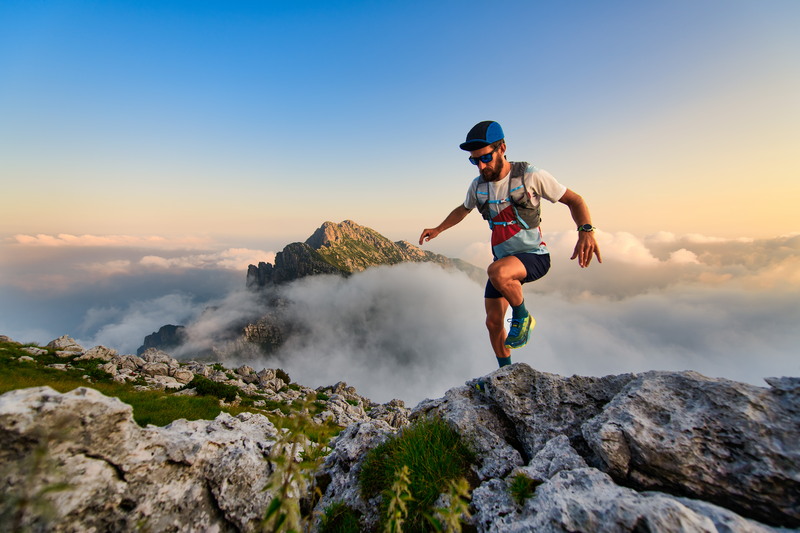
95% of researchers rate our articles as excellent or good
Learn more about the work of our research integrity team to safeguard the quality of each article we publish.
Find out more
REVIEW article
Front. Mech. Eng. , 12 August 2022
Sec. Tribology
Volume 8 - 2022 | https://doi.org/10.3389/fmech.2022.908497
This article is part of the Research Topic Horizons in Mechanical Engineering 2022 View all 7 articles
Superlubricity is a terminology often used to describe a sliding regime in which the adhesion leading to friction or resistance to sliding literally vanishes. For improved energy security, environmental sustainability, and a decarbonized economy, achieving superlubric sliding surfaces in moving mechanical systems sounds very exciting, since friction adversely impacts the efficiency, durability, and environmental compatibility of many moving mechanical systems used in industrial sectors. Accordingly, scientists and engineers have been exploring new ways to achieve macroscale superlubricity through the use of advanced materials, coatings, and lubricants for many years. As a result of such concerted efforts, recent developments indicate that with the use of the right kinds of solids, liquids, and gases on or in the vicinity of sliding contact interfaces, one can indeed achieve friction coefficients well below 0.01. The friction coefficient below this threshold is commonly termed the superlubric sliding regime. Hopefully, these developments will foster further research in the field of superlubricity and will ultimately give rise to the industrial scale realization of nearly-frictionless mechanical systems consuming far less energy and causing much-reduced greenhouse gas emissions. This will ultimately have a substantial positive impact on the realization of economically and environmentally viable industrial practices supporting a decarbonized energy future. In this paper, we will provide an overview of recent progress in superlubricity research involving solid, liquid, and gaseous media and discuss the prospects for achieving superlubricity in engineering applications leading to greater efficiency, durability, environmental quality, and hence global sustainability.
Friction (defined as resistance to sliding) has been one of the most fascinating physical phenomena from the very early ages. In fact, throughout history, mankind realized the importance of friction in their way of life and developed effective means to control it by some very ingenious manners (Holmberg et al., 2012). Prime examples are the transportation of huge colossus and stones on lubricated sledges or pathways by many slaves to their designated locations along the river Nile in ancient Egypt (Dowson, 1998). The use of gypsum, vegetable oils, and animal fats to lubricate wheels of chariots and thus achieve easier and faster mobility can also be regarded as another clever example where mankind has appreciated the importance of friction and developed new ways to control it to its advantage (Nosonovsky, 2007).
More systematic approaches to understanding and controlling friction are thought to start during the Middle Ages. The highly methodical work of Leonardo da Vinci and his explicit drawings depicting a range of friction experiments attest themselves to be extremely ingenious even today and conform to modern days’ treatment of friction (Pitenis et al., 2014). Further analyses of friction by Guillaume Amonton during the 1600s and Charles-Augustin de Coulomb in the 1700s have laid the foundation of many other scientific studies on friction by Desaguliers, Reynolds, Hardy, Holm, Bowden and Tabor, and many other scientists during the 19th and 20th centuries (Dowson, 1998; Ludema, 2001).
With much larger and diverse mobility worldwide today, friction has become an integral part of our daily life and lately, it has gained far more attention due to its enormous impact on energy and environmental matters. Today, we see, feel, and experience its effects in so many ways in a given day but hardly pay attention to its adverse impacts on energy and the environment. We like friction to be high for safe walking or while stopping our cars at a stop sign, but we wish it to be as low as possible in our joints for flawless walking or in our car’s engines to pay less at gas stations. Achieving lower frictional losses in car engines can also lead to fewer greenhouse gas emissions. In passenger cars alone, it is estimated that nearly 1/3 of the fuel’s energy is consumed by friction (this amounts to more than 360 million tons of oil equivalent per year or 7.3 million TJ of energy wasted) (Holmberg et al., 2012). So, the energy, environmental, and economic impacts of friction are rather huge and with the rapid increases in worldwide mobility and industrial activity, its impact will surely surge even higher in the near future (Marian et al., 2022). In short, friction remains a major challenge that requires more coherent and concerted efforts at every level of our society to reduce its adverse impacts on our society and environment.
Despite many dedicated studies in the past, however, controlling friction still remains a very challenging task. It has been one of the most popular research topics for many scientists year after year. According to the ISI Web of Science, more than 16,000 research articles were devoted to the science and technology of friction in 2021 alone. Furthermore, numerous books and handbooks are devoted to describing the fundamentals of friction and wear phenomena in different material systems. Friction studies by early pioneers were mostly directed toward macro/micro-scale understanding and control of friction through the uses of some solid and liquid lubricants. With the advent of technological capabilities, very effective liquid and solid anti-friction and -wear additives have been developed and continuously refined over the years to provide much superior performance (Hirano et al., 1991; Spikes, 2004; Martin and Ohmae, 2008; Romsdahl et al., 2019; Shirani et al., 2020a). Thanks to many great lubrication discoveries, friction coefficients for many sliding systems have been reduced well below 0.1 during the late 2000s. In fact, under some very special test conditions, it was shown that friction coefficients of below 0.01 are quite feasible for not only lubricated but also dry sliding contacts (Erdemir et al., 2021). This regime of less than 0.01 friction coefficient has become very attractive to the scientific community of superlubricity (Hirano, 2003) with more attention being directed to it every year. Over 4,000 research articles appeared in peer-reviewed journals in the past 5 years alone pushing the boundaries of understanding both the fundamental and applied aspects of superlubricity across scales and media.
Figure 1 summarizes the chronological evolution of superlubricity findings through the use and discovery of novel materials across scales during the past two decades. From observing sliding friction between atomic planes in an AFM setup to achieving robust macro-scale superlubricity in multi-asperity contacts and multifarious environments, the domain has vastly expanded over the years to include numerous new material systems. This could be regarded as a great achievement of the tribology community from around the world.
Early proof of concept demonstrations included polymorphs of carbon such as carbon nanotubes, fullerene structures, tetrahedral amorphous carbon, thin diamond films, and MEMS devices. Despite a variety of demonstrations achieving super low friction, many such technologies have faded away from research interest due to the issues with scaling, environmental sensitivity, and application worthiness. Discovery of material systems such as Diamond Like Carbon (DLC) (Erdemir and Eryilmaz, 2014), Graphene and Graphene-based composites (Berman et al., 2015a; Berman et al., 2018a) (such as Graphene-MoS2; Graphene-hBN; Graphene-DLC; Graphene-MXene; and Graphene Oxides) have garnered sustained research interest and product level demonstrations. Recent advancements includ black phosphorus (Ren et al., 2020) and MXenes (Yi et al., 2021a) as superlubricity additives, tribocatalytic systems (Gao et al., 2021) and effective surface termination or passivation (Nosaka et al., 2015; Nosaka et al., 2017) technologies that pushed the chart towards the upper-right corner in the macro-scale range and hence imminent applications of superlubricity in real mechanical systems.
The dedicated studies on friction over the past centuries have undoubtedly increased our understanding and, in return, helped better control it to achieve greater efficiency and longer durability in many industrial applications. These studies also paved the way for developing novel materials and coatings synergistically working with lubricants to provide much lower friction and wear losses than before. Thanks to such leapfrog advances, many moving mechanical systems of today work flawlessly and efficiently for a very long duration. With increasing desires to achieve even far more efficient and clean mobility, we should expect continued progress in friction science and technology in the near future leading to the development of truly frictionless tribological or mechanical systems.
From a practical point of view, achieving superlubric sliding regimes would have been the most ideal type of sliding for almost all moving mechanical systems (except for brakes, clutches, tires, shoes, etc. where high friction is rather a desirable property). However, the most observed or reported superlubricity works can only be useful in certain moderate sliding conditions and often impractical in large mechanical systems operating under severe sliding conditions. Due to a worldwide desire to achieve higher energy efficiency, durability, and environmental compatibility in all types of moving mechanical systems, there is no doubt that research on friction and related matters will gain far more attention in the coming years. It is hoped that achieving a sustainable superlubric sliding regime in all macro/meso-scale mechanical systems will 1 day become a reality and these next-generation systems will consume far less energy and result in much reduced CO2 emissions. Not surprisingly, in most sliding systems where superlubricity was observed, the amount of wear was also found to be extremely small or immeasurable. This property is also very desirable for the realization of reliable, long-lasting mechanical systems.
In the following sections, we will provide detailed information on the present state-of-the-art superlubricity research involving solid, liquid, and gaseous media. Particular emphasis will be placed on those latest developments that can lead to more efficient and environmentally friendly tribological solutions for industry. We will also discuss future directions in relation to energy and environmental concerns which have lately become very important for ensuring a sustainable transportation future including electric vehicles.
Superlubric or nearly-frictionless sliding regimes have existed in a variety of tribological and biological systems for quite a long time but in most of these, the type of motion does not essentially involve direct solid-to-solid contacts. Specifically, under the aero- or hydro-dynamic lubrication condition, the sliding surfaces are well-separated by a fluid (air or liquid) film and the amount of frictional energy dissipation is limited to the shearing of the fluid media due to its viscosity (Hamrock et al., 2004). This type of lubrication is very typical of foil bearings or journal bearings that are used in hydraulics, gas turbines, compressors, or power generation systems. Articular cartilages in the hip and knee joints of the human body are also separated by a viscous synovial fluid and the nominal friction coefficients of these joints are reported to be as low as 0.002 (Jin and Dowson, 2013). Piston rings and liners, piston pins, connecting rods, and other moving parts in modern automotive engines are also separated by a lubricant film and their friction coefficients are often below 0.01 (Hamrock et al., 2004; Jin and Dowson, 2013).
Superlubric sliding regimes are also very typical of superconducting bearing systems (Hull et al., 1995) where opposing surfaces are well-separated by magnetic levitation in which magnetic forces can lift the load and may also be used to propel and guide a vehicle on a high-speed track. During relative motion, there is little or no friction between such levitated surfaces. This concept is now being employed in the development of super-high velocity bullet trains that can reach speeds as high as 500 km/h (Holmer, 2003). Nanoscale levitation due to Casimir forces may also create the kind of conditions that favor frictionless sliding motions (Lamoreaux, 2004). This effect has been demonstrated at nano- to micro-scales but the larger industrial-scale demonstration is yet to be realized. Using colloid probe atomic force microscopy, even repulsive van der Waals forces were shown to sufficiently separate surfaces and lead to superlubric sliding regimes (Feiler et al., 2008). Likewise, the Coulomb repulsion at the nano-scale contacts was reported to produce the conditions for superlubricity in liquid-solid or solid-solid contact interfaces (Sun et al., 2009). Table 1 summarizes the key superlubricity mechanisms and the most representative studies on superlubricity across the media.
Overall, in recent years, significant progress has been made in both the understanding and control of friction, which ultimately resulted in the development of new methods and materials enabling nearly-frictionless sliding regimes under a wide range of tribological conditions, media, and environment (Baykara et al., 2018). In particular, with the advent of new and more powerful computational techniques (such as super-fast, high-capacity computers enabling quantum level simulations, artificial intelligence and machine learning platforms) and advanced analytical tools (AFM, FFM, SFA, QCM, etc.), friction and its effects have lately been explored and simulated down to atomic scales. Using such tools and codes, many researchers have been able to show how atoms interact with one another under static and sliding contacts to produce friction (Hirano and Shinjo, 1990; Sokoloff, 1990; Meyer et al., 1995; Krim, 1996; Robbins and Krim, 1998; Bhushan, 2000; Bennewitz, 2005; Hirano, 2006; Mo et al., 2009; Urbakh and Meyer, 2010). These developments have also enabled the conditions under which superlubric sliding regimes may be most favorable (Sokoloff, 1990; Hirano et al., 1991; Martin et al., 1993; Hirano et al., 1997; Gao et al., 2003; Hirano, 2003; Dienwiebel et al., 2004; Luan and Robbins, 2005; Socoliuc et al., 2006). For example, it was predicted by quantum chemical and molecular dynamics simulations that when surface atoms of certain crystalline solids (such as graphite, MoS2, mica, and silicon) are twisted or rotated from a complete commensurability (or atom-to-atom registry) to completely incommensurate (or out of registry) conditions, the friction begins to transition from strong stick-slip (which is typical of high friction) to eventually effortless sliding (Erdemir, 2001; Dienwiebel et al., 2004; Luan and Robbins, 2005; Socoliuc et al., 2006). These types of superlubric sliding regimes are more typical of atomically smooth surfaces relying on incommensurability for superlubricity (and often at nano-scales). If the surface becomes rough or defective, very steep increases in friction can be expected (Erdemir, 2001; Hirano, 2006). Table 1 summarizes some of the sliding systems that were reported to afford superlubricity under sliding contact conditions. Further details of these systems will be provided under three subcategories and the underlying mechanisms that control superlubric behavior will be discussed in relation to solid, liquid, and gaseous media.
Most of the solutions for achieving a superlubric sliding regime are based on overcoming the possible mechanisms for frictional energy dissipation (Figure 2) (Berman et al., 2018b). The friction is often time associated with wear, which arises when the energy is spent to initiate damages in the sliding surfaces, manifesting themselves as cracks and defects (Figure 2A). The damage cannot be permanent as in the case of the wear, but temporary, as in the case of the molecular deformation (Figure 2B). The effects that usually play smaller roles are associated with the local heating at the asperity contacts, the so-called thermal effect (Figure 2C), or the phonon vibrations propagating inside the contacting materials (Figure 2F). To overcome friction, efforts should also be made to minimize the interactions between the surfaces by reducing the electrostatic attraction of the materials due to sliding induced surface charges (Figure 2D) and minimizing the formation of the chemical bonds between the surface atoms (Figure 2E). In this case, the nature of the surrounding environment plays a critical role, as it can minimize surface interactions by passivating the dangling bonds or inducing surface material defects such as humidity-based corrosion of the contacting interfaces (Figure 2G). Finally, the friction may originate from the structural or mechanical interlocking of the contacting asperities during sliding (Figure 2H). Due to all of these possible contributors to the friction losses, achieving superlubricity has remained highly desirable but very challenging for a long time.
FIGURE 2. Schematics of possible mechanisms for energy dissipation during sliding related to: (A) wear; (B) molecular deformation; (C) thermal effect; (D) electronic effect; (E) bonding; (F) phonons; (G) environment/chemistry; and (H) structural/interlocking. Reprinted with permission from (Berman et al., 2018b).
Fundamental computational studies by Hirano and co-authors have predicted the possibility of superlubric sliding regimes between the defect-free, atomically smooth, and highly-ordered surfaces of some crystalline solids back in early 1990s (Shinjo and Hirano, 1993; Hirano, 2003). According to their studies, the most important requirement for superlubricity is to mate such solids in an incommensurate or perfectly misaligned/misfit manner. This type of superlubricity is often called “structural superlubricity” since when or if the atoms are shifted out of incommensurability, these surfaces begin to show high friction (Müser, 2004; Socoliuc et al., 2004; Dienwiebel and Frenken, 2007; Gnecco et al., 2008a; Filippov et al., 2008).
Experimentally, it was confirmed that if and when the incommensurability requirement is met, superlubricity may indeed become a reality. In fact, several researchers have confirmed the existence of superlubric sliding regimes for the incommensurate surfaces of silicon, mica, graphite, MoS2, and a few other solids (Hirano et al., 1991; Dienwiebel et al., 2004; Li et al., 2017). Using AFM and FFM, researchers have reported friction coefficients ranging from essentially zero to 0.005 for graphite (Lee et al., 2010; Berman et al., 2015b). Figure 3 illustrates the commensurate and incommensurate sliding regimes that lead to very high or super low friction in graphite, respectively. In another sliding system, Hirano’s group has also demonstrated super-low friction for the tungsten tip against silicon wafer under ultra-high vacuum conditions (Hirano and Shinjo, 1993). Likewise, Dienwiebel et al. performed a systematic study with tungsten tip and graphite surface to explore the transition of friction from commensurable to the incommensurable state of sliding surfaces (Dienwiebel et al., 2004). It was shown that the friction force comes down from a very high value to a near-zero level when surface atoms are rotated from a fully commensurate to a completely incommensurate state of contact.
FIGURE 3. Atomic-scale illustration of (A) commensurate (high friction) and (B) incommensurate (super low friction) contacts. A similar concept of (C) commensurability and (D) incommensurability is presented for 2D films of hexagonal structure.
Interestingly, a similar effect of rotation on superlubricity was demonstrated for a non-self-mated material pair, such as in the case of graphene and hexagonal boron nitride (Figure 4) (Song et al., 2018). The molecular dynamic simulations suggested that the observed frictional anisotropy originates from the damping of the out-of-plane distortions of the carbon atoms. This result suggested that the structural superlubricity is achievable for a wider range of the lattice mismatch systems (Chen and Li, 2020).
FIGURE 4. Relationship between the frictional stress and rotation angle between graphite and hBN under ambient conditions. (A) Peaks of high friction are observed at 0, 60, 120, 180, 240, and 320o; these peaks represent a complete state of commensurability. (B) Between these peaks are the regions with ultra-low friction due to the incommensurate state of atomic-scale contact. Reproduced with permission from (Chen and Li, 2020).
Another superlubric sliding regime that is more prevalent to nanoscale contacts is known as thermolubricity. In this type of superlubric sliding regime, the sliding speed is normally very low and the AFM tip has enough time to completely destroy the stick-slip motion through thermal activation (Gnecco et al., 2008a).
Researchers have shown that superlubricity can also be achieved in a number of alkaline halides (e.g., NaCl and KCl) (Steiner et al., 2009). Electro-capacitive or piezo-induced agitation or oscillation at certain resonance frequencies were found to markedly reduce friction in both conducting and insulating alkaline halides like NaCl, KBr, HOPG, and mica surfaces (Socoliuc et al., 2006; Gnecco et al., 2008b).
In addition to materials-enabled superlubricity, system adaptation approaches were considered for enabling the ultra-low friction behavior. Recently, superlubricity was demonstrated in a friction force mode of the atomic force microscope by inducing external vibrations of the system (Shi et al., 2021). The authors showed that while in regular scanning experiments the friction increased with the normal load increase, however, once the vibration was applied there was nearly no change in friction with the load. Selection of certain frequency, i.e., finding the resonance between the external vibration frequency and the resonant frequency of the cantilever beam, was crucial for achieving a significant reduction in friction and achieving superlubricity.
Liquid phase lubrication (that is, lubrication using oils, alcohols, fuels, or other fluids) has been divided by engineers into four lubrication regimes, namely, boundary lubrication, mixed lubrication, elastohydrodynamic and full-fluid film lubrication. Several standard lubrication engineering textbooks explain these regimes in detail. Despite the ubiquitous use of oil-based lubricants in the automotive and engineering/manufacturing fields and incremental improvements over time, achieving and maintaining macro-scale friction coefficients of below 0.01 (superlubric threshold) across the lubrication regimes under real-life operating conditions has been rather difficult. There are several tribological applications where such deficiency in lubricating technologies has been a limiting factor in design and realization of the next-generation moving mechanical systems. Pertinent examples include transportation vehicles, gears and bearing systems of wind turbines, and a myriad of other types of moving mechanical assemblies that exist in manufacturing, aerospace, power generation and other cross-cutting industrial sectors. Fundamental physical aspects of common oil-based lubricants, such as viscosity and its strong dependence on temperature as well as the stability of the additive packages, affect their lubrication properties in the long run. The four lubrication regimes mentioned exert different levels of shear forces and contact pressures within the contact zone, demanding a robust dynamic response from the lubricant itself so that it can remain efficient across the application conditions.
In reality, liquid lubricants that can exhibit superlubric performance in multifarious applications and over a range of operating conditions are yet to be realized. Among the available liquid media, polar and ionic liquids have been found to be most amenable for achieving superlubricity (Zheng et al., 2021). Glycerol and glycol are canonical examples that have shown promising superlubricity performance. These two liquids have lowered friction especially when the sliding parts involve certain ceramics (Wang et al., 2019), are coated with an inert material such as DLC (Björling and Shi, 2019), ta-C (Long et al., 2019), Sapphire (Liu et al., 2019), Alumina (Wang et al., 2019), and when sliding against engineering materials such as bearing steels (Ma et al., 2021a; Ma et al., 2021b), hardened steels (Ma et al., 2021b), carburized steels (Matta et al., 2008), and simple silicate glasses (Zhi-Zuo et al., 2011), silica wafers (Ge et al., 2018a). Additionally, these materials have gained substantial engineering interest since they are amenable to further modification by the addition of 0D materials (Ren et al., 2020), 2D solid phase materials (Ge et al., 2018a; Ren et al., 2021), and liquid additives (Matta et al., 2008; Wang et al., 2016; Liu et al., 2019; Han et al., 2020).
In the presence of viscous fluids, under certain load and sliding speed conditions, the sliding may result in the elastohydrodynamic lubrication (EHL) regime with the formation of a thin lubricant film between the sliding surfaces (Ma et al., 2021a). The properties of this lubricant film have a critical impact on the friction coefficient of the contact interface and therefore the performance and reliability of machine components. The majority of the liquid-lubricated systems that showed the superlubric sliding are aqueous-based (Ge et al., 2019). The liquid lubricant-enabled superlubricity usually relies on the formation of a tribofilm, a hydration layer, or a molecular brush. Reddyhoff et al. (Reddyhoff et al., 2021) have reported a tribosystem which yielded superlubricity under full-film EHL conditions relevant to bearings, gears, and many other machine components. Superlubricity was enabled when the intercalated liquid formed a very thin layer thus enabling easy shearing between the sliding surfaces (Figure 5) (Chen et al., 2013).
FIGURE 5. (A) Friction coefficient as a function of the relative humidity, (B,C) illustrating the molecular level structure and interaction of intercalated water with sliding surfaces. Reprinted with permission from (Chen et al., 2013).
Polymer brushes have also been shown to afford ultra-low friction to sliding interfaces through the formation of very closely spaced layers of end-grafted polymer chains between sliding surfaces (Lee et al., 2003; Feng et al., 2021). Polymer chains stretch out into the carrier fluids in order to reduce the overall free energy of the system and thus form the brush-like structure on both faces. During sliding, these brushes provide super-low friction in oils and some other aqueous environments. Obviously, understanding the underlying mechanisms that produce superlubricity in these liquid lubricants will not only help design new sliding systems but also define the specific application conditions where superlubricity can be maintained for long hours of operations.
Most of the solid lubricants or self-lubricating solids (e.g., DLC, graphite, MoS2, etc.) demonstrated very high sensitivity to the chemical composition of test environments, in particular to humidity (Chhowalla and Amaratunga, 2000; Berman et al., 2013; Berman et al., 2014a). For example, the infamous Galileo High-Gain Antenna failure has been attributed to the delamination of MoS2 coating during terrestrial humid air testing (Galileo, 1992). In most cases, the presence of water in surroundings prevented the superlubricity by interfering with their chemistry reorientation to an incommensurate state of contact at the interface (Berman et al., 2015a). Figure 6 summarizes the concepts used for the superlubricity control by the surface passivation in MoS2 and DLC systems.
Khare et al. (Khare and Burris, 2013) have reported the effects of environmental water and oxygen on the lubricity aspects of MoS2. Despite MoS2 being the preferred lubricant for space applications, its terrestrial performance in terms of reaching macro-scale superlubricity is marred by the presence of water vapor. The easy shear or inter-layer slip in MoS2 is hindered by the formation of MoO3 and by the adsorption of water molecules at the edge/dangling bonds. In their systematic study, they established a direct correlation between the lubrication deterioration and the type of intercalating or interacting species (O2, H2, N2, H2O) when tested at room temperature. Amongst the considered passivating molecules, humidity showed a pronounced effect on tribological performance whereas the performance was rather insensitive to the oxygen content in the sliding atmosphere. This was due to the oxidation (damage) being a surface or sub-surface phenomenon, whereas water molecules had a much more deleterious effect as they adsorbed onto the surface and diffused into the bulk over time, thus preventing easy interlamellar share and achievement of superlubricity. From an experimental and application point of view, researchers must be mindful of the fact that diffusion of water molecules into nano-crystalline MoS2 flakes occurs over time. Improperly stored samples/powders can be contaminated by ambient water that can strongly influence the experimental results. Such physically adsorbed structural water can be rapidly desiccated by thermal treatment as compared to vacuum desorption. The favorable kinetics of thermal desiccation and over vacuum desiccation can be used to engineer high-temperature MoS2 based solid lubricants as discussed later in the manuscript.
Surface passivation of carbonaceous lubricant materials (e.g., bulk diamonds, diamond thin films, ultra-nanocrystalline diamonds (UNCD), Diamond Like Carbon (DLC), and tetrahedral amorphous carbon thin films) was imperative in achieving and maintaining low friction and wear. Unlike MoS2 where water was a degrading agent, both water and hydrogen were suggested as good molecules for effective passivation of dangling σ- or covalent bonds of these materials. Konicek et al. (Konicek et al., 2008) have shown lowering of friction across different normal loads with increasing relative humidity for UNCD and ta-C thin films. Passivation of unsaturated covalent bonds with H, OH, or other groups was essential in hindering the formation of strong covalent bonds across the self-mating interfaces. The gaseous adsorption not only passivates the surface dangling σ-bonds but also weakens π–π∗ interactions between the carbon atoms on counterfaces, thereby enhancing superlubricity.
As an engineering approach, the window for achieving superlubricity using DLC and ta-C sliding in self-mating conditions or against steel can be broadened by introducing the type of surface adsorbates that can enhance surface passivation in the tribosystem. In a model study, Khan et al. (Khan et al., 2018) proposed an acid treatment route to further enhance the surface hydrophilicity of DLC. Such a treatment combined with the presence of an organic friction modifier (such as alkyl-amine-compounds) effectively passivated the dangling σ-bonds and reduced the extent of chemical activity and thereby reduced friction. There is broad scope to exploit the tribological benefits of surface passivation using friction modifiers, and other engineering solutions to further push DLCs towards overcoming the limitations for continuous superlubricity.
Superlubricity has been observed in a variety of solid materials at the nano to macro-scale tribological systems. However, the condition for superlubricity has been very different from one class of materials to the next. In the following, we will divide these into sub-categories and try to elaborate on the underlying or applicable mechanisms that triggered superlubricity under specific conditions.
With the advent of nanotechnology, a myriad of novel nanomaterials with 0 to 3D architectures have recently been developed including 0D nano-onions (Shenderova et al., 2008), nano-diamonds (Shenderova et al., 2008; Shirani et al., 2019a; Shenderova et al., 2019), and amorphous carbon nano-spheres; 1D nano-tubes, -fibers, -rods, and -whiskers (Alexandrou et al., 2004); and 2D graphene (Berman et al., 2014b; Berman et al., 2016), h-BN (Oshima and Nagashima, 1997), MXene (Gogotsi and Anasori, 2019), black phosphorous (Ling et al., 2015), and metal dichalcogenides (Manzeli et al., 2017). More has been discovered recently with the aid of artificial intelligence/machine learning (AI/ML)-based algorithms (Baboukani et al., 2020). Most of these are mixed with oils to achieve nano-colloidal lubrication (Miura et al., 2005), but recent experiments have shown that many of them could also provide superlubricity under dry sliding conditions (Gnecco et al., 2008a; Kawai et al., 2016). In other solid sliding systems involving graphite, Miura et al. achieved nearly frictionless sliding regimes when C60 is used as intercalates between the alternating layers of graphite (Miura et al., 2005). It was thought that with the introduction of C60, the interlayer spacing between graphite sheets was greatly increased, and perhaps the spherical C60 was acting as a molecular-scale ball bearing.
To create a better solid lubricant solution, 2D materials were analyzed in terms of their friction and wear reducing characteristics that can positively affect the operation of the moving systems across scales and sliding regimes. The atomically-thin nature of the films allows using 2D materials both in nanoscale systems, where the lubrication approaches involve the use of the materials properties on their own, and macroscale systems, where conformality of the coating allows to protect the substrate materials from the friction and wear induced damage.
Structural uniformity and easy shearing of the 2D materials make them promising candidates for more precise control of friction and even reduce it down to a near-zero value. With the major goal of minimizing friction and wear at an industrial scale, the efforts in creating structural superlubricity went beyond the nanoscale contact. The major challenge is minimizing the contact area of interactions between the surfaces while preserving the loading capability of the surfaces (Hod et al., 2018). In the case of incommensurate contact, the interactions between the surfaces are minimized at the atomic scale. However, permanently keeping the contact interface in an incommensurate state is technically challenging and a new approach for reducing the contact interactions is needed. The first demonstration of the practically viable macro-superlubricity was provided only a few years ago. In that case, the 2D material, graphene, was combined with diamond nanoparticles (Berman et al., 2015a). By utilizing all the beneficial properties of graphene, superlubricity was achieved from the phenomenon of nanoscroll formation of graphene platelets around the nanodiamonds. The formed scrolls enabled the separation of the sliding macroscale surfaces, leading to a reduction in the contact area. It was demonstrated that only a 65% reduction in the possible contact area is sufficient to substantially minimize the friction losses. Existence of unscrolled graphene preserved beneficial properties of 2D materials in protecting the underlying surfaces and minimizing their interactions with each other. A graphene + nanodiamond combination led to a decrease of the coefficient of friction from ∼0.15 in initial unscrolled configuration to superlubricity regime of ∼0.004 when scrolls are formed. It should be noted that the observed superlubricity was stable over the range of temperature, load, and velocity conditions, though the elimination of the humidity effect was critically important.
A wide range of 2D materials opened new opportunities for achieving ultralow friction regimes with materials beyond graphene. The first discovery of the macroscale graphene-enabled superlubricity suggested that a similar mechanism can be observed for other materials. The test was performed with molybdenum disulfide (MoS2) flakes replacing graphene in a similar 2D material + nanodiamond configuration (Berman et al., 2018a). In that system, friction values also dropped to near-zero, however, analysis of the wear debris suggested that the mechanism of the friction reduction is different from mechanically-initiated nanoscroll formation. Specifically, in the case of MoS2, the superlubricity rather originates from tribochemical activity inside the wear track. During the initial sliding period, when the friction in the system is high, favorable conditions for initiating the tribochemical processes between nanodiamonds and MoS2 flakes induce material transformation. Large contact load and local heating events experienced by the materials in the contact interface induce disintegration of the MoS2 film into molybdenum and sulfur atoms. Sulfur is highly reactive towards sp3-bonded carbon of the nanodiamond lattice, leading to disruption of the diamond lattice and carbon amorphization. Once the heating is released, amorphized carbon converts into onion-like carbon structures, capable of withstanding high contact loads and providing similar graphene + diamond nanoscroll contact area reduction and incommensurability effects. Alternatively, similar concept is true when replacing the nanoparticle material instead of 2D material, as it was shown for graphene + iron nanoparticles configuration (Berman et al., 2019).
Previous research has shown that layered or lamellar materials (such as graphite, MoS2, h-BN, mica, etc.) in the form of bulk structures rather than as several layer 2D films are most suitable for achieving superlubricity. In all of these solids, again the incommensurability was found to be one of the most important prerequisites for superlubricity. For example, Hirano et al. observed four orders of magnitude reductions in the amount of frictional force when two mica sheets were increasingly rotated out of a fully commensurate contact to a totally incommensurate state of sliding (Hirano, 2014). Furthermore, Dienwiebel et al. (2004) reported near-zero friction between sliding contact surfaces of tungsten tips and graphite sheets at nano-scale contacts. In the case of Dienwiebel’s experiments, superlubricity was achieved by bringing contacting surface atoms to complete incommensurability as shown in Figure 2. Martin et al. (1993) achieved superlubricity in ultra-pure MoS2 films under ultrahigh vacuum and incommensurate sliding conditions. Among the other lamellar solids, WS2 has also been shown to achieve superlubric friction values when tested in ultrahigh vacuum test environments (Joly-Pottuz and Iwaki, 2007). Importantly, the large lattice mismatch in MoS2/graphene and MoS2/h-BN enabled the superlubricity even without any twist angle dependence (Liao et al., 2022).
Due to their lamellar structures, certain inorganic solids can afford some of the lowest friction and wear coefficients at appropriate test environments and conditions. For example, when tested in inert gases or vacuum, MoS2 was shown to provide friction coefficients of down to unmeasurable levels by Martin et al. (1993) in ultrahigh vacuum.
Liu et al. (Liu et al., 2012) have lithographically prepared microscale mesa on graphite and upon shearing, observed that the sheared section retracts back without necessitating any force. They attributed such self-retraction to the superlubricity of the incommensurate surfaces of graphite at a micro-scale (Liu et al., 2012).
DLC films are very unique in that they can provide graphite to diamond-like friction and wear behaviors depending on their chemical and structural natures (Erdemir and Donnet, 2006). Concerted efforts by many researchers also resulted in the development of new breeds of diamondlike carbon films providing friction coefficients down to superlubric sliding regimes under both dry and lubricated conditions. The most important requirement for achieving superlubricity was found to be complete hydrogen termination of their sliding surfaces. This was either achieved by synthesizing DLC in a highly hydrogenated plasma to fully terminate dangling sigma bonds of surface carbon atoms or maintaining high hydrogen concentration within the test chambers during tests so that the sigma bonds are instantly and continuously terminated by hydrogen in the vicinity of sliding contacts. Through some very unique tribochemical interactions, it turns out that hydrogen reacts with carbon atoms to form a hydrogen-terminated top layer which in turn creates repulsive forces diminishing adhesion and thus friction. Post-deposition hydrogen plasma treatment of hydrogen-poor or free DLCs was also shown to result in superlubric sliding behaviors (Eryilmaz and Erdemir, 2008).
Previous research has confirmed that there exist many types of DLC coatings that are able to provide superlubricity (Erdemir and Eryilmaz, 2014). In addition to single-phase DLCs, several kinds of DLCs that are doped by other elements are now available and these tend to provide superior mechanical (toughness and hardness), thermal (high resistance to heat and thermal degradations), and tribological properties (friction and wear). Among others, carbon nitride (CNx) coatings have attracted strong interest from the hard-disk recording industry as one of the most preferred hard-disk coatings due to much superior tribological properties in the presence of molecularly thick oil films on their surfaces. The typical concentration of nitrogen may vary from about 5 to more than 15 t% in order to enhance hardness, stiffness, surface energy, and other surface-sensitive properties (Erdemir and Eryilmaz, 2014).
Dedicated studies by Kato and Adachi have shown the possibility of achieving superlubricity with CNx after a brief run-in or surface conditioning in an oxygen environment. Specifically, they have shown that friction coefficients of as low as 0.005 are feasible in dry nitrogen following such surface conditioning stages (Kato and Adachi, 2007). Based on their surface analytical studies, they attributed such superlubric behavior to the extremely shearable nature of tribolayers forming at the sliding interface in dry nitrogen.
Superlubricity (i.e., friction coefficients below 0.01) was also achieved with silicon-doped DLC films in a high vacuum (Sugimoto and Miyake, 1990; Yi et al., 2021b). Underlying mechanisms for such super-low friction are not yet well-understood but ascribed to the generation of an easily shearable transfer layer having a special orientation with respect to the sliding direction.
Fluorine was also used as a doping agent in DLC films to mimic the chemical composition of PTFE which is known to provide very low friction coefficients. However, compared to nitrogen and silicone, fluorine was proven very difficult to incorporate into DLCs in large amounts. Tests with moderately fluorine-doped hydrogenated DLCs were shown to provide friction values down to 0.005 in ultra-high vacuum (Fontaine et al., 2004).
Sulfur was another dopant used to achieve superlubricity with DLCs. The key motivation was that sulfur would drastically alter the surface energy and hence the frictional properties of DLC surfaces. Tribological testing of such coatings indeed provided super-low friction down to 0.004 levels under ambient air conditions (Freyman et al., 2006) mainly because of a weaker bonding between adsorbed water molecules (coming from the humid air) and the sulfur and hydrogen-rich surface.
Researchers have also shown that manipulation of the random network structure of DLCs may also create the conditions under which superlubricity may be achieved. For example, fullerene-like hydrogen-free and hydrogenated DLC films were produced out of CNx tested for their friction and wear. The friction coefficients of fullerene-like CNx were high (e.g., 0.15–0.2) but the friction coefficient of hydrogenated fullerene-like DLC films sliding against Si3N4 was reported to be less than 0.01 depending on the contact load and the type of tribochemical films that were present on rubbing surfaces. Mechanistically, such a superlow friction behavior was attributed to the formation of a hydrogen-rich transfer layer providing very low shear during sliding (Wang et al., 2011).
Recently, it was shown that when hydrogenated DLC films are slid against zirconia balls, superlow friction coefficients (i.e., below 0.001) can be achieved. Such an outstanding friction coefficient was attributed to the formation of a polymer-like tribofilm under extreme pressures (i.e., 2.6 GPa) through a very unique catalytic effect excreted by zirconia balls. It was argued that under such extreme pressures a special kind of tribocatalytic reaction is triggered between the hydrogen molecules in the environment and the top carbon atoms of DLC film giving rise to a situation where strong repulsive forces come into play (Nosaka et al., 2015; Nosaka et al., 2017).
Besides the DLCs mentioned, diamond has also attracted special attention for its potential superlubricity. From a tribological standpoint, bulk diamond or thin diamond films can provide super-hardness and rigidity and hence superior wear resistance. However, friction properties of diamond surfaces can be strongly affected by gaseous species such as hydrogen, oxygen, or water molecules in the surrounding atmosphere. Recent studies by Kumar et al. and Konicek et al. have confirmed extraordinary wear resistance of ultrananocrystalline diamond films and further reported ultralow friction (i.e., down to 0.01 or below) at the macroscale (Konicek et al., 2008; Kumar et al., 2013) in the humid air. Such low friction values were attributed to water molecules being dissociated into hydrogen and hydroxyl ions at the sliding contact interface and then effectively passivating the dangling sigma bonds of surface diamond atoms, thus providing ultralow friction.
While solid material systems demonstrate high applicability at controlled environment conditions, the challenges associated with their design and deposition as well as their eventual degradation signify the need for liquid lubrication solutions. Use of oil-based lubricants [including synthetic (Rudnick and Shubkin, 1999; Jacques et al., 2019) and plant-based (Salimon et al., 2010; Cermak et al., 2013; Li et al., 2018; Romsdahl et al., 2019)] is a common industrial approach allowing to reduce frictional losses in moving components, though achieving the superlubricity with oils is challenging. The materials systems that render superlubricity in liquid media commonly include aqueous hydrocarbons, and ionic systems, as pure systems or with additional solid or liquid additives.
Water has been shown to produce superlubricity with as little as 0.1646 mol/L addition of phosphoric acid into the system (Gao et al., 2018). The tests were conducted in a unidirectional sliding test, under 300 g load (700 MPa pressure) and 56 mm/s liner sliding speed (SiO2 sliding against Si3N4). Following a run-in period of about 12 min, the friction dropped to 0.003 and remained stable thereafter. The addition of phosphoric acid led to the disruption of structural water (that is the ordered O-H network) as evidenced from the sum-frequency generation (SFG) vibrational spectroscopy. The disruption of the O-H structure was in turn attributed to the strong hydration ability of the phosphoric acid. This is different from previously reported studies where under similar conditions, friction was 0.004 and stable for 3 h (Li et al., 2011). In that case, as suggested by the Raman spectroscopy analysis, the superlubricity was attributed to formation of solid-like films, mostly hydrates of phosphoric acid with a hydrogen-bonded network, over the sliding surfaces. The hydrogen bond effect was key in forming a hydrated water layer which has a lower shear strength, and interfacial Coulomb repulsion from the dipole-dipole effects all cumulatively resulting is prolonged superlubricity (Li et al., 2011).
Notably, superlubricity in aqueous solutions has been sensitive to the hydrogen ions concentration (Li et al., 2012). Hydrogen ions firmly adsorbed on sliding systems by protonation reaction thus producing positively charged surfaces. The superlubricity, thus, has been attributed to the synergy of the charged double layer effect and the hydration effect. A more elaborated microscopy investigation after the removal of excess solution indicated formation of hydrogen bond network in the tribolayer composed of thin hydroxide and dihydrogen phosphate (Li et al., 2013).
Repulsions between two negatively charged double layers in conjunction with classical shearing of hydration layers have also been reported in alkali metal salt solutions that effectively produced superlubricity (Han et al., 2019). Divalent and trivalent ions exhibited extremely low friction coefficients of 0.005–0.006 and 0.002–0.004 under similar sliding conditions. Systematic parametric studies also showed the relation between the size of the anion and its effect on the lubricity. Later, similar behavior of attaining superlubricity with smaller ions, such as Li, Na, and K, was demonstrated under high contact pressure between the Si3N4 ball and sapphire disk (Han et al., 2018). Unlike larger ions, the primary mechanism for attaining superlubricity in this case was smoothing of asperities causing boundary layer lubrication, and formation of hydration shells surrounding alkali metal ions effectively separating the tribopairs and thus lowering friction.
1-dodecanol showed superlubricity under sliding-rolling conditions as tested in a miniature traction testing machine (Reddyhoff et al., 2021). Diamond anvil cell experiments showed that 1-dodecanol undergoes a pressure-induced solidification when introduced into elastohydrodynamic contacts, with temperature and pressure affecting the polymorphs that formed under contacts. These morphological changes resulted in the formation of lamellar hydrogen-bonded hexagonal structures that acted as the lubricating sling interlayers. The advantage of such tribosystem is that the phenomenon does not depend on kinetics of the tribolayer formation, but rather on the polymorphism of the system creating the reservoir of surrounding liquid that can immediately replenish the contact when needed. The study also reported that the lamellar structure could rupture under higher temperatures and pressures, thereby making 1-dodecanol amenable for a targeted lubricity application (Reddyhoff et al., 2021).
Pure isooctane was shown to provide superlubricity when sliding against SiC in a flat-on-flat configuration as seen in many engineering systems (Schreiber and Schneider, 2019). SiC being harder than steel, resists plastic deformation and accommodates sliding stresses by local degradation that causes formation of new surfaces. The formed surfaces passivated with siloxane and silanol groups as well as a continuous presence of a thin lubricating isooctane film are responsible for the sustained superlubricity.
While glycerol can be very effective in passivating sliding interfaces, its high viscosity often leads to the formation of thick fluid films, viscous losses, and thus high friction. Water could provide a great option to lower the viscosity and hence act as a friction modifier for glycerol due to its extremely low viscosity, low cost, good miscibility, and worldwide availability. Ma et al. (Ma et al., 2021a) reported on the effect of water content on the macroscale lubricity behavior of glycerol in pure sliding conditions. Their study identified a critical water content for achieving a mixed elastohydrodynamic regime that would favor superlubricity. Specifically, it was observed that increasing water content in glycol produced a monotonous decrease in viscosity, theoretical film thickness, and hence friction up to 0.2 water/glycerol weight ratio, after which friction increased above the superlubric threshold (Ma et al., 2021a). A similar trend was also observed while varying other key operating conditions such as sliding velocity and normal load. In both cases, the friction coefficient decreased up to a certain threshold with the change in one variable while the other one was held constant. Mixed/elastohydrodynamic regime computer simulations indicated the formation of a tribochemical boundary film that limited the interaction of the asperities at the sliding interface and thus enabled exceptional lubricity. These results collectively indicate that there is a specific window for achieving and maintaining superlubricity with respect to load, water content, sliding velocity, and surface roughness.
Like water, the lubricity of glycerol can also be altered by adding small quantities of ionic liquids, especially in the thin film lubrication regime (Hua et al., 2022). Small quantities (0–3 wt.%) of [Choline][Proline] ionic liquid were added to glycerol and the lubricity of mixed fluid was tested under simple sliding conditions with humidity as a variable. Under ambient conditions, as little as 1 wt.% of additives produced a superlubricity effect, with increasing quantities causing further improvements. Additionally, increasing the wt.% of glycerol decreased the time to attain a steady-state, viscosity, and a fraction of water evaporated from the tribosystem. It was shown that H+ ions from water could form a layer on the contact surfaces that in effect preferentially supports the applied normal load and locks in water molecules. The effect is similar when adding ionic liquids adsorbing on the surfaces (Hua et al., 2022). The advantage of this route over pure moisture manipulation is that superlubricity can be achieved even in a thin film lubrication regime rather than in elastohydrodynamic lubrication (EHL) regimes that need thicker liquid entrapment. This development can further seed research in the direction of dynamic lubricity alteration as a function of ambient humidity, thus creating alternate routes for producing superlubricity and high shear rates in thin films.
Chemical reactions taking place in situ due to the interaction of the sliding surfaces are referred to as the tribochemical phenomenon. Surfaces used in engineering applications are often rough, but sliding induced attrition of tall contacting asperities gradually makes mating surfaces conformal. Lubrication, dominated by the interactions between asperities, is known as the boundary lubrication regime where such asperities come into direct physical contact and potentially create friction and wear. With prolonged sliding, the smoothening of surface asperities reduces the contact pressure and promotes the formation of a continuous lubricating film, thereby transitioning the sliding contact to the EHL regime. The wear debris that get entrapped into the system can either contribute to the third-body-wear phenomenon resulting in aggravated wear and friction spike or participate in tribochemical reaction and formation of tribofilms. For instance, superlubric performance was demonstrated when tetrahedral amorphous diamond-like carbon (ta-C) coating was used against steel in glycerol-containing liquid media. Although ta-C vs. ta-C was also studied, superlubric performance was only seen in ta-C vs. steel tribopair, which indicates that the Fe debris available at the contact zone played a critical role in the tribochemical reaction that led to the observed superlubricity. Long et al. (2019) revealed the tribochemical mechanism which included the mechanical smoothening of the steel ball, the formation of a very thin layer of iron oxyhydroxide, FeOOH (lepidocrite), and the subsequent absorption of water onto its surface. Liepidocrite has a 2D structure, which is energetically favorable to form in the tribosystem as compared to the 3D nuclides/crystals and the lubricity between Liepidocrite crystals originates from the weak interaction between hydrogen-faced layers. Besides the formation of FeOOH, the entrapment of glycerol and its degradation products (carbon, water, hydrogen, etc.) results in a highly lubricious EHL film (Figure 7). The in situ development of a thin oxide film that prevents the degradation of glycerol, separates contacting surfaces, and facilitates superlubricity is a tangible technique that can be used as a template for commercial applications in future technologies.
FIGURE 7. Tribochemical generation of complex iron oxyhydroxide, subsequent absorption of water onto its surface resulting in superlubricity. Reproduced with permission from (Long et al., 2019).
Graphene oxide (GO) flakes were also shown to lower friction by limiting wear loss. Macroscale superlubricity was enabled by a synergistic effect of graphene oxide nanoflakes in polyhydroxy alcohols (Ethanediol) when added in very small concentrations in the order of 0.5, 1.0, 1.5, and 2 g/L (Ge et al., 2018a). Like the previous cases, preservation and activation of water molecules were key to the diminished friction. GO invariably is associated with adsorbed water molecules and terminal hydroxyl groups and the interfaces between water molecules/graphene are the most probable sites of shearing during sliding. For sites distant from the graphene oxide flakes, hydrated GO-Ethanediol networks play an important role in the significant friction reduction and contribute toward the effective realization of macroscale superlubricity.
In summary, superior lubrication in liquid phase can be classified broadly into four categories: Engineering the rheology of the lubricants either by solid additives, ionic or polar molecules combined with fine tuning environmental conditions, sustained hydration by activation of water molecules; expanding the regimes of classical lubrication that is most favorable to superlubricity by molecular manipulation; and activation of tribochemical or tribocatalytic reactions to achieve surface passivation. A summary of these observations is highlighted in Table 2.
Achieving and maintaining low friction at temperatures above 200°C is an engineering challenge since most, if not all, traditional mineral and synthetic oil-based lubricants begin to degrade and degenerate at such temperatures under shear. In the case of solid lubrication, thermally accelerated phenomenon such as diffusion and solid-state phase transformations, thermal expansion, and contraction provide their own benefits of material replenishment and adaptation (Shirani et al., 2019b; Aouadi et al., 2020; Shirani et al., 2020b) though render frictionless sliding challenging. Meanwhile, there is a dire need for lubrication solutions in applications involving high-temperature regimes, including all kinds of turbines, transportation and manufacturing operations, and aerospace technology. State of the art of high-temperature lubrication rendering sub-0.01 friction is still in its infancy with a very limited number of studies demonstrating such a phenomenon under some very specific test conditions (Zeng et al., 2015; Gao et al., 2021; Wang et al., 2021).
Gao et al. (Gao et al., 2021) have demonstrated reliable superlubricity using a combination of antimony trioxide (Sb2O3) and magnesium silicate hydroxide coated with carbon (MSH/C) onto a nickel superalloy substrate. The coating of ∼1 µm thickness was deposited on a nickel superalloy using burnishing of a base antimony trioxide (Sb2O3) layer, and then a coaxial layer of MSH/C layer was added on top of the Sb2O3 layer. Despite the relatively soft nature of the coating (hardness of ∼2 GPa), this material combination produced superlubricity with low, steady-state friction of 0.008 at an elevated temperature of 300°C. Their results suggested that superlubricity was triggered through passivation of the base metal by Sb2O3—MSH/C thereby preventing direct metal-metal contact, subsequent in situ welding of tribopairs, and associated friction spikes. In addition to the physical separation of the tribological contacts, the observed high-temperature superlubricity was attributed to the tribochemically-generated carbon-based lubricious surface tribofilm and the formation of -O-H and Si-O groups as evidenced by in situ Raman and TEM investigations.
Observations of the high-temperature superlubricity were further expanded for the system combining Sb2O3 (base layer) and composite burnished coatings of MSH −MoS2 (Wang et al., 2021). The high-temperature superlubricity was observed only at temperatures over 100°C, strongly indicating that evaporation or disassociation of water molecules must have a direct effect on lowering friction. Wang et al. (Wang et al., 2021) revealed that MSH−Sb2O3−MoS2 composite coatings rendered respectable lubricity (friction = 0.075) in room temperature experiments, and the performance surprisingly improved by an order of magnitude to the friction coefficient of 0.007 at 200°C and above. This temperature dependence of friction above the evaporation point of water was deciphered via DSC−TG analysis, which suggested that the temperature increase accelerated the destruction of structural water (hydroxyl group in Mg−O/OH octahedral sheets), its subsequent bonding to the surface elements, and thus directly reducing friction. While no structural or morphological reorientation of MoS2 or MSH crystals was observed in TEM and Raman, water desorption may have magnified the interlayer spacing that enabled easy slip of layers. This thermophysical effect supported by inherently lubricious Sb2O3 and MoS2 exert a synergistic effect on the superlubricity process (Figure 8).
FIGURE 8. Schematic of the macroscale superlubricity accomplished by the MSH–Sb2O3–MoS2 composite coatings at high temperatures. Reprinted with permission from (Wang et al., 2021).
The efforts towards the high-temperature superlubricity also involved the use of DLC coatings. Zeng et al. (Zeng et al., 2015) studied the lubricity of DLC and steel tribopair from room temperature and up to 700°C in ambient atmospheric conditions. The lowest steady coefficient of friction, i.e., 0.008 was observed at 600°C. Although DLC was observed to influence the lubricity at lower temperatures, it was reported to undergo rapid graphitization with the temperature increase. The observed phenomena were attributed to the in situ formation of lubricious oxides such as gamma-Fe2O3 and silica, which have preferred low shearing behavior as compared to other allotropes. It must be noted that such behavior is not expected or seen in pure oxides, but only seen in complex composite oxides sliding against DLC. The high-temperature friction properties of these complex composite oxides are distinct from their room temperature behavior. In the self-generated composite oxides in the abovementioned DLC system, the softer gamma-Fe2O3 phase is chemically bonded to the high strength SiO2 phase through covalent grafting, forming a stable structure that acts as the functional solid lubricant between the contacting surfaces.
Achieving reliable high-temperature lubricity with 2D materials, such as Graphene/Graphene-Oxide and MoS2, is often limited by the processes associated with material degradation, intercalation of structural water, or graphitization or vitrification of Graphene (Khare and Burris, 2013; Khare and Burris, 2014). The superlubricity for MoS2-Graphene/Graphene-Oxide system was reported in sliding and sliding rolling conditions at room temperature (Mutyala et al., 2019a; Mutyala et al., 2019b), but they showed higher friction at elevated temperatures. To address the challenges at higher temperatures, MoS2 flakes were encapsulated with protective graphene-oxide sheets that prevented oxidation of MoS2 when exposed to ambient oxygen and water (Sumant and Ayyagari). The resulting air-brush deposited coatings demonstrated a superlubricity regime at 200°C and above. This effect was attributed to the layer passivation and anti-intercalation of MoS2 that triggered extremely low interfacial shear strength (Figure 9).
FIGURE 9. Passivation of MoS2 flakes by encapsulation with protective graphene oxide sheets. Reprinted with permission from (Ayyagari et al., 2020).
Recently, with the discovery of a range of new materials, the focus in superlubricity research has been redirected to the exploration of these new systems, such as black phosphorus and MXenes.
Among the post-graphene 2D materials, black phosphorus (BP) is one of the rising stars and has gained much attention recently due to its excellent tribological properties. Similar to other 2D materials, BP also has a layered structure, and its unique wrinkle-like anisotropic geometry provides superior optical, electrical, and mechanical properties (Tao et al., 2015). BP nanosheets can be used as additive materials in combination with oil or water-based lubricants. As an oil-based lubricating additive, ultra-thin BP nanosheets can easily enter the contact area and form a solid lubricating tribofilm to prevent direct asperity-asperity contacts. Wang et al. compared the lubricating performance of BP, GO, and MoS2 nanosheets dispersed in hexadecane and found that BP nanosheets had superior tribological performance at the lowest concentration level of 0.1 ppm (Wang et al., 2018a). A recent experimental and simulation study by Tang et al. revealed that the friction coefficient of oleic acids could be reduced from 0.1 to 0.006 with the addition of only 0.1 wt.% BP nanosheets (Tang et al., 2021). Additionally, combining BP with other lubricious materials can create a synergistic effect to reduce friction. A recent study by Tang et al. reported a friction coefficient as low as 0.034 with the addition of Ag/BP nanocomposite in PAO-based oils (Tang et al., 2020). In a related study, Luo et al. (Luo et al., 2021) showed that combining BP with other lubricating materials (such TiO2, TiL4) can also reduce the friction coefficient of PAO 6 oils down to 0.063. Each of these aforementioned studies concluded that BP nanosheets can catalyze in situ formation of carbon-based tribofilms via the decomposition of the base-oil molecules. These kinds of tribofilms are typically known not only to reduce the interfacial shear strength to reduce friction, but also to improve wear resistance under high-pressure sliding conditions (Erdemir et al., 2016; Argibay et al., 2018; Berman and Erdemir, 2021; Shirani et al., 2021).
As a water-based lubricating additive, BP can be effective to achieve superlubricity even under severe sliding conditions. BP nanosheets modified with hydroxyl groups (BP-OH) exhibited superlubricity with friction coefficients between 0.006 and 0.0006 under different sliding speeds, additive concentrations, and hertzian contact pressure conditions (Wang et al., 2018b). This is due to the retention of an interfacial lubricious water layer attached to BP nanosheets via hydrogen bonding. In a comparable study, Ren et al. (2021) reported that partially oxidized BP nanosheets (oBP) can maintain liquid superlubricity with a friction coefficient of 0.0017 even at ultra-high contact pressure (∼1.2 GPa). Oxidized or hydroxyl-terminated BP nanosheets can be trapped at the sliding contact and isolate the friction pairs by transforming the contact zone from Si3N4/Sapphire to oBP/oBP. Their molecular dynamics simulation revealed that these trapped BP nanosheets form P-O and P–OH bonds during oxidation that also facilitate the absorption and retention of water molecules at the BP surface. These retained water layers reduce friction between the nanosheets and promote superlubricity (Figure 10). While these concepts are prevalent in literature, there are some studies that claimed that superlubricity is derived from the rolling effect of BP and their structural conversion to phosphorus oxide. The degradation and tribochemical transformation of BP eventually lead to the formation of an extremely low shear strength tribofilm that reduces the friction coefficient significantly (Ren et al., 2020; Liu et al., 2021).
FIGURE 10. An illustration showing the trapped oBP nanosheets between the sliding contact of Si3N4 and Sapphire. The oBP nanosheets absorb free water molecules and create a lubricious boundary film that reduces friction. Figure adapted and reprinted with permission from (Ren et al., 2021).
Similar to the oil-lubricated contact, BP also shows a synergistic effect to reduce friction in water-lubricated conditions when used with other 2D materials such as GO (Guo et al., 2019).
MXenes, another relatively new and rapidly growing member of the 2D layered material family, are mostly transition-metal carbides, nitrides, or carbonitrides based upon the MAX-phases. The electrical and chemical properties of MXene have been extensively studied for many years to realize their implementation in energy storage devices such as supercapacitors, lithium-ion batteries, and other fields applications. In addition to their outstanding mechanical strength and flexural rigidity, MXenes have many other properties that make them a great candidate as a lubricant material for tribological applications. For instance, like Graphene and BP, MXenes also have a layered structure and low interlayer shear strength imparting self-lubrication properties. Additionally, the higher surface area to volume ratio and characteristic rich surface functional groups allows them to drastically improve the matrix-filler bonding strength when being used as additives. However, despite these unique properties and the tremendous potential to become the next-generation solid lubricating material, surprisingly very few studies concentrated on their use for tribological application to date.
Within the MXene family, Titanium carbide (Ti3C2) is one of the most common materials that has been investigated in many fields. When used as a coating material on steel substrates, the friction-induced graphitization of Ti3C2 can result in a lubricious tribofilm that prevents direct metal-metal contact and reduces wear rate and friction by 10 and 4 times, respectively (Guo et al., 2019). Ti3C2Tx-nanoparticles were also found to be very effective (up to 300%) to prevent adhesive, abrasive, and tribo-chemical wear at very low humidity levels. The observed effect was correlated with different surface terminations including -O, –OH, and -F groups and intercalated water, reducing the interfacial bonding strength and thus resulting in lower interfacial shear strength and frictional force during dry sliding on stainless steel surfaces (Rosenkranz et al., 2019). Ti3C2Tx nanoparticles were also used to reinforce polymer matrix composites. Zhang et al. reported the addition of Ti3C2 nanoparticles reduced the adhesive wear and plow friction of UHMWPE, resulting in a smoother wear surface than pure UHMWPE (Zhang et al., 2016). Ti3C2/graphene hybrid (M-G) with wrapping structure was successfully incorporated into epoxy matrix to reduce wear by 81–88% (Yan et al., 2020). The authors concluded that the self-lubricating and synergistic effect of graphene and MXene hybrid wrapping structure, in combination with the formation of a tribofilm at the sliding interface, resulted in this outstanding wear performance.
In many recent works, Ti3C2Tx MXenes have been incorporated as an additive material to develop metal matrix composites. Hu et al. reported a Ti3C2Tx/Al composite with a COF of twice lower than bare aluminum in dry sliding conditions (Hu et al., 2020). Mai et al. (Mai et al., 2019) designed Ti3C2 nanosheets/copper composite coatings with COF and wear rate 46% and 19 times lower than their Ti3C2-free counterpart. Ti3C2-rich compact tribolayer formed on the worn surface, which reduces the direct metal-to-metal contact, meanwhile provides easy shear in the contact interface. Recently, Yin et al. (Yin et al., 2019) reported a Ti3C2/nanodiamond coating which showed ultra-wear resistance with almost no visible wear when slid against a PTFE ball. Atomic-scale and macroscale characterizations revealed the in situ formation of a nanostructured tribofilm at the sliding interface. The unique lubrication mechanism was derived from the combined effect of PTFE’s self-lubricating effect and their porous structure to incorporate nanoparticles in the tribofilm, MXenes easy layer shearing, and self-rolling effect of the nanodiamonds, resulting in highly flexible polymer chain movement and super low surface energy at the interface. A recent computational study reported very low energy barriers between MXene layers and showed that Ti3C2 MXene terminated with −OH and −OCH3 have a lower interlayer friction coefficient when compared to the ones with -O-terminated surface groups (Yin et al., 2019). Many recent studies also reported using Ti3C2 MXene as an additive material to improve friction properties of base oils by enlarged interlayer spacing, enhanced load capacity, and the formation of a uniform and continuous tribofilm (Yang et al., 2014; Liu et al., 2017; Xue et al., 2017; Zhang et al., 2019).
All of the aforementioned studies utilizing MXene alone or in combination with other 2D materials or lubricants demonstrate that MXenes have great potential as a solid lubricant. However, none of these studies reported superlubricity. One way to achieve this is to use them in conjunction with other lubricious materials such as DLC or glycerol. Huang et al. (Huang et al., 2021) reported a friction coefficient of 0.006 while sliding Ti3C2 MXene deposited on SiO2-coated silicon (Si) substrates against DLC-coated counterface in a dry nitrogen environment. Additionally, they found that the addition of graphene to Ti3C2 had a synergistic effect on friction and wear, with a reduction in friction coefficient and wear rate by 37% and a factor of 3, respectively. Yi et al. (Yi et al., 2021a) have shown that friction can be reduced to as low as 0.002 and be maintained for at least 3 hours when glycerol is doped with Ti3C2 MXene. MXenes when added to glycerol being used as a lubricant between Si3N4 ball and sapphire disk tribopair was observed to form tribofilm containing primarily colloidal silicon oxides and titanium oxides (Figure 11). These tribofilms get uniformly adsorbed on the friction pairs and prevent direct asperity contact. The H+ and OH- groups present in the tribofilm also interact with the MXenes via hydrogen bonds which produces hydration layers on the nanoflakes to reduce the shear strength of the liquid film. Thus, friction is reduced by a series of synergistic lubrication effects between Ti3C2Tx MXene nanoflakes and glycerol. The lubricity effects tend to decrease with higher concentrations of MXene additives. This is due to the agglomeration of MXene nanoflakes and subsequent collision of these aggregates during sliding which leads to an increase in friction coefficient. However, in comparison to other 2D materials that are extremely prone to aggregate formation, such as graphene or MoS2, Ti3C2Tx MXene nanoflakes can maintain uniform distribution in a glycerol solution for a much longer period.
FIGURE 11. An illustration showing the mechanism of superlubricity in a Si3N4/sapphire contact by the incorporation of Ti3C2Tx MXene nanoflakes in a glycerol media. Reprinted with permission from (Yi et al., 2021a).
Despite the technological advancement with MXene addition in glycerol, true industrial viability can only be realized when MXenes’ commercialization and reliable mass production are achieved. However, from a technology standpoint, the inclusion of reactive 2D materials that can form passivating hydroxide species, enable entrapment of free glycerol and water molecules can be a guiding template for future evolution.
With the expansion of the knowledge of the superlubricity mechanism, new efforts were focused on manual control of the friction. The concept has been recently proposed for controlling the ultralow friction behavior by application of the electric potential (Li et al., 2014; Fajardo et al., 2015; Di Lecce et al., 2020). For this, a new class of liquid lubricants, ionic liquid (IL), was considered as a promising candidate. Tribological studies demonstrated that the lubricating properties of ILs can be controlled and manipulated by application of an electric potential to the sliding lubricated surfaces. Li et al. (Li et al., 2014) demonstrated in the AFM experiments that ILs confined between the silica tip and graphite surface can be polarized to reach super-low friction (superlubricity) in situ. Depolarizing, however, suppressed superlubricity and increased friction.
Fajardo et al. (Fajardo et al., 2015) further theoretically evaluated the feasibility for the control of the friction between the layers of nanoconfined ionic liquids (Figure 12). In their simulations, the authors presented the IL as a layer of mixture of oppositely singly charged spheres interacting via short-range repulsive Lennard-Jones and Coulombic potentials. Results indicated a decrease of friction with increasing voltage applied to the surfaces and suggested that anion rich boundary layers are more favorable to easy shear. Thus, superlubricity was activated by strong interactions of the ionic layers with surfaces to sustain the lubricant presence and shearing at the sliding interfaces.
FIGURE 12. (A–C) Schematic of the model and (D) pPotential energy surface for cation sliding. (E) the changes in the friction as a function of load with increase in the applied potential. (F) charge dependencies of the friction force, shown for two loads, 188 MPa (green curve) and 500 MPa (blue curve). Reprinted with permission from (Fajardo et al., 2015).
Thus, future efforts in the superlubricity can be further directed not only to the design of more complex material systems but also to the external manipulation of the frictional forces by applied fields.
From the foregoing, it is very clear that significant progress has been achieved in not only atomic/molecular-scale understanding of superlubricity but also in synthesis and macro-scale demonstration of superlubricity in a myriad of new materials, coatings, and lubricants. In particular, with the discovery of novel 2D materials, there has been an explosion in publications focusing on superlubricity. With recent advances in computational modeling and simulation tools, we now have a better understanding of the underlying mechanisms and such understanding is also helping us to better design surfaces to attain superlubricity. With the culmination of all these developments, it now looks more feasible to design and fabricate new tribological systems that can meet the increasingly more stringent application conditions of future mechanical systems. In particular, new 2D materials like MXene and black phosphorous seem very promising to achieve superlubricity in industrial-scale systems especially when used under liquid lubricated systems also containing highly polar molecules. Regardless of the type, the superlubricity of most materials seems to be strongly influenced by a number of environmental and test-condition-specific factors. For example, the chemical state of the test environment seems to have a strong effect on the friction and wear performance of super-lubricious materials and coatings. Specifically, some 2D materials need inert or ultrahigh vacuum conditions to provide super low friction, while others seem to depend on such molecular species like water and polar or alcohol molecules to provide superlubricity. During dynamic sliding, these molecules react or interact synergistically to minimize adhesive bonding hence friction. Meanwhile, in some other materials systems, such as DLC, MoS2, and Graphene, reactions with environmental species may have an adverse effect; in a sense, they tend to enhance adhesion and hence friction.
It is important to note that in all of the reviewed cases, the surfaces are well-separated by a fluid film or some repulsive force. The absence of direct metal-to-metal contact prevents the rise of strong adhesive forces and the Columbic or roughness effects that only come into play when and if there were a direct or intimate contact. Given the fact that all real engineering surfaces could be very rough and full of structural defects at atomic scales; additional roughness or ploughing effects on friction may arise and thus hinder superlubricity induced by fluid film lubrication (Hirano, 2006; Tartaglino et al., 2006). Furthermore, fluid film lubrication is often not a feasible solution in situations where low friction bulk materials or coatings might be the only choice. For example, for many moveable consumer devices, laptop hinges, desktop mice, touchscreens, cookware, and children’s toys, to name a few, oil or grease-based lubrication systems are just impractical. Additionally, many mechanical systems in the manufacturing process operate in vacuum conditions (lithography machines in the semiconductor industry, vacuum compressors, food packaging industry, etc.) where fluid film lubrication can cause contamination, and even process failure. Finally, another prime example is the Space application. Space shuttles and satellites are loaded with tribological components, but most materials cannot sustain the extreme conditions of the space environment.
Based on all this mechanistic understanding, we are now reaching the point of specifying or designing new materials or interfaces that can reliably provide extremely low friction coefficients (Figure 13). In particular, with the incorporation of artificial intelligence and machine learning algorithms into interface design, it looks that in the near future, we will be able to attain and maintain ultra-low friction on demand or for very long sliding distances or very high contact loads. Hence, future research activities in superlubricity should take advantage of advanced computational tools and methods to more predictively and reliably design, synthesize, and verify new materials or surfaces that can afford superlubricity and hence help minimize energy losses due to friction and wear; ultimately supporting the global sustainability goals.
FIGURE 13. Future directions and scope for advancement of superlubricity materials, methods and systems.
AE and DB conceived the topical area for this review; AA and KA helped with literature survey and figures, all authors contributed to the text.
The authors declare that the research was conducted in the absence of any commercial or financial relationships that could be construed as a potential conflict of interest.
All claims expressed in this article are solely those of the authors and do not necessarily represent those of their affiliated organizations, or those of the publisher, the editors and the reviewers. Any product that may be evaluated in this article, or claim that may be made by its manufacturer, is not guaranteed or endorsed by the publisher.
DB and AA acknowledge support of this work by the National Science Foundation (NSF) (Award No. 2018132). AE and IA acknowledge the Texas A&M Engineering Experiment Station startup funds and the Governor’s University Research Initiative. The authors are also grateful to Megan Simison of the J. Mike Walker ’66 Department of Mechanical Engineering, Texas A&M University, for editorial help.
Alexandrou, I., Wang, H., Sano, N., and Amaratunga, G. A. J. (2004). Structure of Carbon Onions and Nanotubes Formed by Arc in Liquids. J. Chem. Phys. 120, 1055–1058. doi:10.1063/1.1629274
Aouadi, S. M., Gu, J., and Berman, D. (2020). Self-healing Ceramic Coatings that Operate in Extreme Environments: A Review. J. Vac. Sci. Technol. A 38, 050802. doi:10.1116/6.0000350
Argibay, N., Babuska, T. F., Curry, J. F., Dugger, M. T., Lu, P., Adams, D. P., et al. (2018). In-situ Tribochemical Formation of Self-Lubricating Diamond-like Carbon Films. Carbon 138, 61–68. doi:10.1016/j.carbon.2018.06.006
Ayyagari, A. V., Mutyala, K. C., and Sumant, A. V. (2020). Towards Developing Robust Solid Lubricant Operable in Multifarious Environments. Sci. Rep. 10, 15390. doi:10.1038/s41598-020-72666-4
Baboukani, B. S., Ye, Z., Reyes, K. G., and Nalam, P. C. (2020). Prediction of Nanoscale Friction for Two-Dimensional Materials Using a Machine Learning Approach. Tribol. Lett. 68, 1–14. doi:10.1007/s11249-020-01294-w
Baykara, M. Z., Vazirisereshk, M. R., and Martini, A. (2018). Emerging Superlubricity: A Review of the State of the Art and Perspectives on Future Research. Appl. Phys. Rev. 5, 041102. doi:10.1063/1.5051445
Bennewitz, R. (2005). Friction Force Microscopy. Mater. Today 8, 42–48. doi:10.1016/s1369-7021(05)00845-x
Berman, D., Deshmukh, S. A., Narayanan, B., Sankaranarayanan, S. K., Yan, Z., Balandin, A. A., et al. (2016). Metal-induced Rapid Transformation of Diamond into Single and Multilayer Graphene on Wafer Scale. Nat. Commun. 7, 12099. doi:10.1038/ncomms12099
Berman, D., Deshmukh, S. A., Sankaranarayanan, S. K. R. S., Erdemir, A., and Sumant, A. V. (2014a). Extraordinary Macroscale Wear Resistance of One Atom Thick Graphene Layer. Adv. Funct. Mat. 24, 6640–6646. doi:10.1002/adfm.201401755
Berman, D., Deshmukh, S. A., Sankaranarayanan, S. K. R. S., Erdemir, A., and Sumant, A. V. (2015a). Macroscale Superlubricity Enabled by Graphene Nanoscroll Formation. Science 348, 1118–1122. doi:10.1126/science.1262024
Berman, D., and Erdemir, A. (2021). Achieving Ultralow Friction and Wear by Tribocatalysis: Enabled by In-Operando Formation of Nanocarbon Films. ACS Nano 15, 18865–18879. doi:10.1021/acsnano.1c08170
Berman, D., Erdemir, A., and Sumant, A. V. (2018b). Approaches for Achieving Superlubricity in Two-Dimensional Materials. ACS Nano 12, 2122–2137. doi:10.1021/acsnano.7b09046
Berman, D., Erdemir, A., and Sumant, A. V. (2013). Few Layer Graphene to Reduce Wear and Friction on Sliding Steel Surfaces. Carbon 54, 454–459. doi:10.1016/j.carbon.2012.11.061
Berman, D., Erdemir, A., and Sumant, A. V. (2014b). Graphene: a New Emerging Lubricant. Mater. Today 17, 31–42. doi:10.1016/j.mattod.2013.12.003
Berman, D., Erdemir, A., Zinovev, A. V., and Sumant, A. V. (2015b). Nanoscale Friction Properties of Graphene and Graphene Oxide. Diam. Relat. Mater. 54, 91–96. doi:10.1016/j.diamond.2014.10.012
Berman, D., Mutyala, K. C., Srinivasan, S., Sankaranarayanan, S. K. R. S., Erdemir, A., Shevchenko, E. V., et al. (2019). Iron‐Nanoparticle Driven Tribochemistry Leading to Superlubric Sliding Interfaces. Adv. Mat. Interfaces 6, 1901416. doi:10.1002/admi.201901416
Berman, D., Narayanan, B., Cherukara, M. J., Sankaranarayanan, S. K. R. S., Erdemir, A., Zinovev, A., et al. (2018a). Operando Tribochemical Formation of Onion-Like-Carbon Leads to Macroscale Superlubricity. Nat. Commun. 9, 1164. doi:10.1038/s41467-018-03549-6
Bhushan, B. (2000). Modern Tribology Handbook, Two Volume Set. Boca Raton, FL, United States: CRC Press.
Björling, M., and Shi, Y. (2019). DLC and Glycerol: Superlubricity in Rolling/Sliding Elastohydrodynamic Lubrication. Tribol. Lett. 67, 23. doi:10.1007/s11249-019-1135-1
Cermak, S. C., Biresaw, G., Isbell, T. A., Evangelista, R. L., Vaughn, S. F., and Murray, R. (2013). New Crop Oils-Properties as Potential Lubricants. Industrial Crops Prod. 44, 232–239. doi:10.1016/j.indcrop.2012.10.035
Chen, X., Kato, T., Kawaguchi, M., Nosaka, M., and Choi, J. (2013). Structural and Environmental Dependence of Superlow Friction in Ion Vapour-Deposited A-C : H : Si Films for Solid Lubrication Application. J. Phys. D. Appl. Phys. 46, 255304. doi:10.1088/0022-3727/46/25/255304
Chen, X., and Li, J. (2020). Superlubricity of Carbon Nanostructures. Carbon 158, 1–23. doi:10.1016/j.carbon.2019.11.077
Chhowalla, M., and Amaratunga, G. A. J. (2000). Thin Films of Fullerene-like MoS2 Nanoparticles with Ultra-low Friction and Wear. Nature 407, 164–167. doi:10.1038/35025020
Cihan, E., İpek, S., Durgun, E., and Baykara, M. Z. (2016). Structural Lubricity under Ambient Conditions. Nat. Commun. 7, 12055. doi:10.1038/ncomms12055
Cumings, J., and Zettl, A. (2000). Low-Friction Nanoscale Linear Bearing Realized from Multiwall Carbon Nanotubes. Science 289, 602–604. doi:10.1126/science.289.5479.602
Di Lecce, S., Kornyshev, A. A., Urbakh, M., and Bresme, F. (2020). Lateral Ordering in Nanoscale Ionic Liquid Films between Charged Surfaces Enhances Lubricity. ACS Nano 14, 13256–13267. doi:10.1021/acsnano.0c05043
Dienwiebel, M., and Frenken, J. W. (2007). Experimental Observations of Superlubricity and Thermolubricity, Fundamentals of Friction and Wear. Berlin, Germany: Springer, 159–176.
Dienwiebel, M., Verhoeven, G. S., Pradeep, N., Frenken, J. W. M., Heimberg, J. A., and Zandbergen, H. W. (2004). Superlubricity of Graphite. Phys. Rev. Lett. 92, 126101. doi:10.1103/physrevlett.92.126101
Erdemir, A., and Donnet, C. (2006). Tribology of Diamond-like Carbon Films: Recent Progress and Future Prospects. J. Phys. D. Appl. Phys. 39, R311–R327. doi:10.1088/0022-3727/39/18/r01
Erdemir, A., and Eryilmaz, O. (2014). Achieving Superlubricity in DLC Films by Controlling Bulk, Surface, and Tribochemistry. Friction 2, 140–155. doi:10.1007/s40544-014-0055-1
Erdemir, A., Martin, J. M., and Luo, J. (2021). Superlubricity. 2nd Ed. Amsterdam-The Netherlands.: Elsevier.
Erdemir, A., Ramirez, G., Eryilmaz, O. L., Narayanan, B., Liao, Y., Kamath, G., et al. (2016). Carbon-based Tribofilms from Lubricating Oils. Nature 536, 67–71. doi:10.1038/nature18948
Erdemir, A. (2001). “Solid Lubricants and Self-Lubricating Films,” in Modern Tribology Handbook New York, NY, USA: CRC Press, 2, 787–818.
Eryilmaz, O. L., and Erdemir, A. (2008). On the Hydrogen Lubrication Mechanism(s) of DLC Films: An Imaging TOF-SIMS Study. Surf. Coatings Technol. 203, 750–755. doi:10.1016/j.surfcoat.2008.06.156
Fajardo, O. Y., Bresme, F., Kornyshev, A. A., and Urbakh, M. (2015). Electrotunable Lubricity with Ionic Liquid Nanoscale Films. Sci. Rep. 5, 7698. doi:10.1038/srep07698
Feiler, A. A., Bergström, L., and Rutland, M. W. (2008). Superlubricity using repulsive van der Waals forces. Langmuir 24, 2274–2276. doi:10.1021/la7036907
Feng, S., Liu, Y., Li, J., and Wen, S. (2021). Superlubricity Achieved with Zwitterionic Brushes in Diverse Conditions Induced by Shear Actions. Macromolecules 54, 5719–5727. doi:10.1021/acs.macromol.1c00430
Filippov, A. E., Dienwiebel, M., Frenken, J. W., Klafter, J., and Urbakh, M. (2008). Torque and Twist against Superlubricity. Phys. Rev. Lett. 100, 046102. doi:10.1103/PhysRevLett.100.046102
Fontaine, J., Loubet, J. L., Mogne, T. L., and Grill, A. (2004). Superlow Friction of Diamond-like Carbon Films: a Relation to Viscoplastic Properties. Tribol. Lett. 17, 709–714. doi:10.1007/s11249-004-8077-x
Freyman, C. A., Chen, Y., and Chung, Y.-W. (2006). Synthesis of Carbon Films with Ultra-low Friction in Dry and Humid Air. Surf. Coatings Technol. 201, 164–167. doi:10.1016/j.surfcoat.2005.11.075
Gao, G. T., Mikulski, P. T., Chateauneuf, G. M., and Harrison, J. A. (2003). The Effects of Film Structure and Surface Hydrogen on the Properties of Amorphous Carbon Films. J. Phys. Chem. B 107, 11082–11090. doi:10.1021/jp034544+
Gao, K., Wang, B., Shirani, A., Chang, Q., and Berman, D. (2021). Macroscale Superlubricity Accomplished by Sb2O3-MSH/C under High Temperature. Front. Chem. 9, 226. doi:10.3389/fchem.2021.667878
Gao, Y., Ma, L., Liang, Y., Li, B., and Luo, J. (2018). Water Molecules on the Liquid Superlubricity Interfaces Achieved by Phosphoric Acid Solution. Biosurface Biotribology 4, 94–98. doi:10.1049/bsbt.2018.0021
Ge, X., Li, J., and Luo, J. (2019). Macroscale Superlubricity Achieved with Various Liquid Molecules: a Review. Front. Mech. Eng. 5, 2. doi:10.3389/fmech.2019.00002
Ge, X., Li, J., Luo, R., Zhang, C., and Luo, J. (2018a). Macroscale Superlubricity Enabled by the Synergy Effect of Graphene-Oxide Nanoflakes and Ethanediol. ACS Appl. Mat. Interfaces 10, 40863–40870. doi:10.1021/acsami.8b14791
Ge, X., Li, J., Zhang, C., Wang, Z., and Luo, J. (2018b). Superlubricity of 1-Ethyl-3-Methylimidazolium Trifluoromethanesulfonate Ionic Liquid Induced by Tribochemical Reactions. Langmuir 34, 5245–5252. doi:10.1021/acs.langmuir.8b00867
Gnecco, E., Maier, S., and Meyer, E. (2008a). Superlubricity of Dry Nanocontacts. J. Phys. Condens. Matter 20, 354004. doi:10.1088/0953-8984/20/35/354004
Gnecco, E., Socoliuc, A., Maier, S., Gessler, J., Glatzel, T., Baratoff, A., et al. (2008b). Dynamic Superlubricity on Insulating and Conductive Surfaces in Ultra-high Vacuum and Ambient Environment. Nanotechnology 20, 025501. doi:10.1088/0957-4484/20/2/025501
Gogotsi, Y., and Anasori, B. (2019). The Rise of MXenes, 13. ACS Publications, 8491–8494. ACS Nano. doi:10.1021/acsnano.9b06394
Guo, P., Qi, S., Chen, L., Gou, C., Lin, B., Lu, Z., et al. (2019). Black Phosphorus: Black Phosphorus-Graphene Oxide Hybrid Nanomaterials toward Advanced Lubricating Properties under Water (Adv. Mater. Interfaces 23/2019). Adv. Mat. Interfaces 6, 1970143. doi:10.1002/admi.201970143
Hamrock, B. J., Schmid, B. J., and Jacobson, B. O. (2004). Fundamentals of Fluid Film Lubrication. Boca Raton, FL, United States: CRC Press.
Han, T., Yi, S., Zhang, C., Li, J., Chen, X., Luo, J., et al. (2020). Superlubrication Obtained with Mixtures of Hydrated Ions and Polyethylene Glycol Solutions in the Mixed and Hydrodynamic Lubrication Regimes. J. Colloid Interface Sci. 579, 479–488. doi:10.1016/j.jcis.2020.06.095
Han, T., Zhang, C., Li, J., Yuan, S., Chen, X., Zhang, J., et al. (2019). Origins of Superlubricity Promoted by Hydrated Multivalent Ions. J. Phys. Chem. Lett. 11, 184–190. doi:10.1021/acs.jpclett.9b03098
Han, T., Zhang, C., and Luo, J. (2018). Macroscale Superlubricity Enabled by Hydrated Alkali Metal Ions. Langmuir 34, 11281–11291. doi:10.1021/acs.langmuir.8b01722
Hirano, M. (2006). Atomistics of Friction. Surf. Sci. Rep. 60, 159–201. doi:10.1016/j.surfrep.2005.10.003
Hirano, M., and Shinjo, K. (1990). Atomistic Locking and Friction. Phys. Rev. B 41, 11837–11851. doi:10.1103/physrevb.41.11837
Hirano, M., Shinjo, K., Kaneko, R., and Murata, Y. (1991). Anisotropy of Frictional Forces in Muscovite Mica. Phys. Rev. Lett. 67, 2642–2645. doi:10.1103/physrevlett.67.2642
Hirano, M., Shinjo, K., Kaneko, R., and Murata, Y. (1997). Observation of Superlubricity by Scanning Tunneling Microscopy. Phys. Rev. Lett. 78, 1448–1451. doi:10.1103/physrevlett.78.1448
Hirano, M., and Shinjo, K. (1993). Superlubricity and Frictional Anisotropy. Wear 168, 121–125. doi:10.1016/0043-1648(93)90207-3
Hirano, M. (2003). Superlubricity: a State of Vanishing Friction. Wear 254, 932–940. doi:10.1016/s0043-1648(03)00295-3
Hod, O., Meyer, E., Zheng, Q., and Urbakh, M. (2018). Structural Superlubricity and Ultralow Friction across the Length Scales. Nature 563, 485–492. doi:10.1038/s41586-018-0704-z
Holmberg, K., Andersson, P., and Erdemir, A. (2012). Global Energy Consumption Due to Friction in Passenger Cars. Tribol. Int. 47, 221–234. doi:10.1016/j.triboint.2011.11.022
Holmer, P. (2003). Faster Than a Speeding Bullet Train. IEEE Spectr. 40, 30–34. doi:10.1109/mspec.2003.1222045
Hu, J., Li, S., Zhang, J., Chang, Q., Yu, W., and Zhou, Y. (2020). Mechanical Properties and Frictional Resistance of Al Composites Reinforced with Ti3C2T MXene. Chin. Chem. Lett. 31, 996–999. doi:10.1016/j.cclet.2019.09.004
Hua, J., Björling, M., Larsson, R., and Shi, Y. (2022). Controllable Superlubricity Achieved with Mixtures of Green Ionic Liquid and Glycerol Aqueous Solution via Humidity. J. Mol. Liq. 345, 117860. doi:10.1016/j.molliq.2021.117860
Huang, S., Mutyala, K. C., Sumant, A. V., and Mochalin, V. N. (2021). Achieving Superlubricity with 2D Transition Metal Carbides (MXenes) and MXene/graphene Coatings. Mater. Today Adv. 9, 100133. doi:10.1016/j.mtadv.2021.100133
Hull, J. R., Hilton, E. F., Mulcahy, T. M., Yang, Z. J., Lockwood, A., and Strasik, M. (1995). Low Friction in Mixed‐mu Superconducting Bearings. J. Appl. Phys. 78, 6833–6838. doi:10.1063/1.360444
Jacques, K., Joy, T., Shirani, A., and Berman, D. (2019). Effect of Water Incorporation on the Lubrication Characteristics of Synthetic Oils. Tribol. Lett. 67, 105. doi:10.1007/s11249-019-1217-0
Joly-Pottuz, L., and Iwaki, M. (2007). Superlubricity of Tungsten Disulfide Coatings in Ultra High Vacuum, Superlubricity. Berlin, Germany: Elsevier, 227–236.
Kato, K., and Adachi, K. (2007). Superlubricity of CNx-Coatings in Nitrogen Gas Atmosphere, Superlubricity. Amsterdam, The Netherlands: Elsevier, 341–364.
Kawai, S., Benassi, A., Gnecco, E., Söde, H., Pawlak, R., Feng, X., et al. (2016). Superlubricity of Graphene Nanoribbons on Gold Surfaces. Science 351, 957–961. doi:10.1126/science.aad3569
Khan, A. M., He, X., Wu, H., Desanker, M., Erdemir, A., Chung, Y.-W., et al. (2018). Acid Treatment of Diamond-Like Carbon Surfaces for Enhanced Adsorption of Friction Modifiers and Friction Performance. Tribol. Lett. 66, 128. doi:10.1007/s11249-018-1081-3
Khare, H. S., and Burris, D. L. (2014). Surface and Subsurface Contributions of Oxidation and Moisture to Room Temperature Friction of Molybdenum Disulfide. Tribol. Lett. 53, 329–336. doi:10.1007/s11249-013-0273-0
Khare, H. S., and Burris, D. L. (2013). The Effects of Environmental Water and Oxygen on the Temperature-dependent Friction of Sputtered Molybdenum Disulfide. Tribol. Lett. 52, 485–493. doi:10.1007/s11249-013-0233-8
Konicek, A. R., Grierson, D. S., Gilbert, P. U. P. A., Sawyer, W. G., Sumant, A. V., and Carpick, R. W. (2008). Origin of Ultralow Friction and Wear in Ultrananocrystalline Diamond. Phys. Rev. Lett. 100, 235502. doi:10.1103/physrevlett.100.235502
Kumar, N., Ramadoss, R., Kozakov, A. T., Sankaran, K. J., Dash, S., Tyagi, A. K., et al. (2013). Humidity-dependent Friction Mechanism in an Ultrananocrystalline Diamond Film. J. Phys. D. Appl. Phys. 46, 275501. doi:10.1088/0022-3727/46/27/275501
Lamoreaux, S. K. (2004). The Casimir Force: Background, Experiments, and Applications. Rep. Prog. Phys. 68, 201–236. doi:10.1088/0034-4885/68/1/r04
Lee, C., Li, Q., Kalb, W., Liu, X.-Z., Berger, H., Carpick, R. W., et al. (2010). Frictional Characteristics of Atomically Thin Sheets. Science 328, 76–80. doi:10.1126/science.1184167
Lee, S., Spikes, H. A., and Spencer, N. (2003). The Influence of Molecular Architecture on the Macroscopic Lubrication Properties of the Brush-like Co-polyelectrolyte Poly (L-Lysine)-G-Poly (Ethylene glycol)(PLL-G- Ldots. Tribol. Lett. 15, 395–405. doi:10.1023/B:TRIL.0000003063.98583.bb
Li, H., Wang, J., Gao, S., Chen, Q., Peng, L., Liu, K., et al. (2017). Superlubricity between MoS2 Monolayers. Adv. Mat. 29, 1701474. doi:10.1002/adma.201701474
Li, H., Wood, R. J., Rutland, M. W., and Atkin, R. (2014). An Ionic Liquid Lubricant Enables Superlubricity to Be “Switched on” In Situ Using an Electrical Potential. Chem. Commun. 50, 4368–4370. doi:10.1039/c4cc00979g
Li, J., Ma, L., Zhang, S., Zhang, C., Liu, Y., and Luo, J. (2013). Investigations on the Mechanism of Superlubricity Achieved with Phosphoric Acid Solution by Direct Observation. J. Appl. Phys. 114, 114901. doi:10.1063/1.4821063
Li, J., Zhang, C., and Luo, J. (2011). Superlubricity Behavior with Phosphoric Acid-Water Network Induced by Rubbing. Langmuir 27, 9413–9417. doi:10.1021/la201535x
Li, J., Zhang, C., Sun, L., Lu, X., and Luo, J. (2012). Tribochemistry and Superlubricity Induced by Hydrogen Ions. Langmuir 28, 15816–15823. doi:10.1021/la303897x
Li, X., Teitgen, A. M., Shirani, A., Ling, J., Busta, L., Cahoon, R. E., et al. (2018). Discontinuous Fatty Acid Elongation Yields Hydroxylated Seed Oil with Improved Function. Nat. Plants 4, 711–720. doi:10.1038/s41477-018-0225-7
Liao, M., Nicolini, P., Du, L., Yuan, J., Wang, S., Yu, H., et al. (2022). UItra-low friction and edge-pinning effect in large-lattice-mismatch van der Waals heterostructures. Nat. Mat. 21, 47–53. doi:10.1038/s41563-021-01058-4
Ling, X., Wang, H., Huang, S., Xia, F., and Dresselhaus, M. S. (2015). The Renaissance of Black Phosphorus. Proc. Natl. Acad. Sci. U.S.A. 112, 4523–4530. doi:10.1073/pnas.1416581112
Liu, W., Wang, H., Liu, Y., Li, J., Erdemir, A., and Luo, J. (2019). Mechanism of Superlubricity Conversion with Polyalkylene Glycol Aqueous Solutions. Langmuir 35, 11784–11790. doi:10.1021/acs.langmuir.9b01857
Liu, Y., Li, J., Li, J., Yi, S., Ge, X., Zhang, X., et al. (2021). Shear-Induced Interfacial Structural Conversion Triggers Macroscale Superlubricity: From Black Phosphorus Nanoflakes to Phosphorus Oxide. ACS Appl. Mat. Interfaces 13, 31947–31956. doi:10.1021/acsami.1c04664
Liu, Y., Zhang, X., Dong, S., Ye, Z., and Wei, Y. (2017). Synthesis and Tribological Property of Ti3C2T X Nanosheets. J. Mater Sci. 52, 2200–2209. doi:10.1007/s10853-016-0509-0
Liu, Z., Yang, J., Grey, F., Liu, J. Z., Liu, Y., Wang, Y., et al. (2012). Observation of Microscale Superlubricity in Graphite. Phys. Rev. Lett. 108, 205503. doi:10.1103/physrevlett.108.205503
Long, Y., Bouchet, M.-I. D. B., Lubrecht, T., Onodera, T., and Martin, J. M. (2019). Superlubricity of Glycerol by Self-Sustained Chemical Polishing. Sci. Rep. 9, 6286. doi:10.1038/s41598-019-42730-9
Luan, B., and Robbins, M. O. (2005). The Breakdown of Continuum Models for Mechanical Contacts. Nature 435, 929–932. doi:10.1038/nature03700
Ludema, K. (2001). History of Tribology and its Industrial Significance, Fundamentals of Tribology and Bridging the Gap between the Macro-And Micro/Nanoscales. Keszthely, Hungary: Springer, 1–11.
Luo, Z., Yu, J., Xu, Y., Xi, H., Cheng, G., Yao, L., et al. (2021). Surface Characterization of Steel/steel Contact Lubricated by PAO6 with Novel Black Phosphorus Nanocomposites. Friction 9, 723–733. doi:10.1007/s40544-020-0366-3
Ma, Q., He, T., Khan, A. M., Wang, Q., and Chung, Y.-W. (2021a). Achieving Macroscale Liquid Superlubricity Using Glycerol Aqueous Solutions. Tribol. Int. 160, 107006. doi:10.1016/j.triboint.2021.107006
Ma, Q., Wang, S., and Dong, G. (2021b). Macroscale Liquid Superlubricity Achieved with Mixtures of Fructose and Diols. Wear 484-485, 204037. doi:10.1016/j.wear.2021.204037
Mai, Y. J., Li, Y. G., Li, S. L., Zhang, L. Y., Liu, C. S., and Jie, X. H. (2019). Self-lubricating Ti3C2 Nanosheets/copper Composite Coatings. J. Alloys Compd. 770, 1–5. doi:10.1016/j.jallcom.2018.08.100
Manzeli, S., Ovchinnikov, D., Pasquier, D., Yazyev, O. V., and Kis, A. (2017). 2D Transition Metal Dichalcogenides. Nat. Rev. Mater. 2, 1–15. doi:10.1038/natrevmats.2017.33
Marian, M., Berman, D., Rota, A., Jackson, R. L., and Rosenkranz, A. (2022). Layered 2D Nanomaterials to Tailor Friction and Wear in Machine Elements-A Review. Adv. Mater. Inter 9, 2101622. doi:10.1002/admi.202101622
Martin, J. M., Donnet, C., Le Mogne, T., and Epicier, T. (1993). Superlubricity of Molybdenum Disulphide. Phys. Rev. B 48, 10583–10586. doi:10.1103/physrevb.48.10583
Matta, C., Joly-Pottuz, L., De Barros Bouchet, M. I., Martin, J. M., Kano, M., Zhang, Q., et al. (2008). Superlubricity and Tribochemistry of Polyhydric Alcohols. Phys. Rev. B 78, 085436. doi:10.1103/physrevb.78.085436
Meyer, E., Lüthi, R., Howald, L., and Güntherodt, H.-J. (1995). Friction Force Microscopy, Forces in Scanning Probe Methods. Schluchsee, Germany: Springer, 285–306.
Miura, K., Tsuda, D., and Sasaki, N. (2005). Superlubricity of C60 Intercalated Graphite Films. e-J. Surf. Sci. Nanotechnol. 3, 21–23. doi:10.1380/ejssnt.2005.21
Mo, Y., Turner, K. T., and Szlufarska, I. (2009). Friction Laws at the Nanoscale. Nature 457, 1116–1119. doi:10.1038/nature07748
Müser, M. H. (2004). Structural Lubricity: Role of Dimension and Symmetry. Europhys. Lett. 66, 97. doi:10.1209/epl/i2003-10139-6
Mutyala, K. C., Doll, G. L., Wen, J., and Sumant, A. V. (2019b). Superlubricity in Rolling/sliding Contacts. Appl. Phys. Lett. 115, 103103. doi:10.1063/1.5116142
Mutyala, K. C., Wu, Y. A., Erdemir, A., and Sumant, A. V. (2019a). Graphene - MoS2 Ensembles to Reduce Friction and Wear in DLC-Steel Contacts. Carbon 146, 524–527. doi:10.1016/j.carbon.2019.02.047
Nosaka, M., Mifune, A., Kawaguchi, M., Shiiba, T., and Kato, T. (2015). Friction Fade-Out at Polymer-like Carbon Films Slid by ZrO2 Pins under Hydrogen Environment. Proc. Institution Mech. Eng. Part J J. Eng. Tribol. 229, 1030–1038. doi:10.1177/1350650115569857
Nosaka, M., Morisaki, Y., Fujiwara, T., Tokai, H., Kawaguchi, M., and Kato, T. (2017). The Run-In Process for Stable Friction Fade-Out and Tribofilm Analyses by SEM and Nano-Indenter. Tribol. online 12, 274–280. doi:10.2474/trol.12.274
Nosonovsky, M. (2007). Oil as a Lubricant in the Ancient Middle East. Tribol. Online 2, 44–49. doi:10.2474/trol.2.44
Okubo, H., Tsuboi, R., and Sasaki, S. (2015). Frictional Properties of DLC Films in Low-Pressure Hydrogen Conditions. Wear 340-341, 2–8. doi:10.1016/j.wear.2015.03.018
Oshima, C., and Nagashima, A. (1997). Ultra-thin Epitaxial Films of Graphite and Hexagonal Boron Nitride on Solid Surfaces. J. Phys. Condens. Matter 9, 1–20. doi:10.1088/0953-8984/9/1/004
Pitenis, A. A., Dowson, D., and Gregory Sawyer, W. (2014). Leonardo da Vinci's Friction Experiments: An Old Story Acknowledged and Repeated. Tribol. Lett. 56, 509–515. doi:10.1007/s11249-014-0428-7
Reddyhoff, T., Ewen, J. P., Deshpande, P., Frogley, M. D., Welch, M. D., and Montgomery, W. (2021). Macroscale Superlubricity and Polymorphism of Long-Chain N-Alcohols. ACS Appl. Mat. Interfaces 13, 9239–9251. doi:10.1021/acsami.0c21918
Ren, X., Yang, X., Xie, G., He, F., Wang, R., Zhang, C., et al. (2021). Superlubricity under Ultrahigh Contact Pressure Enabled by Partially Oxidized Black Phosphorus Nanosheets. npj 2D Mater Appl. 5, 44. doi:10.1038/s41699-021-00225-0
Ren, X., Yang, X., Xie, G., and Luo, J. (2020). Black Phosphorus Quantum Dots in Aqueous Ethylene Glycol for Macroscale Superlubricity. ACS Appl. Nano Mat. 3, 4799–4809. doi:10.1021/acsanm.0c00841
Robbins, M. O., and Krim, J. (1998). Energy Dissipation in Interfacial Friction. MRS Bull. 23, 23–26. doi:10.1557/s088376940003058x
Romsdahl, T., Shirani, A., Minto, R. E., Zhang, C., Cahoon, E. B., Chapman, K. D., et al. (2019). Nature-Guided Synthesis of Advanced Bio-Lubricants. Sci. Rep. 9, 11711. doi:10.1038/s41598-019-48165-6
Rosenkranz, A., Grützmacher, P. G., Espinoza, R., Fuenzalida, V. M., Blanco, E., Escalona, N., et al. (2019). Multi-layer Ti3C2Tx-Nanoparticles (MXenes) as Solid Lubricants - Role of Surface Terminations and Intercalated Water. Appl. Surf. Sci. 494, 13–21. doi:10.1016/j.apsusc.2019.07.171
Rudnick, L. R., and Shubkin, R. L. (1999). Synthetic Lubricants and High-Performance Functional Fluids, Revised and Expanded. New York, NY, United States: CRC Press.
Salimon, J., Salih, N., and Yousif, E. (2010). Biolubricants: Raw Materials, Chemical Modifications and Environmental Benefits. Eur. J. Lipid Sci. Technol. 112, 519–530. doi:10.1002/ejlt.200900205
Schreiber, P. J., and Schneider, J. (2019). Liquid Superlubricity Obtained for Self-Mated Silicon Carbide in Nonaqueous Low-Viscosity Fluid. Tribol. Int. 134, 7–14. doi:10.1016/j.triboint.2019.01.031
Shenderova, O. A., Shames, A. I., Nunn, N. A., Torelli, M. D., Vlasov, I., and Zaitsev, A. (2019). Review Article: Synthesis, Properties, and Applications of Fluorescent Diamond Particles. J. Vac. Sci. Technol. B 37, 030802. doi:10.1116/1.5089898
Shenderova, O., Jones, C., Borjanovic, V., Hens, S., Cunningham, G., Moseenkov, S., et al. (2008). Detonation Nanodiamond and Onion-like Carbon: Applications in Composites. Phys. Stat. Sol. (a) 205, 2245–2251. doi:10.1002/pssa.200879706
Shi, S., Guo, D., and Luo, J. (2021). Micro/atomic-scale Vibration Induced Superlubricity. Friction 9, 1163–1174. doi:10.1007/s40544-020-0414-z
Shinjo, K., and Hirano, M. (1993). Dynamics of Friction: Superlubric State. Surf. Sci. 283, 473–478. doi:10.1016/0039-6028(93)91022-h
Shirani, A., Gu, J., Wei, B., Lee, J., Aouadi, S. M., and Berman, D. (2019b). Tribologically Enhanced Self-Healing of Niobium Oxide Surfaces. Surf. Coatings Technol. 364, 273–278. doi:10.1016/j.surfcoat.2019.03.002
Shirani, A., Joy, T., Lager, I., Yilmaz, J. L., Wang, H.-L., Jeppson, S., et al. (2020a). Lubrication Characteristics of Wax Esters from Oils Produced by a Genetically-Enhanced Oilseed Crop. Tribol. Int. 146, 106234. doi:10.1016/j.triboint.2020.106234
Shirani, A., Joy, T., Rogov, A., Lin, M., Yerokhin, A., Mogonye, J.-E., et al. (2020b). PEO-chameleon as a Potential Protective Coating on Cast Aluminum Alloys for High-Temperature Applications. Surf. Coatings Technol. 397, 126016. doi:10.1016/j.surfcoat.2020.126016
Shirani, A., Li, Y., Eryilmaz, O. L., and Berman, D. (2021). Tribocatalytically-activated Formation of Protective Friction and Wear Reducing Carbon Coatings from Alkane Environment. Sci. Rep. 11, 20643. doi:10.1038/s41598-021-00044-9
Shirani, A., Nunn, N., Shenderova, O., Osawa, E., and Berman, D. (2019a). Nanodiamonds for Improving Lubrication of Titanium Surfaces in Simulated Body Fluid. Carbon 143, 890–896. doi:10.1016/j.carbon.2018.12.005
Socoliuc, A., Bennewitz, R., Gnecco, E., and Meyer, E. (2004). Transition from Stick-Slip to Continuous Sliding in Atomic Friction: Entering a New Regime of Ultralow Friction. Phys. Rev. Lett. 92, 134301. doi:10.1103/physrevlett.92.134301
Socoliuc, A., Gnecco, E., Maier, S., Pfeiffer, O., Baratoff, A., Bennewitz, R., et al. (2006). Atomic-scale Control of Friction by Actuation of Nanometer-Sized Contacts. Science 313, 207–210. doi:10.1126/science.1125874
Sokoloff, J. B. (1990). Theory of Energy Dissipation in Sliding Crystal Surfaces. Phys. Rev. B 42, 760–765. doi:10.1103/physrevb.42.760
Song, Y., Mandelli, D., Hod, O., Urbakh, M., Ma, M., and Zheng, Q. (2018). Robust Microscale Superlubricity in Graphite/hexagonal Boron Nitride Layered Heterojunctions. Nat. Mater 17, 894–899. doi:10.1038/s41563-018-0144-z
Spikes, H. (2004). The History and Mechanisms of ZDDP. Tribol. Lett. 17, 469–489. doi:10.1023/b:tril.0000044495.26882.b5
Steiner, P., Roth, R., Gnecco, E., Baratoff, A., Maier, S., Glatzel, T., et al. (2009). Two-dimensional Simulation of Superlubricity on NaCl and Highly Oriented Pyrolytic Graphite. Phys. Rev. B 79, 045414. doi:10.1103/physrevb.79.045414
Sugimoto, I., and Miyake, S. (1990). Oriented Hydrocarbons Transferred from a High Performance Lubricative Amorphous C:H:Si Film during Sliding in a Vacuum. Appl. Phys. Lett. 56, 1868–1870. doi:10.1063/1.103072
Sumant, A. V., and Ayyagari, V. A. Superlubrious High Temperature Coatings. Patent# 11,155,762 B2 (Accessed October 26, 2021).
Sun, C. Q., Sun, Y., Ni, Y., Zhang, X., Pan, J., Wang, X.-H., et al. (2009). Coulomb Repulsion at the Nanometer-Sized Contact: a Force Driving Superhydrophobicity, Superfluidity, Superlubricity, and Supersolidity. J. Phys. Chem. C 113, 20009–20019. doi:10.1021/jp907726b
Tang, G., Su, F., Xu, X., and Chu, P. K. (2020). 2D Black Phosphorus Dotted with Silver Nanoparticles: An Excellent Lubricant Additive for Tribological Applications. Chem. Eng. J. 392, 123631. doi:10.1016/j.cej.2019.123631
Tang, G., Wu, Z., Su, F., Wang, H., Xu, X., Li, Q., et al. (2021). Macroscale Superlubricity on Engineering Steel in the Presence of Black Phosphorus. Nano Lett. 21 (12), 5308–5315. doi:10.1021/acs.nanolett.1c01437
Tao, J., Shen, W., Wu, S., Liu, L., Feng, Z., Wang, C., et al. (2015). Mechanical and Electrical Anisotropy of Few-Layer Black Phosphorus. ACS Nano 9, 11362–11370. doi:10.1021/acsnano.5b05151
Tartaglino, U., Samoilov, V. N., and Persson, B. N. J. (2006). Role of Surface Roughness in Superlubricity. J. Phys. Condens. Matter 18, 4143–4160. doi:10.1088/0953-8984/18/17/004
Urbakh, M., and Meyer, E. (2010). The Renaissance of Friction. Nat. Mater 9, 8–10. doi:10.1038/nmat2599
Wang, B., Gao, K., Chang, Q., Berman, D., and Tian, Y. (2021). Magnesium Silicate Hydroxide–MoS2–Sb2O3 Coating Nanomaterials for High-Temperature Superlubricity. ACS Appl. Nano Mater. 4 (7), 7097–7106. doi:10.1021/acsanm.1c01104
Wang, H., Liu, Y., Li, J., and Luo, J. (2016). Investigation of Superlubricity Achieved by Polyalkylene Glycol Aqueous Solutions. Adv. Mat. Interfaces 3, 1600531. doi:10.1002/admi.201600531
Wang, H., Liu, Y., Liu, W., Liu, Y., Wang, K., Li, J., et al. (2019). Superlubricity of Polyalkylene Glycol Aqueous Solutions Enabled by Ultrathin Layered Double Hydroxide Nanosheets. ACS Appl. Mat. Interfaces 11, 20249–20256. doi:10.1021/acsami.9b03014
Wang, W., Xie, G., and Luo, J. (2018a). Black Phosphorus as a New Lubricant. Friction 6, 116–142. doi:10.1007/s40544-018-0204-z
Wang, W., Xie, G., and Luo, J. (2018b). Superlubricity of Black Phosphorus as Lubricant Additive. ACS Appl. Mat. Interfaces 10, 43203–43210. doi:10.1021/acsami.8b14730
Wang, Z., Wang, C. B., Zhang, B., and Zhang, J. Y. (2011). Ultralow Friction Behaviors of Hydrogenated Fullerene-like Carbon Films: Effect of Normal Load and Surface Tribochemistry. Tribol. Lett. 41, 607–615. doi:10.1007/s11249-010-9739-5
Xue, M., Wang, Z., Yuan, F., Zhang, X., Wei, W., Tang, H., et al. (2017). Preparation of TiO2/Ti3C2Tx Hybrid Nanocomposites and Their Tribological Properties as Base Oil Lubricant Additives. RSC Adv. 7, 4312–4319. doi:10.1039/c6ra27653a
Yan, H., Zhang, L., Li, H., Fan, X., and Zhu, M. (2020). Towards High-Performance Additive of Ti3C2/graphene Hybrid with a Novel Wrapping Structure in Epoxy Coating. Carbon 157, 217–233. doi:10.1016/j.carbon.2019.10.034
Yang, J., Chen, B., Song, H., Tang, H., and Li, C. (2014). Synthesis, Characterization, and Tribological Properties of Two-Dimensional Ti3C2. Cryst. Res. Technol. 49, 926–932. doi:10.1002/crat.201400268
Yi, S., Chen, X., Li, J., Liu, Y., Ding, S., and Luo, J. (2021b). Macroscale Superlubricity of Si-Doped Diamond-like Carbon Film Enabled by Graphene Oxide as Additives. Carbon 176, 358–366. doi:10.1016/j.carbon.2021.01.147
Yi, S., Li, J., Liu, Y., Ge, X., Zhang, J., and Luo, J. (2021a). In-situ Formation of Tribofilm with Ti3C2Tx MXene Nanoflakes Triggers Macroscale Superlubricity. Tribol. Int. 154, 106695. doi:10.1016/j.triboint.2020.106695
Yin, X., Jin, J., Chen, X., Rosenkranz, A., and Luo, J. (2019). Ultra-Wear-Resistant MXene-Based Composite Coating via In Situ Formed Nanostructured Tribofilm. ACS Appl. Mat. Interfaces 11, 32569–32576. doi:10.1021/acsami.9b11449
Zeng, Q., Eryilmaz, O., and Erdemir, A. (2015). Superlubricity of the DLC Films-Related Friction System at Elevated Temperature. RSC Adv. 5, 93147–93154. doi:10.1039/c5ra16084g
Zhang, H., Wang, L., Chen, Q., Li, P., Zhou, A., Cao, X., et al. (2016). Preparation, Mechanical and Anti-friction Performance of MXene/polymer Composites. Mater. Des. 92, 682–689. doi:10.1016/j.matdes.2015.12.084
Zhang, X., Guo, Y., Li, Y., Liu, Y., and Dong, S. (2019). Preparation and Tribological Properties of Potassium Titanate-Ti3C2Tx Nanocomposites as Additives in Base Oil. Chin. Chem. Lett. 30, 502–504. doi:10.1016/j.cclet.2018.07.007
Zhang, Y., Rutland, M. W., Luo, J., Atkin, R., and Li, H. (2021). Potential-Dependent Superlubricity of Ionic Liquids on a Graphite Surface. J. Phys. Chem. C 125, 3940–3947. doi:10.1021/acs.jpcc.0c10804
Zheng, Z., Liu, X., Huang, G., Chen, H., Yu, H., Feng, D., et al. (2021). Macroscale Superlubricity Achieved via Hydroxylated Hexagonal Boron Nitride Nanosheets with Ionic Liquid at Steel/steel Interface. Friction 10, 1365–1381. doi:10.1007/s40544-021-0545-x
Keywords: friction, wear, coatings, adaptive materials, 2D materials
Citation: Ayyagari A, Alam KI, Berman D and Erdemir A (2022) Progress in Superlubricity Across Different Media and Material Systems—A Review. Front. Mech. Eng 8:908497. doi: 10.3389/fmech.2022.908497
Received: 30 March 2022; Accepted: 07 June 2022;
Published: 12 August 2022.
Edited by:
Valentin L. Popov, Technical University of Berlin, GermanyCopyright © 2022 Ayyagari, Alam, Berman and Erdemir. This is an open-access article distributed under the terms of the Creative Commons Attribution License (CC BY). The use, distribution or reproduction in other forums is permitted, provided the original author(s) and the copyright owner(s) are credited and that the original publication in this journal is cited, in accordance with accepted academic practice. No use, distribution or reproduction is permitted which does not comply with these terms.
*Correspondence: Diana Berman, ZGlhbmEuYmVybWFuQHVudC5lZHU=; Ali Erdemir, YWVyZGVtaXJAdGFtdS5lZHU=
Disclaimer: All claims expressed in this article are solely those of the authors and do not necessarily represent those of their affiliated organizations, or those of the publisher, the editors and the reviewers. Any product that may be evaluated in this article or claim that may be made by its manufacturer is not guaranteed or endorsed by the publisher.
Research integrity at Frontiers
Learn more about the work of our research integrity team to safeguard the quality of each article we publish.