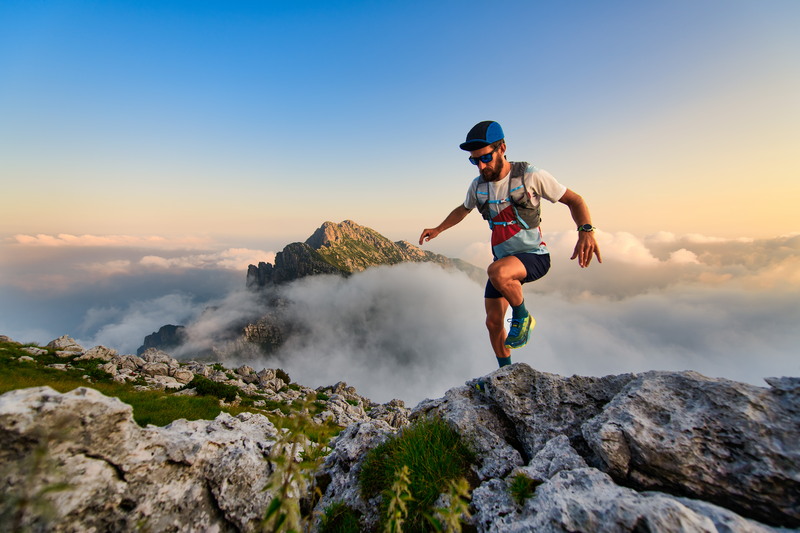
94% of researchers rate our articles as excellent or good
Learn more about the work of our research integrity team to safeguard the quality of each article we publish.
Find out more
EDITORIAL article
Front. Mech. Eng. , 21 February 2023
Sec. Digital Manufacturing
Volume 9 - 2023 | https://doi.org/10.3389/fmech.2023.1160923
This article is part of the Research Topic Applications of Artificial Intelligence and IoT Technologies in Smart Manufacturing View all 5 articles
Editorial on the Research Topic
Applications of artificial intelligence and IoT technologies in smart manufacturing
In recent years, the rapid developments of the industrial era 4.0 have paved a new way for advanced manufacturing operations with applications of artificial intelligence (AI) and Internet of things (IoT) technologies. Therefore, the manufacturing performance by learning various information with IoT systems can increase automation to contribute to the operational efficiency and effectiveness of smart manufacturing processes.
Smart manufacturing requires deep insight into advanced technologies such as AI, IoT, big data analytics, machine learning (ML) and deep learning (DL), virtual reality, and autonomous robots that are integrated into the manufacturing processes. For this reason, smart manufacturing has been getting a great deal of attention from research communities as well as the industry. This themed Research Topic aims to encourage scholars and researchers to present their research to that shed light on this rising Research Topic.
Through a rigorous review process, we have selected four original research papers for this Research Topic of “Applications of Artificial Intelligence and IoT Technologies in Smart Manufacturing”. The four papers present new data processing and machine learning methods in various areas in smart manufacturing such as classifying defects in welding applications, localizing defects of 3D-printed parts in additive manufacturing, detecting hardware Trojans in electronics production lines, and detecting gear faults of gearboxes in mechanical systems. These four papers are briefly summarized below.
(Sekhar et al.) presents an effective machine learning method for identifying and classifying defects of tungsten inert gas welding joints for stainless steel parts. This study would gain a great deal of attention because smart, accurate, and automated identification of welding defects helps improve quality and safety of welding joints while ensuring high productivity of welded parts for various industrial applications. In this study, a transfer learning process is used to initiate pre-trained deep learning models which serve as layers 0 connected to other two subsequent layers in the full structure of the learning architecture. There are eight different pre-trained models used in the transfer learning framework, and they are tuned with four optimizers, resulting in a total of 32 model-optimizer combinations. They are then used to classify images into two separate groups including the two-class group consisting of good weld and bad weld and the multi-class group having good weld and five types of bad welds. The performance of the machine learning architecture is evaluated by using several metrics over successive training epochs. The results reveal that the transfer learning approach helps enhance classification accuracy and better help manufactures optimize the quality-productivity trade-off.
(Halsey et al.) employed the supervised XGBoost ML model to predict localized defects in 3D-printed parts. The study shows the first attempt to link temporal data (obtained from several in situ sensors) to the spatial data (scanning path information) to form a time-space voxel-based map where defects like soot and debris can be identified. The in situ collected data are used to train a XGBoost model to predict localized defects. The overall performance of the model seems to be insufficient to be applied as the main tool to monitor the processing and detect soot defects. Non-etheless, it is able to point out the most relevant data contributing to the defects. Also, the methodology to build the real time integrated temporal-spatial data is effective to detect localized defects.
(Kulkarni and Xu) developed a deep learning technique to optically detect hidden hardware trojans in electronics devices for cybersecurity. An effective convolutional neural network (CNN) incorporated with Resnet transferred ML is used to identify three classes of instances including the hardware trojans, defects and misalignments in an image dataset. The pre-processed differencing-image-based data are used to train the CNN model, and it is evaluated by using a confusion. The results show that with Resnet34 (including 34 layers) the model can detect malicious modification with high accuracy.
(Du et al.) presents a new method to detect symptoms of gear faults of gearboxes in non-stationary conditions based on sideband analysis. Firstly, the 1D vibration signal was converted into a time-frequency domain, then a two-step method was applied to determine the meshing frequency. Finally, the sideband features extracted around the meshing frequency can effectively detect the gearbox fault. The proposed approach shows the effectiveness without additional measuring equipment. The study shows the possibility to establish a real time diagnostic system for machines and equipment with the least number of measuring devices while ensuring high detection accuracy.
The contributions of the four selected papers suggest some further research highlighted below.
• Data analysis is still the first and foremost technique in ML processes, AI and IoT technologies. To this end, it is important to develop effective and reliable methods to integrate accurately temporal data (e.g., processing parameters) and spatial data (e.g., scanning paths) in manufacturing processes including but not limited to additive manufacturing, and represent these data of different modalities in a connected manner to better mine the relationships between inputs and targets, as well as, to be able to detect localized defects and properties. This is one of the stepping stones in developing IoT systems.
• Continue to develop new ML models that give better performance with more appropriate metrics and can be used in various applications.
• In order to promote the use of AI and IoT technologies in the industrial environment, researchers are encouraged to establish built-in ML model libraries (like XGBoost, Resnet, etc.) that are available in some commercial software packages such as Python, Java, Scala, Julia, Perl, etc., so that users can easily access and apply to their work.
In this themed Research Topic, we present four selected papers to introduce the reader to several recent applications of AI, ML, and IoT technologies across various fields of smart manufacturing such as additive manufacturing, 3D-printing, welding, electronics manufacturing, and mechanical fault diagnosis. We also suggest some possible future research directions that help to make AI, revolutionize ML, and IoT technologies more effective, reliable and easy to use. This will contribute to revolutionize the manufacturing operations as the core mission of the Industry 4.0.
Conceptualization: VV and M-QT; project management: M-QT; methodology: VV and LV; writing—original draft: VV. Review: LV. All authors have read and agreed to the current version of the manuscript.
The authors would like to thank the chief editors of Frontiers in Mechanical Engineering for giving us the opportunity to lead and organize this Research Topic. The authors also would like to thank Thai Nguyen University of Technology (TNUT) and TUETECH University for their support.
The authors declare that the research was conducted in the absence of any commercial or financial relationships that could be construed as a potential conflict of interest.
All claims expressed in this article are solely those of the authors and do not necessarily represent those of their affiliated organizations, or those of the publisher, the editors and the reviewers. Any product that may be evaluated in this article, or claim that may be made by its manufacturer, is not guaranteed or endorsed by the publisher.
Keywords: artificial intelligence (AI), IoT technologies, smart manufacturing, additive manufacturing, 3D-printing, machine learning (ML), welding, defect detection
Citation: Vu VQ, Tran M-Q and Vu LT (2023) Editorial: Applications of artificial intelligence and IoT technologies in smart manufacturing. Front. Mech. Eng 9:1160923. doi: 10.3389/fmech.2023.1160923
Received: 07 February 2023; Accepted: 13 February 2023;
Published: 21 February 2023.
Edited and reviewed by:
Amit Bandyopadhyay, Washington State University, United StatesCopyright © 2023 Vu, Tran and Vu. This is an open-access article distributed under the terms of the Creative Commons Attribution License (CC BY). The use, distribution or reproduction in other forums is permitted, provided the original author(s) and the copyright owner(s) are credited and that the original publication in this journal is cited, in accordance with accepted academic practice. No use, distribution or reproduction is permitted which does not comply with these terms.
*Correspondence: Viet Q. Vu, dnF2aWV0QHRudXQuZWR1LnZu; Minh-Quang Tran, bWluaHF1YW5nLnRyYW5AbWFpbC5udHVzdC5lZHUudHc=
Disclaimer: All claims expressed in this article are solely those of the authors and do not necessarily represent those of their affiliated organizations, or those of the publisher, the editors and the reviewers. Any product that may be evaluated in this article or claim that may be made by its manufacturer is not guaranteed or endorsed by the publisher.
Research integrity at Frontiers
Learn more about the work of our research integrity team to safeguard the quality of each article we publish.