- Department of Mechanical Engineering, Ulsan National Institute of Science and Technology, Ulsan, South Korea
Bioinspired adhesives that emulate the unique dry and wet adhesion mechanisms of living systems have been actively explored over the past two decades. Synthetic bioinspired adhesives that have recently been developed exhibit versatile smart adhesion capabilities, including controllable adhesion strength, active adhesion control, no residue remaining on the surface, and robust and reversible adhesion to diverse dry and wet surfaces. Owing to these advantages, bioinspired adhesives have been applied to various engineering domains. This review summarizes recent efforts that have been undertaken in the application of synthetic dry and wet adhesives, mainly focusing on grippers, robots, and wearable sensors. Moreover, future directions and challenges toward the next generation of bioinspired adhesives for advanced industrial applications are described.
Introduction
Numerous living organisms have evolved various adhesion systems. Robust and repeatable adhesion that has been adapted to various environments is a key factor for survival as it enables efficient activities, including climbing, clinging, and catching prey. Among the various species, gecko lizards, beetles, octopuses, and remoras have attracted substantial attention owing to their excellent adhesion properties, such as high adhesion to curved or rough target surfaces, functionality in wet environments, reusability, and biocompatibility (Figure 1A) (Autumn et al., 2000; Dirks and Federle, 2011; Baik et al., 2017; Wang et al., 2017). Extensive studies over the past two decades have revealed that their superior adhesion properties originate from their unique terminal structures (Wang L. et al., 2020). For example, gecko lizards and beetles can walk freely on walls or ceilings with strong adhesion based on numerous pillar structures with spatulated or mushroom-shaped tips on their toes (Autumn et al., 2000; Arzt et al., 2003; Jeong et al., 2009b). Furthermore, they have an efficient self-cleaning property in both dry and wet conditions so that contaminants rarely attach to or are maintained on the adhesive surface (Hansen and Autumn, 2005; Lee and Fearing, 2008; Sethi et al., 2008; Spinner et al., 2013). The self-cleaning capability enables easy removal of the contaminants from the adhesive surfaces, i.e., the dry adhesive can quickly and fully recover a clean adhesion that does not transfer contaminants to the substrate (Bhushan and Sayer, 2007; Sethi et al., 2008). Moreover, underwater organisms, such as octopuses, remoras, and clingfishes, use a unique sucker structure to stably adhere to various wet surfaces (Lee et al., 2016, 2019). Strong wet adhesion allows them to grasp objects or to firmly adhere to slippery surfaces with ease.
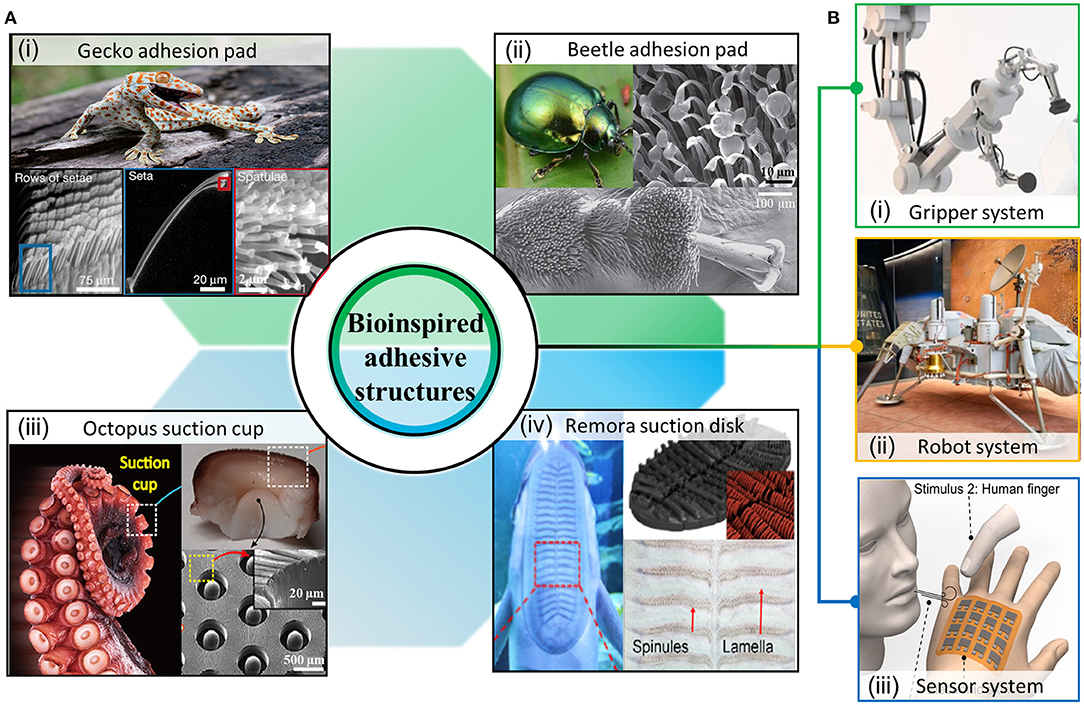
Figure 1. Research schematic of bioinspired adhesive structures for reversible dry and wet adhesion. (A) Representative examples of adhesive structures in nature: (i) gecko's toes [reprinted with permission from ref Zhao et al. (2008)] (ii) beetle's pads [reprinted with permission from ref Amador et al. (2017)]. (iii) octopus suction cup [reprinted with permission from ref Baik et al. (2019)]. (iv) remora suction disk [reprinted with permission from ref Lee et al. (2019)]. (B) Application field of adhesion structure (i) gripper (top), (ii) robot system (middle), (iii) wearable sensor system (bottom) [reprinted with permission from ref An et al. (2017)].
The unique adhesion systems that exist in nature offer high potential in various advanced industries, such as grippers, robots, and wearable sensors (Figure 1B) (Drotlef et al., 2017; Shahsavan et al., 2017). These application fields require strong and repeatable adhesion, particularly under harsh conditions, such as rough surfaces, high humidity, or even underwater environments. However, conventional contact methods, including mechanical fixation and chemical adhesion, are limited by their inferior adhesion performance. Mechanical fixations, whereby friction or an interlocking force are primarily applied, cause surface damage (Fuentes et al., 2015; O'Brien et al., 2019; Ozaki et al., 2020). Chemical adhesives have limitations such as low repeatability, surface contamination by residue, and vulnerability to moisture (Yuk et al., 2016; Pan et al., 2020). As a novel solution to these problems, bioinspired synthetic dry and wet adhesives have been applied to adhesion systems in advanced industries. For example, grippers integrated with bioinspired adhesives have been used for the precise and safe transportation of thin and fragile wafers (Zhou et al., 2013). Similarly, bioinspired adhesive-based mobile robots that can climb vertical walls, hang from the ceiling, or cling to underwater surfaces have been presented (Seo and Sitti, 2013; Yu et al., 2018). Moreover, adhesive microstructures enable wearable sensors that strongly adhere to skin, where continuous deformation and sweat may occur (Drotlef et al., 2017; Wi et al., 2017; Chun et al., 2019). In recent years, bioinspired adhesives with functional materials, such as conductive, biocompatible, and stimuli-responsive polymers or nanocomposites, have been proposed for advanced applications (Gu et al., 2018; Hwang et al., 2020; Tian et al., 2020).
In this review, we provide an overview of the use of bioinspired dry and wet adhesives in advanced applications. The remainder of this paper is organized as follows. In the first section, we briefly introduce the fundamental adhesion mechanisms that can be classified as dry and wet adhesion. In the second section, we describe how these novel adhesion systems are currently applied in three specific applications: grippers, robots, and wearable sensors. Finally, recent challenges and future directions for bioinspired adhesives and their applications are discussed.
Reversible Adhesion Mechanisms of Living Systems
Bioinspired Dry Adhesive Structures
Among the living organisms that exist in nature, beetles, flies, spiders, and geckos have versatile adhesion mechanisms that enable robust, reversible, repeatable, and clean adhesion on various rough surfaces (Figure 2A) (Autumn et al., 2000, 2002; Arzt et al., 2003; Geim et al., 2003). Many studies have revealed that their superior adhesion originates from their nano- or micrometer-scale hairy structures (Autumn et al., 2000, 2002; Arzt et al., 2003; Varenberg et al., 2010). For example, the gecko lizard has arrays of millions of microscale foot hairs, containing hundreds of nanoscale projections terminating in spatula-shaped tip structures (Niewiarowski et al., 2016). Similarly, beetles have hierarchical hairy structures on their legs, which are composed of numerous tiny setae with flattened and widened mushroom-shaped plates (Gorb et al., 2010; Bullock and Federle, 2011). These structures maximize the van der Waals interactions based on the three common structural features, grouped as hairy structures, extruded tips, and hierarchical structures (Figure 2B).

Figure 2. Bioinspired dry adhesive structures. (A) Various animals' tips and their properties [reprinted with permission from ref Arzt et al. (2003)]. (B) Schematic in hairy structures, tip shapes, and hierarchy of dry adhesive. (C) Fabricated high aspect ratio nano hairs [reprinted with permission from ref Jeong et al. (2006)]. (D) Experimental results in pull-off test of dry adhesive with different tips [reprinted with permission from ref Del Campo et al. (2007b)]. (E) Hierarchical pillar for high efficiency of adhesion [reprinted with permission from ref Murphy et al. (2009)].
Hairy structures are one of the most important features of dry adhesive systems. Numerous high-aspect-ratio hair structures enable effective adaptation to rough surfaces, resulting in a maximized contact area. Arzt et al. theoretically suggested that the adhesion of the pillar structure is based on Hertzian theory (Arzt et al., 2003). According to this study, when a single pillar structure with a hemispherical tip contacts the target surface, a finite pull-off force (FC) occurs, which is expressed as:
where γ is the adhesion energy per area and R is the hemisphere radius. Assuming that the entire contact surface consists of n pillars, each with a radius R/n0.5, the total adhesion force () can be increased to:
According to Equations (1) and (2), the adhesion resulting from the pillar structure becomes stronger as the number of pillars per unit area increases. Additionally, submicron- or nano-scale structures significantly reduce the effective modulus of the adhesives, enhancing the surface adaptability. The effective modulus (Eeff) of the pillar structures is given by (Autumn et al., 2006):
where E is the elastic modulus of the material, I is the moment of inertia, D is the pillar density, L is the pillar length, μ is the friction coefficient, and θ is the slanted angle of the pillar. The effective modulus can describe how relatively hard materials (Young's modulus higher than 100 kPa) function as a pressure-sensitive adhesive, emphasizing the need for high-aspect-ratio hairy structures. However, the effective modulus needs to be incorporated with proper contact geometry because the shape of the tips (or caps) dominates the stress distribution on the contact interfaces (Kroner and Arzt, 2012).
The extruding tip structure, such as spatula and mushroom (symmetric spatulae), which can be observed at the end of the pillar structure, has a significant effect on the adhesion of the dry adhesive structure (Kim and Sitti, 2006; Del Campo et al., 2007b; Bullock and Federle, 2011; Kwak et al., 2011a; Heepe et al., 2012; Kroner and Arzt, 2012; Oh et al., 2019). The extruding tip structures not only increase the contact area of the hairy structures but also uniformly distribute the stress at the contact interface until they are separated from the target substrate (Carbone et al., 2011). As a result, the adhesives can be strongly attached to the substrate with high stability, even over millions of cycles of repeated attachment and detachment.
The hierarchical arrangement of gecko foot hair is also a key element that can maximize adhesion performance (Murphy et al., 2009; Bae et al., 2014). Various studies have revealed that the hierarchy improves adaptability to surfaces with roughness at different length scales (macro – nano). Furthermore, they significantly improved the structural stability by effectively distributing the stress between hierarchies during repeated loading cycles.
Based on these mechanisms, many studies have been conducted to mimic the superior adhesion performance of dry adhesives in nature. Studies have been proposed that maximize the van der Waals interactions of micro-and nanoscale hairy structures by increasing the aspect ratio and reducing the diameter (Geim et al., 2003; Mahdavi et al., 2008). Greiner et al. developed microscale vertical pillars with high aspect ratios using a soft molding method (Greiner et al., 2007). The pull-off strength was measured up to 20 kPa in pillars with aspect ratios above 5. Nanoscale hairy structures with a high aspect ratio of over 20 and a small radius (~80 nm) were proposed based on the nanodrawing method (Figure 2C) (Jeong et al., 2006). Qu et al. presented a carbon nanotube (CNT)-based dry adhesive to achieve an extremely small radius (~15 nm) and high aspect ratio of the nanoscale hair array (Qu et al., 2008).
On the other hand, to realize adhesion enhancement, many researchers have focused on controlling 3D tip geometries (Del Campo et al., 2007a; Carbone et al., 2011; Kwak et al., 2011b). For example, artificial dry adhesives with various 3D tip structures, including spatulae, mushroom (symmetric spatulae), and triangular shapes have been developed (Del Campo et al., 2007b; Kwak et al., 2011a). Among them, mushroom-shaped tip structures were reported to exhibit outstanding adhesion performance (Figure 2D) (Del Campo et al., 2007b; Yi et al., 2016). The diameter and thickness of the mushroom-shaped tip structures are key factors in determining adhesion strength and structural stability. Yi et al. demonstrated that the adhesion of optimized tip structures was ~10 times stronger than that of non-optimized tips (Yi et al., 2016). Several studies have presented finite element analyses (FEA) incorporating contact geometry optimization of dry adhesives for uniform stress distribution within the tips (Zhang X. et al., 2021). Recently, Kim et al. reported deep learning-based optimization of mushroom-shaped structures composed of smoothly mixed convex and concave parts and demonstrated improved uniformity in the interfacial stress distribution (Kim et al., 2020).
Furthermore, various studies have reported improved adhesion performance based on hierarchical structures. For example, aligned CNT forests integrated with micro-sized pillars were utilized as hierarchical adhesives exhibiting 9 times stronger shear adhesion than that of a micropillar uncovered with CNT forests (Rong et al., 2014). Jeong et al. developed monolithic micro-and nanoscale hierarchical hairs using a 2-step UV-assisted molding technique, which has a robust shear adhesion force even on a rough surface (Jeong et al., 2009b). In addition, Murphy et al. proposed a novel adhesive structure that integrates the structural advantages of hierarchical and extruding tip structures (Figure 2E) (Murphy et al., 2009). Hierarchical structures with mushroom-shaped tips fabricated through the multilevel molding technique exhibited 5.3 times higher adhesion than unstructured surfaces.
Bioinspired Wet Adhesive Structures
Organisms that live in wet and underwater environments have different adhesive mechanisms than those living in dry conditions. In particular, the octopus, tree frog, and clingfish can achieve reversible adhesion with a strong attachment to surfaces under wet conditions (Drotlef et al., 2013; Zou et al., 2016; Wang et al., 2017; Zhao et al., 2017; Zhang et al., 2019; Chen et al., 2020). These strong wet adhesions are derived from special micro/nanostructures on the surface of organisms, such as suction cups and polygonal patterns. Their unique structures enable them to maintain strong wet adhesion to various curved and rough surfaces through suction, which is driven by a pressure difference and capillary adhesion. In recent years, extensive research has been conducted to determine the principles of wet adhesion and to emulate the adhesion mechanism (O'Brien et al., 2019; Chen et al., 2020).
An octopus achieves adhesion using a mechanism that causes a pressure difference through a suction cup in a wet environment (Figure 3A) (Tramacere et al., 2014, 2015; Oh et al., 2018). A hollowed space, known as the sucker cavity, exists inside the suction cup. With an applied preload, a pressure drop in the suction cup occurs with a volumetric change, where the dome-like structure inside the cavity maximizes the pressure difference between the inside and outside (Figure 3B) (Tramacere et al., 2013). The pressure difference can serve as a major mechanism underwater because of the higher external pressure. The governing equation for the adhesion force (Fnormal) that can be induced through the suction cup structure is expressed as follows (Chen and Yang, 2017):
where ΔP is the pressure difference between the inside and outside of the suction cup, and Atotal is the total adhesion area of the suction structure. According to this equation, the pressure difference plays a significant role in adjusting the suction cup adhesion.
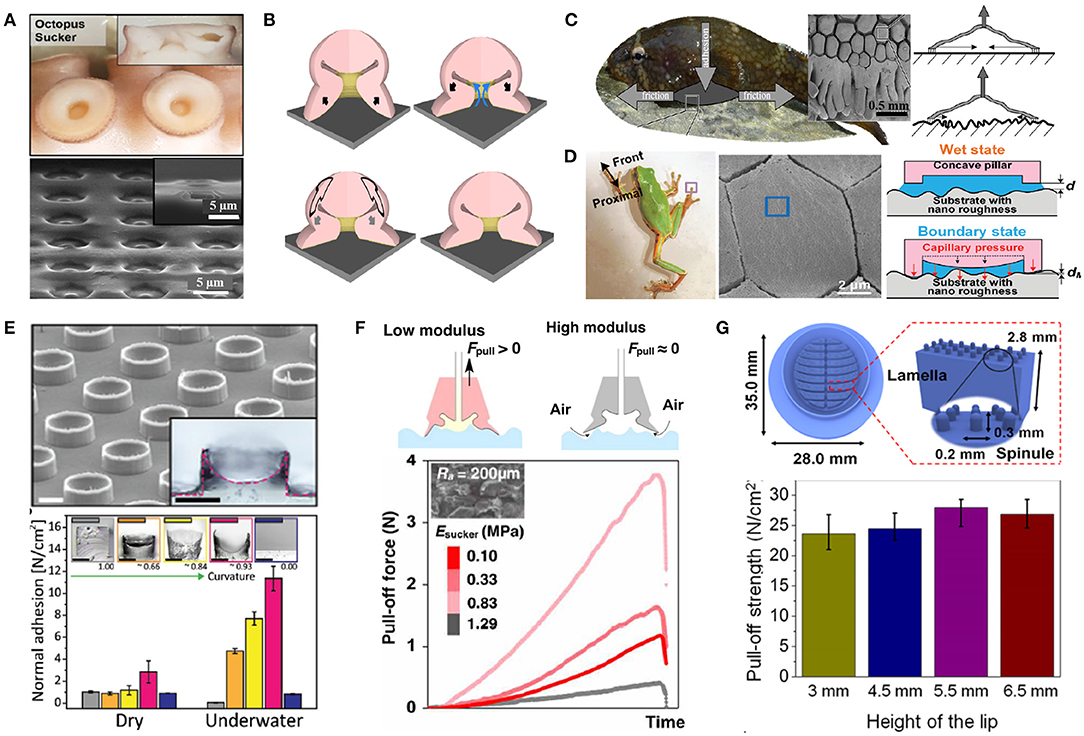
Figure 3. Bioinspired wet adhesive structures. (A) Octopus-inspired suction cup [reprinted with permission from ref Oh et al. (2018)]. (B) Adhesion mechanism of suction cup under wet conditions [reprinted with permission from ref Tramacere et al. (2013)]. (C) Clingfish-inspired sucker and hexagonal microstructure mechanism under wet conditions [reprinted with permission from ref Wainwright et al. (2013)]. (D) Tree frog-inspired regular hexagonal microstructure and adhesion mechanism under wet conditions [reprinted with permission from ref Zhang et al. (2020)]. (E) Section of sucker cavity and adhesion strength under dry/underwater conditions [reprinted with permission from ref Baik et al. (2018)]. (F) Organohydrogel-based sucker and adhesion strength under wet conditions [reprinted with permission from ref Zhuo et al. (2020)]. (G) Lamella and spinule structure of suction and varying adhesion strength with lip height under wet conditions [reprinted with permission from ref Lee et al. (2019)].
Clingfish can strongly attach themselves to various wet surfaces because of their hierarchical adhesion mechanism, which consists of suction and friction (Wainwright et al., 2013). The adhesive disc of the clingfish is composed of a suction chamber and rows of papillae structures around the chamber. The papillae structures divided into a polygonal shape increases the friction, regardless of the roughness of the target surface. When the suction chamber fails, the edges slide toward the center of the chamber. However, the increase in friction at the edges significantly improves the adhesion by resisting sliding. Due to this hierarchical structure of the adhesive disc, clingfish adhere well to surfaces of different roughness, developing pull-off forces that are 80 to 230 times the bodyweight of the clingfish (Figure 3C) (Wainwright et al., 2013; Sandoval et al., 2019, 2020).
Tree frogs exhibit different types of wet adhesive mechanisms (Iturri et al., 2015; Langowski et al., 2018). Polygonal patterns on the toe pads of the tree frog can strongly adhere to the liquid-vapor interface. The wet adhesion principle originates from the capillary force, whereby the attraction between the surface and structure is transformed into an adhesion force (Fnormal) (Figure 3D) (Zhang et al., 2020). According to this principle, organisms can adhere to surfaces by obtaining high adhesion/friction, even under wet conditions. The capillary-force-based adhesion force is expressed as follows (Chen et al., 2020):
where Rl is the liquid film radius, h is the liquid film thickness, θ1 and θ2 are the contact angles, and η is the viscosity coefficient of the liquid.
Research on the superior adhesion mechanism of suction cups and polygonal patterns has promoted the development of artificial wet adhesives. In particular, several strategies have been reported to construct more complex 3D configurations and scale down to submicron/nano. Nano-or microsuckers with cavity structures were presented based on hole-patterned mold-assisted soft lithography (Chen and Yang, 2017; Oh et al., 2018). In addition, complex configurations of the suction cup components, such as the orifice and protuberance, were successfully mimicked for wet adhesives by controlling the meniscus of a liquid precursor (Baik et al., 2017). They revealed that the combination of the complex structures helps the adhesive to exert a strong adhesion of up to 110 kPa under wet conditions (Baik et al., 2018) (Figure 3E). Lee et al. developed a suction cup composed of thermoresponsive polymers exhibiting enhanced adhesion of up to 94 kPa (Lee et al., 2016). Zhou et al. also presented a pneumatic sucker exhibiting excellent adaptable adhesion up to 3.75 N on a rough surface (with surface roughness Ra = 200 μm) under a sucker's modulus of 1.29 MPa (Figure 3F) (Zhuo et al., 2020). Recently, a 3D Printing based bottom-up approach was applied to a micro-suction disk, which exerts high friction of up to 266.8 kPa (Figure 3G) (Lee et al., 2019). Furthermore, hexagonal-shaped micropatterns were presented as strong wet adhesives, where the synergistic effects of the low bending stiffness of the pillars and a high number density of the pattern in the sliding direction exhibit a robust friction force, even underwater (Chen et al., 2015; Iturri et al., 2015; Ko et al., 2017a).
The gecko-inspired nano/microstructure can be utilized as wet adhesives, where the surface wettability of both the gecko adhesives and target substrates can also play a significant role in wet conditions (Stark et al., 2014; Stark and Mitchell, 2019; Mitchell et al., 2020). When the micropillars and wet substrate come into contact, the interfacial water layer reduces adhesion by causing van der Waals interference and the lubrication effect. In the case of a hydrophilic substrate, the surface does not effectively prevent or repel interfacial water, which significantly reduces adhesion compared to dry conditions (Stark et al., 2014). However, on a hydrophobic substrate, the interface between the adhesive and substrate can repel water and maintain dry adhesion based on van der Waals interactions. Based on this principle, Soltannia et al. presented mushroom-shaped microfibers with strong and reversible underwater adhesion (Soltannia and Sameoto, 2014), which can be applied to attachable gaskets in microfluidic devices and microstrips (Wasay and Sameoto, 2015; Zandvakili et al., 2017).
Research on the integration of dry and wet adhesives has also been actively conducted. Representatively, Lee et al. presented a dry-wet hybrid mechanism in which gecko-inspired dry adhesives were integrated with mussel-inspired wet adhesives of 3,4-dihydroxy-L-phenylalanine (DOPA) proteins (Lee et al., 2007) that form non-covalent interactions (hydrogen bonding, cation-pi interaction, metal coordination, hydrophobic interaction) on diverse organic and inorganic substrates, both in air and underwater (Hofman et al., 2018). Furthermore, the hydrogel was combined with gecko adhesives for the synergistic effect of mushroom-shaped micropillars and water-absorbing properties with the hydrophilic nature of the hydrogel (Yi et al., 2018). The combination enables strong van der Waals adhesion under dry conditions and capillary adhesion under wet conditions. Recently, Wang et al. proposed fibrillar adhesives with angled tip structures (cupped microstructures), exhibiting strong and reversible adhesion properties under both dry and wet conditions (Wang et al., 2019b; Wang Y. et al., 2020). The cup-shaped contact geometry enables strong adhesion mechanisms attributed to van der Waals interactions under dry conditions, while suction under wet conditions. Because the wet adhesion of existing flat mushroom structures is feasible under limited conditions (e.g., hydrophobic mating surfaces), the hybrid approach is expected to be an effective solution for robust adhesion in both dry and wet environments.
Applications of Bioinspired Dry and Wet Adhesives
Robust adhesion systems have been actively explored in advanced industries. In particular, grippers, robots, and sensors require reversible and versatile adhesion to dry/wet conditions. Accordingly, many researchers have introduced bioinspired dry/wet adhesive structures for advanced applications. In this section, we discuss how dry/wet adhesives are applied to these application fields in detail.
Bioinspired Adhesives on Advanced Grippers
In recent years, gripper systems have been used in various industrial fields to improve the efficiency of manufacturing processes by transporting objects or assisting repetitive work (Tai et al., 2016). With the development of various manufacturing industries, industrial grippers with the ability to grasp fragile or rough objects and to hold and release an object repeatedly without residue or damage are highly required (Sinatra et al., 2019). Wet adhesion capability is also required to allow grippers to easily transport objects in wet or underwater environments (Nishimura et al., 2017).
Bioinspired dry adhesives help grippers improve grasping capability with excellent adhesion properties. Furthermore, the switchable adhesion properties provide simple and efficient grip control (Lee et al., 2008; Zhou et al., 2013; Seo et al., 2014). For example, mushroom-shaped pillar arrays were integrated into a transportation system for fragile wafers (Zhou et al., 2013) (Figure 4A). The transportation system exhibited strong adhesion to the objects without a high preloading force, as well as controllable switchable adhesion properties by applying a small shear force without the consumption of external energy. Jiang et al. developed a gripper system with multiple patches and angled microwedges (Jiang et al., 2017). The discrete patches allow the gripper system to hold the curved objects by allowing the patches to form conformal contact from micro- to macroscale on the target surface. A gripper system with an elastic microfibrillar membrane was presented, which could be deformable under pneumatic control to exhibit robust adhesion to curved or irregular objects (Figure 4B) (Song and Sitti, 2014; Song et al., 2017).
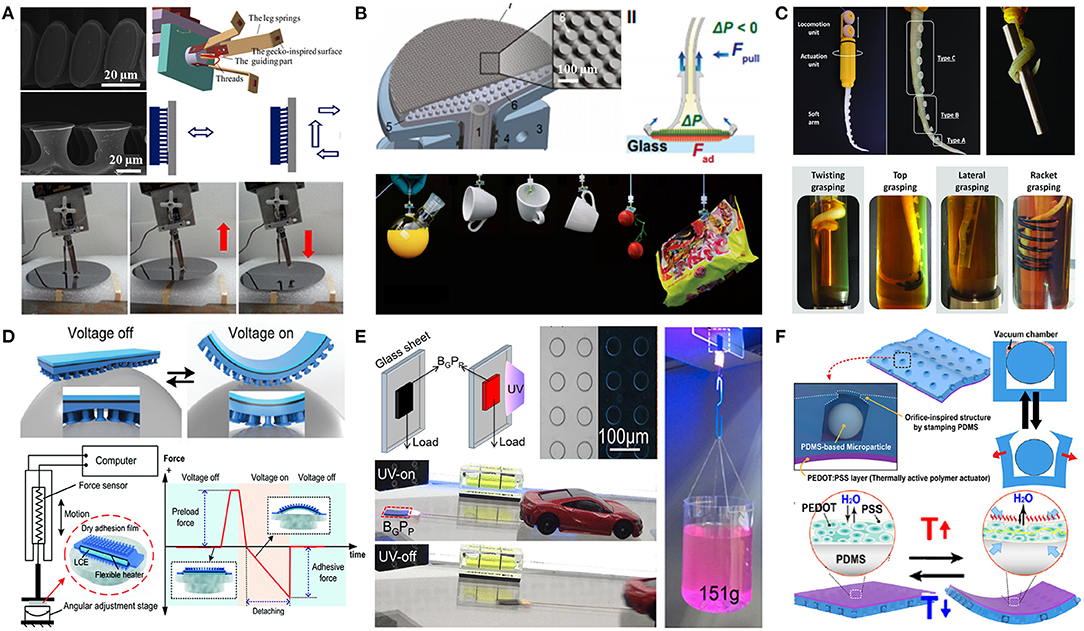
Figure 4. Dry and wet adhesion structure application in gripper system. (A) Gecko dry adhesive structure to obtain strong adhesion [reprinted with permission from ref Zhou et al. (2013)]. (B) Dry adhesive structure applied to sucker structure [reprinted with permission from ref Song et al. (2017)]. (C) Wet adhesive structure applied to gripper system [reprinted with permission from ref Mazzolai et al. (2019)]. (D) Control of gripper adhesion with dry adhesion structure at low voltage [reprinted with permission from ref Tian et al. (2020)]. (E) Light-responsive adhesion control of dry adhesion structure [reprinted with permission from ref Wang X. et al. (2019)]. (F) Electrothermal-based adhesion control of wet adhesion structure [reprinted with permission from ref Baik et al. (2021)].
Moreover, a gripper system with wet adhesives, such as suction cup structures, is capable of grasping wet objects in various morphologies without slipping under wet environments. Mazzolai et al. presented a soft arm with suction cups to retrieve non-standard objects under various dry/wet conditions, including the medium of air, water, and oil (Figure 4C) (Mazzolai et al., 2019). Furthermore, the combined pneumatic-controllable suckers enable the soft gripper to grasp objects with various configurations (i.e., flat, spherical, and hexagonal shapes in wet conditions) (Zhuo et al., 2020).
Dry/wet adhesive structures based on stimuli-responsive materials have been applied to gripper systems to achieve controllable adhesion strength. Tian et al. presented a gripper that could control adhesion using a dry adhesive with an electrically responsive characteristic (Figure 4D) (Tian et al., 2020). In addition, photothermal polymers were adapted to micropatterned soft grippers for a fast switchable dry adhesive, where the adhesion strength could increase up to a maximum of 2.5 times after exposure to UV light (Figure 4E) (Wang X. et al., 2019). A gripper system with an electrothermally controllable sucker was presented, which was capable of fast underwater adhesion control (Figure 4F) (Baik et al., 2021).
Bioinspired Adhesives on Advanced Robots
In recent years, various robotic systems have been utilized to perform tasks in extreme situations that are inaccessible to humans, such as confined spaces or underwater (Jiang et al., 2017; Ma et al., 2018). The adhesion system is considered an important technical component: it enables the robotics to be highly mobile, settle down safely, and sense the object through conformal contact, even on a ceiling, steep slope, or underwater (Kwak et al., 2011c). However, conventional adhesive methods, such as vacuum or electrostatic adsorption, are not suitable for tuning the adhesion of remote-controllable robots owing to the connection of the pneumatic or electrical control system. Furthermore, adhesion switching systems are quite energy-consuming because they require a continuous supply of external energy to maintain adhesion (Gu et al., 2018). As a solution to existing problems, various approaches utilizing bioinspired adhesives have been actively conducted.
The nano/micro-scale hairy structures of the gecko and beetle have been applied to dry adhesive systems in robots. A four-legged climbing robot with a bioinspired multi-toe with a dry adhesive exhibited strong adhesion without high pressure during attachment (Figure 5A) (Kim et al., 2008; Wang et al., 2018). Furthermore, the adhesive structure enhanced the stability and adaptability to a rough surface. The dry adhesive structure was also integrated into a controllable locomotion wheel (Figure 5B) (Liu J. F. et al., 2020). Depending on the rotational direction of the wheel and belt, the anisotropic dry adhesive on the belt can control the adhesion for continuous attachment and detachment. In numerous studies, a dry adhesive capable of maintaining robust contact under peeling conditions has been applied to robots for high mobility on ceilings, steep slopes, and curved surfaces. Ko et al. presented a wall-and-ceiling-climbing quadruped robot with mushroom-shaped dry adhesive pads positioned on the foot (Figure 5C) (Ko et al., 2017b). This design allowed the robot system to adhere firmly to the ceiling or wall against its weight and reduce the peeling stress. In addition, a bioinspired robot that mimicked the multi-joint leg and dry adhesive footpad of a gecko has been reported (Figure 5D) (Tang et al., 2019). The multi-joint leg with attachable and deformable dry adhesive microstructures enabled the robots to move vertically without slipping.
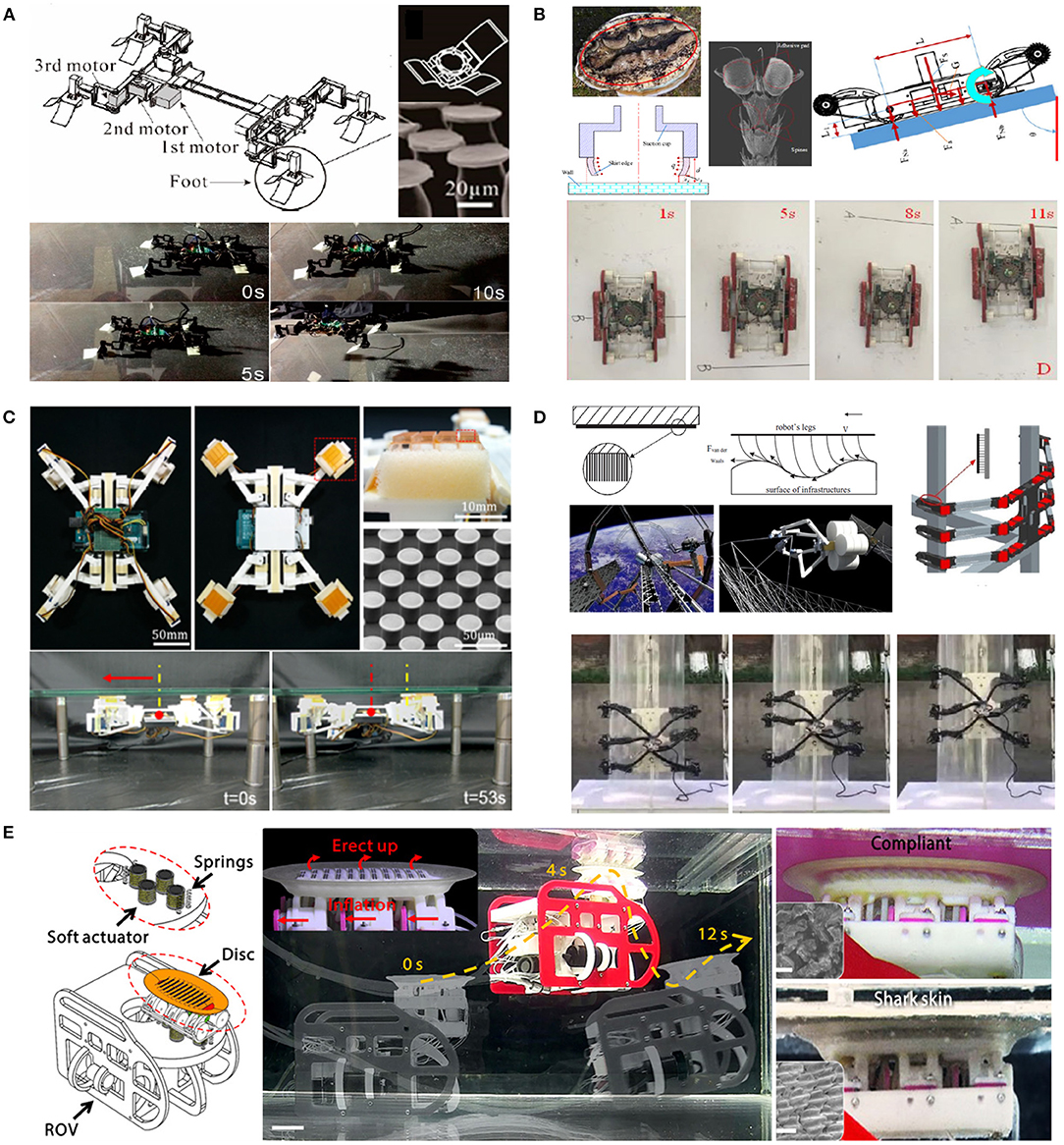
Figure 5. Dry and wet adhesive applied to mobile robots. (A) Robot system with mushroom-shaped dry adhesive and locomotion by controlling adhesion strength [reprinted with permission from ref Wang et al. (2018)]. (B) Wall-climbing robot with an adhesive belt and four-wheeled system [reprinted with permission from ref Liu J. F. et al. (2020)]. (C) Wall and ceiling climbing quadruped robot with mushroom-shaped dry adhesive pads [reprinted with permission from ref Ko et al. (2017b)]. (D) Space truss-crawling robot with multi-joint leg and dry adhesive [reprinted with permission from ref Tang et al. (2019)]. (E) Remora-inspired biorobot with suction disc and locomotion under wet conditions [reprinted with permission from ref Wang et al. (2017)].
Moreover, numerous bioinspired wet adhesives have been applied to robots to ensure stable contact with the target object and settle down exactly on the target point in a wet environment. The anatomical properties of suction disks in the clingfish were applied to the marine robot (Figure 5E) (Wang et al., 2017). Suction disks allowed clingfish robots to exhibit wet adhesion of up to 436.6 N, which is capable of adhering to biological and non-biological target objects, such as fishes and hulls. Iwasaki et al. presented a medical soft robot with a millimeter-scale suction cup array integrated with a neodymium magnet that could control the adhesion and locomotion via external magnetic fields, enabling strong adhesion to the wet surfaces of an internal organ (Iwasaki et al., 2020). Ma et al. presented a robot system that can climb to a steep slope under dry and wet conditions using a gecko dry adhesive coated poly(dopamine methacrylate-co-2-methoxyethyl acrylate-co-isopropyl acrylamide)(p(DMA-co-MEA-co-NIAAM))/iron oxide (Fe3O4) composite (Ma et al., 2018). The superior and reversible adhesion performance enables the robot to move swiftly and adhere firmly on the slippery surface in wet conditions.
Bioinspired Adhesives on Advanced Sensors
Conformal contact without slip or peeling is fundamental for the stable detection of advanced sensors (Wang C. H. et al., 2019; Zhang C. et al., 2021). Conventional approaches, such as a pressure-sensitive adhesive (PSA) and an ionic gel, can adhere to the substrate with a tacky surface. However, these methods not only cause damage or injury to a substrate but also delaminate the sensors from the substrate under wet conditions (Ameri et al., 2017; Park et al., 2020). The application of bio-inspired dry/wet adhesives to sensors has superior advantages compared to previous methods: (1) reversible and restorable adhesion, (2) enhanced conformality to the rough surface, and (3) versatility to diverse substrates with different surface properties (Hwang et al., 2020).
In particular, it is challenging for sensors to adhere to the skin because it is rough and deforms as the body moves (Hwang et al., 2018). To enhance the adhesion of the sensor to the skin, a high-aspect-ratio micro hair electrocardiogram (ECG) sensor was developed, in which conformally adapted microstructures can reduce the noise of the generated pulse signals from the body (Pang et al., 2015). Furthermore, several microfibrillar adhesives have been applied to wearable sensors that allow conformal contact with the microgroove of the skin and achieve stable detection with a low signal-to-noise ratio even on deformed skin (Drotlef et al., 2017; Liu X. J. et al., 2020).
In addition, various studies have been conducted on smart devices for sensing human motion to maintain high adhesion despite dynamic movements. Seong et al. showed a self-attachable and flexible strain sensor with CNT-coated, mushroom-shaped microstructures (Figure 6A) (Seong et al., 2020). The protruding tips of the mushroom structures exhibited robust adhesion to the target surface while the conductive CNT layer was highly sensitive to strain, even for repeatable detection cycles. Furthermore, a mushroom-shaped dry adhesive based on a graphene/CNT/PDMS nanocomposite was utilized as an attachable ECG sensor that sensed a fine electrical signal and precisely distinguished various types of human movements without detachment (Figure 6B) (Kim et al., 2016).
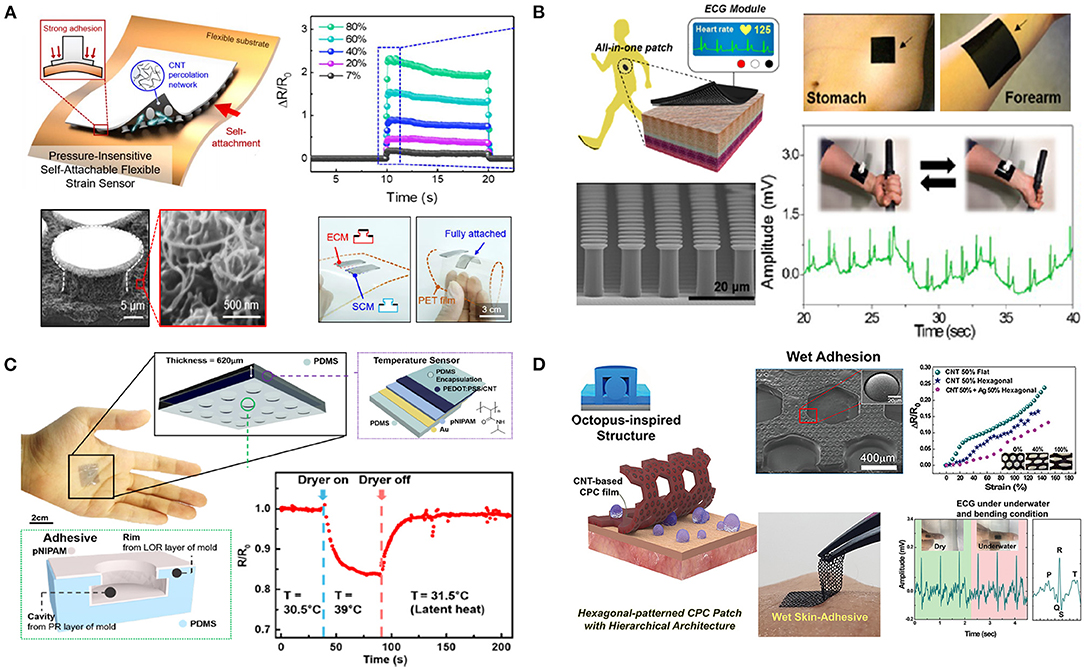
Figure 6. Bioinspired adhesive applied sensors. (A) Gecko-inspired dry adhesive applied to strain sensor exhibiting conformal contact on a flexible curved surface [reprinted with permission from ref Seong et al. (2020)]. (B) Gecko-inspired dry adhesive applied to a wearable sensor with conductive nanocomposite for ECG signal and motion detection [reprinted with permission from ref Kim et al. (2016)]. (C) Octopus-inspired microstructure adhesive applied to temperature sensor exhibiting relative resistance changes according to skin temperature [reprinted with permission from ref Oh et al. (2018)]. (D) Octopus-inspired wet adhesive applied to a sensor with conductive polymer composite for bio-signal detection under underwater conditions [reprinted with permission from ref Min et al. (2020)].
Furthermore, wet adhesives have been applied to sensors to maintain strong adhesion and sensing performance on sweaty skin or underwater (Wu et al., 2021). Many studies have integrated octopus-inspired suckers into sensors. Octopus-inspired suction cups have been demonstrated for medical sensor applications to improve wet adhesion by inducing negative pressure within the cavity under wet conditions, where various vital signals — including body temperature, respiration, electrocardiogram (ECG), pulse, and blood pressure — can be detected stably (Choi et al., 2016). Furthermore, wet adhesive microstructures mimicking octopus sucker rims were presented as skin-attachable temperature sensors (Figure 6C) (Oh et al., 2018). The octopus-inspired structures enhanced the sensing accuracy of body temperature, even when sweating. Min et al. developed a skin-attachable sensor with a dome-shaped sucker that was drainable owing to mesh patterns, where the skin patch showed high normal adhesion strength under wet and underwater conditions (Figure 6D) (Min et al., 2020).
Conclusions
With the development of advanced industrial applications, such as grippers, robots, and sensors, bioinspired adhesives have become a promising solution to the low adhesion functionality of existing adhesion systems. Accordingly, bioinspired adhesive structures represented by pillar and sucker structures are being actively studied owing to their extraordinary adhesion with conformal, controllable, damage- and contamination-free properties, even in wet environments. In this review, we investigated the application of these adhesive structures in the field. Bioinspired adhesives enable robotic systems to perform efficient locomotion, such as climbing, clinging, and gripping. In addition, they improve the sensing performance of attachable sensors by allowing them to make close contact with the target surfaces, even in wet environments. However, despite these advances, certain problems remain to be solved.
First, although various studies have been conducted on dry and wet adhesives for strong skin adhesion, it is still challenging to adhere to skin that has various surface contaminants, such as dead cells, hair, secreted oil, and sweat (Bae et al., 2013; Choi et al., 2016; Kim et al., 2016; Baik et al., 2017; Stauffer et al., 2018). In particular, repeated deformations, such as bending or stretching of the joints (e.g., elbows and knees), hinder stable and long-term attachment (Liu et al., 2017; Stauffer et al., 2018).
Second, bioinspired adhesives with actively and rapidly switchable adhesion require further development. Controllable adhesives that are responsive to external stimuli enable the rapid transportation of industrial gripper systems, swift climbing of robots, and easy detachment of skin patches. Although various stimuli-responsive materials, such as heat, light, and electricity have been suggested, several limitations restrict their practical application to real industries. For example, thermo-responsive polymers have been integrated into mushroom-shaped adhesives for electrothermally controllable soft grippers, which have a relatively slow response time of ~10 min per pick and place cycle (Li et al., 2020). An electro-responsive adhesive based on a dielectric elastomer was developed for the feet of soft wall-climbing robots (Gu et al., 2018). Even though they respond quickly (within a second per gait cycle), for adhesion control they require an operating voltage of at least 6,000 V for fast movement, which is quite energy-consuming in terms of industrial application.
Third, the hierarchy structure is an important factor because it improves structural stability and adaptability to surfaces with various roughnesses. However, most studies that mimic the hierarchy of the adhesives tend to produce no net benefit because of manufacturing defects. Various molding techniques, including soft lithography (Jeong et al., 2009a), porous membrane base molding (Kustandi et al., 2007; Bhushan and Lee, 2012), and dip transfer (Murphy et al., 2009), have been applied to hierarchical structures, whereas the dramatic change in geometries between micro-and nanostructures produces concentrated stress in the joints and impedes demolding with reduced yields (Chan-Park et al., 2005). Rohrig et al. introduced a laser printing-based bottom-up approach to fabricate hierarchical structures, whereas the low resolution of laser printing resulted in insufficient adhesion performance (Rohrig et al., 2012). To solve manufacturing problems, various approaches, such as geometrical optimizations (Chan-Park et al., 2005), chemical modifications (Otto et al., 2004; Cortese et al., 2008), and advanced manufacturing methods with high precision (Zhang et al., 2010; Park et al., 2014; Wang et al., 2019a), are required.
Several efforts have been made to commercialize bioinspired dry adhesives (Nanogriptech®, Geckskin®, and Gecko® Nanoplast®). In particular, continuous fabrication techniques based on a roll-to-roll process have been successfully applied to the large-scale fabrication of bioinspired dry adhesives (Sameoto and Ferguson, 2014; Yi et al., 2014; Lee et al., 2018; Yu et al., 2019). Despite these efforts, the complex microstructural features (e.g., suction cups, mushrooms with angled tips) (Wang et al., 2019b) or additional chemical treatments (Lee et al., 2007; Zhao et al., 2017) impede the fabrication process and lower yields in continuous manufacturing, which need to be overcome for the widespread use of bioinspired adhesives. We expect that these limitations can be overcome in the near future through multidisciplinary studies on functional materials, optimal structural design, and precise manufacturing techniques, enabling more versatile uses of bioinspired adhesives in various industries, including precision manufacturing, biomedical devices, and flexible electronics.
Author Contributions
All authors participated fully to the data acquisition, analysis, manuscript writing, and contributed to preparing the manuscript.
Funding
This work was supported by the National Research Foundation of Korea (NRF) (2021R1A2C3006297) and Korea Electric Power Corporation (R19XO01-26). The authors declare that the funder Korea Electric Power Corporation was not involved in the study design, collection, analysis, interpretation of data, the writing of this article or the decision to submit it for publication.
Conflict of Interest
The authors declare that the research was conducted in the absence of any commercial or financial relationships or otherwise that could be perceived as a potential conflict of interest.
References
Amador, G. J., Endlein, T., and Sitti, M. (2017). Soiled adhesive pads shear clean by slipping: a robust self-cleaning mechanism in climbing beetles. J. R. Soc. Interface 14:20170134. doi: 10.1098/rsif.2017.0134
Ameri, S. K., Ho, R., Jang, H. W., Tao, L., Wang, Y. H., Wang, L., et al. (2017). Graphene electronic tattoo sensors. ACS Nano 11, 7634–7641. doi: 10.1021/acsnano.7b02182
An, J. N., Le, T. S. D., Huang, Y., Zhan, Z. Y., Li, Y., Zheng, L. X., et al. (2017). All-graphene-based highly flexible noncontact electronic skin. ACS Appl. Mater. Interfaces 9, 44593–44601. doi: 10.1021/acsami.7b13701
Arzt, E., Gorb, S., and Spolenak, R. (2003). From micro to nano contacts in biological attachment devices. Proc. Natl. Acad. Sci. U. S. A. 100, 10603–10606. doi: 10.1073/pnas.1534701100
Autumn, K., Liang, Y. A., Hsieh, S. T., Zesch, W., Chan, W. P., Kenny, T. W., et al. (2000). Adhesive force of a single gecko foot-hair. Nature 405, 681–685. doi: 10.1038/35015073
Autumn, K., Majidi, C., Groff, R. E., Dittmore, A., and Fearing, R. (2006). Effective elastic modulus of isolated gecko setal arrays. J. Exp. Biol. 209, 3558–3568. doi: 10.1242/jeb.02469
Autumn, K., Sitti, M., Liang, Y. C. A., Peattie, A. M., Hansen, W. R., Sponberg, S., et al. (2002). Evidence for van der Waals adhesion in gecko setae. Proc. Natl. Acad. Sci. U. S. A. 99, 12252–12256. doi: 10.1073/pnas.192252799
Bae, W. G., Kim, D., Kwak, M. K., Ha, L., Kang, S. M., and Suh, K. Y. (2013). Enhanced skin adhesive patch with modulus-tunable composite micropillars. Adv. Healthc. Mater. 2, 109–113. doi: 10.1002/adhm.201200098
Bae, W. G., Kim, H. N., Kim, D., Park, S. H., Jeong, H. E., and Suh, K. Y. (2014). 25th anniversary article: scalable multiscale patterned structures inspired by nature: the role of hierarchy. Adv. Mater. 26, 675–699. doi: 10.1002/adma.201303412
Baik, S., Hwang, G. W., Jang, S., Jeong, S., Kim, K. H., Yang, T. H., et al. (2021). Bioinspired microsphere-embedded adhesive architectures for an electrothermally actuating transport device of dry/wet pliable surfaces. ACS Appl. Mater. Interfaces 13, 6930–6940. doi: 10.1021/acsami.0c21847
Baik, S., Kim, D. W., Park, Y., Lee, T. J., Ho Bhang, S., and Pang, C. (2017). A wet-tolerant adhesive patch inspired by protuberances in suction cups of octopi. Nature 546, 396–400. doi: 10.1038/nature22382
Baik, S., Kim, J., Lee, H. J., Lee, T. H., and Pang, C. (2018). Highly adaptable and biocompatible octopus-like adhesive patches with meniscus-controlled unfoldable 3D microtips for underwater surface and hairy skin. Adv. Sci. 5:1800100. doi: 10.1002/advs.201800100
Baik, S., Lee, H. J., Kim, D. W., Min, H., and Pang, C. (2019). Capillarity-enhanced organ-attachable adhesive with highly drainable wrinkled octopus-inspired architectures. ACS Appl. Mater. Interfaces 11, 25674–25681. doi: 10.1021/acsami.9b05511
Bhushan, B., and Lee, H. (2012). Fabrication and characterization of multi-level hierarchical surfaces. Faraday Discuss 156, 235–241. doi: 10.1039/c2fd00115b
Bhushan, B., and Sayer, R. A. (2007). Surface characterization and friction of a bio-inspired reversible adhesive tape. Microsyst. Technol. 13, 71–78. doi: 10.1007/s00542-006-0256-2
Bullock, J. M. R., and Federle, W. (2011). Beetle adhesive hairs differ in stiffness and stickiness: in vivo adhesion measurements on individual setae. Sci. Nat. 98, 381–387. doi: 10.1007/s00114-011-0781-4
Carbone, G., Pierro, E., and Gorb, S. N. (2011). Origin of the superior adhesive performance of mushroom-shaped microstructured surfaces. Soft Matter. 7, 5545–5552. doi: 10.1039/c0sm01482f
Chan-Park, M. B., Lam, Y. C., Laulia, P., and Joshi, S. C. (2005). Simulation and investigation of factors affecting high aspect ratio UV embossing. Langmuir 21, 2000–2007. doi: 10.1021/la035124e
Chen, H. W., Zhang, L. W., Zhang, D. Y., Zhang, P. F., and Han, Z. W. (2015). Bioinspired surface for surgical graspers based on the strong wet friction of tree frog toe pads. ACS Appl. Mater. Interfaces 7, 13987–13995. doi: 10.1021/acsami.5b03039
Chen, Y. C., and Yang, H. T. (2017). Octopus-inspired assembly of nanosucker arrays for dry/wet adhesion. ACS Nano 11, 5332–5338. doi: 10.1021/acsnano.7b00809
Chen, Y. P., Meng, J. X., Gu, Z., Wan, X. Z., Jiang, L., and Wang, S. T. (2020). Bioinspired multiscale wet adhesive surfaces: structures and controlled adhesion. Adv. Funct. Mater. 30:1905287. doi: 10.1002/adfm.201905287
Choi, M. K., Park, O. K., Choi, C., Qiao, S. T., Ghaffari, R., Kim, J., et al. (2016). Cephalopod-inspired miniaturized suction cups for smart medical skin. Adv. Healthc. Mater. 5, 80–87. doi: 10.1002/adhm.201500285
Chun, S., Son, W., Kim, D. W., Lee, J., Min, H., Jung, H., et al. (2019). Water-resistant and skin-adhesive wearable electronics using graphene fabric sensor with octopus-inspired microsuckers. ACS Appl. Mater. Interfaces 11, 16951–16957. doi: 10.1021/acsami.9b04206
Cortese, B., D'Amone, S., Manca, M., Viola, I., Cingolani, R., and Gigli, G. (2008). Superhydrophobicity due to the hierarchical scale roughness of PDMS surfaces. Langmuir 24, 2712–2718. doi: 10.1021/la702764x
Del Campo, A., Greiner, C., Alvarez, I., and Arzt, E. (2007a). Patterned surfaces with pillars with controlled 3D tip geometry mimicking bioattachment devices. Adv. Mater. 19, 1973–1977. doi: 10.1002/adma.200602476
Del Campo, A., Greiner, C., and Arzt, E. (2007b). Contact shape controls adhesion of bioinspired fibrillar surfaces. Langmuir 23, 10235–10243. doi: 10.1021/la7010502
Dirks, J. H., and Federle, W. (2011). Fluid-based adhesion in insects - principles and challenges. Soft Matter. 7, 11047–11053. doi: 10.1039/c1sm06269g
Drotlef, D. M., Amjadi, M., Yunusa, M., and Sitti, M. (2017). Bioinspired composite microfibers for skin adhesion and signal amplification of wearable sensors. Adv. Mater. 29:1701353. doi: 10.1002/adma.201701353
Drotlef, D. M., Stepien, L., Kappl, M., Barnes, W. J. P., Butt, H. J., and Del Campo, A. (2013). Insights into the adhesive mechanisms of tree frogs using artificial mimics. Adv. Funct. Mater. 23, 1137–1146. doi: 10.1002/adfm.201202024
Fuentes, C. A., Brughmans, G., Tran, L. Q. N., Dupont-Gillain, C., Verpoest, I., and Van Vuure, A. W. (2015). Mechanical behaviour and practical adhesion at a bamboo composite interface: physical adhesion and mechanical interlocking. Compos. Sci. Technol. 109, 40–47. doi: 10.1016/j.compscitech.2015.01.013
Geim, A. K., Dubonos, S. V., Grigorieva, I. V., Novoselov, K. S., Zhukov, A. A., and Shapoval, S. Y. (2003). Microfabricated adhesive mimicking gecko foot-hair. Nat. Mater. 2, 461–463. doi: 10.1038/nmat917
Gorb, E. V., Hosoda, N., Miksch, C., and Gorb, S. N. (2010). Slippery pores: anti-adhesive effect of nanoporous substrates on the beetle attachment system. J. R. Soc. Interface 7, 1571–1579. doi: 10.1098/rsif.2010.0081
Greiner, C., Del Campo, A., and Arzt, E. (2007). Adhesion of bioinspired micropatterned surfaces: effects of pillar radius, aspect ratio, and preload. Langmuir 23, 3495–3502. doi: 10.1021/la0633987
Gu, G. Y., Zou, J., Zhao, R. K., Zhao, X. H., and Zhu, X. Y. (2018). Soft wall-climbing robots. Sci. Robot. 3:eaat2874. doi: 10.1126/scirobotics.aat2874
Hansen, W. R., and Autumn, K. (2005). Evidence for self-cleaning in gecko setae. Proc. Natl. Acad. Sci. U. S. A. 102, 385–389. doi: 10.1073/pnas.0408304102
Heepe, L., Kovalev, A. E., Varenberg, M., Tuma, J., and Gorb, S. N. (2012). First mushroom-shaped adhesive microstructure: a review. Theor. Appl. Mech. Lett. 2:014008. doi: 10.1063/2.1201408
Hofman, A. H., van Hees, I. A., Yang, J., and Kamperman, M. (2018). Bioinspired underwater adhesives by using the supramolecular toolbox. Adv. Mater. 30:1704640. doi: 10.1002/adma.201704640
Hwang, I., Kim, H. N., Seong, M., Lee, S. H., Kang, M., Yi, H., et al. (2018). Multifunctional smart skin adhesive patches for advanced health care. Adv. Healthc. Mater. 7:1800275. doi: 10.1002/adhm.201800275
Hwang, I., Seong, M., Yi, H., Ko, H., Park, H. H., Yeo, J., et al. (2020). Low-resistant electrical and robust mechanical contacts of self-attachable flexible transparent electrodes with patternable circuits. Adv. Funct. Mater. 30:2000458. doi: 10.1002/adfm.202000458
Iturri, J., Xue, L. J., Kappl, M., Garcia-Fernandez, L., Barnes, W. J. P., Butt, H. J., et al. (2015). Torrent frog-inspired adhesives: attachment to flooded surfaces. Adv. Funct. Mater. 25, 1499–1505. doi: 10.1002/adfm.201403751
Iwasaki, H., Lefevre, F., Damian, D. D., Iwase, E., and Miyashita, S. (2020). Autonomous and reversible adhesion using elastomeric suction cups for in-vivo medical treatments. IEEE Robot. Autom. Lett. 5, 2015–2022. doi: 10.1109/LRA.2020.2970633
Jeong, H. E., Kwak, R., Khademhosseini, A., and Suh, K. Y. (2009a). UV-assisted capillary force lithography for engineering biomimetic multiscale hierarchical structures: from lotus leaf to gecko foot hairs. Nanoscale 1, 331–338. doi: 10.1039/b9nr00106a
Jeong, H. E., Lee, J. K., Kim, H. N., Moon, S. H., and Suh, K. Y. (2009b). A nontransferring dry adhesive with hierarchical polymer nanohairs. Proc. Natl. Acad. Sci. U. S. A. 106, 5639–5644. doi: 10.1073/pnas.0900323106
Jeong, H. E., Lee, S. H., Kim, P., and Suh, K. Y. (2006). Stretched polymer nanohairs by nanodrawing. Nano Lett. 6, 1508–1513. doi: 10.1021/nl061045m
Jiang, H., Hawkes, E. W., Fuller, C., Estrada, M. A., Suresh, S. A., Abcouwer, N., et al. (2017). A robotic device using gecko-inspired adhesives can grasp and manipulate large objects in microgravity. Sci. Robot. 2:eaan4545. doi: 10.1126/scirobotics.aan4545
Kim, S., and Sitti, M. (2006). Biologically inspired polymer microfibers with spatulate tips as repeatable fibrillar adhesives. Appl. Phys. Lett. 89:261911. doi: 10.1063/1.2424442
Kim, S., Spenko, M., Trujillo, S., Heyneman, B., Santos, D., and Cutkosky, M. R. (2008). Smooth vertical surface climbing with directional adhesion. IEEE Trans. Robot. 24, 65–74. doi: 10.1109/TRO.2007.909786
Kim, T., Park, J., Sohn, J., Cho, D., and Jeon, S. (2016). Bioinspired, highly stretchable, and conductive dry adhesives based on 1D−2D hybrid carbon nanocomposites for all-in-one ECG electrodes. ACS Nano 10, 4770–4778. doi: 10.1021/acsnano.6b01355
Kim, Y., Yang, C., Kim, Y., Gu, G. X., and Ryu, S. (2020). Designing an adhesive pillar shape with deep learning-based optimization. ACS Appl. Mater. Interfaces 12, 24458–24465. doi: 10.1021/acsami.0c04123
Ko, H., Seong, M., and Jeong, H. E. (2017a). A micropatterned elastomeric surface with enhanced frictional properties under wet conditions and its application. Soft Matter 13, 8419–8425. doi: 10.1039/C7SM01493G
Ko, H., Yi, H., and Jeong, H. E. (2017b). Wall and ceiling climbing quadruped robot with superior water repellency manufactured using 3D printing (UNIclimb). Int. J. Precis. Eng. Manuf. 4, 273–280. doi: 10.1007/s40684-017-0033-y
Kroner, E., and Arzt, E. (2012). Single macropillars as model systems for tilt angle dependent adhesion measurements. Int. J. Adhes. Adhes. 36, 32–38. doi: 10.1016/j.ijadhadh.2012.03.008
Kustandi, T. S., Samper, V. D., Ng, W. S., Chong, A. S., and Gao, H. (2007). Fabrication of a gecko-like hierarchical fibril array using a bonded porous alumina template. J. Micromech. Microeng. 17:N75. doi: 10.1088/0960-1317/17/10/N02
Kwak, M. K., Jeong, H. E., Bae, W. G., Jung, H. S., and Suh, K. Y. (2011a). Anisotropic adhesion properties of triangular-tip-shaped micropillars. Small 7, 2296–2300. doi: 10.1002/smll.201100455
Kwak, M. K., Jeong, H. E., and Suh, K. Y. (2011b). Rational design and enhanced biocompatibility of a dry adhesive medical skin patch. Adv. Mater. 23, 3949–3953. doi: 10.1002/adma.201101694
Kwak, M. K., Pang, C., Jeong, H. E., Kim, H. N., Yoon, H., Jung, H. S., et al. (2011c). Towards the next level of bioinspired dry adhesives: new designs and applications. Adv. Funct. Mater. 21, 3606–3616. doi: 10.1002/adfm.201100982
Langowski, J. K. A., Dodou, D., Kamperman, M., and van Leeuwen, J. L. (2018). Tree frog attachment: mechanisms, challenges, and perspectives. Front. Zool. 15:32. doi: 10.1186/s12983-018-0273-x
Lee, H., Lee, B. P., and Messersmith, P. B. (2007). A reversible wet/dry adhesive inspired by mussels and geckos. Nature 448, 338–341. doi: 10.1038/nature05968
Lee, H., Um, D. S., Lee, Y., Lim, S., Kim, H. J., and Ko, H. (2016). Octopus-inspired smart adhesive pads for transfer printing of semiconducting nanomembranes. Adv. Mater. 28, 7457–7465. doi: 10.1002/adma.201601407
Lee, J., and Fearing, R. S. (2008). Contact self-cleaning of synthetic gecko adhesive from polymer microfibers. Langmuir 24, 10587–10591. doi: 10.1021/la8021485
Lee, J. H., Fearing, R. S., and Komvopoulos, K. (2008). Directional adhesion of gecko-inspired angled microfiber arrays. Appl. Phys. Lett. 93:191910. doi: 10.1063/1.3006334
Lee, S. H., Song, H. W., Kang, B. S., and Kwak, M. K. (2019). Remora-inspired reversible adhesive for underwater applications. ACS Appl. Mater. Interfaces 11, 47571–47576. doi: 10.1021/acsami.9b16350
Lee, S. H., Yi, H., Park, C. W., Jeong, H. E., and Kwak, M. (2018). Continuous tip widening technique for roll-to-roll fabrication of dry adhesives. Coatings 8:349. doi: 10.3390/coatings8100349
Li, S., Tian, H. M., Shao, J. Y., Liu, H. R., Wang, D. R., and Zhang, W. T. (2020). Switchable adhesion for nonflat surfaces mimicking geckos' adhesive structures and toe muscles. ACS Appl. Mater. Interfaces 12, 39745–39755. doi: 10.1021/acsami.0c08686
Liu, J. F., Xu, L. S., Xu, J. J., Liu, L., Cheng, G. X., Chen, S. Q., et al. (2020). Analysis and optimization of the wall-climbing robot with an adsorption system and adhesive belts. Int. J. Adv. Robot. Syst. 17:1729881420926409. doi: 10.1177/1729881420926409
Liu, X. J., Liu, J., Wang, J. L., Wang, T., Jiang, Y., Hu, J. Q., et al. (2020). Bioinspired, microstructured silk fibroin adhesives for flexible skin sensors. ACS Appl. Mater. Interfaces 12, 5601–5609. doi: 10.1021/acsami.9b21197
Liu, Z. Y., Wang, X. T., Qi, D. P., Xu, C., Yu, J. C., Liu, Y. Q., et al. (2017). High-adhesion stretchable electrodes based on nanopile interlocking. Adv. Mater. 29:1603382. doi: 10.1002/adma.201603382
Ma, Y. F., Ma, S. H., Wu, Y., Pei, X. W., Gorb, S. N., Wang, Z. K., et al. (2018). Remote control over underwater dynamic attachment/detachment and locomotion. Adv. Mater. 30:1801595. doi: 10.1002/adma.201801595
Mahdavi, A., Ferreira, L., Sundback, C., Nichol, J. W., Chan, E. P., Carter, D. J. D., et al. (2008). A biodegradable and biocompatible gecko-inspired tissue adhesive. Proc. Natl. Acad. Sci. U. S. A. 105, 2307–2312. doi: 10.1073/pnas.0712117105
Mazzolai, B., Mondini, A., Tramacere, F., Riccomi, G., Sadeghi, A., Giordano, G., et al. (2019). Octopus-inspired soft arm with suction cups for enhanced grasping tasks in confined environments. Adv. Intell. Syst. 1:1900041. doi: 10.1002/aisy.201900041
Min, H., Jang, S., Kim, D., Kim, J., Baik, S., Chun, S., et al. (2020). Highly air/water-permeable hierarchical mesh architectures for stretchable underwater electronic skin patches. ACS Appl. Mater. Interfaces 12, 14425–14432. doi: 10.1021/acsami.9b23400
Mitchell, C. T., Dayan, C. B., Drotlef, D. M., Sitti, M., and Stark, A. Y. (2020). The effect of substrate wettability and modulus on gecko and gecko-inspired synthetic adhesion in variable temperature and humidity. Sci. Rep. 10, 1–9. doi: 10.1038/s41598-020-76484-6
Murphy, M. P., Kim, S., and Sitti, M. (2009). Enhanced adhesion by gecko-inspired hierarchical fibrillar adhesives. ACS Appl. Mater. Interfaces 1, 849–855. doi: 10.1021/am8002439
Niewiarowski, P. H., Stark, A. Y., and Dhinojwala, A. (2016). Sticking to the story: outstanding challenges in gecko-inspired adhesives. J. Exp. Biol. 219, 912–919. doi: 10.1242/jeb.080085
Nishimura, T., Mizushima, K., Suzuki, Y., Tsuji, T., and Watanabe, T. (2017). Variable-grasping-mode underactuated soft gripper with environmental contact-based operation. IEEE Robot. Autom. Lett. 2, 1164–1171. doi: 10.1109/LRA.2017.2662086
O'Brien, M., Mortell, D. J., Corbett, M. C., O'Higgins, R. M., and McCarthy, C. T. (2019). Tree frog attachment: mechanisms, challenges, and perspectives. Int. J. Adhes. Adhes. 95, 1–21.
Oh, D. K., Lee, S., Lee, S. H., Lee, W., Yeon, G., Lee, N., et al. (2019). Tailored nanopatterning by controlled continuous nanoinscribing with tunable shape, depth, and dimension. ACS Nano 13, 11194–11202. doi: 10.1021/acsnano.9b04221
Oh, J. H., Hong, S. Y., Park, H., Jin, S. W., Jeong, Y. R., Oh, S. Y., et al. (2018). Fabrication of high-sensitivity skin-attachable temperature sensors with bioinspired microstructured adhesive. ACS Appl. Mater. Interfaces 10, 7263–7270. doi: 10.1021/acsami.7b17727
Otto, M., Bender, M., Richter, F., Hadam, B., Kliem, T., Jede, R., et al. (2004). Reproducibility and homogeneity in step and repeat UV-nanoimprint lithography. Microelectron. Eng. 73, 152–156. doi: 10.1016/S0167-9317(04)00090-5
Ozaki, S., Mieda, K., Maegawa, S., and Nakano, K. (2020). Meso–macro coupled analysis of pressure-dependent friction of rubber. Front. Mech. Eng. 6:24. doi: 10.3389/fmech.2020.00024
Pan, F., Ye, S. X., Wang, R. X., She, W., Liu, J. P., Sun, Z. M., et al. (2020). Hydrogel networks as underwater contact adhesives for different surfaces. Mater. Horiz. 7, 2063–2070. doi: 10.1039/D0MH00176G
Pang, C., Koo, J. H., Nguyen, A., Caves, J. M., Kim, M. G., Chortos, A., et al. (2015). Highly skin-conformal microhairy sensor for pulse signal amplification. Adv. Mater. 27, 634–640. doi: 10.1002/adma.201403807
Park, H. W., Seo, H. S., Lee, J. H., and Shin, S. (2020). Adhesion improvement of the acrylic pressure-sensitive adhesive to low-surface-energy substrates using silicone urethane dimethacrylates. Eur. Polym. J. 137:109949. doi: 10.1016/j.eurpolymj.2020.109949
Park, J., Tahk, D., Ahn, C., Im, S. G., Choi, S. J., Suh, K. Y., et al. (2014). Conformal phase masks made of polyurethane acrylate with optimized elastic modulus for 3D nanopatterning. J. Mater. Chem. C 2, 2316–2322. doi: 10.1039/c3tc32194k
Qu, L. T., Dai, L. M., Stone, M., Xia, Z. H., and Wang, Z. L. (2008). Carbon nanotube arrays with strong shear binding-on and easy normal lifting-off. Science 322, 238–242. doi: 10.1126/science.1159503
Rohrig, M., Thiel, M., Worgull, M., and Holscher, H. (2012). 3D direct laser writing of nano-and microstructured hierarchical gecko-mimicking surfaces. Small 8, 3009–3015. doi: 10.1002/smll.201200308
Rong, Z. X., Zhou, Y. M., Chen, B. A., Robertson, J., Federle, W., Hofmann, S., et al. (2014). Bio-inspired hierarchical polymer fiber-carbon nanotube adhesives. Adv. Mater. 26, 1456–1461. doi: 10.1002/adma.201304601
Sameoto, D., and Ferguson, B. (2014). Robust large-area synthetic dry adhesives. J. Adhes. Sci. Technol. 28, 337–353. doi: 10.1080/01694243.2012.693802
Sandoval, J. A., Jadhav, S., Quan, H. C., Deheyn, D. D., and Tolley, M. T. (2019). Reversible adhesion to rough surfaces both in and out of water, inspired by the clingfish suction disc. Bioinspir. Biomim. 14:066016. doi: 10.1088/1748-3190/ab47d1
Sandoval, J. A., Sommers, J., Peddireddy, K. R., Robertson-Anderson, R. M., Tolley, M. T., and Deheyn, D. D. (2020). Toward bioinspired wet adhesives: lessons from assessing surface structures of the suction disc of intertidal clingfish. ACS Appl. Mater. Interfaces 12, 45460–45475. doi: 10.1021/acsami.0c10749
Seo, S., Lee, J., Kim, K. S., Ko, K. H., Lee, J. H., and Lee, J. (2014). Anisotropic adhesion of micropillars with spatula pads. ACS Appl. Mater. Interfaces 6, 1345–1350. doi: 10.1021/am4044135
Seo, T., and Sitti, M. (2013). Tank-like module-based climbing robot using passive compliant joints. IEEE ASME Trans. Mechatron. 18, 397–408. doi: 10.1109/TMECH.2011.2182617
Seong, M. H., Hwang, I., Lee, J., and Jeong, H. E. (2020). A pressure-insensitive self-attachable flexible strain sensor with bioinspired adhesive and active CNT layers. Sensors 20:6965. doi: 10.3390/s20236965
Sethi, S., Ge, L., Ci, L., Ajayan, P. M., and Dhinojwala, A. (2008). Gecko-inspired carbon nanotube-based self-cleaning adhesives. Nano Lett. 8, 822–825. doi: 10.1021/nl0727765
Shahsavan, H., Salili, S. M., Jakli, A., and Zhao, B. X. (2017). Thermally active liquid crystal network gripper mimicking the self-peeling of gecko toe pads. Adv. Mater. 29:1604021. doi: 10.1002/adma.201604021
Sinatra, N. R., Teeple, C. B., Vogt, D. M., Parker, K. K., Gruber, D. F., and Wood, R. J. (2019). Ultragentle manipulation of delicate structures using a soft robotic gripper. Sci. Robot. 4:eaax5425. doi: 10.1126/scirobotics.aax5425
Soltannia, B., and Sameoto, D. (2014). Strong, reversible underwater adhesion via gecko-inspired hydrophobic fibers. ACS Appl. Mater. Interfaces 6, 21995–22003. doi: 10.1021/am5075375
Song, S., Drotlef, D. M., Majidi, C., and Sitti, M. (2017). Controllable load sharing for soft adhesive interfaces on three-dimensional surfaces. Proc. Natl. Acad. Sci. U. S. A. 114, E4344–E4353. doi: 10.1073/pnas.1620344114
Song, S., and Sitti, M. (2014). Soft grippers using micro-fibrillar adhesives for transfer printing. Adv. Mater. 26, 4901–4906. doi: 10.1002/adma.201400630
Spinner, M., Gorb, S. N., and Westhoff, G. (2013). Diversity of functional microornamentation in slithering geckos Lialis (Pygopodidae). Proc. R. Soc. B 280:20132160. doi: 10.1098/rspb.2013.2160
Stark, A. Y., McClung, B., Niewiarowski, P. H., and Dhinojwala, A. (2014). Reduction of water surface tension significantly impacts gecko adhesion underwater. Integr. Comp. Biol. 54, 1026–1033. doi: 10.1093/icb/icu066
Stark, A. Y., and Mitchell, C. T. (2019). Stick or slip: adhesive performance of geckos and gecko-inspired synthetics in wet environments. Integr. Comp. Biol. 59, 214–226. doi: 10.1093/icb/icz008
Stauffer, F., Thielen, M., Sauter, C., Chardonnens, S., Bachmann, S., Tybrandt, K., et al. (2018). Skin conformal polymer electrodes for clinical ECG and EEG recordings. Adv. Healthc. Mater. 7:1700994. doi: 10.1002/adhm.201700994
Tai, K., El-Sayed, A.-R., Shahriari, M., Biglarbegian, M., and Mahmud, S. (2016). State of the art robotic grippers and applications. Robotics 5, 11. doi: 10.3390/robotics5020011
Tang, T. F., Hou, X. Y., Xiao, Y. N., Su, Y. L., Shi, Y. T., and Rao, X. S. (2019). Research on motion characteristics of space truss-crawling robot. Int. J. Adv. Robot. Syst. 16:1729881418821578. doi: 10.1177/1729881418821578
Tian, H. M., Liu, H. R., Shao, J. Y., Li, S., Li, X. M., and Chen, X. M. (2020). An electrically active gecko-effect soft gripper under a low voltage by mimicking gecko's adhesive structures and toe muscles. Soft Matter 16, 5599–5608. doi: 10.1039/D0SM00787K
Tramacere, F., Appel, E., Mazzolai, B., and Gorb, S. N. (2014). Hairy suckers: the surface microstructure and its possible functional significance in the octopus vulgaris sucker. Beilstein J. Nanotechnol. 5, 561–565. doi: 10.3762/bjnano.5.66
Tramacere, F., Beccai, L., Kuba, M., Gozzi, A., Bifone, A., and Mazzolai, B. (2013). The morphology and adhesion mechanism of octopus vulgaris suckers. PLoS ONE 8:e65074. doi: 10.1371/journal.pone.0065074
Tramacere, F., Pugno, N. M., Kuba, M. J., and Mazzolai, B. (2015). Unveiling the morphology of the acetabulum in octopus suckers and its role in attachment. Interface Focus 5:20140050. doi: 10.1098/rsfs.2014.0050
Varenberg, M., Pugno, N. M., and Gorb, S. N. (2010). Spatulate structures in biological fibrillar adhesion. Soft Matter 6, 3269–3272. doi: 10.1039/c003207g
Wainwright, D. K., Kleinteich, T., Kleinteich, A., Gorb, S. N., and Summers, A. P. (2013). Stick tight: suction adhesion on irregular surfaces in the northern clingfish. Biol. Lett. 9:20130234. doi: 10.1098/rsbl.2013.0234
Wang, C. H., Shao, J. Y., Lai, D. S., Tian, H. M., and Li, X. M. (2019). Suspended-template electric-assisted nanoimprinting for hierarchical micro-nanostructures on a fragile substrate. ACS Nano 13, 10333–10342. doi: 10.1021/acsnano.9b04031
Wang, L., Ha, K.-H., Rodin, G. J., Liechti, K. M., and Lu, N. (2020). Mechanics of crater-enabled soft dry adhesives: a review. Front. Mech. Eng. 6:601510. doi: 10.3389/fmech.2020.601510
Wang, X., Tan, D., Hu, S. Q., Li, Q., Yang, B. S., Shi, Z. K., et al. (2019). Reversible adhesion via light-regulated conformations of rubber chains. ACS Appl. Mater. Interfaces 11, 46337–46343. doi: 10.1021/acsami.9b14940
Wang, Y., Kang, V., Federle, W., Arzt, E., and Hensel, R. (2020). Switchable underwater adhesion by deformable cupped microstructures. Adv. Mater. Interfaces 7:2001269. doi: 10.1002/admi.202001269
Wang, Y., Kim, J. C., Wu, R. J., Martinez, J., Song, X. J., Yang, J., et al. (2019a). Van der Waals contacts between three-dimensional metals and two-dimensional semiconductors. Nature 568, 70–74. doi: 10.1038/s41586-019-1052-3
Wang, Y., Rang, V., Arzt, E., Federle, W., and Hensel, R. (2019b). Strong wet and dry adhesion by cupped microstructures. ACS Appl. Mater. Interfaces 11, 26483–26490. doi: 10.1021/acsami.9b07969
Wang, Y. P., Yang, X. B., Chen, Y. F., Wainwright, D. K., Kenaley, C. P., Gong, Z. Y., et al. (2017). A biorobotic adhesive disc for underwater hitchhiking inspired by the remora suckerfish. Sci. Robot. 2:eaan8072. doi: 10.1126/scirobotics.aan8072
Wang, Z. Y., Wang, Z. Y., Dai, Z. D., and Gorb, S. N. (2018). Bio-inspired adhesive footpad for legged robot climbing under reduced gravity: multiple toes facilitate stable attachment. Appl. Sci. 8:114. doi: 10.3390/app8010114
Wasay, A., and Sameoto, D. (2015). Gecko gaskets for self-sealing and high-strength reversible bonding of microfluidics. Lab Chip 15, 2749–2753. doi: 10.1039/C5LC00342C
Wi, J. S., Lee, S., Lee, S. H., Oh, D. K., Lee, K. T., Park, I., et al. (2017). Facile three-dimensional nanoarchitecturing of double-bent gold strips on roll-to-roll nanoimprinted transparent nanogratings for flexible and scalable plasmonic sensors. Nanoscale 9, 1398–1402. doi: 10.1039/C6NR08387K
Wu, H., Yang, G. G., Zhu, K. H., Liu, S. Y., Guo, W., Jiang, Z., et al. (2021). Materials, devices, and systems of on-skin electrodes for electrophysiological monitoring and human-machine interfaces. Adv. Sci. 8:2001938. doi: 10.1002/advs.202001938
Yi, H., Hwang, I., Lee, J. H., Lee, D., Lim, H., Tahk, D., et al. (2014). Continuous and scalable fabrication of bioinspired dry adhesives via a roll-to-roll process with modulated ultraviolet-curable resin. ACS Appl. Mater. Interfaces 6, 14590–14599. doi: 10.1021/am503901f
Yi, H., Kang, M., Kwak, M. K., and Jeong, H. E. (2016). Simple and reliable fabrication of bioinspired mushroom-shaped micropillars with precisely controlled tip geometries. ACS Appl. Mater. Interfaces 8, 22671–22678. doi: 10.1021/acsami.6b07337
Yi, H., Lee, S. H., Seong, M., Kwak, M. K., and Jeong, H. E. (2018). Bioinspired reversible hydrogel adhesives for wet and underwater surfaces. J. Mater. Chem. B 6, 8064–8070. doi: 10.1039/C8TB02598C
Yu, D., Beckelmann, D., Opsolder, M., Schafer, B., Moh, K., Hensel, R., et al. (2019). Roll-to-roll manufacturing of micropatterned adhesives by template compression. Materials 12:97. doi: 10.3390/ma12010097
Yu, Z. W., Shi, Y., Xie, J. X., Yang, S. X., and Dai, Z. D. (2018). Design and analysis of a bionic adhesive foot for gecko robot climbing the ceiling. Int. J. Robot. Autom. 33, 445–454. doi: 10.2316/Journal.206.2018.4.206-5412
Yuk, H., Zhang, T., Lin, S. T., Parada, G. A., and Zhao, X. H. (2016). Tough bonding of hydrogels to diverse non-porous surfaces. Nat. Mater. 15, 190–196. doi: 10.1038/nmat4463
Zandvakili, M., Honari, M. M., Mousavi, P., and Sameoto, D. (2017). Gecko-gaskets for multilayer, complex, and stretchable liquid metal microwave circuits and antennas. Adv. Mater. Technol. 2:1700144. doi: 10.1002/admt.201700144
Zhang, C., Zhou, Y., Han, H., Zheng, H., Xu, W., and Wang, Z. (2021). Dopamine-triggered hydrogels with high transparency, self-adhesion, and thermoresponse as skinlike sensors. ACS Nano 15, 1785–1794. doi: 10.1021/acsnano.0c09577
Zhang, L. W., Chen, H. W., Guo, Y. R., Wang, Y., Jiang, Y. G., Zhang, D. Y., et al. (2020). Micro-nano hierarchical structure enhanced strong wet friction surface inspired by tree frogs. Adv. Sci. 7:2001125. doi: 10.1002/advs.202001125
Zhang, P. C., Zhao, C. Q., Zhao, T. Y., Liu, M. J., and Jiang, L. (2019). Recent advances in bioinspired gel surfaces with superwettability and special adhesion. Adv. Sci. 6:1900996. doi: 10.1002/advs.201900996
Zhang, X., Wang, Y., Hensel, R., and Arzt, E. (2021). A design strategy for mushroom-shaped microfibrils with optimized dry adhesion: experiments and finite element analyses. J. Appl. Mech. 88:031015. doi: 10.1115/1.4049183
Zhang, Y., Lin, C. T., and Yang, S. (2010). Fabrication of hierarchical pillar arrays from thermoplastic and photosensitive SU-8. Small 6, 768–775. doi: 10.1002/smll.200901843
Zhao, B. X., Pesika, N., Rosenberg, K., Tian, Y., Zeng, H. B., McGuiggan, P., et al. (2008). Adhesion and friction force coupling of gecko setal arrays: implications for structured adhesive surfaces. Langmuir 24, 1517–1524. doi: 10.1021/la702126k
Zhao, Y. H., Wu, Y., Wang, L., Zhang, M. M., Chen, X., Liu, M. J., et al. (2017). Bio-inspired reversible underwater adhesive. Nat. Commun. 8, 1–8. doi: 10.1038/s41467-017-02387-2
Zhou, M., Tian, Y., Sameoto, D., Zhang, X., Meng, Y., and Wen, S. (2013). Controllable interfacial adhesion applied to transfer light and fragile objects by using gecko inspired mushroom-shaped pillar surface. ACS Appl. Mater. Interfaces 5, 10137–10144. doi: 10.1021/am402815x
Zhuo, S., Zhao, Z. G., Xie, Z. X., Hao, Y. F., Xu, Y. C., Zhao, T. Y., et al. (2020). Complex multiphase organohydrogels with programmable mechanics toward adaptive soft-matter machines. Sci. Adv. 6:eaax1464. doi: 10.1126/sciadv.aax1464
Keywords: bioinspired adhesive, dry adhesion, wet adhesion, gripper, robot, attachable sensor, skin patch
Citation: Kang M, Sun K, Seong M, Hwang I, Jang H, Park S, Choi G, Lee S-H, Kim J and Jeong HE (2021) Applications of Bioinspired Reversible Dry and Wet Adhesives: A Review. Front. Mech. Eng. 7:668262. doi: 10.3389/fmech.2021.668262
Received: 15 February 2021; Accepted: 31 March 2021;
Published: 07 May 2021.
Edited by:
Stanislav N. Gorb, University of Kiel, GermanyReviewed by:
Dan Sameoto, University of Alberta, CanadaLinmao Qian, Southwest Jiaotong University, China
Copyright © 2021 Kang, Sun, Seong, Hwang, Jang, Park, Choi, Lee, Kim and Jeong. This is an open-access article distributed under the terms of the Creative Commons Attribution License (CC BY). The use, distribution or reproduction in other forums is permitted, provided the original author(s) and the copyright owner(s) are credited and that the original publication in this journal is cited, in accordance with accepted academic practice. No use, distribution or reproduction is permitted which does not comply with these terms.
*Correspondence: Hoon Eui Jeong, aG9vbmVqZW9uZ0B1bmlzdC5hYy5rcg==
†These authors have contributed equally to this work and share first authorship