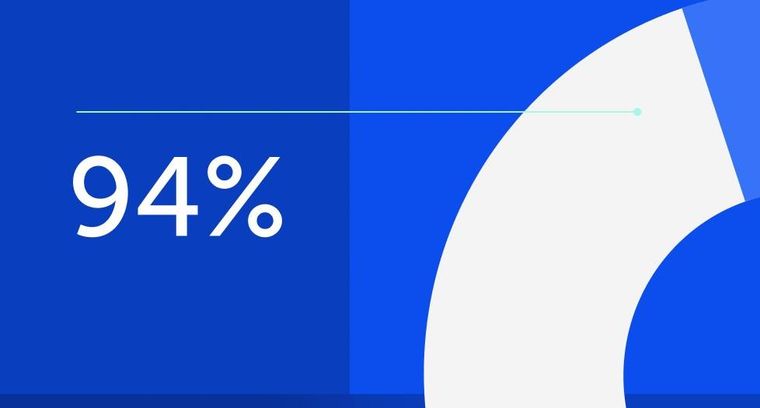
94% of researchers rate our articles as excellent or good
Learn more about the work of our research integrity team to safeguard the quality of each article we publish.
Find out more
ORIGINAL RESEARCH article
Front. Mech. Eng., 10 December 2020
Sec. Engine and Automotive Engineering
Volume 6 - 2020 | https://doi.org/10.3389/fmech.2020.545416
This article is part of the Research TopicAdvances in Compression Ignition Natural Gas – Diesel Dual Fuel EnginesView all 8 articles
Diesel fueled compression ignition engines are widely used in power generation and freight transport owing to their high fuel conversion efficiency and ability to operate reliably for long periods of time at high loads. However, such engines generate significant amounts of carbon dioxide (CO2), nitrogen oxides (NOx), and particulate matter (PM) emissions. One solution to reduce the CO2 and particulate matter emissions of diesel engines while maintaining their efficiency and reliability is natural gas (NG)-diesel dual-fuel combustion. In addition to methane emissions, the temperatures of the diesel injector tip and exhaust gas can also be concerns for dual-fuel engines at medium and high load operating conditions. In this study, a single cylinder NG-diesel dual-fuel research engine is operated at two high load conditions (75% and 100% load). NG fraction and diesel direct injection (DI) timing are two of the simplest control parameters for optimization of diesel engines converted to dual-fuel engines. In addition to studying the combined impact of these parameters on combustion and emissions performance, another unique aspect of this research is the measurement of the diesel injector tip temperature which can predict potential coking issues in dual-fuel engines. Results show that increasing NG fraction and advancing diesel direct injection timing can increase the injector tip temperature. With increasing NG fraction, while the methane emissions increase, the equivalent CO2 emissions (cumulative greenhouse gas effect of CO2 and CH4) of the engine decrease. Increasing NG fraction also improves the brake thermal efficiency of the engine though NOx emissions increase. By optimizing the combustion phasing through control of the DI timing, brake thermal efficiencies of the order of ∼42% can be achieved. At high loads, advanced diesel DI timings typically correspond to the higher maximum cylinder pressure, maximum pressure rise rate, brake thermal efficiency and NOx emissions, and lower soot, CO, and CO2-equivalent emissions.
As part of the Paris Agreement on climate change, Canada has committed to 30% abatement of its greenhouse gas (GHG) emissions from the 2005 levels by the year 2030 (Government of Canada, 2016). As means of achieving this target, Canada has also been developing the Clean Fuel Standard since 2016 with the aim to reduce GHG emissions through use of “lower carbon fuels, energy sources and technologies” (Government of Canada, 2019).
Diesel fueled compression ignition (CI) engines are widely used in power generation and freight transport owing to their high fuel conversion efficiency and ability to operate reliably for long periods of time at high loads. Owing to their ubiquity and extent of use, the carbon dioxide (CO2), nitrogen oxides (NOx) and particulate matter (PM) emissions from these engines can cause a significant adverse impact on the environment. Natural gas (NG) and renewable natural gas (RNG) are lower carbon and renewable fuels which generate about 20–30% and 80–90%, respectively, lower life-cycle CO2 emissions per unit of energy compared to diesel (Sharpe, 2019). One solution to reduce the CO2 and PM emissions of diesel engines while maintaining their efficiency and reliability is to replace diesel by NG using diesel-NG dual-fuel combustion technology. A possible configuration of an NG-diesel dual-fuel engine is intake port injection of compressed NG to form a homogenous air/NG mixture in the cylinder, and ignition of this mixture using a direct injection (DI) of diesel. In addition to offsetting diesel consumption, the potential advantages of such a configuration are lower PM emissions and limited engine modifications (Sahoo et al., 2009). Besides, such dual-fuel engines can operate as conventional diesel engines when NG is not available. One of the main disadvantages of NG-diesel dual-fuel engines is the higher methane emissions in comparison to conventional diesel engines (Liu et al., 2013; Guo et al., 2015). The global warming potential of methane over 100 years is 25 times that of CO2 (United States Environmental Protection Agency, 2020). Moreover, methane is difficult to oxidize effectively in the exhaust after-treatment (EAT) system (Osman, 2016; Gärtner et al., 2018). Methane emissions can therefore offset the advantage of lower CO2 emissions of the dual-fuel engines, especially at low load conditions. Advanced combustion strategies have been proposed that can minimize the methane emissions at low loads (Srinivasan et al., 2006; Guo et al., 2017; Yousefi et al., 2018). At medium to high load conditions, owing to the high fueling rate and higher temperatures which result in higher flame propagation speed, methane emissions are much lower than that at low load conditions, but they may still be greater than those of diesel engines (Papagiannakis and Hountalas, 2003). The main sources of these methane emissions at medium to high load conditions are crevice regions (Yousefi et al., 2019).
NG-diesel dual-fuel engines have been studied extensively over the years. There are many examples in literature that have summarized the fundamental performance of such dual-fuel engines (Karim, 1980; Wagemakers and Leermakers, 2012; Wei and Geng, 2016). There have also been researches on the effect of the injection parameters of NG and diesel of dual-fuel engines with the aim to improve engine efficiency and reduce methane emissions (Figer et al., 2014; Yang et al., 2015; Guo et al., 2017). Increasing the NG fraction in the total fuel energy input, especially at low and intermediate loads, can cause the brake thermal efficiency (BTE) to decrease and the carbon monoxide and methane emissions to increase (Papagiannakis et al., 2010; Imran et al., 2014). Increasing the NG fraction also tends to cause higher maximum pressure rise rate and lower maximum combustion pressure (Sahoo et al., 2009). However, at all engine loads and speeds, increasing the NG fraction tends to decrease NOx and soot emissions (Papagiannakis et al., 2010). The reduced NOx emissions with increased NG fraction can be caused by the increase in the higher specific heat capacity of the NG-air gas mixture and the lower maximum combustion pressure (Imran et al., 2014). One way to counter the reduced efficiency associated with higher NG fraction is to advance the timing of the diesel injection and increase the diesel injection pressure (Sahoo et al., 2009; Yang et al., 2015). However, this is accompanied by an increase in the NOx emissions and maximum combustion pressure and pressure rise rate (Sahoo et al., 2009). Therefore, there exists a trade-off between NOx-methane emissions for dual-fuel combustion (Wei and Geng, 2016). Additionally, there is an insignificant effect of NG injection timing on combustion performance and emissions at the advanced diesel injection timings (Yang et al., 2015).
The authors’ laboratory has previously studied pollutant emissions from dual-fuel engines including the pollutant formation mechanisms (Guo et al., 2017; Li et al., 2018). The present work builds on the previous research by studying the effect of increasing NG fraction and DI timing (of diesel) on engine performance and exhaust emissions at high load-low speed operating conditions. Potential application of such research is the conversion of existing diesel engines to dual-fuel engines in which the diesel DI timing and NG fraction can be the simplest control parameters for optimization without extensive engine hardware modification. An additional and unique metric deployed in this research is the injector tip temperature. Dual-fuel engines with the capability to operate in diesel-only mode tend to use the stock diesel injectors. When operating in dual-fuel mode, the diesel flow rate through the injector may be significantly reduced. Since the diesel also functions as a coolant to reduce the injector tip temperature, the reduced diesel flow rate may cause over-heating and potential coking inside the injector nozzles. This can disrupt the diesel injection and adversely affect the performance of the engine. Past investigations have found that injector coking problems increased when the injector tip temperature exceeded 300°C (Argueyrolles et al., 2007). Research on injector tip temperature for NG-diesel dual-fuel engines is limited. Königsson et al. found that increasing NG fraction caused the injector tip temperature to increase (Königsson et al., 2012). The authors’ laboratory conducted research on injector tip temperature at a constant NG fraction of 75% (Guo and Liko, 2018). This study furthers the analysis of injector tip temperature at different NG fractions with the goal to determine if the 300°C threshold can be reached in high load dual-fuel operation. Based on the authors’ search, this reported work is unique in its representation of the correlations between NG fraction, diesel DI timing, and injector tip temperature.
In this paper, two high load conditions—75% and 100% load are investigated. The two main variables are the NG fraction and the diesel DI timing of the diesel injection. Combustion performance, injector tip temperature and exhaust emissions are evaluated. The paper is organized as follows. Experimental setup and procedure as well as test conditions are described in Experimental Setup and Methods, followed by the discussion of results in Results and Discussion which consists of three sub-sections describing the combustion performance, injector tip temperature and exhaust emissions. The main conclusions of this research are presented in Conclusions.
This section is organized into two sub-sections. The first sub-section on experimental setup describes the testing system in detail. The second sub-section describes the experimental procedure and conditions, including calculation methods, test parameters and hardware constraints.
The research was performed on a single cylinder research engine. The setup consisted of a Caterpillar 3401 heavy-duty, four-stroke diesel engine coupled with a 131 kW eddy current dynamometer. The specifications of the engine are given in Table 1 and the schematic of the experimental setup is shown in Figure 1. A DC electric motor was used for starting and motoring of the engine.
The test setup also included a gas injection manifold in-line and immediately upstream of the intake port of the engine. Compressed NG was supplied by the local utility provider (Enbridge, Inc.) through their pipeline infrastructure into the test cell directly and a pressure regulator was used to maintain the injection pressure. A Bronkhorst mass flow meter was used to measure the flow rate of NG into the engine. Downstream of the flow meter and upstream of the gas injection manifold, a gas chamber was used to dampen any pressure pulses in the flow. The gas injection manifold consisted of eight gas fuel solenoid injectors (model Gs60 manufactured by Alternative Fuel Systems (AFS) Incorporated) which were individually controlled to inject precise quantities of NG into the intake charge of the engine. Since the composition of NG in the supply line may vary, the NG composition was determined before the tests using an Ametek Model 292B BTU Analyzer. The result is shown in Table 1. A custom diesel common rail DI system consisting of a Ganser six-hole solenoid injector and a high pressure fuel pump operated independent of the engine was used to deliver diesel to the engine. The diesel injector had a K-type thermocouple mounted into the sidewall to measure the injector tip temperature. The location of this thermocouple with respect to the nozzle is shown in Figure 2. The properties of the Canadian ultra-low-sulphur diesel (ULSD) used in this study are listed in Table 1. The diesel flow rate was measured with a Bronkhorst flow meter. The diesel and NG fueling were controlled by National Instruments (NI) hardware and LabVIEW based software (Stand-alone Direct Injector Drive System, Drivven Inc.). The hardware consisted of NI PXI-1031 chassis with NI PXI-8184 embedded controller, NI cRIO-9151 expansion chassis, and NI 7813R RIO injector driver card (for the diesel injector). The PXI-8184 controlled two four-channel AFS Injector Driver modules to drive the eight gas injectors.
The engine was aspirated with a conditioned air supply system with independent control of air pressure (oil-free air compressor and pressure regulators) and in-line intake heating. The air flow rate was measured with a thermal wire-type mass flowmeter manufactured by Sierra Instruments Inc. Intake and exhaust surge tanks were installed in the intake loop and the exhaust loop to dampen pressure waves in the system. An electro-pneumatic back pressure valve was used to simulate back pressure from the turbocharger. The lubricating oil and engine coolant conditioning systems were also operated independent of the engine with both oil and coolant temperatures maintained at 85°C.
CAI 600 series gas analyzers were used to determine the concentrations of CO, CO2, CH4, total HC, O2, and NOx in the engine exhaust. An AVL 415S smoke meter was used to determine the soot emissions. The filter smoke number (FSN) output of the smoke meter was converted to mass concentration (msoot in mg/m3) using Eq. 1 (Christian et al., 1993).
Additional instrumentation of the engine included the water-cooled, flush-mounted Kistler 6041A pressure transducer for measuring cylinder pressure and an AVL 365 series crank angle encoder. The outputs of the pressure transducer and the encoder were processed using AVL IndiModule combustion analysis system. Engine load and speed were controlled through the AVL Digalog Testmate system. Thermocouples were mounted at multiple locations in the test cell to monitor temperature. The test cell was also equipped with an exhaust gas recirculation (EGR) loop though it was not used in this research. Further details of the test setup are described in Guo and Liko (2018).
In NG-diesel dual-fuel engines, a primary parameter is the NG fraction (denoted by “
where, “m” and “LHV” were the mass flow rate (kg/s) and lower heating value (MJ/kg), respectively, and the subscripts “NG” and “D” represented natural gas and diesel, respectively.
The cylinder pressure data was stored for 100 consecutive engine cycles at a resolution of 0.2 crank angle degree (CAD). This data was used to calculate the net heat release rate (“HRRnet” in J/CAD) using Eq. 3.
In Eq. 3, “γ” was the ratio of the specific heat at constant pressure to the specific heat at constant volume and was calculated as a function of the in-cylinder gas temperature and composition, “p” was the in-cylinder pressure (Pa), “V” was the cylinder volume (m3) and “θ” was the crank angle (CAD). The heat release analysis was used to calculate the combustion timing values such as start of combustion (denoted by “CA10”), combustion phasing (denoted by “CA50”) and end of combustion (denoted by “CA90”). CA10, CA50, and CA90 corresponded to the specific crank angles at which 10%, 50% and 90%, respectively, of the total heat release occurred. Combustion duration was denoted by CA10-90.
The brake thermal efficiency (BTE) was used as a measure of the engine efficiency. It was expressed as a percentage and calculated using Eq. 4. In Eq. 4, “Powerbrake” was the brake power of the engine measured by the dynamometer (kW), “LHVf” was the lower heating value of the NG-diesel fuel combination (kJ/kg), and “
The experiments consisted of detailed investigation of combustion performance at two typical high load conditions—12.86 and 17.65 bar brake mean effective pressure (BMEP) at engine speeds of 1,010 and 1,120 rpm respectively corresponding to 75% and 100% load respectively. These choices were based on a previous study in which the highest injector tip temperatures had been observed between 75% and 100% load especially at low engine speeds of ∼1,000 rpm albeit at a fixed NG fraction of 75% (Guo and Liko, 2018). The lower engine speeds were consistent with the trend of downspeeding of heavy-duty engines especially in transportation applications in the interest of increasing fuel efficiency. While the original intention was to operate the engine at ∼1,000 rpm for the 100% load condition as well, in the interest of maintaining the load and stability over varying NG fractions and DI timings, the engine speed had to be increased to 1,120 rpm. The experimental conditions are listed in Table 2. The two variables for this stage of experiments were
All testing was conducted at steady state conditions without EGR. There are two main reasons for this. First, the purpose of this research was to isolate the effects of NG fraction and diesel DI timing which would be complicated by the profound effects of EGR on the combustion. Second, EGR control would typically be outside the scope of a simple conversion of a diesel engine to operate as an NG-diesel dual-fuel engine. However, the importance of EGR in optimizing NG-diesel combustion cannot be overstated and EGR effects have been evaluated in a separate study (Dev et al., 2020). The test procedure involved the following steps for each load condition. First, the engine motoring was started with the DC motor and a steady motoring speed of 600 rpm was maintained. Next, the diesel DI was initiated to fire the engine. Fueling rate was controlled to maintain the idle speed of 600 rpm and thereafter, the DC motor was disengaged. Subsequently, the engine load and speed were increased gradually to the target value using the dynamometer feedback. The engine was operated at the target load and speed for several minutes to reach steady conditions. Finally, the diesel DI timing was swept over a range. The limits of this range were based on the engine hardware. The timing advance limit was subject to constraints such as the peak pressure rise rate (<12 bar/CAD) and the peak cylinder pressure (<150 bar). The timing retard limit was constrained by the exhaust temperature (<600°C). For dual-fuel conditions, the diesel flow rate was gradually decreased and NG fueling rate was gradually increased to set the
This section is organized into three sub-sections. The combustion performance is described first, followed by the injector tip temperature and the emission results in the second and third sub-sections respectively.
The cylinder pressure and heat release rate traces for 75% of full load (BMEP = 12.86 bar) are shown in Figure 3 at the diesel DI timing of -18 CAD after top dead center (ATDC) and different NG fractions. At each NG fraction, there are two major peaks on the net heat release rate curve. At
At the full load condition (BMEP = 17.65 bar), owing to the hardware limitations of exhaust temperature and peak pressure, there were limited overlaps in the DI timing sweeps. Therefore, the pressure and heat release traces are shown at
The maximum cylinder pressure, exhaust temperature, CA50 and CA10–90 at 75% load are shown in Figure 5. This figure also highlights the constraints for advancing and retarding the DI timing explained in the previous section. For all
FIGURE 5. 75% load results–(A): Maximum cylinder pressure; (B): CA50; (C): Exhaust Temperature; (D): CA10–90.
With increasing
At the 100% load condition (Figure 6), the overall trends are similar to those at 75% load with one exception. For
FIGURE 6. 100% load results–(A): Maximum cylinder pressure; (B): CA50; (C): Exhaust Temperature; (D): CA10–90.
Advancing the DI timing can be advantageous in terms of increasing the BTE at both load levels (Figure 7). This is probably due to the optimization of the CA50. When the CA50 is too advanced, the energy release from the fuel combustion could be working against the engine compression. When the CA50 is too retarded, the energy release may be too late to derive useful mechanical work. Therefore, for
FIGURE 7. (A). BTE at 75% load; (B). BTE at 100% load; (C). Peak pressure rise rate at 75% load; (D). Peak pressure rise rate at 100% load.
The DI timing advance is subject to an additional hardware constraint of peak pressure rise rate (Figure 7). The peak pressure rise rate tends to increase with the advance in the CA50 either through the advance of DI timing or the increase of
The injector tip temperature at 75% and 100% loads are shown in Figure 8. The injector tip temperature is expected to be correlated to the average cylinder temperature during each cycle. However, the range of in-cylinder temperature during a cycle is usually quite wide. At 75% load, as the DI timing is advanced, the injector tip temperature increases probably due to the increased heat release near the TDC and therefore higher cylinder temperature. This is further supported by the fact that the injector tip temperature keeps increasing even though the BTE decreases with advancing DI timing, since the most advanced CA50 approaches the TDC. With increasing
At 100% load, data of injector tip temperature was not available for
For all test conditions, the injector tip temperatures were lower than the critical temperature for coking to occur inside the injector (Argueyrolles et al., 2007). The authors’ laboratory has previously conducted a detailed load-speed analysis of the injector tip temperature at
NOx, soot, CO and non-methane total hydrocarbons (HCs) are some of the primary regulated emissions for diesel engines used in the transportation sector. Figure 10 shows the brake specific emissions of the test cases at 75% load (denoted by “bs” prefix). NOx formation is primarily dependent on the in-cylinder temperature. Generally, at a particular NG fraction and DI timing, the maximum cylinder pressure and the maximum cylinder temperature would be directly correlated. It is noted from Figure 10 that NOx emissions generally decrease with retarding DI timing. This is because the CA50 is further away from the TDC, which in turn reduces the peak cylinder temperature. The NOx emissions of
Soot tends to form in the in-cylinder regions where the temperature is high and the air-fuel mixture is rich (Dec, 1997; Dec, 2009). When the DI timing is retarded, diesel is injected later in the compression stroke when the temperature is higher and time period available for the diesel to mix with the air/NG background and form a homogenous mixture is limited. This can cause the soot emissions to increase when the DI timing is retarded. With increasing
The CO emissions for the 75% load cases are shown in Figure 10 as well. CO typically originates from the incomplete combustion of hydrocarbons. With DI timing retard, the CO emissions increase. The BTE decreases with DI timing retardation. Therefore, as the fueling rate is increased to maintain the load, the relative air/fuel ratio decreases thereby reducing the oxygen availability (Figure 11). Moreover, a delayed DI timing can reduce the time available for diesel to mix with the air/NG background. These two factors can decrease the probability of CO oxidation. With increasing
The non-methane HC emissions are also shown in Figure 10. When the αNG is increased, the non-methane HC emissions increase. With increasing αNG, while the reactivity of the air/NG background mixture may increase, more HC molecules (from NG) may make their way into the crevice volumes and remain unburnt. When the DI timing is retarded, the non-methane HC emissions decrease. This may be due to the delayed combustion and higher temperatures during the expansion stroke which may enhance the combustion of the charge trapped in the crevices.
At 100% load, the emission trends are qualitatively similar to those at 75% load (Figure 12). There are other exceptions, however. The specific NOx emissions for 100% load cases are lower than the 75% load cases probably due to the retarded CA50 and to a small extent, the higher load. There is slight reduction in the NOx emissions for the dual-fuel cases in comparison to diesel. This could be due to the DI timing retardation necessary to limit the peak cylinder pressure which counters the reduction in CA10–90 as more NG is used. Soot emissions for the diesel case are less than 0.1 g/kWh, and for
While non-methane HC trends with increase in
One of the main objectives of developing diesel-NG dual-fuel engines is the reduction in GHG emissions. Figure 13 shows the methane emissions and CO2-equivalent emissions at 75% and 100% load. The trends are similar for both load levels with respect to DI timing and
FIGURE 13. (A). Methane emissions at 75% load; (B). Methane emissions at 100% load; (C). CO2-equivalent emissions at 75% load; (D). CO2-equivalent emissions at 100% load.
The CO2-equivalent emissions are calculated based on the CO2 and methane emissions (Figure 13). Methane is a more potent GHG than CO2, and a weightage of 25 is included in the CO2-equivalent calculation. Regardless of the higher methane emissions from dual-fuel cases, it is found that increasing
A study on the effects of DI timing and increasing NG fraction on diesel-NG dual-fuel combustion is conducted on a heavy-duty engine setup. Injector tip temperature is measured using a specially modified injector. Combustion performance and exhaust emissions are studied as well. Tests are conducted at 75% and 100% load at the lower range of engine speeds. The main conclusions of this research are
• Combustion phasing (CA50) is a very critical determinant of dual-fuel combustion performance at high engine loads. Increasing NG fraction can advance the CA50 and cause the combustion duration to decrease. Using an optimized CA50 obtained through control of the DI timing, brake thermal efficiencies of the order of ∼42% can be achieved.
• At high loads, advanced diesel DI timings typically correspond to the higher maximum cylinder pressure, maximum pressure rise rate, NOx emissions, lower soot and CO emissions, and higher BTE and lower CO2-equivalent emissions.
• With increasing NG fraction at a given DI timing, injector tip temperature increases. With advancing DI timing at a given NG fraction, injector tip temperature increases as well. At all the test conditions, injector tip temperature does not exceed 250°C. This is lower than the temperature threshold of 300°C beyond which injector coking issues could be exacerbated.
• CO emissions tend to decrease and HC emissions (methane and non-methane) tend to increase with increase in the NG fraction at a given DI timing.
• At high loads, increasing NG fraction can increase the methane emissions. However, the CO2-equivalent emissions decrease with increasing NG fraction.
The raw data supporting the conclusions of this article will be made available by the authors, without undue reservation.
SD processed the data, made the figures and wrote the manuscript. HG collected and processed the data, and also edited the manuscript. BL conducted the tests and organized the raw data.
Funding for this work was provided by Natural Resources Canada through the PERD Energy End Use (Project 3B03.003) and National Research Council of Canada through the internal Bioenergy program.
The authors declare that the research was conducted in the absence of any commercial or financial relationships that could be construed as a potential conflict of interest.
The Supplementary Material for this article can be found online at: https://www.frontiersin.org/articles/10.3389/fmech.2020.545416/full#supplementary-material.
Argueyrolles, B., Dehoux, S., Gastaldi, P., Grosjean, L., Levy, F., Michel, A., et al. (2007). Influence of injector nozzle design and cavitation on coking phenomenon. SAE Technical Paper No. 2007-01-1896.
Christian, V. R., Knopf, F., Jaschek, A., and Schindler, W. (1993). Eine neue Messmethodik der Bosch-Zahl mit erhohter Empfindlichkeit. Motortech Z. 54, 16–22.
Dec, J. E. (1997). A conceptual model of DL diesel combustion based on laser-sheet imaging. SAE Trans. 1319–1348. doi:10.4271/970873
Dec, J. E. (2009). Advanced compression-ignition engines—understanding the in-cylinder processes. Proc. Combust. Inst. 32 (2), 2727–2742. doi:10.1016/j.proci.2008.08.008
Dev, S., Guo, H., Lafrance, S., and Liko, B. (2020). An experimental study on the effect of exhaust gas recirculation on a natural gas-diesel dual-fuel engine. SAE Technical Paper 2020-01-0310.
Figer, G., Seitz, H. F., Graf, G., and Schreier, H. (2014). Commercial vehicle natural gas engines with diesel efficiency. MTZWorldwide. 75 (10), 10–15. doi:10.1007/s38313-014-0229-2
Grtner, U., Rabl, H.-P., and Zink, U. (2018). Exhaust gas aftertreatment of the future. MTZ Worldwide. 79, 70–75. doi:10.1007/s38313-018-0060-2
Government of Canada (2019). Clean fuel standard. Available at: https://www.canada.ca/en/environment-climate-change/services/managing-pollution/energy-production/fuel-regulations/clean-fuel-standard.html (Accessed March 07, 2020).
Government of Canada (2016). The Paris agreement. Available at: https://www.canada.ca/en/environment-climate-change/services/climate-change/paris-agreement.html (Accessed March 07, 2020).
Graves, B., Olfert, J., Patychuk, B., Dastanpour, R., and Rogak, S. (2015). Characterization of particulate matter morphology and volatility from a compression-ignition natural-gas direct-injection engine. Aerosol. Sci. Technol. 49 (8), 589–598. doi:10.1080/02786826.2015.1050482
Guo, H., and Liko, B. (2018). “Injector tip temperature and combustion performance of a natural gas-diesel dual fuel engine at medium and high load conditions,” in Proceedings of the ASME 2018 internal combustion engine division fall technical conference. American Society of Mechanical Engineers Digital Collection, San Diego, CA, November 2018.
Guo, H., Liko, B., and Neill, W. S. (2017). “Effect of diesel injection split on combustion and emissions performance of a natural gas–diesel dual fuel engine at a low load condition,” in Proceedings of the ASME 2017 internal combustion engine division fall technical conference. American Society of Mechanical Engineers Digital Collection, Seattle, WC, October 2017.
Guo, H., Liu, F., and Smallwood, G. J. (2005). A numerical study on NOx formation in laminar counterflow CH4/air triple flames. Combust. Flame. 143 (3), 282–298. doi:10.1016/j.combustflame.2005.06.004
Guo, H., Neill, W. S., and Liko, B. (2015). “An experimental investigation on the combustion and emissions performance of a natural gas–diesel dual fuel engine at low and medium loads,” in Proceedings of the ASME 2015 internal combustion engine division fall technical conference. American Society of Mechanical Engineers Digital Collection, Houston, TX, November 2015.
Imran, S., Emberson, D. R., Diez, A., Wen, D. S., Crookes, R. J., and Korakianitis, T. (2014). Natural gas fueled compression ignition engine performance and emissions maps with diesel and RME pilot fuels. Appl. Energy. 124, 354–365. doi:10.1016/j.apenergy.2014.02.067
Karim, G. A. (1980). A review of combustion processes in the dual fuel engine—the gas diesel engine. Prog. Energy Combust. Sci. 6 (3), 277–285. doi:10.1016/0360-1285(80)90019-2
Königsson, F., Stalhammar, P., and Angstrom, H. E. (2012). Controlling the injector tip temperature in a diesel dual fuel engine. SAE Technical Paper No. 2012-01-0826.
Li, Y., Li, H., and Guo, H. (2018). A numerical investigation on NO2 formation reaction pathway in a natural gas–diesel dual fuel engine. Combust. Flame. 190, 337–348. doi:10.1016/j.combustflame.2017.12.006
Liu, J., Yang, F., Wang, H., Ouyang, M., and Hao, S. (2013). Effects of pilot fuel quantity on the emissions characteristics of a CNG/diesel dual fuel engine with optimized pilot injection timing. Appl. Energy. 110, 201–206. doi:10.1016/j.apenergy.2013.03.024
Miller, J. A., and Bowman, C. T. (1989). Mechanism and modeling of nitrogen chemistry in combustion. Prog. Energy Combust. Sci. 15 (4), 287–338. doi:10.1016/0360-1285(89)90017-8
Momenimovahed, A., Liu, F., Thomson, K. A., Smallwood, G. J., and Guo, H. (2019). Effect of fuel composition on properties of particles emitted from a diesel–natural gas dual fuel engine. Int. J. Engine Res. doi:10.1177/1468087419846018
Mustafi, N. N., and Raine, R. R. (2009). Electron microscopy investigation of particulate matter from a dual fuel engine. Aerosol. Sci. Technol. 43 (9), 951–960. doi:10.1080/02786820903067210
Mustafi, N. N., Raine, R. R., and James, B. (2010). Characterization of exhaust particulates from a dual fuel engine by TGA, XPS, and Raman techniques. Aerosol. Sci. Technol. 44 (11), 954–963. doi:10.1080/02786826.2010.503668
Osman, A. I., Abu-Dahrieh, J. K., Laffir, F., Curtin, T., Thompson, J. M., and Rooney, D. W. (2016). A bimetallic catalyst on a dual component support for low temperature total methane oxidation. Appl. Catal. B Environ. 187, 408–418. doi:10.1016/j.apcatb.2016.01.017
Papagiannakis, R. G., and Hountalas, D. T. (2003). Experimental investigation concerning the effect of natural gas percentage on performance and emissions of a DI dual fuel diesel engine. Appl. Therm. Eng. 23 (3), 353–365. doi:10.1016/S1359-4311(02)00187-4
Papagiannakis, R. G., Rakopoulos, C. D., Hountalas, D. T., and Rakopoulos, D. C. (2010). Emission characteristics of high speed, dual fuel, compression ignition engine operating in a wide range of natural gas/diesel fuel proportions. Fuel. 89 (7), 1397–1406. doi:10.1016/j.fuel.2009.11.001
Sahoo, B. B., Sahoo, N., and Saha, U. K. (2009). Effect of engine parameters and type of gaseous fuel on the performance of dual-fuel gas diesel engines—a critical review. Renew. Sustain. Energy Rev. 13 (6-7), 1151–1184. doi:10.1016/j.rser.2008.08.003
Srinivasan, K. K., Krishnan, S. R., Singh, S., Midkiff, K. C., Bell, S. R., Gong, W., et al. (2006). The advanced injection low pilot ignited natural gas engine: a combustion analysis. ASME. J. Eng. Gas Turbines Power. 128 (1), 213–218. doi:10.1115/1.1915428
United States Environmental Protection Agency (2020). Overview of greenhouse gases. Available at: https://www.epa.gov/ghgemissions/overview-greenhouse-gases (Accessed February 15, 2020).
Wagemakers, A. M. L. M., and Leermakers, C. A. J. (2012). Review on the effects of dual-fuel operation, using diesel and gaseous fuels, on emissions and performance. SAE Technical Paper No. 2012-01-0869.
Wei, L., and Geng, P. (2016). A review on natural gas/diesel dual fuel combustion, emissions and performance. Fuel Process. Technol. 142, 264–278. doi:10.1016/j.fuproc.2015.09.018
Yang, B., Xi, C., Wei, X., Zeng, K., and Lai, M. C. (2015). Parametric investigation of natural gas port injection and diesel pilot injection on the combustion and emissions of a turbocharged common rail dual-fuel engine at low load. Appl. Energy. 143, 130–137. doi:10.1016/j.apenergy.2015.01.037
Yousefi, A., Guo, H., and Birouk, M. (2018). An experimental and numerical study on diesel injection split of a natural gas/diesel dual-fuel engine at a low engine load. Fuel. 212, 332–346. doi:10.1016/j.fuel.2017.10.053
Keywords: natural gas, dual-fuel, compression ignition, high load, greenhouse gas reduction
Citation: Dev S, Guo H and Liko B (2020) A Study on the High Load Operation of a Natural Gas-Diesel Dual-Fuel Engine. Front. Mech. Eng. 6:545416. doi: 10.3389/fmech.2020.545416
Received: 24 March 2020; Accepted: 17 November 2020;
Published: 10 December 2020.
Edited by:
Xiaosong Hu, Chongqing University, ChinaReviewed by:
Alpaslan Atmanli, National Defense University, TurkeyCopyright © 2020 Dev, Guo and Liko. This is an open-access article distributed under the terms of the Creative Commons Attribution License (CC BY). The use, distribution or reproduction in other forums is permitted, provided the original author(s) and the copyright owner(s) are credited and that the original publication in this journal is cited, in accordance with accepted academic practice. No use, distribution or reproduction is permitted which does not comply with these terms.
*Correspondence: Shouvik Dev, c2hvdXZpay5kZXZAbnJjLWNucmMuZ2MuY2E=
Disclaimer: All claims expressed in this article are solely those of the authors and do not necessarily represent those of their affiliated organizations, or those of the publisher, the editors and the reviewers. Any product that may be evaluated in this article or claim that may be made by its manufacturer is not guaranteed or endorsed by the publisher.
Research integrity at Frontiers
Learn more about the work of our research integrity team to safeguard the quality of each article we publish.