- 1Department of Mechanical and Industrial Engineering, Universitas Syiah Kuala, Banda Aceh, Indonesia
- 2Department of Mechanical Engineering, Faculty of Engineering, Universitas Negeri Padang, Padang, Indonesia
- 3Department of Chemical Engineering, Universitas Syiah Kuala, Banda Aceh, Indonesia
- 4Department of Mechanical Engineering, Andalas University, Padang, Indonesia
- 5Department of Mechanical Engineering, Universitas Indonesia, Jakarta, Indonesia
- 6Graphene and Advanced 2D Materials Research Group (GAMRG), School of Engineering and Technology, Sunway University, Bandar Sunway, Malaysia
The demand for bio-degradable lubricants is continuously increasing due to environmental concerns. One of the methods to achieve the bio-degradability property of lubricants is by using nanoparticles from bio-resources as additives in bio-degradable oils. Among the nanomaterials are nanofibers, cellulose, and graphene nanoplatelets. They can be mixed in Polyolester (POE) oil to produce lubricants for tribological applications. In a previous study, it has been confirmed that friction and wear of the tribo-pair reduced from 5 to 10% by mixing various volume percentages of bacterial cellulose (BC) into PEO as the base lubricant. The tribological performance BC containing POE base lubricant can further be enhanced by incorporating graphene nanoplatelets. This study shows that the specific wear rate of the material decreased by 20% by adding graphene nanoplatelets in BC containing POE oil. The friction and wear improvement can be related to the formation of tribofilm on the contact interface. EDS analysis indicates that oxygen played an important role in the friction and wear performance of the POE oil-based lubricant with BC and graphene additives. The tribofilm shows significant traces of oxygen elements. The presence of graphene nanoplatelets in POE oil removed the oxygen-rich layer but could not reduce the wear rate. However, incorporating both graphene and BC in POE oil significantly improved friction and wear, although the oxygen element was still traceable on the contact interface.
Introduction
Technological advancement in the lubrication industry has been directed not only to minimize the friction loss of the components but also to develop lubricants that are bio-compatible and bio-degradable. The additive is one of the most effective methods to achieve this purpose. Additives with various functions can be designed and applied to improve the stability, viscosity, thermal conductivity, as well as ability to produce a protective layer on the sliding surface to reduce friction and wear. Unfortunately, not all additives are environmentally friendly. Calcium sulphonates, tricresyl phosphates, and zinc dialkyl dithiophosphates are among the highly effective additives but have a harmful effect on the environment due to heavy metals and toxic elements (Hewstone, 1994). Nowadays, thanks to technological advancement in the material field, eco-friendly functional additives can be developed from bio-resources such as 1D material of nanocellulose and 2D material of graphene and MoS2.
Nanocelluloses are biopolymer that has numerous advantages for industrial applications (Klemm et al., 2018), including tribological applications. The performance of cellulose nanocrystals (CNCs) as lubricant additives has been investigated by using mineral lubricants such as SAE40 oil (Awang et al., 2019a) or bio-degradable oils such as polyalphaolefin (PAO) base oil (Awang et al., 2019b; Li et al., 2019). It can also be used as a viscosity modifier in biodegradable greases (Quinchia et al., 2014). It improves the tribological properties of the tribo-pair by forming a protective layer on the contact interface, reducing friction and wear of the material (Singh et al., 2014; Awang et al., 2019; Li et al., 2019).
On the other hand, graphene has shown a remarkable tribological performance as a lubricant additive. Graphene is two-dimensional, has a high specific surface area, weak interlayer interaction, and good chemical stability. It has the capability to produce superlubricity at the tribo-pair due to the formation of nanoscrolls at the sliding interface (R. Li et al., 2020). A small amount of graphene as a lubricating additive can reduce the friction coefficient due to its capability to produce a nano-bearing layer (Eswaraiah et al., 2011). The frictional performance can be related to the physical interaction, and the antiwear performance can be associated with the chemical interaction between nanoparticles and the environment (Dai et al., 2016). The lubrication mechanism of graphene includes tribofilm or protective film formation (Awang et al., 2019), transformation at microscale lever, interlayer sliding, and synergetic effect (Zhao et al., 2017; Pham et al., 2019).
The performance of graphene as additives in eco-friendly lubricants such as Polyalphaolein (PAO) (Jia et al., 2015; Meng et al., 2017; Zheng et al., 2017) and esterified bio-oil (Xu et al., 2015) has also been investigated. It is shown that the additive has good dispersion stability with the lubricant and improves the friction and wear of the material. Mixing various volume percentages of bacterial cellulose (BC) into polyol ester (POE) oil as a base lubricant can reduce friction and wear of the material from 5 to 10% (Rahmadiawan et al., 2021a).
Although nanoparticles as lubricant additives have been widely investigated, the tribological performance of lubricant containing multiparticles from different sources simultaneously as additives have not been much discussed (Zhang et al., 2014). Hybrid nanofluids are highly potential not only as heat transfer fluid compared to mono type nanofluids but also as lubricant additives. Incorporation of more than one nanoparticles improves the performance of heat transfer fluid due to improved thermal conductivity and viscosity (Sharma et al., 2020). Hybrid nanoparticles also improves the tribological performance of the lubricant because of improved dispersity and stability (Gara and Zou, 2013; Zhang et al., 2014).
In this study, we used bacterial cellulose and graphene nanoplatelets as additives in Polyol ester (POE) based lubricant. POE is considered as bio-degradable and mainly applied in refrigeration system. Therefore, a hybrid bacterial cellulose and graphene nanoplatelets nanoparticles could improve not only the heat transfer performance of the fluid but also the tribological properties of the tribo system. Since both materials are bio-degradable, they could also enhance the tribological performance of the bio-lubricant. In this study, the friction and wear of the tribo-pair lubricated by POE base oil were investigated and compared to those containing additives. The enhancement of the tribological properties of the lubricants due to the additive’s incorporation is elucidated.
Materials and Methods
The investigation on tribological properties of the bio-lubricant was conducted in several steps, i.e., bio-lubricant preparation, tribo-pair preparation, friction test using tribometer, wear evaluation, and surface characterization. Each step is explained in the following.
Lubricants Sample Preparation
POE oil (commercial brand Emkarate) was used as the base oil. The oil in its original form is used as one of the lubricant samples. In this study, four lubricant samples were prepared (Figure 1). The first lubricant sample is POE base oil, denoted as L1. Furthermore, BC microparticles and graphene nanoplatelets were used as additives for the base oil; lubricant samples L2, L3, and L4. Lubricant sample L2 contains graphene dispersed in POE oil, lubricant L3 contains BC particles, Span 60 dispersed in POE oil, and lubricant sample L4 contains graphene, BC particles, and span 60 dispersed in POE oil.
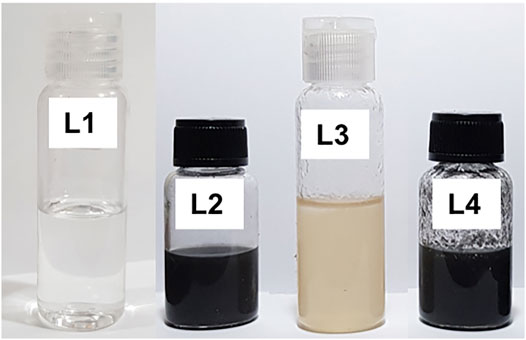
FIGURE 1. Lubricant specimens: L1 (POE oil), L2 (POE oil + graphene), L3 (POE oil + BC particles), L4 (POE oil + BNC particles + graphene).
The graphene particle used in this investigation was acquired commercially. Figure 2A indicated that the particle is in sheet form with a thickness less than 1 μm (Figure 2B). Sample L1 was prepared by adding 1 mg graphene particles into 50 ml POE oil. The mixture was placed in an ultrasonic bath for 60 min. The BC microparticle was prepared by a series of procedures involving 2,2,6,6-Tetramethylpiperidine-1-oxyl (TEMPO)-oxidized wet BC pellicle. Figure 3 shows the BC film indicating the BC interlinked nanofibers used for obtaining the BC particle. Detail explanation of the BC particle preparation and its stability can be found in ref. (Rahmadiawan, et al., 2021). The most stable composition of BC containing POE oil was used for lubricant sample L3. Lubricant sample L4 was prepared by adding 1 mg graphene particle in L3 continued by sonification for 60 min.
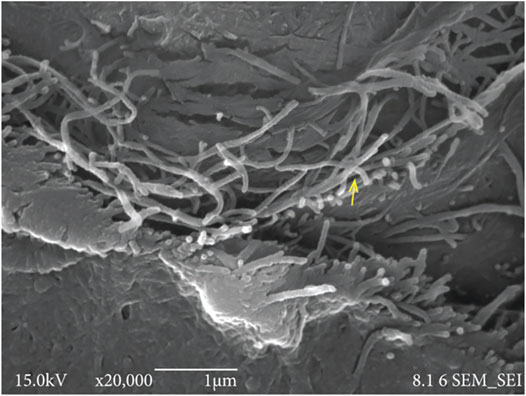
FIGURE 3. Bacterial cellulose fiber used for obtaining cellulose particles for the lubricant additive.
Friction and Wear Evaluation
A pin-on-disc reciprocating tribometer was used to evaluate the tribological performances of the lubricant samples (Figure 4A). The tribometer consists of a pin, a disc, a load sensor, an arm for load application, and a linear guide. The disc, made of AISI5210, is installed in a shallow chamber, in which lubricant is supplied. The pin is installed on a cantilever beam, serves as the load sensor by using strain gauges. The chamber bed is moved in a reciprocal direction by an electric motor. A non-contact heater unit was installed to provide a working temperature of 65 ± 2°C to the contact interface. The temperature is controlled by a thermostat, as shown in Figure 4A. The disc is 40 mm in diameter and 5 mm in thickness. The pin, directly taken from a bearing, is 4 mm in diameter and 20 mm in length. The contact interface of both the pin and disc was mirror polished. The surface roughness of the contact interface was not evaluated, but the surfaces were polished with emery paper gradually until grid #7000 and finished with the diamond paste of 1 μm at the final stage.
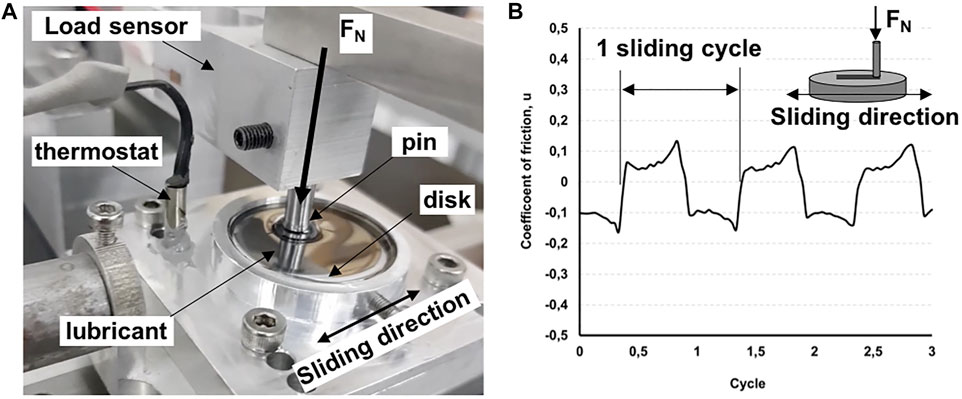
FIGURE 4. A reciprocating pin-on-disc tribometer used to evaluate the friction and wear in this analysis (A) and the friction coefficient acquired from a friction test (B).
In order to simulate a severe friction condition at the contact interface, the friction tests were conducted with a normal force, FN, of 10 N, applied using gravitational force. The material for tribo-pair is AISI52100, bearing steel. The tip of the pin is hemispherical with a contact radius of 10 mm. This contact combination, sphere on flat, resulted in an initial contact pressure (Hertzian) of 1 GPa for a normal load of 10 N, material Young’s modulus (E) of 210 GPa, and Poisson’s ratio of 0.3.
In the friction tests, the disk mount was moved in a reciprocating direction. A sliding cycle, back and forth, is completed in 3 s with a sliding distance of 15 mm. Therefore, the sliding speed was between 0 to 0.2 m/s. The friction force was acquired using strain gauges connected to a data acquisition system. The friction data was acquired with a sampling frequency of 10 Hz. The load sensor was calibrated for the normal load using gravitational forces. Figure 4B illustrates the coefficient of friction (CoF) graph obtained from the tribometer. It can be observed from the graph that the friction curve shows a U-shape, indicating a static friction coefficient at the reversing point where sliding velocity reaches zero. Here, the reciprocating sliding direction resulted in CoF having both positive and negative value. In a complete cycle, the forth direction results in positive CoF value and vice versa.
The friction tests were conducted for 4 h, 4,800 cycles, resulting in 72 m total sliding distance. The friction tests were conducted at low sliding velocity to simulate a severe friction condition of the tribo-pair, enabling the evaluation of the lubricant’s performance. The wear evaluation is focused on the pin-worn surface because it is constantly in sliding contact during friction. Scanning Electron Microscope together with EDS were used to evaluate the worn surfaces of the pins.
Results and Discussion
Stability of the Lubricants
Figure 5 shows the stability of the lubricant as a function of time, evaluated by capturing the image of the lubricant in a clear container. Such a stability evaluation method has been applied in many works, such as (Oliveira et al., 2017; Awang et al., 2019; Periyasamy et al., 2020; Rahmadiawan et al., 2021a). Images at day 1 indicate the lubricant after 1-h sonification. Sedimentation for L1 and L3 has been detected starting day 4, but lubricant L4 showed good stability until day 7. Overall, lubricants L3 and L4 show good stability because they show less than 30% sedimentation after 30 days, and literature stated that sedimentation that is not more than 30% indicates that the suspension is stable (Samylingam et al., 2018). Lubricant sample L1 shows poor stability because the graphene particle has completely sedimented after 60 days. Similar work related to a nanoparticle dispersed in oil disclosed that this is probably due to a high difference between the density of base oil and graphene (Rahmadiawan et al., 2021b).
Friction Coefficient
The result of friction tests for all lubricant samples are given in Figures 6, 7. All friction tests were conducted with a normal load FN = 10 N, a temperature of 65°C, and a sliding distance of 75 m. Figure 6 shows the CoF curve for the first four sliding cycles (sliding distance 0–60 mm), and Figure 7 shows the CoF curve for the sliding cycle no. 3000 to 3,004 (sliding distance 4,500 to 4,060 mm. Here, the negative value of CoF indicates the sliding in reverse direction, as indicated in Figure 4.
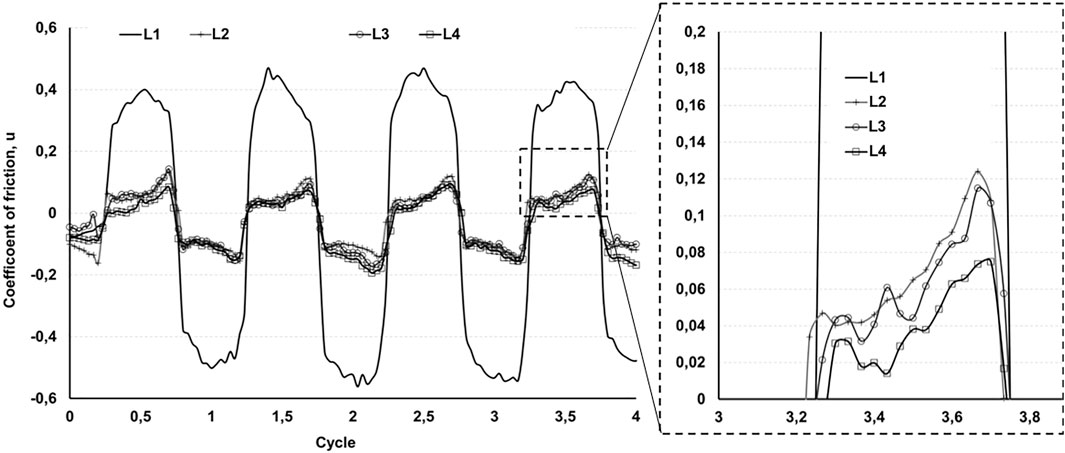
FIGURE 6. Friction coefficient at the beginning of sliding test showing the decrease the friction of the tribo-pair due to the presence of additives in the lubricant.
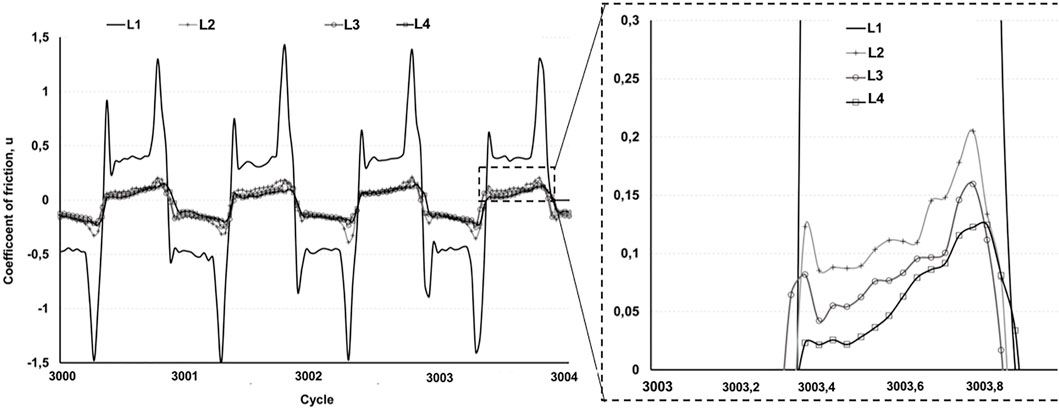
FIGURE 7. The presence of additive in the lubricant stabilizes the friction of the tribo-pair; CoF at sliding distance 45 m.
At the beginning of the sliding, as seen in Figure 6, L1 (POE oil) gave the highest CoF; 0.3 to 0.45 for the first three sliding cycles. The CoF for L1 increased with the increase of sliding distance. As it can be seen in Figure 7, the kinetic CoF value for L1 reached a value of 0.4 at sliding cycle 3,004 (sliding distance of 45 m). However, the static value of CoF reached a significantly high value of 1.4, indicating a severe friction condition at the tribo-pair. Stick-slip were observed during the friction test using lubricant L1, which can be related to the high difference between the static and kinetic coefficient of friction value. Such high friction condition was observed for L1 until the end of the sliding test.
The incorporation of additives to POE oil has resulted in a significant friction reduction of the tribo-pair. As it can be seen in Figure 6, all lubricant specimens of L2, L3, and L4, gave a CoF value of less than 0.12 at the beginning of the sliding (0–60 mm sliding distance). The presence of graphene in POE (L2) reduced the CoF of the tribo-pair from 0.4 to less than 0.12 at the first 60 mm sliding distance. In the case of L3, POE + BC particles, the CoF was in the range of 0.04–0.12, while further addition of graphene particles in BC contained POE oil (L3) has further decreased the CoF value of the tribo-pair to less than 0.08 at the first 60 mm sliding distance.
The presence of graphene particles in POE oil, L2, has prevented the tribo-pair from high friction until the sliding distance of 45 m, as shown in Figure 7. Although the CoF increased to a value of 0.13–0.2, the CoF was significantly lower than that in the case of L1. Figure 7 also shows that POE with BNC particles gave better friction performance to the tribo-pair compared to POE with graphene particles, with a CoF value of 0.9–0.13. However, POE containing both BC and graphene, L4, gave the lowest CoF for the tribo-pair with the CoF value less than 0.1 at the sliding distance of 45 m. Compared to the CoF at the beginning of sliding, as observed in Figure 6, the maximum CoF value of the tribo-pair lubricated by L4 only increased slightly from 0.08 to 0.1 (Figure 7). This indicated that the presence of graphene particles had enhanced the tribological performance of BNC containing POE oil.
In summary, the incorporation graphene in POE reduced the kinetic CoF from 0.45 to 0.12 whereas the incorporation of BC in POE reduced the kinetic CoF from 0.45 to 0.16 (Figure 7). However, incorporation of both BC and graphene particles in POE have resulted in kinetic CoF decrease from 0.45 to 0.12, which is 73% reduction. Similar trends were reported in literatures for other types of nanoparticles. A friction reduction of the tribo-pair by 20% was reported by mixing oleic acid and ZnO nanoparticle in the base fluid (Gara and Zou, 2013). Other researchers also reported that a friction reduction of 46.6% was achieved by addition of SiO2/MoS2 hybrid nanoparticles into the base oil (Xie et al., 2018) whereas 48% friction reduction was achieved by mixing 15W50 base oil with multi-wall carbon nanotube and graphene nanosheets nanoparticles (Kamel et al., 2021).
Wear Analysis
Figure 8 shows the specific wear rate of the pin, evaluated by calculating the volume loss of the pin using the dimension of the worn scar diameter on the pin. The presence of graphene particles in POE oil (L2) had not resulted in the reduction of the Specific Wear Rate (SWR) of the material. However, the presence of BC particles as additive in POE oil (L3) had reduced the SWR of the pin from 1.28 × 10–10 mm3/N.m to 9.14 × 10–11 mm3/N.m. Furthermore, the incorporation of graphene particles in BC containing POE oil (L4) had resulted in the reduction of the specific wear rate of the pin by 50% from 1.28 × 10–10 mm3/N.m to 6.11 × 10–11 mm3/N.m.
Wear reduction promoted by the addition of hybrid nanoparticles have also been reported by various researchers. For example, multi-walled carbon nanotube and graphene added in the base oil improved the wear scar dimension by 48% (Kamel et al., 2021) while SiO2/MoS2 hybrid nanoparticles in the base oil gave 50.5% wear volume reduction (Xie et al., 2018). When incorporated in the cutting fluid, hybrid alumina/graphene nanoparticles can also reduce the flank wear by 12.29% (Sharma et al., 2018).
The microscopic images of the pin’s worn surfaces for various lubricants are given in Figure 9. It can be observed that for the case of L1, the worn surface consisted of micrometer size pores, an indication of severe contact condition (Figures 9A,B). The presence of graphene particle in POE oil, L2, although not reducing the specific wear rate, has resulted in a relatively smoother contact interface of the pin (Figures 9C,D), indicated by the absence of micro-pores on the contact interface such as those in Figure 9B. A relatively smooth contact interface of the pin was also achieved for the case of L3 (Figures 9E,F), as the effect of BC particles additive in POE oil. Although the contact interface contains many scratch marks, the nominal contact area shown in Figure 9E is smaller than Figure 9C. It seems that certain tribofilm was developed on the contact interface assisted by the BC microparticles that prevented the worn area from getting wider. Furthermore, Figures 9G,H indicates that the presence of graphene and BC particles in the lubricant has resulted in a significant reduction of the worn area on the pin, despite a relatively rough contact interface compared to those of Figure 9D or Figure 9F.
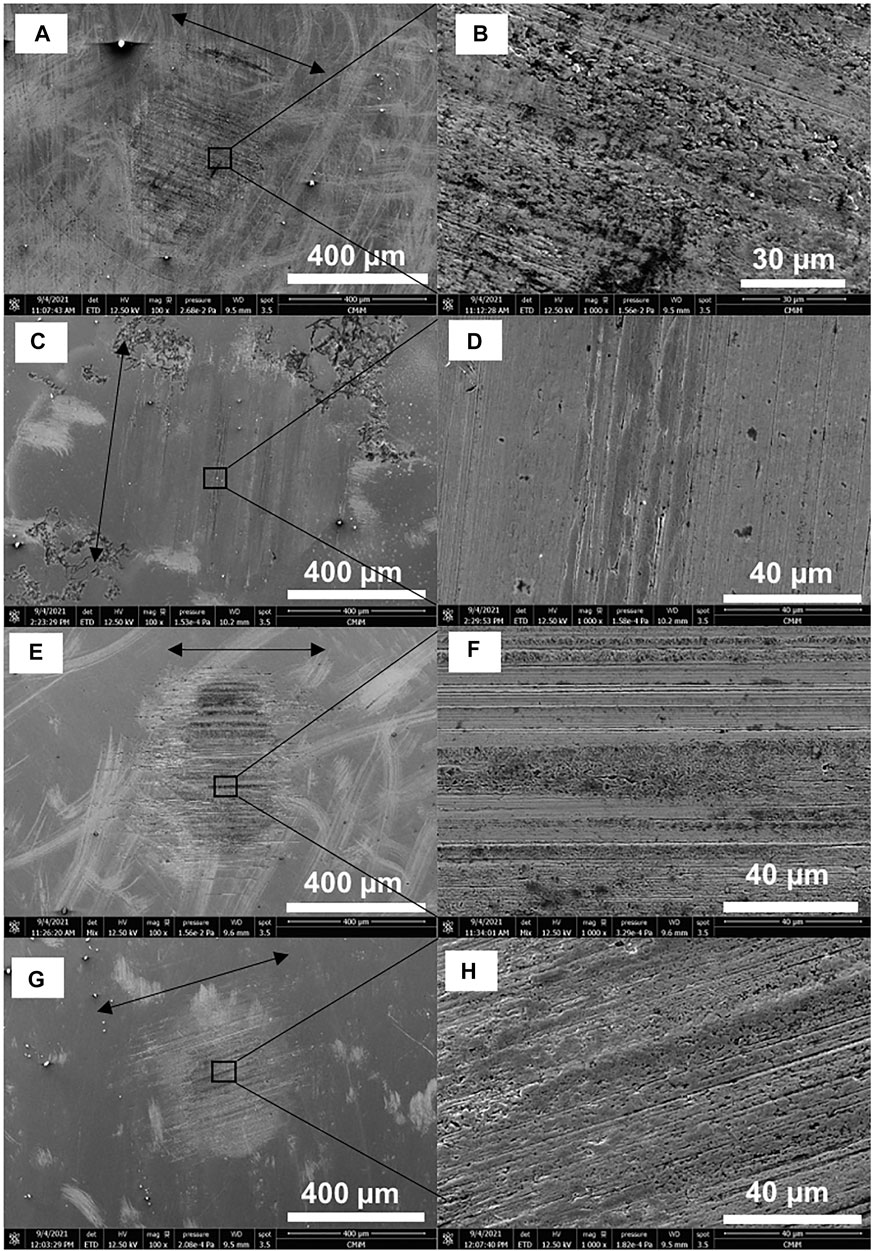
FIGURE 9. Worn scar of the pin; lubricated by L1 (A) and (B), L2 (C) and (D), L3 (E) and (F), and L4 (G) and (H), arrow indicating the sliding direction.
Wear Mechanism on the Contact Interface
The above results show that the incorporation of additives in the base oil has resulted in enhanced tribological performances of the tribo-pair. It was found that nanocellulose particles reduced friction and wear by mending effect (Li et al., 2019). Cellulose nanoparticles formed chain entanglement with the base oil and filled micropores on the contact interface. This study shows that the presence of BC particles had produced a relatively smoother contact interface of the tribo-pair as shown in (Figure 9F) compared to that without BC particles. Cellulose nano-crystal (CNC), including Bacterial Cellulose (BC), are crystalline structure products (Klemm et al., 2018; Thomas et al., 2018). Poorly structured crystallized particles have a better tendency to exfoliate when subjected to shear force, forming a sheet-like tribofilm on the contact interface (Lahouij et al., 2012), decreasing the friction and wear of the tribo-pair. Graphene particles, already in sheet-like nanoplatelets, also acted as interlayers between adjacent contact interfaces. A weak van der Waals force among the interlayers can easily exfoliate under shear force (Spear et al., 2015), resulting in further friction and wear rate reduction.
Figure 10 shows the results of EDS mapping for the pin’s worn surface for all lubricant conditions. It seems that oxygen plays an important role in friction and wear of the tribo-pair. Figure 10A indicates that the oxygen layer dominated the contact interface of the tribo-pair in the case of lubricant L1. High oxygen concentration means that oxides or hydroxides were formed on the contact interface, which led to severe oxidation causing high friction and wear loss (Morita et al., 2009). Therefore, the relatively rough contact interface shown in Figure 9B could be caused by material weakening due to oxidation. POE oil is highly sensitive to oxygen and water vapor and prone to becoming acidic as it absorbs the elements. The presence of organic acids can attack metal parts, leading to corrosion, excessive wear, and poor lubrication (Cartlidge and Schellhase 2003). This seems to occur in the friction test using L1 lubricant since it was conducted in the open air at a relatively high temperature.
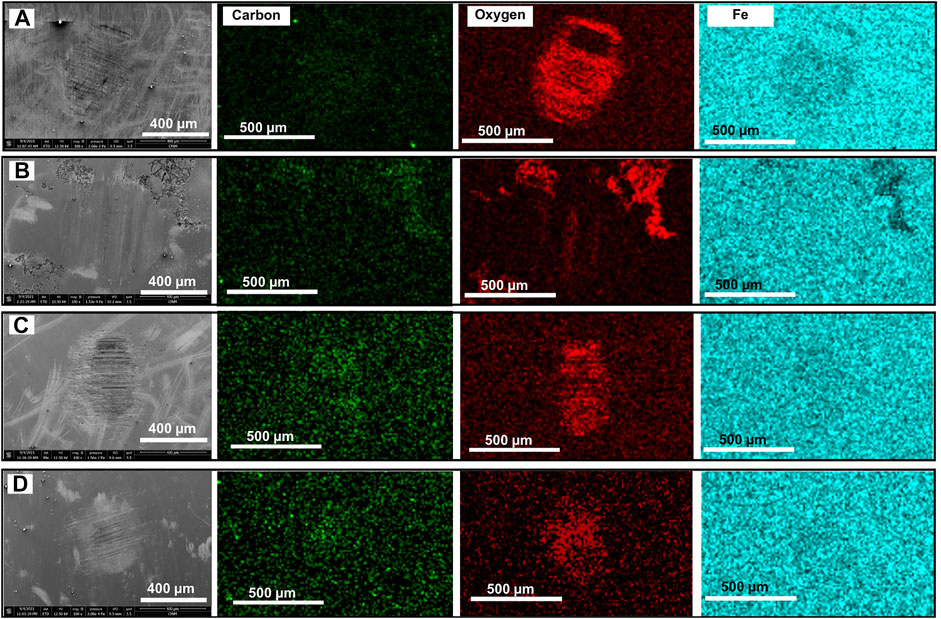
FIGURE 10. EDS map of the worn scar the pin; lubricated by L1 (A), L2 (B), L3 (C), and L4 (D), indicating the elements of Carbon, Oxygen and Iron (Fe).
With the presence of graphene in the POE oil, in the case of L2, the oxygen layer on the contact interface has significantly reduced, as indicated in Figure 10B. However, the oxygen layer existed outside the sliding track, seemingly wiped off by the sliding process and accumulated outside the contact area. The contact interface is relatively smooth without noticeable pores. A detailed observation of the oxygen accumulated area outside the sliding tract indicates the aggregation of wear particles. Graphene and its derivatives tend to aggregate, resulting in poor dispersion stability in the base oil medium (Ismail et al., 2021). It seems that the graphene particles have acted as abrasive particles providing a polishing effect to the contact interface. This has lowered the friction coefficient, although not reduced the specific wear rate of the pin.
Figure 10C indicates the presence of such a blackish tribo-layer on the contact area. In this case, the tribo-pair was lubricated by POE oil with BC additive; L3. Detailed observation conducted to the contact area revealed the presence of surface scratches around the adjacent contact area. It seems that at the early stage of friction, the contact area was wider. Furtherly, as friction continued, the tribofilm started developing. At the later stage of friction, as the tribofilm was fully developed, it prevented the worn area from getting wider, reducing the wear of the material. The tribofilm is oxygen-rich, but unlike that developed in the case of L1, it is not corrosive as it did not cause severe wear or rough contact interface. A possible explanation for the wear reduction is the formation of a crystalline tribo-layer of BNC particles by a mending mechanism (Li et al., 2019). The tribofilm prevented direct metal contact between the tribo-pair, resulting in low friction and wear of the material.
The incorporation of graphene nanoplatelets into the BC containing POE oil, L4, has further reduced the amount of oxygen trace on the contact interface (Figure 10D). Such a “blackish” tribo-layer similar to that in Figure 10C can also be observed on the contact interface (Figure 10D) although in a smaller amount. This emphasized the role of BC particles in tribofilm formation. Since the worn area is the smallest among all cases, it seems that the tribo-layer property has been further enhanced by graphene. The presence of graphene as an additive can form the protective film or tribological adsorption film on the contact interface, by tribo-chemical process, to improve the tribological properties of the lubricants (Berman et al., 2013; Fan et al., 2014; Zhao et al., 2017; Wang et al., 2018). The tribofilm is in an amorphous carbon structure indicated by the presence of sp2 and sp3 peaks in the Raman spectrograph (Wang et al., 2018; Ge et al., 2019). In this study, although the structural properties of the tribofilm are still unknown, it is highly possible that the structure is also carbon-based since graphene nanoplatelets are involved in the formation. Further analysis is required to clarify such tribofilm structure.
The presence of graphene nanoplatelets in the lubricant also provides a “healing” effect to the tribo-pair, possibly due to the tribofilm development of the contact interface. As shown in Figure 11, the friction was relatively low at the beginning of sliding (up to 45 mm sliding distance). The CoF increased to a value of more than 0,3 at the sliding distance of 7.5 m. However, it decreased again to a value of 0.15 (maximum) at the sliding distance of 45 m. This was observed for the case where both graphene and BC particles existed in the lubricant; L4. Graphene nanoplatelets only removed the oxygen-rich layer on the contact interface and smoothened the contact interface (Figure 10B). BC particles only reduced the contact area and produced an oxygen-rich tribofilm on the contact interface (Figure 10C). However, both graphene and BC particles in base oil not only reduced the contact area but also produced protective tribofilm on the contact interface. Therefore, the presence of both graphene nanoplatelets and BC particles is beneficial in improving the tribological properties of POE lubricant, bearing in mind that the friction tests were conducted at extreme contact conditions with an initial contact pressure of 1 GPa.
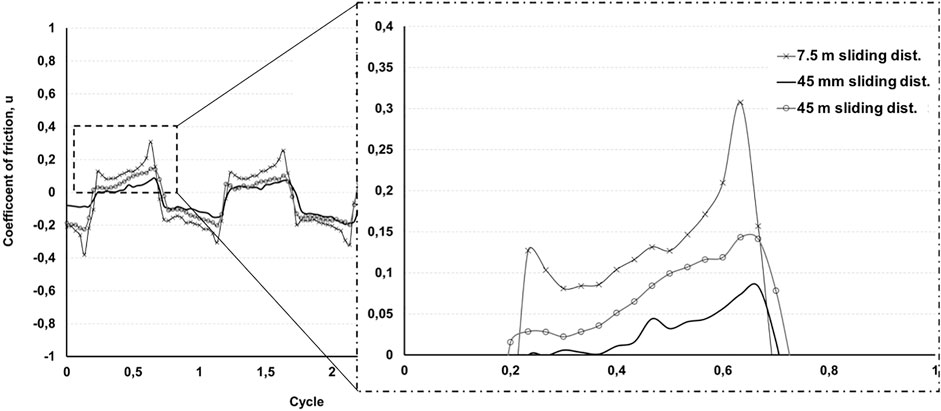
FIGURE 11. The presence of graphene in the lubricant provides a “healing” effect to the tribo-pair; friction increases at first but decreases again in the long run.
Conclusion
A combined effect of graphene nanoplatelets and Bacterial Cellulose (BC) particles as additives in POE lubricating oil enhanced the tribological properties. High friction and wear were observed under POE oil alone due to the formation of oxidative oxygen-rich tribofilm, causing pores on the contact interface. The graphene nanoplatelets additives dispersed in PEO oil significantly reduced the coefficient of friction, although unable to reduce wear. On the other hand, BC dispersed in POE oil reduced both frictions and wear rate (specific wear rate reduction approximately 30% after adding BC particle). Optimal tribological properties of POE oil were achieved when both BC particles and graphene nanoplatelets were dispersed in the lubricant, indicated by friction and wear reduction (specific wear rate reduction approximately 50%). These findings can be explained by the combined effect of both BC and graphene nanoplatelets in producing a protective tribofilm on the contact interface. Although the structure of this tribofilm is still not clear, it is highly possible that it is carbon-based since graphene is involved in the formation. Further analysis is required to reveal the structure of the tribofilm.
Data Availability Statement
The raw data supporting the conclusions of this article will be made available by the authors, without undue reservation.
Author Contributions
ZF carried out the data analysis and manuscript writing. DR carried out the lubricant’s preparation and analysis. RK conducted the experiment and data acquisition. FM carried out the lubricant’s analysis. HA, NN, and MK contributed in the data analysis and manuscript preparation. All authors read and approved the final manuscript.
Funding
Funding for this research is provided by Direktorat Riset dan Pengabdian Masyarakat, Kementerian Pendidikan, Kebudayaan, Riset dan Teknologi Republik Indonesia with Penelitian Dasar Scheme (154/E4.1/AK.04.PT/2021) and Sunway University’s International Research Network Grant Scheme (STR-IRNGS-SET-GAMRG-01-2021).
Conflict of Interest
The authors declare that the research was conducted in the absence of any commercial or financial relationships that could be construed as a potential conflict of interest.
Publisher’s Note
All claims expressed in this article are solely those of the authors and do not necessarily represent those of their affiliated organizations, or those of the publisher, the editors and the reviewers. Any product that may be evaluated in this article, or claim that may be made by its manufacturer, is not guaranteed or endorsed by the publisher.
Acknowledgments
Authors also thank Zulham and Shahibul Mighvar for their valuable contributions in the preparation and set-up of the tribometer used in this research.
Supplementary Material
The Supplementary Material for this article can be found online at: https://www.frontiersin.org/articles/10.3389/fmech.2022.810847/full#supplementary-material
References
Awang, N. W., Ramasamy, D., Kadirgama, K., Najafi, G., and Che Sidik, N. A. (2019a). Study on Friction and Wear of Cellulose Nanocrystal (CNC) Nanoparticle as Lubricating Additive in Engine Oil. Int. J. Heat Mass Transfer 131, 1196–1204. doi:10.1016/j.ijheatmasstransfer.2018.11.128
Awang, N. W., Ramasamy, D., Kadirgama, K., Samykano, M., Najafi, G., and Sidik, N. A. C. (2019b). An Experimental Study on Characterization and Properties of Nano Lubricant Containing Cellulose Nanocrystal (CNC). Int. J. Heat Mass Transfer 130, 1163–1169. doi:10.1016/j.ijheatmasstransfer.2018.11.041
Berman, D., Erdemir, A., and Sumant, A. V. (2013). Reduced Wear and Friction Enabled by Graphene Layers on Sliding Steel Surfaces in Dry Nitrogen. Carbon 59, 167–175. doi:10.1016/j.carbon.2013.03.006
Cartlidge, D., and Schellhase, H. (2003). Using Acid Number as a Leading Indicator of Refrigeration and Air Conditioning System Performance. U.S. Department of Commerce National Technical Information Service ARTI-21CR/. Available at: https://www.osti.gov/servlets/purl/823889 (Accessed November 7, 2021).
Dai, W., Kheireddin, B., Gao, H., and Liang, H. (2016). Roles of Nanoparticles in Oil Lubrication. Tribology Int. 102, 88–98. doi:10.1016/j.triboint.2016.05.020
Eswaraiah, V., Sankaranarayanan, V., and Ramaprabhu, S. (2011). Graphene-Based Engine Oil Nanofluids for Tribological Applications. ACS Appl. Mater. Inter. 3 (11), 4221–4227. doi:10.1021/am200851z
Fan, X., Xia, Y., Wang, L., and Li, W. (2014). Multilayer Graphene as a Lubricating Additive in Bentone Grease. Tribol Lett. 55 (3), 455–464. doi:10.1007/s11249-014-0369-1
Gara, L., and Zou, Q. (2013). Friction and Wear Characteristics of Oil-Based ZnO Nanofluids. Tribol. Trans. 56 (2), 236–244. doi:10.1080/10402004.2012.740148
Ge, X., Li, J., Wang, H., Zhang, C., Liu, Y., and Luo, J. (2019). Macroscale Superlubricity under Extreme Pressure Enabled by the Combination of Graphene-Oxide Nanosheets with Ionic Liquid. Carbon 151, 76–83. doi:10.1016/j.carbon.2019.05.070
Hewstone, R. K. (1994). Environmental Health Aspects of Lubricant Additives. Sci. Total Environ. 156 (3), 243–254. doi:10.1016/0048-9697(94)90191-0
Ismail, N. A., Zulkifli, N. W. M., Chowdhury, Z. Z., and Johan, M. R. (2021). Functionalization of Graphene-Based Materials: Effective Approach for Enhancement of Tribological Performance as Lubricant Additives. Diamond Relat. Mater. 115, 108357. doi:10.1016/j.diamond.2021.108357
Jia, Z., Chen, T., Wang, J., Ni, J., Li, H., and Shao, X. (2015). Synthesis, Characterization and Tribological Properties of Cu/Reduced Graphene Oxide Composites. Tribology Int. 88, 17–24. doi:10.1016/j.triboint.2015.02.028
Kamel, B. M., Emad El-Kashif, W., Hoziefa, M. S. S., and Abou Bakr, E. (2021). The Effect of MWCNTs/GNs Hybrid Addition on the Tribological and Rheological Properties of Lubricating Engine Oil. J. Dispers. Sci. Tech. 42, 1811–1819. doi:10.1080/01932691.2020.1789470
Klemm, D., Cranston, E. D., Fischer, D., Gama, M., Kedzior, S. A., Kralisch, D., et al. (2018). Nanocellulose as a Natural Source for Groundbreaking Applications in Materials Science: Today's State. Mater. Today 21 (7), 720–748. doi:10.1016/j.mattod.2018.02.001
Lahouij, I., Vacher, B., Martin, J.-M., and Dassenoy, F. (2012). IF-MoS2 Based Lubricants: Influence of Size, Shape and Crystal Structure. Wear 296 (1–2), 558–567. doi:10.1016/j.wear.2012.07.016
Li, K., Zhang, X., Du, C., Yang, J., Wu, B., Guo, Z., et al. (2019). Friction Reduction and Viscosity Modification of Cellulose Nanocrystals as Biolubricant Additives in Polyalphaolefin Oil. Carbohydr. Polym. 220, 228–235. doi:10.1016/j.carbpol.2019.05.072
Li, R., Yang, X., Hou, D., Wang, Y., and Zhang, J. (2020). Superlubricity of Carbon Nanostructural Films Enhanced by Graphene Nanoscrolls. Mater. Lett. 271, 127748. doi:10.1016/j.matlet.2020.127748
Meng, Y., Su, F., and Chen, Y. (2017). Au/Graphene Oxide Nanocomposite Synthesized in Supercritical CO2 Fluid as Energy Efficient Lubricant Additive. ACS Appl. Mater. Inter. 9 (45), 39549–39559. doi:10.1021/acsami.7b10276
Morita, T., Izumi, N., Matsukuma, N., and Sugimura, J. (2009). Effects of Oxygen Concentration on Friction and Wear of Stellite 6B and SUS316. Toraibarojisuto/Journal Jpn. Soc. Tribologists 54 (9), 637–641.
Oliveira, L. R., Silva, A. C. A., Dantas, N. O., and Bandarra Filho, E. P. (2017). Thermophysical Properties of TiO2-PVA/Water Nanofluids. Int. J. Heat Mass Transfer 115, 795–808. doi:10.1016/j.ijheatmasstransfer.2017.07.094
Periyasamy, C., Kumar, M., and Manickam, C. (2020). Experimental Studies on Stability of Multi Walled Carbon Nanotube with Different Oil Based Nanofluids. Therm. Sci. 24, 533–539. doi:10.2298/TSCI190412432P
Pham, S. T., Wan, S., Tieu, K. A., Ma, M., Zhu, H., Nguyen, H. H., et al. (2019). Unusual Competitive and Synergistic Effects of Graphite Nanoplates in Engine Oil on the Tribofilm Formation. Adv. Mater. Inter. 6 (19), 1901081. doi:10.1002/admi.201901081
Quinchia, L. A., Delgado, M. A., Reddyhoff, T., Gallegos, C., and Spikes, H. A. (2014). Tribological Studies of Potential Vegetable Oil-Based Lubricants Containing Environmentally Friendly Viscosity Modifiers. Tribology Int. 69, 110–117. doi:10.1016/j.triboint.2013.08.016
Rahmadiawan, D., Abral, H., Nasruddin, N., and Fuadi, Z. (2021a). Stability, Viscosity, and Tribology Properties of Polyol Ester Oil-Based Biolubricant Filled with TEMPO-Oxidized Bacterial Cellulose Nanofiber.” Edited by Subrata Mondal. Int. J. Polym. Sci. 2021, 5536047. doi:10.1155/2021/5536047
Rahmadiawan, D., Aslfattahi, N., Nasruddin, N., Saidur, R., Arifutzzaman, A., and Mohammed, H. A. (2021b). MXene Based Palm Oil Methyl Ester as an Effective Heat Transfer Fluid. J. Nano Res. 68, 17–34. doi:10.4028/www.scientific.net/jnanor.68.17
Samylingam, L., Anamalai, K., Kadirgama, K., Samykano, M., Ramasamy, D., Noor, M. M., et al. (2018). Thermal Analysis of Cellulose Nanocrystal-Ethylene Glycol Nanofluid Coolant. Int. J. Heat Mass Transfer 127, 173–181. doi:10.1016/j.ijheatmasstransfer.2018.07.080
Sharma, A. K., Arun Kumar, T., Amit Rai, D., Rabesh Kumar, S., and Mahip, S. (2018). Novel Uses of Alumina/Graphene Hybrid Nanoparticle Additives for Improved Tribological Properties of Lubricant in Turning Operation. Tribol. Int. 119, 99–111. doi:10.1016/j.triboint.2017.10.036
Sharma, A. K., Rabesh Kumar, S., Arun Kumar, T., Amit Rai, D., and Jitendra Kumar, K. (2020). Rheological Behaviour of Hybrid Nanofluids: A Review. Tribol. Mater. Appl., 77–94. doi:10.1007/978-3-030-47451-5_4
Singh, R. K., Sharma, O. P., and Singh, A. K. (2014). Evaluation of Cellulose Laurate Esters for Application as Green Biolubricant Additives. Ind. Eng. Chem. Res. 53 (25), 10276–10284. doi:10.1021/ie501093j
Spear, J. C., Ewers, B. W., and Batteas, J. D. (2015). 2D-Nanomaterials for Controlling Friction and Wear at Interfaces. Nano Today 10, 301–314. doi:10.1016/j.nantod.2015.04.003
Thomas, B., Raj, M. C., B, A. K., H, R. M., Joy, J., Moores, A., et al. (2018). Nanocellulose, A Versatile Green Platform: From Biosources to Materials and Their Applications. Chem. Rev. 118, 11575–11625. doi:10.1021/acs.chemrev.7b00627
Wang, J., Guo, X., He, Y., Jiang, M., and Gu, K. (2018). Tribological Characteristics of Graphene as Grease Additive Under Different Contact Forms. Tribology Int. 127, 457–469. doi:10.1016/j.triboint.2018.06.026
Xie, H., Jiang, B., Dai, J., Peng, C., Li, C., Li, Q., et al. (2018). Tribological Behaviors of Graphene and Graphene Oxide as Water-Based Lubricant Additives for Magnesium Alloy/Steel Contacts. Materials 11 (2), 206. doi:10.3390/ma11020206
Xu, Y., Peng, Y., Dearn, K. D., Zheng, X., Yao, L., and Hu, X. (2015). Synergistic Lubricating Behaviors of Graphene and MoS2 Dispersed in Esterified Bio-Oil for Steel/Steel Contact. Wear 342-343, 297–309. doi:10.1016/j.wear.2015.09.011
Zhang, Z. J., Dorin, S., and Mao, S. (2014). Graphite and Hybrid Nanomaterials as Lubricant Additives. Lubricants 2, 44–65. doi:10.3390/lubricants2020044
Zhao, J., Li, Y., Mao, J., He, Y., and Luo, J. (2017). Synthesis of Thermally Reduced Graphite Oxide in Sulfuric Acid and its Application as an Efficient Lubrication Additive. Tribology Int. 116, 303–309. doi:10.1016/j.triboint.2017.06.023
Keywords: bacterial nanocellulose, graphene nanoplatelets, bio-degradable lubricant, friction, wear
Citation: Fuadi Z, Rahmadiawan D, Kurniawan R, Mulana F, Abral H, Nasruddin N and Khalid M (2022) Effect of Graphene Nanoplatelets on Tribological Properties of Bacterial Cellulose/Polyolester Oil Bio-Lubricant. Front. Mech. Eng 8:810847. doi: 10.3389/fmech.2022.810847
Received: 08 November 2021; Accepted: 19 January 2022;
Published: 07 March 2022.
Edited by:
Nurin Wahidah Mohd Zulkifli, University of Malaya, MalaysiaReviewed by:
Jitendra Kumar Katiyar, SRM Institute of Science and Technology, IndiaT V V L N Rao, Madanapalle Institute of Technology & Science (MITS), India
Copyright © 2022 Fuadi, Rahmadiawan, Kurniawan, Mulana, Abral, Nasruddin and Khalid. This is an open-access article distributed under the terms of the Creative Commons Attribution License (CC BY). The use, distribution or reproduction in other forums is permitted, provided the original author(s) and the copyright owner(s) are credited and that the original publication in this journal is cited, in accordance with accepted academic practice. No use, distribution or reproduction is permitted which does not comply with these terms.
*Correspondence: Zahrul Fuadi, emFocnVsLmZ1YWRpQHVuc3lpYWguYWMuaWQ=