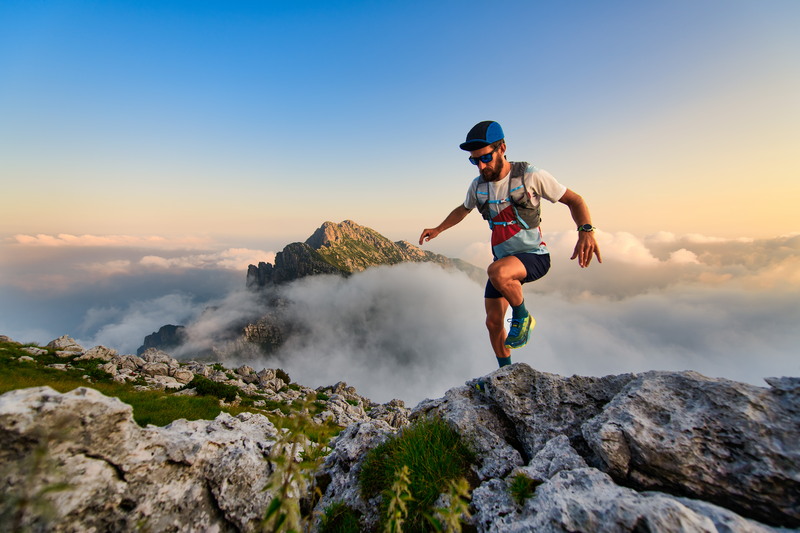
95% of researchers rate our articles as excellent or good
Learn more about the work of our research integrity team to safeguard the quality of each article we publish.
Find out more
HYPOTHESIS AND THEORY article
Front. Mech. Eng. , 03 September 2019
Sec. Tribology
Volume 5 - 2019 | https://doi.org/10.3389/fmech.2019.00055
There is an increasing diffusion of the industry 4. 0 concept today. The fourth industrial revolution, following three other previous industrial revolutions, is considered related to the introduction of modern information and communication technologies in production. Tribological concepts are much older than industry. Tribology has always been connected to industrial problems from the birth of industry. It was strongly connected with the previous industrial revolutions and it is surely related to industry 4.0. In this work, the main aspects of the four industrial revolutions and the main evolutions of tribology are firstly reviewed from a historical point of view. The relationships between tribology and industry are described with particular attention to the aspects that relate the modern tribology 4.0 to industry 4.0. Tribology can have in particular a big impact on the industrial needs to reduce losses and wastes, for instance with the development of new tribological components and materials also in connection with electronic smart systems and taking advantage of the information and communication technologies.
The name industrial revolution is usually connected to a certain historical period at the end of the eighteenth century. However, during the recent years a new industrial revolution labeled industry 4.0 has been defined (Kagermann et al., 2011) considering the existence of three previous industrial revolutions. Actually many subjects of industry 4.0 are not new, but it is the manner or the point of view from which they are considered that is new. In industry 4.0 the physical world merges with the virtual; information technology, telecommunications and manufacturing are linked together. Since the definition of industry 4.0 there has been an increasing diffusion of its concepts, with a continuous flowering of conferences, meetings, seminars, symposia, fairs, webcasts and webinars focused on industry 4.0. Particularly there is an exponential development of publications regarding with industry 4.0 today (Lu, 2017), including books, proceeding of specific conferences, doctoral and master theses (Bartodziej, 2017), journals (Liao et al., 2017; Pfeiffer, 2017), almost all related to manufacturing, production ad economy.
Tribology is the science that deals with every problem of friction, wear and lubrication. The name tribology officially arises from the so called Jost Report dated 1966 (Jost, 1966) (“Tribology is the science and technology of interacting surfaces in relative motion and of the practices related thereto”), but tribological concepts, as for instance the way to reduce friction using rolling elements and lubricants, are much older than industry (Frêne et al., 1997; Dowson, 1998). There is a vast literature on tribology, including specific journals, proceedings of conferences and particularly books (Tabor and Bowden, 1973; Halling, 1975; Czichos, 1978; Jones and Scott, 1983; Stolarski, 1990; Hutchings, 1992; Stachowiak and Batchelor, 1993; Williams, 1994; Goryacheva, 1998; Gohar and Rahnejat, 2008; Khonsari and Booser, 2008). Tribology is highly interdisciplinary involving many research fields as physics, mathematics, chemistry, materials science and engineering, and therefore connecting basic and applied sciences. This makes it very fascinating but also very complex. However, tribology continues to be unknown to most people despite its enormous contribution to the industrial world as well as to the everyday life. This could be related to its complexity (tribological problems are generally not simple) but also to the limited diffusion of its name (it is quite common to speak with someone that heard the word tribology for the first time even if facing with friction problems everyday). A better communication to people will surely help the knowledge of tribology. As stated in Popov (2018), tribology has had relatively low visibility among both the engineering world and the general public, but there is the hope that the new research areas will produce a “golden age” of tribology in the coming years. The industrial world is full of machines of every kind that contain moving parts contacting each other. Tribology is of fundamental importance for understanding what happens at these interfaces and is essential for design and reliability of the machines. For instance, there is a strong request today for machines that use less energy for the same output and have components that last longer in service, and tribology can play a very important role for their design and for online monitoring of lubricants to increase the lifetime of the components.
In this work, based on heterogeneous data sources, the industrial revolutions and the historical progresses of tribology are firstly reviewed. The relationships between tribology and industry are presented and the key aspects of industry 4.0 and tribology 4.0 are reported to evidence the extreme importance of tribology for industry.
Four industrial revolutions are often mentioned today. This essentially arose after the definition of industry 4.0 in order to be coherent with its definition. According to this, somebody names today even industry 1.0, industry 2.0, and industry 3.0 the three previous industrial revolutions briefly described in the following. In literature there are some discrepancies regarding with the exact periods of these revolutions (Lele, 2019). Starting from the second half of the eighteenth century, when everybody agrees that the (first) industrial revolution started with the development of the mechanization, different time lapses ranging usually between four and ten decades have been usually indicated as the length of every revolution. It is not the intention of the author to present a comprehensive history of the industrial revolutions (Xu et al., 2018; Lele, 2019), but just to propose a frame for the tribological studies mainly related to the progresses of industry.
The first industrial revolution, commonly known as industrial revolution, the “age of steam” (Xu et al., 2018), is characterized by the use of the steam machine (Dalenogare et al., 2018). It is related to mechanization and connected to the transformation from an agricultural to an industrial world. It began at the end of the eighteenth century. It was characterized by the introduction of water- and steam-powered machines in manufacturing so that the steam engine, the textile industry and the mechanical engineering are its fundamental aspects (Lele, 2019). Its duration is often indicated from the end of the 18th to the beginning of to 19th century. Sometimes specific decades are indicated, as 1760–1840 (Lele, 2019) and 1750–1850 (Dowson, 1998). The year 1784, when the first power loom was built, is often indicated as a key date for this revolution (Kagermann et al., 2013).
The so-called second industrial revolution, the “age of electricity” (Xu et al., 2018), related to mass production, connected to the intensive use of electrical energy, occurred between the end of the 19th and the beginning of the 20th century [1840–1900, according to Lele (2019)]. It was characterized by the introduction of electricity and petroleum in mass production, by the intensive division of labor, and by the development of railway and steel industry (Lele, 2019). The year 1870, when the first assembly line was used on a large scale in slaughterhouses, is sometimes indicated as a key date (Kagermann et al., 2013).
The third industrial revolution, the “information age” (Xu et al., 2018), characterized by the extensive digitization (computerization). It is the entrance of the first generation information and communication technology (ICT) in industry. Industry 3.0 started in the middle of twentieth century, during the 1960s. Some thinkers consider its conclusion around the 1990s (Lele, 2019) or in 2000, while others think that it is still continuing at the present days smoothly transforming into the new age of industrialization, the fourth industrial revolution. It is characterized by the use of electronics and information technologies (digital revolution) in industry. MODICON 084, the first programmable logic controller (PLC) brought the PLC into commercial production in 1969. This date is sometimes indicated as the key date (Kagermann et al., 2013).
The fourth industrial revolution, the “age of cyber physical systems” (Xu et al., 2018) or the digital revolution, is characterized by the linkage of real objects and people with virtual objects using the network. Its key element is the deep change in the manufacturing systems connectivity thanks to the integration of ICT, Internet of Things (IoT) and machines in the so-called cyber-physical systems (CPS) (Kagermann et al., 2013; Dalenogare et al., 2018). Its starting point is often considered at the beginning of the 21st century. A key date is the year 2011, when the term industry (“Industrie” in German) 4.0 appeared for the first time during the industrial trade fair Hannover Messe (Kagermann et al., 2011) as a high-tech strategy of the German industry. The German working group on industry 4.0 was successively created that defined the industry 4.0 environment in its final report (Kagermann et al., 2013). The concepts of industry 4.0 spread then to other countries and was definitively adopted at the 2015 World Economic Forum Annual Meeting as reported in Pfeiffer (2017). The fourth industrial revolution is taking over the third one smoothly. In the view of some thinkers the term “evolution” is more appropriate than “revolution” for the ongoing changes because the main elements already exist and only some further developments occur (Bartodziej, 2017). In any case the major transformation is toward digitization.
Key aspects of industry 4.0 are reported in a following specifically dedicated section.
The four industrial revolution are schematically represented in Figure 1.
Figure 1. The four industrial revolutions. From the Wikimedia Commons. Christoph Roser at AllAboutLean.com licensed under the Creative Commons Attribution-Share Alike 4.0 International license (Roser, 2015).
Tribology has had a continuous evolution during time. Even if, as already mentioned, the official definition of tribology arises from the so called Jost Report (Jost, 1966), tribological concepts were applied since the prehistoric epoch and are much older than the industrial ones. A brief review of some fundamental progresses of tribology during the several epochs is reported below, mainly based on what is reported in Frêne et al. (1997), Dowson (1998), and Bartz (2001). It is not intention of the author to furnish in this section a detailed review of references, a very hard task due to the vastness of the subject, but just to mention some fundamental subjects and people in order to give a sufficiently wide idea of the developments of tribology during the different epochs. The fundamental tribological progresses are presented in a mainly chronological way also in relation to the epochs of the industrial revolutions, even if there can be obviously other potential ways to identify large steps in tribology research and development.
In the monumental work of Dowson (1998) tribological developments are framed inside some time lapses starting from the prehistoric epoch (the stone age) until 3500 before Christ (B.C.), when the generation of fire by friction between two pieces of wood can be considered as one of the first example of tribological applications.
Several finds show examples of friction reduction for moving heavy objects during early civilization, between 3,500 and 900 B.C., as stone sockets for the lower pivot of doors lubricated with bitumen or animal fat and wood cylindrical pieces placed below heavy monuments. In some Egyptian bas-relieves dated around 2,000 B.C., showing the transports of stone colossuses on slides, men pouring liquids (lubricants) appear in front of the slides.
The Greek and Roman epoch, from 900 B.C. to 400 A.D. (Anno Domini), was characterized by developments in journal bearings and gears. The first designs of roller bearings appeared; a famous example is the rolling bearing for rotating platforms on Roman ships found at the bottom of lake Nemi in Italy, dated around 50 A.D. Vegetable and animal oils were used as lubricants and it was known that friction and wear could be reduced by the use of certain pairs of materials.
In the Middle Ages, roughly from 400 to 1,450, an epoch with a certain stagnation or even regression, no significant improvements in the field of tribology occurred. Some metallic bearings in China were developed since around the year 900 and several mechanical clocks were built using also metal gears and brass journal bearings toward the end of this epoch.
The epoch of Renaissance, from 1450 to 1600, was marked out by several tribological developments, particularly related to friction, but with some difficulties to transfer the new theories into practice. This can be considered the era of Leonardo da Vinci, exceptional precursor in many fields, author of innumerable inventions several of which remained at the theoretical stage and only later were developed or even reinvented. He was involved in many aspects of machine elements, friction and wear. His studies on friction are shown by many drawings in the so-called codices (Hutchings, 2016). One of Leonardo's most famous drawing in the field of tribology is the ball bearing with a cage used to reduce friction avoiding the contact between the rolling bodies (da Vinci, 1493). He is considered as the first well-known tribologist.
During the epoch of the rising industrial revolution, from 1600 to 1750, outstanding improvements in the field of bearings and gears occurred. The geometrical principles of gears were defined and some machinery to open doors with worm gears and conical bearings were built. The application of lubricants became more and more important. Studies on friction developed remarkably with several scientists involved in them, as Hook (relationships of rolling friction), Newton (definition of inner friction in fluids, introducing what later will be defined viscosity), Amontons (experimental work and laws on friction), and Euler (analytical approach to friction and definition of the friction coefficient).
The epoch from 1750 to 1850 was characterized by improved designs of machine elements. It was the era of Watt and his steam engine. New gears, journal bearings (also for railway), roller bearings and lubricants (mineral oils, lubricant formulations and solid lubricants) were developed. Very important studies on friction were made by Coulomb (1782) that confirmed the laws of Leonardo da Vinci and Amontons. The word viscosity was coined by Navier that defined with Stokes the well-known equations. Poiseuille performed his studies on fluid flow in a pipe.
About a century (from 1850 to 1940) of technical progress follows the previous epoch, with several further developments in bearings and lubrication. The relationship between friction, wear and lubrication was investigated. The hydrodynamic pressure development in journal bearings was discovered by Tower, the hydrodynamic friction was investigated by Hirn and the rolling friction by Hertz. Reynolds developed his well-known equation for the hydrodynamic pressure that is the basis for the calculation of bearings (Reynolds, 1886). Stribeck determined his curve showing the relationship between friction, load, speed and viscosity; Sommerfeld proposed an analytical solution of Reynolds' equation and the Sommerfeld number. Rolling bearings were developed by Wingquist, founder of SKF. The first additives were put in oils. Many scientists and engineers were involved in theoretical aspects of journal and thrust hydrodynamic bearings at the beginning of the 20th century, as Michell, Stribeck, Kingsbury, Rayleigh, Gümbel. Particular types of bearings were also invented, as the tilting pad (Michell, Kingsbury) and the step (Rayleigh) bearings, and hydrostatic lubrication was also introduced. During the 1930s further analytical and approximate solutions of the Reynolds equation were proposed by Swift, Stieber, and Kingsbury. The relationship between scuffing and the total transient temperature that includes the flash temperature was proposed by Blok.
The time span from the 1940s to the 1960s can be considered the starting epoch of the Elastohydrodynamic lubrication (EHL) theory, the fundamental kind of lubrication for rolling bearings and gears that takes into account, in addition to the hydrodynamic effect, the effects of elastic deformation of the contacting bodies and the dependence of the viscosity of the lubricant on pressure. Starting from the so called Grubin's formula published in 1949 for the evaluation of the minimum film thickness, that more correctly should be mentioned as Ertel-Grubin formula (Popova and Popov, 2015; Morales-Espejel and Wemekamp, 2018), numerical solutions were obtained in the late 1950s by Dowson and Higginson (1966). Further developments were also produced in other tribological fields. The approximate solution for short journal bearings was also proposed by Ocvirk and Du Bois. Starting from the 1950s, the first numerical solutions were proposed by Cameron and Wood and then by Pinkus, Raymondi, and Boyd. Friction studies progressed with the development of the adhesion theories. Bowden and Tabor proposed their simple relationship for the friction coefficient as the ratio of the shear stress and the hardness of the asperity junctions. Archard investigated wear problems producing the classical equation for the volume of worn material.
The epoch from the late 1960s to the late 1990s is characterized by the birth of the “official” tribology, commonly dated in 1966 with the Jost Report (Jost, 1966) that highlighted the economic importance of tribology for a bigger reliability and efficiency of the mechanical systems thanks to the possible reductions of friction and wear. Tremendous progresses in both understanding of fundamental aspects of tribology as well in its industrial applications occurred some of which are reported in the following. Elastohydrodynamic studies continued with numerical extension to point contacts thanks also to the availability of the new powerful computers (Hamrock and Dowson, 1981). Non-Newtonian rheological models (for instance the one of Bair and Winer) were developed that allowed more realistic evaluation of friction and therefore of power losses. Both computational and experimental developments (optical interferometry for film thickness evaluation) and several experimental studies allow investigations up to mixed and boundary lubrication conditions, including the presence of asperity contacts (micro-EHL), very thin film lubrication and non-steady state conditions (for instance Spikes and Kaneta). Further developments in very low friction bearings, as air lubricated (Gross, 1962) and magnetic (Moon, 1993) bearings, and in hydrostatic lubrication (Bassani and Piccigallo, 1985). Surface engineering aspects were further investigated: it's worth mentioning the contact mechanics studies of Greenwood with the introduction of the plasticity index, and the studies on friction up to the atomic scale of molecular dynamics and experimentally with the surface force apparatus (SFA) and atomic force microscope (AFM). Tribology of magnetic storage systems also developed (Bhushan, 1999). Several nondimensional groups useful for lubrication and contact mechanics studies were developed by Blok, Greenwood, Johnson, Dowson, Higginson, Hamrock, Moes. New fundamental studies on wear were performed (Kimura, Ludema, and Kato, just to mention a few). Progress in reducing wear was also performed with new materials and coatings, particularly with physical or chemical vapor deposition (PVD or CVD), as diamond like carbon (DLC) coatings. The third body concept was also introduced (Godet, 1984). Advances in non-metallic bearings occurred; the PV (pressure times velocity) factor became a well-established criterium for material selection of bearings. Lubricant technology also developed with the use of new solid lubricants and synthetic lubricants and additives. Condition monitoring started to be applied particular in large-scale production where the downtime (machine-stops) produce big economical losses. Temperature and vibrations are the most common monitored quantities, but also checks of the lubricant conditions through techniques such as ferrography was recognized to be very useful. Studies on lubrication and wear of synovial joints started and the term “Biotribology” was officially introduced by Dowson in 1970, including other topics as wear of dental tissues and replacement heart valves, tribology of skin and friction of hair.
From 2000 to today is the present tribology epoch. Further developments occur in all previously mentioned fields. Tribology involves more and more scientific, environmental and socioeconomic aspects. Tribological studies regard several aspects of transports, as road, rail and engines, machine components, machining processes (grinding, turning, …), cold/hot forming processes, atomic scale investigations, industrial applications of micro and nano mechanics, information systems (storage technology), bio-technology (new biomaterials and biomedical applications), new materials (ceramics), surface texturing and coatings, lubricants (ionic liquids) and additives. There is a significant development of the environmental friendly tribology, or ecotribology; the term “Green Tribology” is introduced by Zhang in 2001. Superlubricity and hydration lubrication concepts are introduced by Klein. Space tribology is also developed for aerospace applications. The term “Tribotronics,” or active tribology, integrating tribology and electronics, is coined at Luleå University of Technology (2008). Smart tribological systems, including models. sensors and actuators, need to be developed to improve performances of industrial machinery. The tribological researches of this epoch more connected to industry 4.0 are reported in more detail below.
The tribology evolutions are schematically represented in Figure 2. Some important tribological achievements are shown connected to the beginning of each industrial revolution, as highlighted in the next section. A logarithmic scale is used for time on the abscissa with the full scale coincident with the present year.
Figure 2. The tribology evolutions. From the left: Egyptian bas-relief with a man pouring lubricants (adapted from Newberry and Fraser, 1895); Rotating platforms on Roman ships of lake Nemi (adapted from Ucelli, 1950); ball bearing of Leonardo da Vinci (adapted from da Vinci, 1493); experimental test on friction of Coulomb (adapted from Coulomb, 1782); principles of the hydrodynamic lubrication (Reynolds, 1886); meeting of the working group of the department of education and science lubrication engineering, London 1966; schematic drawing of a computer connected electronic system for measuring gear tooth temperature at the Research Center on Advanced Technology Mechanical Transmissions of the University of Pisa; smart experimental system at the laboratory for Rotordynamics and Bearings of the Research Center for the Mechanics of Turbomachinery of the University of Pisa.
Tribological developments surely influenced the technical progresses connected to the industrial revolutions. From the other side, the innovations related to the industrial revolutions introduced new tribological problems to be solved.
Looking at the industrial progresses as a continuum, speaking of evolutions rather than of revolutions, four time spans can be considered for the four Industrial and Tribological evolutions: from 1750 to 1850, from 1850 to 1950, from 1950 to 2000, and from 2000. Some fundamental aspects of industry and tribology during these time spans are summarized in Table 1. The commonly considered beginning of every industrial revolution can be put in relation to some important tribological developments that occurred in close years. The beginning of the first industrial revolution (1784) is characterized in the field of tribology by the studies on friction performed by Coulomb (1781), the beginning of the second one (1870) by the lubrication developments of Reynolds (1886), the start of the third one (1969) by the birth of the “official” tribology (1966) and the beginning of the fourth one (2011) by Tribotronics (2008).
Table 1. The fundamental aspects of industry and tribology during the four industrial and tribological evolutions time spans.
Tribology has been always strictly connected to industrial aspects. The importance of the link between tribology and industry is stressed in several books, journals and plenary and invited talks at conferences as particularly the World Tribology Congresses (WTC) starting from the first edition in London in 1997.
Among the books, the needs of industry are reported in Jones and Scott (1983). Indications for the choice of bearings, both sliding and rolling, gears, seals, lubrication and lubrication systems are given. Several worn surfaces of machine components and diagnosis of failures are reported. Other subjects treated in the book are the level of contamination in the lubricant, condition monitoring, health and safety aspects of lubricants, tribology in metal cutting and laboratory test machines. Handbooks have been realized during the years specifically addressed to practical and industrial design, as O'Connor and Boyd (1968) and Neale (1973). More recent developments in reduction of wear and energy consumption are reported in Mang et al. (2011) with an analysis of tribosystems using modern test equipments.
Some journals are specifically addressed to the link between tribology and industry, as tribology in industry, a Journal of the Serbian Tribology Society, and Industrial Lubrication and Tribology, an Emerald Journal.
Among the presentations at WTC's, the link between the academic tribological research and the industrial world is stressed in Neale (1997). In Kato (2009) the need to develop technologies of friction and wear control taking into account sustainability for an energy revolution in industry is reported. Renewable lubricants, water-, nitrogen-, or hydrogen-lubrication, on-demand lubrication, anti-wear coatings, surface texturing, surface modification, non-metallic bulk materials, and life cycle tribology are indicated as the main future research developments of industrial tribology.
In the same manner as industry is mentioned in tribological publications, tribological aspects start to be mentioned in industrial publications. Wear is for instance mentioned in the industry 4.0 report (Kagermann et al., 2013). Another example is the work (Tolochko et al., 2017), included in a book devoted to the changes connected to the new digital landscape of industry 4.0, on new composite materials for industrial applications based on an aluminum and copper matrix with carbon nanofibers. Coefficient of friction and wear loss of the tested materials are presented in a table and tribological applications and the tribological characteristics of the materials investigated are mentioned in the text. The presence of so detailed tribological information in a book specifically addressed to industry 4.0 is a symptom of an increasing awareness of the importance of Tribology.
There are several tribological studies that can have influence on the technologies related to industry 4.0. In the next sessions, the key technologies of industry 4.0 are briefly pointed out and the connections of tribology with some of them are evidenced.
The concept of industry 4.0 is essentially related to increased automation and digital information transfer in manufacturing. Important aspects are the increased power of computers at lower cost, the expansion of wireless communication and networks, the availability of increasingly intelligent robots and machines and the ubiquitous use of sensors. This fourth industrial revolution promises to boost industrial efficiency and productivity (Van Camp, 2018). A question can arise, as for every technological step, if this progress could be useful for the society or only for a few. The advances in technology with increased productivity and costs reduction should be used for reducing resource use and environmental impact, and to produce new or improved products and services for all people (Holdren, 2008). But there is also the risk of loss of millions of jobs counterbalanced only by a reduced number of highly specialized emerging jobs. This aspect should be faced carefully by governments and entrepreneurs (Devezas et al., 2017).
A key concept of industry 4.0 is the Smart Factory where people, machines, and resources communicate with each other as in a social network (Kagermann et al., 2013). The factory should be flexible and safe and able to produce both large series and customized individual products with an optimal use of resources thanks also to the cooperation between humans and robots. In other words, important aspects of the new industrial world are the customization of the products, high performance, ecological sustainability, reconfigurability.
Several technology fields are usually considered related to industry 4.0 because able to affect in a significant manner the manufacturing sector. There are technologies characterized by high know-how and research and development intensity that are often called Key Enabling Technologies (KETs). An essential list of KETs and keywords related to industry 4.0, mainly based on Sendler (2013), Kagermann et al. (2013), Bauer et al. (2014), Santos et al. (2017), Dalenogare et al. (2018), and Ciffolilli and Muscio (2018) is reported below. It's worth to note that some terms are synonymous and some are strongly interconnected each other so that this is just one of the possible ways in which they can be grouped.
Cyber physical systems relate the concepts of internet of things that enables real-time data sharing among all parts of the industrial systems, information and communication technology, internet of services, connectivity, wireless network, cloud computing and services, machine-to-machine communication. Internet of things has brought to have sensors of every kind (biosensors, smart sensors, photonic sensors) used almost everywhere today (Winters, 2018).
Advanced monitoring, diagnostics and maintenance are connected with the use of sensors, wireless sensor network, real-time data acquisition and analysis, signal processing, remote access and control, remote maintenance.
Advanced technologies for energy saving include environment-friendly or green technologies, alternative energy conversion (solar, wind and hydrogen energy production), energy recovery.
Advanced manufacturing solutions with digital-to-physical conversion include flexible manufacturing lines, supervisory control and data acquisition (SCADA), computer-aided design and manufacturing (CAD, CAM), and additive manufacturing, also known as fast prototyping or 3-D printing, that can produce reduction in waste and costs and simplification in assembly (Brown, 2018a).
Advanced engineering technologies and materials include laser, plasma, ultrasound, radiation and optical technologies, microtechnologies for microelectromechanical systems (MEMS), nanotechnologies, new polymers, composite and ceramic materials and coatings, new efficient, and intelligent materials.
Machine learning indicates the capability of a software to analyze big amount of data and to learn how to solve problems automatically. A related concept is adaptive control (the capability of a system to identify the problem and to decide how to modify its operation to achieve the best possible mode of operation). Big data is connected for instance to the use of costumer data to optimize product strategies and the analysis of big amount of data to optimize products and processes.
Human machine interaction includes augmented and virtual reality, wearable technologies, human-machine interface (HMI) or man-machine interface (MMI) (speech-recognition interfaces, touch screens, 3D scanner). Robotics includes autonomous robots, interconnected robots, co-robots (or collaborative robots, robots working together with people) allowing the human labor to be addressed toward more value-added activities.
It is worth noting that a keyword frequently used in industry 4.0 publications and conferences is the word “smart.” It is mainly used for defining something related with interconnectivity and automation. Some samples are: smart applications, smart grid, smart manufacturing, smart systems, smart technologies, smart objects, and also smartifying industry as reported in Gerdin (2016).
The contribute of tribology in industry 4.0 can be very important. Many tribological studies can have a direct or indirect influence on the technologies mentioned in the above section. This relationship can be expressed in a concise way with the term “Tribology 4.0.” Most probably the most direct connection between tribology and industry 4.0 occurs through the information and communication technologies. Tribological data are transferred to industry using internet and wireless connections among several electronic devices. However, several other relationships can be found with the key technologies of industry 4.0. An attempt to organize the different tribological subjects in relation to the key technologies of industry 4.0 is reported below.
The connection of tribology with electronics (sensors) and informatics (computers, internet) is today extremely strong. The need of reliable and affordable on-line sensors providing information on both lubricant and machinery wear condition in order also to reduce manpower needs was already stated in Murphy et al. (2005). The connection between tribology and electronics is well-highlighted by the term “Tribotronics” (Glavatskih and Höglund, 2008). The smart machines are intelligent devices able to monitor and change their own conditions thanks to the use of sensors and actuators. Smart tribological systems, including models, sensors and actuators, can improve the performances of industrial machinery. They should be self-adjusting including on-line tuning of tribological systems to optimize performances. Live data related particularly to wear, friction, vibrations and temperatures can be recorded and used to improve the performances of the tribological systems so that efficiency and reliability of the entire machine are increased. For instance sensors can monitor the conditions of the surfaces and of the lubricant in the machines and through communication systems the information is transferred for control and possible consequent actions. In this way the machines are connected into internet of things establishing typical cyber-physical systems. Possible actuation mechanisms could modify the geometry of tribological components. For instance active controlled bearings can be used, as the actuated tilting pad journal bearings reported in Salazar and Santos (2017a,b). The use of a feedback-controlled or active lubrication allows further vibration reductions with suppression of resonant vibrations thus improving the whole dynamic performance of turbomachinery. The properties of the lubricant can be controlled by using smart materials as magneto-rheological and electro-rheological fluids (Phulé, 2001) and active control of friction can be realized by electronic control of fluid viscosity (Nakano et al., 1995) or by transverse oscillations (Benad et al., 2019). Progresses on bearings can be directly pushed by the internet of things (Brown, 2018b).
The fundamental role of tribology in maintenance engineering is well-known (Kimura, 1997; Tung et al., 2005). When a machine is working, it is of fundamental importance to detect possible problems as soon as possible in order to reduce its downtime and the related costs. Tribology is involved in the improvements in life prediction of components, as rolling bearings (Ioannides, 1997), in the investigation on the failure mechanisms and in the diagnostic analysis and prognostic predictions (Holmberg, 2001), in maintenance of operating machinery (Roylance, 2003). Rolling bearings with integrated sensors, measuring torque, force, vibrations and temperatures, have been developed, as for instance the sensor bearing with encoder unit reported in Mathé and Grellier (2016), or even a combination of sensors, power, and diagnostics and communications within the bearings for a complete condition monitoring system (Howieson, 2014). Online monitoring of lubricants in machinery is essential for increasing the lifetime of the lubricated components. Real time measurement of wear debris in the lubricant are performed (Iwai et al., 2010), but often vibration analysis is used, in combination with wear debris analysis or not, for fault diagnosis of machinery containing rolling bearings and gears (Peng and Kessissoglou, 2003; Tandon et al., 2007; Randall, 2016). Several examples of techniques used for tribological condition monitoring are reported in Marklund (2017). Maintenance-free mechanical assemblies are required in space applications; the study of tribological interactions is important for industrially relevant applications in the space environment (Krick et al., 2013).
The importance of tribology for energy saving is well-evidenced in Holmberg and Erdemir (2017) where the impact of friction and wear on energy losses also from economical and emissions points of view is presented. It is shown in the paper that about 23% of the world's energy consumption, the energy used by people for their activities, mainly related to transportation, manufacturing, power generation, and residential, originates from tribological contacts. The contribute of tribology is fundamental both at the design stage of industrial components or systems and during their working (monitoring, corrective actions based on friction-wear-lubrication problems). Efficiency, performance, maintainability and lifetime of machine elements as seals, bearings and gears can be dramatically increased by a correct tribological design. There is a high industrial demand nowadays toward higher power density machines with higher efficiency. Reduced dimensions to have lighter machine components are consequently requested. To achieve the same or even higher power than in the former machines higher speeds are necessary that are normally connected to hotter operating conditions. Environmental aspects and costs are also taken into account which brings to the employment of minor quantities of lubricant, related again to higher temperatures. In these ways more severe conditions for the lubricated contacts are reached so that their design becomes extremely complex and tests on real machine components are necessary (Ciulli, 2019). Tribological studies related to transports (cars, airplanes, helicopters, trains) can have a big impact on the environment due to the enormous number of means of transport around the world. Automotive tribology is still an open issue; applications of tribological results to the world of cars is probably one of the most visible example of how tribology can have a great impact on energy and environmental issues (Masuko and Sugimura, 2017). Studies on engines are reported for instance in Woidt (1997) and Erdemir et al. (2017). Particle emissions is another important problem related to vehicles. One of the main source of emission of small polymer particles (microplastics) in the environment is tire wear (Kole et al., 2017; Sommer et al., 2018). According to Kole et al. (2017), pollution produced by wear and tear from tires is as important as the one produced by plastic bottles and bags and could therefore produce some effects on human health. Tribological studies can be very useful for a reduction in particle emission from tires (Foitzik et al., 2018) and also from brakes (Perricone et al., 2018; Joo et al., 2019).
Bearings and gears, mainly for automotive and aeronautical applications, are surely among the most investigated components. New bearings and gears are under development for a completely new aeronautical engine, the LEAP (Leading Edge Aviation Propulsion) that represents one of the major recent technological advances (Halimi, 2018). Rolling bearings constitute one of the classical example of components that have reduced their size during the years. The improvements in their design has taken during 100 years of bearing evolution to bearings with reduced size and friction, high carrying capacity, higher speed, and longer life (Weidinger, 2009; Grellier and Re, 2014; Landerl, 2018). The minimization of the use of lubricants for bearings is reported in Schmidt and Schwartz (2014). The hybrid bearings, with steel rings and silicon nitride rolling elements, show good performance in severe conditions such as poor lubrication and contaminated conditions (Vieillard et al., 2017). Studies on gears are performed to eliminate (or at least to reduce) noise and vibrations, to increase power density (to use smaller and lighter gearboxes than before), to realize low-loss gears by minimizing the quantity of lubricant necessary. Gears, with reduced quantities of oil are for instance tested in Ebner et al. (2018). A final target could be to arrive to oil-free powertrain, as well as to oil-free engines (Woidt, 1997). All these tribological studies are very important for a sustainable development that meets the present human needs and the integrity and stability of the environment. More generally, tribology can have influence, directly or indirectly, on several of the 17 United Nations sustainable development goals (United Nations, 2015), such as the goal 3, good health and well-being for people (think to biotribology), goal 7, affordable and clean energy (improving energy efficiency by friction reduction), goal 12, responsible consumption and production (reducing material waste by reducing wear), and goal 13, climate action (reducing emissions by friction losses reduction). A big effort has been done toward new ecological lubricants and sustainability of tribology. The importance of increasing environmental compatibility minimizing health and water hazards is reported in Bartz (1997). Novel and environmentally friendly lubrication concepts and additives are under development. Several aspects of green tribology are treated in Nosonovsky and Bhushan (2012) and Bhushan (2013).
Alternative energies can pose new tribological problems. Wind turbines constitute a significant example because their maintenance problems. New bearings, surface treatments as the black oxidation and lubrication systems are developed for wind turbines (Stadler et al., 2015; Bittorf and Slembeck, 2016; Hofmann, 2017). Condition monitoring of wind turbines helps to control operation and maintenance costs (Drommi, 2017).
Tribology in manufacturing is another important tribological research field. Hot metal forming (friction and heat transfer) is for instance investigated in Beynon (1997), while the importance of the reduction of fluids is reported in Shareef and Natarajan (2005). The Minimum Quantity Lubrication (MQL), an efficient method of applying cutting fluids by minimizing their amount, is today important in machining processes, being environmentally friendly and reducing costs (Emami et al., 2014; Li et al., 2017).
Tribology can contribute to the development of additive manufacturing with tribological investigations on the new printed products in order to investigate their surface mechanical characteristics (friction, wear, lubricant interaction). Additive manufacturing can be used to integrate sensors and actuators directly into machine components.
Polymer and ceramic tribology, micro- and nanotribology, and nanotechnology, investigating for instance nanoparticles to increase material resistance, nanocoatings and nano-reinforced materials, and the development of 2D materials like graphene are surely related to development of new advanced techniques and materials. Attention should be payed to the potential toxicity of the new materials and their structures. Biomimetics can be helpful for this, learning from living nature which materials and nanostructures are not toxic.
Big data is a concept that can be related to tribology in several ways. Tribology networks and databases of tribological data (for instance friction coefficient or wear data) already exist. Big quantity of data from disparate instruments and sensors are captured particularly in transient tribological experimental tests (Ciulli, 2019). Data are often recorded on magnetic storage systems, with their tribological problems.
Human machine interaction and wearables are related to tribological aspects at the interface, as friction and wear problems of the skin.
Friction, wear and lubrication problems of joints in robots have to be solved, particularly to avoid vibrations and allow precise positioning.
Tribological concepts have been applied since antiquity. Tribology plays a fundamental role both in technological and economical fields so that it has always been connected with industry since the first industrial revolution. According to Stachowiak (2017), “during the industrial revolution … it became clear that without advancements in tribology the technological progress would be limited.” Tribological, as more generally scientific and technological progresses, can influence industrial developments. At the same time the industrial changes and the connected problems can stimulate new advances in tribology (for instance new devices can need new materials, coatings and lubricants).
It is possible today to find several concepts of industry 4.0 in tribological researches. Taking into account tribological aspects from the design stage of an industrial component or system can have a huge impact on wear and on friction losses of the machines, so on their reliability and efficiency and emissions. Monitoring with adequate sensors quantities as wear, friction, vibrations and temperatures can furnish data to be used to improve the performances of the tribological industrial systems and to avoid or at least to reduce expensive downtime. Energy saving is surely one of the widest fields where tribology can have a big impact on the industrial need to reduce losses and wastes, for instance with the development of new tribological components (as the everywhere used bearings and gears) and materials (including new environmental friendly lubricants) also taking advantage from new electronic smart sensors and actuators.
Tribological knowledge and data can be easily transferred to the industrial world particularly taking advantage from the industry 4.0 information and communication technologies. Tribology networks and databases of tribological data can furnish to industry important information using internet and wireless connections among several electronic devices.
The new smart sensors could push progresses also in other tribological research fields such as biotribology. Biotribology can give a great help to medical engineering in the frame of 4.0. Every time that something is inserted in the human body, from artificial joints to endoscopes and to small capsules, there is a tribological problem (contacting surfaces, lubrication). Ingestible sensing capsules are an example of sensors collecting data that can be seen online by both users and physicians thanks to smart phones connected to the internet (Kalantar-zadeh et al., 2017). The interaction between the skin and wearables, that can be used for instance for health monitoring and diagnostics, as fitness trackers or for interactive communications, is another interesting tribological problem.
Cyber physical systems are important for space technology that deserves new tribological solutions, due to the extreme environmental conditions with very large temperature gradients in vacuum and in presence of radiations. Specific lubricants and coatings should be developed.
The development of new micro sensors and micro machines can take advantage on the studies on micro- and nano-tribology and on the synthesis of new materials and coatings, as for instance super-slick and 2D materials like graphene that can produce very low friction and wear.
New industrial progresses have to face with ecological sustainability, climate changes, and pollution. Green tribology can furnish an essential contribute in this field.
The author confirms being the sole contributor of this work and has approved it for publication.
The author declares that the research was conducted in the absence of any commercial or financial relationships that could be construed as a potential conflict of interest.
I would like to thank Harry van Leeuwen of Einhoven University of Technology and Enrica Cane of SKF for the useful discussions and the material provided at the time of the work conception, and the Italian Istituto Poligrafico e Zecca dello Stato for the permission to reproduce an elaborated version of figures from the book Le navi di Nemi. Many thanks also to the reviewers for the several suggestions based on deep analyses from different point of views.
Bartodziej, C. J. (2017). The Concept industry 4.0—An Empirical Analysis of Technologies and Applications in Production Logistics. Wiesbaden: Springer Fachmedien Wiesbaden GmbH.
Bartz, W. J. (1997). “Lubricants and the environment,” in New Directions in Tribology, ed I. M. Hutchings (London: Mechanical Engineering Publications Limited, 103–119.
Bartz, W. J. (2001). “History of tribology—the bridge between the classical antiquity and the 21st century,” in Tribology 2001—Scientific Achievements, Industrial Applications, Future Challenges, eds F. Franek, W. J. Bartz, and A. Pauschitz (Wien: The Austrian Tribology Society, 3–12.
Bauer, W., Schlund, S., Marrenbach, D., and Ganschar, O. (2014). Industry 4.0 - Volkswirtschaftliches Potenzial für Deutschland. Studie. Berlin; Stuttgart: BITKOM (Bundesverband Informationswirtschaft, Telekommunikation und neue Medien e. V.); Das Fraunhofer-Institut für Arbeitswirtschaft und Organisation IAO. Available online at: https://www.produktionsarbeit.de/content/dam/produktionsarbeit/de/documents/Studie-Industrie-4-0-Volkswirtschaftliches-Potential-fuer-Deutschland.pdf
Benad, J., Nakano, K., Popov, V. L., and Popov, M. (2019). Active control of friction by transverse oscillations. Friction 7:74. doi: 10.1007/s40544-018-0202-1
Beynon, J. H. (1997). “Tribology in hot metal forming,” in New Directions in Tribology, ed I. M. Hutchings (London: Mechanical Engineering Publications Limited, 135–139.
Bhushan, B. (2013). “Biomimetics: bioinspired superhydrophobic, self-cleaning/antifouling and low drag surfaces for green tribology,” in Proceedings of the 5th World Tribology Congress WTC2013 (Torino).
Bittorf, A., and Slembeck, M. (2016). Up in the Air or Deep in the Sea, Lubrication is Key. Available online at: http://evolution.skf.com/up-in-the-air-or-deep-in-the-sea-lubrication-is-key/
Brown, A. S. (2018a). Chain reaction. Why additive manufacturing is about to transform the supply chain. Mech. Eng. 140, 30–35. doi: 10.1115/1.2018-OCT1
Brown, A. S. (2018b). IoT puts a new spin on bearings. Mech. Eng. 140, 42–47. doi: 10.1115/1.2018-JUL-3
Ciffolilli, A., and Muscio, A. (2018). Industry 4.0: national and regional comparative advantages in key enabling technologies. Eur. Planning Stud. 26, 2323–2343. doi: 10.1080/09654313.2018.1529145
Ciulli, E. (2019). Experimental rigs for testing components of advanced industrial applications. Friction (2019) 7:59. doi: 10.1007/s40544-017-0197-z
Czichos, H. (1978). Tribology: A Systems Approach to the Science and Technology of Friction, Lubrication and Wear. Amsterdam: Elsevier.
Dalenogare, L. S., Brittes Benitez, G., Ayala, N. F., and Frank, A. G. (2018). The expected contribution of Industry 4.0 technologies for industrial performance. Int. J. Prod. Econ. 204, 383–394. doi: 10.1016/j.ijpe.2018.08.019
Devezas, T., Leitão, J., and Sarygulov, A. (2017). Industry 4.0—Entrepreneurship and Structural Change in the New Digital Landscape. Oxford: Springer International Publishing AG.
Dowson, D. (1998). History of Tribology. 2nd Edn. London and Bury St Edmunds: Professional Engineering Publishing Limited.
Dowson, D., and Higginson, G. R. (1966). Elasto-Hydrodynamic Lubrication. 1st Edn. Oxford: Pergamon.
Drommi, F. (2017). Reducing Wind Turbine Operating Costs through a Statistical Approach. Available online at: http://evolution.skf.com/reducing-wind-turbine-operating-costs-through-a-statistical-approach/
Ebner, M., Yilmaz, M., Lohner, T., Michaelis, K., Höhn, B.-R., and Stahl, K. (2018). On the effect of starved lubrication on elastohydrodynamic (EHL) line contacts. Tribol. Int. 118, 515–523. doi: 10.1016/j.triboint.2017.06.004
Emami, M., Sadeghi, M. H., Diaa Sarhan, A. A., and Hasani, F. (2014). Investigating the Minimum Quantity Lubrication in grinding of Al2O3 engineering ceramic. J. Cleaner Prod. 66, 632–643. doi: 10.1016/j.jclepro.2013.11.018
Erdemir, A., Eryilmaz, O., and Ramirez, G. (2017). “Advances in tribological coatings for more efficient and green transportation technologies,” in Proceedings World Tribology Congress (Beijing).
Foitzik, M.-J., Unrau, H.-J., Gauterin, F., Dörnhöfer, J., and Kochb, T. (2018). Investigation of ultra fine particulate matter emission of rubber tires. Wear 394–395, 87–95. doi: 10.1016/j.wear.2017.09.023
Frêne, J., Nicolas, D., Degueurce, B., Berthe, D., and Godet, M. (1997). Hydrodynamic Lubrication. Bearings and Thrust Bearings. Chapter 1: Tribology from Antiquity to Our Times. Oxford: Elsevier.
Gerdin, S. (2016). The Making of a Smart Industry. Available online at: http://evolution.skf.com/the-making-of-a-smart-industry/
Glavatskih, S., and Höglund, E. (2008). Tribotronics—Towards active tribology. Trib Int. 41, 934–939. doi: 10.1016/j.triboint.2007.03.001
Godet, M. (1984). The third body approach. A mechanical view of wear. Wear 100, 437–452. doi: 10.1016/0043-1648(84)90025-5
Grellier, A., and Re, P. (2014). Longer Life and Lower Energy Use with SKF Sealed Energy Efficient Deep Groove Ball Bearings. Available online at: http://evolution.skf.com/longer-life-and-lower-energy-use-with-skf-sealed-energy-efficient-deep-groove-ball-bearings/
Halimi, S. (2018). A Giant LEAP Forward. Available online at: http://evolution.skf.com/a-giant-leap-forward/
Hamrock, B. J., and Dowson, D. (1981). Ball Bearing Lubrication—The Elatohydrodynamics of Elliptical Contacts. New York, NY: Wiley-Interscience.
Hofmann, M. (2017). New Challenges for Rotor Bearings in the 8-MW Offshore Category. Available online at: http://evolution.skf.com/new-challenges-for-rotor-bearings-in-the-8-mw-offshore-category/
Holdren, J. P. (2008). Science and technology for sustainable well-being. Science 319, 424–434. doi: 10.1126/science.1153386
Holmberg, K. (2001). “Tribology in reliability engineering,” in Tribology 2001—Scientific Achievements, Industrial Applications, Future Challenges, eds F. Franek, W.J. Bartz, and A. Pauschitz (Wien: The Austrian Tribology Society, 13–19.
Holmberg, K., and Erdemir, A. (2017). Influence of Tribology on global energy consumption, costs and emissions. Friction 5, 263–284. doi: 10.1007/s40544-017-0183-5
Howieson, D. (2014). The Future of Condition Monitoring. Available online at: http://evolution.skf.com/the-future-of-condition-monitoring/
Hutchings, I. M. (2016). Leonardo da Vinci's studies of friction. Wear 360–361, 51–66. doi: 10.1016/j.wear.2016.04.019
Ioannides, E. (1997). “Life prediction in rolling element bearings,” in New Directions in Tribology, ed I. M. Hutchings (London: Mechanical Engineering Publications Limited, 281–289.
Iwai, Y., Honda, T., Miyajima, T., Yoshinaga, S., Higashi, M., and Fuwa, Y. (2010). Quantitative estimation of wear amounts by real time measurement of wear debris in lubricating oil. Tribol. Int. 43, 388–394. doi: 10.1016/j.triboint.2009.06.019
Jones, M. H., and Scott, D. (1983). Industrial Tribology—The Practical Aspects of Friction, Lubrication and Wear. Amsterdam: Elsevier.
Joo, B. S., Chang, Y. H., Seo, H. J., and Jang, H. (2019). Effects of binder resin on tribological properties and particle emission of brake linings. Wear 434–435:202995. doi: 10.1016/j.wear.2019.202995
Jost, H. P. (1966). Lubrication (Tribology) Education and Research, A Report on the Present Position and Industry's Needs. London: Her Majesty's Stationary Office, Department of Education and Science.
Kagermann, H., Lukas, W.-D., and Wahlster, W. (2011). Industrie 4.0: Mit dem Internet der Dinge auf dem Weg zur 4. Industriellen Revolution (Industry 4.0: with the Internet of Things towards the 4th Industrial Revolution). Available online at: http://www.vdi-nachrichten.com/Technik-Gesellschaft/Industrie-40-Mit-Internet-Dinge-Weg-4-industriellen-Revolution
Kagermann, H., Wahlster, W., and Helbig, J. (2013). Securing the Future of German Manufacturing Industry. Recommendations for Implementing the Strategic Initiative INDUSTRIE 4.0. Final Report of the Industrie 4.0 Working Group. Munich: Acatech, National Academy of Science and Engineering.
Kalantar-zadeh, K., Ha, N., Ou, J. Z., and Berean, K. J. (2017). Ingestible sensors. ACS Sensors 2, 468–483. doi: 10.1021/acssensors.7b00045
Khonsari, M. M., and Booser, E. R. (2008). Applied Tribology Bearing Design and Lubrication. Chichester: Wiley.
Kimura, Y. (1997). “Tribology as a maintenance tool,” in New Directions in Tribology, ed I. M. Hutchings (London: Mechanical Engineering Publications Limited, 299–308.
Kole, P. J., Löhr, A. J., Van Belleghem, F. G. A. J., and Ragas, A. M. J. (2017). Wear and tear of tyres: a stealthy source of microplastics in the environment. Int. J. Environ. Res. Public Health 14:1265. doi: 10.3390/ijerph14101265
Krick, B. A., Muratore, C., Burris, D. L., Carpick, R. W., Prasad, S. W., Korenyi-Both, A., et al. (2013). “Space tribology: experiments in low earth orbit,” in Proceedings of the 5th World Tribology Congress WTC2013 (Torino).
Landerl, H. (2018). New Bearings for High-Speed Applications. Available online at: http://evolution.skf.com/new-bearings-for-high-speed-applications/
Lele, A. (2019). “Industry 4.0. chapter 13,” in Disruptive Technologies for the Militaries and Security. Smart Innovation, Systems and Technologies, Vol. 132 (Singapore: Springer).
Li, Y., Domrös, R., and Rodriguez, S. (2017). Enough is Enough. Available online at: http://evolution.skf.com/minimum-quantity-lubrication-reduces-total-cost-of-ownership/
Liao, Y., Deschamps, F., de Freitas Rocha Loures, E., and Ramos, L. F. P. (2017). Past, present and future of Industry 4.0—a systematic literature review and research agenda proposal. Int. J. Prod. Res. 55–12, 3609–3629. doi: 10.1080/00207543.2017.1308576
Lu, Y. (2017). Industry 4.0: a survey on technologies, applications and open research issues. J. Ind. Info. Integr. 6, 1–10. doi: 10.1016/j.jii.2017.04.005
Mang, T., Bobzin, K., and Bartels, T. (2011). Industrial Tribology: Tribosystems, Friction, Wear and Surface Engineering, Lubrication. Oxford: Wiley.
Marklund, P. (2017). “Tribo-condition monitoring for optimized performance and longer service life,” in Proceedings World Tribology Congress (Beijing).
Masuko, M., and Sugimura, J. (2017). Special issue on automotive tribology. Tribology 12, 1–8. doi: 10.2474/trol.12.i
Mathé, F., and Grellier, A. (2016). Reliable Motor Control with Newest Generation SKF Sensor Bearings. Available online at: http://evolution.skf.com/reliable-motor-control-with-newest-generation-skf-sensor-bearings/
Moon, F. C. (1993). Superconducting Levitation—Applications to Bearings and Magnetic Transportation. New York, NY: John Wiley & Sons, Inc.
Morales-Espejel, G. E., and Wemekamp, A. W. (2018). Ertel–Grubin methods in elastohydrodynamic lubrication—a review. Proc. IMechE J Eng. Tribol. 222, 15–34. doi: 10.1243/13506501JET325
Murphy, M., Leigh-Jones, C., Kent, T., and Baldwin, A. (2005). “New generation of smart sensors,” in Proceedings of WTC2005 (Washington, DC).
Nakano, K., Kimura, Y., Kato, T., and Morishita, S. (1995). “Active control of friction with liquid crystals,” in Int Tribological Conference (Yokohama).
Neale, M. J. (1997). “Tribology and the needs of industry,” in New Directions in Tribology, ed I. M. Hutchings (London: Mechanical Engineering Publications Limited, 57–65.
Newberry, P. E., and Fraser, G. W. (1895). El Bersheh. Part 1. The Tomb of Tehuti-Hetep. Egypt Exploration Fund: London.
Nosonovsky, M., and Bhushan, B. (2012). Green Tribology—Biomimetics, Energy Conservation and Sustainability. Berlin: Springer.
O'Connor, J. J., and Boyd, J. (1968). Standard Handbook of Lubrication Engineering. Oxford: McGraw-Hill.
Peng, Z., and Kessissoglou, N. (2003). An integrated approach to fault diagnosis of machinery using wear debris and vibration analysis. Wear 255, 1221–1232. doi: 10.1016/S0043-1648(03)00098-X
Perricone, G., Matějka, V., Alemani, M., Valota, G., Bonfanti, A., Ciotti, A., et al. (2018). A concept for reducing PM10 emissions for car brakes by 50%. Wear 396–397, 135–145. doi: 10.1016/j.wear.2017.06.018
Pfeiffer, S. (2017). The Vision of “Industrie 4.0” in the Making—A Case of Future Told, Tamed, and Traded. Nanoethics 11, 107–121. doi: 10.1007/s11569-016-0280-3
Phulé, P. P. (2001). Magnetorheological (MR) fluids: principles and applications. Smart Mater. Bull. 2001, 7–10. doi: 10.1016/S1471-3918(01)80016-2
Popov, V. L. (2018). Is tribology approaching its golden age? Grand challenges in engineering education and tribological research. Front. Mech. Eng. 4, 1–6. doi: 10.3389/fmech.2018.00016
Popova, E., and Popov, V. L. (2015). On the history of elastohydrodynamics: the dramatic destiny of Alexander Mohrenstein-Ertel and his contribution to the theory and practice of lubrication. Angew. Math. Mech. 95, 652–663. doi: 10.1002/zamm.201400050
Randall, R. B. (2016). Vibration-based diagnostics of gearboxes under variable speed and load conditions. Meccanica 51, 3227–3239. doi: 10.1007/s11012-016-0583-z
Reynolds, O. (1886). On the Theory of Lubrication and Its Application to Mr. Beauchamp Tower's Experiments, Including an Experimental Determination of the Viscosity of Olive Oil. London: Philosophical Transactions of the Royal Society of London.
Roser, C. (2015). Industry 4.0 Wikipedia. Available online at: https://en.wikipedia.org/wiki/File:Industry_4.0.png
Roylance, B. J. (2003). Machine failure and its avoidance—what is tribology's contribution to effective maintenance of critical machinery? Proc. J. Eng. Tribol. 217, 349–364. doi: 10.1243/135065003322445278
Salazar, J. G., and Santos, I. F. (2017a). Active tilting-pad journal bearings supporting flexible rotors: Part I—The hybrid lubrication. Tribol. Int. 107, 94–105. doi: 10.1016/j.triboint.2016.11.018
Salazar, J. G., and Santos, I. F. (2017b). Active tilting-pad journal bearings supporting flexible rotors: Part II—The model-based feedback-controlled lubrication. Tribol. Int. 107, 106–115. doi: 10.1016/j.triboint.2016.11.019
Santos, C., Mehrsai, A., Barros, A. C., Araújo, M., and Aresc, E. (2017). Towards Industry 4.0: an overview of European strategic roadmaps. Procedia Manufact. 13, 972–979. doi: 10.1016/j.promfg.2017.09.093
Schmidt, H., and Schwartz, J. (2014). Energy-Efficient Minimal Quantity Lubrication for High-Speed Spindles. Available online at: http://evolution.skf.com/energy-efficient-minimal-quantity-lubrication-for-high-speed-spindles/
Sendler, U. (2013). Industry 4.0. Beherrschung der Industriellen Komplexität mit SysLM. Berlin, Heidelberg: Springer Vieweg.
Shareef, I., and Natarajan, M. (2005). “Dry machinability of aluminium alloys,” in Proceedings of WTC2005 (Washington, DC).
Sommer, F., Dietze, V., Baum, A., Sauer, J., Gilge, S., Maschowski, C., et al. (2018). Tire abrasion as a major source of microplastics in the environment. Aerosol Air Qual. Res. 18, 2014–2028. doi: 10.4209/aaqr.2018.03.0099
Stachowiak, G. W. (2017). How tribology has been helping us to advance and to survive. Friction 5, 233–247. doi: 10.1007/s40544-017-0173-7
Stadler, K., Han, B., Brizmer, V., and Pasaribu, R. (2015). Benefits of Using Black Oxidized Bearings in Wind Applications. Available online at: http://evolution.skf.com/benefits-of-using-black-oxidized-bearings-in-wind-applications/
Tandon, N., Ramakrishna, K. M., and Yadava, G. S. (2007). Condition monitoring of electric motor ball bearings for the detection of grease contaminants. Tribol. Int. 40, 29–36. doi: 10.1016/j.triboint.2006.01.024
Tolochko, O. V., Michailov, V. G., and Rudskoi, A. I. (2017). “Metal matrix/nanocarbons composites based on copper and aluminum,” in Industry 4.0—Entrepreneurship and Structural Change in the New Digital Landscape, eds T. Devezas, J. Leitão, and A. Sarygulov (Oxford: Springer International Publishing AG), 205–217. doi: 10.1007/978-3-319-49604-7_10
Tung, S. C., Paxton, C., and Liang, F. (2005). “Overview and future trends of manufacturing lubrication and conditioning monitoring technologies,” in Proceedings of WTC2005 (Washington, DC).
United Nations (2015). Sustainable Development Goals. Available online at: https://www.un.org/sustainabledevelopment/sustainable-development-goals/
Van Camp, V. (2018). Industry's Fourth Big Wave. Available online at: http://evolution.skf.com/industrys-fourth-big-wave/
Vieillard, C., Brizmer, V., Kadin, Y., Morales-Espejel, G. E., and Gabelli, A. (2017). Benefits of Hybrid Bearings in Severe Conditions. Available online at: http://evolution.skf.com/benefits-of-hybrid-bearings-in-severe-conditions/
Weidinger, A. (2009). 100 Years Evolution of Cylindrical Roller Bearings. Available online at: http://evolution.skf.com/100-years-evolution-of-cylindrical-roller-bearings/
Winters, J. (2018). By the numbers: sensing excitement. Mech. Eng. 140, 28–29. doi: 10.1115/1.2018-JAN-1
Woidt, M. (1997). “Materials-based concepts for an oil-free engine,” in New Directions in Tribology, ed I. M. Hutchings (London: Mechanical Engineering Publications Limited, 459–468.
Keywords: tribology, industry, history of tribology, industrial revolutions, industry 4.0, industrial tribology, tribology 4.0
Citation: Ciulli E (2019) Tribology and Industry: From the Origins to 4.0. Front. Mech. Eng. 5:55. doi: 10.3389/fmech.2019.00055
Received: 02 May 2019; Accepted: 19 August 2019;
Published: 03 September 2019.
Edited by:
Alessandro Ruggiero, University of Salerno, ItalyReviewed by:
Ille C. Gebeshuber, Vienna University of Technology, AustriaCopyright © 2019 Ciulli. This is an open-access article distributed under the terms of the Creative Commons Attribution License (CC BY). The use, distribution or reproduction in other forums is permitted, provided the original author(s) and the copyright owner(s) are credited and that the original publication in this journal is cited, in accordance with accepted academic practice. No use, distribution or reproduction is permitted which does not comply with these terms.
*Correspondence: Enrico Ciulli, Y2l1bGxpQGluZy51bmlwaS5pdA==
Disclaimer: All claims expressed in this article are solely those of the authors and do not necessarily represent those of their affiliated organizations, or those of the publisher, the editors and the reviewers. Any product that may be evaluated in this article or claim that may be made by its manufacturer is not guaranteed or endorsed by the publisher.
Research integrity at Frontiers
Learn more about the work of our research integrity team to safeguard the quality of each article we publish.