat flux is reached when the position coordinates of the heat source are equal to zero (0, 0, 0, 0) (Andreas, 2000; Andreas, 2010). The Goldak model is a suitable model to represent the geometry of the weld pool as it can be considered as a moving heat source, which is why it involves the front and back of the weld bead, as well as the lengths.
5 CFD tool for engineering analysis
One way to solve engineering application problems is through numerical techniques, which, due to the great potential of computation, is a basis for analysis in any engineering discipline. Technological development has progressed in synergy with numerical techniques due to the use of computational tools. Fluid mechanics and energy transfer have been among the disciplines where an evolution in the development of computational tools has been observed since a branch known as computational fluid dynamics (CFD) emerged. CFD has the great advantage of being able to perform studies in a reliable way to improve the design of a process, avoiding the high costs of performing experiments. However, it requires experienced users with specialized training. CFD involves fluid mechanics, mathematics, and computational sciences since it numerically solves the equations of fluid motion in order to apply them to real problems.
There are three numerical techniques, finite difference, finite volume, and finite element, each with an application in the engineering field, although CFD is based on the finite volume technique or method. The need for the development of numerical codes that can be used in different applications or to solve multiple problems allowed the creation of specialized software. In 1981, PHOENICS software was released, and years later, in 1983, FLUENT software was launched (Xamán and Gijón-Rivera, 2015).
In the beginning, both tools only performed modeling under a structured computational domain. It was not until 1991 that FLUENT, with its great versatility, allowed the use of unstructured computational meshes. Thus, although applications have been developed that facilitate the use of the software, running a CFD project correctly requires experience. Figure 5 presents chronologically the commercially available programs developed for CFD.
Thus, with the development of CFD software and its incursion into the market, it has not only been considered for use in universities or research centers but it is already used in the industry. This same demand has caused an increase in the costs of licenses and permits for the use of the programs. So, one of the alternatives has been to follow the trend of using freely distributed numerical codes, under a scheme on the LINUX platform. One of the main precursors of this trend in the creation of free CFD codes is OpenCFD, which for several years has been operating under the C++ module scheme and under the name of OpenFOAM (Open Field Operation and Manipulation) (Fernández Oro, 2012; Stoevesandt et al., 2017).
Simulation of the weld pool through CFD is too complex to solve and largely remains an open problem. Most of the studies that have been reported where the laser welding process is modeled as a result of the joining of materials use the interaction of matter and energy. They use some software under a programming principle, but the software was made for the structural analysis process. Among this software are ABAQUS, CATIA, NX, SOLIDWORKS, and SYSWELD, which is commercial software only for welding. This commercial software has CFD integrated within their functions to perform the simulations, however, they are not CFD specialist software. A notable example is when the light beam is directed to a specific zone or point of the base material, a HAZ is defined, coming from the source, where the distortion due to the energy to achieve a higher penetration could be considered.
For this reason, defining this consideration or other characteristics to model the laser welding process, depending on the case study, is a reason to obtain the qualities of a case study that can complement the development of a more complete model that represents the laser welding phenomenon. Table 4 presents the case studies of laser welding modeling, in a systematic, synthesized, and chronological summary. Likewise, the categories that were observed in the studies were physical model, mathematical model, work descriptors, and case study, as well as whether it is a thermo-mechanical or multi-physical study and the type of software used in the simulation (Cho et al., 2012; Beiranvand et al., 2018; Cho et al., 2018; Ali et al., 2021; Ebrahimi et al., 2021; Halm et al., 2021; Ebrahimi et al., 2022; Examilioti et al., 2022; Jia et al., 2022; Mohan et al., 2022; Xue et al., 2022; Zhang et al., 2022).
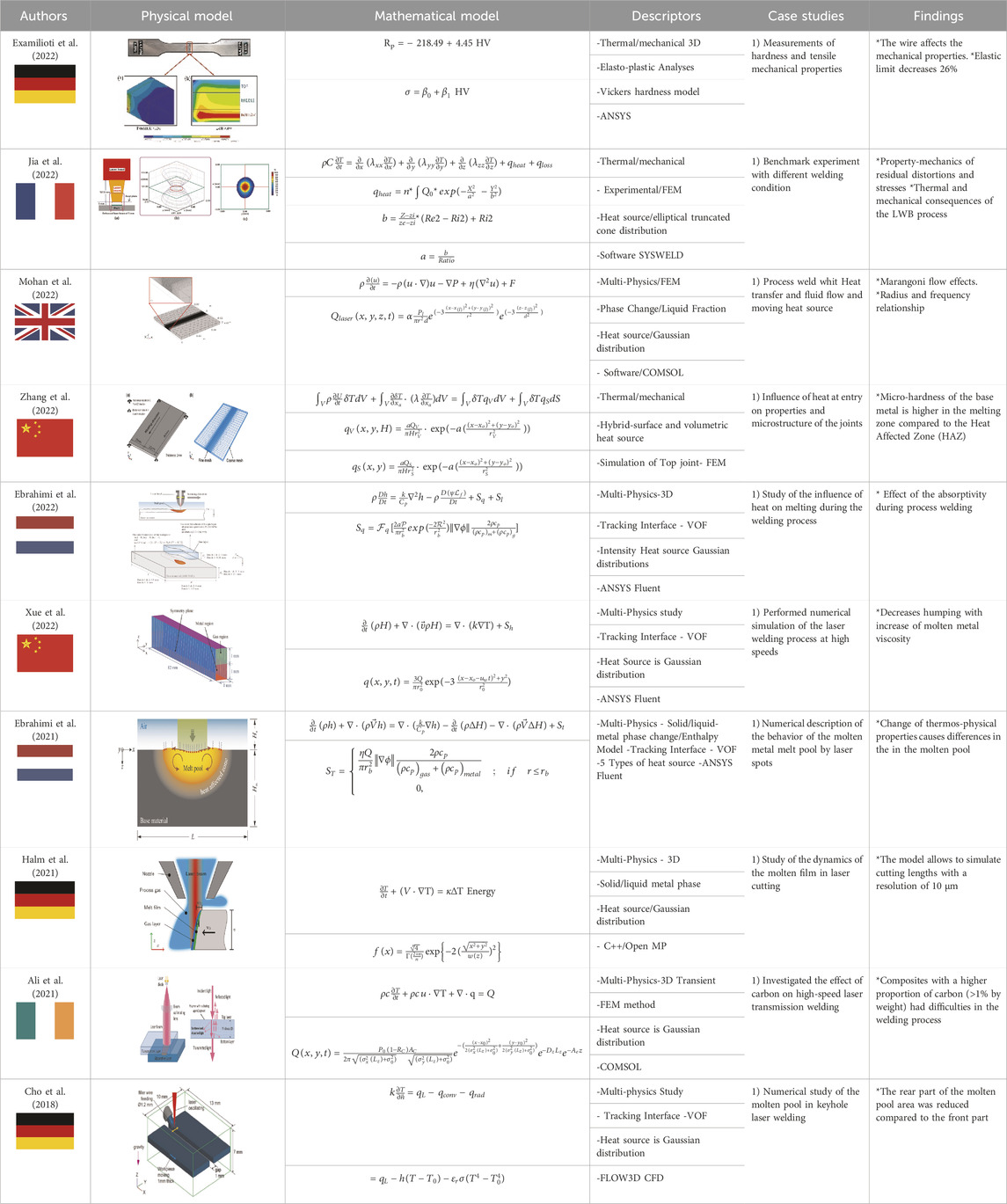
TABLE 4. Characteristics of the studies that consider the implementation of numerical methods in laser welding phenomenon. Note. The Table is authored by the main authors, but for the information it contains, all figures are under a Creative Commons license.
6 Discussion
This section briefly presents a discussion of the topics of interest on which the research work was based. Thermal analysis to know the temperature distribution, the heat flow behavior profile, and each thermal characteristic that allows one to perform an analysis of the material during the welding process are essential since the mechanical properties, distortion, and residual stresses are affected by the temperature field.
Therefore, through the thermal history of the weld, it is possible to maintain excellent quality. The most basic method for calculating the thermal field of welds is the Rosenthal method. However, the model is a point-type heat source, i.e., the energy in a geometric point under the concept of an instantaneous heat source. One of the problems with this type of model is that the properties have a dependence on temperature, therefore, the thermal properties vary with the temperature field of the infinite heat source and to avoid this variation reasonable average values are taken for the properties of materials and alloys.
The Rosenthal model assumes constant properties, which is why it cannot correctly predict the temperature field and because it is a point model, it only determines the temperature field in a geometric point, while physically in the welding phenomenon, the heat source interacts in the melting zone that makes up the weld pool. Therefore, being a point-type model, it presents errors when determining the temperature distribution field in the fusion zones and in the zone affected by the heat.
To consider a point source as opposed to a volumetric heat source is to consider the distribution of the heat source over an area or zone that is affected by the heat source. Such a low heat source distribution is defined by a double ellipsoidal model since this model allows the heat during the welding process to be similar to the weld puddle.
However, the improvement and achievement of a model that represents the distribution of temperature in the melting zone and in the heat-affected zone has been sought. From these works, Mokrov et al. (2019) present a heat source that shows a better agreement with the heat affected zone compared to other models. They defined it as Goldak-EHS. This model is a consideration of the metal flow within the weld pool where the power enters inside both quarter ellipsoids, from the front and the back of the bead, when the heat source advances. Another is the study by Azar (2015) which considers adding to Goldak’s model modular sinusoidal equations that simulate the variation of the geometrical characteristics of the weld pool as a function of time. Of the most recent, Trupiano et al. (2022) performed a study through a semi-analytical method and the authors determined the parameters of a double ellipsoidal heat source using an NSGA-II genetic algorithm.
The models that have been developed considering the prescribed temperature method and a prescribed heat flux may consider a simple methodology, but will not always be adequate, since temperature is the first property that must be obtained for any laser welding process, either by conduction or high penetration welding (Kou, 2022).
As long as the temperature field in the melt pool, melting zone, heat affected zone, and weld pool is impossible to obtain in experiments, it will be necessary to use the heat source models to determine the temperature profile. Therefore, it does not matter that the Goldak model has been used by many authors since 1984 (Xu et al., 2011; De Freitas Teixeira et al., 2014; Nezamdost et al., 2016; Chen et al., 2018; Nguyen and Chujutalli, 2021; Kiran et al., 2022; Villacís Ramón and Yaulema Castaneda, 2022). This model, with a double Gaussian ellipsoid distribution, is the one that best fits the weld pool.
7 Conclusion
The categorization of the simulation models for laser welding allows us to understand the aspects of the welding process. The first one is based on thermo-metallurgical and thermo-mechanical studies, the second one describes the studies from integrating energy transfer and fluid dynamics. Since this model does not consider fluid dynamics, then the phenomenon of convective heat transfer is not considered. The way to correct this restriction is through the heat source and the conductivity of the material. A volumetric heat source is the most commonly used, because, at the time of joining the materials, it is in the keyhole where the laser-material interaction occurs and the weld pool is formed. Therefore, a double ellipsoidal heat source has larger dimensions in the rear area than in the front area so it allows one to simulate the laser beam from the front to the back, thus representing the geometry of the melt pool. The mechanical calculation considers the estimation of elastic, thermal, and plastic deformation so that the total deformation is the sum of the deformations during the process. A finite element numerical approach allows the development of research studies and the software used for simulations such as ABAQUS (Cheon and Na, 2017; Beiranvand et al., 2018; Liang et al., 2018; Han et al., 2021; Farahani et al., 2023), SYSWELD, COMSOL Multiphysics (Bendaoud et al., 2014), Ansys (Xue et al., 2022), and Simufact (Perulli et al., 2020; Raftar et al., 2023). A bad development of this type of model would be not to consider the proper heat source in the thermo-mechanical and metallurgical simulation. While multi-physics integral models are complex, they allow the solving of multiple variables simultaneously during modeling and even allow one to observe the changes in the melt pool dynamics and keyhole geometry. Therefore, the authors considered the method of ray tracing to express the laser energy absorption of a material, the vaporization that creates the keyhole, and the hydrodynamics of the liquid and vapor flows. However, it is also possible to combine mechanics studies when using integral multiphysics models. The heat source due to pressure by considering the correct heat distribution by double ellipsoidal power density. The software used for the simulations such as SYSWELD (Saadlaoui et al., 2018), COMSOL-Multiphysics, Flow3D (Huang et al., 2020; Liu et al., 2020; Raza et al., 2023), Fluent (Zhang and Wu, 2015), Ansys (Acherjee, 2019; Acherjee, 2021c; Acherjee, 2022; Unni and Muthukumaran, 2022), CFDX, and the use of open source OpenFoam (Tang et al., 2020; Flint et al., 2022; Tang et al., 2022; Flint et al., 2023) through its compiler, have solved the fluid dynamics, evolution, and behavior of the keyhole geometry. Research is still lacking since the thermo-physical properties of the liquid and metal vapor are lacking. Also the considerations and mathematical manipulation to consider the turbulent flow phenomenon during the welding process involves a great challenge.
In the case of thermomechanical models based on FEM analysis, a thermal analysis is used under a heat conduction model which could be in a permanent or transient state, requiring predicting the temperature field to enter the temperature values in the stiffness matrix for mechanical or metallurgical study. In such a way, the study is carried out knowing the properties of the base material. This is unlike studies based on CFD methodology, which use the finite volume method since they are generally multiphase studies and, in some cases, involve mechanical or metallurgical studies. In these cases, a difficulty arises because the properties of the materials or alloys in the different phases are not available, that is, the properties of the material in the heat affected zone (welding bath) and the vapor expelled by the evaporation of the metal. Determining the properties in the process is a great challenge since considerations would not have to be made that limit the models and are considered accurate (Amara and Fabbro, 2008; Svenungsson et al., 2015; Dal and Fabbro, 2016; Kang et al., 2022).
In the case of mechanical and metallurgical studies, since the properties of the base material are not available, it is possible to carry out a characterization study of mechanical and microstructural properties, since thermal affectation is inevitable due to the operating parameters. In this sense, microstructural characterization is possible using optical microscopy, scanning electron microscopy, and electron backscattering diffraction. In this way, to identify the phases present in the welded joints and to carry out an evaluation of the mechanical properties of the weld, it is necessary to perform tension and microhardness type tests. Finally, an analysis of the thermal distribution in the material must be carried out and the synergy between the heat affected zones and the fusion zone under the FEM analysis must be determined.
During the mathematical modeling of the multiphysics phenomenon of laser welding, it is a challenge to know the properties of the material in its phase changes (liquid and vapor), so it is important to determine these properties using some calculation method that allows obtaining the properties with precision. Thus, the inverse heat transfer method is used. In general, the method consists of determining the temperature field or heat flow to estimate unknown quantities in the analysis of physical problems in engineering. The inverse conduction problem requires the calculation of an unknown heat flow in a medium, by estimating the temperature field close to the boundary of the medium and thus obtaining the precise value of the thermophysical properties. This condition of the method allows a focus on experiments close to real conditions, that is, the technical applications of the inverse method can encompass an estimation of the thermophysical properties of materials and control of the solid-liquid interface during a phase change. If it is not possible to use these alternatives, it is advisable to use a specific material and use the values of the properties reported in the literature.
In conclusion, this review article stands as a pivotal resource for higher education students seeking to elevate their research skills and drive educational innovation in the domain of laser welding. By offering a comprehensive overview of mathematical models and numerical simulations grounded in physics, it equips students with a solid understanding of this intricate subject. The innovative structuring and presentation of research findings within this article not only enhance the learning experience but also inspire students to adopt inventive approaches in their academic pursuits, empowering them to contribute to advancements in the field of laser welding.
Author contributions
MJ-X: Conceptualization, Data curation, Formal Analysis, Funding acquisition, Investigation, Methodology, Project administration, Resources, Software, Supervision, Validation, Visualization, Writing–original draft, Writing–review and editing. MH-H: Conceptualization, Investigation, Methodology, Project administration, Resources, Writing–review and editing. RT: Funding acquisition, Investigation, Methodology, Project administration, Resources, Supervision, Validation, Writing–review and editing. SL-D: Conceptualization, Data curation, Investigation, Methodology, Writing–original draft. MR-V: Conceptualization, Formal Analysis, Funding acquisition, Investigation, Methodology, Project administration, Writing–original draft, Writing–review and editing. AA-A: Conceptualization, Data curation, Methodology, Project administration, Resources, Writing–original draft. PC-A: Conceptualization, Data curation, Formal Analysis, Investigation, Methodology, Writing–original draft.
Funding
The author(s) declare financial support was received for the research, authorship, and/or publication of this article.
The authors would like to acknowledge the financial support of Writing Lab, Institute for the Future of Education, Tecnologico de Monterrey, Mexico, in the production of this work. The authors would like to acknowledge the financial support from Tecnologico de Monterrey through the “Challenge-Based Research Funding Program 2022”. Project ID # I003—IFE001—C2-T3—T.
The funder had no role in study design, data collection, analysis, decision to publish, or the preparation of the manuscript.
Acknowledgments
MJ-X acknowledges the support provided by the Consejo Nacional de Humanidades, Ciencia, y Tecnologías (CONAHCYT) given through its “Estancias Postdoctorales por Mexico-Iniciales” scholarship program.
Conflict of interest
The authors declare that the research was conducted in the absence of any commercial or financial relationships that could be construed as a potential conflict of interest.
Publisher’s note
All claims expressed in this article are solely those of the authors and do not necessarily represent those of their affiliated organizations, or those of the publisher, the editors and the reviewers. Any product that may be evaluated in this article, or claim that may be made by its manufacturer, is not guaranteed or endorsed by the publisher.
References
Acherjee, B. (2018). Hybrid laser arc welding: state-of-art review. Opt. Laser Technol. 99, 60–71. doi:10.1016/j.optlastec.2017.09.038
Acherjee, B. (2019). 3-D FE heat transfer simulation of quasi-simultaneous laser transmission welding of thermoplastics. J. Braz. Soc. Mech. Sci. Eng. 41 (10), 466. doi:10.1007/s40430-019-1969-3
Acherjee, B. (2020). Laser transmission welding of polymers – a review on process fundamentals, material attributes, weldability, and welding techniques. J. Manuf. Process. 60, 227–246. doi:10.1016/j.jmapro.2020.10.017
Acherjee, B. (2021a). Laser transmission welding of dissimilar plastics: 3-D FE modeling and experimental validation. Weld. World 65 (7), 1429–1440. doi:10.1007/s40194-021-01079-2
Acherjee, B. (2021b). Laser transmission welding of polymers – a review on welding parameters, quality attributes, process monitoring, and applications. J. Manuf. Process. 64, 421–443. doi:10.1016/j.jmapro.2021.01.022
Acherjee, B. (2021c). State-of-art review of laser irradiation strategies applied to laser transmission welding of polymers. Opt. Laser Technol. 137, 106737. doi:10.1016/j.optlastec.2020.106737
Acherjee, B. (2022). Numerical study of thermo-mechanical responses in laser transmission welding of polymers using a 3-D thermo-elasto-viscoplastic FE model. Weld. World 66 (7), 1421–1435. doi:10.1007/s40194-022-01300-w
Aggarwal, A., and Kumar, A. (2019). “Particle scale modelling of porosity formation during selective laser melting process using a coupled DEM - CFD approach,” in IOP Conference Series: Materials Science and Engineering, Salzburg, Austria, 17–21 June 2019. doi:10.1088/1757-899X/529/1/012001
Ai, Y., Dong, G., Yuan, P., Liu, X., and Yan, Y. (2023). The influence of keyhole dynamic behaviors on the asymmetry characteristics of weld during dissimilar materials laser keyhole welding by experimental and numerical simulation methods. Int. J. Therm. Sci. 190, 108289. doi:10.1016/j.ijthermalsci.2023.108289
Ai, Y., Han, S., and Yan, Y. (2024). An interpolation-based transient solidification conditions model for numerical calculation of grain growth during laser welding. Therm. Sci. Eng. Prog. 47, 102259. doi:10.1016/j.tsep.2023.102259
Ai, Y., Yan, Y., Yuan, P., and Wang, Y. (2024). The numerical investigation of cladding layer forming process in laser additive manufacturing with wire feeding. Int. J. Therm. Sci. 196, 108669. doi:10.1016/j.ijthermalsci.2023.108669
Ali, M. M., Dave, F., Sherlock, R., Mcilhagger, A., and Tormey, D. (2021). Simulated effect of carbon black on high speed laser transmission welding of polypropylene with low line energy. Front. Mater. 8. doi:10.3389/fmats.2021.737689
Alter, L., Heider, A., and Bergmann, J. P. (2018). Investigations on copper welding using a frequency-doubled disk laser and high welding speeds. Procedia CIRP 24, 12–16. doi:10.1016/j.procir.2018.08.003
Amara, E. H., and Fabbro, R. (2008). Modelling of gas jet effect on the melt pool movements during deep penetration laser welding. J. Phys. D Appl. Phys. 41 (5), 055503. doi:10.1088/0022-3727/41/5/055503
Amara, E. H., Fabbro, R., and Bendib, A. (2003). Modeling of the compressible vapor flow induced in a keyhole during laser welding. J. Appl. Phys. 93 (7), 4289–4296. doi:10.1063/1.1557778
Andreas, L. (2000). “Modelling of weld path for use in simulations,” (Oman: University of Technology). Master.
Andreas, L. (2010). “Modelling and simulation of welding and metal deposition,” (Oman: University of Technology). Doctoral.
Azar, A. S. (2015). A heat source model for cold metal transfer (CMT) welding. J. Therm. Analysis Calorim. 122 (2), 741–746. doi:10.1007/s10973-015-4809-4
Azizpour, M., Ghoreishi, M., and Khorram, A. (2015). Numerical simulation of laser beam welding of Ti6Al4V sheet. J. Comput. Appl. Res. Mech. Eng. 4 (2). doi:10.22061/jcarme.2015.272
Barsoum, Z., and Lundbäck, A. (2009). Simplified FE welding simulation of fillet welds - 3D effects on the formation residual stresses. Eng. Fail. Anal. 16 (7), 2281–2289. doi:10.1016/j.engfailanal.2009.03.018
Bayat, M., Dong, W., Thorborg, J., To, A. C., and Hattel, J. H. (2021). A review of multi-scale and multi-physics simulations of metal additive manufacturing processes with focus on modeling strategies. Addit. Manuf. 47, 102278. doi:10.1016/j.addma.2021.102278
Bayat, M., Mohanty, S., and Hattel, J. H. (2019). Multiphysics modelling of lack-of-fusion voids formation and evolution in IN718 made by multi-track/multi-layer L-PBF. Int. J. Heat Mass Transf. 139, 95–114. doi:10.1016/j.ijheatmasstransfer.2019.05.003
Bayat, M., Nadimpalli, V. K., Pedersen, D. B., and Hattel, J. H. (2021). A fundamental investigation of thermo-capillarity in laser powder bed fusion of metals and alloys. Int. J. Heat Mass Transf. 166, 120766. doi:10.1016/j.ijheatmasstransfer.2020.120766
Bedenko, D. V., Kovalev, O. B., and Krivtsun, I. V. (2010). Simulation of plasma dynamics in a keyhole during laser welding of metal with deep penetration. J. Phys. D Appl. Phys. 43 (10), 105501. doi:10.1088/0022-3727/43/10/105501
Beiranvand, Z. M., Ghaini, F. M., Naffakh-moosavy, H., Sheikhi, M., and Torkamany, M. J. (2018). Magnesium loss in Nd:YAG pulsed laser welding of aluminum alloys. Metallurgical Mater. Trans. B Process Metallurgy Mater. Process. Sci. 49 (5), 2896–2905. doi:10.1007/s11663-018-1315-7
Bendaoud, I., Matteï, S., Cicala, E., Tomashchuk, I., Andrzejewski, H., Sallamand, P., et al. (2014). The numerical simulation of heat transfer during a hybrid laser–MIG welding using equivalent heat source approach. Opt. Laser Technol. 56, 334–342. doi:10.1016/j.optlastec.2013.09.007
Chen, C., Lin, Y. J., Ou, H., and Wang, Y. (2018). Study of heat source calibration and modelling for laser welding process. Int. J. Precis. Eng. Manuf. 19 (8), 1239–1244. doi:10.1007/s12541-018-0146-4
Cheon, J., and Na, S.-J. (2017). Prediction of welding residual stress with real-time phase transformation by CFD thermal analysis. Int. J. Mech. Sci. 131 (132), 37–51. doi:10.1016/j.ijmecsci.2017.06.046
Chianese, G., Hayat, Q., Jabar, S., Franciosa, P., Ceglarek, D., and Patalano, S. (2023). A multi-physics CFD study to investigate the impact of laser beam shaping on metal mixing and molten pool dynamics during laser welding of copper to steel for battery terminal-to-casing connections. J. Mater. Process. Technol. 322, 118202. doi:10.1016/j.jmatprotec.2023.118202
Chianese, G., Jabar, S., Franciosa, P., Ceglarek, D., and Patalano, S. (2022). A multi-physics CFD study on the part-to-part gap during remote laser welding of copper-to-steel battery tab connectors with beam wobbling. Procedia CIRP 111, 484–489. doi:10.1016/j.procir.2022.08.075
Cho, J. H., Farson, D. F., Milewski, J. O., and Hollis, K. J. (2009). Weld pool flows during initial stages of keyhole formation in laser welding. J. Phys. D Appl. Phys. 42 (17), 175502. doi:10.1088/0022-3727/42/17/175502
Cho, W. I., Na, S. J., Thomy, C., and Vollertsen, F. (2012). Numerical simulation of molten pool dynamics in high power disk laser welding. J. Mater. Process. Technol. 212 (1), 262–275. doi:10.1016/j.jmatprotec.2011.09.011
Cho, W. I., Woizeschke, P., and Schultz, V. (2018). Simulation of molten pool dynamics and stability analysis in laser buttonhole welding. Procedia CIRP 74, 687–690. doi:10.1016/j.procir.2018.08.042
Chuang, T.-C., Lo, Y. L., Tran, H. C., Tsai, Y. A., Chen, C. Y., and Chiu, C. P. (2023). Optimization of Butt-joint laser welding parameters for elimination of angular distortion using High-fidelity simulations and Machine learning. Opt. Laser Technol. 167, 109566. doi:10.1016/j.optlastec.2023.109566
Courtois, M., Carin, M., Le Masson, P., and Gaied, S. (2013). A two-dimensional axially-symmetric model of keyhole and melt pool dynamics during spot laser welding. Rev. Metall. Cah. D’Informations Tech. 110 (2), 165–173. doi:10.1051/metal/2013060
Courtois, M., Carin, M., Le Masson, P., Gaied, S., and Balabane, M. (2016). Guidelines in the experimental validation of a 3D heat and fluid flow model of keyhole laser welding. J. Phys. D Appl. Phys. 49, 155503. doi:10.1088/0022-3727/49/15/155503
Courtois, M., Carin, M., Masson, P. L., Gaied, S., and Balabane, M. (2013). A new approach to compute multi-reflections of laser beam in a keyhole for heat transfer and fluid flow modelling in laser welding. J. Phys. D Appl. Phys. 46 (50), 505305. doi:10.1088/0022-3727/46/50/505305
Coviello, D., D’Angola, A., and Sorgente, D. (2022). Numerical study on the influence of the plasma properties on the keyhole geometry in laser beam welding. Front. Phys. 9. doi:10.3389/fphy.2021.754672
Cunningham, R., Zhao, C., Parab, N., Kantzos, C., Pauza, J., Fezzaa, K., et al. (2019). Keyhole threshold and morphology in laser melting revealed by ultrahigh-speed x-ray imaging. Science 363 (6429), 849–852. doi:10.1126/science.aav4687
Dal, M., and Fabbro, R. (2016). [INVITED] an overview of the state of art in laser welding simulation. Opt. Laser Technol. 78, 2–14. doi:10.1016/j.optlastec.2015.09.015
Daligault, J., Dal, M., Gorny, C., Coste, F., and Fabbro, R. (2022). Combination of Eulerian and ray-tracing approaches for copper laser welding simulation. J. Laser Appl. 34 (4). doi:10.2351/7.0000786
Daneshgar, M. R., and Daneshgar, S. E. H. E. D. A. (2016). Analysis of residual stresses and angular distortion in stiffened cylindrical shell fillet welds using finite element method. Int. J. Civ. Environ. Eng. 10, 538–548. doi:10.5281/zenodo.112464910.5281/zenodo.1124649
Das, A., Kumar, A., Shankhwar, K., and Gubeljak, N. (2022). A review of heat source and resulting temperature distribution in arc welding. J. Therm. Analysis Calorim. 147, 12975–13010. doi:10.1007/s10973-022-11589-w
Dave, F., Ali, M. M., Sherlock, R., Kandasami, A., and Tormey, D. (2021). Laser transmission welding of semi-crystalline polymers and their composites: a critical review. Polymers 13, 675. doi:10.3390/polym13050675
De Azevedo, A. M., Magalhães, E. d. S., da Silva, R. G. D., and Lima e Silva, S. M. M. d. (2022). A comparison between nonlinear and constant thermal properties approaches to estimate the temperature in LASER welding simulation. Case Stud. Therm. Eng. 35, 102135. doi:10.1016/j.csite.2022.102135
De Freitas Teixeira, P. R., De Araújo, D. B., and Da Cunha, L. A. B. (2014). Study of the Gaussian distribution heat source model applied to numerical thermal simulations of tig welding processes. Ciencia y Engenharia/Sci. Eng. J. 23 (1), 115–122. doi:10.14393/19834071.2014.26140
Deng, D., Liang, W., and Murakawa, H. (2007). Determination of welding deformation in fillet-welded joint by means of numerical simulation and comparison with experimental measurements. J. Mater. Process. Technol. 183 (2–3), 219–225. doi:10.1016/j.jmatprotec.2006.10.013
Dowden, J. M. (2001). The mathematics of thermal modeling: an introduction to the theory of laser material processing, the Mathematics of Thermal Modeling: an Introduction to the Theory of Laser Material Processing. Taylor and Francis. Available at: https://www.taylorfrancis.com/books/mono/10.1201/9781420035629/mathematics-thermal-modeling-john-michael-dowden.
Ebrahimi, A., and Hermans, M. J. M. (2023). Laser butt welding of thin stainless steel 316L sheets in asymmetric configurations: a numerical study. J. Adv. Join. Process. 8, 100154. doi:10.1016/j.jajp.2023.100154
Ebrahimi, A., Kleijn, C. R., and Richardson, I. M. (2021). Numerical study of molten metal melt pool behaviour during conduction-mode laser spot melting. J. Phys. D Appl. Phys. 54 (10), 105304. doi:10.1088/1361-6463/abca62
Ebrahimi, A., Sattari, M., Bremer, S. J., Luckabauer, M., Römer, G. w. R., Richardson, I. M., et al. (2022). The influence of laser characteristics on internal flow behaviour in laser melting of metallic substrates. Mater. Des. 214, 110385. doi:10.1016/j.matdes.2022.110385
Examilioti, T. N., Papanikos, P., Kashaev, N., Klusemann, B., and Alexopoulos, N. D. (2022). Experimental and numerical investigation of laser beam-welded Al–Cu–Li joints using micro-mechanical characteristics. J. Mater. Res. Technol. 19, 2431–2446. doi:10.1016/j.jmrt.2022.05.197
Fabbro, R. (2020). Depth dependence and keyhole stability at threshold, for different laser welding regimes. Appl. Sci. Switz. 10 (4), 1487. doi:10.3390/app10041487
Fan, X., Qin, G., Jiang, Z., and Wang, H. (2023). Comparative analysis between the laser beam welding and low current pulsed GMA assisted high-power laser welding by numerical simulation. J. Mater. Res. Technol. 22, 2549–2565. doi:10.1016/j.jmrt.2022.12.116
Farahani, E. B., Sarhadi, A., Alizadeh-Sh, M., Fæster, S., Danielsen, H., and Eder, M. (2023). Thermomechanical modeling and experimental study of a multi-layer cast iron repair welding for weld-induced crack prediction. J. Manuf. Process. 104, 443–459. doi:10.1016/j.jmapro.2023.08.059
Feng, G., Wang, Y., Luo, W., Hu, L., and Deng, D. (2021). Comparison of welding residual stress and deformation induced by local vacuum electron beam welding and metal active gas arc welding in a stainless steel thick-plate joint. J. Mater. Res. Technol. 13. doi:10.1016/j.jmrt.2021.05.105
Fernández Oro, J. M. (2012). Técnicas Numéricas en Ingeniería de Fluidos. First Edition. Spain: Reverte.
Flint, T. F., Anderson, M., Akrivos, V., Roy, M., Francis, J., Vasileiou, A., et al. (2022). A fundamental analysis of factors affecting chemical homogeneity in the laser powder bed fusion process. Int. J. Heat Mass Transf. 194, 122985. doi:10.1016/j.ijheatmasstransfer.2022.122985
Flint, T. F., Dutilleul, T., and Kyffin, W. (2023). A fundamental investigation into the role of beam focal point, and beam divergence, on thermo-capillary stability and evolution in electron beam welding applications. Int. J. Heat Mass Transf. 212, 124262. doi:10.1016/j.ijheatmasstransfer.2023.124262
Flint, T. F., Francis, J., Smith, M., and Balakrishnan, J. (2017). Extension of the double-ellipsoidal heat source model to narrow-groove and keyhole weld configurations. J. Mater. Process. Technol. 246, 123–135. doi:10.1016/j.jmatprotec.2017.02.002
Flint, T. F., Parivendhan, G., Ivankovic, A., Smith, M. C., and Cardiff, P. (2022). beamWeldFoam: numerical simulation of high energy density fusion and vapourisation-inducing processes. SoftwareX 18, 101065. doi:10.1016/j.softx.2022.101065
Friedman, E. (1975). Thermomechanical analysis of the welding process using the finite element method. J. Press. Vessel Technol. Trans. ASME 97 (3), 206–213. doi:10.1115/1.3454296
Gao, Z., Jiang, P., Mi, G., Cao, L., and Liu, W. (2018). Investigation on the weld bead profile transformation with the keyhole and molten pool dynamic behavior simulation in high power laser welding. Int. J. Heat Mass Transf. 116, 1304–1313. doi:10.1016/j.ijheatmasstransfer.2017.09.122
Ghosh, P. S., Sen, A., Chattopadhyaya, S., Sharma, S., Singh, J., Dwivedi, S. P., et al. (2021). Prediction of transient temperature distributions for laser welding of dissimilar metals. Appl. Sci. Switz. 11 (13), 5829. doi:10.3390/app11135829
Giudice, F., Missori, S., and Sili, A. (2021). Parameterized multipoint-line analytical modeling of a mobile heat source for thermal field prediction in laser beam welding. Int. J. Adv. Manuf. Technol. 112 (5–6), 1339–1358. doi:10.1007/s00170-020-06479-0
Giudice, F., and Sili, A. (2022). A theoretical approach to the residual stress assessment based on thermal field evaluation in laser beam welding. Int. J. Adv. Manuf. Technol. 123 (7–8), 2793–2808. doi:10.1007/s00170-022-10247-7
Goldak, J., Bibby, M., Moore, J., House, R., and Patel, B. (1986). Computer modeling of heat flow in welds. Metall. Trans. B 17 (3), 587–600. doi:10.1007/BF02670226
Goldak, J., Chakravarti, A., and Bibby, M. (1984). A new finite element model for welding heat sources. Metall. Trans. B 15 (2), 299–305. doi:10.1007/BF02667333
Goldak, J. A., and Akhlaghi, M. (2005) Computational welding mechanics, computational welding mechanics. doi:10.1007/b101137
Guo, S., Zou, J., Xu, J., Wu, Q., and Xiao, R. (2021). Multi-stage keyhole evolution in fiber laser welding: an experimental study and theoretical analysis. Results Phys. 31, 104943. doi:10.1016/j.rinp.2021.104943
Halm, U., Nießen, M., and Schulz, W. (2021). Simulation of melt film dynamics in laser fusion cutting using a boundary layer approximation. Int. J. Heat Mass Transf. 168, 120837. doi:10.1016/j.ijheatmasstransfer.2020.120837
Han, C., Jiang, P., Geng, S., and Ren, L. (2024). Multi-physics multi-scale simulation of unique equiaxed-to-columnar-to-equiaxed transition during the whole solidification process of Al-Li alloy laser welding. J. Mater. Sci. Technol. 171, 235–251. doi:10.1016/j.jmst.2023.05.077
Han, C., Jiang, P., Geng, S., Ren, L., and Jin, J. (2024). Ultra grain refinement and mechanical properties improvement of all-weld-metal for medium-thick Al-Li alloy via laser beam oscillation and in-situ alloying. Opt. Laser Technol. 168, 109965. doi:10.1016/j.optlastec.2023.109965
Han, S.-W., Cho, W. I., Zhang, L. J., and Na, S. J. (2021). Coupled simulation of thermal-metallurgical-mechanical behavior in laser keyhole welding of AH36 steel. Mater. Des. 212, 110275. doi:10.1016/j.matdes.2021.110275
Huang, B., Chen, X., Pang, S., and Hu, R. (2017). A three-dimensional model of coupling dynamics of keyhole and weld pool during electron beam welding. Int. J. Heat Mass Transf. 115, 159–173. doi:10.1016/j.ijheatmasstransfer.2017.08.010
Huang, S., Xu, L., Lou, M., Chen, H., Zhang, K., and Li, Y. (2023). Keyhole-induced pore formation mechanism in laser-MIG hybrid welding of aluminum alloy based on experiment and multiphase numerical model. J. Mater. Process. Technol. 314, 117903. doi:10.1016/j.jmatprotec.2023.117903
Huang, W., Cai, W., Rinker, T. J., Bracey, J., and Tan, W. (2023). Effects of laser oscillation on metal mixing, microstructure, and mechanical property of Aluminum–Copper welds. Int. J. Mach. Tools Manuf. 188, 104020. doi:10.1016/j.ijmachtools.2023.104020
Huang, W., Wang, H., Rinker, T., and Tan, W. (2020). Investigation of metal mixing in laser keyhole welding of dissimilar metals. Mater. Des. 195, 109056. doi:10.1016/j.matdes.2020.109056
Jabeen, R., Cosson, B., Akué Asséko, A. C., Verstraete, S., Desplentere, F., and Park, C. H. (2023). Effect of fibre orientation on the light scattering during laser transmission welding. J. Manuf. Process. 86, 1–9. doi:10.1016/j.jmapro.2022.12.042
Jhon, G., and Mahyar, A. (2011). Computational weld mechanics and optimization of welding procedures, welds and welded structures. Trans. Join. Weld. Res. Inst. Osaka Univ. 2011, 55–60. doi:10.18910/23067
Jia, Y., Saadlaoui, Y., Hamdi, H., Sijobert, J., Roux, J. C., and Bergheau, J. M. (2022). An experimental and numerical case study of thermal and mechanical consequences induced by laser welding process. Case Stud. Therm. Eng. 35, 102078. doi:10.1016/j.csite.2022.102078
Jiang, M., Wu, H., An, Y., Hou, T., Chang, Q., Huang, L., et al. (2022). Fiber laser development enabled by machine learning: review and prospect. PhotoniX 3, 16. doi:10.1186/s43074-022-00055-3
Kamat, S., Cai, W., Rinker, T. J., Bracey, J., Xi, L., and Tan, W. (2023). A novel integrated process-performance model for laser welding of multi-layer battery foils and tabs. J. Mater. Process. Technol. 320, 118121. doi:10.1016/j.jmatprotec.2023.118121
Kang, Y., Zhao, Y., Li, Y., Wang, J., and Zhan, X. (2022). Simulation of the effect of keyhole instability on porosity during the deep penetration laser welding process. Metals 12 (7), 1200. doi:10.3390/met12071200
Karlson, K. N., Skulborstad, A. J., Madison, J. D., Polonsky, A. T., Jin, H., Jones, A., et al. (2023). Toward accurate prediction of partial-penetration laser weld performance informed by three-dimensional characterization – Part II: μCT based finite element simulations. Tomogr. Mater. Struct. 2, 100007. doi:10.1016/j.tmater.2023.100007
Karlsson, J., Markmann, C., Minhaj Alam, M., and Kaplan, A. F. (2010). Parameter influence on the laser weld geometry documented by the Matrix Flow Chart. Phys. Procedia 5, 183–192. doi:10.1016/j.phpro.2010.08.043
Kik, T. (2020). Heat source models in numerical simulations of laser welding. Materials 13 (11), 2653. doi:10.3390/ma13112653
Kiran, A., Li, Y., Hodek, J., Brázda, M., Urbánek, M., and Džugan, J. (2022). Heat source modeling and residual stress analysis for metal directed energy deposition additive manufacturing. Materials 15 (7), 2545. doi:10.3390/ma15072545
Kou, S. (2002). Welding metallurgy. 1st ed. United States: John Wiley and Sons, Inc. doi:10.1002/0471434027
Kouraytem, N., Li, X., Cunningham, R., Zhao, C., Parab, N., Sun, T., et al. (2019). Effect of laser-matter interaction on molten pool flow and keyhole dynamics. Phys. Rev. Appl. 11 (6), 064054. doi:10.1103/PhysRevApplied.11.064054
Kwon, K.-B., Kim, J.-W., and Kim, C.-H. (2009). Analysis of welding distortion for laser welded sheet metal structures of aluminum alloy. J. Korean Weld. Join. Soc. 27 (3), 44–51. doi:10.5781/kwjs.2009.27.3.044
Le Guen, E., Carin, M., Fabbro, R., Coste, F., and Le Masson, P. (2011). 3D heat transfer model of hybrid laser Nd:Yag-MAG welding of S355 steel and experimental validation. Int. J. Heat Mass Transf. 54 (7–8), 1313–1322. doi:10.1016/j.ijheatmasstransfer.2010.12.010
Li, J., Jiang, P., Geng, S., and Xiong, J. (2023). Numerical and experimental study on keyhole dynamics and pore formation mechanisms during adjustable-ring-mode laser welding of medium-thick aluminum alloy. Int. J. Heat Mass Transf. 214, 124443. doi:10.1016/j.ijheatmasstransfer.2023.124443
Li, L., Peng, G., Wang, J., Gong, J., and Meng, S. (2019). Numerical and experimental study on keyhole and melt flow dynamics during laser welding of aluminium alloys under subatmospheric pressures. Int. J. Heat Mass Transf. 133, 812–826. doi:10.1016/j.ijheatmasstransfer.2018.12.165
Li, Y., Wang, Y., Yin, X., and Zhang, Z. (2023). Laser welding simulation of large-scale assembly module of stainless steel side-wall. Heliyon 9 (3), e13835. doi:10.1016/j.heliyon.2023.e13835
Liang, L., Hu, R., Wang, J., Luo, M., Huang, A., Wu, B., et al. (2019). A CFD-FEM model of residual stress for electron beam welding including the weld imperfection effect. Metallurgical Mater. Trans. A Phys. Metallurgy Mater. Sci. 50 (5), 2246–2258. doi:10.1007/s11661-019-05154-8
Liang, R., Luo, Y., and Li, Z. (2018). The effect of humping on residual stress and distortion in high-speed laser welding using coupled CFD-FEM model. Opt. Laser Technol. 104, 201–205. doi:10.1016/j.optlastec.2018.02.024
Lienert, T. (2011). “Laser beam welding[1],” in Welding fundamentals and processes (United States: ASM International), 556–569. doi:10.31399/asm.hb.v06a.a0005641
Liu, B., Fang, G., Lei, L., and Liu, W. (2020). A new ray tracing heat source model for mesoscale CFD simulation of selective laser melting (SLM). Appl. Math. Model. 79, 506–520. doi:10.1016/j.apm.2019.10.049
Liu, S., Mi, G., Yan, F., Wang, C., and Li, P. (2018). Real weld geometry determining mechanical properties of high power laser welded medium plates. Opt. Laser Technol. 102, 100–110. doi:10.1016/j.optlastec.2017.11.047
Liu, Y., Zhang, Y., Guo, Z., and Lu, W. (2023). ‘Effect of laser power, speed and offset on the welding performance of 304 SS/Al2O3 ceramics’, Ceramics International [Preprint]. doi:10.1016/j.ceramint.2023.11.289
Lu, Y., Deng, Y., Shi, L., Jiang, L., and Gao, M. (2023). Numerical simulation of thermal flow dynamics in oscillating laser welding of aluminum alloy. Opt. Laser Technol. 159, 109003. doi:10.1016/j.optlastec.2022.109003
Lukačević, Z. Z. (1998). Welding book. Croatia. Slavonski Brod: Faculty of Mechanical Engineering, University of Slavonski Brod. Available at: https://www.croris.hr/crosbi/publikacija/rad-ostalo/741007.
Lundbäck, A., and Runnemalm, H. (2005). Validation of three-dimensional finite element model for electron beam welding of Inconel 718. Sci. Technol. Weld. Join. 10 (6), 717–724. doi:10.1179/174329305X48347
Mackwood, A. P., and Crafer, R. C. (2005). Thermal modelling of laser welding and related processes: a literature review. Opt. Laser Technol. 37 (2), 99–115. doi:10.1016/j.optlastec.2004.02.017
Maekawa, A., Serizawa, H., Nakacho, K., and Murakawa, H. (2013). Fast finite element analysis of weld residual stress in large-diameter thick-walled stainless steel pipe joints and its experimental validation. Yosetsu Gakkai Ronbunshu/Quarterly J. Jpn. Weld. Soc. 31 (4), 129s–133s. doi:10.2207/qjjws.31.129s
Meng, X. (2020). Numerical study of additional element transport in wire feed laser beam welding. Procedia CIRP 94, 722–725. doi:10.1016/j.procir.2020.09.129
Miyamoto, I. (2010). Novel fusion welding technology of glass using ultrashort pulse lasers. Procedia CIRP 5, 483–493. doi:10.1016/j.phpro.2010.08.171
Mohan, A., Ceglarek, D., and Auinger, M. (2022). Effect of beam oscillation on the fluid flow during laser welding. Mater. Today Proc. 59, 1846–1851. doi:10.1016/j.matpr.2022.04.435
Mokrane, A., Boutaous, M., and Xin, S. (2018). Process of selective laser sintering of polymer powders: modeling, simulation, and validation. Comptes Rendus - Mec. 346, 1087–1103. doi:10.1016/j.crme.2018.08.002
Mokrov, O., Simon, M., Schiebahn, A., and Reisgen, U. (2019). A fine modification of the double ellipsoid heat source. Math. Model. Weld Phenom. [Preprint]. doi:10.3217/978-3-85125-615-4
Nandy, J., Yedla, N., Gupta, P., Sarangi, H., and Sahoo, S. (2019). Sintering of AlSi10Mg particles in direct metal laser sintering process: a molecular dynamics simulation study. Mater. Chem. Phys. 236, 121803. doi:10.1016/j.matchemphys.2019.121803
Nascimento, E. J. G., dos Santos Magalhães, E., and dos Santos Paes, L. E. (2023). A literature review in heat source thermal modeling applied to welding and similar processes. Int. J. Adv. Manuf. Technol. 126 (7–8), 2917–2957. doi:10.1007/s00170-023-11253-z
Näsström, M., and Karlberg, M. (2014). “Welding heat input models,” in Encyclopedia of thermal stresses (Dordrecht: Springer Netherlands), 6567–6572. doi:10.1007/978-94-007-2739-7_467
Nazami, G. R., and Sahoo, S. (2020). Influence of hatch spacing and laser spot overlapping on heat transfer during laser powder bed fusion of aluminum alloy. J. Laser Appl. 32 (4). doi:10.2351/7.0000157
Nezamdost, M. R., Esfahani, M. R. N., Hashemi, S. H., and Mirbozorgi, S. A. (2016). Investigation of temperature and residual stresses field of submerged arc welding by finite element method and experiments. Int. J. Adv. Manuf. Technol. 87 (1–4), 615–624. doi:10.1007/s00170-016-8509-4
Nguyen, N., and Chujutalli, J. H. (2021). Simulating convective-radiative heat sink effect by means of FEA-based Gaussian heat sources and its approximate analytical solutions for semi-infinite body. Int. J. Adv. Manuf. Technol. 117 (11–12), 3717–3742. doi:10.1007/s00170-021-07699-8
Nguyen, N. T., Mai, Y. W., Simpson, S., and Ohta, A. (2004). Analytical approximate solution for double ellipsoidal heat source in finite thick plate. Weld. J. (Miami, Fla) 83 (3).
Nisar, S., Noor, A., Shah, A., Siddiqui, U., and Zia Khan, S. (2023). Optimization of process parameters for laser welding of A5083 aluminium alloy. Opt. Laser Technol. 163, 109435. doi:10.1016/j.optlastec.2023.109435
Panda, B. K., and Sahoo, S. (2019). Thermo-mechanical modeling and validation of stress field during laser powder bed fusion of AlSi10Mg built part. Results Phys. 12, 1372–1381. doi:10.1016/j.rinp.2019.01.002
Pang, S., Chen, L., Zhou, J., Yin, Y., and Chen, T. (2011). A three-dimensional sharp interface model for self-consistent keyhole and weld pool dynamics in deep penetration laser welding. J. Phys. D Appl. Phys. 44 (2), 025301. doi:10.1088/0022-3727/44/2/025301
Pang, S., Chen, X., Shao, X., Gong, S., and Xiao, J. (2016). Dynamics of vapor plume in transient keyhole during laser welding of stainless steel: local evaporation, plume swing and gas entrapment into porosity. Opt. Lasers Eng. 82, 28–40. doi:10.1016/j.optlaseng.2016.01.019
Pavelic, V., Tanbakuchi, R., Uyehara, O. A., and Myers, P. S. (1969). Experimental and computed temperature histories in gas tungsten-arc welding of thin plates. Weld. J. 48 (7).
Perulli, P., Dassisti, M., and Casalino, G. (2020). Thermo-mechanical simulation of hybridwelding of DP/AISI 316 and TWIP/AISI 316 dissimilar weld. Materials 13 (9), 2088. doi:10.3390/ma13092088
Piekarska, W., and Kubiak, M. (2011). Three-dimensional model for numerical analysis of thermal phenomena in laser–arc hybrid welding process. Int. J. Heat Mass Transf. 54 (23–24), 4966–4974. doi:10.1016/j.ijheatmasstransfer.2011.07.010
Piekarska, W., and Kubiak, M. (2013). Modeling of thermal phenomena in single laser beam and laser-arc hybrid welding processes using projection method. Appl. Math. Model. 37 (4), 2051–2062. doi:10.1016/j.apm.2012.04.052
Polonsky, A. T., Madison, J. D., Arnhart, M., Jin, H., Karlson, K. N., Skulborstad, A. J., et al. (2023). Toward accurate prediction of partial-penetration laser weld performance informed by three-dimensional characterization – Part I: high fidelity interrogation. Tomogr. Mater. Struct. 2, 100006. doi:10.1016/j.tmater.2023.100006
Pu, X., Zhang, C., Li, S., and Deng, D. (2017). Simulating welding residual stress and deformation in a multi-pass butt-welded joint considering balance between computing time and prediction accuracy. Int. J. Adv. Manuf. Technol. 93 (5–8), 2215–2226. doi:10.1007/s00170-017-0691-5
Raftar, H. R., Ahola, A., Lipiäinen, K., and Björk, T. (2023). Simulation and experiment on residual stress and deflection of cruciform welded joints. J. Constr. Steel Res. 208, 108023. doi:10.1016/j.jcsr.2023.108023
Rao, Z. H., Liao, S. M., and Tsai, H. L. (2011). Modelling of hybrid laser-GMA welding: review and challenges. Sci. Technol. Weld. Join. 16 (4), 300–305. doi:10.1179/1362171811Y.0000000022
Raza, M. M., Lo, Y. L., Lee, H. B., and Yu-Tsung, C. (2023). Computational modeling of laser welding for aluminum–copper joints using a circular strategy. J. Mater. Res. Technol. 25, 3350–3364. doi:10.1016/j.jmrt.2023.06.122
Rehman, A., Lathkar, G. S., and Zubairuddin, M. (2023). Finite element analysis of laser welding of 304L butt joint. Mater. Today Proc. doi:10.1016/j.matpr.2023.10.119
Riquelme, A., and Rodrigo, P. (2021). An introduction on the laser cladding coatings on magnesium alloys. Metals 11 (12), 1993. doi:10.3390/met11121993
Rong, Y., Li, Y., Wang, L., Xu, J., and Huang, Y. (2022). Fusion interface stress and its potential effect on microcrack in 10-kW level laser welding. Appl. Phys. A Mater. Sci. Process. 128 (2), 117. doi:10.1007/s00339-022-05259-9
Rosenthal, D. (1946). The theory of moving sources of heat and its application to metal treatments. J. Fluids Eng. Trans. ASME 68 (8), 849–865. doi:10.1115/1.4018624
Roy, G. G., Elmer, J. W., and DebRoy, T. (2006). Mathematical modeling of heat transfer, fluid flow, and solidification during linear welding with a pulsed laser beam. J. Appl. Phys. 100 (3). doi:10.1063/1.2214392
Saadlaoui, Y., Feulvarch, É., Delache, A., Leblond, J. B., and Bergheau, J. M. (2018). A new strategy for the numerical modeling of a weld pool. Comptes Rendus - Mec. 346, 999–1017. doi:10.1016/j.crme.2018.08.007
Sahoo, S. (2021a). Direct metal laser sintering of AlSi10Mg alloy parts: modeling of temperature profile. Mater. Today Proc. 35, 118–123. doi:10.1016/j.matpr.2020.03.342
Sahoo, S. (2021b). Prediction of residual stress and deformation of build part with variation of hatch spacing in direct metal laser sintering of AlSi10Mg built part: thermo-mechanical modeling. J. Laser Appl. 33 (3). doi:10.2351/7.0000393
Sahoo, S., and Chou, K. (2016). Phase-field simulation of microstructure evolution of Ti–6Al–4V in electron beam additive manufacturing process. Addit. Manuf. 9, 14–24. doi:10.1016/j.addma.2015.12.005
Samardžić, I. (1996). “Contribution to the reliability of welded joints,” (Croatia: University of Rijeka). Dissertation.
Savin, V. V., Reintal, E. A., Likhoshva, V. P., Timoshenko, A. N., Osadchy, A. V., and Savina, L. A. (2018). Mathematical modelling of continuous laser welding and local heat treatment of welded pipes of stainless and heat-resistant chromium-nickel steels. J. Phys. Conf. Ser. 1109, 012003. doi:10.1088/1742-6596/1109/1/012003
Sebayang, D., Manurung, Y., Ariri, A., Yahya, O., Wahyudi, H., Sari, A., et al. (2018). Numerical simulation of distortion and phase transformation in laser welding process using MSC Marc/Mentat. IOP Conf. Ser. Mater. Sci. Eng. 453, 012020. doi:10.1088/1757-899X/453/1/012020
Shapeev, V. P., Cherepanov, A. N., and Isaev, V. I. (2019). Modeling of laser welding of plates made of dissimilar metals with the use of a composite insert. IOP Conf. Ser. Mater. Sci. Eng. 681, 012044. doi:10.1088/1757-899X/681/1/012044
Shen, X., Gao, K., and Dong, S. (2020). Simulation and analysis of electron beam welding residual stress in thin-walled high-temperature alloy aeroengine structures. Int. J. Adv. Manuf. Technol. 107 (9–10), 3953–3966. doi:10.1007/s00170-020-05276-z
Song, Y., Wang, Y., and Zhang, M. (2019). Experimental and numerical simulation on laser welding of high manganese TWIP980 Steel. Procedia Manuf. 37, 385–393. doi:10.1016/j.promfg.2019.12.064
Stoevesandt, B., Steinfeld, G., and Leo, H. (2017). Computational fluid dynamics. First edition. Oldenburg: Carl von Ossietzky University of Oldenburg.
Stone, H. J., Roberts, S. M., and Reed, R. C. (2000). A process model for the distortion induced by the electronbeam welding of a nickel-based superalloy. Metallurgical Mater. Trans. A Phys. Metallurgy Mater. Sci. 31 (9), 2261–2273. doi:10.1007/s11661-000-0143-x
Su, C., Zhou, J., Ye, Y., Huang, S., and Meng, X. (2017). Study on fiber laser welding of aa6061-T6 samples through numerical simulation and experiments. Procedia Eng. 174, 732–739. doi:10.1016/j.proeng.2017.01.213
Suárez, A., Tobar, M., Yáñez, A., Pérez, I., Sampedro, J., Amigó, V., et al. (2011). Modeling of phase transformations of Ti6Al4V during laser metal deposition. Phys. Procedia 12, 666–673. doi:10.1016/j.phpro.2011.03.083
Svenungsson, J., Choquet, I., and Kaplan, A. F. H. (2015). Laser welding process - a review of keyhole welding modelling. Phys. Procedia 78, 182–191. doi:10.1016/j.phpro.2015.11.042
Tan, W., Bailey, N. S., and Shin, Y. C. (2013). Investigation of keyhole plume and molten pool based on a three-dimensional dynamic model with sharp interface formulation. J. Phys. D Appl. Phys. 46 (5), 055501. doi:10.1088/0022-3727/46/5/055501
Tan, W., and Shin, Y. C. (2014). Analysis of multi-phase interaction and its effects on keyhole dynamics with a multi-physics numerical model. J. Phys. D Appl. Phys. 47 (34), 345501. doi:10.1088/0022-3727/47/34/345501
Tang, C., Le, K. Q., and Wong, C. H. (2020). Physics of humping formation in laser powder bed fusion. Int. J. Heat Mass Transf. 149, 119172. doi:10.1016/j.ijheatmasstransfer.2019.119172
Tang, C., Yao, L., and Du, H. (2022). Computational framework for the simulation of multi material laser powder bed fusion. Int. J. Heat Mass Transf. 191, 122855. doi:10.1016/j.ijheatmasstransfer.2022.122855
Tao, P., Zhang, X., Mi, G., and Wang, C. (2023). Research on fiber laser welding formation, microstructure, and mechanical properties of 7.5 mm 304 stainless steel. J. Mater. Res. Technol. 24, 236–249. doi:10.1016/j.jmrt.2023.02.200
Trupiano, S., Belardi, V. G., Fanelli, P., Gaetani, L., and Vivio, F. (2022). A semi-analytical method for the calculation of double-ellipsoidal heat source parameters in welding simulation. IOP Conf. Ser. Mater. Sci. Eng. 1214 (1), 012023. doi:10.1088/1757-899x/1214/1/012023
Tsai, Y.-A., Lo, Y. L., Raza, M. M., N. Saleh, A., Chuang, T. C., Chen, C. Y., et al. (2023). Optimization of lap-joint laser welding parameters using high-fidelity simulations and machine learning mode. J. Mater. Res. Technol. 24, 6876–6892. doi:10.1016/j.jmrt.2023.04.256
Unni, A. K., and Muthukumaran, V. (2022). Modeling of heat transfer, fluid flow, and weld pool dynamics during keyhole laser welding of 316 LN stainless steel using hybrid conical-cylindrical heat source. Int. J. Adv. Manuf. Technol. 122 (9–10), 3623–3645. doi:10.1007/s00170-022-09946-y
Unni, A. K., and Vasudevan, M. (2023). Computational fluid dynamics simulation of hybrid laser-MIG welding of 316 LN stainless steel using hybrid heat source. Int. J. Therm. Sci. 185, 108042. doi:10.1016/j.ijthermalsci.2022.108042
Vaglio, E., Totis, G., Lanzutti, A., Fedrizzi, L., and Sortino, M. (2023) A novel thermo-geometrical model for accurate keyhole porosity prediction in Laser Powder-Bed Fusion, Prog. Addit. Manuf. Prepr. doi:10.1007/s40964-023-00446-3
Vemanaboina, H., Akella, S., and Buddu, R. K. (2014). Welding process simulation model for temperature and residual stress analysis. Procedia Mater. Sci. 6, 1539–1546. doi:10.1016/j.mspro.2014.07.135
Ventrella, V. A., Berretta, J. R., and De Rossi, W. (2010). Pulsed Nd:YAG laser seam welding of AISI 316L stainless steel thin foils. J. Mater. Process. Technol. 210 (14), 1838–1843. doi:10.1016/j.jmatprotec.2010.06.015
Villacís Ramón, M. E., and Yaulema Castaneda, J. L. (2022). Modelo matemático para el análisis del comportamiento térmico en el proceso de soldadura de un acero estructural mediante un software con base en el método de elementos finitos. ConcienciaDigital 5, 289–314. doi:10.33262/concienciadigital.v5i3.1.2254
Villacis Ramón Mayra Elizabeth (2022). Mathematical Model for the Analysis of thermal Behavior in the welding Process of structural Steel using Software based on the finite element method. Máster. Escuela superior politécnica de Chimborazo. Available at: http://dspace.espoch.edu.ec/handle/123456789/17283.
von Allmen, M. (1987). Laser-beam interactions with materials. Berlin, Heidelberg: Springer Berlin Heidelberg. doi:10.1007/978-3-642-97007-8
Wang, H., Shi, Y., and Gong, S. (2006). Numerical simulation of laser keyhole welding processes based on control volume methods. J. Phys. D Appl. Phys. 39 (21), 4722–4730. doi:10.1088/0022-3727/39/21/032
Wang, R., Zhai, J., Kong, H., Zhao, Y., Zheng, M., Jiang, Q., et al. (2023). Joining of 304 stainless steel to PET by semiconductor laser conduction welding. J. Mater. Res. Technol. 27, 5729–5738. doi:10.1016/j.jmrt.2023.11.004
Wasilewski, E., Doynov, N., Ossenbrink, R., and Michailov, V. (2023). Investigations on the thermal conditions during laser beam welding of high-strength steel 100Cr6. Adv. Industrial Manuf. Eng. 6, 100118. doi:10.1016/j.aime.2023.100118
Wu, D., Wang, K., Liu, B., Qu, H., Wang, X., and Liu, G. (2023). Damage evolution of titanium alloy laser-welded joint during hot deformation: experiment and modeling. J. Mater. Res. Technol. 26, 6375–6388. doi:10.1016/j.jmrt.2023.09.023
Wu, J., Zhang, H., Feng, Y., and Luo, B. (2018). 3D multiphysical modelling of fluid dynamics and mass transfer in laser welding of dissimilar materials. Metals 8 (6), 443. doi:10.3390/met8060443
Xamán, J., and Gijón-Rivera, M. (2015). Dinámica de Fluidos Computacional para Ingenieros. First Edition. México: Palabrio.
Xia, P., Wang, C., Mi, G., Zhang, M., Xiong, L., Zhang, X., et al. (2023). Numerical simulation of molten pool flow behavior and keyhole evolution behavior in dual-laser beam oscillating bilateral synchronous welding of T-joints. Int. J. Heat Mass Transf. 209, 124114. doi:10.1016/j.ijheatmasstransfer.2023.124114
Xia, P., Xiong, L., Hu, Y., Feng, X., and Wang, C. (2023). Effect of laser oscillation and beam incident angle on porosity in double-sided filler welding of 2219 aluminum alloy T joint. Opt. Laser Technol. 166, 109581. doi:10.1016/j.optlastec.2023.109581
Xu, G. X., Wu, C. S., Qin, G. L., Wang, X. Y., and Lin, S. Y. (2011). Adaptive volumetric heat source models for laser beam and laser + pulsed GMAW hybrid welding processes. Int. J. Adv. Manuf. Technol. 57 (1–4), 245–255. doi:10.1007/s00170-011-3274-x
Xue, B., Chang, B., Wang, S., Hou, R., Wen, P., and Du, D. (2022). Humping Formation and suppression in high-speed laser welding. Materials 15 (7), 2420. doi:10.3390/ma15072420
Yadaiah, N., and Bag, S. (2014). Development of egg-configuration heat source model in numerical simulation of autogenous fusion welding process. Int. J. Therm. Sci. 86, 125–138. doi:10.1016/j.ijthermalsci.2014.06.032
Yang, Z., Fang, Y., and He, J. (2020). Numerical simulation of heat transfer and fluid flow during vacuum electron beam welding of 2219 aluminium girth joints. Vacuum 175, 109256. doi:10.1016/j.vacuum.2020.109256
Yin, X., Zhao, Y., Liu, Y., Wang, J., Wang, L., and Zhan, X. (2023). Porosity morphology and its evolution mechanism in laser mirror welding of 2219 aluminum alloy. Opt. Laser Technol. 164, 109456. doi:10.1016/j.optlastec.2023.109456
Zain-ul-abdein, M., Nélias, D., Jullien, J. F., Boitout, F., Dischert, L., and Noe, X. (2011). Finite element analysis of metallurgical phase transformations in AA 6056-T4 and their effects upon the residual stress and distortion states of a laser welded T-joint. Int. J. Press. Vessels Pip. 88 (1), 45–56. doi:10.1016/j.ijpvp.2010.10.008
Zhang, G., Li, W., Xu, G., Xing, F., Chang, L., Wu, S., et al. (2023). Simulation of temperature field and residual stress in high-power laser self-melting welding process of CLF-1 steel medium-thick plate. Fusion Eng. Des. 195, 113936. doi:10.1016/j.fusengdes.2023.113936
Zhang, J., Li, W., Yan, L., and Liou, F. (2018). A two-dimensional simulation of grain structure growth within the substrate and the fusion zone during direct metal deposition. Comptes Rendus - Mec. 346, 1072–1086. doi:10.1016/j.crme.2018.08.003
Zhang, K., He, C., Liu, D., Yan, C., Niu, H., Yang, Z., et al. (2022). Effect of heat input on microstructure and tensile properties of laser welded Ti–3Al–6Mo–2Fe–2Zr alloy joint. J. Mater. Res. Technol. 17, 1652–1661. doi:10.1016/j.jmrt.2022.01.089
Zhang, L. J., Zhang, J., Gumenyuk, A., Rethmeier, M., and Na, S. (2014). Numerical simulation of full penetration laser welding of thick steel plate with high power high brightness laser. J. Mater. Process. Technol. 214 (8), 1710–1720. doi:10.1016/j.jmatprotec.2014.03.016
Zhang, X., Li, L., Chen, Y., Zhu, X., and Ji, S. (2019). Numerical simulation analysis of dual-beam laser welding of tailored blanks with different thicknesses. Metals 9 (2), 135. doi:10.3390/met9020135
Zhang, Z., and Wu, C. (2015). Effect of fluid flow in the weld pool on the numerical simulation accuracy of the thermal field in hybrid welding. J. Manuf. Process. 20, 215–223. doi:10.1016/j.jmapro.2015.08.001
Zhou, Y., Wang, J., Zhao, Y., Cheng, L., and Xiaohong, X. (2023). Numerical analysis of coupling dynamics of keyhole and molten pool in vertical-up laser mirror welding of 2219 aluminum alloy. Int. J. Therm. Sci. 192, 108390. doi:10.1016/j.ijthermalsci.2023.108390
Keywords: educational innovation, higher education, laser welding, CFD, heat transfer, computational thinking, keyhole, melt pool
Citation: Jiménez-Xamán M, Hernández-Hernández M, Tariq R, Landa-Damas S, Rodríguez-Vázquez M, Aranda-Arizmendi A and Cruz-Alcantar P (2024) Numerical simulations and mathematical models in laser welding: a review based on physics and heat source models. Front. Mech. Eng 10:1325623. doi: 10.3389/fmech.2024.1325623
Received: 22 October 2023; Accepted: 29 January 2024;
Published: 11 March 2024.
Edited by:
Yatao Ren, Harbin Institute of Technology, ChinaReviewed by:
Seshadev Sahoo, Siksha O Anusandhan University, IndiaChang Li, University of Science and Technology Liaoning, China
Copyright © 2024 Jiménez-Xamán, Hernández-Hernández, Tariq, Landa-Damas, Rodríguez-Vázquez, Aranda-Arizmendi and Cruz-Alcantar. This is an open-access article distributed under the terms of the Creative Commons Attribution License (CC BY). The use, distribution or reproduction in other forums is permitted, provided the original author(s) and the copyright owner(s) are credited and that the original publication in this journal is cited, in accordance with accepted academic practice. No use, distribution or reproduction is permitted which does not comply with these terms.
*Correspondence: Rasikh Tariq, cmFzaWtodGFyaXFAdGVjLm14