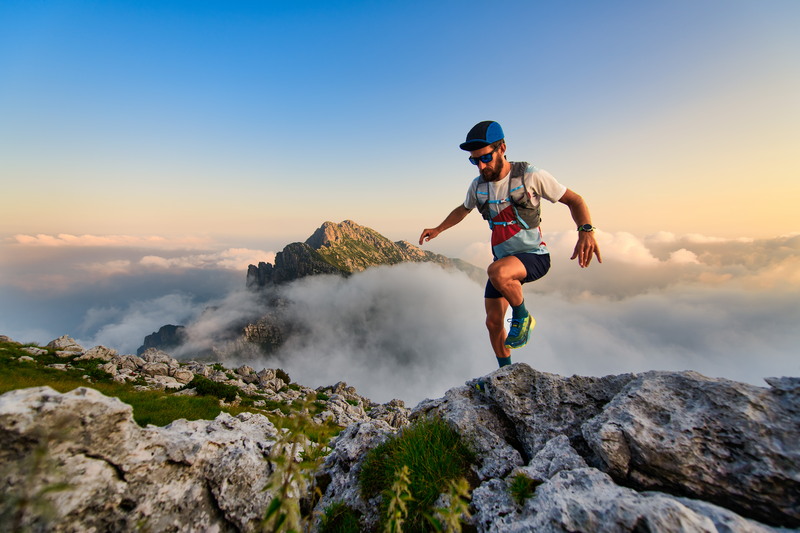
95% of researchers rate our articles as excellent or good
Learn more about the work of our research integrity team to safeguard the quality of each article we publish.
Find out more
REVIEW article
Front. Mech. Eng. , 07 July 2020
Sec. Micro- and Nanoelectromechanical Systems
Volume 6 - 2020 | https://doi.org/10.3389/fmech.2020.00042
This article is part of the Research Topic Nanofilms and Nanostructures for Energy Applications View all 6 articles
The growing demand for energy worldwide and the extensive use of fossil fuels have resulted in severe environmental problems such as air pollution and the accumulation of greenhouse gases in the atmosphere. In this scenario, both new energy sources and more efficient energy conversion processes have been deeply studied. Heterogeneous catalysis is currently widely used for hydrogen production due to its higher selectivity and conversion compared to other processes. Although the use of catalysts is fundamental for green chemistry, their production through traditional methods is less environmentally friendly. Nonetheless, in order to obtain more efficient supported metal catalysts, interest in using non-thermal plasma as a pretreatment or synthesis technique is increasing. Thus, the present article aims at summarizing and briefly discussing the relevant research results on this subject, elucidating the advantages and disadvantages of using non-thermal plasmas in the preparation of supported metal catalysts. Aspects such as morphology, the chemical composition of the catalytic surface, crystallographic phases, average size and dispersion of crystallites, specific surface area, and metal–support interaction have been analyzed. The use of plasma-assisted techniques contributes to the synthesis of supported metal catalysts with smaller, more dispersed, and strongly bonded active particles, resulting in higher catalytic activity, conversion rate, selectivity, and durability. In addition, plasma allows the synthesis of supported metal catalysts to be enhanced by reducing the process time, the use of hazardous substances, and the temperature required.
Supported metal catalysts consist of a metal, i.e., the catalytically active phase, dispersed on the surface of an inert support, usually a metal oxide, or a second active phase. There are several factors that justify the use of a supported catalyst rather than a “pure” catalyst, such as dispersion and stabilization of small particles of catalytically active phase and cost reduction (Bailie et al., 2001). Noble metals such as platinum (Pt) and rhodium (Rh) show remarkable activity in the catalytic conversion of methane (CH4), ethanol (C2H6O), propane (C3H8), and carbon dioxide (CO2) into synthesis gas (H2 and CO) (Ayabe et al., 2003; Silberova et al., 2005; Corthals et al., 2011). Other noble metals such as ruthenium (Ru), palladium (Pd), and silver (Ag) are also active (Fernández et al., 2016; Rouibah et al., 2017). However, the high cost and restricted availability of these metals are major barriers to their use, even in supported metal catalysts. Due to this, significant attention has been given to the use of supported metal catalysts containing non-noble transition metals, especially nickel (Ni) and cobalt (Co) (Corthals et al., 2011; Rouibah et al., 2017). Both noble and non-noble metals have the ability to break carbon–carbon bonds, which promotes the conversion of higher hydrocarbons into H2 (Hou et al., 2015). Also, the chosen support must be stable and resistant to chemical attack and temperature in order to present constant properties under the operating conditions. Highly porous supports are desirable for dispersion of the active phase, preventing agglomerations of particles responsible for catalysis and thus enabling catalyst reuse in successive cycles (Fernández et al., 2016; Aramouni et al., 2018).
Aiming at synthesizing more efficient supported metal catalysts, plasma technology has been investigated as an additional step in the conventional preparation methods. Plasma is basically an ionized gas, i.e., an electrically neutral environment at the macroscopic level, consisting of ions, electrons, and neutral atoms (Chapman, 1980). Thereby, a plasma can be considered thermal or non-thermal, as its temperature is determined by the average energy of species (Fridman, 2008). Thermal plasma is in a state of thermodynamic equilibrium, i.e., all species have the same temperature, which is the gas temperature. Non-thermal plasma is in a state of thermodynamic non-equilibrium in which the temperature of electrons is significantly higher than that of other species present in the plasma (Bogaerts et al., 2002; Lieberman and Lichtenberg, 2005). As a result, high concentrations of active and energetic species can be provided at room temperature, allowing increases in the efficiency of traditional chemical processes and the occurrence of reactions impossible to perform with conventional chemistry (Chen et al., 2017).
Miscellaneous non-thermal plasmas can be generated based on the system used, pressure, and geometry of the electrodes, as shown in Figure 1. Glow discharge, illustrated in Figure 1A, is a low-pressure discharge with negative and positive charges accelerated by AC, DC, or RF sources toward to the cathode and anode, respectively, generating many effects in the discharge volume and walls, such as gas ionization, gas dissociation, charge recombination, photoexcitation, sputtering, secondary electrons emission, etc. The corona discharge illustrated in Figure 1B consists of a non-homogeneous discharge that can be initiated at atmospheric pressure with a high voltage source and using non-identical electrode geometries, such as a flat plate and a pin (Taghvaei et al., 2017). The curvature of the wire tip creates the high electric field necessary to ionize the neutral species. The dielectric barrier discharge (DBD) depicted in Figure 1C is a two-electrode model with dielectric layers, such as quartz plates, inserted in the discharge gap. In this case, the system is usually powered by a high-voltage AC source. In DBD discharges, the dielectric covers at least one of the electrodes in order to limit the discharge current and prevent the transition of the discharge from corona to spark. Once the process begins, the charge builds up on the dielectric and forms an electric field opposite to that of the electrodes, generating micro-discharges at points where there is enough charge for a breakdown due to the interruption of the current flow for some nanoseconds. The duration of these pulses is related to pressure, gas properties, and applied dielectric material (Liu et al., 2016).
Figure 1. Simplified illustrative scheme of commonly used plasma discharges based on the voltage source and electrode geometry. (A) Glow discharge; (B) corona discharge; (C) dielectric barrier discharge (DBD).
The use of non-thermal plasma in the preparation of supported metal catalysts is a promising process that provides greater active phase dispersion, enhanced metal–support interaction, low-temperature activity, higher coke resistance, and stability in the reforming reactions (Cheng, 2008; Liu et al., 2016). In addition, this technique is generally simple and fast, reducing energy consumption and process costs (Liu et al., 2006, 2016; Cheng, 2008). Plasmas can be used at any stage of the supported metal catalyst production process or even for catalyst recovery after use (Wang et al., 2018b). In many cases, it is not easy to achieve high stability with great activity and selectivity withal. Thus, several exertions have been made to understand the fundamental issues in catalysis in order to develop new catalysts or new preparation methods and technologies that provide the desired particle size and structure for better catalytic performance (Liu et al., 2016).
Accordingly, this paper is organized as follows. Section Synergistic Effects Between Plasma and Heterogeneous Catalysis describes the pros and cons of the synergistic effects between plasma and heterogeneous catalysis in terms of reaction system configuration. Section Preparation Methods of Supported Metal Catalysts for Fuel Conversion explores and discusses conventional and alternative methods of supported metal catalyst preparation. Section Using Supported Metal Catalysts Prepared by Plasma-Assisted Processes in Fuel Conversion elucidates some of the advantages of using supported metal catalysts prepared by plasma-assisted processes in fuel conversion. Section Future Trends and Research Topics looks ahead to future trends and research topics regarding the supported metal catalyst production process and its characteristics. Finally, section Final Remarks consists of a final discussion about the subject matter of the present article.
Both catalysis and plasma have specific advantages in fuel conversion. Because of this, coupling plasma reactors, mainly non-thermal plasma, with heterogeneous catalysis systems is being explored as an alternative process for fuel reform. These techniques together can generate a synergistic effect, increasing hydrocarbon conversion rate and synthesis gas selectivity, preventing the occurrence of improper byproducts and reducing energy usage (Liu et al., 2017). The performance accomplished with “plasma catalysis” is superior to that obtained by the sum of the isolated use of plasma or catalysis, making this combination a promising process for H2 generation (Chen et al., 2008). Basically, there are four ways to combine plasma techniques with catalysis processes, as shown in Figure 2: (A) using non-thermal plasma for catalyst preparation or treatment, (B) adopting a one-stage hybrid system, (C) through a two-stage hybrid system with a plasma reactor located downstream of the catalysis reactor, or (D) through a two-stage hybrid system with a plasma reactor located upstream of the catalysis reactor (Chen et al., 2017).
Figure 2. Illustrative examples of (A) catalyst preparation or treatment using non-thermal plasma, (B) a one-stage hybrid system, (C) a two-stage hybrid system with a downstream plasma reactor, and (D) a two-stage hybrid system with an upstream plasma reactor.
The usage of non-thermal plasmas as a technique for catalyst preparation, shown in Figure 2A, unlike the other processes illustrated in Figure 2, is based on the treatment of catalysts prior to chemical reactions. In this way, the plasma itself is not involved directly in the fuel conversion. This method exhibits some interesting advantages compared to other plasma-catalysis processes, which will be discussed later in this topic. The one-stage hybrid system shown in Figure 2B consists of a catalyst immersed in a non-thermal plasma discharge reactor. In this case, due to the direct and constant interface between catalyst and plasma, two main types of interaction are induced. The first is the action of the plasma upon the catalyst, which decreases the temperature required for its activation because the temperature of electrons notably exceeds that of heavier species (gas temperature) and also generates intermediate species from reactants with greater adsorption potential (Du et al., 2015). This latter phenomenon is explained by the fact that plasma modifies the physicochemical characteristics of the catalyst surface, increasing the adsorption of molecules onto it due to electrostatic forces over a large surface area (Chen et al., 2017). As one example of the synergistic effects between plasma and catalyst, Hammer et al. (2004) reported that steam reforming of methane can be performed through plasma-catalysis using Ni-catalyst pellets at temperatures around 200°C. Huu et al. (2015) observed an improvement in CH4 conversion through plasma-catalyst coupling by a factor of 3 at 300°C and 1.4 at 350°C compared to conventional thermal catalytic experiments.
The second effect is the influence of the catalyst on plasma configuration, which may consist of changing the electric field distribution, temperature, and species present in the discharge (Huu et al., 2015; Chen et al., 2017). Therefore, the use of high-adsorption catalysts in pollutant abatement systems may increase retention time by increasing their localized concentration of key species. Thus, there is a greater probability of collision between active plasma species and pollutant molecules, increasing waste removal yield (Chen et al., 2017). It should also be emphasized that the use of thermal plasma in this system is not suitable, since the operating temperature (103−104°C) causes catalyst deactivation (Chung and Chang, 2016).
The plasma-catalyst interactions that occur in the one-stage hybrid systems are very complex and time-varying, making it more convenient to apply a two-stage hybrid system. In these systems, the plasma region is located downstream or upstream of the catalysis region, as shown in Figures 2C,D, respectively, and therefore, is responsible for the preprocessing or post-processing, respectively, of the fuel. In the first case, which is the most common configuration, plasma provides chemically reactive species due to the transformation of reactants into readily convertible intermediates, accelerating the reaction. Chao et al. (2008) achieved high hydrogen yield (89.9 %) and methane conversion (90.2%) via partial oxidation of methane by adding a plasma chamber before the catalysis reactor. On the other hand, when plasma is applied after catalysis, its function is to convert residual reactants from catalysis by eliminating undesired byproducts. Both thermal and non-thermal plasma can be assumed in the two-stage hybrid system (Huu et al., 2015; Chung and Chang, 2016).
The use of hybrid systems in automotive applications for onboard fuel conversion still faces technological barriers due to cost, size, weight, and complexity. So, in this scenario, the use of non-thermal plasma as a pretreatment or preparation technique for catalyst production, as shown in Figure 2A, more specifically supported metal catalysts, has been more intensively investigated (Lee et al., 2009; Rahemi et al., 2013a,b,c; Wang et al., 2018b). The development of catalysts with higher catalytic activity, selectivity, stability, and resistance to deactivation and sintering should consider the appropriate metal (active phase), support, promoter (if necessary), structure, and, consequently, preparation method (Jang et al., 2019). Characteristics such as metal–support interaction, carbon deposition rate, crystallite size, metal dispersion, and acid-basic properties are directly affected by the process used to obtain catalysts (He and Wang, 2015; Das et al., 2017).
The activity of supported metal catalysts in heterogeneous catalysis is strongly influenced by its chemical composition and crystalline structure and phases and the specific surface area of active sites (Liu et al., 2002). Therefore, the importance of the adopted preparation procedure can be highlighted with the ultimate goal of delivering catalytically active nanoparticles well-dispersed on a stable oxide support with strong interaction. Benrabaa et al. (2013) evaluated catalysts prepared by a sol-gel procedure, a hydrothermal method, and co-precipitation, proving that the preparation method strongly influences the catalytic performance of the catalyst, as very different conversion results were obtained due to different particle sizes and distributions. Although an expansion in the catalyst market is expected due to environmental and energy concerns, some challenges related to its preparation, such as control of active site size and structure, are still a major challenge, as traditional methods are longstanding, complex, and non-environmentally friendly (Wang et al., 2018b).
Supported metal catalysts are usually prepared by impregnation or co-precipitation of metal precursors in a liquid phase into an inert support (Poelman et al., 2007). Such techniques require a conjunction of many unitary operations, including the insertion of the metal precursor into the support, drying after deposition, calcination, and, occasionally, reducing or activating the final supported catalyst obtained (Liu et al., 2002). This procedure, however, has some intrinsic disadvantages. One is that undesired ions or solvents may be included in the deposition, resulting in contamination (Poelman et al., 2007). In addition, other disadvantages inherent to the calcination process can be cited, such as particle agglomeration, long treatment duration, the high temperature required, high energy consumption, and lack of process control (Zhang et al., 2000). Usually, the calcination process causes the oxidation of the metal particles on the support. However, in most cases, only free metal particles have catalytic properties, making a further process of catalyst reduction necessary before use (Cheng, 2008). Wang and Ruckenstein (2001) reported the effects of calcination temperature on catalyst production. Adopting 500, 800, and 900°C as standard calcination temperatures, they found that the surface area, the exposed metal area, and the degree of reduction decreased with increasing temperature. Results reported by Palm et al. (2020) elucidated that, at lower temperatures (between 390 and 440°C), the surface area of supported metal catalysts has no significant effect in the ethanol conversion during steam reforming and partial oxidation reactions. However, as the temperature increases, the ethanol conversion was directly influenced by surface morphology, as a higher surface area provides more active metal sites.
The widespread use of chemical methods in catalyst preparation is due to their simplicity and low initial costs (Veith et al., 2006). However, the current status of catalyst preparation is far from where it should be, as the desired metal-support interface is not always achieved (Liu et al., 2002). The final catalytic properties of metal sites are usually defined through catalyst reduction conditions, which are generally provided by a stream of hydrogen at a high temperature (Zhu et al., 2006; Wang et al., 2007). Independent of the process step, plasma technology arises as an interesting processing solution, creating a clean, strong, and direct metal–support interface, with no thermal diffusion of metal particles through the support (Zou et al., 2006a).
The development of new and sustainable methods of catalyst production is still a major challenge (Brault, 2011). Green chemistry seeks to avoid the use of hazardous reactants and solvents in chemical processes, reducing or even eliminating the generation of waste and harmful substances (Sheldon et al., 2007). Such principles should be achieved through process routes that also allow time and cost reductions in catalyst preparation and, if possible, increase their efficiency (Brault, 2011). Due to these obstacles, the use of plasma technologies, mainly non-thermal plasma, in the preparation of supported metal catalysts has attracted a lot of attention (Liu et al., 2002). It can reduce the size of catalytic sites, improving dispersion and metal–support interaction using less or no hazardous chemicals (Du et al., 2015; Chung and Chang, 2016). Such improvements also lead to increased catalyst activity and stability. Moreover, its reduction capacity is not limited to reducing gases. Ar, He, and N2 plasmas can have a similar reducing effect to H2, generating a simple, easy and safe process at room temperature with low energy requirements (Zhang et al., 2000; Liu et al., 2006). In short, plasma allows new catalytically active materials to be obtained, new preparation processes to be developed, used catalysts to be regenerated, and, mainly, catalyst performance to be improved simultaneously with its synthesis (Liu et al., 2006).
Non-thermal plasma is a promising technique for the preparation of supported metal catalysts due to the low energy requirements and the ability to induce physical and chemical reactions at relatively low temperatures (Liu et al., 2006; Cheng, 2008). Through the application of plasma discharge in the catalyst preparation process, structures are obtained that induce superior performance compared to those obtained by traditional thermal methods, providing greater reagent conversion and selectivity (Wang et al., 2018b). For catalysts prepared through conventional processes, this can only be obtained by modification of catalysis parameters, such as increasing the contact time of reactants with the catalyst or raising the reaction temperature (Tsipouriari et al., 1998).
Physical deposition techniques are rarely adopted as a preparation method of supported catalysts. However, they offer some advantages in comparison to classical chemical routes, such as greater process control, high reproducibility, and good adhesion of the active phase on the support (Zou et al., 2006b; Poelman et al., 2007). In addition, compared to conventional preparation routes of supported metal catalysts, the use of plasma-assisted processes enables (1) higher dispersion of active species, (2) greater activation, selectivity, and lifetime (durability) of the obtained catalyst, and (3) shorter preparation time (Liu et al., 2002). In this context, sputtering deposition emerges as a potential alternative to traditional methods of obtaining supported catalysts (Wang et al., 2018b). Inoue et al. (2020) have prepared Ru-based catalysts supported in TiO2 with an anatase structure by RF sputtering (13.56 MHz ± 5 kHz) at room temperature in an Ar atmosphere at a pressure of 0.8 Pa and evaluated the effects of physical plasma deposition on the catalytic activity for CO2 methanation. Small Ru sites, i.e., lower than 5 nm, were formed on the TiO2 surface even when the sputtering time was increased from 4 to 12 h, proving that the plasma technique does not induce particle growth. Hence, lower reaction temperatures could be adopted owing to improved catalytic activity due to reduced Ru particle size and the higher amount of Ru deposited with increasing sputtering time. Furthermore, the small size of Ru particles was preserved for reaction temperatures up to 360°C. In another recent study, Fu et al. (2020) revealed that a Pt/C catalyst prepared by magnetron sputtering deposition has some advantages when compared to one prepared with conventional chemical methods, such as easier operation, higher Pt deposition, and less pollution, thus having a wide range of possible applications in commercial fuel cells.
Also, during sputtering, the catalyst structure can be modified by reduction, oxidation, network restructuring, and formation of oxygen vacancies due to inelastic particle–catalyst collisions (Chung and Chang, 2016). Vacancies and defects created in the support structure during sputtering influence the size and shape of metal particles, inducing a greater number of active sites, and contribute toward the interface energy, i.e., metal–support interaction due to electron donor/acceptor mechanisms (Mahmood and Woo, 2013; Cao et al., 2018). Moreover, structural defects are beneficial for catalyst reduction (Liu et al., 2002). The occurrence of such phenomena depends on parameters like reactor geometry, gas composition, treatment temperature, applied pressure, and catalyst geometry (Chung and Chang, 2016). Cao et al. (2018) reported that the H2/CO ratios obtained with supported Ni catalysts with high vacancy defects are slightly higher than the predicted thermodynamic equilibrium of 0.92, reaching values higher than 1 during 120 h of reaction, whereas the conventional supported Ni catalyst ratio decreased significantly from 0.97 (at the beginning of the catalytic test) to 0.90 (after 20 h) due to carbon deposition. This coke formation may cover the active sites, resulting in lower stability. Two different types of carbon deposits, as shown in Figure 3, are usually observed in supported metal catalysts after use (Zhu et al., 2008). The first is filamentous carbon, which induces the separation between the active phase and the support, making it more prone to pullout during reaction due to weaker interactions. Another common morphology is the encapsulating carbon, which covers the active site and prevents its contact with the reactants.
Figure 3. Illustrative representation of the most common carbon deposit types observed in supported metal catalysts after use.
Due to the complexity of plasma physics and its multidisciplinary characteristics, the interaction mechanism between species from plasma and the catalyst precursor is still not thoroughly understood (Du et al., 2015; Liu et al., 2016). So far, the most accepted explanation of the beneficial results provided by plasma in systems similar to that illustrated in Figure 2A, mainly in terms of metal particle size, is related to the fact that the metal particles deposited in the support are able to trap thousands of electrons due to plasma exposure, creating plasma sheaths around each active site, as shown in Figure 4. These plasma sheaths exhibit strong Coulombic repulsion with the electrons in plasma (Figure 4A), inducing stretching and easy splitting of clusters if impacted by electrons or other energetic species from plasma (Liu et al., 2006). Trapped electrons, as shown in Figure 4B, also generate repulsion forces between electrons trapped in the same particle as well as adjacent particles, affecting the kinetics of metal site nucleation and growth due to interaction with the support surface and creation of defects favorable to the formation of new nuclei instead of coalescence of previously formed sites, as exposed in Figure 4C (Du et al., 2015). As a result, fast nucleation and slow crystal growth in a room-temperature plasma process can reduce the size of active sites (Liu et al., 2006; Peng et al., 2015). Furthermore, during plasma treatment, the catalyst is normally reduced, since electrons can be a reducing agent (Taghvaei et al., 2017).
Figure 4. Mechanism for obtaining a supported metal catalyst with smaller and highly dispersed active sites: (A) catalyst surface bombardment by energetic species and accumulation of electrons on metallic particles; (B) sheath formation and elongation of metallic particles due to repulsive forces; (C) fragmentation of metallic particles, resulting in smaller and more dispersed active sites.
Plasma reactions are much more dynamic than those that occur in conventional thermal preparation, inducing fast crystal nucleation on the support (Liu et al., 2016). As non-thermal plasma is operated at low temperatures, including room temperature, crystal growth is slow, making it possible to obtain more active sites due to greater refining of supported metal particles (Das et al., 2017). Reducing the size of metallic particles present on the surface also favors the occurrence of more intense interactions between the metal and the support, contributing to greater sintering and coke deposition resistance during reactions. Therefore, supported metal catalysts prepared through plasma-assisted processes may present greater stability and durability even under more severe reaction conditions (Lee et al., 2009; Rahemi et al., 2013b; Wang et al., 2013). In the following sections, results reported in the literature about the pros and cons of introducing plasma techniques in supported metal catalyst preparation will be presented and discussed.
Even when plasma is applied before the calcination process, smaller and more dispersed metal particles can be obtained (Taghvaei et al., 2017). Rahemi et al. (2013a) evaluated the morphology of Ni/Al2O3 and Ni/Al2O3-ZrO2 catalysts exposed to three treatment cycles of 15 min each in Ar plasma produced by DC glow discharge (with a current of 100 mA and pressure range of 100 to 200 Pa) prior to calcination and compared the results with samples prepared by a conventional process. The researchers found that, without plasma treatment, Ni metal particles are arranged in large clusters with irregular shapes. On the other hand, plasma-treated samples presented a more homogeneous distribution of metallic sites that were significantly smaller, resulting in larger contact interfaces and a more homogeneous morphology. In another paper, Rahemi et al. (2013b) performed the same comparative study (with the same process parameters) for Ni/Al2O3 and Ni/Al2O3-CeO2 and observed similar results. In addition, through XRD analyzes, the occurrence of slightly wider NiO and NiAl2O4 peaks in plasma-treated samples compared to conventional process samples was observed, indicating the presence of smaller and more dispersed particles. Furthermore, an increase in NiAl2O4 peaks and a decrease in NiO peaks compared to untreated samples were verified, which is evidence that plasma improves the interaction between Ni particles and Al2O3 support.
Wang et al. (2013), through XPS analysis, verified that Ni surface coverage, determined by the Ni/Si atomic ratio on the surface of supported Ni/SiO2-Mg catalysts, was 0.054 and 0.043 for samples with and without, respectively, N2 glow discharge plasma treatment before thermal calcination. The plasma discharge was driven for 2 h under the following parameters: frequency of 13.56 MHz, voltage of 100 V, anodic current of 100 mA, and initial gas pressure of 50 Pa. Considering that the total amount of Ni present in samples was the same (6 wt%), it proves that plasma causes a higher dispersion of Ni particles, preventing cluster formation and growth. This result is in accordance with the study performed by Zhu et al. (2008), who acknowledged that Ar glow discharge plasma treatment before thermal calcination improved Ni distribution on the surface of supported Ni/Al2O3 catalysts. In this case, a voltage of 900 V was supplied by a high voltage amplifier through a function/arbitrary waveform generator with a 100 Hz square wave at a pressure range of 100 to 200 Pa, and the samples were treated five times for 10 min.
Yan et al. (2013) compared the stability and activity of Ni/SiO2 catalysts prepared by a conventional method with and without a DBD process before calcination using an air plasma with an average voltage of 14 kV with a sinusoidal waveform at a frequency of about 22 kHz. Plasma samples were treated 15 times for 4 min in each cycle. The catalyst treated by plasma presented mainly Ni particles with the (111) plane in the surface, resulting in high dispersion, enhanced interaction between Ni and SiO2 support, improved Ni sintering resistance, and excellent coke resistance. On the other hand, the thermally calcinated catalyst without plasma pretreatment presented Ni particles of the (111), (200), and (220) planes. These two latter planes exhibit a strong tendency for coke formation, compromising the catalyst performance (Taghvaei et al., 2017). Similarly, Shi and Liu (2009) also reported that Ni/SiO2 catalyst with a 1 h Ar glow discharge plasma pretreatment exhibits improved activity. Unlike DBD plasma, glow discharge does not decompose the nickel precursor, but a specific hydrate is formed. So, in this case, a subsequent thermal process must always be performed before the use of the catalyst in reactions. The Ar glow discharge plasma was generated by applying 900 V at 100 Pa through a high voltage amplifier with signal input supplied by a function/arbitrary waveform generator with a 100 Hz square wave.
Recently, Chen et al. (2020) prepared vanadium-based supported catalysts by non-thermal plasma deposition in a glow discharge reactor with a power output of 120 W and an internal pressure between 15 and 60 Pa prior to thermal calcination at 500°C for 5 h and compared it with conventionally prepared supported catalyst. The results obtained demonstrated that the plasma-treated catalysts exhibited smaller particle size, greater metal dispersion, and a more uniform distribution of active sites, as well as higher specific surface area. Also, non-thermal plasma treatment generated more oxygen vacancies on the catalyst surface, enhancing the catalytic activity of the catalysts at temperatures below 260°C. These outcomes agree with the study performed by Zhao et al. (2019), in which Ni/SiO2 catalysts were prepared with and without DBD plasma treatment prior to thermal calcination at 500°C for 4 h. Plasma was generated and sustained with an average voltage of 14 kV at a frequency of 22 kHz using air as the plasma-forming gas. The plasma process prevented the formation of NiO species and suppressed Ni sintering, providing higher surface area, enhanced Ni dispersion, and greater metal–support interaction, which increased the activity and stability of catalysts in syngas methanation. The plasma-prepared Ni/SiO2 catalyst showed a CO conversion of 79% at 340°C, compared to 32.5% for conventionally prepared catalysts, both with 10 wt% Ni. Equal propensities were also observed for H2 conversion and CH4 yield.
In general, low-temperature plasma calcination and reduction are quite distinct from traditional thermal methods in terms of nucleation and crystal growth, making it possible to obtain supported metal catalysts of controllable particle size and improved activity and stability (Taghvaei et al., 2017). Glow discharge plasmas can be applied as a green reduction method in supported metal catalyst preparation, as electrons are incredible reducing agents (Liu et al., 2014). However, some metal precursors cannot be reduced by this procedure. For example, plasma calcination of supported Ni(NO3)2, Fe(NO3)3, and Co(NO3)2 precursors in Ar glow discharge causes only decomposition, so metal oxides are normally obtained (Cheng, 2008; Wang et al., 2018b). The propensity of metal ions for reduction by non-hydrogen plasma can be assessed by a basic concept of electrochemistry known as standard electrode potential (Wang et al., 2007). Metal ions with positive standard electrode potential (adopting a standard hydrogen electrode as the reference electrode), such as Pt, Pd, Au, Ag, and Rh, can be readily reduced by non-hydrogen plasma at room temperature due to its ability to adsorb electrons by the mechanism illustrated in Figure 4 (Liu et al., 2014). Zou et al. (2006b) reported that Ar glow discharge plasma created using a DC high-voltage generator with a voltage between 0.9 and 1.2 kV and current in the range of 1 to 2 mA at a pressure of 100 Pa, can be successfully applied for plasma reduction of noble metals supported on non-porous TiO2 and porous γ-Al2O3, providing metal nanoparticles homogeneously distributed and with enhanced interaction with both supports after 60 min of treatment.
Electron-assisted reduction via room-temperature discharges is extraordinarily effective for size control of metallic sites. It is an effortless, cheap, and fast way to reduce metal sites, providing an environmentally friendly process as an alternative to hydrogen reduction at elevated temperature (Zhang et al., 2000; Liu et al., 2006, 2014). Zhu et al. (2006) applied Ar glow discharge plasma for calcination and reduction of Pt/Al2O3 catalysts, obtaining Pt particles with irregular shape but uniform distribution on the Al2O3 support after 5 plasma treatments of 10 min each at a voltage of 900 V and in a pressure range of 100 to 200 Pa. Plasma-reduced Pt/Al2O3 showed activity comparable to a hydrogen-reduced sample for partial oxidation of methane, but greater stability and anti-coke resistance were observed. Similar results were noticed by Wang et al. (2007) in the reduction of Rh/Al2O3 catalyst by argon glow discharge plasma using the same process parameters as Zhu et al. (2006). The average particle size obtained for Rh was 1.2 nm.
On the other hand, for metal ions with negative standard electrode potential in comparison to a standard hydrogen electrode (reference), a combination of plasmas and/or an external heating source can be applied. Moreover, hydrogen plasma can also be applied directly in this case, if preferred (Liu et al., 2014). Kim et al. (2004) reported that supported Co and Pt catalysts can be reduced by H2 atmospheric DBD plasma using an AC source. Hu et al. (2011) reported that a cold plasma jet cannot be used to reduce NiO/Al2O3 catalysts in an Ar atmosphere below 467°C but that it is promptly reduced in a 10%H2/Ar atmosphere. In general, characterization techniques like XRD and XPS can confirm the existence of metallic active phase sites after plasma treatment (Cheng, 2008).
Zhang et al. (2000) reported that Ar plasma RF discharge at 650 Pa for 25 min for calcination followed by an H2 plasma under the same conditions for 65 min for reduction provides beneficial results when used in place of conventional thermal processes for Ni/Al2O3 catalyst preparation. Plasma-treated catalyst demonstrated greater activity and stability in comparison to a conventionally prepared one, inducing an increase in CH4 conversion during natural gas partial oxidation reaction of 3 to 5%. In addition, the total preparation time of the supported metal catalyst was significantly shorter (from 11 to 1.5 h). Similar results were found by Jin et al. (2014) when comparing Ni/Al2O3 catalysts calcined and reduced through a traditional method at 700°C for 8 h in a 20%H2/N2 atmosphere and by an H2 DBD plasma technique at atmospheric pressure for 20 min. The authors observed higher activity, stability, and resistance to carbon deposition in plasma-treated samples, which were attributed to the greater dispersion of undersized Ni particles, generating more active sites. In other research conducted by Foix et al. (2010), calcination of a Pd/Al2O3 catalyst through Ar RF plasma discharge at 500 Pa for 30 min gave rise to Pd2+ sites on the surface surrounded by oxygen species, while thermal calcination of a sample in air at 500°C for 2 h resulted in the predominant formation of PdO species. This difference is related to the higher catalytic activity observed for plasma-treated catalysts in the conversion of NOx to N2 at low temperature. Another interesting point reported by the authors is the reduction in process duration by at least half, making it possible to achieve a drop in energy consumption of up to 87.5%.
Shang et al. (2009) applied 20%H2/Ar plasma jet calcination and reduction to prepare Ni/γ-Al2O3 catalyst, reducing process duration from 7 h (5 h of calcination at 550°C and 2 h of reduction at 750°C) to 10 min. Due to the 20 kHz AC voltage applied, the temperature of the catalyst bed during the plasma treatment was 527°C. The average pore size of the catalyst decreased from 9.8 to 6.9 nm, and Ni nanoparticles as small as 5 nm were obtained, providing higher nickel dispersion, improved anti-coke performance, and higher conversion of CH4 (from 80.3 to 94.2%) and CO2 (from 64.4 to 73.8%) in dry reforming of methane. A similar correlation between average pore size and reactant conversion was noticed by Huang et al. (2011) and Tang et al. (2015). Karuppiah and Mok (2014) applied an AC DBD plasma of 11–12.5 kV (operating frequency: 1 kHz) in a 20%H2/Ar atmosphere to reduce Ni/γ-Al2O3 catalyst, obtaining highly active ultrafine Ni nanoparticles with uniform dispersion after 4 h of reduction. Furthermore, Benrabbah et al. (2017) noticed that Ni/Ce0.58Zr0.42O2 catalyst reduced by H2 DBD plasma through a high-voltage AC source of 15 kV (42.5 kHz) at atmospheric pressure presented enhanced metal–support interaction compared to the same catalyst conventionally treated, which slightly improves its activity for CO2 hydrogenation at low temperature. In a detailed study, Wu et al. (2015) applied atmospheric-pressure H2 DBD plasma to Ni/γ-Al2O3 catalyst after a calcination process to reduce NiO/Ni2+ phase to Ni0. As explained by the authors, during plasma treatment, H2 is dissociated by energetic electrons and forms H atoms responsible for catalyst reduction sputtering. As a result, smaller metal clusters (from 11.2 nm for NiO particles to 9.4 nm for Ni0) are formed, contributing to more uniform dispersal over the surface. Moreover, the authors reported that plasma discharge enhanced the catalytic activity and coke formation resistance for steam reforming of ethanol. The ethanol conversion and the hydrogen yield obtained at 437°C with the plasma-treated catalyst were 20.6 and 10% higher, respectively, than those achieved by an untreated catalyst.
Plasma can be used not only during the preparation of supported metal catalysts but also as a post treatment after conventional methods. Although this alternative does not allow energy consumption and processing duration to be reduced, it enables enhanced catalytic properties like those described previously to be obtained. Wang et al. (2018a) applied an O2/N2 (20/80) DBD plasma through a high-voltage AC source with a frequency of 1.8 kHz for 30 min in Pt/CeO2 catalyst prepared by a conventional method prior to use. Characterization and catalytic tests revealed that the plasma modified the catalyst structure and enhanced the metal–support interaction. Higher catalytic performance and lower activation temperature for toluene oxidation were observed compared to a non-treated sample due to there being smaller, highly dispersed Pt sites, as well as a higher concentration of oxygen vacancies and Ce3+ sites. Also, toluene conversion through catalytic oxidation was conducted with no significant decrease in activity for at least 50 h of use. Di et al. (2019) reported that the atmospheric-pressure DBD plasma treatment of Pd/C-supported catalyst after a calcination process at 300°C for 2 h in an H2-rich atmosphere led to an increase of 12% in the production of H2 and CO2 through formic acid dehydrogenation. Also, greater catalytic stability was observed, as, with plasma treatment, the sample's catalytic activity decreased to 59.6% in a second reaction cycle in comparison with the first cycle, while the commercial sample presented a decrease to 16.3%. The main reason for these results was the small size of Pd nanoparticles and the strong metal–support interaction induced by cold plasma, even after calcination. The plasma treatment was performed through 3 cycles of 2 min each with a discharge voltage of 36.0 kV at a frequency of 13.6 kHz under a high-purity H2 atmosphere.
Plasma post treatment can also be applied for recovering used supported metal catalysts in order to eliminate carbon species deposited during the reaction, but this approach is still poorly explored in the literature. The regeneration effectiveness can be attributed to chemical and thermal effects of plasma such as the formation of reactive intermediates and cost-effective catalyst heat-up due to low-temperature activation (Lee et al., 2019). Zhu et al. (2015) reported that Au/TiO2 catalysts deactivated through CO oxidation were effectively regenerated by atmospheric-pressure air DBD plasma initiated through a high-voltage AC source with a frequency of 1.8 kHz and an input power of 3 W. In contrast, Lokteva et al. (2011) applied a glow-discharge O2 plasma treatment for the recovery of Pd/TiO2 catalyst deactivated due to carbonaceous deposits. A sputtering reactor operated at an AC voltage frequency of 50 Hz, amplitude of 1,500 V, and current of 150 mA was used for discharge maintenance for 20 min at low pressure (120 Pa). Deep oxidation of Pd particles was observed due to the removal of carbonaceous deposits. Thus, PdO sites had to be subsequently reduced by H2 for complete catalyst renewal. It must be highlighted that sintered particles cannot be recovered, but heavy hydrocarbons can be detached via oxidation (Lee et al., 2019).
High activity, selectivity, and long-term stability are primary properties required for a supported metal catalyst that is effective for fuel conversion. As discussed in previous sections, catalytic reactions are influenced by various factors, including active particle size and shape, phase structure, metal–support interaction, surface properties, reaction conditions, among others. In this scenario, non-thermal plasma preparation provides supported metal catalysts with greater dispersion, better metal-support interaction, and improved resistance to carbon deposition and deactivation in fuel conversion reactions (Liu et al., 2016). Fuel reforming consists of chemical extraction of hydrogen from hydrocarbons such as diesel, gasoline, liquefied petroleum gas (LPG), and natural gas (Kang et al., 2008). This catalytic process is commonly conducted at high temperature (up to 1,000°C) and pressure (>10 atm) (Chen et al., 2008; Xu and Tu, 2013). The most reported catalysts for fuel conversion were Ni, Fe, Co, Pt, and Pd, supported on a wide variety of oxide materials, due to their great chemical stability even at higher temperatures.
The production of syngas (H2 + CO) is a relevant process for natural gas conversion into valuable liquid products of high-quality (Alvarez-Galvan et al., 2019). Dry reforming of methane (DRM) is a renowned process for syngas production from two greenhouse gases (CH4 and CO2) (Taghvaei et al., 2017). Syngas can be used as fuel or feedstock for the Fischer–Tropsch process to produce hydrocarbons (Chung and Chang, 2016), as will be discussed in the next paragraphs. Ni-based supported catalysts are considered proper catalysts for this type of reaction due to their high activity and economic feasibility, as the stability issue is overcome by the introduction of plasma discharge methods into the preparation process. Rahemi et al. (2013a,b,c, 2014) conducted many studies into the influence of Ar glow discharge plasma calcination and reduction in Ni-based supported catalysts for dry reforming of methane, obtaining positive results such as an increase of 62% and 33% in H2 selectivity and CH4 conversion, respectively, due to plasma effects.
Partial oxidation of methane is another promising process with which to obtain syngas. In this context, Xi-zhen et al. (2003) obtained Ni-Fe/Al2O3 catalyst with higher methane conversion, as well as greater CO and H2 selectivity, by a glow discharge plasma calcination and reduction method. In contrast to partial oxidation, the Fischer-Tropsch reaction converts syngas to liquid hydrocarbons such as methanol, an alternative clean biofuel that is less expensive than ethanol. Jiang et al. (2013) reported that the replacement of thermal calcination for DBD plasma calcination in Co/SiO2 catalyst preparation induces higher CO conversion and hydrocarbon chain growth. Moreover, the treatment time was reduced from 5 h to 30 min. Nevertheless, not only fuel conversion processes but also other feasible chemical routes with potential application for onboard energy conversion in vehicles could take advantage of the beneficial effects of plasma-prepared supported metal catalysts, such as photocatalytic water splitting (Matsubara et al., 2019) and hydrogen evolution reaction (Nam et al., 2020).
The use of a catalyst in chemical processes such as fuel conversion is one of the 12 principles of green chemistry. Thus, new catalysts are increasingly desired, and non-thermal plasma-based processes are very promising since less hazardous or less expensive chemicals are used (Liu et al., 2016). However, commonly used supports are porous materials, which presents a physical barrier not yet overcome by plasma preparation methods of supported metal catalysts. Moreover, research in this area is still scarce. A study developed by Zhang et al. (2016) suggests that plasma species may be formed within pores whose size is > 10 μm. In order to investigate the influence of porous supports in the plasma preparation of supported metal catalysts, a previous study conducted by the authors of this paper (Santos et al., 2018) presented a sputtering deposition of Fe onto fragments of Al2O3 foams with 26 pores/cm and an average pore size of 300 μm in a plasma reactor using 43.4 sccm of Ar for 2 h at a temperature of 450°C, a pressure of 130 Pa and a voltage of 650 ± 12 V. Despite the large pore size, it was observed that Fe deposition occurred only in the outermost pores. However, this fact does not indicate that the plasma was not able to penetrate the innermost pores, but rather that Fe particles bombarding the support did not have access to internal zones due to collisions and consequent deposition in more external pores. Anyway, it is undeniable that there is great academic and industrial interest regarding the study and development of supported metal catalysts, especially those obtained from transition metals, due to their lower cost and high availability.
On the other hand, the correlations between process parameters and catalyst modifications still need to be better understood, which requires more fundamental studies on cold plasma mechanisms and effects. Full control of the surface characteristics of these catalysts, such as the size and dispersion of metallic particles and their interaction with the support, pore size and morphology, and the presence of structural defects, among others, must be achieved. These aspects are crucial for obtaining properties such as high catalytic activity, selectivity, and durability. Minimizing this knowledge gap will enable major breakthroughs in the production of high-performance catalysts. The introduction of plasma-assisted processes as pretreatment or activation methods of supported metal catalysts has great potential, since it allows all of the aforementioned characteristics to be modified. However, most papers reporting plasma-treated catalysts only compare their catalytic properties and performance with conventionally prepared samples, i.e., almost no attention has been given to opposing plasma procedures (Taghvaei et al., 2017). Depending on the electrode arrangement and operational conditions, non-thermal plasma characteristics can change a lot.
Both catalysis and plasma are effective techniques for generating cleaner and better fuels, although both also exhibit complex reaction mechanisms. Hence, due to room temperature operation, low power requirements, and non-equilibrium properties, plasma preparation or pretreatment of supported metal catalysts can be a very advantageous process. The nucleation and growth promoted by non-thermal plasmas are very different from those observed in conventional thermal processes due to the presence of energetic species. In general, plasma can enhance the dispersion of metallic nanoparticles present in the catalyst surface, causing stronger interaction between active phase and support. Thus, higher activity, selectivity, and stability, as well as lower activation temperature, are observed. This can be attributed to the splitting of metal particles induced by sputtering of the catalyst surface. Glow discharge and dielectric barrier discharge are the most used non-thermal plasma configurations for this purpose because of their simplicity.
Plasma preparation of supported metal catalysts can be performed as a green process, since in most cases, no hazardous chemicals are required. Moreover, a shortened process time is achieved when plasma is applied, and some peculiar problems of high-temperature calcination/reduction like the coalescence of metal sites or active phase oxidation are overcome. Therefore, supported metal catalysts based on transition metals such as Ni and prepared by plasma can provide better fuel conversion performance than supported metal catalysts with noble metals as the active phase prepared by conventional processes, which implies reduced obtention costs. However, more fundamental studies are necessary in order to develop this technology toward industrial application.
AS wrote the first draft of the manuscript, being responsible for conceptualization, investigation, and primary formal analysis. RC and DD contributed to manuscript formal analysis, editing, revision, and approval of the submitted version. All authors contributed to the article and approved the submitted version.
The authors declare that the research was conducted in the absence of any commercial or financial relationships that could be construed as a potential conflict of interest.
The authors of this article thank BMW Group Brazil for the support offered through the grant UFSC/2016/0110.
Alvarez-Galvan, C., Melian, M., Ruiz-Matas, L., Eslava, J. L., Navarro, R. M., Ahmadi, M., et al. (2019). Partial oxidation of methane to syngas over nickel-based catalysts: influence of support type, addition of rhodium, and preparation method. Front. Chem. 7:104. doi: 10.3389/fchem.2019.00104
Aramouni, N. A. K., Touma, J. G., Tarboush, B. A., Zeaiter, J., and Ahmad, M. N. (2018). Catalyst design for dry reforming of methane: analysis review. Renew. Sust. Energ. Rev. 82, 2570–2585. doi: 10.1016/j.rser.2017.09.076
Ayabe, S., Omoto, H., Utaka, T., Kikuchi, T., Sasaki, K., Teraoka, Y., et al. (2003). Catalytic autothermal reforming of methane and propane over supported metal catalysts. Appl. Catal. A 241, 261–269. doi: 10.1016/S0926-860X0200471-4
Bailie, J. E., Hutchings, G. J., and O'Leary, S. (2001). “Supported catalysts” in Encyclopedia of Materials Science and Technology, ed K. H. J. Buschow (Amsterdam; New York: Elsevier), 8986–8990.
Benrabaa, R., Löfberg, A., Rubbens, A., Bordes-Richard, E., Vannier, R. N., and Barama, A. (2013). Structure, reactivity and catalytic properties of nanoparticles of nickel ferrite in the dry reforming of methane. Catal. Today 203, 188–195. doi: 10.1016/j.cattod.2012.06.002
Benrabbah, R., Cavaniol, C., Liu, H., Ognier, S., Cavadias, S., Gálvez, M. E., et al. (2017). Plasma DBD activated ceria-zirconia-promoted Ni-catalysts for plasma catalytic CO2 hydrogenation at low temperature. Catal. Commun. 89, 73–76. doi: 10.1016/j.catcom.2016.10.028
Bogaerts, A., Neyts, E., Gijbels, R., and Mullen, J. (2002). Gas discharge plasmas and their applications. Spectrochim. Acta Part. B At. Spectrosc. 57, 609–658. doi: 10.1016/S0584-8547(01)00406-2
Brault, P. (2011). Plasma deposition of catalytic thin films: experiments, applications, molecular modeling. Surf. Coat. Technol. 205, S15–S23. doi: 10.1016/j.surfcoat.2011.01.052
Cao, Y., Maitarad, P., Gao, M., Taketsugu, T., Li, H., Yan, T., et al. (2018). Defect-induced efficient dry reforming of methane over two-dimensional Ni/h-boron nitride nanosheet catalysts. Appl. Catal. B 238, 51–60. doi: 10.1016/j.apcatb.2018.07.001
Chao, Y., Huang, C., Lee, H., and Chang, M. (2008). Hydrogen production via partial oxidation of methane with plasma-assisted catalysis. Int. J. Hydrog. Energy 33, 664–671. doi: 10.1016/j.ijhydene.2007.09.024
Chapman, B. (1980). Glow Discharge Processes: Sputtering and Plasma Etching. New York, NY: John Wiley and Sons.
Chen, G., Xu, J., Yu, H., Guo, F., Xie, J., and Wang, Y. (2020). Effect of the non-thermal plasma treatment on the structure and SCR activity of vanadium-based catalysts. Chem. Eng. Sci. 380:122286. doi: 10.1016/j.cej.2019.122286
Chen, H. L., Lee, H. M., Chen, S. H., Chao, Y., and Chang, M. B. (2008). Review of plasma catalysis on hydrocarbon reforming for hydrogen production - interaction, integration, and prospects. Appl. Catal. B 85, 1–9. doi: 10.1016/j.apcatb.2008.06.021
Chen, X., Cheng, Y., Li, T., and Cheng, Y. (2017). Characteristics and applications of plasma assisted chemical processes and reactors. Curr. Opin. Chem. Eng. 17, 68–77. doi: 10.1016/j.coche.2017.07.001
Cheng, D. (2008). Plasma decomposition and reduction in supported metal catalyst preparation. Catal. Surv. Asia 12, 145–151. doi: 10.1007/s10563-008-9046-4
Chung, W., and Chang, M. (2016). Review of catalysis and plasma performance on dry reforming of CH4 and possible synergistic effects. Renew. Sust. Energ. Rev. 62, 13–31. doi: 10.1016/j.rser.2016.04.007
Corthals, S., Witvrouwen, T., Jacobs, P., and Sels, B. (2011). Development of dry reforming catalysts at elevated pressure: D-optimal vs. full factorial design. Catal. Today 159, 12–24. doi: 10.1016/j.cattod.2010.06.021
Das, S., Sengupta, M., Patel, J., and Bordoloi, A. (2017). A study of the synergy between support surface properties and catalyst deactivation for CO2 reforming over supported Ni nanoparticles. Appl. Catal. A 545, 113–126. doi: 10.1016/j.apcata.2017.07.044
Di, L., Zhang, J., Ma, C., Tu, Xin., and Zhang, X. (2019). Atmospheric-pressure dielectric barrier discharge cold plasma for synthesizing high performance Pd/C formic acid dehydrogenation catalyst. Catal. Today 337, 201–207. doi: 10.1016/j.cattod.2019.02.062
Du, C., Ma, D., Wu, J., Lin, Y., Xiao, W., Ruan, J., et al. (2015). Plasma-catalysis reforming for H2 production from ethanol. Int. J. Hydrog. Energy 40, 15398–15410. doi: 10.1016/j.ijhydene.2015.09.096
Fernández, A., Arzac, G. M., Vogt, U. F., Hosoglu, F., Borgschulte, A., Haro, M. C. J., et al. (2016). Investigation of a Pt containing washcoat on SiC foam for hydrogen combustion applications. Appl. Catal. A 180, 336–343. doi: 10.1016/j.apcatb.2015.06.040
Foix, M., Guyon, C., Tatoulian, M., and Da Costa, P. (2010). Study of the use of fluidized bed plasma reactors for the treatment of alumina supported palladium catalyst: application for SCR NOx by CH4 in stationary sources. Catal. Commun. 12, 20–24. doi: 10.1016/j.catcom.2010.05.022
Fu, K., Zeng, L., Liu, J., Liu, M., Li, S., Guo, W., et al. (2020). Magnetron sputtering a high-performance catalyst for ultra-low-Pt loading PEMFCs. J. Alloys Compd. 815:152374. doi: 10.1016/j.jallcom.2019.152374
Hammer, T., Kappes, T., and Baldauf, M. (2004). Plasma catalytic hybrid processes: gas discharge initiation and plasma activation of catalytic processes. Catal. Today 89, 5–14. doi: 10.1016/j.cattod.2003.11.001
He, Z., and Wang, X. (2015). Renewable energy and fuel production over transition metal oxides: the role of oxygen defects and acidity. Catal. Today 240, 220–228. doi: 10.1016/j.cattod.2014.04.023
Hou, T., Zhang, S., Chen, Y., Wang, D., and Cai, W. (2015). Hydrogen production from ethanol reforming: catalysts and reaction mechanism. Renew. Sust. Energ. Rev. 44, 132–148. doi: 10.1016/j.rser.2014.12.023
Hu, S., Long, H., Xu, Y., Shang, S., and Yin, Y. (2011). Reduction mechanism of Ni/Al2O3 catalyst reduced by cold plasma jet for carbon dioxide reforming of methane. Chin. J. Catal. 32, 340–344. doi: 10.3724/SP.J.1088.2011.00818
Huang, C., Bai, S., Lv, J., and Li, Z. (2011). Characterization of silica-supported cobalt catalysts prepared by decomposition of nitrates using dielectric-barrier discharge plasma. Catal. Lett. 141, 1391–1398. doi: 10.1007/s10562-011-0627-x
Huu, T. P., Gil, S., Costa, P., Giroir-Fendler, A., and Khacef, A. (2015). Plasma-catalytic hybrid reactor: application to methane removal. Catal. Today 257, 86–92. doi: 10.1016/j.cattod.2015.03.001
Inoue, M., Shima, A., Miyazaki, K., Lu, B., Sone, Y., and Abe, T. (2020). Effects of sputtering conditions on the activities of high-performance CO2 methanation catalysts prepared by a co-sputtering technique using the polygonal barrel system. Appl. Catal. A 597:117557. doi: 10.1016/j.apcata.2020.117557
Jang, W., Shim, J., Kim, H., Yoo, S., and Roh, H. (2019). A review on dry reforming of methane in aspect of catalytic properties. Catal. Today 324, 15–26. doi: 10.1016/j.cattod.2018.07.032
Jiang, Y., Fu, Y., Lü, J., and Li, Z. (2013). A zirconium modified Co/SiO2 Fischer-Tropsch catalyst prepared by dielectric-barrier discharge plasma. J. Energy Chem. 22, 506–511. doi: 10.1016/S2095-4956(13)60066-2
Jin, L., Li, Y., Lin, P., and Hu, H. (2014). CO2 reforming of methane on Ni/γ-Al2O3 catalyst prepared by dielectric barrier discharge hydrogen plasma. Int. J. Hydrog. Energy 39, 5756–5763. doi: 10.1016/j.ijhydene.2014.01.171
Kang, I., Yoon, S., Bae, G., Kim, J. H., Bae, J., Lee, D., et al. (2008). The micro-reactor testing of catalysts and fuel delivery apparatuses for diesel autothermal reforming. Catal. Today 136, 249–257. doi: 10.1016/j.cattod.2008.01.012
Karuppiah, J., and Mok, Y. S. (2014). Plasma-reduced Ni/γ-Al2O3 and CeO2-Ni/γ-Al2O3 catalysts for improving dry reforming of propane. Int. J. Hydrog. Energy 39, 16329–16338. doi: 10.1016/j.ijhydene.2014.08.012
Kim, S., Lee, H., Na, B., and Song, H. K. (2004). Plasma-assisted reduction of supported metal catalyst using atmospheric dielectric-barrier discharge. Catal. Today 89, 193–200. doi: 10.1016/j.cattod.2003.11.026
Lee, D. H., Song, Y., Kim, K., Jo, S., and Kang, H. (2019). Current state and perspectives of plasma applications for catalyst regeneration. Catal. Today 337, 15–27. doi: 10.1016/j.cattod.2019.04.071
Lee, H. M., Juan, L., Yeh, F., Li, H., Chen, H., Chang, M. B., et al. (2009). Plasma-pretreated catalyst for methanol synthesis from syngas. IEEE Trans. Plasma Sci. 37, 2213–2220. doi: 10.1109/TPS.2009.2030726
Lieberman, M. A., and Lichtenberg, A. J. (2005). Principles of Plasma Discharges and Materials Processing. New York, NY: John Wiley and Sons.
Liu, C., Li, M., Wang, J., Zhou, X., Guo, Q., Yan, J., et al. (2016). Plasma methods for preparing green catalysts: current status and perspective. Chin. J. Catal. 37, 340–348. doi: 10.1016/S1872-2067(15)61020-8
Liu, C., Vissokov, G. P., and Jang, B. W. (2002). Catalyst preparation using plasma technologies. Catal. Today 72, 173–184. doi: 10.1016/S0920-5861(01)00491-6
Liu, C., Zhao, Y., Li, Y., Zhang, D., Chang, Z., and Bu, X. (2014). Perspectives on electron-assisted reduction for preparation of highly dispersed noble metal catalysts. ACS Sustain. Chem. Eng. 2, 3–13. doi: 10.1021/sc400376m
Liu, C., Zou, J., Yu, K., Cheng, D., Han, Y., Zhan, J., et al. (2006). Plasma application for more environmentally friendly catalyst preparation. Pure Appl. Chem. 78, 1227–1238. doi: 10.1351/pac200678061227
Liu, L., Wang, Q., Song, J., Ahmad, S., Yang, X., and Sun, Y. (2017). Plasma-assisted catalytic reforming of toluene to hydrogen rich syngas. Catal. Sci. Technol. 7, 4216–4231. doi: 10.1039/C7CY00970D
Lokteva, E. S., Lazhko, A. E., Golubina, E. V., Timofeev, V. V., Naumkin, A. V., Yagodovskaya, T. V., et al. (2011). Regeneration of Pd/TiO2 catalyst deactivated in reductive CCl4 transformations by the treatment with supercritical CO2, ozone in supercritical CO2 or oxygen plasma. J. Supercrit. Fluids 58, 263–271. doi: 10.1016/j.supflu.2011.05.018
Mahmood, A., and Woo, S. I. (2013). Enhancement of catalytic activity of Au/TiO2 by thermal and plasma treatment. Korean J. Chem. Eng. 30, 1876–1881. doi: 10.1007/s11814-013-0120-x
Matsubara, K., Inoue, M., Hagiwara, H., and Abe, T. (2019). Photocatalytic water splitting over Pt-loaded TiO2 (Pt/TiO2) catalysts prepared by the polygonal barrel-sputtering method. Appl. Catal. B 254, 7–14. doi: 10.1016/j.apcatb.2019.04.075
Nam, J. H., Jang, M. J., Jang, H. Y., Park, W., Wang, X., Choi, S. M., et al. (2020). Room-temperature sputtered electrocatalyst WSe2 nanomaterials for hydrogen evolution reaction. J. Energy Chem. 47, 107–111. doi: 10.1016/j.jechem.2019.11.027
Palm, M. O., Silva Júnior, M. E., Cardoso, L. R., Duarte, D. A., and Catapan, R. C. (2020). On the effect of the washcoat on partial oxidation and steam reforming of ethanol on Ni/Al2O3 monolith in short contact time reactors. Energy Fuels 34, 2205–2213. doi: 10.1021/acs.energyfuels.9b03655
Peng, H., Ma, Y., Liu, W., Xu, X., Fang, X., Lian, J., et al. (2015). Methane dry reforming on Ni/La2Zr2O7 treated by plasma in different atmospheres. J. Energy Chem. 24, 416–424. doi: 10.1016/j.jechem.2015.06.015
Poelman, H., Eufinger, K., Depla, D., Poelman, D., De Gryse, R., Sels, B. F., et al. (2007). Magnetron sputter deposition for catalyst synthesis. Appl. Catal. A 325, 213–219. doi: 10.1016/j.apcata.2007.02.028
Rahemi, N., Haghighi, M., Babaluo, A. A., Allahyari, S., and Jafari, M. F. (2014). Syngas production from reforming of greenhouse gases CH4/CO2 over Ni–Cu/Al2O3 nanocatalyst: impregnated vs. plasma-treated catalyst. Energy Convers. Manag. 84, 50–59. doi: 10.1016/j.enconman.2014.04.016
Rahemi, N., Haghighi, M., Babaluo, A. A., Jafari, M. F., and Estifaee, P. (2013a). Synthesis and physicochemical characterizations of Ni/Al2O3-ZrO2 nanocatalyst prepared via impregnation method and treated with non-thermal plasma for CO2 reforming of CH4. J. Ind. Eng. Chem. 19, 1566–1576. doi: 10.1016/j.jiec.2013.01.024
Rahemi, N., Haghighi, M., Babaluo, A. A., Jafari, M. F., and Estifaee, P. (2013b). CO2 reforming of CH4 over CeO2-doped Ni/Al2O3 nanocatalyst treated by non-thermal plasma. J. Nanosci. Nanotechnol. 13, 4896–4908. doi: 10.1166/jnn.2013.7585
Rahemi, N., Haghighi, M., Babaluo, A. A., Jafari, M. F., and Khorram, S. (2013c). Non-thermal plasma assisted synthesis and physicochemical characterizations of Co and Cu doped Ni/Al2O3 nanocatalysts used for dry reforming of methane. Int. J. Hydrog. Energy 38, 16048–16061. doi: 10.1016/j.ijhydene.2013.08.084
Rouibah, K., Barama, A., Benrabaa, R., Guerrero-Caballero, J., Kane, T., Vannier, R., et al. (2017). Dry reforming of methane on nickel-chrome, nickel-cobalt and nickel-manganese catalysts. Int. J. Hydrog. Energy 42, 29725–29734. doi: 10.1016/j.ijhydene.2017.10.049
Santos, A. M., Catapan, R. C., and Duarte, D. A. (2018). Evaluation of the use of plasma-assisted processes as standard method for supported catalysts production. Braz. J. Vac. Appl. 37, 114–119. doi: 10.17563/rbav.v37i3.1113
Shang, S., Liu, G., Chai, X., Tao, X., Li, X., Bai, M., et al. (2009). Research on Ni/γ-Al2O3 catalyst for CO2 reforming of CH4 prepared by atmospheric pressure glow discharge plasma jet. Catal. Today 148, 268–274. doi: 10.1016/j.cattod.2009.09.011
Sheldon, R. A., Arends, I., and Hanefeld, U. (2007). Green Chemistry and Catalysis. Weinheim: Wiley-VCH.
Shi, P., and Liu, C. (2009). Characterization of silica supported nickel catalyst for methanation with improved activity by room temperature plasma treatment. Catal. Lett. 133, 112–118. doi: 10.1007/s10562-009-0163-0
Silberova, B., Venvik, H. J., and Holmen, A. (2005). Production of hydrogen by short contact time partial oxidation and oxidative steam reforming of propane. Catal. Today 99, 69–76. doi: 10.1016/j.cattod.2004.09.025
Taghvaei, H., Heravi, M., and Rahimpour, M. R. (2017). Synthesis of supported nanocatalysts via novel non-thermal plasma methods and its application in catalytic processes. Plasma Process Polym. 14:1600204. doi: 10.1002/ppap.201600204
Tang, X., Gao, F., Xiang, Y., Yi, H., and Zhao, S. (2015). Low temperature catalytic oxidation of nitric oxide over the Mn–CoOx catalyst modified by non-thermal plasma. Catal. Commun. 64, 12–17. doi: 10.1016/j.catcom.2015.01.027
Tsipouriari, V. A., Zhang, Z., and Verykios, X. E. (1998). Catalytic partial oxidation of methane to synthesis gas over Ni-based catalysts. J. Catal. 179, 283–291. doi: 10.1006/jcat.1998.2182
Veith, G. M., Lupini, A. R., Pennycook, S. J., and Dudney, N. J. (2006). The use of magnetron sputtering for the production of heterogeneous catalysts. Stud. Surf. Sci. Catal. 162, 71–78. doi: 10.1016/S0167-2991(06)80892-X
Wang, B., Chen, B., Sun, Y., Xiao, H., Xu, X., Fu, M., et al. (2018a). Effects of dielectric barrier discharge plasma on the catalytic activity of Pt/CeO2 catalysts. Appl. Catal. B 238, 328–338. doi: 10.1016/j.apcatb.2018.07.044
Wang, H. Y., and Ruckenstein, E. (2001). CO2 reforming of CH4 over Co/MgO solid solution catalysts – effect of calcination temperature and Co loading. Appl. Catal. A 209, 207–215. doi: 10.1016/S0926-860X(00)00753-5
Wang, N., Shen, K., Yu, X., Qian, W., and Chu, W. (2013). Preparation and characterization of a plasma treated NiMgSBA-15 catalyst for methane reforming with CO2 to produce syngas. Catal. Sci. Technol. 3, 2278–2287. doi: 10.1039/c3cy00299c
Wang, Z., Zhang, Y., Neyts, E. C., Cao, X., Zhang, X., Jang, B. W., et al. (2018b). Catalyst preparation with plasmas: how does it work? ACS Catal. 8, 2093–2110. doi: 10.1021/acscatal.7b03723
Wang, Z., Zhao, Y., Cui, L., Du, H., Yao, P., and Liu, C. (2007). CO2 reforming of methane over argon plasma reduced Rh/Al2O3 catalyst: a case study of alternative catalyst reduction via non-hydrogen plasmas. Green Chem. 9, 554–559. doi: 10.1039/b614276a
Wu, Y., Chung, W., and Chang, M. (2015). Modification of Ni/γ-Al2O3 catalyst with plasma for steam reforming of ethanol to generate hydrogen. Int. J. Hydrog. Energy 40, 8071–8080. doi: 10.1016/j.ijhydene.2015.04.053
Xi-zhen, L., Wang, J., Liu, C., He, F., and Eliasson, B. (2003). Partial oxidation of methane to syngas over Ni-Fe/Al2O3 catalyst with plasma enhanced activity. React. Kinet. Mech. Catal. 79, 69–76. doi: 10.1023/A:1024155617001
Xu, C., and Tu, X. (2013). Plasma-assisted methane conversion in an atmospheric pressure dielectric barrier discharge reactor. J. Energy Chem. 22, 420–425. doi: 10.1016/S2095-49561360055-8
Yan, X., Liu, Y., Zhao, B., Wang, Z., Wang, Y., and Liu, C. (2013). Methanation over Ni/SiO2: effect of the catalyst preparation methodologies. Int. J. Hydrog. Energy 38, 2283–2291. doi: 10.1016/j.ijhydene.2012.12.024
Zhang, Y., Chu, W., Cao, W., Luo, C., Wen, X., and Zhou, K. (2000). A plasma-activated Ni/α-Al2O3 catalyst for the conversion of CH4 to syngas. Plasma Chem. Plasma Process. 20, 137–144. doi: 10.1023/A:1006978012228
Zhang, Y., Laer, K. V., Neyts, E. C., and Bogaerts, A. (2016). Can plasma be formed in catalyst pores? A modeling investigation. Appl. Catal. B 185, 56–67. doi: 10.1016/j.apcatb.2015.12.009
Zhao, B., Yao, Y., Shi, H., Yang, F., Jia, X., Liu, P., et al. (2019). Preparation of Ni/SiO2 catalyst via novel plasma-induced micro-combustion method. Catal. Today 337, 28–36. doi: 10.1016/j.cattod.2019.04.068
Zhu, B., Li, X., Liu, J., Liu, J., Zhu, X., and Zhu, A. (2015). In-situ regeneration of Au nanocatalysts by atmospheric-pressure air plasma: significant contribution of water vapor. Appl. Catal. B 179, 69–77. doi: 10.1016/j.apcatb.2015.05.020
Zhu, X., Huo, P., Zhang, Y., Cheng, D., and Liu, C. (2008). Structure and reactivity of plasma treated Ni/Al2O3 catalyst for CO2 reforming of methane. Appl. Catal. B 85, 132–140. doi: 10.1016/j.apcatb.2007.11.042
Zhu, X., Huo, P., Zhang, Y., and Liu, C. (2006). Characterization of argon glow discharge plasma reduced Pt/Al2O3 catalyst. Ind. Eng. Chem. Res. 45, 8604–8609. doi: 10.1021/ie060735y
Zou, J., Liu, C., and Zhang, Y. (2006a). Control of the metal-support interface of NiO-loaded photocatalysts via cold plasma treatment. Langmuir 22, 2334–2339. doi: 10.1021/la052135u
Keywords: non-thermal plasmas, supported metal catalysts, green chemistry, heterogeneous catalysis, energy conversion
Citation: Santos AM, Catapan RC and Duarte DA (2020) The Potential of Non-thermal Plasmas in the Preparation of Supported Metal Catalysts for Fuel Conversion in Automotive Systems: A Literature Overview. Front. Mech. Eng. 6:42. doi: 10.3389/fmech.2020.00042
Received: 04 April 2020; Accepted: 19 May 2020;
Published: 07 July 2020.
Edited by:
Rodrigo Sávio Pessoa, Aeronautics Institute of Technology (ITA), BrazilReviewed by:
Marwan Nafea, University of Nottingham Malaysia Campus, MalaysiaCopyright © 2020 Santos, Catapan and Duarte. This is an open-access article distributed under the terms of the Creative Commons Attribution License (CC BY). The use, distribution or reproduction in other forums is permitted, provided the original author(s) and the copyright owner(s) are credited and that the original publication in this journal is cited, in accordance with accepted academic practice. No use, distribution or reproduction is permitted which does not comply with these terms.
*Correspondence: Diego A. Duarte, ZGllZ28uZHVhcnRlQHVmc2MuYnI=
Disclaimer: All claims expressed in this article are solely those of the authors and do not necessarily represent those of their affiliated organizations, or those of the publisher, the editors and the reviewers. Any product that may be evaluated in this article or claim that may be made by its manufacturer is not guaranteed or endorsed by the publisher.
Research integrity at Frontiers
Learn more about the work of our research integrity team to safeguard the quality of each article we publish.